加工余量查询
毛坯加工余量表

工件直径(D)
工 件 长 度 L
<10
11-20
21-45
46-100
101-250
直径上加工余量???????????? 长度方向上余量
150-200
5??? 5
5??? 5
5???? 5
5???? 6
5????? 7
201-300
5??? 6
5??? 6
5???? 6
5???? 7
6????? 8
(毫米)
工件直径(D)
工 件 长 度 L
车刃的割刀量和车削二端面的余量(每件)
<70
71-120
121-200
201-300
301-450
直 径 上 加 工 余 量
≤32
1
2
2
3
4
5-10
33-60
2
33Leabharlann 454-6
61-100
3
4
4
4
5
4-6
101-200
4
5
5
5
6
4-6
?
当D<36时并不适应于调头夹加工,在加工单个工件时,应在L上加夹头量10-15。
301-400
5??? 7
5??? 7
5???? 7
6???? 8
8????? 9
401-500
7??? 8
5??? 8
6???? 8
7???? 9
9???? 10
501-600
7??? 8
6??? 8
6???? 8
7??? 10
10??? 11
注:表中的加工余量为最小余量,其最大余量不得超过厂规定标准。
加工余量参数表

附录三加工余量参数表表 1 粗车、半精车外圆的加工余量(单位:mm)注:加工带凸台的零件时,其加工余量要根据零件的全长和最大直径来确定。
表 2 精车外圆的加工余量(单位:mm)1.舍五入)。
这时的粗车外圆的公差等级为14 级。
2. 决定加工余量用轴的长度计算与装夹方式有关。
3. 粗车外圆的公差带相当于h12~h13。
注:1. 在单件或小批生产时,本表的余量值应乘上系数,并化成一位小数,如×=,采用(四舍五入)。
2. 决定加工余量用轴的长度计算与装夹方式有关。
3. 磨前加工公差相当于h11。
表 4 精车端面的加工余量(单位:mm)1. d2. 表中的公差系指尺寸L 的公差。
表 5 磨端面的加工余量(单位:mm)注: 1. 加工有台阶的轴时,每台阶的加工余量应根据该台阶的d 及零件的全长分别选用。
2. 表中的公差系指尺寸L 的公差。
加工孔直径钻用车刀 扩孔钻粗铰精铰的直径第一次第二次镗以后3- - - - 3H7 4- - - - 4H7 5-- - - 5H7 6- - --6H7 8-- -8H7 10- --10H712--12H7 13- -13H7 14--14H715- -15H7 16--16H718- -18H7 20-20H7 22-22H724-24H7 25-25H726-26H7 28-28H7302830H7 3232H7 3535H73838H7 4040H74242H7 4545H74848H7 5050H760 3060H7 70 3070H780 3080H790 30-90H7 100 30-100H7120 30-120H7 140 30-140H716030-160H7 180 30-180H7注: 1. 在铸铁上加工直径到 15mm 的孔时,不用扩孔钻扩孔。
2. 在铸铁上加工直径为 30 到 32mm 的孔时,仅用直径为 28 与 30mm 的钻头钻一次。
工序间加工余量
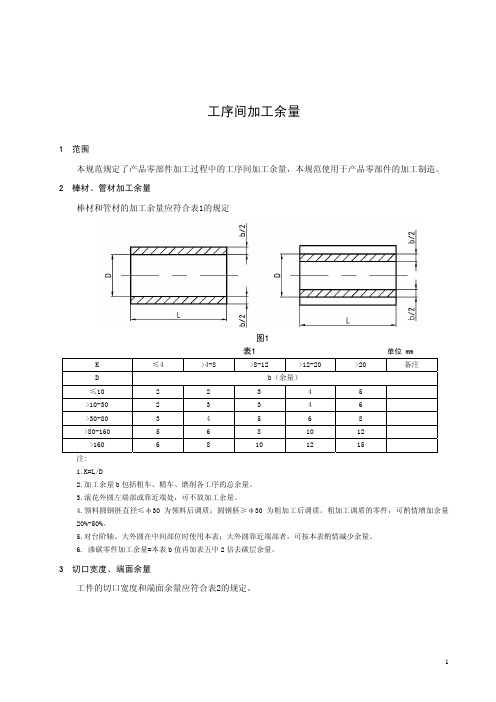
工序间加工余量1 范围本规范规定了产品零部件加工过程中的工序间加工余量,本规范使用于产品零部件的加工制造。
2 棒材、管材加工余量棒材和管材的加工余量应符合表1的规定图1表1单位 mm K ≤4 >4-8 >8-12 >12-20 >20 备注D b(余量)≤10 2 2 3 4 5>10-30 2 3 3 4 6>30-80 3 4 5 6 8>80-160 5 6 8 10 12>160 6 8 10 12 15注:1.K=L/D2.加工余量b包括粗车、精车、磨削各工序的总余量。
3.滚花外圆左端部或靠近端处,可不放加工余量。
4.领料圆钢胚直径≤φ30为领料后调质;圆钢胚≥φ30为粗加工后调质。
粗加工调质的零件,可酌情增加余量20%-50%。
5.对台阶轴、大外圆在中间部位时使用本表;大外圆靠近端部者,可按本表酌情减少余量。
6. 渗碳零件加工余量=本表b值再加表五中2倍去碳层余量。
3 切口宽度、端面余量工件的切口宽度和端面余量应符合表2的规定。
图2表2单位 mm 毛胚直径D 切口宽度a 二端总余量b 备注 ≤20 3 2>20-50 4 3>50-80 5 4>80-120 5>120-160 6>160 8注:1.粗加工调质的零件,切口宽度不变,端面余量可酌情增加余量20-50%。
2.渗碳零件端面余量应为本表b值再加表5中2倍去碳层余量(如一端面加工者则加单面去碳层余量)。
3.带孔零件切口宽度余量。
应将带孔零件壁厚折算成本表D/2后对照选用。
4 夹头留量夹头留量应符合表3的规定。
表3单位 mm 工件长度 ≤50 >50-150 >150-300 >300毛胚直径 夹头留量≤20 15 15 15 15>20-80 15 15 20 20>80-160 15 20 20 25 注:1.本表为单件坯料的夹头留量(包括多件坯料)。
精车余量
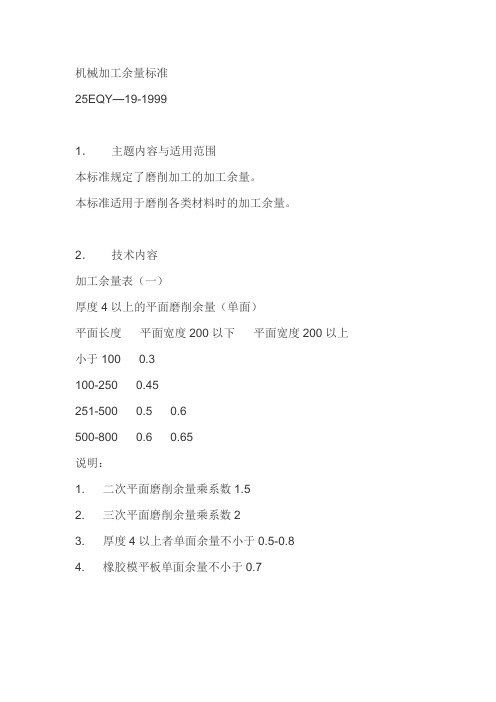
机械加工余量标准25EQY—19-19991.主题内容与适用范围本标准规定了磨削加工的加工余量。
本标准适用于磨削各类材料时的加工余量。
2.技术内容加工余量表(一)厚度4以上的平面磨削余量(单面)平面长度平面宽度200以下平面宽度200以上小于100 0.3100-250 0.45251-500 0.5 0.6500-800 0.6 0.65说明:1. 二次平面磨削余量乘系数1.52. 三次平面磨削余量乘系数23. 厚度4以上者单面余量不小于0.5-0.84. 橡胶模平板单面余量不小于0.7毛坯加工余量表(二)I:园棒类:(1)工件的最大外径无公差要求,光洁度在▽以下,例:不磨外圆的凹模带台肩的凸模、凹模、凸凹模以及推杆、推销、限制器、托杆、各种螺钉、螺栓、螺塞、螺帽外径必须滚花者。
(毫米)工件直径(D)工件长度L 车刃的割刀量和车削二端面的余量(每件)<70 71-120 121-200 201-300 301-450直径上加工余量≤32 1 2 2 3 4 5-1033-60 2 3 3 4 5 4-661-100 3 4 4 4 5 4-6101-200 4 5 5 5 6 4-6当D<36时并不适应于调头夹加工,在加工单个工件时,应在L上加夹头量10-15。
(2)工件的最大外径有公差配合要求,光洁度在▽以上,例如:外圆须磨加工的凹模,挡料销、肩台须磨加工的凸模或凸凹模等。
(毫米)工件直径(D)工件长度L 车刃的割刀量和车削二端面的余量(每件)<50 51-80 81-150 151-250 251-420直径上加工余量≤15 3 3 4 4 5 5-1016-32 3 4 4 5 6 5-1033-60 4 4 5 6 6 5-861-100 5 5 5 6 7 5-8101-200 6 6 6 7 7 5-8当D<36时,不适合调头加工,在加工单个零件时,应加夹头量10 -15。
毛坯加工余量表(三)Ⅱ:圆形锻件类(不需锻件图)(1)不淬火钢表面粗糙度在▽以下无公差配合要求者,例如:固定板、退料板等。
第13章 工序间加工余量
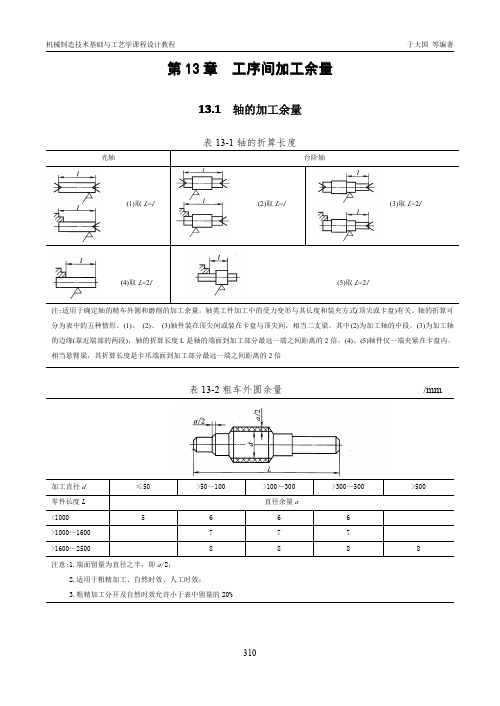
2.表中的公差系指尺寸 L 的公差,当原公差大于该公差时,尺寸公差为原公差值;
3.加工套类零件时余量值可适当增加
13.2 孔、槽的加工余量
表 13-10 精车(铣、刨)槽余量
于大国 等编著 1.2 1.4 1.5 1.7 -0.8
/mm
>500 0.6 0.6 0.6 0.7 0.7 0.8 -0.5
/mm
加工 孔的 直径
钻 第一次 第二次
直径
用车刀 扩孔钻
镗以后
粗铰
精铰 H7 或 H8、H9
加工 孔的 直径
直径
钻 用车刀 扩孔
第一次 第二次 镗以后 钻
粗铰
精铰 H7 或 H8,
H9
3
2.9
-
-
-
-
3
24 22.0
-
23.8 23.8 23.94 24
4
3.9
-
-
-
-
4
25 23.0
-
24.8 24.8 24.94 25
0.3
0.3
0.4
0.5
0.6
>120~260
0.4
0.4
0.5
0.5
0.6
>260~500
0.5
0.5
0.5
0.6
0.7
>500
0.6
0.6
0.6
0.7
0.8
长度公差
-0.12
-0.17
-0.23
-0.3
-0.4
注: 1.加工有台阶的轴时,每个台阶的加工余量应根据该台阶直径 d 及零件的全长 L 分别选用;
≤100
0.2 0.3 0.2 0.3 0.2 0.3 0.2 0.3 0.3 0.3 0.3 0.3 0.3 0.4
加工余量、工序尺寸与及公差的确定
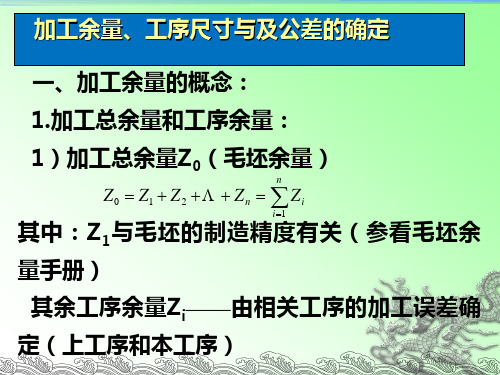
差的选择与标注按:公差等级、配合种类来确 定上下偏差)。
工序余量示意图(图1-40) 1) 轴类尺寸,毛坯 2) 孔类尺寸:毛坯:
2.影响加工余量的因素: 1)上工序的尺寸公差参看图4-21(工序1
余量与毛坯精度有关) 2)上工序的粗糙度Ry和缺陷层Ha(表4-10) 3)上工序的空间误差ea(形状位置误差)
i 1
• 总余量不够,质量得不到保证
• 总余量太大,增加劳动量、消耗、成本
• 总余量与毛坯精度、生产类型、批量大小 有关
机加械工余制量造的工确定艺与机床夹具
2.影响加工余量的因素
• 上道工序的表面质量(包括表面粗糙度Ha 和表面破坏层深度Sa)
• 前道工序的工序尺寸公差(Ta) • 前道工序的位置误差(ρa ) • 本工序工件的安装误差(εb) • 本工序的加工余量必须满足下式:
1、与设计尺寸有关的工序尺寸L01¨、L1¨。 2、中间工序尺寸(与余量有关)Z4、Z5、Z6 3、查找工艺尺寸链,画尺寸链图¨ (三)计算项目 1、确定公差与余量(经济精度与调整) 2、计算余量变动量,平均余量,平均工序尺 寸。 注:粗加工工序毛坯余量较大,可不计算。 3、按“入体”原则标注工序尺寸。
尺寸链中封闭环只有一个,用L0表示。 工艺尺寸链中的封闭环的定义见P.53倒10行。
⑴封闭环一定是工艺过程中间接保证的尺 寸。
⑵封闭环公差值最大,它等于各组成环公 差之和。
3)组成环——尺寸链除封闭外其余各环, 组成环分为增环和减环。
⑴增环—该环变动引起封闭环同向变动。 ⑵减环—该环变动引起封闭环反向变动。
例:图4-22轴线弯曲造成的余量不均匀误差。 各项位置误差造成的影响参看表4-11
加工余量和切削参数表
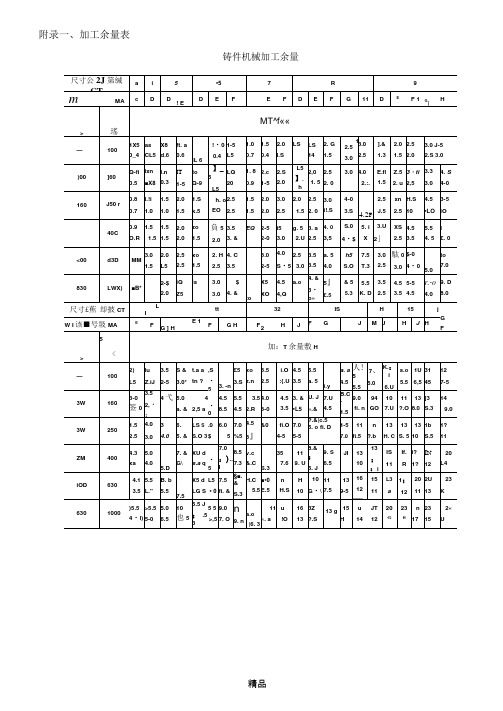
附录一、加工余量表铸件机械加工余量表磨孔余量ft 4-29平面租刨后精诜的加工余■/mm/mm表脣30铳平面的加工余・寬度冬200 寬度>200〜400 宽直M200 «« >200-400加工表面不同长度下的加工余・*8-31 ■平面的加工余・/mm魚处理后«8-33绩面的加工余■/mm« 879各种加工方法所能达到的表面粗糙度/pm 加工方法&值1 加工方法R•值车削外圆10 〜80 圜柱优刀半精车 2. 5 〜10 2. 5 〜20 精车1・25〜10 精饶0. 63〜5.细车0・16〜1・25 细饶0. 32〜1. 25 车削端面-一 - .................粗丰5〜20 aft 2. 5—20 半精车 2. 5〜10 0. 32 〜5 精车】・25〜10 细饶0.167 25 细车“0. 327 25 髙速饶IW车削割槽和切斷粗铳手炉“・・0. 63〜2・5 一次行程10〜20 0. 16~0・ 63 二次行程 2.5-10 刨削僮孔5〜20 粗僅5〜20 精刨1・25〜10 半箱桃2・5〜10 细刨(光»mi)0・16〜1・25 梢铿0・63〜5 槽的表面 2. 5 〜10 细蚀(金刚键床贰孔〉0・16〜1・25 插削 2. 5〜20钻孔 1.25 〜20 拉削扩孔精拉0. 32-2. 5 粗扩(有毛面)5〜20 细拉0. 08〜0・ 32 梢扩 1.25-10 推削储孔•倒角1・25〜5 精推0.16〜1・ 25 较孔细推0. 02〜0・ 63 • 一次较孔嫖纹加工钢2・5〜10 |用板牙、丝傩•自动张开式板牙头0. 63~5附录二、切削***、/ » 8-50碘质合蚩及髙連解车刀粗车外■和■面时的进给■注,1. 1JUT斷续表面及肓冲击时.表内的进给■应象票数K・0・75〜0.85.2. 加工酚热制及其合金不采用大于1.0mm/r的进给*.3. 加工淬缺钢时.我内进给it应桑系数K・0・8 (当材料硬度为44〜56HHC)或K-0. 5《当竇度为57〜62HRC时).表8・52切断及切槽的进给■注,1 •在直径大于60mm 的实心村料上切断时•当切刀接近峯件轴线0・5倍半径时・表中进给量应减小40% 〜50%.2.加工淬理钢时.表内进给量应橄小30% (当现度小于50HRC 时)或50% (当硬度大于50HRC 时).» 8-55切断和切槽时的切削用■/ft 8-57外圓切削速度參考袁,1・6090min.2.车孔切削速度要比车外圆时低10%〜20%.衰8・69高連•祸钻头钻孔时的进给■估头直径几/mm钢 %/MPa铸铁、铜、铝合金硬度<800800〜1000>1000<200HBS>200HBS进给 就//mm •◎0. 05 〜0・ 0§ . 0. 04 〜0・ 05 - 0. 03〜0・04・ 0. 09 〜0・ 11 0. 05—0. 07 >2〜4 0. 08-0.10 0. 06—0. 08 0. 04 〜0・ 06 0. 18 〜0・ 22 •0.11-0.13 >4〜6 0・14〜0・10 0・10〜0・12 0. 08 〜0・ 10 0. 27 〜0・ 33 0. 18-0. 22 >6〜8 0. 18 〜0・ 22 0・13〜0・15 0. 11-0. 13 0. 36〜0・ 44 0. 22 〜0・ 26 >8 〜10 0. 22 〜0・ 28 0.17-0.21 0. 13 〜0・ 17 0. 47〜0・ 57 0. 28 〜0・ 34 >10 〜13 0. 25 〜0・ 31 0.19-0. 23 0. 15 〜0. 19 0. 52〜0・ 64 0・3】〜0・39 >13~160・31〜0・37 0. 22 〜0・ 28 0・】8〜0・22 0.61-0. 75 0. 37 〜0・ 45 >】6〜200. 35〜0・ 43 0. 26 〜0・ 32 0.21-0. 25 0. 70〜0・ 86 0. 43〜0・ 53 >20 〜250. 39〜0.47 0. 29〜0・ 35 0. 23 〜0・ 29 0. 78-0. 96 0. 47〜0・ 57 >25 〜30 0・45〜0・55 0. 32〜0・ 40 0. 27 〜0・ 33 0. 9〜1・1 0. 54〜0・ 66 >30 〜600. 60〜0・ 700. 40〜0・ 500. 30〜0・ 401・0〜1・20. 70 〜0・ 80tt钻头直径必/mm工艺婴 求分类InIn进给 最 //mm •严0. 22*0. 280.8r 0・ 22 0.】8〜0. 22 Q. 13-0.17 >8~12 0. 20〜0・ 36 0. 22 〜0・ 28 0. 25 〜30 0.18〜0・ 22 >12 〜160. 25〜0・ 40 0. 25 〜0・ 30 0・ 28 〜0. 24 0. 20〜0・ 25 1>16 〜20 0. 40〜0・ 48 0. 27〜0・ 33 0. 32〜0・ 28 0・23〜0・28、 >20 〜24 0. 45~0・ 55 0. 33〜0・ 38 0. 38〜0. 43 0. 27〜0・ 32 >24 〜26 0. 50〜0・ 60 0. 37〜0・ 41 0・ 40〜0. 46 0. 32~0・ 28 >20 〜300. 55 〜0・ 650. 40〜0・ 500. 45 〜0. 500. 36〜0・ 44>200HBS復质合金YG8钻头鮎灰铸铁时的进给■/m-1丧8・99各种常用工件材料的饶剤琼度推荐范BI如有侵权请联系告知删除,感谢你们的配合!。
加工余量查询
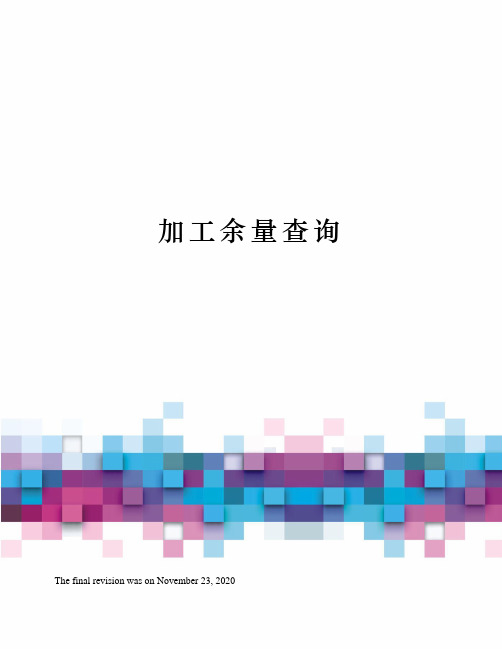
加工余量查询The final revision was on November 23, 2020表7-1 模具常用加工方法的加工余量、加工精度、表面粗糙度加工结果等具体情况而定。
1.加工总余量的确定(1)加工总余量和工序余量加工总余量(毛坯余量)—毛坯尺寸与零件图设计尺寸之差。
工序余量—相邻两工序的工序尺寸之差。
某个表面加工余量Z∑为该表面各加工工序的工序余量Zi之和,即式中n—该表面的加工工序数。
(2)影响加工余量的因素1)加工表面上的表面粗糙度和表面缺陷层深度。
2)加工前或上工序的尺寸公差。
3)加工前或上工序各表面相互位置的空间偏差。
4)本工序加工时的装夹误差。
(3)查表法确定机械加工余量,总余量和半精加工、精加工工序余量可参考有关标准或工艺手册查得,并应结合实际情况加以修正。
粗加工工序余量减去半精加工和精加工工序余量而得到。
2. 工序尺寸及公差计算对于各种工序的定位基准与设计基准重合时的表面的多次加工(如外圆和内孔的加工),工序尺寸可由后续加工的工序尺寸加工上(对被包容面)或减去(对包容面)公称工序余量而求得;工序尺寸公差按所用加工方法的经济精度选定。
图4-2 表示外圆加工时加工余量、工序尺寸及其公差的分布,图中Z1、Z2、Z3为粗加工、半精加工、精加工的公称余量;To为毛坯公差。
T1 、T2、T3为粗加工、半精加工、精加工的工序尺寸公差。
当各工序的公称余量和公差确定后,卡按下面顺序计算每一工序的工序尺寸;终加工(精加工)工序尺寸A3,公差T3由零件图规定。
半精加工的工序尺寸A2=A3+ Z3,公差为T2.粗加工的工序尺寸A1= A2+ Z2,公差为T1。
毛坯尺寸Ao= A1+Z2。
公差为To。
工序尺寸的公差一般应按“入体原则”标注,而在毛坯的基本尺寸上一般都注以双向偏差。
当基准不重合时,或零件在加工过程中需要多次转换工序基准,或工序尺寸尚需在继续加工的表面上标注时,有关工序的工序尺寸及其公差,则需通过尺寸链的分析,计算得到。
加工余量

(1)、加工尾座体的底平面,粗糙度要求为Ra=1.6,采用粗铣—精铣—刮研。
粗铣余量2.7mm,精铣余量0.9mm,刮研余量0.15mm。
(2)、加工尾座体的两侧孔端面,粗糙度要求为Ra=3.2,采用粗铣—半精铣。
采用两次铣加工(粗、精铣)可以满足,粗铣余量取2mm,精铣余量取1mm。
(3)、加工尾座体的前侧面阶梯孔端面,粗糙度要求为Ra=6.3,采用粗铣—半精铣。
加工方法同上。
粗铣深度取1.5mm。
(4)、加工右侧小凸台,粗糙度要求为Ra=3.2,采用粗铣—半精铣。
粗铣余量取1mm,精铣余量取0.7mm。
(5)、加工Φ40H6孔,粗糙度要求Ra=0.4,采用粗镗—半精镗—精镗—浮动镗刀块精镗。
采用粗镗和半精镗、精镗和浮动镗刀块精镗的方式,故考虑分四次进行镗加工。
取粗镗双边余量3mm,半精镗双边余量1.5mm,精镗单边余量0.5mm,浮动镗刀块精镗的双边余量0.2。
(6)、加工肩Φ20H7的孔,粗糙度要求Ra=1.6,采用钻—扩—铰。
钻的单边余量为9mm,扩的单边余量为0.9mm,铰的单边余量为0.1mm。
(7)、加工Φ20H9的凸台孔,粗糙度要求Ra=3.2,采用钻—扩—铰。
钻的单边余量为9mm,扩的单边余量为0.9mm,铰的单边余量为0.1mm。
(8)、加工前侧面Φ10H9孔,粗糙度要求Ra=3.2,采用钻—铰。
采用钻—铰的加工方式,钻的单边余量为4.9mm,再铰加工即可满足要求。
(9)、加工两个阶梯孔,孔内壁粗糙度要求均为Ra=12.5,,采用钻Φ14大孔—钻Φ10小孔,锪出阶梯的加工方式。
(10)、加工Φ6H7后侧面孔和Φ6H7下表面底孔,粗糙度要求Ra=1.6,采用钻—铰。
一次钻不能满足要求,故采用钻—铰的加工方式,钻至直径Φ5.8,再铰加工。
(11)、加工M8和M5螺纹孔,由【7】213页M8螺纹孔:首先选用Φ7的麻花钻头进行钻加工,再用丝锥攻M8螺纹。
M5螺纹孔:首先选用Φ4.2的麻花钻头进行钻加工,再用丝锥攻M5螺纹。
工序间加工余量
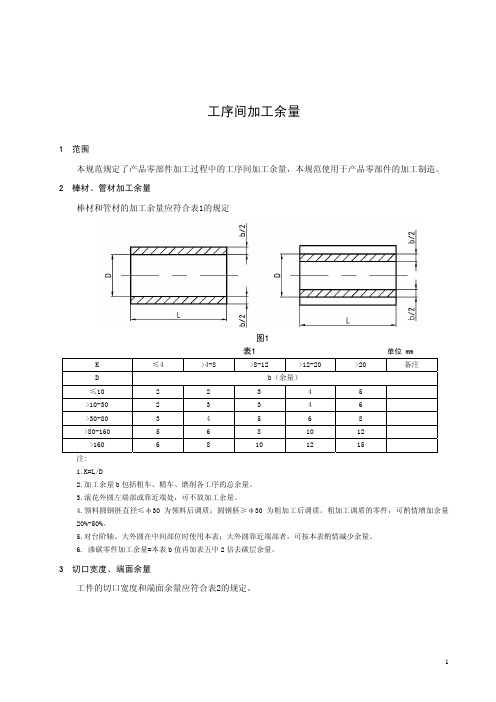
工序间加工余量1 范围本规范规定了产品零部件加工过程中的工序间加工余量,本规范使用于产品零部件的加工制造。
2 棒材、管材加工余量棒材和管材的加工余量应符合表1的规定图1表1单位 mm K ≤4 >4-8 >8-12 >12-20 >20 备注D b(余量)≤10 2 2 3 4 5>10-30 2 3 3 4 6>30-80 3 4 5 6 8>80-160 5 6 8 10 12>160 6 8 10 12 15注:1.K=L/D2.加工余量b包括粗车、精车、磨削各工序的总余量。
3.滚花外圆左端部或靠近端处,可不放加工余量。
4.领料圆钢胚直径≤φ30为领料后调质;圆钢胚≥φ30为粗加工后调质。
粗加工调质的零件,可酌情增加余量20%-50%。
5.对台阶轴、大外圆在中间部位时使用本表;大外圆靠近端部者,可按本表酌情减少余量。
6. 渗碳零件加工余量=本表b值再加表五中2倍去碳层余量。
3 切口宽度、端面余量工件的切口宽度和端面余量应符合表2的规定。
图2表2单位 mm 毛胚直径D 切口宽度a 二端总余量b 备注 ≤20 3 2>20-50 4 3>50-80 5 4>80-120 5>120-160 6>160 8注:1.粗加工调质的零件,切口宽度不变,端面余量可酌情增加余量20-50%。
2.渗碳零件端面余量应为本表b值再加表5中2倍去碳层余量(如一端面加工者则加单面去碳层余量)。
3.带孔零件切口宽度余量。
应将带孔零件壁厚折算成本表D/2后对照选用。
4 夹头留量夹头留量应符合表3的规定。
表3单位 mm 工件长度 ≤50 >50-150 >150-300 >300毛胚直径 夹头留量≤20 15 15 15 15>20-80 15 15 20 20>80-160 15 20 20 25 注:1.本表为单件坯料的夹头留量(包括多件坯料)。
加工余量表

表1轴类调质余量单位:mm
表2齿轮调质余量单位:mm
表3齿圈调质余量单位:mm
表4轴类热处理后外圆磨前半精车(磨削余量)(调用)单位:mm
(2)对于淬火的零件,淬火前半精加工余量应为表中数值乘以1.25;
(3)磨前粗糙度不大于Ra6.3;
表5 渗碳、淬火齿面内外圆(非渗表面涂防渗剂)加工余量(mm)表(试用)
表6渗碳,淬火前齿轮半精车:内孔及端面磨削余量与公差(mm)(一分厂试用)
表7渗碳淬火后精车齿轮:内孔及端面磨削余量与公差(mm)(一分厂试用)
表8 渗碳、淬火齿轮粗滚齿公法线余量(mm) (一分厂试用)
表9渗碳、淬火齿轮粗滚齿公法线余量(mm) (三分厂试用)
表10渗碳、淬火齿轮粗滚齿公法线余量(mm) (四分厂试用)
表11软齿面及中硬齿面粗滚齿余量单位:mm
表12中硬齿面Mn>12热处理(调质)前粗滚齿及齿外圆余量(试用)单位:mm
表13渗碳淬火弧齿锥齿轮磨前铣齿:齿厚留磨余量与公差(mm)(三分厂试用)
表14分箱面焊接箱体粗加工后人工时效余量(试用)单位:mm
表15 分箱面焊接箱体粗加工后振动时效余量(试用)单位:mm
表16铸铁箱体(平行轴)粗加工后人工时效余量单位:mm。
加工余量计算

零件的 公称尺寸 5 6 8 10 11 12 14 16 17 18 19 20 21 22 25 27 28 30 32 33 35 36 37 38 40 42 44 45 46
50 55 60 65 70 75 80 85 90 95 100 110 120 130 95 100 105 115 125 140 150
1.带台阶的轴,如最大直径接近于中间部分,应按最大直径选择毛坯的直径; 如最大直径接近于端部,毛坯直径可以小些。 2.毛坯长度上的余量可选2~6mm。
为350+5=355mm。
=58mm。
54 60 65 70 75 80 85 90 95 105 110 120 125 140 150
55 60 65 70 75 85 90 95 100 105 110 120 130 140 150
55 60 70 75 80 85 90 95 100 105 110 120 130 140 150
1.热轧钢轴类外圆的加工余量 车外圆时总的加工余量,可以根据工件的长度和直径的比值在表中差得。 例 有一根直径40mm、长度350mm的轴,求毛坯的尺寸? L/D=350/40=8.75 查表得到毛坯直径应为45mm,则加工余量为45-40=5mm,长度为350+5=355mm。 例 有一根直径14mm、长度56mm的轴,求毛坯的尺寸? L/D=56/14=4 查表得到毛坯直径应为16mm,则加工余量为16-14=2mm,长度为56+2=58mm。 零件的长度与公称直径之比 ≤4 4~8 8~12 12~20 毛坯的直径 7 7 8 8 8 8 8 8 10 10 10 11 12 12 13 13 14 14 14 14 14 14 15 15 16 16 17 18 18 18 18 19 19 19 20 21 20 20 21 22 21 21 22 23 22 22 23 24 24 24 24 25 25 25 26 26 28 28 28 30 30 30 32 32 32 32 32 32 33 33 34 34 35 35 36 36 36 38 38 38 38 38 39 39 39 40 40 40 40 42 42 42 42 42 42 43 43 45 45 45 45 48 48 48 48 48 50 50 48 48 50 50 50 52 52 52
加工余量参数表
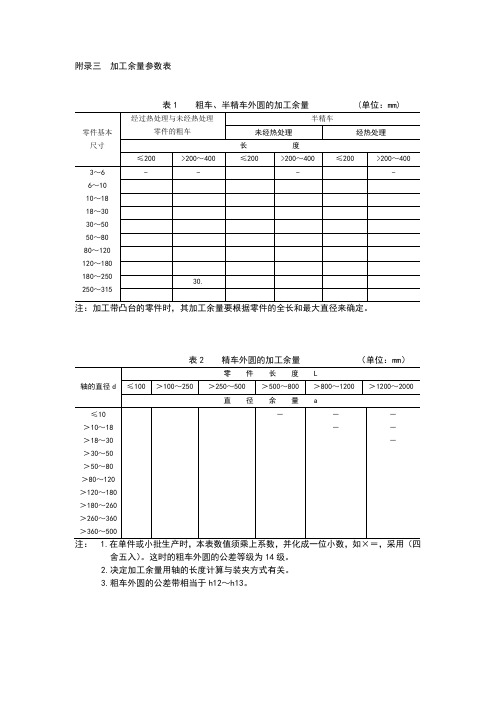
附录三加工余量参数表表1 粗车、半精车外圆的加工余量 (单位:mm)注: 1.在单件或小批生产时,本表数值须乘上系数,并化成一位小数,如×=,采用(四舍五入)。
这时的粗车外圆的公差等级为14级。
2.决定加工余量用轴的长度计算与装夹方式有关。
3.粗车外圆的公差带相当于h12~h13。
表3 磨削外圆的加工余量 (单位:mm)舍五入)。
2.决定加工余量用轴的长度计算与装夹方式有关。
3.磨前加工公差相当于h11。
注:1.加工有台阶的轴时,每台阶的加工余量应根据该台阶的d及零件的全长分别选用。
2.表中的公差系指尺寸L的公差。
表5 磨端面的加工余量 (单位:mm)注:1.加工有台阶的轴时,每台阶的加工余量应根据该台阶的d及零件的全长分别选用。
2.表中的公差系指尺寸L的公差。
2.在铸铁上加工直径为30到32mm的孔时,仅用直径为28与30mm的钻头钻一次。
3.用磨削作为孔的最后加工方法时,精镗以后的直径根据表1-23查得。
4.用金刚石细镗作为孔的最后加工方法时,精镗以后的直径根据表1-24查得。
5.如仅用一次铰孔,则铰孔的加工余量为本表中粗铰与精铰的加工余量总和。
2.在铸铁上加工直径为30、32mm的孔时,仅用直径为28、30mm的钻头钻一次。
3.用磨削作为孔的最后加工方法时,精镗以后的直径根据表1-23查得。
4.用金刚石细镗作为孔的最后加工方法时,精镗以后的直径根据表1-24查得。
5.如仅用一次铰孔,则铰孔的加工余量为本表中粗铰与精铰的加工余量总和。
注:1.当加工在热处理极易变形的、薄的轴套及其他零件时,应将表中的加工余量数值乘以。
2.如被加工孔在以后必须作为基准孔时,其公差应按7级公差来制定。
3.在单件、小批生产时,本表的数值应乘以,并化成一位小数。
例如×=,采用(四舍五入)。
表9 平面加工余量 (单位:mm)注:1.如几个零件同时加工时,长度及宽度为装置在一起的各零件长度或宽度及各零件间的间隙之总和。
加工余量查询
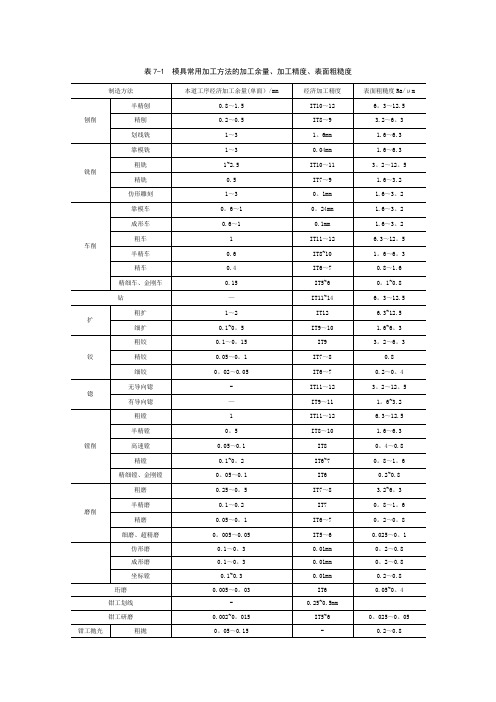
表7-1 模具常用加工方法的加工余量、加工精度、表面粗糙度细抛、镜面抛0。
005~0.01 —0.001~0.1 电火花成形加工—0.05~0。
1mm 1.25~2.5电火花线切割—0。
005~0.01mm 1.25~2.5电解成形加工—±0。
05~0。
2mm 0。
8~3.2 电解抛光0.1~0.15 —0.025~0.8电解磨削0。
1~0。
15 IT6~7 0.025~0.8照相腐蚀0.1~0.4 - 0。
1~0.8超声抛光0.02~0。
1 —0.01~0.1 磨料流动抛光0.02~0。
1 —0.01~0.1 冷挤压—IT7~8 0.08~0。
32注:经济加工余量是指本道工序的比较合理、经济的加工余量。
本道工序加工余量要视加工基本尺寸、工件材料、热处理状况、前道工序的加工结果等具体情况而定。
1。
加工总余量的确定(1)加工总余量和工序余量加工总余量(毛坯余量)—毛坯尺寸与零件图设计尺寸之差。
工序余量—相邻两工序的工序尺寸之差。
某个表面加工余量Z∑为该表面各加工工序的工序余量Zi之和,即式中n—该表面的加工工序数。
(2)影响加工余量的因素1)加工表面上的表面粗糙度和表面缺陷层深度。
2)加工前或上工序的尺寸公差。
3)加工前或上工序各表面相互位置的空间偏差。
4)本工序加工时的装夹误差.(3)查表法确定机械加工余量,总余量和半精加工、精加工工序余量可参考有关标准或工艺手册查得,并应结合实际情况加以修正。
粗加工工序余量减去半精加工和精加工工序余量而得到。
2. 工序尺寸及公差计算对于各种工序的定位基准与设计基准重合时的表面的多次加工(如外圆和内孔的加工),工序尺寸可由后续加工的工序尺寸加工上(对被包容面)或减去(对包容面)公称工序余量而求得;工序尺寸公差按所用加工方法的经济精度选定。
图4—2 表示外圆加工时加工余量、工序尺寸及其公差的分布,图中Z1、Z2、Z3为粗加工、半精加工、精加工的公称余量;To为毛坯公差.T1 、T2、T3为粗加工、半精加工、精加工的工序尺寸公差。
加工余量表
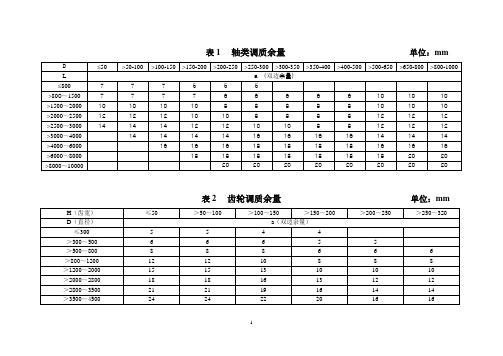
表1轴类调质余量单位:mm
表2齿轮调质余量单位:mm
表3齿圈调质余量单位:mm
表4轴类热处理后外圆磨前半精车(磨削余量)(调用)单位:mm
(2)对于淬火的零件,淬火前半精加工余量应为表中数值乘以1.25;
(3)磨前粗糙度不大于Ra6.3;
表5 渗碳、淬火齿面内外圆(非渗表面涂防渗剂)加工余量(mm)表(试用)
表6渗碳,淬火前齿轮半精车:内孔及端面磨削余量与公差(mm)(一分厂试用)
表7渗碳淬火后精车齿轮:内孔及端面磨削余量与公差(mm)(一分厂试用)
表8 渗碳、淬火齿轮粗滚齿公法线余量(mm) (一分厂试用)
表9渗碳、淬火齿轮粗滚齿公法线余量(mm) (三分厂试用)
表10渗碳、淬火齿轮粗滚齿公法线余量(mm) (四分厂试用)
表11软齿面及中硬齿面粗滚齿余量单位:mm
表12中硬齿面Mn>12热处理(调质)前粗滚齿及齿外圆余量(试用)单位:mm
表13渗碳淬火弧齿锥齿轮磨前铣齿:齿厚留磨余量与公差(mm)(三分厂试用)
表14分箱面焊接箱体粗加工后人工时效余量(试用)单位:mm
表15 分箱面焊接箱体粗加工后振动时效余量(试用)单位:mm
表16铸铁箱体(平行轴)粗加工后人工时效余量单位:mm。
机械加工工序间余量汇总

4、钢板剪切切断耗量
板厚0.5-4.5时,耗量1
板厚4.5-12时,耗量2
板厚12-25时,耗量3
5、钢板气割切断耗量
板厚>25,耗量7
6、条种棒料剪断剪耗量
如上面图3,实心棒材剪断剪耗量如表5
表5
坯料直径
≤20
>20-35
>35-50
>50-60
剪耗量
5-6
6-8
8-10
经热处理后零件的加工余量,除本标准已注明的外,应考虑热处理变形数值,如有特殊要求应在工艺卡片上注明,并相应提出中间工序要求
2、加工余量选择原则
(1)采用最小的加工余量,以求缩短加工时间,并降低零件的制造费用
(2)应有充分的加工余量,加工余量应能保证得到图纸上所规定的表面粗糙度及精度
(3)决定加工余量时应考虑到零件热处理时引起的变形,否则可能产生废品
表12 mm
工件直径
>100-300
300-500
直径留量a
1.0
1.2
允许偏差
0
0.25
0
-0.3
说明:本表摘自《机械加工余量实用手册》表[5-17]
8、轴的研磨余量
表13 mm
直径
直径余量
直径
直径余量
-----10
0.005-0.008
>50-80
0.008-0.012
>10-18
0.006-0.008
0.30
>80-120
1.6
2.5
0.35
>120-180
1.6
1.7
2.0
2.2
2.6
0.40
>180-260
- 1、下载文档前请自行甄别文档内容的完整性,平台不提供额外的编辑、内容补充、找答案等附加服务。
- 2、"仅部分预览"的文档,不可在线预览部分如存在完整性等问题,可反馈申请退款(可完整预览的文档不适用该条件!)。
- 3、如文档侵犯您的权益,请联系客服反馈,我们会尽快为您处理(人工客服工作时间:9:00-18:30)。
.
表7-1 模具常用加工方法的加工余量、加工精度、表面粗糙度
Ram12.56.36.36.312.53.23.23.23.212.56.31.60.812.512.56.36.30.80.412.53.212.56.30.81.60.86.31.60.80.10.80.80.80.40.050.8~.
.
细抛、镜面抛 0.005~0.01
— 0.001~0.1
1.25~0.1mm ~
2.5 0.05电火花成形加工—
1.25~0.005电火花线切割 0.01mm ~—
2.5
0.80.2mm
电解成形加工~—3.2 ~±0.050.025—~电解抛光 0.8 ~0.10.15
0.025~7 0.15 0.1~IT6~电解磨削 0.8
0.1~0.1 照相腐蚀0.4 —~0.8
0.01—0.1 0.02~~超声抛光 0.1
0.01 磨料流动抛光—~~0.020.1
0.1
0.08~IT78
冷挤压~—0.32
注:经济加工余量是指本道工序的比较合理、经济的加工余量。
本道工序加工余量要视加工基本尺寸、工件材料、热处理状况、前道工序的加工结果等具体情况而定。
.
.
. .
. .
. .
. .
. .
. .
. .
. .
.
.
加工总余量的确定1.
)加工总余量和工序余量(1
加工总余量(毛坯余量)—毛坯尺寸与零件图设计尺寸之差。
工序余量—相邻两工序的工序尺寸之差。
Zi之和,即Z∑为该表面各加工工序的工序余量某个表面加工余量
—该表面的加工工序数。
式中n )影响加工余量的因素(2
)加工表面上的表面粗糙度和表面缺陷层深度。
1
)加工前或上工序的尺寸公差。
2
3)加工前或上工序各表面相互位置的空间偏差。
4)本工序加工时的装夹误差。
)查表法确定机械加工余量,总余量和半精加工、精加工工序余量可3 (
粗加工工序余量减并应结合实际情况加以修正。
参考有关标准或工艺手册查得,去半精加工和精加工工序余量而得到。
2. 工序尺寸及公差计算对于各种工序的定位基准与设计基准重合时的表面的多次加工(如外圆
和内孔的加工),工序尺寸可由后续加工的工序尺寸加工上(对被包容面)或减
工序尺寸公差按所用加工方法的经济精度公称工序余量而求得;去(对包容面)选定。
、Z14-2 表示外圆加工时加工余量、工序尺寸及其公差的分布,图中图T3、、T2为粗加工、半精加工、精加工的公称余量;To为毛坯公差。
T1 Z2、Z3当各工序的公称余量和公差确定精加工的工序尺寸公差。
为粗加工、半精加工、后,卡按下面顺序计算每一工序的工序尺寸;
由零件图规定。
终加工(精加工)工序尺寸A3,公差T3
,公差为T2. 半精加工的工序尺寸A2=A3+ Z3
T1A1= A2+ Z2,公差为。
粗加工的工序尺寸。
公差为To。
毛坯尺寸Ao= A1+Z2工序尺寸的公差一般应按“入体原则”标注,而在毛坯的基本尺寸上一
般都注以双向偏差。
当基准不重合时,或零件在加工过程中需要多次转换工序基准,或工序
则需通过有关工序的工序尺寸及其公差,尺寸尚需在继续加工的表面上标注时,尺寸链的分析,计算得到。
机床及工艺装备的选择 3.
机床的选择 1)( 1)机床的加工尺寸范围应与工件的外廓尺寸相适应。
2) 机床的工作精度应与工序要求的精度想适应。
)机床的生产率应与工件的生产类型相适应。
3精度要如果工件尺寸太大, 4)机床的选择应考虑工厂的现有设备条件。
求过高,没有相应设备可供选择时,就需改装设备或设计专用机床。
(2)工艺装备的选择
)夹具的选择,在单件小批生产中,应尽量选用通用夹具或组合夹具, 1.
.
在大批大量生产中,应根据工序要求设计专用高效夹具。
)刀具的选择,主要取决于工序所采用的加工方法,加工表面的尺寸, 2
一般应尽量选生产率及经济性等,工件材料,所要求的加工精度和表面粗糙度、用标准刀具。
在单件小批生产主要根据生产类型和要求检验的精度。
)量具的选择, 3应采用各种极限量规或高生在大批大量生产中,中,应尽量采用通用量具量仪,产率的检查量仪。
4. 时间定额及缩减单件时间的措施)时间定额及其组成,时间定额是在一定的生产条件下,规定生产一(1
表示。
根据时间定额可以安排作业件产品或完成一道工序所消耗的时间,用td 计划。
进行成本核算。
确定设备设备数量和人员编制,规划生产面积。
因此,时时间定额主要利用经过实践而积累的统计间定额是工艺规程中的重要组成部分。
资料及进行部分计算来确定。
时间定额由以下部分组成:
直接改变生产对象的形状、尺寸、相对位置、表tj 1)基本时间定额
基本时间定额通常可用计算的方法面状态或材料性能等工艺过程所消耗的时间。
求出,具体计算公式详见各加工方法章节。
为实现工艺过程所必须进行的各种辅助动作所消) 2辅助时间定额tf
也可以按基本时间的百分数来辅助时间定额可根据统计资料来确定,耗的时间。
估算。
基本时间定额与辅助时间定额的总和称为作业时间定额。
为使加工正常进行,工人照管工作地(如 3)布置工作地时间定额tb
更换刀具、润滑机床、清理切屑、收拾工具等)所消耗的时间。
布置工作地时间定额一般按作业时间的百分数计算。
工人在工作班内为恢复体力和满足生休息与生理需要时间定额tx 4)理上的需要所消耗的时间。
休息与生理需要时间一般也按作业时间的百分数估算。
的产品或零、部N 工人为生产一批数量为 5)准备与终结时间定额tz
件,进行准备和结束工作所消耗的时间。
成批生产时的时间定额:
td=tj+tf+tb+tx+ tz:/N
大量生产时的时间定额:
td=tj+tf+tb+tx
)缩减单件时间的措施( 2
的措施,提高切削用量,减少加工余量,缩短刀具tj 1 )缩减基本时间的工作行程,采用多刀多刃和多轴机床加工,或采用其他新工艺,新技术。
的措施,尽量使辅助动作实现机械或自动化,如采)缩减辅助时间tf 2使辅助时间与基本时间部分地域或全部地提高机床的自动化程度;用先进夹具,采用主动测量或数字显示自动测量装重叠起来,如采用多位夹具或多位工作台,置。
.
.
的措施,采用耐用度较高的刀具或砂轮,采tb 3)缩减布置工作地时间
用各种快换刀夹、刀具微调装置,专用对刀样板和样件以及自动换刀装置。
使夹具和缩减准备与终结时间的措施,采用成组工艺生产组织形式,) 4 刀具的调整通用化,采用准备终结时间较短的先进设备及工艺装备。
.。