压铸模具制作说明
压铸模具设计毕业设计说明书

目录第一章压铸合金与压铸件的设计......................................1.1 压铸合金.....................................................1.1.1 工件的材料性能.........................................2.2 压铸机的型号及主要参数.......................................2.3 压铸机的选用................................................2.3.1 压铸机的基本参数选择...................................2.3.2 计算压铸机的锁模力....................................2.3.3 压室容量的校核........................................2.4 压铸工艺....................................................2.4.1 压射压力的选择.........................................第四章成型零件与模架设计...........................................4.1成型零件的结构设计...........................................4.2 成型零件的成型尺寸的计算.....................................4.3 模架的设计...................................................4.4 加热与冷却系统设计(该模具不采用加热冷却系统,略)...........第五章抽芯结构设计.................................................参考文献............................................................设计了立式冷室压铸机,压铸技术有了一个很大的进步,使得铝、镁、铜等合金均可采用压铸生产。
模具毕业设计34电机端盖压铸模设计说明书

一、零件图如图1-1所示制件为电机端盖,材料为锌合金,属大批量生产。
图1-1一、该压铸件的材料分析和工艺性分析1. 材料分析该产品的成型材料是锌合金,该材料密度大,铸造性能好,可压铸复杂的零件,压铸时不粘模,压铸件表面易镀Cr、Ni等金属,机械切削性能好,但易老化,抗腐蚀性能不高。
2. 工艺性分析1)锌合金压铸,其锌不容易就粘在模具表面上。
2)该压铸件壁厚比较均匀,各个孔小且浅,工艺性好。
3)为了方便加工与成型及脱模,型腔、型芯均采用组合式结构。
4)该压铸件是一般精度等级。
为降低设计难度和设计周期,应采一模一腔,且需要对压铸件去除浇口废料。
二、拟定的成型工艺1.成型方法该压铸件采用冲头下压式全立式压铸机压铸。
2.各工艺参数1)经查教材(压铸成型工艺与模具设计)第32页表3.2可知压射比压为30Mpa2)经查教材第33页表3.4可知压射冲头空行程压射速度为0.3~0.5m/s 3)经查教材第34页表3.5可知充填速度为15 m/s 4)经查教材第36页表3.7可知持压时间3~4s5)经查教材第36页表3.8可知留模时间推荐值为7~12s 6)经查教材第37页表3.9可知浇注温度为410~540C 。
7)经查教材第38页表3.10可知模具预热温度130~180C 。
和工作温度180~200C 。
3. 确定型腔数目1)为降低设计难度和设计周期,应采单型腔,且需要对压铸件去除浇口废料。
2)计算压铸的体积和重量通过三维制图PRO/E 软件测量得:单件压铸件投影面积S=14257㎜2;体积V=153645㎜3查有关资料可知Al 的密度为6.8g/cm 3则压铸件重量m=1044.8g三、初选压铸机1.压铸机的锁模力模具型腔胀型力中心与压铸机压力中心重合时压铸机锁模力 S F K ≥Z N (F +F )式中 S F —压铸机锁模力,N ;Z F —作用于模具型腔且垂直与分型面方向的胀型力,N ; N F —作用于滑快楔紧块面上的法向压力,N ;K —安全系数(一般取K=1~1.3)型腔胀型力Z F =P (123A +A +A )式中 P —最终的压射比压,Pa ;1A —铸件在分型面上的投影面积,㎡;2A —浇注系统在分型面上的投影面积与压铸件投影面积不重叠部分,㎡;3A —溢流槽在分型面上的投影面积,㎡;压铸机所容许的压射比压20.785n Fp D=式中 n p —压铸机所容许的压射比压,Pa ; F —压射力,N ; D —压室直径,m 。
铝合金箱体压铸模具设计说明书

毕业设计(论文)任务书 2015 届机械工程及自动化专业题目:铝合金箱体压铸模具的设计子题:学生姓名:班级学号:指导教师:职称:所在系(教研室):机电与信息工程系下达日期:2014年7月4日完成日期:2015年5月8日摘要压铸模具是铸造液态模锻的一种方法,一种在专用的压铸模锻机上完成的工艺。
它的基本工艺过程是:金属液先低速或高速铸造充型进模具的型腔内,模具有活动的型腔面,它随着金属液的冷却过程加压锻造,既消除毛坯的缩孔缩松缺陷,也使毛坯的内部组织达到锻态的破碎晶粒。
毛坯的综合机械性能得到显著的提高。
本文运用大学所学的知识,了解压铸模具的工作原理,在此基础上,设计一款铝合金箱体压铸模具。
通过查找相关资料,了解铝合金箱体压铸模具的内部结构和工作原理,构建了铝合金箱体压铸模具组成结构的总的指导思想,从而得出了该铝合金箱体压铸模具的优点是高效,经济,并且运行效果好,运行平稳的结论。
关键词:铝合金箱体压铸模具;型腔;效率;模具AbstractThe environment of global economic development, China industries affected by other countries advanced technology at the same time, foreign enterprises and brand spread to more and more Chinese has become an opportunity. Cap pressing machine in industry through a variety of ways have been working with the relevant technology, and constantly improve their own strength and core competitiveness, and narrow the gap with developed countries.In the new market demand, update the sleeve pressing machine is a pressing matter of the moment. The production of pipe pressing machine equipment manufacturing enterprises to fully tap the potential of the market, vigorously develop the sleeves of large low cost pressing special machinery and equipment, plays a positive role in the evolution of automatic assembly, the assembly of mechanical equipment. There is a large pipe equipment on equipment safety index has strict requirements of production. In the production equipment of enterprises, give full consideration to the possible problems in the operation of the equipment, so as to reduce the noise pollution caused by vibration or improper operation of equipment phenomenon and manufacturing of domestic pipe pressing equipment with global appeal, economic, security and stability of the theme consistent. Increase and production pipe pressing equipment of new energy saving.Key word:pneumatic manipulator;cylinder;pneumatic loop;Fout degrees of freedom.目录摘要 (1)Abstract (2)第一章绪论 (3)1.1 模具介绍 (4)1.2 模具在加工工业中的地位................... 错误!未定义书签。
压铸模具设计与制造
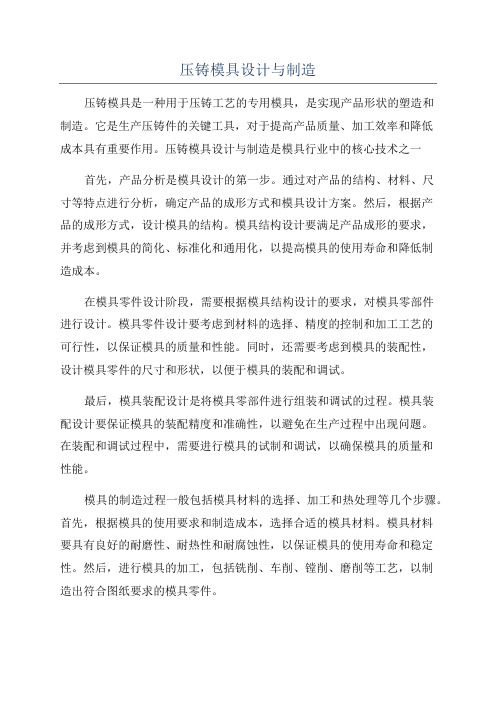
压铸模具设计与制造压铸模具是一种用于压铸工艺的专用模具,是实现产品形状的塑造和制造。
它是生产压铸件的关键工具,对于提高产品质量、加工效率和降低成本具有重要作用。
压铸模具设计与制造是模具行业中的核心技术之一首先,产品分析是模具设计的第一步。
通过对产品的结构、材料、尺寸等特点进行分析,确定产品的成形方式和模具设计方案。
然后,根据产品的成形方式,设计模具的结构。
模具结构设计要满足产品成形的要求,并考虑到模具的简化、标准化和通用化,以提高模具的使用寿命和降低制造成本。
在模具零件设计阶段,需要根据模具结构设计的要求,对模具零部件进行设计。
模具零件设计要考虑到材料的选择、精度的控制和加工工艺的可行性,以保证模具的质量和性能。
同时,还需要考虑到模具的装配性,设计模具零件的尺寸和形状,以便于模具的装配和调试。
最后,模具装配设计是将模具零部件进行组装和调试的过程。
模具装配设计要保证模具的装配精度和准确性,以避免在生产过程中出现问题。
在装配和调试过程中,需要进行模具的试制和调试,以确保模具的质量和性能。
模具的制造过程一般包括模具材料的选择、加工和热处理等几个步骤。
首先,根据模具的使用要求和制造成本,选择合适的模具材料。
模具材料要具有良好的耐磨性、耐热性和耐腐蚀性,以保证模具的使用寿命和稳定性。
然后,进行模具的加工,包括铣削、车削、镗削、磨削等工艺,以制造出符合图纸要求的模具零件。
最后,进行模具的热处理,以提高模具的硬度和综合性能。
热处理过程一般包括淬火、回火、脱碳、氮化等工艺,根据模具的材料和使用要求进行选择。
热处理可以提高模具零件的硬度和耐磨性,增加模具的使用寿命。
总结起来,压铸模具设计与制造是一项复杂而关键的工艺,需要设计师和制造者具有扎实的基础知识和丰富的经验。
只有通过合理的设计和精确的制造,才能获得高质量的模具,为产品的成形提供有力的保障。
压铸模具设计和制造手册
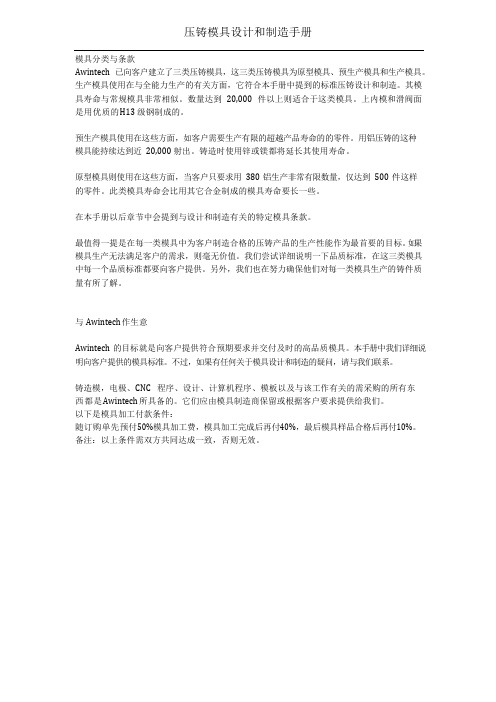
模具分类与条款Awintech 已向客户建立了三类压铸模具,这三类压铸模具为原型模具、预生产模具和生产模具。
生产模具使用在与全能力生产的有关方面,它符合本手册中提到的标准压铸设计和制造。
其模具寿命与常规模具非常相似。
数量达到20,000 件以上则适合于这类模具。
上内模和滑阀面是用优质的H13 级钢制成的。
预生产模具使用在这些方面,如客户需要生产有限的超越产品寿命的的零件。
用铝压铸的这种模具能持续达到近20,000 射出。
铸造时使用锌或镁都将延长其使用寿命。
原型模具则使用在这些方面,当客户只要求用380 铝生产非常有限数量,仅达到500 件这样的零件。
此类模具寿命会比用其它合金制成的模具寿命要长一些。
在本手册以后章节中会提到与设计和制造有关的特定模具条款。
最值得一提是在每一类模具中为客户制造合格的压铸产品的生产性能作为最首要的目标。
如果模具生产无法满足客户的需求,则毫无价值。
我们尝试详细说明一下品质标准,在这三类模具中每一个品质标准都要向客户提供。
另外,我们也在努力确保他们对每一类模具生产的铸件质量有所了解。
与Awintech 作生意Awintech 的目标就是向客户提供符合预期要求并交付及时的高品质模具。
本手册中我们详细说明向客户提供的模具标准。
不过,如果有任何关于模具设计和制造的疑问,请与我们联系。
铸造模,电极、CNC 程序、设计、计算机程序、模板以及与该工作有关的需采购的所有东西都是Awintech 所具备的。
它们应由模具制造商保留或根据客户要求提供给我们。
以下是模具加工付款条件:随订购单先预付50%模具加工费,模具加工完成后再付40%,最后模具样品合格后再付10%。
备注:以上条件需双方共同达成一致,否则无效。
目录1.0.0 模具分类与条款1.1.0 与Awintech 作生意1.2.0 总体步骤与规格1.3.0 胚模规格1.4.0 料表1.5.0 上内模1.6.0 公模滑块零件1.7.0 拉圾钉1.8.0 顶出系统1.9.0 加热与冷却2.0.0 胚模零件2.1.0 液压汽缸筒和接近开关2.2.0 合金工具钢的热处理2.3.0 合金工具钢表面处理2.4.0 焊接2.5.0 金属进料与真空系统2.6.0 文档资料与证明2.7.0 压铸冲模设计和制造总指南和专用指南设计检测表模具加工检测表Awintech 模具改善表Awintech 模具检测规划报告拉极钉概要热电偶安装设计压铸机台板布局真空安装规格1.2.0 总体步骤与规格1、Awintech 会向模具供应商提供最新的客户产品印刷物或资料库用以询价,模具设计和制造。
压铸模具配模指导书

压铸模具配模指导书摘要:一、压铸模具简介1.压铸模具的作用2.压铸模具的分类3.压铸模具的组成结构二、配模前的准备工作1.了解产品结构及要求2.分析产品图纸3.确认压铸工艺参数三、模具选材及设计要求1.模具材料的选择2.模具结构设计原则3.模具零件的公差与配合四、模具制造与试模1.模具制造流程2.模具试模及调试3.试模结果分析与优化五、模具使用与维护1.模具安装与使用2.模具保养与维护3.模具故障分析与处理正文:压铸模具配模指导书一、压铸模具简介压铸模具是压铸生产中不可或缺的设备,主要用于生产各种压铸件。
它将金属熔融后,通过压力将金属液体倒入模具型腔中,并在短时间内冷却成型的过程。
压铸模具的质量和性能直接影响到压铸件的质量和生产效率。
1.压铸模具的作用压铸模具主要用于实现金属液态成形,生产各种压铸件。
它可以提高生产效率,降低生产成本,提高产品质量。
2.压铸模具的分类根据产品类型和生产工艺,压铸模具可分为铝合金压铸模具、锌合金压铸模具、铜合金压铸模具等。
3.压铸模具的组成结构压铸模具主要由模具主体、模具芯、模具腔、冷却系统、喷涂系统等组成。
二、配模前的准备工作在开始模具设计前,需要对产品结构和要求进行全面了解,以便为模具设计提供准确的依据。
1.了解产品结构及要求分析产品图纸,了解产品的形状、尺寸、重量、表面质量等要求。
2.分析产品图纸通过产品图纸,了解产品的结构特点,找出关键尺寸,以便在模具设计中充分考虑。
3.确认压铸工艺参数根据产品要求,确认压铸合金、压铸压力、压铸速度等工艺参数。
三、模具选材及设计要求模具材料的选择和模具设计直接影响到模具的使用寿命和压铸件的质量。
1.模具材料的选择根据压铸合金的类型和性能要求,选择合适的模具材料,如合金钢、硬质合金等。
2.模具结构设计原则模具设计应满足生产工艺要求,结构简单、易于制造、维修方便。
3.模具零件的公差与配合合理设定模具零件的公差和配合,确保模具在装配和使用过程中具有良好的性能。
UG压铸模具设计说明书

UG压铸模具设计说明书文档编号:UG-001日期:[日期]项目名称:UG压铸模具设计说明书1.引言本文档旨在提供UG压铸模具设计的详细说明和指导。
该设计说明书包含以下主要内容:模具设计目的、制造要求、结构设计、材料选择、工艺流程、质量控制、装配要求和测试要求。
2.模具设计目的本次UG压铸模具设计旨在制作适用于[产品名称]的模具,以满足客户的要求和设计规范。
该模具将用于生产高质量、精准的[产品名称]。
3.制造要求3.1 尺寸精度:模具零件的尺寸精确到[精度要求]。
3.2 表面粗糙度:模具零件的表面粗糙度符合[表面要求]。
3.3 使用寿命:模具的设计寿命为[使用寿命]。
4.结构设计4.1 核心与腔体设计:模具将采用两种零件,包括核心和腔体。
核心和腔体的材料为[材料类型],尺寸为[核心和腔体尺寸]。
4.2 引导系统设计:模具将配备合适的引导系统,以确保模具的稳定性和精度。
4.3 固定和定位设计:模具将配备适当的固定和定位系统,以确保模具在使用过程中的稳定性和精度。
5.材料选择5.1 核心和腔体材料:核心和腔体的材料将选用[材料名称],以满足产品的特定要求。
5.2 模具基座材料:模具基座将选用[材料名称],以提供足够的强度和稳定性。
6.工艺流程6.1 制造过程:该模具的制造过程将包括以下步骤:材料准备、加工零件、热处理、表面处理、装配和调试。
6.2 加工工艺:加工工艺将包括以下步骤:铣削、车削、线切割、钻孔、磨削等。
7.质量控制7.1 检验标准:模具将根据[检验标准]进行质量控制。
7.2 检验方法:模具将通过[检验方法]进行质量检验。
7.3 产品检验:通过对[产品名称]进行抽样检验,确保产品质量达到指定要求。
8.装配要求8.1 模具装配:模具将按照装配图纸进行装配。
8.2 装配检查:装配完成后,将进行装配检查,确保模具的正确安装和功能正常。
9.测试要求9.1 试模测试:模具将进行试模测试,以确保模具的性能和质量满足要求。
压力铸造模具设计说明

压力铸造模具设计说明一、压铸简介压力铸造简称压铸,是一种将熔融合金液倒入压室内,以高速充填钢制模具的型腔,并使合金液在压力下凝固而形成铸件的铸造方法。
压铸区别于其它铸造方法的主要特点是高压和高速。
①金属液是在压力下填充型腔的,并在更高的压力下结晶凝固,常见的压力为15—100MPa。
②金属液以高速充填型腔,通常在10—50米/秒,有的还可超过80米/秒,(通过内浇口导入型腔的线速度—内浇口速度),因此金属液的充型时间极短,约0.01—0.2秒(须视铸件的大小而不同)内即可填满型腔。
压铸机、压铸合金与压铸模具是压铸生产的三大要素,缺一不可。
所谓压铸工艺就是将这三大要素有机地加以综合运用,使能稳定地有节奏地和高效地生产出外观、内在质量好的、尺寸符合图样或协议规定要求的合格铸件,甚至优质铸件。
1、压铸机(1)压铸机的分类压铸机按压室的受热条件可分为热压室与冷压室两大类。
而按压室和模具安放位置的不同,冷室压铸机又可分为立式、卧式和全立式三种形式的压铸机。
热室压铸机立式冷室卧室全立式(2)压铸机的主要参数a合型力(锁模力)(千牛)————————KN b压射力(千牛)—————————————KN c动、定型板间的最大开距——————————mm d动、定型板间的最小开距——————————mm e动型板的行程———————————————mm f大杠内间距(水平×垂直)—————————mm g大杠直径—————————————————mm h顶出力——————————————————KN i顶出行程—————————————————mm j压射位置(中心、偏心)——————————mm k一次金属浇入量(Zn、Al、Cu)———————Kg l压室内径(Ф)——————————————mm m空循环周期————————————————s n铸件在分型面上的各种比压条件下的投影面积注:还应有动型板、定型板的安装尺寸图等。
UG压铸模具设计说明书
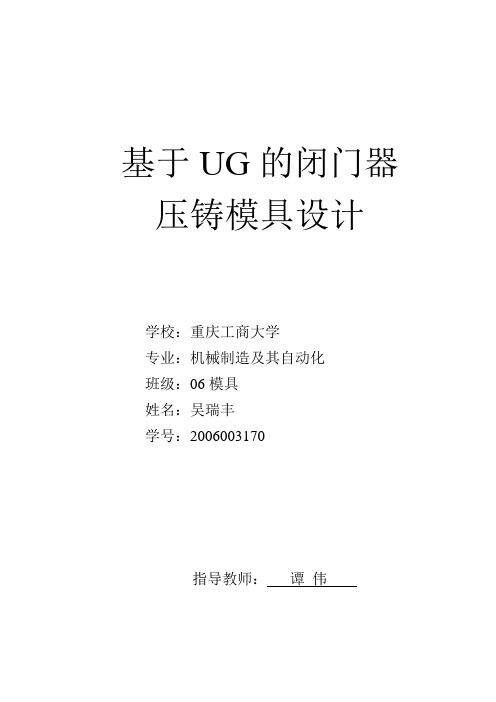
基于UG的闭门器压铸模具设计学校:重庆工商大学专业:机械制造及其自动化班级:06模具姓名:***学号:**********指导教师:**目录1 UG压铸模具设计基础 (1)1.1 压铸模具设计基础 (1)1.1.1 压铸模具结构及其组成 (1)1.1.2 压铸模具设计原则 (2)1.1.3 压铸机的选用 (3)第2章UG压铸件建模 (5)2.1压铸件建模 (5)第3章UG压铸模具分型面设计与零部件的创建 (6)3.1 压铸模具及其零部件的设计过程 (6)3.1.1 压铸模具设计过程 (6)3.1.2 压铸模具零部件及其设计过程 (6)3.1.3 压铸模具零件功能分析 (9)3.1.4 压铸模具零件分类................................................................ 错误!未定义书签。
3.2 压铸件脱模阻力计算与动、定模的划分......................................... 错误!未定义书签。
3.2.1 压铸件的脱模工作过程........................................................ 错误!未定义书签。
3.2.2 压铸件冷却收缩所引起的脱模阻力.................................... 错误!未定义书签。
3.2.3 抽芯机构所引起的压铸件动、定模脱模阻力.................... 错误!未定义书签。
3.2.4 压铸件形状特征在模具动、定模的分布............................ 错误!未定义书签。
3.3 压铸模具成型零件设计..................................................................... 错误!未定义书签。
3.3.1 压铸模具成型零件的结构.................................................... 错误!未定义书签。
铝合金箱体压铸模具设计说明书

毕业设计(论文)任务书 2015 届机械工程及自动化专业题目:铝合金箱体压铸模具的设计子题:学生姓名:班级学号:指导教师:职称:所在系(教研室):机电与信息工程系下达日期:2014年7月4日完成日期:2015年5月8日摘要压铸模具是铸造液态模锻的一种方法,一种在专用的压铸模锻机上完成的工艺。
它的基本工艺过程是:金属液先低速或高速铸造充型进模具的型腔内,模具有活动的型腔面,它随着金属液的冷却过程加压锻造,既消除毛坯的缩孔缩松缺陷,也使毛坯的内部组织达到锻态的破碎晶粒。
毛坯的综合机械性能得到显著的提高。
本文运用大学所学的知识,了解压铸模具的工作原理,在此基础上,设计一款铝合金箱体压铸模具。
通过查找相关资料,了解铝合金箱体压铸模具的内部结构和工作原理,构建了铝合金箱体压铸模具组成结构的总的指导思想,从而得出了该铝合金箱体压铸模具的优点是高效,经济,并且运行效果好,运行平稳的结论。
关键词:铝合金箱体压铸模具;型腔;效率;模具AbstractThe environment of global economic development, China industries affected by other countries advanced technology at the same time, foreign enterprises and brand spread to more and more Chinese has become an opportunity. Cap pressing machine in industry through a variety of ways have been working with the relevant technology, and constantly improve their own strength and core competitiveness, and narrow the gap with developed countries.In the new market demand, update the sleeve pressing machine is a pressing matter of the moment. The production of pipe pressing machine equipment manufacturing enterprises to fully tap the potential of the market, vigorously develop the sleeves of large low cost pressing special machinery and equipment, plays a positive role in the evolution of automatic assembly, the assembly of mechanical equipment. There is a large pipe equipment on equipment safety index has strict requirements of production. In the production equipment of enterprises, give full consideration to the possible problems in the operation of the equipment, so as to reduce the noise pollution caused by vibration or improper operation of equipment phenomenon and manufacturing of domestic pipe pressing equipment with global appeal, economic, security and stability of the theme consistent. Increase and production pipe pressing equipment of new energy saving.Key word:pneumatic manipulator;cylinder;pneumatic loop;Fout degrees of freedom.目录摘要 (1)Abstract (2)第一章绪论 (3)1.1 模具介绍 (4)1.2 模具在加工工业中的地位................... 错误!未定义书签。
端盖压铸模具说明书(可编辑修改word版)
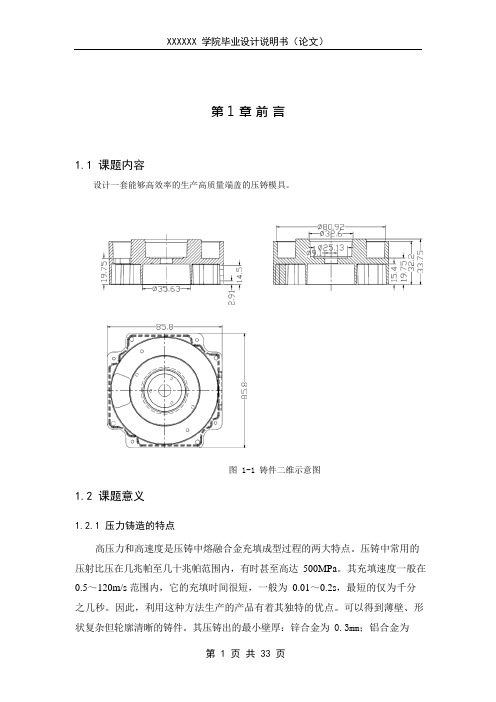
第 1 章前言1.1课题内容设计一套能够高效率的生产高质量端盖的压铸模具。
图 1-1 铸件二维示意图1.2课题意义1.2.1压力铸造的特点高压力和高速度是压铸中熔融合金充填成型过程的两大特点。
压铸中常用的压射比压在几兆帕至几十兆帕范围内,有时甚至高达500MPa。
其充填速度一般在0.5~120m/s 范围内,它的充填时间很短,一般为0.01~0.2s,最短的仅为千分之几秒。
因此,利用这种方法生产的产品有着其独特的优点。
可以得到薄壁、形状复杂但轮廓清晰的铸件。
其压铸出的最小壁厚:锌合金为 0.3mm;铝合金为0.5mm。
铸出孔最小直径为 0.7mm。
铸出螺纹最小螺距 0.75mm。
对于形状复杂,难以或不能用切削加工制造的零件,即使产量小,通常也采用压铸生产,尤其当采用其他铸造方法或其他金属成型工艺难以制造时,采用压铸生产最为适宜。
铸件的尺寸精度和表面粗糙度要求很高。
铸件的尺寸精度为 IT12~IT11 面粗糙度一般为 3.2~0.8μm,最低可达0.4μm。
因此,个别压铸件可以不经过机械加工或仅是个别部位加工即可使用[1]。
压铸的主要优点是:(1)铸件的强度和表面硬度较高。
由于压铸模的激冷作用,又在压力下结晶,因此,压铸件表面层晶粒极细,组织致密,所以表面层的硬度和强度都比较高。
压铸件的抗拉强度一般比砂型铸件高25%~30%,但收缩率较低。
(2)生产率较高。
压力铸造的生产周期短,一次操作的循环时间约 5 s~3 min ,这种方法适于大批量生产。
虽然压铸生产的优势十分突出,但是,它也有一些明显的缺点:(1)压铸件表层常存在气孔。
这是由于液态合金的充型速度极快,型腔中的气体很难完全排除,常以气孔形式存留在铸件中。
因此,一般压铸件不能进行热处理,也不宜在高温条件下工作。
这是由于加热温度高时,气孔内的气体膨胀,导致压铸件表面鼓包,影响质量与外观。
同样,也不希望进行机械加工,以免铸件表面显露气孔。
(2)压铸的合金类别和牌号有所限制。
压铸模设计说明书
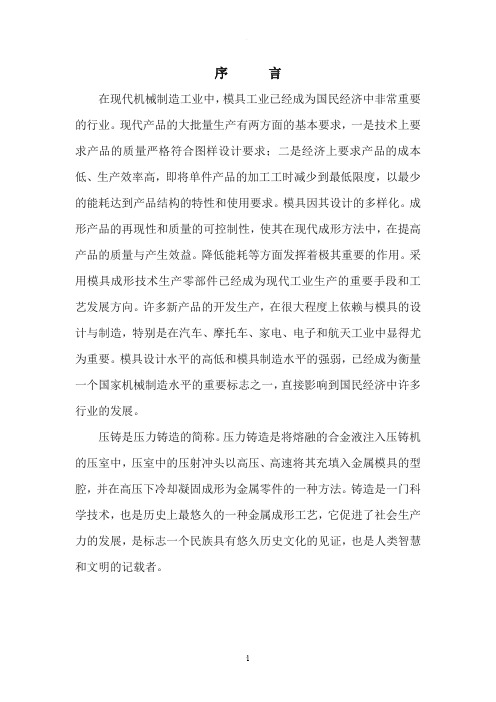
序言在现代机械制造工业中,模具工业已经成为国民经济中非常重要的行业。
现代产品的大批量生产有两方面的基本要求,一是技术上要求产品的质量严格符合图样设计要求;二是经济上要求产品的成本低、生产效率高,即将单件产品的加工工时减少到最低限度,以最少的能耗达到产品结构的特性和使用要求。
模具因其设计的多样化。
成形产品的再现性和质量的可控制性,使其在现代成形方法中,在提高产品的质量与产生效益。
降低能耗等方面发挥着极其重要的作用。
采用模具成形技术生产零部件已经成为现代工业生产的重要手段和工艺发展方向。
许多新产品的开发生产,在很大程度上依赖与模具的设计与制造,特别是在汽车、摩托车、家电、电子和航天工业中显得尤为重要。
模具设计水平的高低和模具制造水平的强弱,已经成为衡量一个国家机械制造水平的重要标志之一,直接影响到国民经济中许多行业的发展。
压铸是压力铸造的简称。
压力铸造是将熔融的合金液注入压铸机的压室中,压室中的压射冲头以高压、高速将其充填入金属模具的型腔,并在高压下冷却凝固成形为金属零件的一种方法。
铸造是一门科学技术,也是历史上最悠久的一种金属成形工艺,它促进了社会生产力的发展,是标志一个民族具有悠久历史文化的见证,也是人类智慧和文明的记载者。
第一章压铸设计的特点压力铸造的主要成形工艺特征是液态金属以高压、高速充填金属模具的型腔,并且在高压下结晶、凝固和成形,因此压铸成形过程中金属液流动的状态将会影响到压铸件的质量。
同时,针对压铸的工艺特点,压铸件的结构工艺性对压铸件质量的影响也需要引起足够的重视。
压铸机是压力铸造的基本设备,压铸的过程是通过压铸机实现的。
压铸机一般可分为热压室压铸机和冷压室压铸机两大类,本次设计使用的是冷压室压铸机。
冷压室压铸机的压室与熔化合金的坩埚是分开的,压铸时,需要从熔化炉的坩埚内盛取金属液注入压室后再进行压铸。
按照压铸模与压室的相对位置,冷压室压铸机又可分为立式、卧式和全立式三种形式。
本次设计选用的是卧式压铸机。
压铸模设计说明书

湘潭大学毕业设计说明书题目:压铸件模具设计学院:机械工程学院专业:材料成型及控制工程学号:姓名:指导教师:完成日期: 2015.3。
16目录一。
设计前准备工作 (1)1。
压铸工艺分析: (1)2.零件初步分析 (1)3.初步确定设计方案: (1)二。
压铸件工艺分析 (2)1.压铸合金工艺分析: (2)2.压铸件工艺分析: (2)3.分型面的选择: (2)三.浇注系统和排溢系统的设计 (3)1.浇注系统的设计: (3)2。
溢流排气系统的设计: (3)四。
压铸机的选择 (4)1.压铸机的种类和特点 (4)2。
选定压射比压 (5)3.确定型腔数目及布置形式 (5)4。
确定模具分型面上铸件的总投影面积 (6)5.计算锁模力: (6)五。
压铸模的结构设计 (7)1。
成型零件设计 (7)2。
结构零件设计 (10)3、各零件采用材料要求 (15)4、螺钉选用 (16)六、压铸模的整体结构 (16)1、压铸模的技术要求 (16)2、压铸模外形和安装部位的技术要求 (17)七、校核模具与压铸机的有关尺寸 (18)1、锁模力的校核 (18)2、铸件最大投影面积校核 (18)3、压室容量校核 (18)4、模具厚度的校核 (18)5、开模行程的校核 (18)八、参考文献: (19)一。
设计前准备工作1。
压铸工艺分析:压力铸造是将液态或半液态的金属,在高压作用下,以高的速度填充压铸模的型腔,并在压力作用下快速凝固而获得铸件的一种方法。
高压力和高速度是压铸时熔融合金充填成型过程的两大特点,也是压铸与其它铸造方法最根本的区别所在。
压铸件尺寸精度和表面粗糙度较好,铸件轮廓清晰,有致密的表层,比内层有更好的机械性能,内部存在气孔和缩孔缺陷。
2。
零件初步分析零件为对称圆筒型零件,截面为工字形,中心开有一小孔。
壁厚为5mm,属于薄壁零件。
型腔深度约为97。
5mm,属于深腔。
零件图如下所示:图1—1 零件图3。
初步确定设计方案:1)压铸合金此铸件的材料为YZCuZn40Pb:此材料属于铅黄铜合金,具有加工性能较好,成本较低等优点,多用于化工、造船的零件和耐磨的零件。
压铸模具制作说明
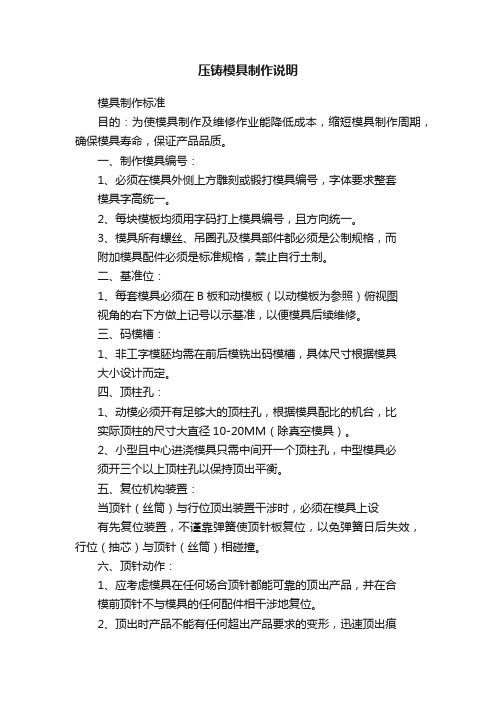
压铸模具制作说明模具制作标准目的:为使模具制作及维修作业能降低成本,缩短模具制作周期,确保模具寿命,保证产品品质。
一、制作模具编号:1、必须在模具外恻上方雕刻或锻打模具编号,字体要求整套模具字高统一。
2、每块模板均须用字码打上模具编号,且方向统一。
3、模具所有螺丝、吊圈孔及模具部件都必须是公制规格,而附加模具配件必须是标准规格,禁止自行土制。
二、基准位:1、每套模具必须在B板和动模板(以动模板为参照)俯视图视角的右下方做上记号以示基准,以便模具后续维修。
三、码模槽:1、非工字模胚均需在前后模铣出码模槽,具体尺寸根据模具大小设计而定。
四、顶柱孔:1、动模必须开有足够大的顶柱孔,根据模具配比的机台,比实际顶柱的尺寸大直径10-20MM(除真空模具)。
2、小型且中心进浇模具只需中间开一个顶柱孔,中型模具必须开三个以上顶柱孔以保持顶出平衡。
五、复位机构装置:当顶针(丝筒)与行位顶出装置干涉时,必须在模具上设有先复位装置,不谨靠弹簧使顶针板复位,以免弹簧日后失效,行位(抽芯)与顶针(丝筒)相碰撞。
六、顶针动作:1、应考虑模具在任何场合顶针都能可靠的顶出产品,并在合模前顶针不与模具的任何配件相干涉地复位。
2、顶出时产品不能有任何超出产品要求的变形,迅速顶出痕迹不影响产品表面质量。
3、顶出应平衡很顺,不可出现顶出倾斜现象及顶出有杂音的产生。
七、行位动作:1、滑块行位动作应顺滑,保证产品不得有拉变形现象,不可出现卡死动作,不均匀松动等现象。
2、大滑块滑动部位应开油槽3、在表面要求较高和壁厚较厚的铸件且有强度要求的产品,滑块上应设有冷却水路。
4、当滑块滑动行程过长时,必须在模座上增长导向,通常滑动部位做到宽度的1.5倍左右为宜,抽芯时滑块在导向槽的部分,要有滑块滑动部位的2/3在导向滑槽内。
5、斜导柱与导柱孔的配合间隙必须留有0.2MM以上,禁止非间隙配合。
6、斜导柱的角度小于滑块锲紧面2度,大滑块的锲尽紧块须伸入下模15-20MM以斜度面互锁反压。
压铸模工艺流程

压铸模工艺流程压铸模工艺流程是指将熔融金属注入金属模具中,通过高压使其冷却凝固,并最终得到制品的一种制造工艺。
下面就具体介绍一下压铸模工艺流程。
首先是准备工作。
准备工作包括确定产品的设计和模具的选择。
根据产品的形状和要求,设计师绘制出产品的3D模型图,然后由工艺师根据产品的形状和材料性质,选择模具的材料和制作方式。
第二步是制作模具。
制作模具是压铸模工艺流程中最关键的一步。
模具可以根据产品的形状分为单腔模和多腔模。
制作模具需要选用高强度材料,并经过数控机床的加工和热处理,以保证模具的精度和寿命。
第三步是准备熔融金属。
熔融金属可以是铝合金、锌合金、镁合金等。
首先将原材料按照一定的比例混合,然后将混合好的原材料放入熔炉中进行熔化。
熔融金属的温度根据具体产品的要求进行调整,通常在600-700摄氏度之间。
第四步是注入金属模具中。
熔融金属在达到合适温度后,通过喷嘴或注射系统将熔融金属注入金属模具的腔室中。
同时,通过高压将熔融金属充分填充到模腔中,以确保产品的完整性和密度。
第五步是冷却凝固。
注入模腔中的熔融金属会随着时间的推移逐渐冷却凝固。
在金属凝固的同时,模具的温度也会逐渐下降。
当金属完全凝固后,模具会被打开,产品会从模具中取出。
最后一步是处理和加工。
取出的产品通常还需要进行去毛刺、修整、清洗等处理工序,以及进行机械加工、表面处理等后续加工工序。
这些工序的目的是给产品赋予更好的表面质量和机械性能。
以上就是压铸模工艺流程的简要介绍。
压铸模工艺流程是一种高效、精确和快速的制造工艺,广泛应用于汽车、电子、航空航天等领域。
随着科技的发展,压铸模工艺也在不断创新和改进,以满足不同领域产品的需求。
压铸模具说明书 (2)

压铸模具说明书1307—YJ—799—A
ﻬ目录
1、模具概述
ﻬ2、毛坯机加工余量示意图
2.1此零件向客户提供压铸件,不做机加工
3、模穴编号示意图
3.1此零件一出一,未刻模穴号,滑块编号如下图:
4、模具镶针编号图
镶针图档请看维响中最终的档案
5、模具备件清单
序号名称规格数量材质备注
1 上模镶针S1 Ф19.5×74 1 SKD61
2 下模镶针X1Ф8×90.1 2 SKD61
3 滑块镶针H1/2 Ф8×952SKD61
4滑块镶针C1Ф7。
5×97 2SKD61
5滑块镶针C2 Ф7。
5×126 2 SKD61
6 滑块镶针C3 Ф7。
5×126 2 SKD61
7滑块A 2 H13有滑块座8滑块B 2 H13有滑块座
9 顶针C1 Ф7×951SKD61
10 顶针C2 Ф7×95 1 SKD61
6、顶针编号表
7、顶针高度表
注:高度以分型面为基准,高出为正,低下为负。
8、模具水路图8.1动模水路如下图:
注:点水1,2铜管高50
8.2定模水路图如下图
9、一模多款产品对照表
9.1此产品目前共六款,通过更换顶针X2,滑块,及滑块镶针C2/3实现,具体对照表如下:
10、装模注意事项及其他
10.1此模具在280T上旋转吊装
10.2此模具在350T上旋转吊装
ﻬ11、喷雾示意图
11。
1动定模喷雾示意图
11。
2定模喷雾示意图。
压铸件模具生产工艺流程
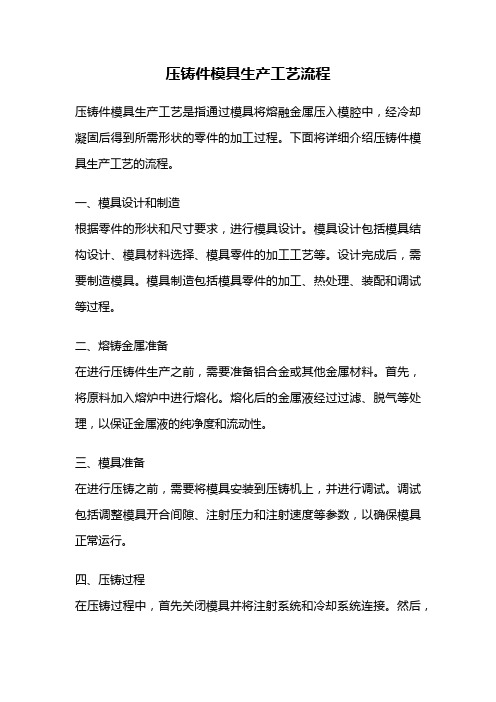
压铸件模具生产工艺流程压铸件模具生产工艺是指通过模具将熔融金属压入模腔中,经冷却凝固后得到所需形状的零件的加工过程。
下面将详细介绍压铸件模具生产工艺的流程。
一、模具设计和制造根据零件的形状和尺寸要求,进行模具设计。
模具设计包括模具结构设计、模具材料选择、模具零件的加工工艺等。
设计完成后,需要制造模具。
模具制造包括模具零件的加工、热处理、装配和调试等过程。
二、熔铸金属准备在进行压铸件生产之前,需要准备铝合金或其他金属材料。
首先,将原料加入熔炉中进行熔化。
熔化后的金属液经过过滤、脱气等处理,以保证金属液的纯净度和流动性。
三、模具准备在进行压铸之前,需要将模具安装到压铸机上,并进行调试。
调试包括调整模具开合间隙、注射压力和注射速度等参数,以确保模具正常运行。
四、压铸过程在压铸过程中,首先关闭模具并将注射系统和冷却系统连接。
然后,将熔化的金属注入模腔中,通过注射系统将金属液注入模具中,并保持一定的注射压力和注射速度。
在注射过程中,模具内的金属液将迅速冷却凝固,形成压铸件的初步形状。
待金属冷却后,打开模具,取出压铸件。
五、后处理取出的压铸件需要进行后处理。
后处理包括去除余渣、切除浇口、修整表面、进行热处理等工艺。
热处理可以提高压铸件的硬度和强度,并消除内应力,提高其综合性能。
六、检验和质量控制对压铸件进行检验,包括外观检查、尺寸测量、物理性能测试等。
通过检验,判断压铸件是否满足要求。
同时,需要进行质量控制,确保每个环节的工艺参数和质量要求都得到满足。
七、包装和出厂经过检验合格的压铸件,进行包装,并标明产品的型号、规格、数量等信息。
然后,进行出厂发货,交付给客户使用。
压铸件模具生产工艺流程包括模具设计和制造、熔铸金属准备、模具准备、压铸过程、后处理、检验和质量控制、包装和出厂等环节。
每个环节都需要严格控制和操作,以确保生产出符合要求的压铸件。
这一流程为压铸件生产提供了指导和保证,也为压铸件的质量和性能提供了保障。
- 1、下载文档前请自行甄别文档内容的完整性,平台不提供额外的编辑、内容补充、找答案等附加服务。
- 2、"仅部分预览"的文档,不可在线预览部分如存在完整性等问题,可反馈申请退款(可完整预览的文档不适用该条件!)。
- 3、如文档侵犯您的权益,请联系客服反馈,我们会尽快为您处理(人工客服工作时间:9:00-18:30)。
模具制作标准
目的:为使模具制作及维修作业能降低成本,缩短模具制作周期,确保模具寿命,保证产品品质。
一、制作模具编号:
1、必须在模具外恻上方雕刻或锻打模具编号,字体要求整套
模具字高统一。
2、每块模板均须用字码打上模具编号,且方向统一。
3、模具所有螺丝、吊圈孔及模具部件都必须是公制规格,而
附加模具配件必须是标准规格,禁止自行土制。
二、基准位:
1、每套模具必须在B板和动模板(以动模板为参照)俯视图
视角的右下方做上记号以示基准,以便模具后续维修。
三、码模槽:
1、非工字模胚均需在前后模铣出码模槽,具体尺寸根据模具
大小设计而定。
四、顶柱孔:
1、动模必须开有足够大的顶柱孔,根据模具配比的机台,比
实际顶柱的尺寸大直径10-20MM(除真空模具)。
2、小型且中心进浇模具只需中间开一个顶柱孔,中型模具必
须开三个以上顶柱孔以保持顶出平衡。
五、复位机构装置:
当顶针(丝筒)与行位顶出装置干涉时,必须在模具上设
有先复位装置,不谨靠弹簧使顶针板复位,以免弹簧日后失效,行位(抽芯)与顶针(丝筒)相碰撞。
六、顶针动作:
1、应考虑模具在任何场合顶针都能可靠的顶出产品,并在合
模前顶针不与模具的任何配件相干涉地复位。
2、顶出时产品不能有任何超出产品要求的变形,迅速顶出痕
迹不影响产品表面质量。
3、顶出应平衡很顺,不可出现顶出倾斜现象及顶出有杂音的
产生。
七、行位动作:
1、滑块行位动作应顺滑,保证产品不得有拉变形现象,不可
出现卡死动作,不均匀松动等现象。
2、大滑块滑动部位应开油槽
3、在表面要求较高和壁厚较厚的铸件且有强度要求的产品,
滑块上应设有冷却水路。
4、当滑块滑动行程过长时,必须在模座上增长导向,通常滑
动部位做到宽度的1.5倍左右为宜,抽芯时滑块在导向槽的部分,要有滑块滑动部位的2/3在导向滑槽内。
5、斜导柱与导柱孔的配合间隙必须留有0.2MM以上,禁止
非间隙配合。
6、斜导柱的角度小于滑块锲紧面2度,大滑块的锲尽紧块须
伸入下模15-20MM以斜度面互锁反压。
7、模具上方的滑块最终定位应用弹弓推或拉,行式上不能用
钢珠定位,以避免模具在生产时滑块松动向下滑落导致与顶针及模具的其它配件相撞。
8、所有的滑块滑动磨檫面必须淬火HRC45度以上,大滑块
必须淬火后氮化增强硬度。
八、吊模孔:
1、小模具保证A、B板上下面均有吊模螺丝孔。
2、大型模具则需每块模板上下面有吊模螺丝孔。
九、模具外侧体现模穴数
1、一模多腔模具必须在模具外露面体现模具穴数如(模具编
号2171853-U-模具穴数4)以式区别,在试模前就打好。
十、异性顶针、镶件
1、异性顶针镶件转动时,必须做好防转装置。
2、防转装置必须可靠,单一定向,禁止两个方向定位(包括
丝筒顶针斜面)
十一、顶针设计
1、所有产品内部顶针必须用绞刀绞出,杜绝用钻头成型,避
免模具在大量生产时顶针孔磨损造成产品毛刺增多。
2、优先采用标准顶针(丝筒),严禁成型部分尺寸多大顶针
就用多大,在产品条件允许的情况下小于成型柱尺寸以便后续顶针孔磨损好做修改。
3、在避免丝筒与丝筒出现偏心是注意,销子部分不宜超过
10MM长。
十二、排气气设计
1、定模A板导柱后面必须开设排气槽,以免模具在正常生产
时导柱形成真空影响开锁模的液压能量损坏机件。
2、排气槽设计时必须注意,为使型腔的气体在压射时尽可能
的排除干净,要将排气槽设置在金属液最后充填的部位。
3、在产品结构较为特殊的情况下,可将排气槽设置在型芯与
推杆的间隙之间。
4、排气槽尺寸:锌合金排气槽深度0.05-0.12MM铝合金排气
槽深度0.1-0.15,排气槽在离开型腔20-30MM后,可将其深度加大至0.3-05MM以提高排气效果。
5、在需要增加排气槽面积时,以增大排气槽的宽度与数量为
宜,不宜过分增加其深度,以防生产时金属液贱出。
十三、排渣设计:
1、设计溢流槽时要注意便于从压铸件上去除,在祛除后铝合
金排渣口不超过1MM,锌合金则不超过0.3MM(特殊结构产品除外)不损坏铸件外观,在溢流槽上开设排气槽时,应合理设计溢流口,避免过早堵塞排气槽。
2、注意避免在溢流槽和铸件之间产生热结。
3、不应在同一溢流槽上开设多处溢流口或过宽的溢流口,以
免金属液产生倒流,部分金属液从溢流槽流回型腔。
4、溢流口的截面积应大于连接在溢流槽的排气槽截面积,否
则排气槽的截面积将被削减。
5、溢流槽的布置应有利于排除型腔中的气体,排除混有气
体、氧化物、分型剂残渣的金属液以及改善模具的热平衡状态。
十四、流道设计
1、内浇口设计原则:
A、金属液从铸件厚壁处向薄壁处充填。
B、内浇口的设置要进入型腔的金属液先流向远离浇口的部
位。
C、金属液进入型腔后不宜立即封闭分型面、溢流槽和排气槽
/
D、从内浇口进入型腔的金属液,不宜正面冲击型芯及型腔。
E、浇口的设置应便于去除,铝合金浇口祛除后残留料头不得
超过1MM,锌合金小于0.3MM。
F、避免在浇口部位产生热节。
G、采用多股内浇口时,要防止金属液进入型腔后从几路汇
合,相互冲击,产生涡流、裹气和氧化渣等缺陷。
H、薄壁铸件内浇口设置要小些,以保持一定的充填速度。
I、根据技术要求,表面要求较高且不在加工的部位,不宜设置
内浇口
J、管型铸件最好设置环型浇道。
2、横浇道设计
A、横浇道的截面积应从直浇道起到内浇口止,逐渐缩小,如
在横浇道出现截面积扩大的情况,金属液流过则会出现负压,由此必然会吸收分型面上的空气,增加金属液流动过程中的涡流。
B、圆弧状的横浇道可以减少金属液流动的阻力,但截面积应
逐渐缩小,防止涡流裹气。
C、横浇道应具有一定的长度与厚度,若横浇道过薄,则热量
损失大;若过厚则冷却速度缓慢,影响生产效率,增大金属损耗,。
保持一定长度的目的,主要对金属液起到稳流和导向作用。
D、多腔模具主横浇道截面积应大于各分支浇道截面积之和。
E、根据产品要求可设置盲浇道,以达到改善模具热平衡条
件,容纳冷污金属液、涂料残渣和气体的目的。
F、横浇道部分,应顺着金属液的流动方向磨光,保证横浇道
的光洁度,以免受阻影响填充速度。
G、在一般情况下,横浇道入口处应位于直浇道的上方,防止
压室中金属液过早流入横浇道内。
十五、分型面设计
1、铸件对动模芯的包紧力大于定模型芯的包紧力
2、分型面应满足合理的浇铸系统布置需求
3、分型面使模具型腔具有良好的溢流排气条件
4、分型面设置在金属液最后冲填的部位。
5、在模仁与模框的配合之间,模仁一般高出摸框0.1-0.3之
间,真空模则0.05-0.1之间。
十七、冷却水路设计
1、同一套模具尽量采用较少的冷却水嘴规格,以免增加设计
与制造的复杂性。
2、冷却水的直径一般为6-14MM。
在模具结构条件允许下尽
量采用数条冷却水路,以保持模具的热平衡。
3、水道与型腔间的距离,一般为15-20MM。
4、在模具外恻标示好进出水标志以(+-)表示
十八、辅助设计
1、模具尽量设计辅助柱,在模具中央如位置允许尽量把辅助
的直径做大。
2、辅助柱的长度一般长于模脚0.15-0.3MM
十九、模具后续维护:
1、铝合金模具在模具试模后5000模次以内(含试模数量)
需进行回火一次,第二次间隔回火时间10000-20000模次,后续按倍数时间延长,回火温度在450度高温回火祛除模具应力。
2、锌合金模具在模具试模后10000模次以内(含试模数量)
需进行回火一次,第二次间隔回火时间30000-50000模次,后续按倍数时间延长,回火温度在450度高温回火祛除模具
应力。
3、在薄壁件和高冲击的深腔模仁必须做氮化。