涂料涂装中的常见问题-失光
油漆在滚涂施工中的常见问题和解决方法

油漆在滚涂施工中的常见问题和解决方法1、滚涂容易起泡的原因u滚涂时由于滚筒在运动中带入大量的空气,导致漆膜容易气泡。
高树脂含量的漆适合于滚涂低树脂含量低的漆可以使用滚涂u溶剂型涂料单次施工膜厚太厚也容易起泡。
u漆膜表干过快,容易起泡。
2、解决滚涂易起泡的途径为了使油漆适合滚涂,需对配方或施工工具进行改进。
u采用流平和润湿优良的树脂和助剂。
u适当提高颜料的比例。
u使用特殊的滚涂工具破泡,如地坪涂料的施工。
u减低单次施工膜厚。
u减低表干速度,延长溶剂释放时间。
u加入特殊或过量的消泡剂。
过多消泡剂的缺陷:成本高、缩孔、附着力不良。
3、滚涂油漆的选择u一般各种底漆和中涂产品可以采用;u高光漆或面漆在使用前应进行施工确认。
u定制适合滚涂的产品。
3、滚涂工具选择注意事项:u滚涂溶剂型涂料时注意选用刷毛、辊轴与所用溶剂不能互溶的毛辊。
u施工粘度小的涂料应选用:刷毛稍长、细而软的毛辊:因为这类毛辊吸浆量大,滚涂过程中不易流淌和不均匀。
u施工粘度大的涂料应选用:刷毛稍短、稍粗、稍硬一些的毛辊:因为这类毛辊在吸饱涂料、滚涂过程中,毛倒下去容易重新立起来,还可保持较好的吸浆量,防止流淌和不均匀。
常见的漆膜弊病及其防治办法⑴、流挂现象:涂料施涂于垂直面上时,由于其抗流挂性差或施涂不当,漆膜过厚等原因而使湿漆膜向下移动,形成各种形状下边缘厚的不均匀涂层。
原因:1、溶剂挥发缓慢。
2、涂得过厚。
3、喷涂距离过近,喷涂角度不当。
4、涂料粘度过低。
5、气温过低。
6、几乎不换气,周围空气中溶剂蒸汽含量高。
7、涂料中含有比重大的颜料(如硫酸钡),在漆基中分散不良的色漆。
8、在旧漆膜上(特别是在有光的漆膜上)涂布新漆时也易产生流痕。
预防措施:1、溶剂选配适当2、对常规涂料一次涂布的厚度控制在20~25μm为宜。
为要获得较厚的涂层,对于热固性涂料可采用“湿碰湿”工艺,或选用高固体分涂料。
3、提高喷涂操作的熟练程度,控制喷涂距离为喷涂大工件25~30cm,喷涂小件15~20cm,并与物面平行移动。
涂膜失光和粉化

涂膜失光的原因可能有:(1)涂料配方不合理,例如:组成成分的相容性不好,稀释剂用量太大,颜料中含水分等都会造成失光;(2)被涂装表面相当粗糙和多孔,也会造成涂膜失光;(3)面漆将底漆咬起,影响面漆失光;(4)某些涂料耐光性不好,不适合户外使用,用于户外不久即失光。
粉化是由于漆膜的成膜物质(树脂)被破坏而引起。
某些颜料尤其是钛白颜料的感光作用很强(容易吸收短波的光),使脂肪酸破坏,产生出过氧化物及羟基酸,而羟基酸易吸水而使涂膜破坏,在破坏的涂膜处造成钛白颜料,成游离状态即导致涂膜粉化。
总之,涂膜粉化的原因主要是由于基料树脂在化学结构上的不稳定性,造成氧化、水分和紫外光波的混合作用而将基料树脂分解破坏所致。
因此在户外使用的涂料,应当选择耐候性好、不易粉化的涂料。
此外,还应注意下列一些易造成涂膜粉化的因素:(1)粉化夏天比冬天明显;(2)漆膜太薄造成早期粉化;(3)锐钛型钛白粉很容易粉化;(4)环氧树脂层耐候性差,一般较易粉化。
常见涂装缺陷产生的原因及预防处理措施
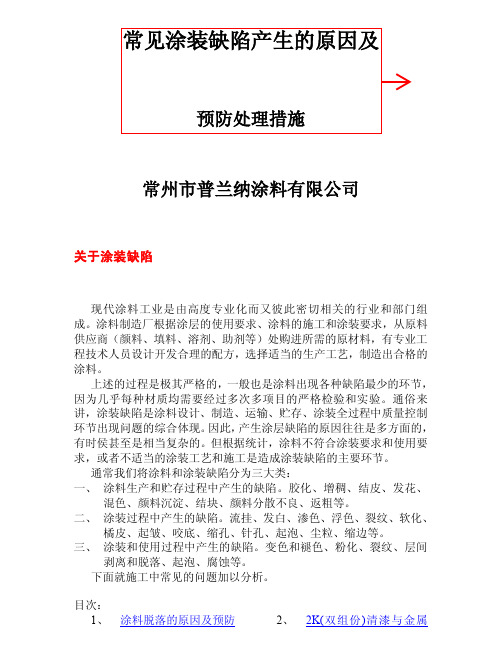
3. 确实了解旧漆的种类, 尽量避免不匹配现象发生。 4. 对于多次修补的漆面,建议尽量使用封闭底漆加以隔离。 5. 按规定使用适当的中间底漆,同时注意按规定使用配套的固化剂及稀释剂等辅
料,并保证产品要求的干燥时间后涂装面漆。 6. 新漆膜,特别是喷涂较厚的新漆膜,必须给予一定的干燥时间。如有条件的,
8、 漆面起泡或痱子 9、 针孔 10、 流挂 11、 渗色与浮红 12、 金属漆发花 13、 涂层的变色与褪色 14、 龟裂
相关说法
剥皮、失去附着力、附着差、脱落
相关说明
此类现象为基底与漆层之间失去附着力,包括面漆与底漆或旧漆之间、底漆和金属 漆之间。
相关原因:
一、 清洁或准备不当。包括: 1、 水磨底漆时使用的水砂纸号数太高,超过 1000#以上,使底漆表面过于光滑, 不利于面漆的附着。 2、 底漆表面研磨后的研磨灰尘或其它表面污染物若未确实彻底清除,则表面 漆层将不能够与底漆层发生适当稳定的接触,以致于造成粘合不良。 3、 底漆水磨后未能使水份完全干燥,或底面在施工前受潮,使其难以正常干燥, 出现粘合不良现象。 4、 使用了不当的材料(如:汽油)作为清洁剂,不但不能去除硅、矽等腊质, 留下一些高沸点的残留物在表面留下一层连续的“油膜”。建议清洁材料使 用 L919 除油剂。 5、 粘尘布使用不当也会造成涂料的附着力降低。使用中必须擦拭速度要快,力 量要轻一些,否则会在表面留下过多的粘性杂质,影响涂料的附着力。
六、封闭材料选择不当。为节约成本,采用硝基色漆打底,烤漆(2K)罩面的施工方 法。此类办法,如处理不当,极易造成面漆的脱落。或者有时在原子灰施工后未 喷涂二道底漆而直接喷涂面漆,也非常容易造成面漆的脱落。
粉末涂层色差和失光的原因及解决办法

粉末涂层色差和失光的原因及解决办法粉末涂层色差是指涂层表面出现不一致的颜色或色差现象。
而失光是指粉末涂层表面失去光泽,看起来暗淡无光。
这些问题会影响涂层的质量和外观,降低产品的价值。
因此,了解粉末涂层色差和失光的原因,并采取相应的解决办法,对于实现高质量的涂层非常重要。
1.颜料的选择与质量问题:粉末涂料中所使用的颜料种类繁多,如红色、黄色、蓝色、黑色等。
不同的颜料有不同的色彩饱和度和耐光性。
在选择颜料时,应根据涂层的使用环境和要求,选择适合的颜料。
解决办法:对于色差问题,通过调整颜料的配方和比例,以及添加适当的外加颜料,可以调整涂层的颜色。
另外,颜料的质量也对色差问题有重要影响,要确保使用的颜料品质符合规定,并且仔细控制颜料的搅拌和混合过程。
2.涂料涂布技术问题:涂料在涂布过程中可能会发生均匀性不佳的问题,如涂料厚度不均匀、涂层涂布后出现斑点等。
解决办法:在涂布过程中,可以采用自动涂布设备,确保涂布均匀。
此外,涂布之前要进行充分的表面处理,确保基材的平整度和涂料与基材的粘附力。
3.人为操作误差:人为因素也是引起涂层色差的原因之一,如工人在施工时的喷涂角度不一致、涂布厚度不一致等。
解决办法:培训和提高工人的技术水平,确保每个工人能够按照规范的要求进行涂层施工。
使用专业的涂装设备和工具,可帮助减少人为误差。
1.颜料问题:颜料的选择和质量对涂层的光泽度有着重要影响。
如果颜料的折射率不合适,或者颜料中含有杂质,都会导致涂层失去光泽。
解决办法:采用高品质的颜料,确保颜料的折射率与基材相匹配,并进行筛选和充分搅拌,以防止杂质对涂层造成不良影响。
2.基材表面处理不当:基材表面的油污、氧化物、铁锈等杂质会降低涂层的附着力和光泽度。
解决办法:在涂装之前,要进行充分的基材准备,包括清洗、脱脂和除锈等工艺。
确保基材表面干净、平整,并具有良好的附着力。
3.涂料固化问题:如果涂层没有得到充分的固化,也会导致失光现象。
解决办法:调整涂料的固化时间和温度,确保涂层能够在理想的环境条件下进行充分固化。
喷涂出现的问题及对策

44
咬底/起皱 (4)
预防:
• 每喷涂的漆层要薄而均匀。 • 各漆层间的流平时间要足,干燥温度要适当,烘炉温 场要均匀。 • 只使用推荐型号的稀料。 • 调整涂料的溶剂或催干剂。
修补方法:
首先让漆膜充分固化。缺陷轻微时,打磨、抛光即可。 若缺陷较严重,将漆膜打磨到基底,重新喷漆。
45
腻子印 (1)
13
鼓泡 / 空气陷入(4)
预防:
• • • • 正确地使用原子灰、填眼灰或底漆。 正确制作羽毛边。 避免油漆一次喷涂过厚,保证油漆渗入缝隙和死角。 一定要使用推荐的稀料,并按照正确的喷涂工艺操作。 底漆要喷涂得薄而湿。 • 检查基底有无气孔,特别要注意玻璃钢表面胶层内的 气泡。仔细清除气泡并封闭基底。 • 烘烤漆膜时,防止温度过高。
14
鼓泡 / 空气陷入(5)
修补:
根据气泡的深度将相应的漆膜全部打磨掉,修 补好下层缺陷后,重新喷涂油漆。
15
泛白 / 起雾(1)
16
泛白/ 起雾(2)
原因:水气凝结并陷在湿漆膜内。
• 环境原因:喷漆室温度、湿度高;喷漆房内有穿堂风, 或者空气流动不良。 • 涂料原因:使用的稀料挥发速度太快;溶剂和稀释剂 选配不当,真溶剂挥发过快,造成树脂析出而泛白; 涂料或稀释剂含有水份。 • 喷涂原因:压缩空气的压力太大,喷枪调整不当;用 压缩空气吹拂漆膜,试图加速溶剂挥发;基底温度低 于室温。
喷涂出现的问题及对策
涂料的施工方式基本上都是喷涂, 这里所讲的问题针对涂料经过涂装成膜 以后所产生的缺陷。在此,特对常出现 的几种问题进行鉴别分析。
1
痱 子 (1)
漆膜表面呈现成片的大小不等、密度不同的气 泡。大气泡直径大于1.5mm,一般成片出现,有时也 会单独出现。小气泡直径一般为0.5mm,其分布蜿蜒 曲折或状似指纹。一般来说面漆层中气泡出现的机会 要比油漆与基底之间的更多。
喷涂涂层常见的弊病及排除方法
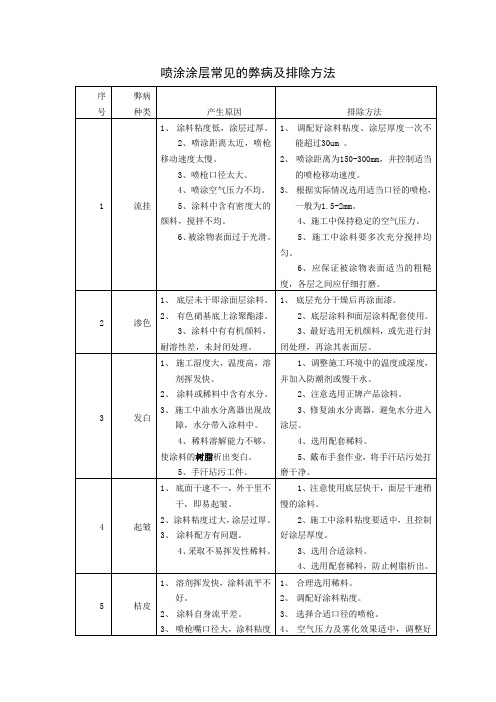
喷涂涂层常见的弊病及排除方法序号弊病种类产生原因排除方法1流挂1、涂料粘度低,涂层过厚。
2、喷涂距离太近,喷枪移动速度太慢。
3、喷枪口径太大。
4、喷涂空气压力不均。
5、涂料中含有密度大的颜料,搅拌不均。
6、被涂物表面过于光滑。
1、调配好涂料粘度、涂层厚度一次不能超过30um 。
2、喷涂距离为150-300mm,并控制适当的喷枪移动速度。
3、根据实际情况选用适当口径的喷枪,一般为1.5-2mm。
4、施工中保持稳定的空气压力。
5、施工中涂料要多次充分搅拌均匀。
6、应保证被涂物表面适当的粗糙度,各层之间应仔细打磨。
2渗色1、底层未干即涂面层涂料。
2、有色硝基底上涂聚酯漆。
3、涂料中有有机颜料,耐溶性差,未封闭处理。
1、底层充分干燥后再涂面漆。
2、底层涂料和面层涂料配套使用。
3、最好选用无机颜料,或先进行封闭处理,再涂其表面层。
3发白1、施工湿度大,温度高,溶剂挥发快。
2、涂料或稀料中含有水分。
3、施工中油水分离器出现故障,水分带入涂料中。
4、稀料溶解能力不够,使涂料的树脂析出变白。
5、手汗玷污工件。
1、调整施工环境中的温度或湿度,并加入防潮剂或慢干水。
2、注意选用正牌产品涂料。
3、修复油水分离器,避免水分进入涂层。
4、选用配套稀料。
5、戴布手套作业,将手汗玷污处打磨干净。
4起皱1、底面干速不一,外干里不干,即易起皱。
2、涂料粘度过大,涂层过厚。
3、涂料配方有问题。
4、采取不易挥发性稀料。
1、注意使用底层快干,面层干速稍慢的涂料。
2、施工中涂料粘度要适中,且控制好涂层厚度。
3、选用合适涂料。
4、选用配套稀料,防止树脂析出。
5桔皮1、溶剂挥发快,涂料流平不好。
2、涂料自身流平差。
3、喷枪嘴口径大,涂料粘度1、合理选用稀料。
2、调配好涂料粘度。
3、选择合适口径的喷枪。
4、空气压力及雾化效果适中,调整好高。
4、喷涂距离不当,空气压力不足,涂料雾化不好。
5、被涂物表面处理不平整,影响涂料流平性。
6、涂料或稀料中吸收有水分。
喷漆的一些原因及处理方法-光泽不良

喷漆的一些原因及处理方
法-光泽不良
有光泽涂层干燥后没有达到应有的光泽或涂装后不久涂层出现光泽下降,表面不均匀,并有轻微纹理,呈雾状朦胧的现象.
1、产生原因
(1)颜料的选择,分散和混合比不适当,树脂的混溶性差,溶剂选择不当.
(2)施喷件表面对涂料的吸收量大,且不均匀.
(3)施喷件表面粗糙,且不均匀.
(4)过烘干或烘干时换气不充分,涂料抗污气性差.
(5)喷涂时有虚雾附着或由补漆造成.
(6)能抛光的涂层未干透就抛光.
(7)在高温,高湿或极低气温的环境下涂装.
2、防治方法
(1)通过试验,选择合适的涂料,选择油漆厂指定的溶剂.
(2)喷涂相应的隔绝底漆,以消除底漆对面漆的吸收或不均匀的吸收.
(3)应仔细打磨(注意打磨手法和砂纸拍好的选择),消除施喷件表面的粗糙度.
(4)严格遵守规定的烘干条件,烤房内换气要适当.
(5)注意喷涂顺序,确保喷涂厚度均匀,减少喷涂虚雾的附着.
(6)抛光工序要在涂层完全干透,熟化后进行.
(7)控制涂装环境.。
涂料常见问题及解决方法

涂料常见病态及解决方法一、针孔——在漆膜表面出现的一种凹陷透底的针尖细孔现象。
这种针尖状小也就像针刺小孔,孔径在100微米左右。
(一)原因:1、木才表面木眼太深,填充困难,打磨不好;2、边疆喷涂两次间隔时间太短,下涂层干燥不完全,上涂层急速干燥;3、被涂面有灰尘,水分,压缩空气有水、油污;4、油漆配好搅拌后静置时间不够(一般应静放10-15分钟);5、一次性厚涂,表面干燥而底层溶剂继续蒸发而凸起;6、使用不良的涂料稀释剂或错用稀释剂;7、固化剂加入太多,或错用固化剂;8、稀释剂用量太小,涂料粘度过高;9、施工环境温度过高,湿度太大;10、喷涂压力过大或距离太远。
(二)解决方法:1、木材表面应充分填补好,砂光打磨达到要求;2、多次涂装时,延长重涂时间,让下层充分干燥;3、处理好补涂面灰尘和水,打水磨后,应晾置2-3小时以上,净化压缩空气;4、搅拌均匀后静置5-10分钟才能用;5、分两次或多次施工;6、使用配套产品;7、按指定的调漆比例正确调漆,并且充分搅拌均匀;8、增加稀释剂用量,达到施工最佳粘度;9、设法改善作业环境,夏天温度过高,要相应减少固化剂用量,适当选用慢干溶剂(如环已酮、CAC);10、调整好喷涂压力的距离。
二、气泡——漆膜干后出现大小不等的突起圆形泡,也叫鼓泡。
(一)原因:1、木材表面木眼深,填充困难,喷涂漆成膜后,白坯的气体向外膨胀顶起漆膜,引起起泡;2、使用过高粘度的涂料;3、喷涂空气压力过高,涂料混入空气过多;4、加热干燥过于激烈;5、物面含水率高,环境温度太高,湿度太大,通风不行;6、空气压缩机及管道带有水分;7、固化剂加入油漆调匀后,放置时间不够;8、采用含水醇高的不良稀释剂刷涂时,溶剂挥发太快;9、一次涂太厚或边疆喷涂层间间隔时间太短。
(二)解决方法:1、刮透明腻子,充分填补木眼,在喷涂前先刷一遍底得宝封闭缝隙,排出木眼中的空气;2、适当调整涂料粘度;3、调整适当的空气压力,减少空气的混入;4、加热干燥时,待溶剂挥发后进行;5、改善施工环境物面应干燥,被涂面打水磨后晾干2-3小时以上;6、使用油水分离器分离,并定期排水,每半天一次;7、搅拌后应静置5-10分钟;8、选用配套稀释剂;9、可加5-10%慢干溶剂(如CAC,环已酮等);10、分多次施工,多次涂装时,延长干燥时间,让下层充分干燥。
涂装过程中发生光泽不良的防治

涂装过程中发生光泽不良的防治1.定义漆膜的光泽因受施工或气候影响而降低的现象称为光泽不良或倒光。
2.现象面漆漆膜干燥后没有达到应有的光泽,或涂装后数小时,长至二、三个星期内产生光泽下降的现象,光泽黯淡、甚至无光。
易产生此种弊病的涂料为硝基纤维素涂料和烘烤型涂料。
外用涂料的漆膜经长时间使用,由于老化的作用而光泽逐渐消失的自然现象不属于这一漆膜弊病,后者称为失光;但常常把光泽的失去统称为失光。
3.原因(1)涂料生产配方和工艺问题。
如油脂和树脂含量不足工聚合度不好,颜填料和溶剂量过多,树脂的相互混溶性差,涂料的细度不够,有尘屑混入等。
(2)被涂物面处理不当,表面过于粗糙,留有油污、水分、蜡质等。
木质表面底漆封闭性不好,面漆的树脂会会渗入至木材的细孔,漆呈现黯淡无光;新的水泥墙面呈碱性,与油性涂料皂化而失光。
(3)涂料没有充分搅拌,树脂等沉在下部,涂装时上半桶颜料少、漆料多,涂后有光;下半桶颜料多、漆料少,涂后无光。
加入的稀释剂过量,冲淡了有光漆的作用。
(4)在寒冷、湿度大的气候施工,使水汽凝结膜面,涂料失光。
施工场所不清洁,灰尘太多或在干燥过程中遇害到风、雨、煤烟等,漆膜也容易出现半光或无光。
特别是桐油涂膜,如遇风雨,漆膜无光。
(5)面漆漆膜过薄,涂装面不平整等引起。
(6)底漆或腻子层未干透就涂装面漆,面漆干未透就抛光,也会造成失光。
(7)烘漆选用溶剂不当,尤其采用挥发性快的溶剂或过早放入烘烤设备中去,烘干时温度过高,或烘干换气不充分等,造成光泽的下降。
4.防治措施(1)涂料中的树脂基料需占有一定比例,否则不仅无光泽而且防腐保护性能也不好。
采用两种或两种以上树脂拼用的涂料,树脂间要有良好的相容性。
涂料生产中防止水分和灰尘的混入;涂料一定要达到较好的细度,研磨得越细,涂料的光泽越高,一般汽车漆的细度要求在20um以下。
(2)加强涂层表面的光滑处理,面漆下要加涂底漆或腻子层。
木器或水泥墙面要涂装相应的封闭底层,防止涂料渗入孔隙。
涂装常见缺陷
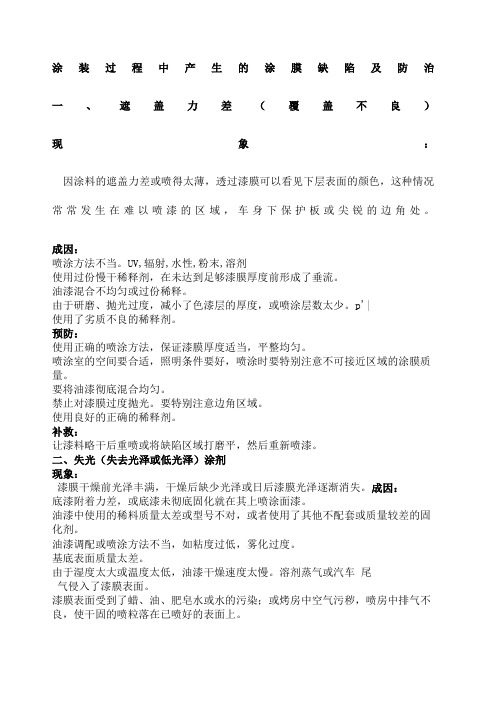
涂装过程中产生的涂膜缺陷及防治一、遮盖力差(覆盖不良)现象:因涂料的遮盖力差或喷得太薄,透过漆膜可以看见下层表面的颜色,这种情况常常发生在难以喷漆的区域,车身下保护板或尖锐的边角处。
成因:喷涂方法不当。
UV,辐射,水性,粉末,溶剂使用过份慢干稀释剂,在未达到足够漆膜厚度前形成了垂流。
油漆混合不均匀或过份稀释。
由于研磨、抛光过度,减小了色漆层的厚度,或喷涂层数太少。
p'|使用了劣质不良的稀释剂。
预防:使用正确的喷涂方法,保证漆膜厚度适当,平整均匀。
喷涂室的空间要合适,照明条件要好,喷涂时要特别注意不可接近区域的涂膜质量。
要将油漆彻底混合均匀。
禁止对漆膜过度抛光。
要特别注意边角区域。
使用良好的正确的稀释剂。
补救:让漆料略干后重喷或将缺陷区域打磨平,然后重新喷漆。
二、失光(失去光泽或低光泽)涂剂现象:漆膜干燥前光泽丰满,干燥后缺少光泽或日后漆膜光泽逐渐消失。
成因:底漆附着力差,或底漆未彻底固化就在其上喷涂面漆。
油漆中使用的稀料质量太差或型号不对,或者使用了其他不配套或质量较差的固化剂。
油漆调配或喷涂方法不当,如粘度过低,雾化过度。
基底表面质量太差。
由于湿度太大或温度太低,油漆干燥速度太慢。
溶剂蒸气或汽车尾气侵入了漆膜表面。
漆膜表面受到了蜡、油、肥皂水或水的污染;或烤房中空气污秽,喷房中排气不良,使干固的喷粒落在已喷好的表面上。
在新喷涂的漆膜上使用了太强洗涤剂或清洁剂,或者喷完后过早地进行抛光,或者使用的抛光蜡太粗。
面漆或清漆喷得太薄。
预防:使用合格的底漆,要等底漆层充分干燥后再在其上喷涂面漆。
只使用推荐型号的稀料和合格的固化剂。
要充分搅拌油漆,保证喷漆环境符合要求,按照正确的方法进行喷涂,喷涂厚度适当。
彻底地清理基底表面。
要保证漆膜在温暖、干燥的条件下进行干燥。
干燥过程中,漆膜表面要有适当的空气流动。
喷涂面漆之前,应当用清洁剂揩擦底漆层,彻底清洁表面。
颜填料,助剂,树脂,乳液,分散sb-BeY!Y1IH禁止在新喷涂的漆膜表面使用强力洗涤剂或清洁剂。
涂装施工中常见问题及处理办法

涂装施工中常见问题及处理办法涂装工程是“面子工程”,做的不好,就要返工,那么时间与金钱就白白的浪费。
俗话说涂装行业是三分油漆、七分施工。
油漆是否好用是与油漆师傅的技术水平密不可分。
公司根据以往案例,深入进行了研究分析,我们明白,因各施工单位的情况不一致,在涂装过程中遇到的问题也各不相同。
因此在施工过程中不可避免地会产生涂膜缺陷,产生的原因与被涂物的状态、选用油漆、涂装工艺及设备与涂装环境等有关。
现将涂装常见的漆病及防治方法详述如下1、渗色被涂物的原有面漆(例;红色、褐色及黄色面漆)的颜料渗入被涂物面漆中,常产生在涂浅色面漆场合。
由底层上除附着的着色物透过或者渗入面涂层,产生异色斑现象称之底层污染。
起因:(1)被涂物表面被底层有渗色倾向颜色的漆料所污染(如落上漆雾)。
(2)设备未清洗干净。
(3)旧漆面未进行适当封固。
(4)底涂漆料被易形成渗色的材料所污染。
预防:勿使易产生渗色的漆雾落在于工作物上。
完全清洗所有设备。
在未进行喷涂前,先在一小片的地方,喷涂一层色漆,测试原有漆膜,如有渗色状况,则按漆厂要求予以封固。
(1)底漆内绝不可混入其它杂质。
(2)使用面漆近似颜色的中涂漆,假如白色或者浅色面漆,则不能使用红色的中涂层。
原子灰腻子使用的固化剂不应过量。
补救方法:在多层底漆及面漆均已喷涂后开始发生渗色时,则可用防渗封底予以隔绝。
2、涂膜产胶状物或者硬块。
起因:(1)稀释剂溶解力差导致涂料中的胶状物不能全部溶解。
稀释时会先出浑浊,然后析出胶状物,尽力搅拌也难溶解,清漆此种现象较好。
(2)色漆析出的胶体与颜色结成硬块,稀释硝基漆中的硝化棉有一定限度,超出限度即析出。
预防:选用质量好的稀释剂、清漆,禁止使用质量差的稀释剂与放置时间过长的清漆。
补救方法:(1)对稀释剂与要紧成膜物质间的配备是否合适难于确信时,可将涂料涂装玻璃上,观察其是否有析出;有严重析出时,则不能使用。
(2)硝基漆有析出时,可加丙酮等强溶剂使其再溶化。
粉末涂层色差和失光的原因及解决办法

粉末涂层色差和失光的原因及解决办法
1. 现象:涂层表面明显色差和失光
2. 形成原因:一般是由涂料弊病、涂装弊病和涂膜成分的分解和变质引起。
①粉末涂料本身的颜料在分布不均匀,不耐温或树脂易发黄时,即可引起
涂膜变色。
②被涂工件前处理质量差时或有残留前处理液时,可引起涂膜变色和失光。
③涂膜烘烤时间过长或温度过高时,可引起涂膜变色和失光。
④两种不同厂家或不同性质的粉末涂料混杂,易产生失光。
⑤工件表面太粗糙或涂层厚薄不均匀,引起色差。
3. 解决方法
①要求粉末涂料厂家改进粉末粉料质量或更换合格的粉末涂料。
②改进前处理方法,选择合适的前处理工艺。
既要能将底材处理干净,并
形成有利于涂装的薄膜,又要不留下任何影响涂装表面质量的残留液。
③制定适当的烘烤条件,选择合适的烘烤温度和时间。
粉末涂料型号和厂
家不同,烘烤的温度和时间也要作相应的变更。
④换粉前必须彻底清理喷粉系统,特别是两种不同颜色的粉末涂料时,有
条件的最好采用两套喷房,避免两种不同性质的粉末涂料混杂,防止渗色和失光。
⑤回收粉末涂料与新粉末涂料混合比例要恰当,一般为1:1或3:2较恰当。
⑥降低工件表面的粗糙度,如打磨、抛光等,调整好喷粉工艺参数,保证
喷粉设备运行良好,以确保涂层厚度均匀一致。
汽车喷涂常见问题及解决方法→失光

汽车喷涂常见问题及解决方法→失光
新喷涂的油漆漆膜光泽度低,称为失光。
形成原因
1、湿涂层吸收了蜡或其它类似的污染物。
2、腻子层在打磨前未完全干透。
3、打磨砂纸过粗。
4、选用的稀释剂干燥速度过快。
5、选用了与涂料不配套的固化剂。
6、固化剂或稀释剂加入量不当。
7、双组分涂料产品的各组分混合方法不正确。
8、没有足够的挥发时间。
9、对单工序金属漆雾喷过头。
10、在湿碰湿体系中,前一道涂层溶剂未经充分挥发便继续喷涂或者一次喷的太厚。
11、烘烤温度太高或时间太长。
解决方法
1、在打磨和喷涂之前,对喷涂区及周边区域进行彻底脱脂。
2、根据周围环境温度和漆膜厚度,选择合理的干燥时间。
3、选择使用合适的砂纸。
4、根据周围环境温度、工件大小和空气流通速度选择稀释剂。
5、按正常配比涂料的各组分。
6、选用推荐与稀释剂配套的固化剂。
7、必须有充足的挥发时间。
8、实行一薄层雾喷。
9、选用正确的固化剂、稀释剂比列,先添加固化剂,搅匀后在加入稀释剂。
10、按照推荐的挥发时间,防止喷涂过多,以免导致涂层过厚。
11、经常检查定时器和温度调节器的工作状态。
12、进行抛光处理,增加光泽度。
若效果不明显,可在烧打磨后重新喷涂。
赞是一种友谊 | 分享传递智慧。
油漆表面失光原因

油漆表面失光原因一、前言油漆表面失光是指油漆表面的光泽度降低或完全消失的现象。
这种现象可能会发生在新涂层上,也可能会在旧涂层上出现。
油漆表面失光不仅会影响美观度,还会降低涂层的保护性能和耐久性能。
二、原因分析1. 油漆质量问题油漆本身质量不好是导致表面失光的主要原因之一。
如果油漆中添加了过多的溶剂或稀释剂,那么在干燥过程中就会导致溶剂挥发太快,使得表面无法形成平滑的薄膜,从而丧失了光泽度。
此外,使用劣质或老化的油漆也容易导致表面失光。
2. 涂装条件问题涂装条件是影响油漆表面质量的重要因素之一。
如果涂装时温度过低或湿度过大,那么就会影响油漆干燥速度和固化效果,从而导致表面失光。
此外,在涂装时未按照正确比例混合基础材料和固化剂也会导致表面失光。
3. 基础处理问题基础处理不当也是导致表面失光的原因之一。
如果在涂装前未对基础进行充分清洁、打磨或去除旧漆层,那么新涂层就无法牢固附着在基础上,从而导致表面失光。
此外,使用不适合的底漆或底漆施工不当也会影响表面质量。
4. 涂装方法问题涂装方法不当也会导致表面失光。
例如,喷涂时喷嘴距离太远、喷枪压力过大或过小、喷涂速度过快等都会影响油漆的均匀性和质量,从而导致表面失光。
此外,在刷涂时刷子的选择和使用方法也很重要。
5. 环境因素问题环境因素也可能影响油漆表面质量。
例如,在强烈阳光下暴晒或风吹雨淋的环境中进行涂装都会影响油漆干燥速度和质量,从而导致表面失光。
三、预防措施1. 选择优质的油漆选择优质的油漆是预防表面失光的关键。
应该选择符合国家标准的产品,并尽量避免使用过多的溶剂或稀释剂。
2. 涂装条件控制在涂装时,应该控制好温度和湿度,保持室内空气流通,以确保油漆干燥速度和固化效果。
同时,在涂装前应该认真混合基础材料和固化剂,并按照正确比例进行混合。
3. 基础处理在涂装前,应该对基础进行充分清洁、打磨或去除旧漆层,并使用适当的底漆。
此外,要确保底漆施工均匀、干燥彻底。
喷漆的一些原因及处理方法-失光

喷漆的一些原因及处理方
法-失光
由于涂料不良导致所提漆膜的光泽低于标准板光泽的现象,以及在使用过程中最初在光泽的漆膜表面上出现光泽减少的现象,统称为失光.后一种失光,有时是可逆的,借助抛光能消除.
1、产生原因
(1)涂装不良,未按工艺执行,如涂得过薄,过烘干和被涂面粗糙等.
(2)所选用涂料的耐候性差.
(3)漆膜(尤其是挥发干燥型涂料)干燥收缩造成.
(4)阳光照射,水气(高温高湿)作用和腐蚀气体的沾污.
2、防治方法
(1)严格工艺要求或漆厂推荐的涂料施工条件进行涂装.
(2)按被涂物的使用条件,选用耐候性优良的涂料.
(3)如所用涂料有抛光性,则进行抛光即可恢复光泽.。
油漆表面失光原因

油漆表面失光原因一、引言油漆是用于保护、美化物体表面的一种涂料。
然而,在使用过程中,我们有时会发现油漆表面出现失光的问题,即表面不再光滑、发亮。
本文将探讨油漆表面失光的原因,并为解决这一问题提供一些建议。
二、油漆表面失光原因的分析2.1 使用劣质原材料1.油漆涂料中含有劣质原材料,如低质量的树脂、填料等,这些材料容易使油漆表面产生异物、晶粒等不均匀的质感,从而导致表面失光。
2.2 涂层施工不当1.涂层施工时,涂料未均匀涂刷在表面上或者涂层过厚,导致油漆表面形成凹凸不平的痕迹,从而影响了光的反射情况,使表面失光。
2.在涂层施工后,未进行足够的干燥时间,或者干燥条件不适宜,导致涂层未完全固化,从而使表面失光。
2.3 使用不当1.在使用油漆涂料后,未进行适当的保养和清洁,导致涂层表面积累了大量的灰尘、污垢等,阻碍了光的反射,使表面失光。
2.使用过程中,摩擦或者刮伤涂层表面,导致表面失去光滑的效果。
三、预防和解决油漆表面失光的方法3.1 选择优质原材料1.在购买油漆涂料时,选择质量可靠的品牌和产品,避免使用劣质原材料,以确保涂层质量。
2.注意查看产品的材料成分,确认是否含有高质量的树脂、填料等,避免使用含有大量劣质原材料的涂料。
3.2 注意涂层施工1.在涂层施工前,充分准备涂刷工具和材料,确保能够均匀地涂刷在表面上。
2.在施工过程中,注意均匀涂刷,控制涂层的厚度,避免形成凹凸不平的表面。
3.在涂层施工后,确保涂层有足够的干燥时间,或者提供适宜的干燥条件,保证涂层能够完全固化。
3.3 做好保养和清洁1.在使用油漆涂料后,定期进行表面的保养和清洁工作,及时清除灰尘、污垢等杂质,保持表面的光亮度。
2.使用合适的清洁剂和工具进行清洁,避免使用粗糙的材质或刷子,以免刮伤涂层表面。
3.如果有刮伤或损坏,及时进行修复,以恢复其光滑的效果。
四、结论油漆表面失光是由于使用劣质原材料、涂层施工不当和使用不当等原因所导致的。
涂装设备喷涂出现失光的原因及处理方法
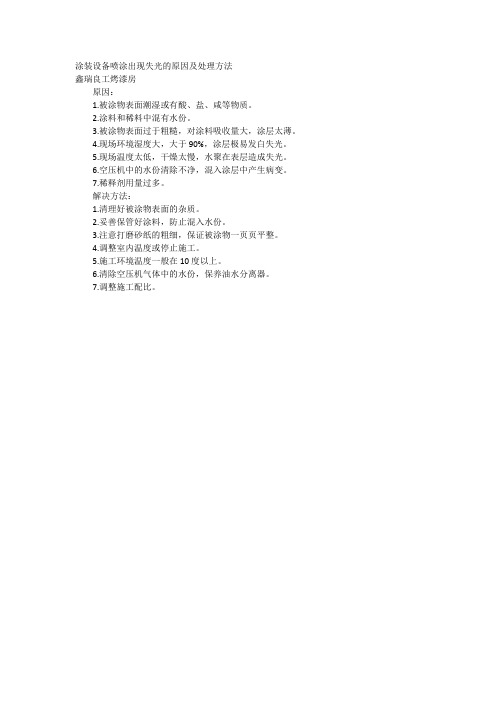
涂装设备喷涂出现失光的原因及处理方法
鑫瑞良工烤漆房
原因:
1.被涂物表面潮湿或有酸、盐、咸等物质。
2.涂料和稀料中混有水份。
3.被涂物表面过于粗糙,对涂料吸收量大,涂层太薄。
4.现场环境湿度大,大于90%,涂层极易发白失光。
5.现场温度太低,干燥太慢,水聚在表层造成失光。
6.空压机中的水份清除不净,混入涂层中产生病变。
7.稀释剂用量过多。
解决方法:
1.清理好被涂物表面的杂质。
2.妥善保管好涂料,防止混入水份。
3.注意打磨砂纸的粗细,保证被涂物一页页平整。
4.调整室内温度或停止施工。
5.施工环境温度一般在10度以上。
6.清除空压机气体中的水份,保养油水分离器。
7.调整施工配比。
汽车漆面退色与失光的治理

汽车漆面退色与失光的治理汽车在使用中,漆面颜色逐渐变浅,并失去原有的光泽,这便是漆面退色、失光。
漆面出现退色、失光现象,应正确判断产生的原因,并采取相应措施进行治理。
一、漆面退色、失光的原因与种类(一)漆面退色、失光的原因1.汽车涂装方面的原因(1)所用涂料耐候性能差,在不良气候条件下易产生退色、失光。
(2)所用涂料耐光性能差,受强光照射易产生退色、失光。
(3)所用涂料耐擦伤性能差,在汽车清洗和擦拭中易产生退色、失光。
2.汽车使用方面的原因(1)使用环境不良。
汽车在烟尘严重的矿区、工地、工业、饭店、烧烤等污染严重的城市,盐雾严重的沿海地区,温差变化大和气候变化大等地区行驶或停放,均会使车身漆面遭受腐蚀和损伤,造成漆面退色、失光。
(2)停放环境不良。
汽车经常在露天停放,受到风吹、日晒、雨淋等自然侵蚀,导致漆面退色、失光。
(3)交通膜的影响。
交通膜是汽车在运行时车身漆面与空气摩擦在其表面形成的静电层。
由于该静电层易吸附灰尘及有害气体等腐蚀性物质,从而导致漆面退色、失光。
3.汽车清洗方面的原因(1)所有清洗剂质量差,尤其是使用碱性较强清洗剂会直接侵蚀漆面。
(2)水质不清洁,含有腐蚀性物质或含有酸、碱性物质,这样会直接造成对漆面的侵蚀,使漆面失光。
(3)水压不当,冲洗时水压过高,使车身漆面的光亮层受到冲刷而失色。
(4)洗车方法不当,在洗车时,一般都是先冲洗,后擦拭,如不先冲就擦拭,往往因车身漆面上有浮尘、砂粒,这样就使漆面擦伤而出现划痕,因而使漆面失色失光。
4.漆面护理方面的原因(1)漆面护理不及时,使漆面得不到应有的保护。
(2)漆面护理用品质量差,起不到保护的作用。
5.其他方面的原因(1)透镜效应。
所谓透镜效应是指当车表漆面上存有小水滴时,由于水滴呈扁平凸透镜状,在阳光的照射下,对日光有聚焦作用,焦点处的温度高达800-1000℃,从而导致漆面被灼蚀,出现用肉眼看不见的小孔洞,有些深达金属基材。
由于透镜效应至使漆面被酌伤,若酌伤范围大,分布密度较高,漆面就会出现严重程度的失光。
- 1、下载文档前请自行甄别文档内容的完整性,平台不提供额外的编辑、内容补充、找答案等附加服务。
- 2、"仅部分预览"的文档,不可在线预览部分如存在完整性等问题,可反馈申请退款(可完整预览的文档不适用该条件!)。
- 3、如文档侵犯您的权益,请联系客服反馈,我们会尽快为您处理(人工客服工作时间:9:00-18:30)。
涂料涂装中的常见问题-失光
涂料失光,涂料涂膜干燥后,表面发暗、无光或出现光泽下降的现象。
涂料失光的原因分析:
(1)烘烤过度或非对流循环干燥(即烘烤时换气不充分)。
(2)被涂物表面粗糙或涂装前被涂物表面处理不干净,对涂料吸收不均匀。
(3)涂料涂装现场湿度过大,或在极高、极低的温度下涂装。
(4)涂料颜色的选择、分散和混合比不适当,或溶剂不配套。
防止涂料涂膜失光的方法:
(1)严格按照涂装工艺选定的干燥温度和时间,进行对流循环方式干燥。
(2)打磨时不可用过粗纱布或砂纸,以免造成打磨表面粗糙。
(3)涂装前表面处理要达到彻底无油、无锈、无水、无其他灰尘和杂质。
(4)涂装环境应符合要求,温度不低于15℃,相对湿度不高于70%。
(5)选择合适的涂料,并按照涂料厂家指定的溶剂与之配套。
中国新型涂料网()。