炼钢的基础理论概论
炼钢基本原理

CaO MgO MnO FeO CaF2 Fe2O3 A12O3 TiO2 SiO2 P2O5 碱性←——中性——→酸性 2.2 炼钢炉渣的主要性质
2
(1)炉渣的碱度。炼钢炉渣碱度常用的表示方法有: 1)当沪料含 P 较低时(铁水 P<0.3%),用渣中碱性最强的 CaO 和酸性最强的 SiO2 含量之比表示。即:R=CaO/ SiO2。 2)当炉料中含 P 量较高时,则要考虑渣中 P2O5 对碱度的影响,此时的表示 方法有多种,其中最简单的人法是将 P2O5 与 SiO2 的作用视为等值的表示方法。 即:R=CaO/ SiO2+ P2O5。 炼钢碱性渣按其碱度大小。一般可分为三类:R=1.3-1.5 为低碱度;R= 1.8-2.0 为中碱度渣;R>2.5 为高碱度渣。 (2)炉渣的氧化性。炉渣的氧化性是指炉渣向金属熔他传氧的能力,一般以 渣中氧化铁含量来表示。 炉渣中的氧化铁有两种形式,即 FeO 和 Fe2O3。化学分析时经常确定总铁量 (即 Fe 量)及 FeO 量,通过计算即可得出 Fe2O3 量。通常用% FeO 表示炉渣 氧化性。把 Fe2O3 折合为 FeO 有两种计算方法: 1)全氧法:% FeO =%Feo 十 1.35×%Fe2O3 式中 1.35=3×72/160 表示各氧化铁中全部的氧为 FeO, 1 摩尔 Fe2O3 可生成 3 摩尔的 FeO。 2)全铁法:% FeO =%FeO 十 0.9×%Fe2O3 式中 0.9=2×72/160 表示各氧化铁中全部的铁为 FeO,1 摩尔 Fe2O3 可生成 2 摩尔的 FeO。 全铁法比较合理。 因为在渣样冷却过程中,有少量低价氧化铁被氧化成高价 氧化铁,使全氧法计算结果偏高,而全铁法则可避免这种误差。 实际炉渣的氧化能力是个综合的概念,其传氧能力还受炉渣粘度、熔池搅拌 强度、供氧速度等因素的影响。 3 炼钢过程的基本反应 在炼钢的氧化精炼过程中,各种炼钢方法去除杂质的基本过程都是一样的。 其主要手段是向熔池吹入氧气(或加入矿石 )并加入造渣剂形成熔渣来去除原材 料中的杂质。因此只有 了解炼钢过程中熔池传氧和各种元素的反应规律,才能认识炼钢工艺操作的本
炼钢基本原理

炼钢基本原理
炼钢是指将生铁或钢水中的杂质和合金元素逐步除去,以获得符合规定化学成分和质量的金属材料的过程。
炼钢的基本原理是通过控制熔炼过程中的温度、氧化还原条件和流体动力学等因素,使金属中的杂质和合金元素发生物理化学变化,从而实现炼钢的目的。
首先,炼钢的原理是基于金属的化学性质。
在炼钢的过程中,通过控制熔炼温度和氧化还原条件,使金属中的氧化物、硫化物和氮化物等杂质得以去除。
同时,通过添加适量的合金元素,调整金属的化学成分,以满足不同用途的要求。
其次,炼钢的原理还涉及金属的物理性质。
在炼钢的过程中,通过控制金属的温度和流体动力学条件,使金属中的夹杂物和气体得以去除。
同时,通过合理的浇注和凝固工艺,调整金属的晶粒结构,提高金属的力学性能和加工性能。
此外,炼钢的原理还包括金属的热力学性质。
在炼钢的过程中,通过控制金属的熔化温度和熔化热量,实现金属的熔化和凝固。
同时,通过控制金属的过冷度和过热度,避免金属的结晶缺陷和组织偏析。
总之,炼钢的基本原理是通过控制金属的化学、物理和热力学性质,实现金属的净化和调整,从而获得符合规定化学成分和质量的金属材料。
在实际生产中,炼钢的原理是与炼钢的工艺、设备和操作密切相关的,需要综合考虑金属的成分、温度、流体动力学和热力学等因素,以实现炼钢的高效、节能和环保。
总的来说,炼钢基本原理是一个复杂而又精密的过程,需要工程师们在实际操作中不断积累经验和改进技术,以满足不同行业对金属材料的需求。
希望通过对炼钢基本原理的深入理解,能够为炼钢工艺的发展和提高提供一定的参考和帮助。
炼钢基础

一、炼钢基础理论1、常见的工业化炼钢方法有哪几类,各有什么特点?常见的工业化炼钢方法有转炉炼钢法、电弧炉炼钢法、平炉炼钢法(已被淘汰)。
各炼钢法的特点:2、转炉炼钢的历史:a.转炉炼钢法是1856年由英国人亨利.贝塞麦研究成功的;b.氧气顶吹转炉炼钢法是1952年和1953年在奥地利的林茨(Linz)和多纳维茨(Donawiz)两地首先投入工业生产,故命名LD。
C.1964年12月,我国第一座30吨的LD转炉在首钢投入生产。
3、高炉炼铁生产工艺流程是怎样的?高炉炼铁是一个还原工艺,主要原料为Fe2O3或Fe3O4含量高的铁矿石、烧结矿或球团矿以及石灰石(调节矿石中脉石熔点和流动性的熔剂),还有焦炭(做为热源、还原剂和料柱骨架)。
原料从炉顶分批加入,由高炉下部风口鼓入热风,焦炭燃烧生成高炉煤气。
炉内下降的炉料与上升的高炉煤气流相遇,水分蒸发,氧化铁与其它氧化物被还原。
铁中溶解大量碳,温度升高高熔炼成铁水和熔渣,每隔一段时间从铁口和渣口放出铁水和熔渣。
4、轧钢产品有哪几类?轧钢产品种类很多,规格不一,可分为板带材(热轧中厚钢板、冷轧薄板、带钢)、管材(无缝钢管、焊接钢管)、型材(角钢、槽钢、工字钢、螺纹钢、线材)。
5、常压下物质有哪几种形态?常压下,物质在微观上是以分子、原子、离子等形式存在,在宏观上是以固态、液态、气态3种状态存在。
6、什么是温度?温度是表征物体冷热程度的物理量。
以感觉判断温度会有偏差,比如在室温下用手摸金属和木材,感觉金属比木材凉些,实际上它们的温度是一样的。
从分子学运动论的观点来讲,温度是大量分子热运动平均动能的量度。
物体的温度越高,组成物体的分子平均动能也越大。
温度单位可采用国际温标或热力学温标。
日常生活中用的国际温标也叫摄氏温标,单位℃。
用符号(t)表示,热力学温标也叫开尔文温标,单位K,用符号T表示。
T=t+2737、什么是化学反应的热效应?热化学方程式怎样表示?一个化学反应的生成物和反应物温度相同时,反应过程中放出或吸收的热量称为化学反应的热效应,也称反应热。
炼钢基本原理
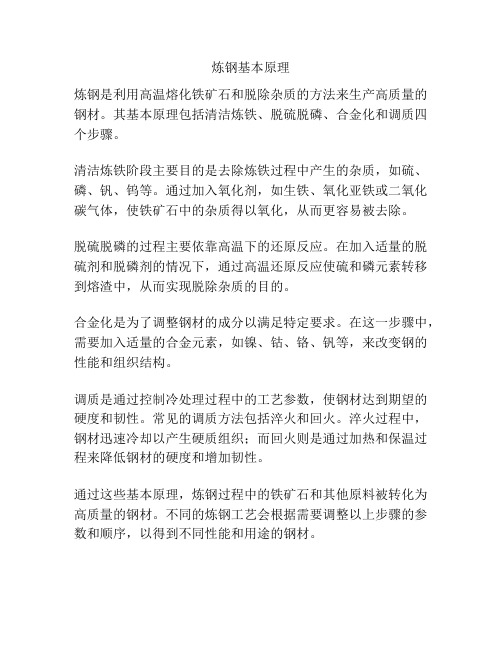
炼钢基本原理
炼钢是利用高温熔化铁矿石和脱除杂质的方法来生产高质量的钢材。
其基本原理包括清洁炼铁、脱硫脱磷、合金化和调质四个步骤。
清洁炼铁阶段主要目的是去除炼铁过程中产生的杂质,如硫、磷、钒、钨等。
通过加入氧化剂,如生铁、氧化亚铁或二氧化碳气体,使铁矿石中的杂质得以氧化,从而更容易被去除。
脱硫脱磷的过程主要依靠高温下的还原反应。
在加入适量的脱硫剂和脱磷剂的情况下,通过高温还原反应使硫和磷元素转移到熔渣中,从而实现脱除杂质的目的。
合金化是为了调整钢材的成分以满足特定要求。
在这一步骤中,需要加入适量的合金元素,如镍、钴、铬、钒等,来改变钢的性能和组织结构。
调质是通过控制冷处理过程中的工艺参数,使钢材达到期望的硬度和韧性。
常见的调质方法包括淬火和回火。
淬火过程中,钢材迅速冷却以产生硬质组织;而回火则是通过加热和保温过程来降低钢材的硬度和增加韧性。
通过这些基本原理,炼钢过程中的铁矿石和其他原料被转化为高质量的钢材。
不同的炼钢工艺会根据需要调整以上步骤的参数和顺序,以得到不同性能和用途的钢材。
冶金学基础理论之炼钢篇

2020/11/21
11
7)电弧
电炉是利用电弧产生的高温(其温度高达3000~8000℃)进行熔 炼金属的。
电弧是气体放电(导电)现象的一种形态。
气体放电的形式:按气体放电时产生的光辉亮度不同可分为: 无声放电—弱,辉光放电—明亮,电弧放电—炫目 三种 。
电弧产生过程:按直流讨论交流的瞬间见电路图5.18。从电炉操 作的表面现象看,合闸后,首先使电极与钢铁料做瞬间接触,而后 拉开一定距离,电弧便开始燃烧——起弧。
这样电极间隙中的带电质点数目会突然增加,并快速向两极移动, 气体导电形成电弧。——带电质点定向运动,形成电弧
电流方向由阳极向阴极,这一过程是在一瞬间完成的,电极与金
属料交换极性,电流以 50次/s 改变方向。
2020/11/21
13
图5.18 电弧产生过程示意图
2020/11/21
14
(2)电炉电控设备
冶金学基础理论之炼钢篇
主要内容
第一章 炼钢概述 第二章 炼钢基础理论 第三章 炼钢原材料 第四章 转炉炼钢法 第五章 电炉炼钢法
2020/11/21
2
第五章 电炉炼钢法之电炉设备 电炉设备的大小与分类; 电炉的机械结构:机械设备的组成及各部件名称,以
及结构特点; 电炉排烟与除尘:烟尘危害及限制,排烟方法与除尘
1)隔离开关
用以检修设备时断开高压电源(进线),为一无载刀形开关。
2)高压断路器(开关)
为电炉的操作开关。当电流过大时,断路器会自动跳闸切断电源, 以保护电源和电器,为一有载开关。
种类有油、空气、磁吹、SF6及真空断路器,后者使用广泛。
3)电抗器
Id
U r2 x2
串联在变压器一次侧,用来增加电路电抗值,以稳定电弧燃烧及
炼钢的基本原理

炼钢的基本原理炼钢是指将生铁或铁合金经过一系列物理和化学反应过程,消除杂质并调整成分,以制造出优质的钢材的过程。
它是钢铁生产的关键步骤之一、炼钢的基本原理涉及多个方面,包括原料选择、炉冶过程、炉渣控制和浇注技术等。
首先,原料选择是炼钢的关键之一、炼钢所使用的原料主要包括生铁、废钢、铁合金和盐酸等。
生铁是指通过高炉冶炼得到的铁水,其中含有很高的碳含量和其他杂质。
废钢具有较高的铁含量,可以作为原料直接投入到炼钢炉中。
铁合金主要用于调整钢材的成分,其中的一些合金元素可以提高钢材的特性。
其次,炉冶过程是炼钢的核心。
炼钢的主要方法包括转炉法、电炉法和平炉法等。
其中,转炉法是最常用的方法之一、在转炉法中,将预先加热的钢水加入到转炉中,并通过喷吹氧气来氧化和燃烧炉中的碳和其他杂质。
氧气的喷吹可以提高炉温和混合物的搅拌效果,以加快反应速度。
通过不断调整喷吹氧气的量和位置,可以控制钢水的成分和温度。
同时,炉渣控制也是炼钢过程中的重要环节。
炉渣是由氧化矿物、渣料等组成的物质,它在炼钢过程中扮演着重要的角色。
炉渣对于钢水的温度和成分具有一定的调节作用。
当炉渣中的氧化剂过多时,会导致钢材表面氧化过度。
而当炉渣中的还原剂过多时,会导致钢材中夹杂物的增加。
因此,通过控制炉渣的成分和熔化温度,可以有效地控制钢材的质量。
最后,浇注技术也是炼钢过程中需要注意的问题。
在进行炼钢过程中,需要将炉内的钢水倒入坯料模具中进行冷却和成形。
浇注时,需要控制好倾倒的速度和角度,以避免产生不均匀的应力和缺陷。
同时,在冷却过程中,也需要控制好温度和冷却速度,以保证钢材的内部组织和性能。
总之,炼钢的基本原理包括原料选择、炉冶过程、炉渣控制和浇注技术等方面。
通过合理的原料选择和炉冶方法,控制好炼钢过程中的各个环节,可以生产出质量优良的钢材。
炼钢作为钢铁生产的核心环节之一,对于提高钢材的质量和性能具有重要意义。
炼钢基本原理概述
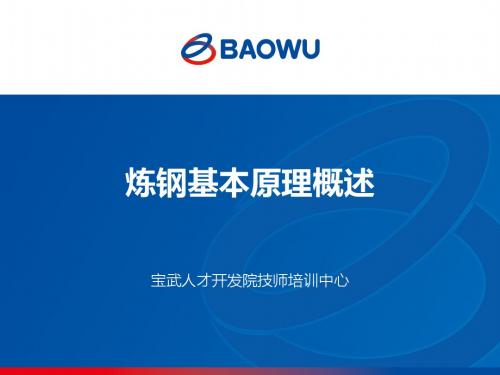
转炉和电炉的炉渣成分和性质
类别 化学成分 CaO+FeO+MnO SiO2 P2O5 CaO/SiO2 CaO FeO MnO MgO 转炉中组成% 50 50 1- 4 3.0-4.5 35-55 7-30 2- 8 2-12 电炉中组成% 50 50 冶金反应特点 [C],[Si],[Mn]氧化缓慢 不能脱P、脱S; 钢水中[O]较低 [C],[Si],[Mn]迅速氧化 能较好脱P; 能脱去50%的S; 钢水中[O]较高。
炼钢基本原理概述
宝武人才开发院技师培训中心
转炉发展
渣钢反应 与泡沫渣
炼钢炉渣 性质
转炉吹炼 过程中炉 渣成分的 变化
瑞典人罗伯特·杜勒首先进行了氧气顶吹转炉炼钢的试验 ,并获得了成功。1952年奥地利的林茨城(Linz)和多纳维 兹城(Donawitz)先后建成了30吨的氧气顶吹转炉车间并投 入生产,所以此法也称为LD法。 美国称为BOF法(Basic Oxygen Furnace)或BOP法。
熔化温度
粘度 表面张力 炉渣碱度 炉渣氧化性
渣钢反应()与[]
脱硅:硅的氧化非常迅速,在吹炼前期所有的硅就已反应完毕并进入渣 中。[Si]+2[O]=SiO2 脱磷和脱硫:为了得到低硫、磷含量的钢,磷硫去除需要严格控制炉渣 形成结构和终渣成分。 [FeS]+(CaO)=(CaS)+[FeO] [S]+(O2-)=[O]+(S2-)
LD/ BOF/ BOP
自供热转炉的发展演变过程
请看flash
炼钢炉渣
炉渣是炼钢过程的必然产物。炉渣的来源有:
金属炉料中各元素氧化所形成的氧化物; 废钢带入的泥沙和铁锈等; 氧化剂或冷却剂(铁矿石、烧结矿等)带入的脉石; 被侵蚀的炉衬耐火材料以及加入的各种造渣材料 ( 石灰或石灰石、铁 矾土、萤石、废火砖块等)。
炼钢工艺基础理论
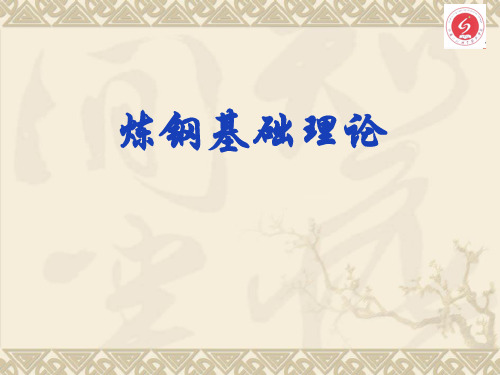
❖ 平衡时
❖
KP=f2
(4CaO P2O5) w2 [P] 5 (FeO) 4 (CaO)
脱磷反应的条件:三高一低,低温、高碱度、 高(FeO)、大渣量。
❖ (1)低温。是保证早化渣的低温,所以冶炼前期 还要快速提温。
❖ (2)高碱度必须保证炉渣有合适的粘度; ❖ (3)大渣量,是参加反应的渣量大,但炉内渣量不
2 硅的氧化与还原
炼钢所用原料铁水和废钢中含有一定数量的硅和锰, 而且二者与氧的亲和力均较大(大于C-O)。因此,无 论是在电炉冶炼中还是在转炉吹炼中都会发生硅、锰的 氧化反应。
(1)硅氧化的特点 ①在任何炼钢操作中,硅在前期大量氧化,速度快。 ②硅的氧化是强放热反应 ③转炉炼钢中,硅含量高,对脱碳反应有抑制作用。 ④在酸性炼钢法中,硅可以还原。
[Mn]+1/2{O2}=(MnO) △G0=-58400+25.98T J/mol (较强放热)
(3)锰的氧化特点
生产中,铁水中锰的氧化具有如下两个特点:
①锰的氧化反应发生在冶炼初期 由上式可见,锰的间接氧化和直接氧化也都是放热反
应,因此锰的氧化反应也是在冶炼的初期进行的。不过 因氧化过程中放热较少,氧化的激烈程度远不及硅。
(2)硅的氧化反应式
在炼钢过程中,硅的氧化方式主要是间接氧化: [Si]+2(FeO)=(SiO2)+2Fe
△G0=-81500+28.53T J/mol (较强放热) 直接向熔池吹氧时,炉料中的硅还会被氧气直接氧化一 部分,其反应式如下:
[Si]+{O2}=(SiO2) △G0=-139300+53.55T J/mol(强放热)
生铁和钢都是以Fe为溶剂,C、Si、Mn、S、P等 为溶质的一种金属溶液,二者在性能上只所以会有这 样大的差别,其根本原因是它们的溶质元素含量不同, 见表1-1。
钢铁冶金学(炼钢学)PPT课件

36
1.3.4 钢中的气体
钢液中的气体会显著降低钢的性能,而且容易 造成钢的许多缺陷。钢中气体主要是指氢与氮, 它们可以溶解于液态和固态纯铁和钢中。 氢在固态钢中溶解度很小,在钢水凝固和冷却 过 程 中 , 氢 会 和 CO 、 N2 等 气 体 一 起 析 出 , 形 成皮下气泡中心缩孔、疏松、造成白点和发纹。
完整编辑ppt
11
炼 钢 方 法(6)
瑞典人罗伯特·杜勒首先进行了氧气顶吹 转炉炼钢的试验,并获得了成功。1952 年奥地利的林茨城(Linz)和多纳维兹城 (Donawitz)先后建成了30吨的氧气顶吹 转炉车间并投入生产,所以此法也称为
LD法。美国称为BOF法(Basic Oxygen Furnace)或BOP法。
完整编辑ppt
23
1.3.1 钢中的磷
对于绝大多数钢种来说磷是有害元素。钢中磷的 含量高会引起钢的 “冷脆”,即从高温降到0℃ 以下,钢的塑性和冲击韧性降低,并使钢的焊接 性能与冷弯性能变差。
磷是降低钢的表面张力的元素,随着磷含量的增 加,钢液的表面张力降低显著,从而降低了钢的 抗裂性能。
完整编辑ppt
完整编辑ppt
39
钢中加入适量的铝,可生成稳定的AlN,能够 压抑Fe4N生成和析出,不仅改善钢的时效性, 还可以阻止奥氏体晶粒的长大。氮可以作为合 金元素起到细化晶粒的作用.在冶炼铬钢,镍铬 系钢或铬锰系等高合金钢时,加入适量的氮, 能够改善塑性和高温加工性能。
完整编辑ppt
40
1.3.5 钢中的夹杂
完整编辑ppt
16
LD- Q- BOP
完整编辑ppt
17
炼 钢 方 法(9)
我国首先在 1972-1973 年 在沈阳第一炼钢 厂成功开发了全 氧侧吹转炉炼钢 工艺。并在唐钢 等企业推广应用。
冶金工程概论炼钢基本原理up讲解

6.3 炼钢过程的基本反应
? 炼钢熔池中氧的来源
氧的来源主要有三种形式: ⑴直接向熔池中吹入工业纯氧(含O2≥98%); ⑵是向熔池中加入富铁矿; ⑶是炉气中的氧传入熔池。
? 铁液中元素的氧化方式:直接氧化与间接氧化
(1)直接氧化
O2=2[O] 氧气与金属液直接接触,气体氧分子分解并吸附在铁液表面:
? 硅的氧化
在炼钢金属料—铁水和废钢中,均含有一定数量的Si,在铁液中有无限溶 解度,它与铁的稳定化合物为FeSi,在炼钢温度下Si可氧化成稳定的化合 物SiO2。 硅和氧的亲和力很强,在吹炼初期就大量氧化。在吹炼初期.一般在5min 以内就被氧化到很低。一直到吹炼终点,也不发生硅的还原。生成的SiO2 进入渣中:
[FeO]=[O]+[Fe] [O]+[Me]=(MeO) 吹入熔池中的气体氧,一部分溶入金属,一部分与杂质元素 反应,一部分则以FeO形式进入炉渣。
特别指出:当金属液不与炉气中的气态氧直接接触或接触很少时,如 在平炉,电炉及氧气顶吹转炉高枪位操作时的情况。这时气态氧主要 通过炉渣传入金属: 首先气—渣界面的FeO被氧化成高价氧化铁:
1)夹杂物来源 脱氧脱硫等反应产物、炉渣及耐火材料、杂质元素析出非金属夹杂物等。 2)夹杂物分类(根据化学成分分类)
(1)氧化物夹杂 简单氧化物:FeO、MnO、SiO2、A12O3、Cr2O3等。 复杂氧化物: FeO-Fe2O3、FeO-A12O3、MgO-A12O3、2FeO-SiO2、2MnO-SiO2、
? 脱氧 来源:炼钢是氧化还原过程。在吹炼过程中,向熔池吹入 了大量的氧气,到吹炼终点,钢水中含有过量的氧。 危害:如果不进行脱氧,将影响其后的浇注操作。而且在 钢的凝固过程中,氧以氧化物的形式大量析出,钢中也将 产生氧化物非金属夹杂,降低钢的塑性和冲击韧性,使钢 变脆。为此,要将钢水按不同钢种要求脱氧。
第3章基本理论

第三章理论基础第一节脱碳反应一.脱碳反应对炼钢的影响炼钢的主要任务之一,就是要把熔池中的碳降低到钢种要求的范围内,因此脱碳反应是炼钢过程中的一个主要反应。
由于碳的蒸汽压不大,它不能从溶液中汽化而去除(即使在真空条件下)。
在冶炼过程中,脱碳反应是通过C、O反应来实现的。
同时,脱碳反应对炼钢过程有多方面的影响:(1)降低熔池中〔C〕含量:反应使熔池中〔C〕含量降低,达到钢种出钢要求;(2)搅拌熔池,均匀熔池温度和成分:CO气体逸出,对熔池形成激烈搅动;(3)促使形成乳化液和泡沫渣:CO气体产生泡沫渣和气—渣—金属三相乳化,对冶炼过程产生重大影响。
(4)清除杂质,改善钢水质量:上浮的CO气体有利于清除钢中气体,并带动夹杂物的聚集和上浮,从而提高钢的质量。
(5)影响熔池温度:吹氧脱碳可以提高熔池内钢水温度;而矿石脱碳,由于矿石的升温和溶解是吸热过程,致使整体上为吸热过程(矿石是一种“冷却剂”)。
(6)导致吹炼过程中的喷溅:CO气体溢出形成泡沫渣并造成熔池上涨,形成喷溅。
二.碳在熔铁中的溶解1.溶解性碳的熔点很高(3500℃),在冶炼温度下不熔化。
但是,能够在钢水中溶解。
P77反应式4,5,在1%C、1300~1800℃的情况下,00∆=∆<。
G G2.溶解度(1)Fe-C二元系:碳在铁中属于有限溶解,P78给出了计算公式。
当1500℃时,C的溶解度为5.15%,而实际上因受其它元素的影响,溶解度有所改变。
(2)多元系(其它元素的影响)通过相互作用系数,铁水中的其它元素会影响C在铁中的溶解度。
在常见元素中,Si、P、S等降低C的溶解度,而Mn、Cr、V等则增加碳的溶解度。
①铁水:一般生铁中为4%左右,高磷生铁3.6%左右,Si高时含碳量下降。
② 合金:FeMn 中C 可以达到7%,FeSi 中几乎不含碳,MnSi 中%C 介于两者之间。
如P78图3-21,P25表2-16所示。
③ 钢水:含Cr 、Mn 较高时,C 的活度系数减小,在浇注和精炼过程中应防止增C 。
4-炼钢基础理论-4

2019/11/18
东北大学/阎立懿
23
S、O是很强的表面活性物质,只要含有很少量的S、 O就能使钢液的表面张力大大下降 。原因是它们在钢 液中的生成物FeS、Fe0被排挤到钢液的表面,浓度出 现偏差,导致表面张力急剧下降。
2019/11/18
东北大学/阎立懿
24
Ni 、 Co 影 响 较 小 , 原 因 是与铁的性质相近;
2019/11/18
东北大学/阎立懿
16
影响钢液黏度因素主要是温度和成分。 温度影响 随温度升高黏度降低,即流动性变好。这是由于温度 升高钢液密度降低、原子间距离增大、相互吸引力减小。 成分影响 成分对钢液黏度影响比较复杂! 碳 钢液中的碳对黏度的影响非常大,这主要是因为 碳含量使钢的密度和熔点发生变化,从而引起黏度的变化。
但当碳含量0.15~0.40
范围时,钢液中存在
δ-Fe、γ-Fe两种晶体结
构(体心立方——面心
立方),密度是随碳含
量的增加而增加,表面
张力增加。
2019/11/18
东北大学/阎立懿
26
5)钢的导热能力
钢的导热能力可用导热系数或热导率来表示,指在 稳定传热条件下,1m厚的材料,两侧表面的温差为1℃, 在1s内,通过1m2面积传递的热量,即当体系内维持单位 温度梯度时,在单位时间内流经单位面积的热量,钢的 导热系数用符号λ表示,导出单位为W/(m·℃)。
2019/11/18
东北大学/阎立懿
21
影响钢液表面张力的因素很多,主要有温度、成分 及钢液接触物,其中影响最大的还是钢液成分。
温度影响
对于一般液体温度升高、表面张力减少,但对于碳 素钢液来说,表面张力是随着的温度升高而增大。原因 之一是温度升高表面活性物质,如C、O等的热运动增强, 使钢液表面过剩浓度减小或浓度均匀化,从而引起表面 张力增大。这也可从成分影响得到解释。
炼钢的基本原理知识总结

炼钢的基本原理知识总结炼钢先炼铁。
钢从生铁而来。
用铁矿石冶炼而得的生铁,含碳量较高,而且含有许多杂质(如硅、锰、磷、硫等)。
因此,生铁缺乏塑性和韧性,力学性能差,除熔化浇铸外,无法进行压力加工,因而限制了它的用途。
为了克服生铁的这些缺点,使它在工业上能起到更大的作用,还必须在高温下利用各种来源的氧,把生铁里面的杂质氧化清除到一定的程度,以得到一定成分和一定性质的铁碳合金——钢。
这种在高温下氧化清除生铁中杂质的方法叫炼钢。
炼钢的基本原理生铁中的各种杂质,在高温环境下,不同程度上都与氧有较大的亲和力。
因此可以利用氧化的方法使它们成为液体、固体或气体氧化物,液体和固体氧化物在高温下与炉衬和加入炉内的熔剂进行反应,结合成炉渣,并在扒渣时被排除炉外,气体也在钢水沸腾时被CO带到炉外。
在炼钢炉内,杂质的氧化主要是依靠FeO的存在而实现的。
2Fe+O2→2FeO01硅元素的氧化硅与氧有较大的亲和力,因此硅的氧化很迅速,它在冶炼初期就已经完全被氧化而生成SiO2:Si+2FeO→SiO2+2Fe同时SiO2又和FeO反应形成硅酸盐:2FeO+SiO2→2FeO·SiO2这种盐是炉渣中很重要的一部分,它与CaO作用生成稳定化合物2CaO·SiO2和FeO,前者牢固存在于炉渣中,后者变成了渣中的游离成分,使渣中FeO的含量增加,对促进杂质的氧化是比较有利的。
其反应如下:2FeO·SiO2+2CaO→2CaO·S iO2+2FeO02锰元素的氧化锰也是易氧化的元素,它所生成的MnO有较高的熔点,MnO在金属液中并不溶解,但是它与SiO2形成化合物浮在液体金属表面,成为炉渣的一部分。
Mn+FeO→MnO+Fe2MnO+SiO2→2MnO·SiO2硅、锰的氧化反应放出大量的热,可以使炉温迅速提高(这一点对转炉炼钢特别重要),大大加速了碳的氧化过程。
03碳元素的氧化碳的氧化需要吸收大量的热能,所以必须在较高的温度下才能进行。
炼钢基本原理及原材料课件
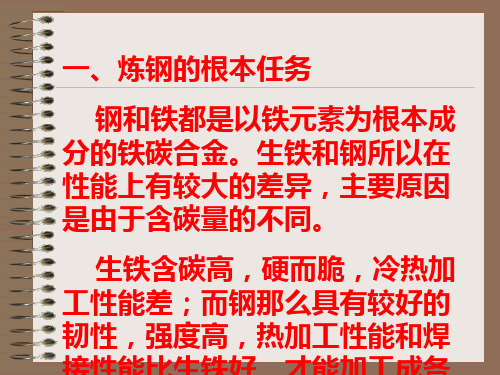
低温虽然对脱磷有利,但温度过低,那么石灰不 易熔化,碱性渣不易形成,炉渣粘度高,炉渣中各 组分的扩散困难,反而对脱磷不利。
正硅酸钙很稳定,故在碱性渣中,冶炼前期硅几乎全 部被氧化,而不会再被复原。
锰的氧化与复原
锰在钢中以MnO、MnS等形式 存在。锰在钢中也是一种有益的元 素,它可以防止钢的热脆,提高钢 的强度、硬度、可锻性等机械性能。 另外锰在炼钢中还起着脱氧剂和脱 硫剂的作用。锰在铁液中有无限的 溶解度,无论在碱性操作过程或酸 性操作过程中都容易被氧化,其氧
炼好钢首先要炼好渣,所有炼钢任务的 完成几乎都与熔渣有关。熔渣的结构决定 着熔渣的物理化学性质,而熔渣的物理化 学性质又影响着炼钢的化学反响平衡及反 响速率。因此,在炼钢过程中必须控制和 调整好炉内熔渣的物理化学性质。
炉渣组成:
主要成分:CaO、 SiO2、Fe2O3、FeO、 P2O5、CaS 等以及一些复杂化合物。
辅助材料
造渣材料 氧化剂
✓ 石灰〔CaO〕 ✓ O2 ✓ 白云石〔MgO〕✓ 铁矿石 ✓ 萤石〔CaF2〕 ✓ 氧化铁皮
冷却剂
➢ 废钢 ➢ 富铁矿 ➢ 氧化铁皮 ➢ 石灰石
三、炼钢炉渣
炉渣是炼钢过程的必然产物。
炉渣的来源: 有意参加的造渣材料;金属炉
料中各元素氧化所形成的氧化 物;废钢带入的泥沙和铁锈等; 铁矿石、烧结矿等带入的脉石; 被侵蚀的炉衬耐火材料以及参 加的各种造渣材料(石灰或石灰
在高炉冶炼中,由于炉内的复原性气氛,矿石中的磷 几乎全部进入铁水,因而从金属中脱除磷,乃是炼钢过 程的重要任务,造渣的目的之一就是为了脱磷。
炼钢的脱磷反响是在金属和炉渣的界面上进行的,其 反响式为:
2 [P] + 5(FeO) = (P2O5) + 5 [Fe]
炼钢理论基础(炼钢工艺)

[C]+O2=CO2 [Si]+O2=(SiO2)
[Mn]+1/2O2=(MnO)
2[P]+5/2O2+3(CaO)=(3CaOP2O5)
Fe+1/2O2=(FeO)
[S]+(CaO)=(CaS)+[O]
24
炼钢工序功能的演变
基本任务
1) 脱碳; 2) 升温; 3) 脱磷;
45
一、脱碳反应的热力学条件 直接氧化:
{O2} + 2[C] = 2{CO} G=-275044-83.64 T[1,2] {O2} + [C] = {CO2} G=-416328+41.8 T[1,2]
[1]Reed Thomas, Free Energy of Formation of Binary Compounds, MIT Press, 1971 [2]J.F. Elliott, Thermochemistry for Steelmaking, Vol.2, Addison-Wesley 1963
10
耐火材料融损及 卷入
炼钢任务:
9)凝固成型
11
炼钢的基本任务:
1、脱碳; 2、脱磷; 3、脱硫; 4、脱氧; 5、脱氮、氢等; 6、去除非金属夹杂物; 7、合金化; 8、升温; 9、凝固成型 。
12
主要炼钢工艺: 铁水预处理; 转炉或电弧炉炼钢; 炉外精炼(二次精炼); 连铸。
13
40
也可以表示为:
(FeO) + [Mn] = (MnO) + (Fe) 2 (FeO) + [Si] = (SiO2) + 2(Fe)
5 (FeO) + 2[P] = (P2O5) + 5(Fe)
(FeO) + [C] = {CO} + (Fe) 2 (FeO) + [C] = {CO2} + 2(Fe)
- 1、下载文档前请自行甄别文档内容的完整性,平台不提供额外的编辑、内容补充、找答案等附加服务。
- 2、"仅部分预览"的文档,不可在线预览部分如存在完整性等问题,可反馈申请退款(可完整预览的文档不适用该条件!)。
- 3、如文档侵犯您的权益,请联系客服反馈,我们会尽快为您处理(人工客服工作时间:9:00-18:30)。
7.05
7.01
6.97
6.83
0.60
6.97
6.89
6.84
6.80
6.70
0.80
6.86
6.78
6.73
6.67
6.57
1.00
6.78
6.70
6.65
6.59
6.50
1.20
6.72
6.64
6.61
6.55
6.47
1.60
6.67
6.57
6.54
6.52
6.43
二、钢的熔点
指钢完全转变成均一液体状态时的温度,或是冷凝时开 始析出固体的温度。钢的熔点是确定冶炼和浇铸温度的重 要参数,纯铁的熔点约为1538℃,当某元素溶入后,纯 铁原子之间的作用力减弱,铁的熔点就降低。降低的程度 取决于加入元素的浓度、原子量和凝固时该元素在熔体与 析出的固体之间的分配。
黏度是指各种不同速度运动的液体各层之间所产生的 内摩擦力。通常将内摩擦系数或黏度系数称为黏度。
黏度表示形式
动力黏度,用符号µ表示;单位为Pa•s (N•s/m2, 1泊=0.1Pa•s);
运动黏度,常用符号ν表示,即:
m2/s
钢液的黏度比正常熔渣的要小得多,1600℃ 时其值在0.002~0.003Pa•s;
或 T熔=1536-78[%C]-7.6[%Si]-4.9[%Mn]-
34[%P]-30[%S]-5.0[%Cu] -3.1[%Ni]1.3[%Cr]-3.6[%Al]-2.0[%Mo]-2.0[%V] -18[%Ti]
三、钢液的黏度
黏度是钢液的一个重要性质,它对冶炼温度参数的制 定、元素的扩散、非金属夹杂物的上浮和气体的去除以及 钢的凝固结晶都有很大影响。
钢液中非金属夹杂物含量增加,钢液黏度增加, 流动性变差。
初期脱氧产物生成,夹杂物含量高,黏度增大, 夹杂物不断上浮或形成低熔点夹杂物,黏度又 下降。脱氧不良,钢液流动性一般不好。
常用流动性来表示钢液的黏稠状况,黏度的倒 数即为流体的流动性。
四、钢液的表面张力
钢液因原子或分子间距非常小,其间的吸引力较强,而且 钢液表面层和内部所引起的这种吸引力的变化是不同的。
第二章 炼钢的基础理论
第一节 钢液的物理性质 第二节 熔渣的物理化学性质 第三节 硅、锰的氧化和还原反应 第四节 碳的氧化反应 第五节 钢液的脱硫 第六节 钢液的脱磷 第七节 钢液的去气 、去夹杂
第一节 钢液的物理性质
一、钢的密度 单位体积钢液所具有的质量,常用符号ρ表示,
单位通常用kg/m3。影响钢液密度的因素主要有 温度和钢液的化学成分。
纯铁液1600℃时黏度为0.0005Pa•s。
影响钢液黏度因素主要是温度和成分。温度 升高,黏度降低。钢液中的碳对黏度的影响非常大, 这主要是因为碳含量使钢的密度和熔点发生变化, 从而引起黏度的变化。
生产实践也表明,同一温度下,高碳钢的流动性 比低碳钢钢液的好。因此,一般在冶炼低碳钢中, 温度要控制得略高一些。碳含量对钢液黏度的影响 见下图。
内部每一质点所受到的吸引力的合力等于零,质点保持平 衡状态;
而表面层质点受内部质点的吸引力大于气体分子对表面层 质点的吸引力,这样表面层质点所受的吸引力不等于零, 且方向指向钢液内部。
这种使钢液表面产生自发缩小倾向的力称为钢 液的表面张力,用符号σ表示,单位为N/m。 实际上,钢液的表面张力就是指钢液和它的饱 和蒸气或空气界面之间的一种力。
钢液的表面张力 对新相的生成如CO气泡的产生,钢液凝固过程中结
晶核心的形成等有影响; 对相间反应,如脱氧产物的、夹杂物和气体从钢液中
排除,渣钢分离,钢液对耐火材料的侵蚀等也有影响。 影响钢液表面张力的因素很多,但主要有温度、钢液
成分及钢液的接触物。
钢液的表面张力是随着温度的升高而增大,原因之 一是温度升高时表面活性物质如C、O等热运动增 强,使钢液表面过剩浓度减少或浓度均匀化,从而 引起表面张力增大。
温度高于液相线50℃时,碳含量对钢液黏度的影响
当[%C]<0.15时,黏度随着碳含量的增加而大幅度下降, 主要原因是钢的密度随碳含量的增加而降低;
当0.15≤[%C]<0.40时,黏度随碳含量的增加而增加, 原因是此时钢液中同时存在δ-Fe和γ-Fe两种结构,密度 是随碳含量的增加而增加,而且钢液中生成的Fe3C体积 较大;
铁碳熔体的密度(kg/m3)
[C] (%)
1500℃
1550℃
密度
1600℃
1650℃
1700℃
0.00
7.46
7.04
7.03
7.00
6.93
0.10
6.98
6.96
6.95
6.89
6.81
0.20
7.06
7.01
6.97
6.93
6.81
0.30
7.14
7.06
7.01
6.98
6.82
0.40
7.14
当[%C]≥0.40时,钢液的结构近似于γ-Fe排列,钢液密 度下降,钢的熔点也下降,故钢液的黏度随着碳含量的 增加继续下降。
Si、Mn、Ni使钢的熔点降低,Si、Mn、 Ni含量增加,钢液黏度降低,尤其含量很 高时,降低更显著。
但Ti、W、V、Mo、Cr含量增加则使钢液 的黏度增加,这些元素易生成高熔点、体 积大的各种碳化物。
总的来讲,温度升高,钢液密度降低,原因在于 原 子 间 距 增大 。 固体 纯 铁密 度 为 7880kg/m3 , 1550℃时液态的密度为7040kg/m3,钢的变化与 纯铁类似。
钢液密度随温度的变化: ρ=8523-0.8358(T+273)
成分对钢液密度的影响: ρ1600℃=ρ01600℃-210[%C]-164[%Al]60[%Si]-550[%Cr]-7.5[%Mn] + 43[%W]+6[%Ni]
各元素使纯铁熔点的降低可表示为:
1020 Mi
(1
) [%i]液
Mi为溶质元素i的原子量; [%i]液为元素i在液态铁中的质量百分数; K为分配系数,而K=[%i]固/[%i]液,(1-K)则 称为偏析系数。
计算钢的熔点经验式:
T熔=1538-90[%C]-28[%P]-40[%S]-17[%Ti]6.2[%Si]-2.6[%Cu]-1.7[%Mn]-2.9[%Ni]5.1[%Al]-1.3[%V]-1.5[%Mo]-1.8[%Cr] -1.7[%Co]-1.0[%W]-1300[%H]-90[%N]100[%B]-65[%O]-5[%Cl]-14[%As]