白车身及车身骨架结构设计要求
白车身设计规范

白车身设计规范白车身设计规范一、冲压件设计规范1.孔1.1钣金上的冲孔设计要与钣金冲压方向一致。
1.2孔的公差表示方法1.3过线孔1.3.1过线孔翻边1.3.1.1过线孔翻边至少要3mm高。
此翻边对钣金起加强作用,防止在安装过程中产生变形,从而影响此孔的密封性。
1.3.1.2如果通过过线孔的零件是面积≤6的固体,或者钣金足够厚,使其在不借助翻边时也能够承受住过线孔安装时的压力,那么此过线孔可以不翻边。
1.3.2过线孔所在平面尺寸1.3.2.1过线孔为圆孔(半径设为Rmm)时,孔周圈的平面半径应为(R+6)mm1.3.2.2过线孔为方孔时,孔周边的平面尺寸应比孔各边尺寸大6mm。
1.4法兰孔1.4.11.5排水孔1.5.1排水孔设计在车身内部空腔的最低处,其直径一般为6.5mm。
1.5.2对于车身内部加固的防撞梁,应同样在其空腔的最低处布置排水孔。
1.5.3在车身结构件的空腔及凹陷处必须布置排水孔。
1.6空调管路过孔1.8管道贯通孔2.圆角3.边3.1密封边3.1.1行李箱下端3.1.1.1.为了使水排出止口,如图所示需要留出3.0mm的间隙。
3.1.1.2安装用止口应该具备恒定的高度和厚度(用于弯角的凸缘除外)。
3.1.1.3车门开口周围的止口厚度变化,包括制造变差的范围通常在1.8mm至6.0mm之间。
厚度的极端值会产生较高的插入作用力和密封条稳定性等问题。
3.1.1.4止口厚度的变化在任何位置不得超过一个金属板的厚度。
如果可能,仅可以使垂直的止口产生厚度变化,绝对不要使弯角半径产生厚度变化。
止口厚度的阶段变化会使密封条托架中的水渗漏。
3.1.1.5应该避免带有焊点的止口出现燃油和其它润滑油,这些物质会降低稳定性。
3.1.1.6止口结构类型及其优缺点3.1.2行李箱上端为了防止水从密封条止口泄漏并且进入行李舱,可按下面结构进行设计:3.1.2.1支架内的胶黏料或可发泡的热熔胶需符合漏水防止设计手册。
白车身BVS设计规范

白车身BVS设计规范白车身BVS设计规范1范围本标准规定了汽车白车身BVS设计规范。
2规范性引用文件卜冽文件对于本文件的应用是必不可少的。
凡是注口期的引用文件,仅所注日期的版本合用于本文件。
凡是不注口期的引用文件,其最新版本(包括所有的修改单)合用于本文件。
GB/T 1. 1-2022标准化工作导则第1部份:标准的结构和编写3术语和定义卜列术语和定义合用于本标准。
3.1整车尺寸技术规范Vehicle dimension technicaI specifications整车尺寸技术规范简称整车DTS,是根据市场调研、市场竞争车型最优信息、用户要求以及创造过程中反馈的信息,确定市场定位、满足用户需求,对车辆外观(外部和内部)质量一一订视零部件之间的间隙、面差、平行度、对齐性、一致性以及装配关系等要求作出的规定。
整车DTS是整车技术规格(VTS)中重要的组成部份,是统-、规范新开辟车型在概念设计、工程设计、工程样车试制、供应商管理、工艺工装开辟、产品质量管理、试生产、批量穩定生产及售后服务等整个新产品车型全生命周期各阶段的技术文件。
3.2白车身BVS Body vehicle spec i f icat ions指从车身调整线卜线的白车身的尺寸技术规范。
4白车身BVS组成白车身BVS主要用于描述白车身零部件之间的间隙和面差的相互关系,通常表示的方式如下:间隙(或者面差)设计名义值+间隙(或者面差)公差要求。
按白车身部位划分,白车身BVS主要包含以下内容:a)前脸区域:翼子板与大灯开II检具间隙面差、翼子板与发动机盖间隙而差:b)侧脸区域:前门周圈区域间隙面差、后门周圏区域间隙面差:c)后脸区域:尾门与后大灯开II检具间隙面差、尾门与侧围、顶盖间隙而差;d)内间隙:前门与侧围胶条密封面间隙、后门与侧围胶条密封而间隙、尾门与侧围胶条密封面间隙。
5白车身BVS影响因素白车身BVS主要有以下影响因素:a)车门重力卜垂引起的车门旋转:b)车门密封胶条推力引起的车门的面差变化;c)其他因装配总装件所带来的尺寸变化。
白车身专业知识(车身设计规则)

白车身设计规则1.基本原则1.1 白车身设计是一个复杂的系统并行设计过程,要彻底地摒弃孤立地单个零件设计方法,任何一个零件只是其所处在的分总成的一个零件,设计时均应考虑其与周边相关零部件的相互关系。
(我们参考一下侧围、车架总成)1.2 任何一种车型的白车身结构均可按三层板的设计思想去构思结构设计,即最外层是外板,最内层是内板,中间是加强板,在车身附件安装连接部位应考虑设计加强板。
(比如侧围、前罩板总成)1.3 所设计的白车身结构在满足整车性能上、结构上、冲压工艺、焊接工艺、涂装工艺、总装工艺是否比参考样车或其他车型更优越,是否符合国内(尤其是客户)的实际生产状况,以便预先确定结构及工艺的改良方案。
1.4 白车身在结构与性能上应提供车身所需的承载能力,即强度和刚度要求。
2.白车身钣金的材料选取原则汽车覆盖件所用材料一般是冷轧钢板。
2.1按国家标准选取钣金材料2.1.1钣金按表面质量分有I,II两级:I级质量最好,适用于外板;II级次之,适用于内板与加强板。
2.1.2钣金按冲压拉延等级分有P,S,Z,F,HF,ZF六级P:普通拉深级,适用于拉延深度浅的零件;S:深拉深级,适用于拉延深度一般的零件;Z:最深拉深级,适用于拉延深度较深的零件;F:复杂拉深级,适用于结构复杂且拉延深度较深的零件;HF:很复杂拉深级,适用于结构较复杂且拉延深度较深的零件;ZF:最复杂拉深级,适用于结构非常复杂且拉延深度较深的零件;2.1.3钣金按强度等级分有:普通强度,高强度,超高强度高强度和超高强度钢板按其强化机理分为:固溶强化、析出强化、组织强化,复合组织强化、热处理硬化型强化、相变强化、冷作强化、时效强化等。
高强度钢板的强化机理定义:固溶强化利用固溶铁中原子产生的格子变形的强化机理。
析出强化使Ti、Nb、V等的碳化物和氮化物以细小的形态析出,由于这些析出物,位错活动受到阻碍,据此形成强化的机理。
组织强化利用将钢从高温的奥氏体急冷时生成硬质的马氏体和贝氏体的强化机理。
白车身车架和车身连接分析标准

车架和车身连接缓冲垫总成
1. 车架和车身连接缓冲垫II总成通过六角头法兰螺栓和平垫圈组合件、二层铁垫圈III、螺母紧固。
其中六角头法兰螺栓和平垫圈组合件、二层铁垫圈III需在车身钣金过孔穿入,垫片直径76mm,车身钣金过孔直径40mm,垫片无法安装,且垫片与车身钣金贴合面是曲面,无法贴合;螺栓自带平垫直径为38mm,车身钣金过孔直径40mm,综合零部件加工及焊接误差,螺栓存在无法装配的风险
对策:1.标准件是六角头法兰螺栓和平垫圈组合件,建议取消二层铁垫圈III,车身钣金过孔尺寸至少44mm,保证螺栓的正常装配。
2. 车架和车身连接缓冲垫II总成通过螺栓、螺母配合。
员工紧固螺母时,需要另一个人使用工具固定螺栓,两个人的配合作业降低生产节拍且操作不便
对策:建议参考车架和车身连接缓冲垫I总成(图一)或车架和车身连接缓冲垫Ⅲ总成(图二)调整车身钣金和螺栓结构,或采用其它形式,防止紧固螺母的过程中,螺栓出现转动。
3. 车架和车身连接缓冲垫I、II、Ⅲ总成均需铁垫圈,单侧6个铁垫圈为6种不同的型号。
员工装配时,易出现错装现象
对策:建议将所有铁垫圈的结构统一。
汽车白车身结构设计规范
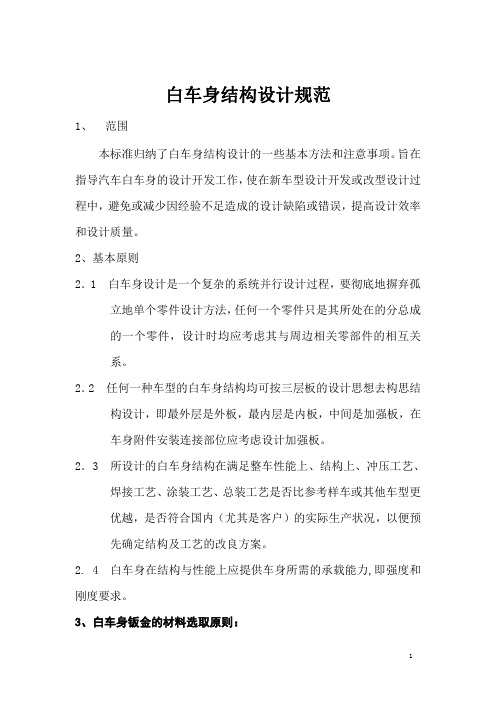
白车身结构设计规范1、范围本标准归纳了白车身结构设计的一些基本方法和注意事项。
旨在指导汽车白车身的设计开发工作,使在新车型设计开发或改型设计过程中,避免或减少因经验不足造成的设计缺陷或错误,提高设计效率和设计质量。
2、基本原则2.1白车身设计是一个复杂的系统并行设计过程,要彻底地摒弃孤立地单个零件设计方法,任何一个零件只是其所处在的分总成的一个零件,设计时均应考虑其与周边相关零部件的相互关系。
2.2任何一种车型的白车身结构均可按三层板的设计思想去构思结构设计,即最外层是外板,最内层是内板,中间是加强板,在车身附件安装连接部位应考虑设计加强板。
2.3所设计的白车身结构在满足整车性能上、结构上、冲压工艺、焊接工艺、涂装工艺、总装工艺是否比参考样车或其他车型更优越,是否符合国内(尤其是客户)的实际生产状况,以便预先确定结构及工艺的改良方案。
2.4白车身在结构与性能上应提供车身所需的承载能力,即强度和刚度要求。
3、白车身钣金的材料选取原则:3.1汽车覆盖件所用材料一般是冷轧钢板。
3.2按国家标准选取钣金材料3.3钣金按表面质量分有I,II两级:I级质量最好,适用于外板;II 级次之,适用于内板与加强板3.4钣金按冲压拉延等级分有P,S,Z,F,HF,ZF六级:P:普通拉深级,适用于拉延深度浅的零件;S:深拉深级,适用于拉延深度一般的零件;Z:最深拉深级,适用于拉延深度较深的零件;F:复杂拉深级,适用于结构复杂且拉延深度较深的零件;HF:很复杂拉深级,适用于结构较复杂且拉延深度较深的零件;ZF:最复杂拉深级,适用于结构非常复杂且拉延深度较深的零件;3.5钣金按强度等级分有:普通强度,高强度,超高强度;3.6按宝钢标准选取钣金材料3.6.1钢板及钢带按用途分:牌号用途DC01(St12)一般用(水箱外壳,制桶等)DC03(St13)冲压用(汽车门、窗、白车身件等)DC04(St14、St15)深冲用(汽车门、窗、白车身件等)DC05(BSC2)特深冲用(汽车门、窗、白车身件等)DC06(St16、St14-T、BSC3)超深冲用(汽车门、窗、白车身件等)3.6.2钢板及钢带按表面质量分:级别代号较高级的精整表面FB(O3)高级的精整表面FC(O4)超高级的精整表面FD(O5)3.6.3钢板及钢带按表面结构分:表面结构代号麻面D光亮表面B3.6.4使用部位及选用牌号标记使用部位牌号标记备注1外覆盖件DC04-XX-FD Q/BQB403—2003DC04-XX-FB Q/BQB403—2003 2内板大件(复杂、深)3内板大件(一般)DC03-XX-FB Q/BQB403—20034其它结构件DC03-XX-FB Q/BQB403—20033.6.5牌号标记说明Q/BQB403——2003材料厚度企业标准号此牌号为冷连轧、深冲用、高级精表面质量的低碳汽车用钢板。
白车身结构设计与技巧 汽车设计技术
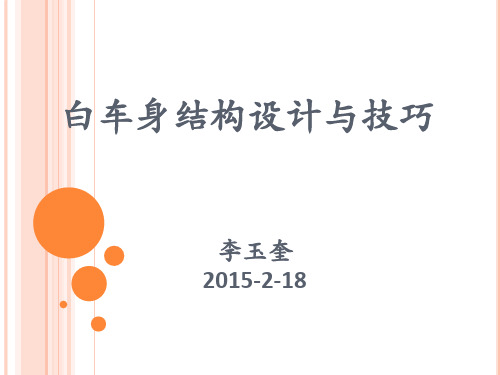
根据制造过 程中出现的 问题对数据 进行优化
完成第二
版冻结数 模
发放附件 供应商
根据第一版冻结数模对 升降器、仪表板等车身 附件和内饰件进行设计
车身结构件——试装验证阶段
钣金一序件制 造完成,模具、 焊装夹具初步 完成,单件检 具全部完成
车身附件及内 外饰快速成型 件或软模件制 造完成
进行车身焊
接及附件、 内外饰装配
力以及使车身结构合理化,采用无承载式车 身。在大客车及轿车现在基本上都采用承载 式车身。
白车身组成:
白车身由前围焊接总成、地板焊接总成、左/右侧围焊 接总成、后围焊接总成、顶盖焊接总成。
三、白车身结构设计的基本原则
白车身设计是一个复杂的系统并行设计过程,要彻底摒弃 孤立地单个零件设计方法,任何一个零件只是其所处在的 分总成的一个零件,设计时均应考虑其与周边相关零部件 的相互关系。
较深的零件
五、白车身设计一般流程
车身结构件———工艺数据设计阶段
车身内板 及加强板 设计
参考标杆车结构与已冻 结的车身外观覆盖件数 模相结合完成整车数模
逆向标杆车关键件及大 件,同时与已冻结的车 身外观覆盖件数模相结 合完成整车数模
完成第一 版工艺数 模
车身结构件——工艺数据设计阶段
工艺分析
第一版工 艺数模
2、钣金按表面质量分有一、二两级:一级质量最好, 适用于外板;二级次之,适用于内板与加强板。
3、钣金按冲压拉延等级分有P、S、Z、F、HF、ZF六 级
4、钣金按强度等级分有:普通强度、高强度、超高 强度钢板。高强度和超高强度按其强化机理分为: 固溶强化、析出强化、组织强化,复合组织强化、 热处理硬化型强化、相变强化、冷作强化、时效强 化等。
SE分析—白车身分析标准

零部件清单及装配工艺白车身总成分析标准1. 车型机舱盖支撑杆后装结构时,需自制工装用于支撑机舱盖,车型机罩钣金为机盖撑 杆工装提供可靠支撑点,上支撑孔孔形更改为钥匙孔形状。
2. 针对车身黑漆件车型内相似件、对称件以及车型间相似件、对称件进行防错处理C 柱护板右上安装支架 C 柱护板左上安装支架C 柱护板上安装更改前:C 柱护板左/右上安装支架为对称件,存在员工拿错、装错风险。
更改后:C 柱护板左/右上安装支架由对称件设计为左右通用件,避免员工拿错、装错风险前排扶手支架前排扶手支架后排扶手支架后排扶手支架前、后排扶手支架结构类似,存在错装风险,要求增加防错标识NO 问题描述 Problem Description对策 Countermeasurea.避免驾驶舱设置与外界联通的孔,如需开必须有有效的密封H6 白车身总成气密性差,气密性总1措施;b.合理设计车身空腔膨胀胶隔断;c.合理设置涂胶种类,值 130SCFM保证驾驶舱密封连续,涂胶方便可靠。
2 车身锈蚀a.根据防锈管控方案,采用镀锌板;b.依照 Q/CC SJ0469 进行 防锈设计,避免气室、电泳沥液不净、电泳屏蔽问题、电泳液 可达性差问题;c.门槛梁、车门腔体进行喷蜡处理。
C30 前轮外沿凸出车身,车辆在行驶 过程中,前车轮带起的泥沙不能完全在侧围外板后轮弧边沿漆面脱落位置增加防石击贴膜;新车型 3 被翼子板下部遮挡,导致泥沙向后甩进行防石击校核。
出,将轮弧边沿的漆面打伤,造成漆面脱落H6 拖拽 1800Kg 拖车,后拖车装置安 在 12%的坡度上依照拖拽能力对拖车装置施加静载荷分析,材4装点 7000Km 耐久破裂料屈服强度与安装点应力满足 3.5 倍安全系数。
5 车身干涉异响a.保证零件搭接零件间隙在 2mm 以上,重要受力部位,不影 响密封时间隙不小于 5mm;b.焊点布置在边部,约束钣金搭接。
a.结构设计避免大于 3mm 的空洞(改变翻遍方向,增加结构6 指压胶脱落、指压胶部位生锈筋等),车身指压胶数量不多于 6 处;b.指压密封孔不大于8mm;c.指压胶应用在涂装电泳后工序。
满足侧碰法规的白车身结构设计

满足侧碰法规的白车身结构设计“满足侧碰法规的白车身结构”设计规范1 适用范围本规范规定了满足国家侧碰法规的白车身结构的设计规则及方法。
本规范适用其质量为基准质量时,最低座椅的R点与地面的距离不超过700mm 的M1和N1类车辆。
2 引用标准下列文件通过本规范的引用而成为本规范的条款。
凡是注日期的引用文件,其随后所有的修改单(不包括勘误的内容)或修订版均不适用于本规范,然而,鼓励根据本规范达成协议的各方,研究是否可使用这些文件的最新版本。
凡是不注日期的引用文件,其最新版本适用于本规范。
本规范引用了ECE R95、FMVSS 214的部分内容。
本规范引用了我国《汽车侧面碰撞的乘员保护》法规的部分内容。
本规范引用了我国《汽车侧面碰撞的乘员保护》法规的部分内容。
3规范内容设计满足侧面碰撞的车身结构时,最大的困难在于即使有足够好的材料来制作缓冲吸能结构,但能用于缓冲和吸能的区间却十分有限。
为使吸能结构充分的发挥作用,常用的改进抗侧碰性能的方法主要是增加缓图1 撞击力传输方向冲吸能区两侧的厚度和加大缓冲吸能区两侧的内部刚度。
根据这一方法,侧面防护的思路是将撞击力有效的转移到车身上具有吸能保护作用的车门、梁、柱、地板、车顶及其部件,以便分散撞击力,吸收碰撞能量。
在进行碰撞试验时,国家侧碰法规对假人的伤害值要求如下表:成员损伤评价指标为头部、胸部、腹部和腰部各损伤值。
头部性能指标HIC 跟假人头部质心加速度相关,除非碰撞时乘员空间有结构突出和假人头部接触,该指标一般很少超标,所以在白车身设计上可不予过多的考虑。
胸部肋骨变形指标与粘性指数可以综合考虑,一般是由车门内板和中立柱内饰板变形产生的,表现在车身上即为侧围内板的侵入量与侵入速度。
由粘性指数的计算公式可见:粘性指数VC 不仅跟肋骨变形量相关,还和变形速率相关,极易超标。
为保证乘员必要的生存空间,中立柱的变形是有限制的,这就要求我们在设计中立柱的时候既要充分考虑变形吸能,又要使变形在我们可接受的范围内。
车身框架及碰撞力传递的设计

中力传递路径
下力传递路径
图 12
上传力路径是翼子板加强梁、前门加强件、A 立柱,中传力路径是前大梁、地板边梁、地板 中间加强梁,下传力路径是发动机托架、地板加强梁
7.3 正面碰撞能量的吸收如图 13 所示:
图 13
前壁障(蜂窝铝)吸收 35%的能量,前纵梁吸收 28%的能量,发动机托架吸收 22%的能量,下车体吸收 5%的能量,侧围吸收 3%的能量。
寿命。 3.2、白车身要有足够的刚度以保证其装配和使用要求
4、车身框架的基本设计原则 4.1、没有物理学上或理论力学上的“平面性”的承载结构,而是力直接作用于 骨架构件的承载形式。 4.2、所有承载骨架构件必须互相连接,分布于整个车身范围,形成承载结构的 网络,它们之间息息相关,一旦承载结构处受力,应通过承载结构的网络,将力 迅速传递至整个车身。 4.3、对车身承载结构进行分析,尽量避免存在不会受力的非承载构件,即没有 多余的不受力构件。 4.4、所有机组,如发动机、变速器及其他部件,必须尽量悬置于车身承载结构 的几何节点处。 4.5、当考滤车身结构总刚度的所有因素时,所设计的承载结构既要取尽量大的 构件截面,以便有足够的刚度,又要顾及车身不宜过重,而且车身承载结构上要 有一个合理的力传递。 5、车体结构设计的过程:车身设计过程可以归结为图 2 所示的 6 个阶段,
图 7 接头结构 CAD 模型
图 8 接头结构 CAE 分析模型
评价指标:变形分析、应力分析、应变分析
5.4、以上分析达到目标值后,接下来就可作白车身的初步工程化设计,初 步工程化设计完成数据
6、一些车型车身结构的介绍
6.一车型结构介绍
4
3
5
6
7
2
1
11
HOFF汽车设计(上海)有限公司白车身设计规范

点焊尺寸要求: 1、“a”不得小于11毫米 2、“b”不得小于5毫米 3、“c”不得小于30毫米;
30<c<50mm时,有特殊焊钳; c>50mm时,就可用普通焊钳 4、 “D”为直径5毫米的焊头,焊点 为6mm 5、 “e”暂缺 6、钣金件层数及厚度要求: (1)、层数最多为3层(超过3层要 得到厂家确认.) (2)、厚度在3毫米以内为宜, 但3---5毫米也能焊接 7、两焊点之间的间距不得小于20毫米
SHEET_M ETRAL
89
未倒角片体
不可见(Invisible) 原车未倒角数模
TITLE
151
图框(标题栏、 反图框)
不可见(Invisible)
2D_DIM 152 2D尺寸
不可见(Invisible) 孔和尺寸的相关标识
2
HOFF汽车设计(上海)有限公司白车身设计规范
白车身数模图层设置
目录
一)实体建模标准: 1、建模的距离公差设定为0.001mm。 2、弯曲件的圆角半径不宜小于最小弯曲半径,以免产生裂纹。但也不宜过大, 因为过大时,受回弹的影响,弯曲角度与圆角半径的精度不易达到要求,以 实测为准。
4
HOFF汽车设计(上海)有限公司白车身设计规范
3、 倒角处让位:当两个件零贴时,倒角处需注意让位,倒角大小以零件 实测为准(最小相差2mm)如下图:
注意:周圈翻边不 是该件成型后切出 来的,此种翻边尺 寸要求不高
27
5
HOFF汽车设计(上海)有限公司白车身设计规范
4、弯曲件的弯边长度不宜过小,其值h>R+2t。当h较小时,弯边在模具上 支持的长度过小,不容易形成足够的弯距。
6
HOFF汽车设计(上海)有限公司白车身设计规范
白车身三维设计规范[1]
![白车身三维设计规范[1]](https://img.taocdn.com/s3/m/85ba28813186bceb19e8bbd2.png)
精选商密×级▲白车身零部件三维设计规范2005-08-××发布2005-10-30实施长安汽车(集团)有限责任公司发布—200×前言中国汽车工业正飞速发展,长安公司也在进行裂变式发展,汽车的自主开发是中国汽车业健康发展的必经之路。
在汽车自主开发设计中,会用到各种参考资料,它们对设计起着非常重要的作用,对这些资料进行整理、归纳,使之成为规范,会使我们思路清晰,设计中有据可依,同时大大提高工作效率。
而车身三维设计是车身结构设计的基础和关键,所以,我们收集了德国EDAG设计公司和意大利IDEA设计公司以及长安公司历年的设计资料及设计经验,并加以比较、整理和完善形成一套完整的车身三维设计规范。
在此对其进行详细的介绍,希望能对车身设计人员特别是刚刚从事车身设计的人员提供参考。
本规范由长安汽车(集团)有限责任公司提出。
本规范由长安汽车(集团)有限责任公司科技委管理。
本规范起草单位:长安汽车工程研究院本规范主要起草人:本规范批准人:(五号宋体)Ⅰ—200×引言车身三维设计是汽车工程化设计的关键阶段。
主要设计工具是三维设计软件CATIA_V5:设计需要完成车身上各个零件的三维模型,焊接打点图、挤胶图及螺母、螺栓图,零件的定位位置、零件的压紧位置,零件的料厚方向等。
本规范的主要目的是让车身设计人员进行车身三维设计时,依据规范的设计规则,了解设计的方法、设计步骤及注意事项,对车身三维设计具有指导作用,从而缩短设计周期,节省研制经费,提高产品可靠性。
—200×车身三维设计规范1、范围本规范规定了车身三维设计的规则及方法。
本规范适用于M1汽车的车身设计。
2、规范性引用文件下列文件通过本规范的引用而成为本规范的条款。
凡是注日期的引用文件,其随后所有的修改单(不包括勘误的内容)或修订版均不适用于本规范,然而,鼓励根据本规范达成协议的各方,研究是否可使用这些文件的最新版本。
白车身设计规则

白车身设计规则1. 范围本标准归纳了白车身结构设计的一些基本方法和注意事项。
本标准适用于本公司白车身结构设计及检查。
2.基本原则2.1 白车身设计是一个复杂的系统并行设计过程,要彻底地摒弃孤立地单个零件设计方法,任何一个零件只是其所处在的分总成的一个零件,设计时均应考虑其与周边相关零部件的相互关系。
2.2 任何一种车型的白车身结构均可按三层板的设计思想去构思结构设计,即最外层是外板,最内层是内板,中间是加强板,在车身附件安装连接部位应考虑设计加强板。
2.3 所设计的白车身结构在满足整车性能上、结构上、冲压工艺、焊接工艺、涂装工艺、总装工艺是否比参考样车或其他车型更优越,是否符合国内(尤其是客户)的实际生产状况,以便预先确定结构及工艺的改良方案。
2.4 白车身在结构与性能上应提供车身所需的承载能力,即强度和刚度要求。
3.冲压工艺要求3.1 在设计钣金件时,对于影响拉延成型的圆角要尽可能放大,原则上内角R≥5,以利于拉延成型;对于折弯成型的圆角可以适当放小,原则上R≈3即可,以减小折弯后的回弹。
3.2在设计钣金件时,考虑防止成型时起皱,应在适当的地方(如材料聚集处)布置工艺缺口,或布置工艺凸台、筋。
3.3 孔与孔,孔与边界距离应大于2t,若在圆角处冲孔,孔与翻边的距离应大于R+2t。
开孔时尽量不要开在倒角面上,以避免模具刃口早期磨损。
3.4 三面或多面交汇的尖角处在倒圆时应尽量倒大成球形。
4.焊接工艺要求4.1 焊接搭接边重叠部分的宽度一般在10~15mm 为佳,最少不得小于8mm;4.2 考虑焊接工艺时应考虑焊枪的接近性。
4.3 对于无法焊接的内板,可以考虑开焊接工艺过孔,一般要求Φ30以上;4.4 对于无法点焊的部位,可以考虑二氧化碳保护焊或塞焊;4.5 考虑布置焊接工艺孔。
5. 装配工艺要求5.1 考虑零部件装配时装配工具的接近性;5.2 考虑零部件自身安装或拆卸的方便性;5.3 对于安装工艺过孔,应考虑做成翻边孔,以增加零件本身的刚度,以及不伤手和工具。
轿车白车身技术条件

型轿车白车身技术条件编制:校对:审核:标准:批准:二〇〇四年八月1 范围本标准规定了A型轿车白车身的技术要求、试验方法、检验规则、运输和储存。
本标准适用于A型轿车白车身。
2规范性引用文件下列文件中的条款通过本标准的引用而成为本标准的条款。
凡是注日期的引用文件,其随后所有的修改单(不包括勘误的内容)或修订版均不适用于本标准,然而,鼓励根据本标准达成协议的各方研究是否可使用这些文件的最新版本。
凡是不注日期的引用文件,其最新版本适用于本标准。
GB7258-2004 机动车运行安全技术条件GB/T11363-1989 钎焊接头强度试验方法QC/T900-1997 汽车整车产品质量检验评定方法3. 技术要求3.1基本要求3.1.1 白车身总成(包括车身本体总成,左右车门总成,发动机罩总成,行李舱门总成)应符合本技术条件要求,并按规定程序批准的图样及技术文件制造。
3.1.2白车身总成的各总成、零件必须经检验验收合格后方可进行焊装3.1.3白车身的焊接(焊点数及焊缝的位置、尺寸)应符合。
轿车的车身焊装图样的规定。
3.1.4白车身的质量(重量)应符合的规定范围内。
3.2 白车身的尺寸要求3.2.1 白车身的焊装尺寸应符合,轿车车身控制要点项目表的规定。
3.2.2 白车身的外形尺寸应符合图(1)的规定。
3.3. 焊接的具体要求3.3.1点焊3.3.1.1 点焊的焊点直径为Φ6±1 mm。
3.3.1.2 同一条焊线上的焊点间距应基本均匀,间距偏差不大于5mm。
3.3.1.3同一条焊线上的焊点应基本上在一条线上,其偏移量不大于3mm。
3.3.1.4有交错搭边的部位的焊点应点焊到基体中部。
3.3.1.5点焊的焊点应牢固,(正式焊接前应做试片检验),不允许虚焊、漏焊及连续开焊,同一条焊线上开焊的焊点数不超过5%。
3.3.1.6焊点处应无飞边毛刺及半点焊等缺陷。
3.3.2二氧化碳气体保护焊3.3.2.1不允许有裂纹、夹渣、漏焊、假焊、烧穿等缺陷。
白车身及车身骨架结构设计要求

白车身总体结构1.1 概述白车身通常指已经焊装好但尚未喷漆的白皮车身(Body in white),即由各种各样的骨架件和板件通过焊接拼装而成的轿车车身。
本章内容主要针对车身骨架进行描述,不包括车身覆盖件。
1.1.1 车身作用主要是为驾驶员提供便利的工作条件,为乘员提供安全、舒适的乘坐环境,隔绝振动和噪声,不受外界恶劣气候的影响。
车身应保证汽车具有合理的外部形状,在汽车行驶时能有效地引导周围的气流,以减少空气阻力和燃料消耗;此外,车身还应有助于提高汽车行驶稳定性和改善发动机的冷却条件,并保证车身内部良好的通风。
同时车身也是一件精致的艺术品,给人以美感享受,反映现代风貌、民族传统以及独特的企业形象。
1.1.2 车身类型车身壳体按照受力情况可分为非承载式、半承载式和承载式(或称全承载式)三种。
1.1.2.1 非承载式非承载式车身的特点是车身与车架通过弹簧或橡胶垫作柔性连接,如图1-1;在此种情况下,安装在车架上的车身对车架的加固作用不大,汽车车身仅承载本身的重力、它所装载的人和货物的重力及其在汽车行驶时所引起的惯性力与空气阻力;而车架则承受发动机及底盘各部件的重力;这些部件工作时,一直承受着支架传递的力以及汽车行驶时由路面通过车轮和悬架传递来的力(最后一项对车架或车身影响最大);这种结构型式一般用在货车、专用汽车及部分高级轿车上。
图1-1 非承载式车身1.1.2.2 半承载式半承载式车身的特点是车身与车架或用用螺钉连接,或用铆接、焊接等方法刚性地连接,如图1-2。
在此种情况下,汽车车身除了承受上述各项载荷外,还在一定程度上有助于加固车架,分担车架的部分载荷。
半承载式是一种过渡型的结构,车身下部仍保留有车架,不过它的强度和刚度要低于非承载式的车架,一般将它称之为底架。
它之所以被命名为半承载式是出于以下考虑:让车身也分担部分载荷,以此来减轻车架的自重力。
这种结构型式主要体现在大客车上。
图1-2 半承载式车身1.1.2.3 承载式承载式车身的特点是没有车架,车身就作为发动机和底盘各总成的安装基础,车身的强度和刚度通常由车身下部来予以保证。
白车身设计应重视的工艺要素

白车身设计应重视的工艺要素现代汽车市场对造型的个性化、潮流化、多样化的需求越来越强烈,由此带来车身造型更新的周期大大缩短,车身开发需求呈大幅度上升的态势,本文探索的是在车身开发过程中白车身设计应重视的主要工艺要素。
O86rX c 一、造型设计C>`B.z在造型过程前期,必须由总布置按设计任务书确定的参数提出造型的边界控制硬点,如引擎罩、发动机仓、轮罩等,并且对造型设计的效果图评估,这样能保证今后通过评审的效果图结构设计的可行性。
-二、车身结构设计@造型冻结在车身结构设计前期,应开始进行设计检测特征点(RPS检测点)的设计工作,使白车身总成RPS点六大片总成RPS点分总成RPS点零件RPS点的尺寸链能有序传递,合理的分布与控制。
RPS点应涵盖全部设计硬点和工艺控制硬点。
三、白车身设计应注意的工艺要素`? *x{[p G1.焊接流程要素。
白车身设计开始即硬编制零部件的分级明细表,确定每个零件的隶属关系,从每一个零件到分总成、总成、白车身总成,清晰的表示以焊接流程为主线的分级层次,这样能保证设计的工艺合理性及焊接的可行性,是白车身详细设计的重要依据之一。
2.焊接定位孔工艺孔的设计,为确保焊接质量和满足生产节拍的要求,一般主要的零件都设计1~2定位孔焊接的定位,专用定位孔一般可以利用结构安装孔在图纸数模中加以明确,也可设计专用定位孔,如两个定位孔则必需明确主孔与辅孔,专用定位孔直径一般为8mm~12mm直径公差±0.2,位置公差±0.3。
工艺孔是为满足焊接的通过性而设计的通孔,一般应在零件上加带翻边5mm的凸台孔。
-+L^4JH33.冲压工艺要素。
白车身的钣金件设计必须考虑冲压工艺的合理性,在设计中一般应初步确定冲压方向,并以冲压方向检查各特征面,原则上除造型、结构特定要求不能改变的部位外不允许出现负角,板棱角一般在2º~7º,对于复杂零件,前期还应进行冲压仿真CAE分析验证冲压工艺性,一般应遵循过渡区域圆角在确保设计硬点的前提下,尽量加大的原则,并且过渡区域应平滑,不出现突变区域。
白车身结构设计的原则

QJ/ZX 03.0X—2007 Array5 白车身结构设计的原则5.1 基本原则5.1.1 白车身设计是一个复杂的系统并行设计过程,要彻底地摒弃孤立地单个零件设计方法,任何一个零件只是其所处在的分总成的一个零件,设计时均应考虑其与周边相关零部件的相互关系。
5.1.2 任何一种车型的白车身结构均可按三层板的设计思想去构思结构设计,即最外层是外板,最内层是内板,中间是加强板,在车身附件安装连接部位应考虑设计加强板。
5.1.3 所设计的白车身结构应首先确定在满足整车性能、结构、冲压工艺、焊接工艺、涂装工艺、总装工艺上是否比参考样车或其他车型更优越,是否符合本公司或国内(客户)的实际生产状况,以便预先确定结构及工艺的改良方案。
5.1.4 白车身在结构与性能上应满足车身所需的承载能力,即强度和刚度要求。
5.1.5 除非有更优越的结构,逆向设计时应尽量保持与样车一致。
5.1.6 白车身设计应坚持经济性原则。
5.2 零部件结构选用原则5.2.1 新开发零部件应采用当前国内外技术成熟、性能先进、质量可靠的零部件。
5.2.2 改型产品应尽可能选用基础车型中的技术成熟、性能先进、质量可靠的零部件,以提高零部件的通用化程度,减少产品的开发费用和零部件的管理费用。
5.2.3 对于有产品系列规格要求的零部件,应按标准规定的规格选择设计。
5.3 钣金件设计的原则5.3.1 结构复杂化,以求最大强度、刚度设计车身钣金结构尽可能复杂化,在大于50x50mm的区域内布置加强凹坑、筋等特征;车身钣金结构尽可能复杂化,尽可能用自由曲面代替平面。
5.3.2 轻量化设计在满足强度和刚度的前提下,应选取较薄的料厚;在满足强度和刚度的前提下,应考虑布置减重孔;在满足强度和刚度的前提下,不应出现不必要的零件。
5.3.3同一零件设计对于一些零部件(如一些小的加强板,比较规则的纵横梁等),可以考虑设计成自身是关于某一面对称的,这样左右件可以使用同一件。
白车身设计需关注的工艺项

白车身设计需关注的工艺项1.冲压工艺白车身冲压件要保证冲压可行性,首先需保证冲压拔模角,即根据设计中确定的冲压方向,检查各特征面不能有负角(特殊情况除外,可通过工艺方法实现),拔模角一般在3º以上。
其次对于盒状件和梁件要特别注意其拉延深度。
此外需要保证足够大的圆角,复杂特征无突变等。
此外对于切边和冲孔,切边不应急剧过渡,尽量不要切在圆角上,冲孔避免过于靠近圆角。
翻边的急剧变化区域增加工艺缺口,翻边与相邻立壁的距离不能过小。
对于复杂零件,前期应进行冲压仿真分析验证拉伸工艺性。
2.焊接工艺首先要理清焊接顺序,即通过编制零部件的分级明细表,确定焊接流程图。
从单一零件到分总成、总成,理清主次隶属关系,从而保证焊接可行性,这是白车身设计的基础。
要根据焊接顺序定义搭接边层数(杜绝四层焊),保证搭接边宽度除圆角之外的直边在12mm以上。
为保证零件在焊装夹具上的正确定位,需要在零件上设计1到2个定位孔,一般可以将安装孔等用作定位孔,有时也需要设计专用定位孔,在图纸上注明。
如两个定位孔则必需明确主孔与辅孔,专用定位孔直径一般为直径公差±0.2,位置公差±0.3。
此外要注意通过结构设计保证焊接的通过性,有时候需要设计一些过孔保证焊枪的可达性。
为满足焊接的通过性而设计的通孔,一般加5mm 的翻边做成翻边孔。
3.涂装工艺涂装工艺方面的设计一般在车身设计后期进行,根据涂装分析增加一些涂装工艺孔如电泳孔,漏液孔等。
主要包括进水、排水和排气孔。
1)进水孔:设计的车身,在前进方向的前面要有孔位,这样车身一进入涂装的前处理槽液时,就不会漂起来,很轻松的进入到槽子中去洗澡。
2)排水孔:有了进水孔就一定要有排水孔,排水孔的位置一般在地板上以及有凹槽的底部位置。
3)排气孔:在设计弧面时,一定要有排气孔,否则在进入槽子中时,由于气泡无处排泄,会使局部化学处理不到,大大影响外观和防锈能力。
这些部位主要集中在顶盖、轮罩等部位。
汽车白车身设计规范doc

汽车白车身设计规范吉利汽车研究院车身设计科二00八年五月1目的规范车身科关于乘用车车身设计和研发的工作程序与方法。
2范围适用于乘用车车身的设计和开发。
3 职责3.1 车身科科长负责车身科内一切任务及事务的下发、审核、批准(有特殊规定除外)3.2 车身科科内组长负责本组内有关任务的分解、下发、与审核。
3.3 车身科科内审核员负责对本岗位相关设计的校对。
3.4 车身科设计员负责对本岗位相关总成及零部件的设计、修改、验证及技术文件输出。
4. 程序4.1 设计输入4.1.1根据有关领导的指示或经相关程序批准下发的《XX车型设计任务书》或《XX车型整车定义描述》或《XX车型总布置方案》和下发的工作计划进行设计输入。
4.1.2 车身科科长对即将下发的车身设计计划(设计任务书),组织人员收集相关资料。
4.1.3车身科科长将研究院下达的工作计划或工作任务分解到各设计组,并由组长分解到各设计人员。
4.1.4 针对产品的开发策划表,编制车身设计开发计划表(计划表在必要时可作修改)4.2 方案设计4.2.1 按《XX车型设计任务书》或《XX车型整车定义描述》或《XX车型总布置方案》对车身部分的规定与要求确定初步设计方案,广泛调研同类车型的相关结构,在消化、吸收和借鉴的基础上确定初步设计方案,列出主要新开发件清单。
4.2.1.1 依据测量科提供的外曲面点云,设计外曲面数据。
4.2.1.2绘制车身间隙面差图。
共5页第1页4.2.1.3设计人初选车身零部件,按车身外曲面做工程分析,要求出工程分析图,分析图中应包括:a)重要结构、尺寸,和主要断面图b)运动分析图c)车身首次系统图4.2.2 方案设计评审4.2.2.1 时机在完成总体方案设计,尤其在确定具体技术设计方案前进行。
4.2.2.2 评审内容a)是否满足设计输入的要求;b)设计方案的正确性、工艺性、经济性、可靠性以及与国内外同类车型的对比分析;c)产品布局、结构合理性、安全性和维修方便性;d)产品特性对强制性标准、法规的符合性;f)对新技术、新材料、新工艺、新结构采用的必要性,和实际生产的可行性;g)对实现标准化、通用化、系列化要求的可能性;h)是否具有恰如其分的性价比;i)在评审过程中,项目负责人要对评审时提出的各种问题作好详细记录,评审后写出评审会议纪要,以便作为下次评审的重点检查内容。
白车身ABC立柱设计规范(7页)

白车身A柱、B柱、C柱设计规范白车身A柱、B柱、C柱设计规范1 适用范围本标准规定了白车身A柱、B柱、C柱设计的方法。
本标准适用于M1类汽车的车身设计。
2 引用标准下列文件中的条款通过本规范的引用而成为本规范的条款。
凡是注日期的引用文件,其随后所有的修改单(不包括勘误的内容)或修订版均不适用于本规范,然而,鼓励根据本规范达成协议的各方研究是否可使用这些文件的最新版本。
凡是不注日期的引用文件,其最新版本适用于本规范。
2.1侧碰车身结构设计规范2.2车门限位器设计规范3 规范内容3.1 引言3.1.1一般车身有三个立柱,从前往后依次为A柱、B柱、C柱。
立柱的作用:支撑,门框。
结3.1.2 、C3.1.3 汽车立柱的结构主要由断面结构决定。
3.2 A柱、B柱、C柱的设计要点A柱上加强A柱下加强件发展:B柱由多件钢板焊接,复杂,重量大,目前已经有直接采用液压成型的封闭式截面B柱面世,以实现轻量化;还有取消B柱以提高乘客上下车的便利性的汽车国外也有尝试——法国雪铁龙C3轿车。
C 柱一定的强度要求C柱零件相对较大,功能要求较多,必须合理安排布置;满足内饰,线束的安装要求零件大,结构复杂,注意考虑制造工艺性;与车身的密搭接零件较多,必须要考虑车身结构的密封性。
封可靠性材料的选用材料选用方面,推荐材料选用推荐材料与AB柱有所不同。
C柱由于车型不同,断面结构相差很远,下面具几个车型的例子(非断面)1.轿车结构2.面包车结构另外,还有将B柱和C柱连在一起设计的,如下图,这种结构各类车型中均出现过,主要根据总体布置与模块划分而定。
- 1、下载文档前请自行甄别文档内容的完整性,平台不提供额外的编辑、内容补充、找答案等附加服务。
- 2、"仅部分预览"的文档,不可在线预览部分如存在完整性等问题,可反馈申请退款(可完整预览的文档不适用该条件!)。
- 3、如文档侵犯您的权益,请联系客服反馈,我们会尽快为您处理(人工客服工作时间:9:00-18:30)。
白车身及车身骨架结构设计要求白车身总体结构1.1 概述白车身通常指已经焊装好但尚未喷漆的白皮车身(Body in white),即由各种各样的骨架件和板件通过焊接拼装而成的轿车车身。
本章内容主要针对车身骨架进行描述,不包括车身覆盖件。
1.1.1 车身作用主要是为驾驶员提供便利的工作条件,为乘员提供安全、舒适的乘坐环境,隔绝振动和噪声,不受外界恶劣气候的影响。
车身应保证汽车具有合理的外部形状,在汽车行驶时能有效地引导周围的气流,以减少空气阻力和燃料消耗;此外,车身还应有助于提高汽车行驶稳定性和改善发动机的冷却条件,并保证车身内部良好的通风。
同时车身也是一件精致的艺术品,给人以美感享受,反映现代风貌、民族传统以及独特的企业形象。
1.1.2 车身类型车身壳体按照受力情况可分为非承载式、半承载式和承载式(或称全承载式)三种。
1.1.2.1 非承载式非承载式车身的特点是车身与车架通过弹簧或橡胶垫作柔性连接,如图1-1;在此种情况下,安装在车架上的车身对车架的加固作用不大,汽车车身仅承载本身的重力、它所装载的人和货物的重力及其在汽车行驶时所引起的惯性力与空气阻力;而车架则承受发动机及底盘各部件的重力;这些部件工作时,一直承受着支架传递的力以及汽车行驶时由路面通过车轮和悬架传递来的力(最后一项对车架或车身影响最大);这种结构型式一般用在货车、专用汽车及部分高级轿车上。
图1-1 非承载式车身1.1.2.2 半承载式半承载式车身的特点是车身与车架或用用螺钉连接,或用铆接、焊接等方法刚性地连接,如图1-2。
在此种情况下,汽车车身除了承受上述各项载荷外,还在一定程度上有助于加固车架,分担车架的部分载荷。
半承载式是一种过渡型的结构,车身下部仍保留有车架,不过它的强度和刚度要低于非承载式的车架,一般将它称之为底架。
它之所以被命名为半承载式是出于以下考虑:让车身也分担部分载荷,以此来减轻车架的自重力。
这种结构型式主要体现在大客车上。
图1-2 半承载式车身1.1.2.3 承载式承载式车身的特点是没有车架,车身就作为发动机和底盘各总成的安装基础,车身的强度和刚度通常由车身下部来予以保证。
一般中低档轿车车身属于承载式车身。
以S11车身为例,如下图1-3所示。
图1-3 承载式车身为了减小汽车的整车重量和节约材料,大多数中级、普通级、微型轿车和部分客车车身常采用承载式结构。
货车驾驶室只占汽车长度的小部分,不可能采用承载式结构。
没有完整的封闭构架的开式车身(敞篷车)也很难采用承载式结构。
高级轿车车身如果为了提高汽车的舒适性,减轻发动机及底盘各总成工作时传来的振动及汽车行驶时由路面通过车轮和悬架传给车身的冲击,则可采用非承载式结构。
承载式车身的地板有较完整(厚度也较大)的纵、横承力部件,其前部有两根断面尺寸较粗的纵梁,它们往往与两侧的前挡泥板和前面的散热器固定支架等焊接成刚性较好的空间构架,以便直接安装发动机和前悬架等部件并承受其工作载荷。
与此相反,非承载式轿车的车身前部就较薄弱,其车前钣金制件通常不是焊接在车身壳体上,而是用螺钉相互连接起来并安装在车架上。
1.2 车身骨架的结构分块车身骨架主要由车身前部总成、前围总成、侧围总成、地板总成、顶盖总成和后围板总成组成,如图1-4。
1、前部结构2、前围总成3、侧围总成4、地板总成5、顶盖总成6、后围板总成图1-4 车身骨架1.2.1前部结构承载式车身的前部结构,其主要功能是支撑发动机、驱动装置、悬架和散热器等,并承受各种载荷作用。
车身前部结构的横向承载单元主要由前大灯框架、水箱横梁等焊接组成;两侧的纵向承载单元主要由前纵梁、轮罩、前翼子板支架等焊接组成。
1.2.2 前围总成轿车车身前围是分隔车身前部与座舱的结构总成,支承并安装前风挡玻璃、雨刮器、仪表板横梁、转向柱、脚踏板和空调等。
一般由前围上盖板、前围板、转向柱支架等组成。
车身前围对保证车身的扭转刚度、改善座舱舒适环境和提高碰撞安全性等起着重要作用。
1.2.3 侧围总成侧围是形成轿车左右侧壁,是组成座舱的重要结构总成,它是支撑顶盖,连接车身前后部分的侧面构件,是固定前风窗玻璃,并用来安装侧门,保证车身侧面撞击安全性的承载框架,应具有较大的抗弯、抗扭刚性和强度;其主要由侧围外板、A柱、B柱、C柱及加强板等焊接组成。
1.2.4底板总成车身底板是车身的支承部分,应提供足够的强度和刚度,从而保证车身的承载能力。
现代轿车为满足造型和视野等要求,广泛采用细窗柱、大面积玻璃和薄车顶等结构型式,由此加大了车身底部结构部分的承载分量,以致车身设计上对车身底板结构的承载能力要求更高。
加上底板结构的防振、隔音和防腐蚀性能的要求,以及车身室内居住性的不断改善对底板布置的影响,使得合理设计底板结构成为车身结构设计的重要内容。
轿车车身底板结构主要由前底板、后底板、中通道、门槛、连接板、座椅支架等构件组成,见图1-5。
底板总成的关键部件是门槛梁和分置在其间的横梁。
横梁可以起到防止底板折叠的作用。
一般侧向要预留200~300mm的空间,供侧向的皱折变形之用。
为了提高门槛抗弯强度,应尽量加大其断面尺寸。
此外,也可以在门槛梁内增设衬板结构。
图1-5 地板总成结构1.2.5顶盖总成顶盖由顶盖前、后横梁支承,并焊接在其上,从而使其刚度和强度得到增加,如图1-6。
现代轿车设计中,从扩大视野和上下车方便性考虑,已广泛采用薄车顶、四周小圆角过渡的顶部结构型式,既保证了顶盖的刚性,又减小了振动噪声。
1.2.6 后围板总成后围板总成即为行李箱盖下方连接左右翼子板的部分,一般包括上、下连接板、后围加强板、锁销加强板等,并安装后保险杠。
图1-6顶盖总成结构1.3 现代汽车车身骨架的主要构成部件前纵梁前纵梁为轿车车身前部承载的主要结构,主要承担来自前悬架系统、发动机悬置(有的车不需要)的工作载荷,同时它也是前碰的主要吸能结构,所以,它担负着重要的安全功能。
前围板前围板是指发动机舱与车厢之间的隔板,它与地板、前立柱连接,并安装在前围上盖板之下。
前围板上有许多孔口,作为操纵用的拉线、拉杆、管路和线束通过之用;另外,其还要满足脚踏板、转向柱等机件的安装要求。
为防止发动机舱里的废气、高温、噪声窜入车厢,前围板上要有密封措施和隔热装置。
在发生意外事故时,它应具有足够的强度和刚度。
对比车身其它部件而言,前围板装配最重要的工艺技术是密封和隔热,它的优劣往往反映了车辆整体的质量。
前围上盖板前围上盖板一般由上盖板内板、上盖板外板以及加强板等构件焊接而成,支承并安装前风挡玻璃和雨刮器。
通常采用具有很大扭转刚度的箱型断面结构。
前围上盖板通过两侧的端板与车身左右侧围的前立柱焊接,是决定车身扭转刚度的主要构成元件。
A、B、C柱一般轿车车身有三个立柱,从前往后依次为前柱(A柱)、中柱(B 柱)、后柱(C柱)。
对于轿车而言,立柱除了支撑作用,也起到门框的作用。
设计师考虑前柱几何形状方案时还必须要考虑到前柱遮挡驾驶者视线的问题。
一般情况下,驾驶者通过前柱处的视线,其双目重叠角总计为5~6度,从驾驶者的舒适性看,重叠角越小越好,但这涉及到前柱的刚度,既要有一定的几何尺寸以保持前柱的高刚度,又要尽量减少驾驶者的视线遮挡,始终是一个矛盾的问题。
设计者必须尽量平衡两者以取得最佳效果。
在2001年北美国际车展上,瑞典沃尔沃推出的最新概念车SCC,就将前柱改为通透形式,镶嵌透明玻璃以便驾驶者可以透过柱体观察外界,令视野盲点减少到最低程度。
中柱不但支撑车顶盖,还要承受前、后车门的支承力,在中柱上还要装置一些附加零部件,例如前排座位的安全带、线束等。
因此中柱大都有外凸半径,以保证有较好的力传递性能。
现代轿车的中柱截面形状是比较复杂的,它由多件冲压钢板焊接而成。
随着汽车制造技术的发展,不用焊接而直接采用液压成型的封闭式截面中柱巳经问世,它的刚度大大提高而重量大幅减小,有利于现代轿车的轻量化。
另外,有些设计师从乘客上下车的便利性考虑,索性取消中柱;最典型的是法国雪铁龙C3轿车,车身左右两侧的中柱都被取消,前后门对开,乘员完全无障碍上下车。
当然,取消中柱就要相应增强前、后柱,其车身结构必须要用新的型式,材料选用也有所不同。
后柱与前柱、中柱不同的一点就是不存在视线遮挡及上下车障碍等问题,因此构造尺寸大些也无妨,关键是后柱与车身的密封性要可靠。
顶盖是车厢顶部的盖板。
对于轿车车身的总体刚度而言,顶盖不是很重要的部件,这也是允许在车顶盖上开设天窗的理由。
从设计角度来讲,重要的是它如何与前、后窗框及支柱交界处平顺过渡,以求得最好的视觉感和最小的空气阻力。
当然为了安全,车顶盖还应有一定的强度和刚度;另外,除了在顶盖下增加一定数量的加强梁外,顶盖内层也敷设绝热衬垫材料,以阻止外界热量和噪声的传入。
顶盖通常分为固定式顶盖和敞篷式顶盖两种;固定式顶盖是常见的轿车顶盖形式,属于轮廓尺寸较大的大型覆盖件,属于车身整体结构的一部分。
它具有刚性强,安全性好,汽车侧翻时起到保护乘员的特点,缺点是固定不变,无通风性,无法享受到阳光及兜风的乐趣。
敞篷式顶盖一般用于档次较高的轿车或跑车上,通过电动和机械传动,移动部分或全部顶盖,可以充分享受阳光和空气,体验兜风的乐趣;缺点是机构复杂,安全性和密封性较差。
敞篷式顶盖有两种形式,一种称为“硬顶”,顶盖用轻质金属或树脂材料做成;另一种称为“软顶”,顶盖用篷布做成。
目前新型敞篷车多用硬顶形式,例如标致206CC跑车,按动电钮,即可使后行李舱盖向后揭开,顶盖自动折叠并随支柱(车厢后柱)的摆动而向后移动,移至行李舱处降下,降入行李舱内,然后合上行李舱盖,此时整车就成为了一辆敞篷车。
硬顶式敞篷车的各部件之间配合相当精密,整个电控操纵机构较复杂,但由于采用硬性材料,恢复车厢顶盖后的密封性较好。
而软顶敞篷车由篷布及支撑框架构成,将篷布及支撑框架向后折叠就可以获得敞开式车厢。
由于篷布质地柔软,折叠起来比较紧凑,整个机构也相对简单,但密封性及耐用性较差。
固定式顶盖和敞篷式顶盖有各自的优缺点,可不可以去除缺点而保留两者优点?设计师想出了一个折中的办法:在固定顶盖上开窗口,即“天窗”,既可保持固定顶盖的优点,又可在一定程度上获得敞篷效果,两者兼顾,还可增加厢内光线。
这种方式受到了汽车消费者的欢迎,在20世纪80年代后,开天窗的轿车迅速流行起来。
翼子板是遮盖车轮的车身外板,因旧式车身该部件形状及位置似鸟翼而得名。
按照安装位置又分为前翼子板和后翼子板,前翼子板安装在前轮处,因此必须要保证前轮转动及跳动时的最大极限空间,因此设计者会根据选定的轮胎型号尺寸用“车轮跳动图”来验证翼子板的设计尺寸。
后翼子板无车轮转动碰擦的问题,但出于空气动力学的考虑,后翼子板略显拱形弧线向外凸出。
现在有些轿车翼子板已与车身本体成为一个整体,一气呵成。