MTBE工艺
MTBE生产工艺
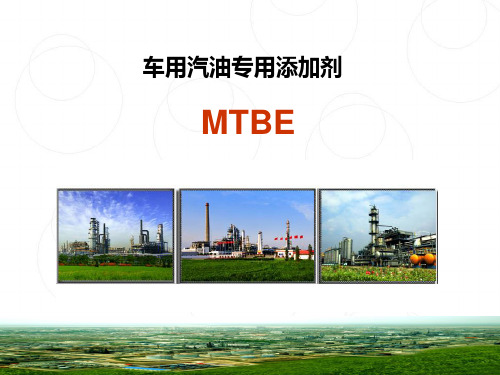
醇烯比过大:可使异丁烯转化率增加,但多余的甲 醇不仅增加了反应精馏塔的分离难度而且增加了 甲醇回收塔的负荷。
醇烯比过小:发生异丁烯聚合反应,放出大量热量, 造成反应器超温,烧坏催化剂。
MTBE反应的主要影响因素
(2)反应温度 反应温度的高低不仅影响异丁烯的转化率,
而且也影响MTBE的选择性、催化剂的使用寿命和 反应速度。
4.2.2 尾气排放量大 按照设计,装置不产生尾气,由于原料中C3
组分含量远高于设计值,装置不得不进行尾气排放。 目前尾气只能排入火炬。
五、吉化MTBE装置的技术改造情况
➢ 原设计:2.75万吨MTBE/年,设计运行时间:7200 小时
➢ 由吉化研究院开发,吉化设计院设计,吉化建设公司 安装的我国第一套万吨级工业化装置;
3.5 甲醇回收原理 利用C4和甲醇在水中溶解度的不同,用水做萃
取剂,将甲醇和C4分离,在用精馏的方法分离甲醇 与水。
流程
C4馏分 V402甲醇储罐 V401C4储罐 V409脱碱罐 R402AB净化器 R401反应器 T401反应精馏塔 T402萃取塔 T403甲醇回收塔
MTBE的工艺流程叙述
生产温度:一般50~70℃为宜,温度超过80 ℃, 副反应增加,催化剂寿命缩短,温度超过120℃, 催化剂失活。
二、工艺原理
3.3 催化蒸馏原理 反应与精馏在同一个塔内进行,反应放出的
热量用于精馏物料汽化,保证反应在恒温下进行。
3.4 产品分离原理 利用C4和甲醇形成最低共沸物的性质,采用共
沸精馏的方法,将MTBE与甲醇、C4进行分离。
3.2 醚化反应原理
混合C4中异丁烯与甲醇在强酸性苯乙烯系大 孔阳离子交换树脂催化剂作用下发生合成反应生 成MTBE。
MTBE装置生产原理和工艺过程
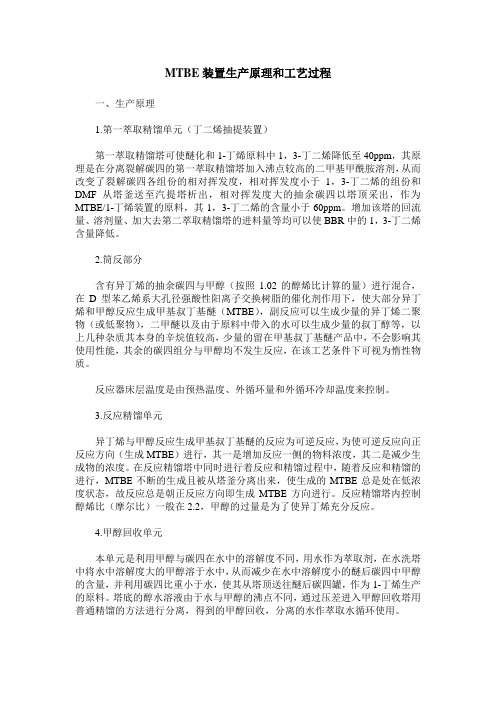
MTBE装置生产原理和工艺过程一、生产原理1.第一萃取精馏单元(丁二烯抽提装置)第一萃取精馏塔可使醚化和1-丁烯原料中1,3-丁二烯降低至40ppm,其原理是在分离裂解碳四的第一萃取精馏塔加入沸点较高的二甲基甲酰胺溶剂,从而改变了裂解碳四各组份的相对挥发度,相对挥发度小于1,3-丁二烯的组份和DMF从塔釜送至汽提塔析出,相对挥发度大的抽余碳四以塔顶采出,作为MTBE/1-丁烯装置的原料,其1,3-丁二烯的含量小于60ppm。
增加该塔的回流量、溶剂量、加大去第二萃取精馏塔的进料量等均可以使BBR中的1,3-丁二烯含量降低。
2.筒反部分含有异丁烯的抽余碳四与甲醇(按照1.02的醇烯比计算的量)进行混合,在D型苯乙烯系大孔径强酸性阳离子交换树脂的催化剂作用下,使大部分异丁烯和甲醇反应生成甲基叔丁基醚(MTBE),副反应可以生成少量的异丁烯二聚物(或低聚物),二甲醚以及由于原料中带入的水可以生成少量的叔丁醇等,以上几种杂质其本身的辛烷值较高,少量的留在甲基叔丁基醚产品中,不会影响其使用性能,其余的碳四组分与甲醇均不发生反应,在该工艺条件下可视为惰性物质。
反应器床层温度是由预热温度、外循环量和外循环冷却温度来控制。
3.反应精馏单元异丁烯与甲醇反应生成甲基叔丁基醚的反应为可逆反应,为使可逆反应向正反应方向(生成MTBE)进行,其一是增加反应一侧的物料浓度,其二是减少生成物的浓度。
在反应精馏塔中同时进行着反应和精馏过程中,随着反应和精馏的进行,MTBE不断的生成且被从塔釜分离出来,使生成的MTBE总是处在低浓度状态,故反应总是朝正反应方向即生成MTBE方向进行。
反应精馏塔内控制醇烯比(摩尔比)一般在2.2,甲醇的过量是为了使异丁烯充分反应。
4.甲醇回收单元本单元是利用甲醇与碳四在水中的溶解度不同,用水作为萃取剂,在水洗塔中将水中溶解度大的甲醇溶于水中,从而减少在水中溶解度小的醚后碳四中甲醇的含量,并利用碳四比重小于水,使其从塔顶送往醚后碳四罐,作为1-丁烯生产的原料。
MTBE装置生产原理及工艺流程
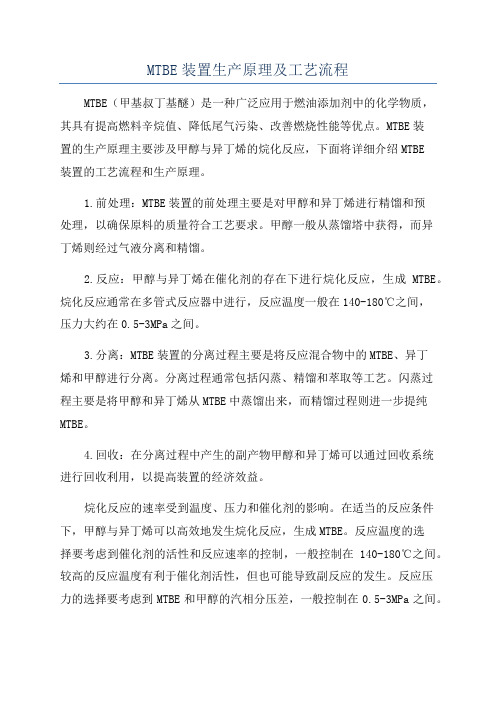
MTBE装置生产原理及工艺流程MTBE(甲基叔丁基醚)是一种广泛应用于燃油添加剂中的化学物质,其具有提高燃料辛烷值、降低尾气污染、改善燃烧性能等优点。
MTBE装置的生产原理主要涉及甲醇与异丁烯的烷化反应,下面将详细介绍MTBE装置的工艺流程和生产原理。
1.前处理:MTBE装置的前处理主要是对甲醇和异丁烯进行精馏和预处理,以确保原料的质量符合工艺要求。
甲醇一般从蒸馏塔中获得,而异丁烯则经过气液分离和精馏。
2.反应:甲醇与异丁烯在催化剂的存在下进行烷化反应,生成MTBE。
烷化反应通常在多管式反应器中进行,反应温度一般在140-180℃之间,压力大约在0.5-3MPa之间。
3.分离:MTBE装置的分离过程主要是将反应混合物中的MTBE、异丁烯和甲醇进行分离。
分离过程通常包括闪蒸、精馏和萃取等工艺。
闪蒸过程主要是将甲醇和异丁烯从MTBE中蒸馏出来,而精馏过程则进一步提纯MTBE。
4.回收:在分离过程中产生的副产物甲醇和异丁烯可以通过回收系统进行回收利用,以提高装置的经济效益。
烷化反应的速率受到温度、压力和催化剂的影响。
在适当的反应条件下,甲醇与异丁烯可以高效地发生烷化反应,生成MTBE。
反应温度的选择要考虑到催化剂的活性和反应速率的控制,一般控制在140-180℃之间。
较高的反应温度有利于催化剂活性,但也可能导致副反应的发生。
反应压力的选择要考虑到MTBE和甲醇的汽相分压差,一般控制在0.5-3MPa之间。
此外,MTBE的分离和回收也是MTBE装置生产的关键环节。
通过采用闪蒸、精馏和萃取等工艺,可以实现对MTBE的高效分离和提纯,并回收副产物甲醇和异丁烯,最大限度地提高装置的经济效益。
总之,MTBE装置的生产原理及工艺流程包括前处理、反应、分离和回收等步骤。
通过合理选择反应条件和适当的分离工艺,可以高效地生产出优质的MTBE产品。
工艺学异丁烯合成MTBE

碳四馏分中异丁烯生产MTBE工艺1、MTBE生产工艺基本情况简介本次生产采用丁二烯/MTBE/丁烯-1联合装置,此装置由丁二烯抽提装置和MTBE装置两部分组成,丁二烯装置以乙烯裂解装置提供的混合C4为原料,以乙腈为溶剂,采用两级萃取精馏和两级普通精馏,得到聚合级1,3-丁二烯产品送产品罐区外售。
MTBE /丁烯-1装置是以丁二烯抽提装置来的抽余C4和工业甲醇为原料,生产甲基叔丁基醚(MTBE)和丁烯-1产品。
本次主要介绍MTBE生产工艺。
图二为改进的一塔一器催化蒸馏生产MTBE,而图三为两塔两器工艺,已逐渐被催化蒸馏所取代,我们以下对其进行比较。
MTBE合成反应的直接结果是获得MTBE,间接结果是将正丁烯和异丁烯分离开来,由于正丁烯和异丁烯的相对挥发度接近1,因此用常规的精馏方法难于分离,因此采用合成MTBE的化学方法进行分离,是目前普遍采用的分离方法。
MTBE是甲基叔丁基醚的商品名,是异丁烯和甲醇在强酸性催化剂作用下反应的产物,它的主要用途是替代四乙基铅作为提高汽油辛烷值的添加剂,纯MTBE的辛烷值为109。
此外MTBE热裂解可以生产高纯度异丁烯,高纯度异丁烯是生产丁基橡胶的原料,它也是其它需要引入叔丁基反应的单体。
2、生产工艺流程图图一 生产MTBE 工艺流程示意图抽余碳四 反应器 甲醇 催化蒸馏 甲醇萃取 丁烯-1精制甲醇回收 MTBE 产品 丁烯-1产品剩余碳四图三两塔两器生产MTBE工艺流程3、工艺流程说明图二中原料甲醇与异丁烯以1.0~1.05的摩尔比在预反应器中进行烯醇的醚化反应,反应温度50~70℃为宜,反应后的物料进入催化精馏塔,再补加甲醇的条件下继续反应,生成的MTBE与未反应的原料在催化精馏塔内,边反应边分离,塔底得到产品MTBE,塔顶得到C4和甲醇的共沸物,一部分回流,另一部分采出进入水洗塔塔底,萃取剂水从塔顶进入水洗塔,根据甲醇与C4在水中溶解度的不同,将C4与甲醇分离,塔底得到甲醇的水溶液,塔顶得到C4;从水洗塔塔底出来的甲醇水溶液进入甲醇回收塔,采用普通精馏的方法将甲醇和水分离,分离后的水打到水洗塔做萃取剂循环利用,分离后的甲醇作为反应原料循环利用。
MTBE丁烯装置工艺技术规程

MTBE丁烯装置工艺技术规程一、工艺流程描述MTBE丁烯装置工艺流程主要包括四个部分,即溶剂提取、脱水、乙烯分离和MTBE生产。
具体流程如下:1. 溶剂提取:将C5烷烃和C4烷烃与乙烯反应生成乙烯丙烯液体混合物,然后将其送入溶剂继续萃取物处理。
萃取物中去除余烯烃,然后通过蒸馏将溶剂与乙烯回收。
2. 脱水:将萃取物送入脱水塔进行脱水处理,去除其中的水分。
脱水处理可能采用吸收剂吸附去除水分的方法。
3. 乙烯分离:将脱水后的乙烯丙烯混合物送入乙烯分离塔,通过分馏将乙烯和丙烯分离。
4. MTBE生产:将分离的乙烯送入MTBE反应器,与异丁醇进行酯化反应,生成MTBE乙醚。
然后将乙醚通过脱水装置去除水分,得到纯净的MTBE乙醚产品。
副产品丙烯醇经过进一步脱水处理,可回收再利用。
二、工艺参数要求1. 溶剂提取:乙烯-丁烯的摩尔比例要保持在适宜的范围内,以保证反应的高效进行。
萃取物中的余烯烃的含量应控制在规定范围内,以确保后续步骤的质量。
2. 脱水:脱水塔的操作温度和压力需要根据试验数据确定,以确保脱水效果良好。
吸附剂的选取需要具有较高的吸附性能和耐水性。
3. 乙烯分离:分离塔的操作条件需要根据乙烯和丙烯的挥发性差异选取,保证乙烯的纯度和丙烯的回收率。
4. MTBE生产:反应器的操作温度和压力需要根据酯化反应的速率和平衡数据确定。
反应时间和混合物的浓度也需要控制在合适的范围内,保证酯化反应的效果。
5. 脱水装置:脱水装置需要具有高效的分离水分的能力,确保MTBE产品的纯度和品质。
操作温度和压力需要根据吸附剂的性能和MTBE的蒸汽压确定。
三、安全措施1. 装置需要具备严格的安全设备,包括防爆、泄露警报和紧急停机装置。
2. 确保装置气体、液体和固体的严密密封,避免泄漏危险。
3. 操作人员需穿戴适当的防护装备,如防护服、护目镜、手套等。
4. 工艺装置需要配备火灾探测和灭火装置。
5. 充分培训操作人员,确保其熟悉安全操作规程和应急处理方法。
车用汽油专用添加剂MTBE生产工艺

车用汽油专用添加剂MTBE生产工艺1. 简介车用汽油专用添加剂MTBE(甲基叔丁基醚)是一种常用的汽油增氧剂和抗爆剂。
它可以改善汽油的抗爆性能,提高发动机的燃烧效率,减少废气排放和空气污染。
本文将介绍MTBE的生产工艺流程。
2. 原料准备MTBE的生产原料主要包括甲醇和异丁烷。
甲醇作为主要原料,是从天然气、煤炭等资源中生产。
异丁烷则可从石化厂中获得。
3. 生产工艺流程MTBE的生产主要分为以下几个步骤:3.1 原料准备首先,需要对甲醇和异丁烷进行精确的测量和配比。
通常情况下,甲醇与异丁烷的比例为1:3。
3.2 反应器反应将预先测量好的甲醇和异丁烷注入反应器中,加入适量的催化剂(通常采用硫酸),然后进行反应。
反应器通常采用连续搅拌式反应器,通过调节反应器的温度和压力,控制反应的进行。
3.3 分离和净化反应完成后,需要对反应液进行分离和净化。
首先利用蒸馏技术将MTBE和未反应的甲醇、异丁烷等物质分离。
经过多级蒸馏后,得到纯净的MTBE。
3.4 脱水和氧化为了进一步提高MTBE的纯度,需要对其进行脱水和氧化处理。
脱水通常采用蒸汽脱水的方式,将水分从MTBE中去除。
氧化处理则是通过加入适量的空气或氧气,使MTBE与氧气发生反应,去除其中的杂质。
3.5 产品回收和储存经过上述处理后,得到高纯度的MTBE产品。
最后,需要对MTBE进行回收和储存。
回收通常采用冷凝技术,通过将MTBE蒸气冷却后液化,得到液态的MTBE。
储存则需要将MTBE存放在密封的容器中,避免与空气中的水分和杂质发生反应。
4. 安全措施在MTBE的生产过程中,需重视安全措施,如:•确保生产场所通风良好,减少MTBE蒸气的积聚;•严格控制反应温度和压力,避免产生过高的温度和压力引发事故;•使用防爆设备和装置,确保生产过程的安全;•工作人员需穿戴合适的防护设备,如防护眼镜、手套等。
5. 结语通过控制好MTBE生产工艺中的各个环节,可以获得高纯度的MTBE产品。
mtbe工艺流程

mtbe工艺流程MTBE(甲基叔丁基醚)是一种广泛应用于汽车燃油中的有机化合物,它具有较高的辛烷值和良好的抗爆震性能,能够提高汽油的燃烧效率和动力性能。
以下是MTBE的生产工艺流程介绍。
MTBE的生产工艺主要分为三个步骤:材料准备、反应和产物分离。
首先要准备反应所需的原料。
主要的原料包括异丁烯和甲醇。
异丁烯是一种液体烃类,可以通过石脑油的轻质馏分或乙烯的高温裂解来获取。
甲醇是一种无色、易挥发的液体,通常通过天然气或煤制气来生产。
此外,还需要一种酸性催化剂来促进反应的进行,常用的酸性催化剂包括硫酸和醋酸。
在反应阶段,将异丁烯和甲醇加入反应釜中,并加入催化剂。
反应釜中通常设置了加热和搅拌系统,以保持反应的恒温和充分混合反应物。
这个反应过程称为醚化反应,其目的是将异丁烯和甲醇进行化学反应,生成MTBE。
醚化反应可以通过控制反应温度和压力、催化剂的使用量等条件来提高产物的产率和纯度。
在反应过程中,异丁烯和甲醇的分子通过催化剂的作用下发生化学结合,生成MTBE的分子结构。
反应完成后,需要对产物进行分离和纯化。
将反应釜中的混合物送入一个分离设备,通常是一个分馏塔。
由于MTBE和其他组分的沸点不同,可以通过控制温度和压力,将MTBE分离出来。
分馏塔通常是一个逐级分离的过程,根据组分的沸点和相对挥发性,可将MTBE逐渐纯化。
分离剩余物中的未反应异丁烯和甲醇可以回流至反应釜中进行再利用。
最后,将纯化后的MTBE收集起来,并通过一系列的检测来确保质量的合格。
一般的检测项目包括MTBE的含量、水分和酸值等。
如果发现不合格的产品,需要进行再处理或剔除。
总体上说,MTBE的生产工艺流程相对简单,但需要严格控制反应条件和分离操作,以确保产品的质量和纯度。
随着汽油需求的增长,MTBE的生产也将持续发展,并迎来更加高效和环保的工艺流程。
mtbe裂解工艺交流材料

mtbe裂解工艺交流材料
来自MTBE(甲基叔丁基醚)裂解工艺方面的交流资料:
材料1:MTBE裂解工艺概述
MTBE裂解工艺是一种将MTBE反应为丙烯的化学过程。
该
工艺利用催化剂将MTBE分解为丙烯、异丁烯和其他副产物。
该工艺具有高产率、高选择性和易操作等优点,被广泛应用于石化工业。
材料2:MTBE裂解催化剂
MTBE裂解反应过程需要催化剂的存在以提高反应效率和选择性。
常用的MTBE裂解催化剂包括氧化型和氯化型催化剂。
氧化型催化剂具有较高的活性和选择性,但易受水分和硫化物的影响;而氯化型催化剂具有较高的稳定性和抗水性能,但反应活性较低。
合理选择催化剂种类和使用条件对MTBE裂解
反应的效果具有重要影响。
材料3:MTBE裂解工艺优化
为提高MTBE裂解工艺的产率和选择性,可以从多个方面进
行优化。
首先是催化剂的选择和活性调控,通过调整催化剂组成和制备工艺来提高反应效果。
其次是反应条件的优化,包括温度、压力、空速等的调节。
此外,还可以优化反应器的设计和操作参数,如反应器结构、进料方式、混合方式等。
材料4:MTBE裂解工艺的应用
MTBE裂解工艺的丙烯产物广泛应用于合成聚合物、合成橡胶、工业溶剂等领域。
丙烯是一种重要的化工原料,其衍生品在塑
料、合成纤维、涂料等许多行业具有广泛的应用前景。
MTBE 裂解工艺作为丙烯的重要来源之一,在提供丙烯原料的同时,也可以实现MTBE资源的利用。
以上材料为MTBE裂解工艺相关的交流资料,其中没有出现与标题相同的文字。
MTBE装置生产原理及工艺流程
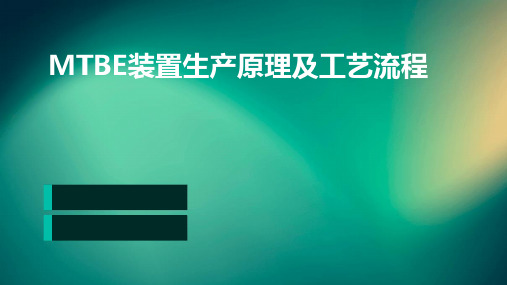
采用环保技术和清洁生产工艺,降低能耗和资源消 耗,减少污染物排放。
03
建立环保监测和报告制度,及时向相关部门报送环 保数据和信息。
THANKS FOR WATCHING
感谢您的观看
详细描述
原料的配比对于化学反应的平衡和速率具有重要影响,进而 影响产品的收率和质量。因此,需要精确控制原料配比,确 保其在工艺要求的范围内,以获得最佳的工艺效果。
05 安全与环保注意事项
安全操作规程
操作人员需经过专业培训,熟悉装置操作规程和 安全注意事项。
操作过程中应严格遵守工艺流程和安全操作规程, 确保生产安全。
MTBE装置生产原理及工艺流程
目 录
• MTBE装置简介 • MTBE生产原理 • MTBE装置工艺流程 • 工艺流程中的关键控制点 • 安全与环保注意事项
01 MTBE装置简介
MTBE的化学结构
甲基叔丁基醚(MTBE)是一 种有机化合物,其化学式为 C5H12O,结构简式为 CH3OC(CH3)3。
甲醇的合成原理
甲醇的合成主要通过一氧化碳和氢气 的反应制得,反应方程式为 CO+2H2→CH3OH。
甲醇的合成需要在高温高压条件下进 行,同时需要严格控制反应温度和压 力,以获得高收率、高纯度和低能耗 的合成效果。
在甲醇合成过程中,催化剂的选择同 样重要,常用的催化剂包括锌铬催化 剂、铜基催化剂和贵金属催化剂等。
分离过程
利用蒸馏原理,将MTBE从反应液 中分离出来,收集MTBE产品。
产品储存
将分离出的MTBE产品储存于指定 容器中,进行质量检测和包装,确 保产品质量符合要求。
04 工艺流程中的关键控制点
温度控制
总结词
温度控制是MTBE装置生产中的重要环节,它直接影响产品的质量和产量。
mtbe生产工艺
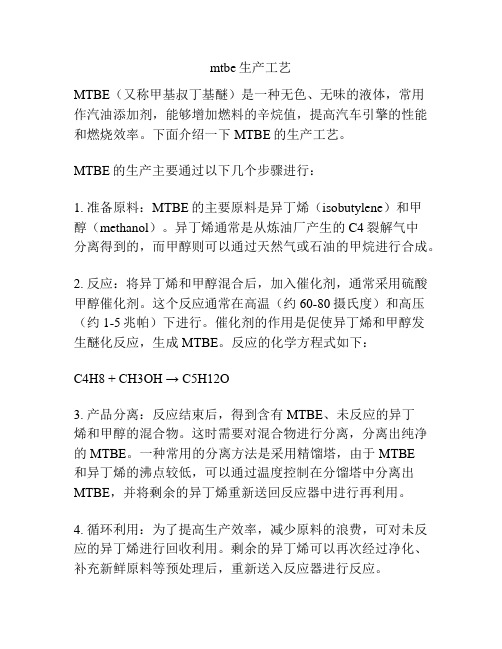
mtbe生产工艺MTBE(又称甲基叔丁基醚)是一种无色、无味的液体,常用作汽油添加剂,能够增加燃料的辛烷值,提高汽车引擎的性能和燃烧效率。
下面介绍一下MTBE的生产工艺。
MTBE的生产主要通过以下几个步骤进行:1. 准备原料:MTBE的主要原料是异丁烯(isobutylene)和甲醇(methanol)。
异丁烯通常是从炼油厂产生的C4裂解气中分离得到的,而甲醇则可以通过天然气或石油的甲烷进行合成。
2. 反应:将异丁烯和甲醇混合后,加入催化剂,通常采用硫酸甲醇催化剂。
这个反应通常在高温(约60-80摄氏度)和高压(约1-5兆帕)下进行。
催化剂的作用是促使异丁烯和甲醇发生醚化反应,生成MTBE。
反应的化学方程式如下:C4H8 + CH3OH → C5H12O3. 产品分离:反应结束后,得到含有MTBE、未反应的异丁烯和甲醇的混合物。
这时需要对混合物进行分离,分离出纯净的MTBE。
一种常用的分离方法是采用精馏塔,由于MTBE和异丁烯的沸点较低,可以通过温度控制在分馏塔中分离出MTBE,并将剩余的异丁烯重新送回反应器中进行再利用。
4. 循环利用:为了提高生产效率,减少原料的浪费,可对未反应的异丁烯进行回收利用。
剩余的异丁烯可以再次经过净化、补充新鲜原料等预处理后,重新送入反应器进行反应。
5. 产品精制:分离出的MTBE可能还含有少量的杂质,需要进行精制。
常用的方法是通过溶剂抽提或吸附剂吸附等方式,将杂质去除,得到纯净的MTBE。
这就是MTBE的生产工艺。
MTBE的生产具有高效、环保、低成本等特点,因此被广泛应用于汽油添加剂的生产中。
此外,MTBE还可以用作溶剂、萃取剂等方面,具有较广泛的应用前景。
但同时,MTBE也存在着环境污染和健康风险等问题,其挥发性较强,易进入水体和大气中,对环境和人体健康造成影响,因此在一些国家和地区已经限制或禁止使用MTBE。
mtbe的生产工艺
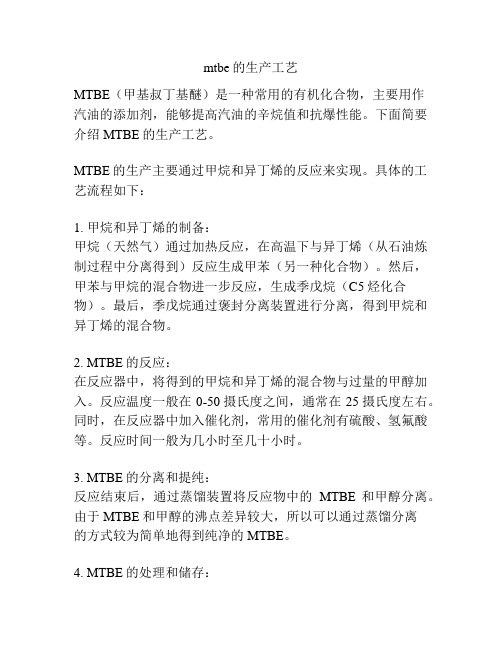
mtbe的生产工艺MTBE(甲基叔丁基醚)是一种常用的有机化合物,主要用作汽油的添加剂,能够提高汽油的辛烷值和抗爆性能。
下面简要介绍MTBE的生产工艺。
MTBE的生产主要通过甲烷和异丁烯的反应来实现。
具体的工艺流程如下:1. 甲烷和异丁烯的制备:甲烷(天然气)通过加热反应,在高温下与异丁烯(从石油炼制过程中分离得到)反应生成甲苯(另一种化合物)。
然后,甲苯与甲烷的混合物进一步反应,生成季戊烷(C5烃化合物)。
最后,季戊烷通过褒封分离装置进行分离,得到甲烷和异丁烯的混合物。
2. MTBE的反应:在反应器中,将得到的甲烷和异丁烯的混合物与过量的甲醇加入。
反应温度一般在0-50摄氏度之间,通常在25摄氏度左右。
同时,在反应器中加入催化剂,常用的催化剂有硫酸、氢氟酸等。
反应时间一般为几小时至几十小时。
3. MTBE的分离和提纯:反应结束后,通过蒸馏装置将反应物中的MTBE和甲醇分离。
由于MTBE和甲醇的沸点差异较大,所以可以通过蒸馏分离的方式较为简单地得到纯净的MTBE。
4. MTBE的处理和储存:经过分离和提纯后,MTBE可以进一步经过活性炭吸附、净化过滤等处理工艺,去除杂质和色度。
最后,MTBE会被储存在特殊的贮罐或罐车中,以便于运输和销售。
需要注意的是,MTBE的生产工艺中要注意工艺条件的控制和安全措施的采用,以确保反应的安全性和产品的质量。
同时,还需要根据不同地区的法律法规要求,对废水、废气等进行处理,以确保环境的安全。
以上是MTBE的生产工艺的简要介绍,通过甲烷和异丁烯的反应,可以获得MTBE这一重要的汽油添加剂,以改善汽油的性能。
mtbe工艺技术
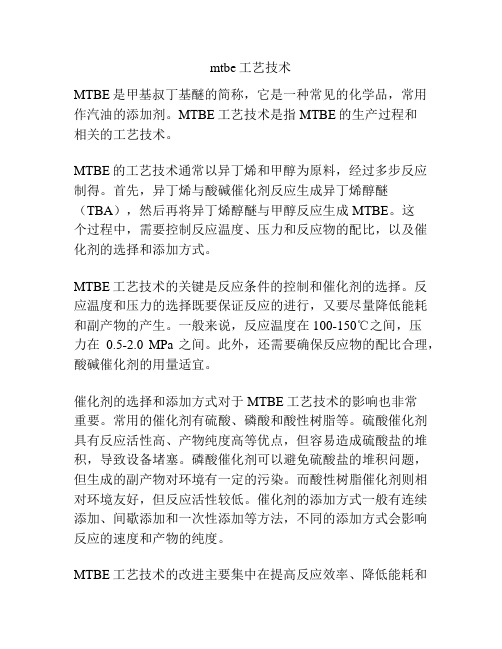
mtbe工艺技术MTBE是甲基叔丁基醚的简称,它是一种常见的化学品,常用作汽油的添加剂。
MTBE工艺技术是指MTBE的生产过程和相关的工艺技术。
MTBE的工艺技术通常以异丁烯和甲醇为原料,经过多步反应制得。
首先,异丁烯与酸碱催化剂反应生成异丁烯醇醚(TBA),然后再将异丁烯醇醚与甲醇反应生成MTBE。
这个过程中,需要控制反应温度、压力和反应物的配比,以及催化剂的选择和添加方式。
MTBE工艺技术的关键是反应条件的控制和催化剂的选择。
反应温度和压力的选择既要保证反应的进行,又要尽量降低能耗和副产物的产生。
一般来说,反应温度在100-150℃之间,压力在0.5-2.0 MPa之间。
此外,还需要确保反应物的配比合理,酸碱催化剂的用量适宜。
催化剂的选择和添加方式对于MTBE工艺技术的影响也非常重要。
常用的催化剂有硫酸、磷酸和酸性树脂等。
硫酸催化剂具有反应活性高、产物纯度高等优点,但容易造成硫酸盐的堆积,导致设备堵塞。
磷酸催化剂可以避免硫酸盐的堆积问题,但生成的副产物对环境有一定的污染。
而酸性树脂催化剂则相对环境友好,但反应活性较低。
催化剂的添加方式一般有连续添加、间歇添加和一次性添加等方法,不同的添加方式会影响反应的速度和产物的纯度。
MTBE工艺技术的改进主要集中在提高反应效率、降低能耗和减少环境污染等方面。
比如,有人提出使用新型催化剂,能够在较低的温度和压力下实现高效的反应。
还有人研究使用微波辐射技术加热反应体系,可以提高反应速率和选择性。
此外,还可以改善催化剂的再生和循环利用,减少资源的消耗和废物的排放。
总之,MTBE工艺技术是一门涉及多个领域的综合技术,需要对反应条件、催化剂和反应器设计等多个方面进行综合考虑。
随着科技的不断进步,相信MTBE工艺技术会越来越成熟和先进,为汽油添加剂生产提供更好的技术支持。
mtbe工艺流程

mtbe工艺流程
《MTBE工艺流程》
MTBE(甲基叔丁基醚)是一种重要的化工产品,主要用作汽油的添加剂,可以提高汽油的辛烷值,降低汽油的挥发性和凝固点。
MTBE的生产工艺流程主要包括醇醚法、异丁烷法和异丁烯法三种。
其中,异丁烷法是目前应用最广泛的一种工艺流程。
异丁烷法的工艺流程如下:
1. 异丁烷制取:首先,通过异丁烷裂解或者异丁烷脱氢的方式得到异丁烷。
2. 壳聚糖催化剂制备:将铝脱氧剂和氟化物调和成壳聚糖催化剂。
3. 催化裂解:将异丁烷和甲醇在壳聚糖催化剂的存在下裂解成异丁烯和乙醇。
4. MTBE合成:将裂解得到的异丁烯和乙醇在酸催化下反应成MTBE。
5. 脱水处理:将合成得到的MTBE进行脱水处理,去除多余的水分。
6. 分离和提纯:对脱水后的MTBE进行分离和提纯,得到最
终的MTBE产品。
该工艺流程具有高效、节能和资源利用率高的特点,能够满足大规模生产需求。
MTBE作为重要的汽油添加剂,在提高汽油质量和保护环境方面发挥着重要作用,其生产工艺流程的不断优化和改进也将有助于推动化工行业的可持续发展。
mtbe工艺计算参考

2.MTBE生产原理及主要生产工艺2.1生产原理2.1.1 反应机理MTBE一般是以甲醇和异丁烯为原料,在酸性催化剂的作用下合成的。
合成MTBE的催化剂主要有:氢氟酸、硫酸、苯乙烯系阳离子交换树脂、固体酸、分子筛、杂多酸等,在工业上用得最多的是树脂催化剂。
2.1.2 反应方程式MTBE的反应是一个选择性加成反应,烯烃中的叔碳原子在酸性催化剂的存在下形成正碳离子,再与醇结合形成醚。
其反应是一个可逆放热反应。
主反应CH2 CH3‖CH3—C—CH3+CH3—OH⇔CH3—C—O—CH3+(—ΔH1)CH3可能的副反应有:①异丁烯水合生成叔丁醇(TBA)CH2 CH3‖CH3—C—CH3+H2O⇔CH3—C—CH3+(—ΔH2)CH3②异丁烯二聚生成二异丁烯(DIB)③甲醇脱水生成二甲醚(DME)和水2CH3—OH⇔CH3—O—CH3+H2OΔH1(298)=36.46kJ·mol-1ΔH2(298)=69.20kJ·mol-1ΔH3(298)=34.96kJ·mol-12.2.3 生产流程MTBE合成装置包括反应系统和分离、回收系统。
工艺流程如图1.1所示。
混合C4与含水为0.05%(质量)的原料甲醇加压至1.472Mpa,并在文丘里混合器内混合后预热至47 C。
混合原料从顶部进入第一醚化反应器,反应器内装有磺酸基离子交换树脂催化剂。
醚化反应产物自反应器底部流出后减压,并和第一C4塔塔底出料进行换热,升温至泡点温度后,由中部进入第一C4塔。
反应产物在第一C4塔中分离为塔底产品(MTBE产品)和塔顶产品(未反应的C4与甲醇形成的共沸物)。
塔顶产品和循环甲醇混合后进入第二醚化反应器进行醚化反应。
第二反应器反应产物自底部流出并减压,冷却至50 C后从底部进入水洗塔,用水作溶剂萃取出未反应得甲醇。
脱甲醇的残余C4自水洗塔顶流出,进入第二C4塔中部。
水洗塔塔底产品为甲醇水溶液,进入甲醇回收塔。
年产5万吨甲基叔丁基醚生产工艺技术

年产5万吨甲基叔丁基醚生产工艺技术甲基叔丁基醚(MTBE)是一种重要的有机化工产品,具有广泛的应用领域,例如作为汽油的抗爆剂、溶剂和交联剂等。
本文将介绍一种年产5万吨MTBE的生产工艺技术。
首先,原料选择和储存是生产MTBE的关键步骤。
本工艺使用甲醇和叔丁醇作为原料,在严格控制其质量的前提下储存于密闭容器中,以防止水分和杂质的进入。
其次,本工艺采用异构化法制备MTBE。
先将甲醇和叔丁醇按一定比例混合,在反应器中控制好温度和压力条件,添加适量的酸性催化剂作为催化剂。
在均相条件下,甲醇和叔丁醇通过异构化反应聚合生成MTBE。
在反应中,需要控制好温度和压力,一般温度在40-60摄氏度之间,压力在0.1-0.2兆帕之间。
同时,需要控制反应时间,一般反应时间在2-3小时之间,以保证反应充分。
完成反应后,通过分离装置将产物分离出来。
首先,经过汽提操作去除未反应的甲醇和叔丁醇,并通过冷凝器将其回收利用。
然后,利用蒸馏塔将MTBE纯化,去除其中的杂质和水分,得到高纯度的MTBE。
最后,通过储存和包装,将MTBE产品进行整理和储存。
MTBE具有易挥发的特性,在储存和包装过程中需要采取相应措施,以避免损失和污染。
常见的包装方式包括采用密闭的钢质容器或塑料容器进行包装,并注明相应的标识和警示。
总结来说,年产5万吨MTBE的生产工艺技术主要包括原料选择和储存、异构化反应、分离纯化以及储存和包装等步骤。
通过合理控制反应条件和储存操作,可以稳定高效地生产出高纯度的MTBE产品,满足市场需求。
继续写相关内容,我们还可以探讨以下方面:1. 原料选取和储存优化:甲基叔丁基醚的质量和产率受原料质量的影响较大,因此需要选择高纯度的甲醇和叔丁醇作为原料。
同时,为了防止原料受到空气、水分和杂质的污染,需要采取严格的储存措施,例如在储存过程中可以使用干燥剂和密闭容器。
原料的纯度和储存环境的控制对最终产品的质量具有重要意义。
2. 反应条件的优化:在MTBE的生产过程中,反应温度、压力和催化剂的选择都会影响反应速率和选择性。
- 1、下载文档前请自行甄别文档内容的完整性,平台不提供额外的编辑、内容补充、找答案等附加服务。
- 2、"仅部分预览"的文档,不可在线预览部分如存在完整性等问题,可反馈申请退款(可完整预览的文档不适用该条件!)。
- 3、如文档侵犯您的权益,请联系客服反馈,我们会尽快为您处理(人工客服工作时间:9:00-18:30)。
MTBE加工工艺(1999)
甲基叔丁基醚(MTBE)辛烷值较高(RON为117,MON 为101),是生产无铅、含氧、低芳烃及高辛烷值车用汽油的优良调合组分;含氧新配方汽油的使用,更推动了MTBE等含氧高辛烷值调合组分的发展。
自1973年意大利建成世界上第一套0.1Mt/a MTBE生产装置以来,至1990年世界MTBE年产量已达10Mt,预计到2000年将达到30Mt。
MTBE是近二十几年发展最快的石油化工产品之一。
为适应石油化工发展及汽油改质的需要,自70年代末开始我国开始了MTBE生产技术的研究,先后研究并应用了列管固定床反应、固定床外循环反应、膨胀床反应、混相床反应、催化蒸馏和混相反应蒸馏等技术,这些技术已达到或超过国外同类技术水平。
至今我国已有30余套MTBE生产装置在运行或正在建设中,总生产能力超过
0.7Mt/a,预计到2000年,我国MTBE总生产能力可达
1.0Mt/a。
随着我国石油化工的发展和环境保护的日益严格,MTBE生产将有巨大的发展。
1催化剂
到目前为止,国内外MTBE生产装置大都采用大孔强酸阳离子交换树脂催化剂,其中应用最广泛的是美国Romanhass公司生产的Amberlyst-15树脂催化剂,技术比较成熟。
我国在开发MTBE生产技术的同时,也研制生产了自己的树脂催化剂,如北京大兴县树脂厂生产的S54,
天津大学生产的D72及丹东化工三厂生产的D005等树脂催化剂,均已成功地用于MTBE的工业生产。
工业应用的树脂催化剂的典型性能见表1。
2国内MTBE生产技术的现状
2.1列管固定床反应技术
采用列管固定床合成MTBE的工艺流程为:混合碳四物料中的异丁烯与甲醇在列管固定床反应器中在催化剂的作用下进行反应,反应热由壳层冷却水移走;生成的MTBE产品在共沸蒸馏塔中分离,未反应的碳四物料和甲醇从塔顶流出,经水萃取分离和甲醇精馏回收未反应的甲醇。
该技术的特点是催化剂使用效率高,但反应器结构复杂,造价高,催化剂床层中存在热点,反应热未利用,异丁烯转化率为90%~95%。
国内应用该技术的有两套MTBE生产装置,加工能力25.5kt/a。
2.2固定床外循环反应技术
采用固定床外循环反应合成MTBE的工艺流程为:混合碳四物料中异丁烯与甲醇预热到一定温度后,从顶部进入反应器,在催化剂作用下进行反应。
为了控制反应温度,将部分反应后的物料冷却后循环回反应器中;生成的MTBE产品在共沸蒸馏塔中分离,未反应的甲醇经水萃取后,到甲醇回收塔中回收。
该技术的特点是,反应器结构简单,操作灵活,但是催化剂使用效率低,反应热不能利用。
国内有21套生产装置(有的用作催化蒸馏塔的预反应器)应用此技术,加工能力约为676.5kt/a,异丁烯转化率为90%~95%。
2.3膨胀床反应技术
采用膨胀床反应合成MTBE的工艺流程为:混合碳四物料中异丁烯与甲醇以一定比例混合,预热到一定温度后从反应器底部进入反应器,在催化剂作用下进行反应。
为了控制反应温度,反应后的部分物料经冷却后循环至反应器底部;MTBE产品在共沸蒸馏塔中分离,未反应的甲醇经水萃取后,到甲醇回收塔回收。
该技术的特点是反应器结构简单,催化剂膨胀扰动,有利于反应过程中的传质和传热,从而减少副反应;但是催化剂使用效率低,反应热不能利用。
国内已采用该技术建成9套生产装置,加工能力200kt/a,异丁烯转化率为90%~95%。
2.4混相床反应技术
混相床合成MTBE的工艺流程为:混合碳四物料中异丁烯与甲醇以一定比例混合,预热到一定温度后进入反应器,在催化剂的作用下反应,反应热使反应物料温度升高。
当温度升高到操作压力下的泡点时,反应热由部分反应物料汽化吸收。
该技术的特点是反应器结构简单,利用了反应热,降低了能耗和设备投资。
目前,国内已有9套生产装置采用该技术(有的作为催化蒸馏塔的预反应器),加工能力190kt/a。
异丁烯转化率为90%~95%。
2.5催化蒸馏技术
上述几种技术的异丁烯转化率仅为90%~95%,满足不了化工生产的需要。
若要求异丁烯转化率大于99.5%,须采用反应-分离-再反应-再分离的工艺流程。
这样流程长,投资大,能耗高。
美国CDTECH公司开发了催化蒸馏技术。
该技术的特点是将反应和产品分离结合在一台设备中进行,由于反应与分离同时进行,破坏反应平衡,提高转化率,缩短工艺流程,减少设备投资,利用反应热,降低能耗。
催化蒸馏塔分为三段:上部为精馏段,中部为反应段,下部为汽提段。
由于合成MTBE用的催化剂粒径很小,直接装填到催化蒸馏塔的反应段,阻力很大,塔内向上流动的汽相物料与向下流动的液相物料不能对流穿过反应段。
为了解决这个问题,CDTECH公司开发了捆包式催化剂装填结构,催化剂包装在玻璃丝布特制的袋子中,卷成捆后装填在催化蒸馏塔中。
催化剂装填结构复杂,催化剂不易装卸,催化剂包装费用高。
国内引进该技术建有两套MTBE生产装置,预反应器采用固定床外循环反应技术。
另外,将催化剂装填在不锈钢筐中,然后置于反应段的塔板上,国内有2套MTBE生产装置采用了该技术,催化剂装卸仍然复杂,投资高。
齐鲁石油化工公司研究院开发了MP-III型催化蒸馏技术,催化剂直接堆放在反应段的催化剂床层中,并留有气相通道。
向上流动的气相物料绕过催化剂床层,塔内向下流动的液相物料直接穿过催化剂床层,在催化剂作用下进行反应;各床层之间设分馏塔板,反应与分馏交替进行,使反应达到完全或一定要求为止。
这种技术催化剂装填结构简单,投资低,反应效率高,异丁烯转化率达到99.5%以上。
其结构与工艺流程如图1所示。
国内已有11套生产装置采用该技术,加工能力372kt/a。
如果采用混相反应与催化蒸馏串联的工艺流程,反应热可全部利用。
图1新型催化蒸馏合成MTBE工艺流程
1—混相预反应器;2—MP-III型催化蒸馏塔;
3—水萃取塔;4—甲醇回收塔
2.6混相反应蒸馏技术
在混相反应技术与新型催化蒸馏技术的基础上,齐鲁石油化工公司研究院开发了混相反应蒸馏(MRD)技术,这是我国独创的合成MTBE新技术。
MRD塔的反应段包括下部混相反应区和上部催化蒸馏区。
反应原料预热到一定温度后,进入下部混相反应区顶部,强制向下流动穿过催化剂床层,并在催化剂的作用下进行反应。
反应后物料由底部流出,其气相部分与来自汽提段的气相物料一起,经过气相通道向上流动,穿过催化蒸馏区床层中的气相通道与床层间的分馏塔板。
精馏段的液相物料向下流动,穿过催化蒸馏区的催化剂床层与床层之间的分馏塔板。
液相物料在催化蒸馏区的催化剂床层中进行醚化反应,气相物料与液相物料在床层间的塔板上进行热质传递。
产品经下部汽提段由塔底出装置;未反应的碳四物料和甲醇经上部精馏段由塔顶出装置,进入甲醇回收单元。
该技术简化了工艺流程,降低了能耗。
国内已有2套生产装置采用MRD技术,加工能力25kt/a,异丁烯转化率在99.5%以上。
3国内MTBE生产装置概况
我国MTBE生产技术研究始于70年代末期,1983年在齐鲁石油化工公司橡胶厂建成第一套5.5kt/a MTBE生产装置,至今已有29套装置在运行,总生产能力为0.653Mt/a,还有10套装置在设计建设中。
这些装置全部
建成后总生产能力将达到0.79Mt/a。
从我国有关MTBE生产装置情况看,采用了已有的各种MTBE生产技术,但装置的规模较小;产品MTBE主要用作汽油调合组分,未反应的碳四物料用于生产丁烯-1的装置有5套,目前每年仅有几千吨的MTBE用作生产高纯异丁烯的原料,生产目的单一;MTBE生产的原料主要来自催化裂化装置的碳四物料,只有几套装置是用乙烯装置副产碳四物料为原料,原料资源受到限制。
4国内MTBE生产展望
随着我国环境保护法的实施,要求汽油无铅化,并使用MTBE等含氧高辛烷值调合组分,以减少汽车尾气对环境的污染。
目前,我国汽油耗量约28Mt/a,以MTBE调合量为10%计,每年就需要约2.8Mt/a的MTBE。
MTBE的生产还远不能满足需求;另外,随着石油化工的发展,需要更多的丁烯-1、丁二烯和异丁烯等化工原料,这将进一步促进MTBE新技术的发展与应用。
为此,我国应建更多的MTBE装置,以满足日益增长的需求。
目前,我国MTBE 的生产受原料限制,装置规模小。
为了扩大原料资源,可采用如下的措施:(1)利用现有的异丁烯资源最大限度生产MTBE,如炼油厂的催化裂化装置的碳四物料和乙烯装置的裂解碳四物料等,均可直接作为生产原料;(2)改进现有的炼油工艺,开发新的催化裂化技术,增加催化裂化装置的碳四物料的产量及异丁烯的含量;(3)采用异构化技术,将碳四物料中的烯烃(如丁烯-1、顺丁烯-2和反丁烯-2)异构化
为异丁烯;(4)应用丁烷异构、脱氢技术,将碳四物料中的正丁烷异构化为异丁烷,然后脱氢生产异丁烯。
5结束语
二十多年来,我国已开发了具有自己特色的合成MTBE 技术,包括树脂催化剂研制、成套技术开发及工程放大,并成功地用于工业生产,使我国的MTBE生产达到了世界先进水平。
为了适应汽油无铅化的需求,应扩大MTBE生产装置的规模,并进一步增加异丁烯原料资源。
作者简介:郝兴仁,高级工程师,1986年毕业于华东理工大学化学工程系,一直从事石油化工工艺过程的研究开发工作。
作者单位:郝兴仁杨宗仁齐鲁石油化工公司研究院(山东省淄博市255400)
收稿日期:1999-02-08。