电脑主板生产工艺及流程培训资料
电脑主板生产工艺及流程介绍
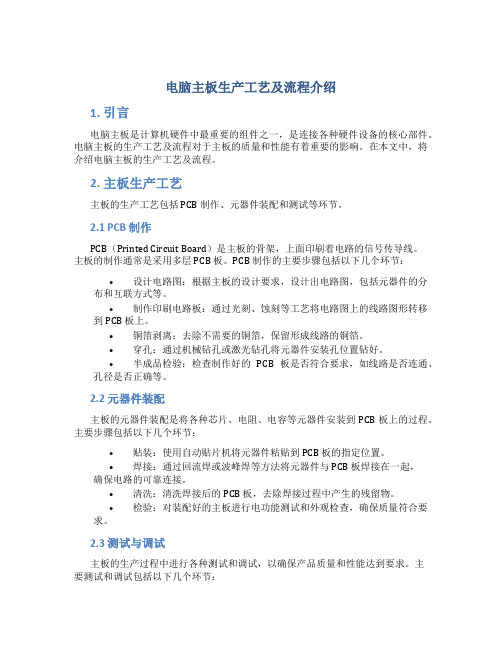
电脑主板生产工艺及流程介绍1. 引言电脑主板是计算机硬件中最重要的组件之一,是连接各种硬件设备的核心部件。
电脑主板的生产工艺及流程对于主板的质量和性能有着重要的影响。
在本文中,将介绍电脑主板的生产工艺及流程。
2. 主板生产工艺主板的生产工艺包括 PCB 制作、元器件装配和测试等环节。
2.1 PCB 制作PCB(Printed Circuit Board)是主板的骨架,上面印刷着电路的信号传导线。
主板的制作通常是采用多层 PCB 板。
PCB 制作的主要步骤包括以下几个环节:•设计电路图:根据主板的设计要求,设计出电路图,包括元器件的分布和互联方式等。
•制作印刷电路板:通过光刻、蚀刻等工艺将电路图上的线路图形转移到 PCB 板上。
•铜箔剥离:去除不需要的铜箔,保留形成线路的铜箔。
•穿孔:通过机械钻孔或激光钻孔将元器件安装孔位置钻好。
•半成品检验:检查制作好的PCB 板是否符合要求,如线路是否连通、孔径是否正确等。
2.2 元器件装配主板的元器件装配是将各种芯片、电阻、电容等元器件安装到 PCB 板上的过程。
主要步骤包括以下几个环节:•贴装:使用自动贴片机将元器件粘贴到 PCB 板的指定位置。
•焊接:通过回流焊或波峰焊等方法将元器件与 PCB 板焊接在一起,确保电路的可靠连接。
•清洗:清洗焊接后的 PCB 板,去除焊接过程中产生的残留物。
•检验:对装配好的主板进行电功能测试和外观检查,确保质量符合要求。
2.3 测试与调试主板的生产过程中进行各种测试和调试,以确保产品质量和性能达到要求。
主要测试和调试包括以下几个环节:•静态测试:通过测量电阻、电容等参数,检查主板上的电路元件是否正常。
•动态测试:通过给主板施加电压和信号,检查主板的工作状态和性能。
•BIOS 测试:对主板上的 BIOS 芯片进行测试,确保 BIOS 软件的正常工作。
•稳定性测试:持续运行主板,对其进行长时间的稳定性测试,以验证主板的耐久性和可靠性。
电脑主板生产工艺及流程介绍
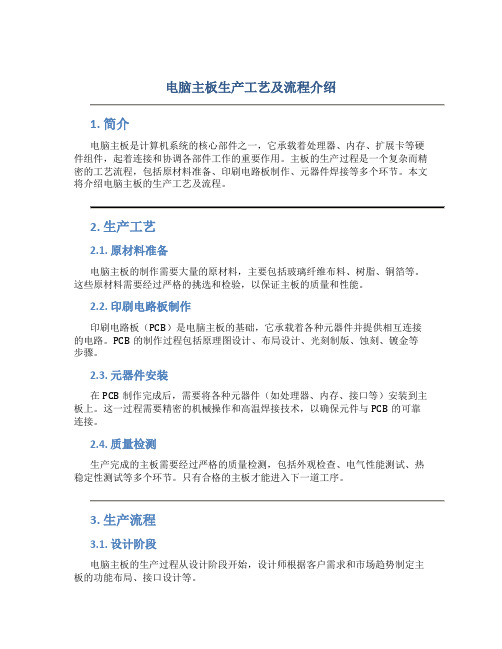
电脑主板生产工艺及流程介绍1. 简介电脑主板是计算机系统的核心部件之一,它承载着处理器、内存、扩展卡等硬件组件,起着连接和协调各部件工作的重要作用。
主板的生产过程是一个复杂而精密的工艺流程,包括原材料准备、印刷电路板制作、元器件焊接等多个环节。
本文将介绍电脑主板的生产工艺及流程。
2. 生产工艺2.1. 原材料准备电脑主板的制作需要大量的原材料,主要包括玻璃纤维布料、树脂、铜箔等。
这些原材料需要经过严格的挑选和检验,以保证主板的质量和性能。
2.2. 印刷电路板制作印刷电路板(PCB)是电脑主板的基础,它承载着各种元器件并提供相互连接的电路。
PCB的制作过程包括原理图设计、布局设计、光刻制版、蚀刻、镀金等步骤。
2.3. 元器件安装在PCB制作完成后,需要将各种元器件(如处理器、内存、接口等)安装到主板上。
这一过程需要精密的机械操作和高温焊接技术,以确保元件与PCB的可靠连接。
2.4. 质量检测生产完成的主板需要经过严格的质量检测,包括外观检查、电气性能测试、热稳定性测试等多个环节。
只有合格的主板才能进入下一道工序。
3. 生产流程3.1. 设计阶段电脑主板的生产过程从设计阶段开始,设计师根据客户需求和市场趋势制定主板的功能布局、接口设计等。
3.2. 原材料准备生产前需要准备各种原材料,包括PCB板材、元器件、焊料等。
3.3. PCB制作PCB制作是主板生产的关键环节,需要经过多道工序包括蚀刻、镀金等步骤。
3.4. 元器件安装PCB制作完成后,元器件需要按照设计要求进行安装和焊接,这个阶段需要高度的精密度和技术要求。
3.5. 质量检测生产完成的主板需要经过各种质量检测,确保产品符合标准要求。
3.6. 包装出货通过严格的检测和测试后,合格的主板进行包装,最终出货到客户手中。
4. 结论电脑主板的生产工艺和流程是一个复杂而多环节的过程,需要严格的质量管理和精密的技术操作。
只有在每个环节都严格控制质量和细节,才能保证生产出优质的主板产品。
主板生产流程
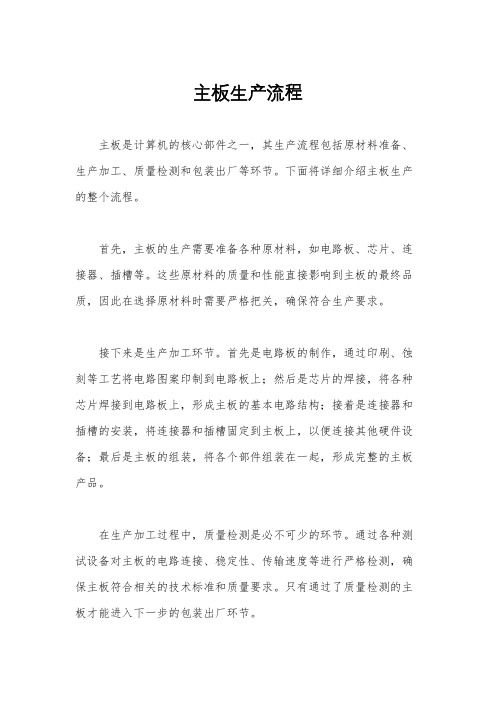
主板生产流程
主板是计算机的核心部件之一,其生产流程包括原材料准备、生产加工、质量检测和包装出厂等环节。
下面将详细介绍主板生产的整个流程。
首先,主板的生产需要准备各种原材料,如电路板、芯片、连接器、插槽等。
这些原材料的质量和性能直接影响到主板的最终品质,因此在选择原材料时需要严格把关,确保符合生产要求。
接下来是生产加工环节。
首先是电路板的制作,通过印刷、蚀刻等工艺将电路图案印制到电路板上;然后是芯片的焊接,将各种芯片焊接到电路板上,形成主板的基本电路结构;接着是连接器和插槽的安装,将连接器和插槽固定到主板上,以便连接其他硬件设备;最后是主板的组装,将各个部件组装在一起,形成完整的主板产品。
在生产加工过程中,质量检测是必不可少的环节。
通过各种测试设备对主板的电路连接、稳定性、传输速度等进行严格检测,确保主板符合相关的技术标准和质量要求。
只有通过了质量检测的主板才能进入下一步的包装出厂环节。
最后是包装出厂环节。
在这个环节中,主板需要进行外观整理和包装,确保产品的外观和包装符合市场需求,并对主板进行包装标识、防震防潮处理,最终将成品主板送入仓库,准备发往市场。
以上就是主板生产的整个流程。
每一个环节都需要严格把关,确保主板的品质和性能达到市场需求。
只有通过精心的生产流程和严格的质量控制,才能生产出优质的主板产品,满足用户的需求。
主板生产流程
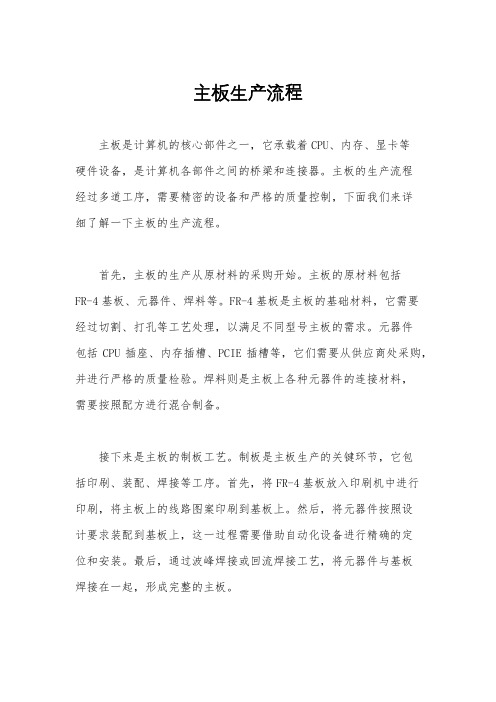
主板生产流程主板是计算机的核心部件之一,它承载着CPU、内存、显卡等硬件设备,是计算机各部件之间的桥梁和连接器。
主板的生产流程经过多道工序,需要精密的设备和严格的质量控制,下面我们来详细了解一下主板的生产流程。
首先,主板的生产从原材料的采购开始。
主板的原材料包括FR-4基板、元器件、焊料等。
FR-4基板是主板的基础材料,它需要经过切割、打孔等工艺处理,以满足不同型号主板的需求。
元器件包括CPU插座、内存插槽、PCIE插槽等,它们需要从供应商处采购,并进行严格的质量检验。
焊料则是主板上各种元器件的连接材料,需要按照配方进行混合制备。
接下来是主板的制板工艺。
制板是主板生产的关键环节,它包括印刷、装配、焊接等工序。
首先,将FR-4基板放入印刷机中进行印刷,将主板上的线路图案印刷到基板上。
然后,将元器件按照设计要求装配到基板上,这一过程需要借助自动化设备进行精确的定位和安装。
最后,通过波峰焊接或回流焊接工艺,将元器件与基板焊接在一起,形成完整的主板。
随后是主板的测试和调试。
主板制造完成后,需要进行严格的测试和调试,以确保其性能和稳定性。
测试包括外观检查、功能测试、电气参数测试等,通过这些测试可以排除制造过程中可能存在的缺陷和故障。
调试则是在测试的基础上,对主板的性能进行优化和调整,以满足不同用户的需求。
最后是主板的包装和出厂。
经过测试和调试的主板将进行包装,包装包括防静电包装、外包装等,以确保主板在运输和存储过程中不受损坏。
包装完成后,主板将被送往仓库,等待发往各个销售渠道,最终送到用户手中。
总的来说,主板的生产流程包括原材料采购、制板工艺、测试调试和包装出厂等环节,每个环节都需要严格的控制和管理,以确保主板的质量和性能。
在这个过程中,需要借助先进的设备和技术,以及严格的质量管理体系,才能生产出性能稳定、质量可靠的主板产品。
主板生产流程范文
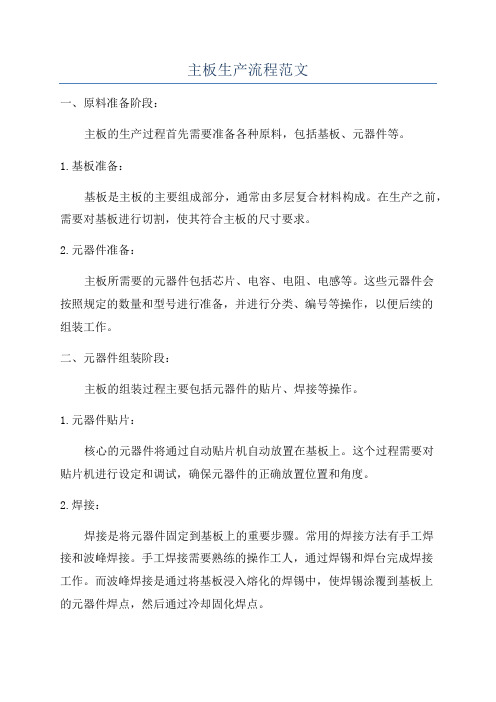
主板生产流程范文一、原料准备阶段:主板的生产过程首先需要准备各种原料,包括基板、元器件等。
1.基板准备:基板是主板的主要组成部分,通常由多层复合材料构成。
在生产之前,需要对基板进行切割,使其符合主板的尺寸要求。
2.元器件准备:主板所需要的元器件包括芯片、电容、电阻、电感等。
这些元器件会按照规定的数量和型号进行准备,并进行分类、编号等操作,以便后续的组装工作。
二、元器件组装阶段:主板的组装过程主要包括元器件的贴片、焊接等操作。
1.元器件贴片:核心的元器件将通过自动贴片机自动放置在基板上。
这个过程需要对贴片机进行设定和调试,确保元器件的正确放置位置和角度。
2.焊接:焊接是将元器件固定到基板上的重要步骤。
常用的焊接方法有手工焊接和波峰焊接。
手工焊接需要熟练的操作工人,通过焊锡和焊台完成焊接工作。
而波峰焊接是通过将基板浸入熔化的焊锡中,使焊锡涂覆到基板上的元器件焊点,然后通过冷却固化焊点。
三、主板测试阶段:为了确保主板的质量和性能,需要进行严格的测试。
1.电气测试:通过专业的测试设备对电路板进行电气测试,测试各个引脚的连通性和电阻值等参数。
如果测试结果不符合要求,则需要进行修复或返工。
2.功能测试:将装配完成的主板插入测试设备中,对主板进行功能测试。
测试设备会模拟各种使用场景和负载条件,检测主板在不同工作状态下的性能。
四、焊接阶段:主板测试完成后,还需要进行其他焊接工作。
1.插件焊接:将插座、接口等插件焊接到主板上,为其他设备的连接提供接口。
2.引脚修整:通过修整和清洁电路板上的引脚,确保引脚的完整性和连通性。
五、质量检验阶段:在主板生产的最后阶段,还需要进行质量检验,确保主板符合质量要求。
1.外观检查:检查主板面板的质量和外观,包括颜色、印刷质量、尺寸等。
2.性能测试:再次对主板进行性能测试,确保主板在各项指标上都符合要求。
六、包装和出货阶段:完成质量检验后,主板将进行包装和出货。
1.包装:将主板放入专用的包装盒中,并加入缓冲材料,保护好主板不受损。
电脑板基本知识培训资料
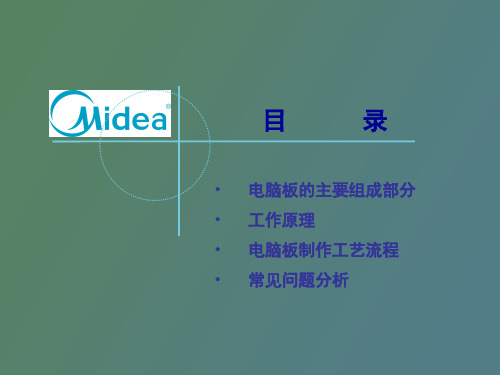
电源部分电路原理图
桥堆
上图中【T1】为变压器,其作用是将AC 120/220/230V的交流电降压为 AC7V、AC11V两组交流电,然后通过图中的“桥堆”,实现全波整流, 转化为直流电,再通过电容的滤波作用,滤除整流后的杂波信号,实现波 形较平整的直流电。
下图即为变压器实物照片。变压器右侧的四个二极管即组成了“桥堆”, 实现交流电到直流电的转换,故这些二极管称为“整流二极管”。
5.显示不良:给电脑板通用电后,一般LED显示屏会显示 “0:00”,在按其它按键前,LED显示屏的其它部分均不能点 亮。 若有其它部分的暗亮、串亮(即该点亮的部分周围的显示屏有 亮光)均属于显示不良问题。若上电后显示不全、暗亮、串亮 等现象,可能的原因有: (1)显示屏损坏。 (2)显示部分的电路有短路、断路现象。 (3)显示部分电路元件误装、漏装。 (4)程序错误或单片机损坏。
目
录
• 电脑板的主要组成部分 • 工作原理 • 电脑板制作工艺流程 • 常见问题分析
一、电脑板的组成
电脑板主要由以下几个部分组成:
按功能分: (1)电源部分:为电脑板主要部件提供电源 (2)显示部分:显示主要功能及时间等参数 (3)按键扫描电路:将“按键输入”转化为功能输出。 (4)负载部分:驱动蜂鸣器、继电器等负载。 (5)单片机外围电路:保证单片机正常工作。
② 触点烧坏:上述负载不能启动。 对上述问题的检测,可用万用表的 欧姆档测量触点之间的电阻值。
(2)MICRO继电器:微波继电器控制微波炉高压变压器 的启动,以控制磁控管的微波输出。目前外销的微波继 电器一般为“淞川”302WP-1AH-C。
微波继电器损坏则直接导致微 波输出的不正常。特别是触点粘结 将造成在关门状态下微波一直输出 可能造成起火。
笔记本主板制作过程与技术解析说明书

Pin in paste stencil design for notebook mainboardPin in paste stencil design for notebook mainboardEveryday laptops we use are a little bit more than a keyboard and an LCD screen. If we take our time to take a look under the hood, we’ll find a complex notebook mainboard together with many additional components. Less space, more functionality is what a laptop stands for, and a notebook mainboard is probably one of the most dense, compact and complex electronic assemblies in use today.Traditional SMT process calls for screen printing, component placement and reflow phases, respectively for each side. The exception would be adding THTs and processing them together with SMDs ina single operation. However, when we go deeper into the process, we see it is not that simple.As the surface mount componentsget smaller, and the component density increases as a result, soldering becomes a challenging task. Soldered joints are not always accessible for some components like QFNs and BGAs, since they are covered by the component body itself. These SMDs for sure require extra care, but what if we like to solder all THTs on a single pass together with them?A notebook mainboard is a 1,2 mm thick 6 to 8 layer board with more than 2000 components on it. Our aim is to complete the soldering process aftertwo reflow cycles and send the board immediately to ICT. In order to make this happen, first we should define all process parameters. On the first pass we will have only SMDs in place, but on the second pass THTs will come into stage.In this article, we focus on the bottom side stencil and will define the stencil construction and aperture design requirements. There are strict procedures that govern the manufacture of stencils in any SMT production environment but I will try to keep our vision as wide as possible.If we consider a seamless placement process where no placement issues are apparent–• All SMDs are placed with high accuracy.• THT devices are either manually placed of placed in automation withrequired accuracy and pressure. (InVestel Digital all devices are placedin automation by the help of specialnozzles and gripper arms.)–then the key parameters left will be stencil design and reflow profile.Pin in hole reflow techniqueHow to incorporate through hole components into the reflow soldering process? This question is the rally point for a simple to understand but hard to follow task. The pin in hole or pin in paste method lets the PCB go through the reflow oven once it is completely placed and,as a result, everything becomes ‘soldered’ right after the oven. In this process, paste is applied to all SMD pads, and holes are filled with solder for THT components.The difference from the SMD screen printing process is that the amount of solder pushed into the holes is more than the amount applied for regular pads–overprinting. Multilayer stencil requirement Consistent stencil design requires a clear definition of aperture parameters for each and every special component. Special components are the ones that need to be validated when a new process parameteris conducted or modified. On a typical notebook mainboard, 0.8 mm pitchand 1,27 mm pitch BGAs, 0.4 mm fine pitch QFPs, 0.5 pitch QFNs, 0.5 pitch connectors and all leaded peripherals–the so called THTs–sit on the same surface. Since our aim is to solder them all on a single pass, we will exercise extra careon each of them in order to optimize the stencil design for a repeatable process.Let us consider the bottom side of a notebook mainboard and identify the stencil design parameters for each special SMD. Chipset BGABall Pitch : 0.8 mmBall Diameter : 0.358 mmRule 1: The ratio of the round aperture’s surface area divided by the surface area of the side walls of the hole should be greaterThis paper examines theconstruction of a notebookmainboard with more than2000 components and no wavesoldering required.The board contains standardSMD, chipset BGAs, connectors,through hole components and oddforms placed using full automationand soldered after two reflowcycles under critical processparameters. However, state ofthe art technology does not help ifthe process parameters are not setcarefully. Can all complex BGAs,THT s and even screws be solderedon a single stencil? What will helpus overcome bridging, insufficientsolder and thombstoning issues?This paper will demonstratethe placement of all odd shapecomponents using pin-in-pastestencil design and full completionof the motherboard after tworeflow cycles.Keywords: Screen Printing,Stencil, Multilayer, Fine Pitch,ElectroformAtilim Demirtas, Vestel Digital, Manisa, Turkey 28 – Global SMT & Packaging - February 2008Equation 1 half of it shrinks. The multiplier ‘2’ is the shrinkage factor and compensates for anyMore possibilities with Selective SolderingSee what the SPA rangefrom EBSO can do for you*************。
电脑主板生产工艺及流程11
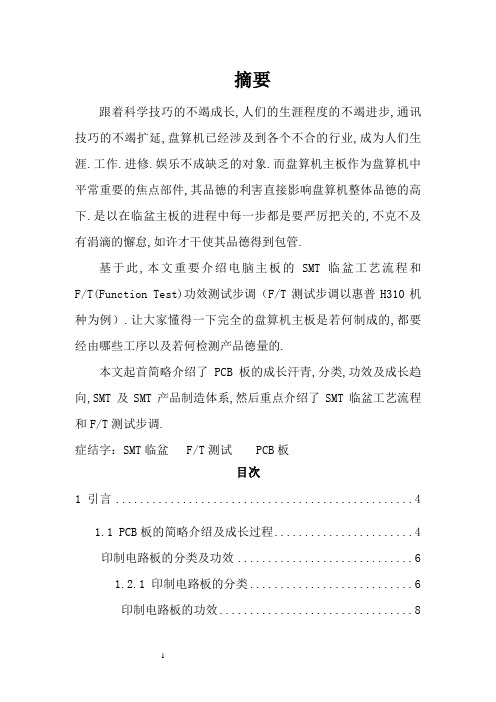
摘要跟着科学技巧的不竭成长,人们的生涯程度的不竭进步,通讯技巧的不竭扩延,盘算机已经涉及到各个不合的行业,成为人们生涯.工作.进修.娱乐不成缺乏的对象.而盘算机主板作为盘算机中平常重要的焦点部件,其品德的利害直接影响盘算机整体品德的高下.是以在临盆主板的进程中每一步都是要严厉把关的,不克不及有涓滴的懈怠,如许才干使其品德得到包管.基于此,本文重要介绍电脑主板的SMT临盆工艺流程和F/T(Function Test)功效测试步调(F/T测试步调以惠普H310机种为例).让大家懂得一下完全的盘算机主板是若何制成的,都要经由哪些工序以及若何检测产品德量的.本文起首简略介绍了PCB板的成长汗青,分类,功效及成长趋向,SMT及SMT产品制造体系,然后重点介绍了SMT临盆工艺流程和F/T测试步调.症结字:SMT临盆 F/T测试 PCB板目次1 引言 (4)1.1 PCB板的简略介绍及成长过程 (4)印制电路板的分类及功效 (6)1.2.1 印制电路板的分类 (6)印制电路板的功效 (8)印制电路板的成长趋向 (8)1.4 SMT简介 (8)1.5 SMT产品制造体系 (11)2 SMT临盆工艺流程 (11)来料检测 (12)2.2 锡膏印刷机 (12)印刷机的根本构造 (13)2.2.2 印刷机的重要技巧指标 (13)2.2.3 印刷焊膏的道理 (14)2.3 3D锡膏检测机 (14)2.4 贴片机 (15)贴片机的的根本构造 (16)贴片机的重要技巧指标 (16)2.4.3 主动贴片机的贴装进程 (17)2.4.4 持续贴装临盆时应留意的问题 (17)再流焊(Reflow soldring) (18)再流焊炉的根本构造 (18)再流焊炉的重要技巧指标 (19)再流焊道理 (19)再流焊工艺特色(与波峰焊技巧比拟) (20)再流焊的工艺请求 (21)DIP插接元件的装配 (21)波峰焊(wave solder) (22)波峰焊工艺 (22)2.7.2 波峰焊操纵步调 (23)2.7.3 波峰焊道理 (25)双波峰焊理论温度曲线 (27)2.7.5 波峰焊工艺对元器件和印制板的根本请求 (27)3 焊接及装配质量的检测 (28)3.1 AIO(automatic optical inspection)检测 (28)概述 (28)3.1.2 AOI检测步调 (30)3.2 ICT在线测试 (31)3.2.1 慨述 (31)3.2.2 ICT在线测试步调 (32)4 MAL段工作流程 (33)4.1 MAL锁附站需手工装配的零件 (34)4.2 MAL LQC目检的项目 (34)4.2.1 S1面磨练项目 (35)4.2.2 S2面磨练项目 (36)5 F/T(Function Test) 测试程序 (36)测试治具的熟悉 (37)5.2 拆装测试治具步调 (37)5.3 DOS体系下测试程序 (39)电源开机测试 (39)5.3.2 Scan Sku 测试 (40)5.3.3 微动开关测试 (40)烧录Lan Mac ID 测试 (40)电池电量测试及LCD EDID测试 (41)5.4 WINDOWS体系测试程序 (41)体系组态测试 (41)5.4.2 无线网卡/WWAN测试 (42)5.4.3 音效测试 (42)5.4.4 键盘触控按键测试 (42)LED Test (43)5.4.6 MS & MMC & SD & XD & NEW Disk Card Test ..43检讨条码测试 (44)停止语 (44)申谢 (45)参考文献 (46)1 引言1.1 PCB板的简略介绍及成长过程印刷电路板(Printed Circuit Board)简称PCB,又称印制板,是电子产品的重要部件之一.用印制电路板制造的电子产品具有靠得住性高.一致性好.机械强度高.重量轻.体积小.易于尺度化等长处.几乎每种电子设备,小到电子手表.盘算器,大到盘算机.通讯设备.电子雷达体系,只要消失电子元器件,它们之间的电气互连就要应用印制板.在电子技巧成长的早期,电路由电源.导线.开关和元器件构成.元器件都是用导线衔接的,而元件的固定是在空间中立体进行的.跟着电子技巧的成长,电子产品的功效.构造变得很庞杂,元件计划.互连布线都受到很大的空间限制,假如用空间布线方法,就会使电子产品变得目眩纷乱.是以就请求对元件和布线进行计划.用一块板子作为基本,在板上计划元件的计划,肯定元件的接点,应用接线柱做接点,用导线把接点按电路请求,在板的一面布线,另一面装元件.这就是最原始的电路板.这种类型的电路板在真空电子管时期平常风行,因为线路都在同一个平面散布,没有太多的隐瞒点,检讨起来轻易.这时电路板已初步形成了“层”的概念. 单面敷铜板的创造,成为电路板设计与制造新时期的标记.布线设计和制造技巧都已成长成熟.先在敷铜板上用模板印制防腐化膜图,然后再腐化刻线,这种技巧就象在纸上印刷那样轻便,“印刷电路板”是以得名.跟着电子技巧成长和印制板技巧的进步,消失了双面板,即在板子两面都敷铜,两面都可腐化刻线. 跟着电子产品临盆技巧的成长,人们开端在双面电路板的基本上成长夹层,其实就是在双面板的基本上叠加上一块单面板,这就是多层电路板.起先,夹层多用做大面积的地线.电源线的布线,表层都用于旌旗灯号布线.后来,请求夹层用于旌旗灯号布线的情形越来越多,这使电路板的层数也要增长.但夹层不克不及无穷增长,重要原因是成本和厚度问题.是以,电子产品设计者要斟酌到性价比这个抵触的分解体,而最现实的设计办法仍然是以表层做旌旗灯号布线层为首选.高频电路的元件也不克不及排得太密,不然元件本身的辐射会直接对其它元件产生干扰.层与层之间的布线应错开成十字走向,以削减布线电容和电感.1.2 印制电路板的分类及功效印制电路板的分类依据软硬进行分类:通俗电路板和柔性电路板.依据电路层数分类:分为单面板.双面板和多层板.罕有的多层板一般为4层板或6层板,庞杂的多层板可达十几层.从1903年至今若以PCB组装技巧的应用和成长角度来看可分为三个阶段:(THT)阶段PCB1).金属化孔的感化:①.电气互连---旌旗灯号传输②.支持元器件---引脚尺寸**通孔尺寸的缩小a.引脚的刚性b.主动化插装的请求2).进步密度的门路①.减小器件孔的尺寸,但受到元件引脚的刚性及插装精度的**,孔径≥0.8mm②.缩小线宽/间距:0.3mm—0.2mm—0.15mm—0.1mm③.增长层数:单面—双面—4层—6层—8层—10层—12层—64层2.概况装配技巧(SMT)阶段PCB1).导通孔的感化:仅起到电气互连的感化,孔径可以尽可能的小,堵上孔也可以.2).进步密度的重要门路①.过孔尺寸急剧减小:0.8mm—0.5mm—0.4mm—0.3mm—0.25mm②.过孔的构造产生本质变更:a.埋盲孔构造长处:进步布线密度1/3以上.减小PCB尺寸或削减层数.进步靠得住性. 改良了特征阻抗掌握,减小了串扰.噪声或掉真(因线短,孔小)b.盘内孔(hole in pad)清除了中继孔及连线③薄型化:双面板:1.6mm—1.0mm—0.8mm—0.5mm④PCB平整度:a.概念:PCB板基板翘曲度和PCB板面上衔接盘概况的共面性.翘曲度是因为热.机械引起残留应力的分解成果c.衔接盘的概况涂层:HASL.化学镀NI/AU.电镀NI/AU…(CSP)阶段PCBCSP以开端进入急剧的变动于成长其之中,推进PCB技巧不竭向前成长, PCB工业将走向激光时期和纳米时期.印制电路板的功效印制电路板在电子设备中具有如下功效:. 供给集成电路等各类电子元器件固定.装配的机械支持,实现集成电路等各类电子元器件之间的布线和电气衔接或电绝缘,供给所请求的电气特征. 为主动焊接供给阻焊图形,为元件插装.检讨.维修供给辨认字符和图形. 电子设备采取印制板后,因为同类印制板的一致性,防止了人工接线的错误,并可实现电子元器件主动插装或贴装.主动焊锡.主动检测,包管了电子产品的质量,进步了劳动临盆率.降低了成本,并便于维修.1.3 印制电路板的成长趋向印制板从单层成长到双面板.多层板和挠性板,其实不竭地向高精度.高密度和高靠得住性偏向成长.不竭缩小体积.削减成本.进步机能,使得印制板在将来电子产品的成长进程中,仍然保持壮大的性命力. 将来印制板临盆制造技巧成长趋向是在机能上向高密度.高精度.细孔径.细导线.小间距.高靠得住.多层化.高速传输.轻量.薄型偏向成长.1.4 SMT简介跟着科学技巧敏捷成长以及信息技巧的快速推广与应用,电子产品已逐渐成为了人们生涯中不成缺乏的物资资本及公平易近经济的重要构成部分,电子产品制造已慢慢成长成为一门新兴的行业与技巧,成为了现代制造业的重要分支[1],对公平易近经济的成长,对国度分解国力的表现与进步都起到了积极和重要的促进感化.跟着电子产品的微型化.轻量化.集成化.高密度化和高靠得住性的成长,基于基板的板级电子电路产品就成了电子产品的重要情势,板级电子电路产品的制造技巧程度就成为表现现代电子产品制造技巧的重要标记.继手工插装.半主动化插装.全主动插装之后的第四代电子电路制造技巧,概况组装技巧 (SurfaceMountTechnology,SMT)的鼓起和成长摇动了传统板级电子电路产品的组装概念,转变了电子元器件通孔插装技巧(ThroughHoleTechnology,THT)的制造情势,引起了电子产品制造的技巧革命,被称为是电子产品制造技巧的“第二次革命”,并慢慢成长成为融会微电子学.电子材料.半导体集成电路.电路设计主动化 (Eleetronieoesi,Automation,EnA)盘算机帮助测试和先辈制造等各项技巧在内的现代先辈电子制造技巧,该技巧是一项涉及到微电子.周详机械主动掌握.焊接.精致化工.材料.检测等多专业和多学科的新兴.分解性工程科学技巧[2].SMT组装分为芯片级组装(常称为封装或一级封装)和板级组装(也称为二级封装).芯片级组装是将硅片(芯片)贴装在基片上,然后经由过程封接或软钎焊焊接到基板上成为完全的元件.板级组装是将元件贴装在通俗混装印制电路板(PriniedCireuitBoard,PCB)或概况装配印制电路板(SurfaceMount Printed Circuit Board)上.与传统的通孔插装技巧比拟较,采取SMT技巧进行电子产品组装的优胜性重要表如今以下几个方面[3]:1.SMT元器件体积小.重量轻.集成度高.功效多.可贴装于PCB 两面,并使包含立体组装在内的高密度组装成为可能.因为概况贴装元件(SurfaceMountComponent,SMC)和概况贴装器件(surfaeeMountDeviee,SMD)的体积.重量只有传统元器件的1/10,由其构成的PCB模块体小.量轻,可使响应的电子设备和产品体积缩小40~60%,重量减轻60一80%,其大幅度微型化后果明显,应用面极其普遍.尤其是在航空航天和军事设备范畴,应用SMT技巧使产品微型化的意义更为重大.2.SMT产品所采取的SMC.SMD均为无引脚或短引脚,削减了因为引线长度引起的寄生电感和电容,从而削减了电磁干扰和射频干扰,改良了PCB模块和电子设备体系的高频特征.3.SMT产品制造易于实现主动化.降低制造成本.并能经由过程采取散热.抗振高质SMC和主动化组装,改良产品的抗冲击.振动特征,使产品的组装靠得住性大幅度进步.SMT被普遍应用于电子.航空.航天.军事.船舶.汽车.机械.内心等诸多范畴,并且已进入以微组装技巧.高密度组装和立体组装技巧为标记的先辈电子制造技巧新阶段,以及多芯片组件.球型栅格阵列.芯片尺寸封装等新型概况组装元器件的快速成长和大量应用阶段[4].跟着SMT在各个范畴尤其是军事尖端技巧范畴的应用和推广,为电子产品的进一步微型化.薄型化.轻量化和高靠得住性开拓了辽阔的远景,对公平易近经济成长和军事电子设备的现代化正在起着积极的推进感化.1.5 SMT产品制造体系SMT产品制造体系是以SMT为焦点制造技巧手腕,以SMT产品为制造对象的制造体系,根本构成情势是由概况组装设备构成的临盆线,概况组装设备经由过程主动传输线衔接在一路,并设置设备摆设盘算机掌握体系,掌握PCB的主动传输和各组装设备和流水组假装业.广义的SMT产品制造体系是一个以客户需求为目标.以客不雅物资手腕为对象,采取有用的办法,将产品由概念设计转化为最终物资产品,投放市场的制造进程.包含市场调研与猜测.产品设计.工艺设计.临盆加工.质量包管.临盆进程治理.营销.售后等产品全性命周期内一系列互相接洽的活动,SMT产品制造资本是完成SMT产品的全部性命周期所有的临盆活动的物理元素的总称,如图l一1所示[5].图1-1 SMT产品制造体系示意图2 SMT临盆工艺流程来料检测 --> PCB的B面丝印焊膏(点贴片胶) --> 贴片--> 烘干(固化) --> 回流焊接 --> 翻板 --> PCB的A面丝印焊膏 --> 贴片 --> 烘干 --> 回流焊接 --> 插件 --> 波峰焊 --> 清洗 --> 检测 --> 返修2.1 来料检测在临盆组装进程中,平日由委托公司供给PCB和电子元器件,在进入临盆线之前,必须对它们进行品德磨练,这个进程称为IQC(进料品管).PCB的磨练除了肉眼的概况检讨外,还必须应用检测仪器对基板的厚度.插件针孔进行检讨,元器件则包含各类电阻.电容的阻值.容值以及断路.短路等.经由过程IQC磨练的PCB和元器件才干进入下一道工序.因而,加工前的测试对主板全部临盆进程供给了重要包管,有助于进步产品的良品率.2.2 锡膏印刷机SMT临盆线感化是装配渺小的贴片式元件和一些人工无法完成的多引脚IC芯片,在贴片之前,必须在PCB的针孔和焊接部位刮上焊锡膏,这是应用锡膏印刷机来完成的.把PCB板放在锡膏印刷机的操纵台上,操纵工人应用一张与PCB针孔和焊接部位雷同的钢网进行对位,这个进程可用监督器不雅察,以确保定位精确.然后锡膏印刷机的涂料手臂动作,透过钢网响应地位将焊锡膏平均.无误差地涂在PCB板上,为元器件的焊接做预备,再奉上SMT临盆线.如图2-1刮刀钢板PCB图2-1 锡膏印刷机整体外不雅及内部构造印刷机的根本构造a. 夹持基板(PCB)的工作台b. 印刷头体系c. 丝网或模板以及丝网或模板的固定机构d. 包管印刷精度而设置设备摆设的定位.清洗.二维.三维测量体系等选件.e. 盘算机掌握体系印刷机的重要技巧指标a. 最大印刷面积:依据最大的PCB尺寸肯定.b. 印刷精度:一般请求达到±0.025mm.c. 印刷速度:依据产量请求肯定.印刷焊膏的道理焊膏和贴片胶都是触变流体,具有粘性.当刮刀以必定速度和角度向前移动时,对焊膏产生必定的压力,推进焊膏在刮板前滚动,产生将焊膏注入网孔或漏孔所需的压力,焊膏的粘性摩擦力使焊膏在刮板与网板交代处产生切变,切变力使焊膏的粘性降低,使焊膏顺遂地注入网孔或漏孔.如图2-2a在刮板前滚动进步 b 产生将焊膏注入漏孔的压力 c切变力使焊膏注入漏孔刮刀的推进力F 可分化为推进焊膏进步分力X 和将焊膏注入漏孔的压力Yd焊膏释放(脱模)图2-2 焊膏印刷道理示意图2.3 3D 锡膏检测机3D 锡膏检测机是一台锡膏厚度测试仪,他的感化是检测锡膏的“高度”“面积”“体积”个中最重要的是检测“高度”,众刮板模板 PCB 焊膏所周知锡膏数目是断定焊点质量及其靠得住性的一个重要指标.100%的采取锡膏检测(SPI)将有助于削减印刷流程中产生的焊点缺点,并且可经由过程最低的返工(如清洗电路板)成本来削减废品带来的损掉,别的一个利益是焊点的靠得住性将得到包管.2.4 贴片机SMT临盆线是经由过程贴片机(如图2-3)进行的,贴片前必须在贴片机前面装上原料盘(如图2-4),贴片式元件都是附在原料盘传输纸带上的原料盒上,大型的BGA封装的芯片(如“主板芯片组”)的原料盘则放在贴片机后面.操纵进程经由过程单片机编制的程序设定来完成,并应用了激光对中校订体系.贴片时贴片机按照预设的程序动作,机械手臂在响应的原料盘上应用吸嘴汲取元件,放到PCB对应地位,应用激光对中体系进行元件的校订操纵,最后将元件压放在响应的焊接地位.在一台高速贴片机上平日有多个原料盘同时进行工作.但元件大小应当相差不久不多,以利于机械手臂操纵.一条完全的SMT临盆线是由几台高速贴片机来完成的,依据元件大小不合.贴片机元件吸嘴均不雷同,平日情形下是先贴上小元件(如“贴片电阻”),接着对较大的芯片(如“主板芯片组”)进行贴片装配.图2-3 贴片机整体外不雅图2-4 贴片机原料盘贴片机的的根本构造a. 底座b. 供料器.c. 印制电路板传输装配d. 贴装头e. 对中体系f. 贴装头的X.Y轴定位传输装配g. 贴装对象(吸嘴)h. 盘算机掌握体系贴片机的重要技巧指标a. 贴装精度:包含三个内容:贴装精度.分辩率.反复精度贴装精度——是指元器件贴装后相对于印制板尺度贴装位偏移量,一般来讲,贴装Chip元件请求达到±0.1mm,贴装高窄间距的SMD至少请求达到±分辩率——分辩率是贴装机运行时每个步进的最小增量.反复精度——反复精度是指贴装头反复返回标定点的才能—0.6S/ Chip元件阁下.c. 对中方法:有机械对中.激光对中.全视觉对中.激光/视觉混杂对中.d. 贴装面积:指贴装头的活动范围,可贴装的PCB尺寸,最大PCB尺寸应大于250×300 mm.×03 mm~最大60×60mm器件,还可以贴装衔接器等异形元器件.f. 可贴装元件种类数:是指贴装机料站地位的若干(以能容纳8 mm编带的数量来权衡).g. 编程功效:是指在线和离线编程优化功效.主动贴片机的贴装进程a.拿取PCB时不要用手触摸PCB概况,以防破坏印刷好的焊膏;b. 报警显示时,应立刻按下警报封闭键,检讨错误信息并进行处理;c. 贴装进程中填补元器件时必定要留意元器件的型号.规格.极性和偏向;d. 贴装进程中,要随时留意废料槽中的弃料是否聚积过高,并及时进行清算,使弃不克不及高于槽口,以免破坏贴装头;2.5 再流焊(Reflow soldring)再流焊炉(图2-6)是焊接概况贴装元器件的设备.再流焊炉重要有红外炉.热风炉.红外加热风炉.蒸汽焊炉等.今朝最风行的是全热风炉以及红外加热风炉.所有贴片元件装配完成后,及格的产品将送入再流焊接机.再流焊接机采取分为多个温区的内轮回式加热体系,因为焊锡膏采取多种材质构成,温度的不合将引起锡膏状况的转变.在高温区时焊锡膏变成液化状况,贴片式元件轻易与焊接相联合;进入较冷温区后,焊锡膏变成固体状况,就将元件引脚和PCB紧紧焊接起来了.图2-6 再流焊接机再流焊炉的根本构造a. 炉体b. 高低加热源c. PCB传输装配d. 空气轮回装配e. 冷却装配f. 排风装配g. 温度掌握装配h. 以及盘算机掌握体系再流焊炉的重要技巧指标a. 温度掌握精度:应达到±—℃;b. 传输带横向温差:请求±5℃以下;c. 温度曲线测试功效:假如设备无此设置设备摆设,应外购温度曲线收集器;d. 最高加热温度:一般为300—350℃,假如斟酌无铅焊料或金属基板,应选择350℃以上.e. 加热区数目和长度:加热区数目越多.加热区长度越长,越轻易调剂和掌握温度曲线.一般中小批量临盆选择4—5温区,加热区长度1.8m阁下即能知足请求.f. 传送带宽度:应依据最大和最小PCB尺寸肯定.再流焊道理图2-7 再流焊温度曲线从温度曲线(见图2-7)剖析再流焊的道理:当PCB进入升温区(干区)时,焊膏中的溶剂.气体蒸发掉落,同时,焊膏中的助焊剂润湿焊盘.元器件端头和引脚,焊膏软化.塌落.笼罩了焊盘,将焊盘.器件引脚与氧气隔离;PCB进入保温区时,使PCB和元器件得到充分预热,以防PCB忽然进入焊接高温区而破坏PCB和元器件;当PCB进焊接区时,温度敏捷上升使焊膏达到熔化状况,液态焊锡对PCB的焊盘,元器件端头和引脚润湿.集中.漫流或回流混杂形成焊锡接;PCB 进入冷却区,使焊点凝固.此时完成了再流焊.再流焊工艺特色(与波峰焊技巧比拟)a. 不像波峰焊那样,要把元器件直接浸渍在熔融的焊估中,所以元件受到的热冲击小.但因为再流焊加热办法不合,有时会施加给器较大的热应力;b. 只须要在焊盘上施加焊料,并能掌握焊料的施加量,防止了虚焊桥接等焊接缺点的产生,是以焊接质量好,靠得住性高;c. 有自定位效应(self alignment)—当元器件贴放地位有一点偏时,由于熔融焊料概况张力感化,当其全体焊端或引脚与响应焊盘被润湿时,在概况张力感化下,主动被拉回到近似目标地位的.d. 焊估中不会混入不纯物,应用焊膏时,能精确地包管焊料的成分.e. 可以采取局部加热热源,从而可在同一基板上,采取不合焊接工艺进行焊接;f. 工艺简略,修板的工作量微小.从而节俭了人力.电力.材料.再流焊的工艺请求a. 要设置合理的再流焊温度曲线—-再流焊是SMT临盆中症结工序,依据再流焊道理,设置合理的温度曲线,才干包管再流焊质量.不适当的温度曲线会消失焊接不完全,虚焊.元件翘立.焊锡球多等焊接缺点,影响产品德量.要按期做温度曲线的及时测试.b. 要按照PCB设计时的焊接偏向进行焊接.c. 焊接进程中,在传送带上放PCB要轻轻地放安稳,谨防传送带震撼并留意在机械出口处接板,防止后出来的板掉落落在先出来的板上碰伤SMD引脚.d. 必须对首块印制板的焊接后果进行检讨.检讨焊接是否充分有无焊膏熔化不充分的陈迹.焊点概况是否滑腻.焊点外形是否呈半月状.锡球和残留物的情形.连焊和虚焊的情形.还要检讨PCB概况色彩变更情形,再流焊后许可PCB有少许但是平均的变色.并依据检讨成果调剂温度曲线.在整批临盆进程中要准时检讨焊接质量.DIP插接元件的装配经由过程SMT临盆线的PCB可以说是主板的半成品,相对于它的机械化设备智能操纵,DIP插接临盆线要简略得多,它是由工作人员手工完成的.插接元件重要包含:I/O接口. CPU插座.PCI/AGP插槽;内存插槽.BIOS插座.电容.跳线.晶振等.插接之前的元件都必须经由IQC检测,对于一些引脚较长的电容.电阻还要进行修剪,以便插接操纵.PCB奉上DIP临盆线后,操纵工人按照预定的插接次序将部件插在PCB的响应地位,全部工序由多名操纵工人完成.如图2-8 (a)手工电容等元器件 (b)每个工人负责一个自力的工序(c)手工插装I/O接口.内存插槽等 (d)完成图2-8 手插件工序图2.7 波峰焊(wave solder)所有指定元件插接到PCB后经由过程传输带主动送入波峰焊接机(如图2-9),波峰焊接机是主动的焊接设备,在它的前段将给要焊接的插接件喷上助焊剂,经由过程不合的温区变更对PCB加热.波峰焊机的后半部是一个高温的液态锡炉,它平均安稳地流淌,为了防止它的氧化,平日在它的概况还笼罩着一层油.PCB传过来后应用其高温的液态锡和助焊剂的感化将插接件紧紧焊接在PCB上.图2-9 波峰焊接机波峰焊工艺波峰焊重要用于传统通孔插装印制电路板电装工艺,以及概况组装与通孔插装元器件的混装工艺,波峰焊是应用熔融焊料轮回流淌的波峰与装有元器件的PCB焊接面相接触,以必定速度相对活动。
主板生产流程课件

• a.提取元件
• b.元件判定
• c.元件旋转
• d.元件定位
• e.系统传感
贴装头
供料系统
• 供料系统:工作原理根据不同零件的包装方来选择相
同类型型的供料器(Feeder),配合机器的供料装置的供料 装置。作用是将元件按照一定的规律和顺序提供给贴片以 便准确方便的拾取。供料器通常有带状、管状、盘状和散 料
贴片机基本构造
构成组件:机架、PCB传送机构、贴装头、供 料系统、X/Y伺服定位系统、光学识别系统、 控制系统、传感器系统
机架:机架是机器的基础,是传动、定位、传送平 台的机械结构。大部分型号贴片机及其各种送料器 安装在上面。因此机架应有足够机械强度和刚性。 PCB传送机构:作用是将需要贴片的PCB从导轨送到 预定位置,贴装完成后送至另一道工序。
种类 高速机
超高速
特点
采用固定多头(约6头)或双组贴片头,种类最多,生 产厂家最多 采用旋转式多头系统。(安比昂)Assembleon-FCM型 和(富士)FUJI-QP-132型贴片机均装有16个贴片头
功能分
贴装方式 分
自动化程 度
高速/超高速 多功能 同时式
同时在线式 手动式
机电一体化
以贴片式元件为主体,贴片器件品种不多
供料台
Feeder
X/Y伺服定位系统
• X/Y伺服定位系统:支持贴装头进行二维或三
维运动,即贴片头安装在X导轨上,X导轨沿Y方向运 动从而实现在X-Y方向贴片的全过程,实现旋转,平 移等动作
光学识别系统
• 光学识别系统:即CCD识
别系统,原理为贴装头吸取 元件后,CCD摄像机对元件 成像。转化成数字图像型号 。经计算机分析出元件的几 何中心并与控制中心进行比 较。计算出元件中心与吸嘴 中心进行比较元件误差,并 及时反馈至控制系统进行修 正 , 保 证 元 件 引 脚 与 PCB 焊
电脑主板图解知识图解(新手学主板维修资料)
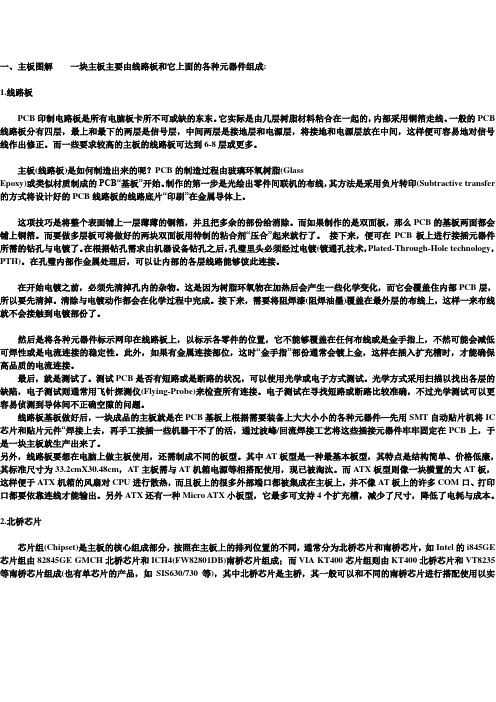
一、主板图解一块主板主要由线路板和它上面的各种元器件组成:1.线路板PCB印制电路板是所有电脑板卡所不可或缺的东东。
它实际是由几层树脂材料粘合在一起的,内部采用铜箔走线。
一般的PCB 线路板分有四层,最上和最下的两层是信号层,中间两层是接地层和电源层,将接地和电源层放在中间,这样便可容易地对信号线作出修正。
而一些要求较高的主板的线路板可达到6-8层或更多。
主板(线路板)是如何制造出来的呢?PCB的制造过程由玻璃环氧树脂(GlassEpoxy)或类似材质制成的PCB“基板”开始。
制作的第一步是光绘出零件间联机的布线,其方法是采用负片转印(Subtractive transfer)的方式将设计好的PCB线路板的线路底片“印刷”在金属导体上。
这项技巧是将整个表面铺上一层薄薄的铜箔,并且把多余的部份给消除。
而如果制作的是双面板,那么PCB的基板两面都会铺上铜箔。
而要做多层板可将做好的两块双面板用特制的粘合剂“压合”起来就行了。
接下来,便可在PCB板上进行接插元器件所需的钻孔与电镀了。
在根据钻孔需求由机器设备钻孔之后,孔璧里头必须经过电镀(镀通孔技术,Plated-Through-Hole technology,PTH)。
在孔璧内部作金属处理后,可以让内部的各层线路能够彼此连接。
在开始电镀之前,必须先清掉孔内的杂物。
这是因为树脂环氧物在加热后会产生一些化学变化,而它会覆盖住内部PCB层,所以要先清掉。
清除与电镀动作都会在化学过程中完成。
接下来,需要将阻焊漆(阻焊油墨)覆盖在最外层的布线上,这样一来布线就不会接触到电镀部份了。
然后是将各种元器件标示网印在线路板上,以标示各零件的位置,它不能够覆盖在任何布线或是金手指上,不然可能会减低可焊性或是电流连接的稳定性。
此外,如果有金属连接部位,这时“金手指”部份通常会镀上金,这样在插入扩充槽时,才能确保高品质的电流连接。
最后,就是测试了。
测试PCB是否有短路或是断路的状况,可以使用光学或电子方式测试。
电脑主板生产工艺及流程
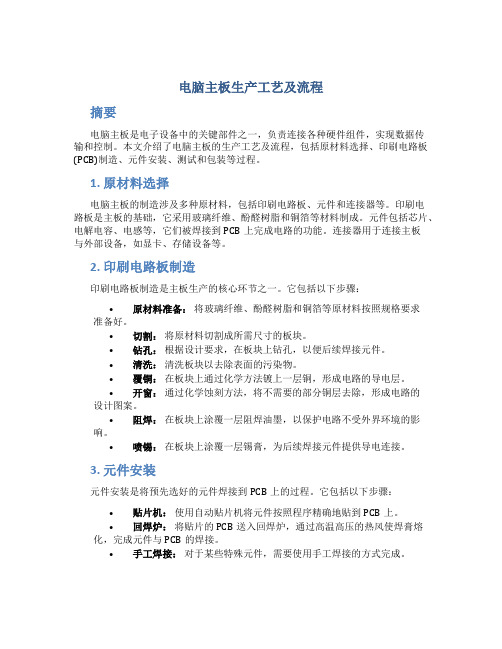
电脑主板生产工艺及流程摘要电脑主板是电子设备中的关键部件之一,负责连接各种硬件组件,实现数据传输和控制。
本文介绍了电脑主板的生产工艺及流程,包括原材料选择、印刷电路板(PCB)制造、元件安装、测试和包装等过程。
1. 原材料选择电脑主板的制造涉及多种原材料,包括印刷电路板、元件和连接器等。
印刷电路板是主板的基础,它采用玻璃纤维、酚醛树脂和铜箔等材料制成。
元件包括芯片、电解电容、电感等,它们被焊接到PCB上完成电路的功能。
连接器用于连接主板与外部设备,如显卡、存储设备等。
2. 印刷电路板制造印刷电路板制造是主板生产的核心环节之一。
它包括以下步骤:•原材料准备:将玻璃纤维、酚醛树脂和铜箔等原材料按照规格要求准备好。
•切割:将原材料切割成所需尺寸的板块。
•钻孔:根据设计要求,在板块上钻孔,以便后续焊接元件。
•清洗:清洗板块以去除表面的污染物。
•覆铜:在板块上通过化学方法镀上一层铜,形成电路的导电层。
•开窗:通过化学蚀刻方法,将不需要的部分铜层去除,形成电路的设计图案。
•阻焊:在板块上涂覆一层阻焊油墨,以保护电路不受外界环境的影响。
•喷锡:在板块上涂覆一层锡膏,为后续焊接元件提供导电连接。
3. 元件安装元件安装是将预先选好的元件焊接到PCB上的过程。
它包括以下步骤:•贴片机:使用自动贴片机将元件按照程序精确地贴到PCB上。
•回焊炉:将贴片的PCB送入回焊炉,通过高温高压的热风使焊膏熔化,完成元件与PCB的焊接。
•手工焊接:对于某些特殊元件,需要使用手工焊接的方式完成。
4. 测试在主板生产过程中,必须进行严格的测试以确保质量和可靠性。
测试内容包括:•电路连通性测试:使用特殊仪器检测主板上各个连接点的连通性。
•功能测试:通过连接各种外部设备,测试主板的各项功能是否正常。
•性能测试:使用压力测试等工具,对主板进行负载测试,以评估其性能。
•可靠性测试:将主板进行长时间的严格测试,以确保其在各种环境下的可靠工作。
5. 包装在主板通过测试后,需要进行最后的包装工作。
电脑主板生产工艺及流程11
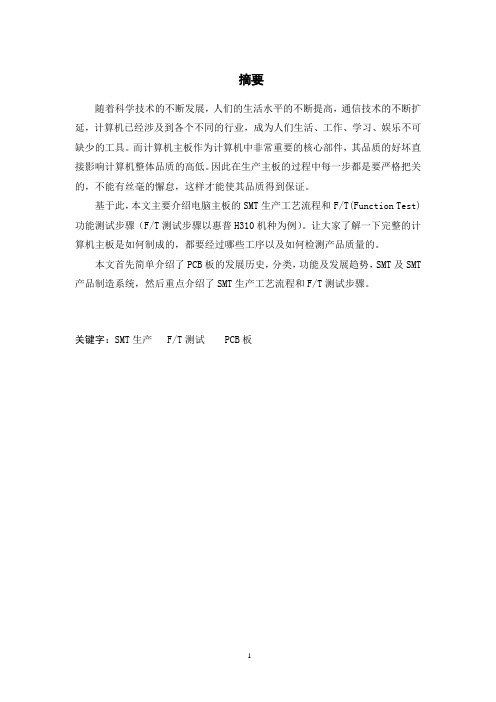
摘要随着科学技术的不断发展,人们的生活水平的不断提高,通信技术的不断扩延,计算机已经涉及到各个不同的行业,成为人们生活、工作、学习、娱乐不可缺少的工具。
而计算机主板作为计算机中非常重要的核心部件,其品质的好坏直接影响计算机整体品质的高低。
因此在生产主板的过程中每一步都是要严格把关的,不能有丝毫的懈怠,这样才能使其品质得到保证。
基于此,本文主要介绍电脑主板的SMT生产工艺流程和F/T(Function Test)功能测试步骤(F/T测试步骤以惠普H310机种为例)。
让大家了解一下完整的计算机主板是如何制成的,都要经过哪些工序以及如何检测产品质量的。
本文首先简单介绍了PCB板的发展历史,分类,功能及发展趋势,SMT及SMT 产品制造系统,然后重点介绍了SMT生产工艺流程和F/T测试步骤。
关键字:SMT生产 F/T测试 PCB板目录1 引言 (4)1.1 PCB板的简单介绍及发展历程 (4)1.2 印制电路板的分类及功能 (5)1.2.1 印制电路板的分类 (5)1.2.2 印制电路板的功能 (6)1.3 印制电路板的发展趋势 (6)1.4 SMT简介 (6)1.5 SMT产品制造系统 (8)2 SMT生产工艺流程 (9)2.1 来料检测 (9)2.2 锡膏印刷机 (9)2.2.1 印刷机的基本结构 (10)2.2.2 印刷机的主要技术指标 (10)2.2.3 印刷焊膏的原理 (10)2.3 3D锡膏检测机 (11)2.4 贴片机 (11)2.4.1 贴片机的的基本结构 (12)2.4.2 贴片机的主要技术指标 (13)2.4.3 自动贴片机的贴装过程 (14)2.4.4 连续贴装生产时应注意的问题 (14)2.5 再流焊(Reflow soldring) (15)2.5.1 再流焊炉的基本结构 (15)2.5.2 再流焊炉的主要技术指标 (16)2.5.3 再流焊原理 (16)2.5.4 再流焊工艺特点(与波峰焊技术相比) (17)2.5.5 再流焊的工艺要求 (17)2.6 DIP插接元件的安装 (18)2.7 波峰焊(wave solder) (19)2.7.1 波峰焊工艺 (19)2.7.2 波峰焊操作步骤 (19)2.7.3 波峰焊原理 (21)2.7.4 双波峰焊理论温度曲线 (23)2.7.5 波峰焊工艺对元器件和印制板的基本要求 (23)3 焊接及装配质量的检测 (24)3.1 AIO(automatic optical inspection)检测 (24)3.1.1 概述 (24)3.1.2 AOI检测步骤 (25)3.2 ICT在线测试 (27)3.2.1 慨述 (27)3.2.2 ICT在线测试步骤 (28)4 MAL段工作流程 (29)4.1 MAL锁附站需手工安装的零件 (29)4.2 MAL LQC目检的项目 (30)4.2.1 S1面检验项目 (30)4.2.2 S2面检验项目 (31)5 F/T(Function Test) 测试程序 (32)5.1 测试治具的认识 (32)5.2 拆装测试治具步骤 (33)5.3 DOS系统下测试程序 (34)5.3.1 电源开机测试 (34)5.3.2 Scan Sku 测试 (34)5.3.3 微动开关测试 (35)5.3.4 烧录Lan Mac ID 测试 (35)5.3.5 电池电量测试及LCD EDID测试 (36)5.4 WINDOWS系统测试程序 (36)5.4.1 系统组态测试 (36)5.4.2 无线网卡/WWAN测试 (37)5.4.3 音效测试 (37)5.4.4 键盘触控按键测试 (38)5.4.5 LED Test (39)5.4.6 MS & MMC & SD & XD & NEW Disk Card Test (39)5.4.7 检查条码测试 (40)结束语 (41)致谢 (42)参考文献 (43)1 引言1.1 PCB板的简单介绍及发展历程印刷电路板(Printed Circuit Board)简称PCB,又称印制板,是电子产品的重要部件之一。
电脑主板生产的全过程图解
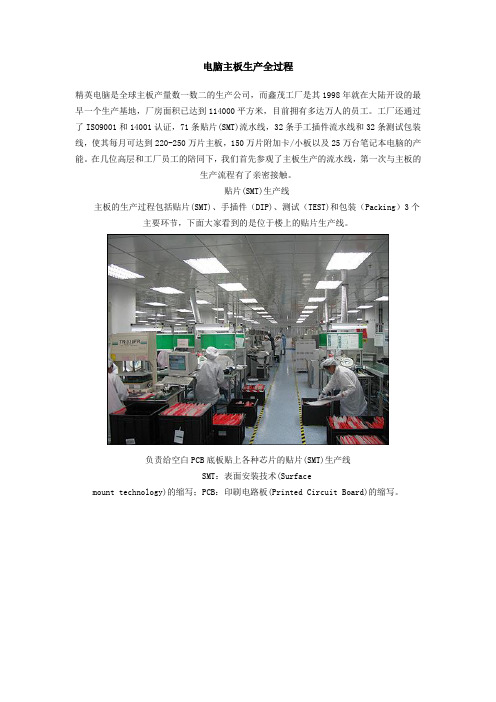
电脑主板生产全过程精英电脑是全球主板产量数一数二的生产公司,而鑫茂工厂是其1998年就在大陆开设的最早一个生产基地,厂房面积已达到114000平方米,目前拥有多达万人的员工。
工厂还通过了ISO9001和14001认证,71条贴片(SMT)流水线,32条手工插件流水线和32条测试包装线,使其每月可达到220-250万片主板,150万片附加卡/小板以及25万台笔记本电脑的产能。
在几位高层和工厂员工的陪同下,我们首先参观了主板生产的流水线,第一次与主板的生产流程有了亲密接触。
贴片(SMT)生产线主板的生产过程包括贴片(SMT)、手插件(DIP)、测试(TEST)和包装(Packing)3个主要环节,下面大家看到的是位于楼上的贴片生产线。
负责给空白PCB底板贴上各种芯片的贴片(SMT)生产线SMT:表面安装技术(Surfacemount technology)的缩写;PCB:印刷电路板(Printed Circuit Board)的缩写。
一片片空白PCB底板堆放在运输架上上面光秃秃的,还什么都没有空白PCB底板首先被送入这台机器添加锡焊剂需要一片片的放入,略微有些慢然后进入自动工作的SONY SI-E1000E Mk Ⅲ等各型贴片机底板将会被贴片机贴上大大小小的各种芯片,通常顺序是从小到大SONY SI-E1000E贴片机先在底板上贴上一些较小的芯片通过SONY SI-E2000E贴片机则贴上南北桥等较大的芯片这些芯片个头够大吧,算是底板上最大的元件贴好芯片的PCB底板与刚才大不一样了用肉眼通过特大“放大镜”检查PCB底板通过TR-518FR这台ICT测试设备进行短路测试等一些底板会出现零件不良的问题手插件生产线在手工插件生产线,首先要给已经贴片的PCB底板贴上隔热胶布还是光秃秃的主板,在接下来插件过程中需要隔热胶布来保护原来电容等元器件是通过手工来插上主板每个工人负责一个独立的工序I/O接口、内存插槽等都在流水线上挨个插上就这样一块主板的手工插装完成了通过波峰机将元器件与主板紧密焊接在一起波峰机升温固化焊锡,处理完毕从波峰机出来还要经过风干后才送入下一道工序工人开始处理从机器里面出来的主板还需要用电烙铁进行一些焊接处理开始工序繁多的质量检查数字万用表也是检测工具之一通过DEBUG卡查找主板是否有故障存在接下来是通过DOS下的测试软件进行检查一块板子需要通过12项测试开始刷写主板的BIOS这个界面,DIYer应该很熟悉吧进入Windows后,还有一系列的测试通过最后的目视检查后装入防静电袋,大功告成!。
笔记本主板制造过程详细说明书

Pin in paste stencil design for notebook mainboardPin in paste stencil design for notebook mainboardEveryday laptops we use are a little bit more than a keyboard and an LCD screen. If we take our time to take a look under the hood, we’ll find a complex notebook mainboard together with many additional components. Less space, more functionality is what a laptop stands for, and a notebook mainboard is probably one of the most dense, compact and complex electronic assemblies in use today.Traditional SMT process calls for screen printing, component placement and reflow phases, respectively for each side. The exception would be adding THTs and processing them together with SMDs ina single operation. However, when we go deeper into the process, we see it is not that simple.As the surface mount componentsget smaller, and the component density increases as a result, soldering becomes a challenging task. Soldered joints are not always accessible for some components like QFNs and BGAs, since they are covered by the component body itself. These SMDs for sure require extra care, but what if we like to solder all THTs on a single pass together with them?A notebook mainboard is a 1,2 mm thick 6 to 8 layer board with more than 2000 components on it. Our aim is to complete the soldering process aftertwo reflow cycles and send the board immediately to ICT. In order to make this happen, first we should define all process parameters. On the first pass we will have only SMDs in place, but on the second pass THTs will come into stage.In this article, we focus on the bottom side stencil and will define the stencil construction and aperture design requirements. There are strict procedures that govern the manufacture of stencils in any SMT production environment but I will try to keep our vision as wide as possible.If we consider a seamless placement process where no placement issues are apparent–• All SMDs are placed with high accuracy.• THT devices are either manually placed of placed in automation withrequired accuracy and pressure. (InVestel Digital all devices are placedin automation by the help of specialnozzles and gripper arms.)–then the key parameters left will be stencil design and reflow profile.Pin in hole reflow techniqueHow to incorporate through hole components into the reflow soldering process? This question is the rally point for a simple to understand but hard to follow task. The pin in hole or pin in paste method lets the PCB go through the reflow oven once it is completely placed and,as a result, everything becomes ‘soldered’ right after the oven. In this process, paste is applied to all SMD pads, and holes are filled with solder for THT components.The difference from the SMD screen printing process is that the amount of solder pushed into the holes is more than the amount applied for regular pads–overprinting. Multilayer stencil requirement Consistent stencil design requires a clear definition of aperture parameters for each and every special component. Special components are the ones that need to be validated when a new process parameteris conducted or modified. On a typical notebook mainboard, 0.8 mm pitchand 1,27 mm pitch BGAs, 0.4 mm fine pitch QFPs, 0.5 pitch QFNs, 0.5 pitch connectors and all leaded peripherals–the so called THTs–sit on the same surface. Since our aim is to solder them all on a single pass, we will exercise extra careon each of them in order to optimize the stencil design for a repeatable process.Let us consider the bottom side of a notebook mainboard and identify the stencil design parameters for each special SMD. Chipset BGABall Pitch : 0.8 mmBall Diameter : 0.358 mmRule 1: The ratio of the round aperture’s surface area divided by the surface area of the side walls of the hole should be greaterThis paper examines theconstruction of a notebookmainboard with more than2000 components and no wavesoldering required.The board contains standardSMD, chipset BGAs, connectors,through hole components and oddforms placed using full automationand soldered after two reflowcycles under critical processparameters. However, state ofthe art technology does not help ifthe process parameters are not setcarefully. Can all complex BGAs,THT s and even screws be solderedon a single stencil? What will helpus overcome bridging, insufficientsolder and thombstoning issues?This paper will demonstratethe placement of all odd shapecomponents using pin-in-pastestencil design and full completionof the motherboard after tworeflow cycles.Keywords: Screen Printing,Stencil, Multilayer, Fine Pitch,ElectroformAtilim Demirtas, Vestel Digital, Manisa, Turkey 28 – Global SMT & Packaging - February 2008Equation 1 half of it shrinks. The multiplier ‘2’ is the shrinkage factor and compensates for anyMore possibilities with Selective SolderingSee what the SPA rangefrom EBSO can do for you*************。
电脑主板生产工艺及流程
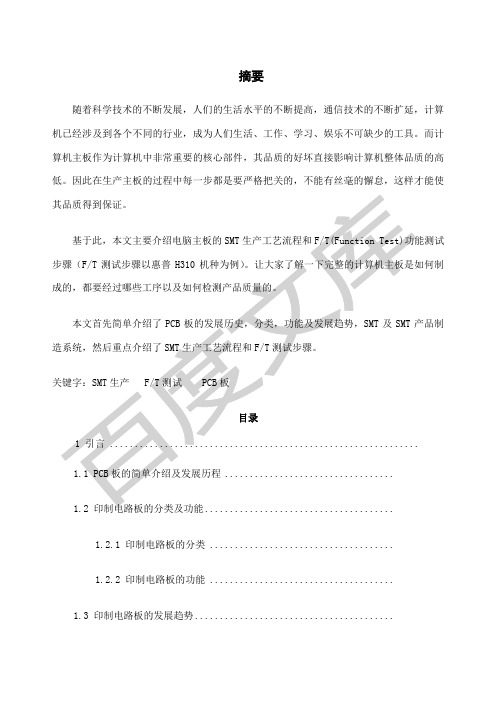
摘要随着科学技术的不断发展,人们的生活水平的不断提高,通信技术的不断扩延,计算机已经涉及到各个不同的行业,成为人们生活、工作、学习、娱乐不可缺少的工具。
而计算机主板作为计算机中非常重要的核心部件,其品质的好坏直接影响计算机整体品质的高低。
因此在生产主板的过程中每一步都是要严格把关的,不能有丝毫的懈怠,这样才能使1.2.1 印制电路板的分类 .....................................1.2.2 印制电路板的功能 .....................................1.3 印制电路板的发展趋势........................................1.4 SMT简介 ....................................................1.5 SMT产品制造系统 ............................................2 SMT生产工艺流程..................................................2.1 来料检测....................................................2.4.4 连续贴装生产时应注意的问题 ..........................2.5 再流焊(Reflow soldring)..................................2.5.1 再流焊炉的基本结构 ..................................2.5.2 再流焊炉的主要技术指标 ..............................2.5.3 再流焊原理 ..........................................2.5.4 再流焊工艺特点(与波峰焊技术相比) ..................2.5.5 再流焊的工艺要求 ....................................2.6 DIP插接元件的安装 .........................................3.1.2 AOI检测步骤.........................................3.2 ICT在线测试 ..............................................3.2.1 慨述 ................................................3.2.2 ICT在线测试步骤......................................4 MAL段工作流程....................................................4.1 MAL锁附站需手工安装的零件 .................................4.2 MAL LQC目检的项目 .........................................4.2.1 S1面检验项目........................................5.3.5 电池电量测试及LCD EDID测试 ........................5.4 WINDOWS系统测试程序 .......................................5.4.1 系统组态测试 ........................................5.4.2 无线网卡/WWAN测试...................................5.4.3 音效测试 ............................................5.4.4 键盘触控按键测试 ....................................5.4.5 LED Test ............................................5.4.6 MS & MMC & SD & XD & NEW Disk Card Test .............连接的,而元件的固定是在空间中立体进行的。
华硕电脑主板研发生产工艺流程介绍
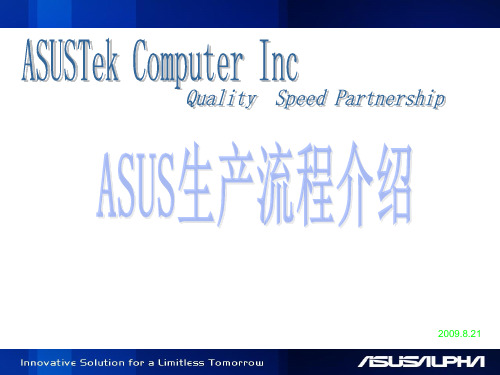
生产型态
• • • • BTO------Build to order SBTO 线(小线): 量少工单多的生产型态 MBTO线(中线): 量中工单中的生产型态 LBTO 线(大线): 量大工单少的生产型
FATP生产流程介绍
PD 物料
ASS’Y
SWDL1
Pretest
CFG
SWDL2
Function
TS(维修)
•目的:将产线上发 现的外观 (如反 白,反向,立碑,偏 移,虚焊,空焊,漏 件,错件…….)不 良品,利用维修工 具热风枪,镊子, 万用表等,及时的 维修成良品,涉及 到电性方面的不 良转到FAE维修.
Router
Router 裁板: 去除多余的PCBA板边.
Router操作顺序:
Ass’y
1,此站的工作 内容为把一 些Mylar与 机构件组装 到PCBA上去. 2,此站又因机 种的不同组 装顺序也不 相同.
3,因组装内容不同又有不同分工.
的不 生同 产的 模部 具分 因 工 艺 要 求 的 不 同 人 而 使 用 相 应
F/T
• 需安装的测试设备: DIMM / CPU / Wlan card / Inverter Cable /FAN / USB cable / CRT Cable / Card bus / HDD / Touch pad FFC / K/B FFC / Led Board / Heat sink / Adapter
FUJI (NXT) M3高速机与M6泛用机两者差异:
1.置件速度: 高速机0 .085~0.15sec/piece 泛用机0.3~2.5sec/piece 2.置件零件分类原则: 高速机:R、L、C 泛用机:QFP、BGA、 CONNECTOR M3高速机 零件大小 管制情况 PAD数 较小 非管制料 较多 M6泛用机 较大 管制料 较少
主板生产工艺
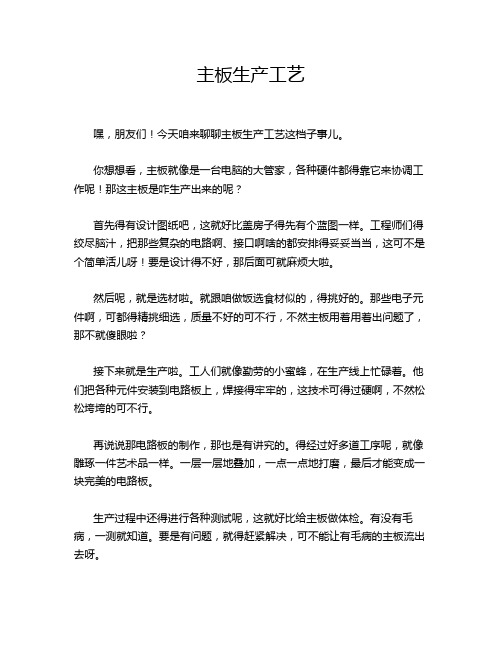
主板生产工艺
嘿,朋友们!今天咱来聊聊主板生产工艺这档子事儿。
你想想看,主板就像是一台电脑的大管家,各种硬件都得靠它来协调工作呢!那这主板是咋生产出来的呢?
首先得有设计图纸吧,这就好比盖房子得先有个蓝图一样。
工程师们得绞尽脑汁,把那些复杂的电路啊、接口啊啥的都安排得妥妥当当,这可不是个简单活儿呀!要是设计得不好,那后面可就麻烦大啦。
然后呢,就是选材啦。
就跟咱做饭选食材似的,得挑好的。
那些电子元件啊,可都得精挑细选,质量不好的可不行,不然主板用着用着出问题了,那不就傻眼啦?
接下来就是生产啦。
工人们就像勤劳的小蜜蜂,在生产线上忙碌着。
他们把各种元件安装到电路板上,焊接得牢牢的,这技术可得过硬啊,不然松松垮垮的可不行。
再说说那电路板的制作,那也是有讲究的。
得经过好多道工序呢,就像雕琢一件艺术品一样。
一层一层地叠加,一点一点地打磨,最后才能变成一块完美的电路板。
生产过程中还得进行各种测试呢,这就好比给主板做体检。
有没有毛病,一测就知道。
要是有问题,就得赶紧解决,可不能让有毛病的主板流出去呀。
咱再想想,要是主板生产工艺不过关,那电脑会咋样?没准儿经常死机、蓝屏,那可太闹心啦!所以说呀,这主板生产工艺可太重要啦,可不能马虎!
你说这主板生产工艺是不是很神奇?从一块光秃秃的电路板,变成了能让电脑正常运行的关键部件。
这背后凝聚着多少人的心血和汗水呀!咱用电脑的时候可得好好珍惜,别随便折腾它,不然可对不起那些辛苦生产主板的人们哟!这主板生产工艺,真的是一门大学问,值得我们好好去了解和探索呢!。
主板生产工艺
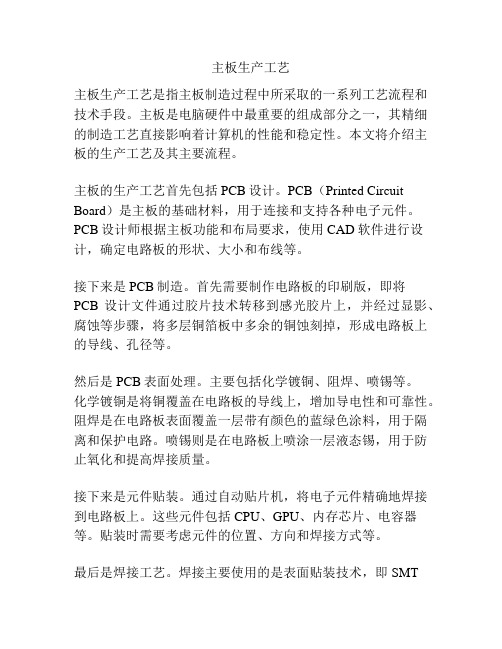
主板生产工艺主板生产工艺是指主板制造过程中所采取的一系列工艺流程和技术手段。
主板是电脑硬件中最重要的组成部分之一,其精细的制造工艺直接影响着计算机的性能和稳定性。
本文将介绍主板的生产工艺及其主要流程。
主板的生产工艺首先包括PCB设计。
PCB(Printed Circuit Board)是主板的基础材料,用于连接和支持各种电子元件。
PCB设计师根据主板功能和布局要求,使用CAD软件进行设计,确定电路板的形状、大小和布线等。
接下来是PCB制造。
首先需要制作电路板的印刷版,即将PCB设计文件通过胶片技术转移到感光胶片上,并经过显影、腐蚀等步骤,将多层铜箔板中多余的铜蚀刻掉,形成电路板上的导线、孔径等。
然后是PCB表面处理。
主要包括化学镀铜、阻焊、喷锡等。
化学镀铜是将铜覆盖在电路板的导线上,增加导电性和可靠性。
阻焊是在电路板表面覆盖一层带有颜色的蓝绿色涂料,用于隔离和保护电路。
喷锡则是在电路板上喷涂一层液态锡,用于防止氧化和提高焊接质量。
接下来是元件贴装。
通过自动贴片机,将电子元件精确地焊接到电路板上。
这些元件包括CPU、GPU、内存芯片、电容器等。
贴装时需要考虑元件的位置、方向和焊接方式等。
最后是焊接工艺。
焊接主要使用的是表面贴装技术,即SMT(Surface Mount Technology)。
通过回流焊接,将贴片元件与电路板焊接在一起。
回流焊接是将整个电路板放入高温炉中,使焊膏中的焊锡熔化并润湿元件和电路板,然后经过冷却固化,实现焊接。
除了上述主要工艺流程外,还有一些其他工艺环节。
例如测试工艺,通过自动测试仪器对主板进行功能和性能的全面测试;包装工艺,将主板进行整理和包装,以便于运输和销售;质量控制工艺,对主板进行质量检查和控制,以确保主板的稳定性和性能。
总之,主板生产工艺是一项复杂而精细的制造过程,涉及到多项工艺和技术手段。
只有通过严格的工艺流程控制和质量控制,才能生产出高质量、稳定性能的主板产品。
- 1、下载文档前请自行甄别文档内容的完整性,平台不提供额外的编辑、内容补充、找答案等附加服务。
- 2、"仅部分预览"的文档,不可在线预览部分如存在完整性等问题,可反馈申请退款(可完整预览的文档不适用该条件!)。
- 3、如文档侵犯您的权益,请联系客服反馈,我们会尽快为您处理(人工客服工作时间:9:00-18:30)。
摘要随着科学技术的不断发展,人们的生活水平的不断提高,通信技术的不断扩延,计算机已经涉及到各个不同的行业,成为人们生活、工作、学习、娱乐不可缺少的工具。
而计算机主板作为计算机中非常重要的核心部件,其品质的好坏直接影响计算机整体品质的高低。
因此在生产主板的过程中每一步都是要严格把关的,不能有丝毫的懈怠,这样才能使其品质得到保证。
基于此,本文主要介绍电脑主板的SMT生产工艺流程和F/T(Function Test)功能测试步骤(F/T测试步骤以惠普H310机种为例)。
让大家了解一下完整的计算机主板是如何制成的,都要经过哪些工序以及如何检测产品质量的。
本文首先简单介绍了PCB板的发展历史,分类,功能及发展趋势,SMT及SMT 产品制造系统,然后重点介绍了SMT生产工艺流程和F/T测试步骤。
关键字:SMT生产 F/T测试 PCB板目录1引言51.1 PCB板的简单介绍及发展历程51.2印制电路板的分类及功能61.2.1 印制电路板的分类61.2.2印制电路板的功能71.3印制电路板的发展趋势71.4 SMT简介71.5 SMT产品制造系统92 SMT生产工艺流程102.1来料检测102.2 锡膏印刷机102.2.1印刷机的基本结构112.2.2 印刷机的主要技术指标112.2.3 印刷焊膏的原理112.3 3D锡膏检测机122.4 贴片机122.4.1贴片机的的基本结构132.4.2贴片机的主要技术指标142.4.3 自动贴片机的贴装过程152.4.4 连续贴装生产时应注意的问题152.5再流焊(Reflow soldring)162.5.1再流焊炉的基本结构162.5.2再流焊炉的主要技术指标172.5.3再流焊原理172.5.4再流焊工艺特点(与波峰焊技术相比)182.5.5再流焊的工艺要求182.6 DIP插接元件的安装192.7波峰焊(wave solder)202.7.1波峰焊工艺202.7.2 波峰焊操作步骤202.7.3 波峰焊原理222.7.4双波峰焊理论温度曲线242.7.5 波峰焊工艺对元器件和印制板的基本要求243 焊接及装配质量的检测253.1 AIO(automatic optical inspection)检测253.1.1概述253.1.2 AOI检测步骤263.2 ICT在线测试283.2.1 慨述283.2.2 ICT在线测试步骤294 MAL段工作流程304.1 MAL锁附站需手工安装的零件304.2 MAL LQC目检的项目314.2.1 S1面检验项目314.2.2 S2面检验项目325 F/T(Function Test) 测试程序335.1测试治具的认识335.2 拆装测试治具步骤345.3 DOS系统下测试程序355.3.1电源开机测试355.3.2 Scan Sku测试355.3.3 微动开关测试365.3.4烧录Lan Mac ID 测试365.3.5电池电量测试及LCD EDID测试375.4 WINDOWS系统测试程序375.4.1系统组态测试375.4.2 无线网卡/WWAN测试385.4.3 音效测试385.4.4 键盘触控按键测试395.4.5LED Test405.4.6 MS & MMC & SD & XD & NEW Disk Card Test405.4.7检查条码测试41结束语42致谢43参考文献441 引言1.1 PCB板的简单介绍及发展历程印刷电路板(Printed Circuit Board)简称PCB,又称印制板,是电子产品的重要部件之一。
用印制电路板制造的电子产品具有可靠性高、一致性好、机械强度高、重量轻、体积小、易于标准化等优点。
几乎每种电子设备,小到电子手表、计算器,大到计算机、通信设备、电子雷达系统,只要存在电子元器件,它们之间的电气互连就要使用印制板。
在电子技术发展的早期,电路由电源、导线、开关和元器件构成。
元器件都是用导线连接的,而元件的固定是在空间中立体进行的。
随着电子技术的发展,电子产品的功能、结构变得很复杂,元件布局、互连布线都受到很大的空间限制,如果用空间布线方式,就会使电子产品变得眼花缭乱。
因此就要求对元件和布线进行规划。
用一块板子作为基础,在板上规划元件的布局,确定元件的接点,使用接线柱做接点,用导线把接点按电路要求,在板的一面布线,另一面装元件。
这就是最原始的电路板。
这种类型的电路板在真空电子管时代非常流行,由于线路都在同一个平面分布,没有太多的遮盖点,检查起来容易。
这时电路板已初步形成了“层”的概念。
单面敷铜板的发明,成为电路板设计与制作新时代的标志。
布线设计和制作技术都已发展成熟。
先在敷铜板上用模板印制防腐蚀膜图,然后再腐蚀刻线,这种技术就象在纸上印刷那样简便,“印刷电路板”因此得名。
随着电子技术发展和印制板技术的进步,出现了双面板,即在板子两面都敷铜,两面都可腐蚀刻线。
随着电子产品生产技术的发展,人们开始在双面电路板的基础上发展夹层,其实就是在双面板的基础上叠加上一块单面板,这就是多层电路板。
起初,夹层多用做大面积的地线、电源线的布线,表层都用于信号布线。
后来,要求夹层用于信号布线的情况越来越多,这使电路板的层数也要增加。
但夹层不能无限增加,主要原因是成本和厚度问题。
因此,电子产品设计者要考虑到性价比这个矛盾的综合体,而最实际的设计方法仍然是以表层做信号布线层为首选。
高频电路的元件也不能排得太密,否则元件本身的辐射会直接对其它元件产生干扰。
层与层之间的布线应错开成十字走向,以减少布线电容和电感。
1.2 印制电路板的分类及功能1.2.1印制电路板的分类根据软硬进行分类:普通电路板和柔性电路板。
根据电路层数分类:分为单面板、双面板和多层板。
常见的多层板一般为4层板或6层板,复杂的多层板可达十几层。
从1903年至今若以PCB组装技术的应用和发展角度来看可分为三个阶段:1.通孔插装技术(THT)阶段PCB1).金属化孔的作用:①.电气互连---信号传输②.支撑元器件---引脚尺寸**通孔尺寸的缩小a.引脚的刚性b.自动化插装的要求2).提高密度的途径①.减小器件孔的尺寸,但受到元件引脚的刚性及插装精度的**,孔径≥0.8mm②.缩小线宽/间距:0.3mm—0.2mm—0.15mm—0.1mm③.增加层数:单面—双面—4层—6层—8层—10层—12层—64层2.表面安装技术(SMT)阶段PCB1).导通孔的作用:仅起到电气互连的作用,孔径可以尽可能的小,堵上孔也可以。
2).提高密度的主要途径①.过孔尺寸急剧减小:0.8mm—0.5mm—0.4mm—0.3mm—0.25mm②.过孔的结构发生本质变化:a.埋盲孔结构优点:提高布线密度1/3以上、减小PCB尺寸或减少层数、提高可靠性、改善了特性阻抗控制,减小了串扰、噪声或失真(因线短,孔小)b.盘内孔(hole in pad)消除了中继孔及连线③薄型化:双面板:1.6mm—1.0mm—0.8mm—0.5mm④PCB平整度:a.概念:PCB板基板翘曲度和PCB板面上连接盘表面的共面性。
b.PCB翘曲度是由于热、机械引起残留应力的综合结果c.连接盘的表面涂层:HASL、化学镀NI/AU、电镀NI/AU…3.芯片级封装(CSP)阶段PCBCSP以开始进入急剧的变革于发展其之中,推动PCB技术不断向前发展, PCB 工业将走向激光时代和纳米时代.1.2.2 印制电路板的功能印制电路板在电子设备中具有如下功能:. 提供集成电路等各种电子元器件固定、装配的机械支撑,实现集成电路等各种电子元器件之间的布线和电气连接或电绝缘,提供所要求的电气特性。
为自动焊接提供阻焊图形,为元件插装、检查、维修提供识别字符和图形。
电子设备采用印制板后,由于同类印制板的一致性,避免了人工接线的差错,并可实现电子元器件自动插装或贴装、自动焊锡、自动检测,保证了电子产品的质量,提高了劳动生产率、降低了成本,并便于维修。
1.3 印制电路板的发展趋势印制板从单层发展到双面板、多层板和挠性板,并不断地向高精度、高密度和高可靠性方向发展。
不断缩小体积、减少成本、提高性能,使得印制板在未来电子产品的发展过程中,仍然保持强大的生命力。
未来印制板生产制造技术发展趋势是在性能上向高密度、高精度、细孔径、细导线、小间距、高可靠、多层化、高速传输、轻量、薄型方向发展。
1.4 SMT简介随着科学技术迅速发展以及信息技术的快速推广与应用,电子产品已逐渐成为了人们生活中不可缺少的物质资源及国民经济的重要组成部分,电子产品制造已逐步发展成为一门新兴的行业与技术,成为了现代制造业的重要分支[1],对国民经济的发展,对国家综合国力的体现与提高都起到了积极和重要的促进作用。
随着电子产品的微型化、轻量化、集成化、高密度化和高可靠性的发展,基于基板的板级电子电路产品就成了电子产品的主要形式,板级电子电路产品的制造技术水平就成为体现现代电子产品制造技术的重要标志。
继手工插装、半自动化插装、全自动插装之后的第四代电子电路制造技术,表面组装技术 (SurfaceMountTechnology,SMT)的兴起和发展动摇了传统板级电子电路产品的组装概念,改变了电子元器件通孔插装技术(ThroughHoleTechnology,THT)的制造形式,引起了电子产品制造的技术革命,被称为是电子产品制造技术的“第二次革命”,并逐步发展成为融合微电子学、电子材料、半导体集成电路、电路设计自动化 (Eleetronieoesi,Automation,EnA)计算机辅助测试和先进制造等各项技术在内的现代先进电子制造技术,该技术是一项涉及到微电子、精密机械自动控制、焊接、精细化工、材料、检测等多专业和多学科的新兴、综合性工程科学技术[2]。
SMT组装分为芯片级组装(常称为封装或一级封装)和板级组装(也称为二级封装)。
芯片级组装是将硅片(芯片)贴装在基片上,然后通过封接或软钎焊焊接到基板上成为完整的元件。
板级组装是将元件贴装在普通混装印制电路板(PriniedCireuitBoard,PCB)或表面安装印制电路板 (Surface Mount Printed Circuit Board)上。
与传统的通孔插装技术相比较,采用SMT技术进行电子产品组装的优越性主要体现在以下几个方面[3]:1.SMT元器件体积小、重量轻、集成度高、功能多、可贴装于PCB两面,并使包括立体组装在内的高密度组装成为可能。
由于表面贴装元件(SurfaceMountComponent,SMC)和表面贴装器件 (surfaeeMountDeviee,SMD)的体积、重量只有传统元器件的1/10,由其组成的PCB模块体小、量轻,可使相应的电子设备和产品体积缩小40~60%,重量减轻60一80%,其大幅度微型化效果显著,应用面极其广泛。