PVC木塑复合材料挤出发泡的研究进展
木塑复合材料的研究进展

木塑复合材料的研究进展现阶段木塑复合材料的基体主要有PP、PE、PVC、PS以及ABS等,从目前市场上的产品来看,主要是PE基的木塑复合材料制品,而PP 基和PVC基的木塑复合材料也占一定的比例。
目前,木塑复合材料的研究也以这三种塑料基体为基础,但许多研究者已经开始进行新型木塑复合材料的研发。
1. PE基木塑复合材料聚乙烯(PE)是一种无毒、质轻、具有优异的耐化学腐蚀性和电绝缘性的热塑性聚合物,广泛应用于电器工业、化学工业、食品工业、机器制造业和农业等方面。
PE 树脂的产量自20世纪60年代中期以来一直高居世界塑料产量的首位,常见的品种有高密度聚乙烯(HDPE)、低密度聚乙烯(LDPE)以及线形低密度聚乙烯(LLDPE),性能各有不同,其中HDPE在木塑复合材料的应用最为广泛。
Cui J.等[1]将丙烯酰胺-甲醛-尿素三元共聚物(AMFU)用于增容植物纤维/HDPE复合材料体系,结果表明AMFU对植物纤维/HDPE复合体系有良好的增容作用,使得复合材料的静态和动态力学性能明显改善,复合材料的吸水率降低。
该研究给出了一种增容木塑复合材料的新途径。
Tan H.等[2]研究了MAPE对椰壳纤维/LLDPE复合材料体系力学性能的影响,并用扫描电子显微镜观察了复合材料冲击断面的形貌。
研究发现,加入MAPE后,复合材料的弯曲强度和冲击强度均高于未加界面改性剂的;SEM照片显示,加入MAPE的复合材料有更好的界面粘接,椰壳纤维和LLDPE树脂基体间的相容性得到了改善,这也是复合材料刚性和韧性提高的主要原因。
2. PP基木塑复合材料聚丙烯(PP)树脂按结构不同,可以分为等规聚丙烯、间规聚丙烯和无规聚丙烯三类,目前作为塑料使用的PP一般均为等规结构的。
PP的电绝缘性和耐化学腐蚀性优良,尤其是力学性能和耐热性在通用塑料中是最好的,但其低温脆性大,耐老化性不好。
由PP的价格相对低廉,目前其在木塑复合材料中的应用也很广泛。
聚乙烯挤出发泡成型研究

聚乙烯挤出发泡成型研究
聚乙烯挤出发泡成型是一种将聚乙烯挤出后发泡成型的生产工艺。
该工艺的优点在于,可以制备轻质、高强度、隔热性能好的聚乙烯制品,如管道、板材、注塑件等。
因此,聚乙烯挤出发泡成型工艺得到
了广泛应用。
在该工艺中,首先将聚乙烯加热至熔融状态,然后通过挤出机将
熔融聚乙烯挤出,形成所需的成型件。
接下来,将成型件送入发泡室,加压向其中注入发泡剂,使其开始发泡。
待发泡完成后,将发泡成品
经过切割、修整等处理,得到所需的成品。
该工艺的成品具有密度低、吸音性好、绝缘性强、韧性好等优点,被广泛应用于建材、家具、汽车、包装等领域。
而随着人们对环保要
求的提高,聚乙烯挤出发泡成型技术也得到了进一步发展,新型的发
泡剂和增强材料的引入,为该工艺的推广和应用提供了更加广阔的空间。
PVC木塑复合发泡板改性研究

木 塑 复合 发泡 板 大 部 分 以聚 氯 乙 烯 ( P VC ) 树脂、 木 粉及 碳 酸钙 粉 末 为 主要 原 料 , 加 入 抗 冲 改 性剂 、 发 泡剂 、 稳定 剂 、 增强 剂 、 润滑 剂等 助剂 , 混 合均 匀经 锥形 双螺 杆挤 出机 塑 化挤 出 , 后 通 过
现 代 塑 料 加 工 应 用
2 0 1 3年 第 2 5卷 第 5期
・ 27 ・
M ODERN PLAS TI CS PROCESS I NG AND APPLI CAT1 0NS
P V O木 塑 复 合 发 泡 板 改 性研 究
高 冬 朱 骏 峰 王洪 廷 吕佳 佳
本 研究考 察 了木粉 、 抗 冲改性 剂 、 发泡 剂 、 润 滑剂、 发 泡调 节 剂 、 增 强剂 对 木 塑 复合 发 泡 板 主
要性 能 的影 响 , 并 提 出适 合 建筑行 业使 用 的木 塑
PVC木塑复合微孔发泡材料挤出成型技术研究
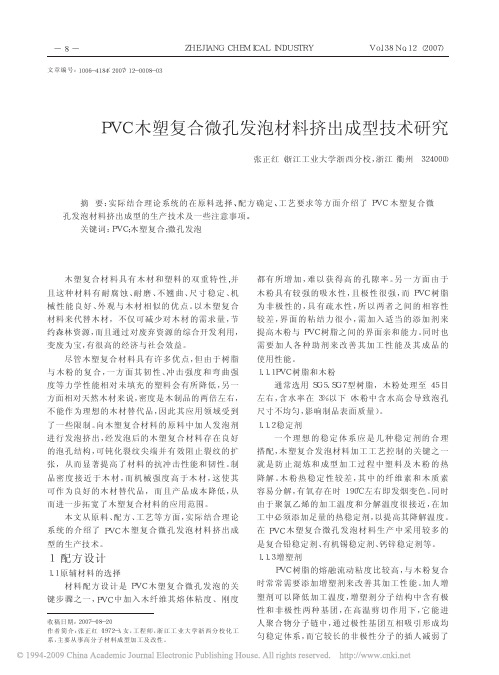
Vol.38No.12(2007)ZHEJIANGCHEMICALINDUSTRY收稿日期:2007-08-20作者简介:张正红(1972-),女,工程师,浙江工业大学浙西分校化工系,主要从事高分子材料成型加工及改性。
文章编号:1006-4184(2007)12-0008-03PVC木塑复合微孔发泡材料挤出成型技术研究张正红(浙江工业大学浙西分校,浙江衢州324000)摘要:实际结合理论系统的在原料选择、配方确定、工艺要求等方面介绍了PVC木塑复合微孔发泡材料挤出成型的生产技术及一些注意事项。
关键词:PVC;木塑复合;微孔发泡木塑复合材料具有木材和塑料的双重特性,并且这种材料有耐腐蚀、耐磨、不翘曲、尺寸稳定、机械性能良好、外观与木材相似的优点。
以木塑复合材料来代替木材,不仅可减少对木材的需求量,节约森林资源,而且通过对废弃资源的综合开发利用,变废为宝,有很高的经济与社会效益。
尽管木塑复合材料具有许多优点,但由于树脂与木粉的复合,一方面其韧性、冲击强度和弯曲强度等力学性能相对未填充的塑料会有所降低,另一方面相对天然木材来说,密度是木制品的两倍左右,不能作为理想的木材替代品,因此其应用领域受到了一些限制。
向木塑复合材料的原料中加人发泡剂进行发泡挤出,经发泡后的木塑复合材料存在良好的泡孔结构,可钝化裂纹尖端并有效阻止裂纹的扩张,从而显著提高了材料的抗冲击性能和韧性。
制品密度接近于木材,而机械强度高于木材,这使其可作为良好的木材替代品,而且产品成本降低,从而进一步拓宽了木塑复合材料的应用范围。
本文从原料、配方、工艺等方面,实际结合理论系统的介绍了PVC木塑复合微孔发泡材料挤出成型的生产技术。
1配方设计1.1原辅材料的选择材料配方设计是PVC木塑复合微孔发泡的关键步骤之一,PVC中加入木纤维其熔体粘度、刚度都有所增加,难以获得高的孔隙率。
另一方面由于木粉具有较强的吸水性,且极性很强,而PVC树脂为非极性的,具有疏水性,所以两者之间的相容性较差,界面的粘结力很小,需加入适当的添加剂来提高木粉与PVC树脂之间的界面亲和能力。
PVC发泡材料技术的研究进展

早在 20 世纪 40 年代,PVC 泡沫塑料在欧洲就已经研发成功并被广泛应用。
随着市场需求的多样化和高标准化, PVC 泡沫塑料的成型配方与加工技术日新月异,得到了不断的完善和优化。
近年来高性能PVC 发泡材料的开发更是成为了国内外学者研究的热点。
Vaikhanski L 等研究了芳纶纤维增强 R-PVC 发泡材料的研究。
利用可发性 PVC 颗粒和改性芳纶纤维通过振动渗透、模压成型的方法解决了纤维在成型过程中分散性和相容差的问题。
结果表明:与无纤维增强的 R-PVC 发泡材料相比,这种复合泡沫材料的拉伸强度、拉伸模量分别提高了 6 倍和 8 倍,剪切强度和剪切模量也增加了 1.8 倍和 2.4 倍;与交联 R-PVC 发泡材料相比,这种材料的冲击强度,抗疲劳强度以及撕裂强度都提高了许多。
Dey S K 等通过将物理发泡剂注射到挤出机型腔内,通过挤出成型的工艺制备了 R-PVC 发泡型材。
通过此方法解决了 PVC 使用化学发泡剂挤出发泡成型的缺陷,如有机发泡剂分解残渣对设备、模具和产品的影响,有机发泡剂因在树脂中发生迁移而影响发泡的稳定性等,同时还可以较大程度地降低了成本。
Sharma V K 等以电子束为辐照源辐照交联改 PVC,分析了 TMPTA、TEGDA和 TEGDM 三种敏化剂对 PVC 热稳定性和交联速率的影响。
研究表明当 TMPTA添加量为为 5%时,PVC 交联效果最佳,拉伸强度达到了 23 MPa,比普通 PVC 提高了 7%,同时热分解温度提高了许多。
Tamas J 等采用三嗪类交联剂对 PVC 进行交联改性,改性条件为:温度 96 ℃,四丁基溴化铵的碱性溶液。
研究表明,交联 PVC 体系的拉伸强度和杨氏模量都得到了很大的提高,而断裂伸长率明显下降。
交联 PVC 产品的热变形温度显著提高,当聚合物的凝胶含量达到为 75%时,热变形温度提高了 13℃。
采用过氧化物和辐射交联 PVC 具有着色严重的缺点,而采用三嗪类化合物对 PVC 进行交联正好可以改善这一问题。
木塑复合材料加工技术研究现状及发展趋势

木塑复合材料加工技术研究现状及发展趋势随着近年来对环境保护意识的提高以及对可持续发展的追求,木塑复合材料作为一种环保、可持续发展的新型材料,得到了越来越广泛的应用。
木塑复合材料是以木材和塑料为主要原料,经过混合、挤压成型等工艺制成的一种新型材料。
它既保留了木材的天然质感和美观性,又具有塑料的耐候性和抗腐蚀性,具有良好的机械性能和性价比优势。
目前,木塑复合材料加工技术已经相对成熟,主要包括原料处理、混合、挤出成型、表面处理等环节。
原料处理包括木材和塑料的预处理,如木材的刨花、干燥和粉碎,塑料的研磨和预掺配等。
混合阶段是将木材颗粒和塑料颗粒按一定比例进行混合,再加入一定的添加剂,如防腐剂、助剂等。
挤出成型是将混合后的原料经过挤压成型机进行挤出,形成所需的产品形状。
最后,对挤出成型后的产品进行表面处理,如砂光、刮痕等,以增加产品的光洁度和表面质感。
目前木塑复合材料加工技术的发展趋势有以下几个方面:1.高效节能:通过改良挤出工艺和提高设备的效率,实现木塑复合材料的高效生产。
同时,优化工艺流程,减少能源消耗,实现节能效果。
2.精细化加工:加强对原料的处理和调控,提高木塑复合材料的品质和稳定性。
通过改善原料的成分和粒度分布,提高产品的强度和表面光洁度。
3.降低成本:通过改进加工工艺和降低原材料成本,降低木塑复合材料的生产成本。
例如,可以采用回收利用的木材和塑料,降低原材料的采购成本。
4.绿色环保:加强对木塑复合材料的环保性能的研究和开发。
例如,研发更环保的添加剂、改进废弃物的处理方法,减少木塑复合材料生产过程中的环境污染。
5.应用拓展:木塑复合材料具有广泛的应用前景,可以代替传统的木制品和塑料制品。
未来,木塑复合材料可以应用在建筑、家居、交通工具等多个领域,例如室内地板、室外装饰板、花箱、道路护栏等。
总之,木塑复合材料加工技术在不断发展,具有广阔的应用前景。
随着技术的进步和需求的增加,木塑复合材料的生产技术和加工工艺将迎来更多的创新和突破。
国内外木塑复合材料的研究进展

国内外木塑复合材料的研究进展摘要:阐述了木塑复合材料在21世纪的研究进展,涉及国内外在近几年的主要研究成果,介绍了包括界面相容性的改善方法、加工工艺的改进以及木塑复合材料的相关性能探讨,并提出了我国木塑复合材料今后的发展方向。
关键词:木塑;复合材料;研究进展木塑复合材料是国内外近年蓬勃兴起的一类新型复合材料,指利用聚乙烯、聚丙烯和聚氯乙烯等,代替通常的树脂胶粘剂,与超过50%以上的木粉、稻壳、秸秆等废植物纤维混合成新的木质材料,再经挤压、模压、注射成型等塑料加工工艺生产出的板材或型材。
主要用于建材、家具、物流包装等行业。
将塑料和木质粉料按一定比例混合后经热挤压成型的板材,称之为挤压木塑复合板材。
1 国内木塑复合材料研究进展木塑复合材料这种新兴的环保材料产品在世界范围得到越来越多的关注和认可,其生产量和使用量都在逐年快速增加。
我国在木塑复合材料方面的研究也一直处于进步状态,进行了大量有益的试验并取得不少成果。
2001年贺德留[1]等在低温和中温环境中进行两个阶段的化学反应引发聚合固化,实验中以速生劣质材杨木为基材,以有机单体甲基丙烯酸甲酯作为浸滞剂,并着以适当颜色,在真空状态下作浸滞处理,处理件在石蜡包围下,制造出木塑复合材料。
该技术实际应用中出现的问题有很多,但在此工艺基础上,通过制作杨木木塑复合材料地板试验已基本解决。
研究得出相关结果有:木材的含水率需要达到一定的指数才可以进行浸注;采用甲基丙烯酸甲酯为浸注液时,偶氮二异丁腈的有机单体量也有一定规定,而且把偶谈二异丁腈作为化学引发剂;微量加入还原剂亚铁离子的方法可以改变和强化复合材料的性能,但须注意要定期往循环浸注液中补加亚铁离子和化学引发剂;制作高硬度的木塑地板时可以在有机单体中加入色素(而且加入量是有一定的规定),这样既改变了复合材料颜色,同时增强了复合材料的性能;浸注过程的真空度尽可能保持不变,当浸注真空度和浸注时间达到要求的数值时可以制作木塑复合材料地板同时也满足材料的硬度要求很大时的情况;最后一步一定要及时进行石蜡包裹,石蜡油温度在一定数值时才能达到理想的包裹效果;有机单体在木材内的聚合固化程序时间也在实验中得到验证。
聚氯乙烯木塑材料的开发与应用进展

丙烯高温氯化法生产工艺成熟,具有生产大型化、连续化和自动化的特点,操作稳定,生产成本较低,其中间产物氯丙烯既可作为精细化工原料又可作为商品出售,再加上环化塔负压操作,反应器改进等先进技术的采用,反应收率,外排废水COD含量均比以前有较大的改进,仍然是目前环氧氯丙烷生产的主流工艺。
醋酸丙烯酯法虽然反应条件缓和,副产物少,而且氯气和石灰原料消耗减半,但该工艺存在着反应步骤多,需用不锈钢材料防醋酸腐蚀导致一次性投资较大,防止烯丙醇单元混合气爆炸的安全可靠性等不足,目前工业化生产基本上不采用该法。
甘油法相对于丙烯高温氯化法和醋酸丙烯酯法具有明显的成本优势和环保优势,不消耗丙烯,无须使用氯气,不需要昂贵的催化剂:操作条件缓和,成本低,投资少,仅为丙烯法的1/4,“三废”少,可实现清洁生产,具有较大的市场竞争力,将是今后发展的方向。
目前,我国环氧氯丙烷的生产主要采用丙烯高温氯化法,随着石油价格的大幅上涨,采用的丙烯高温氯化法生产路线面临越来越大的价格压力,大力发展环氧氯丙烷新的生产技术路线已迫在眉睫。
随着国内生产生物柴油装置的相继投产,副产物甘油的市场供应量将不断增大,因此,应该大力开发促进甘油生产环氧氯丙烷路线的发展,这样既能减少国家对石油的依赖,促进生物质能源产业的顺利发展,又能有利地促进我国环氧氯丙烷及相关行业的健康、有序、稳步发展。
聚氯乙烯木塑材料的开发与应用进展汪多仁(吉化公司石井沟联合化工厂132105)一、理化性质聚氯乙烯木塑料质轻、坚固、价廉、叫锯、可刨、可钉、可焊接和可黏的合复合材料。
它又是一种很好的隔音、隔热、保暖材料,用它制作的下水道同样具有质轻、价廉、抗冲击等优点。
二、工艺开发(一)操作过程硬聚氯乙烯人造木材是PVC与多种助剂经混合、造粒、挤出、发泡而成。
影响PVC基木塑复合材料性能的因素很多,例如热稳定剂.加工助剂、冲击改性剂、润滑剂、加工工艺、木粉的表面处理等都会对复合材种的性能产生影响。
PVC发泡板材的成型机理和发泡材料研究

PVC发泡板材的成型机理和发泡材料研究作者:苗伟来源:《科学与财富》2018年第23期摘要:随着森林和木材资源的日益紧张和国家对资源保护程度逐渐加强,以PVC材料代替木材已经大势所趋。
目前PVC发泡板材已经广泛应用于建筑、化工、医药等行业。
本文通过查阅大量PVC发泡板材的相关文献资料,主要介绍了PVC板材的分类、特点和性能,并对板材的成型机理和常见发泡材料进行了系统的总结,旨在为PVC发泡板材的生产、应用提供一定的参考价值。
关键词:PVC发泡板材;成型机理;发泡材料前言:PVC发泡板材指的是以PVC树脂为主要原料,加入包括稳定剂、发泡剂、润滑剂、发泡调节剂等辅助助剂,经过塑化、挤出发泡加工制备的不同形状的板状材料[1]。
PVC发泡板,即雪弗板、安迪板[2],由于具备较小的密度、较低的热导率,较好吸收噪音的效果,阻燃性好,耐腐蚀性能好,易于加工等优点而被建筑装潢、室内装修、公共建筑隔断板材、建筑地板等领域广泛应用[3]。
目前PVC发泡板材在国外应用较多,目前我国PVC发泡板材的年产量和发达国家相比还存在较大的差距,PVC发泡材料在各行各业还没有得到普及。
然而,随着木材、森林资源的日益紧张,以PVC来代替木材已经成为材料领域研究的热点,PVC发泡板材的发展前景广阔[4]。
不同应用领域所需要的PVC发泡板可能存在形状、性能上的差异,所需的发泡材料也不尽相同,这就决定了不同发泡板材的成型机理存在差异[5]。
1 PVC发泡板材1.1 PVC发泡板材的分类(1)根据发泡程度的不同可以将PVC发泡板材分为低发程度的发泡板材和高发程度的PVC发泡板材。
其中,发泡程度位于20倍以上的被称为高程度发泡板材,位于15倍以下的被称为低程度发泡板材[6]。
(2)根据泡体质地软硬程度的差异,可以将PVC发泡板材分为软质发泡板和硬质发泡板两大类。
其中软质PVC发泡板材的硬度和强度较小,发泡程度高,倍数大,常用于保温材料的制备[7]。
PVC-木粉复合微发泡新型材料的研制

书山有路勤为径;学海无涯苦作舟PVC/木粉复合微发泡新型材料的研制根据国家“九五”发展计划和二0一0年“以塑代木、以塑代钢、节约资源、保护环境”的远景目标规划,北京化工大学塑料机械及塑料工程研究所与上海宸得塑胶制品合作公司经过多年的攻关与研究,成功地研制出PVC/木粉复合新材料及其制品生产技术。
其特点是在PVC塑料原料中添加30-50%的木质纤维填料(木粉)和各种加工助剂如稳定剂、改性剂、润滑剂、发泡剂等,利用高速混合机混合后,经专用造粒挤出机制备成不同规格及等级的木塑颗粒,最后使用成型挤出机、模具及不同工艺生产各种形状的PVC木塑复合微发泡装饰型材。
其关键技术是保证木质粉料较高填充量,以达到制品有较低的生产成本和较高的使用性能,同时由于对木粉进行了表面处理,使其能被PVC 树脂很好地润湿,达到最佳结合界面。
该项目符合国家新上项目要以节材、节能、安全作为发展重点,满足市场需要,填补国内空白要求的精神,符合“以塑代木”、“以塑代钢”的长期技术国策。
PVC/木粉复合材料发展很快,以其高韧性、成本低等优势正逐步取代传统的木质品。
但聚氯乙烯与木粉复合后,其延展性和耐冲击性降低,材料脆性大,密度也比传统木质品高出近2倍,这些因素限制了它的广泛使用。
为了消除上述缺点,通常采用添加冲击改性剂的方法提高其冲击性能,但这种方式对改善制品的延展性和降低密度几乎无效。
近几年,研发方向转向微发泡成型技术,经发泡后的PVC/木粉复合材料由于存在良好的泡孔结构,可钝化裂纹尖端并有效阻止裂纹的扩张,从而显着提高材料的抗冲击性能和延展性,而且大大降低了制品的密度。
挤出微发泡法以其成专注下一代成长,为了孩子。
PVC/木粉复合材料的挤出研究

现 代 塑 料 加 工 应 用
200 7年 第 19卷 第 2 期
・ 27 ・
ห้องสมุดไป่ตู้
M 0DERN PLAS CS PR0CES NG TI SI AND APP CAT1 LI 0NS
P C 木 粉 复合 材 料 的挤 出研 究 V /
孔 展 张 卫 勤 洪筱 茜 张 帆 王长 胜 李 绍 鹤
(. I 1 四J 大学 高分 子 科 学 与 工 程 学 院 ,四J 成 都 ,6 0 6 ; I I I 10 5
2 四 川 绵 阳 英 联 高 新 技术 有 限 责任 公 司 ,四 J 绵 阳 ,2 0 6 . I I I 610)
摘 要 : 用 聚氯 乙烯 ( VC 与木 粉制 得 P / 粉 复合 材 料 。研 究 了 木 粉 的 含 量 、 联 剂 的类 型 和 含 量 、 苯 二 甲酸 二 采 P ) VC 木 偶 邻
PVC,CPE s 1 0 i 0.
o he ma s ofPVC. ft s
Ke r s o y v n l h o i e ;wo d f u ;c mp st ;e t u i n y wo d :p l ( i y l rd ) c o l r o o ie x r so o
Su yo tuino oy vn i ho ie / o dFo rC mp st td nExr s f l(iy c lrd ) W o lu o oi o P e
Ko ng Zha n Zh n e q n a g W ii H o a in ng Xioq a Zh ng Fa a n W a g Cha gs n n n he g LiSha e oh (1 Co lgeofPo y r S inc n . le l me ce e a d Eng ne rn i e i g,Sihua i e s t c n Un v r iy,Che g n du,Sihu n,61 0 c a 0 65; 2 M iny n n in Hi h Te hn og .,Lt . a a g Yi gl g c ol y Co a d.,M i n ng,Sihu n,6 0 a ya c a 2 06 ) 1
PVC木塑发泡材料性能的研究

PVC木塑发泡材料性能的研究李静;刘浩;刘容德;张桦【摘要】研究了PVC树脂基本性能(聚合度、分子质量分布、表观密度)、助剂(发泡剂、发泡调节剂)、木粉及加工工艺(加工温度、挤出速度)对PVC木塑发泡材料性能的影响,并进行了工业化加工试验.结果表明:PVC树脂聚合度越高,发泡材料泡孔壁厚越大,发泡及加工都变得较为困难,适宜的聚合度为650~ 700;PVC树脂分子质量分布变宽,则发泡材料的密度增大,泡孔数量减少,泡孔增大,泡壁增厚,有串泡现象,适宜的分子质量分布指数为1.9 ~2.0;表观密度越高,机身压力越大,发泡材料泡孔数量越多,泡孔结构越均匀,适宜的表观密度为0.57~0.60 mL/g.对于S-700型PVC树脂而言,发泡剂ADC与助发泡剂ZnO的适宜质量比为1∶0.1,且二者的总用量以1.0份为宜;发泡调节剂ZB-530的适宜用量为8份;适宜的加工温度为185℃,适宜的挤出速度为20 r/min.宜采用硅烷偶联剂对木粉进行表面改性,发泡剂、发泡调节剂的用量应随着木粉用量的变化而调整.工业化加工试验结果表明:根据制品及生产设备的不同对试验得出的配方和加工工艺进行调整后,可顺利生产出质量优良的产品.【期刊名称】《聚氯乙烯》【年(卷),期】2017(045)001【总页数】11页(P9-19)【关键词】PVC;木塑;发泡;性能;加工应用【作者】李静;刘浩;刘容德;张桦【作者单位】中国石油化工股份有限公司齐鲁分公司研究院,山东淄博255400;中国石油化工股份有限公司齐鲁分公司研究院,山东淄博255400;中国石油化工股份有限公司齐鲁分公司研究院,山东淄博255400;中国石油化工股份有限公司齐鲁分公司研究院,山东淄博255400【正文语种】中文【中图分类】TQ325.3【材料与性能】目前,塑料市场研究的热点之一是木塑材料,即以塑代木。
兼具木材、塑料优点的木塑材料不但有利于保护森林资源、降低产品成本,还具有优异的木质感、美观、耐腐蚀、强度高等优点。
木塑复合材料加工技术、研究现状及发展趋势
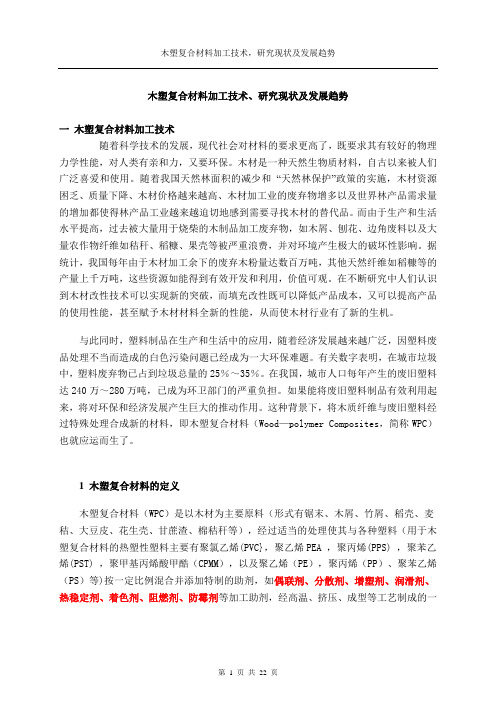
木塑复合材料加工技术、研究现状及发展趋势一木塑复合材料加工技术随着科学技术的发展,现代社会对材料的要求更高了,既要求其有较好的物理力学性能,对人类有亲和力,又要环保。
木材是一种天然生物质材料,自古以来被人们广泛喜爱和使用。
随着我国天然林面积的减少和“天然林保护”政策的实施,木材资源困乏、质量下降、木材价格越来越高、木材加工业的废弃物增多以及世界林产品需求量的增加都使得林产品工业越来越迫切地感到需要寻找木材的替代品。
而由于生产和生活水平提高,过去被大量用于烧柴的木制品加工废弃物,如木屑、刨花、边角废料以及大量农作物纤维如秸秆、稻糠、果壳等被严重浪费,并对环境产生极大的破坏性影响。
据统计,我国每年由于木材加工余下的废弃木粉量达数百万吨,其他天然纤维如稻糠等的产量上千万吨,这些资源如能得到有效开发和利用,价值可观。
在不断研究中人们认识到木材改性技术可以实现新的突破,而填充改性既可以降低产品成本,又可以提高产品的使用性能,甚至赋予木材材料全新的性能,从而使木材行业有了新的生机。
与此同时,塑料制品在生产和生活中的应用,随着经济发展越来越广泛,因塑料废品处理不当而造成的白色污染问题已经成为一大环保难题。
有关数字表明,在城市垃圾中,塑料废弃物已占到垃圾总量的25%~35%。
在我国,城市人口每年产生的废旧塑料达240万~280万吨,已成为环卫部门的严重负担。
如果能将废旧塑料制品有效利用起来,将对环保和经济发展产生巨大的推动作用。
这种背景下,将木质纤维与废旧塑料经过特殊处理合成新的材料,即木塑复合材料(Wood—polymer Composites,简称WPC)也就应运而生了。
1 木塑复合材料的定义木塑复合材料(WPC)是以木材为主要原料(形式有锯末、木屑、竹屑、稻壳、麦秸、大豆皮、花生壳、甘蔗渣、棉秸秆等),经过适当的处理使其与各种塑料(用于木塑复合材料的热塑性塑料主要有聚氯乙烯(PVC},聚乙烯PEA ,聚丙烯(PPS) ,聚苯乙烯(PST) ,聚甲基丙烯酸甲酷(CPMM),以及聚乙烯(PE),聚丙烯(PP)、聚苯乙烯(PS)等)按一定比例混合并添加特制的助剂,如偶联剂、分散剂、增塑剂、润滑剂、热稳定剂、着色剂、阻燃剂、防霉剂等加工助剂,经高温、挤压、成型等工艺制成的一种新型复合材料,是一种高性能、高附加值的绿色环保复合材料,其性能优良、用途广泛、利于环保,有广阔的发展前景,值得大力研发推广。
「木塑复合材料加工技术研究现状及1发展趋势」

「木塑复合材料加工技术研究现状及1发展趋势」木塑复合材料是一种使用木粉和塑料混合制成的新型材料。
它具有木材的外观和质感,同时又有塑料的耐候性和耐腐蚀性。
在近年来,由于其良好的性能和环保特点,木塑复合材料在建筑、家具、装饰等领域得到了广泛应用。
本文将主要探讨木塑复合材料加工技术的研究现状及未来的发展趋势。
目前,木塑复合材料加工技术主要包括干法加工和湿法加工两种方法。
干法加工利用粉状的原料进行混合,然后通过挤出、压制等工艺进行成型。
这种加工技术工艺简单,适用于大规模生产。
湿法加工则是在塑料中添加溶解了的木粉,然后通过挤出、注塑等方法进行成型。
湿法加工可以生产出具有更好强度和耐用性的产品。
在木塑复合材料的加工过程中,添加剂起到了至关重要的作用。
添加剂可以提高材料的强度、耐火性、耐候性等性能。
目前常用的添加剂有阻燃剂、稳定剂以及抗氧化剂。
未来的研究重点将放在开发更加环保的添加剂,并减少对原料的消耗。
另外,木塑复合材料在加工过程中也面临一些挑战。
木材纤维与塑料之间的界面相容性较差,容易发生分离现象。
为了解决这个问题,目前的研究主要集中在改进界面增强剂的性能,提高木材纤维与塑料之间的粘接强度。
此外,优化挤出工艺参数、提高挤出速率等方法也被广泛研究,以增加生产效率和降低成本。
未来木塑复合材料的发展趋势主要在于提高产品的性能和降低成本。
与市场上的竞争越来越激烈,产品的性能要求也越来越高。
因此,研究人员将更多地关注添加剂的开发,以提高产品的质量和性能。
在成本方面,减少对昂贵的原料的需求,提高生产效率将是未来的重点研究方向。
总之,木塑复合材料作为一种绿色环保的建材,具有很大的发展潜力。
在加工技术方面,未来的研究将集中在开发环保的添加剂,改善界面相容性,优化加工工艺参数等方面。
通过这些努力,木塑复合材料的应用范围将会更广泛,更深入地渗透到人们的日常生活中。
木塑复合材料挤出技术研究
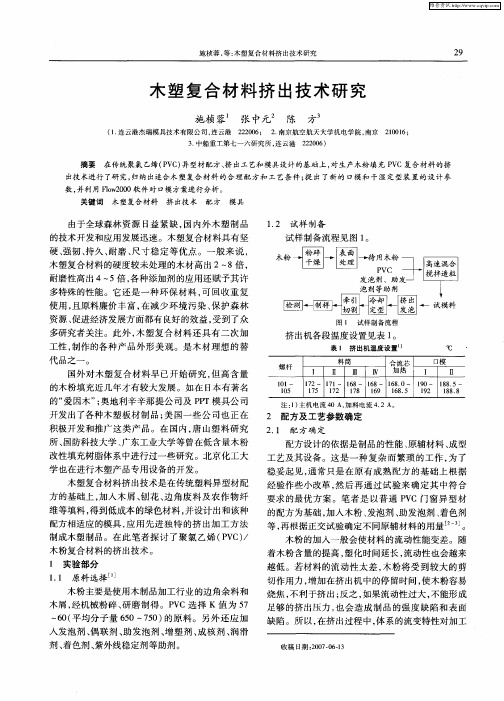
摘要
在传统聚氯 乙烯 ( V ) P C 异型材配方、 出工 艺和模具设计的基础 上 , 挤 对生产木纳 出适合木塑复合 材料 的合理 配方和 工 艺条 件 ; 出了新的 口模 和 干湿定型 装置 的设计参 提 数, 并利用 Fo 2 0 l 00软件 对 口模方案进行分析。 w
等, 再根 据正交试 验 确定不 同原辅 材料 的用 量 J 。
维等填料 , 得到低成本的绿色材料 , 并设计 出和该种
配方相适应 的模 具 , 用先 进 独特 的挤 出加 工 方 法 应 制成 木塑 制品 。在 此笔 者 探讨 了聚 氯 乙烯 ( V / P C)
木粉 的加 入一般 会使 材料 的流动性 能变 差 。随 着 木粉含 量 的提高 , 塑化 时 问延 长 , 流动性也 会越来
维普资讯
施桢蓉 , 木塑复合材料挤出技术研究 等:
2 9
木 塑 复 合材 料 挤 出技术 研 究
施 桢 蓉 张 中元 陈 方
(. 1 连云港杰瑞模具技术有限公司, 连云港 2 2 0 ; 2 南京航空航天大学机电学 院, 2 0 6 . 南京 22 0 ) 2 0 6 201 10 6; 3 中船重工第七一六研究所 , 云港 . 连
木 粉复合 材料 的挤 出技术 。
1 实验 部分 1 1 原料 选择 … . 木粉 主要是使 用木 制 品加 工行业 的边 角余 料和 木屑, 经机 械粉 碎 、 研磨 制 得 。P C选 择 K值 为 5 V 7
~
越低 。若材料的流动性太差 , 木粉将受到较大的剪
切 作用力 , 增加 在挤 出机 中 的停 留时 问 , 使木 粉容 易
表 2 P / 粉 复 合 材 料 的 加 工 性能 VC 木 木 粉 含量 / 份
木塑复合材料挤出成型研究进展

度 升 高并 降低熔 体 粘 度 , 成 气 泡 合 并或 产 生大 气 造
泡 。 因此 , 用 吸热 型 发 泡 剂 通 常 得 到 良好 的气 泡 采
结构 , 而采用 放热 型 发 泡 剂 通 常 得 到 较差 的气 泡 结
进 行 , 头 的温度应 分段 控 制 , 机 即温 度逐 渐 降低 ‘ 。 剖。
出料 ; 当机头 温度 过 高 时 , 头 压 力 降 低 , 出制 品 机 挤
有很 明显 的撕边 现象 , 寸稳定 性 变差 , 至会 造成 尺 甚
物 料无 法定 型 。因此 , 头 温度 应 根 据 物料 的具 体 机 情 况确 定一个 合 理 的范 围 。另 外 , 为保 证 挤 出顺 利
制 品。但机 头压力 并 不是越 大 越好 。对 于 排气挤 出 机 , 头压力 的 上 限与 计 量 段 的充 满 长 度 有关 。 当 机
充满长 度超过 排气 口时 , 出机 的 螺杆 扭 矩 上 升 并 挤
中 图 分 类 号 :T 2 . Q33 6 文献标识码 : A 文 章 编 号 :6 1 3 0 (0 1 0 17 — 26 2 1 ) 6—19 —0 02 3
Re e r h p o r s f W PC x r so o d n s a c r g e so e tu in m lig
由于 木粉 在 2 0℃ 左 右 即分 解 变 色 , 0 因此 , C 的 WP 挤 出温 度不 宜 >2 0o 0 C。 1 3 螺杆 转 速 .
构 和大 尺 寸 的气 泡 [ ] ¨ 。但 Me glg ne l o u等[ 】 】 在研 究 P C基 WP V C的 挤 出 发 泡 时 发 现 , 吸 热 型 发 泡 剂 与 NH O a C 相 比, 用放 热型 的 A 使 C发 泡剂 能得到尺 寸 更 小 的 泡 孑 。 挤 出 温 度 、 杆 转 速 和 机 头 压 力 对 L 螺 WP C的化学 发 泡 有 重 大 影 响 。挤 出 温度 与 发 泡 剂
木塑复合材料发泡成型技术研究进展

第33卷第9期2005年9月塑料工业CHINAPIASTICSINDUSTRY木塑复合材料发泡成型技术研究进展敖欢。
刘廷华。
(四川大学高分子科学与工程学院,四川成都6l0065)摘要:介绍了PE、PP、Pvc、PS和聚氨酯基等类型木塑复合材料发泡成型技术的最新研究进展,并简述了加工过程中水分的影响、温度的控制及主要成型设备的特点。
关键词:木塑;复合材料;发泡;成型技术中图分类号:’rQ323.9文献标识码:A文章编号:1005—5770(2005)09—0001一03TechnologyAdVancesofWood/PIasticsCompositeFoamA0Huan,LIUTing-hua(CollegeofPolymerSci.andEng.,SichuanUIliversity,Chengdu610065,China)Abs觚ct:1herecentdevel叩mentsofthefoam咖uldingofthecompositesofPE,PP,PvC,PSa11dPUwithwcH0dareintmduced.TheirdluenceofwatercontentontIlepmcessing,contmllingoftemperature肌dchamc-teristicsofthemainpmcessingequipmentsarealsosu㈣rized.Keywords:W00d/Plastics;CompoSite;Fo眦ing木塑复合材料(wPc)是将有机纤维素填料如木材、糠壳、竹屑、豆类、亚麻、稻杆、玉米淀粉和坚果硬壳等以粉状、纤维状和刨花等形态作为增强物或填料加入到热塑性或热固性塑料中进行复合得到的新型功能材料。
早在1907年,LeoHBend博士就利用热固性酚醛树脂与木粉复合制得了木塑复合材料L1J。
与现有大多数无机填料如碳酸钙和玻纤等相比:纤维素填料具有原料易得、成本低、密度小、对设备磨损小、无污染和可降解等优点。
木塑复合材料的研究进展

木塑复合材料的研究进展
1.材料组成和制备方法:木塑复合材料的组成取决于木材和塑料的比
例以及其他添加剂的使用。
目前广泛采用的制备方法包括挤出、压制和注
射成型等技术。
2.力学性能:研究人员对木塑复合材料的力学性能进行了广泛的研究。
通过调整木材和塑料的比例以及添加剂的使用,可以改变复合材料的力学
性能,使其适应不同的应用领域。
3.耐久性:木塑复合材料在户外应用中暴露在各种恶劣的气候条件下,需要具备较好的耐久性。
研究人员通过添加抗氧化剂和紫外线吸收剂等添
加剂,提高木塑复合材料的耐久性。
4.界面性能:由于木材和塑料之间存在界面相互作用,研究人员对木
塑复合材料的界面性能进行了深入的研究。
通过改进界面结构或添加界面
改性剂,可以提高复合材料的界面性能,增强其力学性能和耐久性。
5.可再生性:考虑到对可持续发展的需求,研究人员也关注木塑复合
材料的可再生性。
目前一些研究主要集中在利用废旧塑料和废旧木材制备
木塑复合材料,从而减少资源浪费和环境污染。
总的来说,木塑复合材料的研究进展已经取得了一些重要的成果,但
仍存在一些挑战。
例如,如何实现木材与塑料之间更好的相容性和界面结合,如何降低木塑复合材料的成本和改进其可再生性等。
随着科技的不断
发展和研究人员的不懈努力,木塑复合材料将在更广泛的领域得到应用,
为社会和环境带来更大的利益。
PVC木塑复合材料挤出发泡的研究进展
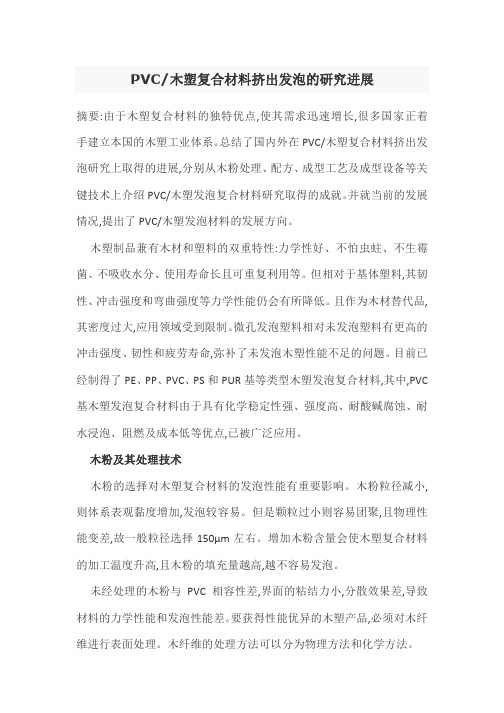
PVC/木塑复合材料挤出发泡的研究进展摘要:由于木塑复合材料的独特优点,使其需求迅速增长,很多国家正着手建立本国的木塑工业体系。
总结了国内外在PVC/木塑复合材料挤出发泡研究上取得的进展,分别从木粉处理、配方、成型工艺及成型设备等关键技术上介绍PVC/木塑发泡复合材料研究取得的成就。
并就当前的发展情况,提出了PVC/木塑发泡材料的发展方向。
木塑制品兼有木材和塑料的双重特性:力学性好、不怕虫蛀、不生霉菌、不吸收水分、使用寿命长且可重复利用等。
但相对于基体塑料,其韧性、冲击强度和弯曲强度等力学性能仍会有所降低。
且作为木材替代品,其密度过大,应用领域受到限制。
微孔发泡塑料相对未发泡塑料有更高的冲击强度、韧性和疲劳寿命,弥补了未发泡木塑性能不足的问题。
目前已经制得了PE、PP、PVC、PS和PUR基等类型木塑发泡复合材料,其中,PVC 基木塑发泡复合材料由于具有化学稳定性强、强度高、耐酸碱腐蚀、耐水浸泡、阻燃及成本低等优点,已被广泛应用。
木粉及其处理技术木粉的选择对木塑复合材料的发泡性能有重要影响。
木粉粒径减小,则体系表观黏度增加,发泡较容易。
但是颗粒过小则容易团聚,且物理性能变差,故一般粒径选择150μm左右。
增加木粉含量会使木塑复合材料的加工温度升高,且木粉的填充量越高,越不容易发泡。
未经处理的木粉与PVC相容性差,界面的粘结力小,分散效果差,导致材料的力学性能和发泡性能差。
要获得性能优异的木塑产品,必须对木纤维进行表面处理。
木纤维的处理方法可以分为物理方法和化学方法。
1.物理方法物理方法不改变纤维的化学成分,但改变纤维的结构和表面性能,从而改善纤维与基体聚合物的物理粘合。
热处理能够除去植物纤维吸附的水分和低沸点物质,但不能除去大部分的果胶、木质素及半纤维素。
由于植物纤维各成分热膨胀系数的差别和水分等物质的挥发,使纤维产生空洞和缺陷,导致木纤维拉伸强度、弹性模量和韧性随着热处理温度升高而下降。
碱处理不改变纤维素的化学结构,但植物纤维中的果胶、木质素和半纤维等低分子杂质能被碱溶解,使表面变粗糙。
挤出成型新进展

挤出成型新进展一、挤出成型新工艺随着聚合物加工的高效率和应用领域的不断扩大和延伸, 挤出成型制品的种类不断出新, 挤出成型的新工艺层出不穷, 其中主要有反应挤出工艺、固态挤出工艺、共挤出工艺、木塑复合材料挤出工艺、精密挤出工艺、气体辅助成型、微孔发泡挤出成型工艺。
(1)反应挤出工艺反应挤出工艺是20 世纪60 年代后才兴起的一种新技术, 是连续地将单体聚合并对现有聚合物进行改性的一种方法, 因可以使聚合物性能多样化、功能化且生产连续、工艺操作简单和经济适用而普遍受到重视。
该工艺的最大特点是将聚合物的改性、合成与聚合物加工这些传统工艺中分开的操作联合起来。
反应挤出成型技术是可以实现高附加值、低成本的新技术, 已经引起世界化学和聚合物材料科学与工程界的广泛关注, 在工业方面发展很快。
与原有的挤出成型技术相比, 它有明显的优点: 节约加工中的能耗; 避免了重复加热降低了原料成本; 在反应挤出阶段, 可在生产线上及时调整单体、原料的物性, 以保证最终制品的质量田〕。
反应挤出机是反应挤出的主要设备, 一般有较长的长径比、多个加料口和特殊的螺杆结构。
它的特点是熔融进料预处理容易; 混合分散性和分布性优异; 温度控制稳定; 可控制整个停留时间分布; 可连续加工; 未反应单体和副产品可以除去; 具有对后反应的限制能力; 可进行粘流熔融输送; 可连续制造异型制品。
2 固态挤出工艺固态挤出是使聚合物在低于熔点的条件下被挤出口模。
固态挤出一般使用单柱塞挤出机, 柱塞式挤出机为间歇式操作。
柱塞的移动产生正向位移和非常高的压力, 挤出时口模内的聚合物发生很大的变形, 使得分子严重取向, 其效果远大于熔融加工, 从而使制品的力学性能大幅度提高。
固态挤出有直接固态挤出和静液压挤出两种方法〔川。
在直接固态挤出中, 预成型的实心圆棒状物料〔29J 被放人料筒, 柱塞直接接触固体物料, 推动物料从口模中挤出。
在静液压挤出中,挤出所需的压力由柱塞经润滑液传递至料锭, 料锭形状与口模相配合以防止润滑液漏失。
- 1、下载文档前请自行甄别文档内容的完整性,平台不提供额外的编辑、内容补充、找答案等附加服务。
- 2、"仅部分预览"的文档,不可在线预览部分如存在完整性等问题,可反馈申请退款(可完整预览的文档不适用该条件!)。
- 3、如文档侵犯您的权益,请联系客服反馈,我们会尽快为您处理(人工客服工作时间:9:00-18:30)。
泡孔调节剂 ZB-530 和 K-400 对 PVC 体系有促进塑化、改善 表观质量、提高熔体强 度及延展度的作用。尿素、碳酸锌、柠檬 酸、醋酸锌、硫酸铬和甘油等助发泡剂活化 后通常能够增加 AC 发泡剂的发气量。 2. 3 增塑剂 F.Mengeloglu[15]、L.M.Matuana 等[11, 12]通过试验证实,增 塑剂 DOP(邻苯 二甲酸二辛酯)可以降低 PVC/木粉复合材料黏 度, 有利于气体在基体中的扩散和泡孔的 生长, 但如果增塑剂 用量过大, 会导致黏度过低, 加速气体从发泡材料的表面溢出, 反 而不利于形成较高的孔隙度。苑会林等[16]减少木粉分解,改善 PVC 和 木粉的亲和性以及熔体流动性,最终改善了材 料的力学性能和加工性能。其它常用的增塑剂有丙烯酸、邻苯二甲酸二丁酯、癸二酸二 辛酯等。其最佳用量为 6% ~8%。 2. 4 润滑剂 加入适量的润滑剂可以提高物料流动性、改善制品表面光泽,也影响发泡气体在熔 体中的混合与分布,从而影响泡孔结构。润滑剂太少,物料流动性差,发泡后易拉伤制 品表面;过多则物料流动性过大,挤出压力过小,不利于泡孔成核。PVC/木塑发泡中常 用的润滑剂有聚乙烯蜡、硬脂酸、硬脂酸铅、石蜡等, 一般用量为 1~4 份。 2. 5 冲击改性剂 L.M.Matuana 等[12]发现, 改性剂 CPE(氯化聚乙烯)可提高 PVC/木塑复合材料的冲击 强度、弯曲强度、压缩强度。ACR (丙烯酸酯类)用作 PVC 的抗冲改性剂与 CPE 相比,具 有优良的抗冲击效果,加工温度范围宽,生产稳定性好,产品表面光泽度和尺寸稳定性 好,且适合高速挤出。L.M.Matuana 等[17]还发现,冲击改性剂的类型和用量对 PVC/木 塑复合材料发泡的孔隙率及 CO2 吸收行为有影响。任何类型的冲击改性剂都会加速发泡 过程中气体的散失,从而阻止泡孔核的生长,因而对制品高孔隙率的形成不利。CPE、EV A(乙烯-醋酸乙烯共聚物)、MBS、ACR 是目前常用的几种 PVC 冲击改性剂。用量通常在 5 ~9 份之间。 2. 6 其他助剂 除了上述主要助剂外, PVC/木塑发泡制品中还需添加稳定剂、防霉剂、着色剂、 阻燃剂等,这些助剂对 PVC/木塑复合材料的发泡性能影响也不应忽视。各组分对发泡的 影响并不是孤立的,国明成[18]的研究表 明:木粉不经表面处理,则增塑剂对复合材 料的孔隙率几乎没有 影响,因为 PVC 与纤维之间的界面粘合性差,气体可以在发泡过 程中通过界面间的通道很快散失。各组分的作用也不是单一的, ZnSt(硬脂酸锌)既是 很好的润滑剂,又是 PVC 的热稳定剂和 AC 的助发泡剂;应该系统、综合地考虑各组分含 量的影响。 3 成型工艺及设备 良好的加工工艺和设备应保证物料和发泡剂混合均匀,并保持足够高的、稳定的机 头压力,使口模压力足够大和压力降足够快,以获得形态良好的泡孔。 3. 1 混料和喂料 混料工艺通过影响不同组分之间的接触与反应影响各组分的分散,进而影响材料性 能[19]。混料时,应该选择合适的加料顺序、加料温度、加料时间。 由于木粉粉料蓬松,加料过程中容易出现“架桥”和“抱杆” 现象。加料不稳定 会使挤出波动,造成挤出质量降低,因此必须对加料方式和加料量作严格的控制,一般
PVC 木塑复合材料挤出发泡的研究进展
PVC/木塑复合材料挤出发泡的研究进展 邓运红 1,赵良知 1,李及珠 2 (1.华南理工大学工业装备及控制工程学院,广东,广州 510640; 2.广州华工百川 科技股份有限公司,塑料事业部,广东,广州 510640 ) 摘要:由于木塑复合材料的独特优点,使其需求迅速增长,很多国家正着手建立本 国的木塑工业体系。总结了国 内外在 PVC/木塑复合材料挤出发泡研究上取得的进展, 分别从木粉处理、配方、成型工艺及成型设备等关键技术上介绍 PVC/木塑发泡复合材料 研究取得的成就。并就当前的发展情况,提出了 PVC/木塑发泡材料的发展方向。 关键词:PVC;木粉;发泡;复合材料;进展 中图分类号:TQ325. 3 文献标识码:A 文章编号: 1001-9456(2008)06-0081-0 4 木塑制品兼有木材和塑料的双重特性:力学性好、不怕虫 蛀、不生霉菌、不吸收 水分、使用寿命长且可重复利用等。但相对于基体塑料,其韧性、冲击强度和弯曲强度 等力学性能仍会 有所降低。且作为木材替代品,其密度过大,应用领域受到限制。微 孔发泡塑料相对未发泡塑料有更高的冲击强度、韧性和疲劳寿命,弥补了未发泡木塑性 能不足的问题。目前已经制得了 PE、PP、PVC、PS 和 PUR 基等类型木塑发 泡复合材料, 其中, PVC 基木塑发泡复合材料由于具有化学稳定性强、强度高、耐酸碱腐蚀、耐水浸 泡、阻燃及成本低等优点,已被广泛应用。 1 木粉及其处理技术 木粉的选择对木塑复合材料的发泡性能有重要影响。木粉粒径减小,则体系表观黏 度增加,发泡较容易。但是颗粒过小则容易团聚,且物理性能变差,故一般粒径选择 15 0μm 左右。增加木粉含量会使木塑复合材料的加工温度升高[1],且木粉的填充量越高, 越不容易发泡。 未经处理的木粉与 PVC 相容性差,界面的粘结力小,分散效果差,导致材料的力学 性能和发泡性能差。要获得性能优异的木塑产品,必须对木纤维进行表面处理。木纤维 的处理方法可以分为物理方法和化学方法[2]。 1. 1 物理方法 物理方法不改变纤维的化学成分,但改变纤维的结构和表面性能,从而改善纤维与 基体聚合物的物理粘合。 热处理能够除去植物纤维吸附的水分和低沸点物质,但不能 除去大部分的果胶、木质素及半纤维素。由于植物纤维各成 分热膨胀系数的差别和水 分等物质的挥发,使纤维产生空洞和缺陷,导致木纤维拉伸强度、弹性模量和韧性随着 热处理温度升高而下降。 碱处理不改变纤维素的化学结构,但植物纤维中的果胶、木质素和半纤维等低分子 杂质能被碱溶解,使表面变粗糙。李兰杰[3]等发现在不使用相容剂的情况下,塑料基质 对木粉的浸润性差,较高的表面粗糙度会使复合材料的界面处更易形成孔洞缺陷,从而 使复合材料力学性能下降。使用相容剂可以改善塑料对木粉的浸润性,提高复合材料的 拉伸强度和冲击强度。RizviG.M.[4]等先将木粉在不同温度干燥,然后用丙酮萃取大部
采用强制加料装置或饥饿喂料,以保证挤出的稳定。 PVC/木粉复合材料挤出发泡成型一般分两步法和一步法两种工艺路线:两步法即先 造粒后成型;一步法即省去造粒工序,采用表面改性后的木粉与 PVC 粉经高速混合后直 接加料挤出。研究表明:母粒法(两步法)有利于提高 PVC/木塑的力学性能[20]。美国 Ci ncinnati 公司简化了原料的合成工序,采用电子称量、喂料,将木粉和其它组分直接加 入挤出机进料斗,使成本节省 40%以上。 3. 2 成型温度 设定挤出成型温度应考虑到物料在挤出机机筒内的物理作用和化学反应。加料段温 度既要保证物料能够快速熔融,阻止分解气体的逃逸,又要防止发泡剂提前分解;压缩 段和计量段温度设定则需要考虑到化学发泡剂分解温度和分解速率,木粉烧焦和 PVC 分 解等因素;机头温度应使熔体保持良好流动性的同时,具有足够的熔体黏度,以维持机 头内的熔体处于高压下,使之在机头内不发泡[21]。姚祝平[22]认为在充分塑化的条件 下, 应采用低温挤出。螺杆和成型模具等设备也应具有低温挤出特性,以保证泡孔有 良好的形态和较小的直径。加料段温度应控 制在 165℃以下,压缩段和均化段在 160~1 80℃之间,机头和口模设在 160℃以下。 3. 3 螺杆转速[23] 螺杆转速对挤出发泡的影响主要体现在以下几个方面:一是影响挤出压力,转速越 高,挤出机内压力越大,从而越有利于成核,成核的泡孔数目也越多,发泡率也就越高。 但压力过高时成核的泡孔生长受到抑制,影响泡孔的充分生长;二是螺杆转速越高,剪 切作用越强,剪切作用过强时容易使泡孔合并或破裂, 影响发泡体质量和低密度泡沫 塑料的形成;三是螺杆转速过高 或过低,使停留时间过短或过长,容易发生提前发泡 或发泡剂分解不充分等现象,不利于形成均匀细密的泡孔结构。因此在其它影响因素不 变的情况下,螺杆转速存在一个最佳值,一般在 12~18 r/min 之间。 3. 4 挤出压力 挤出压力不足会造成制品表面粗糙、强度低,而较高的挤出压力不仅能控制机头内 的含气熔体不提前发泡,而且使机头口模内外压差大,从而使压降速率高,有利于气泡 成核,成核的气泡数量增多,发泡率也随之增大,有利于得到均匀细密的泡孔结构。但 挤出压力过高对泡孔的生长不利。要得到适宜的机头压力,可以通过调节螺杆转速、机 头温度及口模形状来实现。 3. 5 成型设备 单螺杆挤出机主要靠摩擦输送物料,混炼效果差,木粉在机筒中停留时间长,易烧 焦,因此,在 PVC/木塑复合材料挤出中受到较大的限制。为了提高 PVC/木塑的混合效果, 用于 PVC/木塑加工的单螺杆应该设混炼区,或者先造粒,然后用粒料挤出成型,但这个 过程消耗了助剂,降低了 PVC 性能。由于单螺杆挤出机结构简单,挤出压力高,可以承 受大扭矩,投资少,维护费用低,目前仍占有一定的木塑设备市场。 锥形双螺杆挤出机具有物料停留时间短、停留时间分布窄、熔体温度控制效果好的 特点,因此减少了 PVC/木塑的分解,对其加工非常有利。加料段的螺杆直径和表面积大, 有利于蓬松 的 PVC、木粉混合物的压实和输送。低速条件下,锥形螺杆的高扭矩自然形 成对物料的压缩以及柔和的塑化,改善了木粉与 PVC 之间的浸润性。此外,计量段的直 径小也保证了黏性熔体能够充分流入机头[24]。 目前锥形双螺杆挤出机是国内外 PVC 木 塑成型的主要机种。
分挥发物,发现去除挥发物后有更好的泡孔形态。除了上述物理方法外,还有拉伸、压 延、热处理、混纺、电晕、低温等离子体、辐射等物理方法。 1. 2 化学方法 化学改性方法通过改变木粉或 PVC 表面的化学结构,以改善其极性,提高纤维与基 体树脂的界面粘结,也有利于纤维在基体中的均匀分散,是目前木粉处理的主要方法。 苑会林[5]等应用铝酸酯偶联剂和丙烯酸丁酯预聚物处理木塑进行发泡,发现铝酸酯偶联 剂处理提高了 PVC/木塑发泡板材的拉伸强度和冲击强度,而丙烯酸丁酯预聚物处理能够 改善熔体流动性。 钟鑫等[6]采用表面接枝甲基丙烯酸甲酯的方法处理木纤维,用硝酸铈铵作引发剂在 木纤维表面羟基处形成自由基,这些自由基与甲基丙烯酸甲酯发生反应,形成接枝物, 可增强其与 PVC 树脂的界面粘合性。 F.Mengeloglu[7]等发现氨基硅烷处理过的木纤维具有很强的碱性和供电子能力,而 PVC 经氨基硅烷处理后具有更强的酸性,使 PVC 与木粉在界面处发生化学反应,有效提高 了 PVC 和木粉的界面性能。 刘涛[8]等用钛酸酯偶联剂、油酸酰胺、聚氨酯预聚物 3 种表面改性剂对木粉进行处 理, PVC/木塑的力学性能均有不同程度的提高;聚氨酯预聚体对木粉进行表面处理, 还能明显改善复合体系的流变性能。 其他常用的化学表面处理剂有多异氰酸亚甲基多苯酯、甲基丙烯酸甲酯、马来酸酐 等。多种木粉表面处理方法相结合,利用组分之间的协同作用,往往可以获得更好的界 面性能。丁筠[9]等用适当质量分数的 NaOH 溶液浸泡木粉,然后再用硅烷偶联剂处理木 粉。碱溶液降低了木粉的亲水性,使硅烷偶联剂更易与木粉中的羟基发生反应。其界面 性能比只用硅烷偶联剂处理木粉更好。 2 PVC/木塑发泡配方 要获得形态良好的泡孔必须加入适当发泡剂,并通过调节配方,获得适当的熔体强 度、黏度和弹性。 2. 1 发泡剂 F.Mengeloglu[7]使用放热型发泡剂 AC (偶氮二甲酰胺)和吸热型发泡剂 NaHCO3 挤出 发泡 PVC/木塑,发现放热型发泡剂得到的泡孔尺寸较小。卜宪华[10]分别用 AC、NaHCO3、 OBSH (4, 4-氧代双苯磺酰肼)、AC/NaHCO3 复合发泡剂制得发泡 PVC/木塑复合材料, 发现 AC/NaHCO3 复合发泡剂发泡性能最优。因为 AC 在加工过程中分解放热造成熔体局部 过热,黏度降低,使分解生成的气体易逸出,难以饱和。使用 AC 和 NaHCO3 复合发泡剂 则可以改善这一情况。AC 用量为 0·5% ~ 1%时最佳。 L. M.Matuana 等[13]还研究了用木纤维中的水分作发泡剂来发泡硬质 PVC/木塑复合 材料,发现使用适量的丙烯酸发泡改性剂和调整挤出机头温度,可以完全使用木粉中的 水分作发泡剂发泡 PVC/木塑复合材料。 2. 2 助发泡剂 要获得泡孔比较均匀的发泡材料,首先发泡剂的分解温度与树脂的熔融温度接近, 其次是发泡剂应在树脂达到适宜黏度的温度范围内均匀放气;发泡剂 AC 的分解温度远高 于 PVC 的成型温度,因此,必须把 AC 的分解温度降到 PVC 的成型温度附近,并有较大的 发气量。邓辉等[14]使用纳米 ZnO 粒子作为 AC 的助发泡剂,将 AC 突发温度降至 130~1 60℃的范围内,且发气稳定、迅速,用量为 AC 的 10% ~30%。