新型纺纱1
新型纺纱的整经浆纱技术

新型纺纱的整经浆纱技术
新型纺纱的整经浆纱技术在纺织行业中具有重要的意义。
整经浆
纱是将纱线从纱锭拉出后形成纱带,再将纱带交织并浸渍纺织浆液,
最后加热并经过一系列处理后得到的成品。
这项技术的目的是提高纺
织品的质量和效率。
整经浆纱技术的关键在于浆纱的均匀性。
传统的浆纱工艺容易出
现纱线不均匀和节点过大等问题,导致纺织品质量下降。
而新型的整
经浆纱技术通过改进纱线拉伸和浆液浸润等环节,解决了这些问题。
首先,在纱线拉伸环节,采用了先进的拉伸机械装置,能够实现
对纱线的均匀拉伸,并保持纱线的一致性。
这样可以降低纱线的断裂率,并提高纱线的强度和光泽度。
其次,在浆液浸润环节,新型的整经浆纱技术采用了纳米技术,
使纺织浆液分子更好地渗透到纱线内部,提高纱线的浆液吸附能力。
这样可以使纱线更加平滑和柔软,提高纺织品的手感和舒适度。
最后,在加热和处理环节,新型整经浆纱技术运用了先进的加热
设备和处理工艺,确保纺织品经过加热后的表面平整度和色泽均匀度。
同时,减少了处理时间和能耗,提高了生产效率和经济效益。
综上所述,新型纺纱的整经浆纱技术通过改进纱线拉伸、浆液浸
润和加热处理环节,提高了纱线的质量和整经浆纱的效率。
这项技术
将对纺织行业的发展起到积极的推动作用,并有望在未来得到更广泛
的应用。
新型纺纱技术范文

新型纺纱技术范文随着科技的不断发展,纺织行业也在不断进步和创新。
新型纺纱技术的出现,为纺织品的生产提供了更高效、更节能、更环保的方法。
下面将介绍几种新型纺纱技术。
一、无纺布纺纱技术无纺布是一种新型的纺织品制造材料,它是通过纤维材料的单根纤维或纤维的网状物重新组装制成,而不经过纺纱和织造的传统纺织工艺。
与传统纺织品相比,无纺布具有较好的透气性、柔软性、防水性和抗菌性能。
无纺布纺纱技术主要包括干法纺、湿法纺和熔喷纺。
1.干法纺:干法纺是指将纤维原料通过风力或机械力使其悬浮在空气中,再经过静电或压力作用形成网状结构,然后通过加热或涂覆等工艺使其定型。
这种纺纱技术具有操作简便、生产效率高、成本低的特点。
2.湿法纺:湿法纺是将纤维原料加入到溶剂或溶液中,经过溶解、混合和过滤等处理后,通过喷细流的方式使纤维得以凝聚成片状纺丝。
湿法纺纱技术具有纤维均匀、纺丝速度快、纱线质量稳定的特点。
3.熔喷纺:熔喷纺是将熔融的纤维原料从微细孔喷射出来,经过凝结和拉伸等过程形成纤维丝,然后通过集束、冷却和拉伸等工艺使其定型。
熔喷纺纱技术具有纺纱速度快、成本低、纤维之间的结合力强的特点。
二、空气动力纺纱技术空气动力纺纱技术是一种通过高速气流将纤维原料进行纺丝的技术。
空气动力纺纱技术具有操作简单、纺纱速度快、纤维短节短的特点,适用于生产短纤维纱线和造粒丝等纤维产品。
通过调节气流速度和纤维原料的喷射角度,可以控制纺丝过程中纤维的拉伸和取向。
三、湿旋杯纺纱技术湿旋杯纺纱技术是一种通过旋转的杯状结构将纤维原料沉积在杯底的纺纱技术。
湿旋杯纺纱技术具有纺纱速度快、纤维稳定性高的特点,适用于生产高强度和高弹性的纤维纱线。
湿旋杯纺纱技术的关键是通过旋转底部的孔洞使纤维原料被拉伸和拉断,形成纤维丝。
四、气流喷射纺纱技术气流喷射纺纱技术是一种通过高速气流将纤维原料进行纺丝的技术。
气流喷射纺纱技术具有纺纱速度快、纤维耐磨性强的特点,适用于生产耐磨性和耐拉伸性要求较高的纤维纱线。
新型纺纱技术-精品文档
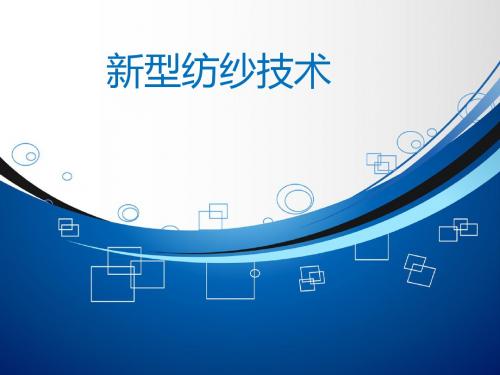
嵌入式复合纺纱
三、嵌入式复合纺纱存在的问题
第一 、生产操作难度大。生头难,需多人多次才能生一个头 ;挡车难, 在加捻三角区内须条断、丝不断,断头不易察觉。 第二 、设备利用率低。根据目前的状态,设备最多只能开50%的锭子;若 通过粗纱架改造来保证100%开机,将影响巡回清洁风机的运行,同时影响 其他机台操作。 第三、用短纤维纺粗号纱。前纺很难实现,高效短流程嵌入式纺纱指出只要 5mm 以上纤维就可以纺纱,没有指出前纺工序应该如何改进设备状况。事 实上,对于5mm 以上短纤维采用环锭纺纱在纺纱的前工序是不可能生产出 适合高效短流程嵌入式纺纱用粗纱的。目前的环锭纺纺纱对于并条机粗纱 机来说,纤维平均长度只可以实现不低于16mm 纤维的纺纱,而且 5%纤维 的长度最好在25mm 以上。
一、赛络菲尔纺的原理
sirofil则是利用一根长
丝与粗纱同时喂入细纱机,
长丝经预牵伸后直接喂入
细纱机的前罗拉钳口,并 与细纱机上同时喂入的粗
纱保持一定的间距 , 在前罗
拉钳口下游汇合加捻成纱。
塞络菲尔纺
二、赛络菲尔纺解决的问题
1、纱线质量的提高
由于长丝的存在以及它使短纤维集合得更紧密这两个原因,使得赛络菲尔纱的强 力高于同细度单纱,甚至优于同细度股线;另外由于短纤维须条被长丝较好地包缠, 使得纱线表面的毛羽较少;同时由于长丝的引入,纱线的条干明显改善,所以纱线质 量获得显著提高。
2、经济效益的提高
赛络菲尔纺纱技术是将牵伸、并合、加捻、卷绕成形在细纱机上一次完成,与传 统股线生产工艺流程相比,省去了并线和捻线工序,缩短了纺纱所用的时间,提高了 产量;另外,与同细度股线相比,细旦长丝的存在可以使所纺赛络菲尔纱线的截面纤 维根数减少,所用短纤维的细度降低一个档次,大大降低了生产成本。
新型纺纱技术

(1)自控程度高 (1)自控程度高
涡流纺整个纺纱过程受到电子系统的监控, 电子清纱器发现纱疵时即自动去除疵点,并立 即应用自动接头装置将纱接起来,因此整个纺 纱过程是全自动、连续式的。此外,每个锭子 的纱都受到自动接头器的监控,如有异常,可 实现单锭自动停止纺纱。
(2)工艺流程短 (2)工艺流程短
2、涡流纺的主要特点
涡流纺无高速回转机件采用旋转涡流加捻成纱,比 机械式加捻效率高,高速回转的涡流只作用在纤维 上,与前罗拉引出的纤维的功能一起形成对纤维的 加捻作用,高速涡流除了完成加捻任务外,并不影 响纱线支数的高低,因此可实现高速纺纱,最高纺 速实际可达380m/min,每锭的产量相当于环锭纺单 锭产量的22倍左右。由于纤维受到具有声速的喷气 涡流及卷取罗拉作用而形成真捻,因此这种特殊的 加捻作用是其它纺纱机械不能取代的,纱线高的回 旋速度下的成纱结构比环锭纱线的结构更为紧密和 稳定。
3、紧密纱线的特点
毛羽少,光洁度高。其毛羽一般比普通纱减少 70%-80%; 强度高,捻度减少。同样的纱支捻度减5%-15%, 而强力却提高约15%-25% ; 条干好。由于纤维的利用率得以提高,乌斯特条干能 够达到3%-5%; 能代替股线。由于紧密纱的强度高,其单纱可以替代 传统股线。如 16.2tex的紧密纱与8.1×2tex的传统股 线具有同等强度,在生产工艺上可以减少合股工序;
从以上紧密纱的特点可以看出它是一种与 众不同的高品质纱。由于它的优良特性给纺 纱、准备、织造、印染等一系列后道加工带 来了工艺创新,降低了后加工流程和成本, 尤其是减少了浆纱和烧毛对环境造成的工业 污染。
总之,紧密纺纱技术是目前环锭细纱机关键的重 要技术进步。纱线质量及生产费用等方面的优势,将 使紧密环锭纺纱技术不但本身具有高档产品的特征, 而且将逐步取代传统环锭纺纱技术,使纺织工业及时 装工业具有更开阔的产品开发空间,使服装设计可以 从紧密纱纺纱到最终产品进行一系列的设计,这种独 特的生产优势,一方面提高了产品档次,另一方面也 考虑了产品的经济性、生态环境特性、创新性及独特 性等。现在, 性等。现在,紧密纱在市场上的售价比传统环锭纱每公 斤高1 3.5美元,经济效益十分可观,更重要的是消费 斤高1-3.5美元,经济效益十分可观,更重要的是消费 者非常欢迎。因此,紧密纺纱技术将得到快速发展。
(完整版)主要新型纺纱的比较

主要新型纺纱的比较1、成纱原理:转杯纺依靠调整回转的纺杯,将纱尾贴紧在纺杯内壁聚槽内,而头端为引纱罗拉握持并连续输出加捻成纱。
喷气纺靠两只喷嘴喷射相反方向的回旋气流,对由牵伸装置输出的须条先加捻后解捻,表面纤维形成包缠成纱。
摩擦纺一般用两只同向回转的摩擦元件,对其楔形区的纤维施加摩擦力偶,使纤维束滚动而加捻成纱。
2、成纱截面中纤维根数不同:喷气纱中最少纤维根数略高于环锭纱,可纺中低线密度纱;摩擦纺和转杯纺中的最少纤维根数较多。
3、对纤维性能要求不同:影响转杯纱强力的主要因素是纤维的强力和线密度,摩擦纱则是纤维的摩擦因数和强力。
4、纺纱速度和成纱线密度:环锭纺的可纺线密度覆盖面最广,但产量太低,各种新型纺纱的纺纱速度都比环锭纺高,但可纺线密度有局限性5、新型特点:新型纺纱取消了锭子、筒管、钢领、钢丝圈等加捻卷绕元件,并将加捻和卷绕作用分开完成,具有产量高,细纱机的产量取决于锭子的速度,而锭速的提高,一方面受钢丝圈速度的限制,另一方面受气圈张力的限制;卷装大,环锭细纱机上增大卷装的途径是增加筒管长度和加大钢领直径,但筒管加长则气圈高度加长,钢领加大则钢丝圈线速度增大,这些都会导致断头增多,而新型纺纱方法将加捻和卷绕分开进行,可直接纺成筒子纱;工艺流程短,新型纺纱采用条子喂入,直接纺成筒子纱,省去粗纱、络筒两道工序。
转杯纺1、原理:纺杯高速旋转,纺杯内便产生离心力,离心力可使从分流腔转移到纺杯内的棉纤维产生凝聚而成为须条,须条被加捻后便成为纱条。
2、工艺过程:条子从条筒中引出送入喂给罗拉,喂给罗拉与喂给板将条子向前输送,经分梳辊分梳成单纤维,被补风口和引纱管的气流吸入纺纱杯,沿纺纱杯壁滑入凝聚槽形成凝聚须条,由于纺纱杯高速回转产生的离心力使引纱纱尾贴附于凝聚槽面而与须条连接,并被纺纱杯摩擦握持而加捻成纱。
3、转杯纱结构与性能:转杯纱由纱芯与外包缠纤维两部分组成,内层的纱芯比较紧密,外层的包缠纤维结构松散;环锭纱没有纱芯,纤维在纱中大多呈螺旋线排列。
新型纺纱方法

新型纺纱方法随着科技的发展,越来越多的行业开始应用新技术、新方法进行生产,纺纱业也不例外。
新型纺纱方法为我们提供了更加高效、智能化、环保的纺纱过程,本文将详细讨论新型纺纱方法所涉及的技术和应用。
1.电子纺纱:电子纺纱是一种采用电子技术进行纺纱的新型纺纱方法,其优点在于可以通过计算机自动化地控制纺纱的整个过程,从而实现了高效率、高精度、高灵敏度的纺纱工艺。
在电子纺纱过程中,将原料纤维进入电子纺纱机中,并采用电子束束角速压榨技术进行加工处理,可以使纳米材料直接变成长纤维,从而有效地提高了纱线强度和纱线的均匀度,充分发挥了原材料的潜力和使用效果,同时还可以大大降低成本,提高生产效率。
2.气流喷射纺纱:气流喷射纺纱方法是一种高精度、高效率、高质量、高环保的新型纺纱方法,主要用气流将纤维直接引入纺纱机中进行加工,从而实现纤维的均匀排布和控制,使之成为一种趋于完美的产品。
这种方法的优点主要在于可以彻底避免纤维切断及纤维松散等问题,同时还可以大大降低成本,缩短工期,使之成为纺织业的一种最佳选择。
3.超微孔纳米纺纱:超微孔纳米纺纱是一种最新型的纺纱方法,通过将纤维送入各种型号的纳米超微孔中进行加工处理,可以使得纤维制品抗洗、抗摩擦等性能更高,同时还可以改善织物的手感和表面光泽度。
该方法适用于各种纤维原料,可以有效地提高纺纱、生产效率和提高产品质量,同时还可以大大降低环境污染和有害气体排放。
4.气流纺纱:气流纺纱是一种新型纺纱方法,利用高速气流将原料纤维吹入纺纱机中进行纱线的制作,也常常称为“飞马纺纱”。
这种方法主要用于纤维粗糙、细度不一致和成28支以下的纱。
其特点主要在于:生产效率高,使用成本低,加工原材料多,纱的平滑度更高,成为了纺织行业中应用最广泛的一种纺纱方法。
新型纺纱方法的应用不仅仅改善了传统纺织过程,也大大提高了产量、质量和环境保护效果。
纺织业作为一个基础性的产业,应该不断探索创新,借助现代科技的力量实现更高效率、更高品质的纺纱生产。
新型纺纱内容

新型纺纱内容第一章绪论一.原始手工纺纱原理:利用回转体的惯性给纤维细条加上捻度。
二.手工机器纺纱原理:脚踏转动绳轮,双手同时纺纱。
三.动力机器纺纱(二)走锭纺纱机原理:罗拉将纤维条一端夹住。
锭子一边回转一边拉着纱条向外侧移动,将罗拉钳口与锭子间的纱条抽长拉细并加上捻回。
然后锭子一边回转,一边向罗拉方向退回,将加上捻度的纱绕到纱管上。
(三)翼锭纺纱机原理:拉细了的纤维条由罗拉钳口出来,先绕过锭帽的下缘,再绕到筒管上。
筒管回转时,罗拉钳口至锭帽下缘间一段纱也随着回转,从而给纱条加上捻度。
(四)环锭纺纱机1.原理:在锭杆四周套放固定环形轨道(钢领),轨道上骑跨下部有缺口的卵圆形钢丝圈。
纤维条从罗拉钳口下来,先穿过钢丝圈,再绕到套在锭杆上的纱管上。
锭子一回转,钢丝圈沿着钢领飞转,给纱条加上捻回,同时把纱条绕到纱管上。
2.特点:加捻和卷绕由同一零件(锭子)完成,两个动作同时进行。
加捻和卷绕组件合一,限制了成纱卷绕尺寸和运转速度。
3.固有缺陷:卷绕尺寸与运转速度之间产生了无法克服的矛盾,这种矛盾只有当加捻与卷绕机构分开时才能克服。
第二节新型纺纱技术概述一.新型纺纱的由来(一)传统纺纱与新型纺纱1.传统纺纱技术的优点(1)机构简单,维修保养方便。
(2)生产率较高。
(3)适纺性强。
(4)成纱质量好。
2.传统纺纱技术的缺点:加捻和卷绕组件合一,限制了成纱卷绕尺寸和运转速度,因而产量难以大幅度提高。
3.新型纺纱的范畴1965年以来发明的不同于传统纺纱技术的纺纱方法统称为新型纺纱。
(二)环锭纺纱技术的固有缺陷分析:1.受钢丝圈转速限制,生产速度不可能有突破性提高。
2.受钢领直径限制,卷绕容量不可能有大幅度提高。
三.新型纺纱的分类(一)按成纱原理分1.自由端纺纱:喂入点与加捻点之间的纤维须条是断开的,形成自由端,自由端随加捻器一起回转使纱条获得真捻。
如转杯纺、涡流纺、静电纺、摩擦纺DREF-II2.非自由端纺纱:喂入点与加捻点之间的纤维须条是连续的,须条两端被握持,借助假捻、包缠、粘合等方法使纤维抱合到一起,从而使纱条获得强力。
纺纱概论—新型纺纱

(4)纱条引出后经电子清纱 器去除疵点后被卷绕在筒子上。
新型纺纱—喷气纺纱
喷气纺纱的成纱结构特点
• 1、喷气涡流纺(MVS)纱 的结构特点 涡流纱也是一种双重结构的纱,纱条的芯纤维是平行排列的、无
捻度,依靠旋转气流的作用使末端纤维包覆缠绕于芯纤维外部加捻成 纱。但与喷气纱不同的是,涡流纱的外层覆盖纤维比重大(约60 %),以致内部未加捻的纤维几乎被完全覆盖,表面纤维排列则更近 似于环锭纱。纱线毛羽很少,织物起球现象亦减少,染色性能及耐磨 性好。 • 2、 喷气纺(MJS)纱线结构
新型纺纱
新型纺纱概述
新型纺纱概述
1、环锭纺的特点和存在的问题 •特点: ①加捻和卷绕不分 (同时由锭子、钢领、钢丝圈完成) ②成纱结构紧密,强度较高。 ③适纺不同线密度的纱线。(细纱机牵伸范围大) •存在的问题: ①钢丝圈和纱线张力的制约 ②气圈稳定性的影响。 ③产量很难大幅度提高。
新型纺纱概述
新型纺纱---自由端纺纱
1、转杯纺原料
①天然纤维:棉、亚麻 ②再生纤维素纤维:粘胶、莫代尔、天丝 ③合成纤维(短纤维):涤纶、腈纶、 ④棉纺厂再用棉:精梳落棉、清花落棉、梳棉落棉
2、适纺纱支范围
国内:10~30英支,国际:6~40英支
3、转杯纺工艺流程
①开清棉 → 梳棉→并条 (二道)→ 转杯纺纱机
(二)非自由端纺纱 一般经过罗拉牵伸——加捻——卷绕三 个工艺过程,即纤维条自喂入端到输出端呈连续状态,加捻器 置于喂入端和输出端之间,对须条施以假捻,依靠假捻的退捻 力矩,使纱条通过并合或纤维头端包缠而获得真捻。自捻纺纱 、喷气纺纱、粘合纺纱就属于这种方法。
新型纺纱
对几种新型纺纱的分析比较及其应用发展前景的看法

对几种新型纺纱的分析比较及其应用发展前景的看法新型纺纱是指利用新材料或新工艺进行纺纱加工的技术和方法。
随着科技的不断进步和纺织行业的发展,新型纺纱技术得到了广泛应用。
下面将对几种新型纺纱进行分析比较,并展望其应用发展前景。
首先,空气纺纱是一种新型纺纱技术,它通过将纺纱过程中的纤维与空气混合,形成纤维的悬浮状态,利用静电力、惯性力等原理使纤维自由自在地旋转,最终形成纱线。
空气纺纱具有纺纱效率高、生产成本低、纺纱过程中没有受力和磨损等优点。
与传统纱线相比,空气纺纱的纱线强度和弹性好,手感柔软,适用于制作高档面料和织物。
其次,喷射纺纱是另一种新型纺纱技术,它通过喷射装置将纤维和气流喷射到喷孔中,形成纤维悬浮状态,然后通过凝固或固化使纤维成为纱线。
喷射纺纱具有生产效率高、单根纱线质量稳定等优点。
与传统纺纱技术相比,喷射纺纱可以提高纱线层长和以较小的纤维长度形成较大的纱线层长,从而改善纺纱品质。
再次,电纺纺纱是一种利用高电压将聚合物熔体喷射并拉伸成纤维的新型纺纱技术。
电纺纺纱具有纺纱速度快、纺丝精度高等特点。
与传统纺纱技术相比,电纺纺纱可以制备出纤维直径小、纤维分散性好、比表面积大的纤维,适用于电子器件、过滤材料、医用材料等领域。
最后,纺织3D打印是一种将纺织品与3D打印技术相结合的新兴技术。
它通过将纺织机构和3D打印机构融合在一起,实现对纺织品的自由定制和复杂结构的制造。
纺织3D打印具有灵活性高、生产效率高、资源利用率高等优势。
它可以用于制作个性化的服装、家居装饰品等,为纺织品行业带来巨大的创新和变革。
综上所述,新型纺纱技术在纺织行业中具有广阔的应用前景。
这些新技术不仅提高了纺纱的效率和质量,还拓宽了纺织品的应用领域。
随着科技的进步和创新的不断涌现,相信新型纺纱技术将继续取得突破性进展,为纺织行业的发展注入新的动力。
《新型纺纱技术》PPT课件
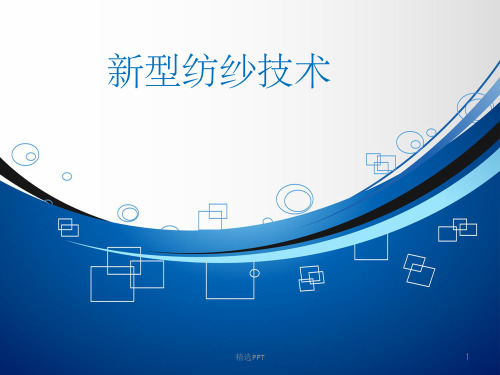
2、经济效益的提高
赛络菲尔纺纱技术是将牵伸、并合、加捻、卷绕成形在细纱机上一次完成,与传 统股线生产工艺流程相比,省去了并线和捻线工序,缩短了纺纱所用的时间,提高了 产量;另外,与同细度股线相比,细旦长丝的存在可以使所纺赛络菲尔纱线的截面纤 维根数减少,所用短纤维的细度降低一个档次,大大降低了生产成本。
精选PPT
14
嵌入式复合纺纱
三、嵌入式复合纺纱存在的问题
第一 、生产操作难度大。生头难,需多人多次才能生一个头 ;挡车难, 在加捻三角区内须条断、丝不断,断头不易察觉。 第二 、设备利用率低。根据目前的状态,设备最多只能开50%的锭子;若 通过粗纱架改造来保证100%开机,将影响巡回清洁风机的运行,同时影响 其他机台操作。 第三、用短纤维纺粗号纱。前纺很难实现,高效短流程嵌入式纺纱指出只要 5mm 以上纤维就可以纺纱,没有指出前纺工序应该如何改进设备状况。事 实上,对于5mm 以上短纤维采用环锭纺纱在纺纱的前工序是不可能生产出 适合高效短流程嵌入式纺纱用粗纱的。目前的环锭纺纺纱对于并条机粗纱 机来说,纤维平均长度只可以实现不低于16mm 纤维的纺纱,而且 5%纤维 的长度最好在25mm 以上。
精选PPT
4
赛络纺
三、赛络纺存在的问题
1、并合前纱条过细,易产生意外牵伸; 2、成纱细节增加,纱线越细增加越明显; 3、细纱断头增多,生产效率降低。
精选PPT
5
赛络纺
四、赛络纺的应用
1、赛络纺的初始目的是用于毛纺; 2、主要是羊毛毛型涤纶腈纶的纯纺或混纺; 3、现在大多用于平布牛仔布等; 4、应用于衬衣和春夏服装面料。
新型纺纱
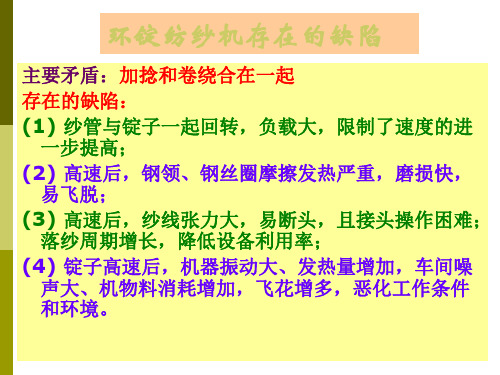
包芯纱 包芯纱是一种以长丝为纱芯,外包短纤维 而纺成的纱线,兼有纱芯长丝和外包短纤维的优 点,使成纱性能超过单一纤维。常用的纱芯长丝 有涤纶丝、锦纶丝、氨纶丝,外包短纤维常用棉、 涤/棉、腈纶、羊毛等。包芯纱目前主要用作缝纫 线、衬衫面料、烂花织物和弹力织物等。
新型纺纱
——转杯纺
1、转杯纺的特点
4、转杯纺纺纱器的主要组成和作用
(1)喂入部分(喂给喇叭、喂给板、喂给罗拉):握持并 积极向前输送纤维条。 (2)分梳部分(分梳辊):将纤维条分梳成单纤维。 (3)气流与纤维输送(输送通道):定向输送纤维到纺纱 杯凝聚槽,并依靠气流使纤维伸直。 (4)纺纱杯(自排风、抽气式):高速回转产生加捻作用 (5)①隔离盘的作用:引导纤维流走向转杯凝聚槽,也引 导气流经扇形缺口通往转杯的排气孔排出。 ②假捻盘作用:增加凝聚槽纱条剥离点至引纱管口纱 段的捻度,减少断头。
涡流纱 涡流纱是用固定不动的涡流纺纱管,代替 高速回转的纺纱杯所纺制的纱。纱上弯曲纤维较 多、强力低、条干均匀度较差,但染色、耐磨性 能较好。此类纱多用于起绒织物,如绒衣、运动 衣等。 尘笼纱 尘笼纱也称摩擦纺纱,是利用一对尘笼 对纤维进行凝聚和加捻纺制的纱。纱线呈分层结 构,纱芯捻度大、手感硬,外层捻度小、手感较 柔软。此类纱主要用于工业纺织品、装饰织物, 也可用在外衣(如工作服、防护服)上。
5、转杯纱的结构特点
⑴转杯纱的结构
由纱芯和外包纤维组成; 内层纱芯比较紧密,外层包缠纤维结构松散。 圆锥形和圆柱形螺旋线纤维比环锭纱少,而弯钩、 对折、打圈、缠绕纤维比环锭纱多得多。
⑵转杯纺纱线特点
①纱线强力比环锭纱低10%~20%,但成纱强 度差异小。 ②成纱条干比环锭纱均匀。 ③纱疵少,只有环锭纱得1/3~1/4。 ④纱线的弹性好,伸长大,耐磨性较好。 ⑤纱线的捻度比环锭纱多15%~30%。 ⑥纱线的蓬松度比环锭纱高10%~15% ⑦纱线的染色性比环锭纱好。
新型纺纱技术的现状与发展方向

新型纺纱技术的现状与发展方向随着科技的不断发展,新型纺纱技术也在不断更新。
新型纺纱技术的发展方向是实现高效、节能、环保、多样化、自动化的生产方式。
以下是新型纺纱技术的现状与发展方向的介绍。
一、新型纺纱技术的现状1. 气流纺纱气流纺纱是一种将纤维松散化并转化为纱线的技术。
它利用空气流动将纤维抛向旋转的锥形容器,形成纱线。
这种技术具有生产效率高、能耗低、纺纱质量好等优点。
2. 喷气纺纱喷气纺纱是一种将纤维通过高速气流推进进入喷口并注入聚合物液中,形成纱线的技术。
这种技术具有生产效率高、生产成本低、纺纱质量好等优点。
3. 液压纺纱液压纺纱是一种将纤维通过高速气流推进进入喷口并注入聚合物液中,形成纱线的技术。
这种技术具有生产效率高、生产成本低、纺纱质量好等优点。
4. 电纺纱电纺纱是一种利用电场将纤维拉伸成纤维轻网,然后再将这些纤维轻网交织在一起,形成纱线的技术。
这种技术具有生产效率高、生产成本低、环保等优点。
二、新型纺纱技术的发展方向1. 实现高效生产新型纺纱技术的发展方向是实现高效生产。
这需要通过改进设备和工艺,提高生产效率,降低生产成本。
2. 实现节能环保新型纺纱技术的另一个发展方向是实现节能环保。
这需要通过改进设备和工艺,减少能源消耗和废弃物的排放,降低对环境的影响。
3. 实现多样化生产新型纺纱技术的第三个发展方向是实现多样化生产。
这需要通过改进设备和工艺,实现不同种类纤维的纺纱,并提高产品的质量和品种。
4. 实现自动化生产新型纺纱技术的最后一个发展方向是实现自动化生产。
这需要通过改进设备和工艺,实现纺纱过程的自动化控制,提高生产效率和产品质量。
新型纺纱技术的发展方向是实现高效、节能、环保、多样化、自动化的生产方式。
这需要通过改进设备和工艺,在不断创新和发展中推动纺纱技术的进步。
新型纺纱课件

(3)分梳辊转速
分梳辊转速高,分梳作用强,杂质易排除,纤维转移顺利,成纱 条干好(粗细节、结杂少、不匀率小),但强力下降。
分梳辊圆周速度<输棉管道入口速度<输棉通道出口速度<纺杯 圆周速度
喂给分梳部分的排杂机构
作用:有利于减少纺杯内凝聚的积尘,增加剥离点的动态强力,
减少断头,延长纺杯的清扫周期,有利于减轻工人的劳动强度。
凝聚槽中会聚积尘杂,影响成纱的均匀率和断头率。 依靠气流输送并重新凝聚排列,纤维的伸直度较差。 最低适纺特数仍高于环锭纱。
三、转杯纺纱的纤维原料及前纺工艺
纤维原料
喂入条要求
(1)含杂率低 (2)纤维的分离度与伸直平行度高
纱类 生条含杂率%
优质纱 0.07~0.08
正牌纱 <0.15
专纺纱 <0.20
种类:
固定式排杂装置 调节式排杂装置
区别:调节式排杂机构的排杂与补气分开,在补气通道处设计阀门
来调节补气量的大小,以控制落棉和落棉含杂率。
固定式排杂装置
调节式排杂装置
纤维的输送
保证纤维在运动过程中其定向度和伸直度不 恶化,输送气流应呈加速运动,使纤维的输 送过程也是一个纤维伸直、牵伸的过程。
二、转杯纺纱概述
(一)转杯纺纱的发展
1937年,丹麦人Berthelson(伯塞耳森)提出专利; 1965年,捷克VUB棉纺织研究所研制成功第一台KS200型转杯纺纱机(60
头),在捷克Brno(布尔诺)国际工程技术博览会上展出,四罗拉牵伸, 条子喂入; VUB研究所与Elitex合作,生产BD200型,分梳辊开松,条筒喂入; 1967年,日本Toyoda购买捷克专利,仿造39台试用 1969年,日本Toyoda生产BS型,研制HS系列; 意大利引进捷克BD200技术,生产BD200NS型; 1965年,英国Platt、瑞士Rieter、德国Ingolstadt三家公司联合,研制 出抽气式;并与1971年,在法国巴黎ITMA上展出; 法国SACM,德国Suessen、Zinzer、Schlafhorst,比利时Woogay,美国 Baber-Colman
现代纺纱技术:第四章 新型纺纱及其发展
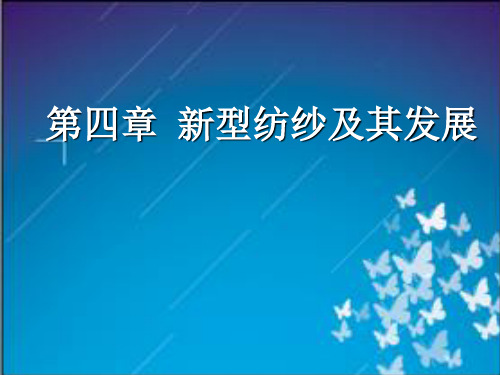
导纱钩
钢丝圈
纱管 钢领
加捻卷绕一体化--速度与卷装的矛盾
细纱加捻卷绕的气圈张力和钢丝圈受力分析中,得到如下的基本 方程式 ,其中: ns-锭子速度 H-卷装高度 D-钢领直径 (卷装的直径) C-常数
导纱钩
钢丝圈
纱管 钢领
三、新型纺纱的发展历程
早在1907年,森莫•威廉就曾提出过把加捻作用和卷绕作用 分开的设想。1937年,百塞尔森提出了转杯纺的雏型。
直到1965年波尔诺(Brno)展出了由捷克研制成功的KS200型转杯纺样机,才在实用上首次获得突破性的进展。
1967年在瑞士巴塞尔第五界国际纺织机械展览会展出了较完 善的BD-200型转杯纺纱机。
转杯纺的成功指出了新型纺纱技术的发展方向。
1971年,在巴黎展出了由澳大利亚研制的MKI型自捻纺纱机。 1975年,在米兰展出了由波兰研制的PF-1型涡流纺纱机,同时展
当代出现的转杯纺、摩擦纺、涡流纺、静电纺、管道纺、喷 气纺、平行纺、自捻纺等新型纺纱技术出现,纺纱速度是环 锭纺的几倍到几十倍。
但由于环锭纺纱机可以纺特细特纱以及成纱质量高,迄今还 没有任何一种新的纺纱机能够完全替代环锭纺纱机。
英国工业革命后的棉纺车间 现代纺纱车间
二、环锭纺纱的局限性
纺
纱
(一)钢丝圈速度和纺纱张力
出了由奥地利研制的DREF型摩镲纺纱机和荷兰研制的Twilo无捻 纺纱机。 1981年在大阪展出了由日本研制的MJS型喷气纺纱机。 所列各种纺纱方法,都在机构上克服了高速生产和大卷装之间的 固有矛盾,单位产量可比环锭纺提高2-10倍,卷装容量可比环 锭纺增加数十倍。
四、新型纺纱的分类 (一)按成纱原理分: 1.自由端纺纱 自由端纺纱是指由喂入点到加捻点之间的须条是断开的
《花式纱线及新型纺纱》平时作业1
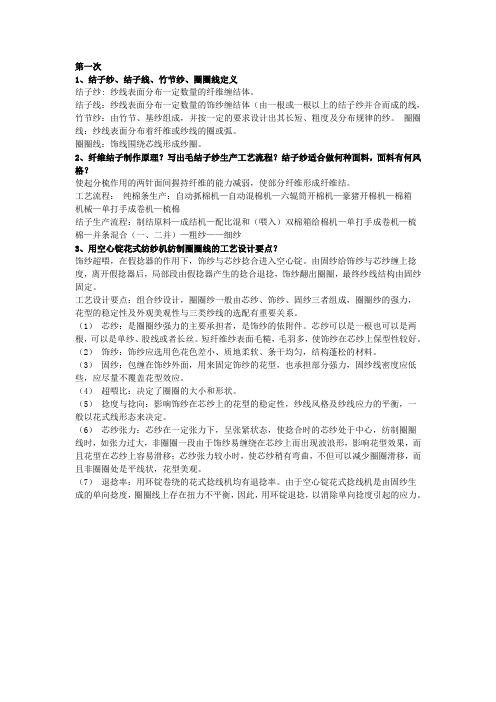
第一次1、结子纱、结子线、竹节纱、圈圈线定义结子纱: 纱线表面分布一定数量的纤维缠结体。
结子线:纱线表面分布一定数量的饰纱缠结体(由一根或一根以上的结子纱并合而成的线,竹节纱:由竹节、基纱组成,并按一定的要求设计出其长短、粗度及分布规律的纱。
圈圈线:纱线表面分布着纤维或纱线的圈或弧。
圈圈线:饰线围绕芯线形成纱圈。
2、纤维结子制作原理?写出毛结子纱生产工艺流程?结子纱适合做何种面料,面料有何风格?使起分梳作用的两针面间握持纤维的能力减弱,使部分纤维形成纤维结。
工艺流程:纯棉条生产:自动抓棉机—自动混棉机—六辊筒开棉机—豪猪开棉机—棉箱机械—单打手成卷机—梳棉结子生产流程:制结原料—成结机—配比混和(喂入)双棉箱给棉机—单打手成卷机—梳棉—并条混合(一、二并)—粗纱——细纱3、用空心锭花式纺纱机纺制圈圈线的工艺设计要点?饰纱超喂,在假捻器的作用下,饰纱与芯纱捻合进入空心锭。
由固纱给饰纱与芯纱缠上捻度,离开假捻器后,局部段由假捻器产生的捻合退捻,饰纱翻出圈圈,最终纱线结构由固纱固定。
工艺设计要点:组合纱设计,圈圈纱一般由芯纱、饰纱、固纱三者组成,圈圈纱的强力,花型的稳定性及外观美观性与三类纱线的选配有重要关系。
(1)芯纱:是圈圈纱强力的主要承担者,是饰纱的依附件。
芯纱可以是一根也可以是两根,可以是单纱、股线或者长丝。
短纤维纱表面毛糙,毛羽多,使饰纱在芯纱上保型性较好。
(2)饰纱:饰纱应选用色花色差小、质地柔软、条干均匀,结构蓬松的材料。
(3)固纱:包缠在饰纱外面,用来固定饰纱的花型,也承担部分强力,固纱线密度应低些,应尽量不覆盖花型效应。
(4)超喂比:决定了圈圈的大小和形状。
(5)捻度与捻向:影响饰纱在芯纱上的花型的稳定性,纱线风格及纱线应力的平衡,一般以花式线形态来决定。
(6)芯纱张力:芯纱在一定张力下,呈张紧状态,使捻合时的芯纱处于中心,纺制圈圈线时,如张力过大,非圈圈一段由于饰纱易缠绕在芯纱上而出现波浪形,影响花型效果,而且花型在芯纱上容易滑移;芯纱张力较小时,使芯纱稍有弯曲,不但可以减少圈圈滑移,而且非圈圈处是平线状,花型美观。
新型纺纱习题答案

《新型纺纱》习题一、概述1. 新型纺纱是如何分类的代表性的纺纱方法有那几种答:1按加捻方法分,可以分为自由端纺纱(加捻)和非自由端纺纱(加捻)两种。
自由端纺纱按纤维凝聚加捻方法不同可分为转杯纺纱、静电纺纱、涡流纺纱、磁性纺纱等。
非自由端纺纱按加捻原理可分为自捻纺纱、无捻纺纱、喷气纺纱、轴向纺纱等。
2按成纱机理分,可分为加捻纺纱、包缠纺纱、无捻纺纱三大类。
包缠纺纱主要有喷气纺纱和平行纺纱等。
无捻纺纱有粘合纺纱、熔融纺纱和缠结纺纱等。
2. 自由端纺纱的原理是什么答:自由端纺纱的基本持点在于喂入端一定要形成自由端。
自由端的形成,通常采用“断裂”纤维结集体的方法,使喂入端与加捻器之间的纤维结集体断裂而不产生反向捻回,并在加捻器与卷绕部件区间获得真捻。
经断裂后的纤维又必须重新聚集成连续的须条,使纺纱得以连续进行。
最后将加捻后的纱条绕成筒子。
3. 各种新型纺纱的生产流程(重点转杯纺,喷气纺)转杯纺:高效开清棉联合机组(附高效除杂装置)——高产梳棉机——两道并条机——转杯纺纱机高效开清棉联合机组(无附加装置)——双联梳棉机——两道并条机——转杯纺纱机喷气纺:采用超大牵伸装置,可省略粗纱和络筒工序。
前纺工艺流程与环锭纺工艺相当,混纺时工厂一般采用三道混并后喂入喷气纺。
如采用双根粗纱喂入,则必须经过粗纱工序。
二、转杯纺1. 与环锭纺纱相比转杯纺纱的特点(生产原理、产品质量、品种等方面)。
答:生产原理:转杯纺属于自由端纺纱,条子从条筒中引出通过喂给机构积极向前输送,经表面包有金属锯条的分梳辊分梳成单纤维。
纺纱杯内由于高速回转产生的离心力或由于风机的抽吸,形成一定负压,迫使被分梳辊分解后的单纤维被吸入纺纱杯,纺纱杯壁滑入凝聚槽形成凝聚须条。
引纱通过引纱管时也被吸入凝聚槽内.引纱纱尾须条连接,并被纺纱杯摩擦握持而加捻成纱。
然后引纱罗拉将纱从纺纱杯中经假捻盘和引纱管引出,依靠卷绕罗拉(槽筒)回转,卷绕成筒子。
由于转杯纺取消了锭子、筒管、钢领、钢丝圈等加捻卷绕元件,并将加捻、卷绕作用分开生产原理简单成熟,速度高,卷壮大,工艺流程短。
- 1、下载文档前请自行甄别文档内容的完整性,平台不提供额外的编辑、内容补充、找答案等附加服务。
- 2、"仅部分预览"的文档,不可在线预览部分如存在完整性等问题,可反馈申请退款(可完整预览的文档不适用该条件!)。
- 3、如文档侵犯您的权益,请联系客服反馈,我们会尽快为您处理(人工客服工作时间:9:00-18:30)。
• 结论: 结论: 环锭纺之所以不能进一步高速化和大卷装,其 核心问题是加捻和卷绕机构本身存在着不可克 服的固有矛盾,即加捻器和卷绕机构(锭子及 服的固有矛盾 插在锭子上的筒管)构成了一个整体系统,只 有在加捻器和卷绕件同时回转时,纱条才可获 得捻回和实现卷绕,即纱条的加捻作用和卷绕 作用必须同时进行才能连续纺纱。也就是说, 如要加大卷装就应降低锭速,如要提高锭速就 应减小卷装,无法兼顾。
• 在纺杯的中心有一个喇叭型的假捻盘 假捻盘,当接头的种子纱的头 假捻盘 端从假捻盘中心的孔中伸出时,在纺杯内旋转流场的作用下 也开始旋转,此时的旋转并没有使纱线获得捻度,因为种子 纱的头端没有被握持,纱线只是绕假捻盘的中心公转,而没 产生绕纱线自身轴线的旋转,随着接头种子纱继续喂入,种 子纱头和纺杯凝聚槽中的已喂入的纤维环相接触,在离心力 的作用下,种子纱头紧贴在纺杯凝聚槽的纤维环上,此时种 子纱头和纺杯同速旋转。当种子纱每绕假捻盘转一圈,就给 纱线加一个捻回,由于纺杯高速旋转,在极短的时间内,就 给纺杯内从假捻盘到凝聚槽之间的一段纱(称为纱臂段 纱臂段)加 纱臂段 上许多捻回,这些捻度传递到种子纱头上使其产生绕自身轴 线的旋转,使种子纱头和凝聚槽中的纤维环捻合在一起。此 时,将纱管放下和引纱罗拉相接触,使纱线迅速被拉出,种 子纱在纺杯凝聚槽中的纤维环上打开一个缺口,和纤维环的 一端粘合在一起形成了接头。以后,纤维不停的喂入,纱线 不停地引出,形成连续纺纱过程。引出的纱线被绕在纱管上, 直接形成筒子纱。
• 按成纱方法分 ⑴加捻成纱:靠给纤维须条施加一定捻度而成纱。 例如:转杯纺,涡流纺等。 ⑵包缠成纱:靠纤维互相包缠而成纱。例如:喷气 纱的结构就是纤维互相包缠而形成的,它是以短 纤维包短纤维的形式成纱。平行纺是用长丝包在 短纤维须条上而成纱的,摩擦纺包芯纱是以长丝 为纱芯,外包短纤维而成纱的,它是短纤维包长 丝(或纱)的形式成纱。 ⑶自捻成纱:靠两根单纱的假捻捻度而自捻成纱。 如自捻纺纱。 ⑷粘合成纱:靠一定的粘合剂使纤维粘合而成纱。 例如:粘合纺纱Twilo等。
• 喂给罗拉 喂给罗拉表面刻有细浅槽,喂给板 喂给板表面一般经 喂给板 电镀处理,十分光滑。在喂给板下有一根压缩 弹簧,使喂给板和喂给罗拉之间保持一定压力。 工艺要求:压力一般为25~30N,当压力过小时, 喂给罗拉容易打滑,纤维条不能正常喂入;当 压力过大时,纤维在喂给板上摩擦力太大不能 正常滑动,纤维容易产生上下分层而拥簇在喂 给喇叭口而引起断头。 • 喂给板分梳面长度: 喂给板分梳面长度: 定义: 定义:自喂给罗拉与喂给板握持点至分梳辊中心 水平线与喂给板交点间的长度。 水平线与喂给板交点间的长度。 作用:直接影响分梳质量,分梳面长度愈短,分 梳作用愈强,但纤维易受损伤;反之,分梳作 用愈弱,分梳效果差;
纺纱杯有两种基本形式,一种为自排风式纺杯 自排风式纺杯, 自排风式纺杯 另一种是抽气式纺杯 抽气式纺杯。 抽气式纺杯 自排风式纺杯工作原理: ⑴自排风式纺杯工作原理:在自排风式纺杯的底 部有八个左右的小孔。当纺杯高速旋转时,使 杯内气流通过杯底小孔排向杯外,使杯内产生 一定负压。由于自排风式纺杯盖和纺杯之间的 密封作用,杯内的补气只能通过输棉管道和引 纱管补入,因此,在输棉管道中产生一定的吸 力,使纤维和气流被吸入纺杯中。而在引纱管 中产生的负压,使接头时的种子纱能顺利输送 到纺纱杯中。另外,气流的吸力也增大了纺纱 的张力。
新型纺纱的发展、 §1.2 新型纺纱的发展、特点及分类
一、新型纺纱的发展: 新型纺纱的发展 新型纺纱的特点: 二、新型纺纱的特点: • 高速高产 环锭纺纱锭子转速一般在15000 r / min 左右, 纺粗中特纱时引纱速度一般在30 m / min 左右。 转杯纺引纱速度最高可达200m / min 。摩擦纺 纱的引纱速度可达200~300 m / min ,纺中细特 纱时可达300~400 m / min 。喷气纺纱的引纱速 度可达150~200 m / min 。其他新型纺纱的纺纱 速度也比环锭纺高的多。
• 抽气式纺纱杯工作原理:在抽气式纺杯的底部 没有孔,杯内的负压靠一台附设的风机抽吸而 形成。杯口和杯盖之间留有一定的间隙,风机 将杯内的气流从杯口与杯盖的间隙处抽走,在 杯内形成一定的负压。 • 转杯纺纱工作过程: 纤维被吸入纺杯后,由于输棉管的出口对着纺 杯入口处的内表面上,所以纤维先落在纺杯入 口处的内表面上。由于纺杯入口处直径小,凝 聚槽处的直径大,当纺杯高速旋转时,纤维在 离心力的作用下从纺杯入口处滑入凝聚槽中。 纤维在凝聚槽中形成一个完整的纤维环,当接 头时,种子纱 种子纱从引纱罗拉上退出一定长度的纱 种子纱 线,喂入引纱管中,由于纺杯内的负压作用, 接头的种子纱被吸入纺杯中。
常见几种新型纺纱分类表
名称 英文名称 转杯纺纱 Rotor Spinning 涡流纺纱 Airvortex Spinning 静电纺纱 Electro-static Spinning 摩擦纺纱 Frictional Spinning(无芯纱) 摩擦纺纱 Frictional Spinning(有芯纱) 喷气纺纱 Air-jet Spinning 自捻纺纱 Self-twist Spinning 聚集纺纱 Bobtex Spinning 平行纺纱 Parallel Spinning 加捻原理 自由端 自由端 自由端 自由端 非自由端 非自由端 非自由端 非自由端 非自由端 成纱捻度 真捻 真捻 真捻 真捻 假捻 缠捻 假捻 无捻 包捻 成纱方法 加捻 加捻 加捻 加捻 包缠 包缠 自捻 粘合 包缠
• 大卷装 环锭纺纱的卷装受钢领直径的影响,卷装都比较 小,每个纱管只能卷绕50~100g 纱线。新型纺纱 将加捻作用和卷绕作用分开进行,在卷装容量上 有了根本性的突破。一般直接绕成纱筒,其容量 大小根据需要决定,可绕成任意大小,一般为3~ 4kg。卷绕的增大不仅使落纱的次数减少,机器的 生产率提高,而且省去了络筒工序,纱线的质量 也明显提高,接头数大为降低。 • 流程短 大多数新型纺纱采用棉条喂入,纺成的纱直接绕 成筒子纱,可以省去粗纱和络筒两道工序,简化 了工艺流程,降低了生产成本。喷气并捻联合机 连并纱和捻线也连为一体,使工艺流程更为缩短。
第一章
绪论
§1.1传统纺纱的限制 传统纺纱的限制
一、纺纱技术的发展历史 二、环锭纺纱存在的问题 1、受钢丝圈转速的限制,生产速度不可能有突 破性的提高: ns 在环锭纺纱中,纱线的捻度为: T = v ∴ ns = T × v 当纱线捻度一定时,锭子转速与前罗拉线速度成 正比。
v 钢丝圈转速nt与锭速ns的关系是: n t = n s − πd 1 n t = v T − πd ∴ 即:捻度一定时,钢丝圈转速与前罗拉线速度成 正比。所以,欲提高环锭纺纱机的产量,即增 加前罗拉线速度V,当捻度一定时,钢丝圈的 转速就要加快,而钢丝圈在钢领跑道上摩擦回 转,转速过高,摩擦加剧,会使机件发热损坏。 2、受钢领直径的限制,大幅度地增加卷装容量 也不可能。
• 输棉管道 输棉管道:纤维脱离分梳辊后进入输棉管道中, 输棉管道是一根入口大出口小的渐缩型管道, 内表面要求十分光滑不挂纤维,输棉管道的入 口处沿着分梳辊的切线方向,其出口伸到纺纱 杯内。由于输棉管道的截面为渐缩型,气流在 输棉管道中必然呈加速度运动,这样就可以减 少纤维在输棉管道中产生掉头弯曲的机会,以 提高纤维在纱中的伸直度。 • 纺纱杯 纺纱杯是转杯纺最重要的部件,其基本形状是 由两个中空的截头圆锥体联接而成,在两个圆 锥体的交界处(最大直径处)形成一个凝聚纤 维的凹槽,称为凝聚槽 凝聚槽。纺纱杯转速的高低标 凝聚槽 志着转杯纺纱机的先进性,现在一般转速为 30000~130000r/min。
• 工艺要求:此工艺长度应等于或接近于纤维品 质长度。当纤维主体长度在29~31mm时,喂给 板与分梳辊进口隔距应保持在2.6mm,出口隔距 (即分梳点)最小隔距应为0.15mm,分梳面长 度为27~28mm。当纤维主体长度为27mm或以 下时,喂给板与分梳辊进口隔距应为2.0mm,出 口隔距为0.15mm,分梳面长度为23~25mm。 • 分梳辊 分梳辊是一个圆柱形铁胎,其表面包有金属锯 条或植有梳针,以5000~9000r/min的速度对纤 维进行充分的梳理。经分梳后得纤维基本上呈 单纤维状态,靠分梳辊的离心力和气流作用脱 离分梳辊表面而进入输棉管道中。 工艺要求:分梳辊上的纤维在经过输棉管入口时 必须全部剥离分梳辊,绝不能使纤维再返回到 喂入点,否则纤维缠绕分梳辊不能纺纱。
二、转杯纺纱原理 • 转杯纺纱机主要由喂给分梳机构 凝聚加捻机 喂给分梳机构、凝聚加捻机 喂给分梳机构 卷绕机构等组成。 构和卷绕机构 卷绕机构
• 喂给喇叭 喂给喇叭用塑料制成,其进出口截面设计成渐 缩形。喂给喇叭的作用 作用是使条子在进入喂给罗 作用 拉与喂给板以前,受到必要的整理与压缩,使 条子宽度压缩在一定范围以内,并改变条子截 面的形态,以扁平形截面进入握持区,使条子 截面上的密度趋于一致,横向压力分布比较均 匀。 工艺要求:喂给喇叭出口截面与喂入条子定量 应有一定的关系,截面尺寸过小或条子定量过 重,容易发生阻塞,反之集合效果差。喂给喇 叭口的出口中心位置应稍低于分梳辊中心,以 免发生纤维绕分梳辊现象。
(1)因环锭纺加捻和卷绕同时进行,管纱也以 锭速高速旋转,纱管从空管到满管,锭子负荷 渐大,不利于锭子高速: (2)增大钢领直径,在捻度不变时,增加了钢 丝圈的线速度,加速了钢丝圈的磨损,缩短了 钢丝圈的使用寿命。 (3)增大钢领直径,由于一落纱中大、中、小 纱在卷绕大小直径时,纱线张力的波动,气圈 形态变化太大,而使断头大大增加。一般环锭 纺采用的最大钢领直径为45mm左右。
三、新型纺纱的分类 • 按成纱原理分类 ⑴自由端纺纱(open-end spinning)指由喂入点至加捻 点之间的须条是断开的纺纱方法,纺出的纱是真捻 结构。如转杯纺。 自由端纺纱在喂入点和加捻点的须条并不是绝 对断开,而是不形成连续的纱条,只以纤维流的形 式存在,纤维流中每一根纤维都可以独立地运动。 ⑵非自由端纺纱(Unopened-end spinning)指在喂入点 至加捻点之间的须条是连续的纺纱方法。由于整个 须条是连续的,在须条的两端分别被给棉罗拉和引 纱罗拉所握持,而在中间加捻,形成了假捻形式, 纺出的纱肯定不是真捻结构。例如:喷气纺纱,摩 擦纺包芯纱等。环锭纺虽然也是非自由端纺纱,但 其将加捻作用和卷绕作用合为一体,采用纱管旋转 的形式形成了真捻,即在纱条的一端由前罗拉握持, 而另一端加捻和卷绕。故成纱为真捻。