钢箱梁施工方法及工艺
施工工艺大全钢箱梁制作
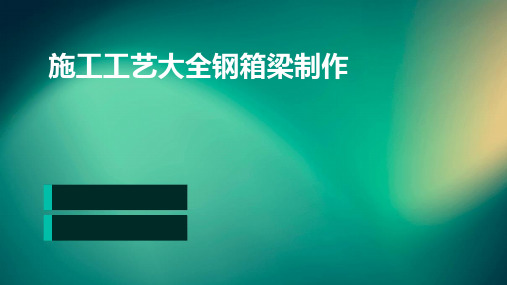
结构强度高
钢箱梁采用高强度钢材,具有 较高的承载能力和抗疲劳性能 。
施工方便
钢箱梁可以采用预制拼装施工 ,缩短了施工周期,降低了工 程成本。
适应性强
钢箱梁可以根据不同的跨度和 荷载要求进行设计,适应各种
桥梁工程的需求。
钢箱梁在施工中的应用
01
02
03
大跨度桥梁
钢箱梁适用于大跨度桥梁 的施工,能够满足跨越峡 谷、河流、高速公路等特 殊需求。
钢材储存与运输
合理规划钢材的储存和运 输,避免在过程中发生变 形或损坏。
钢材切割与加工
钢材切割
边缘处理
采用机械或火焰切割方法,将钢材切 割成所需形状和尺寸。
对钢材边缘进行打磨或倒角处理,以 减少应力集中和便于焊接。
钢材加工
对切割后的钢材进行矫直、平整和钻 孔等加工,以满足后续组装的需要。
钢材组装与焊接
05 钢箱梁制作的注意事项与 安全措施
操作人员资质与培训
01
操作人员需具备相应的专业技能 和资质,熟悉钢箱梁制作的相关 知识和技能。
02
定期对操作人员进行安全培训和 技能提升,确保其具备应对突发 情况和安全事故的能力。
作业环境与安全防护
确保作业现场整洁、有序,避免杂乱 无章和潜在的安全隐患。
提供完备的安全防护设施,如安全带 、防护网、护目镜等,确保操作人员 的安全。
总结词
材料质量控制是钢箱梁制作过程中的重要环节,直接关系到 成品的质量和安全性能。
详细描述
在材料质量控制方面,需要严格筛选供应商,确保所采购的 钢材等原材料质量合格。同时,对进场的原材料进行质量检 查,包括外观、尺寸、材质等,确保符合设计要求和相关标 准。
钢箱梁专项施工方案与技术措施
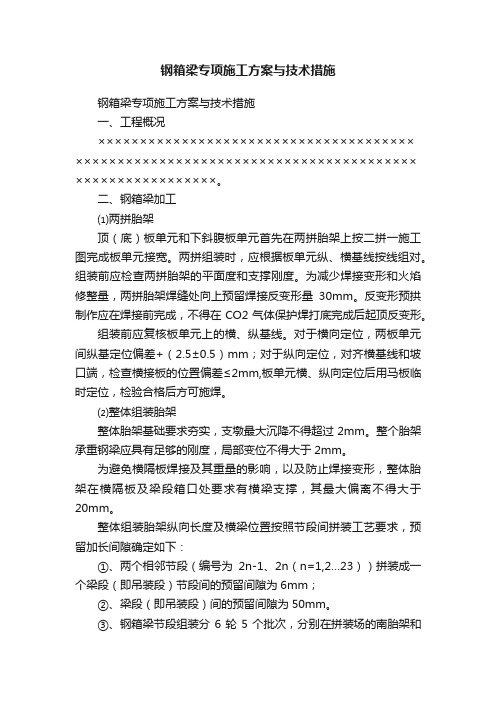
钢箱梁专项施工方案与技术措施钢箱梁专项施工方案与技术措施一、工程概况××××××××××××××××××××××××××××××××××××××××××××××××××××××××××××××××××××××××××××××××××××××××××××××××。
二、钢箱梁加工⑴两拼胎架顶(底)板单元和下斜腹板单元首先在两拼胎架上按二拼一施工图完成板单元接宽。
两拼组装时,应根据板单元纵、横基线按线组对。
组装前应检查两拼胎架的平面度和支撑刚度。
为减少焊接变形和火焰修整量,两拼胎架焊缝处向上预留焊接反变形量30mm。
反变形预拱制作应在焊接前完成,不得在CO2气体保护焊打底完成后起顶反变形。
组装前应复核板单元上的横、纵基线。
对于横向定位,两板单元间纵基定位偏差+(2.5±0.5)mm;对于纵向定位,对齐横基线和坡口端,检查横接板的位置偏差≤2mm,板单元横、纵向定位后用马板临时定位,检验合格后方可施焊。
钢箱梁施工工艺

钢箱梁施工工艺钢箱梁施工工艺1. 引言本旨在提供钢箱梁施工工艺的详细指导,以施工人员顺利进行钢箱梁的安装和施工过程。
钢箱梁是一种常用于桥梁和高速公路建设中的结构元件,在工程建设中起到重要的支撑作用。
本将从最初的准备工作开始,一直到施工结束,对其中的每个环节进行详细描述和解释。
2. 安全准备2.1 工地安全施工前应进行工地安全检查,保证工作区域没有明显的安全隐患。
划定施工范围,设置安全警示标志并进行合理的分流管控措施。
确保所有参与施工的人员都了解相关的安全操作规程和应急预案。
2.2 特殊设备准备钢箱梁施工需要使用特殊设备,如起重机、吊车等。
在施工前,应对这些设备进行全面检查,确保其安装稳固、机能正常,以及对人员进行相应培训,保证操作人员能够熟练使用这些设备。
3. 施工准备3.1 材料准备根据设计要求和钢箱梁的尺寸,准备所需的钢材和配件。
对于钢材的选择,应符合相关的标准要求,并进行质检,以确保其质量合格。
3.2 测量和标记根据设计图纸,对施工现场进行测量和标记,确定钢箱梁的正确位置和尺寸。
在标记过程中,应注意精确度,避免误差。
4. 钢箱梁安装4.1 钢箱梁吊装使用起重机进行钢箱梁的吊装。
在吊装过程中,应注意梁体的平稳和安全,以及梁体与吊装设备的连接牢固。
在梁体吊装到位后,应对其进行检查,确保其位置正确。
4.2 锚固钢箱梁安装后,需要进行锚固固定。
根据设计要求,选择合适的锚固方法,例如使用膨胀螺栓、预埋螺栓等。
确保锚固牢固可靠。
4.3 垫层填充在钢箱梁安装完毕后,进行垫层填充,以确保梁底面与支座接触均匀。
垫层材料可以选用橡胶垫、防水沥青等,根据实际情况进行选择。
5. 钢箱梁施工质量控制5.1 焊接工艺钢箱梁的施工中常涉及到焊接工艺。
在焊接前应对焊材和焊接设备进行检查,确保其质量和安全。
在焊接过程中,要严格按照焊接规范进行操作,确保焊缝的质量。
5.2 铺装层施工在钢箱梁施工完成后,需要进行铺装层的施工。
钢箱梁在工厂内制作工艺及钢箱梁安装方案

安全带使用
高处作业时,必须佩戴安 全带,确保人员不会因坠 落而受伤。
高空作业安全措施
防坠落措施
在高空作业时,应采取防坠落措施,如使用安全 网、安全带等。
防滑措施
在有滑动可能的地方,应采取防滑措施,如穿防 滑鞋、使用防滑垫等。
作业平台安全
作业平台应稳固,防止倾覆,并设置防护栏杆和 踢脚板。
焊接作业安全措施
对安装过程中的各项精度指标进行严格控制,确保钢箱梁安装 精度符合设计要求。
在安装完成后对钢箱梁进行全面的质量检测,包括外观检查、 尺寸精度检测和无损检测等,确保钢箱梁安装质量符合规范要
求。
THANKS
感谢观看
。
钢箱梁安装方案的实施流程
施工准备
现场勘查、材料准备、设备调试 等。
基础制作
浇筑混凝土基础,确保基础稳固 。
钢箱梁拼装
在工厂内完成钢箱梁的拼装,确 保结构稳定。
验收及检测
完成安装后进行验收和检测,确 保施工质量。
焊接及固定
对钢箱梁进行焊接,确保连接牢 固,满足设计要求。
运输及吊装
将钢箱梁运输至安装现场,通过 大型吊装设备进行吊装就位。
VS
钢箱梁吊装
在施工现场,需要使用专业的吊装设备将 钢箱梁吊装到安装位置,吊装过程中要确 保吊装设备的稳定性和安全性,避免在吊 装过程中对钢箱梁造成损伤。
钢箱梁的定位与校正
钢箱梁定位
在吊装完成后,需要对钢箱梁进行定位,确 保钢箱梁的位置和方向符合设计要求。
钢箱梁校正
在定位完成后,需要对钢箱梁进行校正,确 保钢箱梁的平直度和高度符合设计要求。
04
CATALOGUE
钢箱梁安装前的准备工作
技术准备
钢箱梁桥梁施工方案
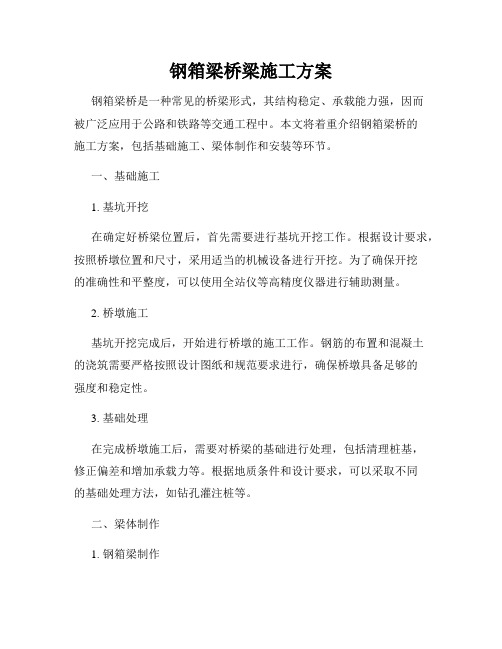
钢箱梁桥梁施工方案钢箱梁桥是一种常见的桥梁形式,其结构稳定、承载能力强,因而被广泛应用于公路和铁路等交通工程中。
本文将着重介绍钢箱梁桥的施工方案,包括基础施工、梁体制作和安装等环节。
一、基础施工1. 基坑开挖在确定好桥梁位置后,首先需要进行基坑开挖工作。
根据设计要求,按照桥墩位置和尺寸,采用适当的机械设备进行开挖。
为了确保开挖的准确性和平整度,可以使用全站仪等高精度仪器进行辅助测量。
2. 桥墩施工基坑开挖完成后,开始进行桥墩的施工工作。
钢筋的布置和混凝土的浇筑需要严格按照设计图纸和规范要求进行,确保桥墩具备足够的强度和稳定性。
3. 基础处理在完成桥墩施工后,需要对桥梁的基础进行处理,包括清理桩基,修正偏差和增加承载力等。
根据地质条件和设计要求,可以采取不同的基础处理方法,如钻孔灌注桩等。
二、梁体制作1. 钢箱梁制作钢箱梁制作前需要准备好所有材料和工具,包括钢板、焊接设备和起重机械等。
根据设计图纸和规范要求,将钢板进行切割、焊接和预处理,形成桥梁所需的钢箱梁构件。
2. 防腐处理为了增加钢箱梁的使用寿命,需要对其进行防腐处理。
防腐处理可以采用涂装或喷涂方式,选择适当的防腐涂料,并按照施工工艺要求进行涂装,确保涂层的均匀和附着力。
3. 预应力加固钢箱梁制作完成后,还需要进行预应力加固工作。
通过应力传递器和拉伸设备等,将预应力钢束或钢绞线固定在梁体内,施加适当的预应力,以提高桥梁的承载能力和抗震性能。
三、梁体安装1. 梁场准备在进行梁体安装前,需要在适当位置设置梁场,并对梁场进行平整和加固,确保能够顺利进行梁体的吊装和安装。
2. 吊装作业梁体的吊装是施工过程中最关键的环节之一。
使用适当的起重机械,按照梁体的吊装计划,将钢箱梁准确地吊装到桥墩之间的空间中。
在吊装过程中,需要严格控制吊点的位置和吊装速度,确保施工安全。
3. 梁体连接在完成梁体吊装后,需要对相邻的钢箱梁进行连接。
根据设计要求,采用焊接或螺栓连接的方式,将钢箱梁牢固地连接在一起,形成整体的桥梁结构。
钢箱梁运架快速施工工法(2)

钢箱梁运架快速施工工法钢箱梁运架快速施工工法一、前言钢箱梁作为一种常见的桥梁构件,在现代交通工程中得到了广泛应用。
为了提高施工效率和质量,钢箱梁运架快速施工工法逐渐成为桥梁施工中的主要选择。
本文将详细介绍钢箱梁运架快速施工工法的特点、施工过程和质量控制措施,通过工程实例展示其实际应用效果。
二、工法特点钢箱梁运架快速施工工法具有以下几个特点:1. 施工速度快:采用装配化结构设计,能够提前制作好钢箱梁并进行预制,施工时只需要进行运输和安装即可,大大缩短了施工周期。
2. 施工质量高:钢箱梁制作精度高,结构稳定,能够保证桥梁的承载能力和使用寿命,提高了工程的质量。
3. 施工操作简单:钢箱梁运架快速施工工法采用模块化设计,施工过程简化了工序,降低了施工难度,减少了操作工人的劳动强度。
4. 适应性强:钢箱梁运架快速施工工法适用于各种类型的桥梁,能够满足不同的设计要求和工程需求。
三、适应范围钢箱梁运架快速施工工法适用于中小跨径的桥梁,如市政道路桥梁、高速公路桥梁和铁路桥梁等,尤其适用于交通量大、施工时间紧迫的工程项目。
四、工艺原理钢箱梁运架快速施工工法通过于实际工程之间的联系、采取的技术措施进行具体的分析和解释,其理论依据和实际应用如下:1. 钢箱梁的预制:根据桥梁设计要求,预制好具有一定长度的钢箱梁,并进行质量检测,保证结构强度和几何尺寸的准确性。
2. 运输与安装:使用专业的起重设备将钢箱梁运输到施工现场,然后进行合理的安装方案,根据设计要求进行严密连接和固定。
3. 焊接与防腐蚀处理:对连接处进行焊接,保证结构的牢固性和稳定性,同时对整个钢箱梁进行防腐蚀处理,延长使用寿命。
五、施工工艺钢箱梁运架快速施工工法主要包括以下几个施工阶段:1. 钢箱梁制作:根据设计要求,预制好钢箱梁并进行质量检测。
2. 运输与安装:使用专业的起重设备将钢箱梁运输到施工现场,并进行严密连接和固定。
3. 焊接与防腐蚀处理:对连接处进行焊接,对整个钢箱梁进行防腐蚀处理,确保结构稳定和使用寿命。
钢箱梁制作安装工程施工方案
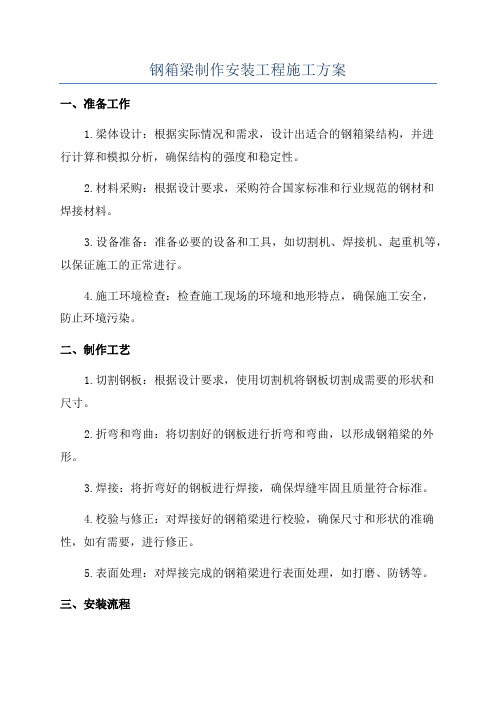
钢箱梁制作安装工程施工方案一、准备工作1.梁体设计:根据实际情况和需求,设计出适合的钢箱梁结构,并进行计算和模拟分析,确保结构的强度和稳定性。
2.材料采购:根据设计要求,采购符合国家标准和行业规范的钢材和焊接材料。
3.设备准备:准备必要的设备和工具,如切割机、焊接机、起重机等,以保证施工的正常进行。
4.施工环境检查:检查施工现场的环境和地形特点,确保施工安全,防止环境污染。
二、制作工艺1.切割钢板:根据设计要求,使用切割机将钢板切割成需要的形状和尺寸。
2.折弯和弯曲:将切割好的钢板进行折弯和弯曲,以形成钢箱梁的外形。
3.焊接:将折弯好的钢板进行焊接,确保焊缝牢固且质量符合标准。
4.校验与修正:对焊接好的钢箱梁进行校验,确保尺寸和形状的准确性,如有需要,进行修正。
5.表面处理:对焊接完成的钢箱梁进行表面处理,如打磨、防锈等。
三、安装流程1.根据设计要求,确定钢箱梁的安装位置和方向,并进行放线和标记。
2.使用起重机或其他适当设备,将钢箱梁吊装到准确的位置,确保对接部位的平齐和垂直度。
3.使用临时支撑或其他固定设备,将钢箱梁暂时固定,以防止在后续施工过程中发生位移。
4.进行钢箱梁的对接焊接,确保焊缝的质量和均匀性,同时注意安全措施。
5.完成钢箱梁的主体安装后,进行精细调整和修正,以保证整体的水平度和精度。
6.在钢箱梁的安装位置进行安全检查,确保结构的稳定性和安全性。
7.根据设计要求,进行必要的油漆和防腐处理,以保护钢箱梁的表面和内部结构。
四、安全措施1.施工现场应设立安全警示标志,加强安全教育和培训。
2.确保施工人员配戴必要的个人防护用品,如安全帽、防护眼镜和手套等。
3.吊装和安装过程中,要严格按照安全操作规程进行,不得超载、超高或者超工作范围操作。
4.遵守焊接安全规范,使用符合质量标准的焊接材料和设备。
5.钢箱梁制作和安装完成后,进行整体的安全检查和评估。
以上是钢箱梁制作安装的工程施工方案,包括准备工作、制作工艺和安装流程等。
钢箱梁吊装施工方法及工艺
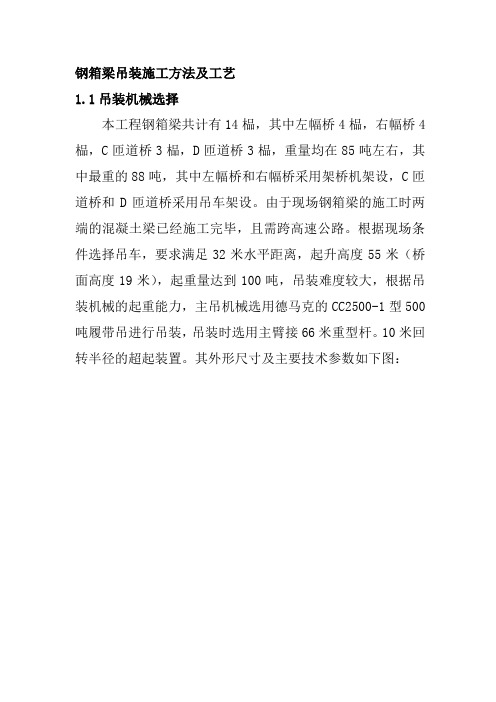
钢箱梁吊装施工方法及工艺1.1吊装机械选择本工程钢箱梁共计有14榀,其中左幅桥4榀,右幅桥4榀,C匝道桥3榀,D匝道桥3榀,重量均在85吨左右,其中最重的88吨,其中左幅桥和右幅桥采用架桥机架设,C匝道桥和D匝道桥采用吊车架设。
由于现场钢箱梁的施工时两端的混凝土梁已经施工完毕,且需跨高速公路。
根据现场条件选择吊车,要求满足32米水平距离,起升高度55米(桥面高度19米),起重量达到100吨,吊装难度较大,根据吊装机械的起重能力,主吊机械选用德马克的CC2500-1型500吨履带吊进行吊装,吊装时选用主臂接66米重型杆。
10米回转半径的超起装置。
其外形尺寸及主要技术参数如下图:1.2吊耳布置图及吊耳验算每片钢梁布置四个吊耳,吊耳纵向位置见下图所示,吊耳在横向方向与腹板对齐。
D匝道钢梁吊耳设置图(蓝色圆点为吊耳位置)C匝道钢梁吊耳设置图四根吊杆同时工作吊杆内力 kN(由于D匝道重量和长度都比C匝道小,故验算C匝道)根据《公路钢筋混凝土及预应力混凝土桥涵设计规范》(JTG D62-2004) 9.1.2,需验算三个吊环同时发挥作用的工况。
三根吊杆同时工作吊杆内力 kN工程所采用的吊耳材质为Q345,板厚为30mm,临时板式吊耳与钢箱梁顶板连接采用双坡口全溶透焊接,坡口角度为60°,板孔孔径为50mm,耳板外缘有效半径为100mm,吊耳长度L为250mm,板式吊耳大样图如下图所示:根据《钢结构设计规范》对吊耳进行计算:耳板强度计算如图所示,拉应力的最不利位置在A -A 断面,其强度计算公式为:589000128.820076.2230n P MPa MPa A σ===<⨯⨯满足要求。
焊缝强度计算589000103.3200(250225)25n P MPa MPa A σ===<-⨯⨯式中:σ――拉应力P ――荷载n A ――耳板与钢梁顶板焊缝接触面积满足要求。
1.3钢丝绳及卸扣的选择吊车吊装钢箱梁示意图如下:由于钢箱梁两侧均有相同配置的钢丝绳,最重钢箱梁99t,单个吊点受力为25t,钢丝绳角度为60度,实际钢丝绳拉力为25/SIN60=21.8t,可取实际单绳拉力约为30t,根据钢丝绳使用拉力公式P<Q/K,其中Q为钢丝绳破断力,K为钢丝绳使用安全系数,取为6,可求得钢丝绳破断力Q>P*K=300*6=1800kN,查五金手册可知取φ=70㎜的钢丝绳满足要求。
钢箱梁施工工艺

(一)、设计概述U12联钢结构桥设计里程为K6+674.1m-K6+734.1m,结构宽度44.5m,双向横坡,坡度为±2.0%,全长60m。
跨径组合为单跨60m。
防撞护栏采用钢护栏,外型与立交范围内其他桥梁一致;桥面铺装为100mm 沥青混凝土+2mm防水层+80mm钢筋混凝土调平层。
箱体顶板宽44.5m,梁高 3.3m,钢箱梁顶板厚14mm;底板在支点附近厚12mm,跨中1/2跨径处厚16mm;纵向腹板间距2.6m-3.3m,纵向腹板厚16mm,横隔板间距3.3m-4m,横隔板厚12mm。
钢桥面采用剪力钉与混凝土铺装层连接。
钢箱梁分节制造出厂,在现场焊接成整体后吊装到位成型。
为保证成桥后主梁线型,工程制作时应进行试拼。
本桥设置成桥预拱度,跨中预拱度值为88mm,以二次抛弧线向两侧支点过渡。
施工预拱度应根据具体施工方法确定。
(二)、材料1、本桥钢结构采用Q345qD钢。
2、中厚板(板厚≥16mm)按正火状态交货,其余薄板(板厚≤16mm)可按控轧状态交货,并提供生产钢板性能基础实验的证明材料。
3、钢板熔炼化学成分符合《桥梁用结构钢》(GB/T 714-2008)相应规定。
4、钢板机械性能符合《桥梁用结构钢》(GB/T 714-2008)相应规定。
5、本桥供货钢板必须有生产厂的出厂质量证明书,并应进行检验和验收,做好记录。
必要时可要求制造厂对钢板进行无损探伤复检。
6、钢板公差带按《热轧钢板和钢带的尺寸、外型、重量及允许偏差》GB/Tt 709-2006 B类执行。
7、焊接材料如焊丝、焊剂等选用与被焊接钢板材料相匹配。
8、使用的焊丝、焊剂,焊接上述钢板后,其熔敷金属屈服强度、极限强度,延伸率及冲击韧性应不低于母材的机械性能,其中焊缝金属的扩散氢的含量应低于5ml/100g,手工电弧焊应采用低氢性焊条。
9、焊接材料供应货应附有质量证明书。
应任意抽查复验就焊丝。
10、桥面砼铺装采用C40混凝土。
钢箱梁-跨径为45m钢箱梁施工方案、方法及其措施
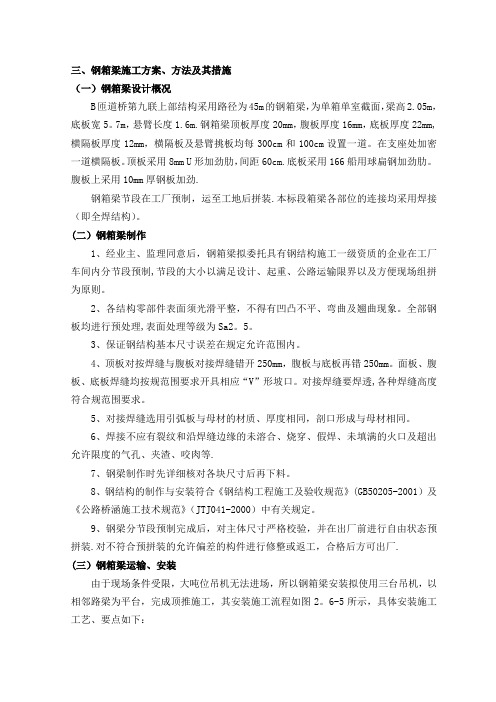
三、钢箱梁施工方案、方法及其措施(一)钢箱梁设计概况B匝道桥第九联上部结构采用路径为45m的钢箱梁,为单箱单室截面,梁高2.05m,底板宽5。
7m,悬臂长度1.6m.钢箱梁顶板厚度20mm,腹板厚度16mm,底板厚度22mm,横隔板厚度12mm,横隔板及悬臂挑板均每300cm和100cm设置一道。
在支座处加密一道横隔板。
顶板采用8mm U形加劲肋,间距60cm.底板采用166船用球扁钢加劲肋。
腹板上采用10mm厚钢板加劲.钢箱梁节段在工厂预制,运至工地后拼装.本标段箱梁各部位的连接均采用焊接(即全焊结构)。
(二)钢箱梁制作1、经业主、监理同意后,钢箱梁拟委托具有钢结构施工一级资质的企业在工厂车间内分节段预制,节段的大小以满足设计、起重、公路运输限界以及方便现场组拼为原则。
2、各结构零部件表面须光滑平整,不得有凹凸不平、弯曲及翘曲现象。
全部钢板均进行预处理,表面处理等级为Sa2。
5。
3、保证钢结构基本尺寸误差在规定允许范围内。
4、顶板对按焊缝与腹板对接焊缝错开250mm,腹板与底板再错250mm。
面板、腹板、底板焊缝均按规范围要求开具相应“V”形坡口。
对接焊缝要焊透,各种焊缝高度符合规范围要求。
5、对接焊缝选用引弧板与母材的材质、厚度相同,剖口形成与母材相同。
6、焊接不应有裂纹和沿焊缝边缘的未溶合、烧穿、假焊、未填满的火口及超出允许限度的气孔、夹渣、咬肉等.7、钢梁制作时先详细核对各块尺寸后再下料。
8、钢结构的制作与安装符合《钢结构工程施工及验收规范》(GB50205-2001)及《公路桥涵施工技术规范》(JTJ041-2000)中有关规定。
9、钢梁分节段预制完成后,对主体尺寸严格校验,并在出厂前进行自由状态预拼装.对不符合预拼装的允许偏差的构件进行修整或返工,合格后方可出厂.(三)钢箱梁运输、安装由于现场条件受限,大吨位吊机无法进场,所以钢箱梁安装拟使用三台吊机,以相邻路梁为平台,完成顶推施工,其安装施工流程如图2。
钢箱梁现场施工方法
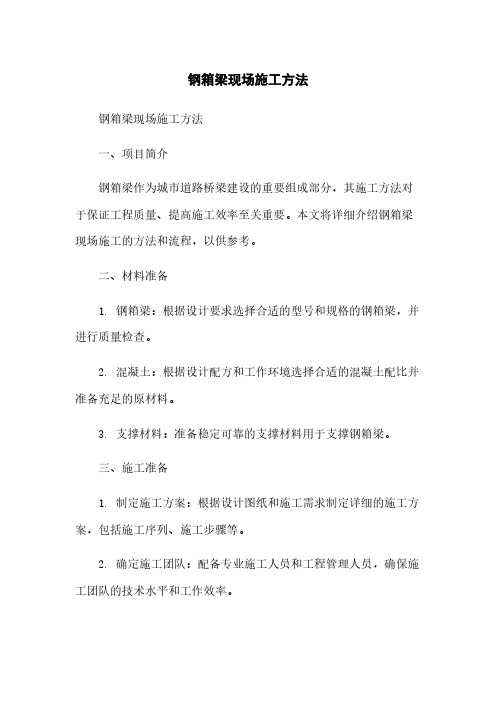
钢箱梁现场施工方法钢箱梁现场施工方法一、项目简介钢箱梁作为城市道路桥梁建设的重要组成部分,其施工方法对于保证工程质量、提高施工效率至关重要。
本文将详细介绍钢箱梁现场施工的方法和流程,以供参考。
二、材料准备1. 钢箱梁:根据设计要求选择合适的型号和规格的钢箱梁,并进行质量检查。
2. 混凝土:根据设计配方和工作环境选择合适的混凝土配比并准备充足的原材料。
3. 支撑材料:准备稳定可靠的支撑材料用于支撑钢箱梁。
三、施工准备1. 制定施工方案:根据设计图纸和施工需求制定详细的施工方案,包括施工序列、施工步骤等。
2. 确定施工团队:配备专业施工人员和工程管理人员,确保施工团队的技术水平和工作效率。
3. 设备准备:准备好吊装机械、安全设施等必要的施工设备和工具。
四、施工流程1. 基础准备:清理施工现场并进行基础勘测,确认基础平整度满足要求后进行标定。
2. 钢箱梁吊装:采用合适的吊装机械将钢箱梁吊装至预定位置,并进行调整和校正。
3. 钢箱梁安装:根据设计要求,进行钢箱梁的拼装和安装,确保连接牢固、平整度满足要求。
4. 混凝土浇注:在钢箱梁内部进行混凝土浇注,严格控制浇筑流程和施工工艺,确保混凝土密实度。
5. 后续工序:安装预应力钢筋、填充附属构件等相关工序,确保钢箱梁的稳定性和完整性。
五、质量控制1. 监测测量:对钢箱梁的垂直度、水平度、尺寸等进行监测和测量,确保符合设计要求。
2. 表面处理:对钢箱梁表面进行清理和防腐处理,确保其耐久性和外观质量。
3. 施工记录:及时记录施工过程中的关键环节和质量控制参数,为施工质量评估提供依据。
六、施工安全1. 安全教育:加强对施工人员的安全教育和培训,提高他们的安全意识和技能水平。
2. 安全设施:设置合适的安全警示标志、防护网等安全设施,确保施工现场的安全。
3. 安全监测:实施安全巡查和监测,发现和处理施工现场存在的安全隐患。
七、附件本所涉及的附件如下:附件1:钢箱梁设计图纸附件2:施工方案示意图附件3:工程进度表八、法律名词及注释本所涉及的法律名词及注释如下:1. 施工方案:指工程项目的施工组织设计和施工方法的规定,是施工工程的具体实施方案。
钢箱梁结构施工方案与技术措施

钢箱梁结构施工方案与技术措施按照钢箱梁分段情况,采用临时支墩现场拼装施工方案。
1、运输方案构件由专业厂家制作完毕后,按设计节段拼装完毕,经双方检查符合设计要求后,由加工场地运至安装现场,这样由大平板车及两台吊车配合装车运输,由于所运钢箱粱节段为超长、超宽运输构件,事先与交通管理部门取得联系,以保证运输过程中的安全,同时应对梁采取临时支承措施加固到位,运输过程中车辆行驶应匀速,避免梁段在运输过程中产生非弹性变形。
卸装现场进行必要的检查:①保证场地宽阔,保证吊车、板车出入自如;②保证场地平整,没有塌陷现象;③对场地进行必要的修整装车及运输:①平稳将构件放在板车上加垫方木;②将构件用牢固的锁紧在板车上;③运输前检验全程道路是否有障碍物及高压线等情况;④确定运输时间,车辆低峰时运输。
2、临时支墩:按照钢箱梁分段情况(纵向分为五个节段,横向分为7段),采用增加4个临时支墩现场拼装施工方案地基处理,临时支墩处原地面破除路面,换填填筑60cm 砂砾进行整体碾压;压实度达到90%以上;在支架位置处浇筑25cm混凝土做为支墩基础。
在地面硬化后,加强箱梁施工范围内的排水工作,在场地两侧开挖30cm×30㎝排水沟,并设置水槽,严禁在施工场地内形成积水,造成地基不均匀沉降,引起临时支墩失稳,出现不安全隐患和事故。
支架搭设:采用30×30cm碗扣支架做为临时支墩,横桥向布满,纵桥向布设3m,支架高度每隔2米设双向水平拉杆,钢管框架之间设交叉斜撑,以保证支架稳定。
3、拼装顺序钢箱梁拼装由钢箱梁制作厂家安排人员到施工现场负责拼装。
现场拼装全部在胎架上完成。
胎架区设置有供单元件调整及角点控制的装置和标识,同时,考虑到不同区域的梁段其纵坡值不一样,而相邻梁段在胎架上预拼时又必须保证其拱度值,因此,在每一轮梁段上胎架组焊前根据每一轮胎架的设计拱度值调整模板高度,模板高度的调整采用插调整垫板形式来完成。
在胎架区的地面上设置供各单元定位的(纵、横向)标记线,在胎架以外的钢柱上设置有各单元件的高度定位基准标记线(即:标高样杆)。
钢箱梁施工方案要点

(5)钢箱梁施工工艺1)总体思路A匝道第三联(2*27.5m)、第四联(30m+45m),B匝道第二联(30m+50m+37.5m)为钢箱梁,采用分节段工厂预制,在桥位现场搭设临时支墩并搭设临时支架,利用汽车吊分段吊装架设就位后进行拼装、焊接、涂装施工。
由于A、B匝道跨越地铁、城铁,应采取保护措施,我单位拟在地铁、城铁上浇筑钢筋混凝土道路,道路宽8m、长20m、厚20cm,并铺设 30cm水泥稳定碎石基层,结构总厚度50cm。
2)工程特点及难点钢箱梁线形控制精度高。
钢箱梁为曲线连续梁,在现场拼装时需要同时保证成桥平曲线线形和竖曲线线形,按线形制造精度要求高,控制难度大。
钢箱梁安装在既有线路上跨线施工,施工过程要求各主要道路交通运营不能中断,尽量减少各类扰民的因素,这对现场安装的施工组织提出了更高的要求。
现场场地有限,运输节段来料存放数量有限,要求严格按架梁顺序供梁,并尽量减少梁段的存放时间;存梁场地与安装位置有一定距离,需要水平运输。
同时现场道路比较窄,转弯半径小,都是水平运输的制约因素。
现场焊接工作包括节段间的纵缝和环缝,工作量较大,焊接质量要求高。
现场的节点均为焊接,将采用手工电弧焊、CO2气体保护和埋弧自动焊等各种焊接方法,焊接位置将有平位焊、立位焊和仰位焊等各种焊接工位,现场焊缝多为熔透焊,要求进行超声波、磁粉及X射线等无损检测。
高空施工危险性大。
钢箱梁的架设高度一般不超过8m,存在着诸多的高空作业,如高空吊装、高空拼装焊接、高空调整、高空涂装等,高空施工的安全保护,是工程施工的重点。
施工防护措施多。
在高空施工要设置施工操作平台,在跨线部分上方施工焊接时,在下面既有线路未封闭时,要在高空进行防护,防止火花、小物件坠落等。
3)分段方案根据现场条件和本工程结构特点,采用工厂内分段预制,运输到现场后,分段吊装架设的方法。
工厂分段方案如下:①A匝道桥第三联钢箱梁沿桥长方向划分为24个节段,相邻两节段之间的顶板、底板、及腹板环缝处分别错开200mm,呈Z字形布置。
钢箱梁施工工艺

钢箱梁施工工艺标题:钢箱梁施工工艺详解与实践应用一、引言钢箱梁作为一种大跨度桥梁的重要结构形式,具有强度高、自重轻、工厂化程度高、施工速度快等显著优点,在现代桥梁建设中得到了广泛应用。
本文主要就钢箱梁的施工工艺进行详细介绍。
二、钢箱梁施工工艺流程1. 设计与制造阶段:(1)设计阶段:根据桥梁的设计要求和荷载条件,进行钢箱梁的整体设计,包括截面形状、尺寸及材质选择等。
(2)制造阶段:在工厂内按照设计图纸进行标准化、模块化的预制工作,主要包括钢板切割、折弯、焊接,形成箱形断面,同时完成防腐处理和预拼装检查。
2. 运输与吊装阶段:(1)运输:采用专用设备对预制好的钢箱梁进行安全包装和装载,确保运输过程中的稳定性。
(2)吊装:到达现场后,通过大型吊车进行精确对位和吊装作业,通常采用临时支撑或悬臂拼装的方式逐步安装到位,保证结构受力合理且符合设计要求。
3. 现场连接与调整阶段:(1)连接:采用高强螺栓或者焊接方式将各节段钢箱梁紧密连接,形成连续稳定的桥梁主体结构。
(2)调整:在所有箱梁安装完毕后,进行整体线形和应力调整,以满足设计规范要求。
4. 防护与涂装阶段:最后,进行钢箱梁表面的防护涂装,提高其耐腐蚀性,延长使用寿命,并进行质量验收,确保整个工程的质量达标。
三、施工注意事项在钢箱梁施工过程中,应严格遵守国家相关法规和技术标准,强化安全管理,做好环境监测和保护;同时,要注重施工精度控制,确保每个环节的质量可控,有效避免因施工误差造成的结构安全隐患。
四、结语随着工程技术的发展,钢箱梁施工工艺也在不断优化和完善。
只有充分理解和熟练掌握这一系列工艺流程,才能确保钢箱梁结构的安全稳定,为我国桥梁建设事业贡献力量。
钢箱梁施工方案

钢箱梁施工方案一、概述钢箱梁是一种常用于桥梁施工的结构,具有较高的承载能力和优异的耐久性。
本文将介绍钢箱梁施工的方案。
二、施工准备1. 施工材料准备施工钢箱梁所需材料包括:•钢板:用于制作钢箱梁的主体结构。
•焊条和气割设备:用于焊接和切割钢板。
•扣件和螺栓:用于连接钢板和其他构件。
•起重机:用于梁块的吊装。
•混凝土:用于填充钢箱梁内部。
•其他施工辅助材料:如脚手架、模板等。
2. 工程准备在施工前,需要进行以下工程准备:•确定施工时间和施工场地。
•绘制详细的工程图纸和施工图纸。
•安排施工人员和机械设备。
•制定施工计划和安全措施。
三、施工步骤1. 制作钢箱梁首先,按照设计要求,采用焊接或拼接的方法制作钢箱梁的主体结构。
将钢板经过切割、焊接等工艺处理,形成钢箱梁的基本形状。
然后使用扣件和螺栓将各个钢板连接在一起,形成一个完整的钢箱梁。
2. 钢箱梁的吊装将起重机安置在适当的位置,将吊钩连接到钢箱梁上。
在确保安全的情况下,利用起重机将钢箱梁吊装到指定位置。
为了保证吊装的稳定性和安全性,在吊装过程中需要做好预先计算和安全措施。
3. 钢箱梁的连接与固定将已吊装到位的钢箱梁与桥墩或其他支撑结构连接固定。
使用螺栓和焊接等方法将钢箱梁与支撑结构紧密连接,并进行必要的检测和调整,确保连接的牢固性和稳定性。
4. 钢箱梁的填充在连接好的钢箱梁内部,以均匀的方式施工混凝土,填充整个钢箱梁的空腔。
填充过程中需要注意混凝土的浇筑方法和浇筑层次,以确保混凝土的质量和完整性。
5. 施工验收和完成在完成钢箱梁的施工后,进行必要的验收和检查。
检查钢箱梁各部位的焊接和连接是否达到设计要求,混凝土填充是否均匀牢固。
同时进行必要的试验和测试,以确保钢箱梁的质量和安全性。
四、施工安全措施在钢箱梁的施工过程中,需要采取以下安全措施:•严格按照施工计划进行施工,避免超负荷施工和不当操作。
•在施工现场设置明显的安全警示标志和围栏,确保施工区域的安全。
钢箱梁工程施工规范
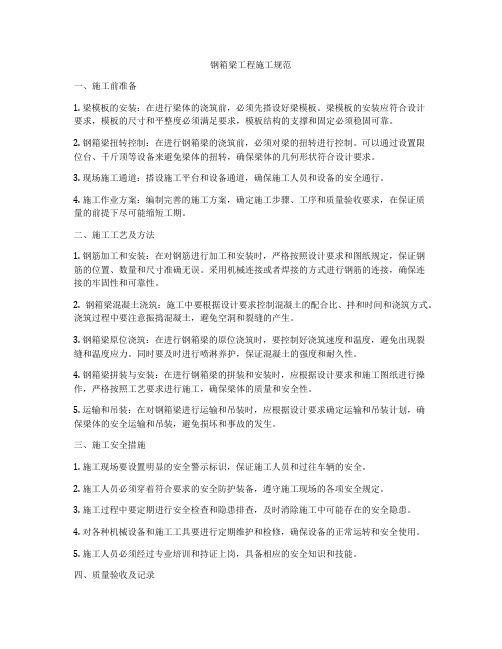
钢箱梁工程施工规范一、施工前准备1. 梁模板的安装:在进行梁体的浇筑前,必须先搭设好梁模板。
梁模板的安装应符合设计要求,模板的尺寸和平整度必须满足要求,模板结构的支撑和固定必须稳固可靠。
2. 钢箱梁扭转控制:在进行钢箱梁的浇筑前,必须对梁的扭转进行控制。
可以通过设置限位台、千斤顶等设备来避免梁体的扭转,确保梁体的几何形状符合设计要求。
3. 现场施工通道:搭设施工平台和设备通道,确保施工人员和设备的安全通行。
4. 施工作业方案:编制完善的施工方案,确定施工步骤、工序和质量验收要求,在保证质量的前提下尽可能缩短工期。
二、施工工艺及方法1. 钢筋加工和安装:在对钢筋进行加工和安装时,严格按照设计要求和图纸规定,保证钢筋的位置、数量和尺寸准确无误。
采用机械连接或者焊接的方式进行钢筋的连接,确保连接的牢固性和可靠性。
2. 钢箱梁混凝土浇筑:施工中要根据设计要求控制混凝土的配合比、拌和时间和浇筑方式。
浇筑过程中要注意振捣混凝土,避免空洞和裂缝的产生。
3. 钢箱梁原位浇筑:在进行钢箱梁的原位浇筑时,要控制好浇筑速度和温度,避免出现裂缝和温度应力。
同时要及时进行喷淋养护,保证混凝土的强度和耐久性。
4. 钢箱梁拼装与安装:在进行钢箱梁的拼装和安装时,应根据设计要求和施工图纸进行操作,严格按照工艺要求进行施工,确保梁体的质量和安全性。
5. 运输和吊装:在对钢箱梁进行运输和吊装时,应根据设计要求确定运输和吊装计划,确保梁体的安全运输和吊装,避免损坏和事故的发生。
三、施工安全措施1. 施工现场要设置明显的安全警示标识,保证施工人员和过往车辆的安全。
2. 施工人员必须穿着符合要求的安全防护装备,遵守施工现场的各项安全规定。
3. 施工过程中要定期进行安全检查和隐患排查,及时消除施工中可能存在的安全隐患。
4. 对各种机械设备和施工工具要进行定期维护和检修,确保设备的正常运转和安全使用。
5. 施工人员必须经过专业培训和持证上岗,具备相应的安全知识和技能。
桥梁钢箱梁施工方法及施工工艺
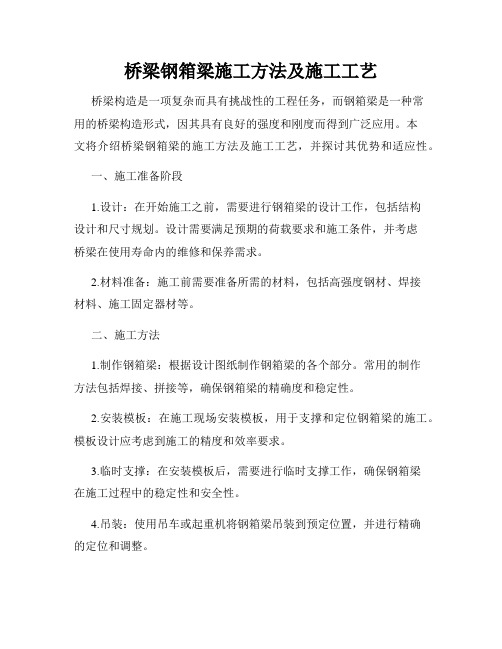
桥梁钢箱梁施工方法及施工工艺桥梁构造是一项复杂而具有挑战性的工程任务,而钢箱梁是一种常用的桥梁构造形式,因其具有良好的强度和刚度而得到广泛应用。
本文将介绍桥梁钢箱梁的施工方法及施工工艺,并探讨其优势和适应性。
一、施工准备阶段1.设计:在开始施工之前,需要进行钢箱梁的设计工作,包括结构设计和尺寸规划。
设计需要满足预期的荷载要求和施工条件,并考虑桥梁在使用寿命内的维修和保养需求。
2.材料准备:施工前需要准备所需的材料,包括高强度钢材、焊接材料、施工固定器材等。
二、施工方法1.制作钢箱梁:根据设计图纸制作钢箱梁的各个部分。
常用的制作方法包括焊接、拼接等,确保钢箱梁的精确度和稳定性。
2.安装模板:在施工现场安装模板,用于支撑和定位钢箱梁的施工。
模板设计应考虑到施工的精度和效率要求。
3.临时支撑:在安装模板后,需要进行临时支撑工作,确保钢箱梁在施工过程中的稳定性和安全性。
4.吊装:使用吊车或起重机将钢箱梁吊装到预定位置,并进行精确的定位和调整。
5.焊接:将各个部分进行焊接,确保钢箱梁的整体刚度和强度。
焊接需要符合相关焊接规范和质量要求。
6.防腐处理:对焊接接头和表面进行防腐处理,以保护钢箱梁在使用寿命内的耐久性。
7.连接和固定:通过螺栓、焊接等方式连接和固定钢箱梁与桥墩或桥面板等构件,确保整个桥梁的稳定性和刚度。
三、施工工艺1.预应力施工:钢箱梁的预应力施工是其中重要的一个环节。
通过张拉预应力钢束来调整钢箱梁的应力和形状,以增强其承载能力和使用寿命。
2.梁底铺装:在钢箱梁安装完成后,进行梁底的铺装工作。
铺装材料可以根据具体要求选择,常见的有沥青、混凝土等。
3.验收和质量控制:在完成施工后,对钢箱梁及相关构件进行验收和质量控制,确保施工的质量和符合规范要求。
钢箱梁作为一种常用的桥梁构造形式,具有施工速度快、质量可控、耐久性好等优势。
其适用于各种桥梁跨度和荷载要求,特别是在需要迅速恢复交通的情况下,钢箱梁的施工工艺可以提供高效的解决方案。
钢箱梁施工方案(3篇)

第1篇一、工程概况本工程为某城市快速通道桥梁工程,桥梁全长500米,主桥采用钢箱梁结构,跨径组合为(60+100+60)米。
钢箱梁总重量约1500吨,由多片钢箱梁拼接而成。
本方案针对钢箱梁的施工进行详细规划,确保工程质量和安全。
二、施工准备1. 技术准备- 完成钢箱梁设计图纸的审查,确保设计符合规范要求。
- 组织施工人员学习钢箱梁施工工艺,提高施工人员的技能水平。
- 制定详细的施工方案,明确施工流程、质量标准和安全措施。
2. 材料准备- 确保钢材质量符合国家相关标准,并进行进场检验。
- 准备焊接材料、涂料、紧固件等施工所需材料。
3. 设备准备- 确保焊接设备、吊装设备、检测设备等施工设备完好,并进行调试。
- 准备施工用的脚手架、防护栏杆等安全设施。
4. 人员准备- 组建专业的施工队伍,明确各工种人员职责。
- 对施工人员进行安全教育和技能培训。
三、施工工艺1. 基础处理- 清理施工现场,确保基础坚实、平整。
- 进行基础验收,确保满足钢箱梁安装要求。
2. 钢箱梁制作- 钢材下料:根据设计图纸,对钢材进行切割、下料。
- 组装焊接:将下料后的钢材按照设计要求进行组装,并进行焊接。
- 表面处理:焊接完成后,对钢箱梁表面进行打磨、除锈、涂装。
3. 钢箱梁运输- 选择合适的运输方式,确保钢箱梁在运输过程中不受损坏。
- 钢箱梁运输至施工现场后,进行验收。
4. 钢箱梁安装- 吊装:采用起重机进行钢箱梁吊装,确保吊装过程中安全可靠。
- 安装就位:将钢箱梁吊装至设计位置,并进行临时固定。
- 精调:对钢箱梁进行精调,确保其位置、标高、垂直度等符合设计要求。
- 焊接:对钢箱梁进行焊接,确保焊接质量。
5. 防腐涂装- 钢箱梁焊接完成后,进行表面清理,确保表面干净、无油污。
- 涂装:按照设计要求,对钢箱梁进行防腐涂装。
四、质量控制1. 材料质量控制- 严格把关钢材质量,确保符合国家相关标准。
- 对焊接材料、涂料等施工材料进行检验,确保质量合格。
钢箱梁施工方法及工艺
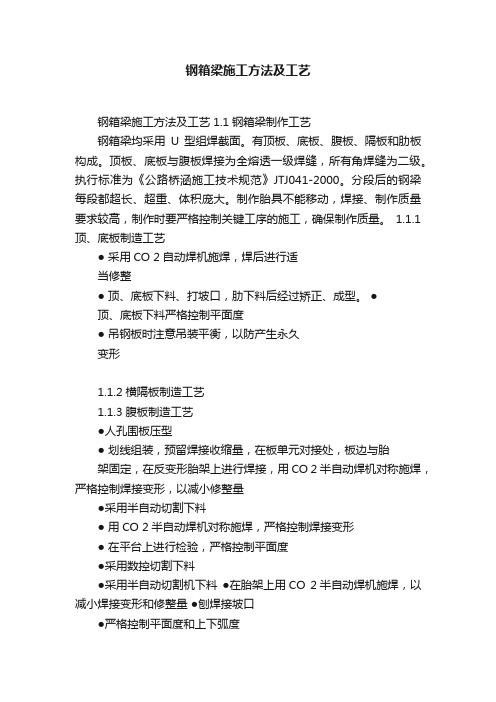
钢箱梁施工方法及工艺钢箱梁施工方法及工艺 1.1钢箱梁制作工艺钢箱梁均采用U 型组焊截面。
有顶板、底板、腹板、隔板和肋板构成。
顶板、底板与腹板焊接为全熔透一级焊缝,所有角焊缝为二级。
执行标准为《公路桥涵施工技术规范》JTJ041-2000。
分段后的钢梁每段都超长、超重、体积庞大。
制作胎具不能移动,焊接、制作质量要求较高,制作时要严格控制关键工序的施工,确保制作质量。
1.1.1顶、底板制造工艺● 采用CO 2自动焊机施焊,焊后进行适当修整● 顶、底板下料、打坡口,肋下料后经过矫正、成型。
●顶、底板下料严格控制平面度● 吊钢板时注意吊装平衡,以防产生永久变形1.1.2横隔板制造工艺1.1.3腹板制造工艺●人孔围板压型● 划线组装,预留焊接收缩量,在板单元对接处,板边与胎架固定,在反变形胎架上进行焊接,用CO 2半自动焊机对称施焊,严格控制焊接变形,以减小修整量●采用半自动切割下料● 用CO 2半自动焊机对称施焊,严格控制焊接变形● 在平台上进行检验,严格控制平面度●采用数控切割下料●采用半自动切割机下料●在胎架上用CO 2半自动焊机施焊,以减小焊接变形和修整量●刨焊接坡口●严格控制平面度和上下弧度●采用CO 2半自动焊,焊后修整严格控制直线度●在胎架上用CO 2半自动焊机按工艺规定的顺序施焊,严格控制焊接变形●采用喷丸(砂)除锈,将表面油污、氧化皮和铁锈以及其它杂物消除干净。
●采用刷涂,最小膜厚需达到规定厚度的90%以上。
●采用高压无气喷涂,应光洁美观、色彩均匀。
● 整体涂装后修补检验。
1.1.4涂装工艺1.2施工精度控制措施 1.2.1总体控制措施(1)工艺控制:从深化图纸开始,钢梁有横向坡度,纵向高差,竖向起拱,都要在详图转化中考虑。
底板为二次抛物线形,腹板、内隔板等要电脑放样。
(2)排板下料:根据详图排版:在钢板上放样,长度方向放出100mm 的余量,横向收缩加20mm 的余量。
主要考虑底板纵横向焊接收缩量。
- 1、下载文档前请自行甄别文档内容的完整性,平台不提供额外的编辑、内容补充、找答案等附加服务。
- 2、"仅部分预览"的文档,不可在线预览部分如存在完整性等问题,可反馈申请退款(可完整预览的文档不适用该条件!)。
- 3、如文档侵犯您的权益,请联系客服反馈,我们会尽快为您处理(人工客服工作时间:9:00-18:30)。
钢箱梁施工方法及工艺 1.1钢箱梁制作工艺钢箱梁均采用U 型组焊截面。
有顶板、底板、腹板、隔板和肋板构成。
顶板、底板与腹板焊接为全熔透一级焊缝,所有角焊缝为二级。
执行标准为《公路桥涵施工技术规范》JTJ041-2000。
分段后的钢梁每段都超长、超重、体积庞大。
制作胎具不能移动,焊接、制作质量要求较高,制作时要严格控制关键工序的施工,确保制作质量。
1.1.1顶、底板制造工艺● 采用CO 2自动焊机施焊,焊后进行适当修整● 顶、底板下料、打坡口,肋下料后经过矫正、成型。
●顶、底板下料严格控制平面度● 吊钢板时注意吊装平衡,以防产生永久变形1.1.2横隔板制造工艺1.1.3腹板制造工艺●人孔围板压型● 划线组装,预留焊接收缩量,在板单元对接处,板边与胎架固定,在反变形胎架上进行焊接,用CO 2半自动焊机对称施焊,严格控制焊接变形,以减小修整量●采用半自动切割下料● 用CO 2半自动焊机对称施焊,严格控制焊接变形● 在平台上进行检验,严格控制平面度●采用数控切割下料●采用半自动切割机下料 ●在胎架上用CO 2半自动焊机施焊,以减小焊接变形和修整量 ●刨焊接坡口●严格控制平面度和上下弧度●采用CO 2半自动焊,焊后修整严格控制直线度●在胎架上用CO 2半自动焊机按工艺规定的顺序施焊,严格控制焊接变形●采用喷丸(砂)除锈,将表面油污、氧化皮和铁锈以及其它杂物消除干净。
●采用刷涂,最小膜厚需达到规定厚度的90%以上。
●采用高压无气喷涂,应光洁美观、色彩均匀。
● 整体涂装后修补检验。
1.1.4涂装工艺1.2施工精度控制措施 1.2.1总体控制措施(1)工艺控制:从深化图纸开始,钢梁有横向坡度,纵向高差,竖向起拱,都要在详图转化中考虑。
底板为二次抛物线形,腹板、内隔板等要电脑放样。
(2)排板下料:根据详图排版:在钢板上放样,长度方向放出100mm 的余量,横向收缩加20mm 的余量。
主要考虑底板纵横向焊接收缩量。
每段制作时考虑拼装收缩量和安装余量。
●保证电弧喷涂涂层的质量和涂层与被喷涂基体之间的结合强度。
(3)对于箱体在专用道胎具上进行组对,根据施工图按1:1比例在制作平台上放样,用水准仪测量在胎架上高程值。
(4)顶板上部用卡板固定。
下端用楔形铁块固定。
箱梁两端设置临时支撑,用经纬仪测定箱口上下垂直度。
(5)注意垂直度,防止扭曲变形是箱型梁制作的重要环节,所以,在组装箱体的每一工序都要检查是否扭曲,如发现及时处理。
控制箱体由自重而引起的下挠。
(6)箱梁的翻转焊接;可用翻转器固定钢梁,钢梁翻转30。
中间部位的钢梁重量大,采用吊耳吊装翻转。
吊耳焊接位置见(安装节点图)(7) 检查工具复检。
钢尺、角尺、塞尺、测量仪器校核。
1.2.2放样、号料和切割(1)放样和号料应根据加工详图和工艺要求进行。
(2)对于形状复杂的隔板和杆件,应通过放样校对后确定。
(3)样板制作的允许偏差应符合表6-1的规定。
(4)号料前应检查钢板的牌号、规格、质量,如发现钢板不平直,有蚀锈、油漆等污物,应矫正清理后再号料。
样板、样杆、样条制作允许偏差表6-1(5)切割时应注意下列事项:1)切割前应将钢板上浮锈、污物清除干净。
钢料应放平、垫稳,割缝下面应留有空隙。
2)切割采用精密切割,采用数控切割机下料。
或多头半自动切割机下料。
3)剪切钢板应控制板厚,厚度不宜超过12mm,剪切边缘应平整,无毛刺、缺肉。
4)矫正和边缘加工,用半自动切割机和数控切割机配以砂轮打磨坡口。
刨光顶紧板和支座垫板用铣床加工。
5)精密切割面质量应符合表6-2的规定,切割面硬度不超过HV350。
切割表面质量要求表6-21.2.3材料拼接钢板长度拼接时,应分次完成。
因为板太长一次接成整板不好校正。
分几次拼接后进行平板矫正,再接成大整板。
操作顺序为:拼接、施焊、矫直、下料放样。
所有对接焊缝采用埋弧自动焊。
焊缝的两端应设引弧板,材质用Q345qD,焊后用气割切除引弧板并修磨平整。
腹板、顶板、底板为定宽板,只需长度方向接板。
(1)拼板接口坡口用半自动切割机进行坡口加工,用砂轮机打磨。
(2)拼接点固时先检查坡口形式,再检查两板是否放在一个平面上。
(3)拼接板(翼缘板、腹板)要求熔透焊,根据质量等级要求进行超声波检查并增加5%的X射线检验。
(4)埋弧焊丝采用同材质同强度的焊丝。
(5)采用焊剂必须同焊丝相匹配,焊丝提前烘干。
控制温度在300-350℃,烘干2小时。
1.3钢梁组装时注意事项(1)底板上必须弹出中心线,隔板位置必须打出样冲眼。
(2)胎架完成后,尺寸经检查后,不得再修改胎架,移动胎架位置。
(3)底板纵向加劲肋误差必须满足规范规定。
解体后的钢梁分三段制作。
顶板、底板和腹板的接口位置错开200mm。
钢梁两端顶板采用25mm厚钢板,翼缘宽度600mm,对应腹板为16mm。
钢梁中间部分顶板为30mm厚钢板,翼缘宽度600mm,对应的腹板为14mm。
中心对称以14mm为基准。
在变截面处以箱梁外侧找平。
顶板翼缘坡度2%,见图示6-3箱梁断面图图6-5 ZY23-ZY24钢桥平面布置图1.4钢梁制作(1)腹板上下端开坡口。
上端开45O坡口,下端腹板内侧开单坡口45O。
(2)腹板与顶板的T型焊缝采用埋弧自动焊接,在H 型钢生产线上焊接成型。
焊丝采用H08Mn2E, 焊剂选用SJ101Q。
电流580~600(A),焊接速度45~50cm/min。
(3)箱体组装前两侧腹板上的四道肋板焊在腹板上。
焊缝采用埋弧制动焊或CO2气体保护焊。
接口位置的肋板预留。
(4)底板铺设在调整好的胎架上,底板上的四道肋板与底板焊接。
焊缝采用CO2气体保护焊。
电流220~240(A),焊接速度20~30cm/min。
接口位置的肋板预留。
(5)横隔板从上部穿入固定在底板上的肋板。
端头板不上,用支撑代替端头板。
端头板最后安装。
(6)把矫正好的T型腹板下端放在底板上进行调整。
腹板上的各道肋板对应的隔板上的槽一一就位。
腹板与底板焊接内侧采用CO2气体保护焊,配以ER50-3焊丝。
外侧采用埋弧自动焊。
(7)横隔板与腹板、底板的焊接采用角焊缝,用CO2气体保护焊,配以ER50-3焊丝。
(8)箱室内支座处的横隔板焊接完成后上端横梁,端板外侧开坡口。
用CO2气体保护焊,配以ER50-3焊丝。
1.4.1现场拼装接口与设计人员沟通后改为右图形式1.4.2隔板的制作与组装横隔板是箱体的内胎,是控制箱型断面尺寸的关键。
隔板分两种,一种为箱室内的隔板,一种为连接横梁隔板,箱室内的隔板制作复杂。
应根据图纸在数控床上制图放样。
切割前检查数据无误后进行切割。
一次成型,保证几何尺寸在误差范围之内。
孔径必须保证光洁度。
隔板矫正不平整度。
1.5钢梁焊接要求在工厂首次焊接工作之前或材料、工艺在施工过程中遇有须重新评定的变化,必须分别进行焊接工艺评定试验。
焊接工艺评定按现行《公路桥涵施工技术规范》进行。
焊工应经过考试,熟悉焊接工艺要求,取得资格证书后方可从事焊接工作。
焊工停焊时间超过6个月,应重新考核。
工厂焊接宜在室内进行,湿度不宜高于80%。
主要杆件应在组装后24h内焊接。
低合金高强度结构钢厚度为25mm以上时进行定位焊、埋弧焊时应进行预热,预热温度80~120℃,预热范围为焊缝两侧,宽度50~80mm。
(1)焊接材料应通过焊接工艺评定确定,具有质量证明书。
埋弧自动焊焊丝,选用H08Mn2E,Φ4.0mm;焊剂选用SJ101Q。
CO2 气体保护焊焊丝选用ER50-3 ,Φ1.2mm;埋弧自动焊必须在距杆件端部80mm以外的引弧板上起、熄弧。
焊缝停弧处刨成l:5斜坡后,并搭接50mm再引弧施焊。
(2)所有焊缝必须进行外观检查,不得有裂纹、未熔合、夹渣、未填满弧坑和超出规定的缺陷。
(3)外观检查合格后,焊缝应在24h后进行无损检验。
(4)超声波探伤时,内部质量分级应符合规定。
其它技术要求可按现行《钢焊缝手工超声波探伤方法和探伤结果分级》(GBll345)执行。
顶板、腹板和底板横向对接焊缝增加10%射线探伤,二级焊缝进行磁粉探伤检查。
焊接规范参数1.6焊接变形的控制方法(1)采用合理焊接顺序。
尽量采取对称焊接和分段退焊法、多层焊、焊前要预热,使焊件在施焊时温度均匀,并且应连续施焊,每一层焊道焊完后应及时清理焊渣和飞溅物。
先焊主要的焊缝后焊次要的焊缝。
先焊单独的小构件,再焊整体构件,而且要减少交叉和密集焊缝。
(2) 起拱:钢梁中心按抛物线起拱120mm,防止钢梁下挠。
(3) 不能随便增大焊肉,焊肉过大容易引起焊接应力集中而过量变形。
(4) 构件吊装时要加固临时支撑。
防止构件扭曲变形。
(5) 合理安排焊接时间,先焊接的主焊缝与后焊接的焊缝不能相隔时间太长,否则后焊接的焊接变形收缩量抵消不了前面焊缝焊接的收缩变形。
(6)组装平台一定要用水准仪找平。
尽量使基准面比较平整。
保证构件组装的精准。
1.7钢梁矫正方法矫正方法主要有机械矫正、火焰矫正和综合矫正。
利用火焰矫正法要适当控制火焰加热的温度,温度过高会使材料机械性能降低,温度过低使矫正效率降低。
火焰矫正的效果,关键在于正确的选择加热位置、范围、加热温度以及加热后的冷却速度,低合金钢材料的加热温度一般为600℃-800℃。
1.8栓钉焊接栓钉焊接要做焊接实验,栓钉进行复检并做焊接工艺评定。
钢梁上翼缘的剪力钉按布置图排列。
请专业的队伍进行栓钉施焊。
栓钉规格为φ22*180mm。
焊机采用RSN-2500型电弧栓柱焊机。
电流控制在1900-1925A,按照栓钉布置图画线定位。
施焊应在专用胎架上。
先把瓷环放在定位线上。
采用M22的卡头夹紧栓钉进行施焊。
每个栓钉焊完后进行检查,位置放的是否准确,焊接是否牢靠。
合格后构件方可出厂。
1.9钢梁预拼装钢梁拼装精度控制(1)要控制起拱度、横向坡度、侧弯、总长度。
(2)在胎架上放出预拱度,用垫铁调整。
(3)钢梁拼装工艺流程:(一组预拼装)。
(4)拼装顺序:胎具的制作—拼装定位—钢梁分解部件验收—钢梁分段组装—除锈涂漆—整体验收。
(5)根据钢梁几何尺寸先布置胎具支架,拼装顺序采用从中间向两端延伸的方法进行,在钢梁每隔3米位置放置一组胎具进行支撑,胎具上平面应根据起拱要求逐次进行标高调整。
用全站仪进行放线确定组装定位点。
(6)第一段(中间部分)放置到胎具后,进行水平位置、垂直度的调整,达到设计要求后,进行临时加固,对本段内部的加劲板进行验尺。
固定完毕后再进行本段整体尺寸校验。
(7)依次进行其各段梁的组装,拼装、连接直到拼装完成。
(8)拼装完成后,进行编号,做标记。
接口位置焊上临时定位板。
便于现场组对时拼接。
梁拼装主要尺寸允许偏差表6-9成梁拼装在龙门吊和汽车吊下配合下进行。
1.10油漆涂装构件验收合格后,进行抛丸除锈,等级达到Sa2.5。
安装焊缝位置处留出30-50mm暂不涂刷油漆。