液压成形
橡皮液压成形
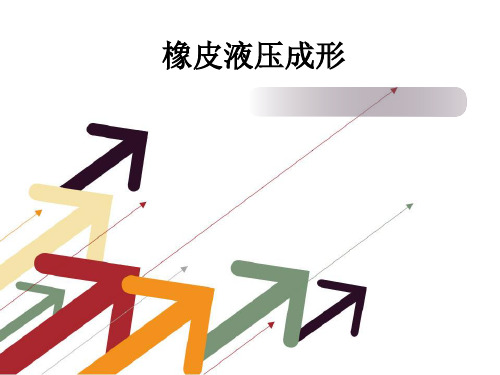
A
凸模
B 带压边圈的凸模
橡皮成形模具形式
• 凹模(图 C)。带有大圆角的深冲件的最合适模具是凹模。因为凹模 比凸模有更大的拉伸区。凹模能使板料受压区更好的贴附凹模表面。 • 胀形凹模(图 D)。胀形凹模的功用是把预成形的板料胀形进入模腔 内。这种模具应由几部分组成以便于能够拆开,使成形件能取出。
C
橡皮液压成形
橡皮液压成形
• 橡皮成形是利用橡皮囊作为弹性 凹模(或凸模),用液体作为传 压介质,使金属板料随刚性凸模 (或凹模)成形的一种软模凸模 (或凹模)成形方法。其中使板 料沿着模具成形的部分就是橡皮 囊,另外约束板料成形的一部分 就是刚性模。
图 1 橡皮囊液压机
橡皮成形研究和应用现状
• 橡皮囊成形属于液压成形,该成形方法是从管件液压成形推广而来,提出橡 皮成形最早的一份专利是在 1872 年。是用一块厚橡皮盖在模具和毛料之上 ,用一般压床对橡皮加压使零件成形。这种自由橡皮成形的方法有很多的缺 点:橡皮外流,压力小,分布不均匀,橡皮寿命短。 1938 年美国人盖林提出把一叠厚橡皮装在一个金属容框内进行橡皮成形的 专利。 1955 年美国人惠龙提出一个实现 1949 年提出的原理的新机床方案。 1963 年, 为了减轻成形机框架的重量和增强液室的强度,采用钢带缠绕增强 技术。
橡皮成形应用
• 汽车方面,顶盖、挡泥板、行李箱 盖板、车门、1/4 面板、防风支架、 发动机支架、排气罩、减震器托架、 赛车前轮罩、前增强板、摩托车油 箱。
• 飞机方面:现在在国外的现代化飞 机制造厂, 通过橡皮囊液压成形的 零件已达飞机钣金零件总数的50%以 上, 国内也占到 35%~40%, 且有进 一步增多的趋势。由于飞机钣金零 件一般为单件小批量生产, 因此需 要的成形模具数量很大, 以 L15 飞 机为例, 共有橡皮囊液压成形模 619 项, 占其钣金制造工装的 51.4%。
液压成型

图1 空心异形截面零件引言液压成形技术同冲压,焊接等传统的成形技术相比,是一门新型的金属成形技术。
为了解决汽车,航空航天等领域的一些复杂的工艺问题和技术要求,从20世纪50年代起,德、美、日等国科学家在相关领域内先后提出了内高压成形技术和板料液压成形技术。
1985年我国科学家王仲仁教授发明了球形容器无模液压成形技术,提出了壳体液压成形技术。
近几年,依托于计算机控制技术和高压液压系统的发展,液压成形技术迅速发展。
目前,很多复杂结构的零件都可以通过该技术批量地加工生产。
一、液压成形技术的概述1.1 液压成形的定义和分类液压成形也称为液力成形是指利用液体作为传力介质或模具使工件成形的一种塑性加工技术。
按使用的液体介质不同,液压成形分为水压成型和油压成型;按使用的配料不同,液压成形分为管材液压成形,板料液压成形和壳体液压成形。
板料和壳体液压成形使用的成形压力较低,而管材液压成形使用的压力较高,又称为内高压成形,本文中称管材液压成形为内高压成形。
1.2 液压成形的特点现代液压成形技术的主要特点表现在两个方面:①液压成形技术仅需要凸模和凹模中的一个,或者不使用任何模具,这样可以省去一半,甚至不需要花费制造模具的费用和加工时间,而且液体作为凸模可以成形很多刚性凸模无法成形的复杂零件。
②液体作为传力介质具有实时可控性,通过液压闭环伺服系统和计算机控制系统可以按给定的曲线精确控制压力,确保工艺参数在设定的数值内,并且随时间可变可调,大大提高了工艺柔性。
二、内高压成形技术2.1 内高压成形技术的原理及分类内高压成形技术是用管材作为原材,通过对官腔内施加液体压力及在轴向施加负荷作用,使其在给定模具型腔内发生塑性变形,管壁与模具内表面贴合,从而得到所需形状零件的成形技术。
内高压成形技术主要可以整体成型轴线为二维或三维曲线的异形截面空心零件,从材料的初始圆截面可以成形为矩形,梯形,椭圆形或其他异形的封闭界面,如图1所示。
波纹管液压成形原理及工艺方法

波纹管液压成形的原理是,将高压液体(如水或液压油)注入预制的管坯中,使管坯在模具中膨胀,然后压缩,管材发生塑性变形,最终得到成形的波纹管。
这种成形方式可以确保管壁减薄量适中,因为液压在管壁上的作用是均匀的。
波纹管液压成形的工艺方法可以分为以下步骤:
1. 按照设计尺寸截取管坯,将管坯放置在下半模上,并闭合上、下半模,左右冲头延伸至管坯的两个端口中形成密闭的空腔,同时向管坯内注入液体。
2. 增大管坯内部液体压力,高压液体均匀作用于模腔,左右冲头固定,利用液体压力和模腔的约束形成初波。
3. 在初波成形完成后,施加轴向压力使模具进给,直至贴合,将初波挤进模腔,之后进一步增大管坯内部液体压力,使得管壁与模腔贴合并固定波形。
4. 成形完成后先卸内压力,再卸载轴向推力,分开上下模具,冲头退出,取出波纹管管件。
按照管坯上波纹成形的顺序是否连贯,波纹管液压成形技术可以分为整体式成形和连续式成形。
其中整体成形是管坯在模具中加载一次,就可以成形管件上所有的波纹,而连续成形是指每次成形一个波纹,依次成形管坯上设计的所有波纹。
请注意,具体的工艺参数和操作细节可能会因波纹管的材料、尺寸和设计要求等因素而有所不同。
因此,在实际生产过程中,需要根据具体情况进行调整和优化。
机械产品介绍
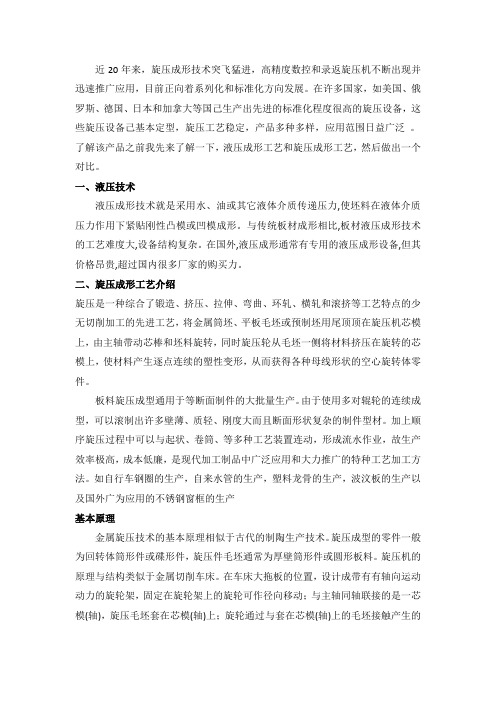
近20年来,旋压成形技术突飞猛进,高精度数控和录返旋压机不断出现并迅速推广应用,目前正向着系列化和标准化方向发展。
在许多国家,如美国、俄罗斯、德国、日本和加拿大等国己生产出先进的标准化程度很高的旋压设备,这些旋压设备己基本定型,旋压工艺稳定,产品多种多样,应用范围日益广泛。
了解该产品之前我先来了解一下,液压成形工艺和旋压成形工艺,然后做出一个对比。
一、液压技术液压成形技术就是采用水、油或其它液体介质传递压力,使坯料在液体介质压力作用下紧贴刚性凸模或凹模成形。
与传统板材成形相比,板材液压成形技术的工艺难度大,设备结构复杂。
在国外,液压成形通常有专用的液压成形设备,但其价格昂贵,超过国内很多厂家的购买力。
二、旋压成形工艺介绍旋压是一种综合了锻造、挤压、拉伸、弯曲、环轧、横轧和滚挤等工艺特点的少无切削加工的先进工艺,将金属筒坯、平板毛坯或预制坯用尾顶顶在旋压机芯模上,由主轴带动芯棒和坯料旋转,同时旋压轮从毛坯一侧将材料挤压在旋转的芯模上,使材料产生逐点连续的塑性变形,从而获得各种母线形状的空心旋转体零件。
板料旋压成型通用于等断面制件的大批量生产。
由于使用多对辊轮的连续成型,可以滚制出许多壁薄、质轻、刚度大而且断面形状复杂的制件型材。
加上顺序旋压过程中可以与起状、卷筒、等多种工艺装置连动,形成流水作业,故生产效率极高,成本低廉,是现代加工制品中广泛应用和大力推广的特种工艺加工方法。
如自行车钢圈的生产,自来水管的生产,塑料龙骨的生产,波汶板的生产以及国外广为应用的不锈钢窗框的生产基本原理金属旋压技术的基本原理相似于古代的制陶生产技术。
旋压成型的零件一般为回转体筒形件或碟形件,旋压件毛坯通常为厚壁筒形件或圆形板料。
旋压机的原理与结构类似于金属切削车床。
在车床大拖板的位置,设计成带有有轴向运动动力的旋轮架,固定在旋轮架上的旋轮可作径向移动;与主轴同轴联接的是一芯模(轴),旋压毛坯套在芯模(轴)上;旋轮通过与套在芯模(轴)上的毛坯接触产生的摩擦力反向被动旋转;与此同时,旋轮架在轴向大推力油缸的作用下,作轴向运动。
液压成形工艺

优点:
原始管坯为低碳钢,管坯的外径 为69. 9mm ,厚度为2. 0mm 工艺过程包括弯曲、液力成形、 冲裁和切边等 左右零件同时用液力成形的方法 生产,然后在下道工序中切开
一、基本情况--成形原理
管件液压成形原理 1 2
合模
充填介质
3
4
液压胀形 轴向进给
脱模
一、基本情况--工艺流程
光管
分管
弯曲
切割
液压胀型
预成形
一、基本情况--主要设备
生产线主要设备:
• • • • • • • • •
CNC弯管机 预成形机及模具 润滑系统 液压成形机及模具 零件端面切割、孔加工及检测 清洗和烘干系统 输送单元 主控系统 测量装置
通用汽车的纵梁
原始管件外径为152. 4mm , 壁厚为2. 0mm , 长度为4876. 8mm 过去采用的方法是采用14 个冲压件焊接或铆接在一起而成 的。现采用液力成形件降低了造价,减轻了重量,并且空间结 构尺寸愈加紧凑
资料来源:管件内高压成型及其在汽车工业中的应用现状
二、应用领域
汽车车身框架
二、应用领域
车身 仪表盘支架 散热器支架 座椅架 车顶侧围横梁 车顶纵梁 底盘 发动机支架 梯形臂 副车架 前后桥 转向系 控制臂 转向柱 从动连杆 其它 排气管 凸轮轴 曲轴
二、应用领域
副车架
此件所采用管件外径为69. 9mm ,壁厚为2. 5mm 传统冲压焊接工艺成形需6 个零件,而液压成形 仅需要一个零件,重量节省了34 %
液压成形
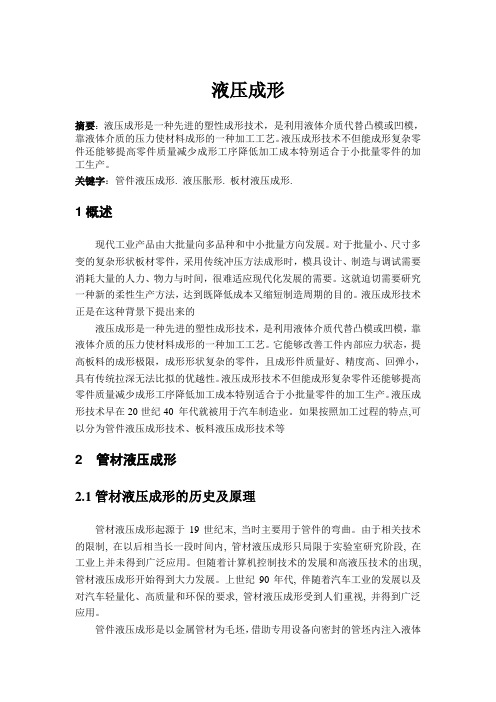
液压成形摘要:液压成形是一种先进的塑性成形技术,是利用液体介质代替凸模或凹模,靠液体介质的压力使材料成形的一种加工工艺。
液压成形技术不但能成形复杂零件还能够提高零件质量减少成形工序降低加工成本特别适合于小批量零件的加工生产。
关键字:管件液压成形. 液压胀形. 板材液压成形.1概述现代工业产品由大批量向多品种和中小批量方向发展。
对于批量小、尺寸多变的复杂形状板材零件,采用传统冲压方法成形时,模具设计、制造与调试需要消耗大量的人力、物力与时间,很难适应现代化发展的需要。
这就迫切需要研究一种新的柔性生产方法,达到既降低成本又缩短制造周期的目的。
液压成形技术正是在这种背景下提出来的液压成形是一种先进的塑性成形技术,是利用液体介质代替凸模或凹模,靠液体介质的压力使材料成形的一种加工工艺。
它能够改善工件内部应力状态,提高板料的成形极限,成形形状复杂的零件,且成形件质量好、精度高、回弹小,具有传统拉深无法比拟的优越性。
液压成形技术不但能成形复杂零件还能够提高零件质量减少成形工序降低加工成本特别适合于小批量零件的加工生产。
液压成形技术早在20世纪40 年代就被用于汽车制造业。
如果按照加工过程的特点,可以分为管件液压成形技术、板料液压成形技术等2 管材液压成形2.1管材液压成形的历史及原理管材液压成形起源于19世纪末, 当时主要用于管件的弯曲。
由于相关技术的限制, 在以后相当长一段时间内, 管材液压成形只局限于实验室研究阶段, 在工业上并未得到广泛应用。
但随着计算机控制技术的发展和高液压技术的出现,管材液压成形开始得到大力发展。
上世纪90年代, 伴随着汽车工业的发展以及对汽车轻量化、高质量和环保的要求, 管材液压成形受到人们重视, 并得到广泛应用。
管件液压成形是以金属管材为毛坯,借助专用设备向密封的管坯内注入液体介质,使其产生高压,同时还在管坯的两端施加轴向推力,进行补料,在两种外力的作用下,管坯材料塑性变形,并最终与模具型腔内壁贴合,得到形状与精度均符合技术要求的中空零件液压成形原理如图1 所示图1 管件液压成形原理示意图当零件轴线不是直线模腔分模面处截面小于管坯截面时,需进行弯管冲压等预工艺,以便管坯能顺利置入模腔中,如有必要,在液压成形之前还需进行退火处理2.2管材液压成形优点:与传统的冲压焊接工艺相比,管件液压成形工艺具有以下优点:(1 ) 减轻零件质量,节约材料; (2 ) 提高零件的强度和刚度,特别是疲劳强度; ( 3) 减少零件数量节约模具成本;(4) 零件整体成形,可减少后续机械加工和组装焊接量,简化生产流程,提高生产效率; (5) 提高加工精度,减少装配误差积累,可提高产品质量; (6)降低生产成本; (7) 结构形状设计更趋灵活优化。
超高压管材液压成形控制系统的研制

21 0 1年 6 月
机 械 工 程 与 自 动 化
M ECHANI CAL ENGI NEERI NG & AUTOMAT1 0N
NO 3 .
Jn u.
文章 编 号 :6 2 6 1 ( 0 1 0 — 0 0 0 17 —4 3 2 1 )3 09 . 3
高达 10 0MP ) 使金 属管坯 变 形成 为具 有 三维 形状 0 a 零 件 的现 代塑 性加工 技术 ,属 于液力成 形的 范畴。 国际上能够 提供 管材液 压成形 成套 技术 与设 备 的 制造 商 多 数 集 中在 欧 洲 ,其 中, 以 德 国 舒 勒 公 司 、 S S 司 和瑞 典 A & P 公 P T公 司为 主要 代表 … 。这些 公 司 的成套 液压成 形设 备价 格 昂贵 ,对 于一般 的实验研 究
计 。本 文 设 计 的 超 高 压 液 压 系统 主 要 用 于 管 材 液 压 成
水平 缸 的活塞 杆在 液压 油 的推动 下及 时进 给 ,直 至在 端 口处建 立新 的受 力平 衡 。两 端 冲头 的及 时进给 既保
( )整 形 阶段 c
图 l 液 压 成 形 原 理 图
作 者 简介 :孟 艳 敏 ( 9 7) 女 , 宁 鞍 山 人 , 16 - , 辽 工程 师 , 士 , 硕 主要 研 究 方 向 : 计算 机 控 制 与 自动 化 。
Байду номын сангаас
21 0 1年 第 3期
盂 艳 敏 , 等 :超 高 压 管 材 液 压 成 形 控 制 系 统 的研 制
向 的 载 荷 进 行 补 料 。 在 两 种 外 力 的共 同 作 用 下 使 管 材
讲一讲将板材“玩弄”于模具之中的液压成形技术
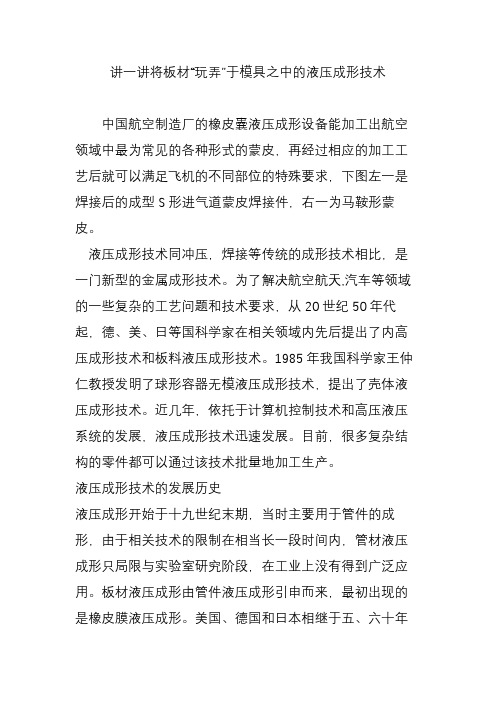
讲一讲将板材“玩弄”于模具之中的液压成形技术中国航空制造厂的橡皮囊液压成形设备能加工出航空领域中最为常见的各种形式的蒙皮,再经过相应的加工工艺后就可以满足飞机的不同部位的特殊要求,下图左一是焊接后的成型S形进气道蒙皮焊接件,右一为马鞍形蒙皮。
液压成形技术同冲压,焊接等传统的成形技术相比,是一门新型的金属成形技术。
为了解决航空航天,汽车等领域的一些复杂的工艺问题和技术要求,从20世纪50年代起,德、美、日等国科学家在相关领域内先后提出了内高压成形技术和板料液压成形技术。
1985年我国科学家王仲仁教授发明了球形容器无模液压成形技术,提出了壳体液压成形技术。
近几年,依托于计算机控制技术和高压液压系统的发展,液压成形技术迅速发展。
目前,很多复杂结构的零件都可以通过该技术批量地加工生产。
液压成形技术的发展历史液压成形开始于十九世纪末期,当时主要用于管件的成形,由于相关技术的限制在相当长一段时间内,管材液压成形只局限与实验室研究阶段,在工业上没有得到广泛应用。
板材液压成形由管件液压成形引申而来,最初出现的是橡皮膜液压成形。
美国、德国和日本相继于五、六十年代开发出了橡皮囊液压成形技术。
日本学者保日春男首先对此进行了改进,开发出了对向液压拉深技术。
随后欧、没等国家也相继开展这方面的工艺研究及设备的开发工作。
1967年,德国SMG公司提出液压机械拉深技术。
板材液压成形技术在九十年代后得到人们的重视和大力研究。
九十年代后,制造业迅猛发展,零件的形状日趋复杂,加之有大量采用铝、镁等质量较轻、但塑性较差的新材料,使得人们将注意力转向了板材液压成形技术。
到了九十年代后期,德国有关学者提出了一种板材成形新工艺--板材成对液压成形。
相对于国外来说,国内对于液压成形的研究较晚。
上世纪九十年代后,国内众多高校开始对液压成形进行研究,例如哈尔滨工业大学、燕山大学、华南理工大学、上海交通大学等分别对液压成形进行了理论分析和实验研究,总结了很多液压成形的数据和经验,但是对板材成对液压成形的研究相对较少,处于最初的探索阶段。
液压成形原理

液压成形原理
嘿,朋友!今天咱就来好好唠唠液压成形原理!
你想想看啊,液压成形就像是一场力量与智慧的舞蹈。
比如说,我们要把一块金属板材变成一个特定形状的部件,这就好像是要给这块金属施魔法一样!液压系统就像一个大力士,它能产生巨大的压力,推动着金属板材按照我们想要的样子变形。
就好比你要做一个超级酷的飞机模型,液压成形就是那个能帮你把一片片零件塑造成完美形状的神奇工具。
你知道吗?在这个过程中,液体就像是一群听话的小士兵,听从液压系统这个指挥官的命令。
当压力施加到液体上时,它们就齐心协力地去推动金属板材。
这多神奇啊!如果没有液压成形,那我们生活中的好多东西都没法制造出来呢!
再比如说汽车的零部件吧,那些复杂的形状,可不就是靠液压成形弄出来的嘛!它可比我们手工敲敲打打厉害多啦!
哎呀呀,我跟你说,液压成形的应用可太广泛了!从航空航天到日常生活用品,到处都有它的身影。
它不就是那个默默奉献,却让我们的生活变得更美好的幕后英雄吗?
我觉得啊,液压成形真的是超级厉害的技术,它让我们能制造出各种各样复杂又精美的东西,丰富了我们的生活!真的值得我们好好去了解和研究它呀!。
小型桥壳液压胀形初始变形条件分析及成形试验

小型桥壳液压胀形初始变形条件分析及成形试验王连东1㊀徐永生1㊀陈旭静1㊀吴㊀娜1,21.燕山大学,秦皇岛,066004㊀㊀2.唐山学院,唐山,063000摘要:介绍了小型汽车桥壳的液压胀形工艺,提出了初始胀形内压的表达式,预测了初始胀形内压与轴向推力的匹配关系(即经向应力比的大小)对预胀形时各部分变形顺序的影响.在普通液压机上进行了两种加载路径下的液压胀形试验,在初始经向应力比小于零并保持恒内压的条件下,预胀形管坯先变形成两侧高㊁中部低的双鼓形,经增压后将中部胀起;在初始经向应力比大于零且内压恒定的条件下,预胀形管坯中部沿轴向胀裂;两种加载路径下,管坯扁锥体凸起与胀形区之间均产生了明显内凹缺陷.理论分析与试验结果均表明,初始变形条件对小型桥壳的预胀形有重要影响.关键词:汽车桥壳;液压胀形;初始胀形内压;经向应力比;预胀形管坯中图分类号:T G 316㊀㊀㊀㊀㊀㊀D O I :10.3969/j.i s s n .1004 132X.2016.03.021A n a l y s e s o f I n i t i a l D e f o r m a t i o nC o n d i t i o n s f o rL i gh t H y d r o f o r m i n g A x l eH o u s i n g a n dF o r m i n g E x pe r i m e n t s W a n g L i a n d o n g 1㊀X uY o n g s h e n g 1㊀C h e nX u j i n g 1㊀W uN a 1,21.Y a n s h a nU n i v e r s i t y ,Q i n h u a n g d a o ,H e b e i ,066004㊀㊀2.T a n g s h a nC o l l e g e ,T a n gs h a n ,H e b e i ,063000A b s t r a c t :T h e h y d r o f o r m i n g t e c h n o l o g y o f l i g h t a x l e h o u s i n g wa s i n t r o d u c e d .T h e f o r m u l a o f i n i t i a l i n t e r n a l pr e s s u r ew a sd e d u c e d ,a n dt h e i n f l u e n c e so f t h er e l a t i o no f t h e i n t e r n a l p r e s s u r ea n da x i a l t h r u s t (a x i a l s t r e s s r a t i o )i n t h e p r e b u l g i n gp r o c e s so nt h ed e f o r m a t i o ns e qu e n c ew a s p r e d i c t e d .T h e h y d r o f o r m i n g e x p e r i m e n t sw e r e d o n e o n g e n e r a l h y d r a u l i cm a c h i n e u n d e r t w o d i f f e r e n t l o a d p a t h s .U n Gd e r t h ef i r s tl o a d p a t h ,t h ei n i t i a la x i a ls t r e s sr a t i o w a sn e ga t i v ea n dt h e p r e s s u r e w a sc o n s t a n t t h r o u g h o u t t h e f e e d i n gp r o c e s s ,t h e p r eb u l g i n g t u b ew a s f i r s td e f o r m e d t oad o u b l e d r u mt y pew i t h t h e d i a m e t e r o f t w o s i d e s l a r g e r t h a n t h e c e n t r a l ,a n d t h e c e n t r a l p a r tw a s f i n a l l y b u l g e db y i n c r e a s i n gt h e i n t e r n a l p r e s s u r e .U n d e r t h es e c o n dl o a d p a t h ,t h e i n i t i a l a x i a l s t r e s sr a t i o w a s p o s i t i v ea n dt h ep r e s s u r ew a s c o n s t a n t t h r o u g h o u t t h e f e e d i n gp r o c e s s ,t h ec e n t r a lo f t h et u b ec r a c k e da x i a l l y.T h e c o mm o n c o n c a v e d e f e c t s o f t h e s a m p l e so f t w o l o a d p a t h sw e r eo b s e r v e da t t h e t r a n s i t i o nr e gi o nb e Gt w e e n f l a t c o n e a n db u l g i n g a r e a ,a n d i tw i l l n o t d i s a p p e a r a f t e r t h e f i n a l b u l g i n g.B o t ho f t h e t h e o r e t i Gc a l a n a l y s e s a n d e x p e r i m e n t s d e m o n s t r a t e t h a t t h e i n i t i a l d e f o r m a t i o n c o n d i t i o n s h a v e a n i m p o r t a n t i n Gf l u e n c e o n t h e p r e b u l g i n gp r o c e s s o f l i g h t a x l eh o u s i n g.K e y wo r d s :a u t o m o b i l e a x l eh o u s i n g ;h y d r o f o r m i n g ;i n i t i a l p r e s s u r e ;a x i a l s t r e s s r a t i o ;p r e b u l g i n g t u b e收稿日期:20150116基金项目:河北省自然科学基金资助项目(E 2012203022)0㊀引言管材液压胀形是制造机械零部件的先进方法,已广泛应用于机械㊁电子㊁航空航天㊁交通运输等领域.近年来,国内外学者对管材液压胀形进行了较多的研究.K o c 等[1]从理论上得到了液压胀形时理想管材轴向屈曲㊁起皱和破裂的临界条件,给出了确定不同工艺条件下胀形内压㊁轴向力和轴向补料量的方法.M a n a b e 等[2]研究了材料的各向异性和硬化系数对液压胀形的影响,指出了应力比对壁厚分布和成形性能的影响.李洪洋等[3]进行了空心阶梯轴内高压成形试验,给出了初始内压的表达式,并进行了不同初始内压下的工艺试验.汽车桥壳为异型截面空心管类件,理论上可以用液压胀形方法制造.20世纪80年代,日本学者用液压胀形方法试制出微型汽车桥壳样件[4 5],取得了一些宝贵经验.21世纪初,国内一些学者提出了汽车桥壳半滑动式液压胀形工艺,给出了极限胀形系数的数学表达式,并研究了内压与轴向力的匹配问题[6 8].汽车桥壳形状复杂,两端小中部大,中部截面与两端截面的当量直径比大于3.0,周向扩张量大,轴向补料多,用液压胀形方法成形难度大.本文针对某小型桥壳的液压胀形工艺,分析了初始胀形内压的大小㊁初始胀形内压与轴向推力的匹配关系(即经向应力比的大小)㊁胀形过渡区的形状等初始胀形条件对桥壳预胀形的影响,预测了胀形区各部分的变形趋势以及可能出现的内凹㊁胀裂等缺陷,并在普通液压机上进行了工艺试验.1㊀小型汽车桥壳液压胀形工艺本文研究的小型汽车桥壳总长1050mm ,中893 Copyright ©博看网. All Rights Reserved.间截面当量直径为212mm,两端直臂圆管部分外径为67mm.受普通液压机开间的限制,将桥壳样件总长度缩减至476mm.无缝钢圆管液压胀形工艺包括端部缩径㊁预胀形和终胀形三个阶段,工艺过程如图1所示.20无缝钢管坯初始直径为102mm㊁壁厚为5 5mm㊁长度为558mm,两端部缩径后直径减至67mm,然后进行预胀形,包括锥形区的挤压变形和中间部分的液压胀形两个过程.液压胀形前,胀形模具轴向推进时先将缩径管坯的圆锥区挤压成宽度相同而高度不同的扁锥体,如图1b㊁图1c 所示.预胀形时将中部液压胀形成中间略低于两侧的马鞍形(图1d),中间截面的胀形系数k1=1 55.预胀形管坯退火后,再进行终胀形得到桥壳样件,如图1e所示.(a)缩径后管坯(b)挤压后管坯垂直纵向视图(c)挤压后管坯水平纵向视图(d)预胀形管坯(e)终胀形图1㊀桥壳液压胀形工艺简图2㊀预胀形管坯初始变形条件分析缩径管坯圆锥区在预胀形前被挤压成扁锥体,如图2所示.垂直纵截面上,扁锥体与轴线倾斜角为α,扁锥体与中部预胀形部分过渡处形成高于初始管坯的凸起,最高点A处的纬向曲率半径为RθA㊁经向曲率半径为R1,凸起部位与预胀形区过渡处B u点处的内凹圆角半径为R2.水平截面上,扁锥体与轴线倾斜角为β,扁锥体与中部预胀形部分过渡处B d点处的外凸圆角半径为R3.(a)管坯垂直纵截面(b)管坯水平纵截面图2㊀缩径管坯预胀形受力分析2.1㊀初始胀形内压的确定对挤压后的缩径管坯进行预胀形:初始内压为p,在管坯两端施加轴向推力F a1㊁F a2,在扁锥体上施加轴向推力F b1㊁F b2,如图2所示.对管坯施加内压和外力后,胀形区各质点处于三向应力状态:纬向应力σθ㊁经向应力σρ和径向应力σr.假设沿管坯壁厚方向,纬向应力σθ㊁经向应力σρ均布,则两者与内压p之间应满足以下平衡方程:pt0-σθRθ-σρRρ=0(1)式中,Rθ为质点处管坯中间层的纬向曲率半径,近似等于外层的纬向曲率半径;Rρ为质点处管坯中间层的经向曲率半径,近似等于外层的经向曲率半径,对于外凸曲线, Rρ为正值,对于内凹曲线,Rρ为负值;t0为质点处管坯的壁厚.经向应力由模具施加于管坯的轴向推力和液体内压共同作用产生,其大小由下式确定:σρ=-F a+F b-πr20pπ(2r0+t0)t0(2)式中,F a为作用于管坯端部的模具推力,即F a1与F a2之和;F b为作用于管坯锥面的模具推力,即F b1与F b2之和; r0为管坯预胀形区内半径.胀形管坯外表面上质点径向应力σr为零,处于平面应力状态,变形时塑性条件按M i s e s屈服准则,即应满足:σ2θ-σθσρ+σ2ρ=σ2s(3)定义经向应力σρ与纬向应力σθ的比值为经993Copyright©博看网. All Rights Reserved.向应力比λ,即σρ=λσθ(4)将式(4)代入式(3)得到σθ=σs1-λ+λ2(5)将式(4)㊁式(5)代入式(1),得到初始胀形的内压p :p =(t 0R θ+λt 0R ρ)σs 1-λ+λ2(6)水平纵截面上,管坯外壁中点C d 发生初始变形所需的内压p C d 为p C d =t 0R θσs1-λd +λd 2(7)扁锥体过渡处B d 点发生变形所需的内压p B d 为p B d =(t 0R θ+λdt 0R 3)σs 1-λd +λ2d(8)管坯垂直纵截面上,管坯中点C u 发生变形所需内压p C u 为p C u =t 0R θσs1-λu +λu(9)扁锥体过渡凹圆角处B u 点发生变形所需的内压p B u 为p B u =(t 0R θ+λut 0R 2)σs 1-λu +λ2u (10)扁锥体凸起点A 处发生变形所需内压p A 为p A =(t 0R θA +λu t 0R 1)σs 1-λu +λ2u(11)2.2㊀初始经向应力比影响分析由于管坯各处变形所需的内压不同,在液压胀形过程中,各处达到塑性屈服条件的顺序也不同,导致变形有先后.比较式(7)㊁式(8)可知:在管坯水平纵截面上,当经向应力比λd =0(即经向应力σρ=0)时,中间C d 点与两侧扁锥体过渡处B d 点变形所需的内压相同,即中部与两侧将同时胀形;当经向应力比λd <0(即σρ为压应力)时,p B d <p C d ,两侧过渡处B d 点先于中间点C d 发生胀形,管坯将呈两侧高㊁中部低的双鼓形;当经向应力比λd >0(即σρ为拉应力)时,p B d >p C d ,中间点C d 先于两侧过渡处B d 点发生变形,管坯将呈中部高于两侧的单鼓形,管坯中部轴向补料效果差,容易胀裂.比较式(8)㊁式(10)可知:当经向应力比为负值时,垂直纵截面上扁锥体过渡处B u 点变形所需的内压p B u 大于水平纵截面上的过渡点B d 所需内压p B d ,即B d 点先于B u 点发生变形;当经向应力比等于零时,B d 点与B u 点变形所需的内压理论上相同,但由于挤压变形后垂直纵截面上B u 点处存在内凹圆角,B u 点的变形受到邻近凸起A 点的影响而不易发生,即B u 点仍将迟于B d 点发生胀形.比较式(7)㊁式(9)可知:在经向应力比相同时,水平截面上的中间点C d 与垂直截面上的中间点C u 将同时起胀.扁锥体的形状使得水平截面上的轴向力F b 2的作用效果好于垂直截面上的轴向力F b 1的作用效果,即λd <λu ,所以C d 点将先于C u 点发生胀形.比较式(9)~式(11)可知:在管坯垂直纵截面上,当经向应力比等于零时,中间点C u ㊁两侧过渡凹圆角处B u 点与扁锥体的凸起点A 将同时达到塑性条件;当经向应力比小于零时,扁锥体的凸起点A 最先达到塑性条件,其次是中间点C u 达到塑性条件,而两侧过渡凹圆角处的B u 点最后达到塑性条件,该处容易形成凹陷.3㊀小型桥壳液压胀形试验3.1㊀预胀形模具根据图1所示的桥壳液压胀形工艺,选取20无缝钢管,屈服极限为350M P a ,强度极限为410M P a ,单向拉伸的均匀延伸率为25%,弹性模量为210G P a ,泊松比为0 28.在普通液压机上依次进行四次缩径,缩径后管坯如图3所示.图3㊀缩径后管坯缩径后管坯在普通液压机上采用半滑动式液压胀形方式[6]进行预胀形,管坯轴向进给85mm ,预胀形模具结构如图4所示.1.左导板㊀2.下模分块3㊀3.柱销㊀4.下模分块2㊀5.导柱6.下模分块1㊀7.控制模㊀8.管坯㊀9.上模分块110.螺钉㊀11.上模分块2㊀12.密封镶块㊀13.上模分块314.密封压头㊀15.管接头㊀16.传感器㊀17.导柱18.限位块㊀19.右导板㊀20.螺钉㊀21.放液孔图4㊀半滑动式预胀形模具004 Copyright ©博看网. All Rights Reserved.3.2㊀初始胀形内压及加载路径假想管坯中部与两侧同时发生塑性变形,即经向应力比等于零时,按式(7)或式(9)计算出的胀形内压p 0为p 0=t 0σs R θ1-λ+λ2=37 7(M P a )当初始内压小于p 0时,胀形两侧部分将先于中部发生变形;当初始内压大于p 0时,胀形部分中部将先于两侧发生变形.液压胀形时管坯内压与轴向进给量之间的关系即加载路径对成形影响至关重要,为比较初始胀形条件对变形的影响,选择以下两种加载路径,如图5所示.图5㊀预胀形试验加载路径(1)加载路径Ⅰ.初始胀形内压p 小于p 0,内压选为37M P a ,则初始经向应力比小于零.管坯轴向推进85mm 过程中保持内压37M P a 不变,合模后将内压升至60M P a 校形.(2)加载路径Ⅱ.初始胀形内压p 大于p 0,内压选为42M P a ,则初始经向应力比大于零.管坯轴向推进85mm 过程中保持内压42M P a 不变,合模后将内压升至60M P a 校形.3.3㊀预胀形试验(1)按加载路径Ⅰ试验.管坯合模时先变成图6a 所示的两侧大中部小的双鼓形:两侧最高点直径为157mm ,中间部分直径仅为123mm ,表明管坯两侧先于中部发生变形;水平纵截面方向的变形区域较垂直方向上的变形区域大,表明管坯两侧水平纵截面方向较垂直方向容易变形;管坯垂直纵截面方向上,扁锥体与胀形区之间产生了明显内凹,表明挤压管坯纵截面上扁锥体凸起与预胀形区之间的内凹圆角处不易变形.模具合模后将双鼓形的管坯内部液体压力增至60M P a 进行校形,得到成形良好的预胀形管坯,如图6b 所示.校形后管坯垂直纵截面方向上扁锥体与胀形区之间的内凹仍然存在.如图7a 所示,选择预胀形管坯,沿水平纵截面㊁垂直纵截面及圆周方向切去1/8部分,在剖面上选取测量点测量壁厚:沿圆周方向从垂直截面至水平截面每间隔4 5ʎ采集一点,共采集20点;㊀(a)增压前样件(b)增压后样件图6㊀路径I 预胀形试验样件在垂直纵截面上从中间向外侧每间隔7 5mm 采集一点,共采集20点.由周向截面上的壁厚变化曲线(图7b )可知:从垂直截面至水平截面,管坯壁厚逐渐增大,最小壁厚为4 2mm ,相对初始壁厚减薄率为23 64%,最大壁厚为4 96mm ,减薄率为9 82%.在垂直纵截面上,胀形区的壁厚较均匀,由胀形区向外侧壁厚由4 2mm 逐渐增加到6 09mm ,如图7c 所示.(a)预胀形剖开试件(b)中间截面周向壁厚(c)纵向截面轴向壁厚图7㊀预胀形管坯壁厚分布(2)按加载路径Ⅱ试验.管坯中部及两侧均胀起,水平截面方向上中部的变形较两侧大,管坯中部沿纵向胀裂,裂口处的壁厚为3 9mm ,减薄率为29 09%.由变形结果可推断:中间部分先于两侧发生变形,在胀形过程中补料效果差导致壁厚减薄率超过了文献[8]给出的胀裂极限而出现胀裂.由图8所示的试件可看出,管坯垂直纵截面方向上扁锥体与胀形区之间仍然存在明显的内凹.图8㊀路径Ⅱ预胀形试验样件104 Copyright ©博看网. All Rights Reserved.(3)终胀形试验.将加载路径Ⅰ得到的预胀形管坯退火后进行终胀形,得到了液压胀形桥壳样件,如图9所示.由样件的外观可以看到,预胀形管坯垂直纵截面方向上扁锥体与胀形区之间的内凹在终胀形过程中没有消除,仍残留在样件中.图9㊀终胀形样件4㊀结论(1)给出了预胀形管坯各部分变形所需初始内压的表达式.初始内压正比于管材的屈服强度和管坯的壁厚,随管坯的纬向曲率半径㊁经向曲率半径的增大而减小,随经向应力比的减小而减小.(2)分析了初始经向应力比λ对预胀形管坯变形的影响:当λ=0时,管坯两侧与中部同时发生变形;当λ>0时,中部先于两侧发生变形,管坯将呈中部高于两侧的单鼓形,中部轴向补料效果差,容易胀裂;当λ<0时,水平截面方向上两侧先于中部发生变形,垂直截面方向上扁锥体凸起先于中部发生变形,两侧过渡凹圆角处不易变形,管坯将呈两侧高㊁中部低的双鼓形,而且垂直截面方向过渡内凹圆角处可能形成内凹缺陷.(3)针对小型桥壳进行了两种加载路径下的液压胀形试验,结果表明:初始经向应力比小于零并保持恒内压胀形时,预胀形管坯先变形成两侧高㊁中部低的双鼓形,经增压后将中部胀起;初始经向应力比大于零并保持恒内压胀形时,预胀形管坯中部沿轴向胀裂;两种加载路径下,管坯垂直纵截面方向上扁锥体与胀形区之间均产生了明显内凹,加载路径Ⅰ下的预胀形管坯退火后进行终胀形时内凹缺陷仍没有消除.(4)缩径后管坯先挤扁圆锥区再胀形中部时,垂直截面上扁锥体与胀形区之间产生的初始凸起限制了其临近处的变形,最终导致样件存在内凹.后续拟先将缩径管坯液压胀形为一定形状的预成形管坯,再进行整体成形得到无内凹的桥壳样件.参考文献:[1]㊀K o c M ,A l t a nT.P r e d i c t i o no fF o r m i n g Li m i t sa n d P a r a m e t e r s i n t h eT u b eH y d r o f o r m i n g Pr o c e s s [J ].I n t e r n a t i o n a l J o u r n a l o fM a c h i n eT o o l s&M a n u f a c Gt u r e ,2002,42(1):123 138.[2]㊀M a n a b eKI ,A m i n o M.E f f e c t so fP r o c e s sP a r a m e Gt e r s a n dM a t e r i a l P r o p e r t i e s o nD e f o r m a t i o nP r o c e s s i nT u b eH y d r o f o r m i n g [J ].J o u r n a l o fM a t e r i a l sP r o Gc e s s i n g T e c h n o l o g y ,2002,123(2):285 291.[3]㊀李洪洋,苑世剑,王小松,等.初始内压对内高压成形阶梯轴影响的实验研究[J ].材料科学与工艺,2005,13(4):143 145.L iH o n g y a n g ,Y u a nS h i j i a n ,W a n g X i a o s o n g ,e ta l .E x p e r i m e n t a l I n v e s t i ga t i o no fI n i t i a l I n t e r n a lP r e s Gs u r e o n H y d r o f o r m i n g M u l t i s t e p pe dS h af t [J ].M a Gt e r i a l S c i e n c e a n dT e c h n o l og y ,2005,13(4):143 145.[4]㊀U e d aT.D i f f e r e n t i a lG e a rC a s t i n g fo rA u t o m o b i l e s b y L i q u i dB u l g eF o r m i n g Pr o c e s s -P a r t 1[J ].S h e e t M e t a l I n d u s t r i e s ,1983,60(3):181 185.[5]㊀U e d aT.D i f f e r e n t i a lG e a rC a s t i n g fo rA u t o m o b i l e s b y L i q u i dB u l g eF o r m i n g Pr o c e s s -P a r t 2[J ].S h e e t M e t a l I n d u s t r i e s ,1983,60(4):48 56.[6]㊀王连东,陈国强,杨东峰,等.普通液压机半滑动式液压胀形汽车桥壳的工艺研究[J ].中国机械工程,2011,22(18):2249 2253.W a n g L i a n d o n g ,C h e n G u o q i a n g ,Y a n g D o n g f e n g,e t a l .R e s e a r c ho fH a l f s l i d i n g H y d r o f o r m i n g A u t o Gm o b i l e H o u s i n g s w i t haC o mm o n P r e s s [J ].C h i n a M e c h a n i c a l E n g i n e e r i n g,2011,22(18):2249 2253.[7]㊀陈国强,王连东,韩晓亮,等.半滑动式液压胀形汽车桥壳的模具设计及成形[J ].塑性工程学报,2011,18(3):61 65.C h e n G u o q i a n g ,W a n g L i a n d o n g ,H a n X i a o l i a n g,e t a l .T h eD i eD e s i g na n d D e f o r m a t i o n A n a l y s i so f H a l f s l i d i n g H y d r o f o r m i n g B u l g i n g ofA u t o m o b i l e A x l e H o u s i n g s [J ].J o u r n a lo fP l a s t i c i t y E n g i n e e r Gi n g,2011,18(3):61 65.[8]㊀王连东,程文冬,梁晨,等.汽车桥壳液压胀形极限成形系数及胀裂判据[J ].机械工程学报,2007,43(5):210 213.W a n g L i a n d o n g ,C h e n g W e n d o n g ,L i a n g Ch e n ,e t a l .F o r m i n g L i m i tC o e f f i c i e n t a n dB u r s t i n g C r i t e r i o no f H y d r o b u l g i n g A u t o m o b i l eA x l eH o u s i n gs [J ].C h i Gn e s eJ o u r n a lo f M e c h a n i c a l E n g i n e e r i n g ,2007,43(5):210 213.(编辑㊀陈㊀勇)作者简介:王连东,男,1967年生.燕山大学车辆与能源学院教授㊁博士研究生导师.主要研究方向为液压胀形工艺理论与技术㊁汽车零部件设计及制造.徐永生,男,1990年生.燕山大学车辆与能源学院硕士研究生.陈旭静,女,1988年生.燕山大学车辆与能源学院硕士研究生.吴㊀娜,女,1980年生.唐山学院机电工程系副教授,燕山大学车辆与能源学院博士研究生.204 Copyright ©博看网. All Rights Reserved.。
液压机的区别
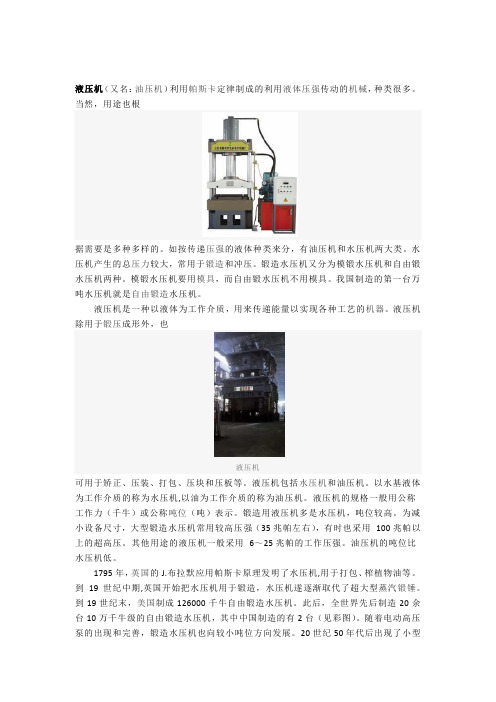
当然,用途也根除用于锻压成形外,也液压机的工作原理。
大、小柱塞的面积分别为S2、S1,柱塞上的作工作介质液压机所用的工作介质的作用不仅是传递压强,而且保证机器工作部件工作灵敏、可靠、寿命长和泄漏少。
液压机对工作介质的基本要求是:①有适宜的流动性和低的可压缩性,以提高传动的效率;②能防锈蚀;③有好的润滑性能;④易于密封;⑤性能稳定,长期工作而不变质。
液压机最初用水作为工作介质,以后改用在水中加入少量乳化油而成的乳化液,以增加润滑性和减少锈蚀。
19世纪后期出现了以矿物油为工作介质的油压机。
油有良好的润滑性、防腐蚀性和适度的粘性,有利于改善液压机的性能。
20世纪下半叶出现了新型的水基乳化液,其乳化形态是“油包水”,而不是原来的“水包油”。
“油包水”乳化液的外相为油,它的润滑性和防蚀性接近油,且含油量很少,不易燃烧。
但水基乳化液价格较贵,限制了它的推广。
一、驱动系统液压机的驱动系统主要有泵直接驱动和泵-蓄能器驱动两种型式。
泵直接驱动这种驱动按作用力的方向区分,液压机有立式和卧式两种。
多数液压机为立式,挤压用液组成的框架承受。
采用泵-蓄能器驱动的大、中型的自由锻水压机常采用三个工作缸,以得到三级工作力。
工作缸外还设有向上施加力的平衡缸和回程缸。
挤压金属成型、薄板拉伸以及横压、弯压、翻透、校正等工艺。
一、优势与传统的冲压工艺相比,液压成形工艺在减轻重量、减少零件数量和模具数量、提高刚度与强度、降低生产成本等方面具有明显的技术和经济优势,在工业领域尤其是汽车工业中得到了越来越多的应用。
在汽车工业及航空、航天等领域,减轻结构质量以节约运行中的能量是人们长期追求的目标,也是先进制造技术发展的趋势之一。
液压成形(hydroforming)就是为实现结构轻量化的一种先进制造技术。
液压成形也被称为“内高压成形”,它的基本原理是以管材作为坯料,在管材内部施加超高压液体同时,对管坯的两端施加轴向推力,进行补料。
在两种外力的共同作用下,管坯材料发生塑性变形,并最终与模具型腔内壁贴合,得到形状与精度均符合技术要求的中空零件。
管梁液压成形凹陷问题的

c) 型管
何 成,等:管梁液压成形凹陷问题的研究
第2期
图7减薄率
形压力200MPa,内腔面积0.132mm2,所需最大合模 压力2640"。
3横梁凹陷问题验证
3.1凹陷问题说明
横梁在液压成形调试过程中出现端头部位凹陷
严重。端头凹陷位置为搭接面,造成与其它件搭接困
难,影响产品美观,凹陷位置是产品定位面,故此处
量
工序与成形工序的集
成卩叫
近年来,液压成形作为实现汽车轻量化的重要
途径之一 是在汽车制
用,与
传统的冲压-拼焊制 工艺 ,液压成形
N液压成形能在
度刚度的
量, 车
一体 , 能
和
点量 高
性能。液压成形产品成本
低、柔性高、度高、量等
点尤其合汽
车和
的要,
用于汽
车工业和 工业。
,液压成形 的发展,也
使汽车
的 和制
形 梁,凹陷
在。合分析首先成形时在
端头位置件内部处于自状,处成形时
流动必然牵动端头,而端头处于自由状态,不受控
制,变形严重。其 成形时凹陷 形状
,
9 扭力梁横梁 陷
图10横梁预成形上模镶块
图11横梁预成形端部合格效果图
液压成形技术在横梁上的应用,基于有限元模
拟结果,横梁成形性良好,并对横梁
试
,经过模具设计与 造、液压压力的调,关键
液压成形主要是指依靠咼压液体作为传力介
质,代替刚性的凹模或凸模,使坯料在传力介质的压
力作用下贴合凸模或凹模成形的一种柔性加工工
艺。液压成形在管材、板材加工方面都能克服常规工
艺的不足,又具有制模简单、周期短、成本低而产品
矩形截面件开式液压成形变形规律及起皱行为

精 密 成 形 工 程第16卷 第5期 182JOURNAL OF NETSHAPE FORMING ENGINEERING 2024年5月收稿日期:2024-02-29 Received :2024-02-29基金项目:国家自然科学基金(52305402);山西省基础研究计划项目(202103021223070);海安太原理工大学先进制造与智能装备产业研究院开放研发项目(2023HA-TYUTKFYF038)Fund :National Natural Science Foundation of China (52305402); The Fundamental Research Program of Shanxi Province (202103021223070); Open Research Fund from the Hai'an & Taiyuan University of Technology Advanced Manufacturing and Intelligent Equipment Industrial Research Institute (2023HA-TYUTKFYF038)引文格式:冯浩, 韩聪, 江树勇. 矩形截面件开式液压成形变形规律及起皱行为[J]. 精密成形工程, 2024, 16(5): 182-192. FENG Hao, HAN Cong, JIANG Shuyong. Deformation and Wrinkling Behavior in Hydroforming of Square Overlapping Parts[J]. Journal of Netshape Forming Engineering, 2024, 16(5): 182-192. *通信作者(Corresponding author ) 矩形截面件开式液压成形变形规律及起皱行为冯浩1a,1b,2,韩聪2*,江树勇1c(1.太原理工大学 a.机械与运载工程学院 b.先进金属复合材料成形技术与装备教育部工程研究中心 c.材料科学与工程学院,太原 030024;2.哈尔滨工业大学 材料科学与工程学院,哈尔滨 150001) 摘要:目的 开式筒壳液压成形采用具有搭接结构的开式筒壳作为坯料,具有提高成形能力、改善壁厚分布、降低成形压力等优势。
液压成型技术

板材液压成型
板材液压成型是利用液体作为传力介质来传递载荷, 使板材成型到单侧模具上的一种板材成型方法。 根据液体介质取代凹模或凸模可将之进一步分为: 1.充液拉深(用液体介质代替凹模)。 2.液体凸模拉深(以液体介质作为凸模)。
充液拉深
热态充液拉深,将材料的温热性能与充液拉深的技术 优势结合起来,可使铝合金及镁合金等成型性能差的 轻体材料成型能力得到提高,促进其在航空航天领域 的应用。
液压成型技术的现状
管材液压成型 现代液压成型压力一般达到400MPa,有时可达到 1000MPa。超高压精度达到0.2-0.5MPa,位移精度 达到0.5MPa。,现在已广泛应用到汽车、航空、自 行车、管路等当中,其中汽车应用最为广泛。 包括: 1.底盘类零件:副车架、纵梁、后轴、保险杠 2.车体结构:座椅框、仪表盘支梁、顶梁等 3.发动机和驱动系统:排气管凸轮轴 4.转向和悬挂系统:控制臂、摆臂等
管材成型工艺
它的成型工艺大致可分为三个阶段:第一个
阶段,填充阶段,将管材放在下模内,然后 闭合上模,使管材内充满液体(并排除气 体),将管的两端用水平冲头压封;第二个 阶段,成型阶段对管内液体加压胀型的同时 两端的冲头按照设定加载曲线向内推进补料, 在内压和轴向补料的联合作用下使管材基本 贴近模具;第三个阶段,整型阶段,提高压 力使过度区圆角完全贴靠模具而成型为所需 的工件,这个阶段基本没有补料,从截面看 可以把管材变为矩型、梯型、椭圆型或其他 异型截面。
液压成型技术的发展趋势
随着液压成型技术的成熟和人们都减轻质量,降低成本的需求的提高,该技术 近十年来在各个领域得到广泛应用。 板材液压成型: 1.进一步提高成型极限和零件质量的成型新技术。 2.低塑性材料的拉深成型。 3.大型复杂型面零件成型 4.与普通拉深工艺复合,提高效率 壳体液压成型: 1. 选用轻质传力介质 2. 应用高能束焊接技术和自动化工艺焊接封闭壳体 3. 铝合金等轻质材料球壳液压成型 管材液压成型: 1.超高压成型 2.新成形工艺不断发展 3. 超高强度钢成型 4. 热态内压成型
液压成形技术
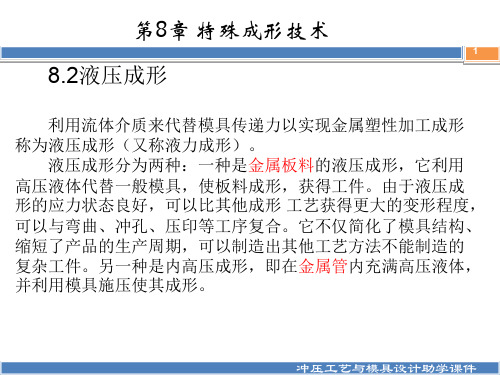
屈曲:当管材成形区长度过长,在成形初期还没有在管材 内建立起足够大的内压时,施加了过大的轴向力造成的。
皱纹:当轴向力过大时,工件在成形初期产生皱纹 。 皱纹可以分为二类,一类是后期加压整形无法展平,这类 皱纹称为死皱,它是一种缺陷。 另一类皱纹通过后期加压可 以展平,称为“有益皱纹”。这类皱纹不仅不是缺陷而且还可 作为一种预成形的手段,在成形初期将管材推出皱纹以补充材 料。但前提条件是后续整形压力能将皱纹展开。
有缘学习更多+谓ygd3076考证资料或关注桃报:奉献教育(店铺)
冲压工艺与模具设计助学课件
第8章 特殊成形技术
13
4.内高压成形设备 一条完整的内高压成形生产线主要由切管机、弯管机、预
成型压力机、内高压成形压力机等设备组成。其中最重要的设 备是内高压成形压力机, 它由合模压力机、高压源、水平缸、液 压泵站、水压系统和计算机控制系统等6部分组成, 其组成和工 作原理如图8-13和图8-14所示。
内高压成形工艺作为一种整体成形薄壁结构件的塑性加工方 法,最近几十年在汽车制造业、航空航天业及卫生洁具业中得到 了广泛的应用。
a)轿车副车架(有18个不同的截面形状和尺寸)
b) 排气歧管
图8-10典型汽车内高压成形零件
冲压工艺与模具设计助学课件
有缘学习更多+谓ygd3076考证资料或关注桃报:奉献教育(店铺)
根据受力和变形特点, 零件分为成形区和送料区2个区间。成 形区是管材发生塑性变形直径和形状发生变化的部分,送料区是 在模具内限制管材外径不变, 主要作用是向成形区补充材料。
冲压工艺与模具设计助学课件
第8章 特殊成形技术
10
液压成型机原理、结构与应用
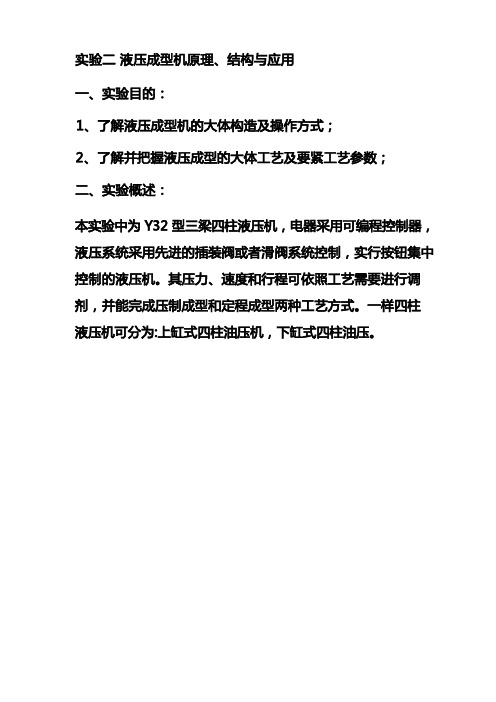
机械具有独立的动力机构和电气系统,采用按钮集中控制,可实现调整、手动及半自动三种工作方式:机械的工作压力、
1、用途
四柱液压机属于锻压机械中的一种,要紧作用确实是金属加工行业。产品普遍合用于:轻工、航空、船舶、冶金、仪表、电器、不锈钢制品、钢结构建造及装璜行业,也合用于可塑性材料的压制工艺,如粉末制品成型、塑料制品成型、冷(热)挤压金属成型、薄板拉伸和横压、弯压、翻透、校正等工艺。四柱液压机具有独立的动力机构和电器系统,采用按钮集中控制,可实现调整、手动及半自动三种操作方式。
图1液压成型机结构
四柱油压机是一种通过专用液压油做为工作介质,液体在密闭的容器中传递压力时是遵循帕斯卡定律。通过液压泵作为动力源,靠泵的作使劲使液压油通过液压管路进入油缸/活
塞,然后油缸/活塞里有几组相互配合的密封件,不同位置的密封都是不同的,但都起到密封的作用,使液压油不能泄露。将油压能转化为机械能油压传动是利用液体压力来传递动力和进行控制的一种传动方式。油压装置是由油压泵,油压缸,油压控制阀和油压辅助元件机。液压机的规格一样用公称工作力(千牛)或者公称吨位(吨)表示。锻造用液压机多是水压机,吨位较高。为减小设备尺寸,大型锻造水压机时常使用较高压强(35兆帕摆布),有时也采用100兆帕以上的超高压。其他用途的液压机一样采用6~25兆帕的工作压强。油压机的吨位比水压机低。
实验二液压成型机原理、造及操作方式;
2、了解并把握液压成型的大体工艺及要紧工艺参数;
二、实验概述:
本实验中为Y32型三梁四柱液压机,电器采用可编程控制器,液压系统采用先进的插装阀或者滑阀系统控制,实行按钮集中控制的液压机。其压力、速度和行程可依照工艺需要进行调剂,并能完成压制成型和定程成型两种工艺方式。一样四柱液压机可分为:上缸式四柱油压机,下缸式四柱油压。
双锥形管液压成形过程中破裂和起皱的力学条件

双锥形管液压成形过程中破裂和起皱的力学条件苑文婧;刘晓航;田浩彬【摘要】Firstly, the geometry condition and the stress condition of the bursting and wrinkles during the hydroforming of double-cone tube were given. Then the analytical results were compared with the FEM analysis and experiments results. The results show that the useful wrinkles must meet both the geometry condition and the stress condition. The geometry condition of useful wrinkles is that the area ofworkpiece in the local zoneat the end of axial feeding is close to the area of the corresponding part. The stress condition of useful wrinkles is that shape parameter G is not smaller than the radius R at the top of middle wrinkle. That means the increment of thickness strain det is positive and no thickness thinning will occur during the calibration. When the wrinkles didn't match geometry condition, the dead wrinkles and the bursting will take place. And whenthe wrinkles didn't match stress condition, the bursting at top of middle wrinkle will occur during the calibration.%针对双锥形管液压成形过程,分析了破裂和皱纹产生的几何及力学原因,并用数值模拟和工艺实验进行了验证。
液压成型技术综述
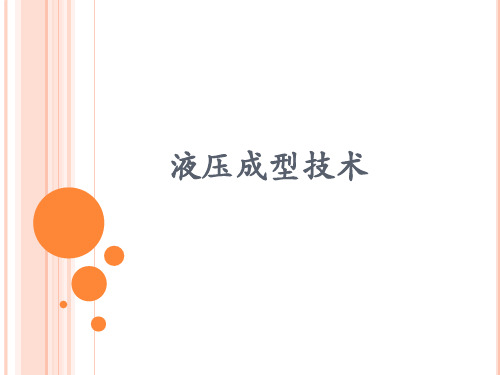
液压成型技术的发展趋势
随着液压成型技术的成熟和人们都减轻质量,降低成本的需求的提高,该技术 近十年来在各个领域得到广泛应用。 板材液压成型: 1.进一步提高成型极限和零件质量的成型新技术。 2.低塑性材料的拉深成型。 3.大型复杂型面零件成型 4.与普通拉深工艺复合,提高效率 壳体液压成型: 1. 选用轻质传力介质 2. 应用高能束焊接技术和自动化工艺焊接封闭壳体 3. 铝合金等轻质材料球壳液压成型 管材液压成型: 1.超高压成型 2.新成形工艺不断发展 3. 超高强度钢成型 4. 热态内压成型
以变径管为例
(a)
(b)
图3 变径管内高压成型技术工艺过程 (a)填充阶段;(b)成型阶段;(c)整型阶段。 (c)
管材液压成型特点
从工艺技术角度,管材液压成型与冲压焊接工艺相对 比的主要优点有: 1.减轻质量,节约材料。 ( 框、梁类 减轻20%-40%, 空心轴 可以减轻40%-50%) 2.减少零件和模具重量,降低模具费用。 3.可减少后续机械加工和组装焊接量,提高生产效率。 4.提高强度和刚度,尤其是疲劳强度。 5.材料利用率高。 (达到90%-95%) 6.降低生产成本。
管材成型工艺
它的成型工艺大致可分为三个阶段:第一个
阶段,填充阶段,将管材放在下模内,然后 闭合上模,使管材内充满液体(并排除气 体),将管的两端用水平冲头压封;第二个 阶段,成型阶段对管内液体加压胀型的同时 两端的冲头按照设定加载曲线向内推进补料, 在内压和轴向补料的联合作用下使管材基本 贴近模具;第三个阶段,整型阶段,提高压 力使过度区圆角完全贴靠模具而成型为所需 的工件,这个阶段基本没有补料,从截面看 可以把管材变为矩型、梯型、椭圆型或其他 异型截面。
板材液压成型技术特点
- 1、下载文档前请自行甄别文档内容的完整性,平台不提供额外的编辑、内容补充、找答案等附加服务。
- 2、"仅部分预览"的文档,不可在线预览部分如存在完整性等问题,可反馈申请退款(可完整预览的文档不适用该条件!)。
- 3、如文档侵犯您的权益,请联系客服反馈,我们会尽快为您处理(人工客服工作时间:9:00-18:30)。
液压成形工艺摘要:液压成形是一种先进的塑性成形技术,是利用液体介质代替凸模或凹模,靠液体介质的压力使材料成形的一种加工工艺。
液压成形技术不但能成形复杂零件还能够提高零件质量减少成形工序降低加工成本特别适合于小批量零件的加工生产。
关键字:管件液压成形. 液压胀形. 板材液压成形.1概述现代工业产品由大批量向多品种和中小批量方向发展。
对于批量小、尺寸多变的复杂形状板材零件,采用传统冲压方法成形时,模具设计、制造与调试需要消耗大量的人力、物力与时间,很难适应现代化发展的需要。
这就迫切需要研究一种新的柔性生产方法,达到既降低成本又缩短制造周期的目的。
液压成形技术正是在这种背景下提出来的液压成形是一种先进的塑性成形技术,是利用液体介质代替凸模或凹模,靠液体介质的压力使材料成形的一种加工工艺。
它能够改善工件内部应力状态,提高板料的成形极限,成形形状复杂的零件,且成形件质量好、精度高、回弹小,具有传统拉深无法比拟的优越性。
液压成形技术不但能成形复杂零件还能够提高零件质量减少成形工序降低加工成本特别适合于小批量零件的加工生产。
液压成形技术早在20世纪40 年代就被用于汽车制造业。
如果按照加工过程的特点,可以分为管件液压成形技术、板料液压成形技术等2 管材液压成形2.1管材液压成形的历史及原理管材液压成形起源于19世纪末, 当时主要用于管件的弯曲。
由于相关技术的限制, 在以后相当长一段时间内, 管材液压成形只局限于实验室研究阶段, 在工业上并未得到广泛应用。
但随着计算机控制技术的发展和高液压技术的出现,管材液压成形开始得到大力发展。
上世纪90年代, 伴随着汽车工业的发展以及对汽车轻量化、高质量和环保的要求, 管材液压成形受到人们重视, 并得到广泛应用。
管件液压成形是以金属管材为毛坯,借助专用设备向密封的管坯内注入液体介质,使其产生高压,同时还在管坯的两端施加轴向推力,进行补料,在两种外力的作用下,管坯材料塑性变形,并最终与模具型腔内壁贴合,得到形状与精度均符合技术要求的中空零件液压成形原理如图1 所示图1 管件液压成形原理示意图当零件轴线不是直线模腔分模面处截面小于管坯截面时,需进行弯管冲压等预工艺,以便管坯能顺利置入模腔中,如有必要,在液压成形之前还需进行退火处理2.2管材液压成形优点:与传统的冲压焊接工艺相比,管件液压成形工艺具有以下优点:(1 ) 减轻零件质量,节约材料; (2 ) 提高零件的强度和刚度,特别是疲劳强度; ( 3) 减少零件数量节约模具成本;(4) 零件整体成形,可减少后续机械加工和组装焊接量,简化生产流程,提高生产效率; (5) 提高加工精度,减少装配误差积累,可提高产品质量; (6)降低生产成本; (7) 结构形状设计更趋灵活优化。
由于以上的诸多优点,德国在20世纪90年代率先在汽车工业中实现了生产应用。
之后,管件液压成形技术在欧洲其它国家、北美、日本和韩国等国迅速得到广泛关注和推广。
采用液压成形工艺制造的汽车零件主要有排气系统异型管件、车身框架结构件驱动轴以及安全构件等(约占汽车总重量10~15%)。
如排气岐管、排气管、车顶横梁、仪表盘支架、散热器支架、副车架、车顶纵梁、车身纵梁、座椅架、发动机支架、车门柱、车门槛、侧框、地板横梁、后延纵臂、车桥、转向柱以及保险杠等。
如图1-2是典型的管件液压成形汽车结构类零件典型液压成形汽车零件2.3.管件液压成形设备国际上能够提供液压成形成套技术与设备的制造商多数集中在欧洲,其中,以德国舒勒公司、SPS公司和瑞典AP&T公司为主要代表。
管件液压成形设备目前主要着大合模力、大吨位、超高压、确控制的方向发展。
德国舒勒公司(SchulerAG)开展内高压成形技术的研发始于1994年,目前是全球范围内高压成形成套技术与设备最主要的供应商之一。
1998年,舒勒公司开发成功了世界上最大吨位的管件液压成形液压机,合模力100MN,可以生产长6m的零件。
德国SPS公司(Siempelkamp Pressen Systeme GmbH&Co.)研究液压成形工艺及设备始于1965年,至今已向用户提供了50多台管件液压成形液压机,但近60%是最近6年内交货投产的。
1994年,SPS公司制造的世界上第一条全自动液压成形专用生产线在德国宝马公司工厂投入使用,该生产线主要由2台16MN 内高压成形液压机组成,用于生产轿车后桥上的四种空心铝合金零件,日产量达4500件。
瑞典AP&T公司从事液力成形的研究已有30多年的历史,在注意到液压成形技术广阔的市场前景之后,AP&T司组建AP&T Schafer Technol GmbH公司。
2000年底,AP&T司建成了一台100MN内高压成液压机,用于前期工艺开发和试研究。
2001年底,AP&T公司为国KWS公司制造了一台80MN高压成形液压机,标志着该公司进入本领域国际顶尖设备与工艺应商的行列。
双滑块结构管件液压成形机3液压胀球液压胀球技术为哈尔滨工业大学王仲仁教授首创, 此技术产生于上世纪80年代, 曾先后获得省科技进步一等奖及国家发明奖, 同时在第18届北美加工研究会上, 液压胀球被列为五项新成果之首。
相对于传统的球形容器加工工艺, 此技术具有缩短生产周期, 降低生产成本, 提高成形质量等优点, 且利用此技术不需要大型压力机和模具。
因此, 此技术已逐渐成为制造球形容器的主流技术。
3. 1液压胀球的基本原理其基本原理是用单曲率壳体或板料, 经过焊接后组装成一个封闭的多面壳体或单曲率壳体, 在壳体中充入传压介质, 使之发生塑性变形并逐步胀形成为球形容器。
理论依据: 一是力学上的趋球原理, 即曲率半径不同的壳体在趋球弯矩的作用下将逐渐趋于一致; 二是金属材料存在塑性变形的自动调节能力, 当某一区域的变形过为集中, 则该区域将发生变形强化, 塑性变形将转移至它处。
3. 2液压胀球的关键问题液压胀球成形时有两个关键点: 一是传压介质的加载, 二是焊接的质量。
传压介质的加载包括液压泵的流量、加载速度以及保压时间。
一般来说, 在成形初期可使用大流量和大的加载速度, 但在成形末期, 必须降低流量和加载速度。
同时在成形过程中, 当压力达到适当的值时, 还须保持一段时间, 以利于球壳成形。
焊接质量也决定着成形的成功与否。
焊接质量不好, 会造成成形过程中焊接处开裂。
因此在成形前需对焊接处进行表面探伤, 一旦发现焊接处有裂纹, 需及时修补3. 3液压胀球的应用球形容器与其它容器相比, 有占地面积小, 承载能力大, 制造相同容积的容器所需材料少等优点。
因此石化工业、冶金业以及建筑行业都大量采用球形容器。
这就使得液压胀球技术有着广泛的应用前景。
从技术产生到现在已有日本、新加坡、瑞典等国家购买此技术,国内的不少企业订购此技术生产的球形容器。
安装于贵州省都匀火车站的我国第一只直径8m的钢制球形水塔便是采用液压胀球加工而成。
位于奥林匹克中心直径为4m的艺术网球也采用此技术加工而成。
3. 4液压胀球的新进展现在液压胀球也逐渐用于非球形容器和多层球形容器的成形。
哈尔滨工业大学已经对此作过多方面的理论分析和实验研究, 积累了不少经验, 目前, 已成功加工出花瓶形容器和双层球罐。
4 板材液压成形板材液压成形则是从管件液压成形推广而来。
美国、德国和日本相继于上世纪五、六十年代开发出了橡皮囊板材液压成形技术。
但由于橡皮囊易损坏,且成形时尚需很高压力以消除法兰部位的起皱,在实际生产中并没有得到广泛应用。
后来日本学者对此进行了改进, 去除了橡皮囊, 开发出对向液压拉深技术。
—意力转向了板材液压成形技术板材液压成形具有传统板材成形方式无法比拟的优越性,它不仅可以成形形状复杂的零件,而且成品零件精度高、表面光洁,加工成本可大幅度降低。
4. 1板材液压成形的原理在板材液压成形中,应用最为广泛,技术也最为成熟的是对向液压拉深技术。
图5是其成形过程示意图。
首先将板料放置于凹模上,压边圈压紧板料,使凹模型腔形成密封状态。
当凸模下行进人型腔时,型腔内的液体由于受到压缩而产生高压,最终使毛坯紧紧贴向凸模而成形。
当然,如成形初期对液体压力要求较高,可在成形一开始使用液压泵实行强制增压,使液体压力达到一定值,以满足成形要求4. 2板材液压成形的关键问题在板材的液压成形过程中, 最为关键的问题是压边力和液体压力的控制。
若压边力过小, 零件的法兰边易起皱, 而且成形所需的液体压力难以形成; 反之, 由于压边力过大, 造成材料难以流动, 导致拉裂。
对于液体压力, 若其值过小, 则凸模和板料之间的摩擦力也会很小, 造成凸模和板料之间的相对滑动, 致使板料在成形过程中变薄, 与传统的拉深相差无几; 若其值过大,成形过程中板料又极有可能胀破。
压边力和液体压力之间也有相互联系。
压边力的大小影响着液体压力的大小, 如果压边力控制得当, 在成形过程中, 液体可通过零件法兰处溢出, 溢出的液体能有效地润滑凹模上表面, 降低板料边缘的阻力, 使得零件更易成形。
因此,对压边力和液体压力的控制就决定了零件成形的成功与否。
同管材液压成形一样, 压边力和液体压力的匹配以及加载路径需要从实验中得出, 通过计算机进行精确控制, 方能取得最佳效果。
4. 3板材液压成形的应用现在板材液压成形主要应用于汽车覆盖件生产。
世界众多著名汽车制造商都在采用此技术, 丰田公司所使用的板材液压成形机的成形力达40000kN, 能成形平面尺寸为1300mm×950mm, 重达7kg [ 7]。
同时, 板材液压成形也用于航天、航空制品的生产, 如通信用的雷达罩也逐渐采用液压成形加工。
4. 4板材液压成形的新进展现在板材液压成形的进展主要体现在以下几个方面, 一是对现有工艺的引申和扩展。
例如周向液压拉深技术以及板材成对液压成形技术等。
周向液压拉深技术是在对向拉深的基础上将液体介质引导至板材外周边, 从而对板材产生径向推力, 使板材更易向凹模内流动, 同时在板材上下两面实现双面润滑, 减小了板材流动阻力, 进一步提高成形极限。
周向液压拉深的拉深比可达到3. 3, 高于一般的液压拉深所能达到的拉深比。
板材成对液压成形工艺适用于箱体零件的成形。
成形前需先将板材充液预成形, 切边后再将周边焊接, 然后在两板中间充入高压液体使其贴模成形。
中间过程采用焊接, 可使两块板材准确定位, 保证了零件精度。
同时焊接后再充液成形, 能消除焊接引起的变形。
图6则是板材成对液压成形的示意图。
板料成对液压成形另一方面则是技术的改进。
由于压边力在成形中起着重要的作用, 对于不规则的零件, 在成形时法兰处材料的流动情况是不一样的, 为了控制法兰不同区域材料的流动, 有关专家研制出了多点压边系统。