铜转炉白烟尘加压浸出工艺研究
铜冶炼烟尘工艺及其性质分析控制

铜冶炼烟尘工艺及其性质分析控制铜是一种重要的金属材料,被广泛用于电气、建筑、交通等领域。
铜矿石经过矿石选矿后,要进行铜的冶炼,以获得纯净的铜金属。
在铜冶炼过程中,会产生大量的烟尘污染,对环境造成严重影响。
研究铜冶炼烟尘工艺及其性质分析控制变得尤为重要。
一、铜冶炼烟尘工艺1.1 烟尘产生过程在铜冶炼过程中,主要通过煅烧、熔炼和转炉法三个阶段来获得铜金属。
在这个过程中,烟尘主要由矿石中的有害物质、燃料中的灰分和冶炼渣中的残余杂质等组成。
烟尘产生的主要环节包括矿石破碎、配混、熔炼、大气输送等过程。
1.2 烟尘成分铜冶炼烟尘主要成分包括氧化铁、硅酸盐、硫酸盐、氧化铜、氧化硅等。
硫酸盐是最常见、也是最有害的成分,因为硫酸盐容易与大气中的水蒸气结合形成硫酸雾,对环境造成酸雨的危害。
1.3 烟尘排放规模世界铜产业占到全球工业中烟尘和气体排放的15%左右,而在中国,铜冶炼产业排放量更是庞大。
伴随着铜冶炼工业的发展,烟尘排放的规模也不断增加。
二、铜冶炼烟尘性质分析2.1 粒径分布铜冶炼烟尘中的颗粒物主要由不同大小的颗粒组成,其粒径分布对烟尘的扩散、沉降和治理具有重要影响。
研究表明,铜冶炼烟尘颗粒的平均粒径大约在0.1~5μm之间,细颗粒占主导地位。
2.2 毒性铜冶炼烟尘中的有害物质对环境和人体健康均有一定影响。
硫酸盐、氧化硅等成分具有一定的毒性,并且易造成呼吸道问题。
烟尘中还可能携带重金属物质,对土壤和水源也造成一定的污染。
2.3 酸度铜冶炼烟尘中的硫酸盐容易形成硫酸雾,使得烟尘具有一定的酸性。
这种酸性烟尘在大气中扩散后容易形成酸雨,对周围生态环境产生危害。
2.4 粉尘爆炸性铜冶炼烟尘中可能富含极细的铜粉颗粒,与大气中的氧气容易发生爆炸。
矿石选矿和粉尘处理等环节要严格防止火花的产生。
三、铜冶炼烟尘控制技术3.1 烟尘治理设备目前,主要采用的烟尘治理技术包括除尘器、静电除尘器、湿式电除尘器等。
这些设备能够有效地收集和处理铜冶炼烟尘,减少其排放。
铜转炉白烟尘加压浸出工艺研究

doi:10.3969/j.issn.1007-7545.2018.04.002铜转炉白烟尘加压浸出工艺研究刘飞1,2,洪育民1,赵磊2(1.江西铜业集团公司贵溪冶炼厂,江西贵溪335424;2.北京矿冶科技集团有限公司,北京100160)摘要:针对铜冶炼转炉白烟尘中有价金属的综合利用,开展了加压浸出工艺研究。
在液固比6︰1(mL/g)、初始硫酸浓度0.6 mol/L、浸出温度120 ℃、氧分压0.6 MPa、浸出时间3 h、搅拌速度500 r/min的条件下,Cu、Zn 浸出率均高于95%,Cd浸出率大于90%,As、Fe浸出率可以控制在10%以下。
同步实现Cu、Zn、Cd高效浸出与As、Fe的抑制,有利于后续加压浸出液中的有价金属的分离。
关键词:白烟尘;加压浸出;铜;砷;铁中图分类号:TF811 文献标志码:A 文章编号:1007-7545(2018)04-0000-00Study on Pressure Leaching of Copper Converter White DustLIU Fei1,2, HONG Yu-min1, ZHAO Lei2(1.Guixi Smelter, Jiangxi Copper Corporation, Guixi 335424, Jiangxi, China;2. BGRIMM Technology Group, Beijing 100160, China)Abstract:To realize comprehensive utilization of valuable metals in copper converter white dust, pressure leaching process was carried out. The results show that leaching rate of metals is Cu>95%, Zn>95%, Cd>90%, As<10%, Fe<10% under the optimum conditions including L/S of 6︰1(mg/L), initial sulfuric acid concentration of 0.6 mol/L, leaching temperature of 120 ℃, oxygen partial pressure of 0.6 MPa, leaching time of 3 h, and stirring speed of 500 r/min. Valuable elements of copper, zinc and cadmium can be effectively separated from impurities of arsenic and iron which facilitates separation of valuable metals in lixivium.Key words:white dust; pressure leaching; copper; arsenic; iron国内大型铜冶炼厂多通过闪速熔炼、PS转炉吹炼和回转式阳极炉精炼等工序将铜精矿和废杂铜冶炼成能满足电解精炼工序需求的阳极板。
铜吹炼白烟尘处理的研究及应用进展

作者简介:蒋清元(1982-),男,助理工程师,主要从事铜冶炼生产技 术管理工作。
2 白烟尘处理及利用现状
为减轻砷对 后 续 回 收 产 品 质 量 的 影 响,许 多 科 技人员对白烟尘预处理脱砷做了大量研究。火法脱 砷有低温还原焙烧脱砷、真空焙烧脱砷法,脱砷效率 约 80%,火法脱砷更多适合 As大于 10%的物料,存 在环境 污 染 严 重 等 问 题[6~8]。湿 法 脱 砷 主 要 有 酸 法、碱法,碱法 脱 砷 效 率 高 些,但 脱 砷 物 料 后 续 回 收 多半采用酸浸,导致浸出酸耗增加,且产生大量含盐 废水难以处 理,同 时 碱 法 预 脱 砷 也 更 适 合 处 理 高 砷 物料 。 [9~12]
还有的 冶 炼 厂 直 接 向 浸 出 液 中 添 加 硫 化 钠 溶 液,通过控制 硫 化 钠 加 入 量 使 大 部 分 铜 以 硫 化 铜 形 式析出,得 到 的 硫 化 铜 返 回 熔 炼 炉。 但 硫 化 钠 加 入 量难以把握,得 到 硫 化 铜 的 同 时,部 分 砷、锌 也 以 硫 化物形式析出,导致砷在冶炼厂无效循环。
因此,铜冶炼 过 程 中 必 须 将 白 烟 尘 定 期 开 路 处 理。如何处理及利用白烟尘中有价金属成为铜冶炼 企业的难题。
1 白烟尘主要成分
由于 受 原 料、工 艺 方 法、控 制 条 件 和 操 作 的 影 响,不同冶炼厂铜烟尘的成分不尽相同,白烟尘主要 成分见表 1[5]。 表 1 国内部分冶炼厂转炉白烟尘分析结果 %
铜转炉白烟灰湿法提取铋的工艺研究
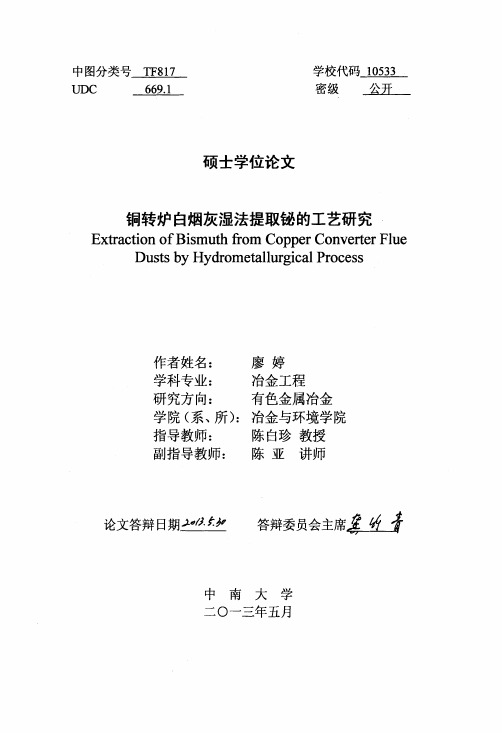
One of these is white ash,namely the copper converter flue dust produced in the copper smelting method.which iS also
a
kind of raw material
can
containing bismuth.A variety of valuable heavy metals by leaching from white ash.which makes it
solubility element such as Zn、Cd、CU、Fe
can
be separated and Bi。Sb
Can
be enriched by the first leaching,when the leaching agent Was 0.5 mol・L’1 H2S04.The optimized results show that
and the impact of pH value
precipitation rate of the five
elements(Bi、
Sb、As、Pb、Cu)was examined respectively.The optimized results show
that by
adjusting
can
作者签名:兽每导师签名峭日期.坐年上月坚日
铜转炉白烟灰湿法提取铋的工艺研究
摘要:我国铋冶炼生产的原料中有60%是来自其它金属(铅、铜、锡 等)冶炼过程中产出的含铋副产品和中间产物,这些原料的有价金属 含量复杂、品位也高低不等。铜转炉白烟灰是火法炼铜过程中产生的 烟尘,经浸出可回收其中的多种有价重金属,也是铜冶炼过程中产出
从铜冶炼烟尘中氧压浸出有价金属试

2 试验结果与讨论
2.
1 氧分压对金属浸出率的影响
铜冶炼烟尘质量200g,木质素用量0.
2g,初
始硫酸质量浓 度 120g/L,液 固 体 积 质 量 比 5/1,
由图 3 看出:随温度从 90 ℃ 升至 130 ℃ ,铜、
锌、铟浸出率均明显升高;升至 130 ℃ 后,铜、锌、铟
浸出率升高幅度变小,趋于稳定。随温度升高,氧
A
DOI:
10.
13355/
cnk
i.
s
f
2022.
06.
004
j.
y
j.
文章编号:
1009
2617(
2022)
06
0498
04
铜 冶 炼 烟 尘 中 含 有 大 量 有 价 金 属 铅、锌、铜、
铋、铟等,也包含少量有毒有害元素砷
,因此,从
[
1]
中回收有价金属及实现无害化处理有重要意义。
铜冶炼烟尘成分复杂,物相组成波动大,处理
2.
3 反应时间对金属浸出率的影响
铜冶炼烟尘质量 200g,木质素用量 0.
2g,初
Copyright©博看网. All Rights Reserved.
· 500 ·
2022 年 12 月
湿法冶金
/L,液固体积质量比 5/1,温
始硫酸质量浓度 120g
/L
升高幅 度 较 大;初 始 硫 酸 质 量 浓 度 增 至 120g
2ZnS+2H2SO4 +O2 2ZnSO4 +
2S0 +2H2O;
(
1)
(
2)
(
3)
2
转炉白烟尘处理工艺
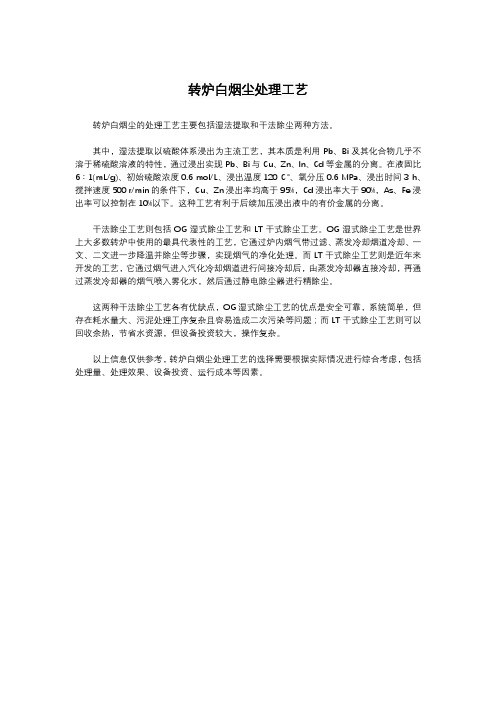
转炉白烟尘处理工艺
转炉白烟尘的处理工艺主要包括湿法提取和干法除尘两种方法。
其中,湿法提取以硫酸体系浸出为主流工艺,其本质是利用Pb、Bi及其化合物几乎不溶于稀硫酸溶液的特性,通过浸出实现Pb、Bi与Cu、Zn、In、Cd等金属的分离。
在液固比6︰1(mL/g)、初始硫酸浓度0.6 mol/L、浸出温度120 ℃、氧分压0.6 MPa、浸出时间3 h、搅拌速度500 r/min的条件下,Cu、Zn浸出率均高于95%,Cd浸出率大于90%,As、Fe浸出率可以控制在10%以下。
这种工艺有利于后续加压浸出液中的有价金属的分离。
干法除尘工艺则包括OG湿式除尘工艺和LT干式除尘工艺。
OG湿式除尘工艺是世界上大多数转炉中使用的最具代表性的工艺,它通过炉内烟气带过滤、蒸发冷却烟道冷却、一文、二文进一步降温并除尘等步骤,实现烟气的净化处理。
而LT干式除尘工艺则是近年来开发的工艺,它通过烟气进入汽化冷却烟道进行间接冷却后,由蒸发冷却器直接冷却,再通过蒸发冷却器的烟气喷入雾化水,然后通过静电除尘器进行精除尘。
这两种干法除尘工艺各有优缺点,OG湿式除尘工艺的优点是安全可靠,系统简单,但存在耗水量大、污泥处理工序复杂且容易造成二次污染等问题;而LT干式除尘工艺则可以回收余热,节省水资源,但设备投资较大,操作复杂。
以上信息仅供参考,转炉白烟尘处理工艺的选择需要根据实际情况进行综合考虑,包括处理量、处理效果、设备投资、运行成本等因素。
铜冶炼烟尘工艺及其性质分析控制
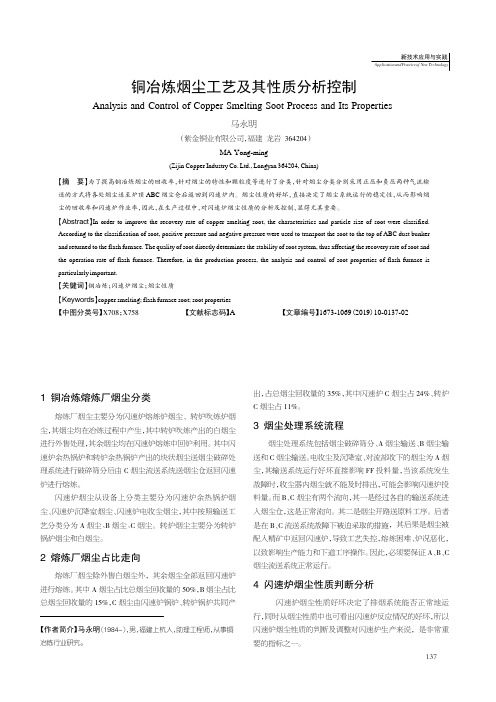
1铜冶炼熔炼厂烟尘分类熔炼厂烟尘主要分为闪速炉熔炼炉烟尘、转炉吹炼炉烟尘,其烟尘均在冶炼过程中产生,其中转炉吹炼产出的白烟尘进行外售处理,其余烟尘均在闪速炉熔炼中回炉利用。
其中闪速炉余热锅炉和转炉余热锅炉产出的块状烟尘送烟尘破碎处理系统进行破碎筛分后由C烟尘流送系统送烟尘仓返回闪速炉进行熔炼。
闪速炉烟尘从设备上分类主要分为闪速炉余热锅炉烟尘、闪速炉沉降室烟尘、闪速炉电收尘烟尘,其中按照输送工艺分类分为A烟尘、B烟尘、C烟尘。
转炉烟尘主要分为转炉锅炉烟尘和白烟尘。
2熔炼厂烟尘占比走向熔炼厂烟尘除外售白烟尘外,其余烟尘全部返回闪速炉进行熔炼。
其中A烟尘占比总烟尘回收量的50%,B烟尘占比总烟尘回收量的15%,C烟尘由闪速炉锅炉、转炉锅炉共同产出,占总烟尘回收量的35%,其中闪速炉C烟尘占24%、转炉C烟尘占11%。
3烟尘处理系统流程烟尘处理系统包括烟尘破碎筛分、A烟尘输送、B烟尘输送和C烟尘输送。
电收尘及沉降室、对流部收下的烟尘为A烟尘,其输送系统运行好坏直接影响FF投料量,当该系统发生故障时,收尘器内烟尘就不能及时排出,可能会影响闪速炉投料量。
而B、C烟尘有两个流向,其一是经过各自的输送系统进入烟尘仓,这是正常流向。
其二是烟尘开路送原料工序。
后者是在B、C流送系统故障下被迫采取的措施,其后果是烟尘被配入精矿中返回闪速炉,导致工艺失控,熔炼困难、炉况恶化,以致影响生产能力和下道工序操作。
因此,必须要保证A、B、C 烟尘流送系统正常运行。
4闪速炉烟尘性质判断分析闪速炉烟尘性质好坏决定了排烟系统能否正常地运行,同时从烟尘性质中也可看出闪速炉反应情况的好坏,所以闪速炉烟尘性质的判断及调整对闪速炉生产来说,是非常重要的指标之一。
铜冶炼烟尘工艺及其性质分析控制Analysis and Control of Copper Smelting Soot Process and Its Properties马永明(紫金铜业有限公司,福建龙岩364204)MA Yong-ming(Zijin Copper Industry Co.Ltd.,Longyan364204,China)【摘要】为了提高铜冶炼烟尘的回收率,针对烟尘的特性和颗粒度等进行了分类,针对烟尘分类分别采用正压和负压两种气流输送的方式将各处烟尘送至炉顶ABC烟尘仓后返回到闪速炉内。
铜冶炼高砷白烟尘酸浸脱砷工艺研究

世界有色金属 2020年 8月下4冶金冶炼M etallurgical smelting1 前言砷及其砷化合物易挥发[1],在火法炼铜过程中80%以上的砷进入烟尘,呈灰色略带白色,一般称为白烟尘[2]。
白烟尘中含有Cu、Pb、Zn、Au、Ag 等有价金属[3-4],具有较大的回收价值,但砷含量高[5-6]、成分复杂,影响回收效果。
因此,对白烟尘进行脱砷处理十分必要。
铜冶炼企业中,一般将白烟尘收集后作为配料重新熔炼进行闭路循环或堆存,这两种做法都存在较多问题。
白烟尘中含有砷,长期堆存存在较多安全隐患,另外烟尘中的金属元素无法得到有效回收,造成资源浪费。
而“闭路循环”的危害也是显而易见的,会造成As、Pb 等元素不断循环积累,使烟道结焦,影响作业环境,而且会对铜阳极板质量产生影响。
因此多数铜冶炼企业开始进行白烟尘的处理工艺研究,实现白烟尘中砷的开路,并回收铜铅锌等有价金属元素。
本文以山东恒邦冶炼股份有限公司铜冶炼白烟尘为研究对象,探究了脱砷预处理及有价金属综合回收的最佳工艺条件,使白烟尘中的砷形成开路,有价金属得以综合回收。
2 实验2.1 试验原料实验所用铜冶炼白烟尘来自山东恒邦冶炼股份有限公司冶炼一公司侧吹熔炼电除尘器产出的烟灰(铜冶炼白烟尘),其主要化学成分如表1所示。
从表1可以看出:烟尘中含有Au、Ag、Cu、Pb、Zn 等有价金属,具有较高的回收价值;含砷16.74%,需要预处理脱砷。
2.2 实验原理根据Au、Ag、Cu、Pb、Zn 等的溶解度不同,采用酸性浸出,将烟尘中的As、Cu、Zn 等有价金属最大限度的溶解在浸出液中,以利于后续回收,而Pb、Au、Ag 等金属形成沉淀留在渣中。
2.3 实验方法:取铜冶炼白烟尘300g 和一定量的浸取剂于1000mL 烧杯中,在一定的温度、适宜的搅拌速度下进行搅拌浸出。
浸出实验结束后,进行抽滤,滤渣洗涤并烘干。
分析砷质量分数,计算砷浸出率即砷脱除率。
浸出率计算公式如下式:其中,Me 为As、Cu、Zn。
炼铜烟灰加压浸出试验研究

炼铜烟灰加压浸出试验研究①陈荣升,谌宏海,王细军,李亚杰,廖诗佳,李㊀杰(湖北大江环保科技股份有限公司,湖北黄石435005)摘㊀要:为利用炼铜烟灰中的有价金属,采用加压浸出法浸出铜冶炼烟灰中的铜和锌,考察了温度㊁压力㊁始酸浓度㊁浸出时间对浸出效果的影响㊂研究结果表明,最佳浸出条件为:温度160ħ㊁压力1.2MPa㊁始酸浓度130g/L㊁浸出时间3h,该条件下铜㊁锌浸出率分别为98.9%和97.8%㊂关键词:炼铜烟灰;加压浸出;浸出率;铜;锌;氧化中图分类号:TF811文献标识码:Adoi:10.3969/j.issn.0253-6099.2020.04.031文章编号:0253-6099(2020)04-0124-03ExperimentalStudyonPressureLeachingofFlueDustfromCopperSmeltingCHENRong⁃sheng,CHENHong⁃hai,WANGXi⁃jun,LIYa⁃jie,LIAOShi⁃jia,LIJie(HubeiDajiangEnvironmentalProtectionTechnologyCoLtd,Huangshi435005,Hubei,China)Abstract:Apressureleachingprocesswasadoptedinordertorecovercopperandzincinthefluedustfromcoppersmelting.Effectsoftemperature,pressure,initialacidconcentrationandleachingtimeonthefinalleachingrateswereinvestigated.Theresultsshowthata3h⁃pressureleachingat160ħ,withthepressureat1.2MPaandaninitialacidconcentrationof130g/L,canleadtotheleachingrateofcopperandzincupto98.9%and97.8%,respectively.Keywords:fluedustfromcoppersmelting;pressureleaching;leachingrate;copper;zinc;oxidation㊀㊀铜是一种玫瑰红色重金属,广泛用于电气㊁国防等各个领域[1-2],目前绝大部分金属铜是通过火法工艺产出的[3-5]㊂火法炼铜底吹炉造锍熔炼是将含铜物料与溶剂一起加入底吹炉内,通入富氧空气使物料在高温下熔化,发生一系列物理化学反应后得到冰铜和炉渣[6-8],铜精矿中伴生的Pb㊁Zn等易挥发组分进入烟气中[9]㊂因底吹炉特殊的结构,铜烟灰中元素种类多且含有较多的金属硫化物,增加了烟灰的处理难度㊂目前国内外对底吹炉烟灰的研究较少,处理时存在工艺流程长㊁回收率低㊁有害物质难于开路等难题[10-12]㊂本文针对底吹炉炼铜烟灰的组成特性,采用加压浸出法,实现铜㊁锌两种金属元素的提取,主要研究了温度㊁压力㊁始酸浓度㊁浸出时间对铜㊁锌浸出效果的影响,为后续分离提取提供参考㊂1㊀试㊀㊀验1.1㊀试验原料试验所用原料来自我国某铜冶炼企业底吹炉熔炼过程产生的铜烟灰,样品经干燥㊁缩分㊁混匀后取样,粉磨和筛分处理,保证物料粒度小于0.074mm㊂铜烟灰粒度较细,在2 4μm㊁10 20μm和60 70μm粒级呈现相对部分集中分布,平均粒度为3.86μm,比表面积为979.3m2/kg,有利于湿法浸出过程㊂铜烟灰样品的主要化学元素组成见表1,其X射线衍射图见图1㊂表1㊀铜烟灰主要化学元素组成(质量分数)/%PbCuZnFeAsS22.4114.903.128.2310.5410.56①收稿日期:2020-03-05作者简介:陈荣升(1983-),男,辽宁昌图人,工程师,硕士,主要从事冶金及资源综合回收技术研究与管理工作㊂第40卷第4期2020年08月矿㊀冶㊀工㊀程MININGANDMETALLURGICALENGINEERINGVol.40ɴ4August202030201040507060802 (°)θ1 —PbSO 42 — CuSO 43 — CuFeS 24 — As 2O 35 — Fe 2O 36 — Cu x S 7 — Fe 2(SO 4)38 — CuO 9 — Fe 3O 422771133441111111165599988361111111图1㊀铜烟灰XRD图谱为进一步查明铜烟灰中铜㊁铅㊁铁和砷的赋存状态,进行了物相定量分析,结果见表2㊂表2㊀铜烟灰中Pb㊁Cu㊁As㊁Fe的物相分布物相分布率/%PbCuAsFe硫化物相2.6830.873.7510.83硫酸盐相88.6232.256.6812.73氧化物相8.7036.8889.5776.44合计100.00100.00100.00100.001.2㊀反应原理根据铜烟灰中铜㊁铅㊁砷和铁等金属的含量及物相分析结果,拟采用氧压浸出法将铜㊁锌与砷㊁铁㊁铅分离㊂反应可分为3个阶段:第一阶段为易溶于酸的氧化锌㊁氧化铜㊁氧化铁和氧化铅等物质与硫酸反应;第二阶段为金属硫化物在有氧条件下溶出,以及低价态砷㊁铁被氧化为高价,此时烟灰中大部分铜㊁砷㊁铁㊁锌以可溶性硫酸盐形式进入溶液中;第三阶段为溶液中砷㊁铁反应生成砷酸铁沉淀,与锌㊁铜分离[13]㊂由于铜烟灰原料中砷与铁的比例相当,砷与铁基本沉淀,故本文只讨论温度㊁压力㊁始酸浓度㊁浸出时间对铜㊁锌浸出率的影响㊂1.3㊀试验方法称取一定量的铜烟灰,按照一定的温度㊁压力㊁始酸浓度及浸出时间在反应釜(威海宏协化工机械有限公司CJK⁃2L磁力反应釜,内衬锆材)中进行反应,待反应结束后,过滤㊁洗涤,滤渣干燥后进行化学分析检测,微量元素成分采用ICP⁃MS(Agilent7500)检测,铜㊁锌浸出率根据渣的成分数据进行计算㊂采用日本岛津公司DIFFRACTOMETER⁃6000型X射线衍射仪(XRD)进行矿物组成分析;采用百特BT⁃9300S型激光粒度仪进行粒度分析㊂2㊀结果与分析讨论2.1㊀温度的影响压力1.1MPa㊁始酸浓度100g/L㊁浸出时间1h条件下,不同温度对铜㊁锌浸出率的影响见图2㊂从图2可看出,当温度从120ħ增大到160ħ时,铜㊁锌浸出率逐步提高㊂这是因为随着温度不断升高,烟灰中可溶物质在溶液中的溶解度增大,从而使浸出速度加快;同时,升高温度可以降低浸出液黏度,有利于物质扩散,从而促进浸出反应㊂但当温度增大到180ħ时,铜㊁锌浸出率出现略微下降的趋势㊂因此选择温度为160ħ㊂>,857565551201601401801*5——Cu——Zn图2㊀温度对铜烟灰浸出的影响2.2㊀压力的影响温度160ħ,其他条件不变,不同压力下铜㊁锌浸出率如图3所示㊂从图3可知,压力从0.8MPa提高到1.2MPa时,铜浸出率有了明显提高,继续增大压力时,铜浸出率上升缓慢;锌浸出率变化趋势与铜非常类似㊂故选取压力为1.2MPa㊂@4 MPa908070600.8 1.21.01.41*5—— Cu ——Zn 图3㊀压力对铜烟灰浸出的影响2.3㊀始酸浓度的影响始酸浓度对保证生产中的处理能力至关重要㊂压力1.2MPa,其他条件不变,不同始酸浓度时铜㊁锌浸出率如图4所示㊂由图4可知,当始酸浓度从90g/L521第4期陈荣升等:炼铜烟灰加压浸出试验研究增大到130g/L时,铜㊁锌浸出率均明显提高;进一步增大始酸浓度时,铜㊁锌浸出率变化平缓㊂这说明始酸浓度达到130g/L时,铜烟灰与酸的接触反应已经比较充分㊂因此确定始酸浓度为130g/L㊂;<7, (g · L -1)95857565901301101501*5—— Cu —— Zn图4㊀始酸浓度对铜烟灰浸出的影响2.4㊀浸出时间的影响始酸浓度130g/L,其他条件不变,浸出时间对铜㊁锌浸出率的影响如图5所示㊂从图5可看出,当浸出时间从1h延长至3h时,铜㊁锌浸出率逐渐上升,继续延长浸出时间至4h时,铜㊁锌浸出率基本保持不变,因此浸出时间选择为3h㊂1*;0 h100989694929013241*5——Cu ——Zn图5㊀浸出时间对浸出的影响2.5㊀综合试验及浸出渣元素分析根据单因素实验,在温度160ħ㊁压力1.2MPa㊁始酸浓度130g/L㊁浸出时间3h条件下,进行了铜烟灰加压浸出综合试验,铜㊁锌浸出率分别达到98.9%和97.8%㊂对浸出渣进行了化学元素分析,结果如表3所示㊂浸出渣中Cu㊁Zn含量皆为微量,Pb㊁Fe㊁As含量较高,可以作为铅火法冶炼原料㊂表3㊀浸出渣主要化学元素组成(质量分数)/%PbCuZnFeAs34.420.250.1112.3115.38浸出液可通过除铜⁃除铁⁃除锰⁃除镉等净化工序得到纯净的硫酸锌溶液,再通过蒸发结晶制成一水硫酸锌或七水硫酸锌产品㊂3㊀结㊀㊀论1)采用氧压浸出法处理铜冶炼底吹炉造锍熔炼过程中产生的铜烟灰,可有效浸出铜㊁锌,实现铜烟灰中有价资源的回收㊂2)加压浸出的最佳条件为:温度160ħ㊁压力1.2MPa㊁始酸浓度130g/L㊁浸出时间3h,该条件下铜㊁锌浸出率可达到98.9%和97.8%,浸出效果好㊂参考文献:[1]㊀孙乐栋,李㊀杰,光㊀明,等.炼铜烟灰硫酸浸出及铜浸出动力学研究[J].矿冶工程,2016(1):97-100.[2]㊀MontenegroV,SanoH,FujisawaT.Recirculationofhigharseniccontentcoppersmeltingdusttosmeltingandconvertingprocesses[J].MineralsEngineering,2013,49(8):184-189.[3]㊀郝士涛.铜冶炼烟灰碱浸脱砷预处理及有价金属综合回收[D].赣州:江西理工大学材料与化学工程学院,2012.[4]㊀张㊀琰.从铜转炉烟灰中回收铜锌铅的研究[D].兰州:兰州理工大学材料科学与工程学院,2011.[5]㊀高大银,周㊀明,夏兆泉,等.侧吹炉两段法处理含铅铜烟灰的工艺:中国,CN201410038592.6[P].2014.[6]㊀张训鹏.冶金工程概论[M].长沙:中南大学出版社,2005.[7]㊀朱家栋.铜造锍熔炼烟尘的处理工艺研究[D].武汉:武汉科技大学材料与冶金学院,2012.[8]㊀VítkováM,EttlerV,HyksJ,etal.Leachingofmetalsfromcoppersmelterfluedust(Mufulira,ZambianCopperbelt)[J].AppliedGeo⁃chemistry,2011,26:S263-S266.[9]㊀李洪臻.浅淡富氧底吹炉熔池炼铜新工艺[J].山西冶金,2016,39(1):91-93.[10]㊀李学鹏,王㊀娟,常㊀军,等.两段酸浸法浸出铜烟尘中的铜锌铟[J].矿冶工程,2020,40(1):109-113.[11]㊀汪金良,胡华舟,谢凌峰.铜烟灰酸浸⁃磁选预处理过程中元素的分配[J].有色金属(冶炼部分),2018(5):5-9.[12]㊀MoralesA,CruellsM,RocaA,etal.Treatmentofcopperflashsmelterfluedustsforcopperandzincextractionandarsenicstabiliza⁃tion[J].Hydrometallurgy,2010,105(1-2):148-154.[13]㊀蒋开喜.加压湿法冶金[M].北京:冶金工业出版社,2016.引用本文:陈荣升,谌宏海,王细军,等.炼铜烟灰加压浸出试验研究[J].矿冶工程,2020,40(4):124-126.621矿㊀冶㊀工㊀程第40卷。
210978914_铜冶炼烟灰浸出液处理新工艺探究

化学反应方程式如下 :
CuO+H2SO4=CuSO4+H2O
( 式 1-1)
Cu2O+H2SO4=Cu2SO4+H2O
( 式 1-2)
2Cu2SO4+2H2SO4+O2=4CuSO4+2H2O ( 式 1-3)
ZnO+H2SO4=ZnSO4+H2O
( 式 1-4)
中沉淀出来,达到铜和砷分别沉淀的目的。化学反应方程式
如下 :
Cu2++H2S=CuS ↓ +2H+
( 式 2-1)
2AsO33-+3H2S+6H+=As2S3 ↓ +6H2O ( 式 2-2)
As2S3+3Cu2++6H2O=2H3AsO3+3CuS+6H+( 式 2-3)
4.3.3 分步硫化试验步骤及化验结果
(1)硫化氢气体的制备。
在气体发生器中预先加入稀硫酸,通过蠕动泵定量向发
CdO+H2SO4=CdSO4 ↓ +H2O
( 式 1-5)
As2O3+3H2O=2H3AsO3
( 式 1-6)
PbO+H2SO4=PbSO4 ↓ +H2O
( 式 1-7)
Bi2O3+2H2SO4=2Bi(OH)SO4 ↓ +H2O ( 式 1-8)
铜冶炼烟灰浸出液处理新工艺探究
景元涛1,2
(1. 中南大学,湖南 长沙 410000 ;2. 东营方泰金属回收利用有限公司,山东 东营 257000)
摘 要 :铜烟灰是当前铜冶炼行业中的主要废弃物之一,其含有 Cu、Zn、Pb、Bi、Ag 等有价金属,也含有 As 等有毒有
炼铜烟灰氧压浸出铜、锌的试验研究

炼铜烟灰氧压浸出铜、锌的试验研究许冬【摘要】The effects of the dosage of leaching agent, leaching time, leaching temperature and partial pressure of oxygen on the leaching rate of copper and zinc from smelting copper were discussed by using oxygen pressure leaching process.The results showed that the leaching rates of Cu and Zn reached 96.5% and 99% respectively under the conditions of 20 mL sulfuric acid, 120 minutes leaching time, 170℃ leaching temperature and 0.8 MPa partial pressure of oxygen.%采用氧压浸出工艺探讨了浸出剂用量、浸出时间、浸出温度、氧分压等工艺条件对炼铜烟灰铜、锌浸出率的影响.结果表明:在硫酸加入量20mL,浸出时间120min,浸出温度170℃,氧分压0.8MPa工艺条件下, Cu、Zn浸出率分别达到97.12%和99%.【期刊名称】《铜业工程》【年(卷),期】2018(000)003【总页数】4页(P95-97,100)【关键词】炼铜烟灰;氧压浸出;浸出剂;浸出时间;浸出温度;浸出率【作者】许冬【作者单位】铜陵有色技术中心,安徽铜陵 244000【正文语种】中文【中图分类】TF111.311 引言在火法炼铜过程中,精矿中部分易挥发的元素,如铅、锌、铟、镉、铋及砷等将挥发进入烟气[1-5],经收尘产出含铜烟灰,成份复杂且波动极大,因此目前尚无固定的处理方法[6-8]。
利用加压酸浸法从烟化炉冰铜中提取铜镍

利用加压酸浸法从烟化炉冰铜中提取铜镍摘要:本文将详细介绍烟化炉冰铜借用加压酸浸法提取铜镍的试验方案,通过专业的研究与调查,找出加压酸浸法提取铜镍的试验过程,并在该过程中合理控制时间要素、浸出温度要素、氧分压要素与液固比要素等,继而更好地掌握试验结论,提升铜镍的提取效率。
关键词:加压酸浸法;烟化炉冰铜;铜镍引言:烟化炉冰铜多为应用烟化炉来提取锌、镍、锡、铜与铁等物料的试验,在使用加压酸浸法期间,多项物料会受到多重要素的影响,若想切实保证试验质量,工作人员应运用合适举措来科学管控其内部要素,从而增强其试验效果。
1烟化炉冰铜借用加压酸浸法提取铜镍的试验方案1.1 试验材料在使用加压酸浸法进行烟化炉冰铜内铜镍的提取前,相关人员应找出该类试验的原料和相应试剂。
具体来看,在某金属有限公司中其内部的烟化炉在熔炼期间会出现一定的冰铜,相关人员将其看作该试验的具体原料,在该冰铜内部,其主要含有FeS、Ni3S2、NiS、CuS与Cu2S等成分,其内部成分中Cu、Ni、Fe、S、As、Sb、Pb与Sn的具体含量分别为19.69、5.12、35.73、19.36、0.36、0.27、0.032、0.7%。
而烟化炉中的杂铜电解液需采用一定的化学试剂,化学试剂中的木质素磺酸钠与硫酸皆带有分析纯,其水属去离子水、氧气带有工业级别。
1.2 试验方法在完成试验材料与相关试剂的选择后,相关人员需明确该试验的对应原理,一般来讲,要将加压冰铜划分成多种形式,并以Ni、Cu等形式放置到对应溶液中,将部分Fe与S开展入侵出渣,在加压过程中可适时关注其反应式,如O2+2H2SO4+2CuS=2H2O+2S0+2CuSO4;O2+2H2SO4+2NiS=2H2O+2S0+2NiSO4;3O2+6H2SO4+4FeS=6H2O+4S0+2Fe2(SO4)3;1.5O2+H2O+S0=H2SO4。
在了解了该试验的工作原理后,相关人员应确认适宜的试验方法,首先,其需将原料与浸出剂依照适宜的固液比进行适时混合,并添入适当的钛加压釜,再完成相应的密封工作。
冶炼厂烟尘中铜的生物浸出

立志当早,存高远冶炼厂烟尘中铜的生物浸出Sarcheshmeh 铜冶炼厂有两台反射炉和三台转炉在运转,这些炉子产生的气体和烟尘通过气球形烟道(回收粗粒烟尘)和静电除尘器(回收细粒烟尘)净化。
这些熔炼炉每天产生烟尘约50 吨,含铜约36%,目前,这些烟尘返回熔炼炉,降低了炉子的效率,增加了熔炼所需能量;此外,还损毁耐火砖,增加炉子循环负荷。
以前的研究表明,Sarcheshmeh 厂铜烟尘主要由次生铜硫化物矿物组成,在生物浸出中比黄铜矿容易反应得多,辉铜矿的浸出速度约为黄铜矿浸出速度的5 倍。
大多数次生铜硫化物可以用中温细菌的培养物来浸出,这些细菌生长的最佳条件为:温度32~35℃,pH=1.5~2.5。
本研究中一系列连续试验都是在两段气升式生物反应器中用嗜酸的铁和硫氧化细菌完成的。
生物浸出和生物氧化最好是在连续操作中完成,在这种操作中,单位时间单位体积的生产率高,反应器体积小。
已研究过的反应器类型包括:搅拌槽渗滤柱、帕丘卡槽、空气升液柱和一些特殊设计的反应器,如旋转式反应器。
空气搅拌生物反应器建造和操作费用高,它的应用仅限于处理高价值的矿石和精矿。
气升式反应器用于很多化学、石油化学、矿物处理和生物技术工业,因为它的设计和建造简单、电耗低、剪切力低、混合特性好,传热和传质好。
在气升式反应器中,保持在上升管和下降管中的气体体积不同,造成一种压力差,迫使液体从下降管底部流向上升管,造成液体的流速和混合。
本研究的目的是在实验室规模评价铜的生物浸出。
冶炼厂混合烟尘的组成如表1。
表1 混合烟尘的化学和矿物成分组成元素/矿物重量(%)估计占铜总量比例(%)Cu(总量)35.8Cua12.9Fe15.3S12.2Cu2S18.861.6CuS1.74.7CuFeS22.02.9CuFeS42.66.8Cu-N5.824FeS20.3FeS2O40.9FeS3O414.8 脉石53.3 注:a-酸溶性铜。
如表1 所。
铜冶炼白烟尘浆化工序的设计与应用
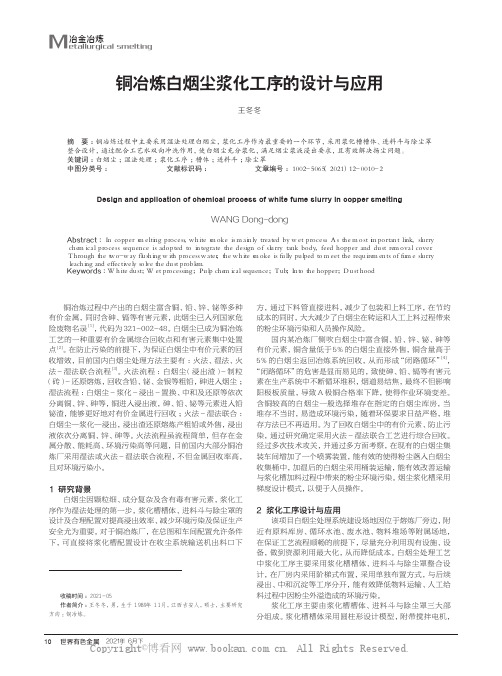
世界有色金属 2021年 6月下10冶金冶炼M etallurgical smelting铜冶炼过程中产出的白烟尘富含铜、铅、锌、铋等多种有价金属,同时含砷、镉等有害元素,此烟尘已入列国家危险废物名录[1],代码为321-002-48。
白烟尘已成为铜冶炼工艺的一种重要有价金属综合回收点和有害元素集中处置点[2]。
在防止污染的前提下,为保证白烟尘中有价元素的回收增效,目前国内白烟尘处理方法主要有:火法、湿法、火法-湿法联合流程[3]。
火法流程:白烟尘(浸出渣)-制粒(砖)-还原熔炼,回收含铅、铋、金银等粗铅,砷进入烟尘;湿法流程:白烟尘-浆化-浸出-置换、中和及还原等依次分离铜、锌、砷等,铜进入浸出液,砷、铅、铋等元素进入铅铋渣,能够更好地对有价金属进行回收;火法-湿法联合:白烟尘—浆化—浸出,浸出渣还原熔炼产粗铅或外售,浸出液依次分离铜、锌、砷等。
火法流程虽流程简单,但存在金属分散、能耗高、环境污染高等问题,目前国内大部分铜冶炼厂采用湿法或火法-湿法联合流程,不但金属回收率高,且对环境污染小。
1 研究背景白烟尘因颗粒细、成分复杂及含有毒有害元素,浆化工序作为湿法处理的第一步,浆化槽槽体、进料斗与除尘罩的设计及合理配置对提高浸出效率、减少环境污染及保证生产安全尤为重要。
对于铜冶炼厂,在总图和车间配置允许条件下,可直接将浆化槽配置设计在收尘系统输送机出料口下方,通过下料管直接进料,减少了包装和上料工序,在节约成本的同时,大大减少了白烟尘在转运和人工上料过程带来的粉尘环境污染和人员操作风险。
国内某冶炼厂侧吹白烟尘中富含铜、铅、锌、铋、砷等有价元素,铜含量低于5%的白烟尘直接外售,铜含量高于5%的白烟尘返回冶炼系统回收,从而形成“闭路循环”[4],“闭路循环”的危害是显而易见的,致使砷、铅、镉等有害元素在生产系统中不断循环堆积,烟道易结焦,最终不但影响阳极板质量,导致A 极铜合格率下降,使得作业环境变差。
铜冶炼烟尘工艺及其性质分析控制

铜冶炼烟尘工艺及其性质分析控制
铜冶炼是非常重要的工业活动,但它也是环境污染的主要来源之一,铜矿冶炼过程中产生的烟尘会严重影响周边环境和人们的健康。
因此,必须采取措施来控制和减少烟尘的排放。
铜冶炼烟尘的主要来源包括炉冶、转炉、煅烧等工段。
其中,炉冶过程中的高温反应会产生较多的烟尘。
同时,铜冶炼烟尘的主要成分是二氧化硫、氮氧化物、烟气颗粒等。
对于铜冶炼烟尘的处理,常用的方法包括重力沉降、湿式收集、静电除尘、过滤等。
其中,重力沉降方法是通过烟气在大气中自然沉积下来,适用于非常小的颗粒。
湿式收集方法是将烟气通过喷雾塔,使其与水接触并凝结,并在水中沉淀下来。
静电除尘方法是利用电场将烟气中的带电颗粒聚集在被带电的收集板上。
过滤方法是利用过滤材料将烟气中的颗粒截留在过滤材料上。
除了上述的治理方法,还有智能控制和技术改进等方法可以控制和减少烟尘的排放。
例如,在炉内对温度和压力等参数进行精确控制,可以减少烟气中的颗粒数目。
此外,铜冶炼企业还可以采用环保高效的新型物料、新型燃料和新型冶炼工艺等技术改进措施来控制烟尘排放。
总之,铜冶炼烟尘是一个不可忽视的环保问题。
针对这个问题,应该采取多种手段,如重力沉降、湿式收集、静电除尘、过滤等物理治理方法,同时也需要借助智能控制和技术改进等手段,从而减少铜冶炼烟尘对环境的影响,实现可持续发展。
探讨铜冶炼烟尘处理技术

探讨铜冶炼烟尘处理技术摘要:铜冶炼烟尘是铜火法冶炼中产出的典型危废,具有砷及有价金属含量高的特点,运输及处理过程中极易造成环境污染,对其就地资源化利用日益受到企业重视。
国内外针对铜烟尘处理开展了大量研究,大致分为火法和湿法两大类。
早期火法应用较多,目前以湿法为主。
根据反应介质的不同,湿法可分为硫酸、氯盐和碱性体系三种。
硫酸体系易与主工艺流程结合,应用最广,具有较强的竞争力。
由于各企业烟尘性质存在差别,处理工艺多样,小型企业多采用硫酸常压浸出—鼓风炉工艺,溶液中砷以砷酸铁等形式沉淀。
关键词:金属冶炼;烟尘处理;环保措施前言近年来,我国的铜冶炼行业进步迅猛,极大地带动了我国工业化的进步,为经济发展增添强大的动力。
不过,随之而来的是一些环保问题。
铜冶炼过程会排放大量的有害烟尘,包含诸多有害物质,严重地破坏了自然环境。
因此,探究铜冶炼过程中的烟尘处理技术对于环境保护具有重要的意义。
国内外针对烟尘处理进行了大量研究及生产实践,大致可分为火法和湿法两大类。
火法主要是将砷挥发进入烟尘,焙砂浸出回收铜等,早期工业应用较多,但砷回收率低,难以避免砷污染问题。
湿法可分为硫酸体系、氯盐体系和碱性体系几大类,近几年针对碱性浸出工艺进行了大量研究,但该工艺成本相对较高,砷以砷酸钠形式进入溶液,需进行转化回收。
由于硫酸体系处理技术成熟,易与主工艺流程结合,工业生产中多采用硫酸浸出工艺处理烟尘,铅渣经火法熔炼生产电铅,或送铅冶炼企业进行处理,高砷浸出液多采用二氧化硫还原生产三氧化二砷,低砷溶液多采用铁盐法沉淀砷酸铁。
国家及行业相关污染防治政策及法案的出台,使得企业对危险废物无害化处理高度重视,含砷物料的就地协同处理及砷的产品化是今后发展的重要方向。
1我国铜冶炼工业背景1.1 国内铜矿冶概况近几年来,我国铜工业在规模和装备水平上有了很大的发展,各大炼铜企业的设备、技术已达到国际先进水平,高污染的工艺、设备被淘汰、替代,自主开发了闪速熔炼工艺;还引进了方圆氧底吹熔炼多金属捕集工艺,经本土化改造后,能耗、炉龄、废气排放等方面与欧美同类冶炼方法相当。
- 1、下载文档前请自行甄别文档内容的完整性,平台不提供额外的编辑、内容补充、找答案等附加服务。
- 2、"仅部分预览"的文档,不可在线预览部分如存在完整性等问题,可反馈申请退款(可完整预览的文档不适用该条件!)。
- 3、如文档侵犯您的权益,请联系客服反馈,我们会尽快为您处理(人工客服工作时间:9:00-18:30)。
doi:10.3969/j.issn.1007-7545.2018.04.002铜转炉白烟尘加压浸出工艺研究刘飞1,2,洪育民1,赵磊2(1.江西铜业集团公司贵溪冶炼厂,江西贵溪335424;2.北京矿冶科技集团有限公司,北京100160)摘要:针对铜冶炼转炉白烟尘中有价金属的综合利用,开展了加压浸出工艺研究。
在液固比6︰1(mL/g)、初始硫酸浓度0.6 mol/L、浸出温度120 ℃、氧分压0.6 MPa、浸出时间3 h、搅拌速度500 r/min的条件下,Cu、Zn 浸出率均高于95%,Cd浸出率大于90%,As、Fe浸出率可以控制在10%以下。
同步实现Cu、Zn、Cd高效浸出与As、Fe的抑制,有利于后续加压浸出液中的有价金属的分离。
关键词:白烟尘;加压浸出;铜;砷;铁中图分类号:TF811 文献标志码:A 文章编号:1007-7545(2018)04-0000-00Study on Pressure Leaching of Copper Converter White DustLIU Fei1,2, HONG Yu-min1, ZHAO Lei2(1.Guixi Smelter, Jiangxi Copper Corporation, Guixi 335424, Jiangxi, China;2. BGRIMM Technology Group, Beijing 100160, China)Abstract:To realize comprehensive utilization of valuable metals in copper converter white dust, pressure leaching process was carried out. The results show that leaching rate of metals is Cu>95%, Zn>95%, Cd>90%, As<10%, Fe<10% under the optimum conditions including L/S of 6︰1(mg/L), initial sulfuric acid concentration of 0.6 mol/L, leaching temperature of 120 ℃, oxygen partial pressure of 0.6 MPa, leaching time of 3 h, and stirring speed of 500 r/min. Valuable elements of copper, zinc and cadmium can be effectively separated from impurities of arsenic and iron which facilitates separation of valuable metals in lixivium.Key words:white dust; pressure leaching; copper; arsenic; iron国内大型铜冶炼厂多通过闪速熔炼、PS转炉吹炼和回转式阳极炉精炼等工序将铜精矿和废杂铜冶炼成能满足电解精炼工序需求的阳极板。
在冶炼过程中,入炉物料含有的微量Pb、Zn、As、Sb、Bi、Cd、In等元素在转炉白烟尘(以下简称白烟尘)中得到了富集。
白烟尘的处理工艺以湿法提取为主,其中硫酸体系浸出又占主流地位,如铜陵有色、金川公司、云南铜业、方圆铜业和中条山有色等企业均采用类似工艺[1-3]。
硫酸体系浸出的本质是利用Pb、Bi及其化合物几乎不溶于稀硫酸溶液的特性,通过浸出实现Pb、Bi与Cu、Zn、In、Cd等金属的分离[4-6]。
但对于含有较多硫化物、低价氧化物和复杂盐类化合物等成分复杂的白烟尘,采用常规硫酸体系浸出效果不是很理想,铜的浸出率不高,约75%,而且大量As、Fe等杂质元素进入浸出液(As浸出率~60%,Fe浸出率50%),加大了浸出液处理难度,拉长了工艺流程。
加压浸出是高温高压下强化浸出过程,同时利用氧气或空气中氧气对物料中的硫化物、低价氧化物进行氧化,可以有效提高元素浸出率,缩短浸出时间[7],在镍精矿、锌精矿、钼精矿、钨精矿、金精矿以及砷滤饼获得大规模的工业推广应用,但在白烟尘处理上尚未有应用。
徐志峰等[8]开展了高铜高砷白烟尘的加压浸出研究,在液固比5︰1(mL/g)、初始硫酸浓度0.74 mol/L、浸出温度180 ℃、氧分压0.7 MPa、浸出时间2 h的条件下,Cu、Zn浸出率分别约95%和99%,As浸出率约20%,Fe浸出率仅6%左右,实现了Cu、Zn与As、Fe较好的分离。
但在浸出温度180 ℃时,蒸汽分压1.0 MPa,再加上氧分压0.7 MPa,总压达到了1.7 MPa。
过高的温度和压力一方面会增加设备投资成本和生产运营成本;另一方面,氧分压过高,不利于安全生产,设备材质选择上也需要单独考虑。
因此,本研究以国内某大型铜冶炼厂白烟尘为原料,并结合该企业需求及现有工艺流程,探索较低温度、较低压力下白烟尘的高效浸出分离技术。
1 试验原料及研究方法试验所用白烟尘的化学成分(%):Cu 14.52、Pb 17.31、Zn 4.34、As 6.51、Fe 4.42、Bi 6.66、Cd 1.55、S 9.29。
其中,铜的物相组成为(%):硫酸铜25.46、硫化铜30.27、氧化铜12.37、氧化亚铜15.61、其他16.29。
收稿日期:2017-10-17基金项目:国家高技术研究发展计划(863计划)项目(2013AA064002)作者简介:刘飞(1980-),男,江苏泗洪人,工学硕士,高级工程师.白烟尘加压浸出试验在2.0 L机械搅拌衬钛高压釜中进行。
首先往钛胆中加入100 g白烟尘、一定体积稀硫酸及分散剂,将其放入加压釜中加盖密封,升温至预设值、补充氧气至预设值反应一定时间。
浸出结束后通水冷却和降压,将浸出渣烘干后送样分析。
2 结果与讨论白烟尘中Zn、Cd属于易浸出元素,在各次试验中Zn的浸出率均高于95%,Cd的浸出率均高于90%,Pb、Bi几乎未浸出。
因此下文仅讨论不同工艺条件下Cu、As和Fe等元素浸出率的变化。
2.1 浸出温度的影响在液固比6︰1(mL/g,下同)、氧分压0.6 MPa、初始硫酸浓度0.6 mol/L、搅拌速度500 r/min、不同温度条件下浸出3 h,试验结果见表1。
从表1可知,随着温度的上升,Cu的浸出率随之增加,当温度达到120 ℃后,Cu的浸出率变化很小。
随着温度的上升,As、Fe浸出率随之下降,当温度达到120 ℃后,As、Fe浸出率均可控制在10%以内,因此,浸出温度选择120 ℃。
表1 不同浸出温度条件下浸出率Table 1 Leaching rate of elements under different temperature /%浸出温度/℃Cu As Fe80 53.23 40.46 53.27100 78.45 22.48 27.87120 96.21 9.65 4.43140 96.68 8.26 6.172.2 浸出时间的影响试验条件:液固比6︰1、初始硫酸浓度0.6 mol/L、浸出温度120 ℃、氧分压0.6 MPa、搅拌速度500 r/min。
浸出时间试验结果如表2所示。
随着浸出时间的增加,Cu的浸出率随之增加,当浸出时间达到3 h后,Cu的浸出率变化很小。
As、Fe在加压浸出过程应是“先浸出后沉淀”的过程,浸出时间达到3 h后,As、Fe在浸出液和浸出渣中基本达成较平衡,As、Fe浸出率变化不大。
因此,选择浸出时间为3 h。
表2 不同浸出时间条件下浸出率Table 2 Leaching rate of elements under different time /%浸出时间/h Cu As Fe2 80.45 21.46 16.273 96.21 9.65 4.434 96.58 10.43 7.875 95.79 7.21 6.652.3 液固比的影响在初始硫酸浓度0.6 mol/L、浸出温度120 ℃、氧分压0.6 MPa、浸出时间3 h、搅拌速度500 r/min的条件下,进行不同液固比试验,结果如表3所示。
表3表明,随着液固比的增大,Cu的浸出率随之增加,但As、Fe浸出率变化不明显。
当液固比达到6︰1后,继续增大液固比对Cu的浸出率影响很小。
较小的液固比可以提高溶液中有价金属离子浓度、降低设备投资和节约生产成本,因此选择液固比6︰1较为合适。
表3 不同液固比条件下浸出率Table 3 Leaching rate of elements under different L/S /%液固比Cu As Fe4︰1 86.43 8.72 7.345︰1 90.68 10.02 3.866︰1 96.21 9.65 4.437︰1 95.97 10.34 6.512.4 初始硫酸浓度的影响研究了不同初始硫酸浓度对Cu、As和Fe等元素浸出率的影响,试验条件:液固比6︰1、浸出温度120 ℃、氧分压0.6 MPa、浸出时间3 h、搅拌速度500 r/min。
根据表4所示试验结果可知,随着初始硫酸浓度的增大,Cu的浸出率随之增加,当初始硫酸浓度达到0.6 mol/L后,继续增大初始硫酸浓度对Cu的浸出率影响很小。
Fe、As在加压浸出条件下水解进入渣中,浸出终点溶液中Fe、As与H2SO4达成平衡,在保障铜的浸出率的同时,控制较低的酸度,有助于抑制Fe、As的溶出。
因此,初始硫酸浓度选择0.6 mol/L。
表4 不同初始硫酸浓度条件下浸出率Table 4 Leaching rate of elements under different initial sulfuric acid concentration /% 初始硫酸浓度/(mol·L-1) Cu As Fe0.5 82.27 8.65 5.920.6 96.21 9.65 4.430.7 96.57 25.69 20.340.8 97.01 50.36 32.872.5 氧分压对浸出率影响试验条件:液固比6︰1、初始硫酸浓度0.6 mol/L、浸出温度120 ℃、浸出时间3 h、搅拌速度500 r/min,试验结果见表5。
从表5可知,随着氧分压的增大,Cu的浸出率随之增加,当氧分压达到0.6 MPa后,继续增大氧分压对Cu的浸出率影响很小。
氧分压对As、Fe浸出率影响很小。
由于较低的氧分压有利于安全生产,因此氧分压选择0.6 MPa。