一种复合材料车轮的设计解析
高强度碳纤维复合材料轮毂的设计与制造

高强度碳纤维复合材料轮毂的设计与制造一、背景介绍复合材料是近年来航空、汽车等高速运动设备中广泛采用的材料。
其中,碳纤维复合材料由于具有高强度、高弹性模量和较小的密度等优点,成为轮毂、车架、车身等几乎所有部件的理想材料。
轮毂是汽车、飞机等高速运输工具的核心部件,承受车辆运行时传来的重力、刹车、加速等各种力,对车辆的安全和性能有巨大的影响。
高强度碳纤维复合材料轮毂的设计和制造是一个前沿且具有挑战性的科技难题。
二、设计要求1.耐久性轮毂需要满足耐久性的要求,以保证它的使用寿命。
高速运动中,轮毂承受着巨大的风荷载和离心力。
这会导致材料疲劳、裂纹等问题。
因此应采用高强度、高韧性的碳纤维复合材料,并考虑制造工艺和受力部位的优化设计。
2.重量轻车辆重量是一个重要的考虑因素。
由于轮毂是转动的质量,轮毂的轻量化可以减小车辆的总重量,提高其性能。
碳纤维材料密度小于金属材料,因此设计时可以通过减小轮毂尺寸、减少配重等方法来实现重量轻量化。
3.制造成本和复杂度高强度碳纤维复合材料的制造工艺相对复杂,生产成本高。
同时,纤维方向的布局和层数的选择等制造参数,对轮毂性能具有重要影响。
因此,制造成本和复杂度也是设计中需要考虑的一个重要因素。
三、材料选择碳纤维复合材料的基本结构是由高强度碳纤维和高韧性树脂组成。
在选择碳纤维时,应考虑弹性模量、强度和密度等性能指标。
目前,聚合物基树脂是一种常用的基质材料,具有较好的机械性能和耐热性能,而且价格相对较低。
与此同时,也可以考虑使用环氧材料,因为它的强度、刚度和弹性模量等方面优于聚合物基树脂。
不过生产成本会稍高一些。
四、设计方案轮毂的设计需要考虑静态和动态受力条件。
在静态方面,应考虑轮毂的重量,并在必要时增加配重来保证稳定性。
在动态方面,应考虑材料的疲劳寿命和减小轮毂的空气力学阻力。
1.设计工艺设计者应采用自动化计算方法,通过各种仿真和强度分析工具来确保设计稳健性和可行性。
设计方法可以借鉴冲压、铸造等传统材料的工艺方法,适当采用机械加工或人工制造等方法。
复合材料储能飞轮包容环的结构设计

复合材料储能飞轮包容环的结构设计复合材料储能飞轮包容环的结构设计随着人们对能源的需求不断增加,能源储存技术日益成为研究的热点。
复合材料储能飞轮作为一种新型的能量储存系统,具有高速、高精度、长寿命等特点,逐渐受到重视。
在复合材料储能飞轮系统中,包容环是一个非常重要的组件,它通过与储能飞轮转子紧密接触,实现转子的能量传递和储存。
为了提高复合材料储能飞轮的性能,包容环的结构设计也变得至关重要。
复合材料储能飞轮的包容环主要由碳纤维复合材料和金属材料组成。
碳纤维复合材料具有高强度、高刚度、低密度等优点,可以增强包容环的耐久性和承载能力;金属材料则具有良好的导热性和导电性,有助于将储能飞轮中的热能和电能传递到外部系统中。
因此,在包容环的设计中需要充分发挥这两种材料的优点,以实现最优的性能表现。
首先,在碳纤维复合材料的选择上,需要考虑其纤维织布方式、环向层数、力学性能等因素。
对于环向层数的设计,需要根据储能飞轮的具体转速和负载情况进行调整,以保证碳纤维复合材料的强度和刚度能够满足实际需求。
此外,也需要对碳纤维复合材料方向的分布进行优化,以减小热应力和微裂纹对包容环的影响,提高其使用寿命和可靠性。
其次,在金属材料的选择上,需要考虑其尺寸、形状等因素对电磁特性的影响。
特别是在高速、高功率储能飞轮中,由于飞轮产生的电磁场很强,所以金属材料的导电性和导热性会对整个系统的性能产生重要影响。
因此,在包容环的设计中,需要选择高导热、高导电的材料,并且对金属材料的形状和排布进行优化,以提高整个系统的热管理和电能传输效率。
最后,为了进一步提高复合材料储能飞轮的性能,包容环的结构也需要进行合理设计。
一般来说,包容环可以分为内外两层,内层负责直接与转子接触,外层则是用来支撑和保护内层的材料。
在内层的设计上,需要考虑包容环与转子之间的间隙和接触面积,以实现高效的能量传递和储存。
在外层的设计上,则需要考虑包容环的刚度和耐久性,以保证其能够承受高速旋转和复杂负载情况下的磨损和冲击。
复合材料飞轮的设计分析
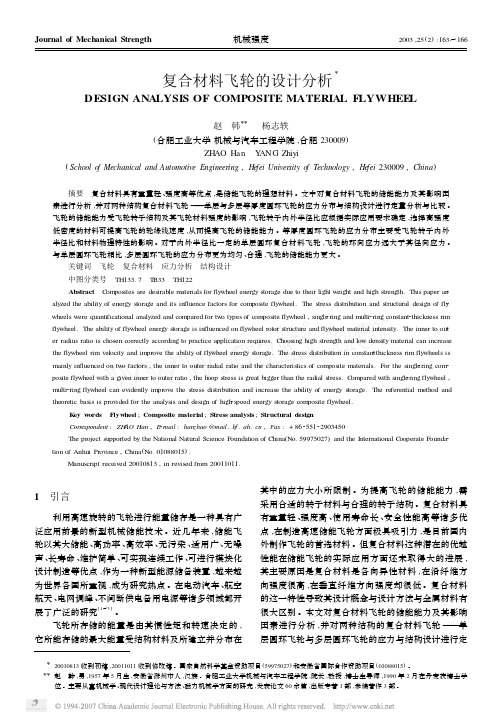
汪小银_基于Altair HyperWorks热塑性复合材料车轮的轻量化设计及强度分析
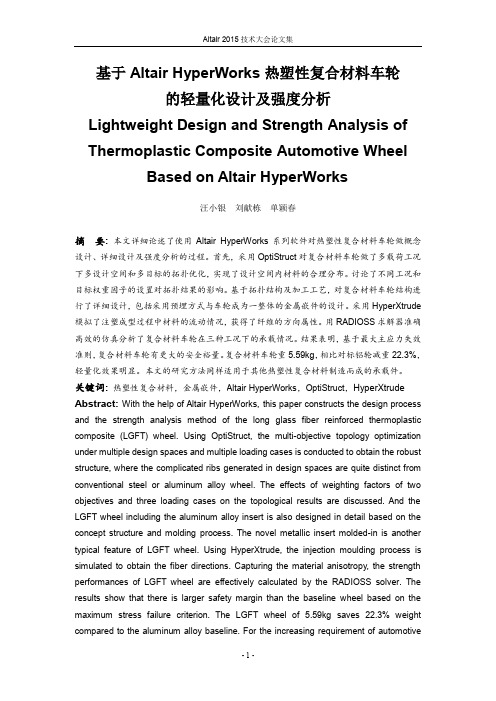
基于Altair HyperWorks热塑性复合材料车轮的轻量化设计及强度分析Lightweight Design and Strength Analysis of Thermoplastic Composite Automotive WheelBased on Altair HyperWorks汪小银刘献栋单颖春摘要: 本文详细论述了使用Altair HyperWorks系列软件对热塑性复合材料车轮做概念设计、详细设计及强度分析的过程。
首先,采用OptiStruct对复合材料车轮做了多载荷工况下多设计空间和多目标的拓扑优化,实现了设计空间内材料的合理分布。
讨论了不同工况和目标权重因子的设置对拓扑结果的影响。
基于拓扑结构及加工工艺,对复合材料车轮结构进行了详细设计,包括采用预埋方式与车轮成为一整体的金属嵌件的设计。
采用HyperXtrude 模拟了注塑成型过程中材料的流动情况,获得了纤维的方向属性。
用RADIOSS求解器准确高效的仿真分析了复合材料车轮在三种工况下的承载情况。
结果表明,基于最大主应力失效准则,复合材料车轮有更大的安全裕量。
复合材料车轮重5.59kg,相比对标铝轮减重22.3%,轻量化效果明显。
本文的研究方法同样适用于其他热塑性复合材料制造而成的承载件。
关键词:热塑性复合材料,金属嵌件,Altair HyperWorks,OptiStruct,HyperXtrude Abstract:With the help of Altair HyperWorks, this paper constructs the design process and the strength analysis method of the long glass fiber reinforced thermoplastic composite (LGFT)wheel. Using OptiStruct, the multi-objective topology optimization under multiple design spaces and multiple loading cases is conducted to obtain the robust structure, where the complicated ribs generated in design spaces are quite distinct from conventional steel or aluminum alloy wheel. The effects of weighting factors of two objectives and three loading cases on the topological results are discussed. And the LGFT wheel including the aluminum alloy insert is also designed in detail based on the concept structure and molding process. The novel metallic insert molded-in is another typical feature of LGFT wheel. Using HyperXtrude, the injection moulding process is simulated to obtain the fiber directions. Capturing the material anisotropy, the strength performances of LGFT wheel are effectively calculated by the RADIOSS solver. The results show that there is larger safety margin than the baseline wheel based on the maximum stress failure criterion. The LGFT wheel of 5.59kg saves 22.3% weight compared to the aluminum alloy baseline. For the increasing requirement of automotivecomponents lightweight design, the method and consideration in this paper may also provide some ways for the design and strength analysis of other carrying structures made of thermoplastic composite.Key words:thermoplastic composite wheel, metallic insert, Altair HyperWorks,OptiStruct,HyperXtrude1 引言车轮是汽车不可或缺的关键安全零部件之一,除了承受垂直载荷外,还要承受因车辆起动、制动和行驶过程中转弯以及路面冲击等产生的多向动态载荷。
复合材料汽车轮毂的成型技术

复合材料汽车轮毂的成型技术作者:李英翔李行飞来源:《企业文化》2017年第05期摘要:随着人类生活水平不断提高,汽车就成为了人们出行的必备代步工具。
汽车的轮毂对汽车来说是很重要的,我们的汽车的绝大多数重量都是依靠轮毂来承担,轮毂的质量将直接决定着汽车的质量和人们的出行安全,下面我们就来简单谈谈复合材料汽车轮毂的成型技术的相关问题。
关键词:复合材料;汽车轮毂;成型技术复合材料相对于传统的金属材料来说具有很大的优势,它具有轻质高强、耐腐蚀和抗蠕变等优点,并且符合社会上倡导的保护环境的要求,所以说使用复合材料来进行汽车轮毂的生产是很有必要的。
汽车在行驶的过程中,汽车的制动是很重要的,它是保障人们安全的很重要前提,复合材料制造的轮毂不仅具有减轻轮毂重量的效果,还能在很大程度上增强汽车的制动效果,对提高汽车的行驶安全是很重要的。
除此之外,复合材料制造出来的轮毂还可以减少燃料的消耗,对减少汽车的燃料消耗是很有效的。
一、复合材料冲击性能研究(一)复合材料层板的制备在进行复合材料层板的制备的时候,我们要选择合适的技术,这样才能保证生产出来的层板符合我们的要求。
我们在制备的时候一般是使用热压罐成型工艺,在制备的过程中我们要在不同的阶段保证制备环境中的空气温度、模具温度、保压压力和保压时间。
我们把制备的过程划分为三个阶段,这三个阶段分别要掌握好不同的温度、压力和时间,这样才能保证生产出来复合材料层板的质量。
第一个阶段我们将空气温度保持在95摄氏度,模具温度是90摄氏度,保压压力是400千帕,第二阶段的时候就要适当的将这些温度、压力和时间升高,并保持在合适的水平,第三个阶段再适度提高,保证复合材料层板的质量,如表1所示。
(二)冲击性能测试及分析我们在进行冲击性能测试的时候要选取适量的样本,在选取样本的时候要注意不能只选取一个样本,因为这样容易产生偶然性,造成测试结果的不准确。
我们可以把测试的样本分成若干组,每个小组中有至少五个样本,保证样本的数量就是保证测量结果的准确性。
基于电机复合材料的轮毂结构设计

基于电机复合材料的轮毂结构设计电机复合材料在工业领域中越来越受到关注,主要应用于轮毂、车身等结构件的制造中,取代传统的金属材料。
而基于电机复合材料的轮毂结构设计也逐渐成为研究热点。
第一部分:电机复合材料1、电机复合材料的定义电机复合材料是一种由两种或两种以上的材料在微观上混合而成的新材料,具有比金属材料更好的机械性能,更高的强度和韧性。
2、电机复合材料的特点电机复合材料主要有以下几个特点:(1)重量轻:与金属材料相比,电机复合材料的比重更小,可以降低结构件的重量,提高汽车、航空器等交通工具的运行效率。
(2)强度高:电机复合材料的强度比金属材料更高,可以提高结构件的承载能力,让车辆在高速行驶中更加稳定。
(3)耐腐蚀:电机复合材料的耐腐蚀性能比金属材料更好,可以延长工业设备的寿命。
(4)耐热性好:电机复合材料具有较好的耐热性能,能够适应各种恶劣环境下的使用。
3、电机复合材料的应用领域电机复合材料在航空、航天、汽车、船舶、电子、建筑等领域中都有广泛的应用。
特别是在航空、航天和汽车制造领域中,电机复合材料代替金属材料的应用越来越多。
第二部分:基于电机复合材料的轮毂结构设计1、传统轮毂材料的缺陷传统的轮毂材料主要是金属材料,具有一定的强度和韧性,但也存在许多缺陷。
例如:(1)重量大:金属材料的比重大,会让轮毂增加额外的负担,降低汽车的耗能效率。
(2)耐腐蚀性差:长时间的使用容易导致金属材料的氧化或腐蚀,降低汽车的寿命。
(3)强度有限:金属材料的强度和韧性相比于电机复合材料优劣很大,不能满足汽车日益增长的性能需求。
2、基于电机复合材料的轮毂结构设计的优点采用电机复合材料作为轮毂的材料,既能保持轮毂的强度和韧性,又能克服传统轮毂的缺点:(1)轮毂重量轻:电机复合材料的比重比金属材料小,因此可以有效降低轮毂的总重量,提高车辆的运行效率。
(2)轮毂结构更为复杂:通过电机复合材料的加工工艺,轮毂设计可以更加复杂,以适应不同的路况和多样化的车型。
- 1、下载文档前请自行甄别文档内容的完整性,平台不提供额外的编辑、内容补充、找答案等附加服务。
- 2、"仅部分预览"的文档,不可在线预览部分如存在完整性等问题,可反馈申请退款(可完整预览的文档不适用该条件!)。
- 3、如文档侵犯您的权益,请联系客服反馈,我们会尽快为您处理(人工客服工作时间:9:00-18:30)。
一种复合材料车轮的设计解析
作者:张伟肖令
来源:《中国新技术新产品》2016年第05期
摘要:本文针对复合材料车轮紧固问题,设计一种轻金属夹层结构,实现车轮的可靠连接。
并分析了车轮转矩的传递,以及复合材料受压部位的压缩强度。
关键词:车轮;复合材料;设计
中图分类号:TQ330 文献标识码:A
碳纤维增强复合材料具有轻质高强的特点,在民用领域的应用日益广泛。
碳纤维本身耐高温、耐摩擦、导电、导热及耐腐蚀,外形有显著的各向异性、柔软、可加工成各种织物,沿纤维轴方向表现出很高的强度。
将碳纤维作为复合材料的增强材料,与采用其它材料增强的复合材料相比,具有显著的性能优势。
碳纤维增强复合材料的比强度、比模量综合指标,在现有结构材料中是最高的。
2020年,中国乘用车平均燃料消耗量标准为5L/100km,同时将实施更加严格的CO2排放标准。
政策制定反映出,能源短缺及环境污染问题已成为国家社会关注的重点问题,也是当前及未来制约汽车产业可持续发展的突出问题。
无论是从社会效益还是经济效益来考虑,低能耗、低排放的汽车都是未来发展的需要。
轻量化是汽车节能减排的重要手段,已成为汽车发展的必然趋势。
有研究表明:汽车质量每下降10%,油耗下降约6%~8%,排放量下降13%。
汽车车轮作为簧下质量,对整车轻量化具有放大效应。
更小的簧下质量同时意味着悬挂系统拥有更好的动态响应能力以及车辆的操控性。
将碳纤维增强复合材料应用于汽车车轮与目前铝合金车轮相比,可实现车轮轻量化30%~50%,对于汽车节能降耗及车辆舒适性具有重要意义。
澳大利亚的Carbon Revolution公司在连续纤维增强复合材料车轮方面进行了广泛研究,德国梅赛德斯-奔驰在长纤维(玻纤)增强复合材料车轮方面进行了研究。
中国此方面的研究处于起步阶段。
在将碳纤维复合材料应用于车轮设计的过程中,车轮的紧固问题尤为突出。
采用现有的铝合金车轮设计方案直接通过螺栓装配车轮后,在疲劳试验过程中出现螺栓扭矩下降。
为解决此问题,保证连接可靠性,设计了汉堡结构方案,如图1所示。
并对此结构的转矩和压缩性能进行了分析。
1 转矩分析
驱动轴通过螺栓将转矩传递给驱动轮。
驱动轮组成包括正面轻合金盘、复合材料体、安装面轻合金盘和轮胎。
复合材料体置于两块轻合金盘之间。
1.1 基本原理
根据汽车行驶的附着条件,地面对轮胎切向反作用力的极限值(最大值)为附着力Fxmax。
Fxmax=Fzφ
式中:Fz—地面作用在车轮上的法向反力;φ—附着系数,与路面和轮胎有关。
常见路面的平均附着系数见表1。
表1 常见路面的平均附着系数
路面条件附着系数
干沥青路面 0.7~0.8
湿沥青路面 0.5~0.6
干燥的碎石路 0.6~0.7
干土路 0.5~0.6
湿土路 0.2~0.4
滚压后的雪路 0.2~0.3
1.2 设计参数
目标车型靠前轮驱动,驱动轮承受车身质量为500kg,车轮规格17×7英寸,偏距38mm,布置5个螺栓孔,螺栓孔节圆直径100mm,轮胎型号225/45 R17,采用10.9级M14×1.5螺栓进行紧固。
1.3 受力分析
汽车在附着系数最大的路面行驶时车轮获得最大切向反作用力,此时车轮传递转矩最大。
以在平地直线行驶时的情况进行简化分析。
驱动轮受力如图2所示。
其中:Fv—车身的垂直压力;T—驱动轴转矩;Gw—车轮自重;Fx—地面对轮胎切向反作用力;Fz—地面对车轮的法向反力。
地面对轮胎切向反作用力为Fx= Fzφ=(Fv+Gw)φ。
其中Fv=500kg ×9.81N/kg=4905N,车轮自重Gw=18kg× 9.81N/kg=176.6N,取附着系数φ为干沥青路面时的最大值0.8,则
Fxmax=(4905+176.6)×0.8=4065.3N
由JATAMA手册可查得225/45 R17轮胎的动载半径为Rdl=0.307m,则车轮可传递的最大转矩为:
Tmax=Fxmax×Rdl=4065.3N×0.307m=1248.0Nm
1.4 转矩传递分析
车轮受到来自驱动轴的转矩T=T1+ T2,如图3所示。
式中:T1—驱动轴通过螺栓传递到车轮的转矩;T2—驱动轴通过安装面之间的摩擦力传递到车轮的转矩。
假设T2为零,则驱动轴的转矩完全通过螺栓传递至车轮。
在车轮结构中,转矩通过正面轻合金盘传递至复合材料体。
T2为零时是正面合金盘传递转矩最大情况,需保证其与复合材料体之间不发生滑动。
1.5 螺栓预紧力
车轮正面轻合金盘如图4所示。
外半径R为64mm,螺栓孔半径为12mm,中心孔半径r 为28mm。
根据装配技术要求,单个M14螺栓的预紧力矩为Mt=130±10Nm,其预紧力为:
式中:K—拧紧力系数;d—螺纹公称直径。
表2常见表面的拧紧力系数
摩擦表面状况有润滑无润滑
精加工表面 0.10 0.12
一般加工表面 0.13~0.15 0.18~0.21
表面氧化 0.20 0.24
镀锌 0.18 0.22
干燥的粗加工表面 0.26~0.3
根据车轮弯曲疲劳试验技术要求,螺栓扭矩下降达到初始扭矩的30%判定为失效。
并且此时正面轻合金盘与复合材料体之间的压力最小,极易发生相对滑动。
此时,M14螺栓最小残余预紧力矩为:
Mtmin=0.7×120Nm=84Nm
正面轻合金盘的螺栓孔为精加工表面,选用拧紧力系数0.12,则5个M14螺栓的最小残余预紧力合力为:
1.6 轻合金盘摩擦转矩分析
螺栓孔简化不计,根据圆环摩擦转矩的传递公式,正面轻合金盘通过摩擦力传递到复合材料体的最小转矩:
由1.4分析可知,T3=T1=T-T2,即12087.0u=1248.0
可得
选用安全系数1.2,则保证正面轻金属盘与复合材料体之间的摩擦系数大于0.12,即满足转矩传递条件。
具体措施是增加二者的表面粗糙度或采用胶接。
2 复合材料耐压分析
对于此种结构,碳纤维增强复合材料体的另一种失效模式是发生压缩破坏。
2.1 压应力计算
由1.5可知,复合材料体所受最大压力:
通过Catia V5软件测量数模,复合材料体的承压面积S为7963.94mm2,计算可得复合材料体受压应力为:
2.2 压应力测试
选取24mm长,16mm宽的样块进行压缩测试,其应力-应变曲线如图5所示。
根据测试结果,可计算出复合材料体的压缩强度为:
由此可知,螺栓紧固部位的复合材料体压缩性能满足要求。
结语
此次研制的复合材料车轮已进行多次试验,紧固问题得到有效解决,多项设计方案获得实用新型专利。
同时在13°冲击试验、弯曲疲劳试验和径向疲劳试验方面取得了突破性进展。
参考文献
[1]国务院关于印发节能与新能源汽车产业发展规划(2012~2020年)的通知[Z].国发〔2012〕22号.。