直接还原铁进高炉
电炉炼钢发展将需要大量直接还原铁

电炉炼钢发展将需要大量直接还原铁目前,全球钢铁炼钢流程主要有两种:高炉—转炉炼钢和废钢—电炉炼钢。
我国炼钢方式主要是以消耗铁矿石的高炉—转炉炼钢为主,对铁矿石原料的依赖度高达80%,而长期的转炉炼钢,给环境带了较重的负荷。
电炉炼钢具有工序短、投资省、建设快、节能减排效果突出等优势,据统计,电炉炼钢流程相对于高炉—转炉流程节省能源60%,减少废气、废水、废渣排放86%、76%、72%。
废钢是一种可无限循环使用的节能再生资源,多用1吨废钢可节约0.4吨焦炭或1吨原煤,可减少1.7吨精矿粉的消耗,减少4.3吨原矿开采,可减少1.6吨二氧化碳的排放。
发达国家和地区普遍重视发展电炉短流程炼钢生产工艺。
2015年,美国电炉钢比例为62.7%,欧洲电炉钢比例为39.4%,韩国电炉钢比例为30.4%,日本电炉钢比例为22.9%,而我国电炉钢比例仅为6.1%。
大力发展电炉短流程炼钢工艺,对我国钢铁行业的结构调整、绿色环保、可持续发展具有重要的意义。
长期以来,废钢供应不足、价格高昂和电力价格昂贵曾是限制我国废钢电炉炼钢的主要因素。
近10年来,我国的钢产量平均增长率超过10%,钢铁蓄积量正在大幅度增长,2015年我国的钢铁蓄积量达到80亿吨,“十三五”期间我国钢铁产业的废钢年供应量将达到1.5亿吨~2.5亿吨,废钢比将达到20%以上;目前实际的供应量更高。
随着新环保法实施,以及钢铁业去产能和结构调整工作的推进,以中频炉为代表的落后产能被全面清查和关闭,我国废钢大量积存,废钢价格大幅降低。
同时,我国电力基础设施建设蓬勃发展,电力供应充足,局部地区电力产能过剩、电价大幅降低,限制电炉炼钢的各种问题得到了有效解决。
专家预计,2025年我国电炉炼钢比例将高达30%以上。
电炉炼钢流程具有诸多优势,但也存在固有的问题,如废钢利用愈多、循环冶炼次数愈多,钢中残余元素(主要是有色金属元素)含量愈高,使电炉钢质量下降。
美国对过去25年生产和使用的碳钢进行分析发现:碳钢中的铜含量增加了20%,镍、铬含量增加了50%,锡含量增加了100%。
气基竖炉直接还原炼铁简介

气基竖炉直接还原炼铁简介XX热能技术有限公司(公章)二零零七年八月八日一、总论1.1 项目背景及项目概况项目起源于焦煤冶金的固有缺陷、优质钢市场需求强劲、废钢严重短缺以及我国天然气资源不足的现实。
自从1735年英国人亚·德尔比发明了煤炭炼焦的方法,采用焦炭的冶炼方法(如高炉)已经取得巨大进步,达到了空前完善的程度,提供的金属材料品种齐全、质量优良、数量巨大,为人类物质文明和社会进步做出了巨大贡献。
然而,随着全球环境和资源压力的日益增大,传统工艺的弊端日益突出,体现在:严重依赖于焦煤;冶金反应重复进行;优质钢生产严重受限;对复杂的多金属矿处理显得无能为力;工厂生产规模大、工艺环节多、需要巨额投资;焦化、烧结、高炉等铁前系统产生的大量烟气、粉尘及水污染;焦化、烧结、高炉等铁前系统的流程长、工艺复杂,导致热效率低,能源浪费严重等。
近年来,随着我国钢铁产量逐年攀升,每年焦煤开采量至少为47425万吨。
按煤炭详查资源总量估计,2070年以后我国的焦煤资源将面临枯竭,传统的焦煤冶金工艺将无法进行正常生产。
与此相反,大量的非焦煤资源在冶炼工艺中却无法得到充分利用,因此开发和采用非焦煤炼铁工艺已迫在眉睫。
非焦煤炼铁工艺是指不使用焦炭进行炼铁生产的各种工艺方法。
按工艺特征、产品类型及用途,可分为直接还原法和熔融还原法两大类别。
直接还原法(Direct Reduction)是指“以气体燃料、液体燃料或非焦煤为能源和还原剂,在天然矿石(粉)或人造团快呈固态的软化温度以下进行还原获得金属的方法”。
熔融还原(Smelting Reduction)则“以非焦煤为能源和还原剂,在高温熔融状态下进行金属氧化物的还原,得到含碳的液态金属”。
与直接还原的不同之处是,熔融还原的发展目标只是探索和推广用煤炭代替焦炭的冶炼方法,其产品还是与传统冶炼工艺一样的液态产品,如铁水。
目前,全世界工业规模的直接还原法已有十几种,而大多数熔融还原工艺还处于研发阶段,已商业化的只有COREX。
直接还原铁生产工艺及发展方向

直接还原铁(海绵铁)生产工艺及发展方向习惯上,我们把铁矿石在高炉中先还原冶炼成含碳高的生铁,而后在炼钢炉内氧化,降低含碳量并精炼成钢,这项传统工艺,称作间接炼钢方法;在低于矿石熔化温度下,通过固态还原,把铁矿石炼制成铁的工艺,称作直接炼铁(钢)法或者直接还原法,用这种方法生产出的铁也就称作直接还原铁(即DRI)。
由于这种铁保留了失氧时形成的大量微气孔,在显微镜下观察形似海绵,所以直接还原铁也称之为海绵铁。
一、直接还原铁(海绵铁)的用途直接还原铁是精铁粉在炉内经低温还原形式的低碳多孔状物质,其化学成分稳定,杂质含量少(碳、硅含量低),主要用作电炉炼钢的原料,也可作为转炉炼钢的冷却剂,如果经二次还原还可供粉末冶金用。
一次还原铁粉(海绵铁)的主要用途有:①作为粉末冶金制品的原料,耗用量约占铁粉总耗用量的60~80%;②作为电焊条的原料,在药皮中加入10~70%铁粉可改进焊条的焊接工艺并显著提高熔敷效率;③作为火焰切割的喷射剂,在切割钢制品时,向氧-乙炔焰中喷射铁粉,可改善切割性能,扩大切割钢种的范围,提高可切割厚度;④还可作为有机化学合成中的还原剂、复印机油墨载体等。
近年来由于钢铁产品朝小型轻量化、功能高级化、复合化方向发展,故钢材中非金属材料和有色金属使用比例增加,致使废钢质量不断下降。
废钢作为电炉钢原料,由于其来源不同,化学成分波动很大,而且很难掌握、控制,这给电炉炼钢作业带来了极大的困难。
如果用一定比例的直接还原铁(30~50%)作为稀释剂与废钢搭配不仅可增加钢材的均匀性,还可以改善和提高钢的物理性质,从而达到生产优质钢的目的。
因此,直接还原铁(海绵铁)不仅仅是优质废钢的替代物,还是生产优质钢材必不可少的高级原料(天津无缝钢管公司国外设计中就明确要求必须配50%的直接还原铁(海绵铁))。
根据国外报导,高功率电炉冶炼时,炉料搭配30~50%直接还原铁,生产率提高10~25%,作业率提高25~30%。
外热式竖炉直接还原法

外热式竖炉直接还原法工艺过程该法的还原过程实质是煤中的碳在高温下气化生成的CO与铁矿石中铁氧化物发生多相高温冶金物化反应。
还原剂可用非结焦煤。
工艺流程见图。
铁矿石、煤与石灰石分别闭路破碎、筛分,取合格粒级配料与混合,混合料从炉顶部加入,随下部排料机构转动,物料沿炉身干燥、预热、还原、冷却各段逐步下降。
竖炉燃烧室的加热采用气体或液体燃料。
燃烧室的热量通过碳化硅砖墙传入竖炉还原反应室并传导至炉料中心。
还原后的排出料包括直接还原铁、煤灰和未反应完的残煤。
经磁选分离,大于3mm的直接还原铁入库;大于3mm 的剩煤可作返煤掺入新煤中再利用。
竖炉由装料漏斗、干燥段、预热段、还原段、水箱冷却段及螺旋排料机构等组成。
反应室上部是炉料预热段,由一排5根φ280mm×3.1m的AISl310s 不锈钢管组成,炉料在钢管内既有均匀下料,又有受燃烧废气预热的作用。
反应室中部为还原段,由碳化硅砖砌成,高度10.4m,截面呈矩形,上口小,下口大,炉型窄、长、高,加热面置于窄向两侧。
一座竖炉内含6个反应室,单室有效容积为7.2m。
反应室外部为燃烧室,炉墙长边方向每边沿高度布置15个短焰烧嘴,窄边方向每端沿高度布置10个长焰烧嘴。
反应室下部是水箱冷却段。
炉子底部是4个水平带水冷套的液压式螺旋排料机,既可排料又起控制炉料在反应室内停留时间的作用。
其他设备及辅助设施包括原燃料的破碎系统、竖炉上料提升卷扬翻斗、移动式布料机、磁选机、残煤和煤灰分离器、炉顶气与燃烧废气返回利用系统。
此外,还有配料、加料、排料和温度自动控制仪表、热工仪表等。
设备构造较简单,运动部件少,电耗较低。
操作中主要控制还原温度、还原时间和排料速度。
这些参数随不同原料特性而变化。
还原段温度一般控制在1000~1050℃,对难还原矿可稍高一些,但应考虑碳化硅砖的承受能力,注意碳化硅砖的保护。
依据直接还原铁所需的金属化率,可调整排料速度以控制炉料在还原段停留的时间。
高炉炼铁还原过程

自然界中没有天然纯铁,在铁矿石中铁与氧结合在一起,成为氧化物,它们是Fe2O3'Fe3O4和FeO:Fe2O3Fe3O4FeO原子比xO/xFe1.51.331.0理论含氧量/?3027铁矿精粉)生产,酸性氧化球团矿的品位可达68%,i02含量在1%~2%;(2)无烧结矿具有的大气孔。
所有气孔都以微气孔形式存在,有利于气-固相还原;(3)Fe0含量低(一般在1%左右),矿物主要是FqO,还原性好。
由于其Si02含量低,因此高温(1200°C)还原性更优于烧结矿和天然矿;(4)冷强度好,每个球可耐2,00~~'00k:"f)的压力,粒度均匀,运输性能好;(5) CO+H20=C02+H2(1-3-20)3(1-3-81-3-9钢铁生产中的重要环节。
这种方法是由古代竖炉炼铁发展、改进而成的。
尽管世界各国研究发展了很多新的炼铁法,但由于高炉炼铁技术经济指标良好,工艺简单,生产量大,劳动生产率高,能耗低,这种方法生产的铁仍占世界铁总产量的95%以上。
炼铁的原理(怎样从铁矿石中炼出铁)用还原剂将铁矿石中的铁氧化物还原成金属铁。
铁氧化物(Fe2O3、Fe3O4、FeO)+还原剂(C、CO、H2)铁(Fe)反应的化学方程式分别为Fe2O3+3CO=2Fe+3CO2,Fe3O4+4CO=3Fe+4CO2等炼铁的方法(1)直接还原法(非高炉炼铁法)(2)高炉炼铁法(主要方法)编辑本段原料及其作用(1)铁矿石:(一般为赤铁矿、磁铁矿)提供铁元素。
冶炼一吨铁大约需要1.5—2吨矿石。
(2)焦炭:提供热量;提供还原剂;作料柱的骨架。
冶炼一吨铁大约需要500Kg焦炭。
反应方程式C(焦炭)+O2=CO2 C焦炭+CO2=2CO(3)熔剂:(石灰石、白云石、萤石)使炉渣熔化为液体;去除有害元素硫(S)、除去杂质(4)空气:为焦碳燃烧提供氧、提供热量。
直接还原炼铁

直接还原炼铁在低于矿石熔化温度下,通过固态还原,把铁矿石炼制成铁的工艺过程。
这种铁保留了失氧时形成的大量微气孔,在显微镜下观察形似海绵,所以也称为海绵铁;用球团矿制成的海绵铁也称为金属化球团。
直接还原铁的特点是碳、硅含量低,成分类似钢,实际上也代替废钢使用于炼钢。
习惯上把铁矿石在高炉中先还原冶炼成含碳高的生铁。
而后在炼钢炉内氧化,降低含碳量并精炼成钢,这项传统工艺,称作间接炼钢方法;而把炼制海绵铁的工艺称作直接还原法,或称直接炼铁(钢)法。
直接还原原理与早期的炼铁法(见块炼铁)基本相同。
高炉法取代原始炼铁法后,生产效率大幅度提高,是钢铁冶金技术的重大进步。
但随着钢铁工业大规模发展,适合高炉使用的冶金焦的供应日趋紧张。
为了摆脱冶金焦的羁绊,18世纪末提出了直接还原法的设想。
20世纪60年代,直接还原法得到发展,其原因是:①50~70年代,石油及天然气大量开发,为发展直接还原法提供了方便的能源。
②电炉炼钢迅速发展,海绵铁能代替供应紧缺的优质废钢,用作电炉原料,开辟了海绵铁的广阔市场。
③选矿技术提高,能提供高品位精矿,使脉石含量可以降得很低,简化了直接还原工艺。
1980年全世界直接还原炼铁生产量为713万吨,占全世界生铁产量的1.4%。
最大的直接还原工厂规模达到年产百万吨,在钢铁工业中已占有一定的位置。
海绵铁中能氧化发热的元素如硅、碳、锰的含量很少,不能用于转炉炼钢,但适用于电弧炉炼钢。
这样就形成一个直接还原炉-电炉的钢铁生产新流程。
经过电炉内的简单熔化过程,从海绵铁中分离出少量脉石,就炼成了钢,免除了氧化、精炼及脱氧操作,使新流程具有作业程序少和能耗低的优点。
其缺点是:①成熟的直接还原法需用天然气作能源,而用煤炭作能源的直接还原法尚不完善,70年代后期,石油供应不足,天然气短缺,都限制了直接还原法的发展。
②直接还原炉-电炉炼钢流程,生产一吨钢的电耗不少于600千瓦·时,不适于电力短缺地区使用。
直接还原铁进高炉
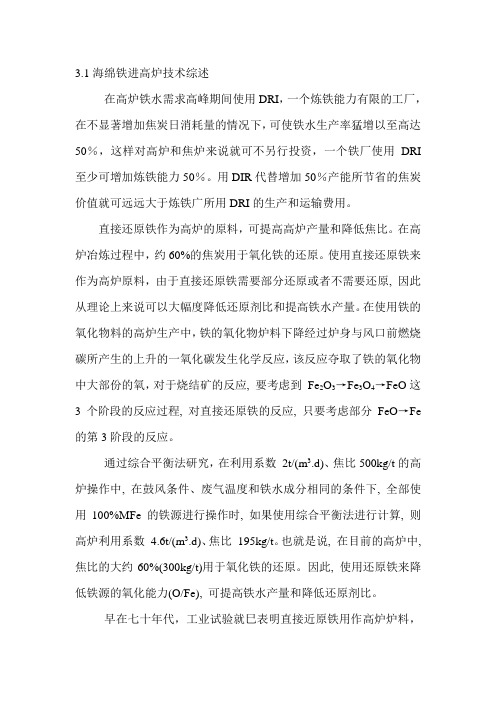
3.1海绵铁进高炉技术综述在高炉铁水需求高峰期间使用DRI,一个炼铁能力有限的工厂,在不显著增加焦炭日消耗量的情况下,可使铁水生产率猛增以至高达50%,这样对高炉和焦炉来说就可不另行投资,一个铁厂使用DRI 至少可增加炼铁能力50%。
用DIR代替增加50%产能所节省的焦炭价值就可远远大于炼铁广所用DRI的生产和运输费用。
直接还原铁作为高炉的原料,可提高高炉产量和降低焦比。
在高炉冶炼过程中,约60%的焦炭用于氧化铁的还原。
使用直接还原铁来作为高炉原料,由于直接还原铁需要部分还原或者不需要还原, 因此从理论上来说可以大幅度降低还原剂比和提高铁水产量。
在使用铁的氧化物料的高炉生产中,铁的氧化物炉料下降经过炉身与风口前燃烧碳所产生的上升的一氧化碳发生化学反应,该反应夺取了铁的氧化物中大部份的氧,对于烧结矿的反应, 要考虑到Fe2O3→Fe3O4→FeO这3个阶段的反应过程, 对直接还原铁的反应, 只要考虑部分FeO→Fe 的第3阶段的反应。
通过综合平衡法研究,在利用系数2t/(m3.d)、焦比500kg/t的高炉操作中, 在鼓风条件、废气温度和铁水成分相同的条件下, 全部使用100%MFe 的铁源进行操作时, 如果使用综合平衡法进行计算, 则高炉利用系数4.6t/(m3.d)、焦比195kg/t。
也就是说, 在目前的高炉中, 焦比的大约60%(300kg/t)用于氧化铁的还原。
因此, 使用还原铁来降低铁源的氧化能力(O/Fe), 可提高铁水产量和降低还原剂比。
早在七十年代,工业试验就巳表明直接近原铁用作高炉炉料,可以降低焦比和提高产量。
1964年一1965年,美国矿业局、美国钢铁公司的试验高炉和安大赂的汉密尔加拿大钢铁公司的商业性生产规模高炉都进行丁试验,探求DIR对铁水生产率和高炉熊比的影响,1970年比利时列日的矮形高炉以及日本新日铁、苏联等也进行了相似试验。
1964年美国矿业局在宾州Bruceton,用一座试验用小高炉进行的试验指出,用金属化率90%左右的直接还原铁球团代替高炉炉料中部分氧化球团矿,可以使铁水生产率明显增加和焦比大为下降。
直接还原铁生产工艺标准

直接还原铁回转窑铁磷还原法生产工艺一、直接还原铁是精铁粉或氧化铁在炉内经低温还原形成的低碳多孔状物质,其化学成分稳定,杂质含量少,主要用作电炉炼钢的原料,也可作为转炉炼钢的冷却剂,如果经二次还原还可供粉末冶金用。
二、直接还原铁生产工艺概述1、什么是直接还原炼铁法?直接还原炼铁法是在低于矿石熔化温度下,通过固态还原,把铁矿石炼制成铁的工艺过程。
2、常用的直接还原炼铁法有哪些?在工业上应用较多的有铁磷还原法,铁精矿粉还原法等,即将轧钢氧化铁磷或精矿粉经还原铁压块机压制成块后,装入焙烧管进窑焙烧,生产出了优质还原铁。
直接还原铁经粗破(将直接还原铁锭破成块状)中破(将块状直接还原铁破碎成0~15mm的颗粒状)后,再经过磁选,去除SiO2、、CaS和游离碳等杂质。
用户可再次使用还原铁压块机压制直接还原铁颗粒,使直接还原铁颗粒成型并达到一定的堆比重g/cm3要求。
直接还原铁破碎颗粒直接影响压块物理特性(压缩性、成型性、堆比重g/cm3)对特钢生产起到至关重要的作用。
三、铁磷还原法概述1、什么是铁磷?铁鳞又称氧化铁皮、氧化皮。
在钢材加热和轧制过程中,由于表面受到氧化而形成氧化铁层,剥落下来的鱼鳞状物。
铁鳞可用作氧化剂和制铁粉的原料。
轧钢氧化铁磷是钢材在加热炉中加热后在轧制过程中,其表面氧化层自行脱落而产生的。
2、为什么用氧化铁磷?有什么注意事项?还原海绵铁可采用热轧沸腾钢氧化铁磷作原料,因为沸腾钢氧化铁磷中的TFe、C、S、P化学成分含量,能满足还原海绵铁生产的技术要求。
在还原海绵铁中最好不要以高碳钢或合金钢氧化铁磷为原料。
3、什么是铁磷还原法?有哪些类型?铁鳞还原法就是以铁鳞为原料的直接还原法生产工艺。
铁鳞还原法生产过程可分为粗还原与精还原。
在粗还原过程中,铁氧化物被还原,铁粉颗粒烧结与渗碳。
增高还原温度或延长保温时间皆有利于铁氧化物还原、铁粉颗粒烧结,但会生产部分渗碳。
鉴于在精还原过程中脱碳困难,在粗还原过程中,控制铁氧化物还原到未渗碳的程度是必要的。
直接还原铁

直接还原铁直按还原铁和熔融还原铁的生产直接还原铁和熔融还原铁的冶炼统称为非高炉法炼铁。
(一)直接还原法生产生铁直接还原法是指在低于熔化温度之下将铁矿石还原成海绵铁的炼铁生产过程,其产品为直接还原铁(即DRI),也称海绵铁。
该产品未经熔化,仍保持矿石外形,由于还原失氧形成大量气孔,在显微镜下观察团形似海绵而得名。
海绵铁的特点是含碳低(<1%),并保存了矿石中的脉石。
这些特性使其不宜大规模用于转炉炼钢,只适于代替废钢作为电炉炼钢的原料。
直接还原法分气基法和煤基法两大类。
前者是用天然气经裂化产出H2和CO气体,作为还原剂,在竖炉、罐式炉或流化床内将铁矿石中的氧化铁还原成海绵铁。
主要有Midrex法、HYL Ⅲ法、FIOR法等。
后者是用煤作还原剂,在回转窑、隧道窑等设备内将铁矿石中的氧化铁还原。
主要有FASMET法等。
直接还原法的优点有:(1)流程短,直接还原铁加电炉炼钢;(2)不用焦炭,不受炼焦煤短缺的影响;(3)污染少,取消了焦炉、烧结等工序;(4)海绵铁中硫、磷等有害杂质与有色金属含量低,有利于电炉冶炼优质钢种。
直接还原法的缺点有:(1)对原料要求较高:气基要有天然气;煤基要用灰熔点高、反应性好的煤;(2)海绵铁的价格一般比废钢要高。
直接还原法已有上百年的发展历史,但直到20世纪60年代才获得较大突破。
进入20世纪90年代,其生产工艺日臻成熟并获得长足发展。
其主要原因是:(1)天然气的大量开发利用,特别是高效率天然气转化法的采用,提供了适用的还原煤气,使直接还原法获得了来源丰富、价格相对便宜的新能源。
(2)电炉炼钢迅速发展以及冶炼多种优质钢的需要,大大扩展了对海绵铁的需求。
(3)选矿技术提高,可提供大量高品位精矿,矿石中的脉石量降低到还原冶炼过程中不需加以脱除的程度,从而简化了直接还原技术。
当前世界上直接还原铁量的90%以上是采用气基法生产的。
我国天然气主要供应化工和民用,不可能大量用于钢铁工业。
直接还原铁生产工艺标准

直接还原铁回转窑铁磷还原法生产工艺一、直接还原铁是精铁粉或氧化铁在炉内经低温还原形成的低碳多孔状物质,其化学成分稳定,杂质含量少,主要用作电炉炼钢的原料,也可作为转炉炼钢的冷却剂,如果经二次还原还可供粉末冶金用。
二、直接还原铁生产工艺概述1、什么是直接还原炼铁法?直接还原炼铁法是在低于矿石熔化温度下,通过固态还原,把铁矿石炼制成铁的工艺过程。
2、常用的直接还原炼铁法有哪些?在工业上应用较多的有铁磷还原法,铁精矿粉还原法等,即将轧钢氧化铁磷或精矿粉经还原铁压块机压制成块后,装入焙烧管进窑焙烧,生产出了优质还原铁。
直接还原铁经粗破(将直接还原铁锭破成块状)中破(将块状直接还原铁破碎成0~15mm的颗粒状)后,再经过磁选,去除SiO2、、CaS和游离碳等杂质。
用户可再次使用还原铁压块机压制直接还原铁颗粒,使直接还原铁颗粒成型并达到一定的堆比重g/cm3要求。
直接还原铁破碎颗粒直接影响压块物理特性(压缩性、成型性、堆比重g/cm3)对特钢生产起到至关重要的作用。
三、铁磷还原法概述1、什么是铁磷?铁鳞又称氧化铁皮、氧化皮。
在钢材加热和轧制过程中,由于表面受到氧化而形成氧化铁层,剥落下来的鱼鳞状物。
铁鳞可用作氧化剂和制铁粉的原料。
轧钢氧化铁磷是钢材在加热炉中加热后在轧制过程中,其表面氧化层自行脱落而产生的。
2、为什么用氧化铁磷?有什么注意事项?还原海绵铁可采用热轧沸腾钢氧化铁磷作原料,因为沸腾钢氧化铁磷中的TFe、C、S、P化学成分含量,能满足还原海绵铁生产的技术要求。
在还原海绵铁中最好不要以高碳钢或合金钢氧化铁磷为原料。
3、什么是铁磷还原法?有哪些类型?铁鳞还原法就是以铁鳞为原料的直接还原法生产工艺。
铁鳞还原法生产过程可分为粗还原与精还原。
在粗还原过程中,铁氧化物被还原,铁粉颗粒烧结与渗碳。
增高还原温度或延长保温时间皆有利于铁氧化物还原、铁粉颗粒烧结,但会生产部分渗碳。
鉴于在精还原过程中脱碳困难,在粗还原过程中,控制铁氧化物还原到未渗碳的程度是必要的。
高炉工艺]高炉冶炼过程
![高炉工艺]高炉冶炼过程](https://img.taocdn.com/s3/m/bc5ac850f01dc281e53af080.png)
高炉工艺]高炉冶炼过程高炉冶炼是把铁矿石还原成生铁的连续生产过程。
铁矿石、焦炭和熔剂等固体原料按规定配料比由炉顶装料装置分批送入高炉,并使炉喉料面保持一定的高度。
焦炭和矿石在炉内形成交替分层结构。
矿石料在下降过程中逐步被还原、熔化成铁和渣,聚集在炉缸中,定期从铁口、渣口放出。
鼓风机送出的冷空气在热风炉加热到800~1350℃以后,经风口连续而稳定地进入炉缸,热风使风口前的焦炭燃烧,产生2000℃以上的炽热还原性煤气。
上升的高温煤气流加热铁矿石和熔剂,使成为液态;并使铁矿石完成一系列物理化学变化,煤气流则逐渐冷却。
下降料柱与上升煤气流之间进行剧烈的传热、传质和传动量的过程。
下降炉料中的毛细水分当受热到100~200℃即蒸发,褐铁矿和某些脉石中的结晶水要到500~800℃才分解蒸发。
主要的熔剂石灰石和白云石,以及其他碳酸盐和硫酸盐,也在炉中受热分解。
石灰石中CaCO3和白云石中MgCO3的分解温度分别为900~1000℃和7 40~900℃。
铁矿石在高炉中于400℃或稍低温度下开始还原。
部分氧化铁是在下部高温区先熔于炉渣,然后再从渣中还原出铁。
焦炭在高炉中不熔化,只是到风口前才燃烧气化,少部分焦炭在还原氧化物时气化成C O。
而矿石在部分还原并升温到1000~1100℃时就开始软化;到1350~1400℃时完全熔化;超过1400℃就滴落。
焦炭和矿石在下降过程中,一直保持交替分层的结构。
由于高炉中的逆流热交换,形成了温度分布不同的几个区域。
在图1中,①区是矿石与焦炭分层的干区,称块状带,没有液体;②区为由软熔层和焦炭夹层组成的软熔带,矿石开始软化到完全熔化;③区是液态渣、铁的滴落带,带内只有焦炭仍是固体;④风口前有一个袋形的焦炭回旋区,在这里,焦炭强烈地回旋和燃烧,是炉内热量和气体还原剂的主要产生地。
液态渣铁积聚于炉缸底部,由于比重不同,渣液浮于铁液之上,定时从炉缸放出。
铁水出炉温度一般为1400~1550℃,渣温比铁温一般高30~70℃。
直接还原铁技术.
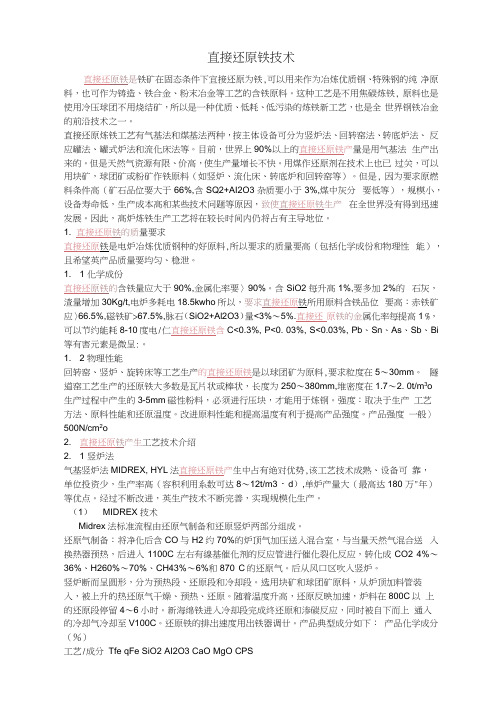
直接还原铁技术直接还原铁是铁矿在固态条件下宜接还原为铁,可以用来作为冶炼优质钢、特殊钢的纯净原料,也可作为铸造、铁合金、粉末冶金等工艺的含铁原料。
这种工艺是不用焦碳炼铁, 原料也是使用冷压球团不用烧结矿,所以是一种优质、低耗、低污染的炼铁新工艺,也是全世界钢铁冶金的前沿技术之一。
直接还原炼铁工艺有气基法和煤基法两种,按主体设备可分为竖炉法、回转窑法、转底炉法、反应罐法、罐式炉法和流化床法等。
目前,世界上90%以上的直接还原铁产量是用气基法生产出来的。
但是天然气资源有限、价高,使生产量增长不快。
用煤作还原剂在技术上也已过关,可以用块矿,球团矿或粉矿作铁原料(如竖炉、流化床、转底炉和回转窑等)。
但是, 因为要求原燃料条件高(矿石品位要大于66%,含SQ2+AI2O3杂质要小于3%,煤中灰分要低等),规模小,设备寿命低,生产成本髙和某些技术问题等原因,致使直接还原铁生产在全世界没有得到迅速发展。
因此,髙炉炼铁生产工艺将在较长时间内仍将占有主导地位。
1. 直接还原铁的质量要求直接还原铁是电炉冶炼优质钢种的好原料,所以要求的质量要高(包括化学成份和物理性能),且希望英产品质量要均匀、稳泄。
1. 1 化学成份直接还原铁的含铁量应大于90%,金属化率要〉90%。
含SiO2每升髙1%,要多加2%的石灰,渣量增加30Kg/t,电炉多耗电18.5kwho所以,要求直接还原铁所用原料含铁品位要高:赤铁矿应〉66.5%,磁铁矿>67.5%,脉石(SiO2+Al2O3)量<3%〜5%.直接还原铁的金属化率每提高1 %,可以节约能耗8-10度电/仁直接还原铁含C<0.3%, P<0. 03%, S<0.03%, Pb、Sn、As、Sb、Bi 等有害元素是微呈:。
1. 2 物理性能回转窑、竖炉、旋转床等工艺生产的直接还原铁是以球团矿为原料,要求粒度在5〜30mm。
隧道窑工艺生产的还原铁大多数是瓦片状或棒状,长度为250〜380mm,堆密度在1.7〜2. 0t/m3o生产过程中产生的3-5mm磁性粉料,必须进行压块,才能用于炼钢。
高炉炼铁的基本原理与工艺流程
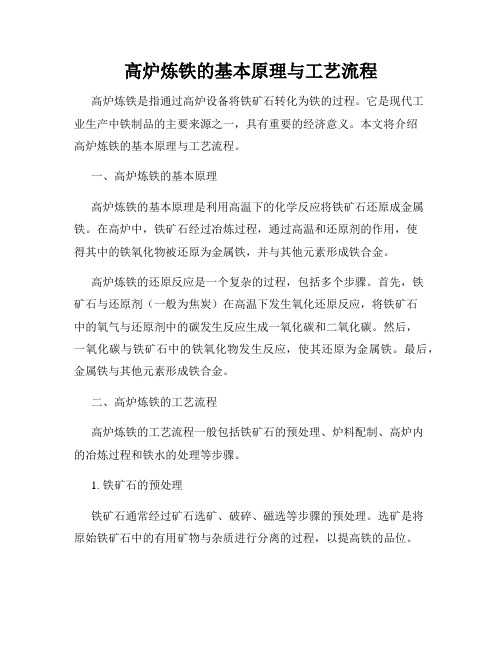
高炉炼铁的基本原理与工艺流程高炉炼铁是指通过高炉设备将铁矿石转化为铁的过程。
它是现代工业生产中铁制品的主要来源之一,具有重要的经济意义。
本文将介绍高炉炼铁的基本原理与工艺流程。
一、高炉炼铁的基本原理高炉炼铁的基本原理是利用高温下的化学反应将铁矿石还原成金属铁。
在高炉中,铁矿石经过冶炼过程,通过高温和还原剂的作用,使得其中的铁氧化物被还原为金属铁,并与其他元素形成铁合金。
高炉炼铁的还原反应是一个复杂的过程,包括多个步骤。
首先,铁矿石与还原剂(一般为焦炭)在高温下发生氧化还原反应,将铁矿石中的氧气与还原剂中的碳发生反应生成一氧化碳和二氧化碳。
然后,一氧化碳与铁矿石中的铁氧化物发生反应,使其还原为金属铁。
最后,金属铁与其他元素形成铁合金。
二、高炉炼铁的工艺流程高炉炼铁的工艺流程一般包括铁矿石的预处理、炉料配制、高炉内的冶炼过程和铁水的处理等步骤。
1. 铁矿石的预处理铁矿石通常经过矿石选矿、破碎、磁选等步骤的预处理。
选矿是将原始铁矿石中的有用矿物与杂质进行分离的过程,以提高铁的品位。
破碎过程将大块的铁矿石破碎成为适合冶炼的小颗粒。
磁选则是利用磁力将磁性矿物与非磁性矿物分离。
2. 炉料配制炉料配制是将预处理后的铁矿石与还原剂(焦炭)、矿石烧结等辅助原料按照一定比例配制成为高炉的进料。
配制过程中需要根据铁矿石的品位、还原剂的质量等因素进行合理的配比,以保证炼铁过程的效果。
3. 高炉内的冶炼过程高炉内的冶炼过程是高炉炼铁的核心环节。
在高炉内,炉料由上部的料槽加入,并由炉底的鼓风口进入。
在高炉内,料层中的铁矿石与还原剂经过一系列的燃烧和还原反应,发生冶炼和还原,最终生成铁水和炉渣。
炉渣由高炉底部排出,而铁水则从高炉的铁口流出,进入下一步的处理。
4. 铁水的处理铁水是高炉炼铁的产物之一,但其中含有一定的杂质,需要进行进一步的处理。
首先,通过除渣工艺将铁水中的炉渣分离出去,得到较为纯净的铁水。
然后,将铁水进行调质处理,加入适量的合金等元素,以调整铁的成分和性能,得到所需的铁产品。
工艺采用焦炉煤气生产直接还原铁

HYL ZR (希尔) 工艺: 采用焦炉煤气生产直接还原铁
Pablo E. Duarte HYL 技术公司直接还原部主管
摘要
目前,钢铁联合企业日常生产中产生的过剩焦炉煤气(COG)、转炉煤气和/或高炉(BF)煤气主要是送往电站用于 发电。现在有一种新的工艺,技术上已证明为可行的,即把这些煤气用在冶金工艺中,生产直接还原铁和粗钢。
综合性钢厂中所回收的气态燃料副产品主要有焦炉煤气(COG)、高炉煤气(BFG)、以及氧气顶吹转炉煤 气(BOFG)。这些煤气的热值和成分有很大差异。
在任何通过高炉/转炉进行钢铁生产的综合性钢厂中,能量是先天性不平衡的。由焦炉、高炉和转炉所 产生的各种可燃性气体所含的能源,总是要多于该钢厂中要求作为燃料使用的能源。较为典型的是,综合 性钢厂的能源平衡显示,大部分过剩的气态能源主要用于发电,甚至是放散燃烧。利用这些气体所生产的 电力中,只有一小部分用于钢厂中,以满足其自身需求,而大部分电力都要输出。
在焦炭的碳化过程中,需要用燃料对炼焦炉进行加热。在这方面,炼焦厂用于加热的燃料就具有很大 的弹性,其燃料来源也变得非常广泛,其中就包括可以使用高炉煤气和炼焦厂自产焦炉煤气。
在以铁水和转炉为基础的综合性钢厂中,焦炉车间与其他生产车间之间,存在一个能量“链接”。
表 1 典型综合性钢厂中的车间/系统的物流和能量流
离开反应炉的炉顶气体中含有在还原过程中所产生的水(H2O)和二氧化碳(CO2)。这些成分将通过循环 气体回路中的炉顶气体清理系统(除去水分)和 CO2 清除系统被消除。还原气体中含有被加入补充焦炉气 体的循环气体。还原气体在煤气加热器中再次加热到 950°C。在喷入氧气使还原气体进行部分氧化后,温 度将进一步升高至 1000°C 以上。
炼铁高炉工艺流程

炼铁高炉工艺流程
炼铁高炉工艺流程是将铁矿石和焦炭经过高温反应,产生铁和炉渣的过程。
下面将简要介绍炼铁高炉工艺流程。
首先,将铁矿石均匀地布置在高炉上部,并逐渐加热。
在炉内逐渐形成了三个区域:还原区、中间区和燃烧区。
在还原区,铁矿石中的氧化铁与焦炭中的碳发生反应,产生一氧化碳和二氧化碳。
这些气体通过上部喷嘴进入炉内,并与铁矿石中的氧化铁反应,将其还原为金属铁。
还原过程中产生的一氧化碳起到了还原剂的作用。
在中间区,金属铁开始熔化。
在炉内,金属铁与石灰石反应,形成液态炉渣。
这些炉渣通过炉底出口排出。
燃烧区是高炉中最热的部分,焦炭发生燃烧反应,产生高温火焰。
这些火焰使铁矿石中的还原反应加剧,并提供了炉内所需的热量。
炉渣通过底吹口排出高炉,而金属铁则通过铁口排出。
炉渣经过冷却后,可以用作建筑材料等。
金属铁则进一步经过冷却和净化处理,最终得到高质量的铁产品。
这就是炼铁高炉工艺流程的基本步骤。
需要注意的是,不同的高炉工艺流程可能会有所不同,但大致的原理和步骤是相似的。
通过高炉工艺,我们可以将铁矿石转化为有用的铁产品,为工业生产提供了重要的原材料。
铁的直接还原度名词解释
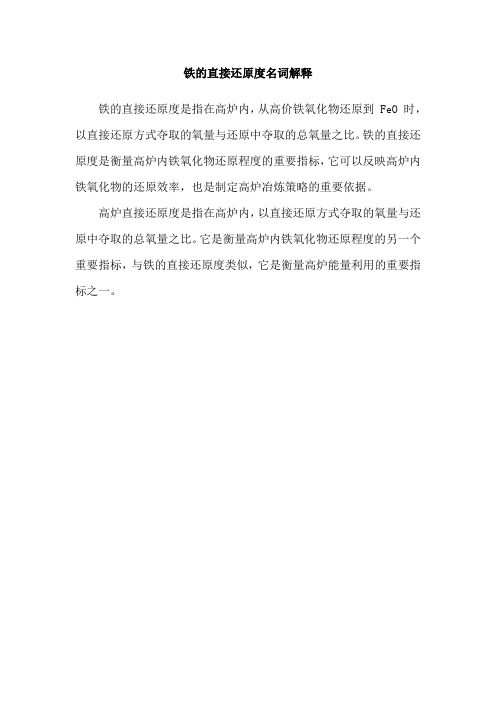
铁的直接还原度名词解释
铁的直接还原度是指在高炉内,从高价铁氧化物还原到 FeO 时,以直接还原方式夺取的氧量与还原中夺取的总氧量之比。
铁的直接还原度是衡量高炉内铁氧化物还原程度的重要指标,它可以反映高炉内铁氧化物的还原效率,也是制定高炉冶炼策略的重要依据。
高炉直接还原度是指在高炉内,以直接还原方式夺取的氧量与还原中夺取的总氧量之比。
它是衡量高炉内铁氧化物还原程度的另一个重要指标,与铁的直接还原度类似,它是衡量高炉能量利用的重要指标之一。
各阶段的作用2.什么是直接还原,什么是间接还原高炉

▪ 其原理是一样的,只是炼铁是还原性气氛,炉渣中的(FeO)会在还 原成Fe,更有利于脱硫。
▪ 在高温下,由于CO2+C==CO反应强烈向右进行,使CO2不能生成, 一旦生成,就会与C反应生成CO,即消耗了固体C,也就是说的发生 的是直接还原。
▪ 而高价铁的氧化物比低价的铁的氧化物容易还原,在炉身上部很容易 发生消耗CO的间按还原。
▪ 3.直接还原是不可逆的强吸热反应,还原过程需要较高的温度,是以 温度来决定还原是否发生的。间接还原只要CO达到要求,即可进行, 所以是以CO浓度是否满足为基础的,
0.5-2.0 8-10 1-2
高炉炼铁炉渣 20-45 35-45 0.3-0.9 0.3-1.5 -
6-8 8-14
0.05-0.03 0.9-1.3
高炉炼铁是通过还原的方式使铁的氧化物还原,炉内气氛是还原性的
炼钢是通过使杂质氧化的方式从钢液中分离出来而达到目的冶炼过程,炉内需要 氧化性气氛
作业:
1.选矿的生产工艺分为几个阶段?各阶段的作用? 2.什么是直接还原,什么是间接还原?高炉内为什么会有这两种还原方 式?各有什么特点? 3.炼铁与炼钢过程中脱硫的原理? 4.高炉炼铁和转炉炼钢的炉渣成分有什么异同?为什么?
一.选矿的生产工艺分为几个阶段?各阶段的作用?
▪ 选矿的生产工艺一般分为三个阶段: 1.矿石的破碎与磨矿。其作用就是通过破碎和磨矿,使矿石中的矿 物实现单体分离,以便根据矿物性质的差别进行选别。 2.选矿。利用不同矿物的性质差异,采用不同的选矿方法,使矿物 分别进入不同的物相中而分离,最大限度的回收有价金属。 3.脱水与干燥。进行液固分离,得到固态的物料,以便运输及满足 冶炼的要求。
- 1、下载文档前请自行甄别文档内容的完整性,平台不提供额外的编辑、内容补充、找答案等附加服务。
- 2、"仅部分预览"的文档,不可在线预览部分如存在完整性等问题,可反馈申请退款(可完整预览的文档不适用该条件!)。
- 3、如文档侵犯您的权益,请联系客服反馈,我们会尽快为您处理(人工客服工作时间:9:00-18:30)。
3.1海绵铁进高炉技术综述在高炉铁水需求高峰期间使用DRI,一个炼铁能力有限的工厂,在不显著增加焦炭日消耗量的情况下,可使铁水生产率猛增以至高达50%,这样对高炉和焦炉来说就可不另行投资,一个铁厂使用DRI 至少可增加炼铁能力50%。
用DIR代替增加50%产能所节省的焦炭价值就可远远大于炼铁广所用DRI的生产和运输费用。
直接还原铁作为高炉的原料,可提高高炉产量和降低焦比。
在高炉冶炼过程中,约60%的焦炭用于氧化铁的还原。
使用直接还原铁来作为高炉原料,由于直接还原铁需要部分还原或者不需要还原, 因此从理论上来说可以大幅度降低还原剂比和提高铁水产量。
在使用铁的氧化物料的高炉生产中,铁的氧化物炉料下降经过炉身与风口前燃烧碳所产生的上升的一氧化碳发生化学反应,该反应夺取了铁的氧化物中大部份的氧,对于烧结矿的反应, 要考虑到Fe2O3→Fe3O4→FeO这3个阶段的反应过程, 对直接还原铁的反应, 只要考虑部分FeO→Fe 的第3阶段的反应。
通过综合平衡法研究,在利用系数2t/(m3.d)、焦比500kg/t的高炉操作中, 在鼓风条件、废气温度和铁水成分相同的条件下, 全部使用100%MFe 的铁源进行操作时, 如果使用综合平衡法进行计算, 则高炉利用系数4.6t/(m3.d)、焦比195kg/t。
也就是说, 在目前的高炉中, 焦比的大约60%(300kg/t)用于氧化铁的还原。
因此, 使用还原铁来降低铁源的氧化能力(O/Fe), 可提高铁水产量和降低还原剂比。
早在七十年代,工业试验就巳表明直接近原铁用作高炉炉料,可以降低焦比和提高产量。
1964年一1965年,美国矿业局、美国钢铁公司的试验高炉和安大赂的汉密尔加拿大钢铁公司的商业性生产规模高炉都进行丁试验,探求DIR对铁水生产率和高炉熊比的影响,1970年比利时列日的矮形高炉以及日本新日铁、苏联等也进行了相似试验。
1964年美国矿业局在宾州Bruceton,用一座试验用小高炉进行的试验指出,用金属化率90%左右的直接还原铁球团代替高炉炉料中部分氧化球团矿,可以使铁水生产率明显增加和焦比大为下降。
如表3.1-1所示,当直接还原铁球团矿在护料中的比例提高到85%的,铁水产量几乎直线的增加了75%,炉料中直接还原铁球团用量在30%时,焦比则下降约23%。
直接还原铁球团的用量较高时,炉料中直接还原球团用量对焦比下降作用减弱,炉料中直接还原铁用量占85%时,焦比仅下降47%。
表3.1-1美国矿业局试验高炉炉料中直接还原铁的使用资料美国钢铁公司引导利同不同类型的直接还原铁原料,而在同一座炉缸直径为1.2m,有效高度为6.1m的试验用小高炉里作过高炉冶炼试验。
在这些试验中,以金属化率69%的压块,高铁压块(HIB),炉料和相当金属化率98.5%的废钢进行了比较。
结果表明,铁水产量增加,焦比下降。
同矿业局试验所得结果十分相似。
同时还表明,产量增加、焦比下降完全地取决于炉料中金属化铁的百分比,而与金属铁来自HIB块或废钢无关。
由于用废钢时渣量较小,含废钢的炉料其生产率略高于含HIB团块的炉料。
作为高炉试验的继续研究,1964年加拿大钢铁公司(Stelco)在一座有效容积588m3工业性高炉炉料里,用直接还原铁球团进行一次大型试验。
表3指出试验分从风口喷天然气和不喷天气两组。
每组实验的基准期都采用100%的氧化球团,试验期则使用氧化球团矿占70%,金属化率为90.5%的直接还原铁球团占30%的炉料。
对不喷吹天然气的试验组,用直接近原铁球团时,铁水产量增加20%,焦比下降大约20%。
对喷吹天然气这个组,用直接还原铁球团时,铁水产量大约增加17%,焦比下降7%左右。
虽然在每种情况下,铁水日产量都增加得较多,但是焦炭日耗量并没有增加,实际上,在两种情况下焦炭消耗量却都下降了。
本试验结果意义非常重大,它意味着即使是个别的工厂,其高炉和焦炉都按最大能力进行生产,当高炉炉料中使用直接还原铁物料时,铁水产量仍能大大地提高。
Tsujihata等在Hagashlda厂的6号高炉进行实验,高炉的工作容量为648m3。
在试验中,直到40%的炉料被DRI取代,原来的炉料是由54%自熔性烧结结矿和46%筛选矿组成的,而DRI是用高炉烟灰和LD转炉泥浆在回转窑内制成的。
DRI含70%全铁和40%金属铁。
虽然这些条件与Stelco的试验大有差别,但如果用每吨铁水从炉料脱除的氧量表示时,测得的生产率和焦比却与Stelco较为相符。
1978年墨西哥高炉公司(AHMSA)的二号高炉上,用金属化率为87%,含碳量2.5%的DRI球团也进行过工业性试验。
该高炉有效容积为918m3,使用含灰分18.2%,含硫1.08%的较低级焦炭操作。
试验有一个基准期(炉料中烧结矿占60%,块矿占40%)和四个试验期,分别使用:15%,25%,30%,35%的直接还原铁代替相当量的块矿,如表4所示,墨西哥高炉公司试验所得结果同加拿大钢铁公司试验所得结果十分相似。
美国人white等报道了一座实验性高炉(炉缸直径1.22米)用75%还原压块的试验,压块是由委内瑞拉铁矿石制成的。
他们确定了由100%烧结矿、50%烧结矿/50%压块和100%还原铁压块组成的炉料的最小焦比和生产率。
还进行了使用废钢/烧结结矿的试验,其金属铁含量与压块/烧结矿矿料相同。
他们的结果再一次证实了这样的结果;炉料每10%金属化,铁水增产8.2%,而焦比下降6%。
废钢和压块的情况与此类似。
铁水产量增加百分比与高炉炉料中金属化率关系焦比下降百分比与高炉炉料中金属化率关系日本和苏联在试验的和工业的高炉里也用过直接还原铁料,进行过试验,取得了十分相似的结果。
新日铁在名古屋1号高炉上进行了使用还原铁(DRI)100kg/t 的试验, 结果表明具有提高生产率和降低还原剂比的效果。
炉料中含有直接还原铁,能够降低昂贵的冶金焦炭的消耗量。
以上所有众多试验取得很好的一致的结果。
试验高炉试验的结果和工业规模高炉试验的结果相比,生产率提高得较多,焦比下降的较多因为试验用小高炉经炉壳的热损失占了每吨铁水所需全部热量的较大部份。
低品位矿石出产的海绵铁,往往因为脉石和杂质含量比较多而无法在炼钢炉中使用,只适宜做高炉炉料。
目前日本一直进行工业规模的应用,其中采用转底炉(RHF炉)工艺处理高锌含铁粉尘生产还原性团块供高炉使用,就是其中成功的一例。
日本新日铁君津公司为年产800万吨的钢铁联合企业,该公司至今一直进行直接还原铁进高炉的工业生产。
含铁粉尘在转底炉脱锌回收后,将直接还原生成的金属化球团通过鼓式冷却器冷却后进入贮料仓,然后再通过皮带机送入高炉原料仓,以直接加入高炉,取得良好的效益。
对于对直接还原铁加入量,众多研究分析表明,随着炉料金属化增加到30%以上,使用还原炉抖的益处将减小。
然而,如果喷射天然气,该极限将能增大到58%。
大体上说,从炉料中还原出一吨铁水大约一半左右(约470公斤/吨铁水)是来自用间接还原反应变成金属铁的,而余下的铁,则必须用气化碳吸热反应来还原。
在高炉冶炼中,吸热的气化碳称为溶解损失碳。
当炉料中相当大的部份是金属化的直接近原铁时,吸热还原反应量就减少了。
因此,不需要消耗大量热能,从而节省了相应的焦炭。
但是,如果增加炉料中直接还原铁的百分比超出抑制大部份吸热还原所需的量,则炉料中每吨直接近原铁节省的燃料就不多。
流化床生产的直接还原铁,金属化率较低,全铁含量也较低,不适合直接用于电炉,如果作为高炉原料,对提高高炉的经济效益还是有很大帮助的。
据资料显示,矿石品位提高1%,焦比会下降2%,产量提高3%,直接还原铁作为高炉炉料,不仅品味提高,而且可以减少直接还原消耗的碳,降低焦比,因此据初步估算,如果全部使用流化床生产的还原铁块作为高炉炉料,可以使铁水产量提高30%以上,焦比降低100kg/t-Fe以上。
在北美高炉中, 为降低焦炭的使用量和确保出铁量, 一直将以废钢为主的金属铁源的使用量保持在100kg/t 左右。
另外, IRSID 在内容积为1816m3的小型高炉上进行了使用100%废钢料的熔化试验,在使用100%废钢的操作中, 还原剂比为222~242kg/t。
虽然还原铁的使用效果受金属化率的影响很大, 但在使用T.Fe91.4%、金属化率为100%的铁源时,还原剂比为228kg/t, 炉顶温度为200℃。
研究人员在对使用直接还原铁时炉墙部的静压分布和大量使用直接还原铁后的块状带、直接还原铁高温荷重软化试验结果表明, 使用直接还原铁软融带的透气阻力有很大的改善,风口上方0.7m 处取样物中的熔化物比例,烧结矿熔化物比直接还原铁多, 由此可以认直接还原铁颗粒的熔化度比烧结矿更低。
在风口上方0.7m处, 由于直接还原铁没有保留原形, 由此可以推测在烧结矿熔化带表面下端附近(炉内温度大约1400℃)的风口上方0.6~1.1m处, 直接还原铁没有形成熔融层而是迅速熔化。
由于直接还原铁的高温透气性比烧结矿好得多, 因此可以推测即使在实际高炉使用, 也没有必要担心直接还原铁会阻碍软化带的透气。
热压块海绵铁是高温性状非常好的铁源,高炉如果大量使用热压块海绵铁,不仅有助于维持炉料的透气性,而且有助于增产和降低还原剂比。
采用热交换简化模型计算表明,当热压块铁使用比例增加时,虽然炉身上部的热流比升高了,但炉身中部的热流比反而下降了,因此没有必要担心与还原铁共存的烧结矿的间接还原速度是否会下降的问题。
实践已证明,在高炉料中使用直接还原铁能大幅度地提高铁水产量和降低碳耗,特别在铁水生产能力有限,用铁水炼钢的现有工厂里,在必须满足最高产量的时候,用直接还原铁来大幅度地提高生产量,是十分有效的。