燃煤烟气脱硝工艺布置及典型工艺流程、还原剂制备及耗量计算、催化剂设计选型基础数据
电厂脱硝系统工艺流程
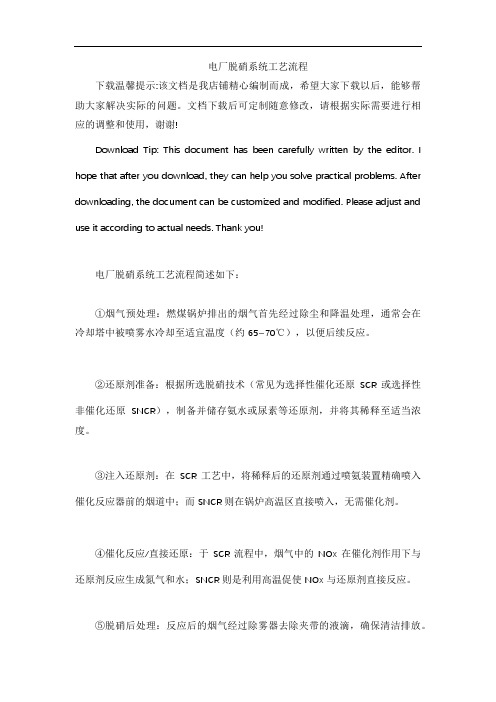
电厂脱硝系统工艺流程下载温馨提示:该文档是我店铺精心编制而成,希望大家下载以后,能够帮助大家解决实际的问题。
文档下载后可定制随意修改,请根据实际需要进行相应的调整和使用,谢谢!Download Tip: This document has been carefully written by the editor. I hope that after you download, they can help you solve practical problems. After downloading, the document can be customized and modified. Please adjust and use it according to actual needs. Thank you!电厂脱硝系统工艺流程简述如下:①烟气预处理:燃煤锅炉排出的烟气首先经过除尘和降温处理,通常会在冷却塔中被喷雾水冷却至适宜温度(约65~70℃),以便后续反应。
②还原剂准备:根据所选脱硝技术(常见为选择性催化还原SCR或选择性非催化还原SNCR),制备并储存氨水或尿素等还原剂,并将其稀释至适当浓度。
③注入还原剂:在SCR工艺中,将稀释后的还原剂通过喷氨装置精确喷入催化反应器前的烟道中;而SNCR则在锅炉高温区直接喷入,无需催化剂。
④催化反应/直接还原:于SCR流程中,烟气中的NOx在催化剂作用下与还原剂反应生成氮气和水;SNCR则是利用高温促使NOx与还原剂直接反应。
⑤脱硝后处理:反应后的烟气经过除雾器去除夹带的液滴,确保清洁排放。
若采用SCR技术,还需考虑热交换器(GGH)对烟气进行加热,恢复至排放温度。
⑥监控与优化:整个过程中,持续监测排放气体中NOx浓度,根据实测数据调整还原剂用量、反应条件等,以优化脱硝效率。
⑦副产品处理:对于特定工艺,如产生石膏等副产品,需进一步进行收集、处理和合理处置。
脱硫脱硝使用的工艺方法和原理

脱硫脱硝工艺方法和原理1. 引言随着工业化进程的加快和环境污染的加重,脱硫脱硝成为了重要的环境保护措施。
脱硫脱硝是指去除燃煤、燃油等燃料中的二氧化硫(SO2)和氮氧化物(NOx)的过程。
本文将详细介绍脱硫脱硝的工艺方法和原理。
2. 脱硫工艺方法和原理2.1 石膏法脱硫石膏法脱硫是一种常用的脱硫工艺方法,其基本原理是利用石灰石(CaCO3)与二氧化硫(SO2)反应生成石膏(CaSO4·2H2O),从而达到脱硫的目的。
其工艺流程如下:1.燃煤锅炉中产生的烟气经过除尘器去除颗粒物后,进入脱硫塔。
2.在脱硫塔中,石灰石与烟气中的二氧化硫反应生成石膏,并吸附一部分颗粒物。
3.脱硫后的烟气经过脱湿器去除水分后,排放到大气中。
石膏法脱硫的原理是利用石灰石的碱性来中和烟气中的酸性物质,将二氧化硫转化为不溶于水的石膏。
其反应方程式如下:CaCO3 + SO2 + 1/2O2 + H2O → CaSO4·2H2O + CO22.2 活性炭吸附法脱硫活性炭吸附法脱硫是一种利用活性炭吸附二氧化硫的工艺方法。
其基本原理是通过活性炭的大孔结构和表面吸附作用,将烟气中的二氧化硫吸附到活性炭上,从而达到脱硫的目的。
其工艺流程如下:1.烟气经过除尘器去除颗粒物后,进入活性炭吸附塔。
2.在吸附塔中,烟气经过活性炭层,其中的二氧化硫被吸附到活性炭上。
3.定期更换或再生活性炭,使其重新具有吸附能力。
4.脱硫后的烟气经过脱湿器去除水分后,排放到大气中。
活性炭吸附法脱硫的原理是利用活性炭的吸附特性,将烟气中的二氧化硫吸附到活性炭表面,从而达到脱硫的目的。
2.3 氨法脱硫氨法脱硫是一种利用氨水与二氧化硫反应生成硫酸铵的工艺方法。
其基本原理是通过氨与二氧化硫的反应生成不溶于水的硫酸铵,从而达到脱硫的目的。
其工艺流程如下:1.烟气经过除尘器去除颗粒物后,进入脱硫塔。
2.在脱硫塔中,氨水与烟气中的二氧化硫反应生成硫酸铵,同时也吸附一部分颗粒物。
烟气脱硝(SCR)技术及相关计算

4.2 SCR技术原理
选择性催化还原法(SCR技术)是以氨(NH3) 作为还原剂,在金属催化剂作用下,将NOx的 还原成无害的N2和H2O。 NH3有选择的与烟气中 NOx反应,而自身不被烟气中的残余的O2氧化, 因此称这种方法为“选择性”。 有氧条件下反应式如下:
4NO + 4NH3 + O2→ 4N2+ 6H2O
氨逃逸率
控制氨逃逸率小于3ppm,因为烟气中部 分SO2会转化为SO3,
NH3+ SO3+H2O——(NH4)SO4/ NH4HSO4
NH4HSO4沉积温度150-200℃,粘度大, 加剧对空预器换热元件的堵塞和腐蚀。
催化剂堵塞和失效
反应器布置在高含尘烟气段,这里的烟气 未经过除尘,飞灰颗粒对催化剂的冲蚀和 沉积比较严重,会引起催化剂空隙堵塞现 象,甚至可能引起催化剂中毒,使催化剂 活性降低。为保证理想的脱除效率,催化 剂表面必须保持清洁,在反应器内安装吹 灰器对催化剂层进行定期清洁。
×m
C NO、C NO2 进口烟气NO、NO2的浓度(mg/Nm3) Q为反应器进口烟气流量(Nm3/h)
Wa为供氨量(kg/h)
0.95为NO占NOx排放总量的95%
17、30、46分别为NH3、 NO、NO2分子量 m为脱硝效率
谢 谢!
4. 烟气脱硝SCR工艺
目前世界上使用最广泛的方法是选择性催化还原法(SCR) 和选择性 非催化还原(SNCR) 。 • SCR技术:选择性催化还原法(SCR为Selected Catalytic Reduction英文缩写) • SNCR技术:选择性非催化还原法(SNCR英文缩写为Selected Non-Catalytic Reduction英文缩写) • SNCR/SCR混合法技术:选择性非催化还原法和选择性催化还原 法的混合技术
图文并茂详解脱硝技术

图文并茂详解脱硝技术脱硝技术简介燃烧烟气中去除氮氧化物的过程,防止环境污染的重要性,已作为世界范围的问题而被尖锐地提了出来。
世界上比较主流的工艺分为:SCR和SNCR。
这两种工艺除了由于SCR使用催化剂导致反应温度比SNCR低外,其他并无太大区别,但如果从建设成本和运行成本两个角度来看,SCR的投入至少是SNCR投入的数倍,甚至10倍不止。
为防止锅炉内煤燃烧后产生过多的NOx 污染环境,应对煤进行脱硝处理。
分为燃烧前脱硝、燃烧过程脱硝、燃烧后脱硝。
高粉尘布置SCR系统工艺流程图选择性非催化还原脱硝技术(SNCR)工艺流程图SCR烟气脱硝工艺流程图SCR烟气脱硝工艺流程图选择性非催化还原(SNCR)烟气脱硫技术选择性非催化还原(SNCR)烟气脱硫技术脱硝工艺流程图水泥工艺脱硝工艺流程图臭氧脱硝系统流程图高粉尘布置SCR系统工艺流程图高粉尘布置SCR系统工艺流程图高粉尘布置SCR系统工艺流程图SNCR与SCR联合脱硝工艺流程图SCR脱硝技术工艺流程图SCR脱硝技术工艺流程图1 氮氧化物的的危害有哪些?答:(1)、NO能使人中枢神经麻痹并导致死亡,NO2会造成哮喘和肺气肿,破坏人的心、肺,肝、肾及造血组织的功能丧失,其毒性比NO更强。
无论是NO、NO2或N2O,在空气中的最高允许浓度为5mg/m3(以NO2计)。
(2)、NOx与SO2一样,在大气中会通过干沉降和湿沉降两种方式降落到地面,最终的归宿是硝酸盐或是硝酸。
硝酸型酸雨的危害程度比硫酸型酸雨的更强,因为它在对水体的酸化、对土壤的淋溶贫化、对农作物和森林的灼伤毁坏、对建筑物和文物的腐蚀损伤等方面丝毫不不逊于硫酸型酸雨。
所不同的是,它给土壤带来一定的有益氮分,但这种“利”远小于“弊”,因为它可能带来地表水富营养化,并对水生和陆地的生态系统造成破坏。
(3)、大气中的NOx有一部分进入同温层对臭氧层造成破坏,使臭氧层减薄甚至形成空洞,对人类生活带来不利影响;同对NOx中的N2O也是引起全球气候变暖的因素之一,虽然其数量极少,但其温室效应的能力是CO2的200-300倍。
锅炉燃煤烟气脱硝处理初步设计方案
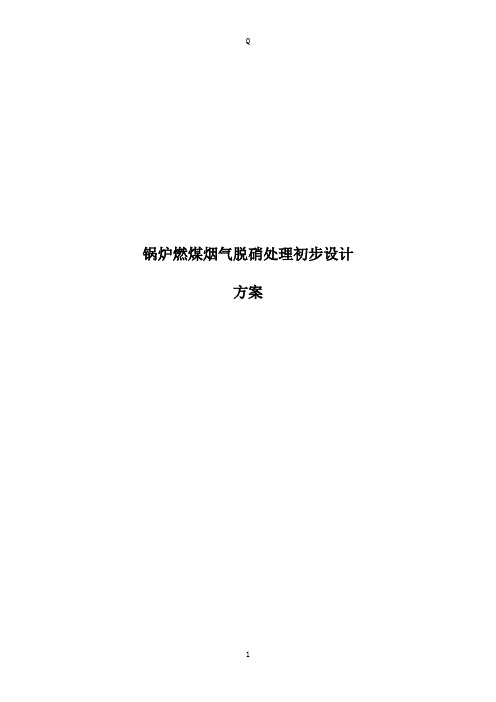
锅炉燃煤烟气脱硝处理初步设计方案目录1、项目概况 (4)2、脱硝工艺简述 (4)2.1 脱硝工艺介绍 (4)2.2 选择性催化还原法(SCR)技术介绍 (4)2.2.1 SCR工作原理 (4)2.2.2 SCR系统组成 (5)2.2.3 SCR工艺流程 (5)2.3.4 SCR反应过程 (6)2.3.5 SCR技术特点 (6)2.4 选择性非催化还原法(SNCR)技术介绍 (6)2.4.1 SNCR工作原理 (6)2.4.2 SNCR系统组成 (6)2.4.4 SNCR反应过程 (7)2.4.5 SNCR技术特点 (8)2.5 SNCR+SCR联合工艺介绍 (8)2.5.1 SNCR+SCR联合工艺工作原理 (8)2.5.2 SNCR+SCR联合工艺的系统组成 (9)2.5.3 SNCR+SCR联合工艺流程 (9)2.5.4 SNCR+SCR联合工艺反应过程 (9)2.5.5 SNCR+SCR联合工艺特点 (9)3、本方案采用的SNCR系统 (12)3.1 系统组成 (12)3.2 系统简述 (13)3.2.1 尿素溶液输送系统 (13)3.2.3 炉前喷射设备 (14)3.3 其工艺流程简图如下: (14)3.4 SNCR工艺的经济性分析 (15)4、后续的SCR工艺 (16)5、工艺计算 (16)5.1设计基础参数(单台) (16)5.2物料衡计算 (17)5.2.1 影响脱硝率的因素 (17)5.2.2 设计参数取值 (17)5.2.3 计算过程 (17)6、SNCR-SCR联合工艺脱硝预期效果 (17)1、项目概况有两台200t/h燃煤锅炉,已建成除尘脱硫装置,但随着国家对烟气排放标准要求的日益提高,锅炉的脱硝工作也被提到了议事日程,在这个背景下,受该公司委托,我公司特编报此脱硝初步方案,供业主参考。
2、脱硝工艺简述2.1 脱硝工艺介绍氮氧化物(NOx)是在燃烧工艺过程中由于氮的氧化而产生的气体,它不仅刺激人的呼吸系统,损害动植物,破坏臭氧层,而且也是引起温室效应、酸雨和光化学反应的主要物质之一。
脱硝系统工艺流程
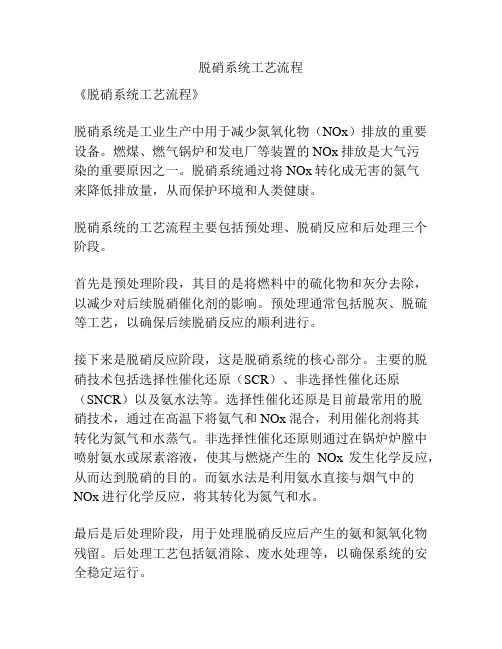
脱硝系统工艺流程
《脱硝系统工艺流程》
脱硝系统是工业生产中用于减少氮氧化物(NOx)排放的重要设备。
燃煤、燃气锅炉和发电厂等装置的NOx排放是大气污
染的重要原因之一。
脱硝系统通过将NOx转化成无害的氮气
来降低排放量,从而保护环境和人类健康。
脱硝系统的工艺流程主要包括预处理、脱硝反应和后处理三个阶段。
首先是预处理阶段,其目的是将燃料中的硫化物和灰分去除,以减少对后续脱硝催化剂的影响。
预处理通常包括脱灰、脱硫等工艺,以确保后续脱硝反应的顺利进行。
接下来是脱硝反应阶段,这是脱硝系统的核心部分。
主要的脱硝技术包括选择性催化还原(SCR)、非选择性催化还原(SNCR)以及氨水法等。
选择性催化还原是目前最常用的脱
硝技术,通过在高温下将氨气和NOx混合,利用催化剂将其
转化为氮气和水蒸气。
非选择性催化还原则通过在锅炉炉膛中喷射氨水或尿素溶液,使其与燃烧产生的NOx发生化学反应,从而达到脱硝的目的。
而氨水法是利用氨水直接与烟气中的NOx进行化学反应,将其转化为氮气和水。
最后是后处理阶段,用于处理脱硝反应后产生的氨和氮氧化物残留。
后处理工艺包括氨消除、废水处理等,以确保系统的安全稳定运行。
总的来说,脱硝系统工艺流程是一个非常复杂的过程,需要各种工艺和设备配合协调。
只有严格按照流程进行操作,并确保设备的高效运行,才能达到减少NOx排放、保护环境的目的。
燃煤电厂烟气脱硝技术

SCR反应机理
SCR是目前最成熟的脱硝技术,利用还原剂(NH3、尿素)在 金属催化剂的作用下,选择性与NOx反应生成N2和H2O,而不是 被氧气氧化,故称为“选择性”。
催化的作用是降低分解反应的活化能,使其反应温度降低至 150—450 ℃之间,其反应如下:
scr工艺流程锅炉省煤器脱硝反应器除尘脱硫装置引风机烟囱sncr选择性非催化还原技术选择性非催化还原sncr脱硝工艺是将含有nhx基的还原剂如氨气氨水或者尿素等喷入炉膛温度为9001100的区域还原剂通过安装在屏式过热器区域的喷枪喷入该还原剂迅速热分解成nh3和其它副产物随后nh3与烟气中的nox进行sncr反应而生成n2和h2osncr是当前nox治理中广泛采用且具有前途的炉内脱硝技术之一
研究背景-NOx简介
NOx简介
热力型NOx
热力型NOx是指空气中的N2 与O2在高温条件(1800K)条 件下反应生成的NOx。温度 对热力型NOx的生成起到决 定性作用。
快速型NOx
快速型NOx在燃烧的早期形 成,快速型NOx和燃料型 NOx有着完全相同的反应途 径,所谓的快速型NOx是相 对于燃料型NOx的缓慢反应 速度而言的。
燃料型NOx
燃料型NOx是由燃料中 氮化合物在燃烧中氧 化而成,燃料型NOx的 形成通常包括挥发性 NO与焦炭性NO两种途 径。
NOx减排措施
目前,主要的NOx减排措施主要有两种:燃烧前燃烧控制和燃 烧后烟气脱硝
01
燃烧控制
02
烟气脱硝
主要是通过低NOx燃烧 技术:低过量空气系数法、 空气分级燃烧法(OFA)、 燃料分级燃烧法、烟气再 循环法等
SCR法烟气脱硝的设备及工艺流程_[全文]
![SCR法烟气脱硝的设备及工艺流程_[全文]](https://img.taocdn.com/s3/m/5e822b1091c69ec3d5bbfd0a79563c1ec5dad704.png)
SCR法烟气脱硝的设备及工艺流程摘要:煤、石油、天然气等化石燃料的燃烧会产生二氧化碳(CO2)、二氧化硫(SO2)、氮氧化物(NOx)和颗粒物等污染物,其中燃煤燃烧产生的污染物最为严重,是我国目前大气污染物的主要来源。
目前,我国的发电机组绝大多数为燃煤机组,而以燃煤为主的电力生产所造成的环境污染是制约电力工业发展的一个重要因素。
其中氮氧化物(NOx)是继粉尘和硫氧化物(SOx)之后燃煤电站环保治理的重点,因此根据相关环境法律法规的要求,需要在燃煤锅炉尾部加装脱硝装置。
烟气脱硝应用较多的是选择性催化还原法(SCR)、选择性非催化还原法(SNCR)及SNCR/SCR联合技术,由于高的还原率及技术的广泛使用,选择性催化还原(SCR)已成为目前国内外电站烟气脱硝的主流技术。
本文分析了选择性催化还原(SCR)技术的脱硝原理、工艺流程、设备布置和系统组成。
关键词:氮氧化物,SCR,工艺流程自从20世纪80年代人们开始对燃煤电厂NOx排放控制方法的研究工作以来,目前已经出现了许多烟气脱硝技术,如:选择性催化还原法(SCR)、选择性非催化还原法(SNCR)、液体吸收法、微生物吸收法、活性炭吸附法、电子束法(EBA)、脉冲电晕等离子体法(PPCP)、液膜法、微波法等等,其中应用较多、已实现商业化的是选择性催化还原法(SCR)。
SCR烟气脱硝系统采用氨气(NH3)作为还原介质,国外较多使用无水液氨。
基本原理是把符合要求的氨气喷入到烟道中,与原烟气充分混合后进入反应塔,在催化剂的作用下,并在有氧气存在的条件下,选择性的与烟气中的NOx(主要是NO、NO2)发生化学反应,生成无害的氮气(N2)和水(H2O)。
SCR系统一般由氨的储存系统、氨与空气混合系统、氨气喷入系统、反应器系统和旁路系统(省煤器旁路和SCR旁路)等组成。
图1-1为SCR法烟气脱硝的工艺流程示意图首先,液氨由槽车运送到液氨储罐贮藏,无水液氨的储存压力取决于储罐的温度(例如20℃时压力为lMPa)。
SNCR烟气脱硝技术工艺流程示意图
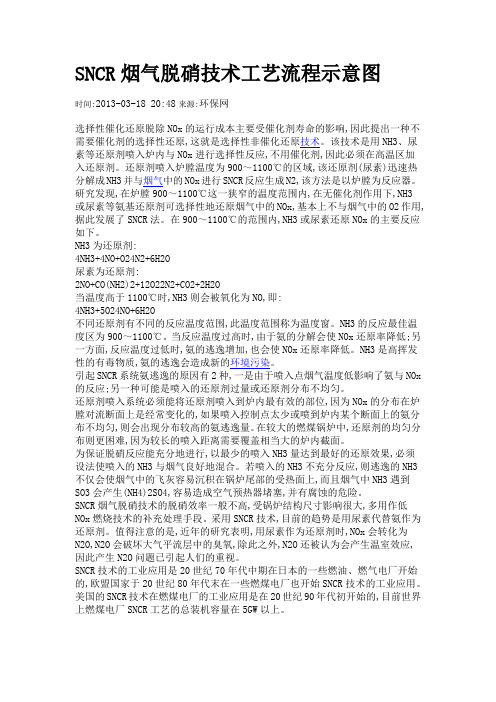
SNCR烟气脱硝技术工艺流程示意图时间:2013-03-18 20:48来源:环保网选择性催化还原脱除NOx的运行成本主要受催化剂寿命的影响,因此提出一种不需要催化剂的选择性还原,这就是选择性非催化还原技术。
该技术是用NH3、尿素等还原剂喷入炉内与NOx进行选择性反应,不用催化剂,因此必须在高温区加入还原剂。
还原剂喷入炉膛温度为900~1100℃的区域,该还原剂(尿素)迅速热分解成NH3并与烟气中的NOx进行SNCR反应生成N2,该方法是以炉膛为反应器。
研究发现,在炉膛900~1100℃这一狭窄的温度范围内,在无催化剂作用下,NH3或尿素等氨基还原剂可选择性地还原烟气中的NOx,基本上不与烟气中的O2作用,据此发展了SNCR法。
在900~1100℃的范围内,NH3或尿素还原NOx的主要反应如下。
NH3为还原剂:4NH3+4NO+O24N2+6H2O尿素为还原剂:2NO+CO(NH2)2+12O22N2+CO2+2H2O当温度高于1100℃时,NH3则会被氧化为NO,即:4NH3+5O24NO+6H2O不同还原剂有不同的反应温度范围,此温度范围称为温度窗。
NH3的反应最佳温度区为900~1100℃。
当反应温度过高时,由于氨的分解会使NOx还原率降低;另一方面,反应温度过低时,氨的逃逸增加,也会使NOx还原率降低。
NH3是高挥发性的有毒物质,氨的逃逸会造成新的环境污染。
引起SNCR系统氨逃逸的原因有2种,一是由于喷入点烟气温度低影响了氨与NOx 的反应;另一种可能是喷入的还原剂过量或还原剂分布不均匀。
还原剂喷入系统必须能将还原剂喷入到炉内最有效的部位,因为NOx的分布在炉膛对流断面上是经常变化的,如果喷入控制点太少或喷到炉内某个断面上的氨分布不均匀,则会出现分布较高的氨逃逸量。
在较大的燃煤锅炉中,还原剂的均匀分布则更困难,因为较长的喷入距离需要覆盖相当大的炉内截面。
为保证脱硝反应能充分地进行,以最少的喷入NH3量达到最好的还原效果,必须设法使喷入的NH3与烟气良好地混合。
脱硝工艺流程图

脱硝工艺流程图脱硝工艺流程图由脱硝的基本步骤组成,包括废气预处理、催化剂选择、反应装置和尾气处理等环节。
下面是一份脱硝工艺流程图示例,该流程图详细描述了脱硝的工艺步骤,以及每个步骤的输入和输出物。
脱硝工艺流程图废气预处理:将含有二氧化硫(SO2)的废气经过布袋除尘和脱硫工艺处理,去除固体颗粒和SO2等杂质。
输入物为含有SO2的废气,输出物为去除固体颗粒和SO2的废气。
催化剂选择:根据废气成分和工艺要求选择适合的脱硝催化剂。
输入物为废气预处理后的气体,输出物为催化剂。
反应装置:将废气通入反应装置,与催化剂发生脱硝反应。
输入物为催化剂和废气,输出物为反应后的废气。
尾气处理:对反应后的废气进行二次脱硫和除尘处理,确保剩余固体和气态污染物达到排放标准。
输入物为反应后的废气,输出物为符合排放标准的废气。
在反应装置中,废气与催化剂接触,其中氮氧化物(NOx)与催化剂发生催化还原反应,生成氮气(N2)和水(H2O)。
脱硝反应的化学方程式为:2NO + 2NH3 → 2N2 + 3H2O。
因此,催化剂的选择和控制是脱硝工艺中的关键步骤。
在尾气处理过程中,废气需要经过二次脱硫工艺,去除残余的SO2。
常见的二次脱硫工艺有湿法脱硫和干法脱硫两种。
湿法脱硫是将废气与吸收液(如石灰石浆液)接触,利用化学反应将SO2转化为硫酸盐。
干法脱硫则是通过固定床或流化床吸附剂,吸附和转化废气中的SO2为固体硫化物。
二次脱硫过程也包括废气的除尘处理,以去除残留的固体颗粒。
最后,经过尾气处理的废气达到排放标准后,可以安全地排放到大气中。
以上是一份简要的脱硝工艺流程图,根据实际情况,该流程图可以进行相应的调整和细化。
脱硝工艺是一项重要的大气污染治理技术,通过合理的工艺流程和催化剂选择,可以有效减少大气中的氮氧化物污染。
燃煤锅炉的选择性催化还原烟气脱硝技术
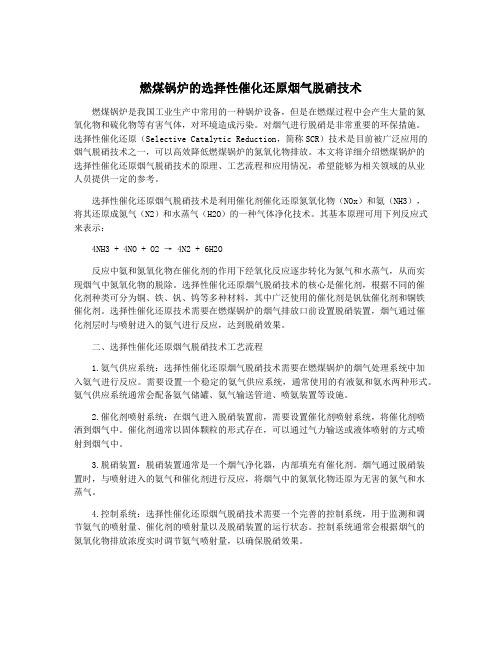
燃煤锅炉的选择性催化还原烟气脱硝技术燃煤锅炉是我国工业生产中常用的一种锅炉设备,但是在燃煤过程中会产生大量的氮氧化物和硫化物等有害气体,对环境造成污染。
对烟气进行脱硝是非常重要的环保措施。
选择性催化还原(Selective Catalytic Reduction,简称SCR)技术是目前被广泛应用的烟气脱硝技术之一,可以高效降低燃煤锅炉的氮氧化物排放。
本文将详细介绍燃煤锅炉的选择性催化还原烟气脱硝技术的原理、工艺流程和应用情况,希望能够为相关领域的从业人员提供一定的参考。
选择性催化还原烟气脱硝技术是利用催化剂催化还原氮氧化物(NOx)和氨(NH3),将其还原成氮气(N2)和水蒸气(H2O)的一种气体净化技术。
其基本原理可用下列反应式来表示:4NH3 + 4NO + O2 → 4N2 + 6H2O反应中氨和氮氧化物在催化剂的作用下经氧化反应逐步转化为氮气和水蒸气,从而实现烟气中氮氧化物的脱除。
选择性催化还原烟气脱硝技术的核心是催化剂,根据不同的催化剂种类可分为铜、铁、钒、钨等多种材料,其中广泛使用的催化剂是钒钛催化剂和铜铁催化剂。
选择性催化还原技术需要在燃煤锅炉的烟气排放口前设置脱硝装置,烟气通过催化剂层时与喷射进入的氨气进行反应,达到脱硝效果。
二、选择性催化还原烟气脱硝技术工艺流程1.氨气供应系统:选择性催化还原烟气脱硝技术需要在燃煤锅炉的烟气处理系统中加入氨气进行反应。
需要设置一个稳定的氨气供应系统,通常使用的有液氨和氨水两种形式。
氨气供应系统通常会配备氨气储罐、氨气输送管道、喷氨装置等设施。
2.催化剂喷射系统:在烟气进入脱硝装置前,需要设置催化剂喷射系统,将催化剂喷洒到烟气中。
催化剂通常以固体颗粒的形式存在,可以通过气力输送或液体喷射的方式喷射到烟气中。
3.脱硝装置:脱硝装置通常是一个烟气净化器,内部填充有催化剂。
烟气通过脱硝装置时,与喷射进入的氨气和催化剂进行反应,将烟气中的氮氧化物还原为无害的氮气和水蒸气。
燃煤锅炉的选择性催化还原烟气脱硝技术

燃煤锅炉的选择性催化还原烟气脱硝技术选择性催化还原(Selective Catalytic Reduction,SCR)是一种通过给予适量还原剂将氮氧化物(NOx)转化为氮气(N2)和水蒸气的技术。
SCR技术已被广泛应用于燃煤锅炉的烟气脱硝过程中,能够有效降低燃煤锅炉排放的氮氧化物浓度,减少大气污染物的排放。
SCR技术主要包括还原剂注入系统、反应器、催化剂和氧化剂注入系统等主要部分。
还原剂通常是氨或尿素,用来在反应器中与NOx反应生成氮气和水蒸气。
催化剂则是通过改变反应物的活性能够加速反应速率的物质。
燃煤锅炉的SCR系统可以根据不同的工况和要求进行选择。
催化剂的选择要考虑到其耐热性和耐腐蚀性,以应对高温和腐蚀性气体的冲击。
常用的催化剂有钒钛催化剂、钴钛催化剂、锆钛催化剂等。
还需要考虑催化剂的净化效率和耐毒性。
净化效率是指催化剂对NOx的转化率,一般要求在70%以上。
耐毒性是指催化剂对氨、尿素等还原剂以及烟气中的硫酸雾等毒性物质的抗腐蚀能力,一般要求催化剂在使用寿命内保持较高的活性。
还需考虑SCR系统的运行成本和能耗。
还原剂的消耗量和催化剂的使用寿命对系统运行成本有着重要影响。
选择适当的还原剂注入系统和氧化剂注入系统能够降低能耗。
在选择SCR技术时,还需考虑到实际情况和技术要求。
不同类型的燃煤锅炉存在着不同的烟气温度、氮氧化物浓度和硫氧化物浓度等特点,需要根据实际情况进行技术调整和优化。
燃煤锅炉的选择性催化还原烟气脱硝技术是一种有效降低锅炉排放的NOx浓度的技术。
在选择催化剂、还原剂注入系统和氧化剂注入系统等方面都需要考虑到耐热性、耐腐蚀性、净化效率、耐毒性、运行成本和能耗等多个因素。
只有综合考虑以上因素,才能选择出适合燃煤锅炉的SCR技术,提高燃煤锅炉的环保水平和经济性。
燃煤锅炉的选择性催化还原烟气脱硝技术

燃煤锅炉的选择性催化还原烟气脱硝技术燃煤锅炉是目前我国工业生产中常用的热能设备,但是燃煤锅炉排放的烟气中含有大量的氮氧化物,其中主要成分为氮氧化物(NOX)。
高浓度的NOX不仅会对环境造成严重污染,还会对人体健康产生不良影响。
燃煤锅炉的NOX排放成为大气污染治理的重点之一。
为了减少燃煤锅炉排放的NOX,选择性催化还原(SCR)烟气脱硝技术被广泛应用。
SCR 技术通过将氨和烟气中的NOX在催化剂的作用下进行反应,将NOX还原成氮气和水,从而达到脱硝的目的。
本文将重点介绍燃煤锅炉的选择性催化还原烟气脱硝技术的选择原则、工艺流程及影响因素等内容。
1.适用性分析:燃煤锅炉的选择性催化还原烟气脱硝技术需要根据燃煤锅炉的排放特点来进行适用性分析。
需要考虑的因素包括燃煤锅炉的烟气温度、NOX排放浓度、燃料性质、燃烧特性等。
2.环保要求:根据国家和地方对燃煤锅炉NOX排放的环保要求,选择合适的SCR系统技术参数和催化剂性能。
3.经济性分析:在选择SCR系统时,还需要进行经济性分析,包括投资成本、运行维护成本、能耗等方面的考虑。
4.可靠性考虑:SCR系统是燃煤锅炉脱硝的关键设备之一,其可靠性对脱硝效果和设备运行稳定性具有重要影响,因此在选择SCR系统时,需考虑其可靠性。
二、工艺流程SCR系统的基本工艺流程包括氨水制备系统、氨水喷射系统、SCR反应器、氨水喷洒均匀性控制系统、变压器、废气均匀性控制系统等。
1.氨水制备系统:氨水制备系统主要由氨气(NH3)制备装置组成,氨气是SCR技术中的还原剂,通过氨气制备装置将液氨和水进行混合制备成氨水。
2.氨水喷射系统:氨水喷射系统主要由氨水喷射器、氨水喷射管和气流分配装置组成,其作用是将制备好的氨水喷射到燃烧炉的烟气中。
3.SCR反应器:SCR反应器是SCR系统的核心部件,是进行NOX还原的主要场所,通常是采用催化床进行NOX还原反应。
4.氨水喷洒均匀性控制系统:氨水在烟气中的喷洒均匀性对SCR反应器的性能有重要影响,因此需要设计合理的氨水喷洒均匀性控制系统。
火电厂脱硝工艺流程图
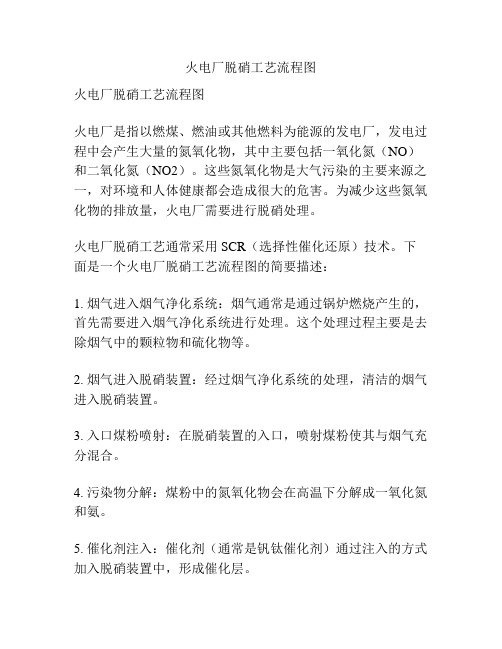
火电厂脱硝工艺流程图火电厂脱硝工艺流程图火电厂是指以燃煤、燃油或其他燃料为能源的发电厂,发电过程中会产生大量的氮氧化物,其中主要包括一氧化氮(NO)和二氧化氮(NO2)。
这些氮氧化物是大气污染的主要来源之一,对环境和人体健康都会造成很大的危害。
为减少这些氮氧化物的排放量,火电厂需要进行脱硝处理。
火电厂脱硝工艺通常采用SCR(选择性催化还原)技术。
下面是一个火电厂脱硝工艺流程图的简要描述:1. 烟气进入烟气净化系统:烟气通常是通过锅炉燃烧产生的,首先需要进入烟气净化系统进行处理。
这个处理过程主要是去除烟气中的颗粒物和硫化物等。
2. 烟气进入脱硝装置:经过烟气净化系统的处理,清洁的烟气进入脱硝装置。
3. 入口煤粉喷射:在脱硝装置的入口,喷射煤粉使其与烟气充分混合。
4. 污染物分解:煤粉中的氮氧化物会在高温下分解成一氧化氮和氨。
5. 催化剂注入:催化剂(通常是钒钛催化剂)通过注入的方式加入脱硝装置中,形成催化层。
6. 进一步反应:一氧化氮和氨在催化剂层上发生反应,生成氮和水。
7. 烟气出口处理:经过脱硝装置的处理,烟气中的氮氧化物被高效地去除,减少了对环境的污染。
处理后的烟气通过烟囱排放出去。
8. 催化剂再生:催化剂在反应中会逐渐失活,需要定期进行再生。
催化剂再生通常是利用高温脱硝气体进行。
9. 催化剂循环:再生后的催化剂通过循环系统再次注入脱硝装置,进行下一轮反应。
以上是火电厂脱硝工艺流程图的简要描述,脱硝工艺主要是通过SCR技术实现的,能够高效地去除烟气中的氮氧化物,从而减少对环境的污染。
脱硝工艺的实施对于火电厂的可持续发展和环境保护具有重要意义。
燃煤电厂烟气脱硫脱销工艺流程

燃煤电厂烟气脱硫脱销工艺流程英文回答:The process of flue gas desulfurization anddenitrification in coal-fired power plants involves several steps to remove sulfur dioxide and nitrogen oxides from the flue gas before it is released into the atmosphere. Themain technologies used for this process are wet flue gas desulfurization (FGD) and selective catalytic reduction (SCR) for denitrification.In the wet FGD process, the flue gas is brought into contact with a slurry of limestone or lime in a scrubber. The sulfur dioxide in the flue gas reacts with the alkaline slurry to form calcium sulfite or sulfate, which can be removed from the flue gas. The scrubbed flue gas is then released into the atmosphere, while the slurry is treatedto recover the sulfur and regenerate the scrubbing solution.For denitrification, the SCR process involves the useof a catalyst to convert nitrogen oxides in the flue gas to nitrogen and water. Ammonia or urea is injected into the flue gas stream, and the catalyst promotes the reaction between the nitrogen oxides and the reducing agent to remove the nitrogen oxides from the flue gas.Overall, the process of flue gas desulfurization and denitrification in coal-fired power plants is essential for reducing air pollution and meeting environmental regulations.中文回答:燃煤电厂烟气脱硫脱销工艺流程涉及几个步骤,用以在释放入大气之前从烟气中去除二氧化硫和氮氧化物。
燃煤电厂烟气脱硫脱销工艺流程

燃煤电厂烟气脱硫脱销工艺流程英文回答:The process of desulfurization and denitrification in coal-fired power plants involves several key steps to remove sulfur dioxide (SO2) and nitrogen oxides (NOx) from the flue gas.Firstly, the flue gas is passed through a wet scrubber, where a slurry of limestone and water is sprayed into the gas stream. The SO2 in the flue gas reacts with the limestone to form calcium sulfite, which is then oxidized to form gypsum. This process effectively removes the majority of the sulfur from the flue gas.Next, the flue gas passes through a selective catalytic reduction (SCR) system, where ammonia is injected into the gas stream. The NOx in the flue gas reacts with the ammonia over a catalyst, forming nitrogen and water. This process helps to significantly reduce the NOx emissions from thepower plant.After the desulfurization and denitrification processes, the cleaned flue gas is released into the atmosphere, meeting the environmental regulations for air quality.中文回答:燃煤电厂烟气脱硫脱销工艺流程涉及几个关键步骤,以去除烟气中的二氧化硫(SO2)和氮氧化物(NOx)。
燃煤烟气脱硝工艺布置及典型工艺流程、还原剂制备及耗量计算、催化剂设计选型基础数据

附 录 A (资料性)工艺布置及典型工艺流程A .1 SCR 工艺布置在燃煤电厂中的SCR 反应器一般采用高尘布置(HD ,High Dust ),位于锅炉后部省煤器与空气预热器之间(见A.1)。
FGDNH 3APH烟囱SCR锅炉空气ESP图A .1 高尘布置图图A .2 低尘布置图FGDNH 3ESP烟囱SCR锅炉空气燃烧器气/气换热器APH图A .3 尾部布置图高尘布置(HD ),SCR 反应器所处位置正好是中高温催化剂的活性温度窗口,这种布置方案烟气在进入SCR 反应器前不需要采用加热器对其进行再加热,因而投资费用与运行费用相对较低。
低尘布置(LD ),该布置方式减少了烟气中烟尘对催化剂的冲刷磨损,避免了催化剂的堵塞,延长催化剂的使用寿命,但需采用高温除尘器(Hot De-Dust )。
尾部布置(TE ),SCR 反应器位于烟气脱硫及除尘之后的低温烟气区,需要加一套额外的烟气再热系统(含烟气换热器和燃烧器),提升脱硫后烟气的温度以满足低温催化剂的温度要求,因而投资费用与运行费用相对较高。
一般情况下SCR首选高尘布置工艺。
A.2 SCR典型工艺流程如图A.4所示,典型的SCR脱硝装备工艺一般包含脱硝反应系统、还原剂储运制备系统及配套系统,其中脱硝反应系统一般由喷氨混合系统、SCR反应器、催化剂、稀释风系统等组成。
图A.4 典型SCR脱硝装备工艺流程图(以尿素水解为例)将还原剂制备系统制备得到的氨气送入氨/空气混合器内与来自稀释风机的空气充分混合,再通过喷氨混合系统将用空气稀释好的氨气喷入SCR反应器入口烟道内与烟气均匀混合,并在下游的SCR反应器内与烟气中的NO x在催化剂催化条件下发生化学反应,生成氮气和水,从而去除了烟气中的大部分NO x。
A.3 SNCR工艺布置及典型流程如图A.5所示,典型的燃煤烟气脱硝SNCR技术装备工艺一般包含脱硝反应系统和还原剂储运制备系统,其中脱硝反应系统一般由还原剂计量喷射系统、SNCR反应区域等组成。
SCR烟气脱硝工艺设计方案
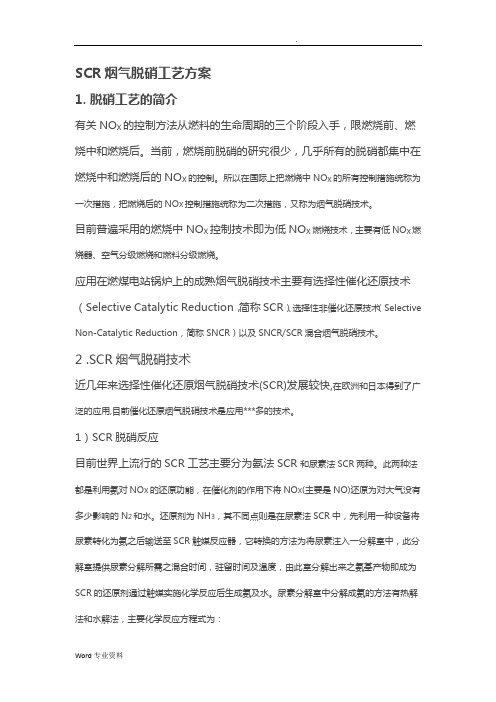
SCR烟气脱硝工艺方案1. 脱硝工艺的简介有关NO X的控制方法从燃料的生命周期的三个阶段入手,限燃烧前、燃烧中和燃烧后。
当前,燃烧前脱硝的研究很少,几乎所有的脱硝都集中在燃烧中和燃烧后的NO X的控制。
所以在国际上把燃烧中NO X的所有控制措施统称为一次措施,把燃烧后的NO X控制措施统称为二次措施,又称为烟气脱硝技术。
目前普遍采用的燃烧中NO X控制技术即为低NO X燃烧技术,主要有低NO X燃烧器、空气分级燃烧和燃料分级燃烧。
应用在燃煤电站锅炉上的成熟烟气脱硝技术主要有选择性催化还原技术(Selective Catalytic Reduction,简称SCR)、选择性非催化还原技术(Selective Non-Catalytic Reduction,简称SNCR)以及SNCR/SCR混合烟气脱硝技术。
2 .SCR烟气脱硝技术近几年来选择性催化还原烟气脱硝技术(SCR)发展较快,在欧洲和日本得到了广泛的应用,目前催化还原烟气脱硝技术是应用***多的技术。
1)SCR脱硝反应目前世界上流行的SCR工艺主要分为氨法SCR和尿素法SCR两种。
此两种法都是利用氨对NO X的还原功能,在催化剂的作用下将NO X(主要是NO)还原为对大气没有多少影响的N2和水。
还原剂为NH3,其不同点则是在尿素法SCR中,先利用一种设备将尿素转化为氨之后输送至SCR触媒反应器,它转换的方法为将尿素注入一分解室中,此分解室提供尿素分解所需之混合时间,驻留时间及温度,由此室分解出来之氨基产物即成为SCR的还原剂通过触媒实施化学反应后生成氨及水。
尿素分解室中分解成氨的方法有热解法和水解法,主要化学反应方程式为:NH2CONH2+H2O→2NH3+CO2在整个工艺的设计中,通常是先使氨蒸发,然后和稀释空气或烟气混合,***后通过分配格栅喷入SCR反应器上游的烟气中。
典型的SCR反应原理示意图如下:在SCR反应器,NO通过以下反应被还原:4NO+4NH3+O2→3N2+6H2O6NO+4NH3→5N2+6H2O当烟气中有氧气时,反应第一式优先进行,因此,氨消耗量与NO还原量有一对一的关系。
- 1、下载文档前请自行甄别文档内容的完整性,平台不提供额外的编辑、内容补充、找答案等附加服务。
- 2、"仅部分预览"的文档,不可在线预览部分如存在完整性等问题,可反馈申请退款(可完整预览的文档不适用该条件!)。
- 3、如文档侵犯您的权益,请联系客服反馈,我们会尽快为您处理(人工客服工作时间:9:00-18:30)。
附 录 A (资料性)工艺布置及典型工艺流程A .1 SCR 工艺布置在燃煤电厂中的SCR 反应器一般采用高尘布置(HD ,High Dust ),位于锅炉后部省煤器与空气预热器之间(见A.1)。
FGDNH 3APH烟囱SCR锅炉空气ESP图A .1 高尘布置图图A .2 低尘布置图FGDNH 3ESP烟囱SCR锅炉空气燃烧器气/气换热器APH图A .3 尾部布置图高尘布置(HD ),SCR 反应器所处位置正好是中高温催化剂的活性温度窗口,这种布置方案烟气在进入SCR 反应器前不需要采用加热器对其进行再加热,因而投资费用与运行费用相对较低。
低尘布置(LD ),该布置方式减少了烟气中烟尘对催化剂的冲刷磨损,避免了催化剂的堵塞,延长催化剂的使用寿命,但需采用高温除尘器(Hot De-Dust )。
尾部布置(TE ),SCR 反应器位于烟气脱硫及除尘之后的低温烟气区,需要加一套额外的烟气再热系统(含烟气换热器和燃烧器),提升脱硫后烟气的温度以满足低温催化剂的温度要求,因而投资费用与运行费用相对较高。
一般情况下SCR首选高尘布置工艺。
A.2 SCR典型工艺流程如图A.4所示,典型的SCR脱硝装备工艺一般包含脱硝反应系统、还原剂储运制备系统及配套系统,其中脱硝反应系统一般由喷氨混合系统、SCR反应器、催化剂、稀释风系统等组成。
图A.4 典型SCR脱硝装备工艺流程图(以尿素水解为例)将还原剂制备系统制备得到的氨气送入氨/空气混合器内与来自稀释风机的空气充分混合,再通过喷氨混合系统将用空气稀释好的氨气喷入SCR反应器入口烟道内与烟气均匀混合,并在下游的SCR反应器内与烟气中的NO x在催化剂催化条件下发生化学反应,生成氮气和水,从而去除了烟气中的大部分NO x。
A.3 SNCR工艺布置及典型流程如图A.5所示,典型的燃煤烟气脱硝SNCR技术装备工艺一般包含脱硝反应系统和还原剂储运制备系统,其中脱硝反应系统一般由还原剂计量喷射系统、SNCR反应区域等组成。
图A.5 典型SNCR脱硝装备工艺流程图(以尿素为例)还原剂(以尿素为例)溶液在稀释和计量分配后通过喷枪雾化喷入炉膛内,在合适的温度区间与NO x反应,生成氮气和水,达到脱硝效果。
A.4 SNCR-SCR联合法工艺典型流程燃煤锅炉中典型的燃煤烟气脱硝SNCR-SCR联合法技术装备为SNCR和SCR的组合,兼顾了脱硝性能和经济性。
如图A.6和A.7所示,SNCR-SCR联合法有两种典型流程,图A.6常用于对现有锅炉的改造,图A.7多用于新建锅炉同步建设脱硝装备。
图A.6 典型SNCR-SCR联合法工艺流程图(内置式)图A.7 典型SNCR-SCR联合法工艺流程图(外置式)附录B(资料性)还原剂的制备及耗量的计算方法B.1 还原剂的制备B.1.1 SCR还原剂制备方法B.1.1.1 液氨法:通过液氨卸料压缩机将液氨由槽车送入储氨罐内,储氨罐内的液氨在压差和自身重力势能的作用下被送至液氨蒸发器内蒸发为氨气,氨气送到氨气缓冲槽经调压阀减压后,送入氨/空气混合器中与来自稀释风机的空气充分混合,再通过喷氨混合系统将用空气稀释好的氨气喷入SCR反应器入口烟道内与烟气均匀混合,随后进入下游的SCR反应器。
氨气系统紧急排放的氨气则引入氨气稀释槽中,经水吸收排入废水池,再由废水泵送至废水处理厂处理。
B.1.1.2 氨水法:将10%~28%的氨水溶液,通过加热装置使其蒸发,并引出氨气。
一般可采用接触式蒸发器法、喷淋式蒸发器法和间壁式蒸发器法。
B.1.1.3 尿素法:一般有水解法和热解法两种。
B.1.1.3.1 水解法:有普通水解法和催化水解法两种,主要流程基本相似。
将储料仓中的干尿素(NH2CONH2)送入混合罐中,通过加水搅拌使尿素完全溶解。
在水解槽中,尿素溶液通过蒸汽预热器加热到一定的温度和压力下,并与水反应成氨和二氧化碳。
催化水解是在普通水解基础上,向水解槽内添加催化剂,提高了水解反应速度,对锅炉负荷变化时的氨需求量有更好的响应速度。
B.1.1.3.2 热解法:将一定温度的空气送入专门设计的热解室,使喷入热解室的高浓度尿素溶液转化成氨气。
B.1.2 SNCR还原剂制备方法B.1.2.1 氨水法:将10%~28%的氨水溶液,通过稀释、计量、分配后通过喷枪送至炉膛内温度适合的区间。
B.1.2.2 尿素法:将50%的尿素溶液,通过稀释、计量、分配后通过喷枪送至炉膛内温度适合的区间。
由于氨水喷入炉膛会迅速气化为氨气,尿素液滴渗入烟气中的运动距离比氨水远,对于较大尺寸的炉膛,一般采用尿素溶液。
B.1.3 还原剂制备原料比较B.1.3.1 液氨属于危险品,需十分注意运输条件和卸料储存的安全防护;氨水容易运输,较液氨安全,氨水区更易整合在电厂总平面布置中,但是运输体积大、长距离运输时不经济。
B.1.3.2 尿素是安全原料(肥料),湿或干的形态都容易运输,但是其制氨的系统相对液氨和氨水来得复杂,设备占地面积大,储存量大时需考虑潮解问题。
B.1.4 安全考虑B.1.4.1 氨对铜、铜合金、铝等有腐蚀性,相关的管道、阀门以及仪器上应严格禁铜。
B .1.4.2 为防止氨气逆流,应设置止回阀。
B .1.4.3 考虑到氨的毒性,在管和管接头、以及阀门类的连接处,应采用焊接连接;若不能采用焊接连接时,也可采用法兰连接,但应采取相应的加强严密性的措施。
B .1.4.4 各管道设备应采取防止静电的接地措施。
B .2 还原剂耗量的计算方法基于SCR 入口烟气中NO 浓度和NO 2浓度,脱硝装备氨小时消耗量按式B.1、式B.2计算。
Q= (62326310210⨯⨯⨯⨯+⨯⨯⨯NO NH NO NO NH NO M M C F M M C F ) ×n …………………(B.1)n= 100)2/(//2233η+⨯+NO NO NO NO NH slipNH M C M C M C …………………………(B.2)基于SCR 入口烟气中NO x 浓度(以NO 2计),脱硝装备氨小时消耗量按式B.3、式B.4计算。
Q= (623110⨯⨯⨯NO NH M M C F ) ×n …………………………(B.3)n= 100//2133η+NO NH slipNH M C M C …………………………(B.4)式(B.1~B.4)中:Q ——氨小时耗量,单位为千克每小时(kg/h );F ——锅炉BMCR 工况入口烟气流量 (标准状态,干基,6%O 2),单位为立方米每小时(m³/h );M NO ——入口烟气中NO 的摩尔质量,单位为克每摩尔(g/mol ); M NO 2——入口烟气中NO 2的摩尔质量,单位为克每摩尔(g/mol ); M NH 3——入口烟气中NH 3的摩尔质量,单位为克每摩尔(g/mol ); C NO ——入口烟气中NO 浓度,单位为毫克每立方米(mg/m³); C NO 2——入口烟气中NO 2浓度,单位为毫克每立方米(mg/m³);C 1——脱硝装备入口烟气中NO x 的浓度(以NO 2计),单位为毫克每立方米(mg/m 3); n ——氨氮摩尔比;C slipNH 3——氨逃逸,单位为毫克每立方米(mg/m³);η——脱硝效率,%。
附录C(资料性)催化剂及催化剂设计选型的基础数据C.1 催化剂材料以钒钛系催化剂为例。
钒钛系催化剂一般由TiO2、V2O5、WO3、MoO3等物质组成。
催化剂材料从功能上划分,可分为活性成分、载体和辅助材料三部分。
所谓活性成分,指能促使氨气与NO x发生化学反应的络合体成分。
一般可以用金属、金属氧化物、活性炭等作为活性成分。
载体是使活性成分得以分散的媒体物质,为了增加活性成分与烟气的接触机会,一般都用多孔质的物质作为载体,且与活性物质相协调,使活性物质均匀分散。
作为载体使用的物质中,有各种多孔质的陶瓷类,矿物等,一般采用铝、钛、硅等的氧化物多孔质材料。
辅助材料主要是指保证为催化剂的机械强度而使用的粘结剂或骨料,根据催化剂的不同形状,可分别采用高岭土、玻璃纤维、陶瓷、钢板、铁丝网等作为载体。
C.2 催化剂选择催化剂的选择应根据烟气特性、飞灰特性、灰份含量、反应器形状、脱硝效率、氨逃逸、SO2/SO3转化率、装备压力降以及使用寿命等条件综合考虑。
当煤质含硫量高时,可选择SO2/SO3转化率低的催化剂,防止对下游设备产生影响;当飞灰含量高时,可选择具有高耐磨损性的催化剂。
含有SO2或者SO3的烟气中,应避免使用多孔质氧化铝(矾土)作为催化剂载体,以避免与SO2和SO3作用形成亚硫酸盐和硫酸盐。
此时,催化剂载体可选用钛或硅的氧化物作为催化剂载体。
C.3 催化剂失活由于受到烟气中的气体条件、粉尘条件和温度条件方面因素的影响,催化剂的活性一般都会随着时间的延长而降低,主要原因如下:1)烟气中成分(碱金属、碱土金属、As、卤素等)使催化剂中毒,降低催化剂的活性;2)烟气中飞灰对催化剂的冲刷、玷污、堵塞,降低催化剂的活性;3)温度过高,引起催化剂烧结,致使催化剂失活。
不同的催化剂有不同的活性温度窗口。
中高温催化剂烟气温度范围控制在300℃~420℃,过高或过低的温度都会导致催化剂无法正常起到催化作用,致使系统脱硝效率降低。
当催化剂工作温度长期低于300℃时,烟气中的SO2经过氧化,与还原剂形成硫酸氢铵,硫酸氢铵在300℃下易粘附、堵塞催化剂,并对后续设备造成影响,选型时需要考虑其影响。
不同厂家、不同配方、不同温度时催化剂所适用的SO2浓度有所差异,图C.1为其中一种催化剂的最大适用SO2浓度与温度关系曲线,供参考,工程应用时应向专业厂家咨询。
图C.1 某种催化剂最大适用SO2浓度与温度关系C.4 催化剂设计选型的基础数据催化剂设计选型的基础数据一般应包括表C.1、表C.2中的信息:表C.1 煤质资料及灰分特性名称符号单位设计煤种校核煤种煤种工业分析全水分Mt %空气干燥基水分Mad %收到基灰分A ar %干燥无灰基挥发分Vdaf %煤种元素分析收到基碳Car %收到基氢Har %收到基氮Nar %收到基氧Oar %全硫St.ar %收到基高位发热量Qgr.ar MJ/kg收到基低位发热量Qnet.ar MJ/kg哈氏可磨指数HGI /煤的冲刷磨损指数Ke /煤中微量元素煤中游离二氧化硅SiO2(F)%煤中氟Far μg/g煤中氯Clar %煤中汞Hgar μg/g表C.2 SCR入口烟气参数在SCR烟气脱硝工程项目前期,还应尽量提供有助于催化剂设计的相关数据如主体工程每年在各种负荷工况下的预计运行时间等。
如果项目中应用到多种燃料,催化剂设计选型的基础数据还应包括各种燃料所使用的比例。