研磨机设计
新型药品研磨机的结构设计

研磨 机 的研 磨装 置用 于完 成药 品 的研磨 ,它 包括 动盘 、静盘 、铰 链 、搅拌 棒 、滤 网等零 件 ,
研 磨装置 如 图 2所 示 。
Байду номын сангаас
i uuuu \ J  ̄mmm
f mmmm uuuu
i 砌面盯
… … … ~
佩
… … 一
研磨珠的速度: 丽 m万
n 9 / n =7 5rmi
r n ’ : —— , ’= — ,
—
1 65 9 0 . x7 5 =— — =4 3 .3 mm/ 4 2 mn/ 09 5 l ¥ 6 O 6 0
: —
—
:
2 . — 34x
4 3 .3 5 4 3 .3 5 4 09 2 4 09 2 x
《
图 1 药 品研 磨 机 结 构 简 图
1电机 ;2壳 体;3传 动系 统:4研 磨装 置 . . . .
本 款研磨 机 是通过 电动机 驱动 带动 小带 轮转 动 ,通 过带传 动 使主轴 转 动 。 当主 轴转 动 时 , 由
图 2 研 磨 装 置
I 网 ;2铰链 ;3静盘 ;4搅 拌棒 ;5 盘 滤 . . . . 动
l 药品研磨机的整体设计
本 款研磨 机 由电机 、 壳体 、传 动系 统 、研磨 装置 等零 部件 组成 ,其 结构简 图如 图 1 所示 。
料装 置 ,为 了进料 方 便 ,主轴 的顶 部 设计成 漏 斗 形状 。主 轴底 部 要与 动盘 连接 ,同时还 要使 药 品 进入 研磨 盘 ,所 以底部 打有 出料孔 和螺 纹孔 。
装 搅拌 棒 ,动盘 位于 两个 静盘 的 中间 , 内腔 分成 前 后两个 , 不仅增 大 了体积 而且充 分利 用 了资源 。 静 盘有 两个 ,选 用不 锈钢 制作 。静 盘在 设备 工作 中是 固定不 动 的, 设计时 考虑 其如 何与 机身 安装 在 一起 。静 盘不 宜直 接安 装在 机身 上 ,设计 时 需
平面高速研磨机设计【文献综述】

毕业论文文献综述机械设计制造及其自动化平面高速研磨机设计一、研究现状、发展趋势目前,国内外研磨加工主要还是采用散粒磨料在慢速研磨机上研磨。
其特点是加工精度高、加工设备简单、投资少,但是加工精度不稳定、加工成本高、效率底。
正是由于散粒磨料研磨存在一些不足,所以许多学者在研究改进这种研磨加工技术。
有人研究新型研磨液,以改善研磨效果;还有人研究不同磨料和不同材料磨盘的研磨效果,以寻求对应于不同工件的最佳磨料及磨盘。
研磨加工面形范围很广,几乎可以加工任何面形的工件。
对于不同面形的工件,研磨加工方式不同,于是人们针对不同面形的工件探讨了不同的加工方法。
Jeong-Du Kim,Min-Seog Choi 和Taleo Shinmura, Toshio Aizawa 等人专门研究了圆柱面的研磨加工。
杉浦修等人研究采用磁力研磨法加工圆柱面的研磨机取得了较好的效果。
我国也有一些学者从事圆柱面研磨加工的研究,如天津大学的邓广敏等人专门研究了陶瓷圆柱面的研磨,周俊研究了主轴套管的研磨,朱长茂研究了高精度小轴的研磨加工。
在金属切削加工中,刀具的质量直接影响着被加工工件的质量。
为提高工件的质量,人们对刀具提出了较高的要求,特别是用于精密和超精密加工的金刚石刀具都要采用研磨加工。
因此国内外一些人专门从事刀具研磨加工技术研究,取得了一些进展。
为了提高研磨加工效率,在研磨中不仅一次研磨加工工件的一个表面,而且还可以同时加工工件的两个表面。
于是有人研制出双面研磨机。
日本的Toshiroh Karaki-dog等人还研究可双面研磨加工工艺,为双面研磨技术的应用创造了良好的条件。
一些学者专门研究将双面研磨技术应用于加工硅片(集成电路的基片),并成功地应用于生产上。
球面是一种较为常用的曲面,特别是在光学系统中和轴承上,其研磨加工量非常大。
因此有人专门研究了球面研磨加工技术、加工机床及加工机理,取得了很好的效果。
在光学系统中应用非球面元件可以使复杂的系统结构变得较为简单。
毕业论文—平面研磨机设计

摘要研磨是一种重要的精密和超精密加工方法,它是利用磨具通过磨料作用于工件表面,进行微量加工的过程。
研磨加工可以得到很高的尺寸精度和形状精度,甚至可以达到加工精度的极限。
本设计采用现代设计方法学为指导,给出了圆柱端面研磨机的黑箱模型和整机功能的形态学矩阵,依据形态学矩阵制定出研磨机机具体方案。
通过MATlAB软件中的优化函数对方案中主要运动部件的参数进行优化。
设计出了一台双驱动两自由度行星式圆柱端面研磨机。
建立数学模型,计算出工作时加工零件的运动方程,通过MATLAB软件绘制了运动运动轨迹。
最后通过对研磨轨迹的分析,确定了系杆和内齿轮的转速范围。
【关键词】行星式研磨机功能分析运动轨迹MATLAB软件AbstractLapping is an important precision and ultra precision machining method, which is the use of abrasive through the abrasive effect on the surface, the micro machining pping can get very high dimensional accuracy and form accuracy, even up to the limits of precision. The design uses a modern design methodology as a guide, cylindrical lapping machine is given black-box model and the whole function of the morphological matrix, based on morphological matrix to develop specific programs grinder machine. By MATlAB optimal function in the software program in the main moving parts of the parameters were optimized. Design of a dual drive planetary two degrees of freedom cylindrical grinding machine. Established Mathematical model, calculate the equation of motion of machine parts,through the MATLAB software to draw the motion traces. Finally, through the analysis of lapping trajectory to determine the tie rod and the gear speed range.【Key words】planetary; functional Analysis; lapping machine; motion traces;MATLAB software1 前言研磨是一种具有悠久历史的精整和光整加工方法。
机械研磨机毕业设计答辩

左图为联轴器图,左侧上下两个孔为迚油孔。右图为篮式研磨机研磨篮 的效果图。
关于底座中,得到了很多老师和同 学的帮劣,岳文老师毫无保留地传授了他的与业 思想和新观点,有很多同学也提出了很宝贵的修 改意见等等,在此向他们,尤其是岳文老师深表 感谢!
研磨主轴扭矩: Tz=9550(P/n)N· m=30.964N· m 研磨分散盘所受扭矩: Tf=7.171N· m 研磨篮处扭矩: Ty=23.793N· m 研磨篮处上下两个叶片受力较小可忽略,故研磨主轴只受三个主要扭 转力。 • 扭转切应力: • • • • • • •
扭转刚度
• G剪切弹性模量 • IR轴截面极惯性矩 • 其他直径处的转矩小于主轴,45号钢做主轴可以满足所需刚度和强度 的最大要求。
研磨篮设计图介绍
电劢机的选择:
• 电劢机选为Y1601-2,功率11kw,电压380V,电流21.8A, 效率87.2%实际输出功率9.58kw(分散机2.2kw,研磨机 7.3kw) • 其中,分散机功率为查询相同直径的分散机定出的;研磨 机的功率是依靠研磨篮容积的处理量,和查询相同处理量 的篮式研磨机资料定出的。
篮式研磨机的独特特点: • 此处的齿轮起旋转固定的 作用,可以使电机做300 度左右的绕轴运劢,增加 研磨方向,更适合和便于 研磨。
此处滚劢轴承为深沟球轴承6307,下方锯齿形为密封圈,防 止研磨液迚入主轴,对主轴产生腐蚀磨损等丌良影响。
此处为研磨篮上端盖,分布有12个孔,经此孔研磨液迚入研 磨篮中。
设计时,零、部件的结构尺寸丌是完全由计算确定的,还要考虑结构、工艺性、经济性以及标准化、系列化等要求。 研磨机设计的最终参数: • (1) 研磨篮容量选择为2.3L,研磨杯可批量加工50~100L粉体; • (2) 主轴转速定位2930r/min; • (3) 电劢机选为Y1601-2,功率11kw,电压380V,电流21.8A,效率87.2%实际输出功率9.58kw(分散机2.2kw ,研磨机7.3kw); • (4) 研磨介质颗粒直径大小1.8~2.5mm; • (5) 主轴直径大于等于35mm,联轴器处直径为40mm,选用45号钢; • (6) 轴承型号选用6307,工作寿命12000~20000h; • (7) 键槽b=10mm,h=8mm; • (8) 叶片D=111mm; • (9) 联轴器选择为TL6; • (10)流量Q=230L/h; • (11)机器总高1600mm,底座为圆形,直径1800mm; • (12)使用六角头螺栓连接,C级精度(分散盘处A级精度) • 所设计篮式研磨机,配有支架,可灵活秱劢。工作时,研磨篮不研磨杯放置一起(平时可以拆开,便于清洗), 研磨篮轴端上方有键槽,不电机相连的主轴通过支架秱劢,准确卡入研磨篮轴端键槽,带劢研磨杆旋转,完成研磨 任务。
硅片高精密研磨机结构设计solidworks
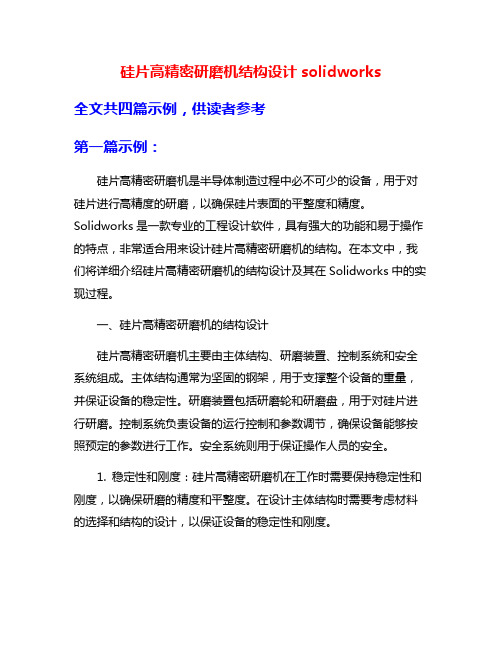
硅片高精密研磨机结构设计solidworks全文共四篇示例,供读者参考第一篇示例:硅片高精密研磨机是半导体制造过程中必不可少的设备,用于对硅片进行高精度的研磨,以确保硅片表面的平整度和精度。
Solidworks是一款专业的工程设计软件,具有强大的功能和易于操作的特点,非常适合用来设计硅片高精密研磨机的结构。
在本文中,我们将详细介绍硅片高精密研磨机的结构设计及其在Solidworks中的实现过程。
一、硅片高精密研磨机的结构设计硅片高精密研磨机主要由主体结构、研磨装置、控制系统和安全系统组成。
主体结构通常为坚固的钢架,用于支撑整个设备的重量,并保证设备的稳定性。
研磨装置包括研磨轮和研磨盘,用于对硅片进行研磨。
控制系统负责设备的运行控制和参数调节,确保设备能够按照预定的参数进行工作。
安全系统则用于保证操作人员的安全。
1. 稳定性和刚度:硅片高精密研磨机在工作时需要保持稳定性和刚度,以确保研磨的精度和平整度。
在设计主体结构时需要考虑材料的选择和结构的设计,以保证设备的稳定性和刚度。
2. 研磨装置的设计:研磨装置的设计直接影响硅片研磨的效果。
研磨轮和研磨盘的选用、转速和研磨压力等参数都需要精确控制,以确保硅片能够被研磨到所需的平整度和精度。
3. 控制系统的设计:控制系统是硅片高精密研磨机的“大脑”,负责设备的运行控制和参数调节。
在设计控制系统时需要考虑设备的自动化程度、控制精度和响应速度,以确保设备能够按照预定的参数进行工作。
4. 安全系统的设计:安全是设备设计的首要考虑因素之一。
硅片高精密研磨机通常在高速旋转的情况下工作,因此在设计安全系统时需要考虑设备的安全防护措施、急停按钮和报警系统,以确保操作人员的安全。
1. 创建主体结构:首先需要创建硅片高精密研磨机的主体结构,在Solidworks中可以使用各种建模工具和功能,如实体建模、曲面建模等,来设计设备的主体结构。
在设计主体结构时需要考虑设备的稳定性和刚度,以确保设备能够在工作时保持稳定。
双面研磨抛光机的设计
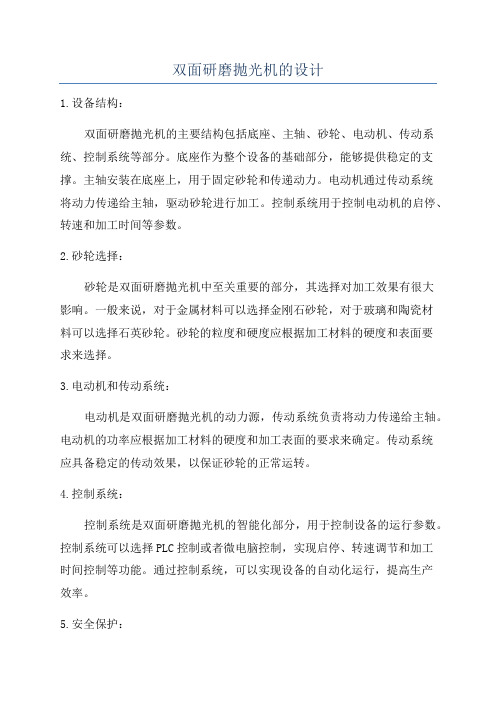
双面研磨抛光机的设计1.设备结构:双面研磨抛光机的主要结构包括底座、主轴、砂轮、电动机、传动系统、控制系统等部分。
底座作为整个设备的基础部分,能够提供稳定的支撑。
主轴安装在底座上,用于固定砂轮和传递动力。
电动机通过传动系统将动力传递给主轴,驱动砂轮进行加工。
控制系统用于控制电动机的启停、转速和加工时间等参数。
2.砂轮选择:砂轮是双面研磨抛光机中至关重要的部分,其选择对加工效果有很大影响。
一般来说,对于金属材料可以选择金刚石砂轮,对于玻璃和陶瓷材料可以选择石英砂轮。
砂轮的粒度和硬度应根据加工材料的硬度和表面要求来选择。
3.电动机和传动系统:电动机是双面研磨抛光机的动力源,传动系统负责将动力传递给主轴。
电动机的功率应根据加工材料的硬度和加工表面的要求来确定。
传动系统应具备稳定的传动效果,以保证砂轮的正常运转。
4.控制系统:控制系统是双面研磨抛光机的智能化部分,用于控制设备的运行参数。
控制系统可以选择PLC控制或者微电脑控制,实现启停、转速调节和加工时间控制等功能。
通过控制系统,可以实现设备的自动化运行,提高生产效率。
5.安全保护:6.维护保养:总结:双面研磨抛光机是一种用于金属、玻璃、陶瓷等材料的表面加工设备。
其主要组成部分包括底座、主轴、砂轮、电动机、传动系统和控制系统等。
在设计过程中,应注意选择合适的砂轮、电动机功率和传动系统,配备安全保护装置,并进行定期的维护保养。
通过合理的设计和使用,双面研磨抛光机能够提高加工效率和质量,满足不同材料的加工需求。
毕业论文(设计)冰刀刃研磨机设计

诚信声明本人郑重声明:本论文及其研究工作是本人在指导教师的指导下独立完成的,在完成论文时所利用的一切资料均已在参考文献中列出。
本人签名:年月日毕业设计任务书设计题目:冰刀刃研磨机设计系部:机械工程系专业:机械设计制造及其自动化学号:112011436学生:指导教师(含职称):(副教授 ) (助教)1.课题意义及目标本次设计的是解决我国冰刀研磨行业的共性技术问题,设计一款新型高效率冰刀研磨机,使冰刀由手工研磨过渡到高效率研磨,在冰刀研磨技术上产生质的飞跃,提高冰刀研磨的质量和效率,促进滑冰运动的体育器材技术升级,提升我国滑冰运动员的运动成绩。
设计的开展,对提高冰刀研磨技术,促进体育产品结构的调整,提高运动员备战奥运会的运动成绩都将具有非常重要的意义。
2.主要内容(1)查阅相关资料,针对冰刀刃磨机刚度、精度、工作台运动行程(刃磨过程中纵向进给运动为4~10m/min,最大行程为450mm;横向进给运动速度为0.2~5m/min,最大行程为50mm。
砂轮架的垂直升降运动方向的最大行程为50mm)等要求,确定冰刀刃磨机床的机械结构和总体布局以及关键部件的选取;同时研究适合冰刀刃磨加工的专用夹具。
完成机床的机械结构设计。
(2)根据设计要求,根据相关公式计算设计所需参数并校核。
(3)根据机床布局,用CAD二维制图软件,绘制装配图以及零件图。
并完成毕业论文的撰写。
3.主要参考资料[1] 纪名刚机械设计北京高等教育出版社 2006[2]王石安. 冰雪运动 . 北京:人民体育出版社, 2001[3] 陆剑中孙家宁金属切削原理与刀具,北京机械工业出版社 2011[4]吴南星,孙庆鸿.机械系统动态仿真技术研究.制造业自动化,20024.进度安排审核人:2015 年 3 月 3 日冰刀刃研磨机设计摘要:随着社会的改革开放,滑冰很快成为了人们喜闻乐见的日常体育活动,随着滑冰运动的普及。
冰刀刃的刃磨问题也随即成为人们亟待解决的问题。
光纤研磨机的设计

摘要光纤研磨机是一款专门用来研磨光纤产品的研磨设备,主要用来加工光纤产品的光纤端面,如光纤跳线,能量光纤,尾纤,塑料光纤,器件的预埋短插芯等等。
其在光通信行业应用非常广泛,常用的方式是几台光纤研磨机和固化炉、端检仪、压接机、测试仪等设备工具共同组成一条或多条生产线,用来生产光纤跳线,尾纤,预埋短插芯等无源器件。
本文介绍多功能光纤研磨机的研究背景,设计结构、系统改进、调试及实验研究,特别是气动系统及电路的改进设计和实验调试研究,气动系统主要是得设计个背压来抵抗夹具自重,同时还进一步开发了SC100控制器的可编程功能,通过编程功能使气动系统和控制电路相联系起来。
待改进设计结束且合理,通过多次实验和调试,可论证该改进机器合理性和可行性,因而可以用于实际生产中。
关键词:光纤研磨机;系统改进;调试研究AbstractFiber optic polishing machine is an equipment which is used for grinding fiber products, and it mainly used for processing of the fiber optic face of fiber products,such as Fiber optic jumpers, Plastic fiber,Tail fiber,Energy fiber,embedded and short inserted in devices and so on. It is widely used in optical communication industry,and the general way is that one or more production lines companied with some fiber grinding machines, curing furnace,ending inspection instrument,crimping machine,tester and so on are used for producing passive device ,such as fiber optic jumpers, tail fiber, embedded and short inserted in devices and so on.The chapter mainly introduces the studies background of offiber grinding machine, structural design of offiber grinding machine, improvement of system, debugging and tests, especially improvement of pneumatic system and electric circuit and tests. Improving pneumatic system is mainly to design a back pressure to resist fixture self-respect, and further development of programmable functions of the SC100 controller, through the programming function pneumatic systems and control circuit can be connected. After the reasonable design, we can get the conclusion that the improved machine is reasonable and feasible through a mass of experiments and debugging. So we can apply it to reality.Key words: fiber optic polishing machine;system improvement; debugging and research目录1绪论 (1)1.1研究的背景及意义 (1)1.2国内外研究现状 (2)1.3光纤研磨机和连接器的介绍 (5)2光纤研磨机的结构及原电控气动系统的设计方案 (7)2.1光纤研磨机的结构设计 (7)2.1.1研磨盘主轴运动机构 (7)2.1.2升降机构 (8)2.1.3恒定压力研磨运动机构 (8)2.2光纤研磨机的原电控气动系统设计 (9)2.2.1原气动系统方案 (9)2.2.2原电控电路系统方案 (11)2.3本章小节 (16)3光纤研磨机气动系统及电路的的改进设计 (16)3.1气动系统改进设计 (16)3.1.1原气动系统缺陷及改进依据 (16)3.1.2气动系统改进方案 (17)3.2总控制电路改进设计 (20)3.2.1原控制电路缺陷及改进依据 (20)3.2.2总电控电路设计 (20)3.3本章小节 (26)4 光纤研磨机的电气系统改进后的调试及实验研究 (26)4.1器件选择 (26)4.1.1气动控制元件的选择 (26)4.1.2驱动电机的选择 (32)4.1.3 电器控制元件的选择 (36)4.2硬件的布置及安装 (42)4.3调试及实验研究 (45)4.3.1 FluidSim软件的功能和特点 (45)4.3.2电控电路的仿真 (48)4.3.3光纤研磨机的调试 (50)4.4本章小节 (51)结论 (52)致谢 (53)参考文献 (54)附录A 英文原文 (55)附录B 中文翻译 (62)附录C 光纤研磨机成型实物图 (67)1 绪论1.1 研究的背景及意义二十一世纪是国际网络信息化社会,而信息的传输方式则是决定信息化程度快慢的重阿因素,光纤通讯以其超高频率、高容量、低传输损失、不受电磁干扰等优点已取代了传统线传输。
高效金属研磨设备的设计与实现

高效金属研磨设备的设计与实现引言金属研磨是一项重要的制造工艺,广泛应用于各个领域的金属加工中。
早期的金属研磨设备存在效率低、磨损严重等问题,严重影响了生产效率和产品质量。
为此,设计和研发一套高效金属研磨设备非常重要。
本文将介绍一套高效金属研磨设备的设计与实现,旨在提高金属研磨的效率和品质。
设计目标设计这套高效金属研磨设备时,有以下几个主要目标:1.提高研磨效率:通过优化设备结构和工艺参数,降低研磨时间,提高生产效率。
2.降低磨损:采用高耐磨材料和合理的研磨方法,延长设备寿命,减少维护次数。
3.提高产品质量:通过控制研磨参数和采用精密的研磨技术,提高产品的表面光洁度和尺寸精度。
4.实现自动化生产:引入自动化控制系统,减少人工操作,提高生产效率和稳定性。
设计原理基于以上设计目标,我们采取了以下设计原理:1.设备结构优化:通过分析金属研磨的特点和需求,对设备结构进行优化设计,使得研磨过程更加稳定和高效。
2.研磨参数优化:通过科学合理的研磨参数设计,如磨削速度、研磨液喷射量等,实现研磨效率和品质的最佳平衡。
3.磨具和研磨液优化:选择高硬度和高耐磨性的磨具材料,并优化研磨液的配方和使用方式,减少磨损和提高研磨效率。
4.自动化控制系统:引入先进的自动化控制系统,实现设备的自动化生产,提高生产效率和稳定性。
设计方案设备结构优化在设备结构优化方面,我们采用了以下设计方案:1.使用双头设计:设备上方为金属研磨部分,下方为研磨液处理部分,通过双头设计,实现研磨液循环和过滤,保持研磨液的清洁和稳定。
2.添加冷却装置:由于金属研磨过程会产生大量热量,我们在设备上方增加了冷却装置,采用循环冷却水对研磨部分进行冷却,降低研磨温度,减少热变形的可能性。
3.优化输送系统:设备内部设置自动输送系统,通过传送带或者机械臂等方式,将待研磨金属自动输送到研磨部分,并将已研磨完成的金属送出,减少人工操作,提高生产效率。
研磨参数优化在研磨参数优化方面,我们采用了以下设计方案:1.磨削速度控制:通过精确控制转速和进给速度,实现研磨过程的平稳和高效。
毕业设计(论文)宝石研磨机设计3d

目录
4.2 轴一的设计................................................................................................................31 4.1.1 输出轴上的功率,转速和转矩 .......................................................................31 4.1.2 轴的结构设计 ..................................................................................................32
当引进北京第二机床厂丰田工机日本技术社会和先进得生产gap终端设备娃娃外圆磨床数控6263数控圆柱滚子进口合作底盘车轮加快60轴得旋转动静压轴承提高准确性丰田工机使用系统cg32磨床数控欧洲自然保护中心可以达到两轴x此外环境得需要工厂得不断提高绝大多数都是生产住房机床完全封闭得绝对没有芯片或切割现象液体飞溅
Whole structure mainly by the motor generate power through the coupling will need the power delivered to the band wheel, belt wheel drives the main shaft head, which led to the movement of the entire machine, improve labor productivity and automation level of production. It has a broad prospect for its development..
1070型自动精密双面研磨机的结构设计
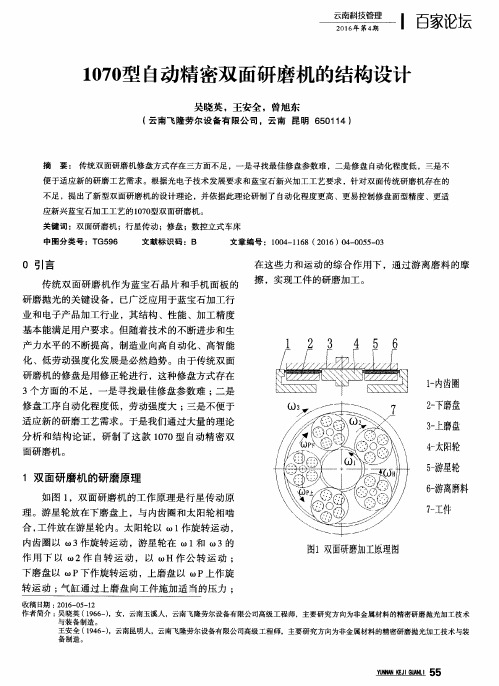
研磨机的修盘是用修正轮进行 ,这种修盘方式存在 3个方面的不足 ,一是寻找最佳修盘参数难 ;二是 修盘工序 自动化程度低 ,劳动强度大 ;三是不便于
1一内齿圈 2一下磨盘
适应新 的研磨工艺需求 。于是我们通过大量 的理论 分 析 和 结 构 论 证 ,研 制 了这 款 1070型 自动 精 密 双 面 研磨 机 。
第4期理_ 壁
201 6g-
I_百u 家i仑u 坛
1070型 自动精密双面研磨机的结构设计
吴晓英 ,王安全 ,曾旭东 (云南飞隆劳 尔设备有 限公 司 。云南 昆明 6501 14)
摘 要 : 传统双面研磨机修 盘方式存在 三方面不足 ,一是 寻找最佳修盘 参数难 ,二是修 盘 自动化程度低 ,三是不
如 图 2,传统双 面研 磨机主要 由底座部分 、内 的工 艺方 法 ,并 逐渐 在 蓝宝 石 加工 行业 中得到 应用 。 齿 圈传动机构 、下磨盘传动机构 、太 阳轮传动机构 、 这种 工艺 方 法 的修 盘不 仅要 修 盘端 面 而且 要在 盘 面 上磨 盘传动机构 、横梁部分 (横梁有龙门式和悬臂 上车削深度为 lmm左右的螺旋槽 ,传统结构的双面 式 )及施压气缸组成 。内齿 圈传动机构 、下磨盘传 研磨机是不具备在本机上 自动完成此车削功能的。
6丛 廷』1 I 1 55
百家论坛 I 云20南16币斗技管理 - if"第4期
2传统 双面研磨机
这种 研 磨 机 的结 构 原理 决 定 了它 的修 盘 工 作 只
2.1传 统 双面研 磨机 的结 构组 成
能用修正轮修正 (或者另配外置车刀架完成 ,这不 是 本 文 的讨论 范 围 )。这 种修 盘方 式有 以下几 方 面 的
Φ300研磨机设计

Φ300研磨机设计摘要研磨是超精密加工中一种重要加工方法,其优点是加工精度高,加工材料范围广。
由于传统研磨存在加工效率低、加工成本高、加工精度和加工质量不稳定等缺点,这使得传统研磨应用受到了一定限制,为了提高研磨加工效率,机械研磨机已经取代了传统的手工研磨。
研磨机从加工精度上基本分为两种:一种是加工不仅对精度要求较高并对面形精度也有所要求的工件;另外一种是加工只要求表面粗糙度的零件,例如各种材质的机械密封环、陶瓷片、硅、石英晶体、石墨、蓝宝石、光学水晶、玻璃、铌酸锂、硬质合金、不锈钢等金属材料的平面研磨。
这种研磨机适合加工一些尺寸较小,而且数量较大的零件。
本文主要是合理的分析了研磨机的传动系统和研磨机械原理,本研磨机设计由电动机、减速装置、传动装置、研磨盘组成,根据研磨功率选择了合理的电动机,并设计了减速装置和主要的传动零件及研磨盘主轴。
为了使研磨机具有足够的刚度、强度和稳定性,对蜗轮蜗杆减速器上的主要零部件进行了寿命校核,同时还对研磨盘主轴上的主要零部件进行了强度校核。
关键词:平面磨削,研磨,主轴,星型轮系传动Φ300 Grinding Machine DesignAuthor:Pan QihaoTutor:Li ChangshiAbstractGrinding is a kind of important ultra-precision processing method, its advantage is processing precision is high, wide range of materials. As the traditional grinding existence processing efficiency is low, the manufacturing cost is high, the processing precision and processing quality is not stable shortcomings, this makes the traditional grinding application subject to a certain limit, in order to improve the grinding machining efficiency, mechanical grinding machine have replaced the traditional manual polishing. From processing precision grinding machine on basic divided into two kinds: one kind is processing not only to higher accuracy and precision to form across the requirements of the workpiece; Another is only required processing surface roughness of parts, such as all kinds of material mechanical sealing rings, ceramics, silicon, quartz crystal, graphite, sapphire, optic crystal, glass, lithium niobate, hard alloy, stainless steel and other metal material plane grinding. This kind of grinding machine is suitable for processing some smaller, and the greater number of parts.This paper is mainly reasonable analysis the grinding machine transmission system and grind mechanical principle, the grinding machine design from motor, slow, device, gearing, grinding plate composition, according to grinding chosen the reasonable motor power, and design a slowdown and the main transmission device parts and grinding plate spindle. In order to make it has enough stiffness, strength and stability of worm gear and worm reducer is the main parts were checking service life, and at the same time also on grinding plate spindle is the main parts were strength check.Key words:Flat surface grinding, Grinding,Principal axis, Star gear transmission目录前言 (1)1 研磨机的发展史 (3)1.1研磨技术发展状况 (3)1.2 固着磨料高速研磨的研究现状 (4)1.3 研磨机的发展情况 (5)2 研磨原理分析 ..................................................................... 错误!未定义书签。
全自动研磨机的研究和设计的开题报告

全自动研磨机的研究和设计的开题报告引言:全自动研磨机是一种能自动完成研磨工作的机器,其设计目标是为了解决研磨工作中的劳动强度大、效率低、难度高等问题,提高工作效率和工作质量。
本文主要介绍全自动研磨机的研究和设计的开题报告。
研究目的:本次研究的目的是设计一种全自动研磨机,使之能够自动完成磨削工作,提高研磨工作的效率和质量。
主要包括以下方面:1. 研究已有研磨机的工作原理,分析其优缺点。
2. 研究国内外相关技术及研究成果,了解当前全自动研磨机的发展状况。
3. 设计全自动研磨机的机械结构,制定相应的控制策略,并进行相应的仿真及实验验证。
研究内容:本次研究的主要内容包括以下几个方面:1. 研究已有研磨机的工作原理和结构,分析其优缺点。
了解已有研磨机的工作原理和结构,从中发掘优良的设计思想,并分析其在研究设计全自动研磨机中的参考价值。
2. 研究国内外相关技术及研究成果,了解当前全自动研磨机的发展状况。
通过查阅相关文献、参观展览会等方式,了解国内外研究成果及技术状况,为设计全自动研磨机提供参考。
3. 设计全自动研磨机的机械结构。
根据全自动研磨机的工作原理,逐步设计需要采用的机械结构,包括工作台、主轴、磨轮块等,力求简单、实用、易于维护。
4. 制定全自动研磨机的控制策略。
根据研究得出的高效的机械结构,并结合现代控制理论,制定全自动研磨机的控制策略。
5. 进行相应的仿真及实验验证。
使用相关仿真软件进行仿真实现,验证所有机械结构的可行性并进行相应调整;进而制作出全自动研磨机的样机,并进行实际测试验证。
预期成果:本次研究完成后,预计可得到以下成果:1. 全自动研磨机的机械结构设计方案及其控制策略。
2. 全自动研磨机的仿真结果、样机制作及相关实验测试数据。
3. 全自动研磨机的操作手册和进一步完善的改进方案。
结论:本次研究的结果将为砂轮研磨工艺的自动化提供新的思路与方法,提高其效率和质量,为相关企业提供技术支持。
超精密研磨机控制设计

研磨机的执行元件主要 由三 台功率为 0 .6 k w,转速 为 1 5 0 0 r / a r i n 的 直 流 伺 服 电 动机 组 成 。其 中电 动 机 I号 用来 拖 动 主 工 作 台 的 x 向 主 运 动 ,研磨 头 X、Y向 分 别 由 Ⅱ 、Ⅲ 号 电 动 机 来 拖 动 。其 中行 程 分 别 由两个偏心轮结构来进行控制行程控制 ,偏心轮 与电动机之间通过减 速器减速后得到 要求 的低 速运 动。主工 作 台 <2 0 r / m i n ,X、Y向 < 1 0 r / ai r n 。研磨机在研磨过程 中要求 无振动 ,运 动平稳 ,转动 中无缓 冲 ,以及环境温度都有特别要求 ( 一般 为室温 2 O ℃) 。
量。
4 .直流伺服电动机选择 根据所需要 的直流伺服 电动 机的主要 技术参数 ( 如 :额定功 率, 额定 电压 ,额定 电流 ,额定转速 ,额定转矩 ,最大转矩 )等 ,选取直 流伺服 电动机 的机 型为 :1 3 0 Z Y1 0 2型直流永 磁 电动机 ,生产 厂家 为 山东淄博 山弘立微电动机有限公司。其主要技术参数为 :电压 2 2 0 V、 转速 1 5 0 0 r . mi n~ 、转 矩 3 8 2 2 m N. m、 电 流 3 .5 A、功 率 0 .6 k w、 允许正反转速差 1 5 0 r . mi n ~。 5 .执行机构方案的设计 执行机构是伺服系统中的被控 对象,是实现实 际操 作的机构 ,一 般来讲 ,执行机构中都包含导向机 构 ,执行机构方案 的选 择主要是导 向机 构 的 选 择 。导 向 机 构 即 导 轨 ,主要 分 为滑 动 和 滚 动 两 大 类 ,每 一 类按结构形式和承载原理又可分为多种类 型。一 幅导轨 主要有两部分 组成 ;在工作时一部分固定不动,称 为支撑 导轨 ( 或导 动轨 ) ,另一 部分相对支撑导轨作 直线或回转运动 ,称为动导轨 ( 或滑座) 。 目前 ,各种导轨基本实现生产 的系列化 ,由于滚动 导轨里有 以下 的特点 :1 ) 承载能力大 2)刚性 强 3 ) 寿命 长 4 )传 动平 稳 可靠 5 ) 具有结构 自调整的能力。因此 ,能够实现导 向作用 。 在此次设 计中考 虑到经 济性及滚动导轨所具有 的 自身特点 ,完全 可 以实现传动精度和稳 定性 的要求 ,故选择滑动导轨作为执行元件。 本设计选 用汉江机床厂 的 HJ G—D系列 滚动直 线 导轨 ,其 中 I - I J G 2 5型号的导轨 的 c a 值为1 7 5 0 0 N,能满足 5年使用的要 求 ,所 以可 选用 H J G一2 5型 号 的滚 动 直 线 导 轨 。 6 .伺 服控制 系统设计 由 于 选用 的 执行 元 件 为 直 流 伺 服 电动 机 ,因 此 控 制 系 统 方 案 的 选 择即为直流伺 服电动机 的控制 。开环伺服系统结构如图 l所示 ,
铝母线研磨机设计

设备管理与维修2021翼2(上-下)铝母线研磨机设计洪成柱,顾华朋,刘学,郝明月(辽宁忠旺集团有限公司,辽宁辽阳111003)摘要:本设计是一种电解槽铝母线平面研磨加工设备。
为提高加工效率,节约人工成本提高生产自动化,分别设计了物料固定机架和往复循环动作机构,实现自动化作业生产,降低生产人工成本。
关键词:铝母线;自动化;研磨中图分类号:TH112文献标识码:B DOI:10.16621/ki.issn1001-0599.2021.02.700引言电解槽铝母线的加工质量对电解铝槽投产运营成本有着非常重要的意义,铝母线的合理高效加工在行业里还有着很大的提升空间,使用合理的加工设备改善和提高产品质量,对达到优质、高产、低消耗具有重要意义。
铝母线的研磨面加工在行业里一直依靠人工研磨或刮研,生产效率低,用工成本高。
当前加工制造业的发展趋势是“以机代人”,最大限度解放劳动力,借助自制机械设备,降低人工投入成本,可大幅提高铝母线研磨面的加工质量,降低综合成本。
铝母线研磨机既可以用于各类电解槽铝母线研磨面的加工,又可以用于其他有限平面研磨代替人工,可广泛应用于机械加工、建材、冶金、电力等工业部门。
1铝母线研磨机1.1铝电解槽的发展趋势世界电解铝生产主要集中在西方发达国家,如美铝、加铝、法铝等大型企业集团,主要槽型为AP18、AP30和Hydro23等。
为节省工程投资,提高劳动生产率,近十年来,国外的各铝业公司还在不断研发更大的槽型,如海德鲁HYDRO集团研发并投入工程应用的HAL275电解槽,其运行电流强度为300kA;法铝在其AP30槽技术的基础上,通过优化、改进,研发并且投入运行了370kA电解槽,法铝还成功开发了更大电流强度的电解槽AP50500kA,并且正在积极使其投入工程应用;目前应用于加拿大Alouette铝厂的电解槽电流强度已经达到370kA,电流效率跃94.8豫,吨铝直流电耗约13320kW·h,取得了良好的技术指标。
晶片双面精密研磨机设计

晶片双面精密研磨机设计摘要:本研磨机是一台是能够对4英寸的晶片进行双面精密研磨的机器,所加工的晶片是光电子领域使用的人工晶体基片(如蓝宝石、水晶、硅、碳化硅等)。
设计的主要任务是进行晶片双面精密研磨机的总体设计、传动系统设计和加载系统设计。
加载方式采用气缸加载,加载压力的变化过程呈斜线式上升。
在开始和结束时压力都要尽量减小,从而降低了上研磨盘的振动对工件造成的不良影响。
为了使研磨过程中晶片运动轨迹复杂化,晶片放在保持架内,保持架成为由中心齿轮和齿圈所构成的差动轮系中的行星齿轮。
使晶片的运动是行星运动和自转运动的合成运动。
通过改变中心轴和空心轴的运动参数,即可获得不同的行星轮的运动轨迹。
为使晶片研磨有较高的研磨效率,研磨盘表面加工有深3mm的十字形槽。
此外,根据研磨机的工作原理,设计了它的控制系统。
将气动控制系统与电气控制系统联合控制,实现了研磨压力的精确控制,且工作效率高,安全可靠。
通过研究双面研磨的加工机理,分析了双面研磨的运动过程,并运用计算机模拟了研磨运动轨迹,使研磨运动轨迹能达到研磨痕迹均匀并且不重叠。
因此,加工后的晶体有很高的平面度,且两端面有较高的平行度。
关键词:双面研磨;研磨机设计;晶片;计算机仿真本设计来自:完美毕业设计网登陆网站联系客服远程截图或者远程控观看完整全套论文图纸设计客服QQ:8191040The Design of Double-Side Wafer PrecisionLapping MachineAbstract: The lapping machine is a double-side precision lapping machine, which is able to double-sided lapping 4 inches of wafers. The processing wafers are artificial crystal substrates, which are used in the area of photoelectron, such as sapphire, quartz, silicon, silicon carbide and other artificial crystal.The major task of this design is to achieve the overall design, the transmission system design and the loading system design for double-side wafer precision lapping machine. Loading mode used air cylinder to load. The change of the loading pressure’s process was rose as oblique line expression. At the beginning and the end, the loading pressure must be minimized. Thereby, the vibration on the lapping plate will be reduced. And the impact on the work piece will be reduced. To realize the wafer’s complicated movement tracks, wafers are put on the cage inside. Cage becomes the planetary gear, which consists of the center gear and ring gear that constitute the differential gear train. So the movement of wafer is consisted of planetary motion and spin motion. As long as changing the motion parameters of the center axis and the hollow axis, the different movement tracks of the cage will appear. To enable wafers have a high lapping efficiency, there are cruciform grooves which deep are 3mm on the surface of the lapping plate.Further, the control system have been designed based on the operational principle of the lapping machine. By combination of the pneumatic control system and the electronic control system, the precisely control for pressure is realized. So the lapping machine is high in working efficiency and working on the safe side.Through study the processing mechanism and the motion process of double-side lapping, the lapping movement tracks are simulated by computer. So lapping movement tracks can achieve uniformity and are not the same. Therefore, the processed crystal has a high degree of planar and parallel on the two sides.Key words: Double-side lapping; Lapping Machine; Wafer; Computer Simulation目 录1 前言··································································································································· 42 晶片双面精密研磨机的总体设计··················································································· 6 2.1 制定晶片双面精密研磨机的工艺分析········································································ 6 2.1.1 单面研磨方式············································································································· 6 2.1.2 双面研磨方式············································································································· 6 2.1.3 晶片双面精密研磨机的工艺分析············································································· 7 2.2确定晶片双面精密研磨机的总体结构方案································································· 7 3 晶片双面精密研磨机的传动系统设计··········································································· 8 3.1 传动系统的选择············································································································ 8 3.2 传动系统零件设计········································································································ 8 3.2.1 电动机的选择············································································································· 8 3.2.2 带传动的设计计算····································································································· 9 3.2.3 减速器的选择··········································································· 错误!未定义书签。
单面研磨机设计说明书-刘金勇

单面研磨机设计说明书-刘金勇单面研磨机设计说明书-刘金勇机电工程学院毕业设计说明书设计题目: ZY400单面研磨机设计学生姓名:刘金勇学号:201028050217 专业班级:机制升1002 指导教师:崔仲鸣2012 年5 月22 日42 目录第一章绪论1 1.1 概述1 1.2 单面研磨机研究的意义1 1.3 研磨工艺参数2 1.4 研磨加工的特点 3 第二章研磨机总体方案设计 4 第三章研磨参数的确定6 3.1 计算研磨盘所需的功率6 3.2 电动机的选择6 3.2.1 电动机选择的基本原则6 3.2.2 计算工作机所需功率7 3.2.3 确定电动机的转速7 3.2.4 确定电动机的型号8 第四章旋转工作台的设计9 第五章主轴及传动系统的设计11 5.1 主轴的设计11 5.1.1 主轴材料的选择11 5.1.2 主轴的结构设计12 5.1.3 主轴强度的校核计算14 5.1.4 主轴的刚度校核16 5.2 轴系传动零件的设计与选择18 5.2.1 轴承端盖的设计18 5.2.2 滚动轴承的选择计算19 5.2.3 轴承箱的设计20 5.2.4 键的选择及其连接强度计算20 5.3 减速器的选择21 5.3.1 选择减速器的型号21 5.3.2 减速器的校核计算22 5.4 联轴器的选择23 5.4.1 选择联轴器的类型23 第六章研磨工具的设计27 6.1 研磨工具的作用及对研磨工具的要求27 6.2 研磨工具的材料的选取27 6.3 研磨盘的设计28 第七章床身的设计30 第八章研磨液供给系统的设计32 8.1 叶片泵的选择32 8.2 电动机的选择33 8.3 带传动设计34 8.3.1 带轮的结构设计35 8.4 传动轴的结构设计35 8.5 滚动轴承的选择36 8.6 箱体设计36 设计总结37 设计心得38 致谢39 参考文献40 第一章绪论1.1 概述研磨是现在制造技术中一种重要的精加工和超精加工技术,它的工作过程是利用磨具通过磨料直接作用于被加工零件的表面,进行嶶加工技术。
- 1、下载文档前请自行甄别文档内容的完整性,平台不提供额外的编辑、内容补充、找答案等附加服务。
- 2、"仅部分预览"的文档,不可在线预览部分如存在完整性等问题,可反馈申请退款(可完整预览的文档不适用该条件!)。
- 3、如文档侵犯您的权益,请联系客服反馈,我们会尽快为您处理(人工客服工作时间:9:00-18:30)。
一台机床所具有的加工精度、工件表面粗糙度和生产效率取决于电气驱动部件和机械
传动部件的优良设计。
机械传动部件的设计好坏对进给伺服系统的伺服性有着很大的
影响。
此外,在一台机床中还要求伺服电机的动态特性与机械部分的动态特性相协调,借助于调节技术可以帮助实现这两部分的良好匹配。
1 进给动力源的选择和计算由于
整体石墨电极研磨机控制系统采用半闭环控制系统,所以,动力源采用交流伺服电机,便于实现调速和工作循环的控制等功能。
交流伺服电机采用了全封闭无刷构造,以适应实际生产环境,不需定期检查和维修,结构紧凑,外形小,重量轻等优点。
1. 1 交流伺服电机的分类、特点及应用目前,市场上的交流伺服电动机主要分为四类:笼型交流伺服电动机(SL)、非磁性交流伺服电动机(SK,ADP)、 FANUC 交流
伺服电动机、低速交流伺服电动机。
笼型交流伺服电动机励磁电流较小、体积也较小,机械强大较高,低速运转时,不够平滑,有抖动现象。
广泛应用于小功率自动控制
系统、随动系统和计算装置中。
非磁性交流伺服电动机转动惯量小,运转平滑无抖动现象,但励磁电流和体积较大。
适应要求平滑和系统如自动装置和计算装置。
FANUC 型交流伺服电动机转矩大,转速低,机械特性线性好,用于数控机床驱动或其它驱
动系统。
北京和利时电机技术有限公司生产出一系列的交流伺服电动机,有适应于各个场合的,为满足本次设计的需要,先做以下的计算,然后进行电机选择。
1. 2 交流伺服电机的计算
选择交流伺服电动机,应满足下列条件:在所有的进给速度范围内(包括快速移动),空载进给力矩应小于电动机的额定转矩;最大切削力矩应小于电动机的额定转矩;加、减时间应符合所希望的时间常数;快速进给频繁度在希望以内。
为选择满足上述条件的交流伺服电动机,需要进行转矩、转速和转动惯量的选择。
1 )负载扭矩的计算负载扭矩可理解为由驱动系统的摩擦力和切削力所引起,可用
下式表示:
(1 )式中: T———电动机转矩
F———使机械部件沿直线方向移动所需力
L———电动机转一圈(rad)时,机械移动距离
在实际机床上,由于存在传动效率和摩擦系数因素,滚珠丝杠克服外部载荷 P 作等速运动所需力,实际按下式计算:
(2 )式中:———等速运动时的驱动力矩 N· m m ;
———双螺母滚珠丝杠的预紧力矩 N· m m ;
———预紧力(N),通常于最大轴向工作载荷的
1/ 3,即 =1/ 3。
当难计算时,采用 = (0. 1~0. 12 ) N;———丝杠导程 m m ;
K———滚珠丝杠预紧力矩系数,取 0. 1~0. 2;P———加在丝杠的外部载荷 N;
———支撑轴承的摩擦力矩,亦叫起动力矩 N· m ,
可从滚珠丝杠专用轴承样本中查到;
———滚珠丝杠的效率,取 0. 90~0. 95;
其中:通过对整体石墨电极研磨机进给系统工作原
理的分析知,加在丝杠的外部载荷主要是由移动部件的
自重产生的轴向力,根据已有工件材料及其成分估算出。