内层制程试车作业管理规范
试车管理制度

试车管理制度试车管理制度1为确保公司路试作业(包括转序)平安,预防道路交通事故的发生,保障职工生命平安和削减国家财产损失,规范路试工的平安作业行为,特制定本规定。
一、适用范围本规定适用于对公司范围内路试作业的平安管理。
本规定所称路试作业,包括进行30公里道路试验以及底盘和整车产品在新老厂区之间的转序,进行这类作业的车辆统称为路试车辆,进行这类作业的车辆驾驶人员统称为路试工。
二、部门职责1、各分厂负责对本单位路试作业进行日常平安管理,保证路试车辆驾驶文明、规范。
2、能源装备部负责配备可拆卸后视镜和专用的平头车身锁紧机构平安销。
由使用单位提出申请,由能源装备部组织自制或外购并进行登记建帐以及日常管理。
3、运输公司负责对各分厂路试作业的日常平安监督管理,并负责对路试工进行岗前、岗中实际操作培训、考试,为分厂办理路试作业临时牌照。
4、人力资源部负责公司内路试工岗前、岗中的`理论学问培训、考试,依据各分厂实际按需配备路试人员。
5、生产管理部负责对公司内路试作业平安的综合监督管理。
三、路试工上岗条件1、必需有两年以上厂外驾驶的工作阅历,并持有交管部门颁发的《机动车辆驾驶证》有效证件。
上岗前必需经过公司主管部门专业培训和考试,考试合格后由生产管理部签发十通公司机动车辆驾驶员《上岗证》方可上岗。
2、身体必需健康,精神良好,有病或处于疲惫状态时不允许上岗。
四、行车前平安检查及预备事项路试工在车辆行驶前必需进行以下检查和预备事项:1、待路试车辆驾驶室两侧必需安装可拆卸的后视镜。
2、对待路试车辆有关行驶平安的部件(位)进行初步检查,如制动、转向、灯光、倒车报警器、离合、喇叭、仪表功能等,发觉有明显故障时应转入调试,不得使有明显故障的车辆强行上路。
例如:转向垂臂、横直拉杆等转向运动零件不得有裂纹、变形,发动机运转及停车时有漏油、漏水、漏电、漏气现象。
3、变速换挡敏捷、轻巧,自锁、互锁牢靠,变速杆无变形。
4、对于平头车身底盘或整车,必需插好驾驶室锁紧机构的平安销。
制程检验作业管理办法模版

制程检验作业管理办法模版第一章总则第一条为规范制程检验作业行为,提高质量管理水平,特制定本制程检验作业管理办法。
第二条制程检验作业管理办法适用于本企业及其供应商所进行的制程检验作业。
第三条制程检验作业包括但不限于材料抽检、工序检验、产品抽检等。
第四条所有参与制程检验作业的人员必须遵守本规定。
第二章制程检验作业规范第五条制程检验操作人员必须熟悉本企业相关质量管理制度和产品标准规范。
第六条制程检验操作人员在进行检验作业前,必须根据作业内容和要求,熟悉相关产品标准规范,并核对检验设备和工具的合格证和校准合格期限。
第七条制程检验操作人员在进行检验作业时,必须按照相关工序指导书操作,确保作业过程规范、准确。
第八条制程检验操作人员必须严格执行检验方法和标准操作流程,确保结果的真实可靠。
第九条制程检验作业应进行记录,记录内容包括但不限于检验员、检验时间、检验结果等。
第十条对于不合格的制程检验项目,必须及时处理,并按照不合格处理流程处理。
第三章检验设备和工具管理第十一条检验设备和工具必须按照规定的校准周期进行校准,并有校准合格证明。
第十二条校准记录应该详细记录设备和工具的校准时间、校准结果、校准人员等信息,并保存备查。
第十三条检验设备和工具的使用人员必须具备相应的资质,且经过培训合格方能上岗。
第十四条检验设备和工具的运输、存放、使用过程中必须保证其完整性和正常状态,发现损坏应及时维修或更换。
第四章差异处理第十五条在制程检验过程中,如发现产品与要求不符或存在缺陷等问题,检验操作人员必须及时停工,并向上级主管报告。
第十六条上级主管收到报告后,应尽快组织相关人员进行分析和处理,并及时采取纠正措施。
第十七条差异处理结果必须记录并进行追踪,确保问题的完全解决。
第五章附则第十八条本办法未尽事宜,由质量管理部门进行解释。
第十九条本办法自颁布之日起生效。
制程检验作业管理办法
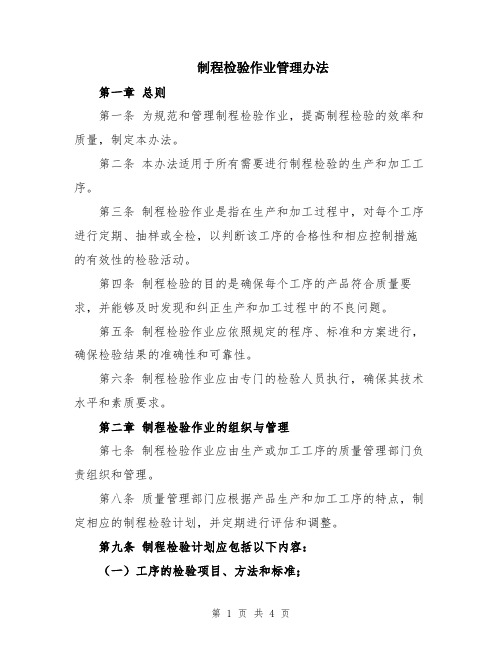
制程检验作业管理办法第一章总则第一条为规范和管理制程检验作业,提高制程检验的效率和质量,制定本办法。
第二条本办法适用于所有需要进行制程检验的生产和加工工序。
第三条制程检验作业是指在生产和加工过程中,对每个工序进行定期、抽样或全检,以判断该工序的合格性和相应控制措施的有效性的检验活动。
第四条制程检验的目的是确保每个工序的产品符合质量要求,并能够及时发现和纠正生产和加工过程中的不良问题。
第五条制程检验作业应依照规定的程序、标准和方案进行,确保检验结果的准确性和可靠性。
第六条制程检验作业应由专门的检验人员执行,确保其技术水平和素质要求。
第二章制程检验作业的组织与管理第七条制程检验作业应由生产或加工工序的质量管理部门负责组织和管理。
第八条质量管理部门应根据产品生产和加工工序的特点,制定相应的制程检验计划,并定期进行评估和调整。
第九条制程检验计划应包括以下内容:(一)工序的检验项目、方法和标准;(二)检验频次和抽样方案;(三)检验人员的培训和考核计划;(四)不合格品的处理程序和措施。
第十条质量管理部门应确保制程检验作业的实施符合质量管理体系的要求,并进行相应的记录和报告。
第十一条质量管理部门应与生产或加工工序的相关责任部门建立良好的沟通与协调机制,及时处理制程检验中的问题和反馈意见。
第十二条质量管理部门应定期进行制程检验的绩效评估,不断改进检验方法和流程,提高制程检验的效率和质量。
第三章制程检验作业的流程和方法第十三条制程检验应采用科学、合理的方法,确保检验结果的真实性和准确性。
第十四条制程检验的流程一般包括以下几个环节:(一)工序准备:对即将进行检验的工序进行准备工作,包括准备检验设备和工具,获取检验所需的样品和数据等。
(二)工序执行:按照检验计划和标准对工序进行检验,对样品进行抽样、检测、记录和分析。
(三)结果判定:根据检验结果和标准,判断工序的合格性,并进行相应的记录和处理。
(四)问题处理:对不合格的产品或工序,进行问题分析、控制和改进措施的制定,并记录和追踪其整改情况。
试车管理制度

试车管理制度第一章总则第一条为规范公司内部试车行为,维护车辆安全和保障试车人员的生命安全,特制定本制度。
第二条本制度适用于公司内部所有试车场地的试车活动。
第三条试车活动应当遵守相关法律法规,确保试车过程安全,保护车辆财产不受损害。
第四条试车人员应具备相应的驾驶技能和驾驶证件,严格遵守交通规则。
第五条试车活动应当在指定的试车场地进行,禁止在非指定场地进行试车。
第六条试车活动需提前申请,报备相关信息,并在指定时间内进行试车活动。
第七条试车活动结束后,应当及时整理车辆,清理场地,保持环境整洁。
第八条试车活动中如有意外事件发生,应及时报告上级主管部门,并做好相关记录工作。
第二章试车人员管理第九条公司应当对试车人员进行专业培训,确保其具备必要的试车技能和安全意识。
第十条试车人员在试车活动中应当佩戴安全帽、安全带等安全装备,并遵守交通规则。
第十一条试车人员应当自觉遵守公司规定的试车制度,不得擅自更改试车计划或试车路线。
第十二条试车人员在试车活动中发现车辆异常情况时,应当及时报告相关人员进行处理。
第十三条试车人员需定期接受公司的安全培训和考核,保持安全意识和技能水平。
第三章车辆管理第十四条公司应当定期对试车车辆进行检查和维护,确保车辆处于良好状态。
第十五条试车车辆需配备完善的安全装备,如灭火器、安全锤、车载医药箱等。
第十六条试车车辆需定期进行保险和年检等相关手续,确保车辆合法上路行驶。
第十七条试车车辆在试车活动中出现故障或事故时,应及时通知相关部门进行修理或处理。
第十八条试车车辆应当定期更换机油、轮胎等易损件,确保车辆正常运行。
第四章试车场地管理第十九条试车场地应当设置指示牌、警示标志等安全设施,确保试车活动安全进行。
第二十条试车场地应当定期进行清理和维护,确保场地整洁有序。
第二十一条试车场地应当配备必要的检测设备和工具,确保试车活动顺利进行。
第二十二条试车场地在试车活动结束后应当及时清理、整理,保持环境卫生。
制程检验作业管理办法

制程检验作业管理办法一、总则为规范制程检验作业、保证产品制程质量和提高生产效益,制定本管理办法。
二、适用范围本管理办法适用于进行制程检验的所有操作人员。
三、管理要求1. 确定制程检验标准:制定制程检验标准,包括检验项目、检验方法、接收标准等内容。
2. 制定制程检验计划:根据生产进度和重要性确定制程检验项目和时间节点,制定制程检验计划。
3. 设定制程检验指标:根据产品质量要求和实际生产情况,设定制程检验指标,包括尺寸、外观、性能等。
4. 选择检验方法和设备:根据不同的制程检验项目,选择适合的检验方法和设备,并确保其准确性和可靠性。
5. 建立制程检验记录:建立制程检验记录表,记录每次检验的结果,包括检验项目、设备和方法、检验结果等。
6. 培训操作人员:对参与制程检验操作的人员进行培训,确保其具备进行制程检验的基本知识和技能。
7. 制定纠正措施:对于发现的不合格制程,及时采取纠正措施,如调整工艺参数、更换设备等。
8. 定期评审和改进:定期评审制程检验的执行情况,并根据评审结果,及时改进管理办法。
四、操作流程1. 制程检验前准备(1) 制定制程检验计划,并通知相关人员;(2) 确定制程检验项目和要求,准备所需的检验方法和设备;(3) 对操作人员进行必要的培训,确保其了解检验项目和方法;(4) 准备制程检验记录表,方便记录检验结果。
2. 制程检验操作(1) 操作人员按照制定的检验计划进行检验,确保按照要求进行操作;(2) 使用合适的检验方法和设备进行检验,确保检验结果准确可靠;(3) 记录每次检验的结果,包括检验项目、设备和方法、检验结果等;(4) 如发现不合格制程,立即采取纠正措施,并进行记录。
3. 制程检验结果处理(1) 检验合格,根据标准接收制程,并记录检验结果;(2) 检验不合格,进行纠正措施,如调整工艺参数、更换设备等;(3) 对于重要制程的不合格情况,需进行追溯分析,并根据分析结果进行调整;(4) 对于严重不合格的制程,及时报告上级领导,并采取紧急措施。
制程检验作业管理办法
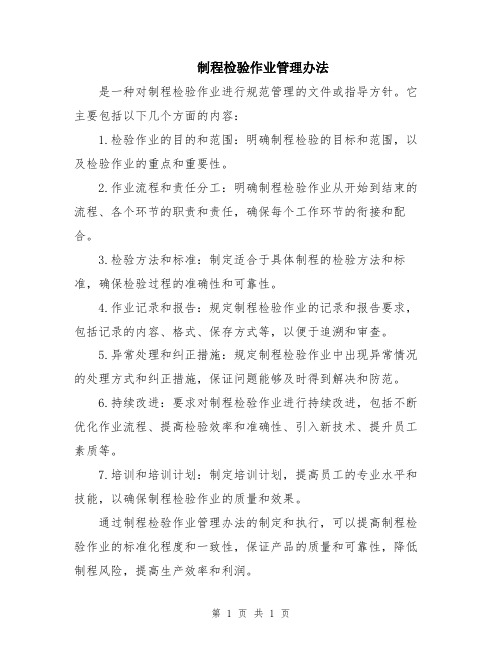
制程检验作业管理办法
是一种对制程检验作业进行规范管理的文件或指导方针。
它主要包括以下几个方面的内容:
1.检验作业的目的和范围:明确制程检验的目标和范围,以及检验作业的重点和重要性。
2.作业流程和责任分工:明确制程检验作业从开始到结束的流程、各个环节的职责和责任,确保每个工作环节的衔接和配合。
3.检验方法和标准:制定适合于具体制程的检验方法和标准,确保检验过程的准确性和可靠性。
4.作业记录和报告:规定制程检验作业的记录和报告要求,包括记录的内容、格式、保存方式等,以便于追溯和审查。
5.异常处理和纠正措施:规定制程检验作业中出现异常情况的处理方式和纠正措施,保证问题能够及时得到解决和防范。
6.持续改进:要求对制程检验作业进行持续改进,包括不断优化作业流程、提高检验效率和准确性、引入新技术、提升员工素质等。
7.培训和培训计划:制定培训计划,提高员工的专业水平和技能,以确保制程检验作业的质量和效果。
通过制程检验作业管理办法的制定和执行,可以提高制程检验作业的标准化程度和一致性,保证产品的质量和可靠性,降低制程风险,提高生产效率和利润。
第 1 页共 1 页。
试车管理制度模板

试车管理制度模板一、目的为确保试车工作的安全性、有效性和合规性,预防事故发生,提高试车效率,特制定本管理制度。
二、适用范围本制度适用于公司内所有新购或大修后的设备、车辆及其他需要进行试运行的机械设施。
三、试车前准备1. 检查设备是否具备试车条件,包括但不限于设备完整性、安全防护装置齐全有效等。
2. 确保所有技术文件、操作手册和试车程序已准备就绪。
3. 组织操作人员进行试车前的安全培训和技术培训。
4. 准备必要的安全防护用品和急救设施。
四、试车流程1. 试车申请:由使用部门提出试车申请,经管理部门审批。
2. 试车准备:按照试车前准备事项进行检查和确认。
3. 试车实施:由经过培训的操作人员按照试车程序进行操作。
4. 试车记录:详细记录试车过程中的各项参数和发现的问题。
5. 试车验收:试车结束后,由管理部门组织验收,并出具试车报告。
五、安全措施1. 设立试车区域,确保非相关人员不得进入。
2. 试车过程中,操作人员必须穿戴规定的劳动保护用品。
3. 试车现场应配备足够的消防器材和急救设备。
4. 试车前应进行安全教育,确保所有参与人员了解安全规程。
六、事故处理1. 试车过程中如发生异常情况,应立即停止试车,迅速撤离人员,并启动应急预案。
2. 对事故原因进行调查分析,并采取相应措施防止类似事件再次发生。
3. 所有事故无论大小,都应记录在案,并及时上报管理部门。
七、试车后处理1. 试车成功后,设备应进行必要的清洁和保养,确保其处于最佳状态。
2. 试车报告应详细记录试车结果,并由相关负责人签字确认。
3. 试车不合格的设备,应按照相关规定进行返修或报废处理。
八、附则1. 本制度自发布之日起生效,由管理部门负责解释。
2. 对本制度的修改和补充,应经过管理部门审议通过。
3. 本制度应定期进行评审和更新,以适应生产和管理的需要。
九、记录与存档1. 所有试车相关的记录应按照公司档案管理规定进行存档。
2. 试车记录应至少保存至设备报废或转让。
试车过程 工艺管理制度

试车过程工艺管理制度一、试车准备工作1. 安排好试车人员:试车人员需要具备相关的技术知识和丰富的试车经验,能够熟练操作试车设备和仪器以及正确判断产品的测试结果。
2. 准备好试车设备和工具:确保试车设备、工具和仪器的完好无损,可以正常使用。
同时要做好试车设备的校准和调试工作,保证测试的准确性。
3. 确认试车方案:根据产品的技术要求和试车要求,制定详细的试车方案,包括测试项目、测试方法、试车时长等内容。
4. 检查试车环境:试车环境应保持干净整洁、通风良好,确保试车设备和仪器的正常运行。
5. 确保试车安全:在试车过程中,要严格遵守安全操作规程,保证试车人员的安全和试车设备的完好。
二、试车过程1. 进行功能测试:首先对产品的功能进行测试,包括启动、停止、调速等操作,确保产品的基本功能正常。
2. 进行性能测试:根据产品的技术要求,进行性能测试,包括输出功率、效率、稳定性等指标的测试,确保产品的性能符合规定的要求。
3. 进行耐久性测试:根据产品的使用场景和预期寿命,进行耐久性测试,包括连续运行、高负荷运行等测试,确保产品的耐久性和可靠性。
4. 进行环境适应性测试:根据产品的使用环境和工作条件,进行环境适应性测试,包括湿热、寒冷、振动等测试,确保产品在各种环境下都能正常工作。
5. 进行安全性测试:根据产品的安全标准,进行安全性测试,包括电气安全、机械安全等测试,确保产品使用过程中不会对人体造成危害。
三、试车结束工作1. 汇总试车数据:将试车过程中得到的数据进行整理和汇总,包括测试结果、问题记录、故障分析等内容。
2. 分析试车结果:对试车结果进行分析,找出可能存在的问题和改进措施,及时对产品进行调整和改进。
3. 编制试车报告:根据试车结果和分析,编制试车报告,包括试车过程、问题分析、改进建议等内容,向有关部门和客户汇报。
4. 反馈试车结果:将试车结果反馈给相关部门,包括生产部门、研发部门、质量部门等,与他们共同探讨问题的原因和解决方案。
试车工艺管理制度
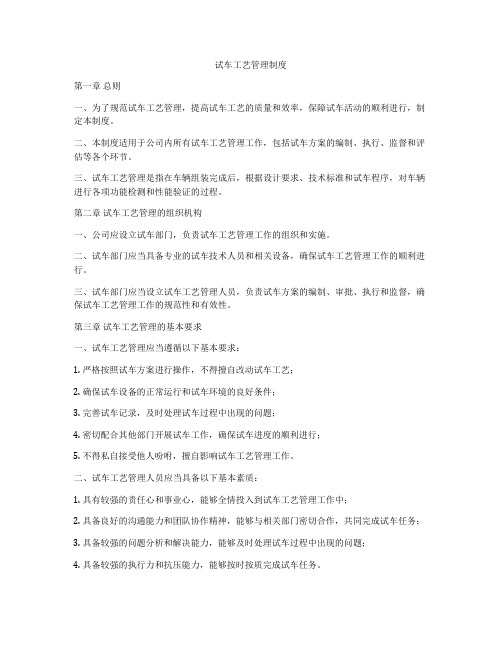
试车工艺管理制度第一章总则一、为了规范试车工艺管理,提高试车工艺的质量和效率,保障试车活动的顺利进行,制定本制度。
二、本制度适用于公司内所有试车工艺管理工作,包括试车方案的编制、执行、监督和评估等各个环节。
三、试车工艺管理是指在车辆组装完成后,根据设计要求、技术标准和试车程序,对车辆进行各项功能检测和性能验证的过程。
第二章试车工艺管理的组织机构一、公司应设立试车部门,负责试车工艺管理工作的组织和实施。
二、试车部门应当具备专业的试车技术人员和相关设备,确保试车工艺管理工作的顺利进行。
三、试车部门应当设立试车工艺管理人员,负责试车方案的编制、审批、执行和监督,确保试车工艺管理工作的规范性和有效性。
第三章试车工艺管理的基本要求一、试车工艺管理应当遵循以下基本要求:1. 严格按照试车方案进行操作,不得擅自改动试车工艺;2. 确保试车设备的正常运行和试车环境的良好条件;3. 完善试车记录,及时处理试车过程中出现的问题;4. 密切配合其他部门开展试车工作,确保试车进度的顺利进行;5. 不得私自接受他人吩咐,擅自影响试车工艺管理工作。
二、试车工艺管理人员应当具备以下基本素质:1. 具有较强的责任心和事业心,能够全情投入到试车工艺管理工作中;2. 具备良好的沟通能力和团队协作精神,能够与相关部门密切合作,共同完成试车任务;3. 具备较强的问题分析和解决能力,能够及时处理试车过程中出现的问题;4. 具备较强的执行力和抗压能力,能够按时按质完成试车任务。
第四章试车工艺管理的具体操作一、试车工艺管理的流程包括试车方案的编制、审批、执行和监督等步骤。
二、试车方案的编制应当包括试车的具体内容、试车的时间计划、试车的人员安排、试车的设备准备等方面。
三、试车方案应当由试车工艺管理人员编制,并提交给相关部门审批。
四、试车方案的执行应当由试车工艺管理人员负责,确保试车工作按照方案的要求进行。
五、试车方案的监督应当由试车部门负责,对试车工作进行监督和评估,及时纠正偏差和问题。
试车作业制度
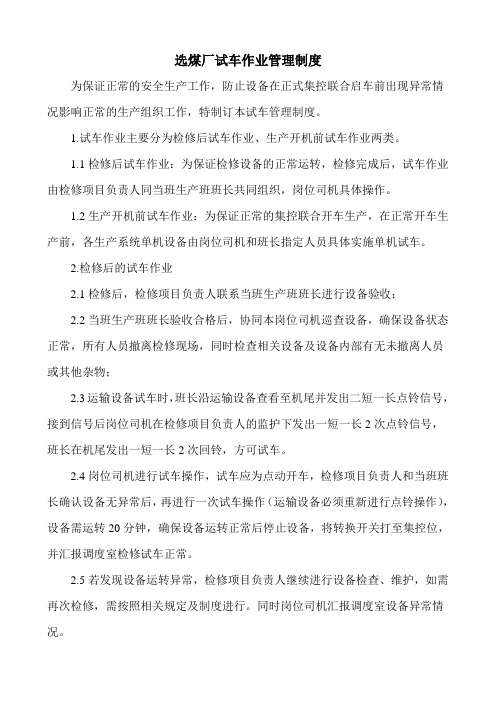
选煤厂试车作业管理制度为保证正常的安全生产工作,防止设备在正式集控联合启车前出现异常情况影响正常的生产组织工作,特制订本试车管理制度。
1.试车作业主要分为检修后试车作业、生产开机前试车作业两类。
1.1检修后试车作业:为保证检修设备的正常运转,检修完成后,试车作业由检修项目负责人同当班生产班班长共同组织,岗位司机具体操作。
1.2生产开机前试车作业:为保证正常的集控联合开车生产,在正常开车生产前,各生产系统单机设备由岗位司机和班长指定人员具体实施单机试车。
2.检修后的试车作业2.1检修后,检修项目负责人联系当班生产班班长进行设备验收;2.2当班生产班班长验收合格后,协同本岗位司机巡查设备,确保设备状态正常,所有人员撤离检修现场,同时检查相关设备及设备内部有无未撤离人员或其他杂物;2.3运输设备试车时,班长沿运输设备查看至机尾并发出二短一长点铃信号,接到信号后岗位司机在检修项目负责人的监护下发出一短一长2次点铃信号,班长在机尾发出一短一长2次回铃,方可试车。
2.4岗位司机进行试车操作,试车应为点动开车,检修项目负责人和当班班长确认设备无异常后,再进行一次试车操作(运输设备必须重新进行点铃操作),设备需运转20分钟,确保设备运转正常后停止设备,将转换开关打至集控位,并汇报调度室检修试车正常。
2.5若发现设备运转异常,检修项目负责人继续进行设备检查、维护,如需再次检修,需按照相关规定及制度进行。
同时岗位司机汇报调度室设备异常情况。
3.生产开机前试车作业3.1日常停产检修或大检修后,未进行检修的设备在调度室的安排下,岗位司机进行生产开机前的试车工作;3.2岗位司机首先巡查设备,确保设备状态正常,同时检查相关设备及设备内部有无人员或其他杂物;3.3运输设备试车时,岗位司机汇报当班班长,由班长指定人员到达机尾并发出二短一长点铃信号,通知机头人员可以试车。
岗位司机在机头发出一短一长2次点铃信号,等待机尾回铃,回铃为一短一长2次回铃。
试车员管理规范

试车员管理规范一、引言试车员是汽车行业中重要的岗位之一,他们负责测试和评估新车型的性能和安全性。
为了确保试车员的工作能够高效、安全地进行,制定一套试车员管理规范是必要的。
本文将详细介绍试车员管理规范的内容和要求。
二、试车员的基本要求1. 资质要求:试车员应具备相应的驾驶技能和驾驶经验,并持有合法的驾驶证。
对于特定车型的试车员,还需要具备相关的专业知识和培训证书。
2. 健康状况:试车员应保持良好的身体健康状况,不得患有影响驾驶安全的疾病或残疾。
3. 遵守交通法规:试车员应严格遵守道路交通法规,不得超速、闯红灯、酒后驾驶等违法行为。
4. 责任心和专业素养:试车员应具备高度的责任心和职业道德,保证工作中的严谨性和准确性,不得泄露试车过程中的商业机密。
三、试车员的管理流程1. 招聘与选拔:根据企业的需求和标准,制定试车员的招聘和选拔流程。
包括发布招聘信息、面试、考核等环节,确保选出合适的试车员人选。
2. 培训与考核:新入职的试车员应接受相关的岗位培训,包括驾驶技能、安全意识、车辆知识等方面的培训。
并定期进行考核,评估试车员的工作表现和能力水平。
3. 工作规范:制定试车员的工作规范,明确试车员的职责和工作流程。
包括试车前的准备工作、试车过程中的注意事项、试车后的记录和反馈等。
4. 安全管理:确保试车员的安全是管理的重点之一。
制定安全管理制度,包括车辆安全检查、紧急情况处理、事故报告和处理等。
同时,提供必要的安全装备和保障措施,确保试车员的人身安全。
5. 数据管理:试车过程中产生的数据是宝贵的资产,应建立科学的数据管理系统,包括数据采集、存储、分析和应用等环节。
同时,保护试车数据的安全性和机密性,防止泄露和滥用。
6. 绩效评估:定期对试车员的工作进行绩效评估,包括驾驶技能、工作质量、安全记录等方面。
根据评估结果,给予相应的奖励或处罚,激励试车员提高工作水平和质量。
四、试车员的职业发展为了激励试车员的积极性和提高整体素质,应制定试车员的职业发展规划。
试车制度模板
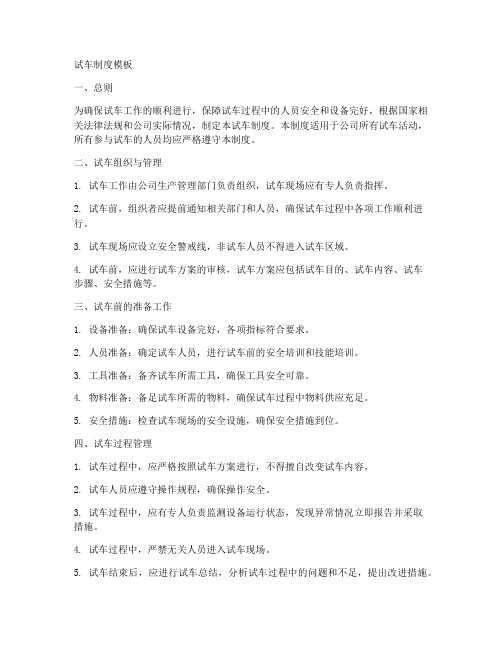
试车制度模板一、总则为确保试车工作的顺利进行,保障试车过程中的人员安全和设备完好,根据国家相关法律法规和公司实际情况,制定本试车制度。
本制度适用于公司所有试车活动,所有参与试车的人员均应严格遵守本制度。
二、试车组织与管理1. 试车工作由公司生产管理部门负责组织,试车现场应有专人负责指挥。
2. 试车前,组织者应提前通知相关部门和人员,确保试车过程中各项工作顺利进行。
3. 试车现场应设立安全警戒线,非试车人员不得进入试车区域。
4. 试车前,应进行试车方案的审核,试车方案应包括试车目的、试车内容、试车步骤、安全措施等。
三、试车前的准备工作1. 设备准备:确保试车设备完好,各项指标符合要求。
2. 人员准备:确定试车人员,进行试车前的安全培训和技能培训。
3. 工具准备:备齐试车所需工具,确保工具安全可靠。
4. 物料准备:备足试车所需的物料,确保试车过程中物料供应充足。
5. 安全措施:检查试车现场的安全设施,确保安全措施到位。
四、试车过程管理1. 试车过程中,应严格按照试车方案进行,不得擅自改变试车内容。
2. 试车人员应遵守操作规程,确保操作安全。
3. 试车过程中,应有专人负责监测设备运行状态,发现异常情况立即报告并采取措施。
4. 试车过程中,严禁无关人员进入试车现场。
5. 试车结束后,应进行试车总结,分析试车过程中的问题和不足,提出改进措施。
五、试车后的验收与总结1. 试车结束后,应对试车设备进行检查,确保设备完好。
2. 对试车过程中的数据进行整理和分析,判断试车目标是否达成。
3. 撰写试车总结报告,内容包括试车目的、试车过程、试车结果、存在问题及改进措施等。
4. 试车总结报告应提交给相关部门审批,并根据审批意见进行整改。
六、试车安全与环保1. 试车过程中,应严格遵守国家安全生产法律法规,确保人员安全。
2. 试车过程中,应做好环保措施,防止污染环境。
3. 试车现场应配备必要的消防设施,确保火灾事故应急预案的实施。
试车员管理规范

试车员管理规范一、背景介绍试车员是指负责对车辆进行试验、试运行以及测试的专业人员。
试车员的管理规范是为了保证试车工作的安全性、高效性和准确性,提高车辆的品质和性能,确保车辆的安全运行。
二、试车员管理的目标1. 确保试车员具备必要的技能和知识,能够熟练操作和驾驶各类车辆。
2. 提高试车员的安全意识和责任心,减少事故和故障的发生。
3. 优化试车工作流程,提高试车效率和准确性。
4. 加强试车员与其他部门的沟通和协作,促进整体工作的协调和顺利进行。
三、试车员管理的要求1. 岗位要求试车员应具备以下条件:- 具备相关车辆试验、试运行或测试经验;- 熟悉各类车辆的结构和性能特点;- 熟练掌握车辆试验设备的使用和维护;- 具备良好的驾驶技术和安全意识;- 具备较强的沟通和协调能力。
2. 岗位职责试车员的主要职责包括但不限于以下方面:- 根据试验计划和要求,准备试车所需的设备和工具;- 进行试车前的检查和调试工作,确保车辆处于良好的工作状态;- 按照试验要求进行试车操作,记录试车过程中的数据和异常情况;- 及时上报试车过程中出现的问题和意见,提出改进措施;- 维护试车设备和工具的正常运行,确保其可靠性和安全性;- 配合其他部门进行试车工作的协调和安排。
3. 安全管理试车员在试车过程中应严格遵守安全规范,确保人员和设备的安全。
具体要求包括:- 熟悉并遵守车辆试验的安全操作规程;- 使用个人防护装备,如安全帽、安全鞋等;- 遵守交通规则,确保试车过程中的交通安全;- 定期参加安全培训和演练,提高应急反应能力;- 及时上报试车过程中的安全隐患和事故情况。
4. 数据管理试车员应准确记录试车过程中的数据和异常情况,确保数据的可靠性和完整性。
具体要求包括:- 使用专业的数据记录设备,确保数据的准确采集;- 及时整理和归档试车数据,建立完善的数据管理系统;- 对试车数据进行分析和评估,提出改进建议;- 保护试车数据的安全性和机密性,避免泄露和损坏。
制程检验作业管理办法

制程检验作业管理办法
是为了确保制程检验作业的顺利进行和质量控制,从而保证产品制程的稳定性和符合质量要求制定的一系列管理规定。
以下是一个制程检验作业管理办法的示例:
1. 作业目标:制程检验作业的目标是确保产品在各个制程节点都符合质量要求,发现并解决制程中的问题,提高生产效率和产品质量。
2. 职责分工:明确各个岗位的职责和权限,包括制程检验人员、生产责任人和质量管理部门的职责和权限分工。
3. 作业流程:制定制程检验的作业流程,包括检验项目、方法和标准,制程检验的时机和频率,以及检验结果的处理和记录方式。
4. 设备和工具管理:确保制程检验所需的设备和工具的可用性和有效性,制定设备和工具的维护和校准计划,记录设备和工具的使用情况和维护记录。
5. 人员培训和资质管理:制定制程检验人员的培训计划和制程检验技能的评估机制,确保制程检验人员具备必要的技能和知识。
6. 异常处理和改进措施:建立异常处理和改进措施的流程,包括制程检验中发现的异常情况的处理和记录,以及对异常情况的分析和改进措施的制定。
7. 文件管理:制定制程检验的文件管理规定,包括检验记录的保存和归档,制程检验作业相关文件的管理和使用。
8. 监督和评估:建立制程检验作业的监督和评估机制,包括定期进行作业质量评估和绩效评估,及时发现问题并采取改进措施。
9. 安全和环境管理:制程检验作业要符合安全和环境管理规定,确保检验过程不会对人员和环境造成危害。
10. 保密管理:对制程检验作业中涉及的机密信息进行保护和管理,确保信息安全。
以上是一个制程检验作业管理办法的简要示例,具体实施可以根据企业的实际情况和需求进行调整和完善。
钻孔制程试车作业规范

鑽孔製程試車作業規範一、目的---------------------------------------------------------------1二、說明---------------------------------------------------------------3三、設備點檢項目----------------------------------------------------4四、測試項目----------------------------------------------------------5M54-QI-08-R-04-01一、目的測試新進設備品質和製程能力,為現場量產做準備二、說明內層試車計畫包含一個主要設備,清單如下:(1)鑽孔機製程試車計畫由相關製程負責PE編製,交付工程部、製造部及品保部會簽,會同相關製程的各部負責人共同配合執行。
測試板與小量產規定(1) 測試板數量: 20-100PNL ,尺寸:接近設備最大設計尺寸,板厚:無特殊要求時40-60mil.(2) 小量產數量3-10 lot(150PNL/lot)M54-QI-08-R-04-01三設備點檢項目M54-QI-08-R-04-01四測試項目備註: 鑽孔制程參數是針對每一機台每一根軸來檢測M54-QI-08-R-04-01測試方法1.Runout測試方法(1)靜態測試a.夾頭夾住標準棒b.以千分錶頭剛剛接觸標準棒c.在用手帶動主軸的情況下讀出千分錶的讀數.(2)動態測測試M54-QI-08-R-04-01a.夾頭夾住測試PINb.將動態RUNOUT儀以固定PIN固定在PIN夾上c.z軸連續下降四次至測試PIN 下截面與RUNOUT儀在同一水平面上,然後再下降12MMd.啟動鑽孔機,主軸分別以20krpm,60krpm,120krpm旋轉e.讀出RUNOUT儀的讀數2. 孔位精度測試方法(每台每軸測試)一.鑽孔程式由CAM設計完成.每兩孔軸向座標相差0.5,共1505孔.M54-QI-08-R-04-01二.測試材料及參數1.測試材料62mil 1/1 18”×24”裸銅基板2.鑽孔參數三.測試方法1.鑽孔疊構兩片鑽一次為一組.每根Spindle鑽1組數據;對第一次鑽出的數據有偏差的軸,進行第二次鑽,以作確認.M54-QI-08-R-04-01M54-QI-08-R-04-012.具體步驟(1)每軸鑽,上面必須放置鋁板、下面放置墊板. (2)驗前必須檢查墊、面是否清潔、無翹曲. (3)板子以2pin 固定後四邊仍須貼膠帶固定. (4)每鑽一次都用研一針鑽孔至完畢. (5)板子經過打磨後即可進行測試.(6)測試時以左下第三孔為原點,隨機在板內均勻選取另外24孔測量其相對於原點的座標值. (7)所得到的數據與CAM 給出的數據核對表示所選取孔的大概位置原點Y 軸M54-QI-08-R-04-01。
制程检验作业管理办法

制程检验作业管理办法
是为了规范制程检验作业过程,确保产品质量符合标准要求的管理办法。
以下是一份常见的制程检验作业管理办法的内容:
1. 目的和范围:
1.1 确定制程检验的目的,即确保产品质量符合标准要求;
1.2 确定制程检验的范围,即对哪些制程进行检验。
2. 负责人和职责:
2.1 指定制程检验的负责人,并明确其职责;
2.2 制定相关流程和工作指导,并进行必要的培训。
3. 检验程序:
3.1 确定制程检验的步骤和方法;
3.2 确定制程检验所需的检验设备和工具,并进行校准;
3.3 制定样品抽取规则和数量。
4. 检验文件和记录:
4.1 制定制程检验所需的文件和记录表;
4.2 确定文件和记录的保存方式和期限;
4.3 确定文件和记录的查阅权限和程序。
5. 不合格品处理:
5.1 确定制程检验出现不合格品的处理办法;
5.2 确定责任人和处理程序;
5.3 进行不合格品的分类、评估和回溯分析,以及采取纠正措施。
6. 改进措施:
6.1 定期评估制程检验的效果和效率;
6.2 确定改进的目标和措施,提高制程检验的质量和效果。
以上是一份常见的制程检验作业管理办法的内容,具体的内容和步骤可以根据实际情况进行调整和补充。
制程检验作业管理办法

制程检验作业管理办法第一章总则第一条为了规范制程检验作业,保证产品质量,提高生产效率,特制定本管理办法。
第二条本管理办法适用于企业生产过程中的制程检验作业。
第三条制程检验是指在生产加工过程中,对产品的各道工序进行检验的过程。
第四条制程检验的目的是确保产品质量符合规定标准,及时发现和纠正生产过程中的问题,提高生产效率和产品质量。
第五条制程检验的责任主体为相关部门的质量部门。
第六条制程检验的具体内容和方式,由质量部门根据产品特性和生产流程确定,并予以执行。
第七条制程检验应当遵循以下原则:1. 及时性原则,即在生产过程中,要及时对产品进行检验,发现问题及时纠正;2. 全面性原则,即对产品的各道工序都要进行检验,确保每个环节都符合质量要求;3. 规范性原则,即制定统一的操作规程和标准,确保制程检验作业的质量和效率。
第八条制程检验应当采用科学的方法和先进的检测设备,确保检验结果的准确性和可靠性。
第九条制程检验结果应当记录,并及时反馈给相关部门,以便做出相应的调整和改进。
第十条制程检验作业过程中发现的问题,应当及时报告,并采取对应措施进行处理。
第二章制程检验作业流程第一节检验准备第十一条在进行制程检验作业之前,需要对相关设备和仪器进行校验和调试,确保其正常运行。
第十二条制程检验前,相关人员应当进行培训,了解检验标准和要求,熟悉操作流程。
第十三条制程检验前,应当准备好检验样品和检验记录表,确保检验的顺利进行。
第二节制程检验第十四条制程检验应当按照规定的检验方法和标准进行,确保结果的准确性和可靠性。
第十五条制程检验应当在生产过程中进行,及时发现和纠正问题,确保产品质量符合要求。
第十六条制程检验过程中发现的问题,应当及时进行记录,并通知相关部门进行处理。
第三节检验结果处理第十七条制程检验结果应当及时反馈给产品质量管理部门。
第十八条制程检验结果不合格的,应当进行追溯,找出原因,并采取相应的纠正措施。
第十九条制程检验结果合格的,应当及时进行记录和归档,并通知相关部门。
试车作业规范

5.1.5试车单位与制造、生管、品管协调后,由生管安排试车计划。
5.1.6试车单位在试车前召集生产单位和品管等相关人员,说明试车流程、参数及试车重点和注意事项,产品试车由品管整理会议记录。
5.1.7原物料必须凭《试车通知单》领用,《原物料领/发料单》由试车单位人员或其指定的代理部门人员签核。试车专用原物料不管有否耗用完,都必须全部领完,并由品管在《原物料领/发料单》上确认。
制造处、生管处、采购及品管部等相关单位协助试车。
生管处、财务部负责试车费用的汇总和划转。
5.作业内容:
5.1公司外部单位试车作业:流程见附件一。
5.1.1试车主导单位填写《试车申请单》,经试车单位理级以上主管签字确认。结束后并列明费用归属单位,再交相关单位签字并经各级主管核准。(汇总到品管部品质工程,并复印给相关单位)
1.目的:
规范试车作业流程,确保试车顺利进行
2.适用范围:
公司外部单位和公司内部单位在工厂的试车作业。
3.名词解释:无
4.职责:
品质工程员:主导本厂新瓶型,新瓶盖、新设备安装、新产品等工艺试车及配合研发试车;
制程科:负责其他小试车如香精更换厂家及小料开发新厂家、物料上机性能等小试车由制程科主导;
另试车提出单位:主导试车整个过程。
5.1.8生产单位依据试车单位要求的试车流程和参数进行生产作业。
5.1.9试车单位人员在现场主导调配,确认制程参数、包装规格。
5.1.10品管部负责制程管制管制点和成品规格的检测。
5.1.10.1试车前制程科确认调配(包括萃取)的卫生状况及设备状况,记录在《制程管制日报表》上。有异常及时反馈品管主管和调配当班主管,并通知相关部门。待处理正常后,通知相关部门可试车。
- 1、下载文档前请自行甄别文档内容的完整性,平台不提供额外的编辑、内容补充、找答案等附加服务。
- 2、"仅部分预览"的文档,不可在线预览部分如存在完整性等问题,可反馈申请退款(可完整预览的文档不适用该条件!)。
- 3、如文档侵犯您的权益,请联系客服反馈,我们会尽快为您处理(人工客服工作时间:9:00-18:30)。
内层制程试车作业规范
一、目的---------------------------------------------------------------1
二、说明---------------------------------------------------------------3
三、设备点检项目----------------------------------------------------4
四、测试项目----------------------------------------------------------5
一、目的
测试新进设备品质和制程能力,为现场量产做准备
二、说明
内层试车计画包含伍个主要设备,清单如下:
(1)裁板机
(2)前处理线
(3)压膜机
(4)曝光机
(5)後处理
制程试车计画由相关制程负责PE编制,交付工程部、制造部及品保部会签,会同相关制程的各部负责人共同配合执行。
测试板与小量产规定
(1) 测试板数量: 20-100PNL ,尺寸:接近设备最大设计尺寸,板厚:无特殊要求时40-60mil.
(2) 小量产数量 3-10 lot(150PNL/lot)
三设备点检项目
四测试项目
测试方法
1.内层前处理
水破实验的测试方法:
取39 mil 1/1 20"×24"基板走过前处理线後,浸入水中然後拿起,将板子倾斜45,让水沿着板子流下,观察水膜破裂时间,并记录数据.
前处理微蚀量测试方法:
1将板厚39mi l 15cm×15cm裸铜基板作为测试板,将其用水洗净,置於烤箱内以120℃烘烤15分钟.
2烘烤後取出基板并冷却3分钟,称重至小数点以下四位,记录为W1.
3将测试板与生产板一起走完微蚀槽,注意不可与量产板重叠.
4微蚀完毕後将基板取出水洗,然後置於烤箱内以120℃烘烤15分钟,并冷却3分钟,
称重至小数点以下四位,记录为W2..
5 Etch count=( W1-W2) ×92900/(2××A)单位:u"
W1、W2单位:克 A:测试板面积 A的计算:当规格为10cm×10cm 时,A为100
2.内层压膜制程
干膜对准度
测试目的: 测试压膜机压膜对准能力
测试材料: 39mil 1/1 20”×24”裸铜基板
检验工具: 量尺
检验标准: 干膜距板边2±1mm
测试方法: 取测试用基板走过压膜线後,测试干膜与板边间距
板出温度
测试目的:测试压膜机压膜的温度控制能力
测试材料: 39mil 1/1 20”×24”裸铜基板
检验工具:红外线测温器
检验标准: 60±5℃
测试方法: 取测试用基板走过压膜线时过压膜线15cm处量测基板表面左中右三点温度
3.内层曝光制程
曝光能量
测试目的: 测试灯管的能量是否达到要求及干膜的最佳曝光能量范围
测试材料: 39mil 1/1 20”×24”测试板
检验工具: 21格曝表,测试底片
检验标准: ±格
测试方法:1准备好测试板,进行内层前处理作业
2准备"内层干膜,并架到压膜机上,确认压膜机的条件无误後将前处理完毕後的测试板进行压膜作业
3准备一的透明底片,以遮光胶带固定於曝光台面上,再将曝光格数底片固定
於透明底片上,固定时须注意曝光格数底片的药液面必须接触测试板的干
膜。
4将压膜完毕的测试板放於架好的曝格表的曝光机中,确认曝光机条件无误,
曝光完毕後将测试板静置15分钟以上
5确认内层显影段操作条件及显影液是否正常後将曝光并静置完毕的测试板进行显影作业,在水洗後将测试板取出
6观察显影後的测试板,其显示格数即为受测曝光机於制作测试板的实际曝光格数
CCD对位精准度
测试目的: 测试曝光机对位能力
测试材料: 39mil 1/1 20”×24”测试板
检验工具: 金相显微镜
测试方法: 将测试板依内层流程走完DES线後,选取一面含有PAD,另一面有对应的空心圆的区域切下做成切片,把PAD恰好磨去一半时量测其圆心与其对应空
心圆圆心的距离,即为测出的CCD对准度
4.内层DES制程
显影点
测试目的:测试显影线显影效果是否正常
测试材料: 39mil 1/1 20”×24”测试板
检验工具:量尺,秒表
检验标准: 50%±5%,测试速度5.0M/MIN
测试方法:1准备基板10PNL,做前处理、压膜後待用
2将测试板放入显影段,测试板放置时须紧密连靠,此时记录第一片板子经过
显影槽的时间,以米尺量测显影槽的长度,推算出实际速度与设定速度是否
符合
3第一片板子出显影段时,立即将显影液喷压关闭,待走完显影段的水洗後,
将板子取出并按放板的顺序依序排列在显影槽出板处
4依测试板的显影程度,於开始有显影不净处做记录,以米尺量测并除以显影槽的全长,计算出显影点。
5显影点计算方式:[1-(显影乾净的有效长度/显影槽有效长度)]×100%
6显影点未达标准时,检视显影槽的喷嘴、喷压及速度,若有异常则调整至标准值。
氯化铜测试
测试目的: 测试DES线显影、去膜是否乾净
测试材料: 39mil 1/1 20”×24”测试板
检验工具:氯化铜,秒表
测试方法:1准备欲确认的测试板,将其浸泡於氯化铜溶液槽中,浸泡5sec後取出,并立即以水洗将板面残留氯化铜溶液冲净
2观察测试板的板面情形,是否氧化的亮点残筒存在,此即为观察有无scum 残留的氯化铜测试
解析度/附着力
测试目的: 测试内层曝光显影能达到的解析与附着能力
测试材料: 39mil 1/1 20”×24”测试板
检验工具: 测试底片,50倍高脚目镜
检验标准: 75μm /75μm
测试方法:1确认制程参数条件无误後再进行测试
2线距判断方式:测试板制作完成後进行量测,将有短路的区块标出,找出短路之处後以100倍高脚镜判断其短路原因
3线宽的判断方式:线路不变形的最小线宽
蚀刻点
测试目的: 测试蚀刻段蚀刻效果是否正常
测试材料: 39mil 1/1 20”×24”测试板
检验工具:量尺,秒表
检验标准: 70%±5%,测试速度5.0M/MIN
测试方法:1准备基板、依现场条件做至前处理完毕後待用
2将测试板依次放入蚀刻段,并记录第一PNL从进入到出来的时间,算出实际的速度以便与设定速度作比较
3当第一PNL测试板出蚀刻段时立即关闭喷压,待走完水洗後,将板子取出并按放板的顺序依序排列在蚀刻段出板处
4依测试板的蚀刻程式,观察开始有蚀刻不净处,并量出长度,再除以蚀刻段的全长,计算出蚀刻点。
5蚀刻点计算方式:[1-(蚀刻乾净的有效长度/蚀刻段的有效长度)]×100%
6蚀刻点未达标准时,检视蚀刻槽的喷嘴、喷压、速度与药液,若有异常则调整至标准值。
蚀刻均匀性
测试目的: 测试蚀刻段蚀刻是否均匀
测试材料: 39mil 2/2 20”×24”测试板
检验工具: MRX量测仪,PP纸
检验标准:10%↓,测试速度5.0M/MIN
测试方法:1依内层板流程至前处理(微蚀槽不开),把基板表面均分成25个区域,以MRX 量测仪量测每一区域的铜厚,并计算其平均值为A
3内层後处理蚀刻段共有3槽,测试其蚀刻均匀性时需分3 次
1)测试第一槽时,将2、3槽关闭
2)测试2、3槽时方式同上,须关闭其余2槽
4蚀刻完毕後(水洗完毕)把PP垫盖上,以MRX量测每PP上每一空格处蚀刻後的残铜厚度,并计算其平均值为B
5计算其蚀刻均匀性U%,计算公式如下:U% =[R/2(A-B)] ×100% 其中R 值为同一面咬蚀量的最大值与最小值的差异
6未达标准,在准备新的测试板上重复上述步骤,直至均匀性达到13%以下为止
蚀刻因数
测试目的: 测试蚀刻段蚀刻的侧蚀情况
测试材料: 39mil 1/1 20”×24”测试板
检验工具: 测试底片
检验标准: 3↑
测试方法:1确认制程参数条件无误後再进行测试
2把板子走完DES线後做切片,量测线路上下线宽,厚度,并量测底片设计之
线宽计算蚀刻因数,上喷下喷都需量测 EF=H/[(A-B)/2]
3若有未达标,则进行分析(可能原因:喷嘴,喷压,角度,药液等)并进行调整
去膜点
测试目的: 测试显影线去膜效果是否正常
测试材料: 39mil 1/1 20”×24”测试板
检验工具: 量尺,秒表
检验标准: 40%±5%,测试速度5.2M/MIN
测试方法:1准备基板10PNL,做前处理、压膜,用透明底片对其进行曝光静置15分钟後待用
2将测试板放入去膜段,测试板放置时须紧密连靠,此时记录第一片板子经过
去膜槽的时间,以米尺量测去膜槽的长度,推算出实际速度与设定速度是否
符合
3第一片板子出去膜段时,立即将去膜液喷压,传动关闭,打开去膜槽的上盖板,观察去膜情况
4依测试板的去膜程度,於开始有去膜不净处做记录,以米尺量测并除以去膜
槽的全长,计算出去膜点。
测试完毕後,打开喷压,传动,将测试板取出
5去膜点计算方式:[1-(去膜乾净的有效长度/去膜槽有效长度)]×100%
6去膜点未达标准时,检视去膜槽的喷嘴、喷压及速度,若有异常则调整至标准值。