SMC模压成型工艺参数对成型质量的影响
SMC片状模压成型工艺

SMC树脂糊的组成
树脂 引发剂
填料 低收缩添加剂
化学增稠剂 内脱模剂 着色剂
不饱和聚酯(间苯型UP、邻苯型UP) 过氧化物(BPO、TBP) CaCO3 热塑性树脂粉 MgO 硬酯酸金属盐 染料
15
SMC的工艺特点和地位
操作方便,易实现自动化,生产效率高,改善了湿法成型的 作业环境和劳动条件; 通过改变组分的种类与配比,可改变成型工艺和制品性能; 通过改变填料的种类与加入量,可降低成本或使制品轻量化; 成型流动性好,可成型结构复杂的制件或大型制件; 制品尺寸稳定性好,表面平滑,光泽好,纤维浮出少,从而 简化了后处理工序; 增强材料在生产与成型过程中均无损伤,制品强度高,可进 行轻型化结构设计。
通过加入增稠剂就能满足这种要求。 增稠剂又叫增粘剂,其作用是使不饱和聚酯树脂的粘度 迅速增加,粘度达到工艺要求后又相对稳定。
24
增稠剂的特性
① 在浸渍阶段,为了保证良好的浸润性,增稠过程要缓慢; ② 在浸渍后,又要求粘度迅速增高,以适应贮运和模压操作; ③ 增稠后的坯料,在模压温度下能迅速充满模腔,并使树脂与 纤维不发生离析; ④ 增稠后的粘度,在贮存期内必须稳定在可模压的范围内; ⑤ 增稠作用在生产中应该有稳定的重现性。
④不够“绿色”,有一定污染。
2
模压成型
(Compression Molding )
树脂体系 增强纤维 模具 压机
模压料
4
模具及压机
5
模塑料
片状模塑料(Sheet Molding Compound,SMC):不饱和 聚酯树脂浸渍短切纤维或毡片,经增稠后制得薄片状模塑料。 在生产时,只需将片状模塑料裁剪、叠合后放入模具中热压, 就可得到制品。
SMC压制工艺介绍

? 近年来世界发达国家在 SMC方面的研究更是不遗余力,使该材料拥有 广大的市场。SMC具有良好的机械性能与简易加工性,使其成为众所 瞩目的材料。SMC成型一般只需 3~6min,具有节省人力与能源,便于 大量生产,提高产品质量等优点。在与各种材料进行对比中, SMC不 仅优于钢铁、铝等传统金属材料,而且可与一般热塑性塑料及其它增 强材料一争高低。( 1)与金属材料相比, SMC具有优越的电气性能 ,耐腐蚀性能、质轻以及工程设计容易、灵活等特点;( 2)与增强 热塑性塑料相比, SMC的成型周期短,成型设备投资低, SMC制品不 易变形,机械性能与热变形温度较高,耐化学药品性优,且价格较低 ;(3)与一般热塑性塑料相比, SMC的物理性能是后者不可比拟的 。
? 故在该体系中,热塑性树脂相的热膨胀是控制收缩率的主要因素 。低收缩添加剂的玻璃化温度的高低以及玻璃化前后的膨胀情况 对控制收缩率的效果有很大的影响。
? 五)、化学增稠剂
? 在SMC生产中增稠剂是必需的,通过增稠作用使 SMC从利于玻纤 浸渍的低粘度转化为不粘手的高粘度。在浸渍阶段,树脂增稠要 足够缓慢,保证玻纤的良好浸渍;浸渍后后树脂浸渍要足够快, 使SMC尽快进入模压阶段和尽量减少存货量;当 SMC粘度达到可 成型和模压粘度后,增稠过程要立即停止,稳定,以获得尽可能 长的贮存寿命。
研究表明:
? 1.增稠速度与树脂酸值成正比
? 2.体系中水分的存在强烈影响初期粘度上升,水含量超过1.5%, 会使增稠后粘度变低,使 SMC表面发粘,因此生产过程中必须对 所有原材料的含水量进行严格控制;
? 3.温度是影响树脂增稠的最重要因素,较高温度可降低 SMC生产 前期树脂糊粘度而利于输送及玻纤浸渍,又能加快浸渍后树脂糊 粘度的上升,并达到更高的增稠水平,在 SMC制备后,往往要将 其送入加温熟化室中加速稠化,以缩短启用期。
模压成型的压力和温度设定对产品质量的影响

模压成型的压力和温度设定对产品质量的影响
模压成型是一种常用的工艺过程,特别适用于塑料制品的生产。
在模压成型过程中,压力和温度的设定是非常关键的因素,对最终产品的质量有着重要影响。
首先,压力是模压成型过程中的主要控制参数之一。
通过调整模具的开合速度和压力大小,可以有效地控制原料在模具中的填充情况。
适当的压力可以确保原料充分填充模具的每个角落,避免产品出现空洞或瘤状缺陷。
同时,合适的压力还可以帮助原料与模具表面更好地接触,从而提高产品的表面光洁度和精度。
其次,温度设定也是影响产品质量的重要因素之一。
在模压成型过程中,原料需要在一定温度范围内进行加热,使其塑性达到最佳状态,有利于成型和流动。
适当的温度可以保证产品表面光滑、无瑕疵,同时还可以减少产品的收缩率和内部应力,提高产品的尺寸稳定性和力学性能。
此外,压力和温度两者之间的配合也至关重要。
通常情况下,适当增加压力的同时需相应提高温度,以保证原料能够充分流动并填充模具。
过高或过低的温度都会导致产品质量下降,如温度过高可能导致产品烧结或变形,温度过低则可能导致产品表面粗糙或开裂。
因此,在模压成型过程中需要综合考虑压力和温度的互相作用,以获得最佳的成型效果和产品质量。
总的来说,模压成型的压力和温度设定是影响产品质量的重要因素,合理的压力和温度设定可以提高产品的成型精度、表面质量和力学性能,从而满足客户的各种需求。
在生产实践中,运用科学的方法和经验总结,不断优化压力和温度的设定参数,将有助于提高生产效率、降低成本,实现模压成型生产的良性循环发展。
1。
SMC模压成型工艺过程
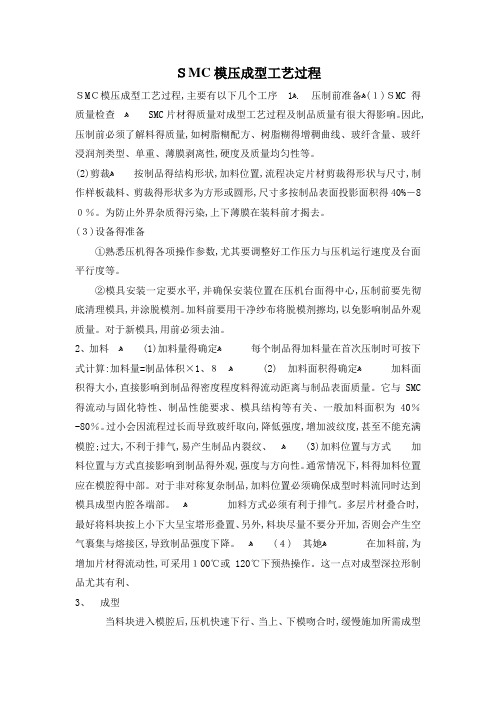
SMC模压成型工艺过程SMC模压成型工艺过程,主要有以下几个工序ﻫ1. 压制前准备ﻫ(1)SMC得质量检查ﻫSMC片材得质量对成型工艺过程及制品质量有很大得影响。
因此,压制前必须了解料得质量,如树脂糊配方、树脂糊得增稠曲线、玻纤含量、玻纤浸润剂类型、单重、薄膜剥离性,硬度及质量均匀性等。
(2)剪裁ﻫ按制品得结构形状,加料位置,流程决定片材剪裁得形状与尺寸,制作样板裁料、剪裁得形状多为方形或圆形,尺寸多按制品表面投影面积得40%-80%。
为防止外界杂质得污染,上下薄膜在装料前才揭去。
(3)设备得准备①熟悉压机得各项操作参数,尤其要调整好工作压力与压机运行速度及台面平行度等。
②模具安装一定要水平,并确保安装位置在压机台面得中心,压制前要先彻底清理模具,并涂脱模剂。
加料前要用干净纱布将脱模剂擦均,以免影响制品外观质量。
对于新模具,用前必须去油。
2、加料ﻫ(1)加料量得确定ﻫ每个制品得加料量在首次压制时可按下式计算:加料量=制品体积×1、8ﻫ(2) 加料面积得确定ﻫ加料面积得大小,直接影响到制品得密度程度料得流动距离与制品表面质量。
它与SMC 得流动与固化特性、制品性能要求、模具结构等有关、一般加料面积为40%-80%。
过小会因流程过长而导致玻纤取向,降低强度,增加波纹度,甚至不能充满模腔;过大,不利于排气,易产生制品内裂纹、ﻫ(3)加料位置与方式加料位置与方式直接影响到制品得外观,强度与方向性。
通常情况下,料得加料位置应在模腔得中部。
对于非对称复杂制品,加料位置必须确保成型时料流同时达到模具成型内腔各端部。
ﻫ加料方式必须有利于排气。
多层片材叠合时,最好将料块按上小下大呈宝塔形叠置、另外,料块尽量不要分开加,否则会产生空气裹集与熔接区,导致制品强度下降。
ﻫ(4) 其她ﻫ在加料前,为增加片材得流动性,可采用100℃或120℃下预热操作。
这一点对成型深拉形制品尤其有利、3、成型当料块进入模腔后,压机快速下行、当上、下模吻合时,缓慢施加所需成型压力,经过一定得固化制度后,制品成型结束。
模压工艺生产操作-成型工艺
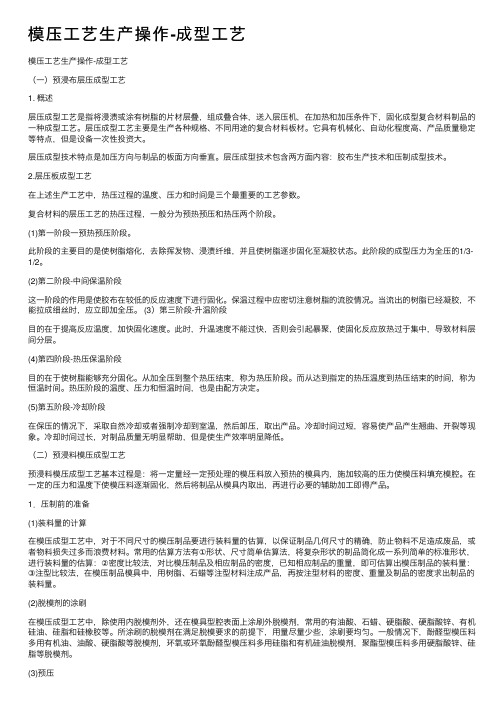
模压⼯艺⽣产操作-成型⼯艺模压⼯艺⽣产操作-成型⼯艺(⼀)预浸布层压成型⼯艺1. 概述层压成型⼯艺是指将浸渍或涂有树脂的⽚材层叠,组成叠合体,送⼊层压机,在加热和加压条件下,固化成型复合材料制品的⼀种成型⼯艺。
层压成型⼯艺主要是⽣产各种规格、不同⽤途的复合材料板材。
它具有机械化、⾃动化程度⾼、产品质量稳定等特点,但是设备⼀次性投资⼤。
层压成型技术特点是加压⽅向与制品的板⾯⽅向垂直。
层压成型技术包含两⽅⾯内容:胶布⽣产技术和压制成型技术。
2.层压板成型⼯艺在上述⽣产⼯艺中,热压过程的温度、压⼒和时间是三个最重要的⼯艺参数。
复合材料的层压⼯艺的热压过程,⼀般分为预热预压和热压两个阶段。
(1)第⼀阶段⼀预热预压阶段。
此阶段的主要⽬的是使树脂熔化,去除挥发物、浸渍纤维,并且使树脂逐步固化⾄凝胶状态。
此阶段的成型压⼒为全压的1/3-1/2。
(2)第⼆阶段-中间保温阶段这⼀阶段的作⽤是使胶布在较低的反应速度下进⾏固化。
保温过程中应密切注意树脂的流胶情况。
当流出的树脂已经凝胶,不能拉成细丝时,应⽴即加全压。
(3)第三阶段-升温阶段⽬的在于提⾼反应温度,加快固化速度。
此时,升温速度不能过快,否则会引起暴聚,使固化反应放热过于集中,导致材料层间分层。
(4)第四阶段-热压保温阶段⽬的在于使树脂能够充分固化。
从加全压到整个热压结束,称为热压阶段。
⽽从达到指定的热压温度到热压结束的时间,称为恒温时间。
热压阶段的温度、压⼒和恒温时间,也是由配⽅决定。
(5)第五阶段-冷却阶段在保压的情况下,采取⾃然冷却或者强制冷却到室温,然后卸压,取出产品。
冷却时间过短,容易使产品产⽣翘曲、开裂等现象。
冷却时间过长,对制品质量⽆明显帮助,但是使⽣产效率明显降低。
(⼆)预浸料模压成型⼯艺预浸料模压成型⼯艺基本过程是:将⼀定量经⼀定预处理的模压料放⼊预热的模具内,施加较⾼的压⼒使模压料填充模腔。
在⼀定的压⼒和温度下使模压料逐渐固化,然后将制品从模具内取出,再进⾏必要的辅助加⼯即得产品。
SMC模压成型工艺过程
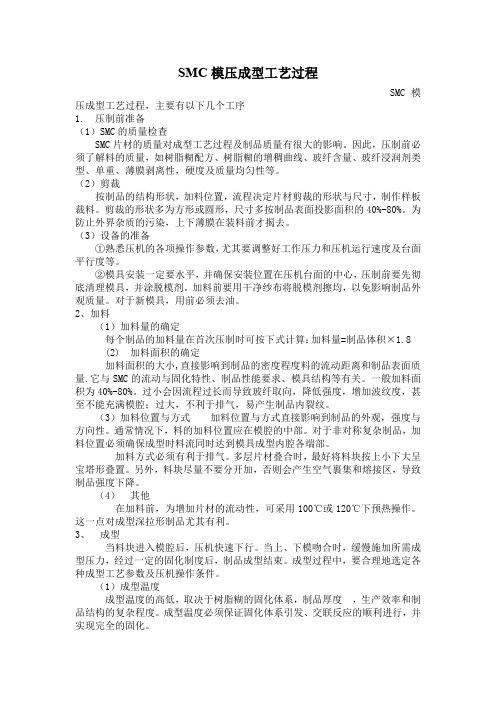
SMC模压成型工艺过程SMC模压成型工艺过程,主要有以下几个工序1. 压制前准备(1)SMC的质量检查SMC片材的质量对成型工艺过程及制品质量有很大的影响。
因此,压制前必须了解料的质量,如树脂糊配方、树脂糊的增稠曲线、玻纤含量、玻纤浸润剂类型、单重、薄膜剥离性,硬度及质量均匀性等。
(2)剪裁按制品的结构形状,加料位置,流程决定片材剪裁的形状与尺寸,制作样板裁料。
剪裁的形状多为方形或圆形,尺寸多按制品表面投影面积的40%-80%。
为防止外界杂质的污染,上下薄膜在装料前才揭去。
(3)设备的准备①熟悉压机的各项操作参数,尤其要调整好工作压力和压机运行速度及台面平行度等。
②模具安装一定要水平,并确保安装位置在压机台面的中心,压制前要先彻底清理模具,并涂脱模剂。
加料前要用干净纱布将脱模剂擦均,以免影响制品外观质量。
对于新模具,用前必须去油。
2、加料(1)加料量的确定每个制品的加料量在首次压制时可按下式计算:加料量=制品体积×1.8(2) 加料面积的确定加料面积的大小,直接影响到制品的密度程度料的流动距离和制品表面质量.它与SMC的流动与固化特性、制品性能要求、模具结构等有关。
一般加料面积为40%-80%。
过小会因流程过长而导致玻纤取向,降低强度,增加波纹度,甚至不能充满模腔;过大,不利于排气,易产生制品内裂纹。
(3)加料位置与方式加料位置与方式直接影响到制品的外观,强度与方向性。
通常情况下,料的加料位置应在模腔的中部。
对于非对称复杂制品,加料位置必须确保成型时料流同时达到模具成型内腔各端部。
加料方式必须有利于排气。
多层片材叠合时,最好将料块按上小下大呈宝塔形叠置。
另外,料块尽量不要分开加,否则会产生空气裹集和熔接区,导致制品强度下降。
(4)其他在加料前,为增加片材的流动性,可采用100℃或120℃下预热操作。
这一点对成型深拉形制品尤其有利。
3、成型当料块进入模腔后,压机快速下行。
当上、下模吻合时,缓慢施加所需成型压力,经过一定的固化制度后,制品成型结束。
SMC模压成型工艺过程1

教学设计 授课学科:模压成型工艺授课班级: 授课教师: 授课章节:第四章 授课类型:新授课 学时安排:2学时授课题目:SMC 模压成型工艺过程教学目的:SMC 模压成型工艺过程的主要工序教学重点:SMC 模压成型工艺过程,主要有几个工序教学难点:SMC 的质量检查教学方法:讲练结合教学准备:课件设计思路:教 学 过 程设计思路及时间分配课前探究:导入新课:教学内容:SMC 模压成型工艺过程,主要有以下几个工序1. 压制前准备(1)SMC 的质量检查SMC 片材的质量对成型工艺过程及制品质量有很大的影响。
因此,压制前必须了解料的质量,如树脂糊配方、树脂糊的增稠曲线、玻纤含量、玻纤浸润剂类型、单重、薄膜剥离性,硬度及质量均匀性等。
(2)剪裁按制品的结构形状,加料位置,流程决定片材剪裁的形状与尺寸,制作样板裁料。
剪裁的形状多为方形或圆形,尺寸多按制品表面投影面积的40%-80%。
为防止外界杂质的污染,上下薄膜在装料前才揭去。
(3)设备的准备①熟悉压机的各项操作参数,尤其要调整好工作压力和压机运行速度及台面平行度等。
②模具安装一定要水平,并确保安装位置在压机台面的中心,压制前要先彻底清理模具,并涂脱模剂。
加料前要用干净纱布将脱模剂擦均,以免影响制品外观质量。
对于新模具,用前必须去油。
2、加料(1)加料量的确定每个制品的加料量在首次压制时可按下式计算:加料量=制品体积×1.8(2)加料面积的确定加料面积的大小,直接影响到制品的密度程度料的流动距离和制品表面质量.它与SMC的流动与固化特性、制品性能要求、模具结构等有关。
一般加料面积为40%-80%。
过小会因流程过长而导致玻纤取向,降低强度,增加波纹度,甚至不能充满模腔;过大,不利于排气,易产生制品内裂纹。
(3)加料位置与方式加料位置与方式直接影响到制品的外观,强度与方向性。
通常情况下,料的加料位置应在模腔的中部。
对于非对称复杂制品,加料位置必须确保成型时料流同时达到模具成型内腔各端部。
SMC模压成型工艺流程

SMC模压成型工艺流程SMC模压成型工艺是一种常用于复合材料制造的工艺方法,其原理是将预先混合好的Sheet Molding Compound(SMC)料在模具中进行加热压缩,使其固化成型成为最终产品。
SMC模压成型工艺具有成型速度快、制品质量高、生产效率高等优点,因此在汽车、航空航天、建筑等领域得到广泛应用。
在SMC模压成型工艺中,首先需要准备好SMC料,SMC料是由树脂、增强纤维、填料等原料混合制得的预浸料,具有一定的流动性和可成型性。
接着,将准备好的SMC 料铺放在模具的一侧,然后关闭模具,通过加热和压缩的方式对SMC料进行固化成型。
在这个过程中,加热可以使树脂固化,压缩则能够使SMC料充分填充模具的每个角落,确保最终产品的质量。
SMC模压成型工艺一般包括以下几个主要步骤:1.准备工作:在进行SMC模压成型之前,需要准备好所需的原材料,包括树脂、增强纤维、填料等。
同时,需要清洁和涂抹模具,确保模具表面光滑干净,以便产品成型时表面光洁平整。
2.SMC料铺放:将预先混合好的SMC料铺放在模具的一侧,要求均匀、密实。
在铺放SMC料时,需要根据产品的结构和要求进行合理的叠放和布置,以确保最终产品的强度和外形要求。
3.模具封闭:将装有SMC料的模具封闭好,确保模具的密封性以及加热和压缩系统的正常工作。
模具封闭后,即可进行下一步操作。
4.加热压缩:启动加热系统和压缩系统,对SMC料进行加热和加压处理。
加热系统会使SMC料中的树脂在一定温度下固化,压缩系统则会通过一定的压力使SMC料充分填充模具,并使其成型固化。
5.冷却固化:经过一定时间的加热和压缩后,关闭加热系统和压缩系统,让模具中的产品自然冷却,直至完成固化。
在这个过程中,冷却速度和固化时间的控制非常重要,影响着产品的质量和性能。
6.脱模和修整:等产品完全固化后,打开模具,将成型好的产品从模具中取出,进行必要的修整和处理。
包括修边、打磨、去毛刺等工序,以确保产品表面光滑平整,符合设计要求。
SMCBMC模压成型工艺控制三要素下

SMCBMC模压成型工艺控制三要素下
首先,温度控制是SMCBMC模压成型工艺中的首要要素之一、在模压成型过程中,树脂的熔融温度应适宜,过低的温度会导致树脂无法充分熔融,影响产品的密实性和质量,而过高的温度则可能引起熔体的分解或炭化。
因此,通过对模具和加热系统的温度控制,确保树脂在适宜的温度下熔融并充分流动,是保证模压成型产品质量的关键。
其次,时间控制也是SMCBMC模压成型工艺中不可忽视的一环。
时间包括两个方面,一是树脂熔融和填充时间,二是冷却和固化时间。
树脂的熔融和填充时间应足够,以确保熔融的树脂能充分填充模具空腔,避免产生气泡等缺陷。
而冷却和固化时间则应根据具体的树脂种类和产品要求来确定,确保树脂能够在模具中完全固化,以获得良好的产品性能。
最后,压力控制也是SMCBMC模压成型工艺中需要重视的一个要素。
在成型过程中,适当的压力可以促使树脂充分填充模具空腔,并保证产品的致密性和尺寸精度。
过高或过低的压力都会影响产品的质量,因此需要通过良好的控制技术来确保压力的准确掌握和传递。
除了上述三个基本要素外,还需要注重其他影响因素的控制,例如定型剂的添加量、模具的设计和制造等。
同时,SMCBMC模压成型工艺还需要进行相应的工艺参数优化和过程监控,以确保产品的质量稳定性和一致性。
综上所述,SMCBMC模压成型工艺的控制三要素包括温度控制、时间控制和压力控制。
通过合理的控制和调整,可以获得高质量的模压成型产品。
热压成型工艺参数对材料成型质量的影响分析

热压成型工艺参数对材料成型质量的影响分析热压成型是一种常见的金属加工工艺,通过在高温和高压下对金属材料进行塑性变形,从而获得具有一定形状和性能的零件。
在热压成型过程中,工艺参数的选择对成型质量有着重要的影响。
本文将从温度、压力和保温时间三个方面探讨热压成型工艺参数对材料成型质量的影响。
首先,温度是热压成型过程中最重要的工艺参数之一。
温度的选择直接影响到材料的塑性变形能力和形状保持能力。
一般来说,较高的温度有利于材料的塑性变形,使得材料更容易填充模具的空腔,从而获得较高的成型质量。
然而,过高的温度可能导致材料的烧结和晶粒长大,从而影响材料的力学性能。
因此,在选择温度时需要综合考虑材料的熔点、烧结温度和所需的力学性能。
其次,压力是热压成型中另一个重要的工艺参数。
压力的大小直接决定了材料的填充程度和成型密度。
较高的压力可以有效地排除材料中的气孔和夹杂物,提高材料的密实性和强度。
此外,适当的压力还可以改善材料的表面质量,减少成型过程中的缺陷和变形。
然而,过高的压力可能导致模具磨损和能耗增加,同时也会增加设备的投资成本。
因此,在选择压力时需要综合考虑成型质量和经济效益。
最后,保温时间是热压成型中的另一个关键参数。
保温时间的长短直接影响到材料的烧结程度和晶粒尺寸。
较长的保温时间有利于材料的烧结和晶粒长大,从而提高材料的力学性能和耐磨性。
然而,过长的保温时间会增加成本和生产周期,同时也可能导致材料的过烧和晶粒粗化。
因此,在选择保温时间时需要综合考虑材料的烧结性能和生产效率。
综上所述,热压成型工艺参数对材料成型质量有着重要的影响。
温度的选择影响材料的塑性变形能力和形状保持能力,压力的选择影响材料的填充程度和成型密度,保温时间的选择影响材料的烧结程度和晶粒尺寸。
在实际生产中,需要根据材料的特性和成型要求综合考虑这些工艺参数,以获得最佳的成型质量和经济效益。
值得注意的是,热压成型工艺参数的选择并非一成不变,而是需要根据具体情况进行调整和优化。
SMC成型工艺分析报告

4.3.2 SMC的组分及其性能
SMC的组分及其性能
树脂糊
增强纤维
UP树脂
引发剂
交联剂
增稠剂
脱模剂
低收缩添加剂
无机填料
SMC
4.3.2 SMC的组分及其性能
1.不饱和聚脂树脂(Up树脂)
1、低粘度;便于浸渍GF。2、易同增稠剂反应;满足增稠的要求。3、可降低收缩性;4、固化迅速,提高生产效率;5、应具有较高的热强度和一定的韧性;在制品脱模时,不易损坏或开裂。
9、静夜四无邻,荒居旧业贫。。10、雨中黄叶树,灯下白头人。。11、以我独沈久,愧君相见频。。12、故人江海别,几度隔山川。。13、乍见翻疑梦,相悲各问年。。14、他乡生白发,旧国见青山。。15、比不了得就不比,得不到的就不要。。。16、行动出成果,工作出财富。。17、做前,能够环视四周;做时,你只能或者最好沿着以脚为起点的射线向前。。9、没有失败,只有暂时停止成功!。10、很多事情努力了未必有结果,但是不努力却什么改变也没有。。11、成功就是日复一日那一点点小小努力的积累。。12、世间成事,不求其绝对圆满,留一份不足,可得无限完美。。13、不知香积寺,数里入云峰。。14、意志坚强的人能把世界放在手中像泥块一样任意揉捏。15、楚塞三湘接,荆门九派通。。。16、少年十五二十时,步行夺得胡马骑。。17、空山新雨后,天气晚来秋。。9、杨柳散和风,青山澹吾虑。。10、阅读一切好书如同和过去最杰出的人谈话。11、越是没有本领的就越加自命不凡。12、越是无能的人,越喜欢挑剔别人的错儿。13、知人者智,自知者明。胜人者有力,自胜者强。14、意志坚强的人能把世界放在手中像泥块一样任意揉捏。15、最具挑战性的挑战莫过于提升自我。。16、业余生活要有意义,不要越轨。17、一个人即使已登上顶峰,也仍要自强不息。
模压成型参数是什么

模压成型参数是什么模压成型是一种常见的制造工艺,广泛应用于塑料制品、橡胶制品等行业。
在模压过程中,模压成型参数的设置对产品质量和生产效率有着至关重要的影响。
了解和控制模压成型参数是确保产品质量稳定的关键之一。
1. 温度参数在模压成型过程中,温度是一个至关重要的参数。
通常需要控制模具、熔料以及模压设备的温度。
模具温度的控制直接影响着产品的表面质量和尺寸精度,过高或过低的温度都可能导致产品质量不稳定。
熔料的温度对于填充性能和产品密度也有很大影响。
因此,在模压成型过程中,需要根据材料的特性和产品的要求,合理设置和控制温度参数。
2. 压力参数压力是模压成型过程中另一个重要的参数。
在模压过程中,需要施加一定的压力使熔料充分填充模具腔,同时确保产品的密实度和表面质量。
过高或过低的压力都会导致产品出现缺陷,例如气泡、翘曲等。
因此,合理设置和控制模压过程中的压力是确保产品质量的关键。
3. 时间参数时间也是模压成型过程中需要关注的参数之一。
包括注塑时间、保压时间、冷却时间等。
注塑时间影响着塑料充填模具的速度和充填性能,过长或过短都可能导致产品的缺陷。
保压时间则影响产品的密实度和尺寸稳定性。
冷却时间则直接决定了产品成型周期和产品脱模后的温度分布。
因此,合理设置和控制时间参数对于生产稳定性至关重要。
4. 其他参数除了上述的主要参数外,模具结构、注射速度、定位精度等都是模压成型过程中需要考虑和控制的参数。
合理设计模具结构能够提高产品质量和生产效率,确定合适的注射速度可以提高生产速度和充填性能,精准的定位可以保证产品尺寸的一致性。
综上所述,模压成型参数的设置对于产品质量和生产效率有着直接的影响。
只有合理设置和控制这些参数,才能够保证模压产品的质量稳定、生产效率高效。
因此,在实际生产中,需要根据具体的材料、产品和设备状况,合理调整模压成型参数,不断优化生产过程,提高产品质量和生产效率。
成型工艺参数对材料表面质量的影响研究
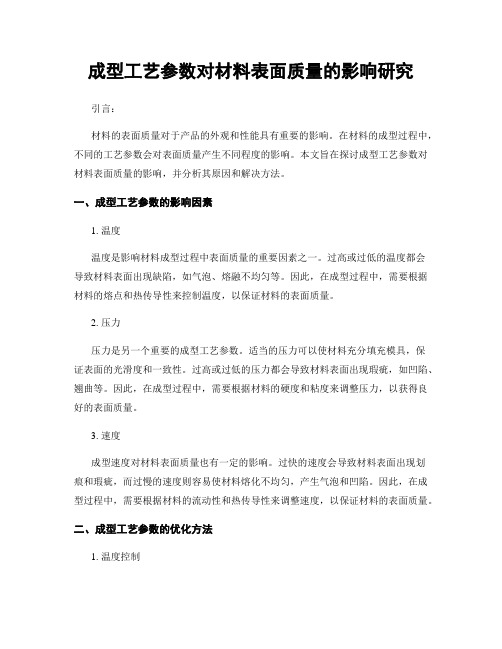
成型工艺参数对材料表面质量的影响研究引言:材料的表面质量对于产品的外观和性能具有重要的影响。
在材料的成型过程中,不同的工艺参数会对表面质量产生不同程度的影响。
本文旨在探讨成型工艺参数对材料表面质量的影响,并分析其原因和解决方法。
一、成型工艺参数的影响因素1. 温度温度是影响材料成型过程中表面质量的重要因素之一。
过高或过低的温度都会导致材料表面出现缺陷,如气泡、熔融不均匀等。
因此,在成型过程中,需要根据材料的熔点和热传导性来控制温度,以保证材料的表面质量。
2. 压力压力是另一个重要的成型工艺参数。
适当的压力可以使材料充分填充模具,保证表面的光滑度和一致性。
过高或过低的压力都会导致材料表面出现瑕疵,如凹陷、翘曲等。
因此,在成型过程中,需要根据材料的硬度和粘度来调整压力,以获得良好的表面质量。
3. 速度成型速度对材料表面质量也有一定的影响。
过快的速度会导致材料表面出现划痕和瑕疵,而过慢的速度则容易使材料熔化不均匀,产生气泡和凹陷。
因此,在成型过程中,需要根据材料的流动性和热传导性来调整速度,以保证材料的表面质量。
二、成型工艺参数的优化方法1. 温度控制通过控制加热器的温度和冷却器的温度,可以实现对材料温度的精确控制。
此外,还可以采用预热和后冷却的方式,使材料在成型过程中温度变化更加均匀,从而提高表面质量。
2. 压力控制通过调整液压系统的压力和流量,可以实现对成型过程中压力的精确控制。
此外,还可以采用多级压力和快速压力释放的方式,使材料在填充模具过程中压力分布更加均匀,从而提高表面质量。
3. 速度控制通过调整液压系统的流量和速度,可以实现对成型过程中速度的精确控制。
此外,还可以采用加速和减速的方式,使材料在填充模具和冷却过程中速度变化更加平稳,从而提高表面质量。
三、成型工艺参数的实验研究为了验证成型工艺参数对材料表面质量的影响,进行了一系列实验研究。
选取了不同的温度、压力和速度参数,并通过显微镜和表面粗糙度仪等测试设备对材料的表面质量进行了评估。
SMC复合材料及其SMC模压说明

SMC复合材料及其SMC模压说明SMC复合材料及其SMC模压制品,具有优异的电绝缘性能、机械性能、热稳定性、耐化学防腐性。
所以SMC制品的应用范围相当广泛,主要有以下应用领域:1、电气工业的应用。
2、汽车工业中的应用。
3、铁路车辆中的应用。
4、通讯工程中的应用。
5、防爆电器设备外壳的应用等等。
成型工艺由低收缩添加剂(LPA)的作用机理可知,LPA与UP固化网络的相分离和微孔的形成是低收缩添加剂能降低聚酯树脂固化收缩的关键。
许多研究资料表明,收缩控制的相分离和微孔均与工艺条件如成型温度、成型压力等有关。
正确的控制模压工艺参数可以降低收缩率,有效地改善制品的表面质量,达到A级表面。
成型温度SMC的成型温度主要取决于树脂和固化剂类型。
如果模温过高,熔融物反应快,固化快,不易流动,使压力失效,造成制品尺寸欠缺;如果模温太低,固化不完全,达不到理想的性能;如果温度不均匀,也会造成制品局部缺陷。
为了使SMC制品内表面光滑平洁,要求上、下模要有一定温差,一般使上模温度比下模高5~10℃。
模具控温通常使用导热油电加热器,其温度控制精度可达到±1℃。
经济上允许的话,上模和下模可以分开用两台导热油电加热器来控制,维持上下模之间温差在5~10℃。
SMC的收缩主要由两部分组成:一是由固化反应收缩引起的体积减小,另一是由温度降低引起的热收缩。
根据LPA热膨胀理论,模压温度越高则LPA占有的初始体积就越大,抵消收缩的能力也就越强。
因而升高温度就存在两种相互矛盾的影响:一方面引起热收缩的增加,另一方面引起抵消收缩能力的增强。
但是大量实验表明,热收缩占主导地位,随着温度的升高,制品表现出收缩率增加的趋势。
因此,应当在能够保证固化体系引发、交联反应的顺利进行和实现完全固化的前提下,使用较低的成型温度,以利于降低收缩率,得到表面质量。
成型压力成型压力的大小应根据制品形状及所用SMC的特性决定。
片状模塑料的增稠程度越高,所需的成型压力越大;流动性越差、加料面积越小所需的成型压力也越大。
SMC模压常见缺陷、原因与解决方法

SMC模压常见缺陷、原因与解决方法一、气泡和空洞缺陷描述:在SMC模压成型后,产品内部或表面出现不规则的气泡或空洞。
原因分析:原料混合不均匀,存在空气囊。
模压过程中排气不充分,导致气体被困。
模压温度过高或过低,影响气体排出。
解决方法:加强原料混合工艺,确保物料均匀无气泡。
优化模具设计,增加排气孔和排气槽,提高排气效率。
调整模压温度,确保在合适的温度范围内进行模压。
二、翘曲变形缺陷描述:SMC模压件在成型后出现形状改变,不符合设计要求。
原因分析:模压过程中温度分布不均匀,导致产品局部收缩不一致。
模具设计不合理,未能完全限制产品变形。
材料性能差异,如收缩率不同。
解决方法:改善模压工艺,确保模腔内温度分布均匀。
优化模具结构,增加支撑和限位装置,减少变形。
选用性能稳定、收缩率一致的原材料。
三、表面瑕疵缺陷描述:SMC模压件表面出现裂纹、划痕、凹坑等缺陷。
原因分析:模具表面不光洁,存在磨损或异物。
脱模过程中操作不当,导致产品损伤。
原材料含有杂质或颗粒过大。
解决方法:定期对模具进行维护和保养,保持其表面光滑清洁。
改进脱模工艺,使用专用脱模剂,避免划伤产品。
严格控制原材料质量,去除杂质和过大颗粒。
四、强度不足缺陷描述:SMC模压件在使用过程中表现出较低的机械强度,易发生断裂或变形。
原因分析:原材料配比不当,影响产品性能。
模压压力不足或时间过长,导致产品内部结构疏松。
产品固化不充分,未能达到设计强度。
解决方法:调整原材料配比,确保各组分含量符合设计要求。
优化模压工艺参数,提高模压压力和缩短模压时间。
延长固化时间或提高固化温度,确保产品充分固化。
综上所述,针对SMC模压常见的气泡和空洞、翘曲变形、表面瑕疵以及强度不足等缺陷,可以通过调整原材料、优化模具设计、改进工艺参数和加强质量控制等方法来有效解决。
在实际生产过程中,应根据具体情况采取相应措施,以提高产品质量和降低成本。
SMC成型工艺
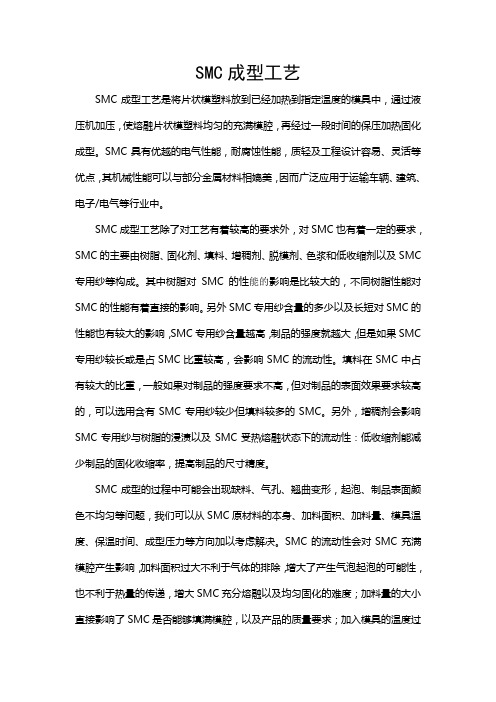
SMC成型工艺SMC成型工艺是将片状模塑料放到已经加热到指定温度的模具中,通过液压机加压,使熔融片状模塑料均匀的充满模腔,再经过一段时间的保压加热固化成型。
SMC具有优越的电气性能,耐腐蚀性能,质轻及工程设计容易、灵活等优点,其机械性能可以与部分金属材料相媲美,因而广泛应用于运输车辆、建筑、电子/电气等行业中。
SMC成型工艺除了对工艺有着较高的要求外,对SMC也有着一定的要求,SMC的主要由树脂、固化剂、填料、增稠剂、脱模剂、色浆和低收缩剂以及SMC 专用纱等构成。
其中树脂对SMC的性能的影响是比较大的,不同树脂性能对SMC的性能有着直接的影响。
另外SMC专用纱含量的多少以及长短对SMC的性能也有较大的影响,SMC专用纱含量越高,制品的强度就越大,但是如果SMC 专用纱较长或是占SMC比重较高,会影响SMC的流动性。
填料在SMC中占有较大的比重,一般如果对制品的强度要求不高,但对制品的表面效果要求较高的,可以选用含有SMC专用纱较少但填料较多的SMC。
另外,增稠剂会影响SMC专用纱与树脂的浸渍以及SMC受热熔融状态下的流动性:低收缩剂能减少制品的固化收缩率,提高制品的尺寸精度。
SMC成型的过程中可能会出现缺料、气孔、翘曲变形,起泡、制品表面颜色不均匀等问题,我们可以从SMC原材料的本身、加料面积、加料量、模具温度、保温时间、成型压力等方向加以考虑解决。
SMC的流动性会对SMC充满模腔产生影响,加料面积过大不利于气体的排除,增大了产生气泡起泡的可能性,也不利于热量的传递,增大SMC充分熔融以及均匀固化的难度;加料量的大小直接影响了SMC是否能够填满模腔,以及产品的质量要求;加入模具的温度过高,加压过快,会使SMC表面快速固化,不利于热量的传递,中间部位不能充分熔融,使SMC不能够充满模腔,并且由于表面固化太快,SMC中裹有的气体不易排出,那么容易在制品表面形成气孔和起泡;保温时间过短不利于制品的充分固化;成型压力过小,不利于增加制品的密实性以及降低制品的收缩率,从而可能会制品翘曲变形。
SMC模压成型工艺参数对成型质量的影响
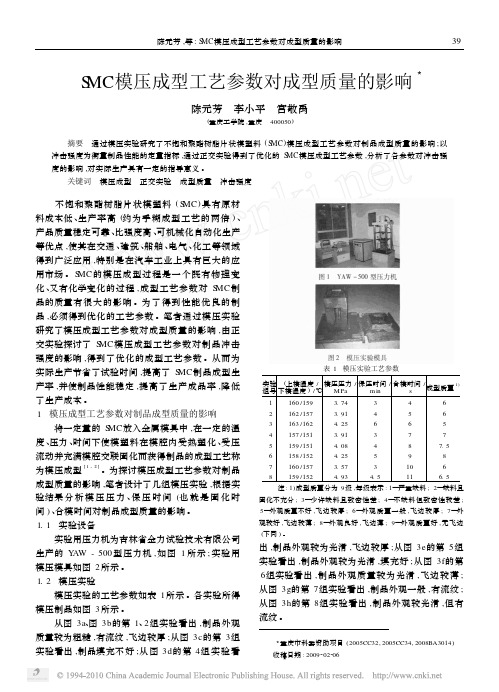
表 1 模压实验工艺参数
实验 (上模温度 / 模压压力 组号 下模温度 ) / ℃ MPa
/
保压时间 m in
/
合模时间 s
/成型质量 1)
1 160 /159
3. 74
3
4
6
2 162 /157
3. 91
4
5
6
3 163 /162
4. 25
6
6
5
4 157 /151
3. 91
3
7
7
5 159 /151
不饱和聚酯树脂 SMC模压成型过程中 ,影响制 品成型质量及性能的因素主要是模压温度 、保压时 间 、合模时间 。因此 ,在设计正交表时 ,以这几个参 数为影响因素 ,于是模压成型工艺实验的正交表为 L9 ( 34 ) 。
陈元芳 ,等 : SMC模压成型工艺参数对成型质量的影响
41
2. 2 冲击强度的正交实验 冲击实验参照 GB / T 1451 - 1983; 冲击实验机
观较好 ,飞边较薄 ; 8—外观良好 ,飞边薄 ; 9—外观质量好 ,无飞边
(下同 ) 。
出 ,制品外观较为光滑 ,飞边较厚 ;从图 3e的第 5组
实验看出 ,制品外观较为光滑 ,填充好 ;从图 3f的第
6组实验看出 ,制品外观质量较为光滑 ,飞边较薄 ;
从图 3g的第 7组实验看出 ,制品外观一般 ,有流纹 ;
陈元芳 ,等 : SMC模压成型工艺参数对成型质量的影响
39
SMC模压成型工艺参数对成型质量的影响 3
陈元芳 李小平 宫敬禹
(重庆工学院 ,重庆 400050)
摘要 通过模压实验研究了不饱和聚酯树脂片状模塑料 ( SMC)模压成型工艺参数对制品成型质量的影响 ;以 冲击强度为衡量制品性能的定量指标 ,通过正交实验得到了优化的 SMC模压成型工艺参数 ,分析了各参数对冲击强 度的影响 ,对实际生产具有一定的指导意义 。
SMC模压工艺中常见质量问题分析及对策

SMC模压工艺中常见质量问题分析及对策SMC材料模压工艺是玻璃钢/复合材料成型工艺中生产效率最高的一种。
SMC模压工艺有很多优点,例如:制品尺寸准确、表面光洁、制品外观及尺寸重复性好、复杂结构也可一次成型、二次加工无需损伤制品等。
但在SMC模压生产过程中也会出现不良缺陷现象,主要表现在以下几个方面:问题一:缺料缺料是指SMC模压成型件没完全充满,其产生部位多集中在SMC制品的边缘,尤其是边角的根部和顶部。
原因分析:1、放料量少;2、SMC材料流动性差;3、设备压力不充足;4、固化太快。
产生机理及对策:1、SMC材料受热塑化后,熔融粘度大,在交联固化反应完成前,没有足够的时间、压力、和体积使融体充满模腔。
2、SMC模压料存放时间过长,苯乙烯挥发过多,造成SMC模压料的流动性能明显降低。
3、树脂糊未浸透纤维。
成型时树脂糊不能带动纤维流动而造成缺料。
由上述原因所引起的缺料,最直接的解决方法是切料时剔除这些模压料。
4、加料量不足引起缺料。
解决方法是适当增大加料量。
5、模压料中裹有过多的空气及大量挥发物。
解决方法有:适当增加排气次数;适当加大加料面积,隔一定时间清理模具;适当增大成型压力。
6、加压过迟,模压料在充满模腔前已完成交联固化。
7、模温过高,交联固化反应提前,应适当降温。
问题二:气孔产品表面上有规则或不规则的小孔,其产生部位多在产品顶端和中间薄壁处。
产生机理及对策:1、SMC模压料中裹有大量空气以及挥发物含量大,排气不畅;SMC料的增稠效果不佳,不能有效赶出气体。
对于上述引起原因,可通过增加排气次数以及清理模具相结合的方法而得到有效的控制。
2、加料面积过大,适当减少加料面积可得到控制。
在实际操作过程中,人为因素也有可能造成砂眼。
比如加压过早,有可能使模压料裹有的气体不易排出,造成制品表面出现气孔的表面缺陷。
问题三:翘曲变形产生的主要原因是模压料固化不均匀和脱模后产品的收缩。
产生机理及对策:在树脂固化反应过程中化学结构发生变化,引起体积收缩,固化的不均匀使得产品有向首先固化的一侧翘曲的趋势。
塑料成型工艺参数对产品质量的影响实验心得

塑料成型工艺参数对产品质量的影响实验心得
1. 温度:温度是塑料成型的重要参数,对产品的物理性能、表面质量以及尺寸稳定性都有影响。
如果温度过高,可能导致材料熔化不均匀,产生气泡或烧焦的现象;如果温度过低,则可能导致成型件不完整或收缩不足。
因此,合适的温度范围对于保证产品质量非常重要。
2. 压力:压力是保证塑料充填和充实的重要参数。
适当的压力可以确保塑料在模具中充填均匀,并充实到预定的位置,避免产生缩孔和其他缺陷。
不同的成型工艺有不同的压力要求,需要进行适当的调整。
3. 时间:成型时间直接影响到产品形状的准确性和尺寸的稳定性。
过长或过短的时间都可能导致产品质量不稳定、尺寸变化或翘曲等问题。
因此,需要根据具体材料和产品要求来调整成型时间。
4. 冷却系统:冷却是保证产品质量的关键环节。
合理的冷却系统可以确保成型件在模具中完全固化和收缩,避免变形和内应力的产生。
因此,冷却时间和温度的控制非常重要。
总的来说,塑料成型工艺参数的调整对产品质量有重要影响。
合理调整温度、压力、时间和冷却系统,可以确保产品的物理性能、表面质量和尺寸稳定性。
在实际操作中,还需要结合具体的材料和产品要求,进行综合考虑和优化调整。
SMC模压成型工艺过程之欧阳数创编
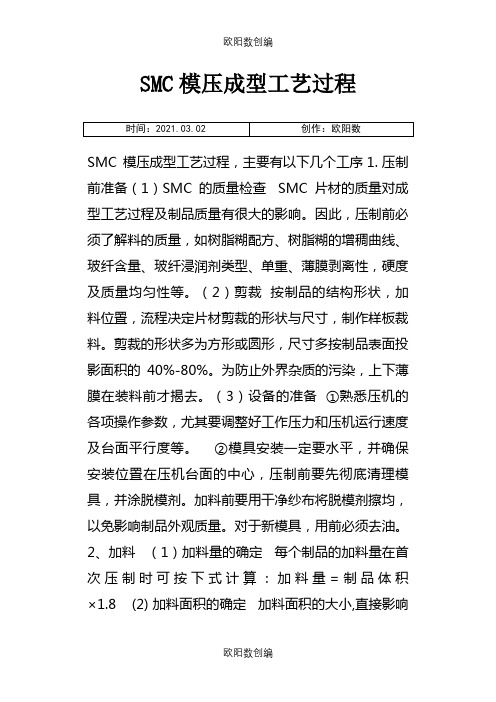
SMC模压成型工艺过程SMC模压成型工艺过程,主要有以下几个工序 1. 压制前准备(1)SMC的质量检查 SMC片材的质量对成型工艺过程及制品质量有很大的影响。
因此,压制前必须了解料的质量,如树脂糊配方、树脂糊的增稠曲线、玻纤含量、玻纤浸润剂类型、单重、薄膜剥离性,硬度及质量均匀性等。
(2)剪裁按制品的结构形状,加料位置,流程决定片材剪裁的形状与尺寸,制作样板裁料。
剪裁的形状多为方形或圆形,尺寸多按制品表面投影面积的40%-80%。
为防止外界杂质的污染,上下薄膜在装料前才揭去。
(3)设备的准备①熟悉压机的各项操作参数,尤其要调整好工作压力和压机运行速度及台面平行度等。
②模具安装一定要水平,并确保安装位置在压机台面的中心,压制前要先彻底清理模具,并涂脱模剂。
加料前要用干净纱布将脱模剂擦均,以免影响制品外观质量。
对于新模具,用前必须去油。
2、加料(1)加料量的确定每个制品的加料量在首次压制时可按下式计算:加料量=制品体积×1.8 (2) 加料面积的确定加料面积的大小,直接影响到制品的密度程度料的流动距离和制品表面质量.它与SMC的流动与固化特性、制品性能要求、模具结构等有关。
一般加料面积为40%-80%。
过小会因流程过长而导致玻纤取向,降低强度,增加波纹度,甚至不能充满模腔;过大,不利于排气,易产生制品内裂纹。
(3)加料位置与方式加料位置与方式直接影响到制品的外观,强度与方向性。
通常情况下,料的加料位置应在模腔的中部。
对于非对称复杂制品,加料位置必须确保成型时料流同时达到模具成型内腔各端部。
加料方式必须有利于排气。
多层片材叠合时,最好将料块按上小下大呈宝塔形叠置。
另外,料块尽量不要分开加,否则会产生空气裹集和熔接区,导致制品强度下降。
(4)其他在加料前,为增加片材的流动性,可采用100℃或120℃下预热操作。
这一点对成型深拉形制品尤其有利。
3、成型当料块进入模腔后,压机快速下行。
当上、下模吻合时,缓慢施加所需成型压力,经过一定的固化制度后,制品成型结束。
- 1、下载文档前请自行甄别文档内容的完整性,平台不提供额外的编辑、内容补充、找答案等附加服务。
- 2、"仅部分预览"的文档,不可在线预览部分如存在完整性等问题,可反馈申请退款(可完整预览的文档不适用该条件!)。
- 3、如文档侵犯您的权益,请联系客服反馈,我们会尽快为您处理(人工客服工作时间:9:00-18:30)。
图 4 模压压力与成型质量关系曲线
从图 4可以看出 , 随着模压压力的增加 , 成型质 量初始呈上升趋势 , 但当模压压力超过 4.25 MPa以 后 , 成型质量反而呈下降趋势 , 说明在模压成型过程 中不是模压压力越高越好 。 从图 4 还可看出 , 本实 验所用 SMC, 当模压压力为 3.91 ~ 4.25 MPa时 , 成 型质量良好 。取其平均值 4.08 MPa为宜 。
陈元芳 , 等 :SMC模压成型工艺参数对成型质量的影响
39
SMC模压成型工艺参数对成型质量的影响 *
陈元Байду номын сангаас 李小平 宫敬禹
(重庆工学院 , 重庆 400050)
摘要 通过 模压实验研究了不饱和聚酯树脂片状 模塑料 (SMC)模压成 型工艺 参数对 制品成 型质量 的影响 ;以 冲击强度为衡量制品性能 的定量指标 , 通过正交实验得到了优化的 SMC模压成型工艺参数 , 分析了各参数对 冲击强 度的影响 , 对实际生产具有一定的指导意义 。
图 5 保压时间与成型质量关系曲线
(3)合模时间对成型质量的影响 由于 SMC是一个快速固化系统 , 因此压力机的 快速闭合十分重要 。如果在加料后压力机闭合过于 迟缓 , 那么在制品表面就会出现预固化斑 , 或者产生 缺料 、尺寸过大等缺陷 。 在成型温度比较高的情况 下,更容易产生上述缺陷。另外 , 在快速闭合的同 时 , 应尽可能使被困集的空气能顺利排出 。 本实验 合模时间与成型质量的关系如图 6所示 。从图 6看 出 , 合模时间为 7 ~ 9 s时成型质量良好 。
表 2所示。
表 2 模压成型工艺 L9 (34)正交实验极差分析表
因 素
考查指标
实验号
(A)
(B)
(C) 冲击强度 /
保压时间 /min合模时间 /s模压温度 /℃ kJ· m-2
1
A1 (3.5) B1 (7) C1 (150) 69.12
2
A1 (3.5) B2 (8) C2 (155) 66.24
由图 8、图 9可以看出 , 在优化的模压工艺参数 下压制的制品表面光滑 , 填充均匀 , 飞边薄而少 , 便 于后续的处理加工 。 3 结论
(1)保压时间对制品冲击强度的影响最大 , 合 模时间的影响次之 , 模压温度的影响最小 。
(2)由正交实验得到 的 SMC模压成型优 化工 艺参数为 :模压温度 155℃, 保压时间 4 min, 合模时 间 7 s, 通过实验验证 , 该优化的工艺参数是正确的 。
观较好 , 飞边较 薄 ;8— 外观良 好 , 飞边 薄 ;9— 外 观质量 好 , 无 飞边 (下同 )。
出 , 制品外观较为光滑 , 飞边较厚 ;从图 3e的第 5组
实验看出 , 制品外观较为光滑 , 填充好 ;从图 3f的第
6组实验看出 , 制品外观质量较为光滑 , 飞边较薄 ;
从图 3g的第 7组实验看出 , 制品外观一般 , 有流纹 ;
4.25
5
9
8
7 160/157
3.57
3
10
6
8 159/152
4.93
4.5
11
6.5
注 :1)成型质量分为 9 级 , 每级表示 :1— 严重缺料 ;2— 缺料且
固化不充分 ;3— 少许缺 料且致 密性 差;4— 不 缺料但 致密性 较差 ;
5— 外观质量不好 , 飞 边较厚 ;6— 外 观质 量一般 , 飞边 较厚 ;7— 外
表 1 模压实验工艺参数
实验 组号
(上模温度 / 下模温度 )/℃
模压压力 MPa
/
保压时间 min
/
合模时间 s
/成型质量
1)
1 160/159
3.74
3
4
6
2 162/157
3.91
4
5
6
3 163/162
4.25
6
6
5
4 157/151
3.91
3
7
7
5 159/151
4.08
4
8
7.5
6 158/152
将一定量的 SMC放入金属模具中 , 在一定的温 度 、压力 、时间下使模塑料在模腔内受热塑化 、受压 流动并充满模腔交联固化而获得制品的成型工艺称 为模压成型 [ 1 -2] 。为探讨模压成型工艺参数对制品 成型质量的影响 , 笔者设计了几组模压实验 , 根据实 验结果 分析 模 压压 力 、保 压时 间 (也 就是 固 化时 间 )、合模时间对制品成型质量的影响 。 1.1 实验设备
从图 3h的第 8组实验看出 , 制品外观较光滑 , 但有
流纹 。
*重庆市科委资助项目 (2005CC32, 2005CC34, 2008BA3014) 收稿日期:2009-02-06
40
工程塑料 应用
2009年 , 第 37卷 , 第 4期
制品厚度为 6 mm, 保压时间与成型质量的关系如图 5所示 。 从图 5看出 , 随着保压时间的增加 , 成型质 量提高 , 但当保压时间达到 6 min以后成型质量开 始下降 , 保压时间为 4.5 ~ 6 min时成型质量良好 。
61.40 80.11 64.74
各因素水平 指标和的 平均值
极差 优化方案
25.21 A2
25.10 B1
18.71 最优方案为 :
C2
A2B1C2
由正交实验的极差分析可知 , 3个因素对制品 冲击强度的影响按大小顺序为 :保压时间最大 , 合模 时间次之 , 模压温度最小 。 根据正交 实验 分析结果
参考文献 [ 1] 梁国正 , 顾媛娟 .模压成 型技术 [ M] .北 京 :化 学工业 出版社 ,
1999. [ 2] 闻 荻 江 .复 合材 料 原理 [ M] .武 汉 :武汉 工 业 大 学 出版 社 ,
1998. [ 3] 刘建平 , 郑玉斌 .高分子科学与材料 工程实验 [ M] .北京 :化学
为 6 /3冲击试验机 。 试样类型为 Ⅲ型 , 其尺寸大小 为 120 mm×15 mm×10 mm, 缺口类型为 A型 。
实验用试样由试样模具按正交实验条件制备 , 如图 7所示 。
得出该实验用 SMC最佳模压工艺参数为模压温度 155℃, 保压时间 4 min, 合模时间 7 s。 2.4 实验验证
ChenYuanfang, LiXiaoping, GongJingyu (ChongqingInstituteofTechnology, Chongqing 400050, China) ABSTRACT TheeffectofformingparametersofSMConformingqualitywasresearchedbasedontheexperimentofdiepressing forming.Bythequadratureexperiment, thebestparametersofSMCdiepressingformingwasobtainedandtheinfluenceofparameters onimpactstrengthwasanalyzed.TheresultswasofvaluefordirectingtheproductionofSMCdiepressingforming. KEYWORDS diepressingforming, quadratureexperiment, formingquality, impactstrength
为了检验正交实验得出的模压工艺参数 , 笔者 按照这一组模压工艺参数做了 4组模压实验 , 制品 如图 8、图 9所示 。
图 7 冲击实验试样
2.3 正交实验结果分析
由于保压时间越长越易发生烧糊 、脆化现象 , 影
响制品成型质量 , 因此正交实验保压时间的设计取
1.3(2)中优化范围的下限 。 正交冲击实验结果如
3
A1 (3.5) B3 (9) C3 (160) 61.46
4
A2 (4)
B1 (7) C2 (155) 91.94
5
A2 (4)
B2 (8) C3 (160) 87.55
6
A2 (4)
B3 (9) C1 (150) 66.46
7
A3 (4.5) B1 (7) C3 (160) 45.20
8
A3 (4.5) B2 (8) C1 (150) 48.62
(2)保压时间对成型质量的影响 SMC在成型温度下的保压时间与 其性质及固 化体系 、成型温度 、制品厚度等因素有关 。 保压时间 一般按 40 s/mm计算 。 对于厚制品 (3 mm以上 ), 每增加 4 mm, 保压时间增加 1 min。 本模压实验的
图 6 合模时间与成型质量关系曲线
2 通过正交实验确定最佳模压工艺参数[ 3 -5] 在模压实验中 , 笔者得到了模压成型工艺的一
不饱和聚酯树脂 SMC模压成型过程中 , 影响制 品成型质量及性能的因素主要是模压温度 、保压时 间 、合模时间 。 因此 , 在设计正交表时 , 以这几个参 数为影响因素 , 于是模压成型工艺实验的正交表为 L9 (34 )。
陈元芳 , 等 :SMC模压成型工艺参数对成型质量的影响
41
2.2 冲击强度的正交实验 冲击实验参照 GB/T1451 -1983;冲击实验机
a~ h— 分别对应实验 1 ~ 8组 图 3 模压实验制品
1.3 模压实验结果分析 (1)模压压力对成型质量的影响 SMC的模压压力随树脂粘稠程度 的提高而增
加 , 流动性越差 , 加料面积越小 (即料层越厚 )所需 的模压压力也越 大 ;模压压 力还与制品的 结构 、形 状 、尺寸有关 。 形状简单的制品 , 仅需 2.5 ~ 3 MPa 的模压压力 ;形状复杂的制品 , 如带有加强筋 、深槽 结构的制品 , 模压压力可达 14 ~ 21 MPa;制品尺寸 越大 , 模压压力也相应增加 。另外 , 模压压力的大小 与模具结构有关 , 垂直分型的模具所需的模压压力 低于水平分型的模具 。本模压实验模压压力与成型 质量的关系如图 4所示 。