演讲资料:多点模具成形技术
多点成形工艺技术
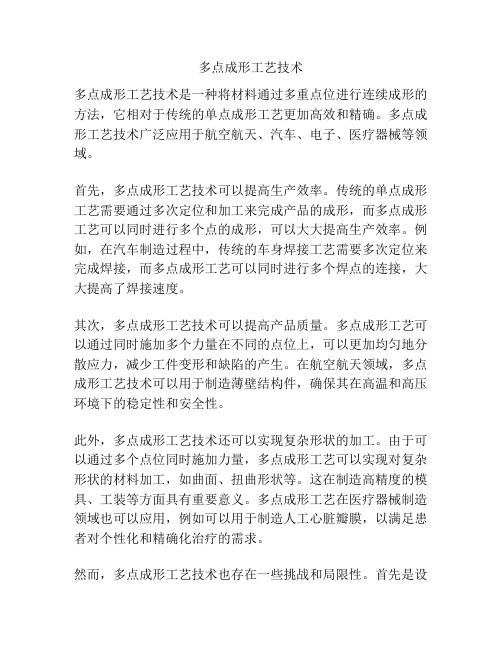
多点成形工艺技术多点成形工艺技术是一种将材料通过多重点位进行连续成形的方法,它相对于传统的单点成形工艺更加高效和精确。
多点成形工艺技术广泛应用于航空航天、汽车、电子、医疗器械等领域。
首先,多点成形工艺技术可以提高生产效率。
传统的单点成形工艺需要通过多次定位和加工来完成产品的成形,而多点成形工艺可以同时进行多个点的成形,可以大大提高生产效率。
例如,在汽车制造过程中,传统的车身焊接工艺需要多次定位来完成焊接,而多点成形工艺可以同时进行多个焊点的连接,大大提高了焊接速度。
其次,多点成形工艺技术可以提高产品质量。
多点成形工艺可以通过同时施加多个力量在不同的点位上,可以更加均匀地分散应力,减少工件变形和缺陷的产生。
在航空航天领域,多点成形工艺技术可以用于制造薄壁结构件,确保其在高温和高压环境下的稳定性和安全性。
此外,多点成形工艺技术还可以实现复杂形状的加工。
由于可以通过多个点位同时施加力量,多点成形工艺可以实现对复杂形状的材料加工,如曲面、扭曲形状等。
这在制造高精度的模具、工装等方面具有重要意义。
多点成形工艺在医疗器械制造领域也可以应用,例如可以用于制造人工心脏瓣膜,以满足患者对个性化和精确化治疗的需求。
然而,多点成形工艺技术也存在一些挑战和局限性。
首先是设备和工艺的复杂性。
多点成形工艺需要一个精密的控制系统来同时控制多个点位的加工,这对设备的制造和维护都提出了更高的要求。
其次,多点成形工艺的优势在于可以实现多点同步加工,但是对于一些较大尺寸的工件,多点成形工艺可能并不适用,因为需要很大的力量来同时加工多个点位。
综上所述,多点成形工艺技术是一种提高生产效率和产品质量的重要工艺方法。
尽管它存在一定的挑战和局限性,但其广泛的应用前景和技术的不断创新仍然使其受到了广泛的关注和研究。
未来,随着科技的不断发展和工艺技术的进步,多点成形工艺技术将进一步完善和推广,为各个领域的制造业带来更高效、精确的生产方式。
多点数字化成形技术的发展及应用
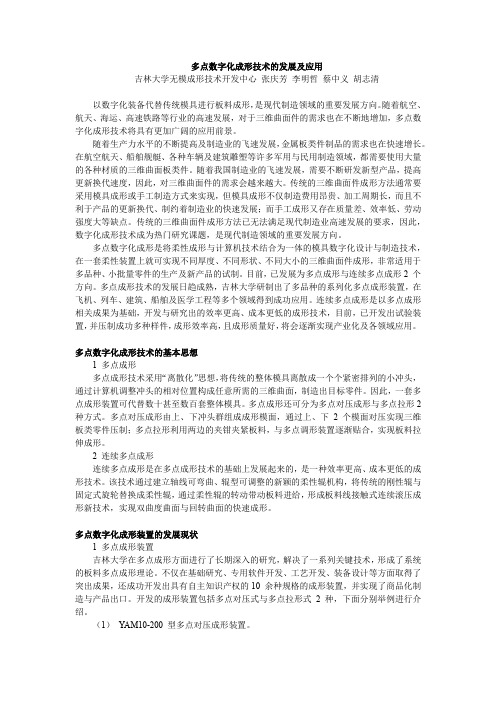
多点数字化成形技术的发展及应用吉林大学无模成形技术开发中心张庆芳李明哲蔡中义胡志清以数字化装备代替传统模具进行板料成形,是现代制造领域的重要发展方向。
随着航空、航天、海运、高速铁路等行业的高速发展,对于三维曲面件的需求也在不断地增加,多点数字化成形技术将具有更加广阔的应用前景。
随着生产力水平的不断提高及制造业的飞速发展,金属板类件制品的需求也在快速增长。
在航空航天、船舶舰艇、各种车辆及建筑雕塑等许多军用与民用制造领域,都需要使用大量的各种材质的三维曲面板类件。
随着我国制造业的飞速发展,需要不断研发新型产品,提高更新换代速度,因此,对三维曲面件的需求会越来越大。
传统的三维曲面件成形方法通常要采用模具成形或手工制造方式来实现,但模具成形不仅制造费用昂贵、加工周期长,而且不利于产品的更新换代、制约着制造业的快速发展;而手工成形又存在质量差、效率低、劳动强度大等缺点。
传统的三维曲面件成形方法已无法满足现代制造业高速发展的要求,因此,数字化成形技术成为热门研究课题,是现代制造领域的重要发展方向。
多点数字化成形是将柔性成形与计算机技术结合为一体的模具数字化设计与制造技术,在一套柔性装置上就可实现不同厚度、不同形状、不同大小的三维曲面件成形,非常适用于多品种、小批量零件的生产及新产品的试制。
目前,已发展为多点成形与连续多点成形2 个方向。
多点成形技术的发展日趋成熟,吉林大学研制出了多品种的系列化多点成形装置,在飞机、列车、建筑、船舶及医学工程等多个领域得到成功应用。
连续多点成形是以多点成形相关成果为基础,开发与研究出的效率更高、成本更低的成形技术,目前,已开发出试验装置,并压制成功多种样件,成形效率高,且成形质量好,将会逐渐实现产业化及各领域应用。
多点数字化成形技术的基本思想1 多点成形多点成形技术采用“离散化”思想,将传统的整体模具离散成一个个紧密排列的小冲头,通过计算机调整冲头的相对位置构成任意所需的三维曲面,制造出目标零件。
模具行业发言稿范文模板
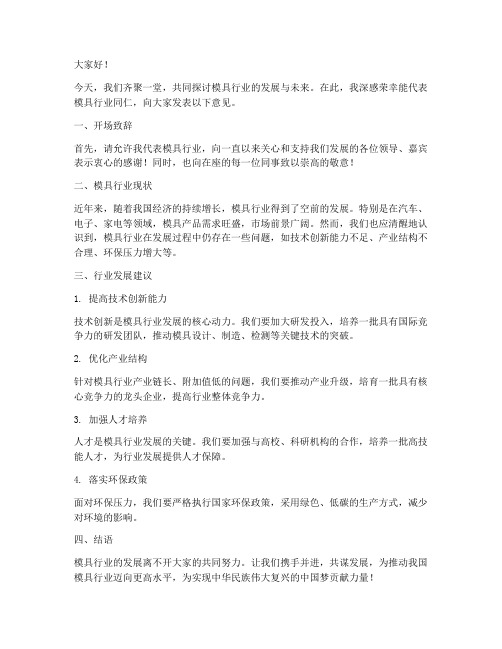
今天,我们齐聚一堂,共同探讨模具行业的发展与未来。
在此,我深感荣幸能代表模具行业同仁,向大家发表以下意见。
一、开场致辞
首先,请允许我代表模具行业,向一直以来关心和支持我们发展的各位领导、嘉宾表示衷心的感谢!同时,也向在座的每一位同事致以崇高的敬意!
二、模具行业现状
近年来,随着我国经济的持续增长,模具行业得到了空前的发展。
特别是在汽车、电子、家电等领域,模具产品需求旺盛,市场前景广阔。
然而,我们也应清醒地认识到,模具行业在发展过程中仍存在一些问题,如技术创新能力不足、产业结构不合理、环保压力增大等。
三、行业发展建议
1. 提高技术创新能力
技术创新是模具行业发展的核心动力。
我们要加大研发投入,培养一批具有国际竞争力的研发团队,推动模具设计、制造、检测等关键技术的突破。
2. 优化产业结构
针对模具行业产业链长、附加值低的问题,我们要推动产业升级,培育一批具有核心竞争力的龙头企业,提高行业整体竞争力。
3. 加强人才培养
人才是模具行业发展的关键。
我们要加强与高校、科研机构的合作,培养一批高技能人才,为行业发展提供人才保障。
4. 落实环保政策
面对环保压力,我们要严格执行国家环保政策,采用绿色、低碳的生产方式,减少对环境的影响。
四、结语
模具行业的发展离不开大家的共同努力。
让我们携手并进,共谋发展,为推动我国模具行业迈向更高水平,为实现中华民族伟大复兴的中国梦贡献力量!
(完)
注:以上发言稿模板仅供参考,实际发言内容可根据具体情况调整。
多点成形简介

1.2.2 多点成形的产生与发展多点成形的构想最早是在上世纪六十年代由日本学者提出,由于造船业的迅速发展,需要找到新的加工方法来提高生产效率。
因此,那时就出现了许多柔性加工方法,例如多点成形、柔性辊轧成形、滚球成形、喷丸成形、数控钣金、局部加热成形等。
从中岛尚正最早对多点成形进行尝试而制作的简单成形实验装置——钢丝捆工具[6]、石川岛播磨重工业株式会社试制的万能调整式压力机[7],到而后Nakajima制造的第一个可自动调节模具型面的多点模具[8],这些试验装置的成功研制使得多点成形这项技术从构想阶段过渡到了试验阶段。
由于当时的科学技术水平有限,许多问题得不到解决。
就万能调整式试验压力机而言,它使用了61 16个冲头以实现对船体外板的弯曲加工,却不能保证制品成形后的精度,成形缺陷问题也未能解决;由紧密排列的圆柱形小冲头组成的型面可调的多点模具,它通过安装在数控机床上的铁针来调节每个小冲头的高度,由于调节过程的繁琐并且不能抑制成形缺陷的产生等因素,导致其未能应用于实际生产中。
日本造船协会、三菱重工业株式会社等也在这方面提出许多设想并进行大量研究,为推动多点成形技术的发展做出了一定的贡献[9,10]。
关于多点成形的相关技术并不只有日本在研究,美国麻省理工学院David. E. Hardt等人也对多点成形方法进行了数年的研究,并且成功制造了一台用于成形试验原型机。
1999 年,他们投入了1400多万美元,开发出了多点式拉弯成形装置,不过该装置只能用于拉弯成形形状较为简单(接近二维变形)的薄板类件[11-16],而且他们对多点式成形的不良现象也没有进行细致的研究。
近年来,韩国科学技术研究院的朴钟雨也对多点成形技术进行了研究,开发了上部为10×10个冲头,下部用弹性体(如人造橡胶泡沫材料等)的装置。
该装置采用一个机械手依次对基本体高度进行调整,机械手每移动1次可以同时调整5个基本体。
国内无模多点成形技术的研究主要集中在吉利大学,早在李明哲教授日本留学期间就对多点成形的基本理论和其相关技术进行了系统的研究,并于1992年首次将这种成形方法命名为多点成形法。
无模多点成形技术
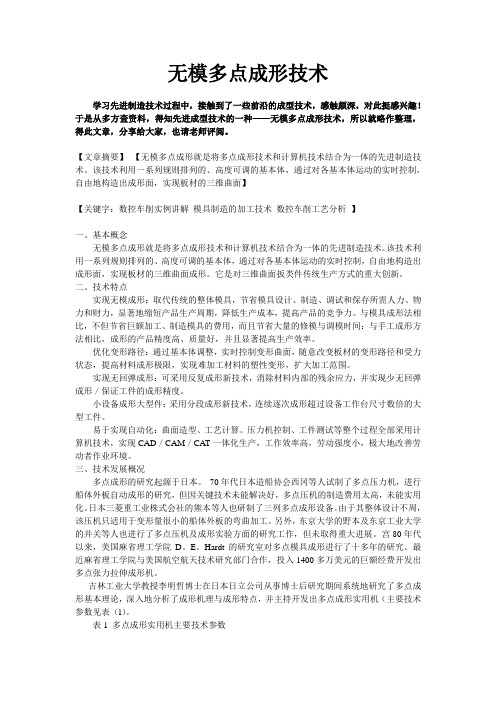
无模多点成形技术学习先进制造技术过程中,接触到了一些前沿的成型技术,感触颇深,对此挺感兴趣!于是从多方查资料,得知先进成型技术的一种——无模多点成形技术,所以就略作整理,得此文章,分享给大家,也请老师评阅。
【文章摘要】【无模多点成形就是将多点成形技术和计算机技术结合为一体的先进制造技术。
该技术利用一系列规则排列的、高度可调的基本体,通过对各基本体运动的实时控制,自由地构造出成形面,实现板材的三维曲面】【关键字:数控车削实例讲解模具制造的加工技术数控车削工艺分析】一、基本概念无模多点成形就是将多点成形技术和计算机技术结合为一体的先进制造技术。
该技术利用一系列规则排列的、高度可调的基本体,通过对各基本体运动的实时控制,自由地构造出成形面,实现板材的三维曲面成形。
它是对三维曲面扳类件传统生产方式的重大创新。
二、技术特点实现无模成形:取代传统的整体模具,节省模具设计、制造、调试和保存所需人力、物力和财力,显著地缩短产品生产周期,降低生产成本,提高产品的竞争力。
与模具成形法相比,不但节省巨额加工、制造模具的费用,而且节省大量的修模与调模时间:与手工成形方法相比,成形的产品精度高、质量好,并且显著提高生产效率。
优化变形路径:通过基本体调整,实时控制变形曲面,随意改变板材的变形路径和受力状态,提高材料成形极限,实现难加工材料的塑性变形,扩大加工范围。
实现无回弹成形:可采用反复成形新技术,消除材料内部的残余应力,并实现少无回弹成形/保证工件的成形精度。
小设备成形大型件:采用分段成形新技术,连续逐次成形超过设备工作台尺寸数倍的大型工件。
易于实现自动化:曲面造型、工艺计算。
压力机控制、工件测试等整个过程全部采用计算机技术,实现CAD/CAM/CA T一体化生产,工作效率高,劳动强度小,极大地改善劳动者作业环境。
三、技术发展概况多点成形的研究起源于日本。
70年代日本造船协会西冈等人试制了多点压力机,进行船体外板自动成形的研究,但因关键技术未能解决好,多点压机的制造费用太高,未能实用化。
模具讲稿
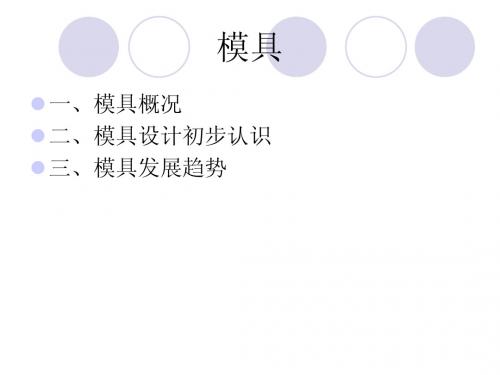
模具发展趋势
1、高精度注塑模具 2、计算机技术与模具技术完美结合 3、模具制造新工艺的进展 4、模具标准化 5、特种成型模具
高精度注塑模具
普通塑件的精度很难达到金属切屑零件的 IT8或IT7级精度要求,特别是大型制件,但 在某些特殊的使用场合又必须采用精密塑 件,这时就不得不采用精密注塑成型模具。 对精密注塑成型模具有一系列的要求,其 中最重要的是模具型腔成型尺寸精度高、 形位精度高、配合精度高、运动精度高。 此外,要求模温均匀、模温精确简易空中、 型腔内压力梯度小,这就必须采用高强度、 高模量、耐磨性好的金属来制模。
如何确定分型面,需要考虑的因素比较复杂。由于分型面 受到塑件在模具中的成型位置、浇注系统设计、塑件的结 构工艺性及精度、嵌件位置形状以及推出方法、模具的制 造、排气、操作工艺等多种因素的影响,因此在选择分型 面时应综合分析比较,从几种方案中优选出较为合理的方 案。选择分型面时一般应遵循以下几项原则:
分型面应选在塑件外形最大轮廓处。 便于塑件顺利脱模,尽量使塑件开模时留在动模一边。 保证塑件的精度要求。 满足塑件的外观质量要求。 便于模具加工制造。 对成型面积的影响。 对排气效果的影响。 对侧向抽芯的影响。
浇注系统形式和浇口的设计
浇口设计的原则: 1、尽量缩短流动距离。 2、浇口应开设在塑件壁厚最大处。 3、必须尽量减少熔接痕。 4、应有利于型腔中气体排出。 5、注意对外观质量的影响。
模具标准化
模具标准化为塑料模具设计和制造都带 来了极大的方便,由于标准件可直接购买, 因此模具设计制造者只需精心设计和加工 型腔,这使得塑料模具的设计和制造周期 大为缩短,成本降低,质量得到保证。当 前我国模具标准化程度还不高,尚需大力 推广,充实完善,扩大模具标准件新系列。
多元材料多点式混合一体成型技术

多元材料多点式混合一体成型技术在当今社会,随着科学技术的飞速发展,各行各业的生产制造都在不断探索更高效、更节能、更环保的生产工艺和技术。
多元材料多点式混合一体成型技术,作为一种新型的先进制造技术,正逐渐受到人们的关注和重视。
一、多元材料多点式混合一体成型技术的概念多元材料多点式混合一体成型技术是指将不同性质的原始材料,通过多点式的混合方式,进行一体成型的技术方法。
这种技术可以对原材料进行更加精细的混合,从而提高产品的质量和性能。
二、多元材料多点式混合一体成型技术的应用领域多元材料多点式混合一体成型技术目前已经在许多领域得到了广泛应用,比如汽车制造、航空航天、建筑材料等。
通过这种技术,原材料可以更好地融合在一起,从而提高制品的强度、耐磨性和耐腐蚀性。
三、多元材料多点式混合一体成型技术的优势与传统的单一材料成型技术相比,多元材料多点式混合一体成型技术具有许多优势。
它可以实现不同性质材料的精细混合,从而使得最终产品的性能得到提高。
通过这种技术,还可以实现生产过程的自动化和智能化,从而提高生产效率,降低生产成本。
四、个人观点对于多元材料多点式混合一体成型技术,我认为它是未来制造业发展的趋势之一。
随着科学技术的不断进步,人们对产品质量和性能的要求也越来越高,而多元材料多点式混合一体成型技术恰恰可以满足这一需求。
我对这种技术充满信心,相信它会在未来发展中发挥越来越重要的作用。
总结回顾多元材料多点式混合一体成型技术是一种新型的制造技术,通过对不同性质材料的多点混合,可以实现成型制品的提高性能。
它具有许多优势,可以应用于多个领域,是未来制造业发展的趋势之一。
我对这种技术充满信心,并期待着它在未来的发展中发挥更大的作用。
通过以上对多元材料多点式混合一体成型技术的探讨,我相信你已经能够更深入地理解这一主题,并且对它的发展前景有了更清晰的认识。
希望我的文章对你有所帮助,也期待你能在未来的学习和工作中运用这些知识。
多元材料多点式混合一体成型技术作为一种新型的先进制造技术,正在逐渐成为制造业的重要发展方向。
多元材料多点式混合一体成形技术
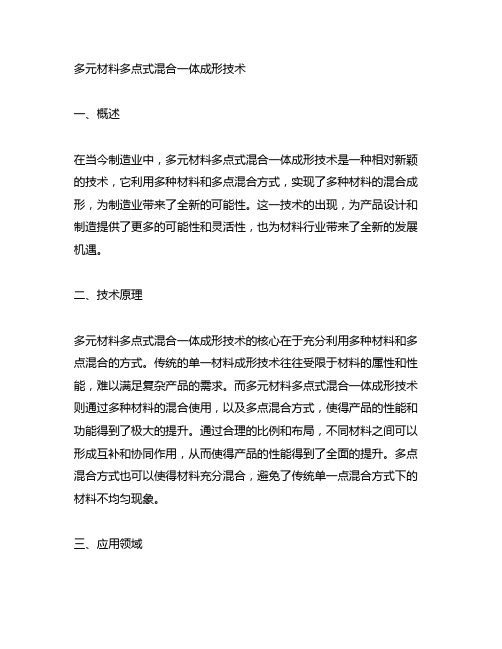
多元材料多点式混合一体成形技术一、概述在当今制造业中,多元材料多点式混合一体成形技术是一种相对新颖的技术,它利用多种材料和多点混合方式,实现了多种材料的混合成形,为制造业带来了全新的可能性。
这一技术的出现,为产品设计和制造提供了更多的可能性和灵活性,也为材料行业带来了全新的发展机遇。
二、技术原理多元材料多点式混合一体成形技术的核心在于充分利用多种材料和多点混合的方式。
传统的单一材料成形技术往往受限于材料的属性和性能,难以满足复杂产品的需求。
而多元材料多点式混合一体成形技术则通过多种材料的混合使用,以及多点混合方式,使得产品的性能和功能得到了极大的提升。
通过合理的比例和布局,不同材料之间可以形成互补和协同作用,从而使得产品的性能得到了全面的提升。
多点混合方式也可以使得材料充分混合,避免了传统单一点混合方式下的材料不均匀现象。
三、应用领域多元材料多点式混合一体成形技术在制造业中有着广泛的应用。
在汽车制造领域,通过多元材料多点式混合一体成形技术,可以实现汽车车身的轻量化设计,提高汽车的燃油经济性和安全性。
在航空航天领域,这一技术也可以应用于飞行器结构件的制造,使得飞行器的性能得到了显著提升。
另外,在电子产品制造领域,多元材料多点式混合一体成形技术也可以应用于电子产品外壳的制造,提高了电子产品的耐用性和美观度。
四、个人观点多元材料多点式混合一体成形技术的出现,为制造业和材料行业带来了全新的机遇和挑战。
作为一名制造业工作者,我深切感受到了这一技术带来的变革。
在未来的工作中,我将更加注重学习和应用这一技术,不断提升自己的专业能力,为公司的发展贡献力量。
总结在文章中,我们深入探讨了多元材料多点式混合一体成形技术的原理和应用领域,以及个人的观点。
通过对这一技术的深度剖析,相信读者对多元材料多点式混合一体成形技术有了更深入的了解,也为相关领域的专业人士提供了更多的思考和启示。
未统计字数,但确保文章字数满足要求。
多元材料多点式混合一体成形技术的应用领域还在不断扩展,尤其是在生物医药领域,该技术也展现出了巨大的潜力。
多点成型技术的简述

学士论文摘要多点成形技术是金属板材三维自由曲面成形的一种柔性加工方法,其基本思想是将传统的整体模具离散化,由一系列规则排列的基本体(或称冲头)组成的“柔性多点模具”来代替,由基本体球头的包络曲面来完成板材成形。
多点成形技术作为一种新兴的技术已在飞机、船舶、汽车等诸多制造领域有着广泛的应用前景。
无压边多点成形通常用于变形量不大的曲面成形,是板材多点成形过程中使用频率很高的一种成形方法。
由于没有压边圈,板材面内变形力较小,主要以面外弯曲变形为主,导致在多点成形中起皱缺陷更容易出现,特别是在薄板多点成形中,起皱是工艺上必须克服的成形缺陷。
由于没有压边圈的作用,板材成形过程中,回弹对成形件最终形状的影响要比有压边时大。
影响回弹的因素很多,如板材厚度,板材的材质以及成形件变形量的大小等。
本文采用数值模拟技术对多点成形过程的起皱和回弹进行了分析,谈论了各个因素对成形柱面成形件时起皱和回弹的影响。
1.板材无压边多点成形的起皱数值模拟采用显式算法对柱面成形件进行了详细的数值模拟,研究了板材厚度、曲率半径以及材质等对起皱的影响。
板厚与变形程度是影响起皱的重要因素,增大板材厚度,减小成形件曲率半径均可有效的抑制起皱的产生。
2.板材无压边多点成形的回弹数值模拟。
完整的板材成形包括加载和卸载两个过程。
本文采用动态显式算法模拟板材成形过程,采用隐式算法模拟卸载回弹过程。
主要分析了板材厚度、成形件变形量以及材质等对柱面成形件无压边多点成形的回弹影响。
由数值模拟结果可以看出,在多点成形中,板材厚度越小,变形量越小,卸载后回弹越大,反之,厚度越大,变形量越大则回弹越小。
关键词:多点成形,数值模拟,起皱,回弹,动态显式算法,隐式算法。
- 1 -学士论文ABSTRACTMulti-point forming(MPF)is a flexible manufacturing technology for three dimensional sheet metal forming. In multi-point forming, the conventional solid die is replaced by“ flexible Multi-point die”composed by a series of discrete elements (or punches).The forming process of sheet metal is implemented by the envelope surface of punches. Multi-point Forming can be applied extensively in a lot offields such as aircraft, stream and navel ships, vehicle, large sculpture and modern architecture etc.Sheet metal forming in MPF without blank holder, which is a common process method, is usually applied in processing those kinds of surface parts which have not big deformation amount. without blank holder, the deformation inside the surface is distinctly smaller than the bending outside the surface. Wrinkle is a key factor to determine whether the part could be formed and become one of primary forming defects especially for thin metal sheet in MPF.On the other hand,in this condition, springback was more serious than those forming with blank holder. Springback was affected by numerous factors, such as thickness of metal sheet, material property and deformation amount and so on.???????1. Numerical simulation of wrinkling in multi-point forming for metal sheet without blank holderThe Multi-point forming process of cylindrical surface of different materials with different thickness and deformations were simulated, and those results show that metal sheet thickness, deformation and material property have effect on wrinkle defect. With metal sheet thickness increasing, deformation diminishing, wrinkle can be gradually weakened. Simultaneously, wrinkle was affected by material property too.2.Numerical simulation of springback in multi-point forming for- 2 -学士论文metal sheet without blank holderThere were included loading and unloading course in an intact metal sheet forming. Based on explicit-implicit algorithm , the finite element model for numerical simulation of springback was established. Dynamic-explicit formulation was employed to analyze the loading process and implicit formulation to unloading process. The multi-point forming processes of cylindrical surface with different thickness under different deformations were simulated. In terms from the numerical simulation results, in multi-point forming for metal sheet without blank holder, increasing thickness and deformation can weaken the springback.Keywords: Multi-point forming, Numerical simulation, Wrinkle, springback, Dynamic-explicit algorithm, Implicit algorithm.- 3 -学士论文目录第一章绪论 (6)1.1多点成形技术简介 (6)1.1.1概述 (6)1.1.2基本原理 (6)1.1.3产生与发展 (6)1.1.4成形缺陷及抑制方法 (7)1.1.5多点成形应用实例 (8)1.2板材成形数值模拟 (9)1.2.1板材数值模拟的发展及现状 (10)1.2.2板材多点成形数值模拟 (12)1.3选题的意义及本文的主要研究内容。
多点成形技术

比较:主要区别,在成形前或在成形过程中改变基本体的相对位置,改变被成形件的变形路径及受力状态,以达到不同的成形结果。
多点成形技术经过多年的发展,已达到了实用化阶段,具有如下特点:1.实现无模成形无需另外生产模具,避开了模具从设计、制造和调试的这一整套过程。
2.变形路径可控通过控制各个基本体的位移和速度,实时的调整基本体冲头包络面形成的成形面形状,这种成形路径可变的特点是整体模具成形无法实现的。
3.通用性强,适用范围广:多点成形放宽了对板材厚度的限制,整体模具成形通常只能冲压固定厚度的板材,但多点成形可以冲压最大厚度和最小厚度比值高达10 的板料。
4.小设备成形大型件采用分段多点成形技术,连续逐次成形超过设备工作台尺寸几倍到几十倍的大型工件。
5.易于实现自动化:多点压机成形能够充分体现柔性特点,实现板料最佳变形。
多点压机成形的基本思想是最大程度地均匀化板料变形,按照任意时刻成形面中间构形曲率均匀变化方法确定变形路径。
1成形结果:可以看出板料应变值不断下降,说明局部剧烈变形程度逐渐减小;应变极值比不断下降,说明板料变形趋于均匀。
多点压机成形方式使变形得到最大程度的改善2.成形能力08AL 板料在相同条件下多点压机成形下的极限变形量有了较大程度的提高,多点压机成形能够显著地提升板料成形性能,提高成形能力。
3.回弹板料回弹分布是否均匀反应了变形的均匀程度3.1其中四条虚线框表示回弹前的板料位置,比较可知,随着变形路径的改善,板料成形后回弹分布趋于均匀,多点压机成形方式时回弹分布最为均匀;3.2板料变形越来越均匀,回弹量逐渐减小;板料在多点压机成形方式下,受力状态良好,只发生面内变形,板料没有局部过度变形,应力分布均匀,因此应力释放均匀,所引起的板料形状变化较小,因此回弹分布均匀。
起皱是板料沿不良路径成形的一种现象。
应用范例在具体施工方面第一大难题就是大量的钢结构部件需要三维曲面成形,而目前世界上还没有类似形状的钢结构建筑。
多点成型
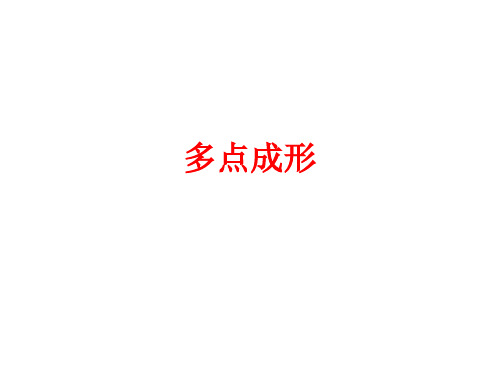
4.技术特点(与传统模具成形相比):
4.小设备成形大型件 可采用分段成形新技术,可以连续逐次成形超过 设备台尺寸数倍或数十倍的大型工件。 5.易于实现自动化 曲面造型、工艺计算、压力机控制、工件测试等 整个过程都可以采用计算机技术,实现 CAD/CAE/CAM一体化生产,工作效率高,劳动 强度小,极大的改善劳动者作业环境。
3.基本原理:
多点成形是在成形之前将基本体调整到所需 的适当位置,使基本体群形成制品曲面的包络面, 而在成形各基本体间没有相对运动。其实质与模 具成形基本相同,只是将模具分成离散点。
1.整体板料成型时,板材由模具曲面来成型; 2.多点成型由基本体群冲头的包络面(或成型曲面) 完成。柔性特点体现:基本体行程可以调节,改变 基本体的位置就可以改变成型曲面,也就相当于重 新构造了成型模具
2.概念:
通俗地说,无模多点成形是一种 全新的板材曲面柔性成形技术,主要 思路是将整体模具离散化,在一台设 备上布置很多基本体单元,通过计算 机控制这些基本体单元的高度,形成 型面可变的柔性模具,达到对板材柔 性成形的目的,而无需对每一种零件 都制作相应的模具。
3.工作原理:
将传统的整体模具离散成一系列规则 排列、高度可调的调形单元(或称冲头), 由这些调形单元组成的“柔性多点模具” 代替 传统的冲压成形。
5.多点成形设备组成: 1.多点成形主机 YAM和SM两个系列
5.多点成形设备组成:
5.1多点成形主机 • 机架:开式、四柱式、框架式...... • 基本体调形机构
(1)机械手式:通过机械手一次调整每个基本体的行程; (2)电机式:每个基本体由一个小型电机控制,调型效率 高; (3)液压缸式:每个基本体由一个小型液压缸控制,调型 效率高。
多点成型技术的原理和特点
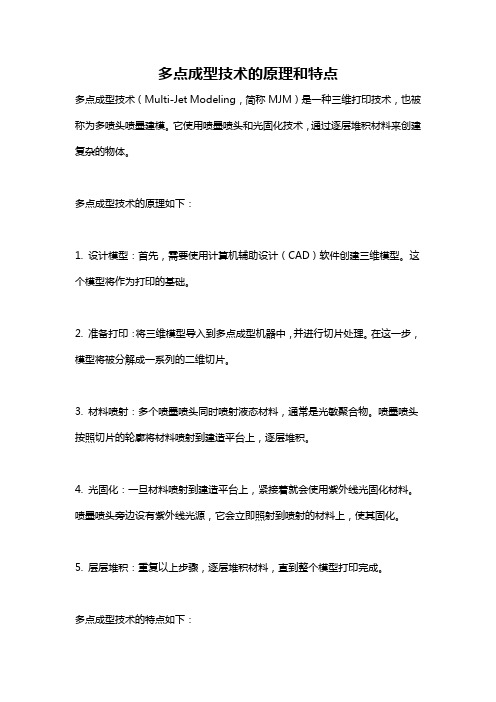
多点成型技术的原理和特点
多点成型技术(Multi-Jet Modeling,简称MJM)是一种三维打印技术,也被称为多喷头喷墨建模。
它使用喷墨喷头和光固化技术,通过逐层堆积材料来创建复杂的物体。
多点成型技术的原理如下:
1. 设计模型:首先,需要使用计算机辅助设计(CAD)软件创建三维模型。
这个模型将作为打印的基础。
2. 准备打印:将三维模型导入到多点成型机器中,并进行切片处理。
在这一步,模型将被分解成一系列的二维切片。
3. 材料喷射:多个喷墨喷头同时喷射液态材料,通常是光敏聚合物。
喷墨喷头按照切片的轮廓将材料喷射到建造平台上,逐层堆积。
4. 光固化:一旦材料喷射到建造平台上,紧接着就会使用紫外线光固化材料。
喷墨喷头旁边设有紫外线光源,它会立即照射到喷射的材料上,使其固化。
5. 层层堆积:重复以上步骤,逐层堆积材料,直到整个模型打印完成。
多点成型技术的特点如下:
1. 高精度:多点成型技术可以实现较高的打印精度,可以打印出细节丰富、复杂的物体。
2. 多材料:它可以使用多种不同的材料进行打印,包括不同颜色的聚合物。
3. 快速打印:多点成型技术的打印速度相对较快,可以在短时间内完成打印任务。
4. 支撑结构:该技术可以打印具有复杂内部结构的物体,并使用支撑结构来支撑打印过程中的悬挂部分。
5. 应用广泛:多点成型技术在产品设计、快速原型制作、医疗领域、艺术和创意设计等领域得到了广泛应用。
请注意,以上描述仅为一般性原理和特点,实际的多点成型技术可能会因具体机型和制造商而有所不同。
演讲资料:多点模具成形技术
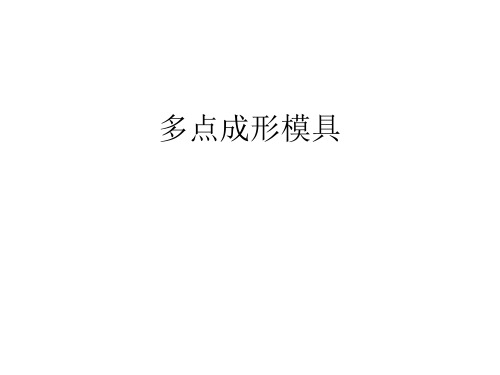
• 主要缺陷:压痕,起皱
• 挠曲变形的大小取决于挠曲变形刚度,刚度大,则变形小;刚度 小,则变形大。某一基本体对板材所作的功,使板材产生局部压 入变形及挠曲变形。当接触点处挠曲变形刚度很大时,挠曲变形 需要的变形力很大,挠曲变形很难产生,这时,大部分外力功使 板材产生压入变形,表面将出现压痕;当接触点处挠曲变形刚度 较小时(如板材较薄的情况),挠曲变形需要的变形力比较小, 挠曲变形极易产生,这时,若约束条件不合理,则将出现包络式 压痕。可见,理想的多点成形要求板材在成形过程中应始终保持 适度的挠曲变形刚度。
4、模具可以重构
一、有重叠区的成形方法
二、过渡区变形协调的成形方法
剧烈 塑性变形和硬化
三、多道分段成形方法 应用实例:
路径优化
数字化渐进成形
多点成形模具的分类
半多点靠模成形法
多点成形压力机
• 多点成形压力机,按冲头基本体调形分有:逐点调形式和快速调 形式;按机架形式分有开式、三梁四柱式和框架式;按加工板材
状的误差,可以用加弹性垫的方法进行弥补。
• 多点成形模具具有柔性特点,根据不同零件的 需要进行调整,以便适应不同零件的需要。
• 采用具有柔性的多点模具,可以省去模具费用。 • 缩短生产准备时间。 • 适合单件、小批量钣金件的生产。 • 避免了手工方法中成形质量差、生产效率低、
劳动强度大的不足。
多点成形方法的优点
(3)采用多点压机成形方式,在成形过程中调整基本 体位置,改变板材的变形路径,使所有的基本体在 成形过程中始终与板材接触,分散接触压力,使各 部分尽量均匀地变形,也是抑制压痕的有效办法。
• 采用多道 成形方法, 能够明显 地抑制成 形缺陷, 提高材料 的成形极 限。
成形力对工件质量的影响
多点成形技术简介
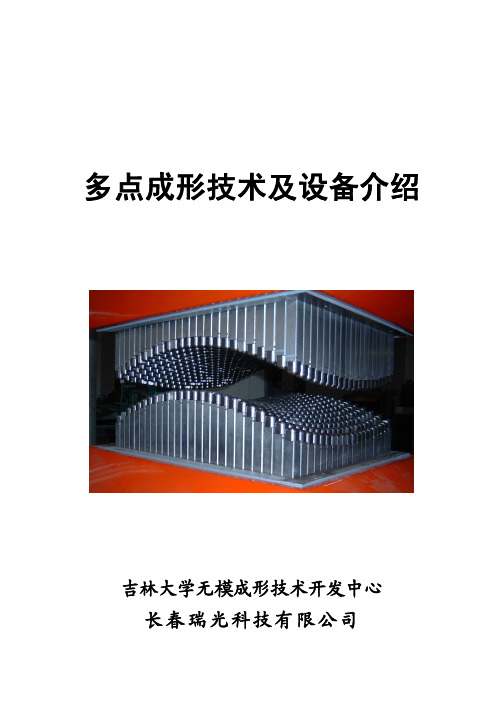
多点成形技术及设备介绍吉林大学无模成形技术开发中心长春瑞光科技有限公司一、多点成形技术简介多点成形是金属板材三维曲面成形的全新技术,是对传统板料生产方式的重大变革。
其原理是将传统的整体模具离散成一系列规则排列、高度可调的基本体(或称冲头)。
在整体模具成形中,板材由模具曲面来成形,而多点成形中则由基本体群冲头的包络面(或称成形曲面)来完成,如图1-1所示。
相当于重新构造了成形模具,由此体现了多点成形的柔性特点。
调节基本体行程需要专门的调整机构,而板材成形又需要一套加载机构,以上、下基本体群及这两种机构为核心就构成了多点成形压力机。
一个基本的多点成形装备应由三大部分组成,即CAD软件系统、控制系统及多点成形主机,如图1-2所示。
CAD软件系统根据要求的成形件目标形状进行几何造型、成形工艺计图1-2 多点成形系统的基本构成算,将数据文件传给控制系统,控制系统根据这些数据控制压力机的调整机构,构造基本体群成形面,然后控制加载机构成形出所需的零件产品。
二、技术先进性与应用领域在多点成形装备中,基本体群及由其形成的“可变模具”是多点成形压力机的主要组成部分。
从这个意义上讲,“多点成形”也可称为“无模成形”。
这种成形装备具有很多传统成形方式无法比拟的优点,其先进性主要表现为:1)实现无模成形,不需另外配置模具。
因此,不存在模具设计、制造及调试费用的问题。
与整体模具成形方法相比节省了大量的资金与时间;更重要的是过去因模具造价太高而不得不采用手工成形的单件、小批零件的生产,在此系统上可完全实现规范的自动成形。
无疑,这将大大提高成形质量。
2)该技术由基本体群的冲头包络面成形板材,而成形面的形状可通过对各基本体运动的实时控制自由地构造出来,甚至在板材成形过程中都可随时进行调整。
因而,板材成形路径是可以改变的,这也是整体模具成形无法实现的功能。
结合有效的数值模拟技术,设计适当的成形路径,即可消除板材的成形缺陷,提高板材的成形能力。
模具的成型方法
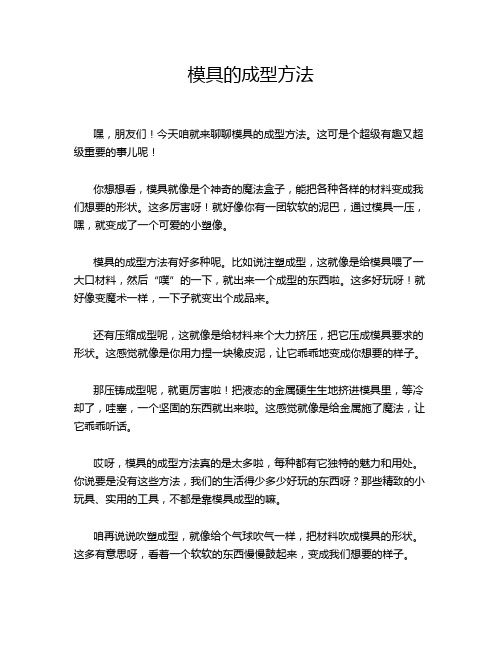
模具的成型方法嘿,朋友们!今天咱就来聊聊模具的成型方法。
这可是个超级有趣又超级重要的事儿呢!你想想看,模具就像是个神奇的魔法盒子,能把各种各样的材料变成我们想要的形状。
这多厉害呀!就好像你有一团软软的泥巴,通过模具一压,嘿,就变成了一个可爱的小塑像。
模具的成型方法有好多种呢。
比如说注塑成型,这就像是给模具喂了一大口材料,然后“噗”的一下,就出来一个成型的东西啦。
这多好玩呀!就好像变魔术一样,一下子就变出个成品来。
还有压缩成型呢,这就像是给材料来个大力挤压,把它压成模具要求的形状。
这感觉就像是你用力捏一块橡皮泥,让它乖乖地变成你想要的样子。
那压铸成型呢,就更厉害啦!把液态的金属硬生生地挤进模具里,等冷却了,哇塞,一个坚固的东西就出来啦。
这感觉就像是给金属施了魔法,让它乖乖听话。
哎呀,模具的成型方法真的是太多啦,每种都有它独特的魅力和用处。
你说要是没有这些方法,我们的生活得少多少好玩的东西呀?那些精致的小玩具、实用的工具,不都是靠模具成型的嘛。
咱再说说吹塑成型,就像给个气球吹气一样,把材料吹成模具的形状。
这多有意思呀,看着一个软软的东西慢慢鼓起来,变成我们想要的样子。
还有挤出成型,就像挤牙膏一样,把材料源源不断地挤出来,变成长长的形状。
这感觉是不是很神奇呀?你看,模具的成型方法就像是一个百宝箱,里面装满了各种各样的惊喜。
我们可以根据不同的需求,选择不同的方法,让材料变成我们想要的宝贝。
在生活中,我们可处处都能看到模具成型的东西呢。
你手里拿的手机壳,说不定就是注塑成型的;你用的勺子,可能就是压铸成型的。
这些东西都离不开模具的功劳呀。
所以呀,模具的成型方法真的是太重要啦!它们让我们的生活变得更加丰富多彩,让我们能拥有那么多好用又好玩的东西。
咱可得好好感谢这些神奇的模具成型方法呀,没有它们,我们的生活可就没那么有意思啦!你们说是不是呀?。
模具技术汇报总结发言稿
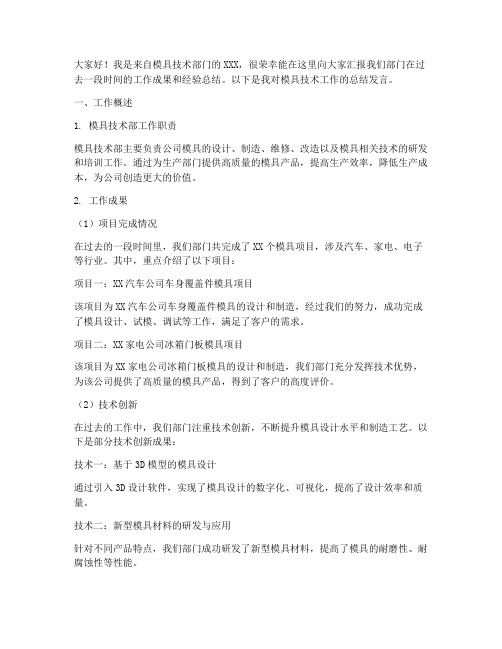
大家好!我是来自模具技术部门的XXX,很荣幸能在这里向大家汇报我们部门在过去一段时间的工作成果和经验总结。
以下是我对模具技术工作的总结发言。
一、工作概述1. 模具技术部工作职责模具技术部主要负责公司模具的设计、制造、维修、改造以及模具相关技术的研发和培训工作。
通过为生产部门提供高质量的模具产品,提高生产效率,降低生产成本,为公司创造更大的价值。
2. 工作成果(1)项目完成情况在过去的一段时间里,我们部门共完成了XX个模具项目,涉及汽车、家电、电子等行业。
其中,重点介绍了以下项目:项目一:XX汽车公司车身覆盖件模具项目该项目为XX汽车公司车身覆盖件模具的设计和制造,经过我们的努力,成功完成了模具设计、试模、调试等工作,满足了客户的需求。
项目二:XX家电公司冰箱门板模具项目该项目为XX家电公司冰箱门板模具的设计和制造,我们部门充分发挥技术优势,为该公司提供了高质量的模具产品,得到了客户的高度评价。
(2)技术创新在过去的工作中,我们部门注重技术创新,不断提升模具设计水平和制造工艺。
以下是部分技术创新成果:技术一:基于3D模型的模具设计通过引入3D设计软件,实现了模具设计的数字化、可视化,提高了设计效率和质量。
技术二:新型模具材料的研发与应用针对不同产品特点,我们部门成功研发了新型模具材料,提高了模具的耐磨性、耐腐蚀性等性能。
技术三:模具快速制造技术运用快速制造技术,实现了模具的快速生产,缩短了产品上市周期。
二、经验总结1. 团队协作模具技术工作涉及多个环节,需要团队成员之间的紧密协作。
我们部门注重团队建设,加强沟通与协作,确保项目顺利进行。
2. 技术积累通过不断学习、总结和研发,我们部门积累了丰富的模具技术经验,为今后的工作奠定了坚实基础。
3. 客户至上始终以客户需求为导向,为客户提供优质的产品和服务,赢得了客户的信任和支持。
4. 不断学习紧跟行业发展趋势,不断学习新技术、新工艺,提高自身技术水平。
三、未来展望1. 提升模具设计水平继续优化模具设计流程,提高模具设计质量,为客户提供更加优秀的模具产品。
多点成形技术
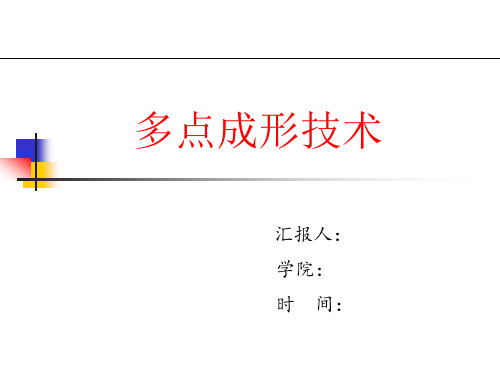
10/17
3 成形工艺
薄板件多点成形时不仅需要设计基本体群成形面,还需 要正确设计压边型面并选择压边力。
图5 薄板多点成形示意图 11/17
3 成形工艺
3.2 分段成形工艺 分段成形通过改变基本体群成形面的形状,逐段、分区 域地对板材连续成形,从而实现小设备成形大尺寸、大变 形量的零件。
图6 分段成形 12/17
3 成形工艺
3.3 反复成形工艺 回弹是板材冲压成形中不可避免的现象,在多点成形中 , 可采用反复成形的方法减小回弹并降低残余应力。 首先使变形超过目标形状, 然后反向变形并超过目标形 状,再正向变形;以目标形状为中心循环反复成形,直至收敛 于目标形状。
图7 反复成形
13/17
4 应用
多点成形(新的冲压成形技术)应用: 我国吉林大学在2000年研制出多点成形机,其无模成形技术 开发中心随后开发出一系列商用多点成形设备,已成功应用 于多个领域。
成形前把基本体调整到适当位置,使基本体群形成制品曲面的包络面,
成形时各基本体间无相对运动。基本体不是始终与板材接触。 特点:装置简单,容易制作成小型设备。需要较长时间调整各基本体,
调整精度也不易保证。
图3 成形原理图
7/17
2 概念
2.3.2 多点压机成形基本原理
实时控制各基本体的运动,形成随时变化的瞬时成形面。在成形过程中,
16/17
17/17
9/17
3 成形工艺
3.1 一次成形工艺
根据零件的几何形状并考虑材料的回弹等因素设计出成形面,在成形前调整 各基本体的位置,按调整后基本体群成形面一次完成零件成形。
3.1.1 中、厚板成形
对于中、厚度板,变形不太剧烈曲面零件,可直接进行多点成形,不需要压边。
- 1、下载文档前请自行甄别文档内容的完整性,平台不提供额外的编辑、内容补充、找答案等附加服务。
- 2、"仅部分预览"的文档,不可在线预览部分如存在完整性等问题,可反馈申请退款(可完整预览的文档不适用该条件!)。
- 3、如文档侵犯您的权益,请联系客服反馈,我们会尽快为您处理(人工客服工作时间:9:00-18:30)。
弹性垫厚 度及变形
多点模具针控制
实用化多点成形技术
2பைடு நூலகம்分段成形技术
对于尺寸大于设备成形尺寸的零件,可以逐段、分片连 续成形,在这种成形方式中,板材分成若干个区:已成 形区、过渡成形区及未成形区。这几个区域在变形过程 中是相互影响的,过渡区中基本体群成形面的几何形状 对分段成形效果具有决 定性作用,过渡区的设 计是分段成形最关键的 技术问题。应用多点分 段成形技术已成形出零 件尺寸大于一次成形尺 寸数倍以上的样件,成
• 将传统的整体模具离散化,变成形状可变的“柔性模 具”,则可用于任意形状的板材成形。这样将省去大量 的模具制造费用,又能解决单件、小批量零件的生产问 题,这种先进的金属板材成形技术就是板材多点成形技 术。
国内外现状
国内外现状
国内外现状
多点成形技术的特点
• 模具型面由离散的点构成,这些点的位置可调。 • 用离散点取代连续的模具型面,会带来局部形
形出的扭曲面扭曲角超 过400°。
分段多点成形技术
应用于大型和超大型钣 金件成形(汽车、造船 等)。解决设备尺寸和 批量的限制。例如高速 火车的流线型车头外壳、 巨型天线、潜艇外壳、 大型建筑装饰件等
多点分段成形的特点:
1、可以采用小型设备成形大型钣金件; 2、工件受力和变形比整体成形复杂; 3、多点成形模具的柔性特点可以减小模具成本,缩短生产准备 时间;
状的误差,可以用加弹性垫的方法进行弥补。
• 多点成形模具具有柔性特点,根据不同零件的 需要进行调整,以便适应不同零件的需要。
• 采用具有柔性的多点模具,可以省去模具费用。 • 缩短生产准备时间。 • 适合单件、小批量钣金件的生产。 • 避免了手工方法中成形质量差、生产效率低、
劳动强度大的不足。
多点成形方法的优点
(3)利用成形面可变的特点,可以实现板材的分段、分片成形, 在小设备上能成形大于设备成形面积数倍甚至数十倍的大尺寸零 件!
(4)通用性强,适用范围宽! 通常整体模具成形方法只适用于指定 厚度的板材,而这种成形方法可用于最大厚度与最小厚度之比达 到10 的各种材质板料!
多点成形技术的分类
1、整体一次成形 2、分段成形 3、反复成形 4、多次成形
多点成形模具
内容
多点成形技术的概念 多点成形技术的背景及意义 多点成形技术的特点 多点成形技术的分类 多点成形技术的模具 多点成形技术的应用 多点成形技术的关键技术与难点 多点成形技术的数值模拟 多点成形技术的质量评价
多点成形技术的概念
多点成形是将柔性成形技术和计算机技术 结合为一体的先进技术。它利用多点成形 装备的柔性与数字化制造特点,无需换模 就可完成板材不同曲面的成形,从而实现 无模、快速、低成本生产。该工艺目前已 在高速列车流线型车头制作、船舶外板成 形、建筑物内外饰板成形及医学工程等领 域,得到广泛应用。
4、模具可以重构
一、有重叠区的成形方法
二、过渡区变形协调的成形方法
剧烈 塑性变形和硬化
三、多道分段成形方法 应用实例:
路径优化
数字化渐进成形
多点成形模具的分类
半多点靠模成形法
多点成形压力机
• 多点成形压力机,按冲头基本体调形分有:逐点调形式和快速调 形式;按机架形式分有开式、三梁四柱式和框架式;按加工板材
(1)无需另外配置模具,因此不存在模具设计、制造及调试费用 的问题与整体模具成形方法相比节省了大量的资金与时间;更重 要的是过去因模具造价太高而不得不采用手工成形的单件、小批 零件,采用此技术可完全实现规范的自动成形,无疑,这将大大 提高成形质量。
(2)用于成形板材的基本体群成形面形状,可通过对各基本体运 动的实时控制自由地构造出来,甚至在板材成形过程中都可随时 进行调整! 因而,这种成形方法的板材成形路径是可选择的,而 这是整体模具成形无法实现的功能!
最基本的多点成形系统由三大部分组成,即
软件系统、计算机控制系统及多点成形主机。
多点模成形产生的背景和意义
• 由于模具费用昂贵,大尺寸(如巨型天线、开发阶段列 车的机头覆盖件、船上的大型钣金件等)、小批量、多 品种的零件只能采用手工成形方法,如在造船行业,每 一块船体外板形状都各不相同,并且都非批量生产。我 国第一台国产准高速列车的流线形车头外壳采用的也是 手工操作的对击锤成形方法。手工成形方法成形质量差、 生产效率低,而且劳动强度极大。对飞机行业也存在这 个问题。
分有厚板和薄板之分。目前,有代表性的产品如下:
①2000kN逐点调形式多点成形压力机。采用开式机架,机械手 调形,上下冲头基本群体采用28×20布置方式。公称力2000kN, 一次成形尺寸840mm×600mm。该机是世界上首台商品化多点 成形压力机。机器主要用于高速列车流线型车头覆盖件的加工。
②200kN快速调形式多点成形压力机。机架为三梁四柱式结构, 冲头群(采用16×12布置方式)相对液压机偏心布置。压机公称 力200kN,一次成形尺寸416mm×312mm;采用分段成形时, 宽度尺寸可为一次成形的两倍,长度方向只要不与机架干涉,可
多点成形技术的模具
• 模具的构成 • 模具的控制 • 模具型面的确定 • 模具型面的光顺
模具的构成、控制、型面确定、光顺
实用化多点成形技术
1、无缺陷成形的弹性垫技术。
由于多点成形时工具与工件为点 接触,在基本体与板材的接触 点附近小区域内容易产生压痕。 这些压痕产生于接触压力的高 度集中,塑性变形过于局部化。 通过对压痕产生机理的研究及 数值模拟分析,开发了弹性垫 技术。弹性垫可以增大基本体 与板材的接触面积,均匀分散 接触压力,非常有效地抑制了 压痕缺陷。
无限长。新近又开发了宽台面3150kN快速调形式多点成形压力
图1
原理:
多点成形是金属板材三维曲面成形方法。其核心原理是将传统 的整体模具离散成一系列规则排列、高度可调的基本体(或称冲 头),在整体模具成形中,板材由模具曲面来成形,而多点成形 中则由基本体冲头的包络面.
各基本体的行程可独立地调节,改变各基本体的位置就改变了 成形曲面,也就相当于重新构造了成形模具。