电厂脱硫培训—石灰石及石膏湿法FGD原理和主要参数
石灰石-石膏湿法烟气脱硫原理及工艺流程

石灰石-石膏湿法烟气脱硫原理及工艺流程摘要:文中主要对目前火力发电厂普遍使用的石灰石-石膏湿法烟气脱硫工艺的化学反应原理及工艺流程进行了阐述。
为运行及检修提供理论基础。
关键词:火力发电厂石膏湿法烟气脱硫目前,我国的电力供应仍以燃煤的火力发电厂为主,并因此产生的大量SO2的排放而产生的酸雨对我国的生态环境造成了极大的危害,因此,减少SO2的排放是我国大气治理的一个重要方面。
当前,我国火力发电厂减少SO2排放主要采用的为烟气脱硫技术,其中石灰石—石膏湿法FGD技术由于最为成熟、可靠而被广泛采用。
一、石灰石-石膏湿法烟气脱硫工艺介绍石灰石-石膏湿法烟气脱硫工艺属于煤燃烧后脱硫,脱硫系统位于除尘器之后,脱硫过程在溶液中进行,脱硫剂及脱硫生成物均为湿态,脱硫过程的反应温度低于露点,故脱硫后的烟气一般需要经再加热后排出,或提高烟囱的防腐等级。
1 工艺流程介绍其工艺流程为:从锅炉出来的烟气首先经过电除尘器进行除尘,去除烟气中的大部分粉尘颗粒,经除尘后的烟气进入到吸收塔中,同时,浆液循环泵由吸收塔下部抽取浆液并提升到一定高度后,通过喷淋层内设置的喷嘴喷射到吸收塔中。
在吸收塔内烟气向上流动,浆液向下流动,两种物料在吸收塔内进行逆流接触混合,此时,SO2与浆液中的碳酸钙相接触,在空气作用下进行化学反应,并最终形成石膏(CaSO4•2H2O)。
为保证有足量空气使亚硫酸根离子的充分氧化,还需设置氧化风机进行强制氧化。
整个过程中,吸收塔内浆液被循环泵连续不断的向上输送到喷淋层,浆液通过喷嘴喷出,在喷嘴的雾化作用下,气液两相物质充分混合。
每个循环泵与各自的喷淋层相连接,形成多层浆液喷嘴,根据锅炉烟气量及烟气含硫量开启相应的喷嘴层数。
随着烟气中SO2的不断被吸收,在吸收塔中不断的产生石膏,因此必须将石膏排出,以维持物料平衡,故在吸收塔底部设置石膏浆液泵,将二氧化硫与石灰石浆液反应生成的石膏浆液输送至石膏脱水系统,形成可被利用的工业石膏。
石灰石-石膏湿法烟气脱硫工艺的化学原理

石灰石-石膏湿法烟气脱硫工艺的化学原理一、概述:脱硫过程就是吸收,吸附,催化氧化和催化还原,石灰石浆液洗涤含SO烟气,产生化学反应分离出脱硫副产物,化学吸收速率较快与扩散速率有关,2又与化学反应速度有关,在吸收过程中被吸收组分的气液平衡关系,既服从于相平衡(液气比L/G,烟气和石灰石浆液的比),又服从于化学平衡(钙硫比Ca/S,二氧化硫与炭酸钙的化学反应)。
1、气相:烟气压力,烟气浊度,烟气中的二氧化硫含量,烟尘含量,烟气中的氧含量,烟气温度,烟气总量2、液相:石灰石粉粒度,炭酸钙含量,黏土含量,与水的排比密度,-,它们与溶解了的CaCO和SOHSO的反应3、气液界面处:参加反应的主要是323是瞬间进行的。
二、脱硫系统整个化学反应的过程简述:1、 SO在气流中的扩散,22、扩散通过气膜3、 SO被水吸收,由气态转入溶液态,生成水化合物24、 SO水化合物和离子在液膜中扩散25、石灰石的颗粒表面溶解,由固相转入液相6、中和(SO水化合物与溶解的石灰石粉发生反应)27、氧化反应8、结晶分离,沉淀析出石膏,三、烟气的成份:火力发电厂煤燃烧产生的污染物主要是飞灰、氮氧化物和二氧化硫,使用静电除尘器可控制99%的飞灰污染。
四、二氧化硫的物理、化学性质:①. 二氧化硫SO的物理、化学性质:无色有刺激性气味的有毒气体。
密度比2空气大,易液化(沸点-10℃),易溶于水,在常温、常压下,1体积水大约能溶解40体积的二氧化硫,成弱酸性。
SO为酸性氧化物,具有酸性氧化物的通性、2还原性、氧化性、漂白性。
还原性更为突出,在潮湿的环境中对金属材料有腐蚀性,液体SO无色透明,是良好的制冷剂和溶剂,还可作防腐剂和消毒剂及还原2剂。
②. 三氧化硫SO的物理、化学性质:由二氧化硫SO催化氧化而得,无色易挥23发晶体,熔点16.8℃,沸点44.8℃。
SO为酸性氧化物,SO极易溶于水,溶于33水生成硫酸HSO,同时放出大量的热,42③. 硫酸HSO的物理、化学性质:二元强酸,纯硫酸为无色油状液体,凝固点423,浓硫酸溶于水会放出大量的热,密度为1.84g/cm具有10.4℃,沸点338℃,为强氧化性(是强氧化剂)和吸水性,具有很强的腐蚀性和破坏性,五、石灰石湿-石膏法脱硫化学反应的主要动力过程:1、气相SO被液相吸收的反应:SO经扩散作用从气相溶入液相中与水生成亚硫22-+,当PHH 亚硫酸迅速离解成亚硫酸氢根离子HSO值较高时,和氢离子酸HSO3232-,要使SO吸收不断进行下去,必须中和HSO二级电离才会生成较高浓度的SO233++当,即降低吸收剂的酸度,碱性吸收剂的作用就是中和氢离子电离产生的HH 吸收液中的吸收剂反应完后,如果不添加新的吸收剂或添加量不足,吸收液的酸度迅速提高,PH值迅速下降,当SO溶解达到饱和后,SO的吸收就告停止,脱22硫效率迅速下降2、吸收剂溶解和中和反应:固体CaCO 的溶解和进入液相中的CaCO的分解,33+浓度(PH固体石灰石的溶解速度,反应活性以及液相中的H值)影响中和反应2+2+的形CaCa的氧化反应,以及其它一些化合物也会影响中和反应速度。
石灰石-石膏湿法脱硫工艺
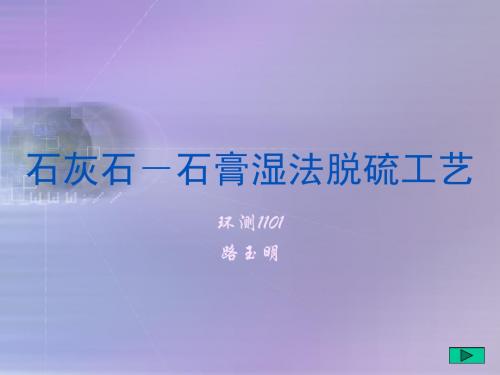
●烟气(再热)系统:提高烟气压头克服系统阻力,将净烟气加热。
4.2SO2吸收系统(吸收塔):吸收SO2净化烟气。 4.3石膏脱水系统:回收吸收剂,再利用。
4.4工艺水和压缩空气系统系统:系统冲洗、补水等。
废水排放系统 其他系统
电气系统
热工自动化系统 脱硫废水处理系统
4.1石灰石浆液制备系统
石灰石浆液制备系统由: ☆石灰石粉仓 ☆ 流化风机 ☆旋转给料阀 ☆称重给料机 ☆石灰石粉制浆罐 ☆搅拌器 ☆石灰石浆液输送泵 ☆浆液密度计 ☆至石灰石供浆罐的管道以及 相关的辅助设备组成。
石灰石-石膏湿法脱硫工艺
环测1101 路玉明
主要内容 ★一、石灰石-石膏湿法脱硫工艺原理 ★二、石灰石-石膏湿法脱硫工艺流程图 ★ 三、石灰石-石膏湿法脱硫工艺的优点
★ 四、石灰石-石膏湿法脱硫装置的主要系统
★ 五、石灰石-石膏湿法脱硫工艺的主要设备
一、石灰石-石膏湿法脱硫工艺原理
石灰石-石膏湿法脱硫工艺是目前世界上应用最为广泛和最可靠的工艺。
4.3石膏脱水系统
石膏脱水系统主要由:
◆吸收塔排浆泵;
◆石膏浆液旋流站;
◆ 真空皮带脱水机;
◆ 石膏脱水区集水坑及其相关辅助设备构成。 ◆ 真空皮带脱水机将脱水后的石膏送入石膏临时储存库中,再经卡车运出 外销。
4.3回流水系统
回流水系统由: ◆回流水箱 ◆回流水泵 ◆脱水区集水坑 ◆相关的辅助设备组成。
(7)系统可用率可达98%以上,具有较高的可靠性; (8)对锅炉燃煤煤质变化适应性好,当燃煤含硫量增加时,仍可 保持较高的脱硫效率; (9)对锅炉负荷变化有良好的适应性,在不同的烟气负荷及SO2 浓度下,脱硫系统仍可保持较高的脱硫效率及系统稳定性。
石灰石石膏湿法脱硫的工艺

石灰石石膏湿法脱硫的工艺【石灰石石膏湿法脱硫的工艺】导语:石灰石石膏湿法脱硫是一种常见的烟气脱硫技术,通过将石灰石与石膏反应,可以高效地去除燃煤发电厂和工业锅炉烟气中的二氧化硫。
本文将深入探讨石灰石石膏湿法脱硫的工艺原理、优势以及相关问题。
一、工艺原理1. 石灰石石膏湿法脱硫原理:石灰石与石膏发生反应生成硬石膏,将烟气中的二氧化硫转化为硫酸钙,并形成可回收利用的石膏产物。
主要反应方程式如下所示:CaCO3 + SO2 + 2H2O → CaSO4·2H2O + CO22. 脱硫反应的特点:该反应是一个快速的液相反应,在一定反应温度、气体流速和石膏浆液浓度下进行。
反应速率受碱性、反应温度、质量浓度等因素的影响。
二、工艺步骤1. 石灰石石膏湿法脱硫的基本步骤:(1)石灰石破碎、磨细:将原料石灰石经过破碎和磨细处理,提高其活性和反应速率。
(2)制备石膏浆液:将石灰石与水混合,形成石灰石浆液。
为了提高脱硫效果,还可加入一定量的添加剂。
(3)脱硫反应:将石灰石浆液喷入脱硫塔,通过与烟气的接触和反应,使二氧化硫转化为硫酸钙。
(4)石膏产物处理:将脱硫过程中生成的硬石膏经过脱水、干燥等处理后,得到成品石膏。
2. 工艺改进:为了提高脱硫效率和经济性,石灰石石膏湿法脱硫工艺进行了多方面的改进。
例如引入喷雾器、增加反应塔数目、采用高效填料等,以增加烟气与石灰石浆液的接触面积,加强反应效果。
三、工艺优势1. 脱硫效率高:石灰石石膏湿法脱硫工艺能够高效地将烟气中的二氧化硫转化为重质石膏产物,脱硫效率可达到90%以上。
2. 石膏产物可回收利用:脱硫过程中生成的硬石膏可以用于建材、石膏板等行业,实现资源的循环利用。
3. 工艺成熟可靠:石灰石石膏湿法脱硫工艺经过多年的实践应用,技术成熟可靠,广泛应用于燃煤发电厂和工业锅炉等领域。
四、问题与挑战1. 石膏处理与排放:脱硫过程中生成的硬石膏需要进行后续的脱水、干燥等处理,同时还需要解决石膏产物的长期存储和排放问题。
浅谈燃煤电厂石灰石-石膏湿法脱硫技术

浅谈燃煤电厂石灰石 -石膏湿法脱硫技术摘要:对于燃煤电厂石灰石-石膏湿法法脱硫技术及分析的研究,其主要目的在于了解湿式石灰石- 石膏法脱硫技术的相应原理,同时分析该技术在使用过程中的需要注意的问题,为日后提高湿式石灰石- 石膏法脱硫技术的应用水平提供宝贵的建议。
湿式石灰石-石膏法脱硫技术是目前我国最主要的脱硫技术,该技术能够有效的将烟气中二氧化硫脱除。
本篇文章主要对燃煤电厂石灰石-石膏湿法脱硫技术中存在问题进行分析。
关键词:燃煤电厂;石灰石-石膏湿法脱硫;煤质;石灰石原料;结垢;运行条件现阶段燃煤电厂是我国电力生产的主要生产力,其发电技术成熟,电力输出相对稳定,但是也是大气污染物排放的主体工程。
在其燃煤发电过程中会产生大量的二氧化硫、氮氧化物等污染物排入空气,各类颗粒物也会随之排入空气中。
火电厂在为经济发展带来贡献的同时也对其周围环境造成了一定程度的威胁,为了降低其对环境的影响,有必要提高脱硫工艺的水平,提高脱硫效率,减少二氧化硫的排放,以此来减少火电厂对大气环境的影响。
1.火电厂脱硫工艺存在的问题分析1.、技术与设备较为落后现阶段,我国在脱硫过程中的技术与设备均处于落后状态。
随着国家对经济环境的不断规划与控制,并结合世界经济对环保的控制标准和发展需求,我国在环保经济方面作出了越来越严格的要求,这些标准和政策的出台也在一定程度上暴露了我国现阶段火电厂环境保护方面所存在的问题。
我国多数火电厂正在使用的脱硫设备大多都是从国外进口,这就大大提高了生产成本,当企业资金不足以满足进口先进设备的时候,就会造成设备老化,脱硫设备不能够满足现在的大气排放标准,影响脱硫效率,造成环境污染,这也是火电厂现存的大问题。
1.、燃煤质量较差火电厂生产过程中产生的二氧化硫量与燃烧的煤质息息相关,当燃煤质量较差时,煤质中存在的硫分也偏高,使得脱硫设备处理工艺达不到处理标准,造成排放浓度过高。
1.石灰石-石膏湿法脱硫技术的应用(一)、石灰石-石膏湿法脱硫原理石灰石-石膏法是利用石灰石浆液吸收烟气中的SO2,生成亚硫酸钙,经分离的亚硫酸钙(CaSO3)可以抛弃,也可以氧化为硫酸钙(CaSO4),以石膏形式回收。
石灰石-石膏湿法烟气脱硫工艺原理
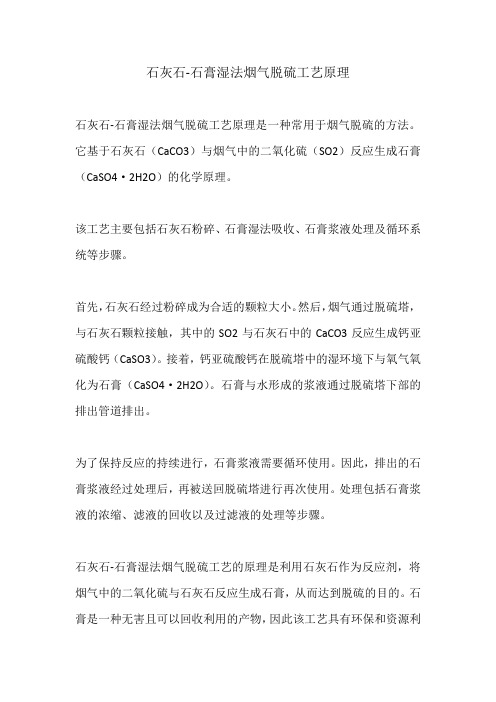
石灰石-石膏湿法烟气脱硫工艺原理
石灰石-石膏湿法烟气脱硫工艺原理是一种常用于烟气脱硫的方法。
它基于石灰石(CaCO3)与烟气中的二氧化硫(SO2)反应生成石膏(CaSO4·2H2O)的化学原理。
该工艺主要包括石灰石粉碎、石膏湿法吸收、石膏浆液处理及循环系统等步骤。
首先,石灰石经过粉碎成为合适的颗粒大小。
然后,烟气通过脱硫塔,与石灰石颗粒接触,其中的SO2与石灰石中的CaCO3反应生成钙亚硫酸钙(CaSO3)。
接着,钙亚硫酸钙在脱硫塔中的湿环境下与氧气氧化为石膏(CaSO4·2H2O)。
石膏与水形成的浆液通过脱硫塔下部的排出管道排出。
为了保持反应的持续进行,石膏浆液需要循环使用。
因此,排出的石膏浆液经过处理后,再被送回脱硫塔进行再次使用。
处理包括石膏浆液的浓缩、滤液的回收以及过滤液的处理等步骤。
石灰石-石膏湿法烟气脱硫工艺的原理是利用石灰石作为反应剂,将烟气中的二氧化硫与石灰石反应生成石膏,从而达到脱硫的目的。
石膏是一种无害且可以回收利用的产物,因此该工艺具有环保和资源利
用的双重优势。
总结起来,石灰石-石膏湿法烟气脱硫工艺原理是通过石灰石与烟气中的二氧化硫反应生成石膏,再将石膏浆液进行循环利用,以达到脱硫的效果。
这种工艺在工业生产中被广泛应用,为减少大气污染做出了重要贡献。
石灰石-石膏湿法烟气脱硫工艺原理及特点

石灰石-石膏湿法烟气脱硫工艺原理及特点一、工艺原理该工艺采用石灰石或石灰做脱硫吸收剂,石灰石破碎与水混合,磨细成粉壮,制成吸收浆液(当采用石灰为吸收剂时,石灰粉经消化处理后加水搅拌制成吸收浆)。
在吸收塔内,烟气中的SO2与浆液中的CaCO3(碳酸钙)以及鼓入的氧化空气进行化学反应生成二水石膏,二氧化硫被脱除。
吸收塔排出的石膏浆液经脱水装置脱水后回收。
脱硫后的烟气经除雾器去水、换热器加热升温后进入烟囱排向大气。
烟气从吸收塔下侧进入,与吸收浆液逆流接触,在塔内CaCO3与SO2、H2O进行反应,生成CaSO3·1/2H2O和CO2↑;对落入吸收塔浆浆池的CaSO3·1/2H2O和O2、H2O 再进行氧气反应,得到脱流副产品二水石膏。
化学反应方程式:2CaCO3+H2O+2SO2====2CaSO3·1/2H2O+2CO22CaSO3·1/2H2O+O2+3H2O====2CaSO4·2H2O二、FGD烟气系统的原理从锅炉引风机后烟道引出的烟气,通过增压风机升压,烟气换热器(GGH)降温后,进入吸收塔,在吸收塔内与雾状石灰石浆液逆流接触,将烟气脱硫净化,经除雾期除去水雾后,又经GGH升温至大于75摄氏度,再进入净烟道经烟囱排放。
脱硫系统在引风机出口与烟囱之间的烟道上设置旁路挡板门,当FGD装置运行时,烟道旁路挡板门关闭,FGD装置进出口挡板门打开,烟气通过增压风机的吸力作用引入FGD系统。
在FGD装置故障和停运时,旁路挡板门打开,FGD装置进出口挡板门关闭,烟气由旁路挡板经烟道直接进入烟囱,排向大气,从而保证锅炉机组的安全稳定运行。
FGD装置的原烟气挡板、净烟气挡板及旁路挡板一般采用双百叶挡板并设置密封空气系统。
旁路挡板具有快开功能,快开时间要小于10s,挡板的调整时间在正常情况下为75s,在事故情况下约为3~10s。
一、旁路挡板门的控制原理概述一、烟气脱硫挡板风门的结构简述1.烟气脱硫挡板风门——风门框架和截面的主体部分和叶片均按设计用不同材质、规格的钢板制造。
石灰石-石膏湿法脱硫工艺的基本原理
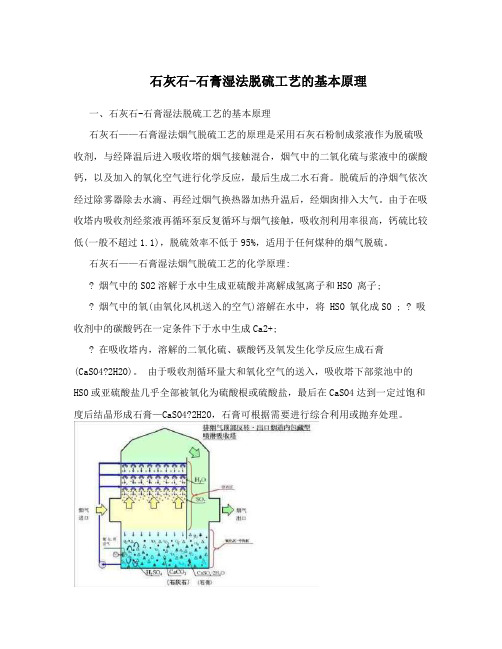
石灰石-石膏湿法脱硫工艺的基本原理一、石灰石-石膏湿法脱硫工艺的基本原理石灰石——石膏湿法烟气脱硫工艺的原理是采用石灰石粉制成浆液作为脱硫吸收剂,与经降温后进入吸收塔的烟气接触混合,烟气中的二氧化硫与浆液中的碳酸钙,以及加入的氧化空气进行化学反应,最后生成二水石膏。
脱硫后的净烟气依次经过除雾器除去水滴、再经过烟气换热器加热升温后,经烟囱排入大气。
由于在吸收塔内吸收剂经浆液再循环泵反复循环与烟气接触,吸收剂利用率很高,钙硫比较低(一般不超过1.1),脱硫效率不低于95%,适用于任何煤种的烟气脱硫。
石灰石——石膏湿法烟气脱硫工艺的化学原理:烟气中的SO2溶解于水中生成亚硫酸并离解成氢离子和HSO 离子;烟气中的氧(由氧化风机送入的空气)溶解在水中,将 HSO 氧化成SO ; ? 吸收剂中的碳酸钙在一定条件下于水中生成Ca2+;在吸收塔内,溶解的二氧化硫、碳酸钙及氧发生化学反应生成石膏(CaSO4?2H2O)。
由于吸收剂循环量大和氧化空气的送入,吸收塔下部浆池中的HSO或亚硫酸盐几乎全部被氧化为硫酸根或硫酸盐,最后在CaSO4达到一定过饱和度后结晶形成石膏—CaSO4?2H2O,石膏可根据需要进行综合利用或抛弃处理。
二、工艺流程及系统湿法脱硫工艺系统整套装置一般布置在锅炉引风机之后,主要的设备是吸收塔、烟气换热器、升压风机和浆液循环泵我公司采用高效脱除SO2的川崎湿法石灰石,石膏工艺。
该套烟气脱硫系统(FGD)处理烟气量为定洲发电厂,1和,2机组(2×600MW)100,的烟气量,定洲电厂的FGD系统由以下子系统组成:(1)吸收塔系统(2)烟气系统(包括烟气再热系统和增压风机)(3)石膏脱水系统(包括真空皮带脱水系统和石膏储仓系统)(4)石灰石制备系统(包括石灰石接收和储存系统、石灰石磨制系统、石灰石供浆系统) (5)公用系统(6)排放系统(7)废水处理系统1、吸收塔系统吸收塔采用川崎公司先进的逆流喷雾塔,烟气由侧面进气口进入吸收塔,并在上升区与雾状浆液逆流接触,处理后的烟气在吸收塔顶部翻转向下,从与吸收塔烟气入口同一水平位置的烟气出口排至烟气再热系统。
火电机组用湿式石灰石-石膏脱硫系统(WFGD)原理和运行分析
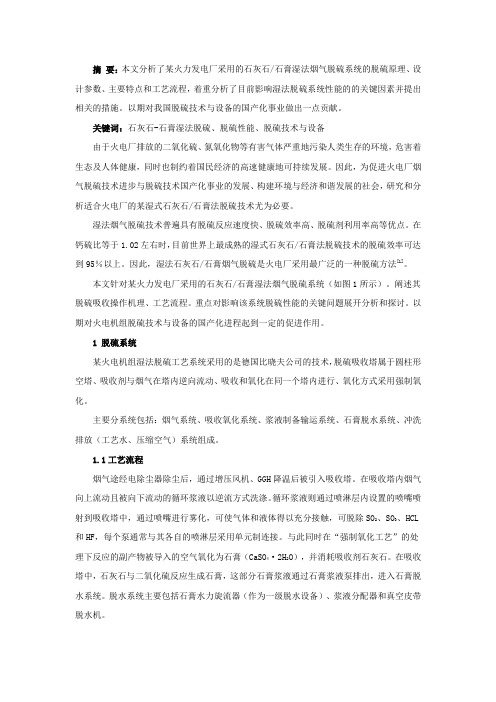
摘要:本文分析了某火力发电厂采用的石灰石/石膏湿法烟气脱硫系统的脱硫原理、设计参数、主要特点和工艺流程,着重分析了目前影响湿法脱硫系统性能的的关键因素并提出相关的措施。
以期对我国脱硫技术与设备的国产化事业做出一点贡献。
关键词:石灰石-石膏湿法脱硫、脱硫性能、脱硫技术与设备由于火电厂排放的二氧化硫、氮氧化物等有害气体严重地污染人类生存的环境,危害着生态及人体健康,同时也制约着国民经济的高速健康地可持续发展。
因此,为促进火电厂烟气脱硫技术进步与脱硫技术国产化事业的发展、构建环境与经济和谐发展的社会,研究和分析适合火电厂的某湿式石灰石/石膏法脱硫技术尤为必要。
湿法烟气脱硫技术普遍具有脱硫反应速度快、脱硫效率高、脱硫剂利用率高等优点。
在钙硫比等于1.02左右时,目前世界上最成熟的湿式石灰石/石膏法脱硫技术的脱硫效率可达到95%以上。
因此,湿法石灰石/石膏烟气脱硫是火电厂采用最广泛的一种脱硫方法[1]。
本文针对某火力发电厂采用的石灰石/石膏湿法烟气脱硫系统(如图1所示)。
阐述其脱硫吸收操作机理、工艺流程。
重点对影响该系统脱硫性能的关键问题展开分析和探讨。
以期对火电机组脱硫技术与设备的国产化进程起到一定的促进作用。
1 脱硫系统某火电机组湿法脱硫工艺系统采用的是德国比晓夫公司的技术,脱硫吸收塔属于圆柱形空塔、吸收剂与烟气在塔内逆向流动、吸收和氧化在同一个塔内进行、氧化方式采用强制氧化。
主要分系统包括:烟气系统、吸收氧化系统、浆液制备输运系统、石膏脱水系统、冲洗排放(工艺水、压缩空气)系统组成。
1.1工艺流程烟气途经电除尘器除尘后,通过增压风机、GGH降温后被引入吸收塔。
在吸收塔内烟气向上流动且被向下流动的循环浆液以逆流方式洗涤。
循环浆液则通过喷淋层内设置的喷嘴喷射到吸收塔中,通过喷嘴进行雾化,可使气体和液体得以充分接触,可脱除SO2、SO3、HCL 和HF,每个泵通常与其各自的喷淋层采用单元制连接。
与此同时在“强制氧化工艺”的处理下反应的副产物被导入的空气氧化为石膏(CaSO4·2H2O),并消耗吸收剂石灰石。
石灰石_石膏湿法烟气脱硫工艺与关键参数分析

1 京能 4 号炉湿法烟气脱硫的工艺流程
北京京能热电股份有限公司 (以下简称京能 公司) 4 号炉烟气脱硫工程采用的是引进的典型
石灰石2石膏湿法烟气脱硫工艺 (以下简称湿法脱 硫工艺) ,是最先实施的国内自主设计 ,设备基本 国产化的燃煤电厂湿法烟气脱硫项目 。
相对于其他湿法脱硫工艺的吸收塔 ( 如 : 三菱 U 形单级液柱塔 、美国巴威公司多孔托盘 喷淋塔 、德 国 比 晓 夫 公 司 电 磁 脉 冲 pH 分 层 控 制吸收塔) , 京能 4 号炉脱硫装置采用的是烟 气逆流喷淋空塔 ,内部仅设置除雾器 、喷淋层 、 氧化空气喷嘴及浆液搅拌器 ,最大限度地减少 吸收塔内部结构 ,以减少浆液结垢的可能性。 同时 设 置 石 灰 石 预 破 碎 系 统 、研 磨 制 浆 系 统 、 石膏脱 水 处 理 系 统 及 仓 式 存 储 系 统 。整 个 流 程设备设置完全具备常规湿法脱硫工艺的特 点 。其工艺流程见图 1 。
火电厂石灰石∕石灰-石膏湿法_烟气脱硫系统运行导则_概述及解释说明

火电厂石灰石∕石灰-石膏湿法烟气脱硫系统运行导则概述及解释说明1.1 概述:烟气脱硫是指通过对石灰石或石灰-石膏湿法进行处理,去除火电厂烟气中的硫化物,以减少大气污染和保护环境。
该系统运行导则旨在提供指导和规范,确保火电厂石灰石/石灰-石膏湿法的脱硫系统能够高效、安全地运行。
1.2 文章结构:本文将按以下结构进行描述: 引言、正文、火电厂石灰石/石灰-石膏湿法烟气脱硫系统运行导则概述、解释说明和结论等。
1.3 目的:本文的主要目的是详细介绍火电厂石灰石/石灰-石膏湿法烟气脱硫系统运行导则,并提供相应的解释说明。
通过了解该系统的运行原理和注意事项,可以加强对其重要性和操作技术要求的认识,并有效地应用于实践中。
这一部分主要对文章引言部分进行了概述,简要介绍了文章所涉及的内容和目标。
2. 正文在火电厂中,烟气脱硫系统是一项关键的环保设备,用于降低燃煤过程中产生的二氧化硫(SO2)排放。
其中,火电厂石灰石/石灰-石膏湿法是一种广泛应用的技术,在全球范围内被广泛采用。
2.1 火电厂石灰石/石灰-石膏湿法的基本原理火电厂使用石灰石或者活性石灰作为脱硫剂,并与进入脱硫系统的废气相接触。
这些脱硫剂会与废气中的二氧化硫发生化学反应,生成硫酸钙或者其他低水溶性物质。
这些物质会被捕集并沉积在吸收塔中的喷射层上。
通过周期性地从喷射层上刮走含有脱除硫酸盐沉淀物的污泥,并将其送至富含二氧化碳的稀释乳液中,就可以得到可回收的CaCO3或Ca(OH)2溶液,并继续循环使用于吸收塔的喷射装置中。
2.2 石灰石/石灰-石膏湿法系统运行导则为确保火电厂石灰石/石灰-石膏湿法系统的高效稳定运行,以下是一些运行导则:2.2.1 控制废气流量和温度:废气流量和温度对于脱硫反应的进行至关重要。
必须通过合适的调节措施确保进入吸收塔的废气流量和温度在合适的范围内,以保证反应能够顺利进行。
2.2.2 确保脱硫剂供应充足:火电厂需要确保有足够的石灰石或者活性石灰供应给脱硫系统,以满足脱硫反应所需。
石灰石-石膏湿法脱硫技术的工艺流程、反应原理及主要系统
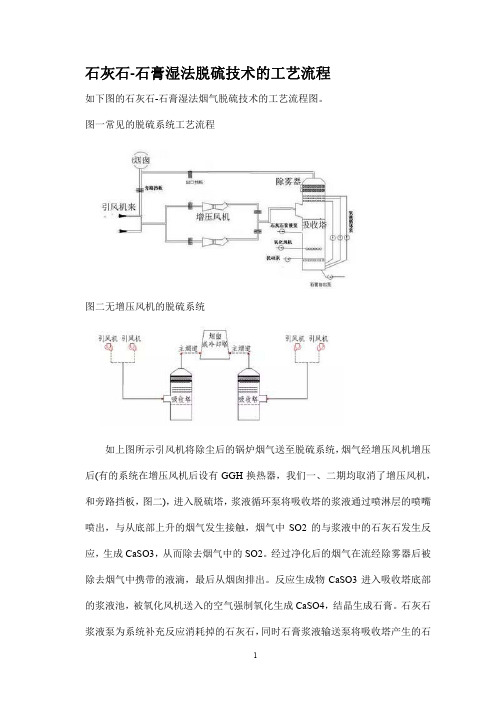
石灰石-石膏湿法脱硫技术的工艺流程如下图的石灰石-石膏湿法烟气脱硫技术的工艺流程图。
图一常见的脱硫系统工艺流程图二无增压风机的脱硫系统如上图所示引风机将除尘后的锅炉烟气送至脱硫系统,烟气经增压风机增压后(有的系统在增压风机后设有GGH换热器,我们一、二期均取消了增压风机,和旁路挡板,图二),进入脱硫塔,浆液循环泵将吸收塔的浆液通过喷淋层的喷嘴喷出,与从底部上升的烟气发生接触,烟气中SO2的与浆液中的石灰石发生反应,生成CaSO3,从而除去烟气中的SO2。
经过净化后的烟气在流经除雾器后被除去烟气中携带的液滴,最后从烟囱排出。
反应生成物CaSO3进入吸收塔底部的浆液池,被氧化风机送入的空气强制氧化生成CaSO4,结晶生成石膏。
石灰石浆液泵为系统补充反应消耗掉的石灰石,同时石膏浆液输送泵将吸收塔产生的石膏外排至石膏脱水系统将石膏脱水或直接抛弃。
同时为了防止吸收塔内浆液沉淀在底部设有浆液搅拌系统,一期采用扰动泵,二期采用搅拌器。
石灰石-石膏湿法脱硫反应原理在烟气脱硫过程中,物理反应和化学反应的过程相对复杂,吸收塔由吸收区、氧化区和结晶区三部分组成,在吸收塔浆池(氧化区和结晶区组成)和吸收区,不同的层存在不同的边界条件,现将最重要的物理和化学过程原理描述如下:(1)SO2溶于液体在吸收区,烟气和液体强烈接触,传质在接触面发生,烟气中的SO2溶解并转化成亚硫酸。
SO2+H2O<===>H2SO3除了SO2外烟气中的其他酸性成份,如HCL和HF也被喷入烟气中的浆液脱除。
装置脱硫效率受如下因素影响,烟气与液体接触程度,液气比、雾滴大小、SO2含量、PH值、在吸收区的相对速度和接触时间。
(2)酸的离解当SO2溶解时,产生亚硫酸,同时根据PH值离解:H2SO3<===>H++HSO3-对低pH值HSO3-<===>H++SO32-对高pH值从烟气中洗涤下来的HCL和HF,也同时离解:HCl<===>H++Cl-F<===>H++F-根据上面反应,在离解过程中,H+离子成为游离态,导致PH值降低。
石灰石石膏湿法脱硫技术

编辑ppt
22
图1-6 晶种生成速率和晶体增长速率与相对过饱和度σ的关系
编辑ppt
23
根据以上分析,保持亚稳平衡区域中相对过饱和度为适
当值时,可使浆液中生成较大的晶体。为保持脱硫装置的正
常运行,维持这些条件非常重要。
工艺上一般控制相对过饱和度σ=0.1~0.3(或相对饱和度
RS为1.1~1.3),以保证生成的石膏易于脱水,同时防止系
双膜理论的基本要点如下: ① 相互接触的气、液两流体间存在着稳定的相界面,界 面两侧各有一个很薄的有效滞流膜层,吸收质以分子扩散方 式通过此二膜层。 ② 在相界面处,气、液两相达到平衡。 ③ 在膜层以外的中心区,由于流体充分湍动,吸收质浓 度是均匀的,即两相中心区内浓度梯度皆为零,全部浓度变 化集中在两个有效膜层内。
石灰石-石膏湿法脱硫
工艺流程
编辑ppt
提纲
一、石灰石-石膏湿法脱硫工艺的基本原理 二、石灰石浆液制备系统 三、烟气系统及设备 四、吸收系统 五、石膏脱水系统 六、脱硫废水系统
编辑ppt
一、石灰石-石膏湿法脱硫工艺的基本原理
编辑ppt
石灰石-石膏湿法烟气脱硫工艺的原理是采用石灰石(块)粉 制成浆液作为脱硫吸收剂,与经降温后进入吸收塔的烟气接 触混合,烟气中的二氧化硫与浆液中的碳酸钙,以及加入的 氧化空气进行化学反应,最后生成二水石膏。脱硫后的净烟 气依次经过除雾器除去水滴、再经过烟气换热器加热升温后, 经烟囱排入大气。由于在吸收塔内吸收剂经浆液再循环泵反 复循环与烟气接触,吸收剂利用率很高,钙硫比较低(一般 不超过1.03),脱硫效率不低于95%,适用于任何煤种的烟 气脱硫。
0
0.2 0.4 0.6 0.8
1 2
1 mol/L
660MW火力发电厂石灰石灰石—石膏法脱硫技术分析

660MW火力发电厂石灰/石灰石—石膏法脱硫技术分析引言近年来,环保成了当今社会最热门的话题,身边的空气受到污染就会通过呼吸系统进入人的身体,使人的呼吸系统以及整体的健康状况受到影响。
因此,在环境治理方面,相关的学者和专家投入了大量精力在大气污染的防治工作中。
1 石灰石-石膏法脱硫的工作原理采用石灰石或石灰作为脱硫吸收剂,石灰石经破碎磨细成粉状与水混合搅拌成吸收浆液,当石灰为吸收剂时,石灰粉经消化处理后加水制成吸收剂浆液。
在吸收塔内,吸收浆液与烟气混合,烟气中的二氧化硫与浆液中的碳酸钙以及鼓入的氧化空气进行化学反应被脱除,最终反应产物为石膏。
在脱硫过程中,主要起作用的是石灰石,其与废气中的二氧化硫反应,最终生成亚硫酸氢钙;然后亚硫酸钙和亚硫酸氢钙与氧气反应最终生成石膏(CaSO4·2H2O)。
当完成脱硫和氧化过程后,吸收塔会将石膏浆液排出,排出的浆液再经过浓缩、脱水,从而达到含水量小于10%的标准,再送运至储存库,而具体的处理手段因每个火电厂的实际情况而不同,经过脱硫处理的烟气仍然不能直接排放,还要经过除雾器进行除雾,通过火电厂的烟囱排出。
2 脱硫石膏技术中出现的问题2.1石膏浆液质量石膏质量直接取决于石膏浆液质量。
石膏浆液质量的首要指标为石膏纯度,主要由石膏浆液中硫酸盐含量决定。
石灰石利用率反映了石灰石与二氧化硫反应生成硫酸盐的效率,衡量指标为石膏浆液中碳酸盐含量。
脱硫系统运行时,应控制碳酸盐含量低于3%,保证脱硫系统安全运行。
2.2 石灰石化学成分石灰石化学成分影响脱硫石膏品质。
天然石灰石一般都含有少量的硅、铝、镁、铁等杂质,湿法脱硫工艺在设计时,除要求石灰石品质满足表1所示指标外,还要求石灰石中SiO2含量不高于4%,铁铝氧化物含量不高于1.5%。
2.3 粒径石灰石颗粒大小和表面积既影响脱硫性能,又影响脱硫石膏质量。
石灰石粒径过大,不易溶解,在接触反应过程中,需要的pH值低,但低pH值既降低脱硫效率,又影响石膏浆液质量。
石灰石石膏湿法脱硫工艺

石灰石石膏湿法脱硫工艺一、工艺简介石灰石石膏湿法脱硫工艺是目前应用最广泛的脱硫技术之一,其原理是利用石灰石和石膏反应生成硬度较高的钙硫石,从而达到减少二氧化硫排放的目的。
该工艺具有投资成本低、运行成本低、处理效率高等优点,在电力、钢铁、化工等行业得到广泛应用。
二、原材料准备1. 石灰石:选用纯度高、颗粒均匀的优质石灰石。
2. 石膏:选用纯度高、含水量适中的优质天然石膏。
3. 水:选用清洁无杂质的自来水或经过处理后的水源。
三、工艺流程1. 粉碎:将采购回来的石灰石和石膏进行粉碎,使其颗粒大小均匀,便于后续反应。
2. 配料:按一定比例将粉碎好的石灰石和石膏混合在一起,制成配料。
3. 反应:将配料加入搅拌槽中,加入适量的水,进行搅拌反应。
反应过程中,石灰石和石膏发生化学反应,生成硬度较高的钙硫石。
4. 沉淀:将反应后的钙硫石沉淀到底部,分离出上清液。
5. 过滤:将上清液通过过滤器过滤,去除其中的杂质和悬浮物。
6. 浓缩:将过滤后的液体进行浓缩处理,使其达到一定浓度。
7. 干燥:将浓缩后的液体进行干燥处理,制成成品。
四、关键工艺参数控制1. 配料比例:配料比例是影响反应效果和产品质量的关键因素之一。
通常采用1:1~1:1.5的比例进行配料。
2. 反应温度:反应温度对反应速率和产物质量有很大影响。
通常采用55℃左右的温度进行反应。
3. 反应时间:反应时间也是影响产物质量和工艺效率的重要因素之一。
通常采用2~4小时左右的时间进行反应。
4. 搅拌速度:搅拌速度对于保证反应均匀和产物质量也有很大影响。
通常采用20~30转/分的速度进行搅拌。
五、工艺优化及改进1. 采用先进的粉碎设备,提高石灰石和石膏的粉碎效率,提高配料的均匀性。
2. 采用自动化控制系统,实现对关键工艺参数的实时监测和调节,提高生产效率和产品质量。
3. 优化反应槽结构,提高反应效率和产物质量。
4. 加强废水处理,减少对环境的污染。
六、安全措施1. 在操作过程中要注意防护眼睛、皮肤等部位,避免接触到化学品。
- 1、下载文档前请自行甄别文档内容的完整性,平台不提供额外的编辑、内容补充、找答案等附加服务。
- 2、"仅部分预览"的文档,不可在线预览部分如存在完整性等问题,可反馈申请退款(可完整预览的文档不适用该条件!)。
- 3、如文档侵犯您的权益,请联系客服反馈,我们会尽快为您处理(人工客服工作时间:9:00-18:30)。
电厂脱硫培训一石灰石/石膏湿法FGD原理和主要参对于一般的湿法脱硫技术喷淋塔而言,吸收液通过喷嘴雾化喷入脱硫塔,分散成细小的液滴并覆盖脱硫塔的整个断面。
这些液滴与塔内烟气逆流接触,发生传质与吸收反应,烟气中的SO2、SOs及HC1、HF被吸收。
S02吸收产物的氧化和中和反应在脱硫塔底部的氧化区完成并最终形成石膏。
为了维持吸收液恒定的PH值并减少石灰石耗量,石灰石被连续加入脱硫塔,同时脱硫塔内的吸收剂浆液被搅拌机、氧化空气和脱硫塔循环泵不停地搅动,以加快石灰石在浆液中的均布和溶解第一节主要运行变量概念1、脱硫塔烟气流速脱硫塔烟气流速是脱硫塔内饱和烟气的平均流速,在标准状态下,它等于饱和烟气的体积流量除以垂直于烟气流向的脱硫塔断面面积。
上述计算中,脱硫塔横断面积不扣除塔内支撑件、喷淋目管和其他内部构件所占有的面积,因此又称为空塔烟气平均流速。
2、液气比液气比表示洗涤单位体积饱和烟气(m3)的浆液体积数(1),即1/G。
3、脱硫塔PH值脱硫塔PH值表示脱硫塔中H'的浓度,是FGD工艺控制的一个重要参数,PH的高低直接影响系统的多项功能。
4、脱硫塔浆液循环停留时间脱硫塔浆液循环停留时间(t)表示脱硫塔浆液全部循环一次的平均的时间,此时间等于脱硫塔中浆液体积(V)除以循环浆液流量(1),即t(min)=60V∕1o5、浆液在脱硫塔中的停留时间浆液在脱硫塔中的停留时间(t)又称为固体物停留时间。
它等于脱硫塔浆液体积(V)除以脱硫塔排出泵流量(B),BPt(h)=V∕Bo固体停留时间也等于脱硫塔中存有固体物的质量(kg)除以固体副产物的产出率(kg∕h)06、吸收剂利用率吸收剂利用率(∏)等于单位时间内从烟气中吸收的SO2摩尔数除以同时间内加入系统的吸收剂中钙的总摩尔数,即n(100%)=已脱除的SO?的摩尔数/加入系统中的Ca的摩尔数X1OO机吸收剂利用率也可以理解为在一定时间内参与脱硫反应的CaC0,的数量占加入系统中的Caeo3总量的百分比。
7、氧化率氧化率(H)等于脱硫塔中氧化成硫酸盐的SO2摩尔数除以已吸收的SO2总摩尔数,即n=已氧化的SO2摩尔数/已吸收的SO2摩尔数。
氧化率也可看作离开工艺过程的硫酸盐总摩尔数除以烟气中已吸收的S(λ总摩尔数,用固体副产物中硫酸盐和亚硫酸盐摩尔数来表示,即n二副产物中SO1摩尔数/副产物中S(VSO1摩尔数。
8、氧化空气利用率氧化空气利用率(n)是指氧化已吸收的SO2理论上所需要的氧化空气量与强制氧化实际鼓入的氧化空气之比,也可指理论上需要的气量与实际鼓入量之比。
氧硫比是氧化空气利用率的另一种表示方法,指氧化ImOIS实际鼓入的。
2的摩尔数。
理论上0.5mo1θ2可氧化In1oIS(⅛,如果强制氧化InIoIS实际鼓入的空气中。
2的摩尔数为1.5,那么氧硫比二1.5,氧化空气或。
2的利用率n=0.5/1.5,因此n(100%)=0.5/氧硫比XIOO虬第二节FGD系统中的化学反应原理一、气体吸收过程的机理吸收过程中进行的方向与极限取决于溶质(气体)在气液两相中的平衡关系,当气相中溶质的实际分压高于与液相成平衡的溶质分压时,溶质便由气相向液相转移,即发生吸收过程。
实际分压与平衡分压相差越大,吸收的速率也越大,或称吸收的推动力也越大。
反之,如果气相中溶质的分压低于与液相成平衡的溶质分压时,溶质便由液相向气相转移,即吸收的逆过程,这种过程称为解吸(或脱吸)。
不论是吸收还是解吸,均与气液平衡有关。
气体吸收的平衡关系是指气体在液相中的溶解度。
平衡状态下气相中的溶质分压称为平衡分压或饱和分压,液相中溶质浓度称为平衡浓度或饱和浓度。
它们的大小随温度和压力而改变的,所谓气体在液相的溶解度,就是一定条件下气体在液体中饱和浓度。
气体在液体中溶解度表明一定条件下,吸收过程可能达到的极限程度。
要确定吸收设备内任何位置气、液实际浓度与其平衡浓度的差距,需明了系统的平衡关系。
在一定温度下,溶液的平衡浓度(即溶解度)随溶解的气体的压力增大而增大。
在一定温度下,表示溶液中气体溶质的组成与气体平衡压力关系的曲线称为气体的溶解度曲线或平衡曲线,各种系统的曲线一般都是根据实验结果做出。
互成平衡的气、液两相彼此依存,而且任何平衡状态都是有条件的。
1)亨利定律对于单组分的物理吸收有P*=f(t,X,P)的关系,当总压不很高时(如小于5atm),上式又可简化为P*=f(t,X);若确定在一定温度下,则P*只是的X函数,即P*=f(X),即被吸收气体的平衡分压只与其在液相中的浓度有关,对于稀溶液,上列平衡关系式可以是一条通过原点的直线,即气液两相的浓度成正比,此即著名的亨利定律,它表示总压不很高时,一定温度下,当溶液达到平衡时,稀溶液上方溶质A的平衡分压与其在溶液中浓度成正比。
P*=EX式中:X一被吸收组分在液相中摩尔分率(无因次)E—亨利系数,单位与P*相同,Pa在恒定温度下,对指定的物系进行实验,测得一系列平衡状态下的X与P*,将其在普通的直角坐标系中进行表示,求出浓度趋近于O时的P*∕X值,便是系统在该温度下的亨利系数。
对于一定的体系,E是温度的函数,一般来说,温度上升则E增大,表明温度升高不利于气体的吸收,在同一溶剂中,难溶气体E值很大,反之则小。
2)传质机理与吸收速率吸收操作是溶质从气相转移到液相的过程,其中包括溶质由气相主体向气液界面的传递,及由界面向液相主体的传递,因此,要研究传质机理,首先就要搞清楚物质在单一相(气相或液相)中的传递规律。
物质在单一相的传递是靠扩散作用。
发生在流体中的扩散有分子扩散与涡流扩散两种。
前者发生在静止或滞流流体中,凭借流体分子的热运动传递物质,后者发生在湍流流体中,凭借流体质点的湍动和旋涡传递物质。
在静止或滞流流体中,分子运动是漫无边际的,若一处某种分子的浓度较邻近的另一处为高,则这种离子离开的便比进入的多,其结果自然是物质从浓度较高的区域扩散到浓度较低的区域,两处的浓度差,便成了扩散的推动力。
用来描述分子扩散速率的定律是著名的菲克定律,或称菲克第一定律,即气相中稳定分子扩散;等分子反向扩散发生在静止的或在垂直于浓度方向上作滞流运动的流体中,是一种最单纯的分子扩散过程。
一组分通过另一停滞组分的扩散,这种情况出现于气体的吸收过程,例如氨和空气的混合物沿盘内的水面成滞流缓慢流过,空气不溶于水,在水面上方积累起来一薄层,氨通过这一停滞的空气薄层扩散到水面并溶解下来,这一部分氨的溶解是通过分子扩散实现的。
另外,随着氨分子的溶解,将会在界面附近出现空缺,于是将有混合气体的沿着扩散方向流动过来,以补充空缺。
这种现象成为包括氨和空气在内的总体流动。
由于总体流动的发生,加大了氨的传递速率。
在总体流动中,氨和空气所占的份额与其摩尔分率相同。
显然,在氨溶解过程中,氨的传递总量应等于氨的分子扩散通量和总体流动中氨的传递通量之和。
一组分通过另一停滞组分的传质速率之所以增大,是因为出现了与扩散方向一致的总体流动。
物质在湍流流体中传递,主要是依靠流体质点的无规则运动,湍流中发生的旋涡,引起各部流体间的剧烈混合,在有浓度差存在的情况下,物质便向其浓度降低的方向传递,这种凭借流体质点的湍动和旋涡来传递物质的现象,称为湍流扩散。
对流扩散是湍流主体与相界面之间的涡流扩散和分子扩散这两种传质作用的总称。
吸收过程是一个相际传质过程,而工业上所遇到的吸收过程是一个相间的传质过程,即溶质先从气相主体扩散到气液界面,穿过界面,再由界面向液相主体扩散。
关于吸收这样的相际传质机理,刘易斯和惠特曼在本世纪二十年代提出的双膜理论一直占有重要地位。
双膜理论的基本论点为:相互接触的气液两相流间存在稳定的相界面,界面两侧各有一个很薄的有效滞流膜层,吸收质以分子扩散方式通过此二膜层;在相界面处,气液两相达于平衡;在膜层以外的中心区,由于流体充分湍动,吸收质浓度是均匀的,即两相中心区内浓度梯度皆为零,全部浓度变化集中在两个有效膜区内。
通过以上假设,就把整个相际传质过程简化为经由气液两膜的分子扩散过程。
双膜理论认为相界面上处于平衡状态,这样整个相际传质过程的阻力便全部集中在两个有效膜层内,在两相主体浓度一定的情况下,两膜的阻力便决定了传质速度率的大小。
因此,双膜理论也可以称为双阻力理论。
双膜理论把复杂的相际传质过程大为简化,对于具有固定相界面的系统及速度不高的两流体间的传质,双膜理论与实际情况是相当符合的。
根据这一理论的基本概念所确定的相际传质速度关系,至今仍是传质设备设计的主要依据,这一理论对于生产实践具有重要的指导意义。
但是,对于具有自由相界面的系统,尤其是高度湍流的两流体间的传质,双膜理论表现出它的局限性,因为在这种情况下,相界面已不再是稳定的,界面两侧存在的稳定的有效滞流膜层及物质以分子扩散的形式通过此二膜层的假设都很难成立。
气体吸收可分为物理吸收和化学吸收两种。
如果吸收过程不发生显著的化学反应,单纯是被吸收气体溶解于液体的过程,称为物理吸收,如用水吸收S02。
物理吸收的特点是随着温度的升高,被吸气体的吸收量减少。
化学吸收是指溶质与溶剂发生化学反应的吸收操作,化学吸收可大幅度地提高溶剂对溶质组分的吸收能力。
物理吸收过程涉及两相间的物质传递,它包括三个步骤:(1)溶质由气相主体传递到两相界面,即气相内的物质传递;(2)溶质在界面上的溶解,由气相转入液相,即界面上发生的溶解过程;(3)溶质自界面被传递至液体主体,即液相内的物质传递。
一般来说,第(2)步界面上发生的溶解过程是很易进行的,其阻力很小。
因此,通常认为界面上气液两相的溶质浓度满足平衡关系。
这样,总传质过程速率将由两个单相即气相与液相内的传质速率所决定。
不论气相或液相,物质传递的机理有两种:(2)分子扩散当流体内部存在着某一组分的浓度差,则因分子的无规律热运动使该组分由浓度较高处传递至浓度较低处,这种现象称为分子扩散。
如香水的气味扩散。
分子扩散也可由温度梯度、压力梯度产生,由温度梯度产生的分子扩散叫热扩散,如湿木棍一头加热,另一端会冒出热气或水滴。
在此讨论的分子扩散仅因浓度梯度产生的。
分子扩散与传热中由于温度差而引起的热传导相似。
该现象可通过亨利定律解释:在总压不很高(V5atm=时,一定温度下,当溶解达到平衡时,稀溶液上方溶质的平衡分压与其在溶液中的浓度成正比。
图4-2溶液忠溶质的摩尔分率与气体中溶质的平衡压力根据亨利定律P*=EX,其中P*为平衡分压;E为亨利系数,随温度升高而增大;X为被吸收组分在液相中的摩尔分率。
该公式指出:被吸收气体的平衡分压只与其在液相中的浓度有关。
对于稀溶液,上式平衡关系可以是一条通过原点的直线(见上图S02的溶解度曲线),即气液两相的浓度成正比。
1855年费克揭示了分子扩散的基本规律一一费克定律。