电炉炼钢最终资料.doc
电炉炼钢原理及工艺
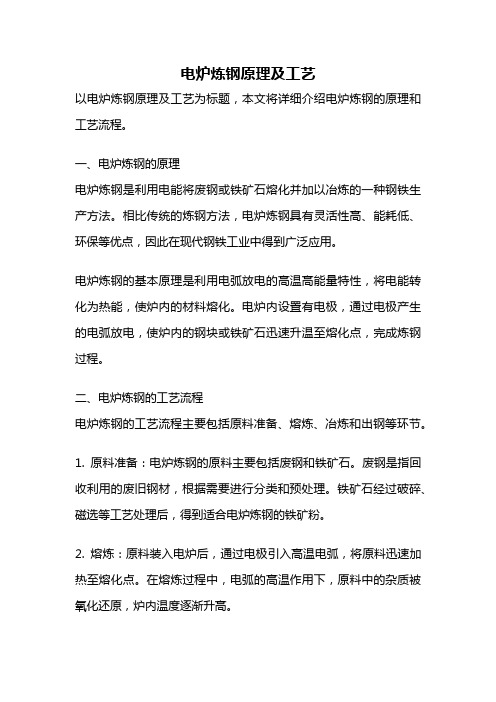
电炉炼钢原理及工艺以电炉炼钢原理及工艺为标题,本文将详细介绍电炉炼钢的原理和工艺流程。
一、电炉炼钢的原理电炉炼钢是利用电能将废钢或铁矿石熔化并加以冶炼的一种钢铁生产方法。
相比传统的炼钢方法,电炉炼钢具有灵活性高、能耗低、环保等优点,因此在现代钢铁工业中得到广泛应用。
电炉炼钢的基本原理是利用电弧放电的高温高能量特性,将电能转化为热能,使炉内的材料熔化。
电炉内设置有电极,通过电极产生的电弧放电,使炉内的钢块或铁矿石迅速升温至熔化点,完成炼钢过程。
二、电炉炼钢的工艺流程电炉炼钢的工艺流程主要包括原料准备、熔炼、冶炼和出钢等环节。
1. 原料准备:电炉炼钢的原料主要包括废钢和铁矿石。
废钢是指回收利用的废旧钢材,根据需要进行分类和预处理。
铁矿石经过破碎、磁选等工艺处理后,得到适合电炉炼钢的铁矿粉。
2. 熔炼:原料装入电炉后,通过电极引入高温电弧,将原料迅速加热至熔化点。
在熔炼过程中,电弧的高温作用下,原料中的杂质被氧化还原,炉内温度逐渐升高。
3. 冶炼:炉内温度达到要求后,加入适量的脱氧剂和合金元素,调整炉内成分,提高钢的质量。
同时,通过喷吹氧气等方式进行氧化剂的供给,控制冶炼过程中的氧化还原反应,进一步净化钢液。
4. 出钢:冶炼结束后,通过倒炉或倾炉等方式将炼好的钢液从电炉中倾出,进一步加工成所需的钢材。
出钢后,需要进行连铸、轧制等工艺,最终得到成品钢材。
三、电炉炼钢的特点和优势1. 灵活性高:电炉炼钢可灵活调整炉内温度和成分,适应不同的钢种和质量要求,具有较强的适应性和灵活性。
2. 能耗低:电炉炼钢相比传统炼钢方法,能耗更低。
电能可以高效转化为热能,提高能源利用效率,减少能源浪费。
3. 环保:电炉炼钢过程中没有燃料燃烧产生的废气和废渣,减少了对环境的污染。
另外,电炉炼钢可以使用废钢作为原料,有效促进了废钢的回收利用,减少了资源浪费。
4. 生产效率高:电炉炼钢的工艺流程简单,生产周期短,可以实现快速连续生产,提高生产效率。
电炉炼钢
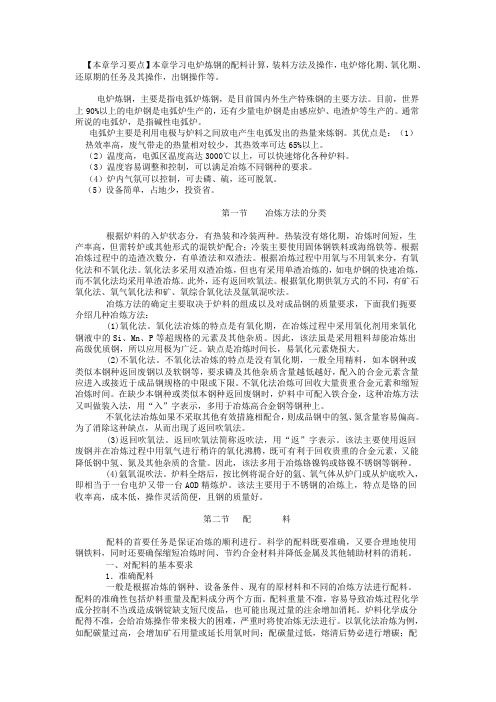
【本章学习要点】本章学习电炉炼钢的配料计算,装料方法及操作,电炉熔化期、氧化期、还原期的任务及其操作,出钢操作等。
电炉炼钢,主要是指电弧炉炼钢,是目前国内外生产特殊钢的主要方法。
目前,世界上90%以上的电炉钢是电弧炉生产的,还有少量电炉钢是由感应炉、电渣炉等生产的。
通常所说的电弧炉,是指碱性电弧炉。
电弧炉主要是利用电极与炉料之间放电产生电弧发出的热量来炼钢。
其优点是:(1)热效率高,废气带走的热量相对较少,其热效率可达65%以上。
(2)温度高,电弧区温度高达3000℃以上,可以快速熔化各种炉料。
(3)温度容易调整和控制,可以满足冶炼不同钢种的要求。
(4)炉内气氛可以控制,可去磷、硫,还可脱氧。
(5)设备简单,占地少,投资省。
第一节冶炼方法的分类根据炉料的入炉状态分,有热装和冷装两种。
热装没有熔化期,冶炼时间短,生产率高,但需转炉或其他形式的混铁炉配合;冷装主要使用固体钢铁料或海绵铁等。
根据冶炼过程中的造渣次数分,有单渣法和双渣法。
根据冶炼过程中用氧与不用氧来分,有氧化法和不氧化法。
氧化法多采用双渣冶炼,但也有采用单渣冶炼的,如电炉钢的快速冶炼,而不氧化法均采用单渣冶炼。
此外,还有返回吹氧法。
根据氧化期供氧方式的不同,有矿石氧化法、氧气氧化法和矿、氧综合氧化法及氩氧混吹法。
冶炼方法的确定主要取决于炉料的组成以及对成品钢的质量要求,下面我们扼要介绍几种冶炼方法:(1)氧化法。
氧化法冶炼的特点是有氧化期,在冶炼过程中采用氧化剂用来氧化钢液中的Si、Mn、P等超规格的元素及其他杂质。
因此,该法虽是采用粗料却能冶炼出高级优质钢,所以应用极为广泛。
缺点是冶炼时间长,易氧化元素烧损大。
(2)不氧化法。
不氧化法冶炼的特点是没有氧化期,一般全用精料,如本钢种或类似本钢种返回废钢以及软钢等,要求磷及其他杂质含量越低越好,配入的合金元素含量应进入或接近于成品钢规格的中限或下限。
不氧化法冶炼可回收大量贵重合金元素和缩短冶炼时间。
电炉炼钢原理及工艺
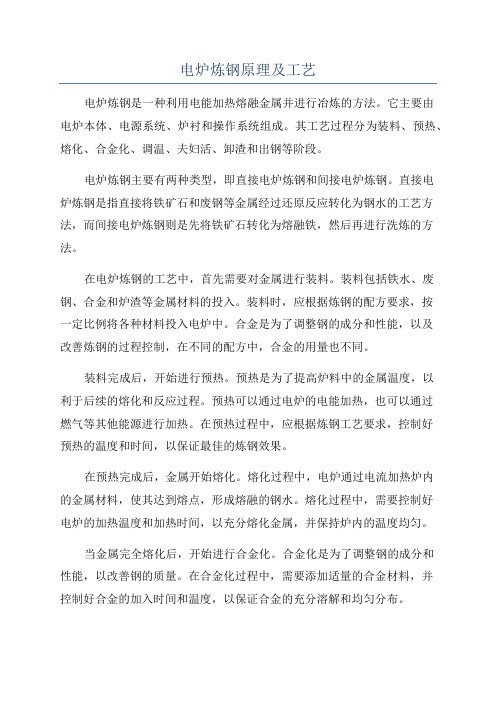
电炉炼钢原理及工艺电炉炼钢是一种利用电能加热熔融金属并进行冶炼的方法。
它主要由电炉本体、电源系统、炉衬和操作系统组成。
其工艺过程分为装料、预热、熔化、合金化、调温、夫妇活、卸渣和出钢等阶段。
电炉炼钢主要有两种类型,即直接电炉炼钢和间接电炉炼钢。
直接电炉炼钢是指直接将铁矿石和废钢等金属经过还原反应转化为钢水的工艺方法,而间接电炉炼钢则是先将铁矿石转化为熔融铁,然后再进行洗炼的方法。
在电炉炼钢的工艺中,首先需要对金属进行装料。
装料包括铁水、废钢、合金和炉渣等金属材料的投入。
装料时,应根据炼钢的配方要求,按一定比例将各种材料投入电炉中。
合金是为了调整钢的成分和性能,以及改善炼钢的过程控制,在不同的配方中,合金的用量也不同。
装料完成后,开始进行预热。
预热是为了提高炉料中的金属温度,以利于后续的熔化和反应过程。
预热可以通过电炉的电能加热,也可以通过燃气等其他能源进行加热。
在预热过程中,应根据炼钢工艺要求,控制好预热的温度和时间,以保证最佳的炼钢效果。
在预热完成后,金属开始熔化。
熔化过程中,电炉通过电流加热炉内的金属材料,使其达到熔点,形成熔融的钢水。
熔化过程中,需要控制好电炉的加热温度和加热时间,以充分熔化金属,并保持炉内的温度均匀。
当金属完全熔化后,开始进行合金化。
合金化是为了调整钢的成分和性能,以改善钢的质量。
在合金化过程中,需要添加适量的合金材料,并控制好合金的加入时间和温度,以保证合金的充分溶解和均匀分布。
合金化完成后,开始进行调温。
调温是为了得到合适的熔融铁水温度和钢水温度,以满足后续冶炼工艺的需求。
调温可以通过调节电炉的加热功率和炉内的温度控制装置来实现。
调温完成后,进行夫妇活。
夫妇活是为了提高钢水的纯净度和均匀性,以去除炉渣和杂质。
夫妇活可以通过在炉内注入草酸、石灰和氮气等化学物质,或者进行吹炼和搅拌来实现。
夫妇活完成后,开始卸渣。
卸渣是指将炉渣从熔融金属中移除的过程。
卸渣可以通过倾炉或者顶炉的方式来进行。
电弧炉炼钢的原理和工艺的详细过程
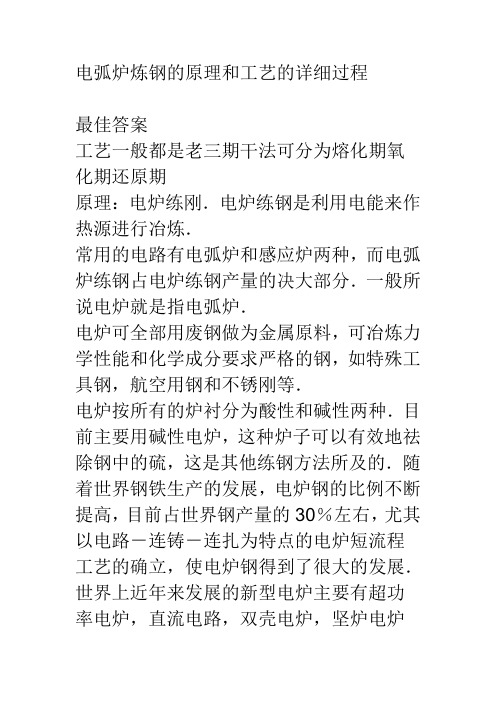
电弧炉炼钢的原理和工艺的详细过程最佳答案工艺一般都是老三期干法可分为熔化期氧化期还原期原理:电炉练刚.电炉练钢是利用电能来作热源进行冶炼.常用的电路有电弧炉和感应炉两种,而电弧炉练钢占电炉练钢产量的决大部分.一般所说电炉就是指电弧炉.电炉可全部用废钢做为金属原料,可冶炼力学性能和化学成分要求严格的钢,如特殊工具钢,航空用钢和不锈刚等.电炉按所有的炉衬分为酸性和碱性两种.目前主要用碱性电炉,这种炉子可以有效地祛除钢中的硫,这是其他练钢方法所及的.随着世界钢铁生产的发展,电炉钢的比例不断提高,目前占世界钢产量的30%左右,尤其以电路-连铸-连扎为特点的电炉短流程工艺的确立,使电炉钢得到了很大的发展.世界上近年来发展的新型电炉主要有超功率电炉,直流电路,双壳电炉,坚炉电炉等.随着炉外精练工艺的发展,电炉作为初练炉的功能更加突出.电炉-精练炉的联合超作,使电炉的冶炼周期大大缩短,有生产节奏转炉化的趋势,生产效率大大提高.(累啊~~本人就是电炉练钢的本质料全部来源书)电弧炉熔炼(1)电弧炉构造及工作原理电弧炉熔炼是利用石墨电极与铁料(铁液)之间产生电弧所发生的热量来熔化铁料和使铁液进行过热的。
生产上普遍使用的是三相电弧炉,其炉体部分的构造示于图1。
在电弧炉熔炼过程中,当铁料熔清后,进一步地提高温度及调整化学成分的冶炼操作是在熔渣覆盖铁液的条件下进行。
电弧炉依照炉渣和炉衬耐火材料的性质而分为酸性和碱性两种。
碱性电弧炉具有脱硫和脱磷的能力。
(2)弧炉熔炼的优缺点及其应用电弧炉熔炼的优点是熔化固体炉料的能力强,而且铁液是在熔渣覆盖条件下进行过热和调整化学成分的,故在一定程度上能避免铁液吸气和元素的氧化。
这为熔炼低碳铸铁和合金铸铁创造了良好的条件。
电弧炉的缺点是耗电能多,从熔化的角度看不如冲天炉经济,故铸铁生产上常采用冲天一电弧炉双联法熔炼。
由于碱性电弧炉衬耐急冷急热性差,在间歇式熔炼条件下,炉衬寿命短,导致熔炼成本高,故多采用酸性电弧炉与冲天炉相配合。
电炉炼钢最终资料全
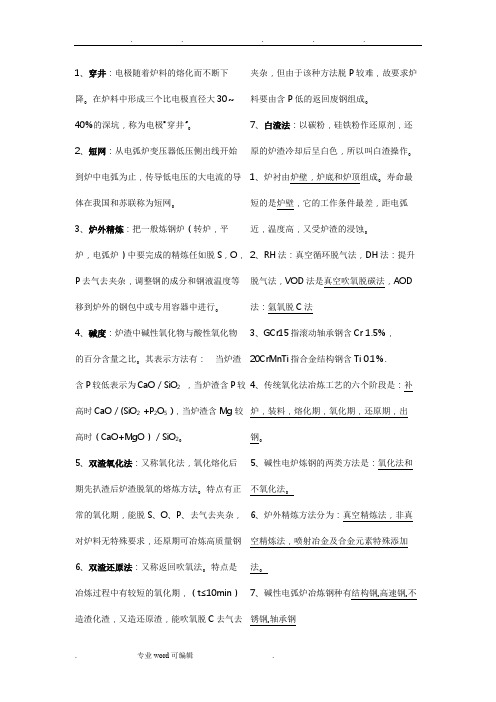
1、穿井:电极随着炉料的熔化而不断下降。
在炉料中形成三个比电极直径大30~40%的深坑,称为电极“穿井”。
2、短网:从电弧炉变压器低压侧出线开始到炉中电弧为止,传导低电压的大电流的导体在我国和苏联称为短网。
3、炉外精炼:把一般炼钢炉(转炉,平炉,电弧炉)中要完成的精炼任如脱S,O,P去气去夹杂,调整钢的成分和钢液温度等移到炉外的钢包中或专用容器中进行。
4、碱度:炉渣中碱性氧化物与酸性氧化物的百分含量之比。
其表示方法有:当炉渣含P较低表示为CaO/SiO2,当炉渣含P较高时CaO/(SiO2 +P2O5 ),当炉渣含Mg较高时(CaO+MgO)/SiO2。
5、双渣氧化法:又称氧化法,氧化熔化后期先扒渣后炉渣脱氧的熔炼方法。
特点有正常的氧化期,能脱S、O、P、去气去夹杂,对炉料无特殊要求,还原期可冶炼高质量钢6、双渣还原法:又称返回吹氧法。
特点是冶炼过程中有较短的氧化期,(t≤10min)造渣化渣,又造还原渣,能吹氧脱C去气去夹杂,但由于该种方法脱P较难,故要求炉料要由含P低的返回废钢组成。
7、白渣法:以碳粉,硅铁粉作还原剂,还原的炉渣冷却后呈白色,所以叫白渣操作。
1、炉衬由炉壁,炉底和炉顶组成。
寿命最短的是炉壁,它的工作条件最差,距电弧近,温度高,又受炉渣的浸蚀。
2、RH法:真空循环脱气法,DH法:提升脱气法,VOD法是真空吹氧脱碳法,AOD 法:氩氧脱C法3、GCr15指滚动轴承钢含Cr 1.5%,20CrMnTi指合金结构钢含Ti 0.1%.4、传统氧化法冶炼工艺的六个阶段是:补炉,装料,熔化期,氧化期,还原期,出钢。
5、碱性电炉炼钢的两类方法是:氧化法和不氧化法。
6、炉外精炼方法分为:真空精炼法,非真空精炼法,喷射冶金及合金元素特殊添加法。
7、碱性电弧炉冶炼钢种有结构钢,高速钢,不锈钢,轴承钢8、碱性电弧炉冶炼氧化法分为矿石氧化法,吹氧氧化法,综合氧化法。
9、脱氧的方法有:沉淀脱氧,扩散脱氧,综合脱氧。
电炉炼钢原理及工艺
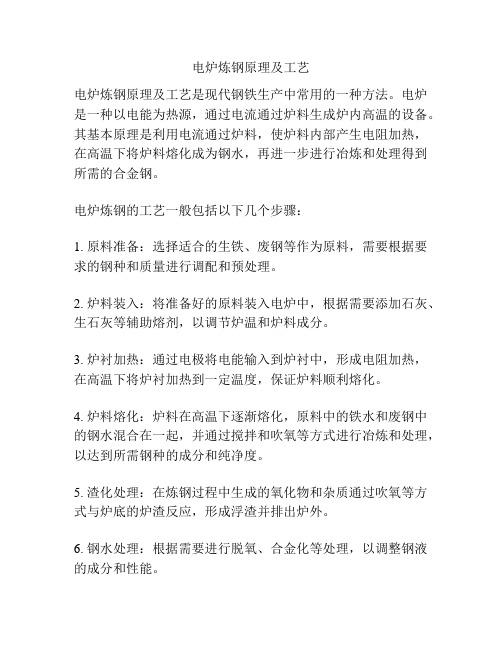
电炉炼钢原理及工艺
电炉炼钢原理及工艺是现代钢铁生产中常用的一种方法。
电炉是一种以电能为热源,通过电流通过炉料生成炉内高温的设备。
其基本原理是利用电流通过炉料,使炉料内部产生电阻加热,在高温下将炉料熔化成为钢水,再进一步进行冶炼和处理得到所需的合金钢。
电炉炼钢的工艺一般包括以下几个步骤:
1. 原料准备:选择适合的生铁、废钢等作为原料,需要根据要求的钢种和质量进行调配和预处理。
2. 炉料装入:将准备好的原料装入电炉中,根据需要添加石灰、生石灰等辅助熔剂,以调节炉温和炉料成分。
3. 炉衬加热:通过电极将电能输入到炉衬中,形成电阻加热,在高温下将炉衬加热到一定温度,保证炉料顺利熔化。
4. 炉料熔化:炉料在高温下逐渐熔化,原料中的铁水和废钢中的钢水混合在一起,并通过搅拌和吹氧等方式进行冶炼和处理,以达到所需钢种的成分和纯净度。
5. 渣化处理:在炼钢过程中生成的氧化物和杂质通过吹氧等方式与炉底的炉渣反应,形成浮渣并排出炉外。
6. 钢水处理:根据需要进行脱氧、合金化等处理,以调整钢液的成分和性能。
7. 出钢:达到要求后,将炉内的钢水倾倒到包铸机或连铸机中进行连铸或铸锭。
8. 后续处理:根据需要对钢水的温度、成分、物理性能等进行进一步调整和处理,以获得可供应市场的成品钢材。
总之,电炉炼钢是一种使用电能为热源的钢铁生产方法。
其原理是利用电阻加热炉料达到高温,将炉料熔化成钢水,再经过冶炼和处理得到所需的合金钢。
根据具体工艺要求,通过合理选料、调配、预处理、炉衬加热、炉料熔化、渣化处理、钢水处理等一系列步骤,最终获得合格的钢材产品。
电炉炼钢原理及工艺

电炉炼钢原理及工艺
电炉炼钢是利用电力作为热源,通过电弧加热的方式,将生铁
或废钢进行熔炼,加入适量的合金元素,最终得到符合特定要求的
钢铁产品的一种炼钢工艺。
电炉炼钢具有能耗低、环保、生产灵活
等优点,因此在现代钢铁工业中得到了广泛应用。
电炉炼钢的原理主要是通过电弧将炉料加热至熔化温度,同时
控制合金元素的加入,最终实现对炉料成分和温度的精确控制,从
而得到符合要求的钢铁产品。
电炉炼钢主要包括三种类型,直接电
弧炉、感应电炉和电渣重熔炉。
不同类型的电炉在原理和工艺上略
有不同,但基本的炼钢原理是相似的。
电炉炼钢的工艺流程一般包括,炉料装入、预热、电弧加热、
合金元素加入、脱氧、脱硫、炉渣处理等环节。
在整个工艺过程中,需要严格控制炉料的成分和温度,合理控制电弧加热的能量,确保
炼钢过程中的各项参数处于合适的范围,从而保证炼钢的质量。
电炉炼钢的原理和工艺虽然相对复杂,但是在实际生产中已经
得到了充分的验证和应用。
随着现代工艺技术的不断进步,电炉炼
钢的工艺也在不断完善和提高。
在炼钢过程中,需要考虑原料的选
择、电弧加热的控制、合金元素的加入、炉渣的处理等诸多因素,以确保最终生产出符合要求的钢铁产品。
总的来说,电炉炼钢是一种先进的炼钢工艺,其原理和工艺流程相对复杂,但是通过合理的控制和优化,可以实现对钢铁产品质量的精确控制。
随着工艺技术的不断进步,电炉炼钢必将在钢铁工业中发挥越来越重要的作用,为钢铁生产的发展做出更大的贡献。
电炉冶炼

1.2 电弧炉炼钢的特点电弧炉是靠电弧进行加热的,其温度可以高达2000℃以上,超过了其它炼钢炉用一般燃料燃烧加热时所能达到的最高温度。
同时熔化炉料时热量大部分是在被加热的炉料包围中产生的,而且无大量高温废气带走的热损失,所以热效率比平炉、转炉炼钢法要高。
还能精确的控制温度,因为炉内没有可燃烧的气体,所以可以根据工艺要求在各种不同的气氛中进行加热,也可在任何压力或真空中进行加热。
能保证冶炼含磷、硫、氧低的优质钢,能使用各种元素(包括铝、钛等容易被氧化的元素)来使钢合金化,冶炼出各种类型的优质钢和合金钢。
1.3 碱性电弧炉与酸性电弧炉1.4 传统碱性电弧炉炼钢过程介绍碱性电弧炉炼钢的工艺方法,一般分为:氧化法、不氧化法(又称装入法)及返回吹氧法。
氧化法冶炼操作由扒补炉、装料、熔化期、氧化期、还原期、出钢等6个阶段组成。
其特点是在氧化期,用加矿石或吹氧进行脱磷和脱碳,使熔池沸腾,以降低钢中气体和杂质,再经过脱氧还原和调整钢液的化学成分及温度,然后出钢。
用这种方法冶炼,可以得到含磷量及气体、夹杂物含量都很低的钢,还可以利用廉价废钢为原料,因此一般钢种大多采用氧化法冶炼。
其缺点是如果炉料中有合金返回料,则其中的某些合金元素会被氧化而损失于炉渣中。
不氧化法在冶炼过程中没有氧化期,能充分回收原料中的合金元素。
因此,可在炉料中配入大量的合金钢切头、切尾、废锭、注余钢、切屑和汤道钢等,减少铁合金的消耗,降低钢的成本。
炉料熔清后,经过还原调整钢液成分和温度后即可出钢。
冶炼时间较短,低合金钢、不锈钢、高速工具钢等均可以用此法冶炼。
其缺点是不能去磷、去夹杂物和除气,因此对炉料要求高,须配入清洁无锈、含磷低的钢铁料,并在冶炼过程中要求采取各种措施防止吸气。
同时钢液的化学成分基本上取决于配料的成分,这就要求炉料配料的化学成分和称量力求准确,致使这种冶炼方法用的比较少。
返回吹氧法是在炉料中配入大量的合金钢返回料。
依据碳和氧的亲和力在一定的温度条件下比某些合金元素和氧的亲和力大的理论,当钢液升到一定温度以后,向钢液进行吹氧,强化冶炼过程,达到在脱碳、去气、去夹杂物的同时,又回收大量合金元素的目的。
电炉炼钢原理及工艺
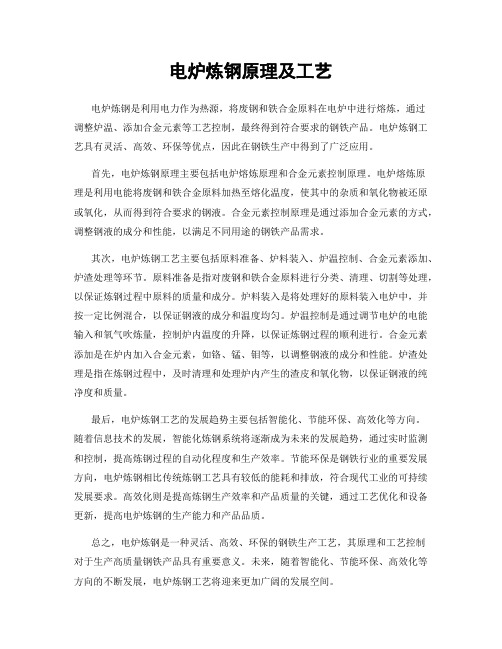
电炉炼钢原理及工艺电炉炼钢是利用电力作为热源,将废钢和铁合金原料在电炉中进行熔炼,通过调整炉温、添加合金元素等工艺控制,最终得到符合要求的钢铁产品。
电炉炼钢工艺具有灵活、高效、环保等优点,因此在钢铁生产中得到了广泛应用。
首先,电炉炼钢原理主要包括电炉熔炼原理和合金元素控制原理。
电炉熔炼原理是利用电能将废钢和铁合金原料加热至熔化温度,使其中的杂质和氧化物被还原或氧化,从而得到符合要求的钢液。
合金元素控制原理是通过添加合金元素的方式,调整钢液的成分和性能,以满足不同用途的钢铁产品需求。
其次,电炉炼钢工艺主要包括原料准备、炉料装入、炉温控制、合金元素添加、炉渣处理等环节。
原料准备是指对废钢和铁合金原料进行分类、清理、切割等处理,以保证炼钢过程中原料的质量和成分。
炉料装入是将处理好的原料装入电炉中,并按一定比例混合,以保证钢液的成分和温度均匀。
炉温控制是通过调节电炉的电能输入和氧气吹炼量,控制炉内温度的升降,以保证炼钢过程的顺利进行。
合金元素添加是在炉内加入合金元素,如铬、锰、钼等,以调整钢液的成分和性能。
炉渣处理是指在炼钢过程中,及时清理和处理炉内产生的渣皮和氧化物,以保证钢液的纯净度和质量。
最后,电炉炼钢工艺的发展趋势主要包括智能化、节能环保、高效化等方向。
随着信息技术的发展,智能化炼钢系统将逐渐成为未来的发展趋势,通过实时监测和控制,提高炼钢过程的自动化程度和生产效率。
节能环保是钢铁行业的重要发展方向,电炉炼钢相比传统炼钢工艺具有较低的能耗和排放,符合现代工业的可持续发展要求。
高效化则是提高炼钢生产效率和产品质量的关键,通过工艺优化和设备更新,提高电炉炼钢的生产能力和产品品质。
总之,电炉炼钢是一种灵活、高效、环保的钢铁生产工艺,其原理和工艺控制对于生产高质量钢铁产品具有重要意义。
未来,随着智能化、节能环保、高效化等方向的不断发展,电炉炼钢工艺将迎来更加广阔的发展空间。
电炉炼钢知识点总结

电炉炼钢知识点总结一、电炉炼钢的基本原理电炉炼钢是利用电能将生铁、废钢或铁合金作为主要原料,通过高温加热与熔融,加入合适的脱氧合金元素进行精炼,最终获得符合要求的钢水的工艺过程。
电炉炼钢主要依靠电弧能量加热熔化金属,通过电渣或氧下吹气使金属氧化物脱碳、脱硅、脱磷、脱硫,同时调整合金成分,最终得到符合要求的钢水。
二、电炉炼钢的主要工艺流程1.电弧炉的装料电弧炉装料时要根据炉子的规格与性能参数,配合合理的装料方案,通常按照一定比例混装生铁、废钢和铁合金,并加入适量的脱氧合金元素和渣料。
装料时要尽量均匀分布,防止料层不均匀导致炉子内部温度不均匀。
2.炉内燃烧与电弧熔炼电弧炉工作过程中,先点燃炉内燃料,形成初步熔融的金属料,然后接通电源,形成电弧加热金属料,使其完全熔化。
电弧能量直接作用在炼钢料上,既可以加热料中金属,也可以加热电炉底部和侧壁,使整个炉子的温度均匀。
3.氧气吹炼和脱氧合金元素加入在炉内形成熔池后,通过氧下吹或氧气桩等方式加入氧气进行吹炼,脱除炉内废气和不良成分,同时加入脱氧合金元素,使炉内金属达到合适的成分、温度和质量。
4.渣液处理和连铸过程最后一步是对炉内渣液进行处理,通过加入合适的矿物质进行还原、脱硅和脱氧等操作,最终得到净化的钢水。
随后将净化的钢水通过连续铸造工艺进行浇铸,成为成形的连铸坯料。
三、电炉炼钢的主要设备和工艺特点1.电弧炉电弧炉是电炉炼钢的关键设备,通过钢包、电极、电极架、转子、电子控制系统等部件组成,其优点是操作灵活、能耗低、生产周期短等。
2.电渣重熔炉电渣重熔炉是对废钢进行冶炼的主要设备,通过电渣电磁感应加热,使废钢迅速熔化。
其优点是炉内温度均匀、温度可控、冶炼环境稳定等。
3.电弧炉与LF精炼炉的联合工艺电弧炉与LF精炼炉的联合工艺是近年来发展的新工艺,通过将电炉炼钢与LF精炼技术结合起来,能够有效控制合金成分、温度和氧化物含量,提高钢水质量。
四、电炉炼钢的主要操作技术1.控制装料质量装料时要严格按照比例进行混装,控制原料质量和成分,防止过多的杂质与氧化物的夹杂。
电炉炼钢
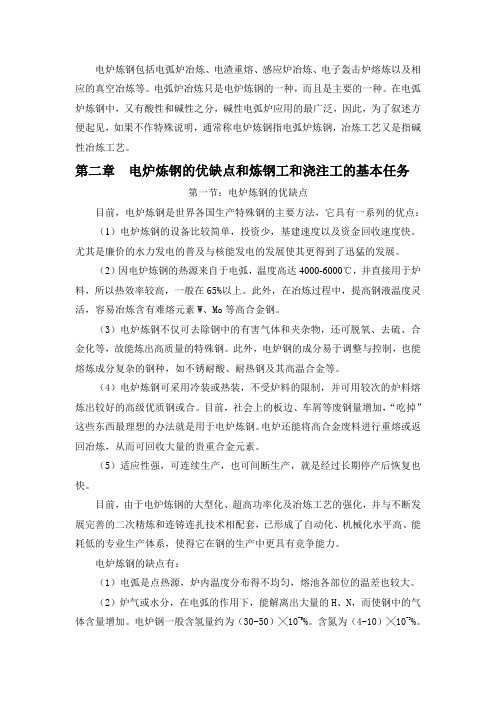
电炉炼钢包括电弧炉冶炼、电渣重熔、感应炉冶炼、电子轰击炉熔炼以及相应的真空冶炼等。
电弧炉冶炼只是电炉炼钢的一种,而且是主要的一种。
在电弧炉炼钢中,又有酸性和碱性之分,碱性电弧炉应用的最广泛,因此,为了叙述方便起见,如果不作特殊说明,通常称电炉炼钢指电弧炉炼钢,冶炼工艺又是指碱性冶炼工艺。
第二章电炉炼钢的优缺点和炼钢工和浇注工的基本任务第一节:电炉炼钢的优缺点目前,电炉炼钢是世界各国生产特殊钢的主要方法,它具有一系列的优点:(1)电炉炼钢的设备比较简单,投资少,基建速度以及资金回收速度快。
尤其是廉价的水力发电的普及与核能发电的发展使其更得到了迅猛的发展。
(2)因电炉炼钢的热源来自于电弧,温度高达4000-6000℃,并直接用于炉料,所以热效率较高,一般在65%以上。
此外,在冶炼过程中,提高钢液温度灵活,容易冶炼含有难熔元素W、Mo等高合金钢。
(3)电炉炼钢不仅可去除钢中的有害气体和夹杂物,还可脱氧、去硫、合金化等,故能炼出高质量的特殊钢。
此外,电炉钢的成分易于调整与控制,也能熔炼成分复杂的钢种,如不锈耐酸、耐热钢及其高温合金等。
(4)电炉炼钢可采用冷装或热装,不受炉料的限制,并可用较次的炉料熔炼出较好的高级优质钢或合。
目前,社会上的板边、车屑等废钢量增加,“吃掉”这些东西最理想的办法就是用于电炉炼钢。
电炉还能将高合金废料进行重熔或返回冶炼,从而可回收大量的贵重合金元素。
(5)适应性强,可连续生产,也可间断生产,就是经过长期停产后恢复也快。
目前,由于电炉炼钢的大型化、超高功率化及冶炼工艺的强化,并与不断发展完善的二次精炼和连铸连扎技术相配套,已形成了自动化、机械化水平高、能耗低的专业生产体系,使得它在钢的生产中更具有竞争能力。
电炉炼钢的缺点有:(1)电弧是点热源,炉内温度分布得不均匀,熔池各部位的温差也较大。
(2)炉气或水分,在电弧的作用下,能解离出大量的H、N,而使钢中的气体含量增加。
电炉钢一般含氢量约为(30-50)╳10-5%。
电炉炼钢的工作原理

电炉炼钢的工作原理电炉炼钢的工作原理是利用电能将铁矿石经过还原、脱硫、脱磷等工艺步骤,使其变为高品质的钢铁产品。
电炉炼钢是一种革命性的钢铁生产方式,相较于传统的炼铁炉,它更加环保、高效,并且可以调控炉料、操作简单,因而在钢铁工业中得到广泛应用。
电炉炼钢的基本工作原理是通过电阻加热和电弧加热作用下,将炉料加热到高温,并进行融化和化学反应。
通常,电炉采用三相交流电能作为能源,通过电极引入到炉内,使电能转化为热能。
在电极的引入点,形成弧电焰,推动氧和炉料之间的分解和还原反应。
电炉主体通常由炉壳、电极和熔化室等主要组成部分构成。
首先,炉壳是用来固定和保护电炉炉体、电极和隔热层的结构,它通常采用钢板焊接而成。
其次,电极是引入电能的通道,一般设有两个或多个电极,通过与炉料接触,使其受到电极电流的加热和融化。
最后,熔化室是指炉内容纳炉料和进行炉内化学反应的空间,其材质通常由耐火材料构成,以保证电炉内部的高温和耐腐蚀。
电炉炼钢的工作过程大致可以分为预处理、熔化和精炼三个阶段。
首先,在预处理阶段,先将原料炉料准备好,包括选矿、破碎、烘干等工艺,同时加入适量的底料和熔剂,以保证炉内化学反应和熔化过程的顺利进行。
预处理完成后,开始进行熔化阶段。
这个阶段主要是将炉料和底料投入电炉中,通过电弧加热和电极电流作用下的高温,使炉料在熔化室中迅速融化,并通过氧化和还原反应,将杂质和不需要的元素通常以气体和渣的形式排出。
最后,通过精炼阶段,对熔融的炉料进行进一步的净化和改良,一般包括脱硫、脱磷和调整合金成分等工艺,使得炉料的品质达到钢铁生产的要求。
电炉炼钢的一个显著特点是可以使用废钢等回收材料作为主要炉料,这极大地降低了钢铁生产的成本和资源消耗,也对环境产生了积极的影响。
同时,电炉具有反应灵活、操作方便、生产适应性强等特点,可以生产各种不同品种和规格的钢铁产品。
此外,电炉还具有生产周期短、炉渣综合利用和能源利用效率高等优点,因此在现代钢铁工业中得到了广泛应用。
电炉炼钢最终资料

1、穿井:电极随着炉料的熔化而不断下降。
在炉料中形成三个比电极直径大30~40%的深坑,称为电极“穿井”。
2、短网:从电弧炉变压器低压侧出线开始到炉中电弧为止,传导低电压的大电流的导体在我国和苏联称为短网。
3、炉外精炼:把一般炼钢炉(转炉,平炉,电弧炉)中要完成的精炼任如脱S ,O ,P 去气去夹杂,调整钢的成分和钢液温度等移到炉外的钢包中或专用容器中进行。
4、碱度:炉渣中碱性氧化物与酸性氧化物的百分含量之比。
其表示方法有: 当炉渣含P 较低表示为CaO /SiO 2 ,当炉渣含P 较高时CaO /(SiO 2 +P 2O 5 ),当炉渣含Mg 较高时(CaO+MgO )/SiO 2。
5、双渣氧化法:又称氧化法,氧化熔化后期先扒渣后炉渣脱氧的熔炼方法。
特点有正常的氧化期,能脱S 、O 、P 、去气去夹杂,对炉料无特殊要求,还原期可冶炼高质量钢6、双渣还原法:又称返回吹氧法。
特点是冶炼过程中有较短的氧化期,(t ≤10min )造渣化渣,又造还原渣,能吹氧脱C 去气去夹杂,但由于该种方法脱P 较难,故要求炉料要由含P 低的返回废钢组成。
7、白渣法:以碳粉,硅铁粉作还原剂,还原的炉渣冷却后呈白色,所以叫白渣操作。
1、炉衬由炉壁,炉底和炉顶组成。
寿命最短的是炉壁,它的工作条件最差,距电弧近,温度高,又受炉渣的浸蚀。
2、RH 法:真空循环脱气法,DH 法:提升脱气法,VOD 法是真空吹氧脱碳法,AOD 法:氩氧脱C 法 3、GCr15指滚动轴承钢含Cr 1.5%,20CrMnTi 指合金结构钢含Ti 0.1%. 4、传统氧化法冶炼工艺的六个阶段是:补炉,装料,熔化期,氧化期,还原期,出钢。
5、碱性电炉炼钢的两类方法是:氧化法和不氧化法。
6、炉外精炼方法分为:真空精炼法,非真空精炼法,喷射冶金及合金元素特殊添加法。
7、碱性电弧炉冶炼钢种有结构钢,高速钢,不锈钢,轴承钢8、碱性电弧炉冶炼氧化法分为矿石氧化法,吹氧氧化法,综合氧化法。
电炉炼钢研究报告

电炉炼钢研究报告《电炉炼钢研究报告》一、背景介绍电炉炼钢是利用高温电弧将废钢和生铁等原料进行熔炼,并通过加料、渣分离、调温等工艺控制,最终得到各种钢种的炉渣和钢水的炼钢技术。
电炉炼钢技术由于其生产效率高、环保绿色、可实现轻质化、自动化程度高等优点而被广泛应用。
二、电炉炼钢的原理1.电弧炉原理电弧炉是将高温电弧引入加热炉中,使原料加热熔化并进行反应的设备,通过电极、电弧、电极喷水、料包、加料、冷却水等部件组成。
2.电炉炼钢原理电炉炼钢原理是在电弧炉的基础上,通过合理的原料配比、电极参数选择、炉渣控制等一系列工艺参数进行精密控制,实现废钢和生铁等原料的熔融和转化为钢水。
三、电炉炼钢技术的优势与应用1.生产效率高电炉炼钢可以快速熔化废钢和生铁等原料,转化为钢水,生产效率高,可以大大提高生产效益。
2.环保绿色相对于传统炼钢技术,电炉炼钢不需要大量的燃料,能源消耗较少,废气排放和渣等污染物量也少,对环境影响小,具有环保绿色的特点。
3.可实现轻质化电炉炼钢通过掌握工艺参数,可以实现不同钢种的调制,从而达到特定的力学性能与成分要求。
且通过选用优质废钢作为原料和精密调控工艺,轻质序列化的高强高韧钢材也能够炼制出来。
4.自动化程度高电炉炼钢生产过程具有智能化、自动化程度高的特点,采用先进的全程自动化控制系统,并配有先进的物联网技术,可以实现工厂的智能化运营管理。
四、未来展望随着钢材行业的快速发展和市场对高品质、环保钢材的需求增加,电炉炼钢技术已经成为钢材生产的重要生产技术之一,发展前景十分广阔。
而随着技术的不断革新和提升,电炉炼钢将能够进一步提高生产效率和钢材质量,更好地服务于行业创新和国民经济的发展。
第一章 电炉炼钢知识
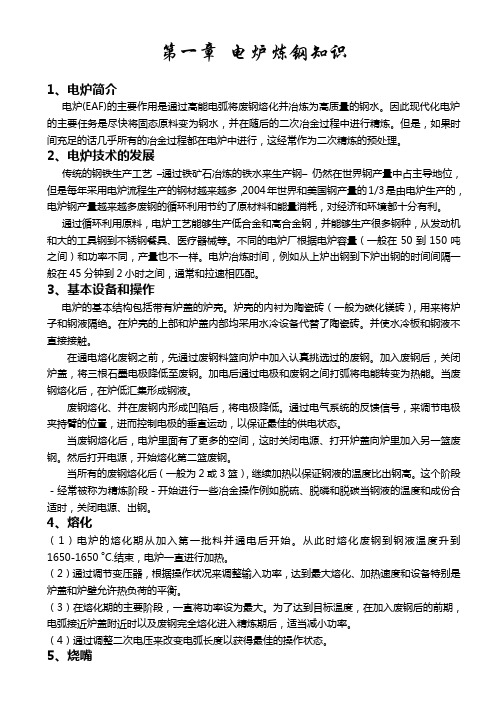
第一章电炉炼钢知识1、电炉简介电炉(EAF)的主要作用是通过高能电弧将废钢熔化并冶炼为高质量的钢水。
因此现代化电炉的主要任务是尽快将固态原料变为钢水,并在随后的二次冶金过程中进行精炼。
但是,如果时间充足的话几乎所有的冶金过程都在电炉中进行,这经常作为二次精炼的预处理。
2、电炉技术的发展传统的钢铁生产工艺–通过铁矿石冶炼的铁水来生产钢–仍然在世界钢产量中占主导地位,但是每年采用电炉流程生产的钢材越来越多,2004年世界和美国钢产量的1/3是由电炉生产的,电炉钢产量越来越多废钢的循环利用节约了原材料和能量消耗,对经济和环境都十分有利。
通过循环利用原料,电炉工艺能够生产低合金和高合金钢,并能够生产很多钢种,从发动机和大的工具钢到不锈钢餐具、医疗器械等。
不同的电炉厂根据电炉容量(一般在50到150吨之间)和功率不同,产量也不一样。
电炉冶炼时间,例如从上炉出钢到下炉出钢的时间间隔一般在45分钟到2小时之间,通常和拉速相匹配。
3、基本设备和操作电炉的基本结构包括带有炉盖的炉壳。
炉壳的内衬为陶瓷砖(一般为碳化镁砖),用来将炉子和钢液隔绝。
在炉壳的上部和炉盖内部均采用水冷设备代替了陶瓷砖。
并使水冷板和钢液不直接接触。
在通电熔化废钢之前,先通过废钢料篮向炉中加入认真挑选过的废钢。
加入废钢后,关闭炉盖,将三根石墨电极降低至废钢。
加电后通过电极和废钢之间打弧将电能转变为热能。
当废钢熔化后,在炉低汇集形成钢液。
废钢熔化、并在废钢内形成凹陷后,将电极降低。
通过电气系统的反馈信号,来调节电极夹持臂的位臵,进而控制电极的垂直运动,以保证最佳的供电状态。
当废钢熔化后,电炉里面有了更多的空间,这时关闭电源、打开炉盖向炉里加入另一篮废钢。
然后打开电源,开始熔化第二篮废钢。
当所有的废钢熔化后(一般为2或3篮),继续加热以保证钢液的温度比出钢高。
这个阶段-经常被称为精炼阶段-开始进行一些冶金操作例如脱硫、脱磷和脱碳当钢液的温度和成份合适时,关闭电源、出钢。
电炉炼钢原理基本知识

其次章电炉炼钢原理根本学问第一节炼钢有关的物理化学根本概念31.为什么要学习电炉炼钢有关的物理化学根本概念?将生铁废钢炼成钢,必需进展氧化熔炼。
使生铁废钢中的某些元素杂质去除到肯定程度。
它们是怎样进展精炼的,以及如何使它们到达需要的程度,这些都是炼钢生产过程中极重要问题。
应用化学热力学能够提醒炼钢过程中种种元素杂质氧化去除的可能性,去除的程度以及打算去除程度的各种因素;应用化学动力学可以提醒元素杂质氧化反响进展的机理、进展的速度以及打算速度的各种因素。
把握了这些规律,就可以找出炼钢所需要的合理条件,确定过程成效。
这对产品质量提高,能耗下降有根本性意义,这些原理是炼钢生产有力工具,是节能的理论依据。
32.什么是系和相的概念?用来争论化学变化的一组物质通称为系,例如电炉中的钢液、炉渣、炉气就是一个系。
假设一个系中的全部组份的物理性质是全都的,没有分界面,这个系就称为均一系,例如水与酒精的混合物是均一系。
假设一系中各个组成部份是不一样的,则称为不均一系。
电炉中的钢液、炉渣、炉气就属不均一系。
不均一系中的均一局部称相,它以显著的分界面与其他局部分开,而且它的性质也与其他部份不同。
例由铁、碳、硅、猛……等元素组成的钢液是一个相,由于它在物理性质上是全都的。
33.什么是溶液?怎么来表示液态溶液的浓度?由两种或两种以上的物质构成的,其成份可变的均匀混合物称为溶液。
例如炉渣就是有各物氧化物及其相互间形成的化合物组成的溶液。
液态溶液的浓度常用重量百分数来表示。
气体溶液的浓度通常以容积百分数表示。
依据道尔顿定律在同等条件下容积、温度、气体混合物的总压力则等于各气体的分压总和。
例纯空气由21%氧;78%氮;1%的其化气体构成。
则在标准大气压下,这三者分压为:氧 0.21 大气压;氮0.78 大气压;其他气体0.01 大气压。
因此气体溶液的浓度也可用不同气体组成物的分压来表示。
34.什么是反响的热效应?反响的热效应怎么表示?化学反响的进展的同时,有放热或吸热现象。
电炉炼钢法
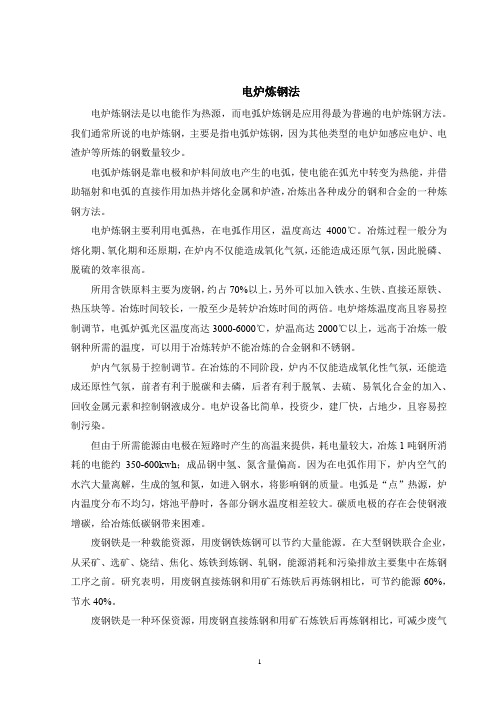
电炉炼钢法电炉炼钢法是以电能作为热源,而电弧炉炼钢是应用得最为普遍的电炉炼钢方法。
我们通常所说的电炉炼钢,主要是指电弧炉炼钢,因为其他类型的电炉如感应电炉、电渣炉等所炼的钢数量较少。
电弧炉炼钢是靠电极和炉料间放电产生的电弧,使电能在弧光中转变为热能,并借助辐射和电弧的直接作用加热并熔化金属和炉渣,冶炼出各种成分的钢和合金的一种炼钢方法。
电炉炼钢主要利用电弧热,在电弧作用区,温度高达4000℃。
冶炼过程一般分为熔化期、氧化期和还原期,在炉内不仅能造成氧化气氛,还能造成还原气氛,因此脱磷、脱硫的效率很高。
所用含铁原料主要为废钢,约占70%以上,另外可以加入铁水、生铁、直接还原铁、热压块等。
冶炼时间较长,一般至少是转炉冶炼时间的两倍。
电炉熔炼温度高且容易控制调节,电弧炉弧光区温度高达3000-6000℃,炉温高达2000℃以上,远高于冶炼一般钢种所需的温度,可以用于冶炼转炉不能冶炼的合金钢和不锈钢。
炉内气氛易于控制调节。
在冶炼的不同阶段,炉内不仅能造成氧化性气氛,还能造成还原性气氛,前者有利于脱碳和去磷,后者有利于脱氧、去硫、易氧化合金的加入、回收金属元素和控制钢液成分。
电炉设备比简单,投资少,建厂快,占地少,且容易控制污染。
但由于所需能源由电极在短路时产生的高温来提供,耗电量较大,冶炼1吨钢所消耗的电能约350-600kwh;成品钢中氢、氮含量偏高。
因为在电弧作用下,炉内空气的水汽大量离解,生成的氢和氮,如进入钢水,将影响钢的质量。
电弧是“点”热源,炉内温度分布不均匀,熔池平静时,各部分钢水温度相差较大。
碳质电极的存在会使钢液增碳,给冶炼低碳钢带来困难。
废钢铁是一种载能资源,用废钢铁炼钢可以节约大量能源。
在大型钢铁联合企业,从采矿、选矿、烧结、焦化、炼铁到炼钢、轧钢,能源消耗和污染排放主要集中在炼钢工序之前。
研究表明,用废钢直接炼钢和用矿石炼铁后再炼钢相比,可节约能源60%,节水40%。
废钢铁是一种环保资源,用废钢直接炼钢和用矿石炼铁后再炼钢相比,可减少废气186%、废水76%和废渣97%,有利于清洁生产和排废减量化。
电弧炉资料
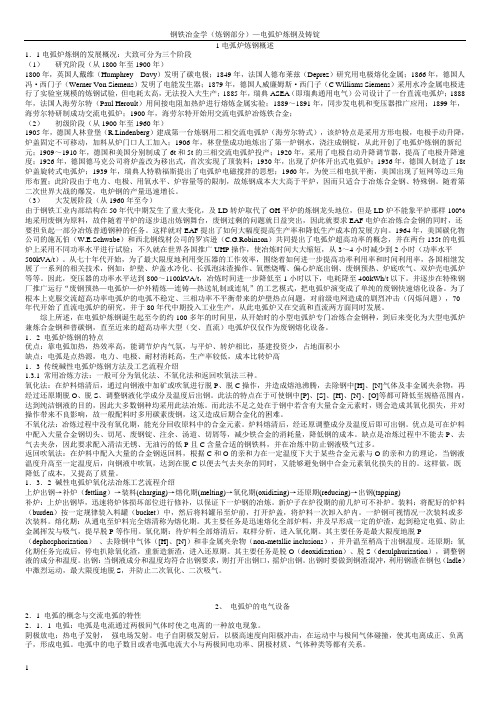
1电弧炉炼钢概述1.1电弧炉炼钢的发展概况:大致可分为三个阶段(1)研究阶段(从1800年至1900年)1800年,英国人戴维(Humphrey Davy)发明了碳电极;1849年,法国人德布莱兹(Deprez)研究用电极熔化金属;1866年,德国人冯·西门子(Werner Von Siemens)发明了电能发生器;1879年,德国人威廉姆斯·西门子(C Williams Siemens)采用水冷金属电极进行了实验室规模的炼钢试验,但电耗太高,无法投入大生产;1885年,瑞典ASEA(即瑞典通用电气)公司设计了一台直流电弧炉;1888年,法国人海劳尔特(Paul Heroult)用间接电阻加热炉进行熔炼金属实验;1889~1891年,同步发电机和变压器推广应用;1899年,海劳尔特研制成功交流电弧炉;1900年,海劳尔特开始用交流电弧炉冶炼铁合金;(2)初级阶段(从1900年至1960年)1905年,德国人林登堡(R.Lindenberg)建成第一台炼钢用二相交流电弧炉(海劳尔特式),该炉特点是采用方形电极,电极手动升降,炉盖固定不可移动,加料从炉门口人工加入;1906年,林登堡成功地炼出了第一炉钢水,浇注成钢锭,从此开创了电弧炉炼钢的新纪元;1909~1910年,德国和美国分别制成了6t和5t的三相交流电弧炉投产;1920年,采用了电极自动升降调节器,提高了电极升降速度;1926年,德国德马克公司将炉盖改为移出式,首次实现了顶装料;1930年,出现了炉体开出式电弧炉;1936年,德国人制造了18t 炉盖旋转式电弧炉;1939年,瑞典人特勒福斯提出了电弧炉电磁搅拌的思想;1960年,为使三相电抗平衡,美国出现了短网等边三角形布置;此阶段由于电力、电极、用氧水平、炉容量等的限制,故炼钢成本大大高于平炉,因而只适合于冶炼合金钢、特殊钢。
随着第二次世界大战的爆发,电炉钢的产量迅速增长。
电弧炉炼钢的工艺原理
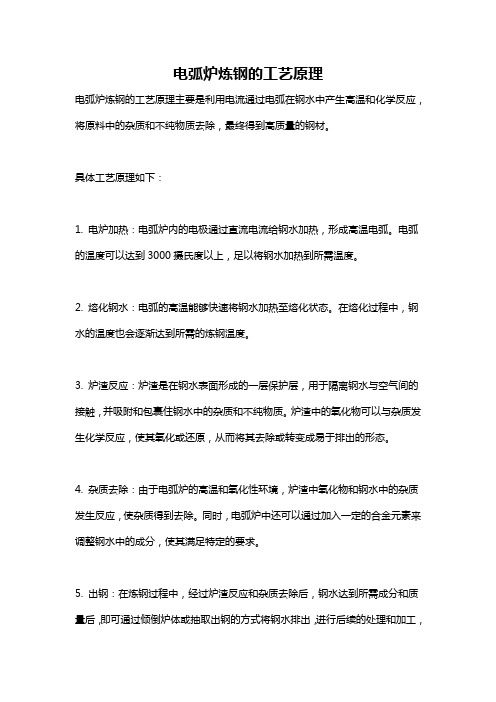
电弧炉炼钢的工艺原理
电弧炉炼钢的工艺原理主要是利用电流通过电弧在钢水中产生高温和化学反应,将原料中的杂质和不纯物质去除,最终得到高质量的钢材。
具体工艺原理如下:
1. 电炉加热:电弧炉内的电极通过直流电流给钢水加热,形成高温电弧。
电弧的温度可以达到3000摄氏度以上,足以将钢水加热到所需温度。
2. 熔化钢水:电弧的高温能够快速将钢水加热至熔化状态。
在熔化过程中,钢水的温度也会逐渐达到所需的炼钢温度。
3. 炉渣反应:炉渣是在钢水表面形成的一层保护层,用于隔离钢水与空气间的接触,并吸附和包裹住钢水中的杂质和不纯物质。
炉渣中的氧化物可以与杂质发生化学反应,使其氧化或还原,从而将其去除或转变成易于排出的形态。
4. 杂质去除:由于电弧炉的高温和氧化性环境,炉渣中氧化物和钢水中的杂质发生反应,使杂质得到去除。
同时,电弧炉中还可以通过加入一定的合金元素来调整钢水中的成分,使其满足特定的要求。
5. 出钢:在炼钢过程中,经过炉渣反应和杂质去除后,钢水达到所需成分和质量后,即可通过倾倒炉体或抽取出钢的方式将钢水排出,进行后续的处理和加工,
最终得到所需的钢材。
总的来说,电弧炉炼钢的工艺原理是通过电流产生高温电弧,利用高温和炉渣的化学反应去除钢水中的杂质,从而实现炼钢的目的。
- 1、下载文档前请自行甄别文档内容的完整性,平台不提供额外的编辑、内容补充、找答案等附加服务。
- 2、"仅部分预览"的文档,不可在线预览部分如存在完整性等问题,可反馈申请退款(可完整预览的文档不适用该条件!)。
- 3、如文档侵犯您的权益,请联系客服反馈,我们会尽快为您处理(人工客服工作时间:9:00-18:30)。
1、穿井:电极随着炉料的熔化而不断下降。
9、脱氧的方法有:沉淀脱氧,扩散脱氧,综在炉料中形成三个比电极直径大30~ 40%的合脱氧。
深坑,称为电极“穿井” 。
10 补炉原则:高温、快补、薄补、先外后里、2、短网:从电弧炉变压器低压侧出线开始到先坏后好。
补炉方法:人工补炉和机械补炉炉中电弧为止,传导低电压的大电流的导体在11、电炉炼钢是以废钢为原料,以三相交变电我国和苏联称为短网。
作为电流,利用电流通过石墨电极与金属料间3、炉外精炼:把一般炼钢炉(转炉,平炉,产生的 3000-6000 度高温来加热融化原料。
电弧炉)中要完成的精炼任如脱S,O,P 去气12、钢的特种炼钢法:真空感应冶炼法、等离去夹杂,调整钢的成分和钢液温度等移到炉外子电弧电渣重熔法、真空自耗电弧炉冶炼法、的钢包中或专用容器中进行。
电子束熔炼法及等离子束熔炼法。
4、碱度:炉渣中碱性氧化物与酸性氧化物的13、电弧炉炼钢常用的铁合金:硅铁、硅锰合百分含量之比。
其表示方法有:当炉渣金、硅钙合金、硅锰铝合金、钛铁等。
含 P 较低表示为 CaO/ SiO2,当炉渣含 P 较高14、熔化期时间占总冶炼时间的50%-70%,电时 CaO/ (SiO +P O ) ,当炉渣含 Mg较高时耗 70%-80%。
其主要操作有:合理供电、及时2 2 5(CaO+MgO)/ SiO2。
吹氧、提前造渣。
5、双渣氧化法:又称氧化法,氧化熔化后期15、氧化期的任务:脱P、脱 C、去气、去夹先扒渣后炉渣脱氧的熔炼方法。
特点有正常的杂、均匀成分和调整钢液温度。
还原期的任务 :氧化期,能脱 S、O、P、去气去夹杂,对炉料脱 S、脱 O、合金化、调整温度,其中脱O是无特殊要求,还原期可冶炼高质量钢核心、温度是条件、造渣是保证。
6、双渣还原法:又称返回吹氧法。
特点是冶16、吹氩的作用:脱 O、脱 C、提高脱气效果、炼过程中有较短的氧化期,(t ≤ 10min)造渣去除非金属夹杂物、均匀钢液成分和温度。
化渣,又造还原渣,能吹氧脱C去气去夹杂,17、炉外精炼的手段和主要内容有: 真空处理,但由于该种方法脱P 较难,故要求炉料要由含吹惰性气体,加入渣料、脱氧剂及合金元素以P 低的返回废钢组成。
及它们的组合。
7、白渣法:以碳粉,硅铁粉作还原剂,还原18、炉外精炼不锈钢的方法: VOD法—真空吹的炉渣冷却后呈白色,所以叫白渣操作。
氧脱 C法, AOD法—氩氧脱 C 法1、炉衬由炉壁,炉底和炉顶组成。
寿命最短19、电弧炉盖上有五个孔分别是:三个电极孔,的是炉壁,它的工作条件最差,距电弧近,温一个加料孔,一个排烟除尘孔。
度高,又受炉渣的浸蚀。
20、电弧加热钢包精炼常用的方法有:ASEA 2、RH法:真空循环脱气法, DH法:提升脱气— SKF法:钢包真空精炼法, VAD法:电弧钢法, VOD法是真空吹氧脱碳法,AOD法:氩氧包脱气法, LF 法:日本式钢包炉精炼法,AOD 脱 C 法法—氩氧脱 C 法。
3、GCr15 指滚动轴承钢含Cr 1.5 %,20CrMnTi 21、电弧炉常用造渣材料:石灰,萤石,粘土指合金结构钢含Ti 0.1 % . 砖块。
4、传统氧化法冶炼工艺的六个阶段是:补炉, 22、熔化期的任务:将块状的固体炉料迅速融装料,熔化期,氧化期,还原期,出钢。
化,并加热到氧化温度,提前造渣,早期去磷,5、碱性电炉炼钢的两类方法是:氧化法和不减少钢液吸气与挥发。
氧化法。
23、真空处理常用方法:液面脱气法,滴硫脱6、炉外精炼方法分为:真空精炼法,非真空气法,循环脱气法( RH法),提升脱气法 (DH精炼法,喷射冶金及合金元素特殊添加法。
法 ) 。
7、碱性电弧炉冶炼钢种有结构钢, 高速钢 , 不 24、补炉材料锈钢 , 轴承钢炉衬主要材料破坏原因8、碱性电弧炉冶炼氧化法分为矿石氧化法,炉顶 2 3 辐射高温熔化高 Al O 硅吹氧氧化法,综合氧化法。
炉壁MgO砂打结高温炉渣浸蚀炉底MgO砂打结层高温炉渣浸蚀,机械+镁砖 +粘土砖破坏精选1.碱性电弧炉造渣材料及要求: 1 )石灰;间短,一般均能满足一般钢种的要求。
还原剂主要成分 CaO含量不小于 85%, SiO2不大在炉内高温下和 CaO反应:( CaO)+3C=( CaC2)2%,S小于0 . 15%。
2)萤石,主要成+CO↑电石渣法:其操作过程和白渣法操作是分 CaF含量在85%-95%之间;3) 粘土一样的,只是用电石渣脱出渣中不稳定的氧化砖含 SiO2约 60%, Al 2O335%. 物,炉渣脱氧剂为碳粉。
渣中CaC2含量由初2.炉外精炼的作用:减少钢中气体,氧含量期 2~ 4%(黑色)变到 1%以下,呈白色炉渣,和非金属夹杂物含量,脱除钢中的S,在特定直至出钢。
碳和渣中 CaO反应,生成 CaC2的条件下可以脱除钢中的碳到极低的水平,精 CaO+3C=CaC+CO2炼出超低碳钢种;可以将钢中的成分和温度调( 3)白渣法与电石渣法操作的比较:电石渣整得很均匀,从而改善钢的质量,提高原有设的脱氧脱硫能力比白渣法的大,但它容易使钢备的生产能力,节约能源和原材料的消耗。
液增碳,增硅,形成电石渣需较长的时间,电3.钢包的喷粉精炼法:是将喷射冶金技术应石渣的钢液湿润性较好,出钢时破坏CaC2不用于钢液的炉外精炼。
向钢液喷粉如石灰粉,彻底时易产生夹杂,钢渣不易分离,增加了钢合金粉等,可以完成脱碳,去硫去磷,脱氧,中的夹杂物。
白渣法操作的形渣速度块,渣液去夹杂,改变夹杂形态,调温,控制微量元素活跃,温度易控制,还原时间短,所以目前各和合金化等精炼操作。
它即可提高钢的质量,厂使用白渣法操作的钢种增多。
又可大大提高生产率,比其他炉外精炼法更为五.读图题方便可靠,而且设备简单,投资少,费用低和灵活性大。
4 喷吹粉常用的粉料: 1)去硫用:石灰,石灰和萤石,石灰加铝,石灰加萤石加电石加石灰石,电石等; 2)脱氧用:硅钙合金,硅钙锰合金,硅钙合金加硼。
3)去磷用:石灰加萤石加氧化铁, 4)合金化:相应的合金剂。
试述白渣法操作工艺及其与电石渣法操作的特点比较(1)白渣法的操作要点: 1)必须快速干净的扒除氧化渣以减少扒渣过程中赤裸的钢渣直OA表示熔化期:熔化期占这个冶炼时期的接从空气中吸收氧; 2)造稀薄渣,向钢液面50%-70%,电耗占 70%-80% 其主要操作有:合加渣料,加入两为还原期总渣量的一半以上;理供电、适时吹氧、尽快造渣。
任务是:将块3)加预脱氧剂:当稀薄渣形成后,根据钢种状的固体炉料迅速融化,并加热到氧化温度,中对硅,锰的要求范围加入适量的硅锰合金,提前造渣,早期去磷,减少钢液吸气与挥发硅钙合金,硅锰铝合金或铝进行预脱氧。
4) AB 氧化前期:大渣量脱磷反应式为:补加渣料:在加入脱氧剂的同时或之后,或在 2[P]+5(FeO)+4(CaO)=5[Fe]+(4CaO ·P O)2 5加入预脱氧剂后立即补加石灰,萤石或火砖脱磷条件:造高碱度的强氧化性炉渣并控制冶块,最终达到总渣量的 4~ 6%的要求。
5) 加炼温度较低入粉状脱氧剂:对炉渣进行脱氧;6) 看脱氧: BC表示氧化后期:薄渣层脱碳。
反应为:白渣保持时间一般为 20~ 30 分钟左右,[C]+[O]={CO 2}FeO<0.5% , 此时中碳钢中的 [O]<0.01 % . 取样氧化期的任务:脱 P、脱 C、去气(氢、氮)、看钢液收缩情况。
7)调整钢液成分; 8)调去氧化物夹杂、均匀成分、提高钢液温度和调整钢液温度到出钢温度;9)终脱氧 - 插铝,出整钢液的碳含量。
钢。
脱碳作用:生成CO脱碳,去除钢液中的气体(2)白渣法以碳粉,硅铁粉作还原剂,还原和夹杂物的炉渣冷却后呈白色。
渣中 FeO< 1%冶炼时氧化期控制:1在氧化顺序上先氧化P 后氧化精选C ;2 在温度上先低温后高温, 先慢升后快升 3 钢过程的一项最主要任务; 脱磷、硫 ——通过 在造渣上先大渣量脱 P 再薄渣层脱 C ; 4 在供 造渣把有害元素磷、 硫去除到钢种允许的限度 氧上先加矿石氧化,后吹氧氧化。
以下;去气、去夹杂 ——把熔炼过程中进入钢 气体与夹杂的去除时间 :在氧化期的脱碳过液中的有害气体 (氢和氮)及非金属夹杂物 (氧程中进行的。
它是借助碳氧反应产生CO 气泡 化物、 硫化物和硅酸盐等) 排除掉; 调温 ——上浮使熔池产生激励沸腾, 促进气体和夹杂的 依靠铁水物理热和化学热或外加热源,按照熔去除, 均匀成分、 和温度而进行的。
机理 :① 炼工艺的需要, 适时地提高和调整钢液温度到 C-O 反应生成 CO 使熔池沸腾, CO 气泡对氢气 出钢温度;脱氧与合金化 ——把氧化熔炼过程 和氮气来说, 氮气和氢气分压为零, 氮气和氢 中生成的对钢质有害的过量的氧(以 FeO 形气极易随 CO 上浮去除; ② C-O 反应易使 式存在)从钢液中排除掉; 同时加入合金元素,2FeO .SiO 2, 2FeO . Al 2O 32FeO .TiO 2 等氧 将钢液中的各种合金元素的含量调整到所炼化物夹杂聚合长大而上浮, CO 上升过程中粘 钢号的规格范围内。
附氧化物夹杂上浮排除。
电弧炉炼钢用原材料CD 是还原期 :任务 :去除钢液中的氧、硫、 废钢 :⑴ 废钢表面清洁少锈。
⑵ 废钢中不得调整钢液成分到规格范围、 调整钢液温度到出 混有铜、铅、锌、锡、锑、砷等有色金属。
⑶ 钢温度(脱 S 、脱 O 、合金化、调整温度) ,其 废钢中不得混有爆炸物、 易燃物、封闭器皿和中脱 O 是核心、 温度是条件、 造渣是保证。
脱 毒品。
⑷ 废钢要有明确的化学成分。
⑸ 废钢硫反应: [FeS]+(CaO)=(CaS)+(FeO). 脱氧反 要有合适的块度和外形尺寸。
应: x[E]+y[O] → (ExOy)生铁 :一般用于提高炉料的配碳量或代替一部 脱硫的热力学条件是 :炉渣中含 (FeO) 较低, 分废钢。
氧化剂 :1)铁矿石 要求铁矿石的含 碱度要高( 3.5 左右),较大的渣量(渣量大 铁量高, 2)比重大。
氧化铁皮是比较纯净的 于 5%),合适的温度。
氧化剂,杂质(磷、硫等)较少。
3)氧气是还原期的脱氧方法 : 1)沉淀脱氧:将块状脱最主要的氧化剂。
要求含O2≥99%,水分≤氧剂加入钢液中,直接进行钢液脱氧。
其特 3g ∕ m3,熔化期氧压为 0.3~ 0.7MPa ,氧化期 点是操作简单, 脱氧迅速, 脱氧产物易留在钢 氧压为 0.7~ 1.2MPa 。
中。
2) 扩散脱氧: 将粉状脱氧加在渣中, 使炉 脱氧剂和铁合金 : 1)脱氧剂和铁合金中的有渣脱氧, 钢中氧再向渣中扩散, 间接脱除钢中 用元素含量要高,以减少熔化时的热能消耗。