零件技术要求
第12章零件的技术要求
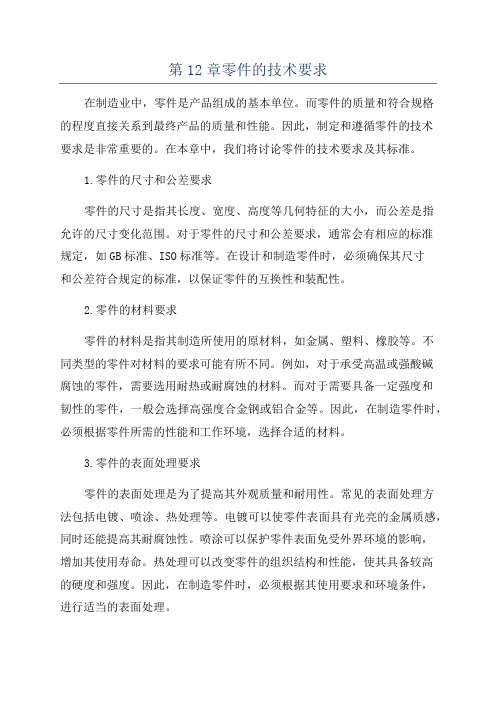
第12章零件的技术要求在制造业中,零件是产品组成的基本单位。
而零件的质量和符合规格的程度直接关系到最终产品的质量和性能。
因此,制定和遵循零件的技术要求是非常重要的。
在本章中,我们将讨论零件的技术要求及其标准。
1.零件的尺寸和公差要求零件的尺寸是指其长度、宽度、高度等几何特征的大小,而公差是指允许的尺寸变化范围。
对于零件的尺寸和公差要求,通常会有相应的标准规定,如GB标准、ISO标准等。
在设计和制造零件时,必须确保其尺寸和公差符合规定的标准,以保证零件的互换性和装配性。
2.零件的材料要求零件的材料是指其制造所使用的原材料,如金属、塑料、橡胶等。
不同类型的零件对材料的要求可能有所不同。
例如,对于承受高温或强酸碱腐蚀的零件,需要选用耐热或耐腐蚀的材料。
而对于需要具备一定强度和韧性的零件,一般会选择高强度合金钢或铝合金等。
因此,在制造零件时,必须根据零件所需的性能和工作环境,选择合适的材料。
3.零件的表面处理要求零件的表面处理是为了提高其外观质量和耐用性。
常见的表面处理方法包括电镀、喷涂、热处理等。
电镀可以使零件表面具有光亮的金属质感,同时还能提高其耐腐蚀性。
喷涂可以保护零件表面免受外界环境的影响,增加其使用寿命。
热处理可以改变零件的组织结构和性能,使其具备较高的硬度和强度。
因此,在制造零件时,必须根据其使用要求和环境条件,进行适当的表面处理。
4.零件的装配要求零件的装配是将多个零件组装成完整产品的过程。
对于零件的装配要求,通常包括安装位置、间隙要求、装配顺序等。
正确的装配要求可以确保产品的正确性和稳定性。
在制造零件时,必须根据相关装配要求,精确控制零件的尺寸和公差,以保证装配的准确性和方便性。
5.零件的耐用性要求零件的耐用性是指其可以在正常工作条件下,持续使用的能力。
耐用性要求通常包括使用寿命、可维修性、可靠性等。
在制造零件时,必须选择合适的材料和工艺,以确保零件具有较长的使用寿命和可靠性。
同时,还应考虑到零件的维修性,即在出现故障或损坏时,是否容易维修或更换。
零件的技术要求.

(一)改善切削性能
用作改善切削性能的热处理方法有正火和退火。通常安排在毛坯加工之
后、切削加工之前进行。
(二)改善零件的使用性能
用作改善零件的使用性能的热处理方法有调质和正火。调质处理一般安
排在粗加工之后、半精加工之前进行。
(三)提高表面硬度
用作提高表面硬度的热处理方法有表面淬火、表面渗碳和表面渗氮等。 表面淬火、渗碳热处理一般安排在磨削加工之前;渗氮热处理通常安排 在精磨之前。 (四)消除内应力 用作消除内应力的方法有正火、退火热处理,以及人工时效、冰冷和振 动时效等方法。
(四)主动测量法 1、在加工过程中,利用自动测量装置边加工边测量加工尺寸,并将测量 结果与要保证的工序尺寸比较后,或使机床继续工作,或使机床停止 工作,就是主动测量法。 2、该方法生产率高,加工精度稳定,是目前机械加工的发展方向之一。 (五)自动控制法 1、在加工过程中,利用测量装置或数控装置等,自动控制加工过程的加
(三) 仿形法
通过仿形装置作进给运动对工件进行加工的方法称为仿形法。随着数控 加工的广泛应用,机械式仿形法的应用将日益减少。
(四) 展成法
利用工件和刀具作展成切削运动进行加工的方法称为展成法。如滚齿和 插齿加工就是典型的展成法加工。
三、位置精度
• 位置精度指加工后零件的几何图形的实际位置与理想位置的符合(接 近)程度。 • 常用的有平行度、垂直度、同轴度、对称度等。 • 国家标准GB/T1182-1996《形状和位置公差》中规定,形状和位置公 差共有14个项目,见附表所示。 • 获得位置精度的方法 (一)一次安装获得法:把零件上有相互位置要求看相关表面安排在工 件的一次装夹中进行加工,从而保证其相互位置精度。 (二)多次安装获得法:该方法是人为地将工件的加工过程分作几次装 夹来完成,每次装夹有关表面的位置精度可采用适当的装夹方法(如 找正法或夹具)获得,随着装夹加工的次数不断增多,加工表面与定 位基准之间的位置精度也不断提高,最终实现工件的位置精度。
零件技术要求

郑州裕兴电动技术有限公司关键件检验技术规范一、前叉:1.螺纹符合QB/T1220与QB/T1221规定2.前叉挡台的尺寸与精度符合QB1881-2008中的要求3.电镀符合QB/T1217-1991中的一类件要求4.前叉的安全性能符合GB3565-2005的要求5.漆膜外观及附着力符合QB/T1218-1991中的一类件要求6.电镀件符合QB/T1217-1991中的一类件要求7.外观应无明显划伤、磕碰等缺陷8.安装尺寸按采购订单要求二、车把:铝质车把1.把横管弯曲处圆度相差不大于0.2mm2.把横管左右高低相差不大于5mm3.安全性能应符合GB3565-2005的要求4.铝把的外观、氧化膜厚度及氧化膜耐碱度按一类件要求,氧化膜耐腐蚀应达到六级以上。
5.车把尺寸按采购订单要求,长度公差±1mm(铁质车把)1.把横管弯曲处圆度相差不大于2mm2.把横管左右高低相差不大于5mm3.车把安全性能符合GB3565-2005的要求,4.漆膜外观及附着力符合QB/T1218-1991中的一类件要求5.电镀符合QB/T1217-1991中的一类件要求6.车把尺寸按采购订单要求,长度公差±1mm三、车架:1.车架精度应符合QB1880-2008的要求2. 车架安全性能符合GB3565-2005的要求3. 漆膜外观及附着力符合QB/T1218-1991中的一类件要求4.外观各部位不得有锐边、毛刺、焊渣及磕碰伤等;焊道鱼鳞纹应宽窄一致、饱满、均匀,无漏焊、假焊、虚焊等现象;5.各安装尺寸应与固定的零件相对应,公差±1mm之内四、塑料件:1.表面不得有裂纹、气泡、杂质、划痕、压痕及毛刺、飞边的现象;2.塑件不得有注塑造成的变形等现象3.各安装尺寸及材料按订单要求,公差±1mm之内4.塑件表面不得有油污及影响喷涂的化学成分五、护杠:1. 安装固定尺寸应符合要求,公差±1mm之内2.弯曲出角度应对称,圆度公差不大于2mm3. 各部位不得有锐边、毛刺、焊渣及磕碰伤等;焊道应宽窄一致、饱满、均匀,无漏焊、假焊、虚焊等现象;4.烤漆应外观及附着力符合QB/T1218-1991中的要求5. 电镀符合QB/T1217-1991中的要求。
产品零件技术要求大全
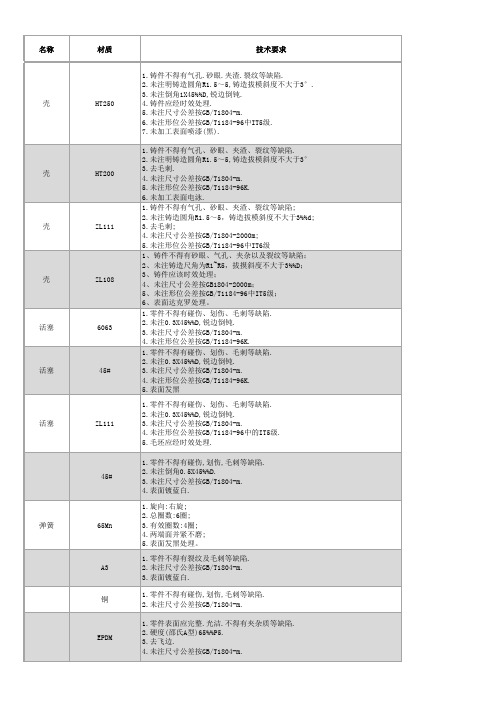
1.零件不得有裂纹及毛刺等缺陷. 2.未注尺寸公差按GB/T1804-m. 3.表面镀蓝白.
1.零件不得有碰伤,划伤,毛刺等缺陷. 2.未注尺寸公差按GB/T1804-m.
1.零件表面应完整.光洁.不得有夹杂质等缺陷. 2.硬度(邵氏A型)65%%P5. 3.去飞边. 4.未注尺寸公差按GB/T1804-m.
1.铸件不得有气孔、砂眼、夹渣、裂纹等缺陷. 2.未注明铸造圆角R1.5~5,铸造拔模斜度不大于3° 3.去毛刺. 4.未注尺寸公差按GB/T1804-m. 5.未注形位公差按GB/T1184-96K. 6.未加工表面电泳. 1.铸件不得有气孔、砂眼、夹渣、裂纹等缺陷; 2.未注铸造圆角R1.5~5,铸造拔模斜度不大于3%%d; 3.去毛刺; 4.未注尺寸公差按GB/T1804-2000m; 5.未注形位公差按GB/T1184-96中IT6级 1、铸件不得有砂眼、气孔、夹杂以及裂纹等缺陷; 2、未注铸造尺角为R1~R5,拔摸斜度不大于3%%D; 3、铸件应该时效处理; 4、未注尺寸公差按GB1804-2000m; 5、未注形位公差按GB/T1184-96中IT5级; 6、表面达克罗处理。 1.零件不得有碰伤、划伤、毛刺等缺陷. 2.未注0.3X45%%D,锐边倒钝. 3.未注尺寸公差按GB/T1804-m. 4.未注形位公差按GB/T1184-96K. 1.零件不得有碰伤、划伤、毛刺等缺陷. 2.未注0.3X45%%D,锐边倒钝. 3.未注尺寸公差按GB/T1804-m. 4.未注形位公差按GB/T1184-96K. 5.表面发黑
名称 壳 壳 壳 壳 活塞 活塞 活塞
弹簧
材质 HT250
机械零件制造的技术要求
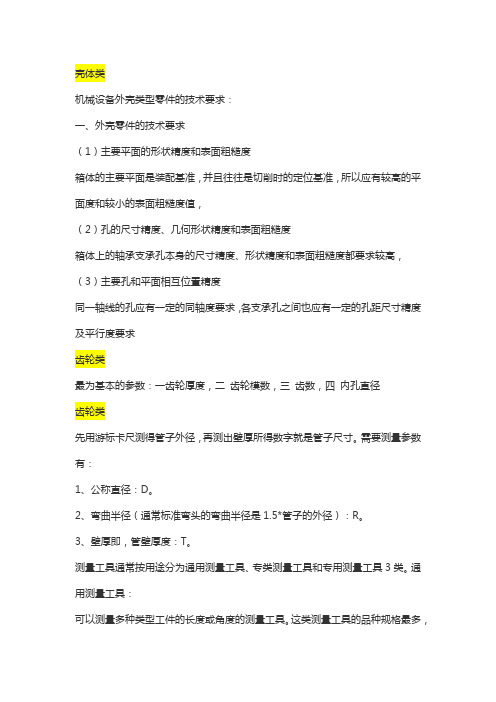
壳体类机械设备外壳类型零件的技术要求:一、外壳零件的技术要求(1)主要平面的形状精度和表面粗糙度箱体的主要平面是装配基准,并且往往是切削时的定位基准,所以应有较高的平面度和较小的表面粗糙度值,(2)孔的尺寸精度、几何形状精度和表面粗糙度箱体上的轴承支承孔本身的尺寸精度、形状精度和表面粗糙度都要求较高,(3)主要孔和平面相互位置精度同一轴线的孔应有一定的同轴度要求,各支承孔之间也应有一定的孔距尺寸精度及平行度要求齿轮类最为基本的参数:一齿轮厚度,二齿轮模数,三齿数,四内孔直径齿轮类先用游标卡尺测得管子外径,再测出壁厚所得数字就是管子尺寸。
需要测量参数有:1、公称直径:D。
2、弯曲半径(通常标准弯头的弯曲半径是1.5*管子的外径):R。
3、壁厚即,管壁厚度:T。
测量工具通常按用途分为通用测量工具、专类测量工具和专用测量工具3类。
通用测量工具:可以测量多种类型工件的长度或角度的测量工具。
这类测量工具的品种规格最多,使用也最广泛,有量块、角度量块、多面棱体、正弦规、卡尺、千分尺、百分表(见百分表和千分表)、多齿分度台、比较仪、激光测长仪、工具显微镜、三坐标测量机等。
轴类⑴尺寸精度轴类零件的主要表面常为两类:一类是与轴承的内圈配合的外圆轴颈,即支承轴颈,用于确定轴的位置并支承轴,尺寸精度要求较高,通常为IT 5~IT7;另一类为与各类传动件配合的轴颈,即配合轴颈,其精度稍低,常为IT6~IT9。
⑵几何精度轴类零件一般是用两个轴颈支撑在轴承上,这两个轴颈称为支撑轴颈,也是轴的装配基准。
除了尺寸精度外,一般还对支撑轴颈的几何精度(圆度、圆柱度)提出要求。
对于一般精度的轴颈,几何形状误差应限制在直径公差范围内,要求高时,应在零件图样上另行规定其允许的公差值。
(3)相互位置精度包括内、外表面、重要轴面的同轴度、圆的径向跳动、重要端面对轴心线的垂直度、端面间的平行度等。
(4)表面粗糙度轴的加工表面都有粗糙度的要求,一般根据加工的可能性和经济性来确定。
零件技术要求
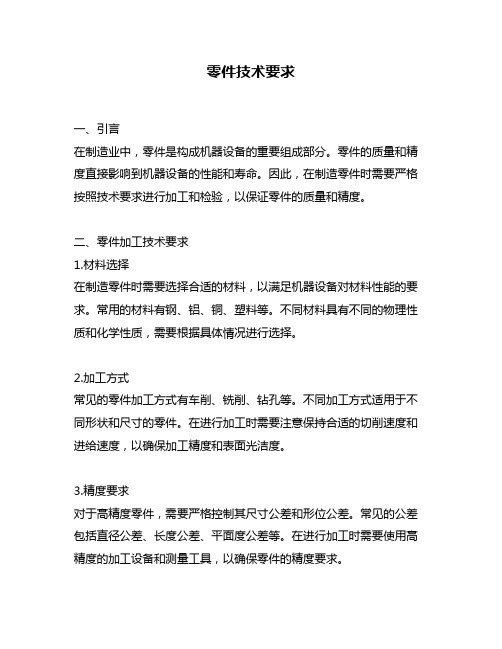
零件技术要求一、引言在制造业中,零件是构成机器设备的重要组成部分。
零件的质量和精度直接影响到机器设备的性能和寿命。
因此,在制造零件时需要严格按照技术要求进行加工和检验,以保证零件的质量和精度。
二、零件加工技术要求1.材料选择在制造零件时需要选择合适的材料,以满足机器设备对材料性能的要求。
常用的材料有钢、铝、铜、塑料等。
不同材料具有不同的物理性质和化学性质,需要根据具体情况进行选择。
2.加工方式常见的零件加工方式有车削、铣削、钻孔等。
不同加工方式适用于不同形状和尺寸的零件。
在进行加工时需要注意保持合适的切削速度和进给速度,以确保加工精度和表面光洁度。
3.精度要求对于高精度零件,需要严格控制其尺寸公差和形位公差。
常见的公差包括直径公差、长度公差、平面度公差等。
在进行加工时需要使用高精度的加工设备和测量工具,以确保零件的精度要求。
4.表面处理零件加工完成后需要进行表面处理,以提高其耐腐蚀性和美观度。
常见的表面处理方式有喷涂、电镀、氧化等。
在进行表面处理时需要注意控制处理时间和温度,以确保处理效果。
三、零件检验技术要求1.检验方法常见的零件检验方法包括三坐标测量、光学投影仪测量、影像测量等。
不同的检验方法适用于不同形状和尺寸的零件。
在进行检验时需要使用高精度的测量设备,以确保检验结果准确可靠。
2.检验标准对于不同类型的零件需要制定不同的检验标准。
常见的标准包括国家标准、行业标准和企业标准等。
在进行检验时需要按照相应标准进行操作,并记录下相关数据和结果。
3.质量控制在制造过程中需要对每个环节进行质量控制,以确保最终产品符合要求。
常见的质量控制方法包括过程控制、SPC(统计过程控制)、FMEA(失效模式与影响分析)等。
在进行质量控制时需要对每个环节进行详细记录,并及时纠正不良现象。
四、结论零件技术要求是制造高品质机器设备的关键环节。
在制造过程中需要注意材料选择、加工方式、精度要求和表面处理等方面的要求,同时也需要注重零件检验和质量控制,以确保最终产品符合要求。
零件的技术要求

零件的技术要求随着科学技术的不断进步,机械制造行业也越来越受人们的关注。
机械零件作为机械的组成部分之一,其精度、质量和可靠性直接影响机械的性能。
因此,机械零件的技术要求显得十分重要。
一、精度要求机械零件的精度是指零件的尺寸、形状和位置精度等参数的精度,在一定条件下与设计要求相比的偏差。
精度是衡量机械零件质量的一个重要指标。
机械零件的精度要求应符合以下标准:1、符合设计要求,灵活应变,注重以质量为导向;2、精度要求与机械设备的主要性能指标相适应;3、生产过程中要严格控制制造误差,特别是加工误差;4、使用合适的检测手段和设备,对零件进行精度测量检查。
二、质量要求机械零件的质量是指零件的物理性质、化学性质、力学性质、表面质量等方面符合设计要求。
质量是机械零件功能和可靠性的保证,也是确保机械设备性能的重要保障。
机械零件的质量要求应符合以下标准:1、完全符合设计要求,材料应符合国家规定标准,材质选择应符合实际情况;2、零件表面不能有任何裂纹、疤痕、气泡等瑕疵;3、零件的内部和表面应进行适当的防腐处理;4、机械零件使用寿命应与机械设备的寿命要求相符。
三、可靠性要求机械零件的可靠性是指零件在规定的使用条件下,能够满足设计要求,确保机械设备的正常运转和寿命。
可靠性是机械设备工作的关键因素,也是机械零件的重要指标之一。
机械零件的可靠性要求应符合以下标准:1、零件的设计应考虑到机械设备工作的环境、负载条件等因素,确保零件的刚度、强度、耐磨损性等达到设计要求;2、零件的生产工艺和制造材料应符合标准,严格按照标准加工;3、使用适当的检测手段和设备对零件进行质量检查,确保零件质量符合要求;4、在机械设备的维护和保养过程中,对零件进行适当的检查和维护,防止出现故障和损坏。
在机械零件制造的过程中,应注重零件的精度、质量和可靠性要求,生产过程中要不断加强技术的研究和改进,以创造出更好的机械零件。
因此,机械零件的技术要求非常重要,它不仅关系到整个机械设备的质量和性能,也关系到机械行业的发展和进步。
常见机械零部件技术要求规范总结

常见机械零部件技术要求一、机械零件常用技术要求:1、锐角倒钝、去除毛刺飞边。
2、零件去除氧化皮。
3、未注圆角半径R5。
4、未注倒角均为2×45°。
5、未注形状公差应符合GB1184-80的要求。
6、未注长度尺寸允许偏差±0.5mm。
7、零件加工表面上,不应有划痕、擦伤等损伤零件表面的缺陷。
8、精加工后的零件摆放时不得直接放在地面上,应采取必要的支撑、保护措施。
加工面不允许有锈蛀和影响性能、寿命或外观的磕碰、划伤等缺陷。
9、加工的螺纹表面不允许有黑皮、磕碰、乱扣和毛刺等缺陷。
二、铸件技术要求:1、铸件表面上不允许有冷隔、裂纹、缩孔和穿透性缺陷及严重的残缺类缺陷(如欠铸、机械损伤等)。
2、铸件应清理干净,不得有毛刺、飞边,非加工表面上的浇冒口应清理与铸件表面齐平。
3、对错型、凸台铸偏等应予以修正,达到圆滑过渡,一保证外观质量。
4、铸件非加工表面上的铸字和标志应清晰可辨,位置和字体应符合图样要求。
5、铸件非加工表面的粗糙度,砂型铸造R,不大于50μm。
6、铸件应清除浇冒口、飞刺等。
非加工表面上的浇冒口残留量要铲平、磨光,达到表面质量要求。
7、铸件上的型砂、芯砂和芯骨应清除干净。
8、铸件有倾斜的部位、其尺寸公差带应沿倾斜面对称配置。
9、铸件上的型砂、芯砂、芯骨、多肉、粘沙等应铲磨平整,清理干净。
10、铸件公差带对称于毛坯铸件基本尺寸配置。
11、铸件非加工表面的皱褶,深度小于2mm,间距应大于100mm。
12、机器产品铸件的非加工表面均需喷丸处理或滚筒处理,达到清洁度Sa2 1/2级的要求。
13、经喷丸或手工除锈的待涂表面与涂底漆的时间间隔不得多于6h。
14、铸件表面应平整,浇口、毛刺、粘砂等应清除干净。
15、铸件不允许存在有损于使用的冷隔、裂纹、孔洞等铸造缺陷。
16、所有需要进行涂装的钢铁制件表面在涂漆前,必须将铁锈、氧化皮、油脂、灰尘、泥土、盐和污物等除去。
17、除锈前,先用有机溶剂、碱液、乳化剂、蒸汽等除去钢铁制件表面的油脂、污垢。
- 1、下载文档前请自行甄别文档内容的完整性,平台不提供额外的编辑、内容补充、找答案等附加服务。
- 2、"仅部分预览"的文档,不可在线预览部分如存在完整性等问题,可反馈申请退款(可完整预览的文档不适用该条件!)。
- 3、如文档侵犯您的权益,请联系客服反馈,我们会尽快为您处理(人工客服工作时间:9:00-18:30)。
编者按:本文摘自“化工设备图样技术要求”TCED41002-2000,若有疑问,请查阅原文。
零件技术要求对于化工设备零部件,首先应考虑按相应标准选用,并按其标准规定进行制造、检验和验收,锻件等级按2.1.3中的要求填写。
对于暂无标准或超出标准的零部件,应进行图样设计并提出相应的设计要求。
本章所列化工设备常用零部件技术要求属举例示范性,也可参照相近的零部件系列标准填写技术要求。
9.1 锻件零件1锻件的制造、检验和验收应符合,级锻件规定。
﹤注(1)﹥2 材料的化学成分为;﹤注(2)﹥热处理后的机械性能为:3锻件需作晶间腐蚀试验,按。
﹤注(3)﹥4锻件需进行设计温度下的夏比(V型缺口)低温冲击实验。
其Akw≥ J。
﹤注(4)﹥5加工面和非加工面线性尺寸的未注公差,按GB/T1804-92的m级和c级(或V级)要求。
6其它要求﹤注(5)﹥注:(1)压力容器用钢锻件的级别,应按GB150-1998中规定或参照HG20581-1998中的说明确定。
非受压元件可参照上述标准或其它相关标准要求。
(2)按照JB4726-4728-94《压力容器用钢锻件》造、检验和验收的锻件其化学成分,热处理后机械性能应符合标准中规定,本条文应取消.对于超出标准所列材料的锻件,本条要求应保留.并需明确规定应遵循的制造、检验和验收标准或具体要求.(3)对于有晶间腐蚀倾向的不锈钢锻件,需进行晶间腐蚀倾向试验,试验标准(GB4334.1~4334.5-94)及合格要求需明确规定。
(4)对于设计温度≤20o C 的受压锻件,应进行夏比应符合(V型缺口)低温冲击实验,其冲击功值AkvGB150-1998附录E和C的要求,试验温度取设计温度或材料规定的最低试验温度。
(5)其它要求,包括零件的表面及密封面缺陷、压力试验、致密性试验等要求,按零件的需要填写。
9.2铸造零件1铸件按的规定。
﹤注(1)﹥2铸件应进行消除内应力热处理。
﹤注(2)﹥3热处理后的机械性能。
﹤注(3)﹥4铸件需作晶间腐蚀倾向试验,按。
﹤注(4)﹥5除注明外,加工面线性尺寸的未注公差按GB/T1804-92的m级要求;非加工面未注公差尺寸的极限偏差按GB6414-86的CT级要求。
注:(1)常用材料铸件的技术条件如下:①灰铸铁件:GB9439-88《灰铸铁件》;②可锻铸铁件:GB9440-88《可锻铸铁件》;③球墨铸铁件:GB1348-88《球墨铸铁件》;④耐热铸铁件:GB9437-88《耐热铸铁件》;⑤碳素钢铸件:11352-89《一般工程用碳素钢铸件》;⑥不锈耐酸钢铸件:GB2100-80《不锈耐酸钢铸件技术条件》;⑦合金铸钢:JB/ZQ4297-86《合金铸钢》;⑧耐热铸钢:GB8492-87《耐热铸钢》;(2)铸件热处理要求按下列情况填写:①灰铸铁件:要求消除内应力时,需填写此条。
②耐热铸铁件:标准规定对硅系、硅铝系耐热铸铁件应进行消除内应力热处理,其它牌号如需要应提出要求。
③球墨铸铁件:标准中规定热处理由供方自行决定。
对热处理有特殊要求时,应供需双方协议。
④ 碳素钢铸件:标准规定,无特殊要求,热处理工艺由制造厂自定。
常用工艺:退火,正火,正火加回火特殊要求应供需双方协议。
⑤ 不锈耐酸钢铸件:标准中规定了热处理规范;如有特殊要求,需另外提出。
⑥ 合金铸钢件:标准中规定热处理工艺由制造厂自定。
(3)若机械性能完全按1中所列标准规定的项目和指标 ,本条可取消,否则按下列情况提出要求:① 灰铸铁件:GB9439-88中规定以单铸试棒测定抗拉强度。
若要以附铸试棒(块)或从铸件上切确试块来测定,应提出要求供需双方协议。
② 可锻铸铁件:GB9440-88中规定以抗拉强度和延伸率为依据。
若对屈服强度、硬度或其它性能有要求,应提出由供需双方协议。
③ 球墨铸铁件:GB1348-88中规定以抗拉强度和延伸率为依据。
若对屈服强度、硬度有要求,应提出由供需双方协议。
冲击试验只适用下列牌号,若有需要其要求按下表提出: 最小冲击功值A kv J(Kg.m)(v 型缺口)室温23±5o C -20±2 o C牌号 铸铁壁厚 mm试样 三试样均值 单个值三式样均值 单个值QT400-1814(1.43) 11(1.12) QT400-18L单铸 12(1.22) 9(0.92) >30~6014(1.43) 11(1.12)QT400-18A >60~200 12(1.22) 9(0.92)>30~60 12(1.22) 9(0.92) QT400-18AL >60~200附铸 10(1.02) 7(0.71)④ 碳素钢铸件:对其机械性能若不提出要求,则断面收缩率和冲 击韧性由制造厂选择其一。
⑤ 不锈耐酸钢铸件:机械性能一般不作验收项目,如有要求, 参照GB2100-80中规定值提出,供需双方协议.⑥ 耐热铸钢件:GB8492-87中元旦出了机械性能和短时高温抗 拉性能,如有要求应提出供需双方协议.(4) 当铸件为不锈耐酸钢材料,且有晶间腐蚀倾向时,应作晶间腐 蚀倾向试验,其方法按GB2100-80表3选择.其中:T 法相当于GB4334.5;X 法相当于GB4334.3;C 法相当于GB4334.1.(5) GB6414-86≤铸件尺寸公差≥中对正常生产情况下能达到的公差等级有所说明.其中对小批和单件生产、基本尺寸大于25mm 的铸件,其公差等级 一般按下表选择.有特殊要求可另选级别公差等级范围造型材料铸钢灰铸铁球墨铸铁无湿型砂 13~15 13~15 13~15自硬砂 12~14 11~13 11~139.3法兰、法兰盖1 材料应符合规定. ﹤注(1)﹥2 法兰(盖)应进行热处理.﹤注(2)﹥3 法兰(盖)密封面及表面不得有裂纹及其它降低法兰强度和连接可靠性的缺陷.4 法兰(盖) 上螺柱孔中心圆直径和相邻螺柱孔弦长极限偏差为±0.6mm,任意两螺柱孔弦长极限偏差为mm﹤注(3)﹥ 5除注明外,加工面和非加工面线性尺寸未注公差按GB/T1804- 92m级(或v级).6其它要求﹤注(4)﹥注: (1) 材料要求:①法兰(盖)为锻制时填写如下要求:锻件的制造、检验和验收应符合JB4726~4728-92《压力容器用钢锻件》中级规定.标准号按锻件材料对应填写,锻件级别按GB150-1998或参照HG20581-1998中说明确定.②法兰(盖)采用钢板时,应符合GB150-1998《钢制压力容器》和3274-88《碳素结构钢和低合金结构热轧厚钢板和钢带》及GB6654-1996《压力容器用钢板》的规定.厚度大于50mm的20R和16MnR钢板,厚度大于16mm的15MnVR钢板,须要求正火状态供货、使用.(2)对焊法兰(盖),包括轧制和锻制的应进行正火处理或正火加回火处理。
(3)任意两螺柱孔弦长极限偏差,按下表规定:公称直径DN≤550 >550~1200 >1200±2.0±1.0 ±1.5公差(mm)(4) 本节内容适用于一般形式的法兰(盖),若结构特殊,或另有特殊材料等其它要求,如采用钢板拼接或型钢焊接法兰(盖),其焊缝必须经100%射线(RT)或超声(UT)检测,按JB4730-94RT-I级为合格;并须经焊后消除应力热处理等,应补充相应技术要求.9.4人孔、手孔1人(手)孔制造、检验和试验按的规定. ﹤注(1)﹥2 9.3中3、4、5条适应于本节.3人(手)孔待与所在设备组焊后一起进行压力试验,见装配图技术要求.注(1)当人(手)孔采用带衬里或不锈耐酸钢制作时,按HGJ503-86 ≤不锈钢人孔和手孔分类与技术条件≥.当人(手)孔采用碳钢时,按HG21514-95≤碳素钢、低合金人孔和手孔类型与技术条件≥.9.5补强圈1补强圈应与容器壳体接触面密切贴合.2补强圈焊接后,应以0.4~0.5 Mpa的压缩空气检验其连接焊缝质量.2 线性尺寸的未注公差按GB/T1804-92中v级.9.6 螺栓螺栓一般可按GB5780-5790-86选用,特殊情况需设计绘图,按如下要求:1 材料及其机械性能应符合GB150-1998和相应材料标准中规定; ﹤注(1)﹥23 螺栓尺寸公差按GB3103.1-82 级. ﹤注(1)﹥3 螺栓表面质量按GB5779.1-86规定.注(1) 材料的化学成分、机械性能、冲击试验等要求应符合GB150-1998和GB700-88《碳素结构钢》、GB699-88《优质碳素结构钢技术条件》、GB3077-88《合金结构钢技术条件》的规定.需要热处理的材料,其热处理后机械性能应符合标准中规定.(2) 螺栓尺寸公差分为A、B、C三级,可按使用要求选择确定:A级:最精确,用于螺纹公称直径d≤24mm和螺杆长度L≤10d或≤150mm(按较小值);B级:次精度,用于螺纹公称直径d>24mm和螺杆长度L<10d或>150mm(按较小值).C级:不精确.9.7 螺柱螺柱一般可按GB897-88和GB953-88选用.特殊情况需设计绘图,按如下要求:1 9.6.中1、2 、4适用于本节.﹤注(1)﹥2 螺柱直线度公差为mm/100mm标长.﹤注(2)﹥3其它要求:注:(1)螺柱直线度公差按下表选定:直线度公差(mm)/杆长100mm 公称直径d(mm)≤240.4>240.3(2) 重要的螺柱可参照8.12要求进行超声(UT)、磁粉(MT)检测和表面磷化处理。
9.8 螺母螺母一般按GB6170-88、GB41-86和GB6175-86选用。
特殊情况需按下述要求设计绘图:1 9.6.中1、2、4适用于本节。
﹤注(1)﹥2 螺母尺寸公差GB3103.2-82 级。
﹤注(2)﹥3其它要求注:(1)螺纹公称直径d≤16mm用A级;(2)重要的螺母可参照8.13要求。
9.9视镜1视镜玻璃应符合HGJ501-86-0《钢化视镜玻璃的制造、验收技术条件》中的规定。
﹤注(1)﹥2接缘上螺孔和压紧环上螺栓孔中心圆直径和弦长极限偏差为±0.6mm,任意两孔弦长极限偏差为±1mm。
3除注明外。
加工面和非加工面线性尺寸的未注公差按GB/T1804-92m级和c 级(或v级)。
﹤注(2)﹥4其它要求。
注:(1)HGJ501-86-0中规定:视镜玻璃工作压力≤25Kg/cm2(2.45Mpa),热稳定性保证耐急变温差为180o C,使用温度为0~200 o C(2) 当采用带颈焊接或带衬里视镜,以及材料为不锈耐酸钢时,还应提出相应的焊接方法,焊接接头形式及尺寸、焊条牌号。
衬里方法、晶间腐蚀试实验等要求。
9.10 玻璃板液面计1 9.9中2、3条适用于本节。