6. 金属板料成形
材料加工工程——板金属成形

第八章金属板料成形基本概念板成形产品:金属桌椅、文件柜、汽车覆盖件、食品罐头……早期的板成形产品:金、银、铜,家用器皿、珠宝首饰……常用材料:低碳钢低成本、高强度、好的可成形性航空航天器用材料:铝合金、钛合金生活中实例3金属板料成形工艺分类金属板料成形工艺分类4分离工艺5成形工艺16成形工艺27冲裁成形冲裁工艺(冲孔和落料)冲裁成形过程8分离工序主要参数:冲头/模具间隙量重叠量冲头/模具的材料和形状落料速度润滑状态910间隙量c:影响冲裁边缘形状和质量的主要影响因素间隙量增加,冲裁边缘粗糙!!各个参数的影响1、间隙量增加,冲裁边缘粗糙。
2、金属板材塑性的增加,冲裁边缘光亮带和粗糙区域的比值增加,同时随着板材厚度和间隙量的增加而减少。
3、变形区的宽度依赖于凸模的速度。
随着速度的增加,由于塑性变形产生的热量被限制在越来越小的范围。
进而冲裁区变窄,表面变得更光滑,形成更少的毛刺。
11冲裁力计算冲裁力:F(冲裁力)=0.7×t(板厚)×l(周长)×σb (强度极限)50.7(0.0032)()(0.025)(1.410)0.17F M N π=⨯=例:估算室温下在厚度为3.2mm 的钛铝合金(Ti-6Al-4V )板上冲裁一个直径25mm 的孔所需的冲裁力。
剪切操作图8-4 各种板金属剪切操作13精密冲裁(a)图5-5 普通冲裁与精密冲裁的效果对比15精冲模工作部分的组成(a )带齿圈压板精冲(b )(c )普通冲裁 1-凸模2-齿圈压板3-板料4-凹模5-顶出器精密冲裁分条图8-6 圆盘剪纵切分条16其它冲裁工艺分段冲裁nibbling钢尺模切steel rules,适用于软金属、皮革、纸张、橡胶剪切余料scrap in shearing:高达30%,计算机排样冲裁间隙:小孔大间隙,大孔小间隙;c板厚的(1%~)2%~8%(~30%);17冲裁模具间隙量材料类型、性能、厚度、坯料尺寸以及与初始板料边缘的距离等因素的函数图8.9 冲裁边缘进行修整的示意图冲裁边修整冲裁、修整组合工艺18冲裁模具图8.10 冲头和模具使用剪切角的实例19冲裁模具复合模(a)(b)图8.11 复合模工作示意图2021连续级进模图8-10 连续模工作示意图(c)板成形中金属的重要特征表 16.2特性 重要性延伸率 Determines the capability of the sheet metal to stretch without necking and failure; high strain-hardening exponent (n)and strain-rate sensitivity exponent (m)desirable.屈服点延伸 Observed with mild-steel sheets; also called Lueder’s bands and stretcher strains; causes flamelike depressions on the sheet surfaces; can be eliminated by temper rolling, but sheet must be formedwithin a certain time after rolling.各向异性(面内) Exhibits different behavior in different planar directions; present in cold-rolled sheets because of preferred orientation or mechanical fibering; causes earing in drawing; can be reduced or eliminatedby annealing but at lowered strength.各向异性(法向) Determines thinning behavior of sheet metals during stretching; important in deep-drawing operations.晶粒尺寸 Determines surface roughness on stretched sheet metal; the coarser the grain, the rougher the appearance (orange peel); also affects material strength.残余应力 Caused by nonuniform deformation during forming; causes part distortion when sectioned and can lead to stress-corrosion cracking; reduced or eliminated by stress relieving.回弹 Caused by elastic recovery of the plastically deformed sheet after unloading; causes distortion of part and loss of dimensional accuracy; can be controlled by techniques such as overbending andbottoming of the punch.起皱 Caused by compressive stresses in the plane of the sheet; can be objectionable or can be useful in imparting stiffness to parts; can be controlled by proper tool and die design.切边质量 Depends on process used; edges can be rough, not square, and contain cracks, residual stresses, and a work-hardened layer, which are all detrimental to the formability of the sheet; quality can beimproved by control of clearance, tool and die design, fine blanking, shaving, and lubrication.表面质量 Depends on rolling practice; important in sheet forming as it can cause tearing and poor surface quality; see also Section 13.3.2223屈服点延伸图8.12(a)板金属试样上的屈服点延伸;(b)低碳钢板表面的吕德斯带;(c)钢制封头表面的延伸带(a)(b)(c)Erichsen杯突试验(a)(b)a)Erichsen杯突试验原理b)杯突试验样品杯突试验,一种冲压工艺性能试验,用来衡量材料的深冲性能的试验方法。
板料成形CAE技术

板料成形CAE 技术贵州风华机器厂童春桥一、前言计算机辅助设计技术以其强大的冲击力,影响和改变着工业的各个方面,甚至影响着社会的各个方面。
它使传统的产品技术、工程技术发生了深刻的变革,极大地提高了产品质量,缩短了从设计到生产的周期,实现了设计的自动化。
板料成形是利用模具对金属板料的冲压加工,获得质量轻、表面光滑、造型美观的冲压件,具有节省材料、效率高和低成本等优点,在汽车、航空、模具等行业中占据着重要地位。
由于板料成形是利用板材的变形得到所需的形状的,长期以来,困扰广大模具设计人员的主要问题就是较长的模具开发设计周期,特别是对于复杂的板料成形零件无法准确预测成形的结果,难以预防缺陷的产生,只能通过经验或类似零件的现有工艺资料,通过不断的试模、修模,才能成功。
某些特殊复杂的板料成形零件甚至制约了整个产品的开发进度。
板料成形CAE 技术及分析软件,可以在产品原型设计阶段进行工件坯料形状预示、产品可成形性分析以及工艺方案优化,从而有效地缩短模具设计周期,大大减少试模时间,帮助企业改进产品质量,降低生产成本,从根本上提高企业的市场竞争力。
板料成形CAE 技术对传统开发模式的改进作用可以通过图 1 和图 2 进行对比=> 试模催模模具方案僱图1传统板料成形模具开发模式■ - -JJ RBi^a-j ri-BHMnHI _ liHHd I图2 CAE技术模具开发方式通过比较,就可发现板料成形CAE技术的主要优点(1) 通过对工件的可成形工艺性分析,做岀工件是否可制造的早期判断;通过对模具方案和冲压方案的模拟分析,及时调整修改模具结构,减少实际试模次数,缩短开发周期。
(2) 通过缺陷预测来制定缺陷预防措施,改进产品设计和模具设计,增强模具结构设计以及冲压方案的可靠性,从而减少生产成本。
(3) 通过CAE分析可以择优选择材料,可制造复杂的零件,并对各种成形参数进行优化,提高产品质量。
(4) 通过CAE分析应用不仅可以弥补工艺人员在经验和应用工艺资料方面的不足,还可通过虚拟的冲压模拟,提高提高工艺人员的经验。
金属薄板成形性能与试验方法 成形极限图(FLD)试验

1. 试样表面上网格圆畸变后的形状如图3 05 所示, 畸变后网格圆的长轴记作d 短轴记作d、 2并将d ,
和 d 近似视为试样平面内一点上的两个主应变方向。 7
d 夕 do d <do , ,
dJ do d -d. , ,
d d, d , d > ad, , 户
图 3 网格圆畸变 1. 测量临界网格圆的长、 06 短轴 d 和 d 时, , 2 可以使用读数显微镜、 测量显微镜、 投影仪或专门设计的 测量工具、 检测装置等压 如工程应变比例尺, 见附录 A( 参考件)。 」 1. 根据测量结果, 07 按公式()() 1 ,2计算试样的表面极限应变。
图 2 网格圆图案
62 试样表而的网格圆可用照像制版、 . 光刻技术、 电化学腐蚀或其他方法制取。
63 网格圆初始直径d 的大小, . 。 影响试验的测量计算结果, 其选用原则为: 采用大尺 寸 模具时可将 d , 的数值取大一些, 而用小尺寸 模具时则取小一些。
64 如果使用本标准 7 1 . . 条推荐的凸模尺寸, 则推荐使用 d=15 ". 的网格圆。 o . 25 ^ mm 65 网格圆直径的偏差不大 f . - 其数值的 2 Y4 o
了 模具
71 对于试验模具的几何尺寸 ( . 包括拉深筋的部位、 形状和尺寸等) 不作具体规定, 仅推荐使用直径为
伸试验和液压胀形试验 。 42 刚性凸模胀形试验时, . 将一侧表面制有网格圆的试样置于凹模与压边圈之间, 利用压边力压紧拉 国家技术监督局 1 9 一 2 1 批准 951一3 1 9 一 8 0 实施 9 60 一 1
GB T 5 2 . 一 1 9 / 1 8 5 8 9 5
深筋以外的试样材料, 试样中部在凸模力作用下产生胀形变形并形成凸包( 见图 1 , )其表而上的网格圆 发生畸变, 当凸包上某个局部产生缩颈或破裂时 , 停止试验 , 测量缩颈区( 或缩颈区附近) 或破裂区附近 的网格圆长轴和短轴尺寸, 由此计算金属薄板允许的局部表面极限主应变量(, 或(, 2。 e,2 。、 ) e) 。
金属材料成形工艺及控制
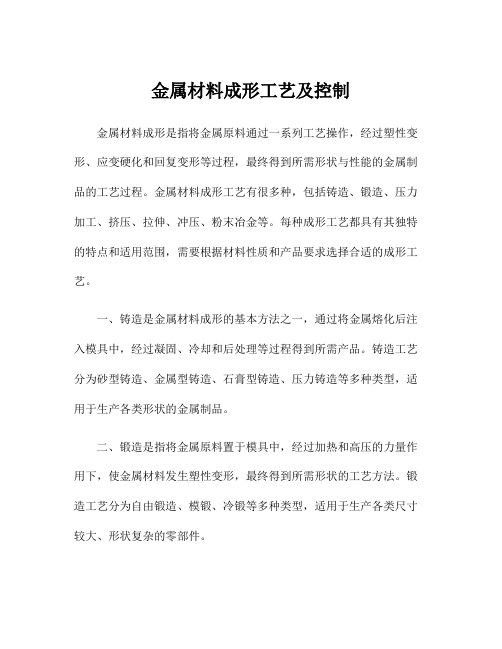
金属材料成形工艺及控制金属材料成形是指将金属原料通过一系列工艺操作,经过塑性变形、应变硬化和回复变形等过程,最终得到所需形状与性能的金属制品的工艺过程。
金属材料成形工艺有很多种,包括铸造、锻造、压力加工、挤压、拉伸、冲压、粉末冶金等。
每种成形工艺都具有其独特的特点和适用范围,需要根据材料性质和产品要求选择合适的成形工艺。
一、铸造是金属材料成形的基本方法之一,通过将金属熔化后注入模具中,经过凝固、冷却和后处理等过程得到所需产品。
铸造工艺分为砂型铸造、金属型铸造、石膏型铸造、压力铸造等多种类型,适用于生产各类形状的金属制品。
二、锻造是指将金属原料置于模具中,经过加热和高压的力量作用下,使金属材料发生塑性变形,最终得到所需形状的工艺方法。
锻造工艺分为自由锻造、模锻、冷锻等多种类型,适用于生产各类尺寸较大、形状复杂的零部件。
三、压力加工是指通过金属材料受到外力压缩、拉伸、弯曲等作用,使其发生塑性变形,并最终得到所需形状的金属成形方法。
压力加工包括挤压、拉伸、剪切、折弯等多种工艺,适用于生产各类薄板、管材、棒材等产品。
四、挤压是指将金属加热至熔点后,在压机的作用下通过模具挤出,得到所需形状的工艺方法。
挤压工艺适用于生产各类型材、异型材、电线电缆、铝箔等产品。
五、拉伸是指通过将金属材料置于拉伸机中,受到拉力的作用下,使其发生塑性变形,最终得到所需形状的金属成形方法。
拉伸工艺适用于生产各类细丝、线材、管子等产品。
六、冲压是指通过冲压机将金属板材置于模具中,经过冲击力的作用下,使其发生塑性变形,最终得到所需形状的金属成形方法。
冲压工艺适用于生产各类薄板金属产品,如汽车车身板、电器外壳等。
七、粉末冶金是指将金属粉末与非金属粉末按一定配比混合,压制成坯料后通过烧结等过程,最终得到具有一定形状和性能的金属制品的工艺方法。
粉末冶金工艺适用于生产各类复杂形状、高精度的金属制品。
以上是金属材料成形工艺的简要介绍,为了保证金属制品质量和实现成形工艺的控制,需要进行相应的工艺控制。
【机械专业中文翻译】金属板料成型过程控制器的设计
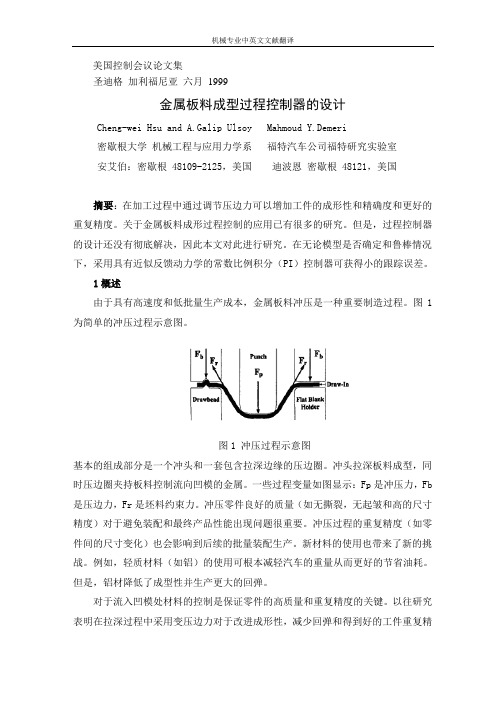
美国控制会议论文集圣迪格加利福尼亚六月1999金属板料成型过程控制器的设计Cheng-wei Hsu and A.Galip Ulsoy Mahmoud Y.Demeri密歇根大学机械工程与应用力学系福特汽车公司福特研究实验室安艾伯:密歇根 48109-2125,美国迪波恩密歇根 48121,美国摘要:在加工过程中通过调节压边力可以增加工件的成形性和精确度和更好的重复精度。
关于金属板料成形过程控制的应用已有很多的研究。
但是,过程控制器的设计还没有彻底解决,因此本文对此进行研究。
在无论模型是否确定和鲁棒情况下,采用具有近似反馈动力学的常数比例积分(PI)控制器可获得小的跟踪误差。
1概述由于具有高速度和低批量生产成本,金属板料冲压是一种重要制造过程。
图1为简单的冲压过程示意图。
图1 冲压过程示意图基本的组成部分是一个冲头和一套包含拉深边缘的压边圈。
冲头拉深板料成型,同时压边圈夹持板料控制流向凹模的金属。
一些过程变量如图显示:Fp是冲压力,Fb 是压边力,Fr是坯料约束力。
冲压零件良好的质量(如无撕裂,无起皱和高的尺寸精度)对于避免装配和最终产品性能出现问题很重要。
冲压过程的重复精度(如零件间的尺寸变化)也会影响到后续的批量装配生产。
新材料的使用也带来了新的挑战。
例如,轻质材料(如铝)的使用可根本减轻汽车的重量从而更好的节省油耗。
但是,铝材降低了成型性并生产更大的回弹。
对于流入凹模处材料的控制是保证零件的高质量和重复精度的关键。
以往研究表明在拉深过程中采用变压边力对于改进成形性,减少回弹和得到好的工件重复精度。
一种变压边力应用的策略(如过程控制)如图2所示。
图2 是金属板材成型中的过程控制在该策略中,通过控制压边力按照事先设定好的轨迹(如冲头的力-位移曲线)控制一个可测的过程变量(如冲力)。
相似的方法在文献【5,6,7】中有所报道。
最近对于金属板成型的研究又得出以下结论:1.零件质量的一致性可以通过反馈跟踪特性来提高。
无模金属板料成形技术(单点渐进式成形)

中国首辆标准校车0001号 无锡市澳富特精密快速成形科技有限公司
轿车部件生产
无模金属板第料1成步形技: 术成(单形点渐进式成形)
第2步 : 切边, 割孔
无模成形
激光切边, 割孔
无模数控成形
激光切割完成
无锡市澳富特精密快速成形科技有限公司
引擎罩外壳
无模金属板料成形技术(单点渐进式成形)
无锡市澳富特精密快速成形科技有限公司
单点渐进式成形的成形方法
无模金属板料成形技术(单点渐进式成形)
无锡市澳富特精密快速成形科技有限公司
单点渐进式成形技术简介
无模无金模金属属板板料料成的形技成术形(单点技渐术进式是成国形)际上一种先进的柔性加工工艺。该工艺不需 要专用模具,具有生产周期短、成本低的优点。特别适合于小批量、多品种、 复杂金属板材零件的生产。
无锡市澳富特精密快速成形科技有限公司
单点渐进式成形的优势
无模金属板料成形技术(单点渐进式成形)
板料厚度:从0.1~4毫米 压头的运行速度:可达100米/分种 成形时间:取决于工件的尺寸和成形参数,通常数小时 材料的延伸率:可高达300%
无锡市澳富特精密快速成形科技有限公司
单点渐进式成形的应用领域
汽无车模制金属造板料业成:形技汽术(车单点样渐进车式覆成形盖) 件生产、限量版汽车生产、汽车覆盖件 的维修备件市场; 模具制造业:风电机舱罩,风电叶片,游艇外壳等玻璃钢产品的模具 制作;EPS、PU等发泡材料模具制作;滚塑成型产品模具制作; 机械制造业:机器设备上复杂造型、曲面的面板生产; 航空航天业:飞机内壳体、内饰件、雷达抛物天线、人造卫星外壳、 火箭导流罩的生产; 建筑业:城市雕塑,个性建筑装修外观; 船舶制造业:金属冲锋舟、摩托艇、救生艇的船身制作; 医学领域:颅骨修补及医用支架的制造;
金属板料成形数值模拟的研究现状

金属板料成形数值模拟的研究现状一、引言金属板料成形数值模拟是现代制造业中不可或缺的一环。
通过数值模拟可以预测金属板料在成形过程中的变形、应力分布等物理量,从而优化工艺参数,提高成形质量和效率。
本文将介绍金属板料成形数值模拟的研究现状。
二、数值模拟方法1. 有限元法有限元法是目前最为常用的数值模拟方法之一。
它将连续体划分为多个小单元,在每个小单元内近似求解其物理量,最后通过组合得到整体的物理量分布。
有限元法可以考虑材料非线性、边界条件复杂等因素,适用范围广泛。
2. 边界元法边界元法是另一种常用的数值模拟方法。
它将问题转化为求解边界上的物理量分布,避免了对整个区域进行离散化计算。
边界元法适用于具有对称性或者具有复杂几何形状的问题。
3. 网格无关法网格无关法是相对于传统有限元法而言的新兴方法。
它不需要事先确定网格大小和结构,可以自动适应物理量分布的变化。
网格无关法适用于具有较大变形或者复杂几何形状的问题。
三、数值模拟在金属板料成形中的应用1. 成形过程分析数值模拟可以对金属板料成形过程进行分析,预测变形、应力分布等物理量。
通过优化工艺参数,可以避免一些不必要的缺陷和失效。
2. 模具设计数值模拟可以为模具设计提供依据。
通过对成形过程中应力和变形的预测,可以确定合适的模具结构和尺寸,从而达到更好的成形效果。
3. 材料选择数值模拟还可以为材料选择提供参考。
通过预测不同材料在成形过程中的性能表现,可以选择最为适合的材料,提高生产效率和质量。
四、数值模拟存在的问题及发展趋势1. 计算精度问题目前数值模拟存在计算精度不高、计算时间长等问题。
需要进一步发展更加高效精确的数值模拟方法。
2. 跨尺度建模问题金属板料成形涉及到多个尺度,如宏观尺度、晶体尺度等。
如何将不同尺度的模型相结合,进行跨尺度建模是一个重要的研究方向。
3. 多物理场耦合问题金属板料成形涉及到多种物理场,如力学、热学、电磁学等。
如何将这些物理场相互耦合起来进行计算,是数值模拟发展的重要方向之一。
金属工艺及材料成形技术
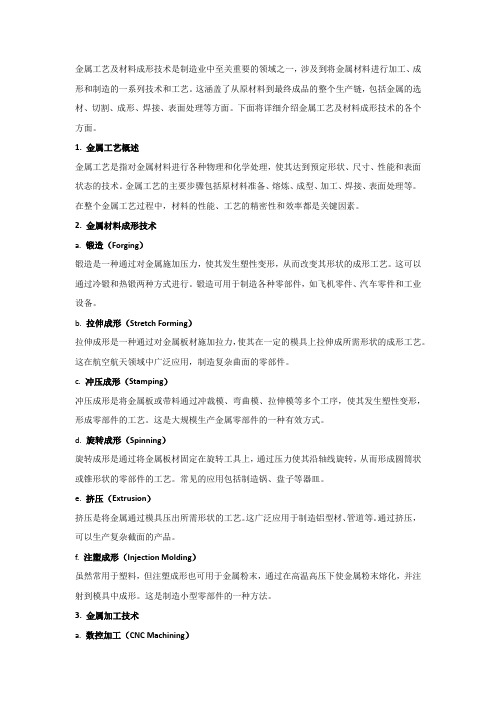
形和制造的一系列技术和工艺。
这涵盖了从原材料到最终成品的整个生产链,包括金属的选材、切割、成形、焊接、表面处理等方面。
下面将详细介绍金属工艺及材料成形技术的各个方面。
1. 金属工艺概述金属工艺是指对金属材料进行各种物理和化学处理,使其达到预定形状、尺寸、性能和表面状态的技术。
金属工艺的主要步骤包括原材料准备、熔炼、成型、加工、焊接、表面处理等。
在整个金属工艺过程中,材料的性能、工艺的精密性和效率都是关键因素。
2. 金属材料成形技术a. 锻造(Forging)锻造是一种通过对金属施加压力,使其发生塑性变形,从而改变其形状的成形工艺。
这可以通过冷锻和热锻两种方式进行。
锻造可用于制造各种零部件,如飞机零件、汽车零件和工业设备。
b. 拉伸成形(Stretch Forming)拉伸成形是一种通过对金属板材施加拉力,使其在一定的模具上拉伸成所需形状的成形工艺。
这在航空航天领域中广泛应用,制造复杂曲面的零部件。
c. 冲压成形(Stamping)冲压成形是将金属板或带料通过冲裁模、弯曲模、拉伸模等多个工序,使其发生塑性变形,形成零部件的工艺。
这是大规模生产金属零部件的一种有效方式。
d. 旋转成形(Spinning)旋转成形是通过将金属板材固定在旋转工具上,通过压力使其沿轴线旋转,从而形成圆筒状或锥形状的零部件的工艺。
常见的应用包括制造锅、盘子等器皿。
e. 挤压(Extrusion)挤压是将金属通过模具压出所需形状的工艺。
这广泛应用于制造铝型材、管道等。
通过挤压,可以生产复杂截面的产品。
f. 注塑成形(Injection Molding)虽然常用于塑料,但注塑成形也可用于金属粉末,通过在高温高压下使金属粉末熔化,并注射到模具中成形。
这是制造小型零部件的一种方法。
3. 金属加工技术a. 数控加工(CNC Machining)加工具有高精度、高效率和灵活性的优势,广泛应用于定制零部件制造。
b. 电火花加工(EDM)电火花加工是通过电脉冲放电的方式在金属工件上形成微小的放电坑,从而实现零部件的精密加工。
金属材料的成型工艺

5
20231/7./17爆炸焊
爆炸焊是以炸药为能源进行金属间焊接的方法。这种焊接是 利用炸药的爆轰,使被焊金属面发生高速倾斜碰撞,在接触面上造 成一薄层金属的塑性变形,在此十分短暂的冶金过程中形成冶金结 合。
爆炸焊的特点是: 1)能将任意相同的、特别是不同的金属材料迅速牢固地焊接起来。 2)工艺十分简单,容易掌握。 3)不需要厂房、不需要大型设备和大量投资。 4)不仅可以进行点焊和线焊,而且可以进行面焊-爆炸复合,从 而获得大面积的复合板、复合管和复合管棒等。 5)能源为低焊速的混合炸药,它们价廉、易得、安全和使用方便。
4
锻造基础知识
锻202造1/7/是17 对金属坯料(不含板材)施加外力,使其产生塑性变形、改变尺
寸、形状及改善性能,用以制造机械零件、工件、工具或毛坯的成形加 工方法。
根据在不同的温度区域进行的锻造,针对锻件质量和锻 造工艺要求的不同,可分为冷锻、温锻、热锻三个成型温 度区域。一般地讲,在有再结晶的温度区域的锻造叫热锻, 不加热在室温下的锻造叫冷锻。
的工件,形状和尺寸精度高,表面光洁,加工工序少, 便于自动化生产。当加工工件大、厚,材料强度高、 塑性低时,都采用热锻压。
(4)等温锻压 工件在整个成形过程中温度保持
不变。等温锻压是为了充分利用某些金属在某一温度 下所具有的高塑性,或为了获得特定的组织和性能, 所需费用较高,仅用于特殊的锻压工艺,如超塑成形。
7
4.冲压 2021/7/17
冲压:金属板料在冲压模之间受压产生分离或产生塑
性变形的加工方法。
按加工温度分类:热冲压和冷冲压。前者适合变 形抗力高,塑性较差的板料加工;后者在室温 下进行,是薄板常用的冲压方法。
8
•冲压基础知识
金属板料高频冲击成形技术研究
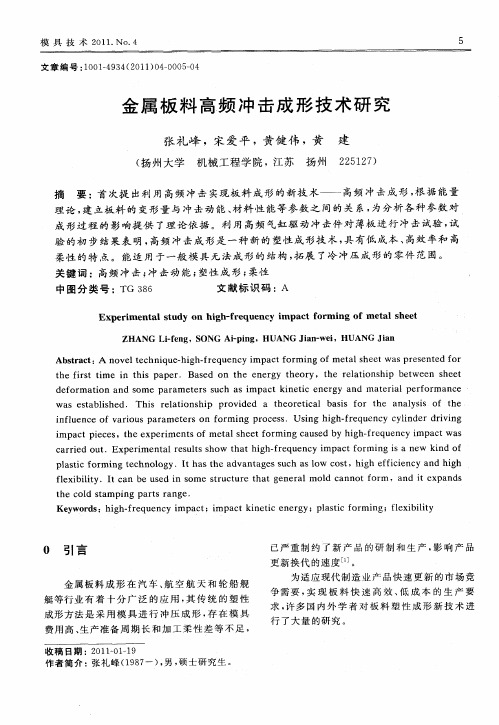
摘 要 :首 次提 出利 用 高频 冲 击 实 现 板 料 成 形 的 新技 术— — 高频 冲 击 成 形 , 据 能 量 根
理 论 , 立 板 料 的 变形 量 与 冲 击动 能 、 料 性 能 等 参 数 之 间 的 关 系 , 分析 各 种 参 数 对 建 材 为 成 形 过 程 的 影 响提 供 了理 论 依 据 。利 用 高 频 气缸 驱 动 冲 击件 对 薄板 进 行 冲 击试 验 , 试
板料成形工艺及模具

载荷值。
图6-15
拉深变形规律
2)主要工艺参数 拉深系数m=d/D或它的倒数拉深比R= D/d反映了拉深变形程度。当m≤mmin或 R≥Rmax时,制件会开裂。在生产中,m或R是 进行工艺计算和模具设计最主要工艺参数。 mmin或Rmax表示拉深的加工极限。一般而言, 圆筒形件的首次极限拉深系数mmin为0.5左右。
来决定。
图6-17 胀形变形规律
如图6-18所示,当相对法兰直径比df/d≥2.5 时,法兰处进行拉深变形的阻力大于底部胀 形变形所需的力,工序性质属于胀形。与拉 深加工相同,除了毛坯几何尺寸外,压边力 大小、润滑和摩擦条件、模具的形状与几何 尺寸等因素也会在不同程度上影响到工序的 变形性质。
2)主要工艺参数 胀形工序种类繁多,表示胀形变形程度的 参数也不相同。 在生产中,常用 工程应变:ε=(l-l0)/l0×100% (压筋:l0—原始长度,l—变形后弧长); 胀形深度:h(压凸包)
(4)拉深力-行程曲线 由图6-14可见,变 形初到中期,硬化使拉深力增大的速度超过法 兰面积减小使拉深力降低的速度,拉深力增加。 此后,面积减小使拉深力降低的速度超过加工 硬化使拉深力增大的速度,拉深力下降。拉深 力先增后降。
图6-14
拉深力-行程曲线
(5)拉深变形规律 图6-15显示了毛坯几何尺 寸和板料成形工序类型的关系。由图可见, 若毛坯底部带有底孔时,坯料在外力作用下 可能产生拉深、胀形和内孔翻边三种形式的 变形。坯料进行哪种形式的变形由金属的变 形规律所决定,即金属的变形对应于最低的
图6-20 翻边变形过程与变形区应力、应变状态
(2)主要变形区 如图6-20a所示,内孔翻 边时,主要变形区被限制在凹模圆角以内的 (d—d0)环形区域内。与拉深成形相同,在内 孔翻边过程中,变形区在不断缩小。
板料成形技术的原理
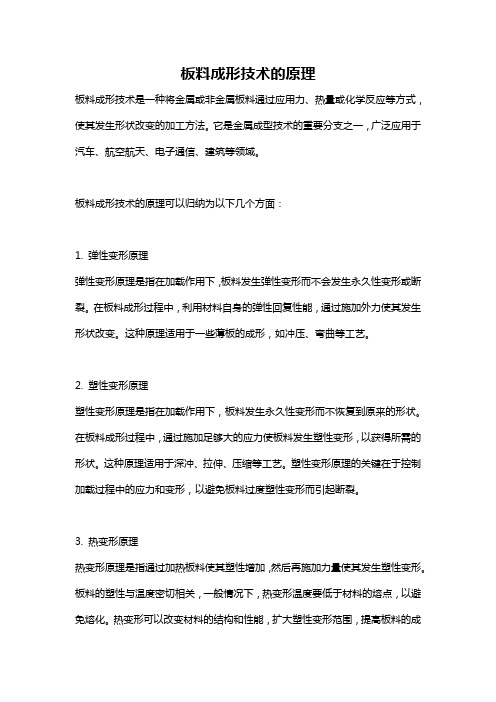
板料成形技术的原理板料成形技术是一种将金属或非金属板料通过应用力、热量或化学反应等方式,使其发生形状改变的加工方法。
它是金属成型技术的重要分支之一,广泛应用于汽车、航空航天、电子通信、建筑等领域。
板料成形技术的原理可以归纳为以下几个方面:1. 弹性变形原理弹性变形原理是指在加载作用下,板料发生弹性变形而不会发生永久性变形或断裂。
在板料成形过程中,利用材料自身的弹性回复性能,通过施加外力使其发生形状改变。
这种原理适用于一些薄板的成形,如冲压、弯曲等工艺。
2. 塑性变形原理塑性变形原理是指在加载作用下,板料发生永久性变形而不恢复到原来的形状。
在板料成形过程中,通过施加足够大的应力使板料发生塑性变形,以获得所需的形状。
这种原理适用于深冲、拉伸、压缩等工艺。
塑性变形原理的关键在于控制加载过程中的应力和变形,以避免板料过度塑性变形而引起断裂。
3. 热变形原理热变形原理是指通过加热板料使其塑性增加,然后再施加力量使其发生塑性变形。
板料的塑性与温度密切相关,一般情况下,热变形温度要低于材料的熔点,以避免熔化。
热变形可以改变材料的结构和性能,扩大塑性变形范围,提高板料的成形性能。
热变形原理适用于复杂形状的成形,如热深拉、热冲压等工艺。
4. 化学反应原理化学反应原理是指通过在板料表面产生化学反应,改变板料的表面性质从而达到成形的目的。
常用的化学反应方法有电镀、化学腐蚀等。
通过这些方法,可以在板料表面形成一层新的物质,改变其摩擦、润滑、耐蚀性等性能,以便进行成形。
总之,板料成形技术的原理主要包括弹性变形、塑性变形、热变形和化学反应。
不同的板料成形工艺根据材料的特性和形状要求,选择适合的原理和方法进行成形。
通过合理控制成形参数和工艺流程,可以实现对板料的精确成形,满足不同工业领域对于各种复杂形状的需求。
大学金属工艺的金属塑性加工的相关问题的讲解
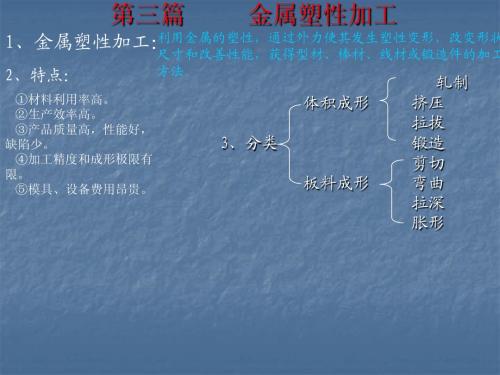
金属纤维组织
图3-6铸锭热变形前后的组织
纤维组织的特点
变形程度越大,纤维组织越明显。 常用锻造比γ表示变形程度。坯料拔长时的锻造比为: γ=F0/F 式中F0为坯料拔长前的横截面积;F为坯料拔长后的横截面积。 纤维组织使金属在性能上具有方向性。 纵向(平行于纤维方向)上的塑性、韧性提高, 横向(垂直于纤维方向)上的塑性、韧性则降低。 纤维组织的稳定性很高,不能用热处理或其它方法加以消除 不能用热处理或其它方法加以消除, 不能用热处理或其它方法加以消除 只有经过锻压使金属变形,才能改变其方向和形状。
知识点:
第二章
锻造
1、自由锻和模锻。 2、胎模锻。 3、余块、机械加工余量。 4、模锻--焊接成形。
锻造:在加压设备及工(模)具作用下,铸锭产生局部或全部的塑
性变形,以获得一定几何尺寸、形状和质量的锻件的加工方法。
第一节 锻造方法
一、自由锻
(1)、 (1)、自由锻是利用冲击力或压力使金属在上、下砧之间产生塑性变
位错移动:高位能的位错处原子, 位错移动 在比理论值小的切应力下滑移。从 一个位置滑移到另一个位置。
未变形
弹性变形
弹塑性变形
塑性变形
图3-2
位错运动引起塑性变形示意图
位 错 移 动 的 结 果: 塑 性 变 形。
晶内变形:金属由大量微小晶粒组成的 晶内变形 多晶体,由组成多晶体的许多单个晶粒 产生变形。其综合效果是塑性变形。 其综合效果是塑性变形。 其综合效果是塑性变形
A 锻造比: 锻造比:Y镦= A0 >1
拔长、镦粗、冲孔、弯曲、扭转、错移、 拔长、镦粗、冲孔、弯曲、扭转、错移、切割
使坯料高度减小,截面积增大的工序。 使坯料高度减小,截面积增大的工序。
金属板料成形摩擦机理研究
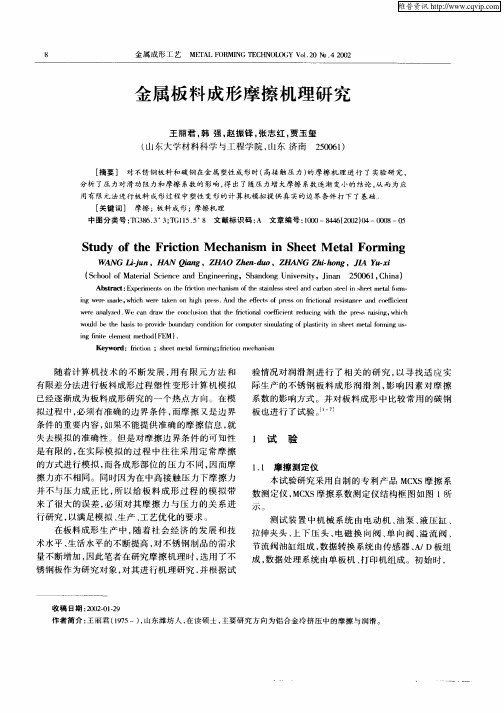
ig w r n d , ih w r tk n o ih p e s An h f cso r s n f cin lrss n e mi  ̄mee t n e e la e whc ee ' e n hg r ̄ . d te e e t fp s o r t a e it c d c a e i o a in w r n y e We c n d a i o c u in ta h it n le mee trd cn i e p e s r i n , ic ee a a z d. a r w te c n lso h tte f ci a  ̄ l l r o in e u i g w t t rs as g wh h hh i w ud t h b sst r vd o n a y c n io rc mp trs lt g o lsii ns e t tl o mig U — o l ) te a i o po ie b u d r o d t n f o ue i ai f at t i h e mea r n S e ' i o mu n p cy f
中 图分 类 号 :G 8 . 3 T I5 5 T 36 3 :G 1 . 8 文 献 标 识 码 : 文 章 编 号 :00—84 (02 0 A 10 4 6 20 )4—00 0 08— 5
S u y o h i to e h n s n S e t M e a r i g t d f t e Fr c i n M c a im i h e t lFo m n
际生 产 的不 锈 钢 板 料 成 形 润 滑 剂 , 响 因 素 对 摩 擦 影
已经逐渐成为板料成形研究的一个热点方 向。在模 系数 的影 响 方式 。并对 板 料成 形 中 比较 常 用 的碳 钢 【 拟过 程 中 , 须有 准确 的边界 条 件 , 摩 擦 又是边 界 板也 进 行 了试 验 。卜 必 而
金属板料成形模具接触应力研究现状及应用
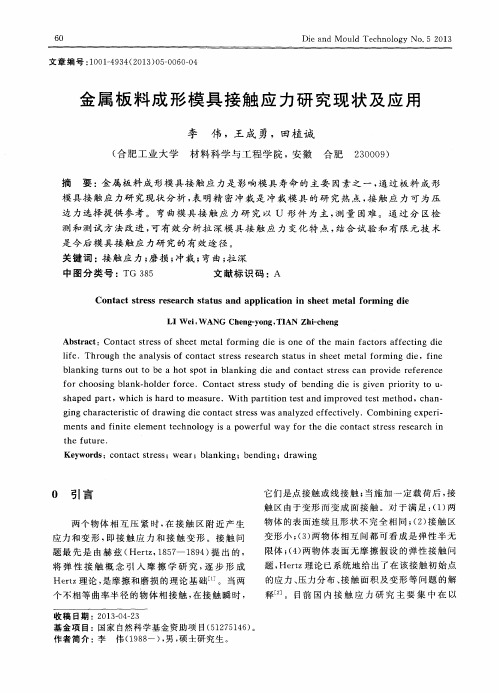
边 力选择提供参 考 。弯曲模具接 触 应 力研 究 以 u 形 件 为主 , 测 量 困难 。通过 分 区检
测 和 测试 方 法 改进 , 可 有 效 分 析 拉 深 模 具 接 触 应 力 变化 特 点 , 结 合 试 验 和 有 限 元 技 术
是 今 后 模 具接 触 应 力 研 究 的有 效 途 径 。 关键 词 : 接 触应 力; 磨损 ; 冲裁 ; 弯曲 ; 拉 深
LI We i , W AN G Che ng - y on g, TI AN Zh i — c he ng
Abs t r a c t  ̄Cont a c t s t r e s s of s hee t me t a l f or mi ng di e i s o ne of t he mai n f ac t or s a f f e c t i ng di e
60
Байду номын сангаас
Di e a n d Mo ul d Te c h no l o gy No . 5 2 0 1 3
文章 编号 : 1 0 0 1 — 4 9 3 4 ( 2 0 1 3 ) 0 5 — 0 0 6 0 — 0 4
金 属 板 料 成 形 模 具 接 触 应 力 研 究 现 状 及 应 用
t he f ut u r e.
Ke y wo r d s :c o n t a c t s t r e s s ;we a r ;b l a n k i n g ;b e n d i n g;d r a wi n g
0
引言
两个物体 相 互压 紧 时 , 在 接 触 区 附 近 产 生
中 图 分 类 号 :T G 3 8 5
金属板料拉深成形工艺参数优化的正交试验研究
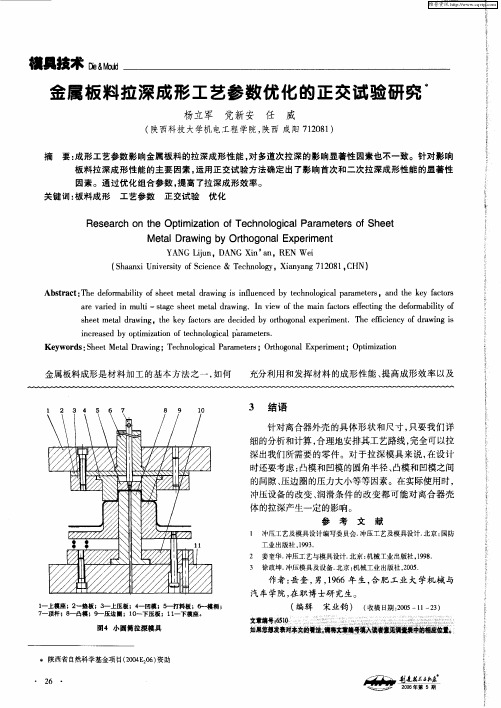
关键词 : 板料成形
工艺参数
正交试验 优化
Re e rho h t z t n o e h oo ia rmee so e t s ac nte Opi ai fT c n lgc l mi o Paa tr fSh e
Ab t a t T e d fr b l y o h e tld a i g i i f e c d b e h oo i a p r mee s n h e a tr s r c : h e o ma i t fs e tmea r w n s n u n e y tc n l gc l a a tr ,a d t e k y fco s i l a e v re n mut —sa e s e tmea rwi g I iw o e ma n f co s efc i g t e d f r b l y o r a id i l i tg h e tld a n . n ve ft i a tr f t h eo ma i t f h e n i s e tme a r w n ,t e k y f co s a e d cd d b r o o a e p r n .T e ef in y o r w n s h e tld a i g h e a tr r e i e y o t g n l x e i h me t h f c e c fd a i g i i 维普资ຫໍສະໝຸດ 横曼技术 D i e &
金属板料 拉深成形工艺参数优化 的正 交试验研究
冲压工艺及模具设计习题库(附答案)

第1章冲压工艺基础知识一、填空题1.冲压加工是利用安装在压力机上的模具对材料施加外力,使其产生塑性变形或分离,从而获得所需形状和尺寸工件的一种压力加工方法。
2.冲压一般在常温下进行,故又称冷冲压。
因为冲压主要是用板料加工成零件,所以又叫板料冲压。
3.冲压的三要素是指设备(压力机)、模具、原材料。
4.冲压和锻造合称为压力加工,简称锻压。
5.同一副模具生产出来的同一批产品尺寸一致性高,具有很好的互换性。
6.冲压件的尺寸稳定,互换性好,是因为其尺寸公差由冲压模来保证。
7.分离工序是使板料的一部分与另一部分沿一定的轮廓线发生断裂而分离。
8.伸长类变形时,变形区最大主应力为拉应力,其破坏形式为拉裂,变形区材料厚度减薄。
9.压缩类变形时,变形区最大主应力为压应力,其破坏形式为起皱,变形区材料厚度增厚。
10.冲压按工序的组合形式可分为单工序冲压、复合冲压和级进冲压。
11.冲压材料的成形性能主要体现为抗破裂性、贴模性和定形性三个方面。
12.贴模性是指金属板料在成形过程中获得模具形状和尺寸且不产生皱纹等板面几何缺陷的能力。
13.定形性是指冲压制件脱模后抵抗回弹,保持其在模内既得形状和尺寸的能力。
14.材料屈服极限与强度极限的比值称为屈强比,其值越大,说明塑性变形区间范围越大。
15.常用冲压材料有金属材料和非金属材料。
16.JB23-63型号的压力机的公称压力为630KN 。
17.中小型冲压模是将模柄安装在压力机的滑块模柄孔中。
18.压力机滑块从上死点到下死点所经过的距离称为滑块行程。
二、判断题(正确的打√,错误的打×)1.冲模的制造一般是单件小批量生产,因此冲压件也是单件小批量生产。
(×)2.落料和弯曲都属于分离工序,而拉深、翻边则属于变形工序。
(×)3.分离工序是指对工件的剪裁和冲裁工序。
(√)4.所有的冲裁工序都属于分离工序。
(√)5.成形工序是指对工件弯曲、拉深、成形等工序。
(√)6.成形工序是指坯料在超过弹性极限条件下而获得一定形状。
《金属塑性成型原理》(俞汉清主编)课后习题及答案

第一章1.什么是金属的塑性?什么是塑性成形?塑性成形有何特点?塑性----在外力作用下使金属材料发生塑性变形而不破坏其完整性的能力;塑性变形----当作用在物体上的外力取消后,物体的变形不能完全恢复而产生的残余变形;塑性成形----金属材料在一定的外力作用下,利用其塑性而使其成型并获得一定力学性能的加工方法,也称塑性加工或压力加工;塑性成形的特点:①组织、性能好②材料利用率高③尺寸精度高④生产效率高2.试述塑性成形的一般分类。
Ⅰ.按成型特点可分为块料成形(也称体积成形)和板料成型两大类1)块料成型是在塑性成形过程中靠体积转移和分配来实现的。
可分为一次成型和二次加工。
一次加工:①轧制----是将金属坯料通过两个旋转轧辊间的特定空间使其产生塑性变形,以获得一定截面形状材料的塑性成形方法。
分纵轧、横轧、斜轧;用于生产型材、板材和管材。
②挤压----是在大截面坯料的后端施加一定的压力,将金属坯料通过一定形状和尺寸的模孔使其产生塑性变形,以获得符合模孔截面形状的小截面坯料或零件的塑性成形方法。
分正挤压、反挤压和复合挤压;适于(低塑性的)型材、管材和零件。
③拉拔----是在金属坯料的前端施加一定的拉力,将金属坯料通过一定形状、尺寸的模孔使其产生塑性变形,以获得与模孔形状、尺寸相同的小截面坯料的塑性成形方法。
生产棒材、管材和线材。
二次加工:①自由锻----是在锻锤或水压机上,利用简单的工具将金属锭料或坯料锻成所需的形状和尺寸的加工方法。
精度低,生产率不高,用于单件小批量或大锻件。
②模锻----是将金属坯料放在与成平形状、尺寸相同的模腔中使其产生塑性变形,从而获得与模腔形状、尺寸相同的坯料或零件的加工方法。
分开式模锻和闭式模锻。
2)板料成型一般称为冲压。
分为分离工序和成形工序。
分离工序:用于使冲压件与板料沿一定的轮廓线相互分离,如冲裁、剪切等工序;成型工序:用来使坯料在不破坏的条件下发生塑性变形,成为具有要求形状和尺寸的零件,如弯曲、拉深等工序。
- 1、下载文档前请自行甄别文档内容的完整性,平台不提供额外的编辑、内容补充、找答案等附加服务。
- 2、"仅部分预览"的文档,不可在线预览部分如存在完整性等问题,可反馈申请退款(可完整预览的文档不适用该条件!)。
- 3、如文档侵犯您的权益,请联系客服反馈,我们会尽快为您处理(人工客服工作时间:9:00-18:30)。
8
间隙对剪切裂纹与断面质量的影响 a)间隙过小 b)间隙合理 c)间隙过大
9
各个参数的影响
1、间隙量增加,冲裁边缘粗糙。 2、金属板材塑性的增加,冲裁边缘光亮带和粗糙区 域的比值增加,同时随着板材厚度和间隙量的增加 而减少。
3、变形区的宽度依赖于凸模的速度。随着速度的
增加,由于塑性变形产生的热量被限制在越来越小
剪切操作
各种板金属剪切操作
12
精密冲裁
(a)
普通冲裁与精密冲裁的效果对比
精密冲裁
精冲模工作部分的组成 (a)带齿圈压板精冲(b)(c)普通冲裁
1-凸模 2-齿圈压板 3-板料 4-凹模 5-顶出器
14
分条
圆盘剪纵切分条
15
其它冲裁工艺
分段冲裁 钢尺模切,适用于软金属、皮革、纸张、橡胶
41
拉深的应用
2、变薄拉深
所谓变薄拉深,主 要是在拉深过程中 改变拉深件筒壁的 厚度,而毛坯的直 径变化很小
42
拉深的应用
3、重拉深
一次拉深比较困难时
43
拉深的应用
4、无压边圈 5、压印
Figure 16.37 An embossing operation with two dies. Letters, numbers, and designs on sheet-metal parts and thin ash trays can be produced by this process.
弯管成形
弯管成形 常用芯棒、填砂等方法防止管壁皱曲
35
拉深
利用具有一定圆角半 径的模具将冲裁后得 到的平板坯料加工变 形成为开口空心零件 的冲压工艺方法。
拉深件
拉深工艺
36
深冲
图8.32(a)圆形板坯进行深冲的示意图;(b)深冲过程中的工艺变量,除了冲压力图中指出 的所有变量都是独立的。
37
55
深冲性
是指钢板冲压成型时,钢板厚度方向上的变 化和平面(长度和宽度方向)变化。如果在 平面上性能不同,会出现制耳。在厚度上性 能不好,会出现冲漏的现象。通常深冲性能 用r值表示。 制耳是冲压件边部高低不平。 冲漏是指冲压件局部有空洞。
38
各向异性
拉伸实验中的试样应变,该应变用于确定板 料法向和平面各向异性。
图16.19 弯曲回弹. 弯曲后零件有回复弹性的趋势,使其弯曲角度增加 。
影响回弹的因素
1、材料的力学性能 (屈服点和弹性模量) 2、弯曲角(弯曲角大,弯曲变形区大,回弹值大) 3、弯曲方式(自由弯曲回弹量大,校正弯曲回弹量小) 4、弯曲件形状(形状复杂回弹量小)
29
消除回弹
图16.20 减小或消除回弹的方法
冲裁模具
复合模
(a) (b)
复合模工作示意图
19
2. 弯曲 Bending
利用模具或其它工具将坯料一部分相对另一部 分弯曲成一定的角度和圆弧的变形工序。
20
弯曲时受力分析
变形区:
外层:受切向拉力作用,发生伸长变形。为最危 险部位。 内层:受切向压力作用,发生压缩变形 中性层Neutral Line:切向应力或切向应变为零, 位于板料中心部位
44
其他板材成形工艺
45
橡皮成形
金属板弯曲及压印实例。金属凸模、 柔性材料凹模
胀形
胀形工艺 (a) 管件胀形常用柔性填料(橡胶、水等); (b) 通过内部液体压力胀形得到T型管
47
波纹管成形
图 波纹管成形过程
48
液压胀形工艺
49
旋压成形(spinning)
一种成形金属空心回转体件的工艺方法。在坯料随 模具旋转或旋压工具绕坯料旋转中,旋压工具与坯 料相对进给,从而使坯料受压并产生连续、逐点的 变形。包含普通旋压和变薄旋压(即强力旋压)。
影响因素: 1、材料的力学性能 2、板料的方向性 3、板料的表面和侧面质量 4、弯曲件的宽度、弯曲角度以及材料的厚度等。 主要利用经验数据来确定材料许可的最小弯曲半径。
各种材料在室温下的最小弯曲半径
表 16.3 状态 材料 铝合金 紫铜 青铜、低铅青铜 镁 钢 奥氏体不锈钢 低碳、低合金、高强度低合金钢 钛 钛合金 退火 0 0 0 5T 0.5T 0.5T 0.7T 2.6T 硬化 6T 4T 2T 13T 6T 4T 3T 4T
金属板料成形工艺分类
4
本章内容
板料的冲裁 板料的弯曲 板料的拉深 板料的其他成形工艺
5
1. 冲裁 Blanking
使板料沿封闭轮廓线分离的工序,包括落料与冲孔。
落料 :得到片状冲压件的外形
冲孔 :得到冲压件上的孔
6
冲裁成形
冲裁工艺(冲孔和落料)
冲裁成形过程
7
分离工序
主要参数: 冲头/模具间隙量 重叠量 冲头/模具的材料和形状 落料速度 润滑状态
21
为避免造成板料的破裂:
相对弯曲半径(r/t) :表示弯曲变形程度
坯料越厚,弯曲半径越小,其变形程度越大。
最小相对弯曲半径rmin/t ≥(0.25~1.0)。
材料塑性好,相对弯曲半径可小些。
22
弯曲
(a)
(b)
(c)
最小弯曲半径
最小弯曲半径:在保证弯曲毛坯外层纤维不发生破坏的条件 下,弯曲件内表面所能达到的最小圆角半径。
剪切余料:高达30%,计算机排样
冲裁间隙:小孔大间隙,大孔小间隙;
c板厚的(1%~)2%~8%(~30%);
16
Hale Waihona Puke 冲裁模具间隙量 材料类型、性能、厚度、坯料尺寸以及与 初始板料边缘的距离等因素的函数
冲裁边修 整 冲裁、修整 组合工艺
冲裁边缘进行修整的示意图
17
冲裁模具
冲头和模具使用剪切角的实例
18
的范围。进而冲裁区变窄,表面变得更光滑,形成
更少的毛刺。
10
冲裁力计算
冲裁力: F(冲裁力)=0.7×t(板厚)×l(周长)×σb(强度极限)
例:估算室温下在厚度为3.2mm的钛铝合金(Ti-6Al-4V)板上 冲裁一个直径25mm的孔所需的冲裁力。
F 0.7(0.0032)( )(0.025)(1.4 105 ) 0.17 MN
不同金属板材拉深比与平均法向 各向异性的关系
39
制耳
图8.45拉深筒形件产生的制耳现象,由于金属板材的各项异性引起。
40
拉深的应用
1、拉延筋 在成形过程中,由于各个部分变形情况复杂、板料流动速度不 一致,易出现拉裂,起皱等现象, 因此需要在凹模周围布置拉延 筋来改善成形质量。
图 (a) 拉延筋示意图 (b)当利用拉延筋控制材料移动时,拉深盒形件金属的流动 (c) 采用深 冲在翻边处成形圆形栅格
弯曲操作
常见的弯曲工艺。模具尺寸W用于计算弯曲力。
26
最小弯曲力
最小弯曲力(a系数,U型砧时为0.3~0.7,V型砧时为1.3)
a s lt P w
2
回弹
材料塑性变形必然伴随着弹性变形,当弯曲工件所受外力去除后,塑 性变形保留下来,弹性变形部分恢复,结果使弯曲件的弯曲角、弯曲 半径与模具尺寸不一致,这种现象称为弯曲回弹。
50
旋压成形
利用辊轮、压头等工具对随旋压模转动的坯料作进给 运动并施压,使其径向尺寸产生显著变化,形成所需 形状、尺寸零件的冲压加工方法。
模具
坯料
51
辊轮
特点: 点成形,变形小,在一次成形中可完成普 通方法的多道工序,形状精度高,模具费用低, 加工方法简单,可完成大型件的旋压成形。
52
压缩机轴旋压成形工艺
超音速协和飞机用涡喷发动机轴的旋压成形
铝饮 料罐 (两 片罐) 制作 工艺
54
表 16.1 工艺 辊成形 张拉成形 拉伸 冲压
板金属成形工艺的主要特点
特点 适用于复杂断面长零件生产,表面质量好,生产效率高,工具成本高 适用于薄壁、长零件生产,产量低、劳动力成本高、工具和设备成本与零件尺寸相关 适用于简单断面、深、中空零件生产,生产效率高、工具和装备成本高 包括很多种成形工艺,如冲孔、落料、弯曲、卷边、压印等,适用于多种简单或复杂形状零件生 产,生产效率高、工具和设备成本较高,劳动力成本低 橡胶胀形 适用于简单或复杂形状零件的拉伸或胀形。金属表面用橡胶填料保护,操作柔性化程度高,工具 成本低。 回转成形 适用于各种尺寸轴对称零件成形。表面光洁度高,工具成本低,劳动力成本高 超塑性成形 适用于形状复杂、表面结构精细、尺寸精度高零件的成形。成形时间长、效率低。产品不适用于 高温工况。 抛丸成形 适用于大型金属板壳加工,操作柔性化程度高,设备成本高 爆炸成形 适用于小批量、大型复杂形状金属板成形,一般用于成形轴对称零件成形。工具成本低,劳动力 成本高、生产周期长 电脉冲成形 适用于低强度金属板中空零件的胀凸成形。产品一般为管状,生产效率高、需要专用工具
30
其它弯曲工艺1
不同弯曲工艺实例
31
其它弯曲工艺2
辊成形工艺示意图
32
其它弯曲工艺3
(a) 单模卷边成形. (b) 双模卷边成形
33
其它弯曲工艺4
图8.25 不同的翻边工艺 (a) 板片上的翻边 (b) 压凹痕. (c) 金属板上的孔翻边,不需要事先冲孔. 注意,翻边边缘粗糙. (d) 34 管材翻边,翻边边缘变薄
金属板料成形
基本概念
板成形产品:金属桌椅、文件柜、汽车覆盖件、食品罐头…… 早期的板成形产品:金、银、铜,家用器皿、珠宝首饰……
常用材料:低碳钢 低成本、高强度、好的可成形性
航空航天器用材料:铝合金、钛合金
金属塑性加工分类