机械外文翻译中英文 机床 模具 机械 材料.doc
机械材料中英文对照.doc

A123/A123M-02
Standard Specification for Zinc (Hot-Dip Galvanized) Coatings on Iron and Steel Products
钢铁产品的锌镀层(热浸镀锌)技术规范
A125-96(2001)
Standard Specification for Steel Springs, Helical, Heat-Treated
优质冷加工碳素钢棒材技术规范
A109/A109M-03
Standard Specification for Steel, Strip, Carbon (0.25 Maximum Percent), Cold-Rolled
冷轧碳素钢带技术规范
A111-99a(2004)e1
Standard Specification for Zinc-Coated (Galvanized) Iron Telephone andTelegraph Line Wire
Standard Specification for Seamless Carbon Steel Pipe for High-Temperature Service
高温用无缝碳素钢管
A108-03e1
Standard Specification for Steel Bar, Carbon and Alloy, Cold-Finished
钢铸件,奥氏体锰
A131/A131M-04ae1
Standard Specification for Structural Steel for Ships
海船用结构钢
A132-04
Standard Specification for Ferromolybdenum
机械外文翻译中英文

英文资料Limits and TolerancesThe breakage of the machine spare parts ,generally always from the surface layer beginning of .The function of the product ,particularly its credibility and durable ,be decided by the quantity of spare parts surface layer to a large extent. Purpose that studies the machine to process the surface quantity be for control the machine process medium various craft factor to process the surface quantity influence of regulation, in order to make use of these regulations to control to process the process, end attain to improve the surface quantity, the exaltation product use the function of purpose .The machine processes the surface quantity to use the influence of the function to the machine(A) The surface quantity to bear to whet the sexual influence1.Rough degree of surface to bear to whet the sexual influenceA just process vice-of two contact surfaces of good friction, the first stage is rough only in the surface of the peak department contact ,the actual contact area is much smaller than theoretical contact area, in contact with each other the peak of the units have very great stress, to produce actual contact with the surface area of plastic deformation, deformation and peak between the Department of shear failure, causing serious wear.Parts wear may generally be divided into three stages, the initial stage of wear and tear, normal wear and tear all of a sudden intense phase of stage wear.Parts of the surface roughness of the surface wear big impact. In general the smaller the value of surface roughness, wear better. However, surface roughness value is too small, lubricants difficult to store, contact between the adhesive-prone elements, wear it to increase. Therefore, the surface roughness of a best value, the value and parts of the work related to increased work load, the initial wear increased, the best rough surface is also increased.2.Cold Working hardening the surface of the wear resistanceProcessing the Cold Work hardening the surface of the friction surface layer of metal microhardness increase, it will generally improve the wear resistance. Cold Working but not a higher degree of hardening, wear resistance for the better, because too much will lead to hardening of the Cold Working excessive loose organization ofmetal, even a crack and peeling off the surface of the metal, declined to wear resistance.(B)The surface quality of the impact of fatigue strengthMetal hand alternating loads of fatigue after the damage occurred in parts often Chilled layer below the surface and, therefore parts of the surface quality of fatigue very influential.1.Surface roughness on the impact of fatigue strengthIn alternating load, the surface roughness of the Au-site easily lead to stress concentration, a fatigue crack, the higher the value of surface roughness, surface traces of Yu Shen Wen, Wen at the end of the radius smaller, anti-fatigue damage at the end of the more capacity Worse.2.Residual stress, fatigue Cold Work hardening of the impactResidual stress on the impact of large parts fatigue. Surface layer of residual stress fatigue crack will expand and accelerate the fatigue damage the surface layer and the residual stress can prevent fatigue crack growth, delaying the formation of fatigue damage.(C)The surface quality of the corrosion resistance of the impactParts of the corrosion resistance to a large extent depends on the surface roughness. The higher the value of surface roughness, Au Valley accumulate on the more corrosive substances. Corrosion resistance of the more worse.Surface layer of residual stress will produce stress corrosion cracking, lower parts of the wear-resistance, and the residual stress is to prevent stress corrosion cracking.(D) The surface quality with qualityRough surface will affect the value of the size of the co-ordination with the surface quality. The gap with rough value will increase wear and tear, increased space, with the requirements of the destruction of nature. For Fit, the assembly part of the process of convex surface-crowded peak times, the actual reduction of the surplus and reduce the support of the connection between the strength.DimensioningThe design of a machine includes many factors other than those of determining the loads and stresses and selecting the proper materials. Before construction or manufacture can begin, it is necessary to have complete assembly and detail drawings to convey all necessary information to the shop men. The designer frequently is called upon to check the drawings before they are sent to the shop. Much experience andfamiliarity with manufacturing processes are needed before one can become conversant with all phases of production drawings.Drawings should be carefully checked to see that the dimensioning is done in a manner that will be most convenient and understandable to the production departments. It is obvious that a drawing should be made in such a way that it has one and only one interpretation. In particular, shop personnel should not be required to make trigonometric or other involved calculations before the production machines can be set up.Dimensioning is an involved subject and long experience is required for its mastery.Tolerances must be placed on the dimensions of a drawing to limit the permissible variations in size because it is impossible to manufacture a part exactly to a given dimension. Although small tolerances give higher quality work and a better operating mechanism, the cost of manufacture increases rapidly as the tolerances are reduced, as indicated by the typical curve of Fig 14.1. It is therefore important that the tolerances be specified at the largest values that the operating or functional considerations permit.Tolerances may be either unilateral or bilateral. In unilateral dimensioning, one tolerance is zero, and all the variations are given by the other tolerance. In bilateral dimensioning, a mean dimension is used which extends to the midpoint of the tolerance zone with equal plus and minus variations extending each way from this dimension.The development of production processes for large-volume manufacture at low cost has been largely dependent upon interchangeability of component parts. Thus the designer must determine both the proper tolerances for the individual parts, The manner of placing tolerances on drawings depends somewhat on the kind of product or type of manufacturing process. If the tolerance on a dimension is not specifically stated, the drawing should contain a blanket note which gives the value of the tolerance for such dimensions. However, some companies do not use blanket notes on the supposition that if each dimension is considered individually, wider tolerance than those called for in the note could probably be specified. In any event it is very important that a drawing be free from ambiguities and be subject only to a single interpretation.Dimension and ToleranceIn dimensioning a drawing, the numbers placed in the dimension lines represent dimension that are only approximate and do not represent any degree of accuracy unless so stated by the designer.To specify a degree of accuracy, it is necessary to add tolerance figures to the dimension. Tolerance is the amount of variation permitted in the part or the total variation allowed in a given dimension. A shaft might have a nominal size of 2.5 in. (63.5mm), but for practical reasons this figure could not be maintained in manufacturing without great cost. Hence, a certain tolerance would be added and , if a variation of ±0.003 in.(±0.08mm) could be permitted, the dimension would be stated 2.500±0.003(63.5±0.008mm).Dimensions given close tolerances mean that the part must fit properly with some other part. Both must be given tolerances in keeping with the allowance desired, the manufacturing processes available, and the minimum cost of production and assembly that will maximize profit. Generally speaking, the cost of a part goes up as the tolerance is decreased. If a part has several or more surfaces to be machined, the cost can be excessive when little deviation is allowed from the nominal size.Allowance, which is sometimes confused with tolerance, has an altogether different meaning.It is the minimum clearance space intended between mating parts and representsthe condition of tightest permissible fit. If a shaft, size 1.4980.0000.003+-, is to fit a hole ofsize 1.5000.0030.000+-, the minimum size hole is 1.500 and the maximum size shaft is 1.498.Thus the allowance is 0.002 and the maximum clearance is 0.008 as based on the minimum shaft size and maximum hole dimension.Tolerances may be either unilateral or bilateral. Unilateral tolerance means that any variation is made in only one direction from the nominal or basic dimension.Referring to the previous example, the hole is dimensioned 1.5000.0030.000+-, whichrepresents a unilateral tolerance. If the dimensions were given as 1.500±0.003, the tolerance would be bilateral; that is , it would vary both over and under the nominal dimension. The unilateral system permits changing the tolerance while still retaining the same allowance or type of fit. With the bilateral system, this is not possible without also changing the nominal size dimension of one or both of the two mating parts. In mass production, where mating parts must be interchangeable, unilateral tolerances are customary. To have an interference or fore fit between mating parts, the tolerances must be such as to create a zero or negative allowance.Tolerances Limits and FitsThe drawing must be a true and complete statement of the designer’s expr essed in such a way that the part is convenient to manufacture. Every dimension necessary to define the product must be stated once and repeated in different views. Dimensions relating to one particular feature, such as the position and size of hole, where possible, appear on the same view.There should be no more dimensions than are absolutely necessary, and no feature should be located by more than one dimension in any direction. It may be necessary occasionally to give an auxiliary dimension for reference, possibly for inspection. When this is so, the dimension should be enclosed in a bracket and marked for reference. Such dimensions are not governed by general tolerances.Dimensions that affect the function of the part should always be specified and not left as the sum or other dimensions. If this is not done, the total permissible variation on that dimension will form the sum or difference of the other dimensions and their tolerance, and this with result in these tolerances having to be made unnecessarily tight. The overall dimension should always appear.All dimensions must be governed by the general tolerance on the drawing unless otherwise stated. Usually, such a tolerance will be governed by the magnitude of the dimension. Specific tolerances must always be stated on dimensions affecting or interchangeability.A system of tolerances is necessary to allow for the variations in accuracy that are bound to occur during manufacture, and still provide for interchangeability and correct function of the part.A tolerance is the difference in a dimension in order to allow for unavoidable imperfections in workmanship. The tolerance range will depend on the accuracy of the manufacturing organization, the machining process and the magnitude of the dimension. The greater the tolerance range is disposed on both sides of the nominal dimension. A unilateral tolerance is one where the tolerance zone is on one side only of the nominal dimension, in which case the nominal dimension may from one of the limits.Limits are the extreme dimensions of the tolerance zone. For example, nominal dimension30mm tolerance 30.0230.000++ limits 30.02530.000Fits depend on the relationship between the tolerance zones of two mating parts,and may be broadly classified into a clearance fit with positive allowance, a transition fit where the allowance may be either positive or negative (clearance or interference) , an interference fit where the allowance is always negative.Type of Limits and FitsThe ISO system of Limits and Fits, widely used in a number of leading metric countries, is considerably more complex than the ANSI system.In this system, each part has a basic size. Each limit of part, high and sign being obtained by subtracting the basic size form the limit in question. The difference between the two limits of size of a part is called the tolerance, an absolute without sign.There are three classes of fits: 1) clearance fits, 2) transition fits ( the assembly may have either clearance or interference ), and 3) interference fits .Either a shaft-basis system or a hole-basis system may be used. For any given basic size, a range of tolerance and deviations may be specified with respect to be line of zero deviation, called the zero line. The tolerance is a function of the basic size and is designated by a number symbol, called the grade-thus the tolerance grade. The position of the tolerance with respect to the zero line also a function of the basic size-is indicated by a letter symbol(or two letter), a capital letter for holes and a lowercase letter for shafts. Thus the specification for a hole and shaft having a basic size of 45mm might be45H8/g7.Twenty standard grades of tolerance are provided, called IT 01,IT 0 ,IT 1-18, providing numerical values for each nominal diameter, in arbitrary steps up to 500mm (for example 0-3,3-6,6-10…, 400-500mm). The value of the tolerance unit, I, for grades 5-16 is=+0.0.001i DWhere i is in microns and D in millimeters.Standard shaft and hole deviations similarly are provided by sets of formulas, However, for practical, both tolerances and deviations are provided in three sets of rather complex tables. Additional tables gives the values for basic sizes above 500mm and for “Commonly Used Shafts and Holes” in two categories ---“General Purpose” and “Fine Mecbanisms and Horology”.中文翻译极限与误差机械零件的破坏,一般总是从表层开始的。
机床行业中英文对照

机床行业中英文对照3-Jaws indexing spacers 三爪、分割工具头A.T.C.system 加工中心机刀库Aluminum continuous melting & holding furnaces 连续溶解保温炉Balancing equipment 平衡设备Bayonet 卡口Bearing fittings 轴承配件Bearing processing equipment 轴承加工机Bearings 轴承Belt drive 带传动Bending machines 弯曲机Blades 刀片Blades,saw 锯片Bolts,screws & nuts 螺栓,螺帽及螺丝Boring heads 搪孔头Boring machines 镗床Cable making tools 造线机Casting,aluminium 铸铝Casting,copper 铸铜Casting,gray iron 铸灰口铁Casting,malleable iron 可锻铸铁Casting,other 其他铸造Casting,steel 铸钢Chain drive 链传动Chain making tools 造链机Chamfer machines 倒角机Chucks 夹盘Clamping/holding systems 夹具/支持系统CNC bending presses 电脑数控弯折机CNC boring machines 电脑数控镗床CNC drilling machines 电脑数控钻床CNC EDM wire-cutting machines 电脑数控电火花线切削机CNC electric discharge machines 电脑数控电火花机CNC engraving machines 电脑数控雕刻机CNC grinding machines 电脑数控磨床CNC lathes 电脑数控车床CNC machine tool fittings 电脑数控机床配件CNC milling machines 电脑数控铣床CNC shearing machines 电脑数控剪切机CNC toolings CNC刀杆CNC wire-cutting machines 电脑数控线切削机Conveying chains 输送链Coolers 冷却机Coupling 联轴器Crimping tools 卷边工具Cutters 刀具Cutting-off machines 切断机Diamond cutters 钻石刀具Dicing saws 晶圆切割机Die casting dies 压铸冲模Die casting machines 压铸机Dies-progressive 连续冲模Disposable toolholder bits 舍弃式刀头Drawing machines 拔丝机Drilling machines 钻床Drilling machines bench 钻床工作台Drilling machines,high-speed 高速钻床Drilling machines,multi-spindle 多轴钻床Drilling machines,radial 摇臂钻床Drilling machines,vertical 立式钻床drills 钻头Electric discharge machines(EDM) 电火花机Electric power tools 电动刀具Engraving machines 雕刻机Engraving machines,laser 激光雕刻机Etching machines 蚀刻机Finishing machines 修整机Fixture 夹具Forging dies 锻模Forging,aluminium 锻铝Forging,cold 冷锻Forging,copper 铜锻Forging,other 其他锻造Forging,steel 钢锻Foundry equipment 铸造设备Gear cutting machines 齿轮切削机Gears 齿轮Gravity casting machines 重力铸造机Grinder bench 磨床工作台Grinders,thread 螺纹磨床Grinders,tools & cutters 工具磨床Grinders,ultrasonic 超声波打磨机Grinding machines 磨床Grinding machines,centerless 无心磨床Grinding machines,cylindrical 外圆磨床Grinding machines,universal 万能磨床Grinding tools 磨削工具Grinding wheels 磨轮Hand tools 手工具Hard/soft and free expansion sheet making plant 硬(软)板(片)材及自由发泡板机组Heat preserving furnaces 保温炉Heating treatment funaces 熔热处理炉Honing machines 搪磨机Hydraulic components 液压元件Hydraulic power tools 液压工具Hydraulic power units 液压动力元件Hydraulic rotary cylinders 液压回转缸Jigs 钻模Lapping machines 精研机Lapping machines,centerless 无心精研机Laser cutting 激光切割Laser cutting for SMT stensil 激光钢板切割机Lathe bench 车床工作台Lathes,automatic 自动车床Lathes,heavy-duty 重型车床Lathes,high-speed 高速车床Lathes,turret 六角车床Lathes,vertical 立式车床Lubricants 润滑液Lubrication Systems 润滑系统Lubricators 注油机Machining centers,general 通用加工中心Machining centers,horizontal 卧式加工中心Machining centers,horizontal & vertical 卧式及立式加工中心Machining centers,vertical 立式加工中心Machining centers,vertical double-column type 立式双柱加工中心Magnetic tools 磁性工具Manifolds 集合管Milling heads 铣头Milling machines 铣床Milling machines,bed type 床身式铣床Milling machines,duplicating 仿形铣床Milling machines,horizontal 卧式铣床Milling machines,turret vertical 六角立式铣床Milling machines,universal 万能铣床Milling machines,vertical 立式铣床Milling machines,vertical & horizontal 立式及卧式铣床Mold & die components 模具单元Mold changing systems 换模系统Mold core 模芯Mold heaters/chillers 模具加热器/冷却器Mold polishing/texturing 模具打磨/磨纹Mold repair 模具维修Molds 模具Nail making machines 造钉机Oil coolers 油冷却器Overflow cutting machines for aluminium wheels 铝轮冒口切断机P type PVC waterproof rolled sheet making plant P型PVC高分子防水PCB fine piecing systems 印刷电器板油压冲孔脱料系统Pipe & tube making machines 管筒制造机Planing machines 刨床Planing machines vertical 立式刨床Pneumatic hydraulic clamps 气油压虎钳Pneumatic power tools 气开工具Powder metallurgic forming machines 粉末冶金成型机Presses,cold forging 冷锻冲压机presses,crank 曲柄压力机Presses,eccentric 离心压力机Presses,forging 锻压机Presses,hydraulic 液压冲床Presses,knuckle joint 肘杆式压力机Presses,pneumatic 气动冲床Presses,servo 伺服冲床Presses,transfer 自动压力机Pressing dies 压模Punch formers 冲子研磨器Quick die change systems 速换模系统Quick mold change systems 快速换模系统Reverberatory furnaces 反射炉Rollers 滚筒Rolling machines 辗压机Rotary tables 转台Sawing machines 锯床Sawing machines,band 带锯床Saws,band 带锯Saws,hack 弓锯Saws,horizontal band 卧式带锯Saws,vertical band 立式带锯shafts 轴Shapers 牛头刨床Shearing machines 剪切机Sheet metal forming machines 金属板成型机Sheet metal working machines 金属板加工机Slotting machines 插床spindles 主轴Stamping parts 冲压机Straightening machines 矫直机Switches & buttons 开关及按钮Tapping machines 攻螺丝机Transmitted chains 传动链Tube bending machines 弯管机Vertical hydraulic broaching machine 立式油压拉床Vises 虎钳Vises,tool-maker 精密平口钳Wheel dressers 砂轮修整器Woven-Cutting machines 织麦激光切割机Wrenches 扳〔2〕:按中文拼音字母排序铝轮冒口切断机 Overflow cutting machines for aluminium wheels 离心压力机 Presses,eccentric六角立式铣床 Milling machines,turret vertical六角车床 Lathes,turret螺栓,螺帽及螺丝 Bolts,screws & nuts螺纹磨床 Grinders,thread冷却机 Coolers冷锻 Forging,cold冷锻冲压机 Presses,cold forging立式双柱加工中心 Machining centers,vertical double-column type 立式铣床 Milling machines,vertical立式油压拉床 Vertical hydraulic broaching machine立式刨床 Planing machines vertical立式车床 Lathes,vertical立式带锯 Saws,vertical band立式加工中心 Machining centers,vertical立式及卧式铣床 Milling machines,vertical & horizontal立式钻床 Drilling machines,vertical联轴器 Coupling连续溶解保温炉 Aluminum continuous melting & holding furnaces 连续冲模 Dies-progressive链传动 Chain drive切断机 Cutting-off machinesCNC刀杆 CNC toolings曲柄压力机 presses,crank修整机 Finishing machines舍弃式刀头 Disposable toolholder bits润滑系统 Lubrication Systems润滑液 Lubricants熔热处理炉 Heating treatment funaces三爪、分割工具头 3-Jaws indexing spacers伺服冲床 Presses,servo输送链 Conveying chains手工具 Hand tools砂轮修整器 Wheel dressers蚀刻机 Etching machines外圆磨床 Grinding machines,cylindrical搪磨机 Honing machines搪孔头 Boring heads卧式铣床 Milling machines,horizontal卧式带锯 Saws,horizontal band卧式加工中心 Machining centers,horizontal卧式及立式加工中心 Machining centers,horizontal & vertical万能铣床 Milling machines,universal万能磨床 Grinding machines,universal镗床 Boring machines弯曲机 Bending machines弯管机 Tube bending machines通用加工中心 Machining centers,general铜锻 Forging,copper铣头 Milling heads铣床 Milling machines无心磨床 Grinding machines,centerless无心精研机 Lapping machines,centerless压模 Pressing dies压铸冲模 Die casting dies压铸机 Die casting machines油冷却器 Oil coolers造链机 Chain making tools造线机 Cable making tools造钉机 Nail making machines印刷电器板油压冲孔脱料系统 PCB fine piecing systems摇臂钻床 Drilling machines,radial硬(软)板(片)材及自由发泡板机组 Hard/soft and free expansion sheet making plant 辗压机 Rolling machines液压元件 Hydraulic components液压冲床 Presses,hydraulic液压动力元件 Hydraulic power units液压工具 Hydraulic power tools液压回转缸 Hydraulic rotary cylindersP型PVC高分子防水 P type PVC waterproof rolled sheet making plant刨床 Planing machines牛头刨床 Shapers其他铸造 Casting,other其他锻造 Forging,other模芯 Mold core模具 Molds模具维修 Mold repair模具打磨/磨纹 Mold polishing/texturing 模具单元 Mold & die components模具加热器/冷却器 Mold heaters/chillers 磨轮 Grinding wheels磨削工具 Grinding tools磨床 Grinding machines磨床工作台 Grinder bench平衡设备 Balancing equipment气油压虎钳 Pneumatic hydraulic clamps 气动冲床 Presses,pneumatic气开工具 Pneumatic power tools轴 shafts轴承 Bearings轴承配件 Bearing fittings轴承加工机 Bearing processing equipment 肘杆式压力机 Presses,knuckle joint铸铝 Casting,aluminium铸铜 Casting,copper铸造设备 Foundry equipment铸钢 Casting,steel铸灰口铁 Casting,gray iron织麦激光切割机 Woven-Cutting machines 重力铸造机 Gravity casting machines重型车床 Lathes,heavy-duty主轴 spindles扳手 Wrenches拔丝机 Drawing machines保温炉 Heat preserving furnaces插床 Slotting machines齿轮 Gears齿轮切削机 Gear cutting machines冲压机 Stamping parts冲子研磨器 Punch formers超声波打磨机 Grinders,ultrasonic车床工作台 Lathe bench磁性工具 Magnetic tools传动链 Transmitted chains床身式铣床 Milling machines,bed type带传动 Belt drive带锯 Saws,band带锯床 Sawing machines,band电脑数控镗床 CNC boring machines电脑数控弯折机 CNC bending presses电脑数控铣床 CNC milling machines电脑数控线切削机 CNC wire-cutting machines电脑数控磨床 CNC grinding machines电脑数控车床 CNC lathes电脑数控电火花线切削机 CNC EDM wire-cutting machines 电脑数控电火花机 CNC electric discharge machines电脑数控雕刻机 CNC engraving machines电脑数控机床配件 CNC machine tool fittings电脑数控剪切机 CNC shearing machines电脑数控钻床 CNC drilling machines电动刀具 Electric power tools电火花机 Electric discharge machines(EDM)雕刻机 Engraving machines刀片 Blades刀具 Cutters倒角机 Chamfer machines多轴钻床 Drilling machines,multi-spindle锻铝 Forging,aluminium锻压机 Presses,forging锻模 Forging dies仿形铣床 Milling machines,duplicating粉末冶金成型机 Powder metallurgic forming machines 反射炉 Reverberatory furnaces钢锻 Forging,steel高速车床 Lathes,high-speed高速钻床 Drilling machines,high-speed管筒制造机 Pipe & tube making machines滚筒 Rollers工具磨床 Grinders,tools & cutters攻螺丝机 Tapping machines弓锯 Saws,hack虎钳 Vises换模系统 Mold changing systems夹盘 Chucks夹具 Fixture夹具/支持系统 Clamping/holding systems剪切机 Shearing machines加工中心机刀库 A.T.C.system激光切割 Laser cutting激光雕刻机 Engraving machines,laser激光钢板切割机 Laser cutting for SMT stensil集合管 Manifolds矫直机 Straightening machines金属板成型机 Sheet metal forming machines 金属板加工机 Sheet metal working machines 锯片 Blades,saw锯床 Sawing machines卷边工具 Crimping tools晶圆切割机 Dicing saws精密平口钳 Vises,tool-maker精研机 Lapping machines可锻铸铁 Casting,malleable iron快速换模系统 Quick mold change systems卡口 Bayonet开关及按钮 Switches & buttons钻石刀具 Diamond cutters钻头 drills钻模 Jigs钻床 Drilling machines钻床工作台 Drilling machines bench自动压力机 Presses,transfer自动车床 Lathes,automatic注油机 Lubricators转台 Rotary tables。
机械外文翻译中英文

附录附录1英文原文Rolling Contact BearingsThe concern of a machine designer with ball and roller bearings is fivefold as follows:(a) life in relation to load; (b) stiffness,i.e.deflections under load; (c) friction;(d) wear; (e) noise. For moderate loads and speeds the correct selection of a standard bearing on the basis of a load rating will become important where loads are high,although this is usually of less magnitude than that of the shafts or other components associated with the bearing. Where speeds are high special cooling arrangements become necessary which may increase fricitional drag. Wear is primarily associated with the introduction of contaminants,and sealing arrangements must be chosen with regard to the hostility of the environment.Because the high quality and low price of ball and roller bearing depends on quantity production,the task of the machine designer becomes one of selection rather than design. Rolling-contact bearings are generally made with steel which is through-hardened to about 900HV,although in many mechanisms special races are not provided and the interacting surfaces are hardened to about 600HV. It is not surprising that,owing to the high stresses involved,a predominant form of failure should be metal fatigue, and a good deal of work is based on accept values of life and it is general practice in bearing industry to define the load capacity of the bearing as that value below which 90 percent of a batch will exceed life of one million revolutions.Notwithstanding the fact that responsibility for basic design of ball and roller bearings rests with he bearing manufacturer, the machine designer must form a correct appreciation of the duty to be performed by the bearing and be concerned not only with bearing selection but with the conditions for correct installation.The fit of the bearing races onto the shaft or onto the housings is of critical importance because of their combined effect on the internal clearance of the bearing as well as preserving the desired degree of interference fit. Inadequate interference can induce serious trouble from fretting corrosion. The inner race is frequently located axially by against a shoulder. A radius at this point is essential for the avoidance ofstress concentration and ball races are provided with a radius or chamfer to follow space for this.Where life is not the determining factor in design, it is usual to determine maximum loading by the amount to which a bearing will deflect under load. Thus the concept of "static load-carrying capacity" is understood to mean the load that can be applied to a bearing, which is either stationary or subject to slight swiveling motions, without impairing its running qualities for subsequent rotational motion. This has been determined by practical experience as the load which when applied to a bearing results in a total deformation of 0.0025mm for a ball 25mm in diameter.The successful functioning of many bearings depends upon providing them with adequate protection against their environment, and in some circumstances the environment must be protected from lubricants or products of deterioration of the bearing design. Moreover, seals which are applied to moving parts for any purpose are of interest to tribologists because they are components of bearing systems and can only be designed satisfactorily on basis of the appropriate bearing theory.Notwithstanding their importance, the amount of research effort that has been devoted to the understanding of the behavior of seals has been small when compared with that devoted to other aspects of bearing technology.LathesLathes are widely used in industry to produce all kinds of machined parts. Some are general purpose machines, and others are used to perform highly specialized operations.Engine lathesEngine lathes, of course, are general-purpose machine used in production and maintenance shop all over the the world. Sized ranger from small bench models to huge heavy duty pieces of equipment. Many of the larger lathes come equipped with attachments not commonly found in the ordinary shop, such as automatic shop for the carriage.Tracer or Duplicating LathesThe tracer or duplicating lathe is designed o produce irregularly shaped parts automatically. The basic operation of this lathe is as fallows. A template of either a flat or three-dimensional shape is placed in a holder. A guide or pointer then moves along this shape and its movement controls that of the cutting tool. The duplication may include a square or tapered shoulder, grooves, tapers, and contours. Work such asmotor shafts, spindles, pistons, rods, car axles, turbine shafts, and a variety of other objects can be turned using this type of lathe.Turret LathesWhen machining a complex workpiece on a general-purpose lathe, a great deal of time is spent changing and adjusting the several tools that are needed to complete the work. One of the first adaptations of the engine lathe which made it suitable to mass production was the addition of multi-tool in place of the tailstock. Although most turrets have six stations, some have as many as eight.High-production turret lathes are very complicated machines with a wide variety of power accessories. The principal feature of all turret lathes, however, is that the tools can perform a consecutive serials of operations in proper sequence. Once the tools have been set and adjusted, little skill is require to run out duplicate parts.Automatic Screw MachineScrew machines are similar in construction to turret lathes, except that their heads are designed to hold and feed long bars of stock. Otherwise, their is little different between them. Both are designed for multiple tooling, and both have adaptations for identical work. Originally, the turret lathe was designed as a chucking lathe for machining small casting, forgings, and irregularly shaped workpieces.The first screw machines were designed to feed bar stock and wire used in making small screw parts. Today, however, the turret lathe is frequently used with a collect attachment, and the automatic screw machine can be equipped with a chuck to hold castings.The single-spindle automatic screw machine, as its name implies, machines work on only one bar of stock at a time. A bar 16 to 20 feet long is feed through the headstock spindle and is held firmly by a collect. The machining operations are done by cutting tools mounted on the cross slide. When the machine is in operation, the spindle and the stock are rotated at selected speeds for different operations. If required, rapid reversal of spindle direction is also possible.In the single-spindle automatic screw machine, a specific length of stock is automatically fed through the spindle to a machining area. At this point, the turret and cross slide move into position and automatically perform whatever operations are required. After the machined piece is cut off, stock is again fed into the machining area and the entire cycle is repeated.Multiple-spindle automatic screw machines have from four to eight spindleslocated around a spindle carrier. Long bars of stock, supported at the rear of the machine,pass though these hollow spindles and are gripped by collects. With the single spindle machines, the turret indexes around the spindle. When one tool on the turret is working, the others are not. With a multiple spindle machine, however, the spindle itself index. Thus the bars of stock are carried to the various end working and side working tools. Each tool operates in only one position, but tolls operate simultaneously. Therefore, four to eight workpieces can be machined at the same time.Vertical Turret LathesA vertical turret is basically a turret lathe that has been stood on its headstock end. It is designed to perform a variety of turning operations. It consists of a turret, a revolving table, and a side head with a square turret for holding additional tools. Operations performed by any of the tools mounted on the turret or side head can be controlled through the use of stops.Machining CentersMany of today's more sophisticated lathes are called machining centers since they are capable of performing, in addition to the normal turning operations, certain milling and drilling operations. Basically, a machining center can be thought of as being a combination turret lathe and milling machine. Additional features are sometimes included by the versatility of their machines.Numerical ControlOne of the most fundamental concepts in the area of advanced manufacturing technologies is numerical control(NC). Prior to the advent of NC, all machine tools were manually operated and controlled. Among the many limitations associated with manual control machine tools, perhaps none is more prominent than limitation of operator skills. With manual control, the quality of the product is directly related to and limited to the skills of the operator. Numerical control represents the first major step away from human control of machine tools.Numerical control means the control of machine tools and other manufacturing systems through the use of prerecorded, written symbolic instructions. Rather than operating a machine tool, an NC technician tool to be numerically controlled, it must be interfaced with a device for accepting and decoding the programmed instructions, known as a reader.Numerical control was developed to overcome the limitation of humanoperators, and it has done so. Numerical control machines are more accurate than manually operated machines, they can produce parts more uniformly, they are faster, and the long-run tooling costs are lower. The development of NC led to the development of several other innovations in manufacturing technology:1.Electrical discharge machining.ser cutting.3. Electron beam welding.Numerical control has also made machines tools more versatile than their manually operated predecessors. An NC machine tool can automatically produce a wide variety of parts, each involving an assortment of widely varied and complex machining processes. Numerical control has allowed manufacturers to undertake the production of products that would not have been feasible from an economic perspective using manually controlled machine tools and processes.Like so many advanced technologies, NC was born in the laboratories of the Masschusetts Institute of Technology. The concept of NC was developed in early 1950s with funding provided by the U.S.Air force. In its earliest stages, NC machines were able to make straight cuts efficiently and effectively.However,curved paths were a problem because the machine tool had to be programmed to undertake a series of horizontal and vertical steps to produce a curve. The shorter is straight lines making up the steps, the smoother is the curve. Each line segment in the steps had to be calculated.This problem led to the development in 1959 of the Automatically Programmed Tools(APT) language. This is a special programming language for NC that uses statements similar to English language to define the part geometry, describe the cutting tool configuration, and specify the necessary motions. The development of the APT language was a major step forward in the further development of NC technology. The original NC systems were vastly different from those used today. The machines had hardwired logic circuits. This instructional programs were written on punched paper, which was later to be replaced by magnetic plastic tape. A tape reader was used to interpret the instructions written on the tape for the machine. Together, all of this represented a giant step forward in the control of machine tools. However, there were a number of problems with NC at this point in its development.A major problem wad the fragility of the punched paper tape medium. Itwas common for the paper tape containing the programmed instructions to break or tear during a machining process. This problem was exacerbated by the fact that each programmed instructions had to be return through the reader. If it was necessary to produce 100 copies of a given part,it was also necessary to run the paper tape through the reader 100 separate times. Fragile paper tapes simply could not withstand the rigors of a shop floor environment and this kind of repeated use.This led to the development of a special magnetic plastic tape. Whereas the paper tape carried the programmed instructions as a series of holes punched in the tape, the plastic tape carried the instructions as a series of magnetic dots. The plastic tape was much stronger than the paper taps, which solved the problem of frequent tearing and breakage. However, it still left two other problems.The most important of these was that it was difficult or impossible to change the instructions entered on the tape. To make even the most minor adjustments in a program of instructions, it necessary to interrupt machining operations and make a new tape. It was also still necessary to run the tape through the reader as many times as there were parts to be produced. Fortunately, computer technology became a reality and soon solved the problem of NC associated with punched paper and plastic tape.The development of a concept known as direct numerical control(DNC)solved the paper and plastic tape problems associated with numerical control by simply eliminating tape as the medium for carrying the programmed instructions. In direct numerical control machine tools are tied, via a data transmission link, to a host computer. Programs for operating the machine tools are stored in the host computer and fed to the machine tool as needed via the data transmission linkage. Direct numerical control represented a major step forward over punched tape and plastic tape. However, it is subject to the same limitations as all technologies that depend o a host computer. When the lost computer goes down, the machine tools also experience downtime. This problem led to the development of computer numerical control.The development of the microprocessor allowed for the development of programmable logic controllers(PNC)and microcomputer. These two technologies allowed for the development of computer numerical control(CNC). With CNC, each machine tool has a PLC or a microcomputer that serves the same purpose. This allows programs to be input and stored at each individual machine tool. It also allows programs to be developed off-line and download at the individual machine tool. CNC solved the problems associated with downtime of the host computer, but it introducedanother known as data management. The same program might be loaded on ten different being solved by local area networks that connect microcomputer for better data management.CNC machine tool feed motion systemsCNC machine tool feed motion systems, especially to the outline of the control of movement into the system, must be addressed to the movement into the position and velocity at the same time the realization of two aspects of automatic control, as compared with the general machine tools, require more feed system high positioning accuracy and good dynamic response. A typical closed-loop control of CNC machine tool feed system, usually by comparing the location of amplification unit, drive unit, mechanical transmission components, such as feedback and testing of several parts. Here as mechanical gear-driven source refers to the movement of the rotary table into a linear motion of the entire mechanical transmission chain, including the deceleration device, turning the lead screw nut become mobile and vice-oriented components and so on. To ensure that the CNC machine tool feed drive system, precision, sensitivity and stability, the design of the mechanical parts of the general requirement is to eliminate the gap, reducing friction, reducing the movement of inertia to improve the transmission accuracy and stiffness. In addition, the feeding system load changes in the larger, demanding response characteristics, so for the stiffness, inertia matching the requirements are very high.Linear Roller GuidesIn order to meet these requirements, the use of CNC machine tools in general low-friction transmission vice, such as anti-friction sliding rail, rail rolling and hydrostatic guideways, ball screws, etc.; transmission components to ensure accuracy, the use of pre-rational, the form of a reasonable support to enhance the stiffness of transmission; deceleration than the best choice to improve the resolution of machine tools and systems converted to the driveshaft on the reduction of inertia; as far as possible the elimination of drive space and reduce dead-zone inverse error and improve displacement precision.Linear Roller Guides outstanding advantage is seamless, and can imposepre-compression. By the rail body, the slider, ball, cage, end caps and so on. Also known as linear rolling guide unit. Use a fixed guide body without moving parts, the slider fixed on the moving parts. When the slider moves along the rail body, ball and slider in the guide of the arc between the straight and through the rolling bed cover ofRolling Road, from the work load to non-work load, and then rolling back work load, constant circulation, so as to guide and move the slider between the rolling into a ball.Bridge CraneBridge crane is having an elevated track running in a bridge-type crane, also known as the crane. Bridge Crane in the laying of the bridge on both sides along the elevated track on the vertical run, lifting trolley along the bridge laying on the track in the horizontal operation, a scope of work of a rectangle, it can take full advantage of having the space below lifting materials from the ground equipment hindered.Bridge Crane widely used in indoor warehouses, factories, wharves and open storage yard and other places. Able to carry items, stood up, lifting status, and adjust operations, mainly for the workshop, sections and steel production lines yard, etc.. Lifting capacity usually in the 10 to 100 t. Bridge crane itself for horizontal movement, the winch frame for the vertical movement of the winch suspended from the hook for vertical movement, the direction of movement of three of the crane can work. In order to prevent bridge crane driver not clear in the specific hook campaign, on the ground are equipped with lifting the general command or folder, put hook. If hanging overhead crane hoisted electromagnetic lifting plate, often operated by the drivers themselves. Bridge cranes can be divided into general overhead crane, simple girder bridge crane for bridge crane and metallurgical three.Ordinary general overhead crane from lifting trolley, having run institutions, having composed of a metal structure. Lifting up from the car and from institutions, agencies and the car running small frame consists of three parts.Lifting bodies, including the motor, brakes, reducer, and the pulley drum group. Motor through the reducer, driven rotating drum so that the wire rope around 42.50 or 42.50 down to lifting weights. Small frame is from the brackets and install or run agencies and institutions, such as car parts rack, usually welded structure.Crane running the driving mode can be divided into two categories: one category is the concentrated drive, which uses a motor-driven initiatives on both sides of the drive shaft driven wheel; were driven to another, that is, on both sides of the initiative the wheels with a motor drive. Small, medium and larger overhead crane with brake, and motor reducer combination into one of the "triple play" drive, the weight of the ordinary from the overhead crane for easy installation and adjustment, often drive the use of universal - axis.Crane normally used only four active and driven wheels, if a great weight,increase common approach to reduce wheel round pressure. When more than four wheels, must adopt a balanced hinged frame device so that the crane load evenly distributed in the wheels.Bridge metal structure from the main sorghum and sorghum-composed of the main beam is divided into single-and double-girder bridge having two categories. Single-beam bridge from the main beam and a single on both sides of the span at the end of sorghum, dual-beam bridge by the two main sorghum and sorghum-component.Liang Liang Gang and the end of the link-beam ends with wheels, for supporting an elevated bridge in the running. A main beam welding on track for the lifting trolley running. Having the structure of the main beam type is more a typical box structure, the four truss structure and fasting truss structure.Box structure can be divided into two-track box girder, partial double-track box-beam, single-bias-rail box and several main sorghum. Dual-track box girder is the extensive use of a basic form, the main beam from the upper and lower flange on both sides of the plate and vertical web composition, layout rail car in the center of the flange plates online, and its simple structure , manufacturing convenient, suitable for mass production, but larger forces.Partial tracks box-girder and partial double-track box-section of the main beam are from the upper and lower ranges flange plates and thick web of the main components, rail car in the main web layout above, the short Xiangbenna omit the stiffening plate, which tracks box-side main beam from a wide flange box instead of the main sorghum two main sorghum, respect smaller, but more complex manufacturing.4 truss-type structure from four plane truss structure into a closed space, in the general level of the surface Truss shops follow plate, light weight, rigidity, but compared with other structures, and its dimensions, creating more complex, fatigue lower intensity, has been less productive.Partial fasting truss structure similar to the main tracks box-girder from the four components of a closed steel structure, in addition to the main web for the Solid shaped beam, the other three plate in accordance with the design requirements cut into many windows, forming a no-ramps Fasting Truss, in the lower level of the surface occupied by taking truss plate, cranes and the operation of electrical equipment installed in the bridge house, lighter forces, the overall stiffness, and that in China is amore widely used type.General overhead crane used mainly driven power, the general is in the driver indoor manipulation, but also remote control. From the weight of up to 500 tons, up to 60 m span.Simple beam bridge crane known as sorghum cranes, and the structure and composition of ordinary bridge crane similar to a weight, span and speed are smaller. Bridge is the main sorghum or other steel I-beam and plate steel girder section composed of simple, hand-pull or electric hoist accompanied by gourd simple as lifting trolley car, the car usually in the word sorghum run on the next flange . Bridge can be elevated along the orbit, but also along the elevated suspension in the following orbit, such as a crane hoisted sorghum crane.Metallurgical dedicated bridge crane in the steel production process can be involved in a specific process operation, and its basic structure and general overhead crane similar, but in small vehicles are equipped with lifting the work of special agencies or devices. This feature is the work of a crane used frequently, poor, working-level higher. Dual-beam bridge crane factories on the track along the vertical direction of movement, the lateral movement and trolley movements campaign to hook work. Applied to machining and assembly shop, a metal structure workshop, mechanical workshops, metallurgy and casting workshop and warehouse type lifting work. With scores from the weight of the form, molecular weight mainly Gouqi, the denominator as vice Gouqi weight. There are five main types.Casting Crane: for the lifting of hot metal into Mixer, furnaces and molten steel into lifting equipment or continuous ingot steel ingot mould used. Sheng barrels lifting the car, a flip-sheng, deputy trolley barrels, and other auxiliary work.Tongs crane: Using tongs high temperature steel ingot will be vertically being lifted onto a deep soaking pits, or put it out the car shipped spindles.Stripper Crane: an ingot from the mandatory extrusion ingot mold. There are special small car Stripper devices, spindles Stripper under way and the shape of the model: Some Stripper crane-is attributable to suppress billets, ingots filed with the clamp module; Some of the clamp punctured ingot mould, with Ingot filed small pair of pliers.Feeding Crane: Charge will be added to the open hearth furnace. Trolley bottom of the column with the pick-and inciting material to me and it into the furnace. The main column to bypass the vertical axis rotation, pick-and rotary can swing from topto bottom. Deputy car repair furnace for such auxiliary operations.Forging Crane: to meet with hydraulic forging large workpieces. Trolley displayed on the main hook up special feeder to support and flip the workpiece; Vice car used to lift the workpiece.Dual-beam bridge crane, the biggest weight from 100 tons, the hook-and-grab, electromagnetic, metallurgical cranes, quenching crane, manual double girder bridge crane, electric hoist double girder overhead crane with the crane unit JB / T14405 "generic bridge crane" standard, the quality of products to JB/T53442 "universal overhead crane product quality grade" first-class requirements. Its structural features of starting up and running with the car running on the bridge, a metal structure for the double-girder box form. From the characteristics of the device in accordance with the classification for the hook, grab, electromagnetic and multipurpose bridge crane, mainly for the mines, factories, wharves and warehouses, and other material handling operations frequent stops, as a crane quenching equipment, a high-speed heat treatment process of decline . Metallurgical casting molten steel crane to transport packet is indispensable than smelting industrial equipment. The use of modern means of science and technology, will enable any crane structure with a jump-speed performance. Can be used with high-level rotating hook for stacking operations.Single-girder bridge crane, the largest weight of 10 tons from, hook-and-grab, electromagnetic, flying single-girder bridge crane, manual single-girder bridge crane with the crane unit JB/T1306 "electric single-girder bridge Crane "and JB/T2603" electric single-girder overhead crane hoisted the "standard requirements. Its structure is characterized manual or electric hoist monorail car along the main beam under the flange I-beam operation, material handling operations, normally used for workshops, warehouses and other material handling operations, which manual does not allow for single-girder crane No electricity or power occasions. Grab motor with the monorail or bulk materials can also be used to grab operations, the unit crane compact structure, operational flexibility, can be used to ground, can also be used to operate the cab. Special circumstances can also be used for remote operation. Industrial production or storage is indispensable equipment.Crane normal working hours to allow a lifting of the greatest quality as rated starting weight. Rated crane hook from the hook and the weight does not include the fixed pulley group themselves. Grab sucker and electromagnetic devices, such as the quality of admission included in the ratings from the weight. In accordance with thestandard provisions of the bridge crane from the weight of a series of priority number system is R10, from 3.2 t, beginning with the increment of 1.25 Gongpi 4,5,6.3,8,10,12.5,16,20,25,32, 40,50 t……. But domestic products only under the bridge crane years of production practices, from the above series of elected part of the actual composition of a series of weight. Is the most commonly used Series 5 t, 10t, 16t, 20t, 32t and 50 t. Normally, when a weight of more than 10 t, or from the establishment of two bodies, namely the lifting of lifting bodies and institutions, both from the weight of a ratio of about 1:4. Main body from the weight or, for lifting heavy cargo lifting of the weight from the small, but faster, lighter for the lifting of the goods or for supporting efforts to enhance work efficiency.Generally experienced the largest crane lifting weights to determine the starting weight,taking into account the conditions of work reproduced or process requirements. Crane does not allow the use of overloading, in the lifting of the frequent changes of the occasion, crane should consider certain margin. In some cases, the occasional object to the lifting of overweight available when two cranes coordinated operations. In the process fixed, the lifting of the weight will remain basically unchanged, the use of cranes loaded with the basic circumstances, can be lifted up from vice, to simplify the structure of a crane and lower costs. Foreign large-tonnage it is not all bridge crane with a lifting body vice, but necessary option.The use of overhead crane safety matters:(1) Each crane must be obvious from the weight rated local hang the signs.(2) Work, it was not allowed on the bridge or hook couriers.(3) No Operator's Certificate and is not allowed to drink driving cranes.(4) Operating must focus on the spirit, not talk, smoking or do not do.(5) To clean the car; while Luanfang equipment, tools, flammable materials, explosive materials and dangerous goods.(6) The cranes could be allowed to use super.(7) The following situations while lifting: bundling is not solid; mechanical overload; signal unknown; Cable; buried in the ground or frozen items; suspended on some items; no security protection measures for the flammable and explosive - and dangerous goods; drive liquid items do not meet the safe use of wire rope; fault movements institutions.(8) The cranes in the absence of obstructions on the lines running, as well as hanging hook or spreader of the base must be more than 2 m from the ground. If the。
机床——机械类外文文献翻译、中英文翻译

毕业设计(论文)外文资料翻译系部:专业:姓名:学号:外文出处:English For Electromechanical(用外文写)Engineering附件:1.外文资料翻译译文;2.外文原文。
附件1:外文资料翻译译文机床机床是用于切削金属的机器。
工业上使用的机床要数车床、钻床和铣床最为重要。
其它类型的金属切削机床在金属切削加工方面不及这三种机床应用广泛。
车床通常被称为所有类型机床的始祖。
为了进行车削,当工件旋转经过刀具时,车床用一把单刃刀具切除金属。
用车削可以加工各种圆柱型的工件,如:轴、齿轮坯、皮带轮和丝杠轴。
镗削加工可以用来扩大和精加工定位精度很高的孔。
钻削是由旋转的钻头完成的。
大多数金属的钻削由麻花钻来完成。
用来进行钻削加工的机床称为钻床。
铰孔和攻螺纹也归类为钻削过程。
铰孔是从已经钻好的孔上再切除少量的金属。
攻螺纹是在内孔上加工出螺纹,以使螺钉或螺栓旋进孔内。
铣削由旋转的、多切削刃的铣刀来完成。
铣刀有多种类型和尺寸。
有些铣刀只有两个切削刃,而有些则有多达三十或更多的切削刃。
铣刀根据使用的刀具不同能加工平面、斜面、沟槽、齿轮轮齿和其它外形轮廓。
牛头刨床和龙门刨床用单刃刀具来加工平面。
用牛头刨床进行加工时,刀具在机床上往复运动,而工件朝向刀具自动进给。
在用龙门刨床进行加工时,工件安装在工作台上,工作台往复经过刀具而切除金属。
工作台每完成一个行程刀具自动向工件进给一个小的进给量。
磨削利用磨粒来完成切削工作。
根据加工要求,磨削可分为精密磨削和非精密磨削。
精密磨削用于公差小和非常光洁的表面,非精密磨削用于在精度要求不高的地方切除多余的金属。
车床车床是用来从圆形工件表面切除金属的机床,工件安装在车床的两个顶尖之间,并绕顶尖轴线旋转。
车削工件时,车刀沿着工件的旋转轴线平行移动或与工件的旋转轴线成一斜角移动,将工件表面的金属切除。
车刀的这种位移称为进给。
车刀装夹在刀架上,刀架则固定在溜板上。
溜板是使刀具沿所需方向进行进给的机构。
机械外文翻译中英文

附录英文原文N/C Machine Tool ElementN/C machine tool elements consist of dimensioning systems, controlsystems,servomechanisms and open-orclosed-loop systems. It is important to understand each elementprior to actual programming of a numerically controlled port.The term measuring system in N/C refers to the method a machine tool uses to move a partfrom a reference point to a target point. A target point may be a certain locating for drilling a hole,milling a slot, or other machine operation. The two measuring systems used on N/C machines arethe absolute and incremental. The absolute measuring system uses a fixed reference point. It ison this point that all positional information is based. In other words, all the locations to which apart will be moved must be given dimensions relating to that original fixed reference point.Figure shows an absolute measuring system with X and Y dimensions, each based on the origin.The incremental measuring system has a floating coordinating system. With the incrementalsystem, the time the part is moved. Figure 16.2 show X and Y values using an incrementalmeasuring system. Notice that with this system, each new location bases its values in X and Yfrom the preceding location. One disadvantage to this system is that any errors made will berepeated throughout the entire program, if not detected and corrected.There are two types of control systems commonly used on N/C equipment: point-to-point andcontinuous path. A point-to-point controlled N/C machine tool, sometimes referred to as apositioning control type, has the capability of moving only along a straight line. However, whentwo axes are programmed simultaneously with equal values a 45 angle will be generated.Point-to-point systems are generally found on drilling and simple milling machine where holelocation and straight milling jobs are performed. Point-to-point systems can be utilized togenetate arcs and angles by programming the machine to move in a series of small steps. Usingthis technique, however, the actual path machined is slightly different from the cutting pathspecified.Machine tools that have the capability of moving simultaneously in two or more axes areclassified as continuous-path or contouring. These machines are used for machining arcs, radii,circles, and angles of any size in two or there dimensions. Continuous-path machines aremoreexpensive than point-to-point systems and generally require a computer to aid programming when machining complex contours.N/C servomechanisms are devices used for producing accurate movement of a table or slid along an axis. Two types of servos are commonly used on N/C equipment: electric stepping motors and hydraulic motors. Stepping motor servos are frequently used on less expensive N/C equipment. These motors are generally high-torque power servos and mounted directly to a lead screw of a table or tool slide. Most stepping motors are actuated by magnetic pulses from the stator and rotor assemblies. The net result of this action is that one rotation of the motor shaft produces 200 steps. Connection the motor shaft to a 10-pitch lead screw allows 0.0005-in. movements to be made. Hydraulic servos produce a fluid pressure that flows through gears or pistons to effect shaft rotation. Mechanical motion of lead screws and slides is accomplished through various values and controls from these hydraulic motors. However, they are more expensive and noisy. Most larger N/C machines use hydraulic servos.N/C machines that use an open-loop system contain no-feedback signal to ensure that a machine axis has traveled the required distance. That is, if the input received was to move a particular table axis 1.000 in, the servo unit generally moves the table 1.000 in. There is no means for comparing the actual table movement with the input signal, howeve r, The only assurance that the table has actually moved 1.000 in. is the reliability of the servo system used.Open-loop systems are, of course, less expensive than closed-loop systems. A closed-loop system compares the actual output with the input signal and compensates for any errors. A feedback unit actually compares the amount the table has been moved with the input signal. Some feedback units used on closed-loop systems are transducers, electrical or magnetic scales, and synchros. Closed-loop systems greatly increase the reliability of N/C machines. Machining Centers Many of today’s more sophisticated lathes are called machining centers since they are capable of performing, in addition to the normal turning operations, certain milling and drilling operations. Basically, a machining center can be thought of as being a combination turret lathe and milling machine. Additional features are sometimes included by manufacturers to increase the versatility of their machines.Numerical ControlOne of the most fundamental concepts in the area of advanced manufacturing technologies is numerical control (NC). Prior to the advent of NC, all machine tools were manually operated and controlled .Among the many limitations associated with manual control machine tools, perhaps none is more prominent than the limitation of operator skills. With manual control, the quality of the product is directly related to and limited to the skills of the operator. Numerical control represents the first major step away from human control of machine tools.Numerical control means the control of machine tools and other manufacturing systems through the use of prerecorded, written symbolic instructions. Rather than operating a machine tool, an NC technician writes a program that issues operational instructions to the machine tool. For a machine tool to be numerically controlled, it must be interfaced with a device for accepting and decoding the programmed instructions, known as a reader.Numerical control was developed to overcome the limitation of human operators, and it has done so. Numerical control machines are more accurate than manually operated machines, they can produce parts more uniformly, they are faster, and the long-run tooling costs are lower. The development of NC led to the development of several other innovations in manufacturing technology:1. Electrical discharge machining.2. Laser cutting.3. Electron beam welding.Numerical control has also made machine tools more versatile than their manually operated predecessors. An NC machine tool can automatically produce a wide variety of parts, each involving an assortment of widely varied and complex machining processes. Numerical control has allowed manufacturers to undertake the production of products that would not have been feasible from an economic perspective using manually controlled machine tools and processes. Like so many advanced technologies, NC was born in the laboratories of the Massachusetts Institute of Technology. The concept of NC was developed in the early 1950s with funding provided by the U. S. Air force. In its earliest stages, NC machines were able to make straight cuts efficiently and effectively.However, curved paths were a problem because the machine tool had to be programmed to undertake a series of horizontal and vertical steps to produce a curve. The shorter is the straight lines making up the steps, the smoother is the curve. Each line segment in the steps had to be calculated.This problem led to the development in 1959 of the Automatically Programmed Too ls (APT) language. This is a special programming language for NC that uses statements similar to English language to define the part geometry, describe the cutting tool configuration, and specify the necessary motions. The development of the APT language was a major step forward in the further development of NC technology. The original NC systems were vastly different from those used today. The machines had hardwired logic circuits. The instructional programs were written on punched paper, which was later to be replaced by magnetic plastic tape. A tape reader was used to interpret the instructions written on the tape for the machine. Together, all of this represented a giant step forward in the control of machine tools. However, there were a numberof problems with NC at this point in its development.A major problem was the fragility of the punched paper tape medium. It was common for the paper tape containing the programmed instructions to break or tear during a machining process. This problem was exacerbated by the fact that each successive time a part was produced on a machine tool, the paper tape carrying the programmed instructions had to be rerun through the reader. If it was necessary to produce 100 copies of a given part, it was also necessary to run the paper tape through the reader 100 separate times. Fragile paper tapes simply could not withstand the rigors of a shop floor environment and this kind of repeated use.This led to the development of a special magnetic plastic tape. Whereas the paper tape carried the programmed instructions as a series of holes punched in the tape, the plastic tape carried the instructions as a series of holes punched in the tape, the plastic tape carried the instructions as a series of magnetic dots. The plastic tape was much stronger than the paper taps, which solved the problem of frequent tearing and breakage. However, it still left two other problems.The most important of these was that it was difficult or impossible to change the instructions entered on the tape. To make even the most minor adjustments in a program of instructions, it was necessary to interrupt machining operations and make a new tape .It was also still necessary to run the tape through the reader as many times as there were parts to be produced. Fortunately, computer technology became a reality and soon solved the problems of NC associated with punched paper and plastic tape.The development of a concept known as direct numerical control (DNC) solved the paper and plastic tape problems associated with numerical control by simply eliminating tape as the medium for carrying the programmed instructions. In direct numerical control .machine tools are tied, via a data transmission link, to a host computer. Programs for operating the machine tools are stored in the host computer and fed to the machine tool as needed via the data transmission linkage. Direct numerical control represented a major step forward over punched tape and plastic tape. However, it is subject to the same limitations as all technologies that depend on a host computer. When the lost computer goes down, the machine tools also experience downtime. This problem led to the development of computer numerical control.The development of the microprocessor allowed for the development of programmable logic controllers (PLCs) and microcomputers. These two technologies allowed for the development of computer numerical control (CNC).With CNC, each machine tool has a PLC or a microcomputer that serves the same purpose. This allows programs to be input and stored at each individual machine tool. It also allows programs to be developed off-line and downloaded at the individual machine tool. CNC solved the problems associated with downtime of the hostcomputer, but it introduced another known as data management. The same program might be loaded on ten different microcomputers with no communication among them. This problem is in the process of being solved by local area networks that connect microcomputers for better data management. Cutting Tool GeometryShape of cutting tools, particularly the angles, and tool material are very important factors. Angles determine greatly not only tool life but finish quality as well. General principles upon which cutting tool angles are based do not depend on the particular tool, Basically, the same considerations hold true whether a lathe tool, a milling cutter, a drill, or even a grinding wheel are being designed. Since, however the lathe tool, depicted in Fig. 18.1, might be easiest to visualize, its geometry is discussed.Tool features have been identified by many names. The technical literature is full of confusing terminology. Thus in the attempt to cleat up existing disorganized conceptions and nomenclature, this American Society of Mechanical Engineers published AS A Standard B5-22-1950. What follows is based on it.A single-point tool is a cutting tool having one face and one continuous cutting edge, Tool angles identified in Fig. 18.2 are as follows:Tool angle 1, on front view, is the back-rank angle. It is the angle between the tool face and a line parallel to the tool base of the shank in a longitudinal plane perpendicular to the tool base. When this angle is downward from front to rear of the cutting edge, the rake is positive; when upward from front to black, the rake is negative. This angle is most significant in the machining process, because it directly affects the cutting force, finish, and tool life.The side-rake angle, numbered 2, measures the slope of the face on a cross plane perpendicular to the tool base. It, also, is an important angle, because it directs chip flow to the side of the tool post and permits the tool to feed more easily into the work.The end-relief angle is measured between a line perpendicular to the base and the end flank immediately below the end cutting edge; it is numbered 3 in the figure. It provides clearance between work and tool so that its cut surface can flow by with minimum rubbing against the tool. To save time, a portion of the end flank of the tool may sometimes be lest unground, having been previously forged to size. In such case, this end-clearance angle, numbered 4, measured to the end flank surface below the ground portion, would be larger than the relief angle.Often the end cutting edge is oblique to the flank. The relief angle is then best measured in a plane normal to the end cutting edge angle. Relief is also expressed as viewed from side and end of the tool.The side-relief angle, indicated as 5, is measured between the side flank, just below thecutting edge, and a line through the cutting edge perpendicular to the base of the tool. This clearance permits the tool to advance more smoothly into the work.Angle 6 is the end-cutting-edge angle measured between the end cutting edge and a line perpendicular to the side of the tool shank. This angle prevents rubbing of the cut surface and permits longer tool file.The side-cutting-edge angle, numbered 7, is the angle between the side cutting edge and the side of the tool shank. The true length of cut is along this edge. Thus the angel determines the distribution of the cutting forces. The greater the angle, the longer the tool life; but the possibility of charter increases. A compromise must, as usual, be reached.The nose angle, number 8, is the angle between the two component cutting edges. If the corner is rounded off, the arc size is defined by the nose radius 9. The radius size influences finish and chatter.Sand CastingThe first stage in the production of sand castings must be the design and manufacture of a suitable pattern. Casting patterns are generally made from hard word and the pattern has to be made larger than the finished casting size to allow for the shrinkage that takes place during solidification and cooling. The extent of this shrinkage varies with the type of metal or alloy to be cast. For all but the simplest shapes the pattern will be made in two or more pieces to facilitate moulding. If a hollow casting is to be made the pattern design will include extension pieces so that spaces to accept the sand core are moulded into sand. These additional spaces in the mould are termed core prints.Sand moulds for the production of small and medium-sized castings are made in a moulding box. The mould is made in two or more parts in order that the pattern may be removed.The drag half of the mould box is placed on a flat firm board and the drag half of the pattern placed in position. Facing sand is sprinkled over the pattern and then the mould box is filled with moulding sand. The sand is rammed firmly around the pattern. This process of filling and ramming may be done by hand but mould production is automated in a large foundry with the mould boxes moving along a conveyor, firstly to be filled with sand from hoppers and then to pass under mechanical hammers for ramming. When ramming of the sand is complete, excess sand is removed to leave a smooth surface flush with the edges of the moulding box.The completed drag is now turned over and the upper, or cope, portion of the moulding box positioned over it. The cope half of the pattern is placed in position, correct alignment being ensured by means of small dowel pins. Patterns for the necessary feeder, runner and risers are also placed so as to give an even distribution of metal into the mould cavity. The rise rs should coincide with the highest readily escape from the mould. The sizes of risers should be such thatthe metal in them does not freeze too rapidly. An important function of a riser is to act as reservoir of liquid metal to feed solidification within the mould. A thin coating of dry parting sand is sprinkled into mould at this stage. This is to prevent the cope and drag sticking together when the cope half is moulded. The cope is now filled with moulding sand and this is rammed firmly into shape in the same manner as in the making of the drag.After the ramming of sand in the cope is completed the two halves of the moulding box are carefully separated. At this stage venting of the moulding box are carefully separated. At this stage venting of the mould can be done, if necessary, to increase the permeability of the mould. After venting the patterns are carefully removed from both cope and drag, and a gate or gates are carefully cut to connect the runner channel with the main cavity. Gates should be sited to allow or entry into mould with a minimum of turbulence. Any loose sand is gently blown away and if a core is to be used it the cope upon the drag and it is then ready for use. Liquid metal is poured smoothly into the mould via the feeder. Pouring ceases when liquid metal appears at the top of the risers and the feeder channel is also full.When the metal that has been poured into a sand mould has fully solidified the mould is broken and casting is removed. The casting still has the runner and risers attached to it and there will be sand adhering to portions of the surface. Runners and risers are cut off and returned to the melting furnace. Sand cores are broken and adherent sand is cleaned from the surface by vibration or by sand blasting with dry sand. Any fins or metal flash formed at mould parting lines are removed by grinding and the castings are then ready for inspection.The main Elements of Horizontal Milling MachinesColumn and base The column and base form the foundation of the complete machine. Both are made from cast iron, designed with thick sections to ensure complete rigidity and freedom form vibration. The base, upon which the column is mounted, is also the cutting-fluid reservoir and contains the pump to circulate the fluid to cutting area.The column contains the spindle, accurately located in precision bearings. The spindle id driven through a gearbox from a vee-belt drive from the electric motor housed at the base of column. The gearbox enables a range of spindle speeds to be selected. In the model shown, twelve spindle speeds from 32 to 1400rev/min are available. The front of column carries the guideways upon which the knee is located and guided in a vertical direction.KneeThe knee, mounted on the column guideways, provides the vertical movement of the table. Power feed is available, through a gearbox mounted on the side, from a separate built-in motor, providing a range of twelve feed rates from 6 to 250mm/min. Drive is through a leadscrew, whose bottom end is fixed to machine base. Provision is made to raise and lower the knee byhand through a leadscrew and nut operates by a handwheel at the front. The knee has guideways on its top surface giving full-width support to the saddle and guiding it in a transverse direction. lock is provided to clamp the knee in any vertical position on the column.SaddleThe saddle, mounted on the knee guideways, providers the transverse movement of the table. Power feed is provided through the gearbox on the knee. A range of twelve feeds is available, from 12 to 500mm/min. Alternative hand movement is provided through a leadscrew and nut by a hand heel at the front of the knee.Camping of saddle to the knee is achieved by two clamps on the side of the saddle.The saddle has dovetail gun its upper surface, at right angles to the knee guideways, to provide a guide to the table in a longitudinal direction.TableThe table provides the surface upon which all workpieces and workholding equipment are located and clamped. A series of tee slots is provided for this purpose. The dovetail guides on undersurface locate in the guideways on the saddle, giving straight-line movement to the table in longitudinal direction at right angles to the saddle movement.Power feed is provided from the knee gearbox, through the saddle, to the table leadscrew. Alternative hand feed is provided by a handwheel at each end of the table. Stops at the front of the table can be set to disengage the longitudinal feed automatically in each direction. Spindle The spindle, accurately mounted in precision bearings, provides the drive for the milling cutters. Cutters can be mounted straight on the spindle nose or in curter-holding devices which in turn are mounted in the spindle, held in position by a drawbolt passing the hold spindle. Spindles of milling machines have a standard spindle nose to allow for easy interchange of cutters and cutter-holding devices. The bore of the nose is tapered to provide accurate location, the angle of taper being 1. The diameter of the taper depends on the size of the machine and may be 30,40,or 50 IST. Due to their steepness of angle, there tapers –known as non-stick or self-releasing- cannot be relied upon to transmit the drive to the cutter or cutter-holding device. Two driving keys are provided to transmit the drive.Overarm and arbor supportDue to the length of arbors used, support is required at the outer end to prevent deflection when cutting takes place. Support is provided by an arbor-support bracket, clamped to an overarm which is mounted on top of the column in a dovetail slide. The overarm is adjustable in or out for different lengths of arbor, or can be fully pushed in when arbor support is not required. Two clamping bolts are support is located in the overarm dovetail and is locked by which the arbor runs during splindle rotation.中文译文数控机床的组成部分数控机床的组成部分包括测量系统、控制系统、伺服系统及开环或闭环系统,在对数控零件进行实际程序设计之前,了解各组成部分是重要的。
机械类英语论文翻译.doc

机械类英语论文翻译.doc轴承内径 bearing bore diameter轴承寿命 bearing life轴承套圈 bearing ring轴承外径 bearing outside diameter轴颈 journal轴瓦、轴承衬 bearing bush轴端挡圈 shaft end ring轴环 shaft collar轴肩 shaft shoulder轴角 shaft angle轴向 axial direction轴向齿廓 axial tooth profile轴向当量动载荷 dynamic equivalent axial load轴向当量静载荷 static equivalent axial load轴向基本额定动载荷 basic dynamic axial load rating轴向基本额定静载荷 basic static axial load rating 轴向接触轴承 axial contact bearing轴向平面 axial plane轴向游隙 axial internal clearance轴向载荷 axial load轴向载荷系数 axial load factor轴向分力 axial thrust load主动件 driving link主动齿轮 driving gear主动带轮 driving pulley转动导杆机构 whitworth mechanism转动副 revolute (turning) pair转速 swiveling speed rotating speed转动关节 revolute joint转轴 revolving shaft转子 rotor转子平衡 balance of rotor装配条件 assembly condition锥齿轮 bevel gear锥顶 common apex of cone锥距 cone distance锥轮 bevel pulley; bevel wheel锥齿轮的当量直齿轮 equivalent spur gear of the bevel gear 锥面包络圆柱蜗杆 milled helicoids worm准双曲面齿轮 hypoid gear子程序 subroutine子机构 sub-mechanism自动化 automation自锁 self-locking自锁条件 condition of self-locking自由度 degree of freedom, mobility。
(机械制造行业)机械英语——机加工专业(单词词组)中英文对照

(机械制造行业)机械英语——机加工专业(单词词组)中英文对照机械英语机加工专业(单词/词组)中英对照Aabrasion n. 磨料,研磨材料,磨蚀剂, adj. 磨损的,磨蚀的abrasive belt n. 砂带abrasive belt grinding n. 砂带磨削,用研磨带磨光abrasive cut-off machine n. 砂轮切断机abrasive dressing wheel n. 砂轮修整轮abrasive grain n. 磨料粒度abrasive grit n. 研磨用磨料,铁粒abrasive lapping wheel n. 磨料研磨轮accuracy of position n. 位置精度accuracy to shape n. 形状精度active cutting edge n. 主切削刃adapter flange n. 连接器法兰盘adjointing flanks n. 共轭齿廓align n. 找中(心),找正,对中,对准,找平,调直,校直,调整,调准angle milling cutter n. 角铣刀angular grinding n. 斜面磨削,斜磨法angular milling n. 斜面铣削angular plunge grinding n. 斜向切入磨削angular turning n. 斜面车削arbour n. 刀杆,心轴,柄轴,轴,辊轴attachment n. 附件,附件机构,联结,固接,联结法automatic bar machine n. 棒料自动车床automatic boring machine n. 自动镗床automatic copying lathe n. 自动仿形车床automatic double-head milling machine n. 自动双轴铣床automatic lathe n. 自动车床automatic turret lathe n. 自动转塔车床Bbelt grinding machine n. 砂带磨床bench lathe n. 台式车床bevel n. 斜角,斜面,倾斜,斜切,斜角规,万能角尺,圆锥的,倾斜的,斜边,伞齿轮,锥齿轮bevel gear cutting machine n. 锥齿轮切削机床bevel gear tooth system n. 锥齿轮系,锥齿轮传动系统borehole n. 镗孔,镗出的孔,钻眼boring n. 镗孔,钻孔,穿孔boring fixture n. 镗孔夹具boring machine n. 镗床boring tool n. 镗刀boring, drilling and milling machine n. 镗铣床broaching machine n.拉床,铰孔机,剥孔机broaching tool n. 拉刀broad finishing tool n. 宽刃精切刀,宽刃精车刀,宽刃光切刀CCalibrate vt. 校准〔正〕,刻度,分度,检查〔验〕,定标,标定,使标准化,使符合标准cam contour grinder n. 凸轮仿形磨床carbide tip n. 硬质合金刀片carbide turning tool n. 硬质合金车刀carbide-tipped tool n. 硬质合金刀具cast iron machining n. 铸铁加工,铸铁切削加工centerless cylindrical grinder n. 无心外圆磨床ceramic cutting tool n. 金属陶瓷刀具chamfer n.;vt. 倒角,倒棱chamfered cutting edge n. 倒角刀刃champ v. 焦急champing fixture n. 快换夹具champing jaw n. 快换卡爪chaser n. 螺纹梳刀,梳刀盘,板牙chatter vi.;n. 振动,振荡,震颤,刀振cherry n.;a. 樱桃,鲜红的,樱桃木制的chip n. 切屑,铁屑,刀片,刀头,片,薄片,芯片,基片chip breaker groove radius n. 断屑槽底半径,卷屑槽底半径chip clearance n. 切屑间隙chip cross-sectional area n. 切屑横截面面积chip curl n. 螺旋形切屑chip flow n. 切屑流chip formation n. 切屑形成chip removing process n. 去毛刺加工chip variable n. 切屑变量chuck n. 卡盘,夹盘,卡头,〔电磁〕吸盘,vt. 固定,装卡,夹紧,卡住chucker n. 卡盘车床,卡角车床circular drilling machine n. 圆工作台钻床circular path n. 环路,圆轨迹circular pitch measurement n. 周节测量circumference n. 圆周,周线,周界,周围,四周,范围close-grained a. 细颗粒的coffecient of tool thrust n. 刀具推力系数coil chip n. 卷状切屑cold circular saw n. 冷圆锯cold saw n. 冷锯column drilling machine n. 圆〔方〕柱立式钻床combined drill and milling cutter n. 复合钻铣床complete traverse grinding n. 横进给磨削,切入磨削computer-controlled machine n. 计算机控制机床,数控机床contact pattern n. 靠模continuous chip n. 连续切屑continuous spiral chip n. 连续螺旋切屑contour n. 轮廓,外形,外貌,轮廓线,回路,网路,电路,等高线,等值线,轮廓等高距a. 仿形的,靠模的contour grinding n. 仿形磨削,成形磨削contour milling n. 成形铣削,外形铣削,等高走刀曲面仿形法convex milling attachment n. 凸面铣削附件convex turning attachment n. 中凸车削附件,凸面车削附件coolant lubricant n. 冷却润滑剂coolant lubricant emulsion n. 冷却润滑乳液〔剂〕copy n. 样板,仿形,靠模工作法,拷贝复制品,v. 复制,模仿,抄录copy grinding n. 仿形磨床copy-mill n. 仿形铣copying turret lathe n. 仿形转塔车床corner n. 角,弯〔管〕头,弯管counterbore n. 埋头孔,沉孔,锥口孔,平底扩孔钻,平底锪钻, n.;vt. 扩孔,锪孔,镗孔,镗阶梯孔crankshaft grinding machine n. 曲轴磨床crankshaft turning lathe n. 曲轴车床creep feed grinding n. 缓进给磨削cross milling n. 横向铣削curly chip n. 卷状切屑,螺旋形切屑,切屑螺旋cut v.;n. 切削〔割〕,口,片,断,断开,削减,减少,断面,剖面,相交,凹槽cut off n. 切断〔开,去〕,关闭,停车,停止,断开装置,断流器,挡板,截止,截流cut teeth n. 铣齿cut-off grinding n. 砂轮截断,砂轮切割cutter n. 刀具,切削工具,截断器,切断器,切断机cutting n. 切削,切片,切割,切屑,金属屑,截槽cutting edge profile n. 切削刃轮廓〔外形,断面〕,切削刃角度cutting force n. 切削力cutting lip n. 切削刃,刀刃,钻唇,钻刃cutting operation n. 切削加工,切削操作,切削作业cutting rate n. 切削效率,切削速率cutting tool n. 刀具,切削工具,刃具cycle n. 周期,周,循环,一个操作过程,轮转,自行车cylindrical grinder n. 外圆磨床Ddamage n.;vt. 损坏〔害,伤,耗,失〕,破坏,事故,故障,伤害,危害deep-hole drilling n.深孔钻削deep-hole milling n. 深孔铣削design n. 设计,计算,计划,方案,设计书,图纸die-sinking n. 凹模dimension n. 尺寸,尺度,维度,量纲,因次direction of the feed motion n. 进给方向,进刀方向discontinuous chip n. 间断切屑distance n. 距离,间隔〔隙〕,长度,vt. 隔开double-column planer-miller n. 双柱龙门铣床dress v. 修饰,修整,平整,整理,清理,装饰,调制,准备,打磨,磨光,压平,轿直,清洗,清理,分级drilling n. 钻头,钻床,穿孔器,凿岩机,v. 钻孔,打孔,钻井,钻探drilling machine n. 钻床,钻机,钻孔机,打眼机drilling tool n. 钻孔〔削,井,眼〕工具Eedge point n. 刀口,刀刃efficiency n. 效率,效能,性能,功率,产量,实力,经济性,有〔功,实〕效end mill n. 立铣刀external grinding n. 外圆磨削Fface n. 表面,外观,工作面,表盘,屏,幕v. 面向,朝向,表面加工,把表面弄平face grinding machine n. 平面磨床face milling machine n. 端面磨床feed force n. 进给力feed motion n. 进给运动fine adjustment n. 精调,细调,微调fine boring n. 精密镗孔finish v.;n. 精加工,抛光,修整,表面粗糙度,完工,最后加工,最后阶段,涂层,涂料finish-cutting n. 精加工,最终切削fixture n. 夹具,夹紧装置,配件,零件,定位器,支架form n. 型式,类型,摸板,模型,形成,产生,成形,表格v. 形〔组,构〕成,产生,作出,成形,造型form-turn n. 成形车削free-cutting n. 自由切削,无支承切削,高速切削Ggap n. 间隔,间隙,距离,范围,区间,缺口,开口火花隙,vt. 使产生裂缝vi. 豁开gear cutting machine n. 齿轮加工机床,切齿机gear generating grinder n. 磨齿机gear hob n. 齿轮滚刀grinding cutter n. 磨具grinding force n. 磨削力grinding machine n. 磨床grinding wheel diameter n. 砂轮直径grinding wheel width n. 砂轮宽度groove n. 槽,切口,排屑槽,空心槽,坡口,vt. 切〔开,铣〕槽groove milling n.铣槽Hheadstock spindle n. 床头箱主轴,主轴箱主轴,头架轴helical tooth system n. 螺旋齿轮传动装置high precision lathe n. 高精度车床high-speed n. 高速high-speed machining n. 高速加工hob n. 齿轮滚刀,滚刀,螺旋铣刀,v. 滚铣,滚齿,滚削horsepower n. 马力hobbing machine n. 滚齿机,螺旋铣床,挤压制模压力机,反应阴模机hole n. 孔,洞,坑,槽,空穴,孔道,管道,v. 钻〔穿,冲,开〕孔,打洞hone n. vt. 磨石,油石,珩磨头,磨孔器,珩磨,honing machine n. 珩磨机,珩床,搪磨床,磨孔机,磨气缸机Iinclination n. 倾斜,斜度,倾角,斜角〔坡〕,弯曲,偏〔差,角〕转increment n. 增量,增加,增〔大〕长indexing table automatic n. 自动分度工作台infeed grinding n. 切入式磨削installation n. 装置,设备,台,站,安装,设置internal grinding n. 内圆磨削involute hob n. 渐开线滚刀Jjig boring machine n. 坐标镗床Kkeyway cutting n. 键槽切削加工knurling tool n. 滚花刀具,压花刀具,滚花刀Llaedscrew machine n. 丝杠加工机床lap grinding n. 研磨lapping n. 研磨,抛光,精研,搭接,擦准lathe n. 车床lathe dog n. 车床轧头,卡箍,鸡心夹头,离心夹头,制动爪,车床挡块lathe tool n. 车刀level n. 水平,水准,水平线,水平仪,水准仪,电平,能级,程度,强度,a. 水平的,相等的,均匀的,平稳的loading time n. 装载料时间,荷重时间,充填时间,充气时间lock n. 锁,栓,闸,闭锁装置,锁型,同步,牵引,v. 闭锁,关闭,卡住,固定,定位,制动刹住longitudinal grinding n. 纵磨low capacity machine n. 小功率机床〔机器〕Mmachine axis n. 机床中心线machine table n. 机床工作台machine tool n. 机床,工作母机machining n. 机械加工,切削加工machining (or cutting) variable n. 加工(或切削)变量machining allowance n. 机械加工余量machining cycle n. 加工循环machining of metals n. 金属切削加工,金属加工magazine automatic n. 自动化仓库,自动化料斗,自动存贮送料装置manufacture n. 制造者,生产者,厂商,产品,制造material removing rate n. 材料去除率metal cutting n. 金属切削metal-cutting technology n. 金属切削工艺学,金属切削工艺〔技术〕metal-cutting tool n. 金属切削刀具,金属切削工具micrometer adjustment n. 微调milling n. 铣削,磨碎,磨整,选矿milling feed n. 铣削进给,铣削走刀量,铣削走刀机构milling machine n. 铣床milling spindle n. 铣床主轴milling tool n. 铣削刀具,铣削工具mount v. 固定,安装,装配,装置,架设,n. 固定件,支架,座,装置,机构mounting n. 安装,装配,固定,机架,框架,装置mounting fixture n. 安装夹具,固定夹具NNose n. 鼻子,端,前端,凸头,刀尖,机头,突出部分,伸出部分number of revolutions n. 转数numerical control n. 数字控制numerically controlled lathe n. 数控车床Ooblique grinding n. 斜切式磨床operate v. 操纵,控制,运行,工作,动作,运算operating cycle n. 工作循环operation n. 运转,操作,控制,工作,作业,运算,计算operational instruction n. 操作说明书,操作说明operational safety n. 操作安全性,使用可靠性oscillating type abrasive cutting machine n. 摆动式砂轮切割机oscillation n. 振动,振荡,摆动,颤振,振幅out-cut milling n. 切口铣削oxide ceramics n. 氧化物陶瓷oxide-ceramic cutting tool n. 陶瓷刀具Pperformance n. 实行,执行,完成,特性,性能,成品,制作品,行为,动作,生产率,效率peripheral grinding n. 圆周磨削peripheral speed n. 圆周速度,周速,边缘速度perpendicular a. 垂直的,正交的,成直角的n. 垂直,正交,竖直,垂线,垂直面physical entity n. 实体,实物pitch n. 齿距,节距,铆间距,螺距,极距,辊距,坡度,高跨比,俯仰角pitch circle n. 节圆plain (or cylindrical) milling machine n. 普通(或圆柱形)铣床plain grinding n. 平面磨削plain turning n. 平面车床plane n. 平面,面,投影,刨,水平,程度,阶段,飞机a.平的v. 弄平,整平,刨,飞行plane milling n. 平面铣削plane-mill n. 平面铣刀,平面铣床plunge mill n. 模向进给滚轧机plunge-cut n. 切入式磨削,横向进给磨削,全面进刀法,全面进给法plunge-cut thread grinder n. 切入式螺纹磨床plunge-grinding n. 切入式磨削point n. 点,尖端,刀尖,针尖,指针,交点,要点,论点,特点v. 指,面向,瞄准,对准,表明,弄尖,强调power n. 功率,效率,能〔容,力〕量,动力,电源,能源v. 驱〔拖,带,发〕动,给...以动力power hacksaw n. 机动弓锯〔钢锯〕precision boring n. 精镗precision boring machine n. 精密镗床precision machining n. 精密机械加工pressure angle n. 压力角primary cutting edge n. 主切削刃principal feed motion n. 主进给运动,主进刀运动production method s n. 生产方法[式]profile n. 轮廓,形面,剖面,侧面图,分布图。
机械外文翻译中英文机床模具机械材料.doc
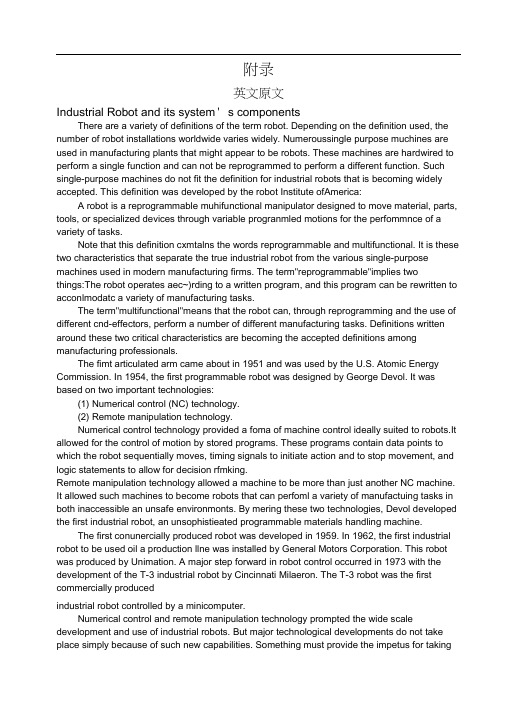
附录英文原文Industrial Robot and its system' s componentsThere are a variety of definitions of the term robot. Depending on the definition used, the number of robot installations worldwide varies widely. Numeroussingle purpose muchines are used in manufacturing plants that might appear to be robots. These machines are hardwired to perform a single function and can not be reprogrammed to perform a different function. Such single-purpose machines do not fit the definition for industrial robots that is becoming widely accepted. This definition was developed by the robot Institute ofAmerica:A robot is a reprogrammable muhifunctional manipulator designed to move material, parts, tools, or specialized devices through variable progranmled motions for the perfommnce of a variety of tasks.Note that this definition cxmtalns the words reprograrnmable and multifunctional. It is these two characteristics that separate the true industrial robot from the various single-purpose machines used in modern manufacturing firms. The term"reprogrammable"implies two things:The robot operates aec~)rding to a written program, and this program can be rewritten to acconlmodatc a variety of manufacturing tasks.The term"multifunctional"means that the robot can, through reprogramming and the use of different cnd-effectors, perform a number of different manufacturing tasks. Definitions written around these two critical characteristics are becoming the accepted definitions among manufacturing professionals.The fimt articulated arm came about in 1951 and was used by the U.S. Atomic Energy Commission. In 1954, the first programmable robot was designed by George Devol. It was based on two important technologies:(1) Numerical control (NC) technology.(2) Remote manipulation technology.Numerical control technology provided a foma of machine control ideally suited to robots.It allowed for the control of motion by stored programs. These programs contain data points to which the robot sequentially moves, timing signals to initiate action and to stop movement, and logic statements to allow for decision rfmking.Remote manipulation technology allowed a machine to be more than just another NC machine. It allowed such machines to become robots that can perfoml a variety of manufactuing tasks in both inaccessible an unsafe environmonts. By mering these two technologies, Devol developed the first industrial robot, an unsophistieated programmable materials handling machine.The first conunercially produced robot was developed in 1959. In 1962, the first industrial robot to be used oil a production llne was installed by General Motors Corporation. This robot was produced by Unimation. A major step forward in robot control occurred in 1973 with the development of the T-3 industrial robot by Cincinnati Milaeron. The T-3 robot was the first commercially producedindustrial robot controlled by a minicomputer.Numerical control and remote manipulation technology prompted the wide scale development and use of industrial robots. But major technological developments do not take place simply because of such new capabilities. Something must provide the impetus for takingadvantage of these capabilities. In the case of industrial robots, the impetus was economies.The rapid inflation of wages experienced in the 1970s tremendously increased the personnel costs of manufacturing firms. At the sametime, foreign competition became a serious problem for U. S. manufacturers. Foreign manufacturers who had under taken automation on a wide scale basis, such as those in Japan, began to gain an increasingly large share of the U.S. and world market for manufactured goods, particularly automobiles.Through a variety of automation techniques, includicg robots, Japanese manufacturers, beginning in the 1970s, were able to produce better automobiles more cheaply than nonautomated U.S. manufacturers. Consequently, in order to survive, U.S. manufacturers were forced to consider any technological developments that could help improve productivity.It became imperative to produce better produets at lower costs in order to be competitive with foreign manufacturers. Other factors such as the need to find better ways of performing dangerous marmfacturing tasks contributed to the development of industrial robots. However, the principal rationale has always been,and is still, improved productivity.Oneof the principal advantages of robots is that they can be used in settings that are dangerous to humans. Welding and parting are examples of applications where rotmts can be dangerous to humans. Even though robots are closely asmciated with safety in the workplace, they can, in themselves, be dangerous.Robots and robot cells must be carefully designed and configured so that they do not endanger human workers and other machines. Robot work envelops should be accurately calculated and a danger zone surroundting the envelop clearly marked off. Red flooring strips and barriers can be userd to keep human workers out of a robot ' s work envelope.Eren with such precautions it is still a good idea to have an automatic shutdown system in situations where robots are used. Such a system should should have the capacity to sense the need for an automatic shutdown of operations. Fault-tolerant computers and redunant systems can be installed to ensure proper shutdown of robotics systems to ensure a safe environment.Industrial robots is the science of designing, building, and applying industrial robcts. What are robots? In the late 1970s the Robotic Industries Association defined a robot as ” a manipulator, designed to move material, parts,tools or specialized devices through variable programmed motions for the performance of a variety of tasks". Although this definition does not directlyinclude pick and place arms as robots, teleoperamrs and remotely controlled devicesare often referred to also as robots. The International Standards Organization(ISO) has a more lengthy definition of an industrial robot:A machine formed by a mechanism including several degrees of freedom, often having tile appearanoa of one or several arms ending in a wrist capable of holding a tool or a workpiece or an inspection device. In particular, its control unit must use a memorizing deviceand .sometimes it can use sensing or adaptation appliances taking into account environment and circumstances. These multipurtpose machines are generally designed to carry out a repetitive function and can be adapted to other functions.The RIA and ISO definitions both stress the muLtifunctional and programmable capabilities and, therefore, exclude special-purpose "hard automation" tools and equipment typically found in high volume production. Also excluded are manual remote manipulators, which are extensions of humanhands for use in, for example, sterile, hot, or radioactive environments.In Japan, the Japanese Industrial Robot Association (JIRA) classifies industrial robots bythe method of input informatkm and the method of teaching:1. Manual Manipulators. Manipulators directly activated by the operator.2. Fixed-sequence Robot. Robot that once programmed for a given sequence of operations is not easily changed.3. Variable-sequence Robot. Robot that can be programmed for a given sequence of operations and can easily be changed or reprogrammed.4. Playback Robot. Robot that "memorizes" work sequences taught by a human being who physically leads the device through the intended work pattern; the robot can then create this sequence repetitively from memory.5. Numerically Controlled (NC) Robot. Robot that operatas from and is controlled by digital data, as in the form of punched tape, cards, or digital switches; operates like a NC machine.6. Intelligent Robot. Robot that uses sensory perception to evaluate its environment andcmake decisions and proceeds to operate accordingly.The first-generation of robot systems was defined for the various robots with limited computer power. Their main intelligant functions include programming by showing a sequence of manipulation steps by a human operator using a teach box. Without any sensors, these robots require a prearranged and relatively fixed factory environment and, therefore, have limited use.The second-generation of robot systems was enhanced by the addition of a computer processor. A major step in industrial robotics development was the integration of a computer with the industrial robot mechanism. This has provided real-time calculation of trajectory to smooth the motions of the end effector and integration of mine simple force and proximity sensors to obtain external signals.The main applications of second generation robots include spot and arc welding, spray painting, and some assembly.Third-generation robot systems incorporate multiple eomputer processors and multiple arms that can operate asynchronously to perform .several functions. Distributed hierarchical mmputer organization is preferred, because it can coordinate motions and interface with external sensors, other machines, and other robots and can communicate with other computers. These robots can already exhibit intelligent behavior, including knowledge-based control and learning abilities.Japan ranks as the world's top robot-producing and robot-using country, with more than 40%of the world's industrial robot installations. The reasons for this penetration are sociological-and technological factors that are unique to Japan: industrial robots brought productivity and quality gains in Japanese industry, coupled with improvements of the work enviromnent. These have perpetuated the social-demand for more robots as well as increased the expectation from this technology.Current and emerging robot applications in industry can be categorized on the complexity and requirements of the job. They range from simple, low technolngy pick-and place operations through medium technology painting, some assembly and welding operations to high technology precision assembly and inspection operations.Pick-and-place Operations The earliest applications of robots were in machine loading unloading, pick-and-place, and material transfer operations. Such robots typically were not servo controlled and worked with pneumatic or hydraulic power. The Icxad-carryingrequirements were high, working in dirty or hazardous factory environments. Replacing unskilled human labor often in hazardous jobs, these robots had to be robust and low in initial and maintenance costs.Painting and Welding Operations The next level in the sophistimtion of industrial robot applications was in spray painting, and spot and arc welding.These applications complemented or replaced certain skilled human labor. Often the justification was by eliminating dangerous environmental exposures. These applications often require tracking complex trajectories such as painting surface mntours, hence mrvo controlled "articulated or spherical robot structures were used.Lead-through teaching modes became commom, and sometimes sophisticated sensors are employed to maintain process consistency. Experience has shown that when properly selected and implemented, thase robotic applications usually lead to reduced overall manufacturing costs and improved product quality compared with manual method.Assembly Operations The most advanced level of technology employing third-generation industrial robots is found in assembly. System repeatability is of utmost importance. End-of-arm tooling must be compliant, i.e., have both force and displacement control to adjust part insertions, which require that the robot actually "feel" its way along. This technology usually requires a measure of artificial intelligence. Assembly robots generally are electronically driven and operate in clean enviromnents. Assembly robots are expected to exceed further technology applications.Other Applications Other typical applications of robots include inspection, quality control, and repair; processing such as laser and water jet cutting and drilling, riveting, and clean room operations; and applications in the wood, paper, and food-processing industries. As industrial robot technology and robot intelligence improve even further, additional applications may be justified effectively.The components of a robot system could be discussed either from a physical point of view or from a systems point of view. Physically, we would divide the system into the robot, power system, and controller (computer). Likewise, the robot itself could be partitioned anthropomorphically into base, shoulder, elbow, wrist, gripper, and tool. Most of these terms require little explanation.Consequently, we will describe the components of a robot system from the point of view of information transfer. That is, what infomtation or signal enters the component; what logical or arithmetic operation does the component perform; and what information or signal does the component produce? It is important to note that the same physical component may perform many different information proees.sirkg operations (e. g. , a central computerperforms many different calculations on different data). Likewise, two physically separate components may perform identical information operations ( e. g., the shoulder and elbow actuators both convert signals to motion in very similar ways).Actuator Asmciated with each joint on the robot is an actuator which causes that joint to move. Typical actuators are electric motors and hydraulic cylinders. Typically, a robot system will contain six actuators, since six are required for full control of position and orientation. Many robot applications do not require this full flexibility, and consequently, robots are often built with five or fewer actuators.Sensor To control an actuator, the computer must have infommtion regarding the position and possibly the velocity of the actuator. In this context, the termposition refers to a displacement from some arbitrary zero reference point for that actuator. For example, in the case of a rotary actuator , "position" would really the angular position and be measured in radians.Many types of sensors can provide indications of position and velocity. The various typesof sensors require different mechanisms for interfacing to the computer. In addition, the industrial use of the manipulator requires that the interface be protected from the harshelectrical environment of the factory. Sources of electrical noise such as arc welders and large motors can easily makena digital system useless unless care is taken in design and construction of the interface.Computation Wecould easily have labeled the computation module "computer,"as most of the Functions to be described are typically perfommd by digital computers. However, many ofthe Functions may be performed in dedicated custom hardware or networks of computers We will, thus, discuss the commputational component as if it were a simple computer, recognizing that tile need for real-time control may require special equipment and that some of this equipment may even be analog, although the current trend is toward fully digital systems.One further note: We will tend to avoid the use of the term microprocessor in this book and simply say computer, although many current robot manufacturers use one or more microprocessors in their systems.The computation component performs the following operations: Servo Given the current position and/or velocity of an actuator, determine the appropriate drivesignal to move that actuator toward its desired position. "This operation mustbe performed for eaeh actuator. Kinematics Given the current statel of the actuators (positionand velocity ),determine the current state of the gripper.Conversely, given a desired state of the hand, determine the desired state for each actuator.Dynamics Given knowledge of the loads on the arm (inertia, friction, gravity, acceleration), use this information to adjust the sorvo operation to achieve better performance.Workplace Sensor Analysis Given knowledge of the task to be performed, determine appropriate robot motion commands. This nmy include analyzing a TV picture of the workplaceor measuring and compensating for forces applied at the hand.In addition to these easily identified co. mponents, there are also supervisory operations such as path planning and operator interaction.中文翻译工业机器人及其系统组成有许多关于机器人这个术语的定义。
机械加工外文翻译、中英文翻译、机械类外文文献翻译
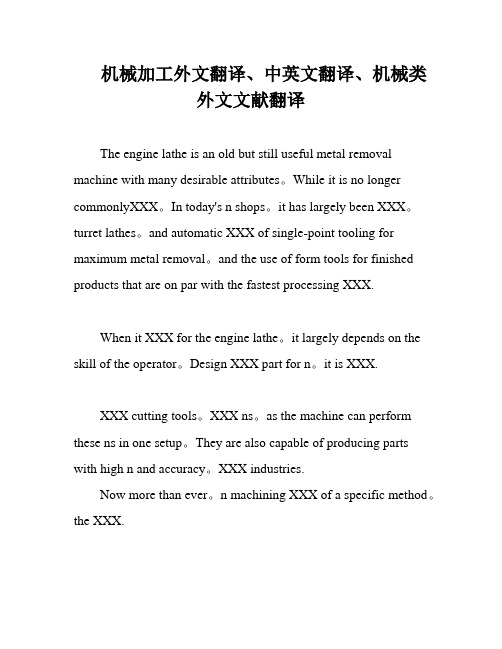
机械加工外文翻译、中英文翻译、机械类外文文献翻译The engine lathe is an old but still useful metal removal machine with many desirable attributes。
While it is no longer commonlyXXX。
In today's n shops。
it has largely been XXX。
turret lathes。
and automatic XXX of single-point tooling for maximum metal removal。
and the use of form tools for finished products that are on par with the fastest processing XXX.When it XXX for the engine lathe。
it largely depends on the skill of the operator。
Design XXX part for n。
it is XXX.XXX cutting tools。
XXX ns。
as the machine can perform these ns in one setup。
They are also capable of producing parts with high n and accuracy。
XXX industries.Now more than ever。
n machining XXX of a specific method。
the XXX.When designing for low quantities。
such as 100 or 200 parts。
it is most cost-effective to use a XXX。
designers should aim to minimize the number of ns required.Another n for n XXX。
机械中英文对照

机械专业英语词汇合成纤维synthetic fibre电化学腐蚀electrochemical corrosion车架automotive chassis悬架suspension转向器redirector变速器speed changer板料冲压sheet metal parts孔加工spot facing machining车间workshop工程技术人员engineer气动夹紧pneuma lock数学模型mathematical model画法几何descriptive geometry机械制图Mechanical drawing投影projection视图view剖视图profile chart标准件standard component零件图part drawing装配图assembly drawing尺寸标注size marking技术要求technical requirements刚度rigidity内力internal force位移displacement截面section疲劳极限fatigue limit断裂fracture塑性变形plastic distortion脆性材料brittleness material刚度准则rigidity criterion垫圈washer垫片spacer直齿圆柱齿轮straight toothed spur gear 斜齿圆柱齿轮helical—spur gear直齿锥齿轮straight bevel gear运动简图kinematic sketch齿轮齿条pinion and rack蜗杆蜗轮worm and worm gear虚约束passive constraint曲柄crank摇杆racker凸轮cams共轭曲线conjugate curve范成法generation method定义域definitional domain值域range导数\\微分differential coefficient求导derivation定积分definite integral不定积分indefinite integral曲率curvature偏微分partial differential毛坯rough游标卡尺slide caliper千分尺micrometer calipers攻丝tap二阶行列式second order determinant逆矩阵inverse matrix线性方程组linear equations概率probability随机变量random variable排列组合permutation and combination气体状态方程equation of state of gas动能kinetic energy势能potential energy机械能守恒conservation of mechanical energy动量momentum桁架truss轴线axes余子式cofactor逻辑电路logic circuit触发器flip-flop脉冲波形pulse shape数模digital analogy液压传动机构fluid drive mechanism机械零件mechanical parts淬火冷却quench淬火hardening回火tempering调质hardening and tempering磨粒abrasive grain结合剂bonding agent砂轮grinding wheel后角clearance angle龙门刨削planing主轴spindle主轴箱headstock卡盘chuck加工中心machining center车刀lathe tool车床lathe钻削镗削bore车削turning磨床grinder基准benchmark钳工locksmith锻forge压模stamping焊weld拉床broaching machine拉孔broaching装配assembling铸造found流体动力学fluid dynamics流体力学fluid mechanics加工machining液压hydraulic pressure切线tangent机电一体化mechanotronics mechanical-electrical integration 气压air pressure pneumatic pressure稳定性stability介质medium液压驱动泵fluid clutch液压泵hydraulic pump阀门valve失效invalidation强度intensity载荷load应力stress安全系数safty factor可靠性reliability螺纹thread螺旋helix键spline销pin滚动轴承rolling bearing滑动轴承sliding bearing弹簧spring制动器arrester brake十字结联轴节crosshead联轴器coupling链chain皮带strap精加工finish machining粗加工rough machining变速箱体gearbox casing腐蚀rust氧化oxidation磨损wear耐用度durability随机信号random signal离散信号discrete signal超声传感器ultrasonic sensor集成电路integrate circuit挡板orifice plate残余应力residual stress套筒sleeve扭力torsion冷加工cold machining电动机electromotor汽缸cylinder过盈配合interference fit热加工hotwork摄像头CCD camera倒角rounding chamfer优化设计optimal design工业造型设计industrial moulding design有限元finite element滚齿hobbing插齿gear shaping伺服电机actuating motor铣床milling machine钻床drill machine镗床boring machine步进电机stepper motor丝杠screw rod导轨lead rail组件subassembly可编程序逻辑控制器Programmable Logic Controller PLC 电火花加工electric spark machining电火花线切割加工electrical discharge wire - cutting相图phase diagram热处理heat treatment固态相变solid state phase changes有色金属nonferrous metal陶瓷ceramics合成纤维synthetic fibre电化学腐蚀electrochemical corrosion车架automotive chassis悬架suspension转向器redirector变速器speed changer板料冲压sheet metal parts孔加工spot facing machining车间workshop工程技术人员engineer气动夹紧pneuma lock数学模型mathematical model画法几何descriptive geometry机械制图Mechanical drawing投影projection视图view剖视图profile chart标准件standard component零件图part drawing装配图assembly drawing尺寸标注size marking技术要求technical requirements刚度rigidity内力internal force位移displacement截面section疲劳极限fatigue limit断裂fracture塑性变形plastic distortion脆性材料brittleness material刚度准则rigidity criterion垫圈washer垫片spacer直齿圆柱齿轮straight toothed spur gear 斜齿圆柱齿轮helical—spur gear直齿锥齿轮straight bevel gear运动简图kinematic sketch齿轮齿条pinion and rack蜗杆蜗轮worm and worm gear虚约束passive constraint曲柄crank摇杆racker凸轮cams共轭曲线conjugate curve范成法generation method定义域definitional domain值域range导数\\微分differential coefficient求导derivation定积分definite integral不定积分indefinite integral曲率curvature偏微分partial differential毛坯rough游标卡尺slide caliper千分尺micrometer calipers攻丝tap二阶行列式second order determinant逆矩阵inverse matrix线性方程组linear equations概率probability随机变量random variable排列组合permutation and combination气体状态方程equation of state of gas动能kinetic energy势能potential energy机械能守恒conservation of mechanical energy 动量momentum桁架truss轴线axes余子式cofactor逻辑电路logic circuit触发器flip—flop脉冲波形pulse shape数模digital analogy液压传动机构fluid drive mechanism机械零件mechanical parts淬火冷却quench淬火hardening回火tempering调质hardening and tempering磨粒abrasive grain结合剂bonding agent砂轮grinding wheelAssembly line 组装线Layout 布置图Conveyer 流水线物料板Rivet table 拉钉机Rivet gun 拉钉枪Screw driver 起子Pneumatic screw driver 气动起子worktable 工作桌OOBA 开箱检查fit together 组装在一起fasten 锁紧(螺丝)fixture 夹具(治具)pallet 栈板barcode 条码barcode scanner 条码扫描器fuse together 熔合fuse machine热熔机repair修理operator作业员QC品管supervisor 课长ME 制造工程师MT 制造生技cosmetic inspect 外观检查inner parts inspect 内部检查thumb screw 大头螺丝lbs. inch 镑、英寸EMI gasket 导电条front plate 前板rear plate 后板chassis 基座bezel panel 面板power button 电源按键reset button 重置键Hi—pot test of SPS 高源高压测试Voltage switch of SPS 电源电压接拉键sheet metal parts 冲件plastic parts 塑胶件SOP 制造作业程序material check list 物料检查表work cell 工作间trolley 台车carton 纸箱sub—line 支线left fork 叉车personnel resource department 人力资源部production department生产部门planning department企划部QC Section品管科stamping factory冲压厂painting factory烤漆厂molding factory成型厂common equipment常用设备uncoiler and straightener整平机punching machine 冲床robot机械手hydraulic machine油压机lathe车床planer |plein|刨床miller铣床grinder磨床linear cutting线切割electrical sparkle电火花welder电焊机staker=reviting machine铆合机position职务president董事长general manager总经理special assistant manager特助factory director厂长department director部长deputy manager |=vice manager副理section supervisor课长deputy section supervisor =vice section superisor副课长group leader/supervisor组长line supervisor线长assistant manager助理to move, to carry, to handle搬运be put in storage入库pack packing包装to apply oil擦油to file burr 锉毛刺final inspection终检to connect material接料to reverse material 翻料wet station沾湿台Tiana天那水cleaning cloth抹布to load material上料to unload material卸料to return material/stock to退料scraped |\\’skr?pid|报废scrape ..v.刮;削deficient purchase来料不良manufacture procedure制程deficient manufacturing procedure制程不良oxidation |\\’ ksi\\’dei?n|氧化scratch刮伤dents压痕defective upsiding down抽芽不良defective to staking铆合不良embedded lump镶块feeding is not in place送料不到位stamping-missing漏冲production capacity生产力education and training教育与训练proposal improvement提案改善spare parts=buffer备件forklift叉车trailer=long vehicle拖板车compound die合模die locker锁模器pressure plate=plate pinch压板bolt螺栓administration/general affairs dept总务部automatic screwdriver电动启子thickness gauge厚薄规gauge(or jig)治具power wire电源线buzzle蜂鸣器defective product label不良标签identifying sheet list标示单location地点present members出席人员subject主题conclusion结论decision items决议事项responsible department负责单位pre-fixed finishing date预定完成日approved by / checked by / prepared by核准/审核/承办PCE assembly production schedule sheet PCE组装厂生产排配表model机锺work order工令revision版次remark备注production control confirmation生产确认checked by初审approved by核准department部门stock age analysis sheet 库存货龄分析表on-hand inventory现有库存available material良品可使用obsolete material良品已呆滞to be inspected or reworked 待验或重工total合计cause description原因说明part number/ P/N 料号type形态item/group/class类别quality品质prepared by制表notes说明year—end physical inventory difference analysis sheet 年终盘点差异分析表physical inventory盘点数量physical count quantity帐面数量difference quantity差异量cause analysis原因分析raw materials原料materials物料finished product成品semi-finished product半成品packing materials包材good product/accepted goods/ accepted parts/good parts良品defective product/non-good parts不良品disposed goods处理品warehouse/hub仓库on way location在途仓oversea location海外仓spare parts physical inventory list备品盘点清单spare molds location模具备品仓skid/pallet栈板tox machine自铆机wire EDM线割EDM放电机coil stock卷料sheet stock片料tolerance工差score=groove压线cam block滑块pilot导正筒trim剪外边pierce剪内边drag form压锻差pocket for the punch head挂钩槽slug hole废料孔feature die公母模expansion dwg展开图radius半径shim(wedge)楔子torch—flame cut火焰切割set screw止付螺丝form block折刀stop pin定位销round pierce punch=die button圆冲子shape punch=die insert异形子stock locater block定位块under cut=scrap chopper清角active plate活动板baffle plate挡块cover plate盖板male die公模female die母模groove punch压线冲子air—cushion eject—rod气垫顶杆spring—box eject-plate弹簧箱顶板bushing block衬套insert 入块club car高尔夫球车capability能力parameter参数factor系数phosphate皮膜化成viscosity涂料粘度alkalidipping脱脂main manifold主集流脉bezel斜视规blanking穿落模dejecting顶固模demagnetization去磁;消磁high-speed transmission高速传递heat dissipation热传rack上料rinse水洗alkaline etch龄咬desmut剥黑膜D.I. rinse纯水次Chromate铬酸处理Anodize阳性处理seal封孔revision版次part number/P/N料号good products良品scraped products报放心品defective products不良品finished products成品disposed products处理品barcode条码flow chart流程表单assembly组装stamping冲压molding成型spare parts=buffer备品coordinate座标dismantle the die折模auxiliary fuction辅助功能poly—line多义线heater band 加热片thermocouple热电偶sand blasting喷沙grit 砂砾derusting machine除锈机degate打浇口dryer烘干机induction感应induction light感应光response=reaction=interaction感应ram连杆edge finder巡边器concave凸convex凹short射料不足nick缺口speck瑕??shine亮班splay 银纹delamination起鳞cold slug冷块blush 导色gouge沟槽;凿槽satin texture段面咬花witness line证示线patent专利grit沙砾granule=peuet=grain细粒grit maker抽粒机cushion缓冲magnalium镁铝合金magnesium镁金metal plate钣金lathe车mill锉plane刨grind磨drill铝boring镗blinster气泡fillet镶;嵌边through—hole form通孔形式voller pin formality滚针形式cam driver铡楔shank摸柄crank shaft曲柄轴augular offset角度偏差velocity速度production tempo生产进度现状torque扭矩spline=the multiple keys花键quenching淬火tempering回火annealing退火carbonization碳化tungsten high speed steel钨高速的moly high speed steel钼高速的organic solvent有机溶剂bracket小磁导liaison联络单volatile挥发性resistance电阻ion离子beacon警示灯coolant冷却液crusher破碎机阿基米德蜗杆Archimedes worm安全系数safety factor; factor of safety安全载荷safe load凹面、凹度concavity扳手wrench板簧flat leaf spring半圆键woodruff key变形deformation摆杆oscillating bar摆动从动件oscillating follower摆动从动件凸轮机构cam with oscillating follower 摆动导杆机构oscillating guide—bar mechanism 摆线齿轮cycloidal gear摆线齿形cycloidal tooth profile摆线运动规律cycloidal motion摆线针轮cycloidal—pin wheel包角angle of contact保持架cage背对背安装back-to—back arrangement背锥back cone ; normal cone背锥角back angle背锥距back cone distance比例尺scale比热容specific heat capacity闭式链closed kinematic chain闭链机构closed chain mechanism臂部arm变频器frequency converters变频调速frequency control of motor speed变速speed change变速齿轮change gear change wheel变位齿轮modified gear变位系数modification coefficient标准齿轮standard gear标准直齿轮standard spur gear表面质量系数superficial mass factor表面传热系数surface coefficient of heat transfer 表面粗糙度surface roughness并联式组合combination in parallel并联机构parallel mechanism并联组合机构parallel combined mechanism并行工程concurrent engineering并行设计concurred design,CD不平衡相位phase angle of unbalance不平衡imbalance (or unbalance)不平衡量amount of unbalance不完全齿轮机构intermittent gearing波发生器wave generator波数number of waves补偿compensation参数化设计parameterization design,PD残余应力residual stress操纵及控制装置operation control device槽轮Geneva wheel槽轮机构Geneva mechanism ;Maltese cross槽数Geneva numerate槽凸轮groove cam侧隙backlash差动轮系differential gear train差动螺旋机构differential screw mechanism差速器differential常用机构conventional mechanism; mechanism in common use 车床lathe承载量系数bearing capacity factor承载能力bearing capacity成对安装paired mounting尺寸系列dimension series齿槽tooth space齿槽宽spacewidth齿侧间隙backlash齿顶高addendum齿顶圆addendum circle齿根高dedendum齿根圆dedendum circle齿厚tooth thickness齿距circular pitch齿宽face width齿廓tooth profile齿廓曲线tooth curve齿轮gear齿轮变速箱speed-changing gear boxes齿轮齿条机构pinion and rack齿轮插刀pinion cutter;pinion—shaped shaper cutter齿轮滚刀hob ,hobbing cutter齿轮机构gear齿轮轮坯blank齿轮传动系pinion unit齿轮联轴器gear coupling齿条传动rack gear齿数tooth number齿数比gear ratio齿条rack齿条插刀rack cutter;rack-shaped shaper cutter 齿形链、无声链silent chain齿形系数form factor齿式棘轮机构tooth ratchet mechanism插齿机gear shaper重合点coincident points重合度contact ratio冲床punch传动比transmission ratio, speed ratio传动装置gearing;transmission gear传动系统driven system传动角transmission angle传动轴transmission shaft串联式组合combination in series串联式组合机构series combined mechanism串级调速cascade speed control创新innovation creation创新设计creation design垂直载荷、法向载荷normal load唇形橡胶密封lip rubber seal磁流体轴承magnetic fluid bearing从动带轮driven pulley从动件driven link,follower从动件平底宽度width of flat—face从动件停歇follower dwell从动件运动规律follower motion从动轮driven gear粗线bold line粗牙螺纹coarse thread大齿轮gear wheel打包机packer打滑slipping带传动belt driving带轮belt pulley带式制动器band brake单列轴承single row bearing单向推力轴承single—direction thrust bearing单万向联轴节single universal joint单位矢量unit vector当量齿轮equivalent spur gear; virtual gear当量齿数equivalent teeth number;virtual number of teeth当量摩擦系数equivalent coefficient of friction当量载荷equivalent load刀具cutter导数derivative倒角chamfer导热性conduction of heat导程lead导程角lead angle等加等减速运动规律parabolic motion; constant acceleration and deceleration motion 等速运动规律uniform motion; constant velocity motion等径凸轮conjugate yoke radial cam等宽凸轮constant-breadth cam等效构件equivalent link等效力equivalent force等效力矩equivalent moment of force等效量equivalent等效质量equivalent mass等效转动惯量equivalent moment of inertia等效动力学模型dynamically equivalent model底座chassis低副lower pair点划线chain dotted line(疲劳)点蚀pitting垫圈gasket垫片密封gasket seal碟形弹簧belleville spring顶隙bottom clearance定轴轮系ordinary gear train;gear train with fixed axes动力学dynamics动密封kinematical seal动能dynamic energy动力粘度dynamic viscosity动力润滑dynamic lubrication动平衡dynamic balance动平衡机dynamic balancing machine动态特性dynamic characteristics动态分析设计dynamic analysis design动压力dynamic reaction动载荷dynamic load端面transverse plane端面参数transverse parameters端面齿距transverse circular pitch端面齿廓transverse tooth profile端面重合度transverse contact ratio端面模数transverse module端面压力角transverse pressure angle锻造forge对称循环应力symmetry circulating stress对心滚子从动件radial (or in—line )roller follower对心直动从动件radial (or in—line ) translating follower对心移动从动件radial reciprocating follower对心曲柄滑块机构in—line slider-crank (or crank—slider)mechanism 多列轴承multi—row bearing多楔带poly V—belt多项式运动规律polynomial motion多质量转子rotor with several masses惰轮idle gear额定寿命rating life额定载荷load ratingII 级杆组dyad发生线generating line发生面generating plane法面normal plane法面参数normal parameters法面齿距normal circular pitch法面模数normal module法面压力角normal pressure angle法向齿距normal pitch法向齿廓normal tooth profile法向直廓蜗杆straight sided normal worm法向力normal force反馈式组合feedback combining反向运动学inverse (or backward)kinematics反转法kinematic inversion反正切Arctan范成法generating cutting仿形法form cutting方案设计、概念设计concept design,CD防振装置shockproof device飞轮flywheel飞轮矩moment of flywheel非标准齿轮nonstandard gear非接触式密封non—contact seal非周期性速度波动aperiodic speed fluctuation非圆齿轮non-circular gear粉末合金powder metallurgy分度线reference line;standard pitch line分度圆reference circle;standard (cutting) pitch circle 分度圆柱导程角lead angle at reference cylinder分度圆柱螺旋角helix angle at reference cylinder分母denominator分子numerator分度圆锥reference cone;standard pitch cone分析法analytical method封闭差动轮系planetary differential复合铰链compound hinge复合式组合compound combining复合轮系compound (or combined)gear train复合平带compound flat belt复合应力combined stress复式螺旋机构Compound screw mechanism复杂机构complex mechanism杆组Assur group干涉interference刚度系数stiffness coefficient刚轮rigid circular spline钢丝软轴wire soft shaft刚体导引机构body guidance mechanism刚性冲击rigid impulse (shock)刚性转子rigid rotor刚性轴承rigid bearing刚性联轴器rigid coupling高度系列height series高速带high speed belt高副higher pair格拉晓夫定理Grashoff`s law根切undercutting公称直径nominal diameter高度系列height series功work工况系数application factor工艺设计technological design工作循环图working cycle diagram工作机构operation mechanism工作载荷external loads工作空间working space工作应力working stress工作阻力effective resistance工作阻力矩effective resistance moment公法线common normal line公共约束general constraint公制齿轮metric gears功率power功能分析设计function analyses design共轭齿廓conjugate profiles共轭凸轮conjugate cam构件link鼓风机blower固定构件fixed link;frame固体润滑剂solid lubricant关节型操作器jointed manipulator惯性力inertia force惯性力矩moment of inertia ,shaking moment 惯性力平衡balance of shaking force惯性力完全平衡full balance of shaking force惯性力部分平衡partial balance of shaking force 惯性主矩resultant moment of inertia惯性主失resultant vector of inertia冠轮crown gear广义机构generation mechanism广义坐标generalized coordinate轨迹生成path generation轨迹发生器path generator滚刀hob滚道raceway滚动体rolling element滚动轴承rolling bearing滚动轴承代号rolling bearing identification code 滚针needle roller滚针轴承needle roller bearing滚子roller滚子轴承roller bearing滚子半径radius of roller滚子从动件roller follower滚子链roller chain滚子链联轴器double roller chain coupling滚珠丝杆ball screw滚柱式单向超越离合器roller clutch过度切割undercutting函数发生器function generator函数生成function generation含油轴承oil bearing耗油量oil consumption耗油量系数oil consumption factor赫兹公式H。
机械专业中英文对照

机械专业中英文对照后角clearance angle龙门刨削planing主轴spindle主轴箱headstock卡盘chuck加工中心machining center车刀lathe tool车床lathe钻削镗削bore车削turning磨床grinder基准benchmark钳工locksmith锻forge压模stamping焊weld拉床broaching machine拉孔broaching装配assembling铸造found流体动力学fluid dynamics流体力学fluid mechanics加工machining液压hydraulic pressure切线tangent机电一体化mechanotronics mechanical-electrical integration气压air pressure pneumatic pressure稳固性stability介质medium液压驱动泵fluid clutch液压泵hydraulic pump阀门valve失效invalidation强度intensity载荷load应力stress安全系数safty factor可靠性reliability螺纹thread螺旋helix键spline销pin滚动轴承rolling bearing滑动轴承sliding bearing弹簧spring制动器arrester brake十字结联轴节crosshead联轴器coupling链chain皮带strap精加工finish machining粗加工rough machining变速箱体gearbox casing腐蚀rust氧化oxidation磨损wear耐用度durability随机信号random signal离散信号discrete signal超声传感器ultrasonic sensor集成电路integrate circuit挡板orifice plate残余应力residual stress套筒sleeve扭力torsion冷加工cold machining电动机electromotor汽缸cylinder过盈配合interference fit热加工hotwork摄像头CCD camera倒角rounding chamfer优化设计optimal design工业造型设计industrial moulding design 有限元finite element滚齿hobbing插齿gear shaping伺服电机actuating motor铣床milling machine钻床drill machine镗床boring machine步进电机stepper motor丝杠screw rod导轨lead rail组件subassembly可编程序逻辑操纵器Programmable Logic Controller PLC电火花加工electric spark machining电火花线切割加工electrical discharge wire - cutting相图phase diagram热处理heat treatment固态相变solid state phase changesAssembly line 组装线Layout 布置图Conveyer 流水线物料板Rivet table 拉钉机Rivet gun 拉钉枪Screw driver 起子Pneumatic screw driver 气动起子worktable 工作桌OOBA 开箱检查fit together 组装在一起fasten 锁紧(螺丝)fixture 夹具(治具)pallet 栈板barcode 条码barcode scanner 条码扫描器fuse together 熔合fuse machine热熔机repair修理operator作业员QC品管supervisor 课长ME 制造工程师MT 制造生技cosmetic inspect 外观检查inner parts inspect 内部检查thumb screw 大头螺丝lbs. inch 镑、英寸EMI gasket 导电条front plate 前板rear plate 后板chassis 基座bezel panel 面板power button 电源按键reset button 重置键Hi-pot test of SPS 高源高压测试Voltage switch of SPS 电源电压接拉键sheet metal parts 冲件plastic parts 塑胶件SOP 制造作业程序material check list 物料检查表work cell 工作间trolley 台车carton 纸箱sub-line 支线left fork 叉车personnel resource department 人力资源部production department生产部门planning department企划部QC Section品管科stamping factory冲压厂painting factory烤漆厂molding factory成型厂common equipment常用设备uncoiler and straightener整平机punching machine 冲床robot机械手hydraulic machine油压机lathe车床planer |plein|刨床miller铣床grinder磨床linear cutting线切割electrical sparkle电火花welder电焊机staker=reviting machine铆合机position职务president董事长general manager总经理special assistant manager特助factory director厂长department director部长deputy manager | =vice manager副理section supervisor课长deputy section supervisor =vice section superisor副课长group leader/supervisor组长line supervisor线长assistant manager助理to move, to carry, to handle搬运be put in storage入库pack packing包装to apply oil擦油to file burr 锉毛刺final inspection终检to connect material接料to reverse material 翻料wet station沾湿台Tiana天那水cleaning cloth抹布to load material上料to unload material卸料to return material/stock to退料scraped |\\'skr?pid|报废scrape ..v.刮;削deficient purchase来料不良manufacture procedure制程deficient manufacturing procedure制程不良oxidation |\\' ksi\\'dei?n|氧化scratch刮伤dents压痕defective upsiding down抽芽不良defective to staking铆合不良embedded lump镶块feeding is not in place送料不到位stamping-missing漏冲production capacity生产力education and training教育与训练proposal improvement提案改善spare parts=buffer备件forklift叉车trailer=long vehicle拖板车compound die合模die locker锁模器pressure plate=plate pinch压板bolt螺栓administration/general affairs dept总务部automatic screwdriver电动启子thickness gauge厚薄规gauge(or jig)治具power wire电源线buzzle蜂鸣器defective product label不良标签identifying sheet list标示单location地点present members出席人员subject主题conclusion结论decision items决议事项responsible department负责单位pre-fixed finishing date预定完成日approved by / checked by / prepared by核准/审核/承办PCE assembly production schedule sheet PCE组装厂生产排配表model机锺work order工令revision版次remark备注production control confirmation生产确认checked by初审approved by核准department部门stock age analysis sheet 库存货龄分析表on-hand inventory现有库存available material良品可使用obsolete material良品已呆滞to be inspected or reworked 待验或重工total合计cause description缘故说明part number/ P/N 料号type形状item/group/class类别quality品质prepared by制表notes说明year-end physical inventory difference analysis sheet 年终盘点差异分析表physical inventory盘点数量physical count quantity帐面数量difference quantity差异量cause analysis缘故分析raw materials原料materials物料finished product成品semi-finished product半成品packing materials包材good product/accepted goods/ accepted parts/good parts良品defective product/non-good parts不良品disposed goods处理品warehouse/hub仓库on way location在途仓oversea location海外仓spare parts physical inventory list备品盘点清单spare molds location模具备品仓skid/pallet栈板tox machine自铆机wire EDM线割EDM放电机coil stock卷料sheet stock片料tolerance工差score=groove压线cam block滑块pilot导正筒trim剪外边pierce剪内边drag form压锻差pocket for the punch head挂钩槽slug hole废料孔feature die公母模expansion dwg展开图radius半径shim(wedge)楔子torch-flame cut火焰切割set screw止付螺丝form block折刀stop pin定位销round pierce punch=die button圆冲子shape punch=die insert异形子stock locater block定位块under cut=scrap chopper清角active plate活动板baffle plate挡块cover plate盖板male die公模female die母模groove punch压线冲子air-cushion eject-rod气垫顶杆spring-box eject-plate弹簧箱顶板bushing block衬套insert 入块club car高尔夫球车capability能力parameter参数factor系数phosphate皮膜化成viscosity涂料粘度alkalidipping脱脂main manifold主集流脉bezel斜视规blanking穿落模dejecting顶固模demagnetization去磁;消磁high-speed transmission高速传递heat dissipation热传rack上料degrease脱脂rinse水洗alkaline etch龄咬desmut剥黑膜D.I. rinse纯水次Chromate铬酸处理Anodize阳性处理seal封孔revision版次part number/P/N料号good products良品scraped products报放心品defective products不良品finished products成品disposed products处理品barcode条码flow chart流程表单assembly组装stamping冲压molding成型spare parts=buffer备品coordinate座标dismantle the die折模auxiliary fuction辅助功能poly-line多义线heater band 加热片thermocouple热电偶sand blasting喷沙grit 砂砾derusting machine除锈机degate打浇口dryer烘干机induction感应induction light感应光response=reaction=interaction感应ram连杆edge finder巡边器concave凸convex凹short射料不足nick缺口speck瑕??shine亮班splay 银纹gas mark焦痕delamination起鳞cold slug冷块blush 导色gouge沟槽;凿槽satin texture段面咬花witness line证示线patent专利grit沙砾granule=peuet=grain细粒grit maker抽粒机cushion缓冲magnalium镁铝合金magnesium镁金metal plate钣金lathe车mill锉plane刨grind磨drill铝boring镗blinster气泡fillet镶;嵌边through-hole form通孔形式voller pin formality滚针形式cam driver铡楔shank摸柄crank shaft曲柄轴augular offset角度偏差velocity速度production tempo生产进度现状torque扭矩spline=the multiple keys花键quenching淬火tempering回火annealing退火carbonization碳化tungsten high speed steel钨高速的moly high speed steel钼高速的organic solvent有机溶剂bracket小磁导liaison联络单volatile挥发性resistance电阻ion离子titrator滴定仪beacon警示灯coolant冷却液crusher破裂机阿基米德蜗杆Archimedes worm安全系数safety factor; factor of safety安全载荷safe load凹面、凹度concavity扳手wrench板簧flat leaf spring半圆键woodruff key变形deformation摆杆oscillating bar摆动从动件oscillating follower摆动从动件凸轮机构cam with oscillating follower 摆动导杆机构oscillating guide-bar mechanism摆线齿轮cycloidal gear摆线齿形cycloidal tooth profile摆线运动规律cycloidal motion摆线针轮cycloidal-pin wheel包角angle of contact保持架cage背对背安装back-to-back arrangement背锥back cone ;normal cone背锥角back angle背锥距back cone distance比例尺scale比热容specific heat capacity闭式链closed kinematic chain闭链机构closed chain mechanism臂部arm变频器frequency converters变频调速frequency control of motor speed变速speed change变速齿轮change gear change wheel变位齿轮modified gear变位系数modification coefficient标准齿轮standard gear标准直齿轮standard spur gear表面质量系数superficial mass factor表面传热系数surface coefficient of heat transfer 表面粗糙度surface roughness并联式组合combination in parallel并联机构parallel mechanism并联组合机构parallel combined mechanism并行工程concurrent engineering并行设计concurred design, CD不平稳相位phase angle of unbalance不平稳imbalance (or unbalance)不平稳量amount of unbalance 不完全齿轮机构intermittent gearing波发生器wave generator波数number of waves补偿compensation参数化设计parameterization design, PD残余应力residual stress操纵及操纵装置operation control device槽轮Geneva wheel槽轮机构Geneva mechanism ;Maltese cross槽数Geneva numerate槽凸轮groove cam侧隙backlash差动轮系differential gear train差动螺旋机构differential screw mechanism差速器differential常用机构conventional mechanism; mechanism in common use车床lathe承载量系数bearing capacity factor承载能力bearing capacity成对安装paired mounting尺寸系列dimension series齿槽tooth space齿槽宽spacewidth齿侧间隙backlash齿顶高addendum齿顶圆addendum circle齿根高dedendum齿根圆dedendum circle齿厚tooth thickness齿距circular pitch齿宽face width齿廓tooth profile齿廓曲线tooth curve齿轮gear齿轮变速箱speed-changing gear boxes齿轮齿条机构pinion and rack齿轮插刀pinion cutter; pinion-shaped shaper cutter 齿轮滚刀hob ,hobbing cutter齿轮机构gear齿轮轮坯blank齿轮传动系pinion unit齿轮联轴器gear coupling齿条传动rack gear齿数tooth number齿数比gear ratio齿条rack齿条插刀rack cutter; rack-shaped shaper cutter齿形链、无声链silent chain齿形系数form factor齿式棘轮机构tooth ratchet mechanism插齿机gear shaper重合点coincident points重合度contact ratio冲床punch传动比transmission ratio, speed ratio传动装置gearing; transmission gear传动系统driven system传动角transmission angle传动轴transmission shaft串联式组合combination in series串联式组合机构series combined mechanism串级调速cascade speed control创新innovation creation创新设计creation design垂直载荷、法向载荷normal load唇形橡胶密封lip rubber seal磁流体轴承magnetic fluid bearing从动带轮driven pulley从动件driven link, follower从动件平底宽度width of flat-face从动件停歇follower dwell从动件运动规律follower motion从动轮driven gear粗线bold line粗牙螺纹coarse thread大齿轮gear wheel打包机packer打滑slipping带传动belt driving带轮belt pulley带式制动器band brake单列轴承single row bearing单向推力轴承single-direction thrust bearing单万向联轴节single universal joint单位矢量unit vector当量齿轮equivalent spur gear; virtual gear当量齿数equivalent teeth number; virtual number of teeth当量摩擦系数equivalent coefficient of friction当量载荷equivalent load刀具cutter 导数derivative倒角chamfer导热性conduction of heat导程lead导程角lead angle等加等减速运动规律parabolic motion; constant acceleration and deceleration motion等速运动规律uniform motion; constant velocity motion等径凸轮conjugate yoke radial cam等宽凸轮constant-breadth cam等效构件equivalent link等效力equivalent force等效力矩equivalent moment of force等效量equivalent等效质量equivalent mass等效转动惯量equivalent moment of inertia等效动力学模型dynamically equivalent model底座chassis低副lower pair点划线chain dotted line(疲劳)点蚀pitting垫圈gasket垫片密封gasket seal碟形弹簧belleville spring顶隙bottom clearance定轴轮系ordinary gear train; gear train with fixed axes动力学dynamics动密封kinematical seal动能dynamic energy动力粘度dynamic viscosity动力润滑dynamic lubrication动平稳dynamic balance动平稳机dynamic balancing machine动态特性dynamic characteristics动态分析设计dynamic analysis design动压力dynamic reaction动载荷dynamic load端面transverse plane端面参数transverse parameters端面齿距transverse circular pitch端面齿廓transverse tooth profile端面重合度transverse contact ratio端面模数transverse module端面压力角transverse pressure angle锻造forge对称循环应力symmetry circulating stress对心滚子从动件radial (or in-line ) roller follower对心直动从动件radial (or in-line ) translating follower对心移动从动件radial reciprocating follower对心曲柄滑块机构in-line slider-crank (or crank-slider) mechanism多列轴承multi-row bearing多楔带poly V-belt多项式运动规律polynomial motion多质量转子rotor with several masses惰轮idle gear额定寿命rating life额定载荷load ratingII 级杆组dyad发生线generating line发生面generating plane法面normal plane法面参数normal parameters法面齿距normal circular pitch法面模数normal module法面压力角normal pressure angle法向齿距normal pitch法向齿廓normal tooth profile法向直廓蜗杆straight sided normal worm法向力normal force反馈式组合feedback combining反向运动学inverse ( or backward) kinematics反转法kinematic inversion反正切Arctan范成法generating cutting仿形法form cutting方案设计、概念设计concept design, CD防振装置shockproof device飞轮flywheel飞轮矩moment of flywheel非标准齿轮nonstandard gear非接触式密封non-contact seal非周期性速度波动aperiodic speed fluctuation非圆齿轮non-circular gear粉末合金powder metallurgy分度线reference line; standard pitch line分度圆reference circle; standard (cutting) pitch circle分度圆柱导程角lead angle at reference cylinder 分度圆柱螺旋角helix angle at reference cylinder 分母denominator分子numerator分度圆锥reference cone; standard pitch cone分析法analytical method封闭差动轮系planetary differential复合铰链compound hinge复合式组合compound combining复合轮系compound (or combined) gear train复合平带compound flat belt复合应力combined stress复式螺旋机构Compound screw mechanism复杂机构complex mechanism杆组Assur group干涉interference刚度系数stiffness coefficient刚轮rigid circular spline钢丝软轴wire soft shaft刚体导引机构body guidance mechanism刚性冲击rigid impulse (shock)刚性转子rigid rotor刚性轴承rigid bearing刚性联轴器rigid coupling高度系列height series高速带high speed belt高副higher pair格拉晓夫定理Grashoff`s law根切undercutting公称直径nominal diameter高度系列height series功work工况系数application factor工艺设计technological design工作循环图working cycle diagram工作机构operation mechanism工作载荷external loads工作空间working space工作应力working stress工作阻力effective resistance工作阻力矩effective resistance moment公法线common normal line公共约束general constraint公制齿轮metric gears功率power功能分析设计function analyses design共轭齿廓conjugate profiles共轭凸轮conjugate cam构件link鼓风机blower固定构件fixed link; frame固体润滑剂solid lubricant关节型操作器jointed manipulator惯性力inertia force惯性力矩moment of inertia ,shaking moment惯性力平稳balance of shaking force惯性力完全平稳full balance of shaking force惯性力部分平稳partial balance of shaking force 惯性主矩resultant moment of inertia惯性主失resultant vector of inertia冠轮crown gear广义机构generation mechanism广义坐标generalized coordinate轨迹生成path generation轨迹发生器path generator滚刀hob滚道raceway滚动体rolling element滚动轴承rolling bearing滚动轴承代号rolling bearing identification code 滚针needle roller滚针轴承needle roller bearing滚子roller滚子轴承roller bearing滚子半径radius of roller滚子从动件roller follower滚子链roller chain滚子链联轴器double roller chain coupling滚珠丝杆ball screw滚柱式单向超越离合器roller clutch过度切割undercutting函数发生器function generator函数生成function generation含油轴承oil bearing耗油量oil consumption耗油量系数oil consumption factor赫兹公式H. Hertz equation合成弯矩resultant bending moment合力resultant force合力矩resultant moment of force黑箱black box横坐标abscissa互换性齿轮interchangeable gears 花键spline滑键、导键feather key滑动轴承sliding bearing滑动率sliding ratio滑块slider环面蜗杆toroid helicoids worm环形弹簧annular spring缓冲装置shocks; shock-absorber灰铸铁grey cast iron回程return回转体平稳balance of rotors混合轮系compound gear train积分integrate机电一体化系统设计mechanical-electrical integration system design机构mechanism机构分析analysis of mechanism机构平稳balance of mechanism机构学mechanism机构运动设计kinematic design of mechanism机构运动简图kinematic sketch of mechanism机构综合synthesis of mechanism机构组成constitution of mechanism机架frame, fixed link机架变换kinematic inversion机器machine机器人robot机器人操作器manipulator机器人学robotics技术过程technique process技术经济评判technical and economic evaluation技术系统technique system机械machinery机械创新设计mechanical creation design, MCD机械系统设计mechanical system design, MSD机械动力分析dynamic analysis of machinery机械动力设计dynamic design of machinery机械动力学dynamics of machinery机械的现代设计modern machine design机械系统mechanical system机械利益mechanical advantage机械平稳balance of machinery机械手manipulator机械设计machine design; mechanical design机械特性mechanical behavior机械调速mechanical speed governors机械效率mechanical efficiency机械原理theory of machines and mechanisms机械运转不平均系数coefficient of speed fluctuation机械无级变速mechanical stepless speed changes基础机构fundamental mechanism差不多额定寿命basic rating life基于实例设计case-based design,CBD基圆base circle基圆半径radius of base circle基圆齿距base pitch基圆压力角pressure angle of base circle基圆柱base cylinder基圆锥base cone急回机构quick-return mechanism急回特性quick-return characteristics急回系数advance-to return-time ratio急回运动quick-return motion棘轮ratchet棘轮机构ratchet mechanism棘爪pawl极限位置extreme (or limiting) position极位夹角crank angle between extreme (or limiting) positions运算机辅助设计computer aided design, CAD运算机辅助制造computer aided manufacturing, CAM运算机集成制造系统computer integrated manufacturing system, CIMS运算力矩factored moment; calculation moment运算弯矩calculated bending moment加权系数weighting efficient加速度acceleration加速度分析acceleration analysis加速度曲线acceleration diagram尖点pointing; cusp尖底从动件knife-edge follower间隙backlash间歇运动机构intermittent motion mechanism减速比reduction ratio减速齿轮、减速装置reduction gear减速器speed reducer减摩性anti-friction quality渐开螺旋面involute helicoid渐开线involute渐开线齿廓involute profile 渐开线齿轮involute gear渐开线发生线generating line of involute渐开线方程involute equation渐开线函数involute function渐开线蜗杆involute worm渐开线压力角pressure angle of involute渐开线花键involute spline简谐运动simple harmonic motion键key键槽keyway交变应力repeated stress交变载荷repeated fluctuating load交叉带传动cross-belt drive交错轴斜齿轮crossed helical gears胶合scoring角加速度angular acceleration角速度angular velocity角速比angular velocity ratio角接触球轴承angular contact ball bearing角接触推力轴承angular contact thrust bearing角接触向心轴承angular contact radial bearing角接触轴承angular contact bearing铰链、枢纽hinge校正平面correcting plane接触应力contact stress接触式密封contact seal阶梯轴multi-diameter shaft结构structure结构设计structural design截面section节点pitch point节距circular pitch; pitch of teeth节线pitch line节圆pitch circle节圆齿厚thickness on pitch circle节圆直径pitch diameter节圆锥pitch cone节圆锥角pitch cone angle解析设计analytical design紧边tight-side紧固件fastener径节diametral pitch径向radial direction径向当量动载荷dynamic equivalent radial load径向当量静载荷static equivalent radial load径向差不多额定动载荷basic dynamic radial loadrating径向差不多额定静载荷basic static radial load tating径向接触轴承radial contact bearing径向平面radial plane径向游隙radial internal clearance径向载荷radial load径向载荷系数radial load factor径向间隙clearance静力static force静平稳static balance静载荷static load静密封static seal局部自由度passive degree of freedom矩阵matrix矩形螺纹square threaded form锯齿形螺纹buttress thread form矩形牙嵌式离合器square-jaw positive-contact clutch绝对尺寸系数absolute dimensional factor绝对运动absolute motion绝对速度absolute velocity均衡装置load balancing mechanism抗压强度compression strength开口传动open-belt drive开式链open kinematic chain开链机构open chain mechanism可靠度degree of reliability可靠性reliability可靠性设计reliability design, RD空气弹簧air spring空间机构spatial mechanism空间连杆机构spatial linkage空间凸轮机构spatial cam空间运动副spatial kinematic pair空间运动链spatial kinematic chain空转idle宽度系列width series框图block diagram雷诺方程Reynolds‘s equation离心力centrifugal force离心应力centrifugal stress离合器clutch离心密封centrifugal seal理论廓线pitch curve理论啮合线theoretical line of action 隶属度membership力force力多边形force polygon力封闭型凸轮机构force-drive (or force-closed) cam mechanism力矩moment力平稳equilibrium力偶couple力偶矩moment of couple连杆connecting rod, coupler连杆机构linkage连杆曲线coupler-curve连心线line of centers链chain链传动装置chain gearing链轮sprocket sprocket-wheel sprocket gear chain wheel联组V 带tight-up V belt联轴器coupling shaft coupling两维凸轮two-dimensional cam临界转速critical speed六杆机构six-bar linkage龙门刨床double Haas planer轮坯blank轮系gear train螺杆screw螺距thread pitch螺母screw nut螺旋锥齿轮helical bevel gear螺钉screws螺栓bolts螺纹导程lead螺纹效率screw efficiency螺旋传动power screw螺旋密封spiral seal螺纹thread (of a screw)螺旋副helical pair螺旋机构screw mechanism螺旋角helix angle螺旋线helix ,helical line绿色设计green design design for environment马耳他机构Geneva wheel Geneva gear马耳他十字Maltese cross脉动无级变速pulsating stepless speed changes脉动循环应力fluctuating circulating stress脉动载荷fluctuating load铆钉rivet迷宫密封labyrinth seal密封seal密封带seal belt密封胶seal gum密封元件potted component密封装置sealing arrangement面对面安装face-to-face arrangement面向产品生命周期设计design for product`s life cycle, DPLC名义应力、公称应力nominal stress模块化设计modular design, MD模块式传动系统modular system模幅箱morphology box模糊集fuzzy set模糊评判fuzzy evaluation模数module摩擦friction摩擦角friction angle摩擦力friction force摩擦学设计tribology design, TD摩擦阻力frictional resistance摩擦力矩friction moment摩擦系数coefficient of friction摩擦圆friction circle磨损abrasion wear; scratching末端执行器end-effector目标函数objective function耐腐蚀性corrosion resistance耐磨性wear resistance挠性机构mechanism with flexible elements挠性转子flexible rotor内齿轮internal gear内齿圈ring gear内力internal force内圈inner ring能量energy能量指示图viscosity逆时针counterclockwise (or anticlockwise)啮出engaging-out啮合engagement, mesh, gearing啮合点contact points啮合角working pressure angle啮合线line of action啮合线长度length of line of action啮入engaging-in 牛头刨床shaper凝固点freezing point; solidifying point扭转应力torsion stress扭矩moment of torque扭簧helical torsion spring诺模图NomogramO 形密封圈密封O ring seal盘形凸轮disk cam盘形转子disk-like rotor抛物线运动parabolic motion疲劳极限fatigue limit疲劳强度fatigue strength偏置式offset偏( 心) 距offset distance偏心率eccentricity ratio偏心质量eccentric mass偏距圆offset circle偏心盘eccentric偏置滚子从动件offset roller follower偏置尖底从动件offset knife-edge follower偏置曲柄滑块机构offset slider-crank mechanism 拼接matching评判与决策evaluation and decision频率frequency平带flat belt平带传动flat belt driving平底从动件flat-face follower平底宽度face width平分线bisector平均应力average stress平均中径mean screw diameter平均速度average velocity平稳balance平稳机balancing machine平稳品质balancing quality平稳平面correcting plane平稳质量balancing mass平稳重counterweight平稳转速balancing speed平面副planar pair, flat pair平面机构planar mechanism平面运动副planar kinematic pair平面连杆机构planar linkage平面凸轮planar cam平面凸轮机构planar cam mechanism平面轴斜齿轮parallel helical gears一般平键parallel key其他常用机构other mechanism in common use起动时期starting period启动力矩starting torque气动机构pneumatic mechanism奇特位置singular position起始啮合点initial contact , beginning of contact气体轴承gas bearing千斤顶jack嵌入键sunk key强迫振动forced vibration切齿深度depth of cut曲柄crank曲柄存在条件Grashoff`s law曲柄导杆机构crank shaper (guide-bar) mechanism 曲柄滑块机构slider-crank (or crank-slider) mechanism曲柄摇杆机构crank-rocker mechanism曲齿锥齿轮spiral bevel gear曲率curvature曲率半径radius of curvature曲面从动件curved-shoe follower曲线拼接curve matching曲线运动curvilinear motion曲轴crank shaft驱动力driving force驱动力矩driving moment (torque)全齿高whole depth权重集weight sets球ball球面滚子convex roller球轴承ball bearing球面副spheric pair球面渐开线spherical involute球面运动spherical motion球销副sphere-pin pair球坐标操作器polar coordinate manipulator燃点spontaneous ignition热平稳heat balance; thermal equilibrium人字齿轮herringbone gear冗余自由度redundant degree of freedom柔轮flexspline柔性冲击flexible impulse; soft shock柔性制造系统flexible manufacturing system; FMS 柔性自动化flexible automation润滑油膜lubricant film 润滑装置lubrication device润滑lubrication润滑剂lubricant三角形花键serration spline三角形螺纹V thread screw三维凸轮three-dimensional cam三心定理Kennedy`s theorem砂轮越程槽grinding wheel groove砂漏hour-glass少齿差行星传动planetary drive with small teeth difference设计方法学design methodology设计变量design variable设计约束design constraints深沟球轴承deep groove ball bearing生产阻力productive resistance升程rise升距lift实际廓线cam profile十字滑块联轴器double slider coupling; Oldham‘s coupling矢量vector输出功output work输出构件output link输出机构output mechanism输出力矩output torque输出轴output shaft输入构件input link数学模型mathematic model实际啮合线actual line of action双滑块机构double-slider mechanism, ellipsograph 双曲柄机构double crank mechanism双曲面齿轮hyperboloid gear双头螺柱studs双万向联轴节constant-velocity (or double) universal joint双摇杆机构double rocker mechanism双转块机构Oldham coupling双列轴承double row bearing双向推力轴承double-direction thrust bearing松边slack-side顺时针clockwise瞬心instantaneous center死点dead point四杆机构four-bar linkage速度velocity速度不平均( 波动) 系数coefficient of speed fluctuation速度波动speed fluctuation速度曲线velocity diagram速度瞬心instantaneous center of velocity塔轮step pulley踏板pedal台钳、虎钳vice太阳轮sun gear弹性滑动elasticity sliding motion弹性联轴器elastic coupling flexible coupling弹性套柱销联轴器rubber-cushioned sleeve bearing coupling套筒sleeve梯形螺纹acme thread form专门运动链special kinematic chain特性characteristics替代机构equivalent mechanism调剂modulation, regulation调心滚子轴承self-aligning roller bearing调心球轴承self-aligning ball bearing调心轴承self-aligning bearing调速speed governing调速电动机adjustable speed motors调速系统speed control system调压调速variable voltage control调速器regulator, governor铁磁流体密封ferrofluid seal停车时期stopping phase停歇dwell同步带synchronous belt同步带传动synchronous belt drive凸的,凸面体convex凸轮cam凸轮倒置机构inverse cam mechanism凸轮机构cam , cam mechanism凸轮廓线cam profile凸轮廓线绘制layout of cam profile凸轮理论廓线pitch curve凸缘联轴器flange coupling图册、图谱atlas图解法graphical method推程rise推力球轴承thrust ball bearing推力轴承thrust bearing退刀槽tool withdrawal groove 退火anneal陀螺仪gyroscopeV 带V belt外力external force外圈outer ring外形尺寸boundary dimension万向联轴器Hooks coupling universal coupling外齿轮external gear弯曲应力beading stress弯矩bending moment腕部wrist往复移动reciprocating motion往复式密封reciprocating seal网上设计on-net design, OND微动螺旋机构differential screw mechanism位移displacement位移曲线displacement diagram位姿pose , position and orientation稳固运转时期steady motion period稳健设计robust design蜗杆worm蜗杆传动机构worm gearing蜗杆头数number of threads蜗杆直径系数diametral quotient蜗杆蜗轮机构worm and worm gear蜗杆形凸轮步进机构worm cam interval mechanism 蜗杆旋向hands of worm蜗轮worm gear涡圈形盘簧power spring无级变速装置stepless speed changes devices无穷大infinite系杆crank arm, planet carrier现场平稳field balancing向心轴承radial bearing向心力centrifugal force相对速度relative velocity相对运动relative motion相对间隙relative gap象限quadrant橡皮泥plasticine细牙螺纹fine threads销pin消耗consumption小齿轮pinion小径minor diameter橡胶弹簧balata spring。
机械制造中英双语对照

车床 螺栓 螺母
angle bar angle bar channel bar channel bar H-beam spot facing machining drill chamfer lathe bolt nut
垫圈
washer
垫圈 六角螺栓 六角螺母
盘头螺钉 埋头螺钉 木螺钉
washer hexagon head bolt hexagon nut pan head screw countersunk flat head screw tapping screw
挤压加工 落料 穿孔 拉深
压筋 冲缘加工 压印加工 冲孔 薄板
胶着
配合
fitting
高强度钢
质量 比重
mass relative density
弹性变形回复 粘住
金属
metal
复合材料
腐蚀 零件
corrosion part
延展性 废料
收缩
shrink
冲头
膨胀 密封 缺陷 合金
铸铁
软钢 黄铜 青铜 英寸
cross-joint
union
加速度 正火 淬火 回火 退火 应变 焊接 表面粗糙度 铝 铜 钢管 键 公差 间隙配合 过渡配合 过盈配合 法兰 应力集中
轮毂
热压配合 磨床 拉伸强度 屈服点
acceleration normalizing quenching tempering annealing strain weld surface roughness aluminium copper steel tube key tolerance clearance fit transition fit interference fit flange stress concentration
机械及模具中英文对照(完整版)

机械及模具中英文对照(完整版)机械专业英语词汇陶瓷ceramics合成纤维synthetic fibre电化学腐蚀electrochemical corrosion车架automotive chassis悬架suspension转向器redirector变速器speed changer板料冲压sheet metal parts孔加工spot facing machining车间workshop工程技术人员engineer气动夹紧pneuma lock数学模型mathematical model 画法几何descriptive geometry 机械制图Mechanical drawing投影projection视图view剖视图profile chart标准件standard component零件图part drawing装配图assembly drawing尺寸标注size marking技术要求technical requirements刚度rigidity内力internal force位移displacement截面section疲劳极限fatigue limit断裂fracture塑性变形plastic distortion脆性材料brittleness material刚度准则rigidity criterion垫圈washer垫片spacer直齿圆柱齿轮straight toothed spur gear斜齿圆柱齿轮helical-spur gear直齿锥齿轮straight bevel gear运动简图kinematic sketch齿轮齿条pinion and rack蜗杆蜗轮worm and worm gear虚约束passive constraint曲柄crank摇杆rocker凸轮cams共轭曲线conjugate curve范成法generation method定义域definitional domain值域range导数\\微分differential coefficient 求导derivation定积分definite integral不定积分indefinite integral曲率curvature偏微分partial differential毛坯rough游标卡尺slide caliper千分尺micrometer calipers攻丝tap二阶行列式second order determinant逆矩阵inverse matrix线性方程组linear equations概率probability随机变量random variable排列组合permutation and combination气体状态方程equation of state of gas动能kinetic energy势能potential energy机械能守恒conservation of mechanical energy动量momentum桁架truss轴线axes余子式cofactor逻辑电路logic circuit触发器flip-flop脉冲波形pulse shape数模digital analogy液压传动机构fluid drive mechanism 机械零件mechanical parts淬火冷却quench淬火hardening回火tempering调质hardening and tempering 磨粒abrasive grain结合剂bonding agent砂轮grinding wheel后角clearance angle龙门刨削planing主轴spindle主轴箱headstock卡盘chuck加工中心machining center车刀lathe tool车床lathe钻削镗削bore车削turning磨床grinder基准benchmark钳工locksmith锻forge压模stamping焊weld拉床broaching machine拉孔broaching装配assembling铸造found流体动力学fluid dynamics流体力学fluid mechanics加工machining液压hydraulic pressure切线tangent机电一体化mechanotronics mechanical-electrical integration 气压air pressure pneumatic pressure稳定性stability介质medium液压驱动泵fluid clutch液压泵hydraulic pump阀门valve失效invalidation强度intensity载荷load应力stress安全系数safty factor可靠性reliability螺纹thread螺旋helix键spline销pin滚动轴承rolling bearing滑动轴承sliding bearing弹簧spring制动器arrester brake十字结联轴节crosshead联轴器coupling链chain皮带strap精加工finish machining粗加工rough machining变速箱体gearbox casing腐蚀rust氧化oxidation磨损wear耐用度durability随机信号random signal离散信号discrete signal超声传感器ultrasonic sensor集成电路integrate circuit挡板orifice plate残余应力residual stress套筒sleeve扭力torsion冷加工cold machining电动机electromotor汽缸cylinder过盈配合interference fit热加工hotwork摄像头CCD camera倒角rounding chamfer优化设计optimal design工业造型设计industrial moulding design有限元finite element滚齿hobbing插齿gear shaping伺服电机actuating motor铣床milling machine钻床drill machine镗床boring machine步进电机stepper motor丝杠screw rod导轨lead rail组件subassembly可编程序逻辑控制器Programmable Logic Controller PLC电火花加工electric spark machining 电火花线切割加工electrical discharge wire - cutting相图phase diagram热处理heat treatment固态相变solid state phase changes有色金属nonferrous metal陶瓷ceramics合成纤维synthetic fibre电化学腐蚀electrochemical corrosion车架automotive chassis悬架suspension转向器redirector变速器speed changer板料冲压sheet metal parts孔加工spot facing machining车间workshop工程技术人员engineer气动夹紧pneuma lock数学模型mathematical model画法几何descriptive geometry 机械制图Mechanical drawing投影projection视图view剖视图profile chart标准件standard component零件图part drawing装配图assembly drawing尺寸标注size marking技术要求technical requirements 刚度rigidity内力internal force位移displacement截面section疲劳极限fatigue limit断裂fracture塑性变形plastic distortion脆性材料brittleness material刚度准则rigidity criterion垫圈washer垫片spacer直齿圆柱齿轮straight toothed spur gear斜齿圆柱齿轮helical-spur gear直齿锥齿轮straight bevel gear运动简图kinematic sketch齿轮齿条pinion and rack蜗杆蜗轮worm and worm gear虚约束passive constraint曲柄crank摇杆racker凸轮cams共轭曲线conjugate curve范成法generation method定义域definitional domain值域range导数\\微分differential coefficient 求导derivation定积分definite integral不定积分indefinite integral曲率curvature偏微分partial differential毛坯rough游标卡尺slide caliper千分尺micrometer calipers攻丝tap二阶行列式second order determinant逆矩阵inverse matrix线性方程组linear equations概率probability随机变量random variable排列组合permutation and combination气体状态方程equation of state of gas动能kinetic energy势能potential energy机械能守恒conservation of mechanical energy动量momentum桁架truss轴线axes余子式cofactor逻辑电路logic circuit触发器flip-flop脉冲波形pulse shape数模digital analogy液压传动机构fluid drive mechanism 机械零件mechanical parts淬火冷却quench淬火hardening回火tempering调质hardening and tempering磨粒abrasive grain结合剂bonding agent砂轮grinding wheelAssembly line 组装线Layout 布置图Conveyer 流水线物料板Rivet table 拉钉机Rivet gun 拉钉枪Screw driver 起子Pneumatic screw driver 气动起子worktable 工作桌OOBA 开箱检查fit together 组装在一起fasten 锁紧(螺丝)fixture 夹具(治具)pallet 栈板barcode 条码barcode scanner 条码扫描器fuse together 熔合fuse machine热熔机repair修理operator作业员QC品管supervisor 课长ME 制造工程师MT 制造生技cosmetic inspect 外观检查inner parts inspect 内部检查thumb screw 大头螺丝lbs. inch 镑、英寸EMI gasket 导电条front plate 前板rear plate 后板chassis 基座bezel panel 面板power button 电源按键reset button 重置键Hi-pot test of SPS 高源高压测试Voltage switch of SPS 电源电压接拉键sheet metal parts 冲件plastic parts 塑胶件SOP 制造作业程序material check list 物料检查表work cell 工作间trolley 台车carton 纸箱sub-line 支线left fork 叉车personnel resource department 人力资源部production department生产部门planning department企划部QC Section品管科stamping factory冲压厂painting factory烤漆厂molding factory成型厂common equipment常用设备uncoiler and straightener整平机punching machine 冲床robot机械手hydraulic machine油压机lathe车床planer |plein|刨床miller铣床grinder磨床linear cutting线切割electrical sparkle电火花welder电焊机staker=reviting machine铆合机position职务president董事长general manager总经理special assistant manager特助factory director厂长department director部长deputy manager | =vice manager副理section supervisor课长deputy section supervisor =vice section superisor副课长group leader/supervisor组长line supervisor线长assistant manager助理to move, to carry, to handle搬运be put in storage入库pack packing包装to apply oil擦油to file burr 锉毛刺final inspection终检to connect material接料to reverse material 翻料wet station沾湿台Tiana天那水cleaning cloth抹布to load material上料to unload material卸料to return material/stock to退料scraped |\\'skr?pid|报废scrape ..v.刮;削deficient purchase来料不良manufacture procedure制程deficient manufacturing procedure制程不良oxidation |\\' ksi\\'dei?n|氧化scratch刮伤dents压痕defective upsiding down抽芽不良defective to staking铆合不良embedded lump镶块feeding is not in place送料不到位stamping-missing漏冲production capacity生产力education and training教育与训练proposal improvement提案改善spare parts=buffer备件forklift叉车trailer=long vehicle拖板车compound die合模die locker锁模器pressure plate=plate pinch压板bolt螺栓administration/general affairs dept 总务部automatic screwdriver电动启子thickness gauge厚薄规gauge(or jig)治具power wire电源线buzzle蜂鸣器defective product label不良标签identifying sheet list标示单location地点present members出席人员subject主题conclusion结论decision items决议事项responsible department负责单位pre-fixed finishing date预定完成日approved by / checked by / prepared by核准/审核/承办PCE assembly production schedule sheet PCE组装厂生产排配表model机锺work order工令revision版次remark备注production control confirmation生产确认checked by初审approved by核准department部门stock age analysis sheet 库存货龄分析表on-hand inventory现有库存available material良品可使用obsolete material良品已呆滞to be inspected or reworked 待验或重工total合计cause description原因说明part number/ P/N 料号type形态item/group/class类别quality品质prepared by制表notes说明year-end physical inventory difference analysis sheet 年终盘点差异分析表physical inventory盘点数量physical count quantity帐面数量difference quantity差异量cause analysis原因分析raw materials原料materials物料finished product成品semi-finished product半成品packing materials包材good product/accepted goods/ accepted parts/good parts良品defective product/non-good parts不良品disposed goods处理品warehouse/hub仓库on way location在途仓oversea location海外仓spare parts physical inventory list备品盘点清单spare molds location模具备品仓skid/pallet栈板tox machine自铆机wire EDM线割EDM放电机coil stock卷料sheet stock片料tolerance工差score=groove压线cam block滑块pilot导正筒trim剪外边pierce剪内边drag form压锻差pocket for the punch head挂钩槽slug hole废料孔feature die公母模expansion dwg展开图radius半径shim(wedge)楔子torch-flame cut火焰切割set screw止付螺丝form block折刀stop pin定位销round pierce punch=die button圆冲子shape punch=die insert异形子stock locater block定位块under cut=scrap chopper清角active plate活动板baffle plate挡块cover plate盖板male die公模female die母模groove punch压线冲子air-cushion eject-rod气垫顶杆spring-box eject-plate弹簧箱顶板bushing block衬套insert 入块club car高尔夫球车capability能力parameter参数factor系数phosphate皮膜化成viscosity涂料粘度alkalidipping脱脂main manifold主集流脉bezel斜视规blanking穿落模dejecting顶固模demagnetization去磁;消磁high-speed transmission高速传递heat dissipation热传rack上料degrease脱脂rinse水洗alkaline etch龄咬desmut剥黑膜D.I. rinse纯水次Chromate铬酸处理Anodize阳性处理seal封孔revision版次part number/P/N料号good products良品scraped products报放心品defective products不良品finished products成品disposed products处理品barcode条码flow chart流程表单assembly组装stamping冲压molding成型spare parts=buffer备品coordinate座标dismantle the die折模auxiliary fuction辅助功能poly-line多义线heater band 加热片thermocouple热电偶sand blasting喷沙grit 砂砾derusting machine除锈机degate打浇口dryer烘干机induction感应induction light感应光response=reaction=interaction感应ram连杆edge finder巡边器concave凸convex凹short射料不足nick缺口speck瑕??shine亮班splay 银纹gas mark焦痕delamination起鳞cold slug冷块blush 导色gouge沟槽;凿槽satin texture段面咬花witness line证示线patent专利grit沙砾granule=peuet=grain细粒grit maker抽粒机cushion缓冲magnalium镁铝合金magnesium镁金metal plate钣金lathe车mill锉plane刨grind磨drill铝boring镗blinster气泡fillet镶;嵌边through-hole form通孔形式voller pin formality滚针形式cam driver铡楔shank摸柄crank shaft曲柄轴augular offset角度偏差velocity速度production tempo生产进度现状torque扭矩spline=the multiple keys花键quenching淬火tempering回火annealing退火carbonization碳化tungsten high speed steel钨高速的moly high speed steel钼高速的organic solvent有机溶剂bracket小磁导liaison联络单volatile挥发性resistance电阻ion离子titrator滴定仪beacon警示灯coolant冷却液crusher破碎机阿基米德蜗杆Archimedes worm安全系数safety factor; factor of safety 安全载荷safe load凹面、凹度concavity扳手wrench板簧flat leaf spring半圆键woodruff key变形deformation摆杆oscillating bar摆动从动件oscillating follower摆动从动件凸轮机构cam with oscillating follower摆动导杆机构oscillating guide-bar mechanism摆线齿轮cycloidal gear摆线齿形cycloidal tooth profile摆线运动规律cycloidal motion摆线针轮cycloidal-pin wheel包角angle of contact保持架cage背对背安装back-to-back arrangement 背锥back cone ;normal cone背锥角back angle背锥距back cone distance比例尺scale比热容specific heat capacity闭式链closed kinematic chain闭链机构closed chain mechanism臂部arm变频器frequency converters变频调速frequency control of motor speed变速speed change变速齿轮change gear change wheel变位齿轮modified gear变位系数modification coefficient标准齿轮standard gear标准直齿轮standard spur gear表面质量系数superficial mass factor表面传热系数surface coefficient of heat transfer表面粗糙度surface roughness并联式组合combination in parallel并联机构parallel mechanism并联组合机构parallel combined mechanism并行工程concurrent engineering并行设计concurred design, CD不平衡相位phase angle of unbalance不平衡imbalance (or unbalance)不平衡量amount of unbalance不完全齿轮机构intermittent gearing波发生器wave generator波数number of waves补偿compensation参数化设计parameterization design, PD残余应力residual stress操纵及控制装置operation control device槽轮Geneva wheel槽轮机构Geneva mechanism ;Maltese cross槽数Geneva numerate槽凸轮groove cam侧隙backlash差动轮系differential gear train差动螺旋机构differential screw mechanism差速器differential常用机构conventional mechanism; mechanism in common use车床lathe承载量系数bearing capacity factor承载能力bearing capacity成对安装paired mounting尺寸系列dimension series齿槽tooth space齿槽宽spacewidth齿侧间隙backlash齿顶高addendum齿顶圆addendum circle齿根高dedendum齿根圆dedendum circle齿厚tooth thickness齿距circular pitch齿宽face width齿廓tooth profile齿廓曲线tooth curve齿轮gear齿轮变速箱speed-changing gear boxes齿轮齿条机构pinion and rack齿轮插刀pinion cutter; pinion-shaped shaper cutter齿轮滚刀hob ,hobbing cutter齿轮机构gear齿轮轮坯blank齿轮传动系pinion unit齿轮联轴器gear coupling齿条传动rack gear齿数tooth number齿数比gear ratio齿条rack齿条插刀rack cutter; rack-shaped shaper cutter齿形链、无声链silent chain齿形系数form factor齿式棘轮机构tooth ratchet mechanism 插齿机gear shaper重合点coincident points重合度contact ratio冲床punch传动比transmission ratio, speed ratio 传动装置gearing; transmission gear传动系统driven system传动角transmission angle传动轴transmission shaft串联式组合combination in series串联式组合机构series combinedmechanism串级调速cascade speed control创新innovation creation创新设计creation design垂直载荷、法向载荷normal load唇形橡胶密封lip rubber seal磁流体轴承magnetic fluid bearing 从动带轮driven pulley从动件driven link, follower从动件平底宽度width of flat-face 从动件停歇follower dwell从动件运动规律follower motion从动轮driven gear粗线bold line粗牙螺纹coarse thread大齿轮gear wheel打包机packer打滑slipping带传动belt driving带轮belt pulley带式制动器band brake单列轴承single row bearing单向推力轴承single-direction thrust bearing单万向联轴节single universal joint单位矢量unit vector当量齿轮equivalent spur gear; virtual gear当量齿数equivalent teeth number; virtual number of teeth当量摩擦系数equivalent coefficient of friction当量载荷equivalent load刀具cutter导数derivative倒角chamfer导热性conduction of heat导程lead导程角lead angle等加等减速运动规律parabolic motion; constant acceleration and deceleration motion等速运动规律uniform motion; constant velocity motion等径凸轮conjugate yoke radial cam等宽凸轮constant-breadth cam等效构件equivalent link等效力equivalent force等效力矩equivalent moment of force 等效量equivalent等效质量equivalent mass等效转动惯量equivalent moment of inertia等效动力学模型dynamically equivalent model底座chassis低副lower pair点划线chain dotted line(疲劳)点蚀pitting垫圈gasket垫片密封gasket seal碟形弹簧belleville spring顶隙bottom clearance定轴轮系ordinary gear train; gear train with fixed axes动力学dynamics动密封kinematical seal动能dynamic energy动力粘度dynamic viscosity动力润滑dynamic lubrication动平衡dynamic balance动平衡机dynamic balancing machine 动态特性dynamic characteristics动态分析设计dynamic analysis design 动压力dynamic reaction动载荷dynamic load端面transverse plane端面参数transverse parameters端面齿距transverse circular pitch端面齿廓transverse tooth profile端面重合度transverse contact ratio端面模数transverse module端面压力角transverse pressure angle 锻造forge对称循环应力symmetry circulating stress对心滚子从动件radial (or in-line ) roller follower对心直动从动件radial (or in-line ) translating follower对心移动从动件radial reciprocating follower对心曲柄滑块机构in-line slider-crank (or crank-slider) mechanism多列轴承multi-row bearing多楔带poly V-belt多项式运动规律polynomial motion多质量转子rotor with several masses 惰轮idle gear额定寿命rating life额定载荷load ratingII 级杆组dyad发生线generating line发生面generating plane法面normal plane法面参数normal parameters法面齿距normal circular pitch法面模数normal module法面压力角normal pressure angle法向齿距normal pitch法向齿廓normal tooth profile法向直廓蜗杆straight sided normal worm法向力normal force反馈式组合feedback combining反向运动学inverse ( or backward) kinematics反转法kinematic inversion反正切Arctan范成法generating cutting仿形法form cutting方案设计、概念设计concept design, CD 防振装置shockproof device飞轮flywheel飞轮矩moment of flywheel非标准齿轮nonstandard gear非接触式密封non-contact seal非周期性速度波动aperiodic speed fluctuation非圆齿轮non-circular gear粉末合金powder metallurgy分度线reference line; standard pitchline分度圆reference circle; standard (cutting) pitch circle分度圆柱导程角lead angle at reference cylinder分度圆柱螺旋角helix angle at reference cylinder分母denominator分子numerator分度圆锥reference cone; standard pitch cone分析法analytical method封闭差动轮系planetary differential复合铰链compound hinge复合式组合compound combining复合轮系compound (or combined) gear train复合平带compound flat belt复合应力combined stress复式螺旋机构Compound screw mechanism复杂机构complex mechanism杆组Assur group干涉interference刚度系数stiffness coefficient刚轮rigid circular spline钢丝软轴wire soft shaft刚体导引机构body guidance mechanism刚性冲击rigid impulse (shock)刚性转子rigid rotor刚性轴承rigid bearing刚性联轴器rigid coupling高度系列height series高速带high speed belt高副higher pair格拉晓夫定理Grashoff`s law根切undercutting公称直径nominal diameter高度系列height series功work工况系数application factor工艺设计technological design工作循环图working cycle diagram工作机构operation mechanism工作载荷external loads工作空间working space工作应力working stress工作阻力effective resistance工作阻力矩effective resistance moment公法线common normal line公共约束general constraint公制齿轮metric gears功率power功能分析设计function analyses design 共轭齿廓conjugate profiles共轭凸轮conjugate cam构件link鼓风机blower固定构件fixed link; frame固体润滑剂solid lubricant关节型操作器jointed manipulator惯性力inertia force惯性力矩moment of inertia ,shaking moment惯性力平衡balance of shaking force惯性力完全平衡full balance of shaking force惯性力部分平衡partial balance of shaking force惯性主矩resultant moment of inertia 惯性主失resultant vector of inertia冠轮crown gear广义机构generation mechanism广义坐标generalized coordinate轨迹生成path generation轨迹发生器path generator滚刀hob滚道raceway滚动体rolling element滚动轴承rolling bearing滚动轴承代号rolling bearing identification code滚针needle roller滚针轴承needle roller bearing滚子roller滚子轴承roller bearing滚子半径radius of roller滚子从动件roller follower滚子链roller chain滚子链联轴器double roller chain coupling滚珠丝杆ball screw滚柱式单向超越离合器roller clutch过度切割undercutting函数发生器function generator函数生成function generation含油轴承oil bearing耗油量oil consumption耗油量系数oil consumption factor赫兹公式H. Hertz equation合成弯矩resultant bending moment合力resultant force合力矩resultant moment of force黑箱black box横坐标abscissa互换性齿轮interchangeable gears花键spline滑键、导键feather key滑动轴承sliding bearing滑动率sliding ratio滑块slider环面蜗杆toroid helicoids worm环形弹簧annular spring缓冲装置shocks; shock-absorber灰铸铁grey cast iron回程return回转体平衡balance of rotors混合轮系compound gear train积分integrate机电一体化系统设计mechanical-electrical integration system design机构mechanism机构分析analysis of mechanism机构平衡balance of mechanism机构学mechanism机构运动设计kinematic design of mechanism机构运动简图kinematic sketch of mechanism机构综合synthesis of mechanism机构组成constitution of mechanism机架frame, fixed link机架变换kinematic inversion机器machine机器人robot机器人操作器manipulator机器人学robotics技术过程technique process技术经济评价technical and economic evaluation技术系统technique system机械machinery机械创新设计mechanical creation design, MCD机械系统设计mechanical system design, MSD机械动力分析dynamic analysis of machinery机械动力设计dynamic design of machinery机械动力学dynamics of machinery机械的现代设计modern machine design机械系统mechanical system机械利益mechanical advantage机械平衡balance of machinery机械手manipulator机械设计machine design; mechanical design机械特性mechanical behavior机械调速mechanical speed governors 机械效率mechanical efficiency机械原理theory of machines and mechanisms机械运转不均匀系数coefficient of speed fluctuation机械无级变速mechanical stepless speed changes基础机构fundamental mechanism基本额定寿命basic rating life基于实例设计case-based design,CBD基圆base circle基圆半径radius of base circle基圆齿距base pitch基圆压力角pressure angle of base circle基圆柱base cylinder基圆锥base cone急回机构quick-return mechanism急回特性quick-return characteristics 急回系数advance-to return-time ratio 急回运动quick-return motion棘轮ratchet棘轮机构ratchet mechanism棘爪pawl极限位置extreme (or limiting) position极位夹角crank angle between extreme (or limiting) positions计算机辅助设计computer aided design, CAD计算机辅助制造computer aided manufacturing, CAM计算机集成制造系统computer integrated manufacturing system,CIMS计算力矩factored moment; calculation moment计算弯矩calculated bending moment 加权系数weighting efficient加速度acceleration加速度分析acceleration analysis加速度曲线acceleration diagram尖点pointing; cusp尖底从动件knife-edge follower间隙backlash间歇运动机构intermittent motion mechanism减速比reduction ratio减速齿轮、减速装置reduction gear减速器speed reducer减摩性anti-friction quality渐开螺旋面involute helicoid渐开线involute渐开线齿廓involute profile渐开线齿轮involute gear渐开线发生线generating line of。
(整理)机械及模具中英文对照(完整版)

机械专业英语词汇陶瓷ceramics合成纤维synthetic fibre电化学腐蚀electrochemical corrosion车架automotive chassis悬架suspension转向器redirector变速器speed changer板料冲压sheet metal parts孔加工spot facing machining车间workshop工程技术人员engineer气动夹紧pneuma lock数学模型mathematical model画法几何descriptive geometry机械制图Mechanical drawing投影projection视图view剖视图profile chart标准件standard component零件图part drawing装配图assembly drawing尺寸标注size marking技术要求technical requirements刚度rigidity内力internal force位移displacement截面section疲劳极限fatigue limit断裂fracture塑性变形plastic distortion脆性材料brittleness material刚度准则rigidity criterion垫圈washer垫片spacer直齿圆柱齿轮straight toothed spur gear 斜齿圆柱齿轮helical-spur gear直齿锥齿轮straight bevel gear运动简图kinematic sketch齿轮齿条pinion and rack蜗杆蜗轮worm and worm gear虚约束passive constraint曲柄crank摇杆rocker凸轮cams共轭曲线conjugate curve范成法generation method定义域definitional domain值域range导数\\微分differential coefficient求导derivation定积分definite integral不定积分indefinite integral曲率curvature偏微分partial differential毛坯rough游标卡尺slide caliper千分尺micrometer calipers攻丝tap二阶行列式second order determinant逆矩阵inverse matrix线性方程组linear equations概率probability随机变量random variable排列组合permutation and combination气体状态方程equation of state of gas动能kinetic energy势能potential energy机械能守恒conservation of mechanical energy 动量momentum桁架truss轴线axes余子式cofactor逻辑电路logic circuit触发器flip-flop脉冲波形pulse shape数模digital analogy液压传动机构fluid drive mechanism机械零件mechanical parts淬火冷却quench淬火hardening回火tempering调质hardening and tempering磨粒abrasive grain结合剂bonding agent砂轮grinding wheel后角clearance angle龙门刨削planing主轴spindle主轴箱headstock卡盘chuck加工中心machining center车刀lathe tool车床lathe钻削镗削bore车削turning磨床grinder基准benchmark钳工locksmith锻forge压模stamping焊weld拉床broaching machine拉孔broaching装配assembling铸造found流体动力学fluid dynamics流体力学fluid mechanics加工machining液压hydraulic pressure切线tangent机电一体化mechanotronics mechanical-electrical integration 气压air pressure pneumatic pressure稳定性stability介质medium液压驱动泵fluid clutch液压泵hydraulic pump阀门valve失效invalidation强度intensity载荷load应力stress安全系数safty factor可靠性reliability螺纹thread螺旋helix键spline销pin滚动轴承rolling bearing滑动轴承sliding bearing弹簧spring制动器arrester brake十字结联轴节crosshead联轴器coupling链chain皮带strap精加工finish machining粗加工rough machining变速箱体gearbox casing腐蚀rust氧化oxidation磨损wear耐用度durability随机信号random signal离散信号discrete signal超声传感器ultrasonic sensor集成电路integrate circuit挡板orifice plate残余应力residual stress套筒sleeve扭力torsion冷加工cold machining电动机electromotor汽缸cylinder过盈配合interference fit热加工hotwork摄像头CCD camera倒角rounding chamfer优化设计optimal design工业造型设计industrial moulding design有限元finite element滚齿hobbing插齿gear shaping伺服电机actuating motor铣床milling machine钻床drill machine镗床boring machine步进电机stepper motor丝杠screw rod导轨lead rail组件subassembly可编程序逻辑控制器Programmable Logic Controller PLC 电火花加工electric spark machining电火花线切割加工electrical discharge wire - cutting相图phase diagram热处理heat treatment固态相变solid state phase changes有色金属nonferrous metal陶瓷ceramics合成纤维synthetic fibre电化学腐蚀electrochemical corrosion车架automotive chassis悬架suspension转向器redirector变速器speed changer板料冲压sheet metal parts孔加工spot facing machining车间workshop工程技术人员engineer气动夹紧pneuma lock数学模型mathematical model画法几何descriptive geometry机械制图Mechanical drawing投影projection视图view剖视图profile chart标准件standard component零件图part drawing装配图assembly drawing尺寸标注size marking技术要求technical requirements刚度rigidity内力internal force位移displacement截面section疲劳极限fatigue limit断裂fracture塑性变形plastic distortion脆性材料brittleness material刚度准则rigidity criterion垫圈washer垫片spacer直齿圆柱齿轮straight toothed spur gear 斜齿圆柱齿轮helical-spur gear直齿锥齿轮straight bevel gear运动简图kinematic sketch齿轮齿条pinion and rack蜗杆蜗轮worm and worm gear虚约束passive constraint曲柄crank摇杆racker凸轮cams共轭曲线conjugate curve范成法generation method定义域definitional domain值域range导数\\微分differential coefficient求导derivation定积分definite integral不定积分indefinite integral曲率curvature偏微分partial differential毛坯rough游标卡尺slide caliper千分尺micrometer calipers攻丝tap二阶行列式second order determinant逆矩阵inverse matrix线性方程组linear equations概率probability随机变量random variable排列组合permutation and combination气体状态方程equation of state of gas动能kinetic energy势能potential energy机械能守恒conservation of mechanical energy 动量momentum桁架truss轴线axes余子式cofactor逻辑电路logic circuit触发器flip-flop脉冲波形pulse shape数模digital analogy液压传动机构fluid drive mechanism机械零件mechanical parts淬火冷却quench淬火hardening回火tempering调质hardening and tempering磨粒abrasive grain结合剂bonding agent砂轮grinding wheelAssembly line 组装线Layout 布置图Conveyer 流水线物料板Rivet table 拉钉机Rivet gun 拉钉枪Screw driver 起子Pneumatic screw driver 气动起子worktable 工作桌OOBA 开箱检查fit together 组装在一起fasten 锁紧(螺丝)fixture 夹具(治具)pallet 栈板barcode 条码barcode scanner 条码扫描器fuse together 熔合fuse machine热熔机repair修理operator作业员QC品管supervisor 课长ME 制造工程师MT 制造生技cosmetic inspect 外观检查inner parts inspect 内部检查thumb screw 大头螺丝lbs. inch 镑、英寸EMI gasket 导电条front plate 前板rear plate 后板chassis 基座bezel panel 面板power button 电源按键reset button 重置键Hi-pot test of SPS 高源高压测试Voltage switch of SPS 电源电压接拉键sheet metal parts 冲件plastic parts 塑胶件SOP 制造作业程序material check list 物料检查表work cell 工作间trolley 台车carton 纸箱sub-line 支线left fork 叉车personnel resource department 人力资源部production department生产部门planning department企划部QC Section品管科stamping factory冲压厂painting factory烤漆厂molding factory成型厂common equipment常用设备uncoiler and straightener整平机punching machine 冲床robot机械手hydraulic machine油压机lathe车床planer |plein|刨床miller铣床grinder磨床linear cutting线切割electrical sparkle电火花welder电焊机staker=reviting machine铆合机position职务president董事长general manager总经理special assistant manager特助factory director厂长department director部长deputy manager | =vice manager副理section supervisor课长deputy section supervisor =vice section superisor副课长group leader/supervisor组长line supervisor线长assistant manager助理to move, to carry, to handle搬运be put in storage入库pack packing包装to apply oil擦油to file burr 锉毛刺final inspection终检to connect material接料to reverse material 翻料wet station沾湿台Tiana天那水cleaning cloth抹布to load material上料to unload material卸料to return material/stock to退料scraped |\\'skr?pid|报废scrape ..v.刮;削deficient purchase来料不良manufacture procedure制程deficient manufacturing procedure制程不良oxidation |\\' ksi\\'dei?n|氧化scratch刮伤dents压痕defective upsiding down抽芽不良defective to staking铆合不良embedded lump镶块feeding is not in place送料不到位stamping-missing漏冲production capacity生产力education and training教育与训练proposal improvement提案改善spare parts=buffer备件forklift叉车trailer=long vehicle拖板车compound die合模die locker锁模器pressure plate=plate pinch压板bolt螺栓administration/general affairs dept总务部automatic screwdriver电动启子thickness gauge厚薄规gauge(or jig)治具power wire电源线buzzle蜂鸣器defective product label不良标签identifying sheet list标示单location地点present members出席人员subject主题conclusion结论decision items决议事项responsible department负责单位pre-fixed finishing date预定完成日approved by / checked by / prepared by核准/审核/承办PCE assembly production schedule sheet PCE组装厂生产排配表model机锺work order工令revision版次remark备注production control confirmation生产确认checked by初审approved by核准department部门stock age analysis sheet 库存货龄分析表on-hand inventory现有库存available material良品可使用obsolete material良品已呆滞to be inspected or reworked 待验或重工total合计cause description原因说明part number/ P/N 料号type形态item/group/class类别quality品质prepared by制表notes说明year-end physical inventory difference analysis sheet 年终盘点差异分析表physical inventory盘点数量physical count quantity帐面数量difference quantity差异量cause analysis原因分析raw materials原料materials物料finished product成品semi-finished product半成品packing materials包材good product/accepted goods/ accepted parts/good parts良品defective product/non-good parts不良品disposed goods处理品warehouse/hub仓库on way location在途仓oversea location海外仓spare parts physical inventory list备品盘点清单spare molds location模具备品仓skid/pallet栈板tox machine自铆机wire EDM线割EDM放电机coil stock卷料sheet stock片料tolerance工差score=groove压线cam block滑块pilot导正筒trim剪外边pierce剪内边drag form压锻差pocket for the punch head挂钩槽slug hole废料孔feature die公母模expansion dwg展开图radius半径shim(wedge)楔子torch-flame cut火焰切割set screw止付螺丝form block折刀stop pin定位销round pierce punch=die button圆冲子shape punch=die insert异形子stock locater block定位块under cut=scrap chopper清角active plate活动板baffle plate挡块cover plate盖板male die公模female die母模groove punch压线冲子air-cushion eject-rod气垫顶杆spring-box eject-plate弹簧箱顶板bushing block衬套insert 入块club car高尔夫球车capability能力parameter参数factor系数phosphate皮膜化成viscosity涂料粘度alkalidipping脱脂main manifold主集流脉bezel斜视规blanking穿落模dejecting顶固模demagnetization去磁;消磁high-speed transmission高速传递heat dissipation热传rack上料degrease脱脂rinse水洗alkaline etch龄咬desmut剥黑膜D.I. rinse纯水次Chromate铬酸处理Anodize阳性处理seal封孔revision版次part number/P/N料号good products良品scraped products报放心品defective products不良品finished products成品disposed products处理品barcode条码flow chart流程表单assembly组装stamping冲压molding成型spare parts=buffer备品coordinate座标dismantle the die折模auxiliary fuction辅助功能poly-line多义线heater band 加热片thermocouple热电偶sand blasting喷沙grit 砂砾derusting machine除锈机degate打浇口dryer烘干机induction感应induction light感应光response=reaction=interaction感应ram连杆edge finder巡边器concave凸convex凹short射料不足nick缺口speck瑕??shine亮班splay 银纹gas mark焦痕delamination起鳞cold slug冷块blush 导色gouge沟槽;凿槽satin texture段面咬花witness line证示线patent专利grit沙砾granule=peuet=grain细粒grit maker抽粒机cushion缓冲magnalium镁铝合金magnesium镁金metal plate钣金lathe车mill锉plane刨grind磨drill铝boring镗blinster气泡fillet镶;嵌边through-hole form通孔形式voller pin formality滚针形式cam driver铡楔shank摸柄crank shaft曲柄轴augular offset角度偏差velocity速度production tempo生产进度现状torque扭矩spline=the multiple keys花键quenching淬火tempering回火annealing退火carbonization碳化tungsten high speed steel钨高速的moly high speed steel钼高速的organic solvent有机溶剂bracket小磁导liaison联络单volatile挥发性resistance电阻ion离子titrator滴定仪beacon警示灯coolant冷却液crusher破碎机阿基米德蜗杆Archimedes worm安全系数safety factor; factor of safety安全载荷safe load凹面、凹度concavity扳手wrench板簧flat leaf spring半圆键woodruff key变形deformation摆杆oscillating bar摆动从动件oscillating follower摆动从动件凸轮机构cam with oscillating follower 摆动导杆机构oscillating guide-bar mechanism 摆线齿轮cycloidal gear摆线齿形cycloidal tooth profile摆线运动规律cycloidal motion摆线针轮cycloidal-pin wheel包角angle of contact保持架cage背对背安装back-to-back arrangement背锥back cone ;normal cone背锥角back angle背锥距back cone distance比例尺scale比热容specific heat capacity闭式链closed kinematic chain闭链机构closed chain mechanism臂部arm变频器frequency converters变频调速frequency control of motor speed变速speed change变速齿轮change gear change wheel变位齿轮modified gear变位系数modification coefficient标准齿轮standard gear标准直齿轮standard spur gear表面质量系数superficial mass factor表面传热系数surface coefficient of heat transfer表面粗糙度surface roughness并联式组合combination in parallel并联机构parallel mechanism并联组合机构parallel combined mechanism并行工程concurrent engineering并行设计concurred design, CD不平衡相位phase angle of unbalance不平衡imbalance (or unbalance)不平衡量amount of unbalance不完全齿轮机构intermittent gearing波发生器wave generator波数number of waves补偿compensation参数化设计parameterization design, PD残余应力residual stress操纵及控制装置operation control device槽轮Geneva wheel槽轮机构Geneva mechanism ;Maltese cross槽数Geneva numerate槽凸轮groove cam侧隙backlash差动轮系differential gear train差动螺旋机构differential screw mechanism差速器differential常用机构conventional mechanism; mechanism in common use 车床lathe承载量系数bearing capacity factor承载能力bearing capacity成对安装paired mounting尺寸系列dimension series齿槽tooth space齿槽宽spacewidth齿侧间隙backlash齿顶高addendum齿顶圆addendum circle齿根高dedendum齿根圆dedendum circle齿厚tooth thickness齿距circular pitch齿宽face width齿廓tooth profile齿廓曲线tooth curve齿轮gear齿轮变速箱speed-changing gear boxes齿轮齿条机构pinion and rack齿轮插刀pinion cutter; pinion-shaped shaper cutter 齿轮滚刀hob ,hobbing cutter齿轮机构gear齿轮轮坯blank齿轮传动系pinion unit齿轮联轴器gear coupling齿条传动rack gear齿数tooth number齿数比gear ratio齿条rack齿条插刀rack cutter; rack-shaped shaper cutter齿形链、无声链silent chain齿形系数form factor齿式棘轮机构tooth ratchet mechanism插齿机gear shaper重合点coincident points重合度contact ratio冲床punch传动比transmission ratio, speed ratio传动装置gearing; transmission gear传动系统driven system传动角transmission angle传动轴transmission shaft串联式组合combination in series串联式组合机构series combined mechanism串级调速cascade speed control创新innovation creation创新设计creation design垂直载荷、法向载荷normal load唇形橡胶密封lip rubber seal磁流体轴承magnetic fluid bearing从动带轮driven pulley从动件driven link, follower从动件平底宽度width of flat-face从动件停歇follower dwell从动件运动规律follower motion从动轮driven gear粗线bold line粗牙螺纹coarse thread大齿轮gear wheel打包机packer打滑slipping带传动belt driving带轮belt pulley带式制动器band brake单列轴承single row bearing单向推力轴承single-direction thrust bearing单万向联轴节single universal joint单位矢量unit vector当量齿轮equivalent spur gear; virtual gear当量齿数equivalent teeth number; virtual number of teeth当量摩擦系数equivalent coefficient of friction当量载荷equivalent load刀具cutter导数derivative倒角chamfer导热性conduction of heat导程lead导程角lead angle等加等减速运动规律parabolic motion; constant acceleration and deceleration motion等速运动规律uniform motion; constant velocity motion等径凸轮conjugate yoke radial cam等宽凸轮constant-breadth cam等效构件equivalent link等效力equivalent force等效力矩equivalent moment of force等效量equivalent等效质量equivalent mass等效转动惯量equivalent moment of inertia等效动力学模型dynamically equivalent model底座chassis低副lower pair点划线chain dotted line(疲劳)点蚀pitting垫圈gasket垫片密封gasket seal碟形弹簧belleville spring顶隙bottom clearance定轴轮系ordinary gear train; gear train with fixed axes动力学dynamics动密封kinematical seal动能dynamic energy动力粘度dynamic viscosity动力润滑dynamic lubrication动平衡dynamic balance动平衡机dynamic balancing machine动态特性dynamic characteristics动态分析设计dynamic analysis design动压力dynamic reaction动载荷dynamic load端面transverse plane端面参数transverse parameters端面齿距transverse circular pitch端面齿廓transverse tooth profile端面重合度transverse contact ratio端面模数transverse module端面压力角transverse pressure angle锻造forge对称循环应力symmetry circulating stress对心滚子从动件radial (or in-line ) roller follower对心直动从动件radial (or in-line ) translating follower对心移动从动件radial reciprocating follower对心曲柄滑块机构in-line slider-crank (or crank-slider) mechanism 多列轴承multi-row bearing多楔带poly V-belt多项式运动规律polynomial motion多质量转子rotor with several masses惰轮idle gear额定寿命rating life额定载荷load ratingII 级杆组dyad发生线generating line发生面generating plane法面normal plane法面参数normal parameters法面齿距normal circular pitch法面模数normal module法面压力角normal pressure angle法向齿距normal pitch法向齿廓normal tooth profile法向直廓蜗杆straight sided normal worm法向力normal force反馈式组合feedback combining反向运动学inverse ( or backward) kinematics反转法kinematic inversion反正切Arctan范成法generating cutting仿形法form cutting方案设计、概念设计concept design, CD防振装置shockproof device飞轮flywheel飞轮矩moment of flywheel非标准齿轮nonstandard gear非接触式密封non-contact seal非周期性速度波动aperiodic speed fluctuation非圆齿轮non-circular gear粉末合金powder metallurgy分度线reference line; standard pitch line分度圆reference circle; standard (cutting) pitch circle 分度圆柱导程角lead angle at reference cylinder分度圆柱螺旋角helix angle at reference cylinder分母denominator分子numerator分度圆锥reference cone; standard pitch cone分析法analytical method封闭差动轮系planetary differential复合铰链compound hinge复合式组合compound combining复合轮系compound (or combined) gear train复合平带compound flat belt复合应力combined stress复式螺旋机构Compound screw mechanism复杂机构complex mechanism杆组Assur group干涉interference刚度系数stiffness coefficient刚轮rigid circular spline钢丝软轴wire soft shaft刚体导引机构body guidance mechanism刚性冲击rigid impulse (shock)刚性转子rigid rotor刚性轴承rigid bearing刚性联轴器rigid coupling高度系列height series高速带high speed belt高副higher pair格拉晓夫定理Grashoff`s law根切undercutting公称直径nominal diameter高度系列height series功work工况系数application factor工艺设计technological design工作循环图working cycle diagram工作机构operation mechanism工作载荷external loads工作空间working space工作应力working stress工作阻力effective resistance工作阻力矩effective resistance moment公法线common normal line公共约束general constraint公制齿轮metric gears功率power功能分析设计function analyses design共轭齿廓conjugate profiles共轭凸轮conjugate cam构件link鼓风机blower固定构件fixed link; frame固体润滑剂solid lubricant关节型操作器jointed manipulator惯性力inertia force惯性力矩moment of inertia ,shaking moment 惯性力平衡balance of shaking force惯性力完全平衡full balance of shaking force惯性力部分平衡partial balance of shaking force 惯性主矩resultant moment of inertia惯性主失resultant vector of inertia冠轮crown gear广义机构generation mechanism广义坐标generalized coordinate轨迹生成path generation轨迹发生器path generator滚刀hob滚道raceway滚动体rolling element滚动轴承rolling bearing滚动轴承代号rolling bearing identification code 滚针needle roller滚针轴承needle roller bearing滚子roller滚子轴承roller bearing滚子半径radius of roller滚子从动件roller follower滚子链roller chain滚子链联轴器double roller chain coupling滚珠丝杆ball screw滚柱式单向超越离合器roller clutch过度切割undercutting函数发生器function generator函数生成function generation含油轴承oil bearing耗油量oil consumption耗油量系数oil consumption factor赫兹公式H. Hertz equation合成弯矩resultant bending moment合力resultant force合力矩resultant moment of force黑箱black box横坐标abscissa互换性齿轮interchangeable gears花键spline滑键、导键feather key滑动轴承sliding bearing滑动率sliding ratio滑块slider环面蜗杆toroid helicoids worm环形弹簧annular spring缓冲装置shocks; shock-absorber灰铸铁grey cast iron回程return回转体平衡balance of rotors混合轮系compound gear train积分integrate机电一体化系统设计mechanical-electrical integration system design 机构mechanism机构分析analysis of mechanism机构平衡balance of mechanism机构学mechanism机构运动设计kinematic design of mechanism机构运动简图kinematic sketch of mechanism机构综合synthesis of mechanism机构组成constitution of mechanism机架frame, fixed link机架变换kinematic inversion机器machine机器人robot机器人操作器manipulator机器人学robotics技术过程technique process技术经济评价technical and economic evaluation技术系统technique system机械machinery机械创新设计mechanical creation design, MCD机械系统设计mechanical system design, MSD机械动力分析dynamic analysis of machinery机械动力设计dynamic design of machinery机械动力学dynamics of machinery机械的现代设计modern machine design机械系统mechanical system机械利益mechanical advantage机械平衡balance of machinery机械手manipulator机械设计machine design; mechanical design机械特性mechanical behavior机械调速mechanical speed governors机械效率mechanical efficiency机械原理theory of machines and mechanisms机械运转不均匀系数coefficient of speed fluctuation机械无级变速mechanical stepless speed changes基础机构fundamental mechanism基本额定寿命basic rating life基于实例设计case-based design,CBD基圆base circle基圆半径radius of base circle基圆齿距base pitch基圆压力角pressure angle of base circle基圆柱base cylinder基圆锥base cone急回机构quick-return mechanism急回特性quick-return characteristics急回系数advance-to return-time ratio急回运动quick-return motion棘轮ratchet棘轮机构ratchet mechanism棘爪pawl极限位置extreme (or limiting) position极位夹角crank angle between extreme (or limiting) positions计算机辅助设计computer aided design, CAD计算机辅助制造computer aided manufacturing, CAM计算机集成制造系统computer integrated manufacturing system, CIMS 计算力矩factored moment; calculation moment计算弯矩calculated bending moment加权系数weighting efficient加速度acceleration加速度分析acceleration analysis加速度曲线acceleration diagram尖点pointing; cusp尖底从动件knife-edge follower间隙backlash间歇运动机构intermittent motion mechanism 减速比reduction ratio减速齿轮、减速装置reduction gear减速器speed reducer减摩性anti-friction quality渐开螺旋面involute helicoid渐开线involute渐开线齿廓involute profile渐开线齿轮involute gear渐开线发生线generating line of involute渐开线方程involute equation渐开线函数involute function渐开线蜗杆involute worm渐开线压力角pressure angle of involute渐开线花键involute spline简谐运动simple harmonic motion键key键槽keyway交变应力repeated stress交变载荷repeated fluctuating load交叉带传动cross-belt drive交错轴斜齿轮crossed helical gears胶合scoring角加速度angular acceleration角速度angular velocity角速比angular velocity ratio角接触球轴承angular contact ball bearing角接触推力轴承angular contact thrust bearing 角接触向心轴承angular contact radial bearing 角接触轴承angular contact bearing铰链、枢纽hinge校正平面correcting plane接触应力contact stress接触式密封contact seal阶梯轴multi-diameter shaft结构structure结构设计structural design截面section节点pitch point节距circular pitch; pitch of teeth节线pitch line节圆pitch circle节圆齿厚thickness on pitch circle节圆直径pitch diameter节圆锥pitch cone节圆锥角pitch cone angle解析设计analytical design紧边tight-side紧固件fastener径节diametral pitch径向radial direction径向当量动载荷dynamic equivalent radial load径向当量静载荷static equivalent radial load径向基本额定动载荷basic dynamic radial load rating 径向基本额定静载荷basic static radial load tating径向接触轴承radial contact bearing径向平面radial plane径向游隙radial internal clearance径向载荷radial load径向载荷系数radial load factor径向间隙clearance静力static force静平衡static balance静载荷static load静密封static seal局部自由度passive degree of freedom矩阵matrix矩形螺纹square threaded form锯齿形螺纹buttress thread form矩形牙嵌式离合器square-jaw positive-contact clutch 绝对尺寸系数absolute dimensional factor绝对运动absolute motion绝对速度absolute velocity均衡装置load balancing mechanism抗压强度compression strength开口传动open-belt drive开式链open kinematic chain开链机构open chain mechanism可靠度degree of reliability可靠性reliability可靠性设计reliability design, RD空气弹簧air spring空间机构spatial mechanism空间连杆机构spatial linkage空间凸轮机构spatial cam空间运动副spatial kinematic pair空间运动链spatial kinematic chain空转idle宽度系列width series框图block diagram雷诺方程Reynolds‘s equation离心力centrifugal force离心应力centrifugal stress离合器clutch离心密封centrifugal seal理论廓线pitch curve理论啮合线theoretical line of action隶属度membership力force力多边形force polygon力封闭型凸轮机构force-drive (or force-closed) cam mechanism 力矩moment力平衡equilibrium力偶couple力偶矩moment of couple连杆connecting rod, coupler连杆机构linkage连杆曲线coupler-curve连心线line of centers链chain链传动装置chain gearing链轮sprocket sprocket-wheel sprocket gear chain wheel联组V 带tight-up V belt联轴器coupling shaft coupling两维凸轮two-dimensional cam临界转速critical speed六杆机构six-bar linkage龙门刨床double Haas planer轮坯blank轮系gear train螺杆screw螺距thread pitch螺母screw nut螺旋锥齿轮helical bevel gear螺钉screws螺栓bolts螺纹导程lead螺纹效率screw efficiency螺旋传动power screw螺旋密封spiral seal螺纹thread (of a screw)螺旋副helical pair螺旋机构screw mechanism螺旋角helix angle螺旋线helix ,helical line绿色设计green design design for environment马耳他机构Geneva wheel Geneva gear马耳他十字Maltese cross脉动无级变速pulsating stepless speed changes脉动循环应力fluctuating circulating stress脉动载荷fluctuating load铆钉rivet迷宫密封labyrinth seal密封seal密封带seal belt密封胶seal gum密封元件potted component密封装置sealing arrangement面对面安装face-to-face arrangement面向产品生命周期设计design for product`s life cycle, DPLC 名义应力、公称应力nominal stress模块化设计modular design, MD模块式传动系统modular system模幅箱morphology box模糊集fuzzy set模糊评价fuzzy evaluation模数module摩擦friction摩擦角friction angle摩擦力friction force摩擦学设计tribology design, TD摩擦阻力frictional resistance摩擦力矩friction moment摩擦系数coefficient of friction摩擦圆friction circle磨损abrasion wear; scratching末端执行器end-effector目标函数objective function耐腐蚀性corrosion resistance耐磨性wear resistance挠性机构mechanism with flexible elements挠性转子flexible rotor内齿轮internal gear内齿圈ring gear内力internal force内圈inner ring能量energy能量指示图viscosity逆时针counterclockwise (or anticlockwise)啮出engaging-out啮合engagement, mesh, gearing啮合点contact points啮合角working pressure angle啮合线line of action啮合线长度length of line of action啮入engaging-in牛头刨床shaper凝固点freezing point; solidifying point扭转应力torsion stress扭矩moment of torque扭簧helical torsion spring诺模图NomogramO 形密封圈密封O ring seal盘形凸轮disk cam盘形转子disk-like rotor抛物线运动parabolic motion疲劳极限fatigue limit疲劳强度fatigue strength偏置式offset偏( 心) 距offset distance偏心率eccentricity ratio偏心质量eccentric mass偏距圆offset circle偏心盘eccentric偏置滚子从动件offset roller follower偏置尖底从动件offset knife-edge follower偏置曲柄滑块机构offset slider-crank mechanism 拼接matching评价与决策evaluation and decision频率frequency平带flat belt平带传动flat belt driving平底从动件flat-face follower平底宽度face width平分线bisector平均应力average stress平均中径mean screw diameter平均速度average velocity平衡balance平衡机balancing machine平衡品质balancing quality平衡平面correcting plane平衡质量balancing mass平衡重counterweight平衡转速balancing speed平面副planar pair, flat pair平面机构planar mechanism平面运动副planar kinematic pair平面连杆机构planar linkage平面凸轮planar cam平面凸轮机构planar cam mechanism平面轴斜齿轮parallel helical gears普通平键parallel key其他常用机构other mechanism in common use起动阶段starting period启动力矩starting torque气动机构pneumatic mechanism奇异位置singular position起始啮合点initial contact , beginning of contact气体轴承gas bearing千斤顶jack嵌入键sunk key强迫振动forced vibration切齿深度depth of cut曲柄crank曲柄存在条件Grashoff`s law曲柄导杆机构crank shaper (guide-bar) mechanism曲柄滑块机构slider-crank (or crank-slider) mechanism 曲柄摇杆机构crank-rocker mechanism曲齿锥齿轮spiral bevel gear曲率curvature曲率半径radius of curvature曲面从动件curved-shoe follower曲线拼接curve matching曲线运动curvilinear motion曲轴crank shaft驱动力driving force驱动力矩driving moment (torque)全齿高whole depth。
精选机械外文翻译中英文doc
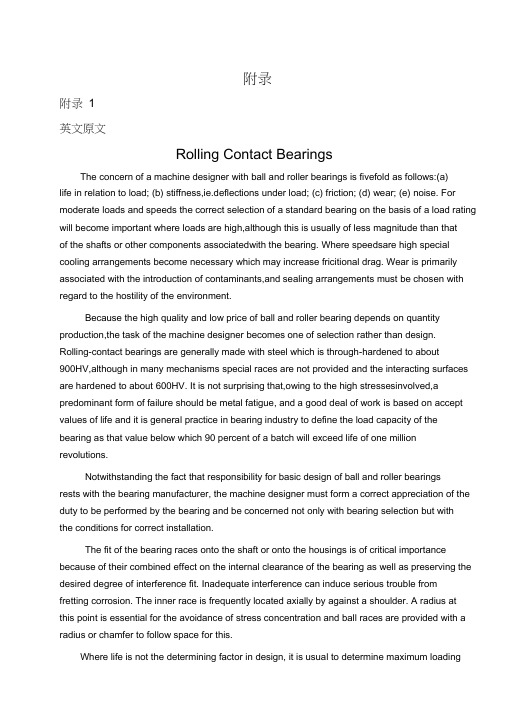
附录附录 1英文原文Rolling Contact BearingsThe concern of a machine designer with ball and roller bearings is fivefold as follows:(a)life in relation to load; (b) stiffness,ie.deflections under load; (c) friction; (d) wear; (e) noise. For moderate loads and speeds the correct selection of a standard bearing on the basis of a load rating will become important where loads are high,although this is usually of less magnitude than thatof the shafts or other components associatedwith the bearing. Where speedsare high special cooling arrangements become necessary which may increase fricitional drag. Wear is primarily associated with the introduction of contaminants,and sealing arrangements must be chosen with regard to the hostility of the environment.Because the high quality and low price of ball and roller bearing depends on quantity production,the task of the machine designer becomes one of selection rather than design.Rolling-contact bearings are generally made with steel which is through-hardened to about900HV,although in many mechanisms special races are not provided and the interacting surfaces are hardened to about 600HV. It is not surprising that,owing to the high stressesinvolved,a predominant form of failure should be metal fatigue, and a good deal of work is based on accept values of life and it is general practice in bearing industry to define the load capacity of thebearing as that value below which 90 percent of a batch will exceed life of one million revolutions.Notwithstanding the fact that responsibility for basic design of ball and roller bearingsrests with the bearing manufacturer, the machine designer must form a correct appreciation of the duty to be performed by the bearing and be concerned not only with bearing selection but withthe conditions for correct installation.The fit of the bearing races onto the shaft or onto the housings is of critical importance because of their combined effect on the internal clearance of the bearing as well as preserving the desired degree of interference fit. Inadequate interference can induce serious trouble fromfretting corrosion. The inner race is frequently located axially by against a shoulder. A radius atthis point is essential for the avoidance of stress concentration and ball races are provided with a radius or chamfer to follow space for this.Where life is not the determining factor in design, it is usual to determine maximum loadingby the amount to which a bearing will deflect under load. Thus the concept of "staticload-carrying capacity" is understood to mean the load that can be applied to a bearing, which is either stationary or subject to slight swiveling motions, without impairing its running qualitiesfor subsequent rotational motion. This has been determined by practical experience as the load which when applied to a bearing results in a total deformation of 0.0025mm for a ball 25mm in diameter.The successful functioning of many bearings depends upon providing them with adequate protection against their environment, and in some circumstances the environment must be protected from lubricants or products of deterioration of the bearing design. Moreover, seals which are applied to moving parts for any purpose are of interest to tribologists because they are components of bearing systems and can only be designed satisfactorily on basis of the appropriate bearing theory.Notwithstanding their importance, the amount of research effort that has been devoted to the understanding of the behavior of seals has been small when compared with that devoted to other aspects of bearing technology.LathesLathes are widely used in industry to produce all kinds of machined parts. Some are general purpose machines, and others are used to perform highly specialized operations.Engine lathesEngine lathes, of course, are general-purpose machine used in production and maintenance shop all over the the world. Sized ranger from small bench models to huge heavy duty pieces of equipment. Many of the larger lathes come equipped with attachments not commonly found in the ordinary shop, such as automatic shop for the carriage.Tracer or Duplicating LathesThe tracer or duplicating lathe is designed o produce irregularly shaped parts automatically. The basic operation of this lathe is as fallows. A template of either a flat or three-dimensional shape is placed in a holder. A guide or pointer then moves along this shape and its movement controls that of the cutting tool. The duplication may include a square or tapered shoulder, grooves, tapers, and contours. Work such as motor shafts, spindles, pistons, rods, car axles, turbine shafts, and a variety of other objects can be turned using this type of lathe.Turret LathesWhen machining a complex workpiece on a general-purpose lathe, a great deal of time isspent changing and adjusting the several tools that are needed to complete the work. One of the first adaptations of the engine lathe which made it suitable to mass production was the additionof multi-tool in place of the tailstock. Although most turrets have six stations, some have asmany as eight.High-production turret lathes are very complicated machines with a wide variety of power accessories. The principal feature of all turret lathes, however, is that the tools can perform a consecutive serials of operations in proper sequence. Once the tools have been set and adjusted, little skill is require to run out duplicate parts.Automatic Screw MachineScrew machines are similar in construction to turret lathes, except that their heads are designed to hold and feed long bars of stock. Otherwise, their is little different between them. Both are designed for multiple tooling, and both have adaptations for identical work. Originally, the turret lathe was designed as a chucking lathe for machining small casting, forgings, and irregularly shaped workpieces.The first screw machines were designed to feed bar stock and wire used in making small screw parts. Today, however, the turret lathe is frequently used with a collect attachment, and the automatic screw machine can be equipped with a chuck to hold castings.The single-spindle automatic screw machine, as its name implies, machines work on only one bar of stock at a time. A bar 16 to 20 feet long is feed through the headstock spindle and is held firmly by a collect. The machining operations are done by cutting tools mounted on the cross slide. When the machine is in operation, the spindle and the stock are rotated at selected speeds for different operations. If required, rapid reversal of spindle direction is also possible.In the single-spindle automatic screw machine, a specific length of stock is automaticallyfed through the spindle to a machining area. At this point, the turret and cross slide move into position and automatically perform whatever operations are required. After the machined piece is cut off, stock is again fed into the machining area and the entire cycle is repeated.Multiple-spindle automatic screw machines have from four to eight spindles located around a spindle carrier. Long bars of stock, supported at the rear of the machine,pass though these hollow spindles and are gripped by collects. With the single spindle machines, the turret indexes around the spindle. When one tool on the turret is working, the others are not. With a multiple spindle machine, however, the spindle itself index. Thus the bars of stock are carried to the various end working and side working tools. Each tool operates in only one position, but tollsoperate simultaneously. Therefore, four to eight workpieces can be machined at the same time.Vertical Turret LathesA vertical turret is basically a turret lathe that has been stood on its headstock end. It is designed to perform a variety of turning operations. It consists of a turret, a revolving table, and a side head with a square turret for holding additional tools. Operations performed by any of the tools mounted on the turret or side head can be controlled through the use of stops.Machining CentersMany of today's more sophisticated lathes are called machining centers since they are capable of performing, in addition to the normal turning operations, certain milling and drilling operations. Basically, a machining center can be thought of as being a combination turret lathe and milling machine. Additional features are sometimes included by the versatility of their machines.Numerical ControlOne of the most fundamental concepts in the area of advanced manufacturing technologies is numerical control(NC). Prior to the advent of NC, all machine tools were manually operated and controlled. Among the many limitations associated with manual control machine tools, perhaps none is more prominent than limitation of operator skills. With manual control, the quality of the product is directly related to and limited to the skills of the operator. Numerical control represents the first major step away from human control of machine tools.Numerical control means the control of machine tools and other manufacturing systems through the use of prerecorded, written symbolic instructions. Rather than operating a machine tool, an NC technician tool to be numerically controlled, it must be interfaced with a device for accepting and decoding the programmed instructions, known as a reader.Numerical control was developed to overcome the limitation of human operators, and it has done so. Numerical control machines are more accurate than manually operated machines, they can produce parts more uniformly, they are faster, and the long-run tooling costs are lower. The development of NC led to the development of several other innovations in manufacturing technology:1. Electrical discharge machining.2. Laser cutting.3. Electron beam welding.Numerical control has also made machines tools more versatile than their manually operated predecessors. An NC machine tool can automatically produce a wide variety of parts, each involving an assortment of widely varied and complex machining processes. Numerical control has allowed manufacturers to undertake the production of products that would not have been feasible from an economic perspective using manually controlled machine tools and processes.Like so many advanced technologies, NC was born in the laboratories of the Masschusetts Institute of Technology. The concept of NC was developed in early 1950s with funding providedby the U.S.Air force. In its earliest stages, NC machines were able to make straight cuts efficiently and effectively.However,curved paths were a problem because the machine tool had to be programmed to undertake a series of horizontal and vertical steps to produce a curve. The shorter is straight lines making up the steps, the smoother is the curve. Each line segment in the steps had to be calculated.This problem led to the development in 1959 of the Automatically Programmed Tools(APT) language. This is a special programming language for NC that uses statements similar to English language to define the part geometry, describe the cutting tool configuration, and specify the necessary motions. The development of the APT language was a major step forward in the further development of NC technology. The original NC systems were vastly different fromthose used today. The machines had hardwired logic circuits. This instructional programs were written on punched paper, which was later to be replaced by magnetic plastic tape. A tape reader was used to interpret the instructions written on the tape for the machine. Together, all of this represented a giant step forward in the control of machine tools. However, there were a numberof problems with NC at this point in its development.A major problem wad the fragility of the punched paper tape medium. It was common forthe paper tape containing the programmed instructions to break or tear during a machining process. This problem was exacerbated by the fact that each programmed instructions had to be return through the reader. If it was necessary to produce 100 copies of a given part,it was also necessary to run the paper tape through the reader 100 separate times. Fragile paper tapes simply could not withstand the rigors of a shop floor environment and this kind of repeated use.This led to the development of a special magnetic plastic tape. Whereas the paper tape carried the programmed instructions as a series of holes punched in the tape, the plastic tape carried the instructions as a series of magnetic dots. The plastic tape was much stronger than thepaper taps, which solved the problem of frequent tearing and breakage. However, it still left two other problems.The most important of these was that it was difficult or impossible to change the instructions entered on the tape. To make even the most minor adjustments in a program of instructions, it necessary to interrupt machining operations and make a new tape. It was also still necessary to run the tape through the reader as many times as there were parts to be produced. Fortunately, computer technology became a reality and soon solved the problem of NC associated with punched paper and plastic tape.The development of a concept known as direct numerical control(DNC)solved the paperand plastic tape problems associated with numerical control by simply eliminating tape as the medium for carrying the programmed instructions. In direct numerical control machine tools are tied, via a data transmission link, to a host computer. Programs for operating the machine tools are stored in the host computer and fed to the machine tool as needed via the data transmission linkage. Direct numerical control represented a major step forward over punched tape and plastic tape. However, it is subject to the same limitations as all technologies that depend o a host computer. When the lost computer goes down, the machine tools also experience downtime. This problem led to the development of computer numerical control.The development of the microprocessor allowed for the development of programmablelogic controllers(PNC)and microcomputer. These two technologies allowed for the developmentof computer numerical control(CNC). With CNC, each machine tool has a PLC or a microcomputer that serves the same purpose. This allows programs to be input and stored at each individual machine tool. It also allows programs to be developed off-line and download at the individual machine tool. CNC solved the problems associated with downtime of the host computer, but it introduced another known as data management. The same program might be loaded on ten different being solved by local area networks that connect microcomputer forbetter data management.CNC machine tool feed motion systemsCNC machine tool feed motion systems, especially to the outline of the control ofmovement into the system, must be addressed to the movement into the position and velocity at the same time the realization of two aspects of automatic control, as compared with the general machine tools, require more feed system high positioning accuracy and good dynamic response.A typical closed-loop control of CNC machine tool feed system, usually by comparing thelocation of amplification unit, drive unit, mechanical transmission components, such as feedbackand testing of several parts. Here as mechanical gear-driven source refers to the movement of the rotary table into a linear motion of the entire mechanical transmission chain, including the deceleration device, turning the lead screw nut become mobile and vice-oriented components and so on. To ensure that the CNC machine tool feed drive system, precision, sensitivity and stability, the design of the mechanical parts of the general requirement is to eliminate the gap, reducing friction, reducing the movement of inertia to improve the transmission accuracy and stiffness. In addition, the feeding system load changes in the larger, demanding response characteristics, so for the stiffness, inertia matching the requirements are very high.Linear Roller GuidesIn order to meet these requirements, the use of CNC machine tools in general low-friction transmission vice, such as anti-friction sliding rail, rail rolling and hydrostatic guideways, ball screws, etc.; transmission components to ensure accuracy, the use of pre-rational, the form of a reasonable support to enhance the stiffness of transmission; deceleration than the best choice to improve the resolution of machine tools and systems converted to the driveshaft on the reduction of inertia; as far as possible the elimination of drive space and reduce dead-zone inverse error and improve displacement precision.Linear Roller Guides outstanding advantage is seamless, and can impose pre-compression. By the rail body, the slider, ball, cage, end caps and so on. Also known as linear rolling guide unit. Use a fixed guide body without moving parts, the slider fixed on the moving parts. Whenthe slider moves along the rail body, ball and slider in the guide of the arc between the straight and through the rolling bed cover of Rolling Road, from the work load to non-work load, andthen rolling back work load, constant circulation, so as to guide and move the slider between the rolling into a ball.附录2中文翻译转动轴承关于球轴承和滚子轴承,一个机械设计人员应当考虑下边五个方面:(a)寿命与载荷关系;(b)刚度,也就是在载荷作用下的变形;(c)摩擦;(d)磨损;(e)噪声。
- 1、下载文档前请自行甄别文档内容的完整性,平台不提供额外的编辑、内容补充、找答案等附加服务。
- 2、"仅部分预览"的文档,不可在线预览部分如存在完整性等问题,可反馈申请退款(可完整预览的文档不适用该条件!)。
- 3、如文档侵犯您的权益,请联系客服反馈,我们会尽快为您处理(人工客服工作时间:9:00-18:30)。
附录英文原文Industrial Robot and its system’s componentsThere are a variety of definitions of the term robot. Depending on the definition used, the number of robot installations worldwide varies widely. Numerous single purpose muchines are used in manufacturing plants that might appear to be robots. These machines are hardwired to perform a single function and can not be reprogrammed to perform a different function. Such single-purpose machines do not fit the definition for industrial robots that is becoming widely accepted. This definition was developed by the robot Institute ofAmerica:A robot is a reprogrammable muhifunctional manipulator designed to move material, parts, tools, or specialized devices through variable progranmled motions for the perfommnce of a variety of tasks.Note that this definition cxmtalns the words reprograrnmable and multifunctional. It is these two characteristics that separate the true industrial robot from the various single-purpose machines used in modern manufacturing firms. The term"reprogrammable"implies two things:The robot operates aec~)rding to a written program, and this program can be rewritten to acconlmodatc a variety of manufacturing tasks.The term"multifunctional"means that the robot can, through reprogramming and the use of different cnd-effectors, perform a number of different manufacturing tasks. Definitions written around these two critical characteristics are becoming the accepted definitions among manufacturing professionals.The fimt articulated arm came about in 1951 and was used by the U.S. Atomic Energy Commission. In 1954, the first programmable robot was designed by George Devol. It was based on two important technologies:(1) Numerical control (NC) technology.(2) Remote manipulation technology.Numerical control technology provided a foma of machine control ideally suited to robots.It allowed for the control of motion by stored programs. These programs contain data points to which the robot sequentially moves, timing signals to initiate action and to stop movement, and logic statements to allow for decision rfmking.Remote manipulation technology allowed a machine to be more than just another NC machine. It allowed such machines to become robots that can perfoml a variety of manufactuing tasks in both inaccessible an unsafe environmonts. By mering these two technologies, Devol developed the first industrial robot, an unsophistieated programmable materials handling machine.The first conunercially produced robot was developed in 1959. In 1962, the first industrial robot to be used oil a production llne was installed by General Motors Corporation. This robot was produced by Unimation. A major step forward in robot control occurred in 1973 with the development of the T-3 industrial robot by Cincinnati Milaeron. The T-3 robot was the first commercially producedindustrial robot controlled by a minicomputer.Numerical control and remote manipulation technology prompted the wide scale development and use of industrial robots. But major technological developments do not take place simply because of such new capabilities. Something must provide the impetus for taking advantage of these capabilities. In the case of industrial robots, the impetus was economies.The rapid inflation of wages experienced in the 1970s tremendously increased the personnel costs of manufacturing firms. At the same time, foreign competition became a serious problem for U. S. manufacturers. Foreign manufacturers who had under taken automation on a wide scale basis, such as those in Japan, began to gain an increasingly large share of the U.S. and world market for manufactured goods, particularly automobiles.Through a variety of automation techniques, includicg robots, Japanese manufacturers, beginning in the 1970s, were able to produce better automobiles more cheaply than nonautomated U.S. manufacturers. Consequently, in order to survive, U.S. manufacturers were forced to consider any technological developments that could help improve productivity.It became imperative to produce better produets at lower costs in order to be competitive with foreign manufacturers. Other factors such as the need to find better ways of performing dangerous marmfacturing tasks contributed to the development of industrial robots. However, the principal rationale has always been,and is still, improved productivity.One of the principal advantages of robots is that they can be used in settings that are dangerous to humans. Welding and parting are examples of applications where rotmts can be dangerous to humans. Even though robots are closely asmciated with safety in the workplace, they can, in themselves, be dangerous.Robots and robot cells must be carefully designed and configured so that they do not endanger human workers and other machines. Robot work envelops should be accurately calculated and a danger zone surroundting the envelop clearly marked off. Red flooring strips and barriers can be userd to keep human workers out of a robot’s work envelope.Eren with such precautions it is still a good idea to have an automatic shutdown system in situations where robots are used. Such a system should should have the capacity to sense the need for an automatic shutdown of operations. Fault-tolerant computers and redunant systems can be installed to ensure proper shutdown of robotics systems to ensure a safe environment.Industrial robots is the science of designing, building, and applying industrial robcts. What are robots? In the late 1970s the Robotic Industries Association defined a robot as” a manipulator, designed to move material, parts,tools or specialized devices through variable programmed motions for the performance of a variety of tasks". Although this definition does not directly include pick and place arms as robots, teleoperamrs and remotely controlled devicesare often referred to also as robots. The International Standards Organization(ISO) has a more lengthy definition of an industrial robot:A machine formed by a mechanism including several degrees of freedom, often having tile appearanoa of one or several arms ending in a wrist capable of holding a tool or a workpiece or an inspection device. In particular, its control unit must use a memorizing device and .sometimes it can use sensing or adaptation appliances taking into account environment and circumstances. These multipurtpose machines are generally designed to carry out a repetitive function and can be adapted to other functions.The RIA and ISO definitions both stress the muLtifunctional and programmable capabilities and, therefore, exclude special-purpose "hard automation" tools and equipment typically found in high volume production. Also excluded are manual remote manipulators, which are extensions of human hands for use in, for example, sterile, hot, or radioactive environments.In Japan, the Japanese Industrial Robot Association (JIRA) classifies industrial robots by the method of input informatkm and the method of teaching:1. Manual Manipulators. Manipulators directly activated by the operator.2. Fixed-sequence Robot. Robot that once programmed for a given sequence of operations is not easily changed.3. Variable-sequence Robot. Robot that can be programmed for a given sequence of operations and can easily be changed or reprogrammed.4. Playback Robot. Robot that "memorizes" work sequences taught by a human being who physically leads the device through the intended work pattern; the robot can then create this sequence repetitively from memory.5. Numerically Controlled (NC) Robot. Robot that operatas from and is controlled by digital data, as in the form of punched tape, cards, or digital switches; operates like a NC machine.6. Intelligent Robot. Robot that uses sensory perception to evaluate its environment andcmake decisions and proceeds to operate accordingly.The first-generation of robot systems was defined for the various robots with limited computer power. Their main intelligant functions include programming by showing a sequence of manipulation steps by a human operator using a teach box. Without any sensors, these robots require a prearranged and relatively fixed factory environment and, therefore, have limited use.The second-generation of robot systems was enhanced by the addition of a computer processor. A major step in industrial robotics development was the integration of a computer with the industrial robot mechanism. This has provided real-time calculation of trajectory to smooth the motions of the end effector and integration of mine simple force and proximity sensors to obtain external signals.The main applications of second generation robots include spot and arc welding, spray painting, and some assembly.Third-generation robot systems incorporate multiple eomputer processors and multiple arms that can operate asynchronously to perform .several functions. Distributed hierarchical mmputer organization is preferred, because it can coordinate motions and interface with external sensors, other machines, and other robots and can communicate with other computers. These robots can already exhibitintelligent behavior, including knowledge-based control and learning abilities.Japan ranks as the world's top robot-producing and robot-using country, with more than 40% of the world's industrial robot installations. The reasons for this penetration are sociological-and technological factors that are unique to Japan: industrial robots brought productivity and quality gains in Japanese industry, coupled with improvements of the work enviromnent. These have perpetuated the social-demand for more robots as well as increased the expectation from this technology.Current and emerging robot applications in industry can be categorized on the complexity and requirements of the job. They range from simple, low technolngy pick-and place operations through medium technology painting, some assembly and welding operations to high technology precision assembly and inspection operations.Pick-and-place Operations The earliest applications of robots were in machine loading unloading, pick-and-place, and material transfer operations. Such robots typically were not servo controlled and worked with pneumatic or hydraulic power. The Icxad-carrying requirements were high, working in dirty or hazardous factory environments. Replacing unskilled human labor often in hazardous jobs, these robots had to be robust and low in initial and maintenance costs.Painting and Welding Operations The next level in the sophistimtion of industrial robot applications was in spray painting, and spot and arc welding. These applications complemented or replaced certain skilled human labor. Often the justification was by eliminating dangerous environmental exposures. These applications often require tracking complex trajectories such as painting surface mntours, hence mrvo controlled "articulated or spherical robot structures were used.Lead-through teaching modes became commom, and sometimes sophisticated sensors are employed to maintain process consistency. Experience has shown that when properly selected and implemented, thase robotic applications usually lead to reduced overall manufacturing costs and improved product quality compared with manual method.Assembly Operations The most advanced level of technology employing third-generation industrial robots is found in assembly. System repeatability is of utmost importance. End-of-arm tooling must be compliant, i.e., have both force and displacement control to adjust part insertions, which require that the robot actually "feel" its way along. This technology usually requires a measure of artificial intelligence. Assembly robots generally are electronically driven and operate in clean enviromnents. Assembly robots are expected to exceed further technology applications.Other Applications Other typical applications of robots include inspection, quality control, and repair; processing such as laser and water jet cutting and drilling, riveting, and clean room operations; and applications in the wood, paper, and food-processing industries. As industrial robot technology and robot intelligence improve even further, additional applications may be justified effectively.The components of a robot system could be discussed either from a physical point of view or from a systems point of view. Physically, we would divide the system into the robot, power system, and controller (computer). Likewise, the robot itself could be partitioned anthropomorphically into base, shoulder, elbow, wrist, gripper, and tool. Most of these terms require little explanation.Consequently, we will describe the components of a robot system from the point of view of information transfer. That is, what infomtation or signal enters the component; what logical or arithmetic operation does the component perform; and what information or signal does the component produce? It is important to note that the same physical component may perform many different information proees.sirkg operations (e. g. , a central computerperforms many different calculations on different data). Likewise, two physically separate components may perform identical information operations ( e. g., the shoulder and elbow actuators both convert signals to motion in very similar ways).Actuator Asmciated with each joint on the robot is an actuator which causes that joint to move. Typical actuators are electric motors and hydraulic cylinders. Typically, a robot system will contain six actuators, since six are required for full control of position and orientation. Many robot applications do not require this full flexibility, and consequently, robots are often built with five or fewer actuators.Sensor To control an actuator, the computer must have infommtion regarding the position and possibly the velocity of the actuator. In this context, the term position refers to a displacement from some arbitrary zero reference point for that actuator. For example, in the case of a rotary actuator , "position" would really the angular position and be measured in radians.Many types of sensors can provide indications of position and velocity. The various types of sensors require different mechanisms for interfacing to the computer. In addition, the industrial use of the manipulator requires that the interface be protected from the harsh electrical environment of the factory. Sources of electrical noise such as arc welders and large motors can easily makena digital system useless unless care is taken in design and construction of the interface.Computation We could easily have labeled the computation module "computer,"as most of the Functions to be described are typically perfommd by digital computers. However, many of the Functions may be performed in dedicated custom hardware or networks of computers We will, thus, discuss the commputational component as if it were a simple computer, recognizing that tile need for real-time control may require special equipment and that some of this equipment may even be analog, although the current trend is toward fully digital systems.One further note: We will tend to avoid the use of the term microprocessor in this book and simply say computer, although many current robot manufacturers use one or more microprocessors in their systems.The computation component performs the following operations: Servo Given the current position and/or velocity of an actuator, determine the appropriate drivesignal to move that actuator toward its desired position. "This operation must be performed for eaeh actuator. Kinematics Given the current statel of the actuators (position and velocity ),determine the current state of the gripper. Conversely, given a desired state of the hand, determine the desired state for each actuator.Dynamics Given knowledge of the loads on the arm (inertia, friction, gravity, acceleration), use this information to adjust the sorvo operation to achieve better performance.Workplace Sensor Analysis Given knowledge of the task to be performed, determine appropriate robot motion commands. This nmy include analyzing a TV picture of the workplace or measuring and compensating for forces applied at the hand.In addition to these easily identified co. mponents, there are also supervisory operations such as path planning and operator interaction.中文翻译工业机器人及其系统组成有许多关于机器人这个术语的定义。