有色金属加工-板材轧制
有色金属扎制
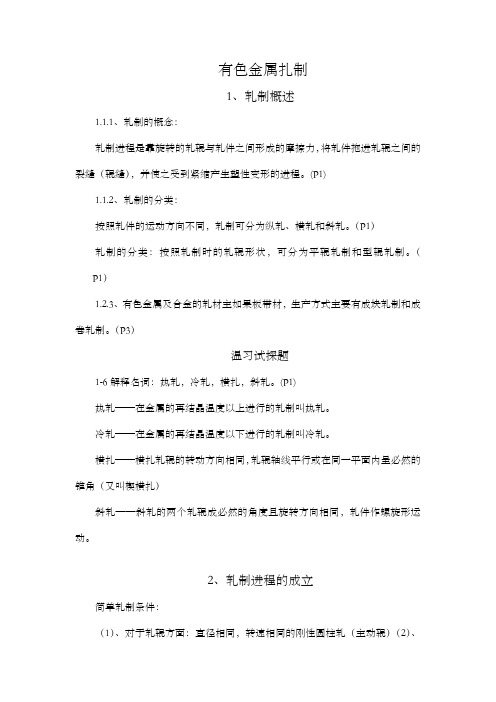
有色金属扎制1、轧制概述1.1.1、轧制的概念:轧制进程是靠旋转的轧辊与轧件之间形成的摩擦力,将轧件拖进轧辊之间的裂缝(辊缝),并使之受到紧缩产生塑性变形的进程。
(P1)1.1.2、轧制的分类:按照轧件的运动方向不同,轧制可分为纵轧、横轧和斜轧。
(P1)轧制的分类:按照轧制时的轧辊形状,可分为平辊轧制和型辊轧制。
(P1)1.2.3、有色金属及合金的轧材主如果板带材,生产方式主要有成块轧制和成卷轧制。
(P3)温习试探题1-6解释名词:热轧,冷轧,横扎,斜轧。
(P1)热轧——在金属的再结晶温度以上进行的轧制叫热轧。
冷轧——在金属的再结晶温度以下进行的轧制叫冷轧。
横扎——横扎轧辊的转动方向相同,轧辊轴线平行或在同一平面内呈必然的锥角(又叫楔横扎)斜轧——斜轧的两个轧辊成必然的角度且旋转方向相同,轧件作螺旋形运动。
2、轧制进程的成立简单轧制条件:(1)、对于轧辊方面:直径相同,转速相同的刚性圆柱轧(主动辊)(2)、对于轧件方面:轧制前后轧件的断面均为矩形或方形,轧件内部各部份组织和性能相同(性能均匀)(P70)、变形区的主要参数:2.2.2、轧辊咬入轧件的条件:β≧α(2-3)轧辊与轧件之间的摩擦系数f必需大于等于咬入角α的正切值,或轧辊与轧件之间的摩擦角β必需大于等于咬入角α。
(P9)2.2.4、成立稳固轧制状态后的轧制条件:继续进行轧制的条件: β≧α或α≦2β(P9)2.2.6改善咬入的大体办法:(1)适当增大轧辊与扎件间的摩擦系数。
(2)适当减小咬入角。
(P11)2.3.1、平均工作辊经:平辊的工作辊径Dκ就是轧辊的实际直径,它与轧辊的假想原始直径D的关系为:Dκ=D-h (2-7)式中h——轧件的扎后厚度,平辊轧制时等于辊缝值(P12)假想原始直径是以为两轧辊靠拢,没有辊缝是两轧辊轴线见距离。
在箱形孔型中轧制时工作辊径为孔型的槽底直径,它与辊环直径D’的关系为:Dκ= D’-(h-s)(2-8)式中S—辊缝值(P12)2.3.2平均压下量:不平均紧缩平均压下量为:△h=H-h=Q/B-q/b (2-11)式中Q,B——别离为轧制前轧件横断面积和轧件宽度q,b——别离为轧制后轧件横断面积和轧件宽度(P12)、三种典型轧制情形:实验证明,对同一金属在不同温度、速度条件下,决定轧制进程本质的主要因素是轧件和轧辊尺寸。
有色金属深加工行业现状分析
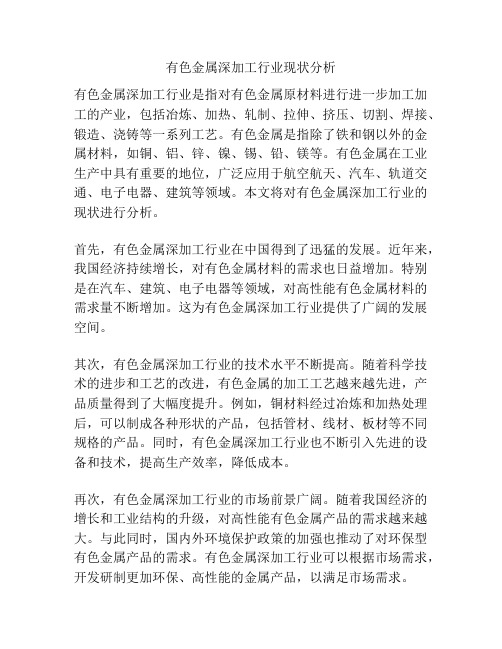
有色金属深加工行业现状分析有色金属深加工行业是指对有色金属原材料进行进一步加工加工的产业,包括冶炼、加热、轧制、拉伸、挤压、切割、焊接、锻造、浇铸等一系列工艺。
有色金属是指除了铁和钢以外的金属材料,如铜、铝、锌、镍、锡、铅、镁等。
有色金属在工业生产中具有重要的地位,广泛应用于航空航天、汽车、轨道交通、电子电器、建筑等领域。
本文将对有色金属深加工行业的现状进行分析。
首先,有色金属深加工行业在中国得到了迅猛的发展。
近年来,我国经济持续增长,对有色金属材料的需求也日益增加。
特别是在汽车、建筑、电子电器等领域,对高性能有色金属材料的需求量不断增加。
这为有色金属深加工行业提供了广阔的发展空间。
其次,有色金属深加工行业的技术水平不断提高。
随着科学技术的进步和工艺的改进,有色金属的加工工艺越来越先进,产品质量得到了大幅度提升。
例如,铜材料经过冶炼和加热处理后,可以制成各种形状的产品,包括管材、线材、板材等不同规格的产品。
同时,有色金属深加工行业也不断引入先进的设备和技术,提高生产效率,降低成本。
再次,有色金属深加工行业的市场前景广阔。
随着我国经济的增长和工业结构的升级,对高性能有色金属产品的需求越来越大。
与此同时,国内外环境保护政策的加强也推动了对环保型有色金属产品的需求。
有色金属深加工行业可以根据市场需求,开发研制更加环保、高性能的金属产品,以满足市场需求。
然而,有色金属深加工行业也面临一些挑战。
首先,随着市场竞争的加剧,产品同质化程度较高,有色金属深加工企业需要加强创新能力,提高产品附加值,才能在竞争激烈的市场中脱颖而出。
其次,由于有色金属深加工行业生产过程中产生大量的废气、废水和废渣,环保压力逐渐增大。
企业需要加强环境保护设施建设和技术改造,提高资源利用效率,减少对环境的污染。
面对这些挑战,有色金属深加工行业可以采取以下几种策略。
首先,加强技术研发和创新,开发出更加环保、高性能的产品,提高竞争力。
其次,与上下游企业建立良好的合作关系,形成产业链协作,提高整体供应链的效率。
有色金属压力加工原理考试复习资料(题)
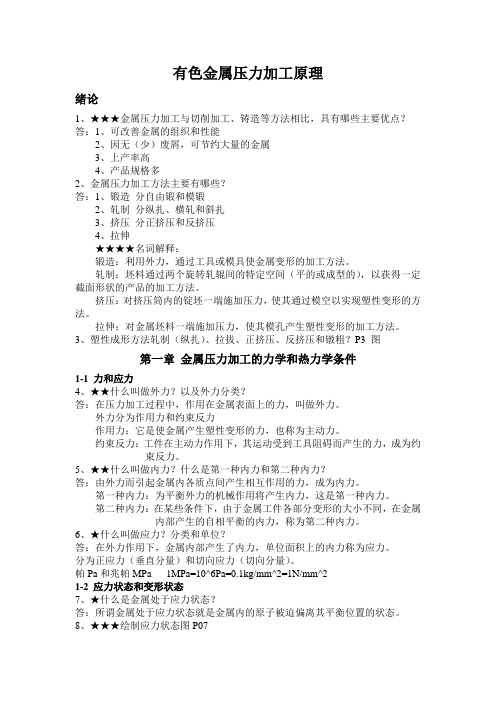
有色金属压力加工原理绪论1、★★★金属压力加工与切削加工、铸造等方法相比,具有哪些主要优点?答:1、可改善金属的组织和性能2、因无(少)废屑,可节约大量的金属3、上产率高4、产品规格多2、金属压力加工方法主要有哪些?答:1、锻造分自由锻和模锻2、轧制分纵扎、横轧和斜扎3、挤压分正挤压和反挤压4、拉伸★★★★名词解释:锻造:利用外力,通过工具或模具使金属变形的加工方法。
轧制:坯料通过两个旋转轧辊间的特定空间(平的或成型的),以获得一定截面形状的产品的加工方法。
挤压:对挤压筒内的锭坯一端施加压力,使其通过模空以实现塑性变形的方法。
拉伸:对金属坯料一端施加压力,使其模孔产生塑性变形的加工方法。
3、塑性成形方法轧制(纵扎)、拉拔、正挤压、反挤压和镦粗?P3 图第一章金属压力加工的力学和热力学条件1-1 力和应力4、★★什么叫做外力?以及外力分类?答:在压力加工过程中,作用在金属表面上的力,叫做外力。
外力分为作用力和约束反力作用力:它是使金属产生塑性变形的力,也称为主动力。
约束反力:工件在主动力作用下,其运动受到工具阻碍而产生的力,成为约束反力。
5、★★什么叫做内力?什么是第一种内力和第二种内力?答:由外力而引起金属内各质点间产生相互作用的力,成为内力。
第一种内力:为平衡外力的机械作用将产生内力,这是第一种内力。
第二种内力:在某些条件下,由于金属工件各部分变形的大小不同,在金属内部产生的自相平衡的内力,称为第二种内力。
6、★什么叫做应力?分类和单位?答:在外力作用下,金属内部产生了内力,单位面积上的内力称为应力。
分为正应力(垂直分量)和切向应力(切向分量)。
帕Pa和兆帕MPa 1MPa=10^6Pa=0.1kg/mm^2=1N/mm^21-2 应力状态和变形状态7、★什么是金属处于应力状态?答:所谓金属处于应力状态就是金属内的原子被迫偏离其平衡位置的状态。
8、★★★绘制应力状态图P079、★什么是主应力状态、主应力、主平面、主切平面、主切应力?答:金属在实际变形过程中,存在着这样的应力状态,即在变形区某点的单元六面体上只作用着正应力,没有切应力,我们把这样的应力状态称之为主应力状态。
轧材种类及其生产工艺流程
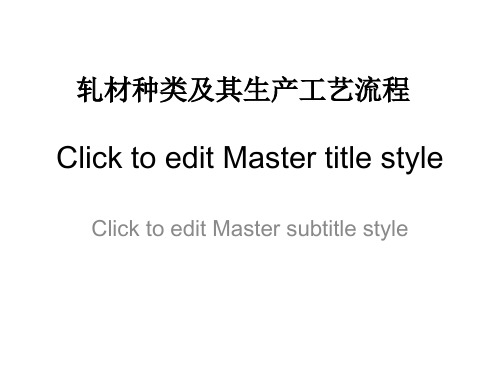
7.1轧材的种类
• 按金属与合金种类的不同,可分为各种钢 材以及铜、铝、钛等有色金属与合金材料 ;
• 按轧材断面形状尺寸的不同,又可分为各 种规格的板材、带材、型材、线材、管材 及特殊品种材料等。
钢材的种类
• 各种钢材是应用最广泛的轧材,按钢种不同可分为普通 碳素钢材、优质碳素钢材、低合金钢材及合金钢材等。
有色金属及合金的轧材
• 在有色金属及合金的轧材中,通常应用较广的 主要是铝、铜、钛等及其合金的轧材,其价格要 比钢材贵得多。
• 纯铝强度较低,要加入其它合金元素制成铝合 金才能做结构材科使用。
• 一般轧制铝合金可分为铝(L)、硬铝(LY)、超硬 铝(Lc)、防锈铝(LF)及待殊铝(LT)等数种;
• 也可按热处理特点不同分为可热处理强化的铝 合金和不可热处理强化的铝合金两大类,每类 又各为很多不同的合金系。
• (2)新技术越来越多地应用于轧钢生产。计算机控制 、液压技术、板型控制、控轧控冷等技术使轧制过程 向最佳化,轧制产品向最优化发展。
• (3)塑性加工基础理论的发展使轧制过程模型化。建 立各种生产条件下的轧制数学模型、综合力学模型, 利用计算机控制生产过程,使工艺技术向工程科学迈 进。
• (4)利用最优化技术确定最佳参数和工艺制度,优化 生产过程。以便优质、高产、低消耗、低成本地生产 各种钢材。
轧材种类及其生产工艺流程
Click to edit Master title style
Click to edit Master subtitle style
轧钢生产慨述
• 轧钢生产的重要性 • 钢铁是广泛应用的一种材料。在工业、农业、交通、
轧制成型的原理和应用
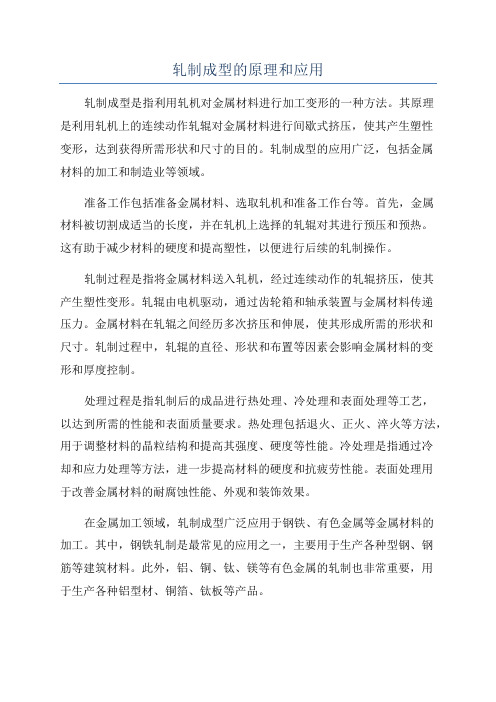
轧制成型的原理和应用轧制成型是指利用轧机对金属材料进行加工变形的一种方法。
其原理是利用轧机上的连续动作轧辊对金属材料进行间歇式挤压,使其产生塑性变形,达到获得所需形状和尺寸的目的。
轧制成型的应用广泛,包括金属材料的加工和制造业等领域。
准备工作包括准备金属材料、选取轧机和准备工作台等。
首先,金属材料被切割成适当的长度,并在轧机上选择的轧辊对其进行预压和预热。
这有助于减少材料的硬度和提高塑性,以便进行后续的轧制操作。
轧制过程是指将金属材料送入轧机,经过连续动作的轧辊挤压,使其产生塑性变形。
轧辊由电机驱动,通过齿轮箱和轴承装置与金属材料传递压力。
金属材料在轧辊之间经历多次挤压和伸展,使其形成所需的形状和尺寸。
轧制过程中,轧辊的直径、形状和布置等因素会影响金属材料的变形和厚度控制。
处理过程是指轧制后的成品进行热处理、冷处理和表面处理等工艺,以达到所需的性能和表面质量要求。
热处理包括退火、正火、淬火等方法,用于调整材料的晶粒结构和提高其强度、硬度等性能。
冷处理是指通过冷却和应力处理等方法,进一步提高材料的硬度和抗疲劳性能。
表面处理用于改善金属材料的耐腐蚀性能、外观和装饰效果。
在金属加工领域,轧制成型广泛应用于钢铁、有色金属等金属材料的加工。
其中,钢铁轧制是最常见的应用之一,主要用于生产各种型钢、钢筋等建筑材料。
此外,铝、铜、钛、镁等有色金属的轧制也非常重要,用于生产各种铝型材、铜箔、钛板等产品。
在制造业中,轧制成型用于生产各种金属制品。
例如,汽车工业中的车身和发动机零部件、航空航天工业中的飞机零部件、电子工业中的散热器等。
此外,轧制成型还用于各种管道、容器、锅炉、轴承及压力容器等的生产。
总之,轧制成型作为加工金属材料的重要方法,具有高效、精度高和成本低等优点。
通过合理的轧辊的设计和选择,可以实现对金属材料的变形控制和形状调整,以满足不同行业对于金属制品的需求。
轧制综述
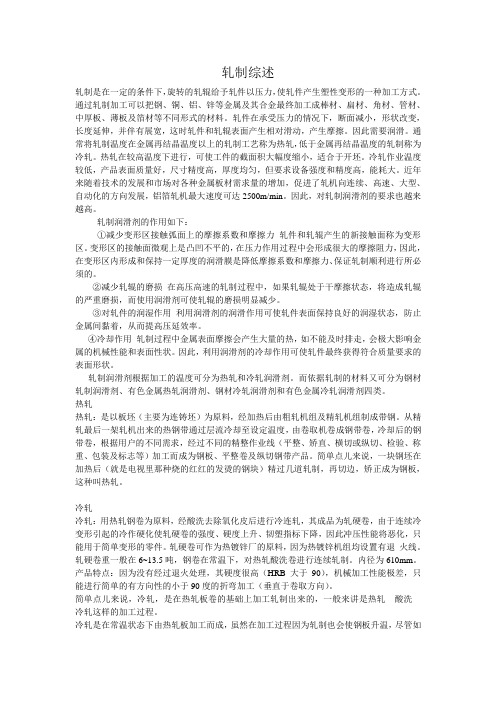
轧制综述轧制是在一定的条件下,旋转的轧辊给予轧件以压力,使轧件产生塑性变形的一种加工方式。
通过轧制加工可以把钢、铜、铝、锌等金属及其合金最终加工成棒材、扁材、角材、管材、中厚板、薄板及箔材等不同形式的材料。
轧件在承受压力的情况下,断面减小,形状改变,长度延伸,并伴有展宽,这时轧件和轧辊表面产生相对滑动,产生摩擦。
因此需要润滑。
通常将轧制温度在金属再结晶温度以上的轧制工艺称为热轧,低于金属再结晶温度的轧制称为冷轧。
热轧在较高温度下进行,可使工件的截面积大幅度缩小,适合于开坯。
冷轧作业温度较低,产品表面质量好,尺寸精度高,厚度均匀,但要求设备强度和精度高,能耗大。
近年来随着技术的发展和市场对各种金属板材需求量的增加,促进了轧机向连续、高速、大型、自动化的方向发展,铝箔轧机最大速度可达2500m/min。
因此,对轧制润滑剂的要求也越来越高。
轧制润滑剂的作用如下:①减少变形区接触弧面上的摩擦系数和摩擦力轧件和轧辊产生的新接触面称为变形区。
变形区的接触面微观上是凸凹不平的,在压力作用过程中会形成很大的摩擦阻力,因此,在变形区内形成和保持一定厚度的润滑膜是降低摩擦系数和摩擦力、保证轧制顺利进行所必须的。
②减少轧辊的磨损在高压高速的轧制过程中,如果轧辊处于干摩擦状态,将造成轧辊的严重磨损,而使用润滑剂可使轧辊的磨损明显减少。
③对轧件的润湿作用利用润滑剂的润滑作用可使轧件表面保持良好的润湿状态,防止金属间黏着,从而提高压延效率。
④冷却作用轧制过程中金属表面摩擦会产生大量的热,如不能及时排走,会极大影响金属的机械性能和表面性状。
因此,利用润滑剂的冷却作用可使轧件最终获得符合质量要求的表面形状。
轧制润滑剂根据加工的温度可分为热轧和冷轧润滑剂。
而依据轧制的材料又可分为钢材轧制润滑剂、有色金属热轧润滑剂、钢材冷轧润滑剂和有色金属冷轧润滑剂四类。
热轧热轧:是以板坯(主要为连铸坯)为原料,经加热后由粗轧机组及精轧机组制成带钢。
《金属的轧制》课件
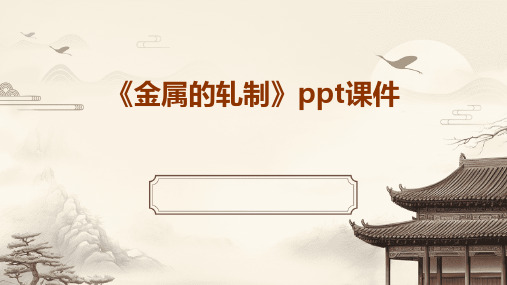
CATALOGUE
目 录
• 轧制技术概述 • 轧制的基本原理 • 轧制工艺流程 • 轧制设备与工具 • 轧制技术的发展趋势与展望
01
CATALOGUE
轧制技术概述
轧制技术的定义
轧制技术是通过旋转轧辊对金属施加压力,使其发生连续塑性变形的工艺过程。
轧制技术的基本原理是利用轧辊与金属之间的摩擦力,使金属产生连续的塑性变形 ,从而获得所需形状和性能的金属制品。
。
通过引入先进的传感器、控制 器和优化算法,实现对轧制过 程的实时监测和控制,提高产
品质量和生产效率。
智能化与自动化的轧制过程可 以减少人工干预和操作误差, 提高生产安全性和稳定性。
未来轧制过程的智能化与自动 化将进一步发展,实现更加智 能化的生产管理和决策支持。
新材料与新工艺的轧制技术探索
01 02 03 04
粗轧机
用于进一步轧制原料,使其接近成品 尺寸,通常具有中等轧制压力和道次 数。
精轧机
用于最终轧制成品,具有较小的轧制 压力和较多的道次数,以确保产品精 度和表面质量。
连轧机
多台轧机连续排列,实现连续轧制, 提高生产效率和产品质量。
轧辊的类型与材料选择
热轧辊
承受高温和较大轧制力,通常选 用高硬度和耐热性好的材料,如
随着新材料和新工艺的不断涌现,轧制技术也在不断探索和创新。
新材料如高强度钢、不锈钢、钛合金等具有更高的强度和耐腐蚀性能 ,需要新的轧制技术和工艺来满足其加工要求。
新工艺如轧制复合技术、轧制变形控制技术等可以显著提高产品质量 和性能,满足更加复杂和多样化的市场需求。
探索新材料与新工艺的轧制技术需要不断投入研发力量,加强产学研 合作和技术交流,推动轧制技术的不断创新和发展。
轧制的工艺
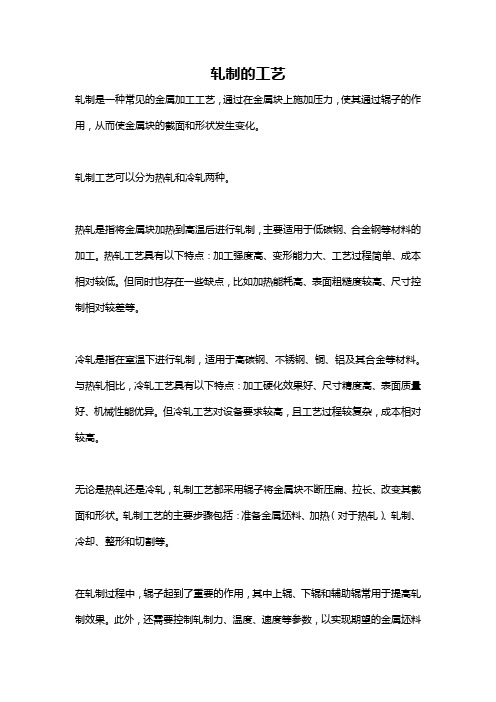
轧制的工艺
轧制是一种常见的金属加工工艺,通过在金属块上施加压力,使其通过辊子的作用,从而使金属块的截面和形状发生变化。
轧制工艺可以分为热轧和冷轧两种。
热轧是指将金属块加热到高温后进行轧制,主要适用于低碳钢、合金钢等材料的加工。
热轧工艺具有以下特点:加工强度高、变形能力大、工艺过程简单、成本相对较低。
但同时也存在一些缺点,比如加热能耗高、表面粗糙度较高、尺寸控制相对较差等。
冷轧是指在室温下进行轧制,适用于高碳钢、不锈钢、铜、铝及其合金等材料。
与热轧相比,冷轧工艺具有以下特点:加工硬化效果好、尺寸精度高、表面质量好、机械性能优异。
但冷轧工艺对设备要求较高,且工艺过程较复杂,成本相对较高。
无论是热轧还是冷轧,轧制工艺都采用辊子将金属块不断压扁、拉长、改变其截面和形状。
轧制工艺的主要步骤包括:准备金属坯料、加热(对于热轧)、轧制、冷却、整形和切割等。
在轧制过程中,辊子起到了重要的作用,其中上辊、下辊和辅助辊常用于提高轧制效果。
此外,还需要控制轧制力、温度、速度等参数,以实现期望的金属坯料
的形状和尺寸。
轧制工艺广泛应用于钢铁、有色金属和合金等行业,被广泛用于制造板材、线材、管材等金属制品。
热轧工艺参数对板材性能的影响研究
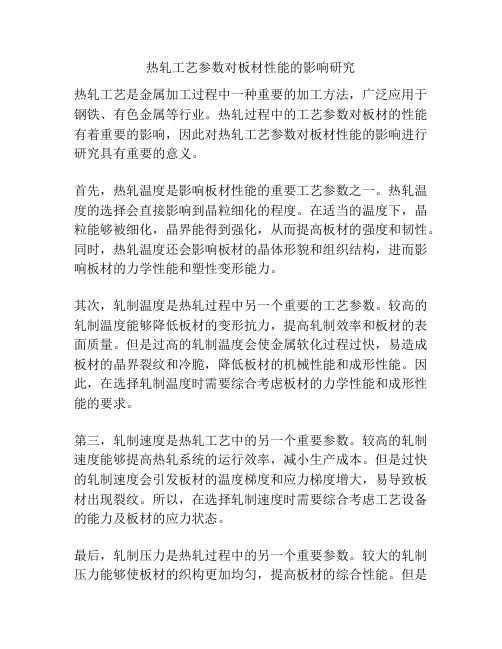
热轧工艺参数对板材性能的影响研究热轧工艺是金属加工过程中一种重要的加工方法,广泛应用于钢铁、有色金属等行业。
热轧过程中的工艺参数对板材的性能有着重要的影响,因此对热轧工艺参数对板材性能的影响进行研究具有重要的意义。
首先,热轧温度是影响板材性能的重要工艺参数之一。
热轧温度的选择会直接影响到晶粒细化的程度。
在适当的温度下,晶粒能够被细化,晶界能得到强化,从而提高板材的强度和韧性。
同时,热轧温度还会影响板材的晶体形貌和组织结构,进而影响板材的力学性能和塑性变形能力。
其次,轧制温度是热轧过程中另一个重要的工艺参数。
较高的轧制温度能够降低板材的变形抗力,提高轧制效率和板材的表面质量。
但是过高的轧制温度会使金属软化过程过快,易造成板材的晶界裂纹和冷脆,降低板材的机械性能和成形性能。
因此,在选择轧制温度时需要综合考虑板材的力学性能和成形性能的要求。
第三,轧制速度是热轧工艺中的另一个重要参数。
较高的轧制速度能够提高热轧系统的运行效率,减小生产成本。
但是过快的轧制速度会引发板材的温度梯度和应力梯度增大,易导致板材出现裂纹。
所以,在选择轧制速度时需要综合考虑工艺设备的能力及板材的应力状态。
最后,轧制压力是热轧过程中的另一个重要参数。
较大的轧制压力能够使板材的织构更加均匀,提高板材的综合性能。
但是过大的轧制压力容易引发板材的变形抗力增大,导致设备负荷过大。
因此,在选择轧制压力时需要综合考虑设备的能力和板材的性能要求。
在研究热轧工艺参数对板材性能的影响时,可以采用实验和数值模拟的方法进行。
通过实验,可以获得不同工艺参数下的板材性能数据,从而分析工艺参数对板材性能的影响规律。
而数值模拟可以模拟出热轧工艺过程中的温度场、应力场和应变场等相关参数,进一步分析和预测不同工艺参数对板材性能的影响。
综上所述,热轧工艺参数对板材性能有着重要的影响。
在进行热轧过程中,合理选择和控制工艺参数,能够使板材获得较好的力学性能和成形性能,并具有更好的应用价值。
有色金属加工技术与生产作业指导书
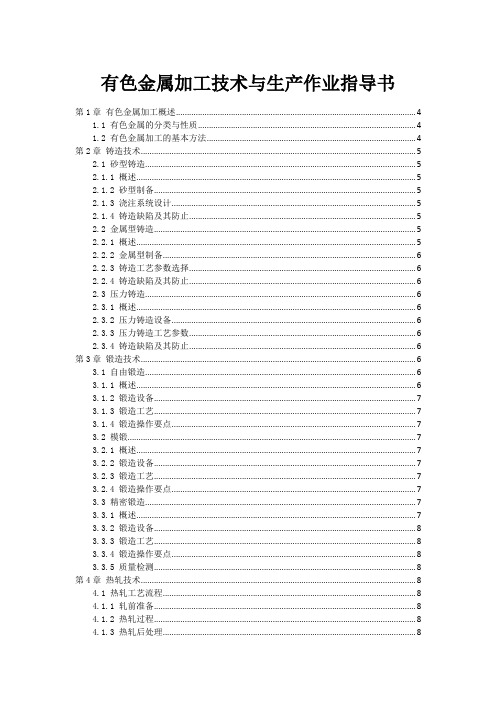
有色金属加工技术与生产作业指导书第1章有色金属加工概述 (4)1.1 有色金属的分类与性质 (4)1.2 有色金属加工的基本方法 (4)第2章铸造技术 (5)2.1 砂型铸造 (5)2.1.1 概述 (5)2.1.2 砂型制备 (5)2.1.3 浇注系统设计 (5)2.1.4 铸造缺陷及其防止 (5)2.2 金属型铸造 (5)2.2.1 概述 (5)2.2.2 金属型制备 (6)2.2.3 铸造工艺参数选择 (6)2.2.4 铸造缺陷及其防止 (6)2.3 压力铸造 (6)2.3.1 概述 (6)2.3.2 压力铸造设备 (6)2.3.3 压力铸造工艺参数 (6)2.3.4 铸造缺陷及其防止 (6)第3章锻造技术 (6)3.1 自由锻造 (6)3.1.1 概述 (6)3.1.2 锻造设备 (7)3.1.3 锻造工艺 (7)3.1.4 锻造操作要点 (7)3.2 模锻 (7)3.2.1 概述 (7)3.2.2 锻造设备 (7)3.2.3 锻造工艺 (7)3.2.4 锻造操作要点 (7)3.3 精密锻造 (7)3.3.1 概述 (7)3.3.2 锻造设备 (8)3.3.3 锻造工艺 (8)3.3.4 锻造操作要点 (8)3.3.5 质量检测 (8)第4章热轧技术 (8)4.1 热轧工艺流程 (8)4.1.1 轧前准备 (8)4.1.2 热轧过程 (8)4.1.3 热轧后处理 (8)4.2.1 设备选型 (9)4.2.2 工艺参数 (9)4.3 热轧产品质量控制 (9)4.3.1 原料质量控制 (9)4.3.2 加热质量控制 (9)4.3.3 轧制过程质量控制 (9)4.3.4 成品质量控制 (9)4.3.5 质量改进 (9)第5章冷轧技术 (10)5.1 冷轧工艺流程 (10)5.1.1 原材料准备 (10)5.1.2 热轧 (10)5.1.3 冷轧 (10)5.1.4 退火 (10)5.1.5 精整 (10)5.2 冷轧设备与工艺参数 (10)5.2.1 冷轧设备 (10)5.2.2 工艺参数 (10)5.3 冷轧产品质量控制 (10)5.3.1 原材料质量控制 (10)5.3.2 轧制过程质量控制 (11)5.3.3 退火过程质量控制 (11)5.3.4 精整过程质量控制 (11)第6章精密切削加工 (11)6.1 车削加工 (11)6.1.1 概述 (11)6.1.2 工艺参数 (11)6.1.3 切削工具 (11)6.1.4 操作要点 (12)6.2 铣削加工 (12)6.2.1 概述 (12)6.2.2 工艺参数 (12)6.2.3 切削工具 (12)6.2.4 操作要点 (12)6.3 钻削加工 (12)6.3.1 概述 (12)6.3.2 工艺参数 (12)6.3.3 切削工具 (13)6.3.4 操作要点 (13)第7章特种加工技术 (13)7.1 电化学加工 (13)7.1.1 概述 (13)7.1.2 基本原理 (13)7.1.4 应用领域 (13)7.2 高能束加工 (14)7.2.1 概述 (14)7.2.2 基本原理 (14)7.2.3 加工特点 (14)7.2.4 应用领域 (14)7.3 超声波加工 (14)7.3.1 概述 (14)7.3.2 基本原理 (14)7.3.3 加工特点 (14)7.3.4 应用领域 (15)第8章表面处理技术 (15)8.1 表面清理与预处理 (15)8.1.1 清理方法 (15)8.1.2 预处理工艺 (15)8.2 表面涂覆层制备 (15)8.2.1 涂覆方法 (15)8.2.2 涂覆材料 (15)8.2.3 涂覆工艺 (15)8.3 表面处理质量检测 (15)8.3.1 检测方法 (15)8.3.2 检测标准 (15)8.3.3 检测仪器与设备 (15)8.3.4 质量控制 (16)第9章有色金属连接技术 (16)9.1 焊接连接 (16)9.1.1 概述 (16)9.1.2 焊接方法 (16)9.1.3 焊接材料 (16)9.1.4 焊接工艺参数 (16)9.2 胶接连接 (16)9.2.1 概述 (16)9.2.2 胶粘剂 (16)9.2.3 胶接工艺 (16)9.3 机械连接 (17)9.3.1 概述 (17)9.3.2 紧固件 (17)9.3.3 连接工艺 (17)9.3.4 检验 (17)第10章生产作业管理 (17)10.1 生产计划与调度 (17)10.1.1 计划编制 (17)10.1.2 调度管理 (17)10.2.1 工艺参数控制 (17)10.2.2 设备维护与管理 (17)10.2.3 操作人员培训与管理 (18)10.3 质量管理与售后服务 (18)10.3.1 质量管理体系 (18)10.3.2 检验与检测 (18)10.3.3 售后服务 (18)10.3.4 客户满意度调查与改进 (18)第1章有色金属加工概述1.1 有色金属的分类与性质有色金属是指除了铁、锰、铬以外的所有金属,以及金属间化合物。
必学-金属材料热处理轧制原理基本理论知识
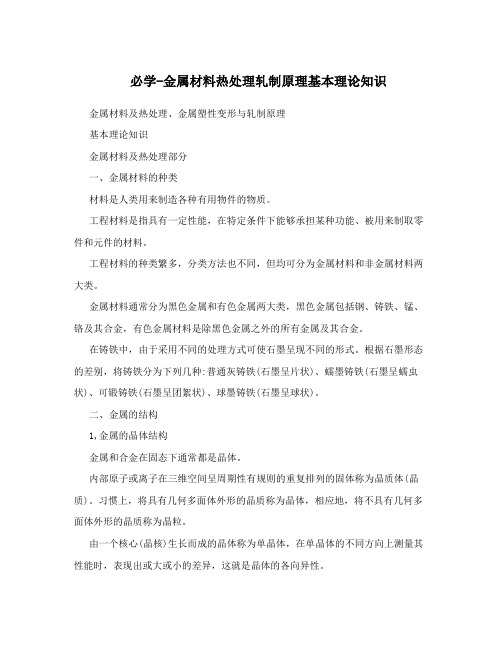
必学-金属材料热处理轧制原理基本理论知识金属材料及热处理、金属塑性变形与轧制原理基本理论知识金属材料及热处理部分一、金属材料的种类材料是人类用来制造各种有用物件的物质。
工程材料是指具有一定性能,在特定条件下能够承担某种功能、被用来制取零件和元件的材料。
工程材料的种类繁多,分类方法也不同,但均可分为金属材料和非金属材料两大类。
金属材料通常分为黑色金属和有色金属两大类,黑色金属包括钢、铸铁、锰、铬及其合金,有色金属材料是除黑色金属之外的所有金属及其合金。
在铸铁中,由于采用不同的处理方式可使石墨呈现不同的形式。
根据石墨形态的差别,将铸铁分为下列几种:普通灰铸铁(石墨呈片状)、蠕墨铸铁(石墨呈蠕虫状)、可锻铸铁(石墨呈团絮状)、球墨铸铁(石墨呈球状)。
二、金属的结构1,金属的晶体结构金属和合金在固态下通常都是晶体。
内部原子或离子在三维空间呈周期性有规则的重复排列的固体称为晶质体(晶质)。
习惯上,将具有几何多面体外形的晶质称为晶体,相应地,将不具有几何多面体外形的晶质称为晶粒。
由一个核心(晶核)生长而成的晶体称为单晶体,在单晶体的不同方向上测量其性能时,表现出或大或小的差异,这就是晶体的各向异性。
金属材料通常由许多不同位向的小晶粒所组成,称为多晶体;多晶体中各晶粒的各向异性互相抵消,故一般不显示各向异性,所以在工业用的金属材料中,通常见不到各向异性特征,称之为伪各向同性。
工业上使用的金属元素中,除了少数具有复杂的晶体结构外,绝大多数都具有比较简单的晶体结构,其中最典型、最常见的金属晶体结构有三种类型,即体心立方结构,面心立方结构和密排六方结构。
2,金属的同素异构转变大部分金属只有一种晶体结构,但也有少数金属如Fe、Mn、Ti、Co等具有两种或几种不同的晶体结构,即具有多晶型。
当外部条件(如温度和压力)改变时,金属可能由一种晶体结构转变成另一种晶体结构。
这种固态金属在不同温度下具有不同晶格的现象称为多晶型性或同素异晶性。
轧制工艺2
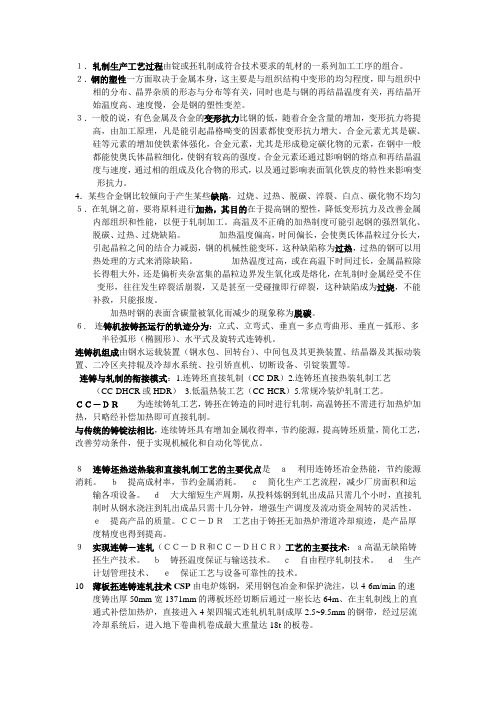
1.轧制生产工艺过程由锭或抷轧制成符合技术要求的轧材的一系列加工工序的组合。
2.钢的塑性一方面取决于金属本身,这主要是与组织结构中变形的均匀程度,即与组织中相的分布、晶界杂质的形态与分布等有关,同时也是与钢的再结晶温度有关,再结晶开始温度高、速度慢,会是钢的塑性变差。
3.一般的说,有色金属及合金的变形抗力比钢的低,随着合金含量的增加,变形抗力将提高,由加工原理,凡是能引起晶格畸变的因素都使变形抗力增大。
合金元素尤其是碳、硅等元素的增加使铁素体强化,合金元素,尤其是形成稳定碳化物的元素,在钢中一般都能使奥氏体晶粒细化,使钢有较高的强度。
合金元素还通过影响钢的熔点和再结晶温度与速度,通过相的组成及化合物的形式,以及通过影响表面氧化铁皮的特性来影响变形抗力。
4.某些合金钢比较倾向于产生某些缺陷,过烧、过热、脱碳、淬裂、白点、碳化物不均匀5.在轧钢之前,要将原料进行加热,其目的在于提高钢的塑性,降低变形抗力及改善金属内部组织和性能,以便于轧制加工。
高温及不正确的加热制度可能引起钢的强烈氧化、脱碳、过热、过烧缺陷。
加热温度偏高,时间偏长,会使奥氏体晶粒过分长大,引起晶粒之间的结合力减弱,钢的机械性能变坏,这种缺陷称为过热,过热的钢可以用热处理的方式来消除缺陷。
加热温度过高,或在高温下时间过长,金属晶粒除长得粗大外,还是偏析夹杂富集的晶粒边界发生氧化或是熔化,在轧制时金属经受不住变形,往往发生碎裂活崩裂,又是甚至一受碰撞即行碎裂,这种缺陷成为过烧,不能补救,只能报废。
加热时钢的表面含碳量被氧化而减少的现象称为脱碳。
6.连铸机按铸抷运行的轨迹分为:立式、立弯式、垂直-多点弯曲形、垂直-弧形、多半径弧形(椭圆形)、水平式及旋转式连铸机。
连铸机组成由钢水运载装置(钢水包、回转台)、中间包及其更换装置、结晶器及其振动装置、二冷区夹持辊及冷却水系统、拉引矫直机、切断设备、引锭装置等。
连铸与轧制的衔接模式:1.连铸坯直接轧制(CC-DR)2.连铸坯直接热装轧制工艺(CC-DHCR或HDR)3.低温热装工艺(CC-HCR)5.常规冷装炉轧制工艺。
轧 制
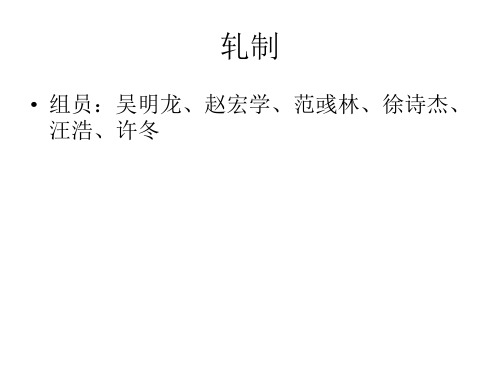
R h
Ψ-力臂系数,一般取0.3-0.6
(b0 b1 ) M p Rh 2
在简单轧制情况下,驱动两辊的轧制力矩
M M1 M 2
M pRh (b0 b1 )
3.2.2 轧制方法 1. 按轧制温度分类
压下系数 h0 h1 压下率 h h 100 % 0 l 延伸系数 1 l0 宽展 b b1 b0
2. 轧制过程的金属流动
设:轧件无宽展,垂直截面水平流动速度相同,则按体积不变条件可知, 变形区流动速度变化: • • • 在轧辊入口:金属的流动速率 < 轧辊表面圆周速度 在轧辊出口:金属的流动速率 > 轧辊表面圆周速度 则在变形区存在一个金属流速 = 轧辊表面园周速度的地方→中性面
使用轧机:单机架可逆式、连续式。 产品一般以卷供应。
(2)工艺流程:
一般工艺流程为:热轧卷料→酸洗→冷轧→退火→平整
二、管材轧制
管材是金属中使用最广的产品,尤其是钢材,就钢管而
言,一般尺度范围为:ф0.1--4000mm 生产方法: X 0.01—100mm。
•
无缝管
热轧无缝钢管 冷轧无缝钢管
1.线材轧制特点 ① 总延伸率大,轧制温降快,头尾温差大,轧速高(100m/s)
② 机架多,分工细
③ 具特殊孔型系统 • 多辊孔型系统
• 45°轧机孔型系统
(a)多辊孔型系统:三角—弧边、三角-圆孔型系统 (b)45°轧机孔型系统:椭-椭-圆、弧菱-弧菱-圆、 椭-圆-椭-圆、平-平-椭-圆
3.线材控制冷却线
板带材的几何外形特征用宽厚比B/H表征。
有色金属压延加工行业市场前景分析

有色金属压延加工行业市场前景分析有色金属压延加工行业是有色金属产业链中的重要环节,它将有色金属原材料通过一系列的加工工艺,如轧制、拉伸、挤压等,制成各种板材、带材、管材、棒材等产品,广泛应用于建筑、交通、电子、机械等众多领域。
近年来,随着全球经济的发展和技术的进步,有色金属压延加工行业也呈现出一些新的发展趋势和特点,其市场前景备受关注。
一、行业现状目前,有色金属压延加工行业在全球范围内已经形成了一定的产业规模。
在生产技术方面,不断有新的工艺和设备被引入,提高了生产效率和产品质量。
同时,企业的规模也在逐渐扩大,一些大型企业通过并购重组等方式,增强了自身的市场竞争力。
从市场需求来看,建筑、汽车、电子等行业对有色金属压延制品的需求持续增长。
特别是在新兴产业的推动下,如新能源汽车、5G 通信等,对高性能、高精度的有色金属压延产品的需求更为迫切。
然而,行业发展也面临着一些挑战。
例如,原材料价格的波动给企业的成本控制带来了较大压力;环保要求的日益严格,使得企业需要加大环保投入;此外,国际市场的贸易保护主义也对行业的出口造成了一定的影响。
二、市场前景的有利因素(一)经济增长带动需求全球经济的持续增长,尤其是新兴经济体的快速发展,将带动基础设施建设、制造业等领域的投资,从而增加对有色金属压延产品的需求。
例如,城市化进程的加速,需要大量的建筑用铝材和钢材;工业制造的升级,对高精度的铜材、铝材等有更高的需求。
(二)新兴产业的发展新能源汽车、光伏、风能等新兴产业的崛起,为有色金属压延加工行业带来了新的机遇。
新能源汽车的电池、电机等部件需要大量的铜箔、铝箔等材料;光伏产业中的太阳能电池板边框通常采用铝合金材料;风能发电设备中的叶片、塔架等也离不开有色金属压延制品。
(三)技术进步推动创新随着科技的不断进步,有色金属压延加工技术也在不断创新。
例如,连续铸轧、精密轧制等技术的应用,提高了产品的性能和质量,拓展了应用领域。
同时,材料科学的发展也为研发新型有色金属压延材料提供了可能。
金属塑性加工技术5-有色金属板带材生产

连铸连轧工艺流程
熔炼、连铸、轧制、冷却、卷 取等环节组成,具有高效、节 能、环保等优点。
连铸连轧设备
包括熔炼炉、结晶器、轧机、 冷却装置、卷取机等,设备精 度和稳定性对产品质量影响较
大。
熔融纺丝法
熔融纺丝原理
将高分子聚合物加热至熔融状态,通 过喷丝孔挤出形成纤维,并在冷却过 程中固化。
有色金属纤维制备
将有色金属粉末与高分子聚合物混合, 经过熔融纺丝制备出有色金属纤维。
熔融纺丝设备
包括熔融装置、喷丝头、冷却装置、 卷取装置等,设备参数对纤维的直径 和形态有重要影响。
熔融纺丝法应用
主要用于制备连续的有色金属纤维, 在复合材料、增强材料等领域有广泛 应用。
其他生产技术
粉末冶金法
通过粉末制备和压制烧结等工艺制备有 色金属板带材,具有材料利用率高、产
表面处理
根据需要,对板带材进行热处理,以调整 其内部组织结构,提高其力学性能和耐腐 蚀性能。
对板带材进行表面处理,如涂装、电镀等 ,以提高其装饰性和功能性。
市场现状与发展趋势
市场现状
随着经济的发展和科技的进步,有色金属板带材市场需求不断增长,尤其在新能 源汽车、5G通信等领域,对高性能有色金属板带材的需求更为迫切。
在熔融纺丝过程中,金属材料的熔 融状态需要保持稳定,否则会导致
纺丝过程中断或产品质量下降。
B
C
D
解决方案
优化纺丝喷嘴设计,提高喷嘴的均匀性和 稳定性,同时控制纺丝速度和温度,以保 证金属丝的均匀性。
纺丝均匀性问题
在熔融纺丝过程中,金属丝的均匀性是关 键,不均匀的丝可能导致产品质量下降。
有色金属塑性加工成型方法概述
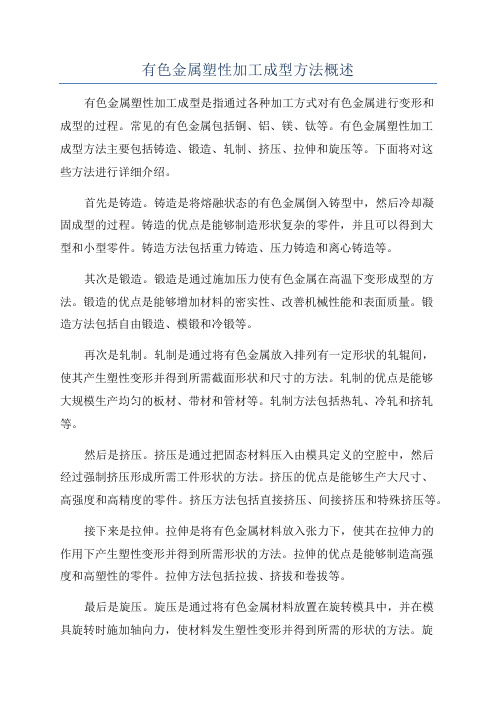
有色金属塑性加工成型方法概述有色金属塑性加工成型是指通过各种加工方式对有色金属进行变形和成型的过程。
常见的有色金属包括铜、铝、镁、钛等。
有色金属塑性加工成型方法主要包括铸造、锻造、轧制、挤压、拉伸和旋压等。
下面将对这些方法进行详细介绍。
首先是铸造。
铸造是将熔融状态的有色金属倒入铸型中,然后冷却凝固成型的过程。
铸造的优点是能够制造形状复杂的零件,并且可以得到大型和小型零件。
铸造方法包括重力铸造、压力铸造和离心铸造等。
其次是锻造。
锻造是通过施加压力使有色金属在高温下变形成型的方法。
锻造的优点是能够增加材料的密实性、改善机械性能和表面质量。
锻造方法包括自由锻造、模锻和冷锻等。
再次是轧制。
轧制是通过将有色金属放入排列有一定形状的轧辊间,使其产生塑性变形并得到所需截面形状和尺寸的方法。
轧制的优点是能够大规模生产均匀的板材、带材和管材等。
轧制方法包括热轧、冷轧和挤轧等。
然后是挤压。
挤压是通过把固态材料压入由模具定义的空腔中,然后经过强制挤压形成所需工件形状的方法。
挤压的优点是能够生产大尺寸、高强度和高精度的零件。
挤压方法包括直接挤压、间接挤压和特殊挤压等。
接下来是拉伸。
拉伸是将有色金属材料放入张力下,使其在拉伸力的作用下产生塑性变形并得到所需形状的方法。
拉伸的优点是能够制造高强度和高塑性的零件。
拉伸方法包括拉拔、挤拔和卷拔等。
最后是旋压。
旋压是通过将有色金属材料放置在旋转模具中,并在模具旋转时施加轴向力,使材料发生塑性变形并得到所需的形状的方法。
旋压的优点是能够制造形状复杂、表面光滑和尺寸精度高的零件。
旋压方法包括手动旋压和自动旋压等。
总结起来,有色金属塑性加工成型方法包括铸造、锻造、轧制、挤压、拉伸和旋压等。
每种方法都有其独特的特点和应用领域,可以满足不同需求的加工要求。
在实际生产中,根据零件的具体要求和性能要求选择适合的加工方法可以提高生产效率和产品质量。
有色金属轧制技术
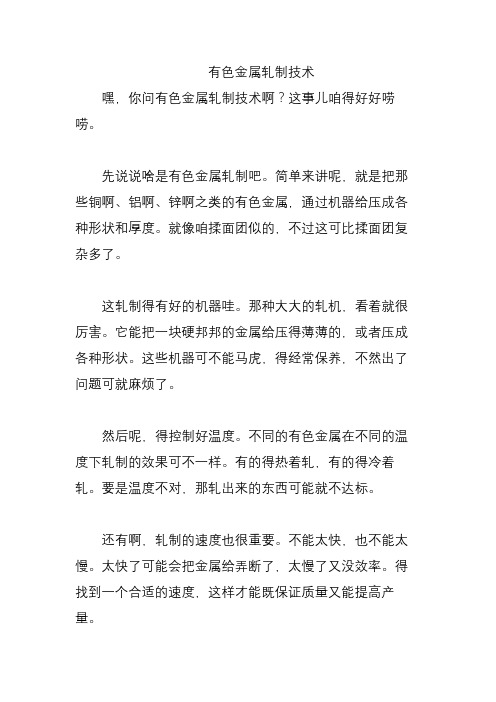
有色金属轧制技术嘿,你问有色金属轧制技术啊?这事儿咱得好好唠唠。
先说说啥是有色金属轧制吧。
简单来讲呢,就是把那些铜啊、铝啊、锌啊之类的有色金属,通过机器给压成各种形状和厚度。
就像咱揉面团似的,不过这可比揉面团复杂多了。
这轧制得有好的机器哇。
那种大大的轧机,看着就很厉害。
它能把一块硬邦邦的金属给压得薄薄的,或者压成各种形状。
这些机器可不能马虎,得经常保养,不然出了问题可就麻烦了。
然后呢,得控制好温度。
不同的有色金属在不同的温度下轧制的效果可不一样。
有的得热着轧,有的得冷着轧。
要是温度不对,那轧出来的东西可能就不达标。
还有啊,轧制的速度也很重要。
不能太快,也不能太慢。
太快了可能会把金属给弄断了,太慢了又没效率。
得找到一个合适的速度,这样才能既保证质量又能提高产量。
在轧制的过程中,还得注意金属的表面质量。
不能有划痕啊、坑啊啥的。
要是有这些问题,那这金属就不好卖了。
所以得经常检查,发现问题及时处理。
另外,操作人员也得有技术。
不能瞎弄,得知道啥时候该调啥,怎么才能轧出好的产品。
这都需要经验积累呢。
我给你讲个事儿吧。
有一次我去一个工厂参观,看到他们在轧制铜片。
那机器轰隆隆地响着,一块红红的铜块进去,不一会儿就变成了薄薄的铜片出来。
我就觉得好神奇啊。
后来我问了那里的工人师傅,他们给我讲了很多关于有色金属轧制的知识。
从那以后,我就知道了这轧制技术可不简单。
总之呢,有色金属轧制技术需要好的机器、控制好温度和速度、注意表面质量,还有有技术的操作人员。
只要把这些都做好了,就能轧出好的有色金属产品。
加油吧!。
- 1、下载文档前请自行甄别文档内容的完整性,平台不提供额外的编辑、内容补充、找答案等附加服务。
- 2、"仅部分预览"的文档,不可在线预览部分如存在完整性等问题,可反馈申请退款(可完整预览的文档不适用该条件!)。
- 3、如文档侵犯您的权益,请联系客服反馈,我们会尽快为您处理(人工客服工作时间:9:00-18:30)。
4.2热轧板带材生产
热轧是指金属在其再结晶温度以上进行的轧制过程
无加工硬化现象 具有较高的塑性和较低的变形抗力 把塑性较低的铸态组织过渡到塑性较高的变形组织(加工组 织),可以显著的改善金属的加工性能 显著地减少轧制时的能量消耗 可以采用较大的变形量进行轧制 可以采用较大的锭坯,提高生产率和成品率,提高轧制速度 , 为轧制过程的连续化和自动化创造了条件
调张力
调节工艺润滑
箔材的精整与深加工
精整包括合卷、分卷、接头、裁切、裱箔、平张剪 切以及染色、印花、压花、打孔等工艺
在叠轧之前把两张或多张铝箔在专用的机列上叠放在一起 的过程称为合卷 经过叠轧后的铝箔必须使其分开,此次生产工序叫做分卷 汽油冲洗掉表面的润滑油 包括裁切、裱箔、平张剪切以及染色、印花、压花、打孔 等,比如香烟包装纸的衬纸
厚度尺寸精确,表面光洁、平坦,缺陷少 性能优良 冷轧可以轧制热轧所不能轧出的薄带和箔材 冷轧时冷却润滑及辊型控制比较重要,并可采用较大的张力, 增加冷轧带材的道次加工率
缺点:道次加工率比较小,能量消耗大
4.3.3冷轧压下制度
根据工艺要求,冷轧可分为
开坯:不宜热轧的合金锭坯(厚度20~70mm)冷轧至厚度 3.5~6mm 粗轧:厚度约为4~13mm的热轧坯 料冷轧至厚度2~6mm 中轧:随后继续压薄轧件的冷轧过程 精轧:为达到成品要求进行的最后冷轧称为精轧
大压下量,并增大轧制速度 较小的道次加工率,适当增 加道次,调整辊型
多数有色金属及合金的最大道次加工率 50% 以上 高塑性的铜合金、铝合金可达到70%
轧制中间阶段
轧制终了阶段
4.2.4.3热轧时温降
热轧时温降的影响因素主要 有
轧件对介质的辐射、对流以 及接触轧辊、辊道等时的热 传导 轧件表面积、重量的大小及 热轧时的冷却水的压力和流 量 轧制速度的快慢、轧制道次 及每道次的间隔时间 锭坯热轧前的加热温度 热轧时塑性变形产生的热效 应等
热轧特点
4.2.4热轧时的压下制度
热轧压下制度
总加工率 道次加工率 轧制道次 立辊轧边
满足优质、高产、低消耗的要求,在合金塑性 及设备能力允许的情况下,尽量采用大加工率 及尽可能少的轧制道次
总加工率—— 有色金属热轧的总加工 率达90%以上
合金的本身性质 合金的高温塑性范围越宽,高温塑性指数越高,高温时变形抗力越 低,热脆性越小,允许采用的热轧总加工率就越大 产品质量要求 供冷轧用的热轧坯料应考虑铣面及冷轧的要求预留足够的冷变形量 冷轧的产品表面质量及尺寸精度要求愈高,则热轧后的坯料厚度应 相应增加 热轧板成品,必须控制轧制温度及变形程度、变形速度等工艺参数 根据晶粒大小及晶粒均匀程度要求的变形程度不能处于临界变形程 度范围内 轧机能力及设备条件 热轧机的机械化程度越高,可以相应增大坯料厚度或减小热轧后坯 料厚度 锭坯尺寸和质量 锭坯越厚,锭坯质量越好,加热质量越高,热轧总加工率也相应愈 大 尽量不采用二次热轧
实际生产中可采用温降曲线 查找每道次的温度降
4.2.5热轧时的冷却润滑
工艺润滑的作用
减少轧制时的能量消耗 冷却轧辊,控制辊型,改善板形 防止辊面粘着金属粉末,改善产品的表面质量 减少轧辊的磨损,增加轧辊的寿命
4.3冷轧板带材生产
冷轧是指金属在再结晶温度以下的轧制过程,因此冷 轧时不发生再结晶,而产生加工硬化,金属的强度和 变形抗力提高,同时还伴随着塑性的降低,容易产生 脆裂 冷轧较热轧有这样几个优点:
铝箔的脱脂清洗
铝箔的深加工
4.5产品质量分析与缺陷消除
质量要求
尺寸精度:厚度精度,包括纵向和横向上的厚度的 精确度 平直度(板形)
板形是指板带材的平直度,即指浪形、瓢曲及旁弯的有无 及程度而言,它主要是由于横向不均匀延伸而引起的
表面质量
表面严重氧化、表面变色及斑点、非金属压入及夹灰、辊 印、压坑、划伤及擦伤等
4.1.1.2板带材的分类及技术要求
成卷生产、供应的横断面呈矩形厚度均一的轧 制产品叫带材 单张生产、供应的叫板材 两种分类方法
按金属及合金的种类分类,可分为铝板带箔材、铜 板带箔材以及镍、铅、锌、锡等的板带箔材 按厚度进行分类,分为厚板、薄板及箔材
薄板:厚度为0.3~4.0mm 厚板:厚度为5.0mm以上 箔材:厚度为0.05(铜板带)~0.20mm(铝板带)以下的 板带材
第四章 板带材生产
4.1板带材生产概述
板带产品的特点:
板带产品外形扁平,宽厚比大,单位体积的表面积也很大, 此种外形特点带来其使用上的特点: 表面积大,故包容、覆盖能力强,在化工、容器、建筑、 金属制品、金属结构等方面得到广泛应用 可任意剪裁、弯曲、冲压、焊接,制成各种制品构件,使 用灵活方便,在汽车、航空等各个部门占有极其重要的地 位 导电、导热、耐蚀、耐酸、防锈等性能良好,故可用在国 防、仪表、电气与电子以及电池、印刷、日常用品等多种 领域
铝箔坯料厚度:0.35~0.8mm 铝箔轧制
特点
由于轧件厚度小,常处于无辊缝或负辊缝轧制状态,即在 轧制之前要把辊缝压靠,此时轧辊给铝箔的压力对其厚度 的影响减弱,而轧制速度、张力及工艺润滑已成为调节厚 度的主要手段 在铝箔轧制中,由于轧件厚度甚薄,因此经常采用双合轧 制,即把几张轧件中间加上润滑油然后叠放在一起轧制的 方法,也可称为叠轧 总加工率99%;多采用二辊或四辊轧机,基本上不用多辊 轧机
冷轧压下制度包括
确定冷轧总加工率 道次加工率 根据产品性能要求控制精轧时的成品加工率
成品冷轧总加工率
硬状态产品:最终性能取决于成品冷轧总加工 率 半硬状态产品:低温退火或控制冷轧总加工率 软状态产品:成品退火
4.4.3铝箔生产工艺
厚度为0.01mm以上的铝箔生产工艺流程为
轧制卷坯(或连续铸轧卷坯)-坯料退火-粗轧-精轧成品退火-成品剪切-检查包装 轧制卷坯(或连续铸轧卷坯)-坯料退火-粗轧-中间 退火-精轧-合卷并切边-清洗-精轧-分卷-成品退火-成 品剪切-检查包装 两生产工艺主要区别在于后者产品更薄,因此需要 合卷轧制,即叠轧
厚度为0.01mm以下的铝箔生产工艺流程为
道次加工率
加大道次压下量——提高轧机的生产率、获得 组织均匀和性能稳定的制品 压下量的分配受到下列条件的限制
金属的塑性 咬入条件的限制 轧辊强度条件的限制 主电机能力的限制
热轧各道次加工率的分配
开始轧制阶段
满足顺利咬入的要求 咬入角20~25° 道次加工率及轧制速度不宜 过大 在锭坯较厚、开始热轧温度 较高的情况下,应适当逐道 增加压下量,采用低速轧制, 使变形能深入内层
机械性能
道次加工率与总加工率
调节轧制速度
轧制速度提高时,轧出的箔材厚度也随之减薄 当其他条件不变时,在一定的范围内,张力越大,则轧出轧 件的厚度越薄 在铝箔材轧制时,张力要恒定,否则会使轧件的轧出厚度发 生波动 润滑油的润滑性能越好,则道次加工率也愈大 当发现铝箔厚度超出正负偏差时,可改变润滑油的成分来调 整轧出厚度