模压制品缺陷及解决办法
SMC模压常见缺陷、原因与解决办法

不良现象
可能原因
解决方法
模压时有先胶化的区域 表 面 多 孔 性
SMC熟料熟成粘度太低 模压太低 熟料配方中硬酯酸锌用量过高 SMC摆料干掉(苯乙烯单体挥发掉)
●降低模温 ●配方中多加些抑制剂 ●增长贮存时间或贮存在较高温处以增加 其熟成 ●配方中增加增粘剂量 ●增加模压 ●降低配方中之硬酯酸锌用量 ●SMC熟料经可防止苯乙烯单体挥发的塑胶膜包装 ●在模压前不要准备太多的熟料 灼烧(Burning)
可能发生之原因
颜料的比重太小 成形前颜料即分离 成形流动时颜料分离
改善对策
●改用无机颜料之色料 ●加速SMC初期的增粘 ●增高SMC熟料之熟成粘度 ●增高SMC熟料之熟成粘度 ●加快合模速度
上 硬 厚 在厚内处产生内压力造成层间之剥离 凸呈化肉 起 圆 表 部 在流动距离大之处,单方向强度减少(玻璃 形 面 份 纤维定向作用)
摆料面积太大,流动距离太短,空气无法逸 ●减少摆料面积或加小面积摆料于较大 出 面积摆料之上 ●降低初期膏状物的粘度 表面多孔性 ●增大SMC机器的压合力量 熟料中玻璃纤维合浸不佳 ●改变合浸较佳的纤维
部份不完全硬化,由于太弱,不易顶出而 ●增加模温 损坏 变形(Warpage) ●配方使用低收缩或不收缩树脂 成形品轻微 由于硬化及冷却时,流动及收缩不均匀而 ●调整模具的温度差 翘曲 翘曲 ●检查顶出系统的正确动作
成形品严重 由于熟料过度的流动,造成玻璃纤维的定向 ●增加摆料面积以缩短流动距离或使用低收缩、不 翘曲 作用(orientation) 收缩树脂 ●使用低收缩或不收缩树脂 ●增加压力,缩短切断纤维的长度,改变模具 设计,更改摆位置,减少剪切边间隙 成形品的厚度和加强肋深,宽间的比例不适 ●调整至最适当的比例 当 波形表面(wavy surface) 在大多数情况不能完全消除改进方法: 成形品的形状不适当或复杂设计,妨碍均匀 ●增大模压 流动 ●改变模具的设计 ●改变摆料位置 摆料重量太低(摆料不足填满模子,合模时 ●增加摆料 不能产生正压(podditive pressure)熟料以乱 心摆放熟料,并降低合模速度 流流动 成形品收缩率太大 收缩率太大(光泽不均匀) 材料 苯乙烯单体量过多 低收缩剂量过多 ●改变配方,使苯乙烯量适中 ●改变配方中低收缩剂量使适中 ●使用低收缩或不收缩熟料 光泽不良,光泽不均匀 ●小
橡胶模压常见质量问题及解决方案

橡胶模压常见质量问题及解决方案模压制品:是指在平板硫化机上用模具成型和硫化的中小型橡胶制品。
橡胶模压中出现的反映在不同制品的同一类问题,如:缺胶、鼓包等。
由于橡胶材料的种类、批次、产地不同、机台、操作者不同、只能具体情况具体分析。
1.缺胶表现为表面(全部或局部)疏松、麻面或有空洞,产生的原因和防止方法:(1)加料量不足为保证每穴制品不缺胶,应准确确定用料量,加足料量并反映在工艺文件内;(2)压力不足,胶量不能充满模腔,应适当增加压力。
(3)胶料流动性太差。
在制品性能允许的情况下,可调整胶料配方,增加可塑性。
工艺上适当增加压力或者在模具表面涂洒一层硬脂酸锌、硅油一类的润滑剂。
(4)模具温度过高,胶料部分焦烧,流动性降低。
应适当降低装料时的模具温度,但不应过多,否则模温在规定时间内升不到硫化温度而使整模胶料报废。
硅橡胶可在较低温度下装料。
(5)胶料的焦烧时间太短应改进配方,提高胶料的耐焦烧性能。
(6)装料合模速度太慢,引起焦烧,应提高操作技术。
(7)坯料安放位置不当,使得胶料不易充满模腔。
(8)模具结构不合理,也会使胶料不易充满模腔如:对于狭长制品,应便于制品长度方向与加压方向垂直。
(9)加压太快,胶料在未充满模腔之前就被挤出模外,使飞边增厚而制品缺料,应减慢加压速度,是胶料在压力下缓缓流入模腔。
2.对合线开裂表现为啓模后在模具对合处制品开裂,有时飞边内缩现象(俗称抽边),产生原因及防止方法:(1)压力不足或压力波动使硫化过程中胶料模腔内部压力大于硫化压力。
而使模具稍稍涨开,引起制品开裂,应检查压力或者检查压力波动原因。
(2)硫化压力过大胶料被严重压缩,启模时,压力急剧下降,硫化胶体积增大,制品其它部分受模具限制无法膨胀,而模具对合模线处则可自由膨胀,因膨胀不均造成的内应力就会导致对合线开裂,应使硫化压力调整到合适的状态,防止过大过小。
如果降压后飞边增厚,可酌情减少加料量或加大流胶槽。
(压力下冷却后出模)。
SMC模压常见缺陷、原因与解决办法

摆料方式不佳或因使用贮存过期熟料造成 ●改善摆料的方式,并使用未过期的熟料 流动不足
可能发生原因
改善对策
熟衬重量过低 ●增加熟料重量直到材料填满模边 模边少数部 合模前熟料散溢 ●熟料摆放位置要更注意或熟料放少些 份未填满 剪切边(Sheal Adge)间隙太大,使熟料发 ●用焊接或镀铬方法减少剪切边间隙 生散溢现象 有模 凹边 凸已 点填 发满 生但 熟料重量过低 空气无法由模具间逸出 加强肋(Rib)或凸栓(Boss)部份有空气存在 致模压时气体无法逸出 ●增加熟料重量 ●重新安排摆料方式,避免空气捕捉之缺点。或使 熟料在流动时,可将成形品内之空气驱除 ●适当处钻引机,使空气排出,若情况不严重,增 加压力,可能有帮助 ●事先压缩去除熟料及熟料间的空气 硬 化 后 的 表 面 呈 现 半 圆 状 凸 起 SMC熟料中及熟料层间存在的空气或气体 ●减少摆料面积或改变摆料方式使空气易于逸出
空气/苯乙烯混合气体存在于未填满部份, ●选用无包覆(trap)空气,流动时可驱走空气之熟料 模压件未完 被压缩后引起混合气体着火烧焦成形品 全填满之处 成型品的形状不适当 有暗棕色或 ●降低合模速度 黑烟表面 合模速度太快 ●改变摆料方式使模压时,气体容易逸出 摆料方式不当 离型不良,脱模不良 模温过低 硬化周期太短 苯乙烯单体挥发,造成部分硬化不完全 内脱模剂太少 成形品难以 取出,在若 新模具或长时间未使用致使模具不能开 干处材料粘 模具表面不良 在模具上表 摆料面积太大,流动距离太小,致使空气无 面有胞孔或 法逸出而包覆的空气延缓硬化反应 疤痕 不正确的顶出系统 模具有倒角(Undercut) SMC的收缩性能 ●增高模温 ●增长硬化时间 ●直至使用时,保持SMC熟料密封于薄膜中 ●配方中增加内脱模剂量 ●在最初数次模压时,涂用外部脱模剂 ●改善模具面 ●减少摆料面积,且在较大摆料上面增放小摆料 ●检查水平顶出动作,在加强肋(Rib) 区域或添顶出梢以防止卡住 ●使用不同收缩等级的熟料 裂痕(Crack) 熟料熟成粘度过低,流动时,树脂与玻璃纤 维分离 ●增设熟料熟成粘度
模压成型工艺实验报告现象分析总结怎么写

模压成型工艺实验报告现象分析总结怎么写引言模压成型工艺作为一种常见的加工方法,广泛应用于塑料制品、橡胶制品等领域。
本文通过对模压成型工艺实验的现象分析总结,旨在探讨实验中可能出现的问题和解决方法,以期提高生产效率和产品质量。
实验条件描述实验中我们选用了标准的模压设备和塑料原料,设定了适当的温度、压力和时间参数进行成型。
模具设计合理,包括了产品的形状、尺寸以及凹凸平整度等要求。
实验过程中,我们发现了以下几个现象:1.成型不完整:部分产品出现了成型不完整的情况,主要表现为产品表面凹凸不平或者有空洞存在。
2.产品变形:有些产品成型后发生了形状变形,与设计要求不符,造成产品无法使用。
3.色差问题:成型后的产品出现了一些色差,与预期颜色不一致。
现象分析成型不完整成型不完整的现象可能由以下原因引起:1.模具问题:模具表面存在划痕、损伤等情况,导致产品表面不平整。
2.温度设置不当:温度过高或过低都会影响塑料的流动性,导致成型不完整。
3.压力不均匀:压力分布不均匀会造成部分区域成型不完整,出现空洞。
解决方法: - 定期检查模具的表面情况,及时保养和更换受损模具。
- 调整温度至适宜范围内,确保塑料材料可以均匀流动。
- 调整压力均匀分布,避免空洞产生。
产品变形产品变形可能是由以下原因引起:1.冷却不均匀:产品在冷却阶段受到外部环境温度影响不均匀,导致变形。
2.材料质量:原料质量差、成分不均匀等因素可能导致产品变形。
解决方法: - 调整冷却设备,保证产品整体受热冷却均匀。
- 定期检查原料质量,选用优质原料,并保持原料成分稳定。
色差问题产品出现色差问题可能由以下原因引起:1.原料选择问题:选用了不同批次或不同品牌的原料可能导致颜色不一致。
2.温度控制:温度波动大或不稳定会影响颜色的稳定性。
解决方法: - 统一选用同一批次、同一品牌的原料,确保颜色一致。
- 稳定温度控制在设定值范围内,避免温度波动。
总结通过对模压成型工艺实验中出现的成型不完整、产品变形以及色差问题进行分析,我们可以看出,影响成型质量的因素是多方面的,需要从多个角度进行改进和优化。
某公司橡胶模压制品常见缺陷及解决方法

橡胶模压制品常见缺陷及解决方法喷霜混炼胶或硫化胶内部的液体或固体配合剂因迁移而在橡胶制品表面析出形成云雾状或白色粉末物质的现象。
这是由于硫、石蜡、某些防老剂、软化剂的使用量超出了它们在橡胶中的溶解度而引起的。
为防止喷霜,上述各种配合剂用量要适当,对常见的硫黄喷霜可采用不溶性硫黄加以防止。
在橡胶中适当加入松焦油,液体古马隆等可增加胶料对上述配合剂的溶解度,以减少喷霜现象。
喷霜-定义和由来喷霜又名喷出(blooming),是橡胶加工过程中常见的质量问题,它是指未硫化胶或硫化胶中所含的配合剂迁移到表面并析出的现象。
有时,这种喷出物呈霜状结晶物,故习惯上称“喷霜”。
较多见的喷霜物为硫,因为硫黄是通用橡胶中应用最广泛的硫化剂,且在橡胶中的溶解度低因而容易产生喷霜。
其实从喷出物外观来看,也未必都呈霜状,也有呈油状(软化剂、增塑剂)或粉粒状(多为填充剂、防老剂、促进剂等)的物质喷出,甚至炭黑喷出也有所见。
喷霜-防霜剂硅胶也会有喷霜现象,采用双二四硫化剂(通常用在挤出成型工艺)高温分解后会产生低分子量的酸性物质,其与硅橡胶不相容,在存放过程中会转移到硅胶表面结晶从而出现喷霜。
防霜剂主要成分为碱性物质,通过酸碱中和反应来达到防霜的目的。
高硬度的硅胶往往加入比较多的内脱模剂,遇水也会喷白,水的酸性对此有遏制作用硅橡胶模具制作方法及注意事项模具是快速模具里的一种最为简单的方法,一般是用硅胶将RP原型进行复模,但寿命很短,只有10-30件左右!他具有很好的弹性和复制性能,用硅橡胶复制模可不用考虑拔模斜度,不会影响尺寸精度,有很好的分割性,不用分上下模可直接进行整体浇注。
再沿预定的分模线进行切割取出母模就可以了!室温硫化硅橡胶又分为加成型和缩合型两种!原料及配方采用专用模具硅橡胶,该品系以双包装形式出售,A组份是胶料,B组份是催化剂。
配制时要考虑室温、模具的强度和硬度,以此来确定AB组份的重量配制比例。
室温在20-25度时,A:B=100:1.5。
橡胶制品外观缺陷及解决方案

橡胶制品外观缺陷及解决方案篇一:橡胶模压制品常见缺陷及解决方法喷霜混炼胶或硫化胶内部的液体或固体配合剂因迁移而在橡胶制品表而析出形成云雾状或白色粉末物质的现象。
这是由于硫、石蜡、某些防老剂、软化剂的使用量超出了它们在橡胶中的溶解度而引起的。
为防止喷霜,上述各种配合剂用量要适当,对常见的硫黄喷霜可采用不溶性硫黄加以防止。
在橡胶中适当加入松焦油,液体古马隆等可增加胶料对上述配合剂的溶解度,以减少喷霜现彖。
喷霜-定义和由来喷霜又名喷出(blooming),是橡胶加工过程中常见的质量问题,它是指未硫化胶或硫化胶中所含的配合剂迁移到表面并析岀的现彖。
有时,这种喷岀物呈霜状结晶物,故习惯上称“喷霜”。
较多见的喷霜物为硫,因为硫黄是通用橡胶中应用最广泛的硫化剂,且在橡胶中的溶解度低因而容易产生喷霜。
其实从喷出物外观来看,也未必都呈霜状,也有呈油状(软化剂、增塑剂)或粉粒状(多为填充剂、防老剂、促进剂等)的物质喷岀,甚至炭黑喷出也有所见。
喷霜-防霜剂硅胶也会有喷霜现象,采用双二四硫化剂(通常用在挤出成型工艺)高温分解后会产生低分子量的酸性物质,其lword版与硅橡胶不相容,在存放过程中会转移到硅胶表面结晶从而出现喷霜。
防霜剂主要成分为碱性物质,通过酸碱中和反应来达到防霜的目的。
高硬度的硅胶往往加入比较多的内脱模剂,遇水也会喷白,水的酸性对此有遏制作用硅橡胶模具制作方法及注意事项模具是快速模具里的一种最为简单的方法,一般是用硅胶将RP原型进行复模,但寿命很短,只有10-30件左右!他具有很好的弹性和复制性能,用硅橡胶复制模可不用考虑拔模斜度,不会影响尺寸精度,有很好的分割性,不用分上下模可直接进行整体浇注。
再沿预定的分模线进行切割取出母模就可以了!室温硫化硅橡胶又分为加成型和缩合型两种!原料及配方采用专用模具硅橡胶,该品系以双包装形式岀售,A组份是胶料,B组份是催化剂。
配制时要考虑室温、模具的强度和硬度,以此来确定AB组份的重量配制比例。
模压制品缺陷及解决办法
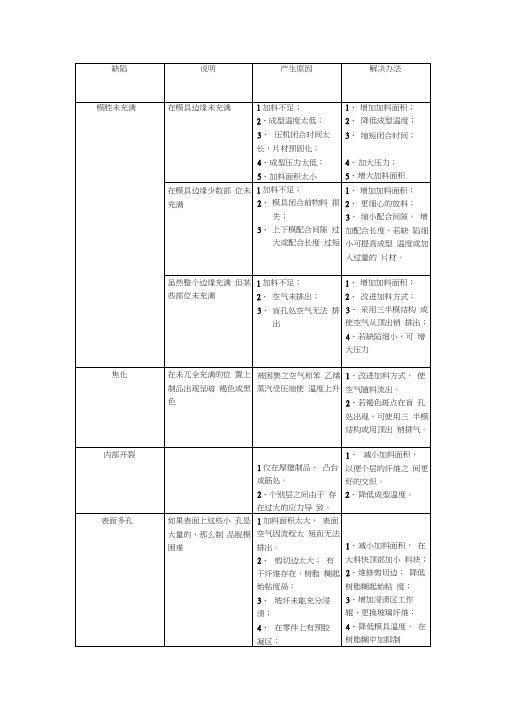
6、增加SMC片材熟
7、零件固化不完
化程度;
全。
7、增加固化周期或 升高模具温度。
在厚制品的表面上
1、在特厚制品中,
1、减小加料面积,
有半圆形鼓起
内应力使个别层间
使各层纤维更好的
扯开;
交织,降低固化温度
2、沿熔接线存在薄
或延长固化时间;
弱区;
2、改变加料方式缺陷
说明
产生原因
解决办法
模腔未充满
在模具边缘未充满
1加料不足;
2、成型温度太低;
3、压机闭合时间太 长,片材预固化;
4、成型压力太低;
5、加料面积太小
1、增加加料面积;
2、降低成型温度;
3、缩短闭合时间;
4、加大压力;
5、增大加料面积
在模具边缘少数部 位未充满
1加料不足;
2、模具闭合前物料 损失;
3、上下模配合间隙 过大或配合长度 过短
2、降低模压温度:减缓聚 合,降低放热温度。
3、加入惰性填料:降低单 位体积内活性基含量,减 缓放热。
4、加入韧性树脂:降低活 性,增加韧性。
5、减少苯乙烯用量:减少 收缩,降低放热温度。
富树脂(玻纤不足)区, 因树脂集中而造成的应 力,即使是中等活性树脂 也会出现裂纹。
2、降低成型温度。
表面多孔
如果表面上这些小 孔是大量的,那么制 品脱模困难
1加料面积太大, 表面空气因流程太 短而无法排出。
2、剪切边太大; 有干纤维存在,树脂 糊起始粘度咼;
3、玻纤未能充分浸 渍;
4、在零件上有预胶 凝区;
1、减小加料面积, 在大料快顶部加小 料块;
2、维修剪切边; 降低树脂糊起始粘 度;
橡胶模压制品常见缺陷及解决方法

喷霜混炼胶或硫化胶内部的液体或固体配合剂因迁移而在橡胶制品表面析出形成云雾状或白色粉末物质的现象。
这是由于硫、石蜡、某些防老剂、软化剂的使用量超出了它们在橡胶中的溶解度而引起的。
为防止喷霜,上述各种配合剂用量要适当,对常见的硫黄喷霜可采用不溶性硫黄加以防止。
在橡胶中适当加入松焦油,液体古马隆等可增加胶料对上述配合剂的溶解度,以减少喷霜现象。
喷霜-定义和由来喷霜又名喷出(blooming),是橡胶加工过程中常见的质量问题,它是指未硫化胶或硫化胶中所含的配合剂迁移到表面并析出的现象。
有时,这种喷出物呈霜状结晶物,故习惯上称“喷霜”。
较多见的喷霜物为硫,因为硫黄是通用橡胶中应用最广泛的硫化剂,且在橡胶中的溶解度低因而容易产生喷霜。
其实从喷出物外观来看,也未必都呈霜状,也有呈油状(软化剂、增塑剂)或粉粒状(多为填充剂、防老剂、促进剂等)的物质喷出,甚至炭黑喷出也有所见。
喷霜-防霜剂硅胶也会有喷霜现象,采用双二四硫化剂(通常用在挤出成型工艺)高温分解后会产生低分子量的酸性物质,其与硅橡胶不相容,在存放过程中会转移到硅胶表面结晶从而出现喷霜。
防霜剂主要成分为碱性物质,通过酸碱中和反应来达到防霜的目的。
高硬度的硅胶往往加入比较多的内脱模剂,遇水也会喷白,水的酸性对此有遏制作用硅橡胶模具制作方法及注意事项模具是快速模具里的一种最为简单的方法,一般是用硅胶将RP原型进行复模,但寿命很短,只有10-30件左右!他具有很好的弹性和复制性能,用硅橡胶复制模可不用考虑拔模斜度,不会影响尺寸精度,有很好的分割性,不用分上下模可直接进行整体浇注。
再沿预定的分模线进行切割取出母模就可以了!室温硫化硅橡胶又分为加成型和缩合型两种!原料及配方采用专用模具硅橡胶,该品系以双包装形式出售,A组份是胶料,B组份是催化剂。
配制时要考虑室温、模具的强度和硬度,以此来确定AB组份的重量配制比例。
室温在20-25度时,A:B=100:1.5。
室低时(但不能低于10度)则适当增加B组份0.1-0.3份。
复合材料模压成型制品的主要缺陷产生原因预防措施

疏松
① 铺层时未充分压实
② 预浸料数量不预浸料压实
② 控制预浸料数量,均匀加料
③ 调整加压时机
贫树脂
① 树脂基体含量过低
② 加压过早,树脂基体流失过多
③ 工装模具加工尺寸精度有偏差
① 提高树脂基体含量,调整预浸料制备工艺
缺陷类别
产生原因
预防措施
外形尺寸超差
①工装模具尺寸精度加工偏差
②预浸料叠层数量控制不严
③热压机工作平台不平行
① 修正工装模具
② 严格控制预浸料叠层数量
③ 校正工装平台精度
翘曲变形
①结构件厚薄差异
②固化度偏低
③固化成型各区域温度不匀
④预浸料挥发份含量偏大
⑤脱模工艺不合理
①改进制品结构设计及成型工艺
②调整及控制固化工艺或采取后固化
③检查、调整加热装置
④充分晾置或采用预热处理
⑤改进脱模工艺或增设脱模工装
裂纹
①制品结构铺层不妥
②脱模工艺不合理
③工装模具结构不合理
④预浸料挥发份含量大
①改进制品结构设计及铺层工艺
②改进脱模工装及脱模工艺
③改进模具结构形式(合理设置排气口及流胶槽)
④控制环境温度、湿度,对预浸料进行充分晾置及预热处理
空隙
② 合理控制加压时机
③ 控制工装模具加工精度
聚合物基复合材料模压成型制品的主要缺陷、产生原因及预防措施
② 严禁将脱模剂或油污物粘在预浸料上,操作时应使用防护用品,防止污染预浸料
③ 控制固化压力,改进脱模工艺
④ 改进操作工艺,避免加工时应力集中现象
富树脂
① 预浸料树脂含量过高
② 未采用预吸胶工艺
模压制品常见的缺陷、产生原因和解决办法

2模温过高,使有机材料分解或使材料老化
3材料混合不均匀
1调整模温均匀性
2降低模温
3加强混合
表面粗糙
1固化不完全
2物料流动性差
3模温太高或合模太慢,使部分物料提前固化
4模压操作不当,合模太快
5模塑料吸潮
1改善固化条件
2调节流动性,高频预热外观较好
3降低模温,快些合模
4一般采用低压慢闭模,预压几秒后再加压
5模具设计不当或顶出装置不好
6制件各部分厚度相差太大
1修改模具设计,合理地设计脱模结构,保证脱模顶出力量平均
2选择适当的嵌件材料,适当加厚模压制品的厚度
3预热模塑料
4降低模温或缩短保温时间
5改正模具设计、调整顶出杆尺寸和位置
6改变制件设计
翘曲
1压制件固化程度不足
2产品设计不合理,如各处壁厚极不匀称,相差过大
模压制品常见的缺陷、产生原因和解决办法
缺陷
产生原因
解决办法
表面起泡或内部鼓起
1物料中挥发物含量太大
2模塑料固化不完全
3模温过高,使物料中某种成分汽化或分解
4排气操作慢,使表面固化,
1充分预热物料
2适度提高模温或延长保压时间
3降低模温
4用适当的速度放气
缺料
1料重不匀
2物料流动性差
3脱模剂用量太多
4操作太快
1型腔表面光洁度差
2保压时间短,模压温度太低
1磨光或抛光型腔表面
2适当调整模压工艺Biblioteka 数电性能差1固化不完全
2模塑料含水及挥发物太大
1改善固化条件
2预热去除水分和挥发物,预压
机械性能差
1固化不完全
SMC模压常见缺陷、原因与解决办法

●降低模温 ●配方中多加些抑制剂 ●增长贮存时间或贮存在较高温处以增加 其熟成 ●配方中增加增粘剂量 ●增加模压 ●降低配方中之硬酯酸锌用量 ●SMC熟料经可防止苯乙烯单体挥发的塑胶膜包装 ●在模压前不要准备太多的熟料 灼烧(Burning)
空气/苯乙烯混合气体存在于未填满部份,被 ●选用无包覆(trap)空气,流动时可驱走空气之熟料 模压件未完 压缩后引起混合气体着火烧焦成形品 全填满之处 成型品的形状不适当 有暗棕色或 ●降低合模速度 黑烟表面 合模速度太快 ●改变摆料方式使模压时,气体容易逸出 摆料方式不当 离型不良,脱模不良 模温过低 硬化周期太短 苯乙烯单体挥发,造成部分硬化不完全 成形品难以 取出,在若 干处材料粘 在模具上表 面有胞孔或 疤痕 内脱模剂太少 新模具或长时间未使用致使模具不能开 模具表面不良 ●增高模温 ●增长硬化时间 ●直至使用时,保持SMC熟料密封于薄膜中 ●配方中增加内脱模剂量 ●在最初数次模压时,涂用外部脱模剂 ●改善模具面
硬化收缩压 在内厚加强肋,凸硬化周期太短,凸栓(boss) ●减少摆料面积使玻璃纤维较吻合 力造成 处,因强烈收缩产生内压力而造成叠层间 ●降低模温 开裂 内厚处因硬化产生温度放热颠峰 部份的粘着,造成离型不良 开模太快 顶出梢的重作不当 经由机械要 因的破裂 顶出梢数目不足,通常位于内薄区 ●降低开模速度 ●调节顶出板及顶出梢系统 ●在破裂处加装顶出梢 ●重新设计以减少内厚部份
摆料方式不佳或因使用贮存过期熟料造成 ●改善摆料的方式,并使用未过期的熟料 流动不足
可能发生原因
改善对策
熟衬重量过低 ●增加熟料重量直到材料填满模边 模边少数部 合模前熟料散溢 ●熟料摆放位置要更注意或熟料放少些 份未填满 剪切边(Sheal Adge)间隙太大,使熟料发 ●用焊接或镀铬方法减少剪切边间隙 生散溢现象 有模 凹边 凸已 点填 发满 生但 熟料重量过低 空气无法由模具间逸出 加强肋(Rib)或凸栓(Boss)部份有空气存在 致模压时气体无法逸出 ●增加熟料重量 ●重新安排摆料方式,避免空气捕捉之缺点。或使 熟料在流动时,可将成形品内之空气驱除 ●适当处钻引机,使空气排出,若情况不严重,增 加压力,可能有帮助 ●事先压缩去除熟料及熟料间的空气 硬 化 后 的 表 面 呈 现 半 圆 状 凸 起 SMC熟料中及熟料层间存在的空气或气体 ●减少摆料面积或改变摆料方式使空气易
复合材料模压成型制品的主要缺陷产生原因预防措施
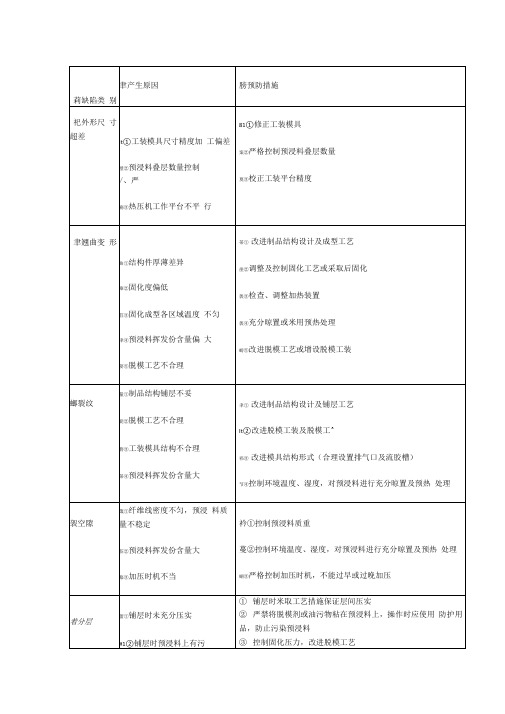
4固化加压时机不当
1调整预浸料制备工艺参数
2控制预吸胶压实工艺
3修正工装模具,控制加工精度要求
4合理控制加压时机
疏松
1铺层时未充分压实
2预浸料数量不足或加料 不匀
3固化加压时机控制/、到 位
1铺层时采用辅助工装使预浸料压实
2控制预浸料数量,均匀加料
3调整加压时机
贫树脂
1树脂基体含量过低
2加压过早,树脂基体流失 过多
1铺层时米取工艺措施保证层间压实
2严禁将脱模剂或油污物粘在预浸料上,操作时应使用 防护用,防止污染预浸料
3控制固化压力,改进脱模工艺
染物
艘③固化压力不够或脱模 不当
苏④制品胶、钏连接时应力 集中
④改进操作工艺,避免加工时应力集中现象
富树脂
1预浸料树脂含量过高
2未采用预吸胶工艺
3工装模具加工精度有偏
节④控制环境温度、湿度,对预浸料进行充分晾置及预热 处理
袈空隙
箴①纤维线密度不匀,预浸 料质量不稳定
莅②预浸料挥发份含量大
幕③加压时机不当
衿①控制预浸料质重
蔓②控制环境温度、湿度,对预浸料进行充分晾置及预热 处理
蝴③严格控制加压时机,不能过早或过晚加压
着分层
蕾①铺层时未充分压实
#1②铺层时预浸料上有污
3工装模具加工尺寸精度 有偏差
1提高树脂基体含量,调整预浸料制备工艺
2合理控制加压时机
3控制工装模具加工精度
聚合物基复合材料模压成型制品的主要缺陷、产生原因及预防措施
For personal use only in study and research; not for commercial use
SMC材料模压工艺中常见的质量问题与对策

SMC材料模压工艺中常见的质量问题与对策SMC材料模压工艺是玻璃钢/复合材料成型工艺中生产效率最高的一种。
SMC模压工艺还有很多优点,例如:制品尺寸准确、表面光洁、制品外观及尺寸重复性好、复杂结构也可一次成型、二次加工无需损伤制品等。
但在SMC模压生产过程中也会出现不良缺陷现象,主要表现在以下几个方面(l)缺料:缺料是指SMC模压成型件没完全充满,其产生部位多集中在SMC制品的边缘,尤其是边角的根部和顶部。
原因分析:(a)放料量少,(b)SMC材料流动性差,(c)设备压力不充足(d)固化太快。
产生机理及对策:①SMC材料受热塑化后,熔融粘度大,在交联固化反应完成前,没有足够的时间,压力,和体积使融体充满模腔。
②SMC模压料存放时间过长,苯乙烯挥发过多,造成SMC模压料的流动性能明显降低。
③树脂糊未浸透纤维。
成型时树脂糊不能带动纤维流动而造成缺料。
由上述原因所引起的缺料,最直接的解决方法是切料时剔除这些模压料。
④加料量不足引起缺料。
解决方法是适当增大加料量。
⑤模压料中裹有过多的空气及大量挥发物。
解决方法有,适当增加排气次数;适当加大加料面积嗝一定时间清理模具;适当增大成型压力。
⑥加压过迟,模压料在充满模腔前已完成交联固化。
⑦模温过高,交联固化反应提前,应适当降温。
(2)气孔。
产品表面上有规则或不规则的小孔,其产生部位多在产品顶端和中间薄壁处。
产生机理及对策:①SMC模压料中裹有大量空气以及挥发物含量大,排气不畅;SMC料的增稠效果不佳,不能有效赶出气体。
对于上述引起原因,可通过增加排气次数以及清理模具相结合的方法而得到有效的控制。
②加料面积过大,适当减少加料面积可得到控制。
在实际操作过程中,人为因素也有可能造成砂眼。
比如加压过早,有可能使模压料裹有的气体不易排出,造成制品表面出现气孔的表面缺陷。
(3)翘曲变形。
产生的主要原因是模压料固化不均匀和脱模后产品的收缩。
产生机理及对策:在树脂固化反应过程中化学结构发生变化,引起体积收缩,固化的个均匀使得产品有向首先固化的一侧翘曲的趋势。
橡胶模压制品最常见的问题及解决办法
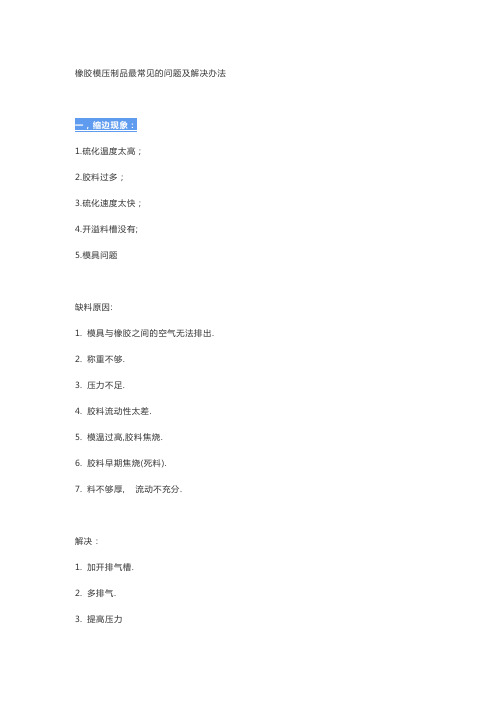
橡胶模压制品最常见的问题及解决办法1.硫化温度太高;2.胶料过多;3.硫化速度太快;4.开溢料槽没有;5.模具问题缺料原因:1. 模具与橡胶之间的空气无法排出.2. 称重不够.3. 压力不足.4. 胶料流动性太差.5. 模温过高,胶料焦烧.6. 胶料早期焦烧(死料).7. 料不够厚, 流动不充分.解决:1. 加开排气槽.2. 多排气.3. 提高压力4. 改配方,增加胶料流动性.5. 改配方,延长焦烧时间;6. 增加料厚度.1. 硫化不足.2. 配合剂过量,超过橡胶的溶解度.解决:1. 延长硫时或采取二次硫化2. 调整配方,减少低溶解度3. 配合剂的用量1. 硫化不足.2. 压力不足.3. 模内或胶料中有杂质或油污.4. 硫化模温过高.5. 硫化剂加少了,硫化速度太慢.解决:1. 加压2. 加长硫时3. 调整配方,加快硫化速度.4. 多排气.5. 模温不能过高.6. 增加硫化剂用量.1. 硫化速度太快,胶流动不充分.2. 模具脏或胶料粘污迹.3. 隔离剂或脱模剂太多4. 胶料厚度不够.解决:1. 降低模温,减慢硫化速度.2. 保持胶料.模具清洁.3. 少用隔离剂或脱模剂.4. 胶料够厚.1. 模温过高或者硫时过长.2. 硫化剂用量过多.3. 脱模方法不对.解决措施:1. 降低模温.2. 缩短硫时.3. 减少硫化剂用量.4. 喷脱模剂.5. 采取正确的脱模方法.1. 产品撕裂强度太好,(如高拉力胶).这种难加工表现为毛边撕不下来.2. 产品强度太差,表现为毛边很脆,会连产品一起撕破.解决措施:1. 如果是撕不掉, 就得调整配方,多填充配合剂,减小收缩率.2. 如果是撕破,a 降低模温,缩短硫时.b 减少硫化剂用量.c 调整配方,增加胶料强度..。
常见模压故障及排除方法

常见模压故障及排除方法模切压痕制作合格的产品,应切位准确,切口干净、无毛边、花刀、压痕清晰、深浅适度。
在模切压痕操作中常见的故障与解决方法:①压痕不清晰、有暗线,炸线。
(暗线指不应有的压痕;炸线指由于压痕压力过重纸板断裂)产生原因:纸质差,纸张含水量过低,使其脆性增加,韧性降低;钢线选择不对;钢线垫纸过低或过高;模压机压力调整不当。
解决方式:重新调整钢线高度;检查钢线选择是否合适;适当调整模切机的压力大小;根据模压纸板的状况,调整模切压痕的工艺条件,使两者尽量适应。
②切口不光洁。
产生原因:钢刀材质不良,刃口不锋利,模切适性差;换到不及时,刃口磨损严重;模切机压力小或压力调整与钢刀高度调整不协调,模切作业压不实。
解决方式:经常检查钢刀刃口磨损情况,做到及时更换钢刀;根据印刷品所用纸张的裁切性能,选用不同质量特性的钢刀;适当增加压力;重新调整或更换钢刀或垫纸,使模切中获得较实的压力效果。
③模切压痕的位置不准。
产生原因:排刀位置与印刷品不符合;模切操作中输纸位置不一致;纸板叼口规矩不准确;操作中纸板变形、套印不准。
解决方法:根据样张要求,重新矫正印版位置;调整模切输纸定位规矩,使与输纸位置保持一致;针对产生位置的原因,降低印刷品缺陷对模切质量的影响。
④压痕线不规矩。
产生原因:排刀、固刀紧度不合适,底部不能同铁台平面达到理想接触效果,压痕时易出现扭动(钢线太紧);压痕中易左右串动(钢线太松);钢线垫纸厚度不足;槽形角度不规范,出现多余的圆角;钢线垫纸上的压痕槽留得太宽,压痕时位置不固定。
解决方法:更换钢线垫纸,将压槽留窄;增加钢线垫纸厚度;修正槽角;排刀固刀紧度要适宜。
⑤模切后纸板有连刀。
产生原因:模版所受的压力不均匀,压力小的地方连刀;模刀刀锋不锐利,致使连刀;纸张厚度太大,不能完全切透纸张。
解决方法:根据实际情况更换模刀;增加局部压力。
⑥模切后纸板粘连刀版。
产生原因:刀线周围填塞的橡皮过于稀疏,回弹力不足;根据橡皮的性能选用不合适;钢刀不锋利,纸张太厚,引起夹刀或压力过大。
模压中易出现问题及解决方法

模压中易出现问题及解决方法模压成型过程中易出现的问题有:制品表面起泡和内部鼓起;制品翘曲变形;制品放置一段时间出现裂缝,制品局部纤维裸露等。
现就有关现象产生的原因及处埋措施分述如下:一、制品表面起泡或内部鼓起此种现象产生的原因可能是物料中水分及挥发物含量过高;模具温度过高或过低;压力不足及保温时间过短;物料加热不均匀等。
其解决措施是:严格控制物料中挥发物含量,适当调整模具温度,合理控制成型压力和保温时间。
改进加热装置使物料受热均匀。
二、制品变形、翘曲此种现象产生原因可能是玻璃钢固化不完全,成型温度较低,保温时间不足;制品薄厚不均,造成收缩率不均等。
其解决措施是:严格控制固化温度和保温时间;选用收缩率小的模压料;在满足制品使用要求的前提下,适当变动制品的结构形式,使制品的厚度尽量均一或平滑过渡。
三、裂缝此种现象多发生于有嵌件的制品中。
其产生原因可能是。
制品中嵌件的结构不合理;嵌件数量过多;脱模方式不合理,制品各部位厚薄相差太大等。
其解决措施是:对制品的给构在允许的条件下进行更改,嵌件要能满足模压的要求;合理的设计脱模机构,保证脱模顶出力量平均。
四、制品欠压,局部缺胶此种现象产生的原因可能是因为压力不足;物料流动性过大,加料量不够;温度过高,以致部分模压料过早固化。
其解决措施是:严格控制成型温度、压力和加压时机;保证物料充足,不得出现缺料现象。
五、制品粘模有时出现制品粘在模具上不易脱模,严重损坏了制品的外观。
其原因可能是物料中漏加内脱模剂;模具清洗不干净,忘涂脱模剂;模具表面损伤等。
其解决措施是:严格控制物料质量,精心操作,模具损坏要及时修理,达到所要求的模具光洁度。
六、制品废边过厚此种现象产生的原因可能是模具设计不合理;物料加得太多等。
其解决措施是:进行合理的模具设计;严格控制加料量。
七、制品尺寸不合格此种现象产生原因可能是物料质量不符合要求;加料不严格;模具磨损;模具设计尺寸不精确等。
其解决措施是:严格控制物料质量,精确加料。
模压制品缺陷型式、发生原因、纠正措施.
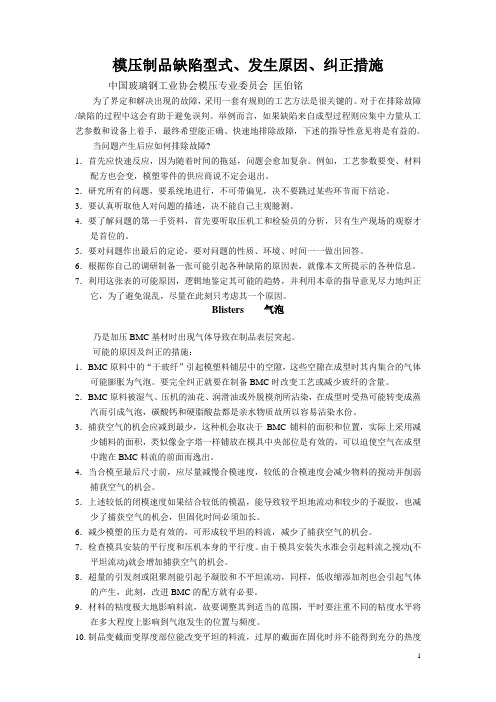
模压制品缺陷型式、发生原因、纠正措施中国玻璃钢工业协会模压专业委员会匡伯铭为了界定和解决出现的故障,采用一套有规则的工艺方法是很关键的。
对于在排除故障/缺陷的过程中这会有助于避免误判。
举例而言,如果缺陷来自成型过程则应集中力量从工艺参数和设备上着手,最终希望能正确、快速地排除故障,下述的指导性意见将是有益的。
当问题产生后应如何排除故障?1.首先应快速反应,因为随着时间的拖延,问题会愈加复杂。
例如,工艺参数要变、材料配方也会变,模塑零件的供应商说不定会退出。
2.研究所有的问题,要系统地进行,不可带偏见,决不要跳过某些环节而下结论。
3.要认真听取他人对问题的描述,决不能自己主观臆测。
4.要了解问题的第一手资料,首先要听取压机工和检验员的分析,只有生产现场的观察才是首位的。
5.要对问题作出最后的定论,要对问题的性质、环境、时间一一做出回答。
6.根据你自己的调研制备一张可能引起各种缺陷的原因表,就像本文所提示的各种信息。
7.利用这张表的可能原因,逻辑地鉴定其可能的趋势,并利用本章的指导意见尽力地纠正它,为了避免混乱,尽量在此刻只考虑其一个原因。
Blisters 气泡乃是加压BMC基材时出现气体导致在制品表层突起。
可能的原因及纠正的措施:1.BMC原料中的“干玻纤”引起模塑料铺层中的空隙,这些空隙在成型时其内集合的气体可能膨胀为气泡。
要完全纠正就要在制备BMC时改变工艺或减少玻纤的含量。
2.BMC原料被湿气、压机的油花、润滑油或外脱模剂所沾染,在成型时受热可能转变成蒸汽而引成气泡,碳酸钙和硬脂酸盐都是亲水物质故所以容易沾染水份。
3.捕获空气的机会应减到最少,这种机会取决于BMC铺料的面积和位置,实际上采用减少铺料的面积,类似像金字塔一样铺放在模具中央部位是有效的,可以迫使空气在成型中跑在BMC料流的前面而逸出。
4.当合模至最后尺寸前,应尽量减慢合模速度,较低的合模速度会减少物料的搅动并削弱捕获空气的机会。
SMC模压常见缺陷、原因及解决方法(仅供参考)

解决方法
●增加装料重量,直到材料填满模边为止 ●Check成型品的比重 ●降低模温 ●缩短合模时间 ●改变硬化系统、拉长Gel time ●增加模压 ●加大熟料面积 ●改善摆料的方式,并使用未过期的熟料 ●增加熟料重量直到材料填满模边 ●熟料摆放位置要更注意或熟料放少些 ●用焊接或镀铬方法减少剪切边间隙 ●增加熟料重量 ●重新安排摆料方式,避免空气捕捉之缺点。或使熟 料在流动时,可将成形品内之空气驱除 ●适当处钻引机,使空气排出,若情况不严重,增加 压力,可能有帮助 ●事先压缩去除熟料及熟料间的空气 ●减少摆料面积或改变摆料方式使空气易于逸出 ●改良熟料的配方,使其流动较佳 ●在流动中心增加摆料 ●用焊接或镀铬方法减少剪切间隙 ●降低模温 ●增加模压时间或模温 ●降低合模速度 ●增加熟成时间或配方中增加粘剂浓度 ●降低SMC膏状物粘度 ●增大SMC机器的压合作用(Compaction) ●改换含浸较佳之纤维 ●减少摆料面积使各层玻璃纤维吻合性较佳 ●降低模温 ●用增加摆料面积缩短流动距离 ●减少摆料面积或加小面积摆料于较大 面积摆料之上 ●降低初期膏状物的粘度 ●增大SMC机器的压合力量 ●改变合浸较佳的纤维 ●降低模温 ●配方中多加些抑制剂 ●增长贮存时间或贮存在较高温处以增加其熟成 ●配方中增加增粘剂量 ●增加模压 ●降低配方中之硬酯酸锌用量 ●SMC熟料经可防止苯乙烯单体挥发的塑胶膜包装 ●在模压前不要准备太多的熟料 ●选用无包覆(trap)空气,流动时可驱走空气之熟料 ●降低合模速度 ●改变摆料方式使模压时,气体容易逸出 ●增高模温 ●增长硬化时间 ●直至使用时,保持SMC熟料密封于薄膜中 ●配方中增加内脱模剂量 ●在最初数次模压时,涂用外部脱模剂 ●改善模具面 ●减少摆料面积,且在较大摆料上面增放小摆料 ●检查水平顶出动作,在加强肋(Rib) ●区域或添顶出梢以防止卡住 ●使用不同收缩等级的熟料 ●增设熟料熟成粘度
SMC模压常见缺陷、原因与解决方法

SMC模压常见缺陷、原因与解决方法一、气泡和空洞缺陷描述:在SMC模压成型后,产品内部或表面出现不规则的气泡或空洞。
原因分析:原料混合不均匀,存在空气囊。
模压过程中排气不充分,导致气体被困。
模压温度过高或过低,影响气体排出。
解决方法:加强原料混合工艺,确保物料均匀无气泡。
优化模具设计,增加排气孔和排气槽,提高排气效率。
调整模压温度,确保在合适的温度范围内进行模压。
二、翘曲变形缺陷描述:SMC模压件在成型后出现形状改变,不符合设计要求。
原因分析:模压过程中温度分布不均匀,导致产品局部收缩不一致。
模具设计不合理,未能完全限制产品变形。
材料性能差异,如收缩率不同。
解决方法:改善模压工艺,确保模腔内温度分布均匀。
优化模具结构,增加支撑和限位装置,减少变形。
选用性能稳定、收缩率一致的原材料。
三、表面瑕疵缺陷描述:SMC模压件表面出现裂纹、划痕、凹坑等缺陷。
原因分析:模具表面不光洁,存在磨损或异物。
脱模过程中操作不当,导致产品损伤。
原材料含有杂质或颗粒过大。
解决方法:定期对模具进行维护和保养,保持其表面光滑清洁。
改进脱模工艺,使用专用脱模剂,避免划伤产品。
严格控制原材料质量,去除杂质和过大颗粒。
四、强度不足缺陷描述:SMC模压件在使用过程中表现出较低的机械强度,易发生断裂或变形。
原因分析:原材料配比不当,影响产品性能。
模压压力不足或时间过长,导致产品内部结构疏松。
产品固化不充分,未能达到设计强度。
解决方法:调整原材料配比,确保各组分含量符合设计要求。
优化模压工艺参数,提高模压压力和缩短模压时间。
延长固化时间或提高固化温度,确保产品充分固化。
综上所述,针对SMC模压常见的气泡和空洞、翘曲变形、表面瑕疵以及强度不足等缺陷,可以通过调整原材料、优化模具设计、改进工艺参数和加强质量控制等方法来有效解决。
在实际生产过程中,应根据具体情况采取相应措施,以提高产品质量和降低成本。