压铸工艺参数与铸件质量的关系
压铸工艺实验报告(3篇)

第1篇一、实验目的1. 了解压铸工艺的基本原理和操作流程。
2. 掌握压铸工艺参数对铸件质量的影响。
3. 提高对压铸工艺缺陷的分析和解决能力。
二、实验设备与材料1. 实验设备:压铸机、压铸模具、加热炉、冷却水系统、实验台等。
2. 实验材料:铝合金、锌合金等。
三、实验原理压铸工艺是一种将熔融金属在高压下快速充填型腔,并在冷却固化后获得所需形状和尺寸的金属零件的加工方法。
实验主要研究压铸工艺参数对铸件质量的影响,包括压力、速度、温度、时间等。
四、实验步骤1. 准备工作:根据实验要求,选择合适的压铸模具和材料,并对模具进行清洗和预热。
2. 加热:将熔融金属加热至适宜的温度,确保金属流动性好,便于充填型腔。
3. 充填:启动压铸机,将熔融金属在高压下快速充填型腔。
4. 冷却:在金属凝固过程中,通过冷却水系统对模具进行冷却,保证铸件尺寸精度。
5. 开模取件:待金属凝固后,打开模具取出铸件。
6. 检查与分析:对铸件进行外观检查,分析铸件缺陷产生的原因,并提出改进措施。
五、实验结果与分析1. 铸件外观质量:实验过程中,铸件外观质量良好,无明显的缩孔、气孔、裂纹等缺陷。
2. 铸件尺寸精度:实验中,铸件尺寸精度较高,与模具设计尺寸基本一致。
3. 铸件内部质量:实验中,铸件内部质量良好,无明显的缩松、夹渣等缺陷。
六、实验结论1. 压铸工艺参数对铸件质量有显著影响。
在实验过程中,通过优化压力、速度、温度、时间等参数,可提高铸件质量。
2. 压铸模具的设计对铸件质量有重要影响。
合理设计模具结构,有利于提高铸件尺寸精度和内部质量。
3. 在压铸过程中,应注意控制熔融金属的温度和流动性,以保证铸件质量。
七、实验改进措施1. 优化压铸工艺参数:通过实验,进一步优化压力、速度、温度、时间等参数,以提高铸件质量。
2. 优化模具设计:针对铸件缺陷,对模具结构进行改进,以提高铸件尺寸精度和内部质量。
3. 加强操作技能培训:提高操作人员对压铸工艺的理解和操作技能,确保实验顺利进行。
压铸原理及工艺参数选择
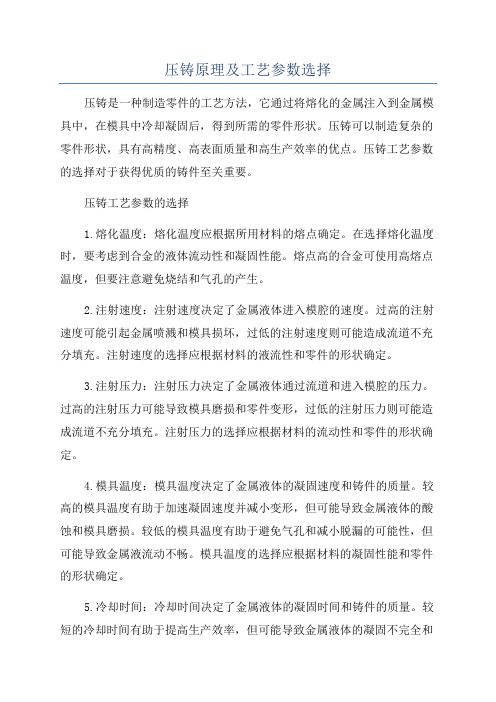
压铸原理及工艺参数选择压铸是一种制造零件的工艺方法,它通过将熔化的金属注入到金属模具中,在模具中冷却凝固后,得到所需的零件形状。
压铸可以制造复杂的零件形状,具有高精度、高表面质量和高生产效率的优点。
压铸工艺参数的选择对于获得优质的铸件至关重要。
压铸工艺参数的选择1.熔化温度:熔化温度应根据所用材料的熔点确定。
在选择熔化温度时,要考虑到合金的液体流动性和凝固性能。
熔点高的合金可使用高熔点温度,但要注意避免烧结和气孔的产生。
2.注射速度:注射速度决定了金属液体进入模腔的速度。
过高的注射速度可能引起金属喷溅和模具损坏,过低的注射速度则可能造成流道不充分填充。
注射速度的选择应根据材料的液流性和零件的形状确定。
3.注射压力:注射压力决定了金属液体通过流道和进入模腔的压力。
过高的注射压力可能导致模具磨损和零件变形,过低的注射压力则可能造成流道不充分填充。
注射压力的选择应根据材料的流动性和零件的形状确定。
4.模具温度:模具温度决定了金属液体的凝固速度和铸件的质量。
较高的模具温度有助于加速凝固速度并减小变形,但可能导致金属液体的酸蚀和模具磨损。
较低的模具温度有助于避免气孔和减小脱漏的可能性,但可能导致金属液流动不畅。
模具温度的选择应根据材料的凝固性能和零件的形状确定。
5.冷却时间:冷却时间决定了金属液体的凝固时间和铸件的质量。
较短的冷却时间有助于提高生产效率,但可能导致金属液体的凝固不完全和热裂纹的产生。
较长的冷却时间有助于提高铸件的密度和表面质量,但可能导致产量降低。
冷却时间的选择应根据材料的凝固性能和零件的形状确定。
总结压铸是一种高效、高精度的制造方法,工艺参数的选择对于获得优质的铸件至关重要。
在选择工艺参数时,要综合考虑材料的性质、零件的形状和制造要求,以及设备和模具的性能。
通过合理选择工艺参数,可以提高铸件的质量和生产效率,降低生产成本。
压铸件工艺参数的设定

压铸件工艺参数的设定2011-11-24 8:57:20在压铸行业,工艺参数对产品质量的影响更多的是靠试验的方法,许多工程技术人员不能深入的进行分析,生产铸件的条件无法用数据来描述。
本文就压铸工艺参数理论计算和实践两方面进行讨论研究。
压力铸造的主要工艺参数有行程(速度转换点)、速度、时间和压力等。
而本文重点分析速度和行程两个主要参数。
1. 压铸的四阶段压射计算压力铸造工艺参数,首先要定义压铸的四个压射阶段。
1.1.1 第一阶段:慢压射1为防止金属液溅出,冲头越过浇料口的过程,压射的第一阶段通常是缓慢的。
1.1.2 第二阶段:慢压射2金属液以较低的速度运动至内浇口的阶段,主要目的是排出压室内的空气,集中铝液于压室内。
1.1.3 第三阶段:快压射金属液由内浇口填充型腔直至充满为止,主要目的是成型并排出型腔中气体。
1.1.4 第四阶段:增压阶段型腔充满后建立最后的增压,使铸件在高压压力下凝固,从而使铸件致密。
1.2 计算模型1.2.1 根据1.1定义(参照图1),可以得到金属液在各阶段合金液的重量关系式。
G2=G浇G3+G4=G铸+G溢流其中:G3+G4为金属液刚达到内浇口处时冲头端面至冲头停止之间的铝液重量,即为快压射起始点位置至冲头停止行程内金属液的容量。
G铸为铸件重量G溢为溢流系统的重量G2为慢压射2行程内压室能容纳的金属液重量G浇为浇注系统的重量1.2.2 流道中单位时间内不同位置截面中通过合金液的流量关系式(见图2)金属液在流动过程中,单位时间内通过截面的流量Q相等,则Q=V1×S1=V2×S2= V3×S3 (注:V3×S3是利用等式,而非金属液流量)其中V1:冲头速度S1:冲头面积V2:内浇口速度S2:内浇口面积V3:排气槽气体速度(推荐值75m/s)S3:排气槽的面积1.2.3压铸时间[1]压铸时间包括充填时间,持压时间及铸件在压铸模型中停留的时间。
压铸工艺参数分析

压铸工艺参数分析1.注射压力:注射压力是指在铸造过程中,金属熔液被压入型腔的压力大小。
注射压力的大小对于铸件的排气、充盈、凝固过程以及零部件的尺寸稳定性有着重要的影响。
过高的注射压力会导致铸件内部气泡的形成、表面粗糙度增大等问题,而过低的注射压力则会导致型腔内充盈不充分。
2.注射速度:注射速度是指熔融金属进入模具腔体的速度。
适当的注射速度可以使熔融金属在型腔内充盈均匀,防止铸件出现疏松、夹杂等缺陷。
过高的注射速度会导致金属熔液的剪切力增加,容易产生气泡和金属破碎现象,而过低的注射速度则会导致金属熔液在充盈过程中受到阻力,形成冷障。
3.注射温度:注射温度是指金属熔液注入型腔时的温度。
注射温度的高低会直接影响到铸件的凝固形态和组织结构。
过高的注射温度会导致铸件的表面质量较差,因为金属熔液的冷却速度过快,易产生冷障和贝氏体组织。
而过低的注射温度则会导致金属熔液黏度增大,充盈性变差。
4.金属液温度:金属液温度是指金属熔体在注射之前的温度。
金属液温度的高低会直接影响到铸件的凝固过程和性能。
过高的金属液温度会导致铸件的组织粗大,出现热裂纹等问题。
而过低的金属液温度则会导致铸件的毛细孔增多,降低铸件的密实性。
5.压射机的闭模力:压射机的闭模力是指用于关闭型腔的力大小。
闭模力的大小会直接影响到铸件的尺寸稳定性和机械性能。
过高的闭模力会导致铸件的尺寸过大,形成表面凸起和冷障等问题。
而过低的闭模力则会导致铸件尺寸的不稳定性和机械性能的下降。
6.模具温度:模具温度是指模具在铸造过程中的温度。
模具温度的高低会直接影响到铸件的组织结构和表面质量。
适当的模具温度可以提高铸件的表面光洁度,减少气孔和缩松等问题。
过高的模具温度会导致铸件的热组织粗大,而过低的模具温度则会导致铸件充盈性差。
总结起来,压铸工艺参数对于铸件质量和性能有着直接的影响。
合理的控制和选择工艺参数可以有效地改善铸件的表面质量、减少缺陷率,提高铸件的力学性能和尺寸稳定性。
压铸工艺-影响压铸件质量的主要工艺参数

过高的速度将产生不利影响 气体不能充分逸出而形成气泡。
金属液成雾状进入型腔并粘附于型壁上,不能与 后来的金属液融合而形成夹杂等表面缺陷。
定期检查型芯是否变形 使用模具时要充分预热并且严格按工艺规程操作 对浇口方案及型芯型腔能否冷却等铸造方案进行重新论证 针对铸件的收缩情况对铸件形状进行改动 改进模具的材料或硬度
修复模具被冲蚀的部分 改进浇口位置、模具结构和铸造方案 改进模具的材料或硬度
检查浇注温度、循环时间、保压时间及模具温度等参数是否正确, 并严格遵守工艺规程 检查金属液化学成分是否合格 如果是由于局部过热造成局部收缩,可调节该部分的冷却水量或改 变浇口位置和金属液成分
产生漩涡,包住空气及冷金属,使铸件产生气孔 及氧化夹杂缺陷。
冲刷模具型腔,加剧磨损,缩短模具使用寿命
速度设定 一速 2000±500MM/S 二速 4000±2000MM/S 切换位置 20±10MM
3、压力
压射力是压铸机压射机构中推动压射活塞 运动的力。压射力是由泵产生压力油,并 通过蓄压罐,在压射缸内传递给压射活塞, 再由压射活塞传递给压射冲头,进而推动 金属液填充入模具型腔中。
(2)金属液温度
①浇注温度的作用及影响
提高浇注温度可以提高金属液的流动性, 有利于铸件表面质量的改善,但气体在金 属液内的溶解度及金属液的氧化增加,使 压铸模的寿命减短,并且易造成粘模。
低的浇注温度会降低金属液的流动性,但 可采用增大排气槽深度来改善排气条件; 由于低温的金属液在压射过程中产生涡流、 包气的可能性减小,铸件内在质量提高, 减小了因壁厚差而在厚壁处产生缩松及气 孔的可能性,同时减少了金属液对模具的 熔蚀及粘模,从而延长了模具使用寿命。
压铸机选用压铸工艺参数设定和调节
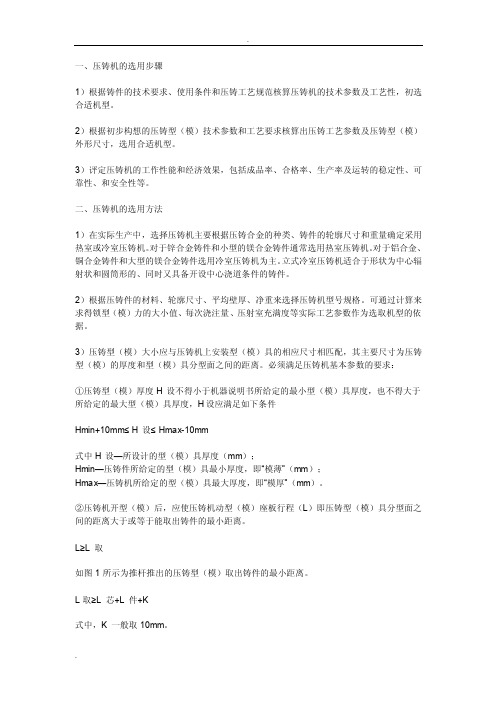
一、压铸机的选用步骤1)根据铸件的技术要求、使用条件和压铸工艺规范核算压铸机的技术参数及工艺性,初选合适机型。
2)根据初步构想的压铸型(模)技术参数和工艺要求核算出压铸工艺参数及压铸型(模)外形尺寸,选用合适机型。
3)评定压铸机的工作性能和经济效果,包括成品率、合格率、生产率及运转的稳定性、可靠性、和安全性等。
二、压铸机的选用方法1)在实际生产中,选择压铸机主要根据压铸合金的种类、铸件的轮廓尺寸和重量确定采用热室或冷室压铸机。
对于锌合金铸件和小型的镁合金铸件通常选用热室压铸机。
对于铝合金、铜合金铸件和大型的镁合金铸件选用冷室压铸机为主。
立式冷室压铸机适合于形状为中心辐射状和圆筒形的、同时又具备开设中心浇道条件的铸件。
2)根据压铸件的材料、轮廓尺寸、平均壁厚、净重来选择压铸机型号规格。
可通过计算来求得锁型(模)力的大小值、每次浇注量、压射室充满度等实际工艺参数作为选取机型的依据。
3)压铸型(模)大小应与压铸机上安装型(模)具的相应尺寸相匹配,其主要尺寸为压铸型(模)的厚度和型(模)具分型面之间的距离。
必须满足压铸机基本参数的要求:①压铸型(模)厚度H 设不得小于机器说明书所给定的最小型(模)具厚度,也不得大于所给定的最大型(模)具厚度,H设应满足如下条件Hmin+10mm≤ H 设≤ Hmax-10mm式中H 设—所设计的型(模)具厚度(mm);Hmin—压铸件所给定的型(模)具最小厚度,即“模薄”(mm);Hmax—压铸机所给定的型(模)具最大厚度,即“模厚”(mm)。
②压铸机开型(模)后,应使压铸机动型(模)座板行程(L)即压铸型(模)具分型面之间的距离大于或等于能取出铸件的最小距离。
L≥L 取如图1所示为推杆推出的压铸型(模)取出铸件的最小距离。
L取≥L 芯+L 件+K式中,K 一般取10mm。
三、压铸机选用方法举例例已知一盒形铸件,如图2所示。
下面以力劲机械厂有限公司生产的卧式冷室压铸机机型技术参数为依据进行选型分析。
压铸模温度场与铸件质量关系的研究与应用
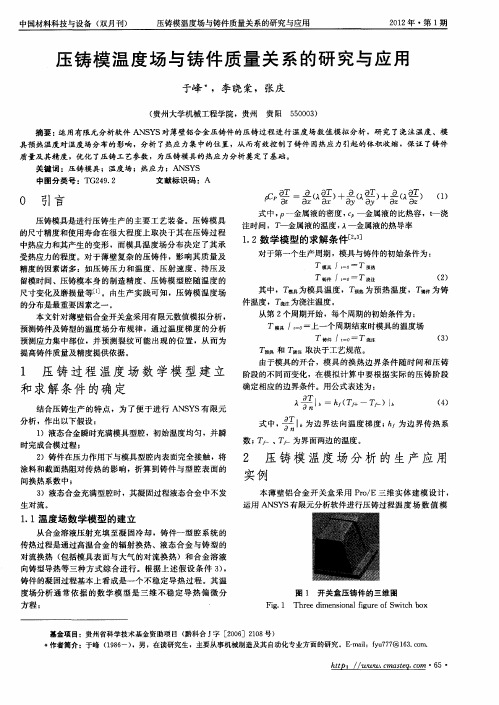
3 ℃为 宜 ,压 铸 铝 合 金 的 浇 注 温 度 一 般 为 6 0 ~ 0 1℃
70 4。为结合实际生产条件 ,模 拟计算 了模具 预热温度 0 ℃[ ] 20 ,浇注温度 分别 为 6 0 ,6 0 ,6 0 时 ,压 铸模 0℃ 3℃ 5℃ 7℃ 具温度场 的分 布 ( 图 4 。 见 )
丁模 / 0 丁预 具 一 热
T铸 / o 件 一丁浇 注 件温度 ,丁 注为浇注温度 。 浇
() 2
其中 ,T 具 模 为模 具温度 ,丁 热 砸 为预热 温度 ,T 件 铸 为铸
从第 2 个周期 开始 ,每个周期的初始条件为 : 丁摸 具/l 一上一个周期结束 时模具 的温度场 : 。
() 4
分析 ,作 出以下假设 :
1 )液态合金 瞬时充满模具型腔 ,初始温度均匀 ,并瞬 时完成合模过程 ;
式中,
I 为边界法向温度梯度; , h 为边界传热系
数 ; s T卜 为界面两边 的温度 。 T -、
2 )铸件在压力作用下与模具 型腔 内表面完全接触 ,将 涂料和截 面热 阻对 传热 的影 响 ,折 算到铸件 与型 腔表面 的
所示 。
p
刍
苫 甚 旨
4 不 同 浇 注 温 度 下模 具 型 腔 表 面 温 度 随 时 间 的 变 化 曲线
口鞫 ●
图 2 定 、动模镶块 t 9 6 s =2 . 5 的温度场分布
Fi . Te p r t r iti u i n o e n g2 m e au e d s rb t fS ta d o
影响压铸件质量的主要因素及控制方法
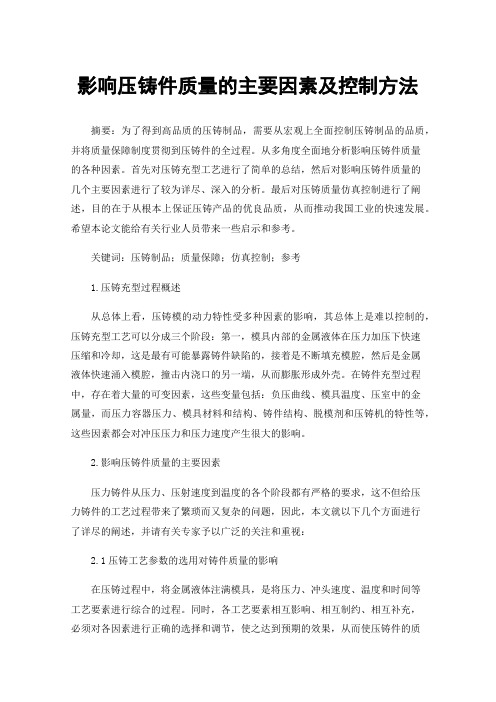
影响压铸件质量的主要因素及控制方法摘要:为了得到高品质的压铸制品,需要从宏观上全面控制压铸制品的品质,并将质量保障制度贯彻到压铸件的全过程。
从多角度全面地分析影响压铸件质量的各种因素。
首先对压铸充型工艺进行了简单的总结,然后对影响压铸件质量的几个主要因素进行了较为详尽、深入的分析。
最后对压铸质量仿真控制进行了阐述,目的在于从根本上保证压铸产品的优良品质,从而推动我国工业的快速发展。
希望本论文能给有关行业人员带来一些启示和参考。
关键词:压铸制品;质量保障;仿真控制;参考1.压铸充型过程概述从总体上看,压铸模的动力特性受多种因素的影响,其总体上是难以控制的,压铸充型工艺可以分成三个阶段:第一,模具内部的金属液体在压力加压下快速压缩和冷却,这是最有可能暴露铸件缺陷的,接着是不断填充模腔,然后是金属液体快速涌入模腔,撞击内浇口的另一端,从而膨胀形成外壳。
在铸件充型过程中,存在着大量的可变因素,这些变量包括:负压曲线、模具温度、压室中的金属量,而压力容器压力、模具材料和结构、铸件结构、脱模剂和压铸机的特性等,这些因素都会对冲压压力和压力速度产生很大的影响。
2.影响压铸件质量的主要因素压力铸件从压力、压射速度到温度的各个阶段都有严格的要求,这不但给压力铸件的工艺过程带来了繁琐而又复杂的问题,因此,本文就以下几个方面进行了详尽的阐述,并请有关专家予以广泛的关注和重视:2.1压铸工艺参数的选用对铸件质量的影响在压铸过程中,将金属液体注满模具,是将压力、冲头速度、温度和时间等工艺要素进行综合的过程。
同时,各工艺要素相互影响、相互制约、相互补充,必须对各因素进行正确的选择和调节,使之达到预期的效果,从而使压铸件的质量得到改善。
本文着重论述了压力和模具温度对铸造工艺的影响。
在铸造过程中,压力是保证铸件组织致密、外形清楚的关键。
在压铸工艺中,压射压力可分为两类:压射力和压射比压。
在压铸机的压射机构中,压射力是一种压力作用于压射活塞的力量。
压铸工艺参数的设定和调节
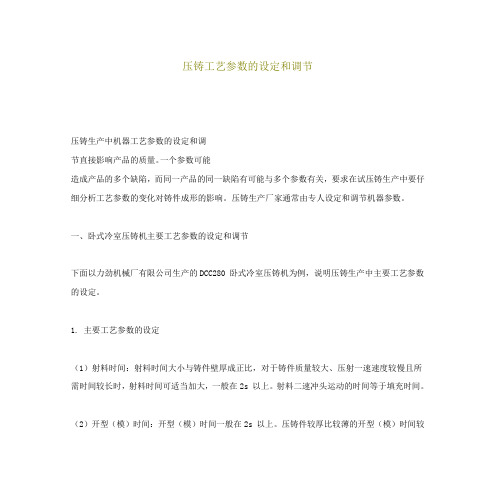
压铸工艺参数的设定和调节压铸生产中机器工艺参数的设定和调节直接影响产品的质量。
一个参数可能造成产品的多个缺陷,而同一产品的同一缺陷有可能与多个参数有关,要求在试压铸生产中要仔细分析工艺参数的变化对铸件成形的影响。
压铸生产厂家通常由专人设定和调节机器参数。
一、卧式冷室压铸机主要工艺参数的设定和调节下面以力劲机械厂有限公司生产的DCC280 卧式冷室压铸机为例,说明压铸生产中主要工艺参数的设定。
1. 主要工艺参数的设定(1)射料时间:射料时间大小与铸件壁厚成正比,对于铸件质量较大、压射一速速度较慢且所需时间较长时,射料时间可适当加大,一般在2s 以上。
射料二速冲头运动的时间等于填充时间。
(2)开型(模)时间:开型(模)时间一般在2s 以上。
压铸件较厚比较薄的开型(模)时间较之要长,结构复杂的型(模)具比结构简单的型(模)具开型(模)时间较之要长。
调节开始时可以略为长一点时间,然后再缩短,注意机器工作程序为先开型(模)后再开安全门,以防止未完全冷却的铸件喷溅伤人。
(3)顶出延时时间:在保证产品充分凝固成型且不粘模的前提下,尽量减短顶出延时时间,一般在0.5s以上。
(4)顶回延时时间:在保证能顺利地取出铸件的前提下尽量减短顶回延时时间,一般在0.5s以上。
(5)储能时间:一般在2s 左右,在设定时操作机器作自动循环运动,观察储能时间结束时,压力是否能达到设定值,在能达到设定压力值的前提下尽量减短储能时间。
(6)顶针次数:根据型(模)具要求来设定顶针次数。
(7)压力参数设定在保证机器能正常工作,铸件产品质量能合乎要求的前提下,尽量减小工作压力。
选择、设定压射比压时应考虑如下因素:1)压铸件结构特性决定压力参数的设定。
①壁厚:薄壁件,压射比压可选高些;厚壁件,增压比压可选高些。
②铸件几何形状复杂程度:形状复杂件,选择高的比压;形状简单件,比压低些。
③工艺合理性:工艺合理性好,比压低些。
2)压铸合金的特性决定压力参数的设定①结晶温度范围:结晶温度范围大,选择高比压;结晶温度范围小,比压低些。
压铸工艺

第三部分压铸工艺一、工艺参数1、压力参数:①压射力用压射压力和压射比压来表示,是获得组织致密、轮廓清晰的压铸件的主要因素,在压铸机上其大小可以调节。
②压射压力压射时压射油缸内的油压,可以从压力表上直接读出,是一个变量,当压铸机进入压射动作时产生压射压力,按照压射动作分段对应的称为一级压射压力(慢压射压力)、二级压射压力(快压射压力)等;增压阶段后转变为增压压力,此时的压射压力达到极大值。
③压射比压压射时压室内金属液在单位面积上所受的压力,简称比压。
可通过改变压射力或更换不同直径的压室及冲头来进行调整。
计算公式为:比压=压射力÷(冲头直径)²×4/π2、速度参数:①压射速度压射时冲头移动的速度。
按照压射过程的不同阶段,压射速度分为慢压射速度(低速压射速度)和快压射速度(高速压射速度)。
一般慢压射速度的选择根据“压室充满度”(即压室内金属液的多少,用百分比快压射速度,是在一定填充时间条件下确定的。
根据铸件的结构特征确定其填充时间后,可用以下公式进行计算:快压射速度=坯件重量/合金比重/压室内截面积/填充时间×[1+(N-1)+0.1]式中“坯件重量”含浇冒系统;“N”为型腔穴数;“填充时间”可查表得到。
按此公式计算出来的快压射速度,是获得优质铸件的理论速度,实际生产中选其1.2倍;对有较大镶嵌件的铸件时可选1.5~2倍。
②内浇口速度金属液在压力作用下通过内浇道导入型腔时的线速度,称为内浇口速度。
内浇口速度对铸件质量有着重要影响,主要是表面光洁度、强度和塑性等方面。
内浇口速度的大小可通过查表得到,调节的方法有:调整压射速度、改变压室直径、调整比压、改变内浇口截面积。
铸件平均壁厚、填充时间、内浇口速度对照表3、时间参数:①填充时间金属液自开始进入型腔到充满铸型的过程所需要的时间。
影响填充时间的因素有:金属液的过热度、浇注温度、模具温度、涂料性能与用量、排气效果等。
决定压铸铝合金铸造性能的冶金因素

决定压铸铝合金铸造性能的冶金因素压铸铝合金的铸造性能受多种冶金因素的影响,这些因素主要包括合金成分、熔炼工艺、铸造工艺以及后续的热处理工艺等。
一、合金成分1. 主元素(1)铝(Al):铝是压铸铝合金的基础,其含量一般在90%以上。
铝的纯度对合金性能有很大影响,纯度越高,合金的铸造性能越好。
(2)硅(Si):硅是压铸铝合金中的主要合金元素,其含量一般在4%13%之间。
硅能显著改善合金的流动性和收缩性能,提高铸件的致密性。
但过高的硅含量会导致合金的强度和硬度降低,因此需要合理控制。
(3)铜(Cu):铜能提高压铸铝合金的强度和硬度,改善耐腐蚀性。
但铜的加入会使合金的流动性下降,增加热裂倾向。
一般铜含量在1%5%之间。
(4)镁(Mg):镁能提高压铸铝合金的强度和硬度,同时保持良好的塑性。
但过高的镁含量会导致合金的热裂倾向增加,镁含量一般在0.5%3%之间。
2. 微量元素(1)铁(Fe):铁在压铸铝合金中通常以杂质形式存在,其含量应控制在0.5%以下。
过高的铁含量会降低合金的塑性和韧性,增加热裂倾向。
(2)锌(Zn):锌可以提高压铸铝合金的强度和硬度,但过多会增加热裂倾向。
锌含量一般在1%8%之间。
(3)锰(Mn):锰能提高压铸铝合金的强度和硬度,同时改善耐腐蚀性。
但过高的锰含量会降低合金的塑性,锰含量一般在0.5%1.5%之间。
二、熔炼工艺1. 炉料炉料的选用对压铸铝合金的性能具有重要影响。
炉料主要包括纯铝、铝硅合金、铝铜合金等。
合理搭配炉料,可以使合金成分均匀,提高熔炼质量。
2. 熔炼设备熔炼设备的选择对熔炼质量有很大影响。
常用的熔炼设备有电阻炉、中频炉、燃气炉等。
不同设备具有不同的熔炼特点和适用范围。
3. 熔炼工艺参数熔炼工艺参数包括熔炼温度、熔炼时间、搅拌速度等。
合理的熔炼工艺参数可以保证合金成分均匀,减少气孔、夹渣等缺陷。
4. 精炼和变质处理精炼和变质处理是提高压铸铝合金性能的关键工艺。
精炼可以去除合金中的气体和杂质,变质处理可以改善合金的组织结构,提高铸造性能。
影响压铸件质量的主要工艺参数

影响压铸件质量的主要工艺参数影响压铸件质量的主要工艺参数包括:1. 压铸工艺温度:压铸件在铸造过程中需要加热熔化金属材料,温度是影响铸件质量的重要因素。
如果温度过高,会导致熔融金属过热,容易产生气孔、缩松等缺陷;如果温度过低,会使铸件成型不完全,表面质量差,容易出现可见缺陷。
2. 压铸压力:压铸压力直接影响到铸件的密度和凝固过程。
过高的压力会使得铸件的细小部分压缩不够,导致铸件中出现气孔、缩松等缺陷;过低的压力则会造成铸件形状不完美,容易产生气孔、翘曲等问题。
3. 注射速度:注射速度是指金属材料进入模具中的速度。
过快的注射速度会导致金属材料冲击力大,易引起气门过冲、表面润色不均等问题;过慢的注射速度则会导致凝固时间过长,容易产生热裂、夹杂等缺陷。
4. 冷却时间:冷却时间是指铸件在模具中冷却至一定温度的时间。
冷却时间过短会导致铸件内部温度分布不均,容易产生热裂、夹杂等缺陷;冷却时间过长则会使生产率降低,成本增加。
5. 模具温度:模具温度直接影响到铸件的凝固速度和整体质量。
模具温度过高会导致金属熔化过快,铸件表面质量较差;模具温度过低则会导致凝固时间延长,生产效率低下。
6. 浇注系统设计:浇注系统包括喷嘴、导槽、浇注口等部分,直接影响到金属材料进入模具的流动性和冷却性能。
如果浇注系统设计不合理,易产生气孔、错流、夹杂等缺陷。
总之,以上主要工艺参数都会对压铸件的质量产生重要影响。
为了获得高质量的压铸件,需要在生产过程中合理控制这些参数,并确保每个参数都处于最佳范围内。
影响压铸件质量的主要工艺参数是压铸生产中非常重要的一环。
通过合理控制这些参数,可以有效地提高压铸件的质量,确保其达到设计要求。
首先,压铸工艺温度是影响压铸件质量的关键参数之一。
合适的温度可以保证金属材料完全熔化,使金属液体顺利流入模具中,并在合适的速度冷却凝固,从而获得高密度、无缺陷的铸件。
如果温度过高,会使金属液体过热,容易产生气孔、缩松等缺陷;相反,如果温度过低,会导致铸件成型不完全,表面质量差,容易出现可见缺陷。
压铸工艺对压铸件质量影响的研究现状及发展
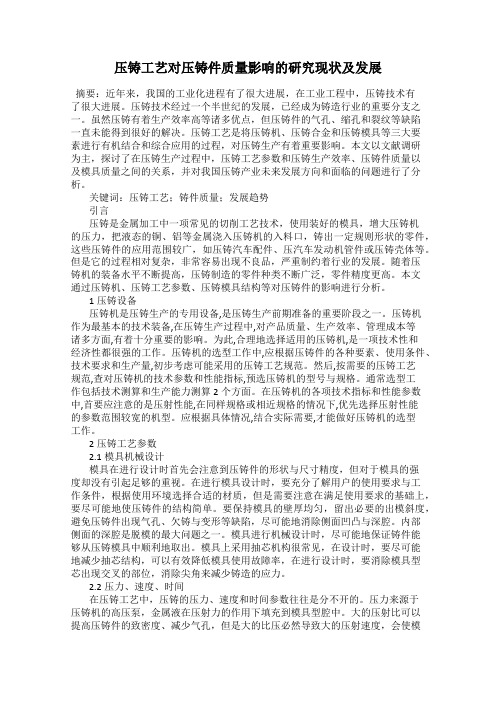
压铸工艺对压铸件质量影响的研究现状及发展摘要:近年来,我国的工业化进程有了很大进展,在工业工程中,压铸技术有了很大进展。
压铸技术经过一个半世纪的发展,已经成为铸造行业的重要分支之一。
虽然压铸有着生产效率高等诸多优点,但压铸件的气孔、缩孔和裂纹等缺陷一直未能得到很好的解决。
压铸工艺是将压铸机、压铸合金和压铸模具等三大要素进行有机结合和综合应用的过程,对压铸生产有着重要影响。
本文以文献调研为主,探讨了在压铸生产过程中,压铸工艺参数和压铸生产效率、压铸件质量以及模具质量之间的关系,并对我国压铸产业未来发展方向和面临的问题进行了分析。
关键词:压铸工艺;铸件质量;发展趋势引言压铸是金属加工中一项常见的切削工艺技术,使用装好的模具,增大压铸机的压力,把液态的铜、铝等金属浇入压铸机的入料口,铸出一定规则形状的零件,这些压铸件的应用范围较广,如压铸汽车配件、压汽车发动机管件或压铸壳体等。
但是它的过程相对复杂,非常容易出现不良品,严重制约着行业的发展。
随着压铸机的装备水平不断提高,压铸制造的零件种类不断广泛,零件精度更高。
本文通过压铸机、压铸工艺参数、压铸模具结构等对压铸件的影响进行分析。
1压铸设备压铸机是压铸生产的专用设备,是压铸生产前期准备的重要阶段之一。
压铸机作为最基本的技术装备,在压铸生产过程中,对产品质量、生产效率、管理成本等诸多方面,有着十分重要的影响。
为此,合理地选择适用的压铸机,是一项技术性和经济性都很强的工作。
压铸机的选型工作中,应根据压铸件的各种要素、使用条件、技术要求和生产量,初步考虑可能采用的压铸工艺规范。
然后,按需要的压铸工艺规范,查对压铸机的技术参数和性能指标,预选压铸机的型号与规格。
通常选型工作包括技术测算和生产能力测算2个方面。
在压铸机的各项技术指标和性能参数中,首要应注意的是压射性能,在同样规格或相近规格的情况下,优先选择压射性能的参数范围较宽的机型。
应根据具体情况,结合实际需要,才能做好压铸机的选型工作。
压铸工艺对压铸件质量影响的研究现状及发展

压铸工艺对压铸件质量影响的研究现状及发展摘要:经过近一个半世纪的发展,压铸工艺已成为铸造工业的一个主要分支。
尽管压铸工艺具有较高的生产质量和较高的生产效率,但是其气孔、缩孔、开裂等问题却没有得到有效的解决。
压铸技术是把压铸机、压铸合金、压铸模三者有机地结合起来,并在一定程度上发挥了压铸技术的作用。
通过对相关文献资料的调查,论述了压铸生产中压铸工艺参数与压铸效率、压铸件、铸件质量与压铸模质量的关系,并对今后压铸工业的发展趋势和存在的问题进行了分析。
关键词:压铸工艺;铸造工业;生产效率;铸模质量引言:压铸是一种在高压力下,将熔化的合金快速填充到模腔中,然后在加压下进行固化。
与其它成形工艺相比,由于压铸工艺具有高的尺寸精度、高生产率、少或无切削、能形成复杂的形状结构,因而受到广泛的关注。
压铸件不仅应用于汽车、摩托车、仪表、工业电器等领域,也可应用于家用电器、农机、纺织、通讯、计算机等领域。
压铸技术包括压铸机、压铸合金和压铸模三大要素,压铸技术是三个因素的有机结合和综合运用。
铝合金是压铸合金中的主要成分,占了70%。
1.压铸工艺参数压铸技术是压铸工艺中各种因素的综合运用,它直接关系到压铸制品的质量和使用寿命。
本文从压力、速度、时间、温度四方面分析了压铸过程中的问题。
由于压铸设备的造价高、操作复杂、风险大、实际压铸试验数据难以获得,因此采用了采用铸件仿真软件和试验相结合的方法,既缩短了试制周期,降低了铸件的废品率,提高了生产效率,也有利于了解铸件的缺陷成因,研究压铸工艺参数与铸件显微结构的关系,提高铸件的质量。
1.1压力、速度、时间在铸造过程中,压力、速度、时间等因素的影响是必不可少的。
压力来自于压铸机的高压泵,通过压力将金属液体注入模腔。
较大的压力比能提高铸件的致密度,减少气孔,但较大的比压必然会导致较大的压射速率,从而对模具产生较强的冲击,从而缩短了模具的使用寿命。
HodaDini等对压铸AZ91D铸造过程中的变形及残余应力进行了分析,发现在压铸过程中,压铸压力对铸件的变形及残余应力有很大的影响。
工艺参数对AE44镁合金外壳压铸件组织和性能的影响
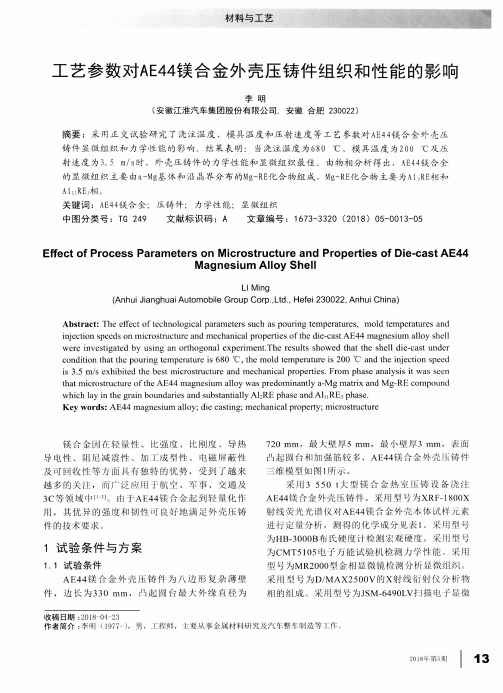
fAnhui Jianghuai Automobile Group Corp.,Ltd.,Hefei 230022,Anhui China)
Abstract:The efect of technological parameters such as pourmg tem peratures, mold temperatures and
采 ,I_f=j 3 5 50 t大 型 镁 合 金 热 室 铸 改 符 浇 注 AE44镁 合 金 外 壳压 铸 件 。采 用 掣 号 为XRF—l 800X 射 线 荧 光 光 谱 仪 埘 AE44镁 合 金 外 壳 本 体 试 样 元素 进 行 定 分 , 测 得 的化 学成 分 见表 1。采 川 型 号 为HB.3000B布 氏硬 度 计一检 测 宏 观硬 度 。 川 型 号 为CMT5105电 :月 能 试 验 机 检 测 力学 性 能 。 采 用 型 号为MR2000型金 相 显做 镜 愉 测 分析 微 引【织 。 采 用 型 ·为 D/MAX2500V的x射 线 衍射 仪 分析 物 相 的 组 成 。采 川 型 号 为JSM一6490LV:[:I描 电 r显 微
conditi0n that the pouring temperature is 680。C,the mold temperature is 200℃ and the injection speed
iS 3.5 m /s exhibited the best m icrostructure and m echanical pl-operhes.From phase analysis it w as seell that m icrostructure of the AE44 m agnesium alloy was predom inantly a-M g m atrix and M g—RE compound w hich lay in the grain boundaries and substantially A 12RE phase and A l l l R E3 phase. Kev words:AE44 magnesium alloy;die casting;mechanicaI property;m lcrostructure
压铸机工艺参数的设定和调节方法(20200731151119).pdf
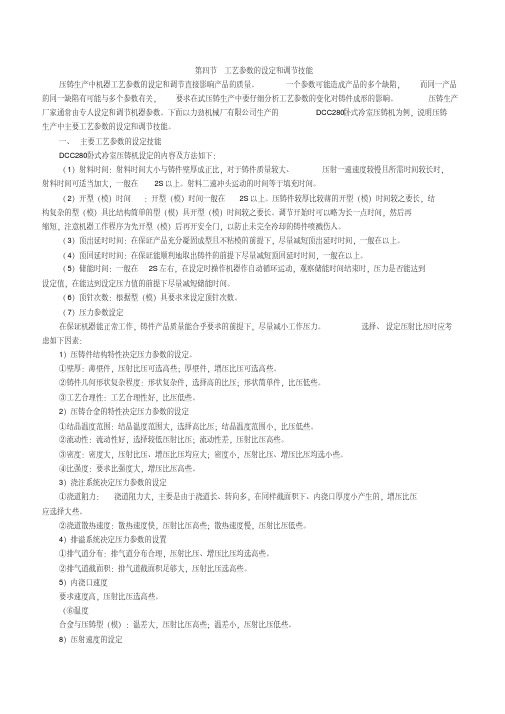
第四节工艺参数的设定和调节技能压铸生产中机器工艺参数的设定和调节直接影响产品的质量。
一个参数可能造成产品的多个缺陷,而同一产品的同一缺陷有可能与多个参数有关,要求在试压铸生产中要仔细分析工艺参数的变化对铸件成形的影响。
压铸生产厂家通常由专人设定和调节机器参数。
下面以力劲机械厂有限公司生产的DCC280卧式冷室压铸机为例,说明压铸生产中主要工艺参数的设定和调节技能。
一、主要工艺参数的设定技能DCC280卧式冷室压铸机设定的内容及方法如下:(1)射料时间:射料时间大小与铸件壁厚成正比,对于铸件质量较大、压射一速速度较慢且所需时间较长时,射料时间可适当加大,一般在2S以上。
射料二速冲头运动的时间等于填充时间。
(2)开型(模)时间:开型(模)时间一般在2S以上。
压铸件较厚比较薄的开型(模)时间较之要长,结构复杂的型(模)具比结构简单的型(模)具开型(模)时间较之要长。
调节开始时可以略为长一点时间,然后再缩短,注意机器工作程序为先开型(模)后再开安全门,以防止未完全冷却的铸件喷溅伤人。
(3)顶出延时时间:在保证产品充分凝固成型且不粘模的前提下,尽量减短顶出延时时间,一般在以上。
(4)顶回延时时间:在保证能顺利地取出铸件的前提下尽量减短顶回延时时间,一般在以上。
(5)储能时间:一般在2S左右,在设定时操作机器作自动循环运动,观察储能时间结束时,压力是否能达到设定值,在能达到设定压力值的前提下尽量减短储能时间。
(6)顶针次数:根据型(模)具要求来设定顶针次数。
(7)压力参数设定在保证机器能正常工作,铸件产品质量能合乎要求的前提下,尽量减小工作压力。
选择、设定压射比压时应考虑如下因素:1)压铸件结构特性决定压力参数的设定。
①壁厚:薄壁件,压射比压可选高些;厚壁件,增压比压可选高些。
②铸件几何形状复杂程度:形状复杂件,选择高的比压;形状简单件,比压低些。
③工艺合理性:工艺合理性好,比压低些。
2)压铸合金的特性决定压力参数的设定①结晶温度范围:结晶温度范围大,选择高比压;结晶温度范围小,比压低些。
影响压铸件质量的主要工艺参数
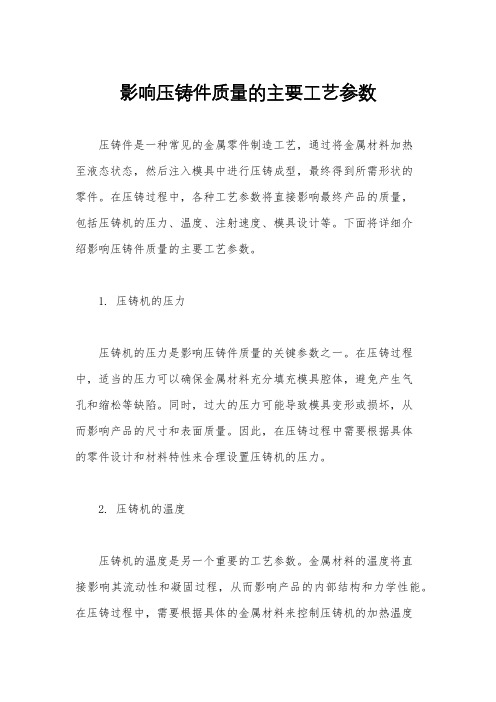
影响压铸件质量的主要工艺参数压铸件是一种常见的金属零件制造工艺,通过将金属材料加热至液态状态,然后注入模具中进行压铸成型,最终得到所需形状的零件。
在压铸过程中,各种工艺参数将直接影响最终产品的质量,包括压铸机的压力、温度、注射速度、模具设计等。
下面将详细介绍影响压铸件质量的主要工艺参数。
1. 压铸机的压力压铸机的压力是影响压铸件质量的关键参数之一。
在压铸过程中,适当的压力可以确保金属材料充分填充模具腔体,避免产生气孔和缩松等缺陷。
同时,过大的压力可能导致模具变形或损坏,从而影响产品的尺寸和表面质量。
因此,在压铸过程中需要根据具体的零件设计和材料特性来合理设置压铸机的压力。
2. 压铸机的温度压铸机的温度是另一个重要的工艺参数。
金属材料的温度将直接影响其流动性和凝固过程,从而影响产品的内部结构和力学性能。
在压铸过程中,需要根据具体的金属材料来控制压铸机的加热温度和保持温度,以确保金属材料能够充分流动并获得良好的凝固组织。
3. 注射速度注射速度是影响压铸件质量的另一个重要参数。
适当的注射速度可以确保金属材料在注射过程中充分填充模具腔体,并避免产生气孔和冷隔等缺陷。
同时,过快的注射速度可能导致金属材料在注射过程中产生过大的流动阻力,从而影响产品的表面质量和尺寸精度。
因此,在压铸过程中需要根据具体的零件设计和模具结构来合理设置注射速度。
4. 模具设计模具设计是影响压铸件质量的另一个重要因素。
合理的模具设计可以确保产品的尺寸精度和表面质量,并避免产生气孔、冷隔和浇口等缺陷。
在模具设计中,需要考虑产品的结构特点、材料流动路径、浇口和冷却系统等因素,以确保产品能够获得良好的凝固组织和表面质量。
5. 金属材料金属材料的选择将直接影响压铸件的质量和性能。
不同的金属材料具有不同的凝固特性和机械性能,因此在压铸过程中需要根据具体的零件设计和使用要求来选择合适的金属材料。
同时,需要注意金属材料的熔点、流动性和气体溶解度等特性,以确保产品能够获得良好的凝固组织和力学性能。
铝合金超低速压铸工艺参数对铸件性能的影响
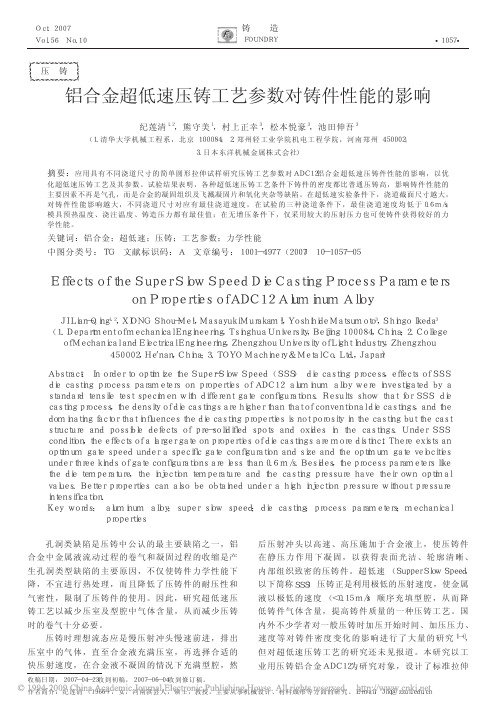
J I Lia n-Qing1, 2, XIONG S hou-Me i1, Ma s a yuki Mura ka mi3, Yos hihide Ma ts umoto3, S hingo Ike da 3 ( 1. De pa rtme nt of me cha nica l Engine e ring, Ts inghua Unive rs ity, Be ijing 100084, China ; 2. Colle ge
·1058·
FOUNDRY
Oct. 2007 Vol.56 No.10
试棒金属模具并进行超低速压铸试验, 从铸件密度、 力学性能、组织等方面, 考察不同超低速压铸工艺参 数对铸件力学性能的影响。
1 试验过程
1.1 试验材料 试验所选材料为商业用压铸铝合金JIS ( 日本工业标
准) ADC12, 用ICP ( 等离子体发射光谱仪Vista-MPX) 测 得 其 化 学 成 分 ( 质 量 分 数 , %, 下 同) 为11.25 Si、 3.09 Fe、2.51 Cu、0.21 Mn、0.096 Mg、1.74 Zn, 其 余 为Al。 1.2 超低速压铸工艺参数
图1 超低速压铸件试样及尺寸 Fig. 1 SSS die cast test specimen and dimension
2 试验结果及讨论
2.1 模具预热温度对超低速压铸件的性能影响 模具预热温度分别采用100 ℃、150 ℃及200 ℃三
种, 其它压铸成形参数固定, 性能测试结果列于表1。 从表1可以看出, 在模具预热温度为150 ℃时, 超
关键词: 铝合金; 超低速; 压铸; 工艺参数; 力学性能 中图分类号: TG 文献标识码: A 文章编号: 1001- 4977 ( 2007) 10- 1057- 05
压力铸造“三要素”分析实
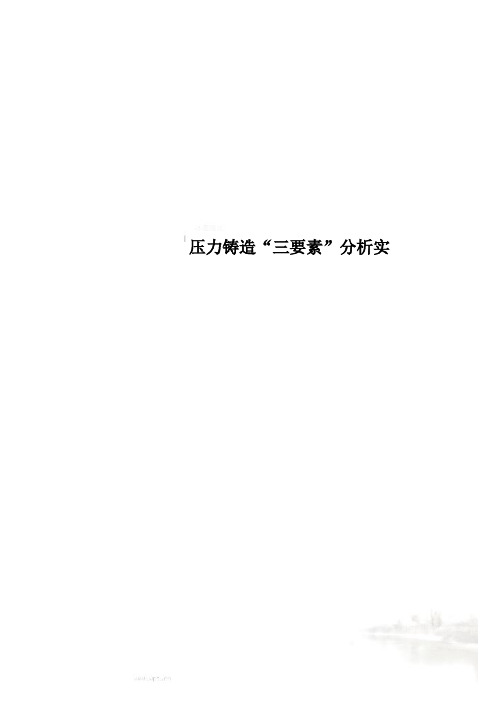
压力铸造“三要素”分析实压力铸造“三要素”分析实压铸模、压铸机、压铸工艺是压力铸造关键的“三要素”。
这三要素是保证压铸件质量、提高压铸件生产效率、降低压铸生产成本的重要因素。
三者之间的关系和作用如下所述:压铸模—是压力铸造中最重要的工具,它是三要素中最关键的要素。
只要压铸模具备了合理的澆注系统,合理的模具结构,又有合理的模具制造精度,就具备了压力铸造的重要条件。
它可以弥补压铸机的某些不足,也可以放宽对压铸工艺参数相应的调整范围,这就给压铸生产带来极大的方便,压铸工艺参数的调整就方便得多,这就加大了保证铸质量的可靠性。
有人说压力铸造需要打造尽量多的傻瓜(非常方便调整工艺参数的)模具也就是此意思。
有很多人说压铸模在压力铸造技术中的重要性占60%的比重,又有很多人说它在压力铸造中的重要性占70—80%的比重,不管是多少,这就反应出压铸模它在众多人心目中的重要性了。
总之压铸模的重要性它占据了三要素之首。
压铸机—是在压力铸造中的一个重要设备。
;是压力铸造成功的一个重要条件;它既是模具安装的场地;又是工艺参数调节处所,起到承上启下的重要作用。
压铸机性能的好坏,直接影响到所生产的压铸件质量和生产效率高低。
压铸工艺参数—实际上是把压铸模具和压铸机联系起来的纽带。
如果有了质量好的模具和性能较好的压铸机,压铸工艺参数的调节范围就放宽多了,工艺参数调整就很方便了。
如果前述的某一个条件较差,工艺参数的调整就困难多,即是调整好了,一但某个工艺因素略有所变动,就直接影响到压铸件生产质量和生产效率,造成生产质量不稳定。
所以压铸工艺参数一定要弥补前两者之不足。
前三者必须是密切配合的情况下,才能对提高压铸件质量,给压力铸造带来整体效益。
每一个压铸工作者,应在实际生产实践中要认清三者的关系,来处理好生产中的实际问题。
分析方法,可参考下述实例进行:例一:成都卑县某公司,将原有800吨压铸机上生产的模具,放到新购的某厂生产的850吨压铸机上生产,所生产出来的压铸件经喷丸后表面多处起皮,尤在内浇口附近均有,生产出来的压铸件质量满足不了铸件用户的要求。
- 1、下载文档前请自行甄别文档内容的完整性,平台不提供额外的编辑、内容补充、找答案等附加服务。
- 2、"仅部分预览"的文档,不可在线预览部分如存在完整性等问题,可反馈申请退款(可完整预览的文档不适用该条件!)。
- 3、如文档侵犯您的权益,请联系客服反馈,我们会尽快为您处理(人工客服工作时间:9:00-18:30)。
压铸工艺参数与铸件质量的关系
一、压铸工艺参数
压铸工艺参数主要有压力,速度、温度和时间。
这些参数是相辅相成,而又相互制约的。
1.压力——在压铸中,压力可用压射力和压射比压来表达 (1)压射力——是压铸机压射油缸推动压射活塞运动的力
P 压=
024
P D π
P 压——压射力(N)
P 0——压射油缸内工作液的压力(MPa) D ——压射油缸内径(mm)
(2)压射比压——压射时压室内金属液单位面积上所承受的压力
2
4d
P P π压= P ——压射比压(MPa)
d ——压室(冲头)直径(mm) 压射比压的调整(内浇口面积不变时)主要是调整压铸机的压射力或改变压室的直径。
(3)选择压射比压所考虑的主要因素见下表
压射比压过小,会使充填时间增长,降低压射速度,使压铸件出现流痕、花纹,轮廓不清,甚至出现冷隔、缩松、缩孔;压射比压过大,铸件产生飞边和气孔。
2.速度
速度分为压射速度和充填速度
(1)压射速度是压射冲头推动金属液时的移动速度(也称冲头速度)。
在压射运动中压射速度分为慢(低)压射速度和快压射速度。
压铸开始时采用慢压射速度以利于排除压室内的气体和减少压力损失。
快压射速度大小直接影响金属的充填速度。
(2)充填速度
充填速度是金属液在压力作用下通过内浇口进入型腔的线速度,又称内浇口充填速度。
充填速度的调节一般用调整压射冲头速度,更换压室直径和改变内浇口面积来实现,即:冲头面积×冲头速度=内浇口截面积×充填速度。
通常选用内浇口充填速度范围:锌合金为25~50m/s,铝合金30-60m/s,镁合金为40-100 m/s。
一般要求不高的压铸件、厚壁、简单件取小值,要求质量高与受力件和壁薄、复杂件取大值。
充填速度过大,产生喷射,易堵塞排气道,出现气孔。
充填速度不够则会容易产生铸件轮廓不清、流痕和花纹,甚至会出现冷隔和缺肉等缺陷。
3.温度
温度有浇注温度与模具温度。
(1)浇注温度
一般指金属液浇入压射室至填充型腔时间段内的平均温度。
通常在保证填充成型和达到质量要求的前提下,采用尽可能低的温度;一般以高于压铸合金液相温度10-20℃为宜,各种合金温度选择范围如下:
锌合金为410℃-450℃;
铝合金为620℃-720℃;
镁合金为610℃-680℃;
选择时应考虑如下因素:合金流动性,铸件复杂程度、壁厚,模具热容量大小与散热的快慢。
浇注温度高低直接关系到裂纹、冷隔、缩孔、缩松和粘模等缺陷的产生。
(2)模具温度
模具温度直接影响到铸件质量和压铸模的寿命,在生产前要进行预热,在压铸过程要保持一定的温度,压铸型的预热温度和工作温度选择参考下表。
铸型预热及工作温度不够,容易产生铸件欠铸、冷隔、流痕;温度过高则易产生粘模,铸件表面出现气泡等缺陷。
4.时间
(1)充填时间
金属液从内浇口开始进入型腔到充满型腔所需时间称为充填时间。
充填时间与比压、内浇口速度、内浇口截面面积有关:
T⋅
=/
F
Q
V
T——充填时间(S);
Q——进入铸型金属液体积(M3);
F——为内浇口截面积(M2);
V——内浇口速度(m/s)。
影响充填时间的因素有:浇注温度与模具温度、铸型型腔结构、铸件壁厚、排气效果、金属液过热度和涂料有关。
充填时间过长,铸件易出现流痕、冷隔、缺肉等缺陷。
选用参考值见《压铸实用技术》表16-3。
(2)持压时间
金属液充满型腔之后,在压力作用下使铸件完全凝固,这段时间称为持压时间,持压时间长短与铸件壁厚和金属结晶温度范围有关。
持压时间不够,不利于压力传递和金属液补缩,使铸件组织不致密。
持压时间的选择可参考《压铸实用技术》表16-4。
(3)留模时间
从持压终了至开模顶出铸件为止的时间称为留模时间,留模时间根据合金性质、铸件结构和壁厚确定。
合金收缩率大、热强度高留模时间可短些,壁薄、结构较复杂的铸件留模时间可短些;常以铸件顶出不变形、不开裂的最短时间为宜。
留模时间不够,铸件内气体膨胀形成气泡;同时,铸件得不到充分冷却,被顶出铸型时会发生变形、甚至出现裂纹等缺陷。
留模时间的选用见《压铸实用技术》表16-5。
二、工艺参数与压铸件质量
综上所述,工艺参数与压铸件质量(部分缺陷)的关系可汇总下表:。