齿轮的变位系数
变位系数
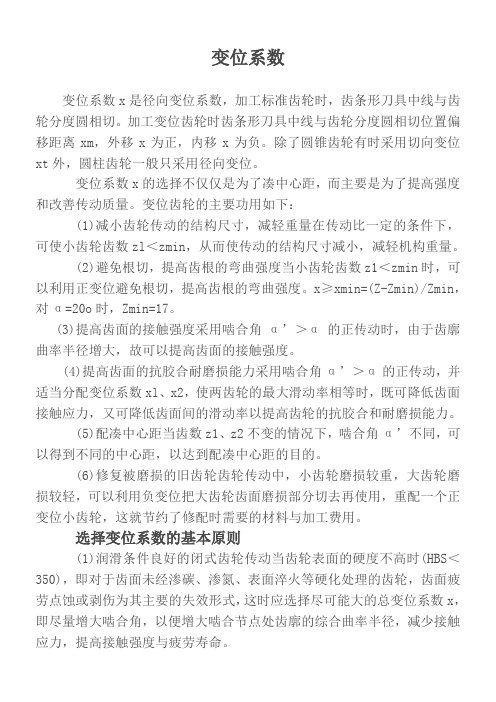
变位系数变位系数x是径向变位系数,加工标准齿轮时,齿条形刀具中线与齿轮分度圆相切。
加工变位齿轮时齿条形刀具中线与齿轮分度圆相切位置偏移距离xm,外移x为正,内移x为负。
除了圆锥齿轮有时采用切向变位xt外,圆柱齿轮一般只采用径向变位。
变位系数x的选择不仅仅是为了凑中心距,而主要是为了提高强度和改善传动质量。
变位齿轮的主要功用如下:(1)减小齿轮传动的结构尺寸,减轻重量在传动比一定的条件下,可使小齿轮齿数zl<zmin,从而使传动的结构尺寸减小,减轻机构重量。
(2)避免根切,提高齿根的弯曲强度当小齿轮齿数z1<zmin时,可以利用正变位避免根切,提高齿根的弯曲强度。
x≥xmin=(Z-Zmin)/Zmin,对α=20o时,Zmin=17。
(3)提高齿面的接触强度采用啮合角α’>α的正传动时,由于齿廓曲率半径增大,故可以提高齿面的接触强度。
(4)提高齿面的抗胶合耐磨损能力采用啮合角α’>α的正传动,并适当分配变位系数xl、x2,使两齿轮的最大滑动率相等时,既可降低齿面接触应力,又可降低齿面间的滑动率以提高齿轮的抗胶合和耐磨损能力。
(5)配凑中心距当齿数z1、z2不变的情况下,啮合角α’不同,可以得到不同的中心距,以达到配凑中心距的目的。
(6)修复被磨损的旧齿轮齿轮传动中,小齿轮磨损较重,大齿轮磨损较轻,可以利用负变位把大齿轮齿面磨损部分切去再使用,重配一个正变位小齿轮,这就节约了修配时需要的材料与加工费用。
选择变位系数的基本原则(1)润滑条件良好的闭式齿轮传动当齿轮表面的硬度不高时(HBS<350),即对于齿面未经渗碳、渗氮、表面淬火等硬化处理的齿轮,齿面疲劳点蚀或剥伤为其主要的失效形式,这时应选择尽可能大的总变位系数x,即尽量增大啮合角,以便增大啮合节点处齿廓的综合曲率半径,减少接触应力,提高接触强度与疲劳寿命。
当轮齿表面硬度较高时(HBS>350),常因齿根疲劳裂纹的扩展造成轮齿折断而使传动失效,这时,选择变位系数应使齿轮的齿根弯曲强度尽量增大,并尽量使相啮合的两齿轮具有相近的弯曲强度。
变位斜齿轮变位系数计算公式
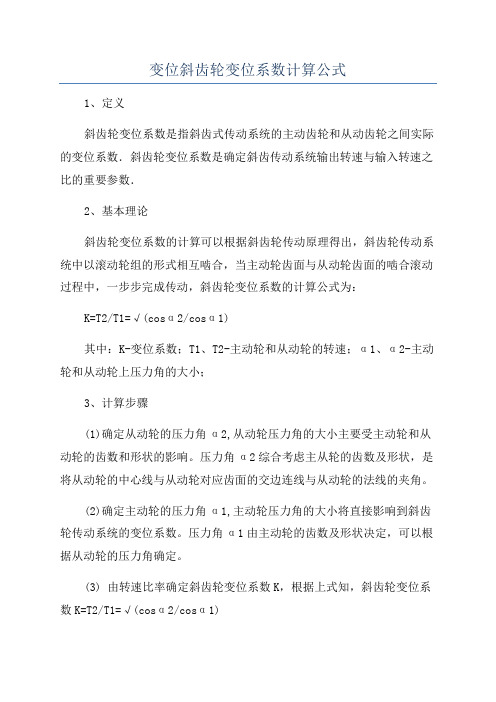
变位斜齿轮变位系数计算公式
1、定义
斜齿轮变位系数是指斜齿式传动系统的主动齿轮和从动齿轮之间实际的变位系数.斜齿轮变位系数是确定斜齿传动系统输出转速与输入转速之比的重要参数.
2、基本理论
斜齿轮变位系数的计算可以根据斜齿轮传动原理得出,斜齿轮传动系统中以滚动轮组的形式相互啮合,当主动轮齿面与从动轮齿面的啮合滚动过程中,一步步完成传动,斜齿轮变位系数的计算公式为:
K=T2/T1=√(cosα2/cosα1)
其中:K-变位系数;T1、T2-主动轮和从动轮的转速;α1、α2-主动轮和从动轮上压力角的大小;
3、计算步骤
(1)确定从动轮的压力角α2,从动轮压力角的大小主要受主动轮和从动轮的齿数和形状的影响。
压力角α2综合考虑主从轮的齿数及形状,是将从动轮的中心线与从动轮对应齿面的交边连线与从动轮的法线的夹角。
(2)确定主动轮的压力角α1,主动轮压力角的大小将直接影响到斜齿轮传动系统的变位系数。
压力角α1由主动轮的齿数及形状决定,可以根据从动轮的压力角确定。
(3) 由转速比率确定斜齿轮变位系数K,根据上式知,斜齿轮变位系数K=T2/T1=√(cosα2/cosα1)
4、示例
以下计算题示例:。
变位齿轮的计算方法

变位齿轮的计算方法1 变位齿轮的功用及变位系数变位齿轮具有以下功用:(1)避免根切;(2)提高齿面的接触强度和弯曲强度;(3)提高齿面的抗胶合和耐磨损能力;(4)修复旧齿轮;(5)配凑中心距。
对于齿数z=8~20的直齿圆柱齿轮,当顶圆直径d a=mz+2m+2xm时,不产生根切的最小变位系数x min,以及齿顶厚S a=0.4m和S a=0时的变位系数x sa=0.4m和x sa=0如表1所列。
2 变位齿轮的简易计算将变位齿轮无侧隙啮合方程式作如下变换:总变位系数中心距变动系数齿顶高变动系数表 1 齿数z=8~20圆柱齿轮的变位系数z x min x sa=0.4m x sa=08 910111213141516171819 200.53 0.47 0.42 0.36 0.30 0.24 0.18 0.12 0.06 0-0.05 -0.11 -0.170.180.220.270.310.350.390.430.460.500.530.560.590.620.560.630.700.760.820.880.930.981.031.081.131.181.23或Δy=xΣ-y式中:α——压力角,α=20°;α′——啮合角;z2、z1——大、小齿轮的齿数。
将上述三式分别除以,则得:由上述公式可以看出,当齿形角α一定时,x z、y z和Δy z均只为啮合角α′的函数。
在设计计算时,只要已知x z、y z、Δy z和α′四个参数中的任一参数,即可由变位齿轮的x z、y z、Δy z和啮合角α′的数值表(表2)中,查出其他三个参数,再进行下列计算。
一般齿轮手册上均列有此数值表。
式中正号用于外啮合,负号用于内啮合。
3 计算实例例1:已知一对外啮合变位直齿轮,齿数z1=18,z2=32,压力角α=20°,啮合角α′=22°18′,试确定总变位系数xΣ、中心距变动系数y及齿顶高变动系数Δy。
齿轮变位系数

变位系数名称由来标准齿轮传动存在着一些局限性:(1)受根切限制,齿数不得少于Zmin,使传动结构不够紧凑;(2)不适合于安装中心距a'不等于标准中心距a的场合。
当a'<a时无法安装,当a'>a时,虽然可以安装,但会产生过大的侧隙而引起冲击振动,影响传动的平稳性;(3)一对标准齿轮传动时,小齿轮的齿根厚度小而啮合次数又较多,故小齿轮的强度较低,齿根部分磨损也较严重,因此小齿轮容易损坏,同时也限制了大齿轮的承载能力。
齿轮传动示意图为了改善齿轮传动的性能,出现了变位齿轮。
如图所示,当齿条插刀齿顶线超过极限啮合点N1,切出来的齿轮发生根切。
若将齿条插刀远离轮心O1一段距离(xm),齿顶线不再超过极限点N1,则切出来的齿轮不会发生根切,但此时齿条的分度线与齿轮的分度圆不再相切。
这种改变刀具与齿坯相对位置后切制出来的齿轮称为变位齿轮,刀具移动的距离xm称为变位量,x称为变位系数。
刀具远离轮心的变位称为正变位,此时x>0;刀具移近轮心的变位称为负变位,此时x<0。
标准齿轮就是变位系数x=0的齿轮。
概念齿轮的变位系数变位系数 x 是径向变位系数,加工标准齿轮时,齿条形刀具中线与齿轮分度圆相切。
加工变位齿轮时齿条形刀具中线与齿轮分度圆相切位置偏移距离 xm,外移 x 为正,内移 x 为负。
除了圆锥齿轮有时采用切向变位 xt 外,圆柱齿轮一般只采用径向变位。
变位系数 x 的选择不仅仅是为了凑中心距,而主要是为了提高强度和改善传动质量。
主要功用(1)减小齿轮传动的结构尺寸,减轻重量在传动比一定的条件下,可使小齿轮齿数 zl< zmin,从而使传动的结构尺寸减小,减轻机构重量。
(2)避免根切,提高齿根的弯曲强度当小齿轮齿数 z1<zmin 时,可以利用正变位避免根切,提高齿根的弯曲强度。
x≥xmin=(Z-Zmin)/Zmin,对α=20°时,Zmin=17。
直齿圆柱齿轮变位系数、公法线长度、齿厚、最小法向侧隙的计算

外啮合直齿圆柱齿轮变位系数、公法线长度、齿厚、最小法向侧隙的计算1,直齿圆柱齿轮变位系数计算:Case1:a,此处例子仅计算用齿条型刀具加工时的情况(插齿刀加工见相关手册公式):小结:由此可知本例选取的齿数在不变位的情况也不会产生根切现象。
b,根据下图选择大小齿轮的变位系数和x∑。
本例在P6-P7区间取值。
即齿根及齿面承载能力较高区,进行选择。
因大小齿轮的齿数和为18+19=37。
所以本例选择的变位系数和x∑=0.8。
本例我们的两个齿轮在工作时属于减速运动,所以按减速运动的变位系数分配线图,进行2个齿轮的变位系数的选择。
先按(z1+z1)/2=18.5,作为横坐标,做一条垂线(图中蓝色的线),再按x∑/2=0.4,作为纵坐标,做一条水平线(图中橙色的线),接着沿着L线的趋势,穿过上面2条线的交点做一条射线(图中红色的线)最后按大小齿轮的齿数做相应的垂线(图中紫色的线),即得到需要的各自变位系数。
最后我们选择的变位系数即为:小齿轮x1=0.42,大齿轮x2=0.38。
【基本保障其和与之前x ∑一致,即可】。
c,验算变位后的齿顶厚度:注:一般要求齿顶厚Sa≥0.25m;对于表面淬火的齿轮要求Sa≥0.4m下表中的da的计算见后面的计算表格中的计算公式(因为当齿轮变位后,齿顶圆的计算和未变位齿轮的计算稍有差别-涉及到变位系数和中心距变位系数。
)。
分度圆直径db mm 73.8 77.9齿轮的齿顶圆直径da mm 83.027 86.799齿轮的齿顶压力角αa °27.27 26.17中间值invα0.0215 0.0215中间值invαa 0.0587 0.0347齿顶厚Sα 5.77 7.47判断值0.25m 1.025 1.025判断值0.4m 1.64 1.64小结:计算发现变位后的齿轮齿顶厚满足设计需求。
根据上面确定的变位系数,计算齿轮的中心距变位系数和节圆直径、齿根圆直径、齿顶圆直径。
斜齿轮变位系数xn和xt

斜齿轮变位系数xn和xt
斜齿轮变位系数xn和xt是机械设计中常用的两个参数,用于描述斜齿轮传动的性能和效果。
斜齿轮传动是一种常见的传动方式,通过斜齿轮的啮合来传递动力和转矩。
斜齿轮变位系数xn是指斜齿轮的变位程度,即齿轮在啮合过程中的相对位移。
它是用来描述斜齿轮传动的精度和平稳性的重要参数。
一般来说,xn的值越小,齿轮的变位程度越小,传动的精度和平稳性越高。
斜齿轮变位系数xt是指斜齿轮的变位角度,即齿轮在啮合过程中的旋转角度。
它是用来描述斜齿轮传动的传力性能的重要参数。
一般来说,xt的值越大,齿轮的变位角度越大,传动的传力性能越好。
斜齿轮变位系数xn和xt的取值范围是根据实际需求来确定的。
在设计斜齿轮传动时,需要根据传动的要求和工作条件来选择合适的xn和xt的值。
一般来说,xn的取值范围在0.1-0.3之间,xt的取值范围在10°-30°之间。
斜齿轮传动具有许多优点,如传动效率高、传动比稳定等。
但是,在设计和制造过程中需要考虑到斜齿轮的变位系数xn和xt的影响。
合理选择xn和xt的值,可以提高斜齿轮传动的性能和效果。
斜齿轮变位系数xn和xt是描述斜齿轮传动性能的重要参数,合理选择其取值范围,可以提高传动的精度、平稳性和传力性能。
在机
械设计中,我们需要根据实际需求来确定xn和xt的值,以实现最佳的传动效果。
齿轮的正负变位知多少

齿轮的正变位和负变位我们通常使用的齿轮的齿廓一般都是标准的渐开线,然而也存在一些情况需要对轮齿进行变位,如调整中心距、防止小齿轮的根切等。
1)齿轮的齿数与形状渐开线齿形曲线随齿数多少而不同。
齿数越多,齿形曲线越趋于直线。
随齿数增加,齿根的齿形变厚,轮齿强度增加。
由上图可以看到,齿数为10的齿轮,其轮齿的齿根处部分渐开线齿形被挖去,发生根切现象。
但是如果对齿数z=10的齿轮采用正变位,增大齿顶圆直径、增加轮齿的齿厚的话,可以得到与齿数200的齿轮同等程度的齿轮强度。
2)变位齿轮下图是齿数z=10的齿轮正变位切齿示意图。
切齿时,刀具沿半径方向的移动量xm(mm)称为径向变位量〔简称变位量)。
xm=变位量(mm)x=变位系数m=模数(mm)通过正变位的齿形变化。
轮齿的齿厚增加,外径(齿顶圆直径〉也变大。
齿轮通过采取正变位,可以避免根切(Undercut)的发生。
对齿轮实行变位还可以达到其它的目的,如改变中心距,正变位可增加中心距,负变位可减少中心距。
不论是正变位还是负变位齿轮,都对变位量有限制。
3)正变位和负变位变位有正变位和负变位。
虽然齿高相同,但齿厚不同。
齿厚变厚的为正变位齿轮,齿厚变薄的为负变位齿轮。
无法改变两个齿轮的中心距时,对小齿轮进行正变位(避免根切),对大齿轮进行负变位,以使中心距相同。
这种情况下,变位量的绝对值相等。
4)变位齿轮的啮合标准齿轮是在各个齿轮的分度圆相切状态下啮合。
而经过变位的齿轮的啮合,如图所示,是在啮合节圆上相切啮合。
啮合节圆上的压力角称为啮合角。
啮合角与分度圆上的压力角(分度圆压力角)不同。
啮合角是设计变位齿轮时的重要要素。
6)齿轮变位的作用可以防止在加工时因为齿数少而产生的根切现象;通过变位可以得到所希望的中心距;在一对齿轮齿数比很大的情况下,对容易产生磨耗的小齿轮进行正变位,使齿厚加厚。
相反,对大齿轮进行负变位,使齿厚变薄,以使得两个齿轮的寿命接近。
齿轮变位系数公式

齿轮变位系数公式
齿轮是机械传动中常用的元件,齿轮传动的稳定性和可靠性是机械传动的关键之一。
在齿轮传动中,齿轮的变位系数是一个重要的参数,它可以反映齿轮传动的稳定性和可靠性等性能指标。
齿轮变位系数是指齿轮轴线之间的垂直距离与模数的比值,通常用符号ε表示。
齿轮变位系数的计算公式如下:
ε = (y1 + y2) / (2m)
其中,y1和y2分别表示相邻两个齿轮齿数之差的绝对值,m为模数。
该公式适用于所有齿轮传动类型,包括直齿轮、斜齿轮、圆弧齿轮等。
齿轮变位系数的计算可以通过手算和计算机辅助设计软件进行。
在手算时,需要准确测量齿轮的齿数和模数,并应用齿轮变位系数公式进行计算。
在计算机辅助设计软件中,可以直接输入齿轮参数,软件会自动计算齿轮变位系数。
齿轮变位系数的大小对齿轮传动的稳定性和可靠性有着重要的影响。
当齿轮变位系数太大时,齿轮传动会出现过载、振动等问题,影响传动系统的性能;当齿轮变位系数太小时,齿轮传动会出现接触不良、噪声等问题,同样会影响传动系统的性能。
因此,在齿轮设计
和选择时,需要合理地选取齿轮变位系数,以保证传动系统的稳定性和可靠性。
齿轮变位系数是齿轮传动中一个重要的性能指标,它的大小对传动系统的稳定性和可靠性有着重要的影响。
齿轮变位系数的计算公式简单易用,可以帮助工程师准确地计算齿轮的变位系数,从而保证传动系统的性能。
齿轮变位系数

齿轮变位系数、侧隙选择
z1=10z2=60m=0.35
安装中心距12.3
材料为pa66
那么变位系数选择
侧隙的控制方法
侧隙根据经验选取
如果中心距为12.3
那么需要0.145的总变位系数
建议你小齿轮采用0.2变位
大齿轮采用-0.055变位
此时小齿轮齿顶稍有变尖
但可以满足0.1齿顶园角(线切割单变偏置)
1>按照常规,总变位0.145027。
按DIN 3992合理分配小齿x1≈0.28 x2 = 0.145027-x1= -0.134473 .
选择较大侧隙,例如GB2363-90 的 d , 也可以按照材料特性自己定义。
2>不需要拉大中心距。
3>小齿轮虽然存在一些根切,对啮合没有太大影响。
进啮点处0.0059 没有渐开线。
齿厚按照-0.03 考虑,用0.15 线丝切割模具型腔,还可以走丝不干涉。
4>PA66 按照 1.35% 考虑收缩,也可以按实际修改。
【本文来源】皇家小铺(/)【原文地址】/post/20090412434.html。
变位齿轮的计算方法

变位齿轮的计算方法1 变位齿轮的功用及变位系数变位齿轮具有以下功用:(1)避免根切;(2)提高齿面的接触强度和弯曲强度;(3)提高齿面的抗胶合和耐磨损能力;(4)修复旧齿轮;(5)配凑中心距。
对于齿数z=8~20的直齿圆柱齿轮,当顶圆直径d a=mz+2m+2xm时,不产生根切的最小变位系数x min,以及齿顶厚S a=0。
4m和S a=0时的变位系数x sa=0.4m和x sa=0如表1所列。
2 变位齿轮的简易计算将变位齿轮无侧隙啮合方程式作如下变换:总变位系数中心距变动系数齿顶高变动系数表 1 齿数z=8~20圆柱齿轮的变位系数z x min x sa=0.4m x sa=08 910111213141516171819 200。
53 0.47 0。
42 0.36 0。
30 0.24 0.18 0。
12 0.06 0-0。
05 -0.11 -0。
170.180.220。
270.310.350。
390。
430.460.500。
530.560.590。
620.560.630。
700。
760.820。
880。
930.981。
031。
081.131。
181.23或Δy=xΣ-y式中:α-—压力角,α=20°;α′--啮合角;z2、z1——大、小齿轮的齿数。
将上述三式分别除以,则得:由上述公式可以看出,当齿形角α一定时,x z、y z和Δy z均只为啮合角α′的函数。
在设计计算时,只要已知x z、y z、Δy z和α′四个参数中的任一参数,即可由变位齿轮的x z、y z、Δy z和啮合角α′的数值表(表2)中,查出其他三个参数,再进行下列计算。
一般齿轮手册上均列有此数值表。
式中正号用于外啮合,负号用于内啮合。
3 计算实例例1:已知一对外啮合变位直齿轮,齿数z1=18,z2=32,压力角α=20°,啮合角α′=22°18′,试确定总变位系数xΣ、中心距变动系数y及齿顶高变动系数Δy。
齿轮的变位系数

齿轮的变位系数变位系数x是径向变位系数,加工标准齿轮时,齿条形刀具中线与齿轮分度圆相切。
加工变位齿轮时齿条形刀具中线与齿轮分度圆相切位置偏移距离xm,外移x为正,内移x为负。
除了圆锥齿轮有时采用切向变位xt外,圆柱齿轮一般只采用径向变位。
变位系数x的选择不仅仅是为了凑中心距,而主要是为了提高强度和改善传动质量。
变位齿轮的主要功用如下:(1)减小齿轮传动的结构尺寸,减轻重量 在传动比一定的条件下,可使小齿轮齿数zl<zmin,从而使传动的结构尺寸减小,减轻机构重量。
(2)避免根切,提高齿根的弯曲强度 当小齿轮齿数z1<zmin时,可以利用正变位避免根切,提高齿根的弯曲强度。
x≥xmin=(Z-Zmin)/Zmin,对α=20o时,Zmin=17。
(3)提高齿面的接触强度 采用啮合角α’>α的正传动时,由于齿廓曲率半径增大,故可以提高齿面的接触强度。
(4)提高齿面的抗胶合耐磨损能力 采用啮合角α’>α的正传动,并适当分配变位系数xl、x2,使两齿轮的最大滑动率相等时,既可降低齿面接触应力,又可降低齿面间的滑动率以提高齿轮的抗胶合和耐磨损能力。
(5)配凑中心距 当齿数z1、z2不变的情况下,啮合角α’不同,可以得到不同的中心距,以达到配凑中心距的目的。
(6)修复被磨损的旧齿轮 齿轮传动中,小齿轮磨损较重,大齿轮磨损较轻,可以利用负变位把大齿轮齿面磨损部分切去再使用,重配一个正变位小齿轮,这就节约了修配时需要的材料与加工费用。
选择变位系数的基本原则(1)润滑条件良好的闭式齿轮传动 当齿轮表面的硬度不高时(HBS<350),即对于齿面未经渗碳、渗氮、表面淬火等硬化处理的齿轮,齿面疲劳点蚀或剥伤为其主要的失效形式,这时应选择尽可能大的总变位系数x,即尽量增大啮合角,以便增大啮合节点处齿廓的综合曲率半径,减少接触应力,提高接触强度与疲劳寿命。
当轮齿表面硬度较高时(HBS>350),常因齿根疲劳裂纹的扩展造成轮齿折断而使传动失效,这时,选择变位系数应使齿轮的齿根弯曲强度尽量增大,并尽量使相啮合的两齿轮具有相近的弯曲强度。
变位系数

变位系数变位系数,是用于减小齿轮传动的结构尺寸。
限制条件保证加工时不根切等选择原则润滑条件良好的闭式齿轮传动等主要功用减小齿轮传动的结构尺寸等目录1. 1 名称由来2. 2 概念3. 3 主要功用4. 4 选择原则5. 5 限制条件变位系数名称由来标准齿轮传动存在着一些局限性:(1)受根切限制,齿数不得少于Zmin,使传动结构不够紧凑;(2)不适合于安装中心距a'不等于标准中心距a的场合。
当a'<a时无法安装,当a'>a时,虽然可以安装,但会产生过大的侧隙而引起冲击振动,影响传动的平稳性;(3)一对标准齿轮传动时,小齿轮的齿根厚度小而啮合次数又较多,故小齿轮的强度较低,齿根部分磨损也较严重,因此小齿轮容易损坏,同时也限制了大齿轮的承载能力。
齿轮传动示意图为了改善齿轮传动的性能,出现了变位齿轮。
如图所示,当齿条插刀齿顶线超过极限啮合点N1,切出来的齿轮发生根切。
若将齿条插刀远离轮心O1一段距离(xm),齿顶线不再超过极限点N1,则切出来的齿轮不会发生根切,但此时齿条的分度线与齿轮的分度圆不再相切。
这种改变刀具与齿坯相对位置后切制出来的齿轮称为变位齿轮,刀具移动的距离xm称为变位量,x称为变位系数。
刀具远离轮心的变位称为正变位,此时x>0;刀具移近轮心的变位称为负变位,此时x<0。
标准齿轮就是变位系数x=0的齿轮。
变位系数概念齿轮的变位系数变位系数x 是径向变位系数,加工标准齿轮时,齿条形刀具中线与齿轮分度圆相切。
加工变位齿轮时齿条形刀具中线与齿轮分度圆相切位置偏移距离xm,外移x 为正,内移x 为负。
除了圆锥齿轮有时采用切向变位xt 外,圆柱齿轮一般只采用径向变位。
变位系数x 的选择不仅仅是为了凑中心距,而主要是为了提高强度和改善传动质量。
变位系数主要功用(1)减小齿轮传动的结构尺寸,减轻重量在传动比一定的条件下,可使小齿轮齿数zl< zmin,从而使传动的结构尺寸减小,减轻机构重量。
齿轮变位系数计算公式
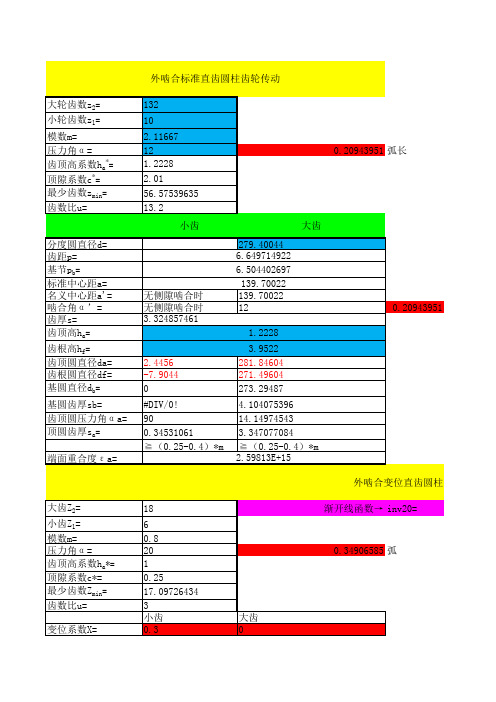
1.743355127
1.622393438
27.87834641
0.295868875
直齿外齿轮
公法线长度
公法线长度的计算 Wk=
标准齿轮 9.70116265
直齿外齿轮 斜齿外齿轮
跨测齿数 公法线长度 跨测齿厚
k= Wkn= k=
5.055555556
直齿外齿轮
公法线长度 跨测齿数
齿顶高hae1= 齿根高hfe1= 全齿高he1= 齿顶圆直径dae1= 分度圆直径de1= 齿根角Øf1= 齿顶角Øa1= 顶锥角δa1= 根锥角δf1= Ak1=
14.212488
齿根圆直径df=
11.14560191
基圆直径db=
12.5630209
法向齿距pn=
端面齿距pt=
5.199545947
法向基圆齿距pbn=
端面基圆齿距pbt=
基圆螺旋角βb=
21.46902352
法向齿厚sn=
2.35619449
端面齿厚st=
2.599772973
端面基圆齿厚sbt= 2.474242055
0.003117051
0.019 要查出,我没查,用时一定要
0.01
查
弧长
αa1
αa2
1.570796327 0.246959646
位直齿圆柱齿轮传动 0.014904
给定x∑求a' 0.320442451
αa1 0.743891086
αa2 0.479274389
inv20= invαa1= invαa2=
变位系数X=
18
6 0.8 20 1 0.25 17.09726434 3 小齿 0.3
齿轮变位系数选择

变位系数x是径向变位系数,加工标准齿轮时,齿条形刀具中线与齿轮分度圆相切。
加工变位齿轮时齿条形刀具中线与齿轮分度圆相切位置偏移距离xm,外移x为正,内移x为负。
除了圆锥齿轮有时采用切向变位xt外,圆柱齿轮一般只采用径向变位。
变位系数x的选择不仅仅是为了凑中心距,而主要是为了提高强度和改善传动质量。
变位齿轮的主要功用如下:(1)减小齿轮传动的结构尺寸,减轻重量在传动比一定的条件下,可使小齿轮齿数zl<zmin,从而使传动的结构尺寸减小,减轻机构重量。
(2)避免根切,提高齿根的弯曲强度当小齿轮齿数z1<zmin时,可以利用正变位避免根切,提高齿根的弯曲强度。
x≥xmin=(Z-Zmin)/Zmin,对α=20o时,Zmin=17。
(3)提高齿面的接触强度采用啮合角α’>α的正传动时,由于齿廓曲率半径增大,故可以提高齿面的接触强度。
(4)提高齿面的抗胶合耐磨损能力采用啮合角α’>α的正传动,并适当分配变位系数xl、x2,使两齿轮的最大滑动率相等时,既可降低齿面接触应力,又可降低齿面间的滑动率以提高齿轮的抗胶合和耐磨损能力。
(5)配凑中心距当齿数z1、z2不变的情况下,啮合角α’不同,可以得到不同的中心距,以达到配凑中心距的目的。
(6)修复被磨损的旧齿轮齿轮传动中,小齿轮磨损较重,大齿轮磨损较轻,可以利用负变位把大齿轮齿面磨损部分切去再使用,重配一个正变位小齿轮,这就节约了修配时需要的材料与加工费用。
选择变位系数的基本原则(1)润滑条件良好的闭式齿轮传动当齿轮表面的硬度不高时(HBS <350),即对于齿面未经渗碳、渗氮、表面淬火等硬化处理的齿轮,齿面疲劳点蚀或剥伤为其主要的失效形式,这时应选择尽可能大的总变位系数x,即尽量增大啮合角,以便增大啮合节点处齿廓的综合曲率半径,减少接触应力,提高接触强度与疲劳寿命。
当轮齿表面硬度较高时(HBS>350),常因齿根疲劳裂纹的扩展造成轮齿折断而使传动失效,这时,选择变位系数应使齿轮的齿根弯曲强度尽量增大,并尽量使相啮合的两齿轮具有相近的弯曲强度。
变位系数

变位系数变位系数x是径向变位系数,加工标准齿轮时,齿条形刀具中线与齿轮分度圆相切。
加工变位齿轮时齿条形刀具中线与齿轮分度圆相切位置偏移距离xm,外移x为正,内移x为负。
除了圆锥齿轮有时采用切向变位xt外,圆柱齿轮一般只采用径向变位。
变位系数x的选择不仅仅是为了凑中心距,而主要是为了提高强度和改善传动质量。
变位齿轮的主要功用如下:(1)减小齿轮传动的结构尺寸,减轻重量在传动比一定的条件下,可使小齿轮齿数zl<zmin,从而使传动的结构尺寸减小,减轻机构重量。
(2)避免根切,提高齿根的弯曲强度当小齿轮齿数z1<zmin时,可以利用正变位避免根切,提高齿根的弯曲强度。
x≥xmin=(Z-Zmin)/Zmin,对α=20o时,Zmin=17。
(3)提高齿面的接触强度采用啮合角α’>α的正传动时,由于齿廓曲率半径增大,故可以提高齿面的接触强度。
(4)提高齿面的抗胶合耐磨损能力采用啮合角α’>α的正传动,并适当分配变位系数xl、x2,使两齿轮的最大滑动率相等时,既可降低齿面接触应力,又可降低齿面间的滑动率以提高齿轮的抗胶合和耐磨损能力。
(5)配凑中心距当齿数z1、z2不变的情况下,啮合角α’不同,可以得到不同的中心距,以达到配凑中心距的目的。
(6)修复被磨损的旧齿轮齿轮传动中,小齿轮磨损较重,大齿轮磨损较轻,可以利用负变位把大齿轮齿面磨损部分切去再使用,重配一个正变位小齿轮,这就节约了修配时需要的材料与加工费用。
选择变位系数的基本原则(1)润滑条件良好的闭式齿轮传动当齿轮表面的硬度不高时(HBS<350),即对于齿面未经渗碳、渗氮、表面淬火等硬化处理的齿轮,齿面疲劳点蚀或剥伤为其主要的失效形式,这时应选择尽可能大的总变位系数x,即尽量增大啮合角,以便增大啮合节点处齿廓的综合曲率半径,减少接触应力,提高接触强度与疲劳寿命。
当轮齿表面硬度较高时(HBS>350),常因齿根疲劳裂纹的扩展造成轮齿折断而使传动失效,这时,选择变位系数应使齿轮的齿根弯曲强度尽量增大,并尽量使相啮合的两齿轮具有相近的弯曲强度。
齿轮对基本参数

齿轮对基本参数****************************法面模数:3齿数:小齿轮=16;大齿轮=69压力角:0.3491螺旋角:0.2619变位系数:小齿轮=0.1;大齿轮=-0.1齿宽:小齿轮=50;大齿轮=36端面分度圆压力角:0.3604端面节圆压力角(即啮合角):0.3604基圆螺旋角:0.2457齿顶圆直径:小齿轮=56.2942;大齿轮=219.7061基圆直径:小齿轮=46.5023;大齿轮=200.5410中心矩:132.000113960836齿数比:4.3125当量齿数:小齿轮=17.6067;大齿轮=75.9289****************************设计参数****************************机构工作级别:M5机构类型:起升机构或非平衡变幅机构机构载荷状态:L2-中(机构经常承受中等载荷,较少承受最大载荷)齿轮啮合类型:外啮合齿轮精度等级:6级允许齿厚的磨损量占原齿厚的百分比:10%试验齿轮齿面接触疲劳极限应力:小齿轮=1350N/mm2;大齿轮=895N/mm2 试验齿轮齿根弯曲疲劳极限应力:小齿轮=325N/mm2;大齿轮=330N/mm2 ****************************计算载荷****************************电动机额定力矩传到计算零件的力矩:303.8980N.m小齿轮转速:155转/min----------------------------小齿轮疲劳计算基本载荷:347.0515N.m小齿轮工作最大扭矩:390.2050N.m----------------------------分度圆上基本切向力:13967.4969N----------------------------循环次数系数:小齿轮=1.0000;大齿轮=0.8208载荷系数:小齿轮=0.8100;大齿轮=0.8100等效切向力:小齿轮=11313.6725N;大齿轮=9286.7739N----------------------------齿轮的动载系数:1.0021齿向载荷分布系数:小齿轮=1.3555;大齿轮=1.4322齿面接触强度用的齿间载荷分配系数:1.0500对于齿面接触疲劳强度计算的计算切向力:小齿轮=16135.7975;大齿轮=13995.1343N----------------------------轮齿弯曲强度用的齿间载荷分配系数:1.0500对于轮齿弯曲疲劳强度计算的计算切向力:小齿轮=16135.7975;大齿轮=13995.1343N ----------------------------分度圆上最大切向力:15704.2609N对于齿面接触静强度计算的最大计算切向力:小齿轮=22351.1439;大齿轮=23617.0211N对于轮齿弯曲静强度计算的最大计算切向力:小齿轮=22351.1439;大齿轮=23617.0211N ****************************齿面接触强度计算参数****************************节点区域系数:2.4246弹性系数:189.8000重合度系数:0.8035螺旋角系数:0.9828节圆处的计算接触应力:小齿轮=1211.2739N/mm2;大齿轮=1128.0691N/mm2----------------------------工作硬化系数:1.0000许用接触耐久性应力:小齿轮=1350.0000N/mm2;大齿轮=895.0000N/mm2齿面接触耐久性安全系数:小齿轮=1.1145;大齿轮=0.7934----------------------------节圆处的最大计算接触应力:小齿轮=1425.5978N/mm2;大齿轮=1465.4119N/mm2齿面接触静强度安全系数:小齿轮=1.5152;大齿轮=0.9772****************************齿根弯曲强度计算参数****************************齿形系数:小齿轮=2.8251;大齿轮=2.2819应力修正系数:小齿轮=1.5634;大齿轮=1.7126重合度系数:0.7327螺旋角系数:0.8764磨损系数:1.2500计算的齿根弯曲应力:小齿轮=529.6723N/mm2;大齿轮=406.4848N/mm2----------------------------试验齿轮的应力修正系数:2.0000尺寸系数:小齿轮=1.0000;大齿轮=1.0000许用弯曲疲劳应力:小齿轮=650.0000N/mm2;大齿轮=660.0000N/mm2轮齿弯曲疲劳强度的安全系数:小齿轮=1.2272;大齿轮=1.6237----------------------------齿根弯曲最大计算应力:小齿轮=733.6968N/mm2;大齿轮=685.9498N/mm2轮齿弯曲静强度的安全系数:小齿轮=2.2148;大齿轮=2.4054********************************************************************************总体评价********************************************************************************-------齿面接触计算(疲劳强度安全系数应该大于等于1.0~1.25,静强度安全系数应该大于等于1。
齿廓变位系数和径向变位系数
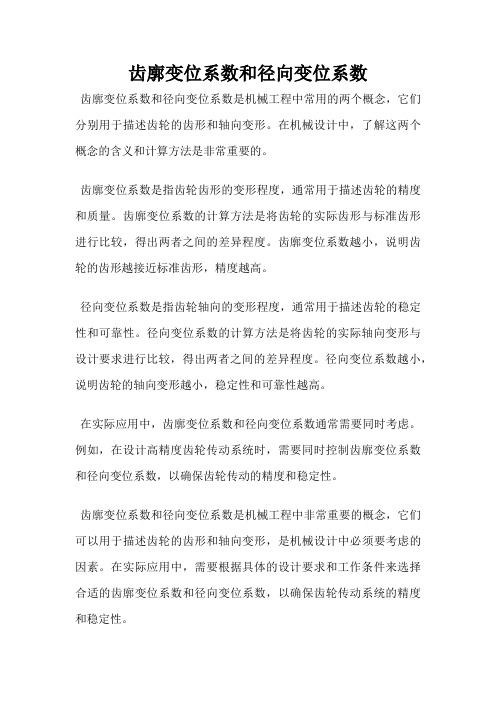
齿廓变位系数和径向变位系数
齿廓变位系数和径向变位系数是机械工程中常用的两个概念,它们分别用于描述齿轮的齿形和轴向变形。
在机械设计中,了解这两个概念的含义和计算方法是非常重要的。
齿廓变位系数是指齿轮齿形的变形程度,通常用于描述齿轮的精度和质量。
齿廓变位系数的计算方法是将齿轮的实际齿形与标准齿形进行比较,得出两者之间的差异程度。
齿廓变位系数越小,说明齿轮的齿形越接近标准齿形,精度越高。
径向变位系数是指齿轮轴向的变形程度,通常用于描述齿轮的稳定性和可靠性。
径向变位系数的计算方法是将齿轮的实际轴向变形与设计要求进行比较,得出两者之间的差异程度。
径向变位系数越小,说明齿轮的轴向变形越小,稳定性和可靠性越高。
在实际应用中,齿廓变位系数和径向变位系数通常需要同时考虑。
例如,在设计高精度齿轮传动系统时,需要同时控制齿廓变位系数和径向变位系数,以确保齿轮传动的精度和稳定性。
齿廓变位系数和径向变位系数是机械工程中非常重要的概念,它们可以用于描述齿轮的齿形和轴向变形,是机械设计中必须要考虑的因素。
在实际应用中,需要根据具体的设计要求和工作条件来选择合适的齿廓变位系数和径向变位系数,以确保齿轮传动系统的精度和稳定性。