催化裂化技术的作用及研究进展
催化裂化催化剂的研究与应用
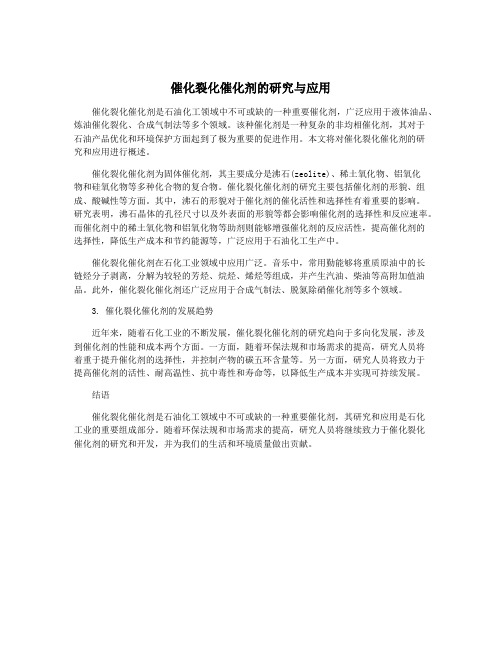
催化裂化催化剂的研究与应用催化裂化催化剂是石油化工领域中不可或缺的一种重要催化剂,广泛应用于液体油品、炼油催化裂化、合成气制法等多个领域。
该种催化剂是一种复杂的非均相催化剂,其对于石油产品优化和环境保护方面起到了极为重要的促进作用。
本文将对催化裂化催化剂的研究和应用进行概述。
催化裂化催化剂为固体催化剂,其主要成分是沸石(zeolite)、稀土氧化物、铝氧化物和硅氧化物等多种化合物的复合物。
催化裂化催化剂的研究主要包括催化剂的形貌、组成、酸碱性等方面。
其中,沸石的形貌对于催化剂的催化活性和选择性有着重要的影响。
研究表明,沸石晶体的孔径尺寸以及外表面的形貌等都会影响催化剂的选择性和反应速率。
而催化剂中的稀土氧化物和铝氧化物等助剂则能够增强催化剂的反应活性,提高催化剂的选择性,降低生产成本和节约能源等,广泛应用于石油化工生产中。
催化裂化催化剂在石化工业领域中应用广泛。
音乐中,常用勤能够将重质原油中的长链烃分子剥离,分解为较轻的芳烃、烷烃、烯烃等组成,并产生汽油、柴油等高附加值油品。
此外,催化裂化催化剂还广泛应用于合成气制法、脱氮除硝催化剂等多个领域。
3. 催化裂化催化剂的发展趋势近年来,随着石化工业的不断发展,催化裂化催化剂的研究趋向于多向化发展,涉及到催化剂的性能和成本两个方面。
一方面,随着环保法规和市场需求的提高,研究人员将着重于提升催化剂的选择性,并控制产物的碳五环含量等。
另一方面,研究人员将致力于提高催化剂的活性、耐高温性、抗中毒性和寿命等,以降低生产成本并实现可持续发展。
结语催化裂化催化剂是石油化工领域中不可或缺的一种重要催化剂,其研究和应用是石化工业的重要组成部分。
随着环保法规和市场需求的提高,研究人员将继续致力于催化裂化催化剂的研究和开发,并为我们的生活和环境质量做出贡献。
1催化裂化的目的和意义
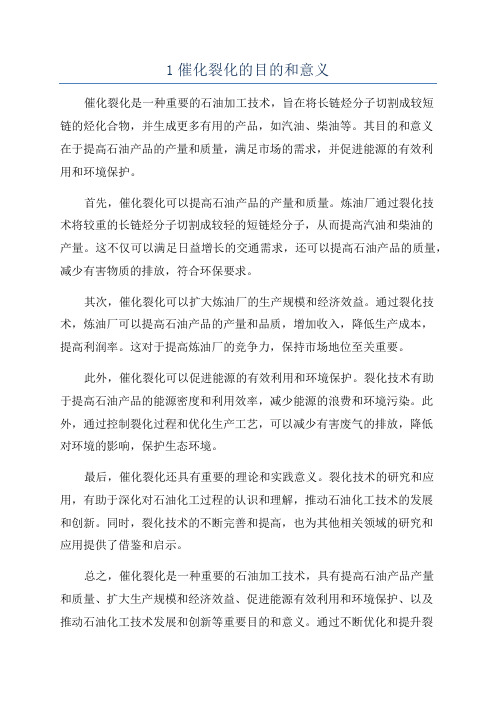
1催化裂化的目的和意义催化裂化是一种重要的石油加工技术,旨在将长链烃分子切割成较短链的烃化合物,并生成更多有用的产品,如汽油、柴油等。
其目的和意义在于提高石油产品的产量和质量,满足市场的需求,并促进能源的有效利用和环境保护。
首先,催化裂化可以提高石油产品的产量和质量。
炼油厂通过裂化技术将较重的长链烃分子切割成较轻的短链烃分子,从而提高汽油和柴油的产量。
这不仅可以满足日益增长的交通需求,还可以提高石油产品的质量,减少有害物质的排放,符合环保要求。
其次,催化裂化可以扩大炼油厂的生产规模和经济效益。
通过裂化技术,炼油厂可以提高石油产品的产量和品质,增加收入,降低生产成本,提高利润率。
这对于提高炼油厂的竞争力,保持市场地位至关重要。
此外,催化裂化可以促进能源的有效利用和环境保护。
裂化技术有助于提高石油产品的能源密度和利用效率,减少能源的浪费和环境污染。
此外,通过控制裂化过程和优化生产工艺,可以减少有害废气的排放,降低对环境的影响,保护生态环境。
最后,催化裂化还具有重要的理论和实践意义。
裂化技术的研究和应用,有助于深化对石油化工过程的认识和理解,推动石油化工技术的发展和创新。
同时,裂化技术的不断完善和提高,也为其他相关领域的研究和应用提供了借鉴和启示。
总之,催化裂化是一种重要的石油加工技术,具有提高石油产品产量和质量、扩大生产规模和经济效益、促进能源有效利用和环境保护、以及推动石油化工技术发展和创新等重要目的和意义。
通过不断优化和提升裂化技术,可以更好地满足市场需求,促进行业健康发展,推动经济社会可持续发展。
催化裂化催化剂的发展历程及研究进展

催化裂化催化剂的发展历程及研究进展催化裂化是一种重要的石油加工技术,通过将石油分子在催化剂的作用下进行裂解,得到高附加值的产品,如汽油和石脂油。
催化裂化催化剂的发展历程可以追溯到20世纪初,经过了多个阶段的演进和改进。
本文将详细介绍催化裂化催化剂的发展历程及研究进展。
20世纪初,催化裂化催化剂主要采用天然矿物催化剂,如石英、蛭石等。
这些催化剂具有一定的催化活性,但缺乏稳定性和选择性,难以应对复杂的原料和严苛的工业操作条件。
20世纪30年代,随着石油需求的增加和技术的进步,人们开始研发新型催化剂。
那时,主要采用的是氧化物催化剂,如铝、硅等。
这些催化剂的活性和稳定性有了一定的提升,但仍然存在一些问题,如选择性不高、催化剂寿命短等。
20世纪50年代,人们开始尝试使用酸性功能组分的催化剂,如酸化铁、硫酸等。
这些催化剂具有较高的催化活性和选择性,但具有腐蚀性,容易造成催化剂失效和设备损坏。
20世纪60年代,人们将焦油催化裂化硅铝酸催化剂推向了催化裂化工业化生产的舞台。
这种催化剂具有良好的热稳定性和选择性,能够实现高效的催化裂化反应。
焦油催化裂化硅铝酸催化剂的应用推动了石油工业的发展,成为当时催化裂化的主流技术。
近年来,催化裂化催化剂的研究进展主要集中在以下几个方面:1.催化剂结构设计:通过调控催化剂的孔径分布、酸中心密度和酸强度等结构参数,以提高其活性、选择性和稳定性。
常见的结构设计方法包括合金化、钾的添加、微介孔化等。
2.催化剂负载材料研究:将催化剂负载在合适的载体上,可以提高催化剂的分散性和稳定性。
常用的载体材料包括Al2O3、SiO2、TiO2等。
3.催化剂表面改性:通过表面改性的方法,如纳米粒子修饰、溶胶-凝胶法制备等,可以改变催化剂的活性中心和表面酸性,以提高其催化效果。
4.新型催化剂开发:人们正在探索使用新型催化剂,如纳米材料、金属有机骨架材料(MOFs)等,以提高催化裂化过程的效率和选择性。
催化裂化催化剂的研究与应用

催化裂化催化剂的研究与应用催化裂化是一种重要的炼油工艺,其主要目的是将原油中的长链烃分子通过催化剂的作用裂解成更加有价值的短链烃分子。
催化裂化技术在炼油工业中具有广泛的应用,可以提高炼油产物的质量,并且有效地提高了炼油产品的产率。
而催化裂化催化剂的研究与应用则是催化裂化技术能够持续发展的重要保障。
一、催化裂化催化剂的研究现状催化裂化催化剂是催化裂化技术中最为关键的部分,其性能直接影响着催化裂化的效率和产品质量。
目前,催化裂化催化剂主要包括酸性固体催化剂和贵金属催化剂两大类。
酸性固体催化剂是催化裂化技术中使用最为广泛的催化剂,其主要成分包括硅铝酸盐和沸石等。
这类催化剂具有良好的酸性和孔道结构,可以有效地裂解重质原油中的长链烃分子。
近年来,随着炼油工业对产品质量要求的提高,科研人员对酸性固体催化剂的研究也在不断深入。
通过提高催化剂的酸性和表面积,优化催化剂的孔道结构等手段,使得酸性固体催化剂在催化裂化中的性能得到了显著提升。
贵金属催化剂是近年来催化裂化领域的一个研究热点。
与传统的酸性固体催化剂相比,贵金属催化剂具有更高的催化活性和选择性,可以实现更加精确的烃分子裂解,得到更加高品质的裂化产品。
目前,科研人员主要将贵金属催化剂应用于催化裂化技术中的深度加工环节,通过与酸性固体催化剂的结合使用,可以实现更加高效的原油加工和产品提纯。
二、催化裂化催化剂的应用现状催化裂化催化剂的应用主要体现在炼油工业中的实际生产中。
目前,国内外的炼油企业对催化裂化催化剂的应用已经非常成熟,可以实现从原油到成品油的高效加工转化。
在实际生产中,催化裂化催化剂的应用主要体现在以下几个方面:1.原油加工:催化裂化催化剂可以将重质原油中的长链烃分子裂解成较为轻质的烃类化合物,提高了成品油的产率,并且显著提高了成品油的质量。
在炼油厂的原油加工装置中,催化裂化催化剂是实现高效加工的关键。
2.产品提纯:通过催化裂化技术,可以将原油中的硫、氮、金属等杂质去除,得到更加纯净的成品油产品。
催化催化裂化技术

催化催化裂化技术催化裂化技术是一种重要的炼油工艺,可以将重质石油馏分转化为高附加值的轻质产品。
本文将从催化裂化技术的原理、应用和发展前景等方面进行探讨,以期为读者提供对该技术的全面了解。
一、催化裂化技术的原理催化裂化技术是通过催化剂的作用将重质石油馏分分解为较轻的产品。
其主要原理是在高温和高压的条件下,将原料油与催化剂接触,使其发生裂化反应。
这种反应可以将长链烃分子裂解成短链烃分子,从而提高汽油和燃料油的产率。
催化裂化反应主要分为两个阶段:热裂化和催化裂化。
在热裂化阶段,原料油在高温下分解成烃气和液体烃。
然后,在催化剂的作用下,烃气和液体烃进一步反应,生成较轻的产品,如汽油、液化气和柴油等。
二、催化裂化技术的应用催化裂化技术在炼油行业中具有广泛的应用。
首先,它可以提高汽油的产率。
由于汽车的普及,对汽油的需求量不断增加。
催化裂化技术可以将重质石油馏分转化为轻质的汽油,从而满足市场需求。
催化裂化技术可以生产出高质量的柴油。
在催化裂化过程中,石油馏分中的硫、氮和金属等杂质可以得到有效去除,从而提高柴油的质量。
这对于减少柴油排放的污染物具有重要意义。
催化裂化技术还可以生产出液化气、石脑油和石化原料等产品。
这些产品在化工、冶金和化肥等行业中具有广泛的应用。
三、催化裂化技术的发展前景随着能源需求的增加和石油资源的日益枯竭,催化裂化技术在未来的发展前景十分广阔。
一方面,随着汽车工业的高速发展,对汽油的需求将持续增加,催化裂化技术将成为满足市场需求的重要手段。
另一方面,随着环境保护意识的提高,对燃料油质量的要求也越来越高。
催化裂化技术可以提高燃料油的质量,减少对环境的污染,因此在未来的发展中具有重要的作用。
随着科技的不断进步,催化剂的研发和改进也将推动催化裂化技术的发展。
新型的催化剂可以提高反应的选择性和活性,从而提高产品的产率和质量。
催化裂化技术作为一种重要的炼油工艺,在提高石油产品产率和质量方面具有重要的作用。
催化裂化技术及其进展
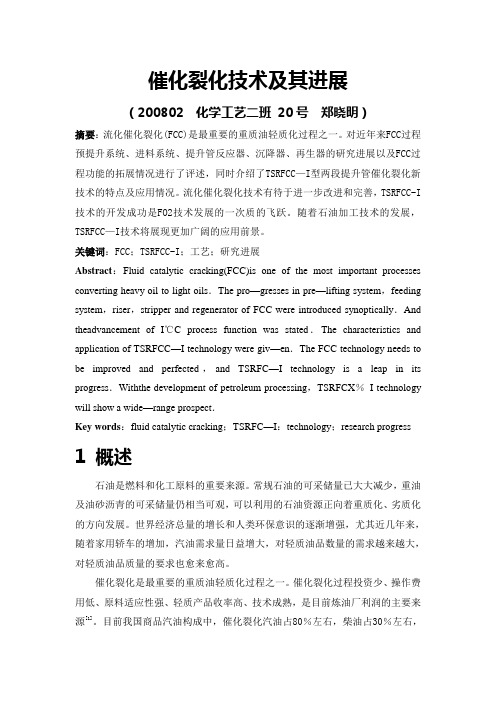
催化裂化技术及其进展(200802 化学工艺二班 20号郑晓明)摘要:流化催化裂化(FCC)是最重要的重质油轻质化过程之一。
对近年来FCC过程预提升系统、进料系统、提升管反应器、沉降器、再生器的研究进展以及FCC过程功能的拓展情况进行了评述,同时介绍了TSRFCC—I型两段提升管催化裂化新技术的特点及应用情况。
流化催化裂化技术有待于进一步改进和完善,TSRFCC-I 技术的开发成功是FO2技术发展的一次质的飞跃。
随着石油加工技术的发展,TSRFCC—I技术将展现更加广阔的应用前景。
关键词:FCC;TSRFCC-I;工艺;研究进展Abstract:Fluid catalytic cracking(FCC)is one of the most important processes converting heavy oil to light oils.The pro—gresses in pre—lifting system,feeding system,riser,stripper and regenerator of FCC were introduced synoptically.And theadvancement of I℃C process function was stated.The characteristics and application of TSRFCC—I technology were giv—en.The FCC technology needs to be improved and perfected,and TSRFC—I technology is a leap in its progress.Withthe development of petroleum processing,TSRFCX%I technology will show a wide—range prospect.Key words:fluid catalytic cracking;TSRFC—I:technology;research progress1 概述石油是燃料和化工原料的重要来源。
催化裂化催化剂研究与应用
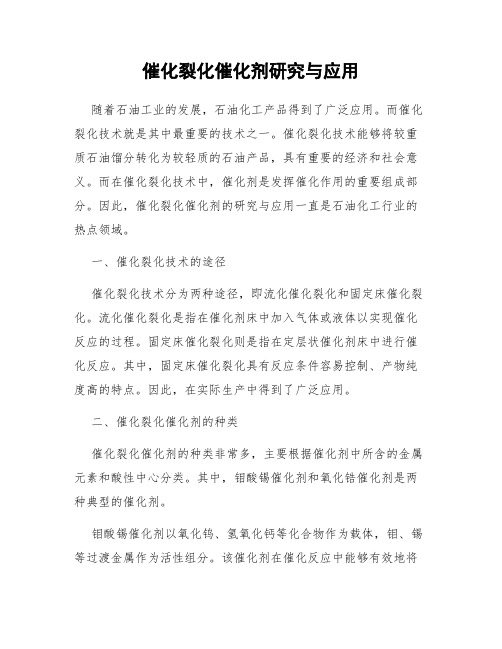
催化裂化催化剂研究与应用随着石油工业的发展,石油化工产品得到了广泛应用。
而催化裂化技术就是其中最重要的技术之一。
催化裂化技术能够将较重质石油馏分转化为较轻质的石油产品,具有重要的经济和社会意义。
而在催化裂化技术中,催化剂是发挥催化作用的重要组成部分。
因此,催化裂化催化剂的研究与应用一直是石油化工行业的热点领域。
一、催化裂化技术的途径催化裂化技术分为两种途径,即流化催化裂化和固定床催化裂化。
流化催化裂化是指在催化剂床中加入气体或液体以实现催化反应的过程。
固定床催化裂化则是指在定层状催化剂床中进行催化反应。
其中,固定床催化裂化具有反应条件容易控制、产物纯度高的特点。
因此,在实际生产中得到了广泛应用。
二、催化裂化催化剂的种类催化裂化催化剂的种类非常多,主要根据催化剂中所含的金属元素和酸性中心分类。
其中,钼酸锡催化剂和氧化锆催化剂是两种典型的催化剂。
钼酸锡催化剂以氧化钨、氢氧化钙等化合物作为载体,钼、锡等过渡金属作为活性组分。
该催化剂在催化反应中能够有效地将较长的油分子链裂化为较短的链,生成较轻的烷烃和芳烃。
同时,钼酸锡催化剂还具有良好的稳定性和抗污染性能。
氧化锆催化剂则以催化剂氧化锆为载体,铝、钙、钾等元素作为辅助活性组分。
该催化剂具有强酸性、高催化活性和很低的积碳倾向,是目前催化裂化催化剂中的佼佼者之一。
同时,氧化锆催化剂还可以有效地去除油中的硫、氮等杂质,提高产品的质量。
三、催化裂化催化剂的应用催化裂化催化剂可以广泛应用于石油化工工业中。
它们不仅可以将较重的石油馏分转化为较轻的产品,还可以用于石油化工中的各种催化反应。
在催化裂化技术中,使用催化剂可以加快反应速率,提高产品产率和品质。
在炼油厂中,针对不同种类的石油原料和生产要求,选择不同的催化剂和反应条件,生产出高品质的轻质石油产品。
同时,还可以有效地去除石油中的硫、氮等杂质,减少对环境的污染。
此外,催化裂化催化剂还可以应用于合成氢气、合成甲醇和合成油等反应中。
催化裂化mip技术

催化裂化MIP技术引言催化裂化是石油化工领域中一项非常重要的加工技术,通过将重质石油馏分在高温、高压和催化剂作用下分子裂解,生产出更高价值的燃料和化工产品。
在催化裂化过程中,MIP(Microsphere-embedded Insulator)技术作为一种新兴的催化剂承载技术发挥着重要作用。
本文将重点探讨催化裂化MIP技术的原理、应用和未来发展方向。
MIP技术的原理MIP技术是一种将催化剂包裹在微粒子(通常是陶瓷、氧化铝等材料)中的方法,形成高度稳定的催化剂载体。
在催化裂化过程中,MIP技术可以提供更好的热稳定性和化学稳定性,延长催化剂的寿命并提高催化效率。
MIP技术的原理包括以下几个方面:1. 载体选择MIP技术的首要任务是选择合适的载体材料。
通常,陶瓷和氧化铝是常用的载体材料,由于它们具有良好的热稳定性和化学稳定性,在高温和高压条件下不易破裂或变形。
此外,载体材料应具有适当的表面积和孔隙结构,以便催化剂能够均匀地分散在载体中,并提供最大的活性表面积。
2. 催化剂包裹催化剂包裹是指将催化剂均匀地分散在载体中。
这一步骤旨在确保催化剂能够充分接触到反应物,从而提高反应效率。
通常,可以通过浸渍法、沉积法和蒸镀法等方法将催化剂包裹到载体表面。
这些方法可以使催化剂在载体上形成均匀分布的颗粒,并保持良好的催化活性。
3. 表面修饰MIP技术可以通过表面修饰来改变载体和催化剂之间的相互作用。
表面修饰可以通过调整催化剂和载体表面的化学性质,如酸碱性和亲疏水性,来改善催化效果。
此外,表面修饰还可以增加载体与底层催化层之间的附着力,从而提高催化剂的稳定性和寿命。
MIP技术的应用MIP技术在催化裂化领域有着广泛的应用。
以下将重点介绍几个方面的应用。
1. 燃料生产催化裂化是燃料生产的重要环节,MIP技术可以在催化裂化过程中提高燃料产率和质量。
MIP技术可以使催化剂更均匀地分散在载体中,从而提高烟气与催化剂的接触效率。
此外,MIP技术还可以提高催化剂的稳定性,延长催化剂的使用寿命。
1催化裂化的目的和意义

1催化裂化的目的和意义催化裂化是一种重要的炼油技术,其目的是将高碳链烃化合物转化为更加有用的低碳链烃化合物,并产生较高价值的产品,如汽油和石脑油。
其意义在于提高石油资源的利用效率、满足不断增长的能源需求、改善环境污染等方面。
首先,催化裂化可以提高石油资源的利用效率。
随着全球能源需求的不断增长和石油储量的有限,高碳链烃化合物的转化成为低碳链烃化合物,可以更好地满足市场上对于汽油、石脑油等石油产品的需求。
通过催化裂化技术,可以将部分无法直接利用的大分子烃通过裂解反应转化为更小分子量的烃,其中较大比例的产物是汽油。
由此,可以提高石油资源的利用效率,减少对于有限石油资源的依赖。
其次,催化裂化可以满足不断增长的能源需求。
世界人口的快速增长和经济的发展,对能源的需求越来越大。
汽油作为一种重要的能源,广泛应用于交通工具和工业生产中。
通过催化裂化技术,可以生产较高价值的汽油产品,满足这一增长的需求。
此外,催化裂化还可以生产其他石油产品,如石脑油,可用于溶剂、涂料、胶粘剂等行业。
这些产品对于社会经济的发展具有重要意义。
另外,催化裂化还可以改善环境污染。
传统的石油加工过程中,高碳链烃化合物会被直接燃烧或用作其他低价值能源,导致大量的废气和废水排放,对环境产生严重的污染。
而催化裂化技术可以将这些高碳链烃转化为有用的低碳链烃,从而减少了燃烧废气的产生,并使得石油加工过程更加环保。
此外,催化裂化还可以减少有害物质的排放,如硫化物和氮化物,对大气和水源的污染也有所改善。
同时,催化裂化还具有经济效益和社会效益。
通过提高石油产品的产出量和质量,催化裂化可以增加炼油企业的收入和利润,提高其竞争力。
此外,催化裂化技术的应用还可以为就业市场提供更多的工作机会,促进经济的发展和社会的稳定。
总之,催化裂化技术的目的在于转化高碳链烃化合物为低碳链烃化合物,并产生较高价值的产品,如汽油和石脑油。
其意义在于提高石油资源的利用效率、满足不断增长的能源需求、改善环境污染等方面。
催化裂化技术的现状及发展趋势

催化裂化技术的现状及发展趋势
催化裂化技术是最近几年来人们极力推进研究的一个技术,它对于提高生物柴油的性能以及破坏有毒有机物质有显著的改善。
目前,催化裂化技术已经发展迅猛,并在未来的发展中有发挥出巨大的潜力,其中包括其在碳氢化合物低温裂化领域的巨量发展。
首先,催化裂化技术在开发绿色燃料、降低有毒物质的排放方面发挥着重要作用。
它为油脂,烃类,污染物,有毒有机物,废弃物,碳氢化合物等制备生物柴油等清洁能源提供了可能。
其中,碳氢化合物的低温裂烃技术可以提高生物柴油的收率,降低有毒有机物的排放,提高燃料的燃烧能效,为构建低碳的绿色社会奠定基础。
其次,催化裂化技术近年来发展迅猛,包括催化剂的合成,催化裂化反应机理,催化剂和反应条件等。
例如,今年在日本开发出用于催化裂化柴油的新型钴催化剂。
此外,也合成了用于催化裂化石油、烃类和有机废料等材料的新型催化剂,例如以钯和钼为分子基础的纳米微粒等。
另外,催化裂化技术也受到国内外科学家的研究关注,已经取得了显著的进展。
国外的研究主要集中在改进催化加氢裂化反应最前沿的技术和装置技术以及提高反应温度和在碳氢化合物低温裂化方面取得巨大进展。
至于国内,主要工作集中在改进催化剂和催化反应机理以及提高催化裂化反应效率的方面,如金属催化剂和非金属催化剂的研究以及反应温度的改进等,以期在技术发展上取得突破性进展。
总的来说,催化裂化技术的发展取得了显著的成绩,在未来的研究中,将会继续完善并发展其本身的技术,并继续在低温碳氢化合物催化裂烃方面展示出巨大的潜力。
催化裂化催化剂的研究与应用

催化裂化催化剂的研究与应用催化裂化是石油加工中主要的重要工艺之一,利用催化剂使长链烯烃在适当的压力和温度条件下发生裂化反应,生成短链烯烃和芳烃。
催化裂化催化剂的研究与应用是提高催化裂化转化率和选择性,改善催化裂化产品质量的关键。
催化裂化催化剂的研究主要集中在两个方面:一是提高裂化活性和选择性;二是提高催化剂的稳定性和寿命。
为了提高催化剂的裂化活性和选择性,研究人员主要从以下几个方面进行优化。
首先是调节催化剂的酸碱性质。
催化裂化反应是一个酸碱催化反应,催化剂表面的酸碱性质直接影响反应速率和选择性。
通过改变催化剂组分、载体、孔结构和酸碱度等方法来调节催化剂的酸碱性质,可以有效提高催化裂化反应的效果。
其次是设计合适的催化剂孔道结构。
催化剂的孔道结构直接影响反应物分子在催化剂内的扩散和反应活性中心的利用率。
通过合理设计催化剂孔道结构,可以增加反应物分子在催化剂内的停留时间,提高反应活性中心的利用率,从而提高催化裂化反应的转化率和选择性。
研究人员还从催化剂组分、活性中心、金属添加剂等方面入手进行改进,进一步提高催化裂化反应的效果。
催化裂化催化剂的研究与应用在石油加工中具有重要的意义。
一方面,催化裂化技术可以提高原油转化率,降低原油中硫、氮等有害元素的含量,提高产品质量和附加值,降低环境污染。
催化裂化催化剂的研究与应用可以为石油工业提供更高效、更环保的生产工艺,促进石油工业的可持续发展。
催化裂化催化剂的研究与应用是提高石油加工效率和产品质量的重要手段。
通过优化催化剂的裂化活性、选择性、稳定性和寿命等方面,可以提高催化裂化反应的效果,实现石油加工的可持续发展。
催化裂化反应机理研究进展及实践应用

催化裂化反应机理研究进展及实践应用一、内容描述随着全球能源需求的不断增长和环境保护要求的日益严格,石油化工行业正面临着巨大的压力和挑战。
为了提高石油加工效率,降低生产成本,实现可持续发展,催化裂化技术作为一种重要的石油加工方法,得到了广泛的关注和研究。
本文将对催化裂化反应机理的研究进展进行概述,并结合实际应用案例,探讨催化裂化技术的发展趋势和前景。
首先本文将介绍催化裂化的基本原理和过程,催化裂化是一种在催化剂的作用下,通过加热、高压等条件使原油中的烃类分子断裂成更小分子的过程。
这一过程中涉及到多种反应类型,如氢转移反应、异构化反应、芳构化反应等。
了解这些反应类型及其动力学特性对于优化催化裂化工艺具有重要意义。
其次本文将重点介绍催化裂化反应机理的研究进展,近年来随着科学技术的不断发展,催化裂化反应机理的研究取得了显著成果。
研究人员通过对实验数据和理论模型的分析,揭示了催化裂化反应中的各种关键因素及其相互作用规律。
例如催化剂的选择和性能、反应温度和压力、进料组成和结构等都对催化裂化反应的速率和选择性产生重要影响。
此外研究人员还发现了一些新的催化裂化反应途径和机制,为优化催化裂化工艺提供了理论指导。
本文将结合实际应用案例,探讨催化裂化技术的发展趋势和前景。
随着环保法规的不断完善和技术水平的提高,催化裂化技术在国内外得到了广泛应用。
例如中国石化、中国石油等国内大型石油化工企业已经在催化裂化领域取得了一系列重要突破,实现了高效、低排放的生产目标。
未来催化裂化技术将继续向高性能、高选择性和低能耗方向发展,为全球石油化工行业的发展做出更大贡献。
1. 催化裂化反应技术的重要性和应用领域提高原油利用率:CFCC技术可以将原油中的长链烃类分子分解为较短的烃类分子,从而提高原油的加工效率和利用率。
这对于资源有限的国家和地区具有重要意义,可以降低对进口原油的依赖,减少能源消耗。
降低生产成本:CFCC技术具有较高的转化率和选择性,可以有效地去除原油中的杂质和有害物质,提高产品的质量。
我国催化裂化工艺技术进展

我国催化裂化工艺技术进展催化裂化工艺技术是一种将重质烃类裂解为轻质烃类和汽油等燃料的重要手段。
在我国,随着石油化工行业的快速发展,催化裂化工艺技术也取得了显著的进步。
本文将简要回顾我国催化裂化工艺技术的发展历程,介绍技术创新与应用情况,并展望未来的发展前景。
自20世纪50年代以来,我国催化裂化工艺技术经历了从引进到自主研发的过程。
早期,我国从国外引进了一批先进的催化裂化装置和技术,在消化吸收的基础上,逐渐开始自主创新。
到20世纪80年代,我国已成功开发出具有自主知识产权的催化裂化工艺技术,并在大型工业装置上得到应用。
进入21世纪,我国催化裂化工艺技术水平进一步提升,已成为世界催化裂化工艺技术的重要研发和应用大国。
近年来,我国催化裂化工艺技术在技术创新和应用方面取得了许多重要成果。
在催化剂的种类和性能方面,通过优化制备工艺和组分设计,成功开发出多种高效、环保型催化剂。
这些催化剂在提高产品收率、降低能源消耗、减少污染物排放等方面具有显著优势。
在反应器设计方面,我国已成功开发出多套具有自主知识产权的反应器设计。
这些反应器在提高原料适应性、优化产品分布、降低能源消耗等方面表现出色。
例如,某新型反应器采用独特的结构设计,有效提高了催化剂的利用率和产品的分离效果,降低了装置的运行成本。
展望未来,我国催化裂化工艺技术将继续深入研究和技术创新。
随着环保要求的日益严格,开发高效、环保型催化裂化工艺技术将成为重要方向。
通过优化催化剂和反应器设计,降低污染物排放,提高资源利用率,实现绿色生产。
市场对燃料油和化工产品的需求将持续增长,因此催化裂化工艺技术的研究和应用将更加注重产品结构的优化和多样性的拓展。
例如,通过引入新的反应条件和原料,开发生产高附加值化学品的技术,提高企业的经济效益。
随着智能化和自动化的快速发展,催化裂化工艺技术将更加注重信息技术和自动化技术的应用。
通过建立自动化控制系统和实时监测分析系统,提高装置的运行效率和安全性,实现生产过程的智能化和信息化。
原油加工行业的催化裂化技术

原油加工行业的催化裂化技术在原油加工行业中,催化裂化技术是一项关键的工艺,它被广泛应用于石油化工领域。
催化裂化技术通过改变原油分子结构,将重质石油转化为高附加值产品,如汽油、石蜡和石油煤等。
本文将介绍催化裂化技术的原理、应用和发展趋势。
一、催化裂化技术的原理催化裂化技术是利用催化剂在适宜温度和压力条件下,将长链烃分子裂解为短链烃分子的过程。
该技术的核心在于催化剂的作用,催化剂能够降低裂解反应的活化能,提高反应速率,促进烃分子的裂解。
常用的催化剂包括硅铝比较高的ZSM-5分子筛和改性的微球状催化剂。
二、催化裂化技术的应用催化裂化技术广泛应用于原油加工行业,主要用于生产高附加值产品,尤其是汽油。
通过催化裂化,重质石油中的长链烃分子可以被分解为低碳烃,如丙烷、丁烷和乙烯等。
这些低碳烃可以作为汽油的组分,提高汽油的辛烷值和抗爆性能,提高汽车发动机的功率和燃油经济性。
催化裂化技术还可以生产其他高附加值产品,如石蜡和石油煤。
石蜡是一种重要的工业原料,广泛用于蜡烛、润滑油和化妆品等领域。
石油煤是一种高热值的燃料,可用于发电和取暖等用途。
三、催化裂化技术的发展趋势催化裂化技术已经取得了长足的发展,并在石油化工行业中得到广泛应用。
然而,随着石油资源的逐渐枯竭和环境保护意识的提高,催化裂化技术也面临着一些挑战和发展方向。
首先,随着原油品质的变差,催化裂化技术需要适应低质量原油的加工需求。
这意味着催化剂要能够在更恶劣的反应条件下稳定运行,同时要提高对杂质的耐受能力,降低催化剂的中毒速度。
其次,环境保护要求也对催化裂化技术提出了更高的要求。
催化裂化过程会产生大量的尾气和废水,其中含有大量的污染物。
因此,开发更高效的催化剂和改良反应工艺,减少有害气体的排放和对水资源的消耗,是催化裂化技术发展的重要方向。
此外,催化裂化技术还可以与其他工艺相结合,实现资源的综合利用。
例如,可以将催化裂化技术与催化重整技术相结合,将重质石油转化为汽油和芳香烃,实现石油资源的高效利用和价值最大化。
我国催化裂化工艺技术进展

我国催化裂化工艺技术进展一、本文概述催化裂化(FCC)作为一种重要的石油加工技术,在我国石油工业中占据着举足轻重的地位。
随着科技的不断进步和环保要求的日益严格,我国催化裂化工艺技术也在持续发展和创新。
本文旨在全面概述我国催化裂化工艺技术的最新进展,包括技术原理、工艺流程、催化剂研发、设备改进以及环保措施等方面的内容。
通过对这些方面的深入探讨,本文旨在展示我国催化裂化工艺技术在提高石油资源利用效率、促进石油工业可持续发展以及减少环境污染等方面的积极贡献。
本文还将对催化裂化工艺技术的发展趋势进行展望,以期为相关领域的科研人员和企业提供有益的参考和借鉴。
二、催化裂化工艺技术的基本原理催化裂化(Catalytic Cracking)是一种重要的石油加工过程,主要目的是将重质烃类转化为更有价值的轻质产品,如汽油、煤油和柴油等。
其基本原理是利用催化剂加速烃类分子在高温高压环境下的热裂解反应,使长链烃类断裂成较短的链烃,从而改善产品的品质和产量。
催化裂化工艺主要包括热裂化和催化裂化两个阶段。
热裂化是在没有催化剂的情况下,通过高温使烃类分子发生热裂解,生成较小的烃分子。
然而,这个过程的选择性较差,会产生大量的裂化气和焦炭,导致产品收率较低。
催化裂化则是在热裂化的基础上引入催化剂,通过催化剂的选择性吸附和表面酸性,使得烃类分子在较低的温度下就能发生裂解,同时提高裂解的选择性和产品的收率。
催化剂的活性、选择性和稳定性对催化裂化过程的影响至关重要。
在催化裂化过程中,烃类分子首先被催化剂表面的酸性位点吸附,然后在催化剂的作用下发生裂解反应。
生成的较小烃分子随后从催化剂表面脱附,进入气相,最后通过冷凝和分离得到所需的产品。
随着科技的不断进步,我国的催化裂化工艺技术也在不断发展。
新型的催化剂、反应器和工艺条件的优化等技术的发展,使得催化裂化过程的效率和选择性得到了显著提高,为我国石油工业的发展做出了重要贡献。
三、我国催化裂化工艺技术的现状我国催化裂化工艺技术自上世纪五十年代引进至今,经历了从引进消化到自主创新的发展历程,目前已经形成了具有自主知识产权的催化裂化工艺技术体系。
催化裂化汽油降烯烃技术的现状及发展
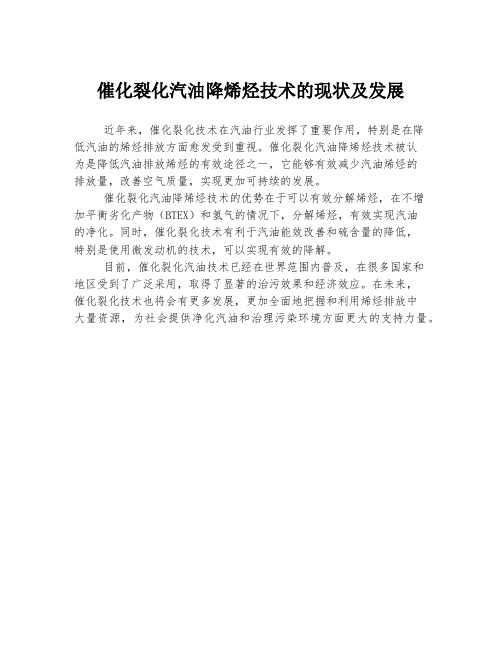
催化裂化汽油降烯烃技术的现状及发展
近年来,催化裂化技术在汽油行业发挥了重要作用,特别是在降
低汽油的烯烃排放方面愈发受到重视。
催化裂化汽油降烯烃技术被认
为是降低汽油排放烯烃的有效途径之一,它能够有效减少汽油烯烃的
排放量,改善空气质量,实现更加可持续的发展。
催化裂化汽油降烯烃技术的优势在于可以有效分解烯烃,在不增
加平衡劣化产物(BTEX)和氢气的情况下,分解烯烃,有效实现汽油
的净化。
同时,催化裂化技术有利于汽油能效改善和硫含量的降低,
特别是使用微发动机的技术,可以实现有效的降解。
目前,催化裂化汽油技术已经在世界范围内普及,在很多国家和
地区受到了广泛采用,取得了显著的治污效果和经济效应。
在未来,
催化裂化技术也将会有更多发展,更加全面地把握和利用烯烃排放中
大量资源,为社会提供净化汽油和治理污染环境方面更大的支持力量。
催化裂化催化剂的发展历程及研究进展

及研究进展2023-10-28CATALOGUE 目录•催化裂化催化剂概述•催化裂化催化剂的发展历程•催化裂化催化剂的研究进展•催化裂化催化剂的未来发展及挑战•结论与展望01催化裂化催化剂概述催化裂化催化剂是一种固体酸催化剂,用于促进石油烃类的大分子裂解成小分子,同时增加低沸点、高价值产品的产率。
催化裂化催化剂定义催化裂化催化剂可以提供活性位点,促进烃类分子的裂解、异构化和氢转移等反应,同时具有高选择性和高转化率的特点。
催化裂化催化剂作用催化裂化催化剂的定义与作用不同类型催化裂化催化剂酸性催化剂(如Y型、X型、ZSM-5等)、基性催化剂(如钙型、钠型等)、金属氧化物催化剂(如V2O5-WO3/TiO2等)。
不同类型催化裂化催化剂特点不同类型的催化裂化催化剂具有不同的酸性和活性特点,可以根据不同原料和产品需求进行选择。
催化裂化催化剂的种类与特点催化裂化催化剂发展历程从20世纪50年代开始,催化裂化技术逐渐发展并应用于工业生产,随着技术的进步,新型的催化裂化催化剂不断涌现。
催化裂化催化剂现状目前的催化裂化催化剂已经实现了高度专业化和精细化,不仅提高了产品的质量和产量,还降低了能耗和环境污染。
催化裂化催化剂的历史与现状02催化裂化催化剂的发展历程总结词第一代催化裂化催化剂主要基于氧化铝和氧化硅为载体,使用稀土元素和碱金属作为活性组分,具有较高的裂化活性和稳定性。
详细描述第一代催化裂化催化剂在上世纪60年代开始商业应用,主要基于氧化铝和氧化硅为载体,通过添加稀土元素和碱金属进行改性,提高了催化剂的活性和稳定性。
该催化剂在当时具有较高的裂化选择性,能够有效地将大分子烃类裂解成小分子烃类。
总结词第二代催化裂化催化剂在第一代催化剂的基础上,使用了新型载体材料和活性组分,进一步提高了裂化活性和选择性,同时降低了压力和温度要求。
详细描述第二代催化裂化催化剂在上世纪80年代开始商业应用,在第一代催化剂的基础上,使用了新型载体材料如分子筛等,并优化了活性组分的组成,进一步提高了催化剂的活化和选择性。
催化催化裂化技术
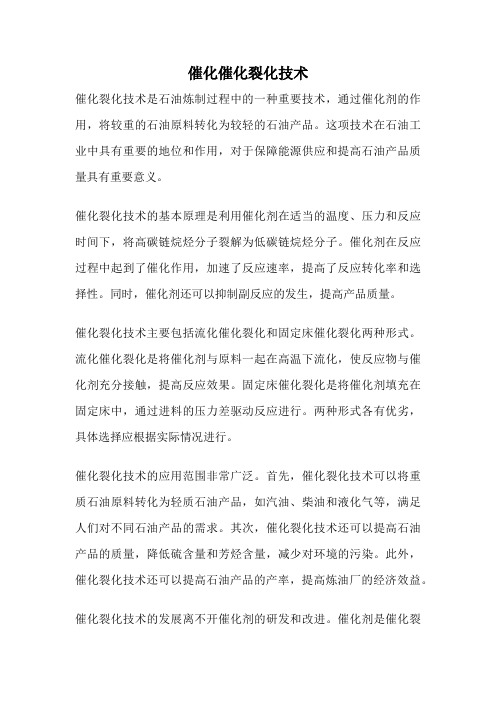
催化催化裂化技术催化裂化技术是石油炼制过程中的一种重要技术,通过催化剂的作用,将较重的石油原料转化为较轻的石油产品。
这项技术在石油工业中具有重要的地位和作用,对于保障能源供应和提高石油产品质量具有重要意义。
催化裂化技术的基本原理是利用催化剂在适当的温度、压力和反应时间下,将高碳链烷烃分子裂解为低碳链烷烃分子。
催化剂在反应过程中起到了催化作用,加速了反应速率,提高了反应转化率和选择性。
同时,催化剂还可以抑制副反应的发生,提高产品质量。
催化裂化技术主要包括流化催化裂化和固定床催化裂化两种形式。
流化催化裂化是将催化剂与原料一起在高温下流化,使反应物与催化剂充分接触,提高反应效果。
固定床催化裂化是将催化剂填充在固定床中,通过进料的压力差驱动反应进行。
两种形式各有优劣,具体选择应根据实际情况进行。
催化裂化技术的应用范围非常广泛。
首先,催化裂化技术可以将重质石油原料转化为轻质石油产品,如汽油、柴油和液化气等,满足人们对不同石油产品的需求。
其次,催化裂化技术还可以提高石油产品的质量,降低硫含量和芳烃含量,减少对环境的污染。
此外,催化裂化技术还可以提高石油产品的产率,提高炼油厂的经济效益。
催化裂化技术的发展离不开催化剂的研发和改进。
催化剂是催化裂化反应的核心,直接影响着反应的效果和产品的质量。
目前,石油工业中主要采用的催化剂是沸石型催化剂和金属催化剂。
沸石型催化剂具有较高的活性和选择性,能够有效地促进裂化反应的进行。
金属催化剂具有良好的抗中毒性能和稳定性,能够提高催化剂的使用寿命。
催化裂化技术的研究和应用还存在一些挑战和问题。
首先,催化剂的选择和制备是关键问题,需要探索新的催化剂材料和合成方法。
其次,催化剂的失活和再生问题也需要解决,以延长催化剂的使用寿命和降低生产成本。
此外,催化裂化技术的节能、环保和安全性问题也需要重视和解决。
催化裂化技术是石油工业中一项重要的技术,对于提高石油产品质量、增加产能和保障能源供应具有重要意义。
催化催化裂化技术
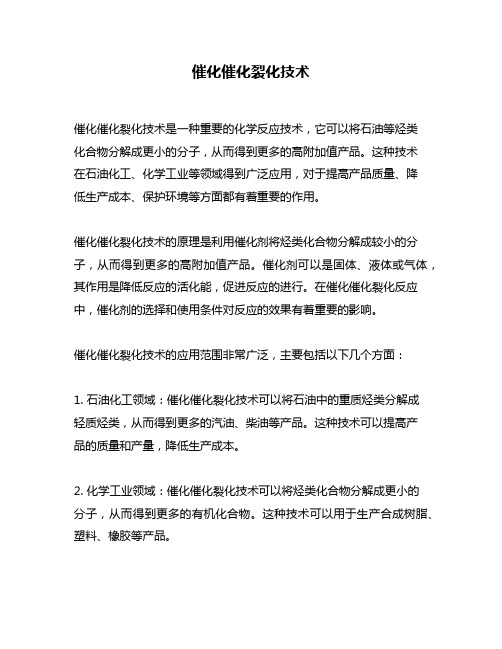
催化催化裂化技术
催化催化裂化技术是一种重要的化学反应技术,它可以将石油等烃类
化合物分解成更小的分子,从而得到更多的高附加值产品。
这种技术
在石油化工、化学工业等领域得到广泛应用,对于提高产品质量、降
低生产成本、保护环境等方面都有着重要的作用。
催化催化裂化技术的原理是利用催化剂将烃类化合物分解成较小的分子,从而得到更多的高附加值产品。
催化剂可以是固体、液体或气体,其作用是降低反应的活化能,促进反应的进行。
在催化催化裂化反应中,催化剂的选择和使用条件对反应的效果有着重要的影响。
催化催化裂化技术的应用范围非常广泛,主要包括以下几个方面:
1. 石油化工领域:催化催化裂化技术可以将石油中的重质烃类分解成
轻质烃类,从而得到更多的汽油、柴油等产品。
这种技术可以提高产
品的质量和产量,降低生产成本。
2. 化学工业领域:催化催化裂化技术可以将烃类化合物分解成更小的
分子,从而得到更多的有机化合物。
这种技术可以用于生产合成树脂、塑料、橡胶等产品。
3. 环保领域:催化催化裂化技术可以将废弃物和污染物分解成无害的物质,从而达到环保的目的。
这种技术可以用于处理废水、废气等污染物。
4. 药物和食品领域:催化催化裂化技术可以用于生产药物和食品添加剂。
这种技术可以将天然产物分解成更小的分子,从而得到更多的有效成分。
总之,催化催化裂化技术是一种非常重要的化学反应技术,它在石油化工、化学工业等领域得到广泛应用。
随着科技的不断发展,催化催化裂化技术的应用范围将会越来越广泛,对于推动经济发展、保护环境等方面都有着重要的作用。
- 1、下载文档前请自行甄别文档内容的完整性,平台不提供额外的编辑、内容补充、找答案等附加服务。
- 2、"仅部分预览"的文档,不可在线预览部分如存在完整性等问题,可反馈申请退款(可完整预览的文档不适用该条件!)。
- 3、如文档侵犯您的权益,请联系客服反馈,我们会尽快为您处理(人工客服工作时间:9:00-18:30)。
催化裂化技术综述摘要:本文主要介绍了催化裂化的工艺流程,阐述了清洁油品对催化裂化提出的挑战,同时指出催化裂化在未来炼厂中仍将发挥主要作用。
本文此外也介绍了重油催化裂化的特点以及其对工艺的要求。
关键词:催化裂化清洁油品地位1 前言催化裂化是最重要的重质油轻质化过程之一。
催化裂化过程投资少、操作费用低、原料适应性强、轻质产品收率高、技术成熟,是目前炼油厂利润的主要来源。
目前我国催化裂化的年加工能力已经超过1亿t,商品汽油构成中,催化裂化汽油占80%左右,柴油占30%左右,而且30%以上的丙烯也来自催化裂化过程。
2003年侯芙生院士和陈俊武院士分别阐述了催化裂化过程在重质油深度加工和炼油厂中的重要地位,认为催化裂化作为主要的重质油轻质化过程,仍将继续发挥骨干作用。
2 工艺介绍催化裂化装置的核心是反应再生系统,在提升管反应器部分完成强吸热的催化裂化反应,在再生器部分完成强放热烧焦再生反应,恢复催化剂活性,通过催化剂的循环实现反应器和再生器之间的热平衡。
尽管不同公司所开发的流化催化裂化(FCC)技术的反应再生系统的具体结构型式不同,但工艺流程没有本质区别。
图1 UOP公司的FCC反应再生系统以UOP公司的高低并列式反应再生系统为例(图1),反应部分由提升管反应器(包括预提升段、进料段、油气分离设备)和沉降器组成。
从再生器来的高温(680~730℃)再生催化剂,在预提升气的推动下向上运动,在进料段与经过喷嘴喷入的雾化原料接触汽化,在沿提升管向上运动的过程中于480~540℃下反应,主要是大分子转化为较小分子的裂化反应,同时由于缩合反应生成少量焦炭沉积在催化剂上使其活性迅速降低,经过很短的反应时间(2~4 s)后,油气与大部分催化剂经提升管末端快分设备分离,并经沉降器内的旋风分离器进一步分离后离开反应系统去分馏塔,而结焦的催化剂进入沉降器的汽提段进一步分离油气,经充分汽提的结焦催化剂由待生斜管进入再生器进行再生,在高温(680~730℃)下由空气烧去催化剂上的焦炭,恢复其活性,再生催化剂经再生斜管返回到反应部分,完成催化剂的循环。
由此可见,FCC反应再生系统是一个连续循环的系统,原料的转化是一个湍流的多相催化快速反应体系。
3 清洁燃料对催化裂化的挑战从全球看,汽、柴油的硫含量不可避免地要下降,烯烃和芳烃也要降低。
国外由于其所加工的原油和相应加工路径的特点,烯烃的体积分数相对不高,一般不超过15 % ,而国内则要高得多,特别是以催化裂化汽油为主的90 号汽油的烯烃体积分数常超过40 %。
[1]3.1 FCC汽油和柴油的脱硫在原料基本固定的情况下,要降低FCC 产品的硫含量,可选用多种方法,如FCC 原料的预处理、在FCC 装置中使用合适的催化剂和添加剂、FCC 产品后处理等,这些方法既可单独使用,也可组合使用。
很明显,不同的方法各有优点和不足。
进料预处理的投资和操作费用都很高,但其优点也很明显,即在降低产品硫含量的同时,降低了烟气硫含量,更重要的是改进了FCC 产品分布和操作,如提高轻质油收率,降低焦炭产率,降低FCC 催化剂消耗等。
因此,从长远的观点看,进料预处理是非常有吸引力的选择。
优化FCC 操作和催化剂(包括添加剂) 虽然简便易行,费用低,但降低硫含量的效果有限,可作为临时性的措施和特定的装置,如进料硫含量低、产品规格要求不严格等情况。
FCC 油品后处理技术的研究是目前最活跃的领域之一。
由于常规的后加氢处理工艺耗氢量高,辛烷值损失大,世界上许多公司都已开发出各具特色的脱硫工艺,且主要是针对催化裂化汽油或柴油(LCO) 。
这些工艺根据其采用的脱硫技术主要可分为选择性加氢、吸附、氧化、生物脱硫等及其他技术。
各项脱硫工艺对汽油辛烷值和产率损失的影响见图2。
图2 脱硫率为99%时FCC汽油辛烷值和产率损失(黑色柱形代表辛烷值损失,白色柱形代表产率损失)在FCC 汽油的后处理工艺中,S Zorb是一较有代表性的技术,由于采用锌吸附剂,其氢耗量低,辛烷值损失和产率损失也较低。
S Zorb工艺的净化学氢耗量与反应温度有很大关系,提高反应温度可降低氢耗量直至零氢耗。
对于不需要提高十六烷值的进料,可采用零氢耗操作。
降低氢耗量不但可降低操作费用,而且可降低二氧化碳和氧化氮的生成。
3.2 国内FCC汽油和柴油的其它质量标准问题对于国内的油品标准,在借鉴国外标准的同时,应充分考虑国内的实际情况。
在新的汽油标准中,对国内炼油企业影响最大的是规定汽油的烯烃体积含量不超过35 % ,而标准规定的芳烃体积含量上限达40 % ,超过作为国内主要油品组分的FCC 汽油1倍以上。
与中国经济快速增长相适应的是炼油工业的快速发展,加上炼油厂的大型化,在发展中调整炼油厂的装置构成,逐步提高除催化裂化外其它工艺装置(重整、加氢等) 的比例。
若FCC 汽油占到总调合汽油的50 %~60 % ,则调合汽油的烯烃体积含量降到25 %以下是可行的。
国内外都在开发用于劣质FCC 柴油的改质技术,国外如UOP 的Redar,国内开发的MCI 技术和RICH 技术已有成功的工业应用。
国内这两种催化裂化柴油加氢改质技术都能在脱硫脱氮的同时,发生芳烃开环,在保证柴油收率高于95%的前提下,提高柴油十六烷值10个单位以上,油品密度下降约01035g/cm3。
4 催化裂化的地位从现有的二次加工工艺看,主要有催化裂化、加氢裂化、重整、焦化。
催化裂化的主要产品是汽油、柴油、液化气(丙烯) ,其产品优点是汽油辛烷值高,芳烃含量不高;缺点是汽油烯烃含量高,柴油十六烷值低,产品硫含量高。
加氢裂化主要产品是石脑油、喷气燃料、加氢裂化柴油和尾油,其最大优点是柴油的十六烷值高,硫含量低,但石脑油辛烷值低,一般不能直接用作汽油调合组分,需要进行重整。
重整汽油虽然辛烷值高,但芳烃和苯含量高,也限制了其在总调合汽油中的调合比例。
对于VGO 加工,用加氢裂化代替催化裂化至少存在两方面的问题,一是加氢裂化投资高,操作费用高,二是加氢裂化生产的重石脑油的出路问题。
加氢裂化生产的轻汽油馏分( < 80℃) 的RON 一般为75~85 ,中重汽油馏分(80~200℃) 的RON 一般为60~70 ,远低于催化裂化汽油的88~94 。
石脑油用作重整原料,可生产大量的重整汽油,但重整汽油的芳烃含量太高,掺入过量也不符合清洁汽油的要求。
在我国,采用加氢裂化工艺还存在氢源的问题,由于重整原料不足,难以为加氢裂化提供足够量价格相对低廉的氢气。
而且加氢裂化一般仅能加工类似VGO一样的原料,它所产生的10 %~40 %的加氢尾油,还需要进一步加工。
使用劣质原料将缩短加氢裂化的生产周期,严重影响其经济性,并且减压渣油难以加氢裂化。
虽然加氢裂化加工渣油技术正在开发之中,但要实现大规模运行并与催化裂化技术相抗衡尚需时日。
加氢裂化和催化裂化技术不能代替,但是可以合作。
特别是在加工高含硫原料和生产优质柴油方面,加氢裂化有其独特的优势。
如UOP 公司提出的部分加氢裂化与催化裂化相结合的工艺,不但可生产更多的优质柴油,还可改进催化裂化装置的产品分布。
用加氢处理与催化裂化的组合工艺加工高硫原料是国外较为常用的加工路线。
加氢处理是20 世纪90年代炼油厂中加工能力增长最快的装置,短短10 年中,加工能力增长超过4 倍。
我国的催化裂化更多地作为渣油加工的手段,这是适应国内原油组成的一种必然选择。
但随着中国进口原油量的增加,特别是环烷基类原油和硫含量的增加,需要增加与催化裂化相配套的劣质渣油加工能力。
劣质渣油的加工,国内同样有加氢和焦化两种路线。
有关经济性的评价表明,两种路线各有利弊。
焦化路线投资少,在目前油价较低时具有优势,但当原油价格上涨时,由于其主要产品之一的石油焦价格基本不变,影响整体收益的提高,未来还面临更严格的环境保护方面的挑战,占地面积大也是一个重要的问题。
加氢路线投资高,但总液体产品收率高,在适应高油价和环境保护方面具有优势。
当前催化裂化在化工方面的贡献主要是生产丙烯,美国炼油厂生产的丙烯约占总丙烯产量的50 % ,乙烯约占1 %。
我国丙烯产量中40 %以上由催化裂化生产。
预计未来的20 年,丙烯需求增长率将超过乙烯,催化裂化装置(含我国开发的DCC、MGG、FDFCC 等工艺) 将是重要的丙烯生产装置。
应用催化裂化的基本原理,采用特制催化剂,我国率先开发成功了将大庆常压渣油裂解为乙烯、丙烯等产品的HCC 和CPP 工艺,加上乙烷裂解,乙烯产率达25 %左右,有望形成一条结合我国国情较为经济的重油制乙烯技术路线。
在高苛刻度转化条件下,催化裂化汽油芳烃含量高,印度Jamnagar 炼油厂从催化裂化汽油中间馏分提取C7~C9 芳烃,进一步转化为对二甲苯,产量可观。
预期催化裂化将是炼油/ 化工一体化的核心装置。
5 重油催化裂化重油催化裂化是指以VGO掺兑渣油,或常压渣油甚至是减压渣油作为原料的催化裂化过程。
渣油与VGO相比,原料更重,残炭和金属含量更高。
原料重,不宜于雾化,更难以完全汽化,使RFCC过程成为更复杂的气液固三相反应体系,给油剂有效接触带来困难;原料重,一般胶质和沥青质含量高,残炭高,会显著增加焦炭产率,给催化剂的汽提和再生带来困难,研究表明,对于不含沥青质的抽提油,其胶质含量与催化裂化反应的焦炭产率之间呈直线关系;渣油中镍、钒等金属的含量高,直接影响到催化剂的活性、选择性和稳定性。
因而,重油催化裂化使传统FCC过程面临严峻挑战,对催化剂、油剂接触、油剂快分、待生剂汽提和再生等提出了更高的要求。
在催化剂方面,筛选载体,调整孔径分布,减小扩散阻力,提高抗镍、钒污染能力;调整沸石的性质,在改善稳定性的同时,改善焦炭的选择性。
在工艺方面,采用干气预提升技术,减少水热失活,减少污染金属对催化剂的破坏及对反应选择性的影响;采用高效雾化喷嘴,优化喷嘴结构及布置,改善油剂接触,提高反应的转化率和选择性;采用终止剂技术,及时终止反应,保证较高的轻质产品收率;采用快分技术和高效汽提技术,强化油剂的分离,减少催化剂携带到再生器的油气量;采用新型催化剂再生技术,在高效再生的同时,减少催化剂的水热失活;采用再生器取热技术,维持反应器和再生器之间的热平衡等。
[2]6 结语催化裂化作为炼油厂中的核心工艺装置,主要在生产汽油、柴油、液化气和丙烯方面发挥着重要作用。
目前,催化裂化虽然面临从原料、生产过程到产品规格等方面一系列的问题,但都可通过合理的途径获得较为满意的解决。
展望未来,催化裂化仍将发挥其在炼油厂中作为主要二次加工装置的作用,尤其在生产汽油方面,它与加氢裂化二者相辅相成。
催化裂化技术也需不断发展,以适应变化着的市场需求。
可以预见今后在炼油/ 化工一体化中催化裂化将扮演重要角色。