高光无痕注塑模具设计规范
注塑模具设计之顶出设计规范

恒模技字(2003)第号电视机模具顶出的设计规范1.目的规范顶出设计,确保安全,顺畅顶出制品2.内容2.1.设计原则a.顶针分布平均.b.应分布在塑件强度较好,尽量接近粘模力较大处。
c.顶针距离哥边或其他零件有3mm。
d.顶针孔尽可能不做成刀口。
e.顶针与模芯间有4个针径或至少20mm以上导向配合。
f.顶针不能半边骑住成品边,不能与定模碰,滑块擦;g.顶针要离开成品哥顶、转接线R位边1mm。
h.顶端有异形之顶针、司筒/针要有销钉防转。
i.顶针高出推方较大时,顶针延迟。
j.司筒针用压片(不是机米螺丝)压着。
k.顶针、司筒/针、推方杆孔离螺丝杯头孔至少2mm。
l.中心K.O孔与唧嘴同轴。
m.顶针、司筒/针、推方杆压台与沉头孔要有0.05~0.15mm的配合间隙。
n.产品倒角留在司筒上,倒角尖端磨平0.2mm。
o.顶针规格不得小于φ8。
p.四角R应在推方上做出。
q.运动推方、角铁之间应有标准连接块连接。
恒模技字(2003)第号电视机模具顶出的设计规范 2.3.顶针的设计形式,2.4 顶针板强制先复位为了保证顶针和滑块的安全,顶针板必须强制先复位.恒模技字(2003)第 号电视机模具顶出的设计规范2.5 推方a.为了方便推方的装拆,推方杆头部采用组合结构,底针板、底板做螺丝装拆孔。
b.推方联接螺丝头部要有堵头螺丝紧固,推方工艺孔在走模前用堵头螺丝堵上,设尺寸如下图。
恒模技字(2003)第号电视机模具顶出的设计规范面壳顶针分布滑块侧的PCB板槽筋脱很困难,顶针分布如图示。
高光模具设计准则

課程內容
„ 前言 „ 高光製程的原理及高光设备运行步骤 „ 采用高光製程的优势 „ 采用高光製程易出现的问题点 „ 高光模具設計流程 --- 浇注系统設計 --- Steam channel与一般冷却水路設計 --- 隔热板及感温线位置设计 „ 產品設計要點
前言
本課程以傳統模具設計技術為基礎,考慮高光即冷即熱製程的差異點 說明高光模具設計的流程及考慮重點,並針對不同的產品型式,藉範例說 明其設計重點及理念。 本課程內容融合韓國模具業界之成熟技術及在中國的實際經驗整理歸納而 成,但不代表可以解決所有高光產品的模具設計難點,個別產品需使用本 課程內容為基礎深入研究。
高光模具設計流程 —— Steam channel与冷却水路設計
LCD TV 模具結構
高光模具設計流程 —— Steam channel与冷却水路設計
模 具 設 計 及 分 析 介 紹
Inlet
邊界條件
– Initial Condition – Mold Temperature : 60℃ - Heating InputPressure : 8kg/cm2 Heat Source : Pressurized Hot Water Inlet Temp. : 165 C - Cooling Input Pressure : 8kg/cm2 Coolant : Water Inlet temp. : 25 C
水路的优化
LX1系列
变更前
LB1系列
变更后
1.
如上图所示,LB1系列与Fuji公司制作的LX1系列相比,结构简单,无需使用O-Ring,可以弥补 水路漏水等问题.(LB1系列当前周期时间为70sec, 而 LX1系列的周期时间为: 110sec) 2. Heat & Cool系统 的IN, OUT分别为12EA, 目前模具设计正在以IN,OUT 4EA两倍,即8EA进行设计 3. LB1系列是在LX1基础上的改善方案。
高光无痕注塑模具的设计制造特点
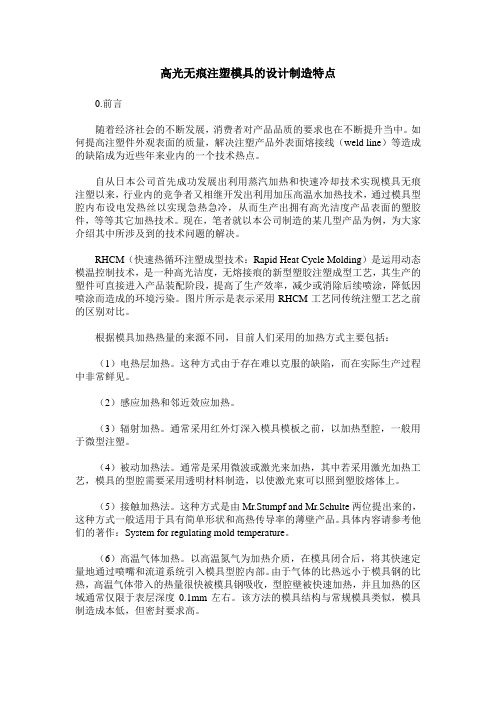
高光无痕注塑模具的设计制造特点0.前言随着经济社会的不断发展,消费者对产品品质的要求也在不断提升当中。
如何提高注塑件外观表面的质量,解决注塑产品外表面熔接线(weld line)等造成的缺陷成为近些年来业内的一个技术热点。
自从日本公司首先成功发展出利用蒸汽加热和快速冷却技术实现模具无痕注塑以来,行业内的竞争者又相继开发出利用加压高温水加热技术,通过模具型腔内布设电发热丝以实现急热急冷,从而生产出拥有高光洁度产品表面的塑胶件,等等其它加热技术。
现在,笔者就以本公司制造的某几型产品为例,为大家介绍其中所涉及到的技术问题的解决。
RHCM(快速热循环注塑成型技术:Rapid Heat Cycle Molding)是运用动态模温控制技术,是一种高光洁度,无熔接痕的新型塑胶注塑成型工艺,其生产的塑件可直接进入产品装配阶段,提高了生产效率,减少或消除后续喷涂,降低因喷涂而造成的环境污染。
图片所示是表示采用RHCM工艺同传统注塑工艺之前的区别对比。
根据模具加热热量的来源不同,目前人们采用的加热方式主要包括:(1)电热层加热。
这种方式由于存在难以克服的缺陷,而在实际生产过程中非常鲜见。
(2)感应加热和邻近效应加热。
(3)辐射加热。
通常采用红外灯深入模具模板之前,以加热型腔,一般用于微型注塑。
(4)被动加热法。
通常是采用微波或激光来加热,其中若采用激光加热工艺,模具的型腔需要采用透明材料制造,以使激光束可以照到塑胶熔体上。
(5)接触加热法。
这种方式是由Mr.Stumpf and Mr.Schulte两位提出来的,这种方式一般适用于具有简单形状和高热传导率的薄壁产品。
具体内容请参考他们的著作:System for regulating mold temperature。
(6)高温气体加热。
以高温氮气为加热介质,在模具闭合后,将其快速定量地通过喷嘴和流道系统引入模具型腔内部。
由于气体的比热远小于模具钢的比热,高温气体带入的热量很快被模具钢吸收,型腔壁被快速加热,并且加热的区域通常仅限于表层深度0.1mm左右。
车灯长条柱形导光件高光无痕模具的设计

车灯长条柱形导光件高光无痕模具的设计发布时间:2022-10-12T07:09:02.548Z 来源:《科技新时代》2022年4月第7期作者:陈佳斌[导读] 车灯长条柱形导光件在生产制作过程中运用到了高光无痕模具陈佳斌广州导新模具注塑有限公司摘要:车灯长条柱形导光件在生产制作过程中运用到了高光无痕模具,它基于多点顺序开发注塑成型,是比较成熟的工艺模具,为汽车车灯灯具长条柱形导光件形成高光无痕模具模型。
本文中就探讨了这一模具的生产制作技术要求,并设计提出模具注塑成型方案。
关键词:车灯长条柱形导光件;高光无痕模具;技术要求;注塑成型;设计目前汽车车灯一般会采用LED新型绿色光源,其安全可靠且低能耗、响应快、体积小,是非常理想的汽车信号灯具。
但是,考虑到LED光源具有单向发光特征,就需要利用导光柱方法确保LED光源能够满足全方位照明要求,即扩大照明面积。
在这里,需要分析导光柱这一光学元件的表面光洁度以及体内介质,了解光学折射影响、反射性能以及反射效率。
一、关于高光无痕注塑成型高光无痕注塑成型技术是目前新兴的注塑技术,该技术对消除注塑件表面的熔接痕缺陷方面表现出色,可以保证注塑模型表面达到镜面效果,如此就能免除二次喷涂,节省成本。
在高光无痕注塑成型技术应用过程中,其技术核心就是模具本身,它可有效应用于汽车车灯灯具中,形成较为完善的长条柱形导光件注塑成型方案,同时也能做到直接NC加工成形[1]。
二、汽车车灯灯具产品的模具生产技术要求汽车车灯灯具产品中长条柱形导光件采用到了柱形导光条,它的材质一般为PMMA,灯具结构为对称结构。
该产品介质通透,且配光表现出色,没有明显翘曲变形,同时也无缩痕与接痕痕迹缺陷。
在研究LED点光源过程中,需要了解光源的折射、反射成光带变化,保证光量与效果表现突出。
一般来说,要在产品中设计齿形花纹并保证其齿高在0.5mm以上,同时齿距控制在1.00mm以上,光洁度则要保证在Ra≤0.1μm。
注塑模具设计规范
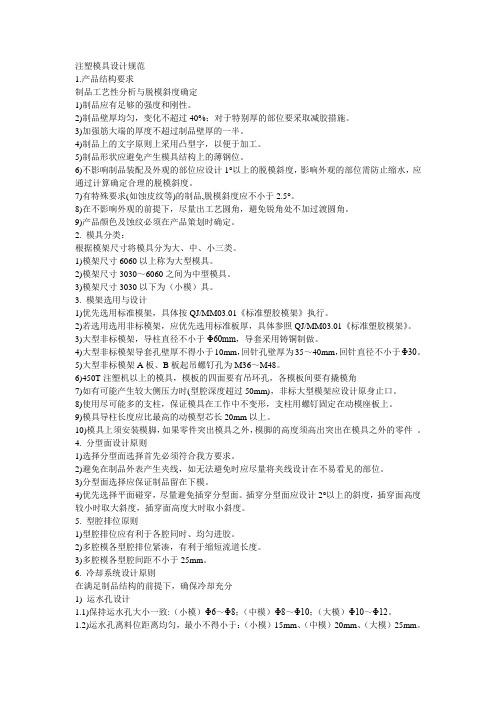
注塑模具设计规范1.产品结构要求制品工艺性分析与脱模斜度确定1)制品应有足够的强度和刚性。
2)制品壁厚均匀,变化不超过40%;对于特别厚的部位要采取减胶措施。
3)加强筋大端的厚度不超过制品壁厚的一半。
4)制品上的文字原则上采用凸型字,以便于加工。
5)制品形状应避免产生模具结构上的薄钢位。
6)不影响制品装配及外观的部位应设计1°以上的脱模斜度,影响外观的部位需防止缩水,应通过计算确定合理的脱模斜度。
7)有特殊要求(如蚀皮纹等)的制品,脱模斜度应不小于2.5°。
8)在不影响外观的前提下,尽量出工艺圆角,避免锐角处不加过渡圆角。
9)产品颜色及蚀纹必须在产品策划时确定。
2. 模具分类:根据模架尺寸将模具分为大、中、小三类。
1)模架尺寸6060以上称为大型模具。
2)模架尺寸3030~6060之间为中型模具。
3)模架尺寸3030以下为(小模)具。
3. 模架选用与设计1)优先选用标准模架,具体按QJ/MM03.01《标准塑胶模架》执行。
2)若选用选用非标模架,应优先选用标准板厚,具体参照QJ/MM03.01《标准塑胶模架》。
3)大型非标模架,导柱直径不小于Φ60mm,导套采用铸铜制做。
4)大型非标模架导套孔壁厚不得小于10mm,回针孔壁厚为35~40mm,回针直径不小于Φ30。
5)大型非标模架A板、B板起吊螺钉孔为M36~M48。
6)450T注塑机以上的模具,模板的四面要有吊环孔,各模板间要有撬模角7)如有可能产生较大侧压力时(型腔深度超过50mm),非标大型模架应设计原身止口。
8)使用尽可能多的支柱,保证模具在工作中不变形,支柱用螺钉固定在动模座板上。
9)模具导柱长度应比最高的动模型芯长20mm以上。
10)模具上须安装模脚,如果零件突出模具之外,模脚的高度须高出突出在模具之外的零件。
4. 分型面设计原则1)选择分型面选择首先必须符合我方要求。
2)避免在制品外表产生夹线,如无法避免时应尽量将夹线设计在不易看见的部位。
高光无痕注塑模具设计规范

高光无痕注塑模具设计规范高光无痕注塑模具设计制造规范一、高光无痕注塑的原理:1、模具成型对温度要求较高(一般为80°~130°左右),在注塑转入保压后改用冷却水,使模具降温至60°~70°度。
在较高的模温下保压成型有利于消除熔接痕、流痕、产品内应力等缺陷。
因此模具在工作时需进行加热处理,为了防止热量损失,一般都会在定模侧加树脂隔热板。
2、模腔表面极度光亮(一般为镜面2级或更高)。
高光模具生产出的产品能够直接用于装机,无需做任何表面处理。
因此它对模具钢材及塑胶材料的要求都很高。
3、热流道系统的热咀较多。
每个热咀必须带封针且有独立的气道,经过电磁阀及时间继电器等进行单独控制,实现分时进胶,从而达到控制甚至消除熔接痕的目的。
4、模具加热的方式一般有水蒸汽加热(见图1)和加热棒加热(见图2)两种。
水蒸汽加热方式是经过特定的模温机在注塑过程中经过模具通蒸汽,从而使模具快速升温;在注塑完后改一般温水(或者冰水)使模具快速降温。
加热棒加热方式是在注塑过程中经过在内模料里面加加热棒使模具快速升温;在注塑完成后经过内模料里面的运水(常温水或者冰水)或者叠层模料底部的铝材(铝材里面通运水)使模具温度快速降温。
(图1)(图2)二、模具材料(一)产品表面普通要求的模具材料可用NK80(日本大同);(二)高光要求的产品选用S136H(瑞典)、CEANA1(日立);(三)NK80可不用淬火处理;S136应在粗加工后淬火至52度;CEANA1号本身具备42度也不需要淬火处理(建议用此材料,因不影响后续加工或改动);(四)德国葛利兹品牌中也有不错的选择:CPM40\GEST80三、模具水道设计(一)水道采用5mm-6mm大小的孔;水嘴用1\8或3\8的牙(模具侧),另一侧用3\4英制螺纹;管件材料用不锈钢管;(二)水道一侧离产品面最近不低于5mm-6mm;水道平行产品面且均匀排布(原则中心距15mm分布,);热电偶应设计在两水道中间,深度在50mm左右;且每套模具的PT100是一配一的,保持它的精确度,埋在模具模仁内,与热流道的热电偶一样,用线连接到模具外侧,转接插座,PT100要有对应的插头与其对接。
RHCM高光无痕注塑系统技术介绍

奥德模温机RHCM高光无痕注塑系统技术介绍2010-5-29 点击:29次180℃过热水“RHCM高光无痕注塑”系统技术介绍:RHCM高光无痕注塑又被称为RHCM (Rapid Heat Cycle Moulding),还有在行业中如:冷热成型,高低温注塑,急冷急热注塑,热变温注塑.高光免喷涂技术等叫法,目前行业中使用效果最好最经济的方法是采用高温过热水加热+水冷却,该技术是透过运用180℃过热水将模具表面快速升温,令成型模腔表面温度达到树脂塑料的玻璃转移温度(Tg – Glass Transition Temperature)以上,然后开始进行射出成型,当完成模腔填充过程后,立即利用水(经处理)作为冷却媒体使模具表面温度急速下降,从而改变塑料产品表面特性。
RHCM “高光无痕注塑”技术发展至今已近4年之多,早期是日本.韩国的3 D蒸汽无痕注塑技术在汽车.家电行业的到广泛的应用,但是由于使用的加热源是采用锅炉产生的蒸汽来给模具加热,所以采用锅炉蒸汽加热的方式会受到地方环保和安全的限制,最重要的是采用锅炉产生的蒸汽给模具加热后,蒸汽没有办法得到回收造成的高成本问题,一直一创新为企业长期发展为根源的奥德公司在2006年初就看到国内这块市场的空白,并成立了专门针对过热水的高光无痕项目研发团队,在2007年初成功推向市场,经过半年的市场考验和用户考核,奥德公司所研发的GWS高光无痕注塑模温控制系统(急速升降模温系统)获得了塑料行业的技术创新奖, 同时获得国家审批专利证书(专利号:ZL。
2008.2.0205521.0), 并得到国内知名的液晶电视及其他高光产品外壳(如惠州TCL.台湾广达集团.广州毅昌科技,无锡金悦.青岛恒佳...昆山亿盛..)等数十家生产厂家的广泛使用,使用RHCM “高光无痕注塑”技术生产LCD液晶平板电视外壳,其中主要优点是可以使树脂塑料产品外壳拥有高光泽度;消除了传统注塑成型工艺存在的熔接痕.结合线.(加波纤产品的浮纤)问题,并省却了产品二次加工的必要和有关的成本(例如:喷漆.UV…..)。
高光无夹线无痕注塑技术

高光无夹线无痕注塑技术高光注塑成型过程◆射出成型现实为了决定射出成型产品的最终外观质量,制造者和需求者必须要对限度样本达成一致意见。
因为所有人都认可射出成型产品的外观本来就不存在完美无缺的质量产品的观点。
即“在射出成型中出现焊接痕weldline, 流痕Flow mark,光泽不均匀等缺点是必然的。
”那么“射出成型产品为什么一定要有外观的缺点呢??”这是由于控制工序的技术还不完善的缘故。
虽然工序的变数很多,但如果有数值控制的方法总会生产出一定的、完美质量的产品,但是射出成型工序并非如此。
即在射出成型过程中,最重要的几种因素不能得到有效控制,其中最有代表性的因素就是不能合适地控制模具温度. 因此塑料这种物质从问世以来就存在这样的问题人们已经束手无策了,人们也接受了相关的质量问题和不可能解决的现实。
◆射出成型中对模具温度的观念虽然到目前为止在射出成型工厂中还不能控制温度到希望的水平,但人们一直在努力想尽办法去控制模具温度。
从其发展过程来看,70年代为止,主要使用的是成型温度较低的范用树脂,当时的目的是尽可能使模具快速冷却;到了80年代,更加重视外观的ABS树脂等出现,提高了模具温度,也使外观质量得到改善。
其后有助于防止ABS 的致命缺点-- stress cracking的相关概念出现,到了90年代,开始有Polycarbonate等高耐热性Engineering Platic和PEEK,Arylate树脂等液晶树脂(LCP)出现,将模具温度加热到200℃以上高温的必要性抬头,同时在一般外观产品中也将其制造成无涂装无缺点外观射出成型产品的要求随着人们对环境保护的日益关心也被提出。
但实际上将模具温度加热到200℃有诸多困难,同时由于热膨胀会导致模具制动部位发生问题,更有甚者,会发生射出成型品粘着在模具上不能被分离、高温导致的分模面Parting部位发生毛刺Burr及收缩等等问题,在实际中并不适用。
◆用超高温加热模具进行射出成型会出现什么现象?那么实际上将模具温度加热到所需的200℃以上超高温会出现什么现象? 没有经历过的人绝对不可能知道。
注塑模设计原则

注塑模设计原则注塑模是塑料成型加工中广泛使用的一种模具类型,其设计的合理性直接影响到塑料制品的质量、生产效率和成本。
在进行注塑模设计时,需要遵循一系列的原则,以确保模具的功能、性能和可靠性。
一、产品分析在设计注塑模之前,必须对所要生产的塑料制品进行全面的分析。
这包括产品的形状、尺寸精度、表面质量要求、材料特性等。
通过对产品的分析,可以确定模具的结构形式、型腔数量、浇口位置和分型面等关键因素。
例如,对于形状复杂的产品,可能需要采用多腔模具或复杂的脱模机构;对于尺寸精度要求高的产品,模具的制造精度和配合精度也需要相应提高;对于表面质量要求高的产品,模具的型腔表面需要进行精细的加工和抛光。
二、材料选择注塑模的材料选择对模具的使用寿命和性能有着重要影响。
模具材料应具有足够的强度、硬度、耐磨性和耐腐蚀性,同时还应考虑其加工性能和成本。
常用的模具钢有 P20、718H、NAK80 等。
对于大批量生产、要求高精度和长寿命的模具,通常会选择性能更好但价格较高的模具钢;对于小批量生产或要求不高的模具,可以选择价格相对较低的模具钢。
此外,模具的其他部件,如导向件、脱模机构等,也需要根据其工作条件和要求选择合适的材料。
三、型腔布局型腔布局的合理性直接影响到生产效率和模具的尺寸。
在确定型腔布局时,需要考虑注塑机的最大注射量、锁模力、注射压力等参数,以及产品的尺寸和形状。
一般来说,型腔布局应尽量对称,以保证模具受力均匀;型腔之间的间距应足够大,以便于冷却水道的布置和模具的加工;对于大型产品,可能采用单型腔模具,以确保产品的质量和尺寸精度。
四、浇口设计浇口是塑料熔体进入型腔的通道,其设计直接影响到塑料制品的质量和成型效率。
浇口的类型、位置和尺寸都需要根据产品的形状、尺寸、材料和成型要求进行合理选择。
常见的浇口类型有直接浇口、侧浇口、点浇口等。
直接浇口适用于大型、深腔的产品,但容易产生较大的残余应力和浇口痕迹;侧浇口应用广泛,加工简单,但可能会在产品表面留下浇口痕迹;点浇口适用于外观要求高的产品,但模具结构相对复杂。
注塑模具技术规范要求

A: 模具外观1: 铭牌内容要打印模具编号、模具重量(KG)、模具外形尺寸(mm),字符均用1/8英寸的字码打上,字符清晰、排列整齐。
2: 铭牌要固定在模腿上靠近后模板和基准角的地方(离两边各有15mm的距离),用四个柳钉固定,固定可靠,不易剥落。
3; 冷却水嘴要用塑料块插水嘴,¢10管,规格可为G1/8″、G1/4″、G3/8″。
如合同有特殊要求,按合同。
4: 冷却水嘴要伸出模架表面,水嘴头部凹进外表面不超过3mm。
5: 冷却水嘴避空孔直径要为¢25、¢30、¢35mm三种规格,孔外沿有倒角,倒角大于1.5×45,倒角一致。
6: 冷却水嘴要有进出标记,进水为IN,出水为OUT,IN、OUT后加顺序号,如IN1、OUT1。
7: 标识英文字符和数字要大写(5/6″),位置在水嘴正下方10mm处,字迹清晰、美观、整齐、间距均匀。
8:进出油嘴、进出气嘴要同冷却水嘴,并在IN、OUT前空一个字符加G(气)、O(油)。
9: 模具安装方向上的上下侧开设水嘴,要内置,并开导流槽或下方有支撑柱加以保护。
1文档来源为:从网络收集整理.word版本可编辑.欢迎下载支持.10: 无法内置的油嘴或水嘴下方要有支撑柱加以保护。
11: 模架上各模板要有基准角符号,大写英文DATUM,字高5/16″,位置在离边10mm处,字迹清晰、美观、整齐、间距均匀。
12: 各模板要有零件编号,编号在基准角符号正下方离底面10mm处,要求同11号。
13: 模具配件要影响模具的吊装和存放,如安装时下方有外漏的油缸、水嘴、预复位机构等,应有支撑腿保护。
14: 支撑腿的安装要用螺丝穿过支撑腿固定在模架上,或过长的支撑腿车加工外螺纹紧固在模架上。
15: 模具顶出孔要符合指定的注塑机,除小型模具外,原则上不能只用一个中心顶出(模具长度或宽度尺寸有一个大于500mm时),顶出孔直径应比顶出杆大5-10mm。
16: 定位圈要可靠固定(一般用三个M6或M8的内六角螺丝),直径一般为¢100或¢150mm,高出顶板10mm。
注塑模具设计原则和核心

注塑模具设计原则和核心注塑模具设计原则和核心是什么?为方便同学们学习并了解,为大家带来注塑模具设计原则和核心知识如下:一、开模方向和分型线每个注塑产品在开始设计时首先要确定其开模方向和分型线,以保证尽可能减少抽芯滑块机构和消除分型线对外观的影响。
1、开模方向确定后,产品的加强筋、卡扣、凸起等结构尽可能设计成与开模方向一致,以避免抽芯减少拼缝线,延长模具寿命。
2、开模方向确定后,可选择适当的分型线,避免开模方向存在倒扣,以改善外观及性能。
二、脱模斜度1、适当的脱模斜度可避免产品拉毛(拉花)。
光滑表面的脱模斜度应≥0.5度,细皮纹(砂面)表面大于1度,粗皮纹表面大于1.5度。
2、适当的脱模斜度可避免产品顶伤,如顶白、顶变形、顶破。
3、深腔结构产品设计时外表面斜度尽量要求大于内表面斜度,以保证注塑时模具型芯不偏位,得到均匀的产品壁厚,并保证产品开口部位的材料强度。
三、产品壁厚1、各种塑料均有一定的壁厚范围,一般0.5~4mm,当壁厚超过4mm时,将引起冷却时间过长,产生缩印等问题,应考虑改变产品结构。
2、壁厚不均会引起表面缩水。
3、壁厚不均会引起气孔和熔接痕。
四、加强筋1、加强筋的合理应用,可增加产品刚性,减少变形。
2、加强筋的厚度必须≤(0.5~0.7)T产品壁厚,否则引起表面缩水。
3、加强筋的单面斜度应大于1.5°,以避免顶伤。
五、圆角1、圆角太小可能引起产品应力集中,导致产品开裂。
2、圆角太小可能引起模具型腔应力集中,导致型腔开裂。
3、设置合理的圆角,还可以改善模具的加工工艺,如型腔可直接用R刀铣加工,而避免低效率的电加工。
4、不同的圆角可能会引起分型线的移动,应结合实际情况选择不同的圆角或清角。
六、孔1、孔的形状应尽量简单,一般取圆形。
2、孔的轴向和开模方向一致,可以避免抽芯。
3、当孔的长径比大于2时,应设置脱模斜度。
此时孔的直径应按小径尺寸(最大实体尺寸)计算。
4、盲孔的长径比一般不超过4。
注塑模具规范

模具技术要求一﹑模具设计﹕A. 水路﹕1.公母模﹕依成品形状来决定﹐水路循环的路径与数量﹐公母模的水路需相互配合.2.脱料板x 2 cycle。
3.水孔接头处需做沉孔,沉孔尺寸φ35*L25mm。
4.模具的水栓处,必需上IN﹑OUT且编号。
5.需附铜制水栓﹐铜水栓的尺寸为3/8” PT。
6.侧面止水栓之做法﹐2PCS止水栓或1PCS止水栓+铜块。
7.若有喷水孔﹐使用铜片做隔板。
B. 料沟﹕依成品进料达到平衡﹐来设计料沟的路径﹑形状﹑尺寸…等。
C. 进点﹕依成品的外观形状要求重点﹐来决定进点的型式﹐为针点﹑侧针点﹑侧边状﹑锥型状等。
D.顶出方式﹕1.PIN顶出﹐需使用DME规范(依不同客户决定)。
2.顶针成品面有形状时﹐需做方向性之定位。
3.顶出环(特别注意打水环之拔模斜度)或顶出块。
E. 定位块X 4﹕于公母模板360度/4﹐加长方型之定位块﹐增加基准面之精度(材质:SKD-61)F. 模仁方式﹕1.锁公母模仁之螺丝﹐设计时愈多愈好﹐且需平均分配﹐使模仁与模座接触面更密合﹐锁螺丝时需封称锁入﹐且扭力一致。
2.公母模仁均须有卡入模座之定位梢。
3.所有insert之模仁形状为圆形时需做定位﹐且只能单方向组装﹐避免组装时方向错误。
G. 4支导柱需有1pcs做偏心﹐X﹑Y轴各偏10mm。
H. 模具的螺丝孔及螺丝﹐须为DME的公制规范。
I. 回位销封边要有耐顶板﹐材质为TDAC+氮化处理。
J. 若有斜销及滑块﹐三面需加耐磨板﹐且必须有油槽(材质﹕TDAC+氮化处理)。
K, 需安装计数器﹐INSERT的型式。
L. 模具的长﹑宽﹑高﹑定位环与KO孔﹐需配合客户的机台尺寸。
O. 模具上需有放电加工之指示箭头。
P. Name Plate ﹑箭头﹑锁模器﹑Part No.﹑日期章﹑穴号﹑回收章﹑计数器…等﹐需标示于结构图上。
Q. 模具出货时箭头需喷黄漆﹐锁模块需喷红漆。
R. 模具需强制回位时﹐需于模脚的箭头下方﹐贴强制回位铭板。
高光无痕注塑技术

高光无痕注塑成型技术高光无痕注塑成型是近年来在注塑行业中快速发展的一种新型技术。
该技术采用高光泽的塑料材料,使用精密的高光模具,利用先进的模温控制系统实现动态的温度控制,以克服表面流痕和熔接痕等不良缺陷,使产品表面达到高光亮的无痕镜面效果,提高产品强度和质量;同时,速冷可大幅缩短注射周期,提高生产效率;产品无需后续的喷涂加工,保护环境的同时有效降低了成本,是一种绿色制造技术。
广泛应用于音响等视听电器的面板、平板电视、液晶显示器、洗衣机、空调、汽车内外饰件、车灯、光学仪器等家电、汽车、通讯、医疗等行业。
高光无痕注塑成型技术采用特殊的速冷速热温控设备,在注射时快速且均匀地把模具表面加热到指定的温度(达到甚至超过塑料的粘流态温度),使物料始终保持粘流态,几乎没有冻结层,这样就会形成没有熔接线、表面良好的成型品;而在冷却时能快速转换为急剧冷却来缩短成型周期,解决翘曲、缩水问题,这就是高光无痕注射成型的技术原理。
其控制过程如图1所示。
模貝急速加热〔如I2&T!>图1:高光注塑的控制过程高光无痕注塑的技术关键点在于模温控制系统、高光泽塑料材料和高光注塑模具三方面。
(1)先进的模温控制系统模温控制系统是高光注塑成型最关键的技术,其设备由高速制热装置、快速冷却装置、控制装置组成,并能够和注塑机信号互锁,实现闭环控制。
按加热方式不同,可分为蒸汽式、电热式、热水式、高油温式和感应加热式模温控制技术,而目前使用较多的是蒸汽式和电加热式两种温控技术:①蒸汽快速模温技术:简称蒸汽模,模具的加热通过高压蒸汽实现,模具表面最高温度达到160°C甚至更高。
冷却时快速转换成低温水对模具进行冷却。
该技术需要锅炉快速产生足够量的蒸汽,但由于生产过程中蒸汽不可循环利用,致使其运行成本较高。
在2005年韩国三星电子开始使用该技术生产LCD液晶平板电视外壳。
(可否不要?)②电加热的快速模温技术:典型的为韩国NADA公司的E-MOLD(ElectricityMold)技术。
高光无痕注塑模具设计要点和模具抛光保养,高光无痕注塑的原理是什么? ...

高光无痕注塑模具设计要点和模具抛光保养,高光无痕注塑的原理是什么? ...目前,绝大部分的家用电器外观零部件都是注塑成型得到的。
在注塑过程中,易出现熔接痕、气痕、变形等缺陷;高光无痕模具能够解决上述缺陷。
下面我们就一起来看看高光无痕注塑模具设计十大要素。
一高光无痕注塑的原理1.温度较高模具成型对温度要求较高(一般为80℃-130℃左右),在注塑转入保压后改用冷却水,使模具温度降至60-70℃。
较高的模温下保压成型有利于消除熔接线、流痕、产品内应力等缺陷。
因此模具在工作时需进行加热处理,为了防止热量损失,通常都会在定模侧加隔热板。
2.模腔表面极度光亮(一般为镜面2级或更高)高光模具生产出的产品可以直接用于装机(装配),无需做任何表面处理。
因此它对模具钢材及塑胶材料的要求都很高。
3.热流道系统的热喷咀较多每个热喷咀必须带封针且有独立的气道,通过电磁阀及时间继电器等进行单独控制,实现分时进胶,从而达到控制甚至消除熔接痕的目的,控制方式复杂。
4.加热方式模具加热的方式通常有水蒸气(热水)加热和电热棒(管)加热两种。
水蒸气(热水)加热方式是通过特定的温控机在注塑过程中给模具输入蒸气(热水),从而使模具快速升温;在注塑完后用冷水冷却模具,使模具快速降温。
电加热的方式与水加热温控机,在原理上是一样的,就是热源不一样,电加热是二次能源,水加热是三次能源,按原理来说电加热能源损耗少,利用率高、节能效益好。
使用方便、所以说:如果是平板(面)产品还是采用电加热方式实慧。
图:水蒸汽加热图:加热棒加热二模具材料1 .产品表面普通要求的模具材料可用:NK80(日本大同)等;2.高光要求材料选用:S136H(瑞典)、CEANA1(日本)等;3.NK80可不用淬火处理;S136H应在粗加工后淬火至52度;CEANA1本身具备42度也不需要淬火处理(建议用此钢材,因不影响后续加工或改动);4.德国葛利兹品牌中也有不错的选择:CPM40/GEST80图高光模具三模具水道设计1.水道孔径大小设计水道采用5-6mm大小的孔径;水嘴用1/8或3/8的牙(模具侧),另一侧用3/4英制螺纹(老式接法);管件材料用不锈钢管;现在我们改成一进一出,分流口最好是做在模具内,接口采用能径用DN25连接,这样热能损耗少,操作方便、接口方便。
免喷涂注塑成型-高光无痕模具设计制造经验规范

1、高光急冷急热模采用高温蒸气,在模具上做均恒的加温通道,当注塑机合 模后吹入高温蒸气,把模具型腔温度提高到设定值(一般为80°~130°左右), 然后开始给模型注胶,在注塑机完成保压转入冷却后,开始注冷水,模温降到 (60°~70°度)后,开模,再向模具吹入空气把冷水吹走,完成整个注塑过程。
四、设计重点:隔热系统
1、模具定模镶芯或动模镶芯四面要做到掏空处理;模框与镶芯要有一定的间隙(视模具 材料的热膨胀系数,单面1mm)。防止模框膨胀,以减少模芯于模框的接触面,做到使 热能损耗最小化;模芯与模框的锁定采用斜契式或其它类似方式,前端采用隔热效果明 显的粉尘树脂或其它材料(如石棉板)。 2、模框与镶芯的详细结构,模框的冷却水非常重要,为防止模仁中的热能传至模框, 要在靠近导柱位臵,上下排布一圈运水。?? 3、导套运动部位尽可能采用石墨材料或者把导柱前端避空处理,配合处只要保证 25mm长度就足够了;
二、高光模温机设备厂家
高光模温机1 (宁波捷信特)
高光模温机2 (北京中拓)
三、高光 产品案例分享
AP31上饰板面板
材质:高光PC
钢材:型腔ASTM-VIP(斯堪纳),预硬HRC40-44
尺寸ห้องสมุดไป่ตู้239*409*78
型芯1.2738 (布德鲁斯),预硬HRC29-33
重量:165g
四、设计重点:产品分析要点 高光模具对产品结构要求很严格,越光亮的产品对光的折射效果越敏感,表面稍 有缺陷很快就会被发现,因此如何解决缩水问题是高光产品的首要问题。 一般PC或PC+ABS材料的产品筋位厚度不超过主体胶位厚度的0.5倍便不会缩水, 或者说缩水较小不易被发现,可忽略不计。但对高光产品而言,这样的要求远远不够, 还需将产品筋位的厚度减小到不超过主体胶位厚度的1/3,对于螺丝柱位还必须做火山 口式斜顶结构。
高光无痕模具设计要点

高光无痕模具设计要点一、原理:1、模具成型对温度要求较高(一般为80°~130°左右),在注塑转入保压后改用冷却水,使模具降温至60°~70°度。
在较高的模温下保压成型有利于消除熔接痕、流痕、产品内应力等缺陷。
因此模具在工作时需进行加热处理,为了防止热量损失,通常都会在定模侧加树脂隔热板。
2、模腔表面极度光亮(一般为镜面2级或更高)。
高光模具生产出的产品可以直接用于装机,无需做任何表面处理。
因此它对模具钢材及塑胶材料的要求都很高。
3、热流道系统的热咀较多。
每个热咀必须带封针且有独立的气道,通过电磁阀及时间继电器等进行单独控制,实现分时进胶,从而达到控制甚至消除熔接痕的目的。
4、模具加热的方式通常有水蒸汽加热(见图1)和加热棒加热(见图2)两种。
水蒸汽加热方式是通过特定的模温机在注塑过程中通过模具通蒸汽,从而使模具快速升温;在注塑完后改通常温水(或者冰水)使模具快速降温。
加热棒加热方式是在注塑过程中通过在内模料里面加加热棒使模具快速升温;在注塑完成后通过内模料里面的运水(常温水或者冰水)或者叠层模料底部的铝材(铝材里面通运水)使模具温度快速降温。
(图1)(图2)二、模具材料(一)产品表面普通要求的模具材料可用NK80(日本大同);(二)高光要求的产品选用S136H(瑞典)、CEANA1(日立);(三)NK80可不用淬火处理;S136应在粗加工后淬火至52度;CEANA1号本身具备42度也不需要淬火处理(建议用此材料,因不影响后续加工或改动);(四)德国葛利兹品牌中也有不错的选择:CPM40\GEST80三、模具水道设计(一)水道采用5mm-6mm大小的孔;水嘴用1\8或3\8的牙(模具侧),另一侧用3\4英制螺纹;管件材料用不锈钢管;(二)水道一侧离产品面最近不低于5mm-6mm;水道平行产品面且均匀排布(原则中心距15mm分布,);热电偶应设计在两水道中间,深度在50mm左右;且每套模具的PT100是一配一的,保持它的精确度,埋在模具模仁内,与热流道的热电偶一样,用线连接到模具外侧,转接插座,PT100要有对应的插头与其对接。
注塑模具设计规程
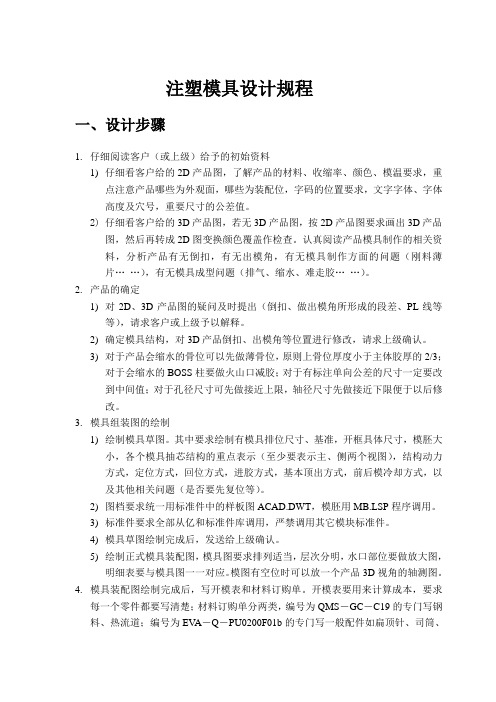
注塑模具设计规程一、设计步骤1.仔细阅读客户(或上级)给予的初始资料1)仔细看客户给的2D产品图,了解产品的材料、收缩率、颜色、模温要求,重点注意产品哪些为外观面,哪些为装配位,字码的位置要求,文字字体、字体高度及穴号,重要尺寸的公差值。
2)仔细看客户给的3D产品图,若无3D产品图,按2D产品图要求画出3D产品图,然后再转成2D图变换颜色覆盖作检查。
认真阅读产品模具制作的相关资料,分析产品有无倒扣,有无出模角,有无模具制作方面的问题(刚料薄片……),有无模具成型问题(排气、缩水、难走胶……)。
2.产品的确定1)对2D、3D产品图的疑问及时提出(倒扣、做出模角所形成的段差、PL线等等),请求客户或上级予以解释。
2)确定模具结构,对3D产品倒扣、出模角等位置进行修改,请求上级确认。
3)对于产品会缩水的骨位可以先做薄骨位,原则上骨位厚度小于主体胶厚的2/3;对于会缩水的BOSS柱要做火山口减胶;对于有标注单向公差的尺寸一定要改到中间值;对于孔径尺寸可先做接近上限,轴径尺寸先做接近下限便于以后修改。
3.模具组装图的绘制1)绘制模具草图。
其中要求绘制有模具排位尺寸、基准,开框具体尺寸,模胚大小,各个模具抽芯结构的重点表示(至少要表示主、侧两个视图),结构动力方式,定位方式,回位方式,进胶方式,基本顶出方式,前后模冷却方式,以及其他相关问题(是否要先复位等)。
2)图档要求统一用标准件中的样板图ACAD.DWT,模胚用MB.LSP程序调用。
3)标准件要求全部从亿和标准件库调用,严禁调用其它模块标准件。
4)模具草图绘制完成后,发送给上级确认。
5)绘制正式模具装配图,模具图要求排列适当,层次分明,水口部位要做放大图,明细表要与模具图一一对应。
模图有空位时可以放一个产品3D视角的轴测图。
4.模具装配图绘制完成后,写开模表和材料订购单。
开模表要用来计算成本,要求每一个零件都要写清楚;材料订购单分两类,编号为QMS-GC-C19的专门写钢料、热流道;编号为EV A-Q-PU0200F01b的专门写一般配件如扁顶针、司筒、弹弓、唧咀斜、导柱等。
高光无痕注塑模具设计规范

高光无痕注塑模具设计制造规范一、高光无痕注塑的原理:1、模具成型对温度要求较高(一般为80°~130°左右),在注塑转入保压后改用冷却水,使模具降温至60°~70°度。
在较高的模温下保压成型有利于消除熔接痕、流痕、产品内应力等缺陷。
因此模具在工作时需进行加热处理,为了防止热量损失,通常都会在定模侧加树脂隔热板。
2、模腔表面极度光亮(一般为镜面2级或更高)。
高光模具生产出的产品可以直接用于装机,无需做任何表面处理。
因此它对模具钢材及塑胶材料的要求都很高。
3、热流道系统的热咀较多。
每个热咀必须带封针且有独立的气道,通过电磁阀及时间继电器等进行单独控制,实现分时进胶,从而达到控制甚至消除熔接痕的目的。
4、模具加热的方式通常有水蒸汽加热(见图1)和加热棒加热(见图2)两种。
水蒸汽加热方式是通过特定的模温机在注塑过程中通过模具通蒸汽,从而使模具快速升温;在注塑完后改通常温水(或者冰水)使模具快速降温。
加热棒加热方式是在注塑过程中通过在内模料里面加加热棒使模具快速升温;在注塑完成后通过内模料里面的运水(常温水或者冰水)或者叠层模料底部的铝材(铝材里面通运水)使模具温度快速降温。
(图1)(图2)二、模具材料(一)产品表面普通要求的模具材料可用NK80(日本大同);(二)高光要求的产品选用S136H(瑞典)、CEANA1(日立);(三)NK80可不用淬火处理;S136应在粗加工后淬火至52度;CEANA1号本身具备42度也不需要淬火处理(建议用此材料,因不影响后续加工或改动);(四)德国葛利兹品牌中也有不错的选择:CPM40\GEST80三、模具水道设计(一)水道采用5mm-6mm大小的孔;水嘴用1\8或3\8的牙(模具侧),另一侧用3\4英制螺纹;管件材料用不锈钢管;(二)水道一侧离产品面最近不低于5mm-6mm;水道平行产品面且均匀排布(原则中心距15mm分布,);热电偶应设计在两水道中间,深度在50mm左右;且每套模具的PT100是一配一的,保持它的精确度,埋在模具模仁内,与热流道的热电偶一样,用线连接到模具外侧,转接插座,PT100要有对应的插头与其对接。
- 1、下载文档前请自行甄别文档内容的完整性,平台不提供额外的编辑、内容补充、找答案等附加服务。
- 2、"仅部分预览"的文档,不可在线预览部分如存在完整性等问题,可反馈申请退款(可完整预览的文档不适用该条件!)。
- 3、如文档侵犯您的权益,请联系客服反馈,我们会尽快为您处理(人工客服工作时间:9:00-18:30)。
高光无痕注塑模具设计规范1、模具成型温度较高(一般为80~130度左右)。
在较高的模温下保压成型有利于消除熔接痕、流痕、产品内应力等缺陷。
因此模具在工作时需进行加热处理,为了防止热量损失,通常都会在定模侧加树脂隔热板。
2、模腔表面极度光亮(一般为镜面2级或更高)。
高光模具生产出的产品可以直接用于装机,无需做任何表面处理。
因此它对模具钢材及塑胶材料的要求都很高。
3、热流道系统的热咀较多。
每个热咀必须带封针且有独立的气道,通过电磁阀及时间继电器等进行单独控制,实现分时进胶,从而达到控制甚至消除熔接痕的目的。
二、模具加热的方式通常有水蒸汽加热(见图1)和加热棒加热(见图2)两种。
水蒸汽加热方式是通过特定的模温机在注塑过程中通过模具通蒸汽,从而使模具快速升温;在注塑完后改通常温水(或者冰水)使模具快速降温。
加热棒加热方式是在注塑过程中通过在内模料里面加加热棒使模具快速升温;在注塑完成后通过内模料里面的运水(常温水或者冰水)或者叠成模料底部的铝材(铝材里面通运水)使模具温度快速降温。
(图1)(图2)一、 模具材料:(一) 产品表面普通要求的模具材料可用NK80(日本大同);(二) 高光要求的产品选用S136H(瑞典)、CEANA1(日立);(三) NK80可不用淬火处理;S136应在粗加工后淬火至52度;CEANA1号本身具备42度也不需要淬火处理(建议用此材料,因不影响后续加工或改动);(四) 德国葛利兹品牌中也有不错的选择:CPM40\GEST80 二、 模具水道设计:(一) 水道采用5mm-6mm大小的孔;水嘴用1\8或3\8的牙(模具侧),另一侧用3\4英制螺纹;管件材料用不锈钢管;(二) 水道一侧离产品面最近不低于5mm-6mm;水道平行产品面且均匀排布(原则中心距15mm分布,);热电偶应设计在两水道中间,深度在50mm左右;(三) 模具水道必须设计在模具上下侧或后侧;操作侧不允许有水道出口或水管排布,以烫伤及人员。
(四) 模具进出水嘴处采用分流板设计,水热模温控制系统只有二进二出的管道,以减少过多的水管连接,减少热能不必要的损耗;且达到安全与节能的目的。
(五)堵头为确保不漏气漏水,需要先用铜堵然后再用锥度喉牙加耐高温胶密封;高光模具对冷却水道的排布比较讲究,好的水道排布不仅可以大大提高注塑效率,而且在改善产品质量方面也起到重要作用。
高光模具的水道不仅要均匀而且必须要充分,这样通过模温机就可以很容易达到所要求的温度;同时,采用加长水管直接将模芯运水引出而不采用密封圈,这样可防止模具长期在高温下作业,致使密封圈老化,也可降低许多模具的维修成本。
值得一提的是,高光模具的运水管必须采用能耐高温250度、高压16公斤/兆帕的油管,以防高温高压下水管爆裂。
对于圆型产品采用环型运水;对于长条型产品采用平行运水;对于高度落差大的产品采用水井形式;对于异形产品采用与产品外型一至的三维运水。
三、 模具隔热系统:(一) 模具定模镶芯或动模镶芯四面要做掏空处理:模框与镶芯要有一定的间隙(视模具材料的热膨胀系数,单面1mm),防止模框膨胀,以减少模芯于模框的接触面,有效使用热能;模芯于模框的锁定采用斜契方式或其他类似方式,前端采用隔热效果明显的粉尘树脂或其他材料。
(二) 模框与镶芯的详细结构见附图1和附图2;(三) 导套运动部位尽可能采用石墨材料;另模框要分布一条至二条冷却水道,确保模框的冷却。
四、模具浇口设计:模具浇口设计要尽可能地减少熔接线,并有利于排气及减少剪切。
对采用水加热模温机的模具,浇口尺寸要开得比较大,并且尽量采用大胶口进胶.在不影響產品機能及成型效率下, 澆口應盡量縮短其長度、深度、寬度。
若澆口過小, 則易造成充填不足(短射)、收縮凹陷、熔接線等外觀上的缺陷, 且成型收縮會增大。
若澆口過大, 則澆口周圍產生過剩的殘餘應力, 導致產品變形或破裂, 且澆口的去除加工困難等。
最好選用一個澆口﹐除非流動比超過實際的極限。
樹脂的流動長度曲線圖﹐將會提供在某一確定的成型條件下材料的流動長度。
多個澆口經常會產生縫合線與融合線。
除了長的﹑窄的成品﹐采用單澆口將會確保更一致的材料﹑溫度﹑保壓分布﹐以及更好的配向的效果。
五、加热棒高光模设计:(一)冷却系统中运水不要有积水,影响升温和降温速度(二)在进胶口处上下侧要有运水,运水孔一般为∅6;两运水孔中心距离为15mm-20mm;加热棒壁离产品表面距离为5mm,两加热棒之间的中心距离为20mm;运水壁于加热棒壁距离为6-8mm。
(三) 内模腔运水可以用耐高温密封圈密封或者采用硬密封方式;(四)加热棒直径为∅4.92,模具设计时∅5,装配加热棒前先用∅5的顶针磨刃口把加热棒孔的毛刺去掉;六、高光对产品的要求高光模具对产品结构要求很严格,越光亮的产品对光的折射效果越敏感,表面稍有缺陷很快就会被发现,因此如何解决缩水问题是高光产品的首要问题。
一般的产品筋位厚度不超过主体胶位厚度的0.6倍便不会缩水,或者说缩水较小不易被发现,可忽略不计。
但对高光产品而言,这样的要求远远不够,还需将产品筋位的厚度减小到不超过主体胶位厚度的1倍,对于螺丝柱位还必须做火山口.七、高光模对塑胶材料的选择目前常用高光塑胶材料一般是HIPS和ABS+PC。
作为常用的两种机壳材料,尽管ABS+PC的成本会大一些,但成型出的产品在耐冲击性、表面光泽度以及硬度方面都比HIPS 好,所以在生产高光产品时,通常选用的是高光ABS材料。
ABS属于无定形聚合物,无明显熔点。
由于其牌号品级繁多,在注塑过程中应按品级的不同制订合适的工艺参数,一般在160℃以上,270℃以下即可成型。
在成型过程中、ABS热稳定性较好,可供选择的范围较大,不易出现降解或分解。
且ABS的熔体粘度适中,其流动性比聚本乙烯(PS)、聚碳酸酯等要好,而且熔体的冷却固化速度比较快,一般在5~15秒内即可冷固。
ABS的流动性与注射温度和注射压力都有关系,其中注射压力稍敏感些。
为此,在成型过程中可从注射压力入手,以降低其熔体粘度,提高充模性能。
ABS因组分的不同,吸水及粘附水的性能各异,其表面粘附水及吸水率在0.2%~0.5%,有时可达0.3%~0.8%之间,为了得到较为理想的制品,在成型前作干燥处理,使含水量降至0.1%以下。
否则制件表面将会出现气泡、银丝等疵病。
通常塑胶材料需要加20%金属粉(深圳族兴公司)提高高光效果八、 模具的抛光与保养:在塑料模具加工中所说的抛光与其他行业中所要求的表面抛光有很大的不同,严格来说,模具的抛光应该称为镜面加工。
它不仅对抛光本身有很高的要求并且对表面平整度、光滑度以及几何精确度也有很高的标准。
表面抛光一般只要求获得光亮的表面即可。
镜面加工的标准分为四级:AO=Ra0.008μm,A1=R a0.016μm,A3=Ra0.032μm,A4=Ra0.063μm,由于电解抛光、流体抛光等方法很难精确控制零件的几何精确度,而化学抛光、超声波抛光、磁研磨抛光等方法的表面质量又达不到要求,所以精密模具的镜面加工还是以机械抛光为主。
(一)机械抛光基本程序 要想获得高质量的抛光效果,最重要的是要具备有高质量的油石、砂纸和钻石研磨膏等抛光工具和辅助品。
最重要的还有抛光的工作环境,要求是无尘车间。
而抛光程序的选择取决于前期加工后的表面状况,如机械加工、电火花加工,磨加工等等。
机械抛光的一般过程如下: (1)粗抛 经铣、电火花、磨等工艺后的表面可以选择转速在35000-40000rpm的旋转表面抛光机或超声波研磨机进行抛光。
常用的方法有利用直径Φ3mm、WA#400的轮子去除白色电火花层。
然后是手工油石研磨,条状油石加煤油作为润滑剂或冷却剂。
一般的使用顺序为# 180~#240~#320~#400~#600~ #800~#1000。
许多模具制造商为了节约时间而选择从#400开始。
(2)半精抛 半精抛主要使用砂纸和煤油。
砂纸的号数依次为:#400~#600~#8 00~#1000~#1200~#1500。
实际上#150 0砂纸只用适于淬硬的模具钢(52HRC以上),而不适用于预硬钢,因为这样可能会导致预硬钢件表面烧伤。
(3)精抛 精抛主要使用钻石研磨膏。
若用抛光布轮混合钻石研磨粉或研磨膏进行研磨的话,则通常的研磨顺序是9μm(#1800)~6μm(#3000)~3μm (#8000)。
9μm的钻石研磨膏和抛光布轮可用来去除#1200和#1500号砂纸留下的发状磨痕。
接着用粘毡和钻石研磨膏进行抛光,顺序为1μm(#14000)~1/2μm(#60000)~1/4μm(#100000)。
精度要求在1μm以上(包括1μm)的抛光工艺在模具加工车间中一个清洁的抛光室内即可进行。
若进行更加精密的抛光则必需一个绝对洁净的空间。
灰尘、烟雾,头皮屑和口水沫都有可能报废数个小时工作后得到的高精密抛光表面。
(二)机械抛光中要注意的问题 用砂纸抛光应注意以下几点:(1)用砂纸抛光需要利用软的木棒或竹棒。
在抛光圆面或球面时,使用软木棒可更好的配合圆面和球面的弧度。
而较硬的木条像樱桃木,则更适用于平整表面的抛光。
修整木条的末端使其能与钢件表面形状保持吻合,这样可以避免木条(或竹条)的锐角接触钢件表面而造成较深的划痕。
(2)当换用不同型号的砂纸时,抛光方向应变换45°~90°,这样前一种型号砂纸抛光后留下的条纹阴影即可分辨出来。
在换不同型号砂纸之前,必须用100%纯棉花沾取酒精之类的清洁液对抛光表面进行仔细的擦拭,因为一颗很小的沙砾留在表面都会毁坏接下去的整个抛光工作。
从砂纸抛光换成钻石研磨膏抛光时,这个清洁过程同样重要。
在抛光继续进行之前,所有颗粒和煤油都必须被完全清洁干净。
(3)为了避免擦伤和烧伤工件表面,在用#1200和#1500砂纸进行抛光时必须特别小心。
因而有必要加载一个轻载荷以及采用两步抛光法对表面进行抛光。
用每一种型号的砂纸进行抛光时都应沿两个不同方向进行两次抛光,两个方向之间每次转动45°~90°。
(三)钻石研磨抛光应注意以下几点: (1)这种抛光必须尽量在较轻的压力下进行特别是抛光预硬钢件和用细研磨膏抛光时。
在用#8000研磨膏抛光时,常用载荷为100~200g/cm2,但要保持此载荷的精准度很难做到。
为了更容易做到这一点,可以在木条上做一个薄且窄的手柄,比如加一铜片;或者在竹条上切去一部分而使其更加柔软。
这样可以帮助控制抛光压力,以确保模具表面压力不会过高。
(2)当使用钻石研磨抛光时,不仅是工作表面要求洁净,工作者的双手也必须仔细清洁。
(3)每次抛光时间不应过长,时间越短,效果越好。
如果抛光过程进行得过长将会造成"橘皮"和"点蚀"。