铸件缩孔
铸件缩孔缩松产生的原因

铸件缩孔缩松产生的原因
一、金属铸件缩孔缩松的原因
1、模具质量不合格:模具的表面没有经过预处理,工作表面毛糙度不够,加工精度不高,导致熔模渗入的位置不正确,从而影响铸件缩孔的精度。
2、砂芯质量不合格没有经过预处理或抛光处理,表面毛糙度不均,加工精度低,砂芯内部出现裂纹,导致不同部位的造型不稳定,从而影响铸件缩孔的精度。
3、工艺条件不合理:模具配套不当,熔模温度过高或过低,模具保温不足,充型压力不足,熔模渗入缓慢,从而影响铸件缩孔的精度。
4、冷却不当:铸件出模后,冷却时间过长或过短,容易出现开裂现象,从而影响铸件缩孔的精度。
二、金属铸件缩孔缩松的改善措施
1、严格模具质量:采用高强度的整体钢,并且经过精密加工,表面经过研磨抛光,以保证熔模渗入的位置准确,从而提高铸件缩孔的精度。
2、严格砂芯质量:采用高质量的砂芯,经过彻底的预处理,能够保证砂芯表面毛糙度均匀,加工精度高,避免出现裂纹,从而确保缩孔的精度。
3、调整熔模温度:严格控制熔模的温度,熔模温度过高可以导致金属分子值过大,熔态液体容易流失。
3.2.2 缩孔、缩松的形成及防止方法

缩孔、缩松的形成及防止方法副教授:陈云铸件中的缩孔与缩松液态金属在铸型内凝固过程中,由于液态收缩和凝固收缩导致体积缩小,若其收缩得不到补充,就在铸件最后凝固的部分形成孔洞。
大而集中的孔洞称为缩孔,细小而分散的孔洞称为缩松。
(a)铝合金缩孔、缩松(b)金相显微镜下缩松(c)扫描电镜下缩松一、缩孔的形成纯金属、共晶成分和凝固温度范围窄的合金,浇注后在型腔内是由表及里的逐层凝固。
在凝固过程中,如得不到合金液的补充,在铸件最后凝固的地方就会产生缩孔。
缩孔形成的条件:铸件呈逐层凝固方式凝固,成分为纯金属或共晶成分的合金。
缩孔产生的基本原因:是合金的液态收缩和凝固收缩值大于固态收缩值,且得不到补偿。
缩孔产生的部位在铸件最后凝固区域,如壁较厚大的上部或铸件两壁相交处,这些地方称为热节。
热节位置可用画内接圆的方法确定。
用画内切圆法确定缩孔位置二、缩松的形成铸件最后凝固的收缩未能得到补充,或者结晶温度范围宽的合金呈糊状凝固,凝固区域较宽,液、固两相共存,树枝晶发达,枝晶骨架将合金液分割开的小液体区难以得到补缩所致。
缩松形成的条件:铸件主要呈糊状凝固方式凝固,成分为非共晶成分或有较宽结晶温度范围的合金。
形成缩松的基本原因:是合金的液态收缩和凝固收缩值大于固态收缩值。
缩松一般出现在铸件壁的轴线区域、冒口根部、热节处,也常分布在集中缩孔的下方。
三、影响缩孔和缩松形成的因素1、合金成分结晶温度范围越小的合金,产生缩孔的倾向越大;结晶温度范围越大的合金,产生缩松的倾向越大。
铁碳合金成分和体积收缩的关系V总—总体积收缩容积;V孔—缩孔容积;V松—缩松容积2、浇注条件提高浇注温度时,合金的总体积收缩和缩孔倾向增大。
浇注速度很慢或向冒口中不断补浇高温合金液,使铸件液态和凝固收缩及时得到补偿,铸件总体积收缩减小,缩孔容积也减小。
V 总—总体积收缩容积;V 孔—缩孔容积;V 松—缩松容积铁碳合金成分和体积收缩的关系3、铸型材料铸型材料对铸件冷却速度影响很大 。
熔模铸造产品缩孔问题的理解与分析

熔模铸造产品缩孔问题的理解与分析王在现代工业领域中,熔模铸造技术以其无与伦比的精度和复杂程度,广泛应用于各类精密零件的制造。
然而,随着生产技术的持续进步,我们面临着一系列挑战。
其中,熔模铸造产品的缩孔及缩松问题显得尤为突出。
这是一个充满复杂性的问题,需要我们深入理解其产生的机理,并找出有效的解决方案。
首先,我们要理解什么是熔模铸造产品的缩孔。
在熔模铸造过程中,由于金属液体在冷却过程中体积收缩,会在铸件内部形成空洞,这就是我们所说的缩孔。
这些缩孔不仅会影响铸件的外观质量,更重要的是,它们会降低铸件的机械性能,甚至可能导致铸件的破裂。
那么,为什么会出现缩孔呢?原因主要有两个方面。
一方面,是由于金属液体在冷却过程中的体积收缩,这是物理规律,无法避免。
另一方面,是由于铸造工艺的问题。
例如,如果铸造速度过快,金属液体在壳模中的冷却时间不足,钢水无法补缩就会导致缩孔的产生。
那么,如何解决这个问题呢?我认为,主要可以从以下几个方面入手:首先,优化铸造工艺。
从产品结构分析,确认产品热节,设置合理的浇口大小以及组树方式,热节-浇口-流道-三者的比例;通过调整铸造速度以及浇注温度,延长金属液体在壳模中的冷却时间,可以有效减少缩孔的产生。
控制液态金属的流动速度和冷却时间,以确保铸件内部结构的稳定性和外观的完整性。
其次,改变以往陈旧观念,尽可能的降低壳模厚度,在产品制壳时应当分析产品在制壳过程中,会不会产生积浆积砂情况,这些问题在制壳过程中要去避免,积浆积砂会导致产品散热不好,出现缩孔及缩松现象,同时壳模厚度减薄利于产品散热,同时也能避免其他铸造问题;此外,通过调整铸造速度以及浇注温度,延长金属液体在壳模中的冷却时间,可以有效减少缩孔的产生。
控制液态金属的流动速度和冷却时间,以确保铸件内部结构的稳定性和外观的完整性。
最后,采用定向凝固技术。
通过改变铸件的凝固方向(如贴保温岩棉、浇注前壳模蘸水、浇注后局部浇水降温等方式),可以使金属液体在凝固过程中产生的缩孔集中在铸件的某一部位,从而减少缩孔对铸件性能的影响。
铸铁件缩松、缩孔、凹陷缺陷的原因分析与防止方法
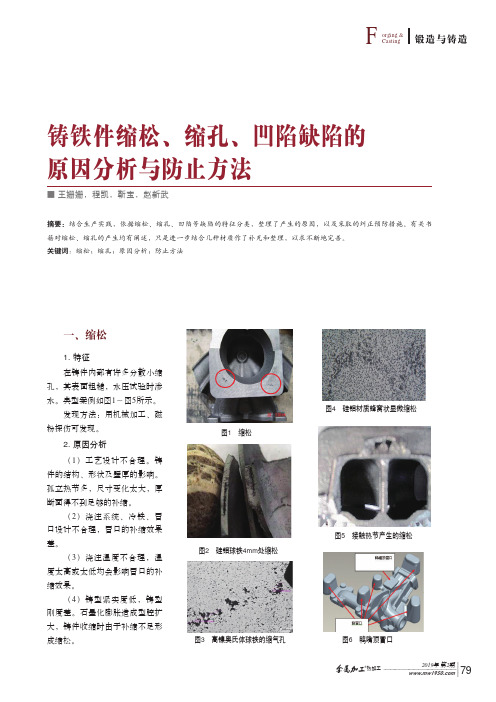
2019年第2期热加工79F锻造与铸造orging &Casting铸铁件缩松、缩孔、凹陷缺陷的原因分析与防止方法■王姗姗,程凯,靳宝,赵新武摘要:结合生产实践,依据缩松、缩孔、凹陷等缺陷的特征分类,整理了产生的原因,以及采取的纠正预防措施。
有关书籍对缩松、缩孔的产生均有阐述,只是进一步结合几种材质作了补充和整理,以求不断地完善。
关键词:缩松;缩孔;原因分析;防止方法一、缩松1. 特征在铸件内部有许多分散小缩孔,其表面粗糙,水压试验时渗水。
典型案例如图1~图5所示。
发现方法:用机械加工、磁粉探伤可发现。
2. 原因分析(1)工艺设计不合理。
铸件的结构、形状及壁厚的影响。
孤立热节多,尺寸变化太大,厚断面得不到足够的补缩。
(2)浇注系统、冷铁、冒口设计不合理,冒口的补缩效果差。
(3)浇注温度不合理,温度太高或太低均会影响冒口的补缩效果。
(4)铸型紧实度低,铸型刚度差。
石墨化膨胀造成型腔扩大,铸件收缩时由于补缩不足形成缩松。
图1 缩松图2 硅钼球铁4mm处缩松图4 硅钼材质蜂窝状显微缩松图3 高镍奥氏体球铁的缩气孔图5 接触热节产生的缩松图6 鸭嘴顶冒口2019年 第2期 热加工80F锻造与铸造orging &Casting(5)碳、硅含量低,磷含量较高;凝固区间大。
硅钼和高镍球墨铸铁对碳、硅含量和氧化铁液的敏感性特大,铁液严重氧化或碳、硅量低时,易出现显微缩松。
即便在薄壁处也容易出现缩松(见图2、图3、图4)。
(6)孕育不充分,石墨化效果差。
(7)残余镁量和稀土量过高。
钼含量较高时也会增加显微缩松。
(8)浇注速度太快。
(9)炉料锈蚀,氧化铁多。
(10)铁液在电炉内高温停放时间太长,俗称“死铁水”,造成严重氧化。
(11)冲天炉熔炼时底焦太底,风量太大,元素烧损大,铁液严重氧化。
(12)冒口径处形成接触热节产生缩松(见图5)。
(13)压箱铁不够(或箱卡未锁紧,箱带断裂等),浇注后由于涨箱造成缩松。
铸件缩孔和缩松缺陷十点分析

铸件缩孔和缩松缺陷十点分析缩孔和缩松都是铸造生产中常见的铸件缺陷。
缩孔是铸件在冷凝过程中收缩,得不到金属溶液的补充而产生的孔洞,形状不规则,孔壁粗糙,一般位于铸件的热节处。
缩孔和气孔在外表上往往极为相似,经常容易混淆。
一般来说,气孔的内壁是平滑的,而缩孔的内壁则呈枝状结晶的末梢状。
缩松是铸件最后凝固的区域没有得到金属溶液的补缩而形成分散和细小的小孔,常出现在铸件的较厚截面以及厚薄截面交接处或热节点上。
缩松的分布面积要比缩孔大得多,往往隐藏于铸件的内部,有时肉眼察觉不到。
缩孔和缩松在铸件废品中占有较大的比例,必须引起足够的重视,以提高铸件合格率。
笔者结合多年的生产实践经验,谈谈铸件缩孔和缩松的产生原因及其防止措施。
1.铸件和模样设计(1)铸件截面尺寸变化过大。
如果在设计中铸件截面尺寸变化过大,薄截面的冷却速度比相邻厚截面的冷凝速度要快得多,这样就很难实现铸件的顺序凝固,同时也难于进行补缩。
设计时要尽量避免这种情况,否则应采用冷铁,以实现铸件的顺序凝固并利于补缩。
(2)铸件断面过厚,如果没有采取相应措施对其进行补缩,会因补缩不良形成缩孔。
(3)圆角太小。
铸件的凹角圆角半径太小,会导致型砂传热能力降低,凝固速度下降,同时由于该处型砂受热作用强,发气压力大,析出的气体可向未凝固的金属液渗入,导致铸件产生气缩孔。
(4)圆角太大。
圆角太大,则圆角部分就成了厚截面,如果相邻的截面较薄,就难以得到有效的补缩,造成补缩不良2.模样(1)模样或芯盒磨损致使铸件截面减薄,导致铸件截面厚度减薄而妨碍补缩。
(2)模样尺寸不当或模样结构不当,导致铸件截面过厚或过薄。
设计时应注意控制模样的厚度,尽量使邻近较厚截面的薄截面保持最大的厚度。
3.砂箱(1)上箱太浅。
生产中为了节省型砂用量或为了降低砂箱和造型成本而使用高度不够的上箱,这是造成缩松缺陷的常见原因。
上箱太浅,会降低金属液的静压力,以致难以进行补缩,补缩压力不够,会导致产生缩松或缩孔,或二者兼有之。
压铸件螺纹孔处缩孔产生的原因

压铸件螺纹孔处缩孔产生的原因
压铸件螺纹孔处缩孔的产生原因可能有以下几种:
1. 模具设计不合理:模具中螺纹孔的设计、尺寸和形状不合理,导致压力分布不均匀,容易造成局部缩孔。
2. 材料问题:压铸件材料中存在各种夹杂物、气孔等缺陷,当受到压力时,这些缺陷会产生局部应力集中,导致局部缩孔。
3. 压力不均匀:在压力注入过程中,如果压力不稳定或者注入速度不均匀,容易造成螺纹孔处局部缩孔。
4. 组织变化:压铸过程中,材料会受到高温和高压的作用,导致其组织发生变化,如果压力不均匀或者温度不合适,容易产生局部缩孔。
5. 冷却问题:压铸过程中材料的冷却速度也会影响缩孔问题,如果冷却速度过快或者不均匀,容易产生局部缩孔。
综上所述,压铸件螺纹孔处缩孔产生的原因主要与模具设计、材料质量、压力、温度、冷却等因素有关。
铸件产生缩孔和缩松产生的原因及防止措施(音频讲解,实用方便)

铸件产⽣缩孔和缩松产⽣的原因及防⽌措施(⾳频讲解,实⽤⽅便)铸件缩松、缩孔问题防治⽅案来⾃制造⼯业联盟 00:00 10:29
缩孔是集中在铸件上部或最后凝固部位容积较⼤的孔洞
合⾦的液态收缩和凝固收缩愈⼤、浇注温度愈⾼、铸件愈厚,缩孔的容积愈⼤. 缩松是分
散在铸件某区域内的细⼩缩孔
形成原因:铸件最后凝固区域的收缩未能得到补⾜,或因为合⾦呈糊状凝固,被树枝状晶体
分隔开的⼩液体区难以得到补缩所⾄
逐层凝固合⾦,缩松倾向⼩。
糊状凝固合⾦缩松倾向⼤,缩孔倾向⼩。
防⽌缩孔和缩松的措施 1)选择合适的合⾦成分选⽤近共晶成分或结晶温度范围较
窄的合⾦ 2)⼯艺措施顺序凝固原则,获得没有缩孔的致密铸件。
定向凝固就是在铸
件上可能出现缩孔的厚⼤部位通过安放冒⼝等⼯艺措施,使铸件远离冒⼝的部位先凝固,然后
靠近冒⼝部位凝固,最后冒⼝本⾝凝固。
⽬的是铸件各个部位的收缩都能得到补充,⽽将缩孔转移到冒⼝中,最后予以清除措施
1、安放冒⼝
2、在⼯件厚⼤部位增设冷铁。
压铸件缩孔缩松的原因及解决办法
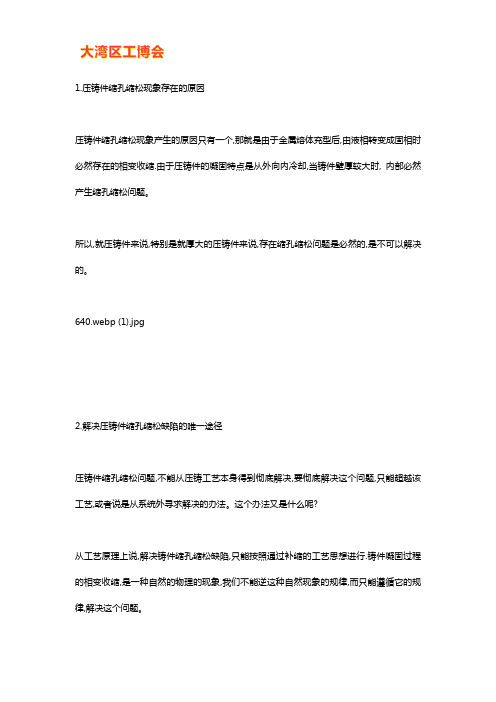
1.压铸件缩孔缩松现象存在的原因压铸件缩孔缩松现象产生的原因只有一个,那就是由于金属熔体充型后,由液相转变成固相时必然存在的相变收缩.由于压铸件的凝固特点是从外向内冷却,当铸件壁厚较大时, 内部必然产生缩孔缩松问题。
所以,就压铸件来说,特别是就厚大的压铸件来说,存在缩孔缩松问题是必然的,是不可以解决的。
640.webp (1).jpg2.解决压铸件缩孔缩松缺陷的唯一途径压铸件缩孔缩松问题,不能从压铸工艺本身得到彻底解决,要彻底解决这个问题,只能超越该工艺,或者说是从系统外寻求解决的办法。
这个办法又是什么呢?从工艺原理上说,解决铸件缩孔缩松缺陷,只能按照通过补缩的工艺思想进行.铸件凝固过程的相变收缩,是一种自然的物理的现象,我们不能逆这种自然现象的规律,而只能遵循它的规律,解决这个问题。
3.补缩的两种途径对铸件的补缩,有两种途径,一是自然的补缩,一是强制的补缩. 要实现自然的补缩,我们的铸造工艺系统中,就要有能实现“顺序凝固”的工艺措施.很多人直觉地以为,采用低压铸造方法就能解决铸件的缩孔缩松缺陷,但事实并不是这么回事.运用低压铸造工艺,并不等于就能解决铸件的缩孔缩松缺陷,如果低压铸造工艺系统没有设有补缩的工艺措施,那么,这种低压铸造手段生产出来的毛坯,也是可能百分之一百存在缩孔缩松缺陷的。
由于压铸工艺本身的特点,要设立自然的“顺序凝固”的工艺措施是比较困难的,也是比较复杂的.最根本的原因还可能是, ”顺序凝固”的工艺措施,总要求铸件有比较长的凝固时间,这一点,与压铸工艺本身有点矛盾。
强制凝固补缩的最大特点是凝固时间短,一般只及”顺序凝固”的四分之一或更短,所以,在压铸工艺系统的基础上,增设强制的补缩工艺措施,是与压铸工艺特点相适应的,能很好解决压铸件的缩孔缩松问题。
4.强制补缩的两种程度挤压补缩和锻压补缩实现铸件的强制补缩可以达到有两种程度.一种是基本的可以消除铸件缩孔缩松缺陷的程度,一种是能使毛坯内部达到破碎晶粒或锻态组织的程度.如果要用不同的词来表述这两种不同程度话,那么,前者我们可以用“挤压补缩”来表达,后者,我们可以用“锻压补缩”来表达。
二、铸件中的缩孔和缩松讲解

§3 铸造内应力、变形和裂纹
Internal Stress,Deformation and Crack of Casting
铸造内应力:铸件冷却时因固态收缩受 阻碍,在铸件内部产生的应力。
一、内应力的形成
类型— 热应力、机械应力 1、热应力
• 热应力的形成 • 形成原因—铸件的壁厚不均匀,冷却和
收缩先后不一致造成内应力。
图2-8 热应力的形成
The formation of Thermal Stress
Internal Stress,Deformation and
Crack of Casting
• 结论:铸件中厚的部分最后冷却,总是 受拉应力,反之,薄的部分受压应力。
普通灰口铸铁缩孔缩松倾向小锡青铜机械应力二铸件的变形与预防deformationitsprevention它会通过适当的变形来减缓自身的内应力趋于一种稳定状态
二、铸件中的缩孔和缩松 Shrinkage void and Porosity
1、缩孔与缩松的形成 (1)缩孔(又称集中缩孔)
• 形成 • 形状:倒锥形 • 形成部位:最后凝固处 • 易形成缩孔的合金:纯金属,共晶成分
的合金→逐层凝固
图2-4 缩孔形成过程
Fig.2-4 The formation of Shrinkage Void
(2)缩松(又称分散缩孔) 形状:宏观缩松—肉眼可见的微小
孔洞; 微观缩松—在显微镜下可见 形成部位:宏观缩松分布在铸件中 心轴线处或缩孔的下方; 形成原因:与糊状凝固有关; 易形成缩松的合金:液相线与固相 线距离大的合金,如锡青铜
例1 T型型材的变形 例2 机架的变形 例3 机床床身
浅谈铸件缩孔缩松产生的原因

浅谈铸件缩孔缩松产生的原因铸件缩孔和缩松是出现在铸件制造过程中的常见缺陷,对铸件的质量和性能产生重要影响。
缩孔和缩松的产生主要有以下几个原因:1.缩孔:缩孔是指铸件中出现内部凹陷或空洞的缺陷。
其主要原因如下:-铸型设计不合理:铸型的收缩系统设计不合理、浇注系统设计不合理、毛坯料和铸型之间的空隙设计不合理等,都会导致金属液在凝固过程中无法顺利填充,从而形成缩孔。
-浇注工艺参数不合理:包括浇注温度过低、浇注速度过快、浇注压力不足等。
这些因素都会影响金属液的流动性和凝固过程,从而产生缩孔。
-快速凝固导致温度梯度大:金属液凝固过程中温度梯度大,会加快金属的凝固速度,导致空洞无法充分填充,形成缩孔。
-毛坯料中夹杂物:毛坯料中的夹杂物如气孔、沙眼等也会导致铸件内部形成缩孔。
2.缩松:缩松是指铸件内部存在小裂纹或局部结构不致密的缺陷。
其主要原因如下:-热应力引起的冷裂纹:在铸造过程中,由于金属液凝固和收缩产生热应力,当应力超过金属的强度时,就会发生冷裂纹,形成缩松。
-毛坯中的气体和夹杂物:毛坯中存在气孔、气泡等夹杂物,会导致铸件内部产生局部脱实和裂纹,形成缩松。
-铸造温度过低:铸造温度过低会导致金属液在凝固过程中形成局部冷凝物,使得金属液无法顺利填充,产生缩松。
-浇注系统设计不合理:浇注系统设计不合理会导致金属液流动不畅,使得铸件内部无法顺利充实,形成缩松。
为防止铸造缺陷的产生,可以采取以下措施:-合理设计铸型:铸型的收缩系统设计要合理,保证金属液顺利充实,并通过改变浇注位置、浇注顺序等因素来减小缩松和缩孔的产生。
-优化浇注工艺参数:要根据具体的铸造材料和结构特点,合理控制浇注温度、浇注速度和浇注压力等参数,以减少缩松和缩孔的产生。
-毛坯清洁处理:在铸造前要对毛坯进行彻底清洁,以排除夹杂物和气泡等缺陷,减少铸件内部缺陷的产生。
-采用适当的热处理工艺:通过热处理来改善铸件内部组织结构,减少缩松和缩孔的产生,提高铸件的力学性能和耐热性能。
简述铸件中缩孔的产生原因及其防止方法

简述铸件中缩孔的产生原因及其防止方法铸件是金属熔化后在模具中冷却凝固成型的工艺,其制作过程中容易产生各种缺陷,其中缩孔是常见的一个问题。
缩孔是指铸件中含有孔隙,并且表面凹陷或凸起的缺陷,严重影响铸件的力学性能。
下面将从铸件中缩孔的产生原因以及防止方法两个方面进行简述。
一、铸件中缩孔的产生原因1.高熔点和低液态温度:某些合金的熔点较高,浆料在浇注过程中凝固速度快,易产生缩孔。
2.铸型材料不合适:铸型材料的选择不合理也会导致缩孔的产生。
比如铸型材料不耐火或热膨胀系数太大,容易损坏或产生内应力,进而引起缩孔。
3.浇注温度过低:浇注温度过低会导致凝固时间过长,浆料在凝固过程中收缩不完全,形成缩孔。
4.浇注速度过快:如果铸件的浇注速度过快,会导致气体无法有效排出,导致缩孔的产生。
5.气体和杂质的存在:铸料中夹杂有气体和杂质,会在凝固过程中形成缩孔。
二、铸件中缩孔的防止方法1.提高浇注温度:适当提高浇注温度可以减缓凝固时间,增加液态时间,有利于气体的排出,减少缩孔的产生。
2.控制浇注速度:合理控制浇注速度,避免过快过慢,以保证气体和杂质顺利排出,并且减少凝固收缩,减少缩孔的产生。
3.选择合适的铸型材料:铸型材料要具有一定的耐火性和热膨胀系数,并且能够充分耐高温应力,避免产生内应力引起缩孔。
4.使用脱气剂:在铸造过程中添加一定比例的脱气剂,能够有效除去铸料中的气体和杂质,降低铸件中气孔和夹杂物的数量。
5.采用真空冶炼和真空注射技术:通过真空冶炼可以减少金属中含气量,降低铸件中气孔的产生。
同时,真空注射技术可以使浆料在铸造过程中迅速排除气体,避免缩孔的产生。
6.优化浇注系统和浇注工艺:设计和优化浇注系统可以改变浇注方式,减少铸件内的气体和杂质,减少缩孔的产生。
7.特殊处理工艺:对于一些特殊的铸件,如大型铸件、厚壁铸件等,可以通过局部预热、冷却措施等特殊处理工艺,改善凝固过程,减少缩孔的产生。
总之,铸件中缩孔的产生是多种因素综合作用的结果,防止缩孔的产生需要从原材料、铸型材料、浇注工艺等多个方面综合考虑,通过优化工艺、控制温度和速度等方式来减少缩孔的发生,保证铸件质量。
铸造缺陷(气孔与缩孔)

铸造缺陷的分类
气孔
铸件内部或表面存在圆形或椭圆形的 孔洞,有时呈集群状分布,气孔的形 成与浇注时气体卷入和凝固时气体析 出有关。
缩孔
铸件在冷却过程中,由于体积收缩而 未能得到足够的金属补充,在铸件内 部形成的空洞或区域,缩孔通常出现 在铸件最后凝固的部位。
02
气孔的形成与控制
气孔的形成原因
材料因素
,导致形成空洞。
浇注系统设计不当,金属液流 动不均匀,局部区域金属液过
早凝固。
铸件结构复杂,厚薄差异大, 导致金属液冷却速度不一致。
浇注时金属液面过低,补缩能 力不足。
缩孔对铸件的影响
缩孔会导致铸件局部厚度减小,降低承载能力。 缩孔会降低铸件的致密度和气密性,影响性能。
缩孔部位容易引起应力集中,降低铸件疲劳强度。 缩孔影响铸件外观质量,可能导致产品不合格。
通过目视或低倍放大镜观察铸件表面,寻找是否 存在气孔和缩孔的迹象。
无损检测
利用射线、超声波、磁粉等无损检测技术对铸件 内部进行检测,确定缺陷的位置和大小。
力学性能测试
对铸件进行拉伸、冲击等力学性能测试,分析其 机械性能是否符合要求。
识别技巧
01
观察表面特征
气孔通常表现为圆形或椭圆形的凸起,而缩孔则表现为不规则的凹陷。
铸造缺陷(气孔与缩孔)
• 引言 • 气孔的形成与控制 • 缩孔的形成与控制 • 气孔与缩孔的检测与识别 • 案例分析
01
引言
铸造缺陷的定义
01
铸造缺陷是指在铸造过程中,由 于各种原因导致铸件内部或表面 出现的不符合技术要求或使铸件 性能下降的区域或点。
02
铸造缺陷的产生与铸造工艺、模 具设计、原材料、操作环境等多 种因素有关。
铸件缩孔与缩松

§2铸件的缩孔和缩松铸件凝结时因液态缩短和凝结缩短使铸件最后凝结部位出现孔洞,容积大而集中的称集中缩孔(缩孔),小而分别的称分别缩孔(缩松)。
一形成机理1缩孔合金性质不一样,缩孔形成的机理各异。
1)凝结过程中无体积膨胀合金如铸钢、白口铸铁、铝合金等。
浇铸后,型壁传热、逐层凝结、液态缩短和凝结缩短大于固态缩短。
如无赔偿,则在最后凝结部位出现缩孔。
2)有体积膨胀的合金(灰铁、球铁)自补缩能力:灰铁共晶凝结过程中,片状石墨尖端在共晶液中优先长大,其产生的体积膨胀绝大多半直接作用在初生奥氏体枝晶或共晶团的液体上,并推进液体经过枝晶间的通道去补缩因为液态和固态缩短所形成的小孔洞。
文档来自于网络搜寻缩前膨胀:石墨长大所产生的膨胀压力经过奥氏体或共晶团最后作用在铸型表面,使型腔扩大的现象。
灰铁的共晶凝结偏向于中间凝结方式,凝结中期已有完整凝结的外壳,能蒙受必定的石墨化膨胀压力,因此其缩前膨胀可忽视不计。
故其产生缩孔的偏向小。
只有当液态缩短和凝结缩短之和大于石墨化膨胀和固态缩短之和才会产生缩孔。
文档来自于网络搜寻球铁共晶凝结呈糊状凝结方式,凝结时期无牢固外壳。
如铸型刚度不够,则使型腔扩大,故球铁缩前膨胀比灰铁大好多。
当球铁液态缩短、凝结缩短和型腔扩大之和大于石墨化膨胀和固态缩短之和时,铸件将产生缩孔。
文档来自于网络搜寻总结:灰铸铁:石墨化膨胀产生的膨胀压力绝大多半直接作用在液体上(共晶团或A枝晶之间的),小部分作用在铸型型壁上。
球铁:石墨化膨胀产生的膨胀压力一小部分直接作用在液体上(共晶团1/3或A枝晶之间的),绝大多半作用在铸型型壁上。
缩松铸件凝结后期,最后凝结的节余金属液,因为温度梯度小,会按同时凝结原则凝结,即金属液中形成很多渺小的晶粒。
当晶粒长大相互连结后,将节余金属液切割成互不相通的小熔池。
这些小熔池在随后的凝结过程中得不到金属液的增补,就形成缩松。
文档来自于网络搜寻缩松按其散布状态分三种:弥散缩松、轴线缩松、局部缩松。
铸件出现缩孔的原因

铸件出现缩孔的原因1. 你知道吗,铸件出现缩孔的一个原因可能是浇注温度不合理呀!就好比煮汤,温度太高或太低都会影响口感,浇注温度不合适,那铸件能好吗?比如浇注温度过高,液态金属收缩大,就容易产生缩孔啦!2. 哎呀,模具设计不合理也会导致缩孔哦!这就像给人做衣服,尺寸不合适怎么能合身呢?如果模具的型腔形状或尺寸不对,金属液的流动和凝固就会受影响,缩孔不就来了嘛,像那种型腔狭窄的地方就很容易出现缩孔呀!3. 喂喂喂,浇注速度也很关键呀!你想想,跑步太快或太慢都可能摔倒吧,浇注速度太快或太慢,铸件也会出问题呀!浇注速度过快,型腔里的气体来不及排出,缩孔就可能出现了,这多糟糕呀!4. 嘿,金属液的化学成分不对也不行呀!这就跟做菜调料放错了一样,味道能好吗?如果金属液中某些成分比例不合适,它的凝固特性改变,缩孔就可能冒出来了,可别小瞧这个呀!5. 哇塞,冷却条件不好也会让铸件出现缩孔呢!好比人在不合适的环境里会不舒服,铸件也是呀!冷却不均匀或者太快太慢,都会引发缩孔问题呢,这可不能马虎!6. 你们知道吗,熔炼工艺不当也是个原因呢!这就像酿酒,工艺不对酒就不香,熔炼工艺不好,铸件就容易有缩孔呀!比如熔炼时间过长或温度过高,都会有影响哦!7. 哎呀呀,铸件的结构设计也得注意呀!如果设计得太复杂或者有不合理的地方,那不就像走迷宫容易迷路一样嘛,缩孔就容易在这些地方出现啦!8. 说真的,浇注系统设计不合理也会惹麻烦呀!这就像交通规划不好会堵车一样,浇注系统设计不好,金属液的流动就不畅,缩孔就可能来啦,可不能随便设计呀!9. 大家想想,冒口设置不合理是不是也会导致缩孔呢?冒口就像是给铸件的一个保障,设置不对,缩孔就容易出现啦,就像没了可靠的后盾一样!10. 最后呀,操作工人的技术水平也很重要呢!就像司机开车技术好坏有很大影响一样,操作不当,铸件出现缩孔的可能性就大啦!我的观点结论就是:铸件出现缩孔的原因有很多,每一个环节都得认真对待,从设计到操作,都不能马虎呀!。
铸件缩孔缩松解决方法

铸件缩孔缩松解决方法铸件缩孔缩松是铸造过程中常见的缺陷问题,会对铸件的强度和密封性能造成影响。
为了解决这一问题,需要采取一系列的措施来减少或消除铸件的缩孔缩松现象。
合理设计铸件的结构是解决缩孔缩松问题的关键。
在铸件设计过程中,应尽量避免出现厚度不均匀、壁厚过大或过小等情况,以免产生应力集中和缩孔缩松的隐患。
同时,应留有足够的浇注系统和冷却系统,以保证铸件在凝固过程中有足够的液态金属供应和冷却条件,从而减少缩孔缩松的产生。
选择合适的铸造材料和工艺参数也是解决缩孔缩松问题的重要措施。
铸造材料的选择应考虑其流动性、凝固收缩率和气孔生成倾向等因素,以减少缩孔缩松的发生。
同时,通过优化浇注温度、浇注速度、浇注压力等工艺参数,可以改善铸件的凝固过程,减少缩孔缩松的产生。
加强铸造过程的控制和监测也是解决缩孔缩松问题的必要手段。
在铸造过程中,应严格控制浇注温度、铸型温度和冷却速度等参数,避免过热或过冷引起的缩孔缩松问题。
同时,通过使用合适的质量监测方法,如X射线探伤、超声波探伤等,及时发现和修复铸件中的缩孔缩松缺陷,确保铸件的质量。
可以采用一些特殊的工艺措施来解决铸件缩孔缩松问题。
例如,可以采用真空铸造、压力铸造或浸渍处理等方法,通过改变铸造环境或材料特性,减少缩孔缩松的发生。
此外,还可以在铸件表面施加压力或采用压力鼓包等方式,增加铸件的实体密度,减少缩孔缩松的存在。
铸件缩孔缩松是铸造过程中常见的缺陷问题,但通过合理的设计、选择合适的材料和工艺参数,加强铸造过程的控制和监测,以及采用特殊的工艺措施,可以有效地解决这一问题。
通过这些措施的综合应用,可以提高铸件的质量和性能,确保产品的可靠性和安全性。
铸造工艺---铸件的缩孔、缩松
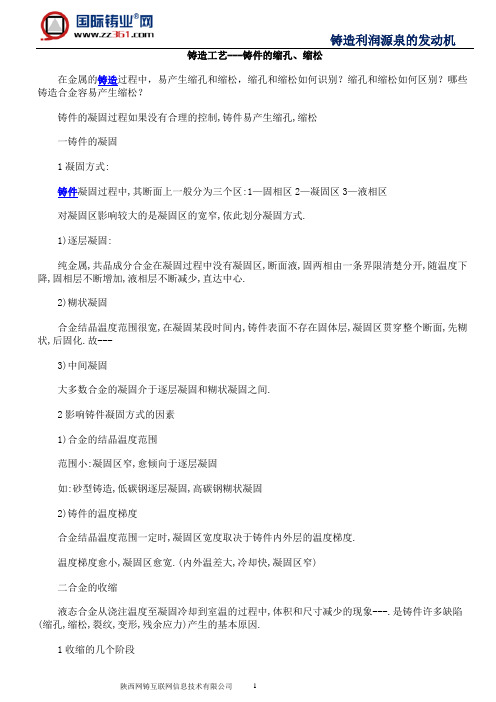
铸造工艺---铸件的缩孔、缩松在金属的铸造过程中,易产生缩孔和缩松,缩孔和缩松如何识别?缩孔和缩松如何区别?哪些铸造合金容易产生缩松?铸件的凝固过程如果没有合理的控制,铸件易产生缩孔,缩松一铸件的凝固1凝固方式:铸件凝固过程中,其断面上一般分为三个区:1—固相区2—凝固区3—液相区对凝固区影响较大的是凝固区的宽窄,依此划分凝固方式.1)逐层凝固:纯金属,共晶成分合金在凝固过程中没有凝固区,断面液,固两相由一条界限清楚分开,随温度下降,固相层不断增加,液相层不断减少,直达中心.2)糊状凝固合金结晶温度范围很宽,在凝固某段时间内,铸件表面不存在固体层,凝固区贯穿整个断面,先糊状,后固化.故---3)中间凝固大多数合金的凝固介于逐层凝固和糊状凝固之间.2影响铸件凝固方式的因素1)合金的结晶温度范围范围小:凝固区窄,愈倾向于逐层凝固如:砂型铸造,低碳钢逐层凝固,高碳钢糊状凝固2)铸件的温度梯度合金结晶温度范围一定时,凝固区宽度取决于铸件内外层的温度梯度.温度梯度愈小,凝固区愈宽.(内外温差大,冷却快,凝固区窄)二合金的收缩液态合金从浇注温度至凝固冷却到室温的过程中,体积和尺寸减少的现象---.是铸件许多缺陷(缩孔,缩松,裂纹,变形,残余应力)产生的基本原因.1收缩的几个阶段1)液态收缩:从金属液浇入铸型到开始凝固之前.液态收缩减少的体积与浇注温度质开始凝固的温度的温差成正比.2)凝固收缩:从凝固开始到凝固完毕.同一类合金,凝固温度范围大者,凝固体积收缩率大.如:35钢,体积收缩率3.0%,45钢4.3%3)固态收缩:凝固以后到常温.固态收缩影响铸件尺寸,故用线收缩表示.2影响收缩的因素1)化学成分:铸铁中促进石墨形成的元素增加,收缩减少.如:灰口铁C,Si↑,收↓,S↑收↑.因石墨比容大,体积膨胀,抵销部分凝固收缩.2)浇注温度:温度↑液态收缩↑3)铸件结构与铸型条件铸件在铸型中收缩会受铸型和型芯的阻碍.实际收缩小于自由收缩.∴铸型要有好的退让性.3缩孔形成在铸件最后凝固的地方出现一些空洞,集中—缩孔.纯金属,共晶成分易产生缩孔*产生缩孔的基本原因:铸件在凝固冷却期间,金属的液态及凝固受缩之和远远大于固态收缩.4影响缩孔容积的因素(补充)1)液态收缩,凝固收缩↑缩孔容积↑2)凝固期间,固态收缩↑,缩孔容积↓3)浇注速度↓缩孔容积↓4)浇注速度↑液态收缩↑易产生缩孔5缩松的形成由于铸件最后凝固区域的收缩未能得到补足,或者,因合金呈糊状凝固,被树枝状晶体分隔开的小液体区难以得到补缩所至.1)宏观缩松肉眼可见,往往出现在缩孔附近,或铸件截面的中心.非共晶成分,结晶范围愈宽,愈易形成缩松.2)微观缩松凝固过程中,晶粒之间形成微小孔洞---凝固区,先形成的枝晶把金属液分割成许多微小孤立部分,冷凝时收缩,形成晶间微小孔洞.凝固区愈宽,愈易形成微观缩松,对铸件危害不大,故不列为缺陷,但对气密性,机械性能等要求较高的铸件,则必须设法减少.(先凝固的收缩比后凝固的小,因后凝固的有液,凝,固三个收缩,先凝固的有凝,固二个收缩区----这也是形成微观缩松的基本原因.与缩孔形成基本原因类似)6缩孔,缩松的防止办法基本原则:制定合理工艺—补缩,缩松转化成缩孔.顺序凝固:冒口—补缩同时凝固:冷铁—厚处.减小热应力,但心部缩松,故用于收缩小的合金.l)安置冒口,实行顺序凝固,可有效的防止缩孔,但冒口浪费金属,浪费工时,是铸件成本增加.而且,铸件内应力加大,易于产生变形和裂纹.∴主要用于凝固收缩大,结晶间隔小的合金.2)非共晶成分合金,先结晶树枝晶,阻碍金属流动,冒口作用甚小.3)对于结晶温度范围甚宽的合金,由于倾向于糊状凝固,结晶开始之后,发达的树枝状骨状布满整个截面,使冒口补缩道路受阻,因而难避免显微缩松的产生.显然,选用近共晶成分和结晶范围较窄的合金生产铸件是适宜的.。
解决铸件缩孔的基本方法

解决铸件缩孔的基本方法
铸件缩孔是铸造过程中常见的一种缺陷,其主要表现为铸件表面或内部出现孔洞或空洞,影响铸件的质量和使用寿命。
下面将介绍解决铸件缩孔的基本方法。
一、改善铸造工艺
铸造工艺是影响铸件质量的重要因素之一,通过改善铸造工艺可以有效地减少铸件缩孔的发生。
具体方法包括:
1.合理设计铸型和浇注系统,避免浇注速度过快或过慢,控制浇注温度和压力,保证铸件内部和表面的充填均匀。
2.选用适当的铸造材料和熔炼工艺,保证铸造材料的质量和纯度,避免铸造材料中含有过多的杂质和气体。
3.加强铸造过程的监控和控制,及时发现和处理铸造缺陷,保证铸件的质量和稳定性。
二、采用预处理技术
预处理技术是指在铸造前对铸造材料进行处理,以消除材料中的缺陷和气体,减
少铸件缩孔的发生。
常用的预处理技术包括:
1.真空处理:将铸造材料置于真空环境中,使其中的气体和杂质得以挥发,减少铸件缩孔的发生。
2.热处理:通过加热和冷却的过程,改变铸造材料的晶体结构和性质,消除材料中的缺陷和气体,提高铸件的质量和强度。
三、采用填充材料
填充材料是一种特殊的材料,可以用于填充铸件中的孔洞和空洞,以提高铸件的密度和强度。
常用的填充材料包括:
1.树脂填充材料:具有良好的流动性和粘附性,可以填充铸件中的孔洞和空洞,提高铸件的密度和强度。
2.金属填充材料:具有较高的熔点和热传导性,可以填充铸件中的孔洞和空洞,提高铸件的密度和强度。
以上是解决铸件缩孔的基本方法,通过改善铸造工艺、采用预处理技术和填充材料,可以有效地减少铸件缩孔的发生,提高铸件的质量和使用寿命。
铸件缩孔样板标准

铸件缩孔样板标准
铸件缩孔样板标准主要涉及缩孔的尺寸、位置和评级方法。
以下是关于铸件缩孔样板标准的一些重要信息:
尺寸:铸件缩孔的尺寸是评价其质量的重要指标之一。
根据国家标准,标准试样的尺寸为100mm×100mm。
对于其他尺寸的铸件,缩孔的尺寸应按比例缩小或放大。
位置:缩孔通常位于铸件的低倍试样中心,形状近似圆形。
评级方法:铸件缩孔的评级方法主要根据缩孔的面积来确定。
当缩孔介于相邻两个等级之间时,可以评为半级,如0.5级、1.5级等。
评级标准通常根据国家标准制定,使用标准样张进行参考和比较。
在实际应用中,铸件缩孔样板标准可能因不同的行业、材料和工艺而有所不同。
因此,在具体操作中,需要参考相关的国家标准和行业规范,以确保铸件的质量和性能符合要求。
请注意,以上信息仅供参考,具体的铸件缩孔样板标准可能因不同的国家和地区、不同的行业和应用而有所不同。
因此,在实际操作中,需要结合具体情况进行评估和确定。
1。
- 1、下载文档前请自行甄别文档内容的完整性,平台不提供额外的编辑、内容补充、找答案等附加服务。
- 2、"仅部分预览"的文档,不可在线预览部分如存在完整性等问题,可反馈申请退款(可完整预览的文档不适用该条件!)。
- 3、如文档侵犯您的权益,请联系客服反馈,我们会尽快为您处理(人工客服工作时间:9:00-18:30)。
铸件缩孔、缩松产生的原因
1、铸件结构方面的原因
由于铸件断面过厚,造成补缩不良形成缩孔。
铸件壁厚不均匀,在壁厚部分热节处产生缩孔或缩松。
由于铸孔直径太小形成铸孔的砂芯被高温金属液加热后,长期处于高温状态,降低了铸孔表面金属的凝固速度,同时,砂芯为气体或大气压提供了信道,导致了孔壁产生缩孔和绣松。
铸件的凹角圆角半径太小,使尖角处型砂传热能力降低,凹角处凝固速度下降,同时由于尖角处型砂受热作用强,发气压力大,析出的气体可向未凝固的金属液渗入,导致铸件产生气缩孔。
2、熔炼方面的原因
液体金属的含气量太高,导致在铸件冷却过程中以气泡形式析出,阻止邻近的液体金属向该处流动进行补缩,产生缩孔或缩松。
当灰铸铁碳当量太低时,将使铁水凝固时共晶石墨析出量减少,降低了石墨化膨胀的作用,使凝固收缩增加,同时也降低铁水的流动性。
认而降低铁水的自补缩能力,使铸件容易产生缩孔或缩松。
当铁水含磷量或含硫量偏高时,磷是扩大凝固温度范围的元素,同时形成大量的低熔点磷共晶,凝固时减少了补缩能力。
硫是阻碍石墨化的元素,硫还能降低铁水的流动性。
同时,铁水氧化严重,也降低液体金属的流动性,使铸件产生缩孔或缩松。
孕育铸铁或球墨铸铁在浇注前用硅铁等孕育剂进行孕育处理时,如果孕育不良,将导致铁水凝固时析出大量的渗碳体,从而使凝固收缩增加,产生缩孔或缩松。
3、工艺设计的原因
(1)浇注系统设计不合理浇注系统设计与铸件的凝固原则相矛盾时,可能会导致铸件产生缩孔或缩松。
主要表现为浇注位置不合适,不利于顺序凝固,内浇口的位置及尺寸不正确。
对于灰铸铁和球墨铸铁,如果将内浇口开在铸件厚壁处,同时内浇口尺寸较厚,浇注后,内浇口则长时间处于液体状态。
在铁水凝固发生石墨化膨胀的作用下,铁水会经内浇口倒流回直浇道,从而使铸件产生缩孔和缩松。
(2)冒口设计不合理冒口位置、数量、尺寸及冒口颈尺寸未能促进铸件顺序凝固,都可能导致铸件产生缩孔和缩松。
如果在暗冒口顶部未放置出气冒口,或冷铁使用不当,也会导致铸件产生缩孔和缩松。
(3)型砂、芯砂方面的原因型砂(芯砂)的耐火度及高温强度太低,热变形量太大。
当在金属液的静压力或石墨化膨胀力的作用下,型壁或芯壁会产生移动。
使铸件实际需要的补缩量增加或在膨胀部位出现新的热节,导致铸件产生缩孔和缩松。
这种现象对大中型铸件是很敏感的。
另外,如果型砂中水分含量太高,将使型壁表面的干燥层厚度减少和水分凝聚区的水分增加,范围扩大,从而使型壁的移动能力增加,导致缩孔及缩松的产生。
(4)浇注方面的原因浇注温度太高,使液态金属的液态收缩量增加;太低时,又会降低冒口的补缩能力,特别是采用底注式浇注系统时更明显,铸件往往在下部产生缩孔和缩松。
当冒口没有浇满或对大中型铸件没有用金属液对明冒口进行补浇时,这将降低冒口的补缩能力,引起铸件产生缩孔或缩松。