齿轮传动系统的动力学仿真分析
机械齿轮传动系统的动力学分析与优化

机械齿轮传动系统的动力学分析与优化齿轮传动是一种常见的动力传递机构,具有传递力矩大、传动效率高等优点,在工业生产中得到广泛应用。
但是,由于齿轮传动系统存在着一些固有的问题,如齿轮啮合时的振动和噪音、齿面磨损等,因此对其进行动力学分析和优化是非常重要的。
1. 动力学分析1.1 齿轮啮合的动力学模型齿轮啮合过程中,齿轮之间存在着瞬时的压力、速度和加速度变化。
可以通过建立齿轮啮合的动力学模型来分析其动态特性。
常用的方法包括等效单齿转动法和有限元法。
通过分析齿轮齿面接触应力和应力分布,可以预测系统的振动和噪音水平,为后续的优化提供依据。
1.2 动力学参数的测量和计算为了进行动力学分析,需要测量和计算一些关键参数,如齿轮的啮合刚度、传递误差、滚子轴承的刚度等。
其中,传递误差是影响齿轮传动系统性能的重要因素之一,其大小与齿轮加工质量、啮合配合、齿轮轴向和径向跳动等因素有关。
通过合理的测量方法和计算模型,可以准确地获取这些参数,并对系统进行分析。
2. 动力学优化2.1 齿轮传动系统的振动和噪音控制由于齿轮啮合时的动态特性,齿轮传动系统常常会产生振动和噪音。
为了减小振动和噪音的水平,可以从多个方面进行优化,如合理设计齿形、减小啮合间隙、提高齿轮加工精度等。
此外,也可以采用减振装置,如弹性联轴器、减震器等,来降低系统的振动能量传递。
2.2 传动效率的提高传动效率是衡量齿轮传动系统性能的重要指标之一。
为了提高传动效率,可以从减小传动误差、改善齿轮表面质量、减小传动间隙等方面入手。
此外,合理选择润滑方式和润滑油,也可以有效地降低系统的摩擦和磨损,提高传动效率。
2.3 齿轮传动系统的寿命预测齿轮传动系统的寿命是评估其使用寿命和可靠性的重要指标。
通过综合考虑齿轮的强度、疲劳寿命和磨损等影响因素,可以建立寿命预测模型,对系统进行寿命预测和优化设计。
此外,还可以通过监测齿轮的工作状态和健康状况,进行实时的故障诊断和维护。
3. 总结齿轮传动系统的动力学分析和优化是提高其性能和可靠性的重要手段。
齿轮传动过程中的动力学分析
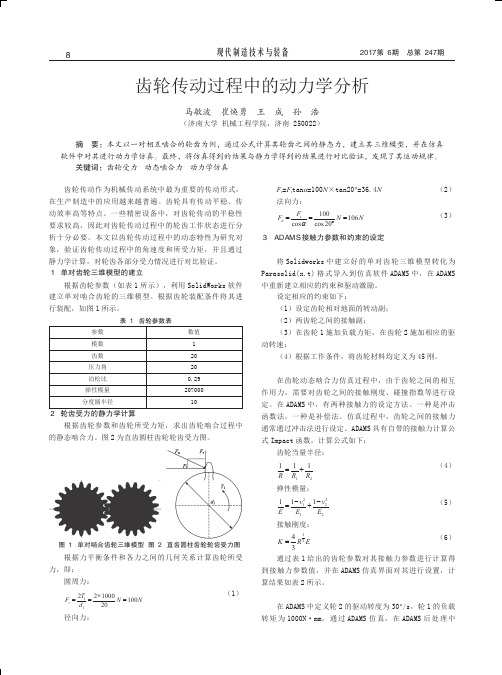
图1 单对啮合齿轮三维模型 图2 直齿圆柱齿轮轮齿受力图根据力平衡条件和各力之间的几何关系计算齿轮所受力,即:圆周力:1122100010020tT F N N d ×=== (1)图3 圆周动态啮合力仿真曲线图4 径向动态啮合力仿真曲线图5 法向动态啮合力仿真曲线通过图6可得出主动轮2所受力矩,而齿轮1负载力矩为1000N·mm。
齿轮2所受力矩根据力的大小围绕1000N·mm波动,所以齿轮在传动过程中所输出力矩并不是一个恒定值,而是会随齿轮动态啮合力大小不断变化。
图6 齿轮2所受力矩仿真曲线图7 齿轮1角速度仿真曲线4 结语首先,根据齿轮传动过程中所受力的大小,由公式计算齿轮的静态啮合力。
其次,利用仿真软件对齿轮实际运动过程中的工况进行动力学仿真,得到实际工况下的动态啮合力和速度图像。
最后,通过得到的动力学图像与静力学条件下计算得到的静态力进行对比验证,并分析了齿轮运动过程中的工况。
参考文献[1]夏永.基于ADAMS的风电齿轮箱动力学仿真分析[D].大连:大连理工大学,2014.[2]江志祥,朱增宝,季军.基于UG与ADAMS的行星齿轮减速器动力学仿真分析[J].煤矿机械,2013,(6):43-44.[3]张白鸽,岑海堂.基于ADAMS的椭圆齿轮动力学仿真分析[J].机械工程与自动化,2016,(2):98-100.[4]陈涛.风力发电机组齿轮箱传动系统动力学仿真与分析[D].北京:华北电力大学,2015.[5]钱直睿,黄晓燕,李明哲,李东平.多轴齿轮传动系统的动力学仿真分析[J].中国机械工程,2006,(3):241-244.Dynamic Analysis of Gear TransmissionMA Minbo, CUI Huanyong, WANG Cheng, SUN Hao(School of Mechanical Engineering, University of Jinan, Jinan 250022)Abstract: In this paper, a pair of meshing teeth, for example, through the formula to calculate the static force between the teeth, and the establishment of its three-dimensional model, in the simulation software for its dynamic simulation. The results of simulation are compared with those obtained by statics, and the laws of motion are found.Key words:gear force, dynamic meshing force, dynamic simulation。
齿轮传动系统的动力学与模态分析
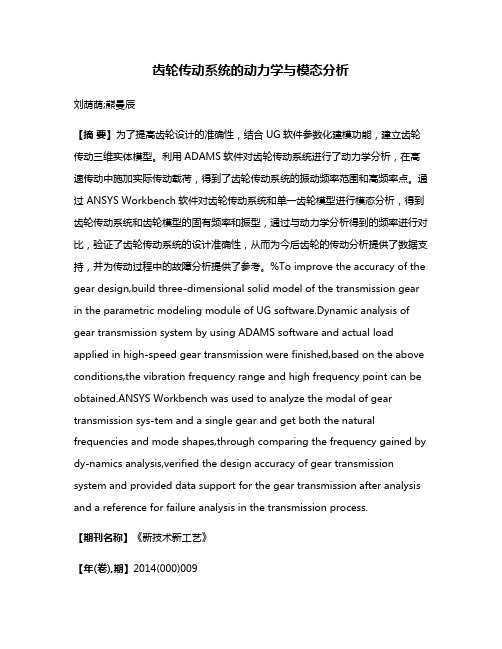
齿轮传动系统的动力学与模态分析刘荫荫;熊曼辰【摘要】为了提高齿轮设计的准确性,结合UG软件参数化建模功能,建立齿轮传动三维实体模型。
利用ADAMS软件对齿轮传动系统进行了动力学分析,在高速传动中施加实际传动载荷,得到了齿轮传动系统的振动频率范围和高频率点。
通过 ANSYS Workbench软件对齿轮传动系统和单一齿轮模型进行模态分析,得到齿轮传动系统和齿轮模型的固有频率和振型,通过与动力学分析得到的频率进行对比,验证了齿轮传动系统的设计准确性,从而为今后齿轮的传动分析提供了数据支持,并为传动过程中的故障分析提供了参考。
%To improve the accuracy of the gear design,build three-dimensional solid model of the transmission gear in the parametric modeling module of UG software.Dynamic analysis of gear transmission system by using ADAMS software and actual load applied in high-speed gear transmission were finished,based on the above conditions,the vibration frequency range and high frequency point can be obtained.ANSYS Workbench was used to analyze the modal of gear transmission sys-tem and a single gear and get both the natural frequencies and mode shapes,through comparing the frequency gained by dy-namics analysis,verified the design accuracy of gear transmission system and provided data support for the gear transmission after analysis and a reference for failure analysis in the transmission process.【期刊名称】《新技术新工艺》【年(卷),期】2014(000)009【总页数】4页(P100-103)【关键词】ADAMS;动力学分析;ANSYS Workbench;模态分析;固有频率【作者】刘荫荫;熊曼辰【作者单位】昆明理工大学机电工程学院,云南昆明 650000;昆明理工大学机电工程学院,云南昆明 650000【正文语种】中文【中图分类】TH132.4渐开线齿轮是一种重要的机械零件,因为齿轮传动的平稳性而在高速传动设置中作为传动装置的核心部分起重要作用。
行星齿轮传动系统的动力学建模与分析

行星齿轮传动系统的动力学建模与分析齿轮传动系统是一种常见的机械传动形式,由多个齿轮通过啮合传递动力。
在齿轮传动系统中,行星齿轮传动系统是一种常见的结构。
它由中央太阳齿轮、外圈行星齿轮和内圈行星齿轮组成。
行星齿轮传动系统具有紧凑结构、传动比变化范围广和承载能力强的特点,所以在很多机械传动系统中得到广泛应用。
了解行星齿轮传动系统的动力学特性对于设计和优化机械传动系统具有重要意义。
行星齿轮传动系统的动力学建模是研究其特性的基础。
一般而言,行星齿轮传动系统的动力学研究可以分为两个方面:传动系统的静态行为和传动系统的动态行为。
首先,我们来讨论行星齿轮传动系统的静态行为。
行星齿轮传动系统的静态行为主要包括传动比和齿轮位置分析。
传动比决定了输入轴和输出轴的转速比,对于不同的工况要求,传动比的变化范围也是需要考虑的因素。
齿轮位置分析是指确定各个齿轮之间的相对位置,这对于齿轮的啮合是否合理具有重要影响。
在行星齿轮传动系统的静态行为分析中,可以采用几何法和力学法相结合的方法,来求解传动比和齿轮位置。
几何法主要通过几何关系求解,力学法则涉及到力矩平衡和力平衡,求解过程需要考虑到齿轮的几何关系和曲柄等部件的力学特性。
其次,我们来讨论行星齿轮传动系统的动态行为。
行星齿轮传动系统的动态行为主要包括齿轮振动、齿轮动力学和齿轮传动系统的自激振动分析。
齿轮振动是指齿轮在运动过程中由于齿轮的不平衡、啮合刚度等因素引起的振动。
齿轮动力学是指齿轮在运动过程中由于齿轮的载荷和齿轮啮合行为引起的力学现象。
自激振动是指齿轮传动系统由于齿轮的不均匀磨损、齿轮啮合误差等因素引起的自激振动。
行星齿轮传动系统的动态行为分析需要采用系统动力学和振动理论等方法,通过建立数学模型来求解相应的动力学方程。
对于行星齿轮传动系统的动态行为分析,可以分为线性动力学分析和非线性动力学分析。
线性动力学分析是指在小扰动情况下对齿轮传动系统进行的分析,一般求解线性化的动力学方程来得到系统的频率响应和稳定性。
齿轮故障动力学仿真matlab-概述说明以及解释

齿轮故障动力学仿真matlab-概述说明以及解释1.引言1.1 概述齿轮是机械传动中常用的零部件,其在各种机械设备中起着至关重要的作用。
然而,由于工作环境的恶劣以及长期使用的磨损,齿轮可能出现故障,导致机械设备的性能下降甚至损坏。
为了更好地理解齿轮故障的动力学特性,可以通过仿真技术来模拟和分析齿轮系统的运行状态,并及时发现潜在的故障点。
本文将介绍齿轮故障动力学仿真在MATLAB中的应用,通过分析齿轮系统的动态特性,探讨不同故障模式对系统性能的影响,从而为齿轮故障诊断和预防提供有益的参考。
通过本文的研究,我们希望能够加深对齿轮故障动力学的理解,提高齿轮系统的可靠性和安全性。
1.2 文章结构文章结构部分的内容如下:文章结构包括以下几个部分:1. 引言:介绍文章的背景和研究意义,引出文章的主题和研究内容。
2. 正文:分为两个部分,分别是齿轮故障动力学简介和MATLAB在齿轮故障动力学仿真中的应用。
在齿轮故障动力学简介部分,将介绍齿轮故障动力学的基本概念和原理,为读者提供必要的背景知识。
在MATLAB 在齿轮故障动力学仿真中的应用部分,将详细介绍MATLAB在该领域的具体应用及其优势。
3. 结论:总结文章的主要内容和研究成果,对研究进行评价和展望未来的研究方向。
通过以上部分的内容安排,读者可以清晰地了解整篇文章的主要结构和内容安排,帮助他们更好地理解和阅读文章。
1.3 目的本文的主要目的在于探讨利用MATLAB进行齿轮故障动力学仿真的方法和技术。
通过对齿轮系统中可能出现的不同故障情况进行建模和仿真,我们可以更好地理解齿轮系统的运行机理,并且能够快速有效地诊断和解决齿轮故障问题。
同时,本文也旨在为工程师和研究人员提供一个基于MATLAB的齿轮故障动力学仿真平台,帮助他们更好地分析和优化齿轮系统的性能,推动齿轮传动技术的发展和应用。
通过本文的研究,我们希望能够为齿轮系统的设计、运行和维护提供更加有效的工程解决方案,提高齿轮系统的可靠性和稳定性。
机械设计中的齿轮系统动力学分析
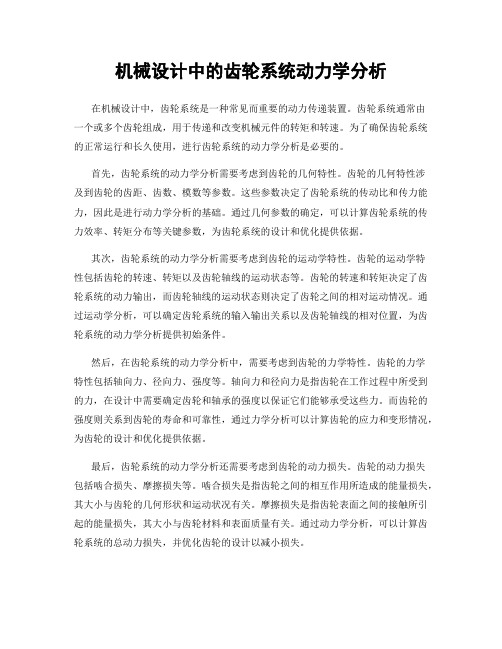
机械设计中的齿轮系统动力学分析在机械设计中,齿轮系统是一种常见而重要的动力传递装置。
齿轮系统通常由一个或多个齿轮组成,用于传递和改变机械元件的转矩和转速。
为了确保齿轮系统的正常运行和长久使用,进行齿轮系统的动力学分析是必要的。
首先,齿轮系统的动力学分析需要考虑到齿轮的几何特性。
齿轮的几何特性涉及到齿轮的齿距、齿数、模数等参数。
这些参数决定了齿轮系统的传动比和传力能力,因此是进行动力学分析的基础。
通过几何参数的确定,可以计算齿轮系统的传力效率、转矩分布等关键参数,为齿轮系统的设计和优化提供依据。
其次,齿轮系统的动力学分析需要考虑到齿轮的运动学特性。
齿轮的运动学特性包括齿轮的转速、转矩以及齿轮轴线的运动状态等。
齿轮的转速和转矩决定了齿轮系统的动力输出,而齿轮轴线的运动状态则决定了齿轮之间的相对运动情况。
通过运动学分析,可以确定齿轮系统的输入输出关系以及齿轮轴线的相对位置,为齿轮系统的动力学分析提供初始条件。
然后,在齿轮系统的动力学分析中,需要考虑到齿轮的力学特性。
齿轮的力学特性包括轴向力、径向力、强度等。
轴向力和径向力是指齿轮在工作过程中所受到的力,在设计中需要确定齿轮和轴承的强度以保证它们能够承受这些力。
而齿轮的强度则关系到齿轮的寿命和可靠性,通过力学分析可以计算齿轮的应力和变形情况,为齿轮的设计和优化提供依据。
最后,齿轮系统的动力学分析还需要考虑到齿轮的动力损失。
齿轮的动力损失包括啮合损失、摩擦损失等。
啮合损失是指齿轮之间的相互作用所造成的能量损失,其大小与齿轮的几何形状和运动状况有关。
摩擦损失是指齿轮表面之间的接触所引起的能量损失,其大小与齿轮材料和表面质量有关。
通过动力学分析,可以计算齿轮系统的总动力损失,并优化齿轮的设计以减小损失。
综上所述,机械设计中的齿轮系统动力学分析是一个综合性的工程问题。
通过考虑齿轮的几何特性、运动学特性、力学特性和动力损失等因素,可以全面了解齿轮系统的工作情况,为齿轮系统的设计和优化提供科学依据。
齿轮仿真耦合实验报告(3篇)
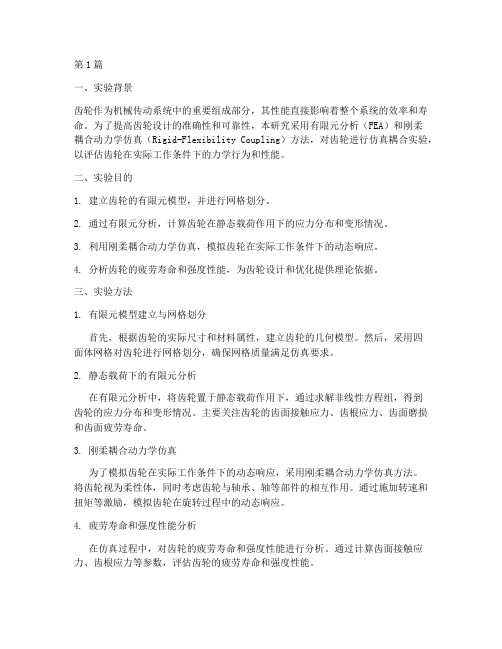
第1篇一、实验背景齿轮作为机械传动系统中的重要组成部分,其性能直接影响着整个系统的效率和寿命。
为了提高齿轮设计的准确性和可靠性,本研究采用有限元分析(FEA)和刚柔耦合动力学仿真(Rigid-Flexibility Coupling)方法,对齿轮进行仿真耦合实验,以评估齿轮在实际工作条件下的力学行为和性能。
二、实验目的1. 建立齿轮的有限元模型,并进行网格划分。
2. 通过有限元分析,计算齿轮在静态载荷作用下的应力分布和变形情况。
3. 利用刚柔耦合动力学仿真,模拟齿轮在实际工作条件下的动态响应。
4. 分析齿轮的疲劳寿命和强度性能,为齿轮设计和优化提供理论依据。
三、实验方法1. 有限元模型建立与网格划分首先,根据齿轮的实际尺寸和材料属性,建立齿轮的几何模型。
然后,采用四面体网格对齿轮进行网格划分,确保网格质量满足仿真要求。
2. 静态载荷下的有限元分析在有限元分析中,将齿轮置于静态载荷作用下,通过求解非线性方程组,得到齿轮的应力分布和变形情况。
主要关注齿轮的齿面接触应力、齿根应力、齿面磨损和齿面疲劳寿命。
3. 刚柔耦合动力学仿真为了模拟齿轮在实际工作条件下的动态响应,采用刚柔耦合动力学仿真方法。
将齿轮视为柔性体,同时考虑齿轮与轴承、轴等部件的相互作用。
通过施加转速和扭矩等激励,模拟齿轮在旋转过程中的动态响应。
4. 疲劳寿命和强度性能分析在仿真过程中,对齿轮的疲劳寿命和强度性能进行分析。
通过计算齿面接触应力、齿根应力等参数,评估齿轮的疲劳寿命和强度性能。
四、实验结果与分析1. 静态载荷下的应力分布和变形通过有限元分析,得到齿轮在静态载荷作用下的应力分布和变形情况。
结果表明,齿轮的齿面接触应力主要集中在齿根附近,齿根应力较大。
同时,齿轮的变形主要集中在齿面和齿根处。
2. 刚柔耦合动力学仿真结果通过刚柔耦合动力学仿真,模拟齿轮在实际工作条件下的动态响应。
结果表明,齿轮的齿面接触应力、齿根应力等参数在旋转过程中发生变化,但总体上满足设计要求。
齿轮传动系统的动态模拟

・
3 8・
机 械 工 程 与 自 动 化
21 0 0年 第 1 期
I 4 g ( 4 0 ) 志 ( 一 0 ) 一 7 。 … … L 0 + f 0 — 3 + 3一 ’
… … … … … … … … … … … … …Байду номын сангаас… … … … … …
高 阶常微分 方程 组为 :
导齿 轮系统 的设 计 。 因此 , 了设 计 出合理 、 为 高效 、 高 性 能 的齿 轮传动 系统 ,改 善 系统 的 动态特 性 ,本 文针 对 齿 轮副 间隙非 线性 振动 问题 展 开 了研究 。
1 直 齿轮 系统 动 力学模 型 的建 立
本 文采 用整 体 变速箱 模 型 , 轮齿 数 比为 7: 0 齿 1, 各 齿轮 主要 参数 见表 1 。齿 轮模 型具 有 1 6自由度 , 模 型示意 图见 图 1 。
表 1 齿 轮模 型 参 数
参 数 名 称
Z l Z 2
图 1 1 自 由 度 齿 轮 动 态 模 型 6
● ●
参 数 含 义
主 动 轮 齿 数 从 动 轮 齿 数
参 数 初 值
2 8 4 0
,
l
+ 吼 ( 一 2 + k ( 一 2 一 r 。 … … 1 ) ) ,
算 了 两 种运 行 状 态 下 , 同接 触 位 置 上 的扭 转 啮 合 刚 度 。 进 行 齿 轮 副非 线 性 振 动 的 分 析 时 , 合 考 虑 了啮合 不 在 综
冲 击 激励 、 时 变 啮 合 刚 度 和 误 差 激 励 等 非 线 性 因 素 ,建 立 了齿 轮 副 非 线 性 动 力 学 模 型 , 采 用 变 步 长 四 阶
基于ANSYS的齿轮仿真分析

基于ANSYS的齿轮仿真分析齿轮是一种常见的机械传动元件,广泛应用于工业生产中的各种机械设备中。
齿轮的工作性能直接影响着整个传动系统的性能和可靠性。
为了确保齿轮的正常工作和延长使用寿命,需要对齿轮进行仿真分析。
本文将介绍基于ANSYS软件的齿轮仿真分析方法和流程。
首先,进行齿轮的几何建模。
使用ANSYS软件中的几何建模工具,根据实际齿轮的参数进行几何建模。
包括齿轮的齿数、模数、齿宽等参数。
建立三维模型后,对齿轮进行网格划分,生成有限元模型。
接下来,进行材料属性的定义。
根据实际齿轮的材料,定义材料属性。
包括弹性模量、泊松比、材料密度等参数。
这些参数将被用于后续的载荷和刚度分析。
然后,进行齿轮的载荷分析。
齿轮在工作过程中受到来自外界的载荷作用,主要包括径向力、切向力和轴向力等。
通过ANSYS中的载荷工具,对齿轮进行载荷加载。
可以根据实际工况设置载荷大小和方向。
进行齿轮的接触分析。
齿轮的接触是齿轮传动中的重要性能指标之一、通过ANSYS中的接触分析工具,可以计算齿轮接触面上的应力分布、接触区域和接触压力等参数。
这些参数对于齿轮的寿命和工作性能有重要影响。
进行齿轮的动力学分析。
齿轮在传动过程中会产生振动和噪声。
通过ANSYS中的动力学分析工具,可以计算齿轮的振动模态、固有频率和振动幅度等参数。
这些参数对于齿轮的运行平稳性和噪声控制有重要意义。
最后,进行疲劳分析。
齿轮在长时间使用过程中,容易出现疲劳破坏。
通过ANSYS中的疲劳分析工具,可以预测齿轮的寿命和疲劳破坏位置。
通过疲劳分析结果,可以调整齿轮的设计参数,提高其工作寿命。
综上所述,基于ANSYS的齿轮仿真分析包括几何建模、材料属性定义、载荷分析、接触分析、动力学分析和疲劳分析等步骤。
通过这些分析,可以评估齿轮的工作性能,指导齿轮的设计和改进。
同时,齿轮仿真分析可以帮助优化整个传动系统的工作性能和可靠性,提高机械设备的制造水平和整体效益。
基于ADAMS的齿轮变速箱动态特性仿真分析

基于ADAMS的齿轮变速箱动态特性仿真分析齿轮变速箱是机械传动系统中常见的一种传动装置,在各种机械设备中广泛应用。
了解齿轮变速箱的动态特性对于提高其性能和可靠性具有重要意义。
在本文中,我们将使用ADAMS软件对齿轮变速箱的动态特性进行仿真分析,以探讨该装置在不同工况下的性能表现。
首先,我们将建立齿轮变速箱的三维模型。
在ADAMS中,我们可以通过建立零件模型、定义零件之间的连接关系和运动约束,快速构建一台完整的齿轮变速箱模型。
我们将考虑齿轮、轴承、轴、传动链等零部件的几何形状、材料性质和运动学特性,确保模型的真实性和精确性。
接下来,我们将定义齿轮变速箱的动力学模型。
在ADAMS中,我们可以设置各个零部件之间的摩擦、惯性、弹簧等物理属性,建立整个系统的动力学模型。
通过运用牛顿-欧拉定律和其他相关理论,我们可以模拟齿轮变速箱在不同工况下的运动规律和受力情况,分析其动态特性。
然后,我们将进行齿轮变速箱的动态仿真分析。
在ADAMS中,我们可以设置不同工况下的输入参数(如速度、扭矩等),模拟齿轮变速箱在这些条件下的运动情况。
通过分析各个零部件的速度、位移、受力等参数变化,我们可以了解齿轮变速箱在不同工况下的动态特性,判断其稳定性、传动效率等指标。
最后,我们将对仿真结果进行评估和优化。
通过对仿真结果的分析,我们可以找出齿轮变速箱在运转过程中存在的问题和不足之处,进而对其结构设计、材料选择、润滑方式等方面进行优化改进,提高其性能和可靠性。
综上所述,基于ADAMS的齿轮变速箱动态特性仿真分析是一种有效的研究手段,可以帮助工程师深入了解齿轮变速箱的运动规律和受力情况,为其设计和优化提供参考和支持。
通过不断优化改进,我们可以不断提升齿轮变速箱的性能和可靠性,满足各种机械设备对传动系统的需求。
齿轮传动系统的动力学仿真分析
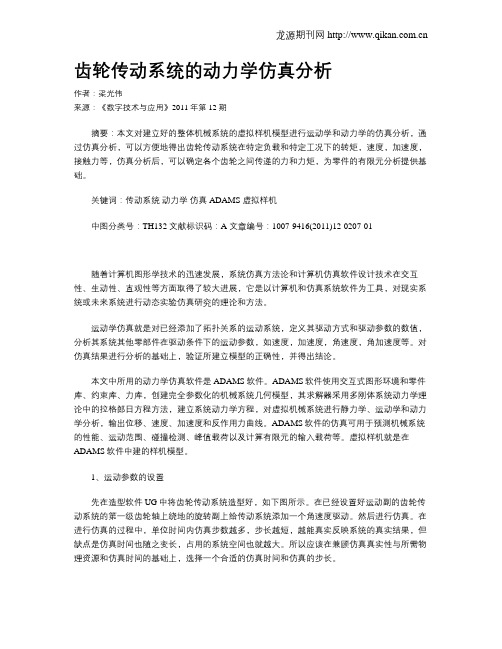
齿轮传动系统的动力学仿真分析作者:梁光伟来源:《数字技术与应用》2011年第12期摘要:本文对建立好的整体机械系统的虚拟样机模型进行运动学和动力学的仿真分析,通过仿真分析,可以方便地得出齿轮传动系统在特定负载和特定工况下的转矩,速度,加速度,接触力等,仿真分析后,可以确定各个齿轮之间传递的力和力矩,为零件的有限元分析提供基础。
关键词:传动系统动力学仿真 ADAMS 虚拟样机中图分类号:TH132 文献标识码:A 文章编号:1007-9416(2011)12-0207-01随着计算机图形学技术的迅速发展,系统仿真方法论和计算机仿真软件设计技术在交互性、生动性、直观性等方面取得了较大进展,它是以计算机和仿真系统软件为工具,对现实系统或未来系统进行动态实验仿真研究的理论和方法。
运动学仿真就是对已经添加了拓扑关系的运动系统,定义其驱动方式和驱动参数的数值,分析其系统其他零部件在驱动条件下的运动参数,如速度,加速度,角速度,角加速度等。
对仿真结果进行分析的基础上,验证所建立模型的正确性,并得出结论。
本文中所用的动力学仿真软件是ADAMS软件。
ADAMS软件使用交互式图形环境和零件库、约束库、力库,创建完全参数化的机械系统几何模型,其求解器采用多刚体系统动力学理论中的拉格郎日方程方法,建立系统动力学方程,对虚拟机械系统进行静力学、运动学和动力学分析,输出位移、速度、加速度和反作用力曲线。
ADAMS软件的仿真可用于预测机械系统的性能、运动范围、碰撞检测、峰值载荷以及计算有限元的输入载荷等。
虚拟样机就是在ADAMS软件中建的样机模型。
1、运动参数的设置先在造型软件UG中将齿轮传动系统造型好,如下图所示。
在已经设置好运动副的齿轮传动系统的第一级齿轮轴上绕地的旋转副上给传动系统添加一个角速度驱动。
然后进行仿真。
在进行仿真的过程中,单位时间内仿真步数越多,步长越短,越能真实反映系统的真实结果,但缺点是仿真时间也随之变长,占用的系统空间也就越大。
齿轮传动系统动力学特性的有限元分析及试验方法研究

齿轮传动系统动力学特性的有限元分析及试验方法研究一、引言齿轮传动系统在机械工程中广泛应用,其动力学特性的研究对于提高传动系统的运行效率和寿命至关重要。
有限元分析及试验方法是研究齿轮传动系统动力学特性的重要手段。
本文将从有限元分析和试验方法两个方面展开,对齿轮传动系统动力学特性的研究进行探讨。
二、有限元分析方法1. 有限元建模齿轮传动系统的有限元建模是研究动力学特性的基础。
建模过程包括几何建模、材料建模和网格划分。
在几何建模中,需要将齿轮的几何形状进行准确描述,并考虑齿轮的大气隙等因素。
材料建模需要考虑齿轮材料的力学性质,如弹性模量、泊松比等。
在网格划分中,需要合理划分网格,以获得准确的数值解。
2. 动力学分析有限元模型构建完成后,可以通过求解动力学方程来研究齿轮传动系统的动力学特性。
动力学方程包括结构平衡方程、动力学平衡方程和边界条件等。
通过有限元分析可以得到齿轮传动系统的振动模态、共振频率等动力学特性。
三、试验方法1. 试验设备为了验证有限元分析的准确性和可靠性,需要进行试验来对齿轮传动系统的动力学特性进行检测。
试验设备包括齿轮传动系统的测试台架、传感器等。
测试台架需要能够模拟实际工作条件,传感器可以测量齿轮传动系统的振动、力和位移等参数。
2. 试验过程试验过程包括数据采集、数据处理和结果分析等步骤。
数据采集需要在试验过程中获取到齿轮传动系统的振动、力和位移等参数。
数据处理包括对试验数据进行滤波、去噪等处理,以得到准确可靠的数据。
结果分析可以通过对试验数据的曲线和图像进行定量和定性分析,从而了解齿轮传动系统的动力学特性。
四、研究进展和趋势目前,有限元分析和试验方法在齿轮传动系统动力学特性的研究中得到了广泛应用。
然而,目前的研究还存在一些问题和不足之处。
一是有限元分析模型的准确性和可靠性有待提高,尤其是对于非线性和非均匀材料的建模;二是试验方法的高效性和精确性有待改进,尤其是对于大规模齿轮传动系统的实验。
斜齿圆柱齿轮传动的弹性动力学仿真分析
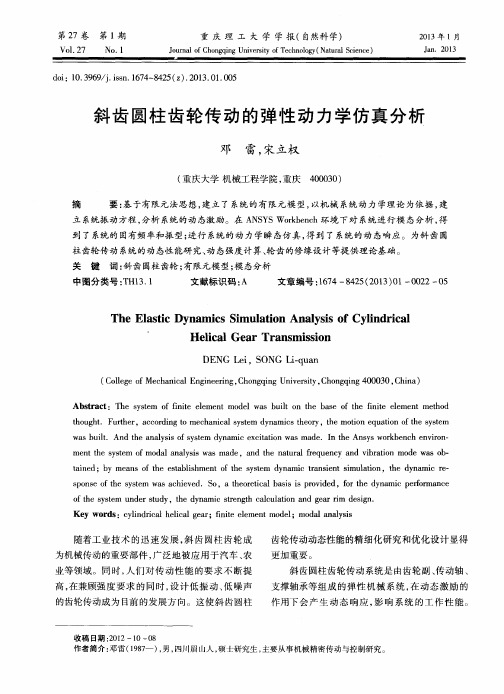
中 图分 类号 : T H1 3 . 1
Th e El a s t i c Dy n a mi c s Si mu l a t i o n An a l y s i s o f Cy l i n dr i c a l
’
He l i c a l Ge a r Tr a ns mi s s i o n
第2 7卷 第 1 期
V0 l _ 2 7
No . 1
重 庆 理 X -大 学 学 报 (自然科 学)
J o u na r l o f C h o n g q i n g U n i v e r s i t y o f T e c h n o l o g y ( N a t u r a l S c i e n c e )
s p o n s e o f t h e s y s t e m w a s a c h i e v e d .S o,a t h e o r e t i c a l b a s i s i s p r o v i d e d,f o r t h e d y n a mi c p e r f o r ma n c e
Abs t r a c t:Th e s y s t e m o f in f i t e e l e me n t mo d e l wa s b ui l t o n t h e b a s e o f t h e in f i t e e l e me n t me t h o d t h o u g h t .Fu r t he r ,a c c o r d i n g t o me c h a n i c a l s y s t e m d y na mi c s t h e o r y,t h e mo t i o n e q u a t i o n o f t h e s y s t e m wa s b ui l t .An d t h e a na l y s i s o f s y s t e m d y n a mi c e x c i t a t i o n wa s ma d e.I n t h e An s y s wo r kb e n c h e n v iJ a n .2 0 1 3
基于虚拟样机技术的齿轮传动动力学与静力学仿真分析_谢永智

际值完全一致。 由图 3、图 4 还可以看出输出轴和中
间轴角速度恒定,且符号相反。 这说明:虚拟样机模
型传动是平稳的;各齿轮转向符合实际工作状况下
外齿轮啮合方向关系;虚拟样机模型是正确的,是能
反映实际工况的;
角 速 度 / (° )·s-1
30 001.5 30 001.0 30 000.5 30 000.0 29 999.5 29 999.00.0
在 UG 中,选择[工具]-[表达式],定义表 1 中的参数
和其参数值,然后选择[插入]-[曲线]-[规律曲线]/[基
本曲线]分别实现渐开线曲线、过度曲线和齿顶圆、
图 2 齿轮虚拟样机模型
齿根圆的二维绘制,接着进行阵列,拉伸即可生成三 2 减速器齿轮动力学仿真
维的齿轮模型,如图 1 所示。
(1)齿轮仿真系统建立步骤:
图, 从云图中可以读出最大的应力应变发生的位置
以及确切数值。 从图 7 可以获得轮齿所受最大应力
值为 105.670 MPa。
NODAL SOLUTION STEP=1 SUB=1 TIME=1 SEQV (AVG) DMX=.270E-04 SMN=.856 271 SMX=105 670
FEB 6 2012 20:49:30
和材料的泊松比 0.3;
④网格划分 设置网格单元尺寸 10。 对模型进
行网格划分。 如图 6;
⑤施加约束条件 在齿轮的内圆柱节点实施全
约束;
⑥施加载荷 把轮齿看作是悬臂梁,外力作用
在齿轮齿顶处,施加在 ADAMS 中测得的外力载荷,
10 375 N;
⑦求解及后处理。
在 ANSYS 中可以获得轮齿的应力应变分布云
(2)测量和分析数据
行星齿轮系统的运动分析及动力学仿真

! & " !’#,$ ) 因 为 ’ 为 原 动 件, $ ’!" , " !’#,$ + )+ 取 $ % & !, 则 行星传动特性参数 * % ’ % , + ! ’$ * - #, (() ( "! % & ( *" ’" ’
图’
・
系统的健合图模型
!’ $( $’ " !’ % & , % , $( !" ") " , " !" ( ( "" % $ "!" % & $ !!!#, % # *" ’" ’ + !,) ! 式中," !" % ! % " % 。 !" + ! +)
!
行星齿轮系统的运动分析
本文要讨论的行星齿轮系统是一种汽车自动变速
器, 机构简图如图 !+ 所示。根据 ,+-,. / 0 / 提出的图
[%] 画转换方法 , 可得到图 !1 所示的齿轮系图画。
式中, ")! 3 $ % ) & % ! ; "&! 3 $ % & & % ! ; ")% 3 % ) & % % ; "&’ 3 其中各齿轮的齿数如图 ! 中标注。 %& & %’ , ! !" 行星齿轮系统的传动比 如图所示当 制 动 组 件 ’ # 作 用 (即 组 件 # 的 转 速 为零 !# 3 ") , 离合器与组件 ’ 接合 ( ( ’ 作 用) , 是该变 速器的一个档位。依据 # 个基本回路方程式, 因 !# 3 可得矩阵式 ", ! ! " " " ) &! $ ! ! ) &’ $ ! " $ ) &! " $ ) &’ $ ) )! !! " " !% " 3 $ ) )% !& " $ ! ’ " !)
基于ADAMS的齿轮传动特性仿真分析
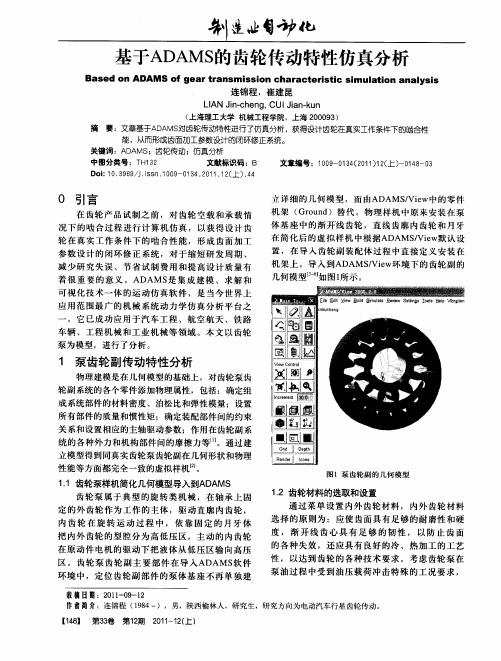
— 0 \∞ 一 0∞
30 7 0
— u—U n u— — v¨ v¨ vn 0 ¨ n ¨ ¨ — — —U U ¨ ¨ ¨ —U — n u— —U ^U —U —U 0 ¨ U — ¨ ¨ ¨ ¨ ¨ ¨ U
—— O tr u e
姗
。 6 鲁 3。 g 5— 0 0
把 内外齿轮 的型腔分为高低压 区,主动 的内齿轮 在 原 动 件 电机 的 驱 动 下 把 液体 从 低压 区 输 向高 压
区 。齿 轮 泵 齿 轮 副 主 要 部 件 在 导 入ADAMS 件 软 环 境 中 ,定 位 齿 轮 副 部件 的泵 体 基 座 不 再 单 独 建
收稿日期:2 1- 9 2 0 1 0 -1 作者简介:连锦程 (9 4一 18 ),男,陕西榆林人 ,研究生 ,研究方 向为电动汽车行星齿轮传 动。
0 引言
在 齿 轮 产 品试 制 之 前 ,对 齿 轮 空 载 和 承载 情
立 详 细 的 几何 模 型 ,而 由ADA SViw中的 零 件 M / e 机 架 ( ru d G o n )替代 。物 理 样机 中原 来 安 装 在泵
况 下 的 啮 合 过程 进行 计 算 机 仿 真 , 以获 得设 计 齿
车 辆 、工 程 机 械 和 工 业 机 械 等领 域 。本 文 以齿 轮 泵 为模 型 ,进行 了分析 。
I A.ie ln }ng e b h u j 圈
. 1I i I
1 泵齿轮副传动特性分析
物理 建模 是在 几何 模型 的基 础上 ,对齿轮 泵齿
囤 . 鲁
1 ‘
— —- — —
一 盛 ■
Gd㈠D t i r eh p
R ne 0¥ edr n l
机械传动系统的设计与仿真分析

机械传动系统的设计与仿真分析一、引言机械传动系统是指通过齿轮、皮带、链条等机构进行动力传递的装置。
在现代工业中,机械传动系统广泛应用于汽车、机器人、航空航天等领域。
本文将探讨机械传动系统的设计原理和仿真分析方法。
二、机械传动系统的设计原理机械传动系统的设计涉及到动力传递、速度转换和扭矩输出等方面。
其主要设计原理包括以下几点:1. 齿轮传动齿轮传动是最常见的一种机械传动形式。
通过不同规格的齿轮进行啮合,实现不同速度和扭矩的传递。
在设计齿轮传动系统时,需要考虑齿轮的材料选择、齿轮模数、齿数比和啮合角等因素。
2. 皮带传动皮带传动是通过拉紧皮带来传递动力的一种机械传动方式。
在设计皮带传动系统时,需要考虑皮带的类型、带速系数、切向力和侧向力等因素。
3. 链传动链传动是由链条、链轮和滚子等组成的一种机械传动系统。
在设计链传动系统时,需要考虑链条的选择、链轮的模数和齿数等因素。
三、机械传动系统的仿真分析方法为了验证机械传动系统的设计方案和性能参数,可以利用仿真分析方法进行验证。
常用的机械传动系统仿真分析方法包括:1. 动力学仿真动力学仿真可以通过建立传动系统的动力学模型,评估系统的运动特性和稳定性。
通过仿真软件,可以模拟传动系统各部件的运动和相互作用,分析系统的振动、噪声和能耗等问题。
2. 强度分析强度分析是对传动系统的零部件进行强度计算和优化设计的过程。
通过有限元分析等方法,可以评估齿轮、链条和皮带等零部件的强度和疲劳寿命,确保传动系统在工作状态下的安全可靠性。
3. 效率仿真效率仿真是对传动系统的能量损失进行分析和优化的方法。
通过建立传动系统的功率流动模型,可以评估传动过程中的损失,根据仿真结果进行优化设计,提高传动系统的效率。
四、案例分析:汽车传动系统设计与仿真以汽车传动系统为例,进行设计与仿真分析。
在汽车传动系统中,齿轮传动、链传动和皮带传动等多种传动机构同时存在。
1. 齿轮传动设计根据汽车的需求,选择适当的齿轮材料和齿轮参数,如模数、齿数比等。
齿轮传动系统动力学性能仿真和应用

齿轮传动系统动力学性能仿真和应用1.概述近年来,齿轮传动系统的NVH、疲劳耐久性能分析面临巨大的挑战。
这个挑战的关键之一是如何高效、精确的模拟齿轮啮合的非线性动力学系统。
想要精确地建立变速箱多体动力学参数化模型往往是一个比较繁琐的过程。
通常需要几天甚至更长时间来准备模型,然后模拟齿轮系统非线性动力学,以获得变速箱系统实际工作过程的载荷,并使用预测的载荷进行系统的NVH、耐久性性能分析,从而进一步优化这些属性。
如图1所示,本文介绍了变速箱多体动力学建模工具Transmission Builder,它改变了CAE工程师建立变速器多体动力学仿真模型的传统方式,同时显著提高了建模效率。
西门子工业软件的开发团队在齿轮传动系统数值方法方面投入了大量的精力,设计了一种新的求解模块,使用户能够根据齿轮接触的三个不同精细化级别(标准、解析和高级)进行动态多体动力学仿真。
图1 基于Simcenter 3D Transmission Builder的变速箱多体动力学建模流程2. 背景:变速箱多体动力学仿真齿轮传动系统的基本部件是齿轮,轴承、轴及壳体。
研究表明,变速箱传递误差大约70%的能量损失发生在齿轮系,30%在轴承上。
因此,变速箱分析的主要的挑战在于如何以高效的方式模拟齿轮啮合以及整个系统的动力学特性。
通常,我们可以以三种方式进行变速箱的机械系统动力学仿真。
第一种,齿轮传动系统行业软件,其主要是针对变速箱的设计,这类软件集成了大量齿轮行业标准和经验公式,可用于设计过程的校核,但具有一定的局限性,比如说不能用于齿轮系统瞬态分析、不能考虑系统级特性、不能与1D仿真软件联合仿真等等;第二种方式是采用非线性有限元工具。
这种方式一方面计算成本太高,另外对于齿轮的某一些特性难以模拟,比如说轮齿微观修型、齿轮啮合表面油膜等;第三种方式是采用通用多体动力学仿真工具(比如说Simcenter 3D Motion),所建立的多体模型除了常规的多体动力学建模元素以外,必须包含精确的齿轮啮合力算法,以准确捕捉到齿轮非线性动力学产生的载荷,从而进一步分析齿轮传动系统的NVH以及结构耐久性能。
基于LS_DYNA的齿轮传动有限元动力学分析仿真

析计 算得 到 齿轮 副在模 拟 工 况下 的接 触应 力 变化 ,同时获得 在考 虑齿 轮接 触 、变形等情 况 下齿轮 传
动 系统输 入 和输 出的关 系.结果 表 明 ,后 传 动 输 出速 度 和 加 速度 明显 滞 后 于前传 动 产 生 的速递后 ,输入 使得 传 动更加 平稳.研 究 结果 可为进 一 步研 究齿轮 传 动 系统 的
.. .
W ANG Chao,SHAO Pengli
(Dept.of Whole Tech.,China North Vehicle Research Institute,Beijing 100072,China)
Abstract: To study the effects on gear stress, which is produced by the inertia m om ent of gear transmission system and the torsion vibration of transmission shaft, the finite element dynamics analysis and simulation are performed on a couple of involute spur gears in a gear transmission. Firstly,the CAD model of the gears is established by Pro/Engineering.Secondly,the model is imported into LS DYNA to
收 稿 日期 :2009—10-17 修 回 日期 :2009—12—01 作者 简介 :王 超(1984一 ),男,河北 高阳人 ,工程 师,硕 士,研 究方向为车辆 工程、计算机仿真 ,(E—mail)wangxlaochaoll@sina.corn;
- 1、下载文档前请自行甄别文档内容的完整性,平台不提供额外的编辑、内容补充、找答案等附加服务。
- 2、"仅部分预览"的文档,不可在线预览部分如存在完整性等问题,可反馈申请退款(可完整预览的文档不适用该条件!)。
- 3、如文档侵犯您的权益,请联系客服反馈,我们会尽快为您处理(人工客服工作时间:9:00-18:30)。
齿轮传动系统的动力学仿真分析
摘要:本文对建立好的整体机械系统的虚拟样机模型进行运动学和动力学的仿真分析,通过仿真分析,可以方便地得出齿轮传动系统在特定负载和特定工况下的转矩,速度,加速度,接触力等,仿真分析后,可以确定各个齿轮之间传递的力和力矩,为零件的有限元分析提供基础。
关键词:传动系统动力学仿真 adams 虚拟样机
中图分类号:th132 文献标识码:a 文章编号:
1007-9416(2011)12-0207-01
随着计算机图形学技术的迅速发展,系统仿真方法论和计算机仿真软件设计技术在交互性、生动性、直观性等方面取得了较大进展,它是以计算机和仿真系统软件为工具,对现实系统或未来系统进行动态实验仿真研究的理论和方法。
运动学仿真就是对已经添加了拓扑关系的运动系统,定义其驱动方式和驱动参数的数值,分析其系统其他零部件在驱动条件下的运动参数,如速度,加速度,角速度,角加速度等。
对仿真结果进行分析的基础上,验证所建立模型的正确性,并得出结论。
本文中所用的动力学仿真软件是adams软件。
adams软件使用交互式图形环境和零件库、约束库、力库,创建完全参数化的机械系统几何模型,其求解器采用多刚体系统动力学理论中的拉格郎日方程方法,建立系统动力学方程,对虚拟机械系统进行静力学、运动学和动力学分析,输出位移、速度、加速度和反作用力曲线。
adams
软件的仿真可用于预测机械系统的性能、运动范围、碰撞检测、峰值载荷以及计算有限元的输入载荷等。
虚拟样机就是在adams软件中建的样机模型。
1、运动参数的设置
先在造型软件ug中将齿轮传动系统造型好,如下图所示。
在已经设置好运动副的齿轮传动系统的第一级齿轮轴上绕地的旋转副上
给传动系统添加一个角速度驱动。
然后进行仿真。
在进行仿真的过程中,单位时间内仿真步数越多,步长越短,越能真实反映系统的真实结果,但缺点是仿真时间也随之变长,占用的系统空间也就越大。
所以应该在兼顾仿真真实性与所需物理资源和仿真时间的基础上,选择一个合适的仿真时间和仿真的步长。
在仿真之前先设置系统所用到的物理量的单位,在工程实际中,角速度一般使用的单位是r/min,所以在系统的基本单位中把时间的单位设为min,角度的单位设成rad,而在adams中转速单位为
rad/min。
本过程仿真的运动过程为:系统从加速运动到额定转速,平稳运动一段时间后,再减速运动直到停止。
运动过程用函数来模拟,输入的角速度驱动的函数表达式为:
step( time ,0 ,0 ,2.5 ,9168.8)+
step(time ,7.5 ,0 ,10 ,-9168.8),此函数表达式的含义为:系统从开始加速运动一直到2.5s时达到了系统的额定转速
9168.8rad/min(1460r/min),从2.5s到7.5s的时间段内,系统以额定转速运动,在7.5s到10s的时间段内,系统从额定转速减速
行使,直到停止。
打开adams,选择import a file,将测试数据输入到adams/view中。
2、模型验证
为了保证仿真分析的顺利进行,在进行仿真分析之前,应该对样机模型进行最后的检验,排除建模过程中隐含的错误。
一般样机模型容易出现的错误为:(1)检查不恰当的连接和约束、没有约束的构件、无质量构件、样机的自由度等。
(2)进行检查所有的约束是否被破坏或者被错误定义,通过装配分析有助于纠正错误的约束。
对于这些潜在的错误,用户可以充分利用adams/view提供的模型检查功能进行样机模型检测:(1)对于第一种可能的错误,用户可以利用模型自检工具。
(2)对于第二种可能的错误,用户可以进行装配分析。
adams/view提供了一个功能强大的样机模型自检工具,进入主菜,选择model verify命令,这时启动模型自检,完成自检后,程序显示自检对话框。
3、样机仿真
模型检验正确后,就可以进行仿真分析。
仿真的分析过程如下:
在主工具箱选择仿真工具图标,显示交互仿真分析参数设置栏;选择仿真类型,adams/view提供了4种仿真类型,即default、dynamic、kinematic和static。
本文就用default这种仿真类型;定义仿真分析时间,本次仿真时间为120秒;设置仿真过程中adams/view输出仿真结果的频率,选取仿真步长数为1000步。
完成以上设置后,开始仿真分析。
在仿真分析过程中,可实时显示样机的运动状况。
4、仿真结果及其分析
在仿真结束后,进入adams/postprocessor后处理模块,可以得到齿轮传动系统的动力学仿真结果曲线图,下图是齿轮1曲线图。
5、结语
以齿轮1和齿轮7为例(其它略),通过上表可以看到,各个啮合齿轮之间传递力的趋势与负载的趋势比较相似,都在14.1秒和73.95附近出现最大值,受力有很大的变化,最大力值为623050n,工作时所允许的范围之内。
在表中,“-”代表所受力的方向与系统默认的方向相反。
仿真结果的平均值与通过计算所得的理论值之间的差别不大,说明仿真结果比较真实的反映了实际的工作状态。
参考文献
[1]郑楷,胡仁喜等.adams2005机械设计高级应用实例.机械工业出版社,2006
[2]陈立平,张云清,任卫群等.机械系统动力学分析及adams应用
教程.清华大学出版社,2005.
[3]李志尊编著.ug nx4.0基础应用与范例解析.机械工业出版
社,2007.。