cnc钻攻中心钻孔编程【技巧】
加工中心钻深孔的编程方法

加工中心钻深孔的编程方法加工中心是一种能够进行多种加工操作的机床,它能够进行钻孔、铣削、切割等各种加工操作。
在加工中心钻深孔时,需要进行编程来控制加工过程。
下面将介绍一下加工中心钻深孔的编程方法。
手工编程是指操作员根据工艺要求和深孔钻的尺寸要求,手动输入程序进行编程。
手工编程需要操作员具备一定的加工经验和编程技术,在加工过程中需要根据具体要求进行调整和修正。
CAD/CAM编程是指通过计算机辅助设计(CAD)和计算机辅助制造(CAM)软件来进行深孔钻的编程。
操作人员首先使用CAD软件进行3D模型的设计,然后通过CAM软件进行加工路径的生成和刀具路径的优化,最后生成机床的加工程序。
CAD/CAM编程可以提高编程的精度和效率,减少操作员的工作量。
在编写加工中心钻深孔的程序时,需要注意以下几点:1.首先,确定深孔钻的参数,包括钻孔的直径、深度、切削速度、进给速度等。
这些参数需要根据具体的工件材料和加工要求来进行选择。
2.确定刀具的选择和安装方式。
深孔钻一般使用长钻杆和内冷却器,可以有效降低切削温度,提高加工质量。
3.编写切削路径。
切削路径应该保证刀具在钻削过程中的稳定性和最优切削条件。
一般来说,采用螺旋切削路径可以提高切削效率和加工质量。
4.设置冷却液的供给。
加工深孔钻时,需要通过内冷却液来降低钻头的温度,从而提高加工质量。
在编程过程中需要设置冷却液的供给时间和流量。
5.考虑加工中心的刀库和刀具切换。
在进行复杂零件的加工时,可能需要多次换刀。
在编写程序时要考虑到刀具的切换和切换点的选择,以避免刀具碰撞或者加工误差。
总结来说,编写加工中心钻深孔的程序需要根据具体的工艺要求和机床的特点来进行选择。
手工编程和CAD/CAM编程是两种常用的方法,都需要考虑到刀具选择、切削路径、冷却液的供给等因素。
通过合理的编程,可以提高加工效率和产品质量。
加工中心钻深孔的编程方法

加工中心钻深孔的编程方法首先,加工中心钻深孔的编程需要采用G代码进行控制,因此需要编写相应的G代码程序。
编程主要分为几个步骤。
第一步是确定钻孔顺序。
在编程的过程中,需要确定钻孔的顺序,即先钻哪些孔,后钻哪些孔。
这取决于工件的几何形状和孔的位置。
通常,可以按照从外到内、从上到下的方式确定钻孔顺序,以便保证加工的稳定性和高效性。
第二步是确定切削参数。
在编程之前,需要事先确定切削参数,包括切削速度、进给速度和切削深度等。
这些参数的选择需要根据工件材料和加工要求来确定。
切削参数的选择直接影响着钻孔的质量和加工效率。
第三步是确定坐标系。
在编程之前,需要确定加工中心的坐标系,以便编写相应的G代码程序。
加工中心的坐标系通常是以工件的一些参考面或参考点为基准建立的。
编程时,需要将钻孔的坐标位置进行转换,使其与加工中心的坐标系一致。
第四步是编写G代码程序。
编写G代码程序是将加工过程指令转换为机床能够理解和执行的代码。
编写G代码程序时,需要按照加工顺序和切削参数依次编写相应的G代码指令。
一般情况下,每一个钻孔都对应着一段G代码程序,包括进给指令、刀具选取指令等。
在编程过程中1.确保钻孔参数正确。
切勿将错误的参数输入到程序中,否则会影响钻孔的质量和加工效果。
2.合理选择进给方式。
对于较深的孔,进给方式选用螺纹进给能够提高加工效率和孔的质量。
3.考虑切削液的使用。
在加工过程中,可以适当使用切削液,以降低切削温度、延长工具寿命和提高加工质量。
总之,加工中心钻深孔的编程方法主要包括确定钻孔顺序、确定切削参数、确定坐标系和编写G代码程序。
编程的准确性和合理性直接影响着钻孔的质量和加工效率。
因此,对于加工中心钻深孔的编程,需要严谨认真地进行,确保编程参数和程序的准确性和合理性。
加工中心钻孔编程实例

加工中心钻孔编程实例一、前言加工中心钻孔编程是数控加工中的重要部分,其精度和效率直接影响到产品的质量和生产效率。
本文将结合实例,详细介绍加工中心钻孔编程的步骤和注意事项,以便读者更好地理解和应用。
二、编程前准备1.选择合适的刀具:根据钻孔直径、深度、材料等因素选取合适的刀具。
2.确定坐标系:加工中心有多种坐标系,如绝对坐标系、相对坐标系等。
在编程前需要确定使用哪种坐标系。
3.测量工件:测量工件尺寸和位置,以便正确设置初始点和结束点。
三、编程步骤1.设置初始点:在程序开头设置起始点,一般为工件表面上方一定距离处。
可以使用G90指令将机床坐标系设为绝对坐标系,在G代码开头使用G00指令快速移动到起始点。
2.设定进给速度:使用F指令设定进给速度,一般根据材料硬度等因素进行调整。
例如:F2000表示进给速度为2000mm/min。
3.设定钻孔深度:使用G81指令设定钻孔深度,例如:G81 X50 Y50 Z-20 R2 F2000表示在X50 Y50处开始钻孔,深度为20mm,进给速度为2000mm/min,R2表示快速进刀距离。
4.设定结束点:使用G80指令设定结束点,例如:G80 X50 Y50 Z5表示在X50 Y50处结束钻孔,Z5表示离工件表面5mm处。
5.重复钻孔:使用M98指令进行循环操作,例如:M98 P100 L10表示执行程序号为100的子程序10次。
6.结束程序:使用M30指令结束程序。
四、注意事项1.刀具选择要合适。
2.坐标系要正确设置,并根据需要进行转换。
3.测量工件尺寸和位置要准确。
4.进给速度要根据材料硬度等因素进行调整。
5.钻孔深度要控制好,避免过深或不足。
6.循环次数要根据实际需要进行设置。
7.编程前应先进行模拟验证,确保程序正确无误后再进行加工操作。
加工中心钻深孔的编程方法

加工中心钻深孔的编程方法加工中心是一种多功能的数控机床,能够进行多种加工操作,包括钻孔。
钻深孔是指钻孔深度较大的孔径。
进行钻深孔加工的编程方法需要考虑到以下几个方面。
首先,需要确定孔径和孔深。
在进行编程之前,需要明确要加工的钻孔的孔径和孔深。
这是编程的基础,也是后续计算加工参数和路径的依据。
其次,需要计算切削参数。
切削参数包括主轴转速、进给速度和切削进给量等。
主轴转速的选择需要考虑材料的硬度和刀具的耐用性。
进给速度的选择需要考虑加工的效率和表面质量。
切削进给量的选择需要考虑刀具和工件的强度和刚性等因素。
然后,需要选择合适的刀具。
钻深孔加工需要选择合适的直柄钻头或深孔钻头。
钻头的选择需要考虑到孔径和孔深,以及材料的硬度和加工精度等因素。
较大的孔径和较深的孔深通常需要较长的钻头和更大的冷却液流量。
接着,需要编写加工程序。
钻深孔加工的编程方法通常有两种:点位编程和插补编程。
点位编程是指根据孔径和孔深,计算每个点的坐标并依次钻孔。
插补编程是指根据加工路径和切削参数,通过插补运动产生连续的切削轨迹。
点位编程适用于简单的孔径和孔深,而插补编程适用于复杂的孔形和大批量的钻深孔加工。
最后,需要进行程序验证和优化。
在进行实际加工之前,需要通过模拟和仿真等方法对加工程序进行验证。
在验证过程中,需要检查加工轨迹、切削参数和表面质量等方面是否满足要求。
如果存在问题,需要及时进行调整和优化。
总之,钻深孔的编程方法需要综合考虑孔径和孔深、切削参数、刀具选择、加工程序编写和程序验证等因素。
只有在充分理解和合理运用这些方法的基础上,才能有效地进行钻深孔加工。
加工中心钻孔程序的编制

加工中心的典型程序编制来源:数控产品网添加:2008-08-12 阅读:276次[ 内容简介 ]钻孔程序的编制1.钻孔程序的编制如图1,沿任意一条直线钻等距的孔。
若使用配备FANUC-6M系统的立式加工中心,则加工程序如下:图1 沿直线钻等距孔O1000N10 G92 X400.0 Y300.0 Z320.0 建立加工坐标系N20 M06 T00 换上中心钻N30 G90 G00 X0 Y0 X、Y向定位N40 Z0 Z向定位N50 M03 S500 F30 主轴启动N60 G81 G99 R-4.0 Z-10.0 钻深为5mm的中心孔N70 G91 G00 X20.0 Y10.0 L03 重复3次钻3中心孔N80 M05 主轴旋转停止N90 G28 Z0 经加工原点回机床原点N100 M06 T01 换钻孔刀,返回加工点NIl0 M03 G90 G00 G44 H01 G81 G99 R-5.0 Z-30.0 钻第一个孔,加刀具补偿N120 G91 X-20.0 Y-10.0 L03 重复钻3次孔N130 M05 G28 G49 Z320.0 撤消刀具长度补偿回Z轴N140 M01 参考点N150 M99 P20 返回到N20程序段程序的特点:1)使用G92建立加工坐标系,坐标系的偏置量在程序中进行设置,修改调整更方便。
2)有两次自动换刀,并使用刀具长度补偿,体现加工中心自动加工的功能。
机床起动后主轴上装的是F 10钻头刀具,刀库的零号刀位上应安装有中心钻。
因整个程序只用两把刀,刀库不用转动,原地换刀就可以了。
3)使用中心钻(N60程序段)预钻定位孔,使孔定位准确。
4)使用相对值指令(N70,N120)给出了孔的位置,使固定循环功能重复使用,直到把孔全部钻完。
L03为重复次数。
5)使用了M01(N140)程序暂停。
注意:使用M01时操作面板上的程序暂停开关应放到接通位置,这样在程序执行到M01时面板上的指示灯燃亮,告诉操作者程序处于任选停止,可以装卸零件,待处理工作结束时按循环起动按钮,程序接着执行。
CNC加工中的数控编程方法与技巧
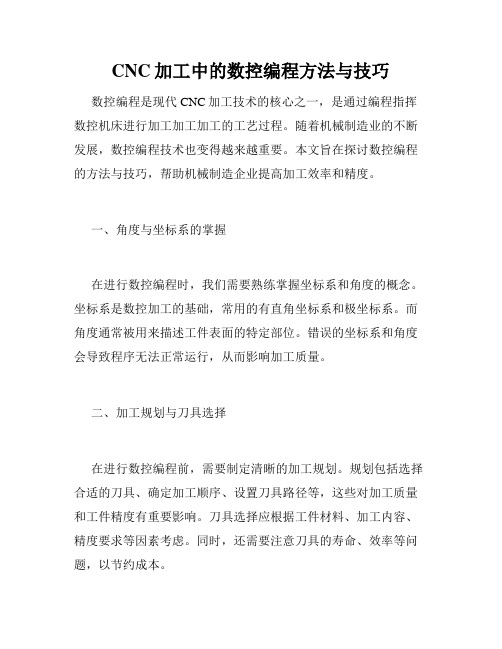
CNC加工中的数控编程方法与技巧数控编程是现代CNC加工技术的核心之一,是通过编程指挥数控机床进行加工加工加工的工艺过程。
随着机械制造业的不断发展,数控编程技术也变得越来越重要。
本文旨在探讨数控编程的方法与技巧,帮助机械制造企业提高加工效率和精度。
一、角度与坐标系的掌握在进行数控编程时,我们需要熟练掌握坐标系和角度的概念。
坐标系是数控加工的基础,常用的有直角坐标系和极坐标系。
而角度通常被用来描述工件表面的特定部位。
错误的坐标系和角度会导致程序无法正常运行,从而影响加工质量。
二、加工规划与刀具选择在进行数控编程前,需要制定清晰的加工规划。
规划包括选择合适的刀具、确定加工顺序、设置刀具路径等,这些对加工质量和工件精度有重要影响。
刀具选择应根据工件材料、加工内容、精度要求等因素考虑。
同时,还需要注意刀具的寿命、效率等问题,以节约成本。
三、编程语言的选择与使用目前常用的数控编程语言有G代码和M代码。
G代码一般用于定义加工轨迹和刀具路径,而M代码则用于指示机床的功能和特定操作。
正确使用编程语言可有效提高程序运行的效率和精度。
四、边缘刀路算法的运用边缘刀路算法是指在数控加工中使用稳健的算法来定义切削轮廓。
这种算法可以使得工件表面的光洁度更高、光滑度更好。
边缘刀路算法适用于不同形状的工件,对于需要进行光洁度检测的工件尤其重要。
五、进给率和转速的控制进给率和转速是影响加工效率和精度的两个重要因素。
进给率过高会导致刀具磨损过快,精度下降,而进给率过低则会使得加工周期长、效率低下。
转速过高则会损耗刀具。
因此,合理控制进给率和转速非常重要。
六、切削力的控制切削力是数控加工过程中必须考虑的关键因素之一。
高强度材料的加工通常需要更高的切削力,为了避免切削过度,需要使用切削力控制系统。
控制切削力可以有效提高加工效率和精度,同时还可以降低能源消耗。
总之,数控编程技术是机械制造工业的发展趋势,正确的数控编程方法和技巧可以提高加工效率、降低成本、提高工件精度。
CNC机床加工中的加工中心的编程与操作技巧

CNC机床加工中的加工中心的编程与操作技巧CNC机床是现代制造业中一种非常重要的设备,它使用计算机数控技术,能够高效、精确地进行加工。
而在CNC机床中,加工中心更是一种非常常见且功能强大的设备,具备多轴控制、多刀具切削能力,能够实现复杂零部件的高速、高精度加工。
在加工中心的编程与操作中,掌握一些技巧是非常重要的。
本文将介绍一些CNC机床加工中心的编程与操作技巧,希望对读者有所帮助。
一、了解加工中心的基本结构与工作原理在编程与操作加工中心之前,首先需要对加工中心的基本结构与工作原理有所了解。
加工中心主要由机床主体、控制系统、夹具系统、刀具系统等组成。
了解加工中心的基本构造,对于编程与操作会有很大的帮助。
二、熟悉加工中心编程语言加工中心的编程语言通常采用G代码,需要熟悉G代码的基本语法与功能。
例如,G01表示直线插补,G02表示圆弧插补,G04表示暂停,等等。
了解G代码的基本指令,能够正确编写程序,提高加工效率。
三、合理设置刀具补偿在编程过程中,需要合理设置刀具补偿。
刀具补偿可以根据具体的切削条件来进行设置,不同的刀具补偿参数会影响加工精度和表面质量。
熟悉刀具补偿的设置,能够使加工效果更好。
四、注意加工过程中的切削参数在进行加工中心的编程与操作时,需要注意切削参数的选择。
切削参数包括切削速度、进给速度、切削深度等。
合理设置切削参数,能够提高加工效率,同时保证加工质量。
五、注意加工中心的安全操作在进行加工中心的编程与操作时,需要注意安全操作。
操作人员应该熟悉机床的安全操作规程,佩戴相关的个人防护装备,并严格按照操作规程进行操作。
保证人员的安全是非常重要的。
六、加工中心编程与操作中的常见问题及解决方法在加工中心的编程与操作中,常会遇到一些问题,例如机床刀具的选择、工件夹紧方式的选择、切削参数的合理设置等。
针对这些常见问题,需要有相应的解决方法。
在实际操作中,运用正确的方法能够解决问题,并提高加工效率。
本文介绍了一些CNC机床加工中心的编程与操作技巧。
加工中心的孔加工编程及技巧
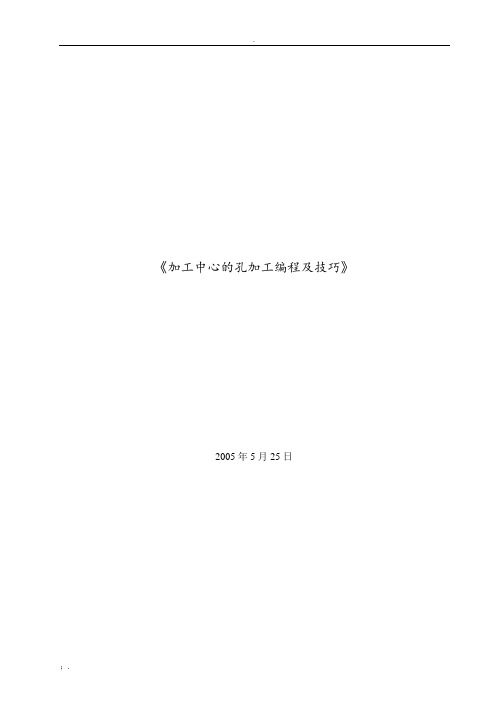
.《加工中心的孔加工编程及技巧》2005年5月25日加工中心的孔加工编程及技巧摘要:孔加工在数控加工中一直占有重要的地位,如何在加工过程中按照合理的工艺编制出正确的加工程序是非常关键的因素。
关键词:孔加工固定循环子程序极坐标一、引言孔加工在数控加工中一直占有重要的地位。
在合理的加工工艺编制好以后如何编制出正确的程序将直接影响到工件是否加工合格。
复杂的孔加工将用到数控系统中的许多功能。
诸如:孔加工固定循环、子程序、极坐标、坐标旋转等。
因此,如何将这些指令灵活应用在加工的程序中将直接关系到程序的合理性。
二、应用实例下面就以一个定位连接板(图1)作为实例,介绍该类程序的编制及技巧。
1、技术要求:1)零件材料:灰铸铁HT2002)加工部位:加粗部分(φ110,2-φ70H7),8-M12深15,18-φ13深20。
3)加工说明:φ70H7预孔为铸造,余量5mm。
基准面A、B、C、D前工序已完成。
夹具形式不用考虑,φ110孔用铣削方式。
4)数控机床:立式加工中心VMC800;数控系统:FANUC 0iM5)按数控工序卡片编制加工中心程序。
6)程序编制方法:固定循环、子程序、坐标系旋转、极坐标指令等图1 定位连接板2、加工工艺夹具3、加工程序主程序O0001;第0001号程序,加工主程序G90G00G55X80.0Y80.0;建立工件坐标系,并运动到φ70H7孔的中心位置N10T02M6;调用02号刀具(粗镗φ69.7)G43H02Z100.0;刀具长度正补偿,并运动到安全高度M03S380;主轴正转M08;打开冷却液G98G86Z-45.0R3.0F95;调用粗加工固定循环加工φ70H7孔至φ69.7X280.0 Y180.0;在X280.0Y180.0位置继续加工G80;取消固定循环N20T03M6;调用03号刀具(φ40立铣刀铣φ110孔)G00X280.0Y180.0;快速定位到φ110孔的中心位置G43H03Z100.0;刀具长度正补偿,并运动到安全高度M3S420;主轴正转G01Z-14.6F2000;下刀至第一次的深度位置(粗加工)M98P0501;调用0501号子程序G01Z-14.8F2000 S560;下刀至第二次的深度位置(半精加工)M98P0501;调用0501号子程序M01;检查尺寸14.8。
数控机床钻孔加工技巧分享

数控机床钻孔加工技巧分享在数控机床加工过程中,钻孔是一项基础而重要的工艺,因此掌握钻孔加工技巧对于提高加工效率和产品质量至关重要。
本文将分享数控机床钻孔加工的技巧,帮助读者更好地理解和掌握这一加工过程。
首先,在进行数控机床钻孔加工之前,我们需要对钻头的选用有所了解。
钻头的选用应根据加工材料来决定,通常有高速钢钻头、硬质合金钻头和多刃钻头等。
高速钢钻头适用于加工一般材料,硬质合金钻头适合较硬的材料,多刃钻头则适用于提高加工效率。
正确选择合适的钻头可以有效提高加工质量和效率。
接下来是机床设备的设置。
在进行钻孔加工之前,我们需要根据加工要求合理设置机床参数,包括转速、进给速度和切削深度等。
转速和进给速度的设置要考虑到材料硬度、钻头尺寸和加工要求等因素,合理的设置可以避免刀具磨损和加工品质下降。
切削深度的设置应适当,过大会增加振动和断刀的风险,过小则会降低加工效率。
钻孔加工过程中需要注意钻孔位置和定位。
对于多个钻孔的加工,我们首先要确定钻孔的位置,并通过工件的定位来保持钻孔的准确度。
通过合理设置机床坐标和夹具,确保工件在加工过程中不会发生位移或晃动,从而保证钻孔位置的准确性和一致性。
辅助设备的使用也是数控机床钻孔加工中需要注意的一点。
例如,使用冷却液可以降低切削温度,减少切削力和热变形的发生,从而提高钻孔质量和延长刀具寿命。
同时,冷却液也可以去除加工过程中产生的切屑,保持钻孔的清洁。
另外,合理的工艺策略也是提高钻孔加工效率的重要因素。
根据加工材料的不同,我们可以选择不同的工艺策略,如快进斜入、快进快出、快进慢进等。
快进斜入适用于较硬的材料,可以减少刀具磨损;快进快出适用于薄壁材料,可以减少切削负荷;快进慢进则适用于提高钻孔加工质量和表面光洁度。
选择适合的工艺策略可以极大地提高钻孔加工效率和质量。
最后,维护刀具和设备的常规保养也不能忽视。
定期检查和更换刀具可以避免刀具磨损和断裂,提高钻孔加工效果。
同时,定期清洁和润滑机床设备,保持机床的正常运行状态,也是保证钻孔加工质量和稳定性的重要保障。
数控加工--钻孔循环指令
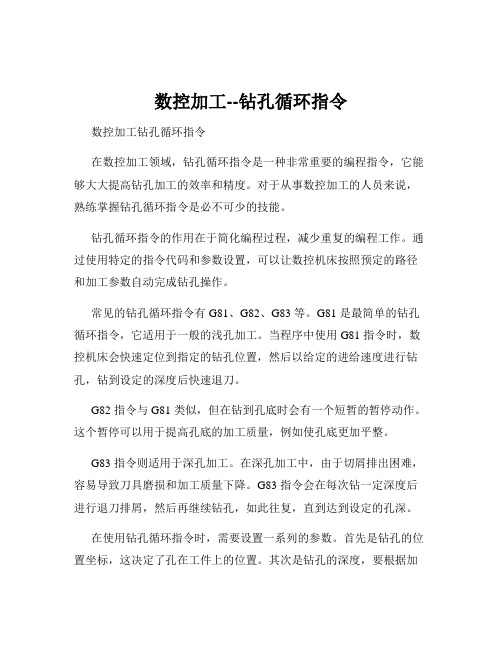
数控加工--钻孔循环指令数控加工钻孔循环指令在数控加工领域,钻孔循环指令是一种非常重要的编程指令,它能够大大提高钻孔加工的效率和精度。
对于从事数控加工的人员来说,熟练掌握钻孔循环指令是必不可少的技能。
钻孔循环指令的作用在于简化编程过程,减少重复的编程工作。
通过使用特定的指令代码和参数设置,可以让数控机床按照预定的路径和加工参数自动完成钻孔操作。
常见的钻孔循环指令有 G81、G82、G83 等。
G81 是最简单的钻孔循环指令,它适用于一般的浅孔加工。
当程序中使用 G81 指令时,数控机床会快速定位到指定的钻孔位置,然后以给定的进给速度进行钻孔,钻到设定的深度后快速退刀。
G82 指令与 G81 类似,但在钻到孔底时会有一个短暂的暂停动作。
这个暂停可以用于提高孔底的加工质量,例如使孔底更加平整。
G83 指令则适用于深孔加工。
在深孔加工中,由于切屑排出困难,容易导致刀具磨损和加工质量下降。
G83 指令会在每次钻一定深度后进行退刀排屑,然后再继续钻孔,如此往复,直到达到设定的孔深。
在使用钻孔循环指令时,需要设置一系列的参数。
首先是钻孔的位置坐标,这决定了孔在工件上的位置。
其次是钻孔的深度,要根据加工要求准确设定。
进给速度也是重要的参数之一,它直接影响加工效率和表面质量。
此外,还有主轴转速、刀具半径补偿等参数需要根据实际情况进行合理设置。
正确设置钻孔循环指令的参数对于保证加工质量至关重要。
如果进给速度过快,可能会导致刀具磨损加剧,甚至折断刀具;如果进给速度过慢,则会降低加工效率。
钻孔深度的设置如果不准确,可能会导致孔深不足或过深,影响工件的使用性能。
为了更好地理解和应用钻孔循环指令,我们可以通过一个实际的编程示例来进行说明。
假设要在一块金属板上钻一个直径为 10mm、深度为 20mm 的孔,使用 G81 指令进行编程,代码可能如下:N10 G90 G54 X50 Y50 ;选择绝对坐标,设定工件坐标系N20 S1000 M03 ;设定主轴转速为 1000r/min,正转N30 G00 Z50 ;快速移动到安全高度N40 G81 R3 Z-20 F100 ;执行钻孔循环,R3 表示安全距离为 3mm,F100 表示进给速度为 100mm/min在实际编程中,还需要根据机床的性能和加工要求进行适当的调整和优化。
CNC机床加工中的数控编程技巧

CNC机床加工中的数控编程技巧数控编程是现代数控机床加工中的关键环节,它涉及到加工的效率和准确性。
在CNC机床加工中,掌握一些数控编程技巧对于提高生产效率和质量至关重要。
本文将探讨数控编程的一些技巧和注意事项,以帮助读者更好地应对CNC机床加工中的挑战。
一、合理使用G代码和M代码G代码和M代码是数控编程中常用的指令集,它们用于控制机床的运动和功能。
合理使用这些代码能够提高加工效率和准确性。
首先,对于重复性高的工序,可以采用宏指令来简化编程过程,减少代码量;其次,尽量避免过于复杂的G代码连续使用,以免影响机床的运行稳定性;最后,选择合适的M代码来实现所需的机床功能,确保加工过程的顺利进行。
二、合理安排刀具路径在数控编程中,刀具路径的合理安排对于加工效率和表面质量有着重要影响。
首先,应根据零件的形状、大小和加工要求等因素来选择合适的切削顺序,尽量减少空程运动和换刀次数,以提高加工效率;其次,在进行连续切削时,要注意刀具路径的平滑性和一致性,避免出现急转弯和重复加工等问题;最后,对于表面要求较高的零件,可以采用多次切削和不同刀具的组合,以提高表面质量。
三、注意切削参数的选择切削参数的选择直接影响到加工效率和零件质量。
在数控编程中,应根据材料性质、机床能力和刀具状况等因素,选择合适的切削速度、进给速度和切削深度等参数。
同时,要根据加工过程中的实际情况进行调整和优化,以达到最佳的切削效果。
此外,还要合理选择冷却液的使用方式和冷却液的喷射位置,以保证加工过程的稳定性和零件的质量。
四、严格控制尺寸精度和位置精度在数控编程中,尺寸精度和位置精度是加工质量的重要指标。
为了保证零件的尺寸和位置精度,应在编程过程中严格控制各个刀具的补偿值和工件坐标系的设定。
此外,还要合理安排测量点和测量方式,及时对加工过程中出现的误差进行修正和调整。
五、科学进行刀具刀径补偿刀具刀径补偿是数控编程中常用的功能之一,它可以在刀具运动过程中自动补偿刀具半径误差,提高加工质量和精度。
加工中心钻深孔的编程方法

加工中心钻深孔的编程方法1.确定孔的加工路径及其坐标系。
首先,需要明确孔的加工深度、直径和坐标系。
然后,根据机床的坐标系和工件的位置,确定加工路径和各个加工点的坐标。
2.选择切削工具。
根据工件材料和孔的直径选择合适的刀具。
同时,还需要确定切削参数,如进给速度、切削速度和切削深度等。
3.编写程序。
根据孔的直径和深度,依次编写孔的加工路径和每个点的坐标。
在编写程序时,需要考虑刀具的进给方向和刀具补偿等因素。
4.调试程序。
在进行实际加工之前,需要通过模拟或手动控制机床,检查程序的正确性。
如果发现问题,可以根据需要进行修改和调整。
自动编程是指利用专门的软件工具进行编程,通过输入工件的几何参数和加工要求,自动生成深孔钻加工的程序。
这种编程方法适用于大批量生产和复杂孔的加工。
1.创建工件模型。
首先,需要使用三维建模软件创建工件的几何模型。
模型的几何参数和加工特征应符合实际要求。
2.设置加工参数。
根据工件材料和切削工具的选择,设置加工参数,如切削速度、进给速度和切削深度等。
3.选择加工策略。
根据孔的直径和深度,选择合适的加工策略,如螺旋加工、分层加工或多通道加工等。
4.生成刀具路径。
根据工件模型、加工参数和加工策略,利用专门的加工软件生成刀具路径。
在生成路径时,软件会自动考虑刀具的进给方向、补偿和退刀等因素。
5.优化路径。
生成刀具路径后,可以对路径进行优化,消除重复移动和减少加工时间。
此外,还可以进行干涉检查,确保刀具在加工过程中不会与工件发生碰撞。
6.输出程序。
最后,将生成的程序输出到机床控制系统中,并进行加工。
在加工过程中,可以随时对程序进行调整和修改。
总的来说,手工编程适用于简单孔的加工和小批量生产,而自动编程适用于大批量生产和复杂孔的加工。
无论采用哪种编程方法,都需要根据工件要求和切削工具选择合适的加工参数,并严格进行程序调试和检查,以确保加工质量和效率。
数控钻床加工编程方法及操作

数控钻床加工编程方法及操作一、数控钻床加工编程方法及操作步骤:1.确定工件的加工要求和图纸,了解工件的尺寸、材质和加工工艺等。
2.根据工件要求,在CAD软件中进行工件的三维建模。
3.运用CAM软件,将三维建模数据转换为数控机床可识别的G代码。
4.将G代码保存在U盘或其他存储介质中。
5.将存储介质插入数控钻床的编程口,启动数控钻床。
6.在数控钻床上输入程序号或文件名,加载G代码。
7.检查数控钻床参数的设置,如主轴转速、进给速度、切削冷却液开关等。
8.使用机床上的控制台或触摸屏,调整加工过程中的各项参数,如切削速度、进给量、刀具半径补偿等。
9.进行手动运行,检查刀具路径和加工过程,确保没有碰撞和误操作。
10.完成手动运行后,进行自动运行,开启自动加工模式。
11.实时监控并调整加工过程中的参数,保持加工质量。
12.完成加工后,打印或保存加工记录。
二、数控钻床加工编程方法及操作的注意事项:1.在进行数控钻床加工编程之前,需要熟悉数控钻床的操作、编程和安全规范等知识。
2.在编写G代码时,要注意准确描述刀具的路径、切削深度和补偿等参数。
3.在加载G代码之前,要确保数控钻床的参数设置正确,并进行必要的校正。
4.在操作数控钻床时,要细心观察切削情况和加工状态,及时调整参数以保证加工质量。
5.在手动运行和自动运行之前,要仔细检查刀具路径、工件夹持和切削液等,确保安全无误。
6.在加工过程中,要注意及时更换刀具和切削液,以保持切削效果和工具寿命。
7.加工完成后,要对加工过程进行总结和记录,以备后续参考和改进。
数控钻床是一种高精密的机床,通过上述的编程方法及操作步骤,可以实现各种工件的高效、精密加工。
但是需要注意的是,不同型号的数控钻床可能有略微不同的操作方式和参数设置,因此在具体操作时,需要参考数控钻床的操作手册和相关资料,以确保正确、安全地进行加工操作。
数控车床的孔加工编程方法举例
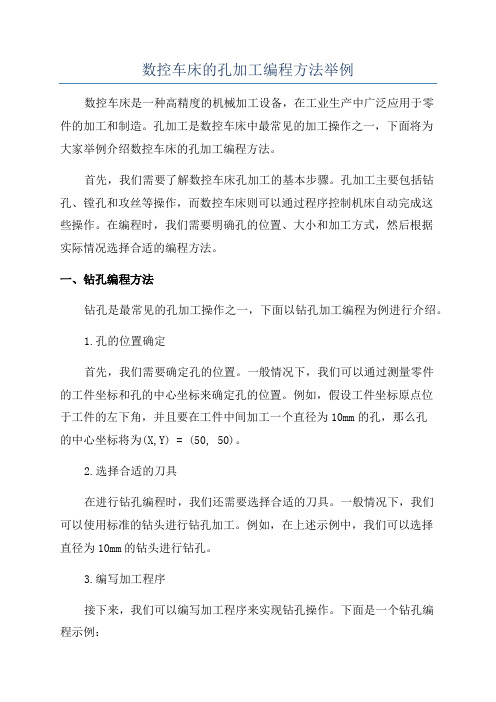
数控车床的孔加工编程方法举例数控车床是一种高精度的机械加工设备,在工业生产中广泛应用于零件的加工和制造。
孔加工是数控车床中最常见的加工操作之一,下面将为大家举例介绍数控车床的孔加工编程方法。
首先,我们需要了解数控车床孔加工的基本步骤。
孔加工主要包括钻孔、镗孔和攻丝等操作,而数控车床则可以通过程序控制机床自动完成这些操作。
在编程时,我们需要明确孔的位置、大小和加工方式,然后根据实际情况选择合适的编程方法。
一、钻孔编程方法钻孔是最常见的孔加工操作之一,下面以钻孔加工编程为例进行介绍。
1.孔的位置确定首先,我们需要确定孔的位置。
一般情况下,我们可以通过测量零件的工件坐标和孔的中心坐标来确定孔的位置。
例如,假设工件坐标原点位于工件的左下角,并且要在工件中间加工一个直径为10mm的孔,那么孔的中心坐标将为(X,Y) = (50, 50)。
2.选择合适的刀具在进行钻孔编程时,我们还需要选择合适的刀具。
一般情况下,我们可以使用标准的钻头进行钻孔加工。
例如,在上述示例中,我们可以选择直径为10mm的钻头进行钻孔。
3.编写加工程序接下来,我们可以编写加工程序来实现钻孔操作。
下面是一个钻孔编程示例:O0001(程序号)N1G90G54G64G80(绝对坐标系,工件坐标系,等距插补模式,取消固定循环)N2S500M3(设置主轴转速为500转/分钟,开启主轴)N3G0X50Y50(快速定位到孔的中心坐标)N4 G81 Z-10 R2 F100 (启动钻孔循环,Z轴下降10mm,每次进刀2mm,进给速度为100mm/分钟)N5G80(取消固定循环)N6M5(关闭主轴)N7M30(程序结束)在上述示例中,首先通过G90指令设置绝对坐标系和工件坐标系。
然后通过G64指令设置等距插补模式,取消固定循环。
接着,通过G0指令进行快速定位,将刀具移动到孔的中心坐标处。
然后通过G81指令启动钻孔循环,设置Z轴下降10mm,每次进刀2mm,进给速度为100mm/分钟。
加工中心钻深孔的编程方法

加工中心钻深孔的编程方法加工中心是一种可以进行多种加工操作的机床,其中包括钻深孔。
钻深孔是指在工件上钻一个较深的孔洞,用以满足特定的工件要求。
编程方法是指如何通过编写程序来实现钻深孔的操作。
首先,编程方法需要考虑以下几个方面:1.选择合适的刀具:根据所需孔洞的直径和深度,选择合适的钻头。
钻头的直径应适合于孔洞的大小,并具有足够的刚性和强度来完成钻孔操作。
2.清洁工件:在进行钻深孔之前,必须确保工件表面的杂质和油脂已经清除干净。
这可以通过使用清洁剂和刷子来完成。
3.设置工件:将工件安装到加工中心上,确保其位置稳定和准确。
在这个过程中,可以使用夹具、定位销和卡盘等工具来帮助固定工件。
4.设置工件坐标系:根据所需的钻孔位置和孔洞的尺寸,设置工件坐标系。
这可以通过加工中心的坐标系设定功能来完成。
5.编写程序:编写程序时,需要指定钻孔的位置、深度和速度。
加工中心通常提供了相应的指令或宏指令来完成这些操作。
这些指令应该根据实际要求进行调整。
下面是一个简单的示例程序,用来说明钻深孔的编程方法:```N10G90G54G17;绝对坐标系选择,工件坐标系选择,XY平面选择N20T1M6;切换钻头,执行刀具长度补偿N30S1000M3;设置主轴转速,主轴旋转方向N40G0X20Y20;快速移动到孔洞位置N50G1Z-50F500;沿Z轴插补下降到孔洞深度N60G0Z5;提升刀具离开表面N70G0X0Y0;快速移动到起始位置N80M30;程序结束```在这个示例程序中,N10至N80是程序的行号,用于程序控制。
G90指令选择了绝对坐标系,G54指令选择了工件坐标系,G17指令选择了XY平面。
T1指令切换到了1号钻头,M6指令执行了刀具长度补偿。
S1000M3指令设置了主轴转速和旋转方向。
G0和G1指令用于快速移动和插补操作。
Z-50指令下降50mm到达孔洞深度,F500指定了下降速度。
G0 Z5指令将刀具提升5mm离开表面。
数控车床的孔加工编程方法举例

数控车床的孔加工编程方法举例对于孔加工,不同的数控机床有不同的指令。
本机床孔加工所使用的指令为直线插补指令G01,下面以下图为例说明孔加工的编程方法。
设一号刀为外圆刀,二号刀为©3mn钻头,三号刀为切断刀,四号刀为© 16mm钻头,六号刀为镗刀。
毛坯为©53mmX100mi的棒料。
选取工件轴线与工件右端面的交点0为坐标原点,其加工设一号刀为外圆刀,二号刀为©3mm钻头,三号刀为切断刀,四号刀为©16mm钻头,六号刀为镗刀。
毛坯为©53mmX100m的棒料。
选取工件轴线与工件右端面的交点0为坐标原点,其加工程序为:N0I G50 X150. Z200.;N02 M03 S800 T0101 ;N03 G00 X55. Z0 ;N04 G01 X0 F0.4 ;N05 G00 Z2.0 ;N06 X50.;N07 G01 Z-73. F0.4;N08 G00 X52.Z2.,N10 G01 2-45. F0.3N11 G02 X50. Z-50. R5.N12 G00 X55. Z1. ;N13 X34. ;N14 G01 X40.Z-2.F0.4;N15 G00 X150. Z200. T0100 ;N16 M03 S1500 T0202 ;N16 M03 S1500 T02 ;N17 GOO X0 Z2.;N18 G01 Z-4. F0.12N19 G00 Z2. ;N20 X150. Z200. T0200 ;N21 M03 S500 T0404 M08;N22 G00 XO 22. ;N23 G01 W-15. F0.12 ;N24 G00 W5. ;N25 G01 W-15. F0.12;N26 GOOW5.;N27 G01 W-15. F0.12N28 G00 W5. ;N29 G0l W-10. F0.12;N30 GOOW40;.N31 M09;N32 GOO X150. Z200. T0400 ;N33 X18. Z2. T0606 M08;N34 G01 Z-30. S1000 FO.1 ;N35 GOO X16.;N36 Z2. ;N37 X20. ;N38 G01 Z-30. FO.1;N39 GOO X18.;N40 Z2. ;N41 X22.;N42 G01 Z0 FO.3 ;N43 X20. Z-1.N44 GOO Z2.;N45 X150. Z200. T0600;N46 GOO X52. Z-70. S500 T0303 ;N47 G01 X0 FO.15;N48 GOO X55.;N49 X150. Z200. ;N50 M09;N51 M30;。
数控钻攻铣一体机编程教程

数控钻攻铣一体机编程教程数控钻攻铣一体机是一种多功能的机床,可以实现多种加工方式,如钻孔、攻丝、铣削等。
通过编程控制,可以实现高效、精确的加工,提高生产效率。
本教程将介绍数控钻攻铣一体机的编程基础和常用功能,帮助读者掌握数控编程技能。
1. 数控编程基础在使用数控钻攻铣一体机进行加工之前,首先需要了解数控编程的基础知识。
数控编程是通过输入一系列指令来控制机床进行加工操作的过程。
每条指令包含了加工的参数信息,如加工速度、进给速度、刀具转速等。
常用的数控编程语言包括G代码和M代码。
1.1 G代码G代码是表示加工操作的指令代码,包括不同的功能,如移动、切削、进给等。
常用的G代码指令包括:•G00:快速移动•G01:直线插补•G02/G03:圆弧插补•G20/G21:英制/公制单位1.2 M代码M代码是表示机床辅助功能的指令代码,如开启冷却系统、换刀、停止等。
常用的M代码指令包括:•M03:主轴正转•M05:主轴停止•M08:冷却系统开启•M09:冷却系统关闭2. 数控钻攻铣一体机编程示例下面通过一个简单的示例介绍数控钻攻铣一体机的编程过程。
假设我们要进行一个直线钻孔操作,首先定义加工坐标和加工参数:N10 G90 G17 G40 G49 G80N20 T1 M06N30 G90 G0 X0 Y0N40 G43 Z1. H01N50 Z-10 F100.N60 G81 R3 Z-15 F50.N70 G80N80 G00 Z10 M09N90 G17 G90N100 M30在上面的示例中,N开头的数字代表程序行号,G代码代表加工指令,T代码代表刀具信息,M代码代表机床功能指令。
3. 常用数控钻攻铣一体机功能除了基本的直线插补和圆弧插补功能外,数控钻攻铣一体机还具有许多其他功能,如:•刀具半径补偿•自动换刀•预置点功能•宏变量编程•自动测量功能结语通过本教程,读者应该能够了解数控钻攻铣一体机的基本编程方法,掌握常用的数控编程技能。
加工中心的孔加工编程及技巧

《加工中心的孔加工编程及技巧》2005年5月25日加工中心的孔加工编程及技巧摘要:孔加工在数控加工中一直占有重要的地位,如何在加工过程中按照合理的工艺编制出正确的加工程序是非常关键的因素。
关键词:孔加工固定循环子程序极坐标一、引言孔加工在数控加工中一直占有重要的地位。
在合理的加工工艺编制好以后如何编制出正确的程序将直接影响到工件是否加工合格。
复杂的孔加工将用到数控系统中的许多功能。
诸如:孔加工固定循环、子程序、极坐标、坐标旋转等。
因此,如何将这些指令灵活应用在加工的程序中将直接关系到程序的合理性。
二、应用实例下面就以一个定位连接板(图1)作为实例,介绍该类程序的编制及技巧。
1、技术要求:1)零件材料:灰铸铁HT2002)加工部位:加粗部分(φ110,2-φ70H7),8-M12深15,18-φ13深20。
3)加工说明:φ70H7预孔为铸造,余量5mm。
基准面A、B、C、D前工序已完成。
夹具形式不用考虑,φ110孔用铣削方式。
4)数控机床:立式加工中心VMC800;数控系统:FANUC 0iM5)按数控工序卡片编制加工中心程序。
6)程序编制方法:固定循环、子程序、坐标系旋转、极坐标指令等图1 定位连接板2、加工工艺3、加工程序主程序O0001;第0001号程序,加工主程序;建立工件坐标系,并运动到φ70H7孔的中心位置N10T02M6;调用02号刀具(粗镗φ);刀具长度正补偿,并运动到安全高度M03S380;主轴正转M08;打开冷却液;调用粗加工固定循环加工φ70H7孔至φ;在位置继续加工G80;取消固定循环N20T03M6;调用03号刀具(φ40立铣刀铣φ110孔);快速定位到φ110孔的中心位置;刀具长度正补偿,并运动到安全高度M3S420;主轴正转;下刀至第一次的深度位置(粗加工)M98P0501;调用0501号子程序S560;下刀至第二次的深度位置(半精加工)M98P0501;调用0501号子程序M01;检查尺寸。
- 1、下载文档前请自行甄别文档内容的完整性,平台不提供额外的编辑、内容补充、找答案等附加服务。
- 2、"仅部分预览"的文档,不可在线预览部分如存在完整性等问题,可反馈申请退款(可完整预览的文档不适用该条件!)。
- 3、如文档侵犯您的权益,请联系客服反馈,我们会尽快为您处理(人工客服工作时间:9:00-18:30)。
图1 孔加工固定循环的动作
加工中心编程中,经常用到的孔加工固定循环功能指令主要有G81~G89九个,如表1所示。
可以实现钻孔、镗孔、攻螺纹等加工。
孔加工固定循环指令由以下6个动作组成,如图1所示。
1)X和Y轴定位;
2)快速运行到R点;
3)孔加工;
4)在孔底的动作,包括暂停、主轴反转等;
5)返回到R点;
6)快速退回到初始点。
CNC加工中心孔加工固定循环程序段的一般格式为
G90/G91 G98/G99 G81~G89 X_ Y_ Z_ R_ Q_ P_ F_ L_;
式中 G90/G91——绝对坐标编程和增量坐标编程指令;
G98/G99——返回点平面指令,G98为返回到初始平面,G99为返回到R平面,参见图2;
G80~G89——孔加工指令,详细图解如2所示;
X、Y——孔位置坐标;
Z——孔底坐标,按G90编程时,编入绝对坐标值,按G91编程时,编入增量坐标值;
R——按G90编程时,编入绝对坐标值,按G91<
给大家举例说明,一块厚10MM的45号钢板上钻两个5.5的孔。
—、
%
o0001(程序号)M6 T1(选择1号刀)
Go G90 G54 X7.Y-5.M3 S1200(快速定位到个孔上方,主轴正转)G43H1Z50.M8(建立刀具长度补偿,打开冷却液)
G98 G817-2.R2.F60.(点孔固定循环格式)
X33.(点第二个孔)
G80(取消固定循环)M5(主轴停止)
G91G28 Z0.M9(切削液关,Z轴返回机床参考点)G28 Y0.(Y轴返回机床参考点)
M01(选择性停止)
M6 T2(钻孔)
G0 G90 G54 X7.Y-5.M3 S1000G43 H2 Z50.M8
G98 G83Z-13.R2.Q2.F60.X33.
G80M5
G91 G28 Z0.M9G28 Y0.
M30(程序结束)%
在厚为10MM的圆料上钻孔3-M4贯穿均布,这个可以使用极坐标钻孔指令(G16),选择三把刀@10的点钻,D3.3的钻头,M4的丝锥。
坐标原点是大圆圆心,这个需要说明的是X为这三个M4圆心所在圆的半径值,V为度数,符合坐标系逆时针为正,顺时针为负。
—、%o0001
M6 T1(点孔)
G0 G90 G54G16X34.5 Y180.M3 S1200 (以极坐标方式快速移动到较左边的孔上方,主轴正
转)G43H1 Z50.M8
G98 G81Z-2.R2.F60.
G91 Y120.K2.(相对坐标旋转两次,每次120度点孔)G0 G80 G90G15(取消相对坐标,固定循环,极坐标)M5
G91 G28 Z0.M9G28 Yo.
M01
M6 T2(钻底孔)
G0 G90G54G16 X34.5 Y180.M3 S1200G43 H2 Z50.M8
G98 G83Z-13.R2.Q2.F60.G91 Y120.K2.
G0 G80 G90 G15M5
G91 G28 Z0.M9G28 Y0.
M01
M6T3(攻丝)
G0 G90 G54G16 X34.5 Y180.M3 S100G43 H3 Z50.M8 G98 G84Z-13.R2.F70G91 Y120.K2.
G0 G80 G90 G15M5
G91 G28Z0.M9G28 YO.M30%。