高温超高压技术在煤气发电中的应用
钢铁厂高温超高压煤气发电技术的分析与应用

钢铁厂高温超高压煤气发电技术的分析与应用发布时间:2022-09-07T08:58:14.061Z 来源:《科学与技术》2022年第9期作者:刘海明[导读] 本文结合某钢铁企业自备电厂项目,探讨了高温超高压煤气发电技术的应用,从而为相关钢铁企业在建设自备电厂时选择发电工艺方案方面提供参考。
刘海明浙江西子联合工程有限公司浙江杭州 310000摘要:本文结合某钢铁企业自备电厂项目,探讨了高温超高压煤气发电技术的应用,从而为相关钢铁企业在建设自备电厂时选择发电工艺方案方面提供参考。
关键词:钢铁厂;煤气发电技术;应用引言在钢铁工业步入利润微利的年代,用剩余的天然气建造自备电厂已是降低成本、提高竞争力的一种有效途径。
在燃气资源十分紧张的条件下,合理配置和合理的生产技术是非常必要的。
一、钢铁企业煤气系统概述随着钢铁行业发展的需要和国家的节约能源,高炉煤气炉技术正在缓慢地被人发现。
到现在,炼钢厂过剩蒸汽的生产工艺大致分为四个时期(常压、高压及以下)、高温和次高压;高温,高压,中间加热。
随着技术的发展,燃气锅炉的主要技术指标也在持续提高;从12 MW到135 MW;各大工厂的热效率都在稳步上升,高温高压技术的效率比以前高出50%左右;不过,每产生1 kW的电能所消耗的气体总量还会继续下降,从4.53立方米/小时下降到2.98立方米/小时。
目前,国内大部分钢铁工业仍采用高温高压技术,与高温高压相比,高温高压机组年用电量比高温高压机组年多发电0.72亿 kWh,若按电费0.5元/kWh计算,在同样天然气耗量(18.25万rn3/h)标准下,高温高压机组年用电量比高温高压机组年多发电0.72亿 kWh,若按电费0.5元/kWh计算,年增效益近3600万余元,在钢铁企业低迷的今天,对钢铁行业相当于锦上添花。
随着技术进步,目前高温高压气体技术的使用领域还在不断扩展,武汉环境保护技术股份有限公司研制的高温高压设备,其核心技术指标已经超过了65 MW,可以进一步降低其主要技术指标;公司先后在河北省、广西壮族自治区、山东省等地区设立数十家高,低压机械装置。
超高压燃烧技术及其在动力技术中的应用

超高压燃烧技术及其在动力技术中的应用超高压燃烧技术是指将燃料和氧气在高于1.5 MPa的压力下混合点火的技术。
在这种高压状态下,燃烧过程更加充分,能够达到更高的效率和更少的污染物排放。
这项技术的应用在动力技术中有着广泛的应用。
一、超高压燃烧技术的发展历程超高压燃烧技术最早起源于20世纪50年代,当时美国和前苏联开始了超高压燃烧技术的研究。
1960年代,该技术被广泛应用于航空发动机的燃烧室设计中。
到了20世纪90年代,人们又对这项技术进行了深入的研究,推动了燃烧技术的飞跃发展。
现在,这项技术已经在动力技术领域中得到了广泛的应用。
二、超高压燃烧技术的原理超高压燃烧技术的原理是将燃料和空气在高压条件下进行混合,加热并点火,使燃料在短时间内充分燃烧。
这项技术的优点在于可以将燃料充分燃烧,从而使发动机的效率得到提高。
同时,燃烧产生的废气排放可以得到有效的减少,使用超高压燃烧技术的动力设备具有更高的效率和更少的污染物排放。
三、超高压燃烧技术在动力技术领域的应用1、航空发动机超高压燃烧技术在航空发动机中得到广泛的应用。
使用超高压燃烧技术的航空发动机具有更高的功率和更高的效率,同时也可以减少废气排放和噪音污染。
因此,在航空航天领域里,超高压燃烧技术的应用是非常广泛的。
2、液化天然气(LNG)发动机超高压燃烧技术在LNG发动机中应用也非常广泛。
LNG作为一种环保型的燃料,使用超高压燃烧技术可以让LNG在更短的时间内充分燃烧,从而提高发动机的效率,并且对环境污染造成的影响更小。
3、燃料电池车燃料电池是将氢气与氧气进行化学反应,通过沉积的氧化还原电对产生电力的原理制造电能。
超高压燃烧技术可以提高燃氧混合物的混合质量,从而提高燃料电池效率和输出功率,使燃料电池的性能得到了很大的提高。
四、超高压燃烧技术的发展前景超高压燃烧技术的发展前景非常广阔。
因为这项技术可以让燃料在更短的时间内充分燃烧,从而提高动力设备的效率和性能。
一种高温超高压高炉煤气机组的应用与研究

一种高温超高压高炉煤气机组的应用与研究李学军;谢毅;袁建德【摘要】目前我国钢铁行业用于高炉煤气发电的机组大多为12耀30 MW中温中压参数机组,机组的热效率低.有必要对高炉煤气发电机组进行升级改造,以便提高钢厂能源使用效率.这里介绍一种135MW高温超高压燃煤气锅炉汽轮发电机组在钢铁工业中的设计应用研究.%Currently most of the power generators using blast furnace gas (BFG) are 12 MW-30 MW medium temperature medium voltage units in domestic steel industry, with poor thermal efficiency. It is necessary to upgrade these BFG generators in order to improve the energy efficiency of steelmakers. The design and application research of a high temperature ultrahigh pressure BFG boiler for 135 MW turbine generator units are introduced.【期刊名称】《冶金动力》【年(卷),期】2015(000)012【总页数】4页(P35-38)【关键词】高温;超高压;高炉煤气;发电机组;应用研究【作者】李学军;谢毅;袁建德【作者单位】中国能源建设集团湖南省电力设计院有限公司, 湖南长沙 410007;中国能源建设集团湖南省电力设计院有限公司, 湖南长沙 410007;中国能源建设集团湖南省电力设计院有限公司, 湖南长沙 410007【正文语种】中文【中图分类】TM61李学军,谢毅,袁建德(中国能源建设集团湖南省电力设计院有限公司,湖南长沙410007)近年来钢铁工业产能的不断增加,以及钢铁工业节能措施的逐步推进,钢厂煤气富余量将进一步提升,煤气需求与价格波动也将会扩大,而现有煤气电厂能力不能满足需要,致使富余煤气的放散增多,浪费能源并污染环境。
高温超高压技术在煤气发电中的应用

高温超高压技术在煤气发电中的应用摘要:随着社会的不断进步,国家开始重视可持续发展战略的实施。
节能减排和资源综合利用是钢铁企业发展的重大战略任务。
为提高资源综合利用率和能源热功转换率,推进企业能源结构的战略调整,钢铁企业应充分利用高炉煤气、转炉煤气,采用高温超高压发电技术,替代常规次高温次高压发电技术和高温高压发电技术,通过对钢厂分散煤气进行集中,增加每标立方煤气发电量,提高能源利用率,降低钢铁厂的能耗。
关键词:高温超高压技术;煤气发电;应用引言节能减排和资源综合利用是钢铁企业发展过程中面临的重大战略任务。
国家发改委在《能源中长期发展规划纲要(2004—2020)》中明确指出,钢铁企业应“充分利用高炉煤气、焦炉煤气、转炉煤气等可燃气体和各类蒸汽,以自备电站为主要集成手段,推动钢铁企业节能降耗”。
提高资源综合利用率和能源热功转换率,推进企业能源结构的战略调整,已成为各钢铁企业研究重点。
1高温超高压煤气发电技术概述1.1技术介绍高温超高压煤气发电是一种效率高、技术成熟的钢铁企业低热值煤气余能利用形式,其主要核心在于:提高主蒸汽参数,增加一次中间再热系统。
常规次高温次高压发电技术主蒸汽参数为5.3MPa、485℃;高温高压发电技术主蒸汽参数为9.8MPa、540℃;高温超高压发电技术主蒸汽参数为13.7MPa、540℃。
采用高温超高压发电技术起,热功转换率比高温高压发电技术高出约5%~6%,节能效果良好。
1.2钢铁企业煤气发电的意义(1)《钢铁行业碳达峰及降碳行动方案》中提出实现其目标有五大路径,分别是推动绿色布局、节能及提升能效、优化用能及流程结构、构建循环经济产业链和应用突破性低碳技术。
节能及提升能效具体措施包括提高余热余能自发电率。
钢铁企业积极推进高效煤气发电项目符合国家碳达峰、碳中和发展目标。
(2)钢铁企业充分利用富余煤气,变废为宝、化害为利。
通过煤气发电,做到节能减排、提质增效,取得良好的经济效益。
高温高压带一次中间再热技术在煤气发电设计方案研究

| 工程技术与应用 | Engineering Technology and Application ·36·2019年第15期高温高压带一次中间再热技术在煤气发电设计方案研究刘 杰(北京钢研新冶工程设计有限公司,北京 100081)摘 要:文章简要介绍了110T/h 高温高压带一次中间再热30MW 高炉煤气发电机组,从高炉煤气利用方案、主要设备参数、工艺系统、主厂房布置等方面进行了论述,详细介绍了小机组采用高温高压带一次再热技术对发电效率的提升,提高了煤气利用效率,为再热机组的小型化提供工程实践支持。
关键词:高温高压;一次中间再热技术;煤气发电中图分类号:TM61 文献标志码:A 文章编号:2096-2789(2019)15-0036-02作者简介:刘杰(1979—),女,工程师,硕士,研究方向:热能工程。
1 概述钢铁工业在生产过程中会消耗各种化石能源,同时会产生大量的煤气,如高炉煤气、焦炉煤气和转炉煤气。
除去钢铁企业生产自用部分外,仍有约34%的富余煤气,尽管该部分煤气的热值仅约760kcal/m 3,属于一种低附加值燃料,但是若不对该部分煤气加以利用,则会产生严重的能源浪费和环境污染问题[1]。
如何挖掘节能潜力、降低能耗和产品成本、取得较好的经济效益,已成为各钢铁企业的当务之急。
为此,福建某钢铁企业把节能减排作为调整优化结构、转变钢铁生产发展方式的突破口,利用富裕高炉煤气建设煤气发电,降低吨钢成本,真正实现协调和可持续发展[2]。
2 高炉煤气资源现状及利用方案福建某钢厂现有主要工艺装备有2台90m 2烧结机、1台180m 2烧结机、2座550m 3高炉、1座1250m 3高炉、3座50t 转炉、2台4机4流方坯连铸机等。
2016年,厂内富余的煤气主要为高炉煤气和转炉煤气,按公司能源平衡及综合利用规划,最终折合高炉煤气的富余量约为110000Nm 3/h 。
2016年,对于30MW 的小机组应用最成熟的就是高温高压参数的煤气发电技术,高温超高压及超高温超高压参数对于小机组的适用性较差,超高压参数更多的是应用到65MW 以上的发电机组。
高温超高压再热煤气发电工程技术方案

1.1 工程概况江阴华西钢铁有限公司拟新建1×40MW高温超高压煤气发电机组,提高煤气发电效率,实现煤气零放散,减少环境污染。
项目名称:江阴华西钢铁有限公司1×40MW高炉煤气发电工程建设单位:江阴华西钢铁有限公司项目地址:江苏省江阴市华西村建设规模:1×140t/h高温超高压煤气锅炉+1×40MW中间一次再热凝汽式汽轮机+1×40MW发电机组及配套辅助设施。
建设方式:承包内容:1.2 工程界限1.2.1 工程项目包含的内容本项目包含的主要内容有:——主厂房1座(包括1台140t/h高温超高压煤气锅炉、1套40MW 高温超高压凝汽式汽轮机、1套40MW发电机组以及配套辅机);——化学水处理站1座(出力2×14t/h);——项目配套循环冷却水系统(含循环水泵房、机力通风冷却塔)以及工业水、消防水、生活水等给排水设施);——项目配套的电气系统;——项目配套的热工检测与控制系统;——项目红线范围内的所有照明;——项目红线范围内的相关配套能源介质管网(不包括经过煤气柜区红线内的能源介质管网)。
1.2.1.1工程设计①.项目范围内的土建设计,包含结构、建筑、检修平台和操作平台、总图、暖通、给排水、消防,建筑本体防雷接地、照明、通讯等。
②.项目范围内的工艺设计,包含锅炉、汽轮机、循环水、化学水等各个工艺系统流程及管道。
③.项目范围的发配电系统的设计,包含电站的电气主接线、电站接入系统、站用电配电、站用辅机控制、电站室外动力及照明配电线路。
④.项目范围的控制系统的设计,包括热工自动化及计算机控制系统。
1.2.1.2设备成套供货1.2.1.3土建工程施工①.厂房土建施工,包含建筑、消防、给排水、采暖通风、通讯、照明及防雷接地的设备采购和安装。
②.设备基础的施工。
③.厂房内外的起重机/电动葫芦的供货和安装。
④.室内外操作平台照明电气设备(含应急照明)的供货和安装。
亚临界超高温煤气发电技术应用和研究
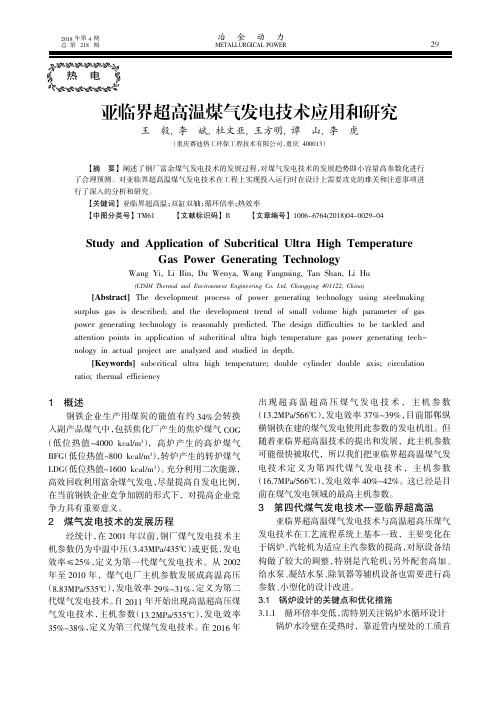
经统计,在 2001 年以前,钢厂煤气发电技术主 机参数仍为中温中压(3.43MPa/435益)或更低,发电 效率臆25%,定义为第一代煤气发电技术。从 2002 年至 2010 年,煤气电厂主机参数发展成高温高压 (8.83MPa/535益),发电效率 29%~31%,定义为第二 代煤气发电技术。自 2011 年开始出现高温超高压煤 气发电技术,主机参数(13.2MPa/535益),发电效率 35%~38%,定义为第三代煤气发电技术。在 2016 年
锅炉水冷壁在受热时,靠近管内壁处的工质首
冶金动力
2018 年第 4 期
30
METALLURGICAL POWER
总 第 218 期
先开始蒸发产生大量小气泡,当循环倍率高时,气泡 被及时带走;亚临界锅炉循环倍率低,蒸发受热面热 负荷和管内含汽率的增加,易使管内壁产生气泡的 速度远大于气泡被带走的速度,气泡就会在管内壁 聚集起来形成所谓的“蒸汽垫”,使管壁得不到及时 冷却,产生膜态沸腾,危及锅炉安全运行。
Wang Yi, Li Bin, Du Wenya, Wang Fangming, Tan Shan, Li Hu
(CISDI Thermal and Environment Engineering Co. Ltd, Chongqing 401122, China)
[Abstract] The development process of power generating technology using steelmaking surplus gas is described; and the development trend of small volume high parameter of gas power generating technology is reasonably predicted. The design difficulties to be tackled and attention points in application of subcritical ultra high temperature gas power generating tech原 nology in actual project are analyzed and studied in depth.
超高温超高压煤气发电机组

超高温超高压煤气发电机组超高温超高压煤气发电机组是一种先进的发电设备,能够在极端的条件下高效地转化燃料能为电能。
本文将对超高温超高压煤气发电机组的原理、应用领域和未来发展进行详细介绍。
超高温超高压煤气发电机组是利用煤气作为燃料,在高温和高压下进行燃烧反应,通过直接燃烧产生的高温高压燃气来驱动发电机发电。
其核心部件是煤气化炉、燃气涡轮机和发电机,通过煤气化炉将煤炭转化为煤气,燃气涡轮机将高温高压燃气转化为机械能,最终通过发电机转化为电能输出。
超高温超高压煤气发电机组具有多项独特优势,首先是高效率。
相较于传统发电方式,超高温超高压煤气发电机组的热效率可高达50%以上,远远超过其他发电方式。
其次是低污染排放。
由于采用了先进的燃烧技术,超高温超高压煤气发电机组的污染物排放量大幅降低,对环境影响较小。
此外,超高温超高压煤气发电机组还具有运行稳定、安全可靠等优点,是未来发电行业的重要发展方向。
超高温超高压煤气发电机组在多个领域具有广泛的应用前景。
首先是电力行业。
作为一种高效、低排放的发电方式,超高温超高压煤气发电机组可以替代传统的火力发电和燃气发电,为电网提供稳定可靠的电力供应。
其次是工业领域。
许多工业企业需要大量的电力供应,超高温超高压煤气发电机组能够满足其电力需求,并降低能源消耗和生产成本。
另外,超高温超高压煤气发电机组还可以应用于冶金、化工、钢铁等行业,为工业生产提供动力保障。
未来,超高温超高压煤气发电机组的发展前景广阔。
一方面,随着对可再生能源的需求日益增长,超高温超高压煤气发电机组可以与可再生能源进行混合利用,提高电力供应的可持续性。
另一方面,随着技术的不断进步,超高温超高压煤气发电机组的热效率和稳定性还有很大的提升空间。
未来,通过改进设计和优化传热、传质等过程,超高温超高压煤气发电机组的性能将进一步提高。
总的来说,超高温超高压煤气发电机组作为一种先进的发电设备,具有高效率、低污染排放等优点,在电力和工业领域具有广泛的应用前景。
高温超高压煤气发电 高温超高压再热煤气发电工程技术方案

高温超高压煤气发电高温超高压再热煤气发电工程技术方案导读:就爱阅读网友为您分享以下“高温超高压再热煤气发电工程技术方案”的资讯,希望对您有所帮助,感谢您对92to 的支持!辅助系统包括:除氧给水系统、循环水系统、化学水系统、有毒气体探测系统等。
2.10.1.5 主要设计原则2.10.1.5.1本工程设计拟按炉、机一体化配置分散控制系统(DCS),实现全LCD监控。
2.10.1.5.2 利用先进的控制技术与网络技术,按照电厂管理、运行和专业分工特点,合理优化集中全厂辅助车间和辅助系统的运行监控点和运行控制方式,减少运行人员,提高电厂的安全可靠性和经济效益。
详见控制系统配置图。
2.10.1.5.3 设置FSSS(炉膛安全监视系统),由DCS完成其功能,设置专用的硬跳闸回路,确保锅炉的安全运行。
2.10.2 热工自动化水平和控制室布置2.10.2.1 热工自动化水平2.10.2.1.1 本工程为单元制机组。
为保证机组的安全经济及合理的运行,机组控制中心将进一步智能化、自动化,减人增效。
本设计拟按炉、机一体化配置分散控制系统(DCS),实现全LCD监控。
其自动化水平将使运行人员在集中控制室内通过LCD和键盘(鼠标)即能完成机组正常运行的全部操作和机组在事故状态时的有关操作。
可以实现对机组正常运行工况的监视操作、紧急情况事故处理及停机,在少量现场操作人员配合下,完成机组的正常启、停。
2.10.2.1.2 按照上述对机组监控的基本要求,本工程分散控制系统功能将包括:数据采集及处理系统(DAS)、模拟量控制系统(MCS)、顺序控制系统(SCS)、锅炉炉膛安全监控系统(FSSS)。
汽机数字电液控制系统(DEH)、汽机安全监视系统(TSI)、汽机第45页紧急跳闸系统(ETS)等设备,随主机厂配套供货。
DEH、ETS通过硬接线连接至DCS,并通过通信进行信息共享,保证系统可靠性。
循环水泵房的监视及控制纳入机组DCS,由DCS统一监控。
华钢高温超高压再热1×40MW煤气发电工程技术方案2016-5-13

1.1 工程概况江阴华西钢铁有限公司拟新建1×40MW高温超高压煤气发电机组,提高煤气发电效率,实现煤气零放散,减少环境污染。
项目名称:江阴华西钢铁有限公司1×40MW高炉煤气发电工程建设单位:江阴华西钢铁有限公司项目地址:江苏省江阴市华西村建设规模:1×140t/h高温超高压煤气锅炉+1×40MW中间一次再热凝汽式汽轮机+1×40MW发电机组及配套辅助设施。
建设方式:承包内容:1.2 工程界限1.2.1 工程项目包含的内容本项目包含的主要内容有:——主厂房1座(包括1台140t/h高温超高压煤气锅炉、1套40MW高温超高压凝汽式汽轮机、1套40MW发电机组以及配套辅机);——化学水处理站1座(出力2×14t/h);——项目配套循环冷却水系统(含循环水泵房、机力通风冷却塔)以及工业水、消防水、生活水等给排水设施);——项目配套的电气系统;——项目配套的热工检测与控制系统;——项目红线范围内的所有照明;——项目红线范围内的相关配套能源介质管网(不包括经过煤气柜区红线内的能源介质管网)。
1.2.1.1工程设计①.项目范围内的土建设计,包含结构、建筑、检修平台和操作平台、总图、暖通、给排水、消防,建筑本体防雷接地、照明、通讯等。
②.项目范围内的工艺设计,包含锅炉、汽轮机、循环水、化学水等各个工艺系统流程及管道。
③.项目范围的发配电系统的设计,包含电站的电气主接线、电站接入系统、站用电配电、站用辅机控制、电站室外动力及照明配电线路。
④.项目范围的控制系统的设计,包括热工自动化及计算机控制系统。
1.2.1.2设备成套供货1.2.1.3土建工程施工①.厂房土建施工,包含建筑、消防、给排水、采暖通风、通讯、照明及防雷接地的设备采购和安装。
②.设备基础的施工。
③.厂房内外的起重机/电动葫芦的供货和安装。
④.室内外操作平台照明电气设备(含应急照明)的供货和安装。
高温超高压再热煤气发电工程技术方案
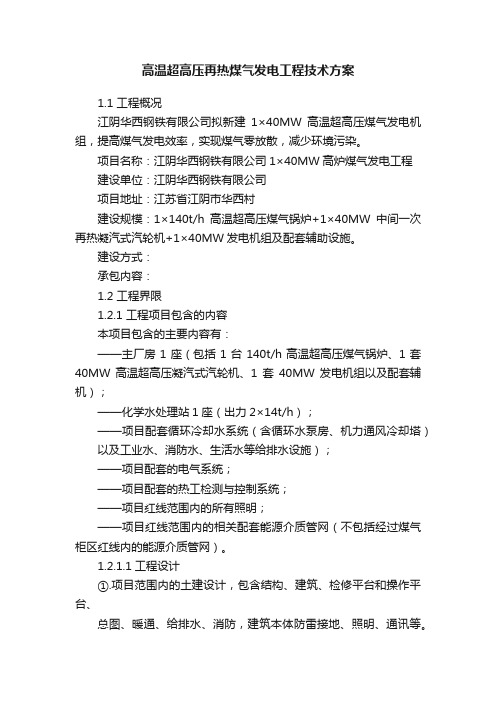
高温超高压再热煤气发电工程技术方案1.1 工程概况江阴华西钢铁有限公司拟新建1×40MW高温超高压煤气发电机组,提高煤气发电效率,实现煤气零放散,减少环境污染。
项目名称:江阴华西钢铁有限公司1×40MW高炉煤气发电工程建设单位:江阴华西钢铁有限公司项目地址:江苏省江阴市华西村建设规模:1×140t/h高温超高压煤气锅炉+1×40MW中间一次再热凝汽式汽轮机+1×40MW发电机组及配套辅助设施。
建设方式:承包内容:1.2 工程界限1.2.1 工程项目包含的内容本项目包含的主要内容有:——主厂房1座(包括1台140t/h高温超高压煤气锅炉、1套40MW 高温超高压凝汽式汽轮机、1套40MW发电机组以及配套辅机);——化学水处理站1座(出力2×14t/h);——项目配套循环冷却水系统(含循环水泵房、机力通风冷却塔)以及工业水、消防水、生活水等给排水设施);——项目配套的电气系统;——项目配套的热工检测与控制系统;——项目红线范围内的所有照明;——项目红线范围内的相关配套能源介质管网(不包括经过煤气柜区红线内的能源介质管网)。
1.2.1.1工程设计①.项目范围内的土建设计,包含结构、建筑、检修平台和操作平台、总图、暖通、给排水、消防,建筑本体防雷接地、照明、通讯等。
②.项目范围内的工艺设计,包含锅炉、汽轮机、循环水、化学水等各个工艺系统流程及管道。
③.项目范围的发配电系统的设计,包含电站的电气主接线、电站接入系统、站用电配电、站用辅机控制、电站室外动力及照明配电线路。
④.项目范围的控制系统的设计,包括热工自动化及计算机控制系统。
1.2.1.2设备成套供货1.2.1.3土建工程施工①.厂房土建施工,包含建筑、消防、给排水、采暖通风、通讯、照明及防雷接地的设备采购和安装。
②.设备基础的施工。
③.厂房内外的起重机/电动葫芦的供货和安装。
④.室内外操作平台照明电气设备(含应急照明)的供货和安装。
超高温亚临界煤气发电项目

超高温亚临界煤气发电项目超高温亚临界煤气发电项目一、引言能源是现代社会发展的重要支撑,而清洁能源的开发和利用对于环保和可持续发展至关重要。
在这方面,超高温亚临界煤气发电项目成为了一个备受瞩目的研究领域。
本文将重点介绍该项目的背景、技术原理、应用前景和环境效益。
二、背景随着全球能源需求的不断增长和环境问题的日益突出,清洁能源的研究和应用成为了全球范围内的热点。
煤炭作为目前主要的能源供应来源之一,其高效利用和减少排放成为了亟待解决的问题。
超高温亚临界煤气发电技术是近年来在此背景下涌现出的一项创新技术。
三、技术原理超高温亚临界煤气发电项目利用亚临界条件下的煤气进行发电,具有以下几个关键技术:1. 煤气化技术:将煤炭进行高效气化,生成合适的煤气作为燃料,并分离出废弃物。
2. 烟气净化技术:对煤气中的固体颗粒物、硫化物等有害物质进行去除和处理,以减少对环境的污染。
3. 亚临界燃烧技术:通过调控燃烧温度和压力,实现效率更高的燃烧过程,减少氮氧化物的生成。
4. 催化技术:引入合适的催化剂,提高煤气的燃烧效率和产能。
四、应用前景超高温亚临界煤气发电项目具有以下几个应用前景:1. 高效能源转化:通过提高煤气的燃烧效率,能够更充分地利用煤炭资源,提高能源利用效率。
2. 清洁能源替代:煤气发电相比传统燃煤发电,废气和废水排放量大大减少,对环境影响更小。
3. 排放减少:通过采用烟气净化技术和亚临界燃烧技术,能够有效减少废弃物和污染物的排放。
4. 运行稳定性:超高温亚临界煤气发电项目运行稳定性较高,投资回报周期较短。
五、环境效益1. 减少温室气体排放:超高温亚临界煤气发电项目减少了二氧化碳、氮氧化物和硫化物等温室气体的排放量,对减缓气候变化起到积极作用。
2. 空气污染物减少:该项目采用烟气净化技术和亚临界燃烧技术,有效减少了颗粒物、二氧化硫、氮氧化物等有害气体的排放,改善了空气质量。
3. 水资源保护:超高温亚临界煤气发电项目减少了对水资源的消耗,降低了水污染的风险。
高温超高压一次再热机组在小型燃煤电站中的应用研究
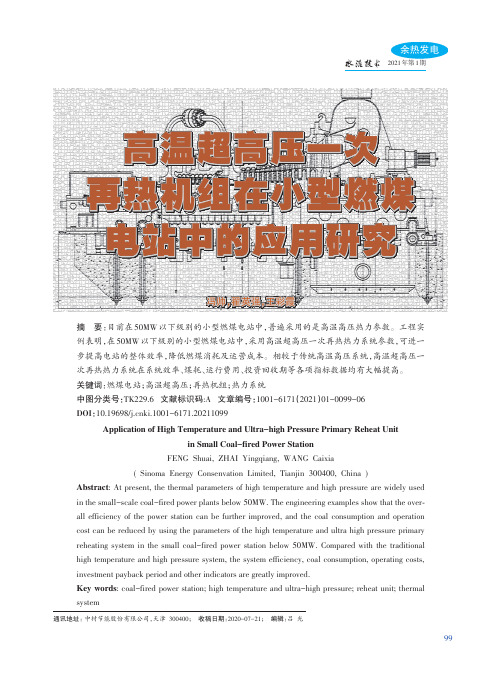
摘要:目前在50MW 以下级别的小型燃煤电站中,普遍采用的是高温高压热力参数。
工程实例表明,在50MW 以下级别的小型燃煤电站中,采用高温超高压一次再热热力系统参数,可进一步提高电站的整体效率,降低燃煤消耗及运营成本。
相较于传统高温高压系统,高温超高压一次再热热力系统在系统效率、煤耗、运行费用、投资回收期等各项指标数据均有大幅提高。
关键词:燃煤电站;高温超高压;再热机组;热力系统中图分类号:TK229.6文献标识码:A 文章编号:1001-6171(2021)01-0099-06DOI :10.19698/ki.1001-6171.20211099通讯地址:中材节能股份有限公司,天津300400;收稿日期:2020-07-21;编辑:吕光高温超高压一次再热机组在小型燃煤电站中的应用研究冯帅,翟英强,王彩霞Application of High Temperature and Ultra-high Pressure Primary Reheat Unitin Small Coal-fired Power StationFENG Shuai,ZHAI Yingqiang,WANG Caixia(Sinoma Energy Consenvation Limited,Tianjin 300400,China )Abstract :At present,the thermal parameters of high temperature and high pressure are widely used in the small-scale coal-fired power plants below 50MW.The engineering examples show that the over⁃all efficiency of the power station can be further improved,and the coal consumption and operation cost can be reduced by using the parameters of the high temperature and ultra high pressure primary reheating system in the small coal-fired power station below pared with the traditionalhigh temperature and high pressure system,the system efficiency,coal consumption,operating costs,investment payback period and other indicators are greatly improved.Key words :coal-fired power station;high temperature and ultra-high pressure;reheat unit;thermalsystem99在电力市场中,对于50MW以下级别的小型燃煤电站,目前普遍采用高温高压的机组参数,而对于50MW以上级别的燃煤电站、50MW以下级别的生物质电站以及钢厂煤气电站,主要采用的是超高压一次再热参数。
超高温亚临界煤气发电原理

超高温亚临界煤气发电原理超高温亚临界煤气发电是一种利用煤炭资源进行发电的新型技术,是当前能源革命的重要方向之一。
本文将从亚临界煤气技术的背景和原理、发电过程及优势等方面来详细介绍。
一、背景和原理目前,全球能源需求不断增加,传统化石燃料的消耗迅猛,给环境造成了巨大压力。
而煤炭作为一种丰富的能源资源,发挥着重要作用。
然而,传统的燃烧煤炭会产生大量的温室气体和污染物,对环境和人类健康造成了极大威胁。
因此,开发出高效、清洁的煤炭利用技术变得尤为重要。
亚临界煤气技术是一种以煤炭为原料,通过高温高压气化产生的亚临界煤气来发电的技术。
该技术通过在高温、高压条件下将煤炭转化为可燃气体,然后再利用这种气体来发电,实现了清洁高效利用煤炭的目标。
二、发电过程超高温亚临界煤气发电包括气化和发电两个过程。
1. 气化过程在亚临界气化过程中,煤炭会经历干馏、热解、气化等化学反应,最终转化为亚临界煤气。
在高温高压条件下,煤炭中的碳氢化合物会发生裂解,产生一系列可燃气体,如一氧化碳、氢气等。
同时,气化过程还会产生一定的固体残渣(灰渣),需要进行处理。
2. 发电过程亚临界煤气通过燃烧产生高温高压的蒸汽,然后蒸汽推动汽轮机旋转,进而带动发电机发电。
在发电过程中,蒸汽会逐渐冷却回流,形成循环发电系统。
三、优势超高温亚临界煤气发电技术相比传统煤炭发电具有以下几个优势:1. 清洁高效:亚临界煤气发电技术利用煤炭气化产生的气体进行发电,燃烧过程中减少了废气的产生,大大降低了温室气体的排放。
同时,高效发电的过程也同时提高了能源利用效率。
2. 资源综合利用:亚临界煤气技术可以利用多种煤炭类型进行气化发电,能够综合利用各类不同特性的煤炭资源,提高了能源资源的有效利用率。
3. 燃料灵活性:亚临界煤气作为一种可燃气体,可以与其他可燃气体混燃,提高了煤气发电系统的灵活性和适应性。
4. 应用广泛:亚临界煤气发电技术可广泛应用于电力、化工等领域,能够为工业和社会经济发展提供可靠、稳定的电力供应。
超高温超高压煤气发电

超高温超高压煤气发电超高温超高压煤气发电是一种新兴的发电技术,通过将煤气在超高温超高压条件下进行燃烧,产生高温高压蒸汽驱动涡轮发电机发电。
这种技术具有高效、环保、可持续等优势,被广泛应用于能源行业和工业生产中。
超高温超高压煤气发电技术的核心是超高温超高压燃烧系统。
该系统由燃烧室、燃烧器、泄压装置、燃气热回收装置、涡轮发电机等组成。
燃烧室采用特殊材料制造,可以承受高温高压环境。
燃烧器采取先进的燃烧技术,将煤气在超高温超高压条件下充分燃烧,产生大量的高温高压蒸汽。
泄压装置用来控制系统的压力,确保系统运行的安全可靠。
燃气热回收装置将燃烧产生的废热利用起来,提高系统的能效。
涡轮发电机将高温高压蒸汽转化为电能,实现发电。
超高温超高压煤气发电技术具有多个优势。
首先,该技术的发电效率较高。
由于采用了先进的燃烧技术和高效的热回收装置,能够充分利用燃气的热能,提高能源的利用效率。
其次,该技术的燃烧过程相对环保。
由于煤气是一种清洁能源,不含硫、灰等有害物质,因此燃烧过程中产生的废气排放相对较少,对环境的影响较小。
此外,该技术还具有可持续性。
煤气是可再生能源,可以通过多种方式获得,如煤矿煤气、生物质气化产生的煤气等,不会消耗地球资源。
超高温超高压煤气发电技术的应用领域非常广泛。
首先,它可以作为一种清洁的发电方式,广泛应用于能源行业。
在电力行业,煤气发电可以替代传统的燃煤发电方式,减少燃煤带来的环境污染和能源浪费。
其次,该技术还可以应用于工业生产中。
例如,煤气发电可以提供给各类工业厂房使用,满足工业生产的电力需求,降低企业的能源成本。
此外,煤气发电还可以应用于农业生产、城市供暖等领域,为农村和城市提供可靠的电力供应。
当然,超高温超高压煤气发电技术也存在一些挑战和局限性。
首先,该技术的设备和材料需要具备较高的耐高温高压性能,这对设备制造和材料研发提出了较高的要求。
此外,煤气的获取和净化也是一个问题。
煤气的获取需要建设相应的气体生产设施,净化过程中可能会产生一定的废气和废水,需要采取适当的处理措施。
高温高压条件下煤的燃烧特性研究

高温高压条件下煤的燃烧特性研究
煤是人类能源供应的重要来源之一,在中国更是占据了绝大部分的能源供应量。
为了更好地利用煤,研究煤的燃烧特性是非常重要的。
煤的燃烧特性
首先,了解煤的燃烧特性是研究高温高压条件下煤的燃烧特性的基础。
煤燃烧
主要是由碳在氧气中燃烧产生二氧化碳,同时产生热能。
但是,在煤的不同部位以及不同类型的煤中,燃烧特性会有所不同。
这就需要通过实验来研究。
高温高压条件下煤的燃烧特性研究需要使用高温高压炉进行实验。
高温高压炉
是指在高温(1000℃以上)和高压(20MPa以上)的条件下对材料进行热处理的
实验装置。
这种实验装置能够模拟煤在地下深处的压力和温度条件,从而更好地了解其燃烧特性。
在实验中,我们可以测量煤在高温高压条件下的燃烧速率、反应动力学参数等
指标。
这些指标可以帮助我们更好地了解煤的燃烧规律和特性,为优化煤的利用提供指导。
同时,高温高压条件下煤的燃烧也与大气污染相关。
煤的燃烧会产生大量的二
氧化碳、氮氧化物和颗粒物等有害物质。
研究煤的燃烧特性可以更好地理解这些有害物质的生成机理和规律,为大气污染治理提供依据。
总之,在高温高压条件下煤的燃烧特性研究中,实验是非常必要的手段。
通过
实验可以更好地了解煤的燃烧规律和特性,为优化煤的利用提供指导,并为大气污染治理提供依据。
同时,还需要注意研究过程中对环境和安全的保护。
高温高压的燃气推动
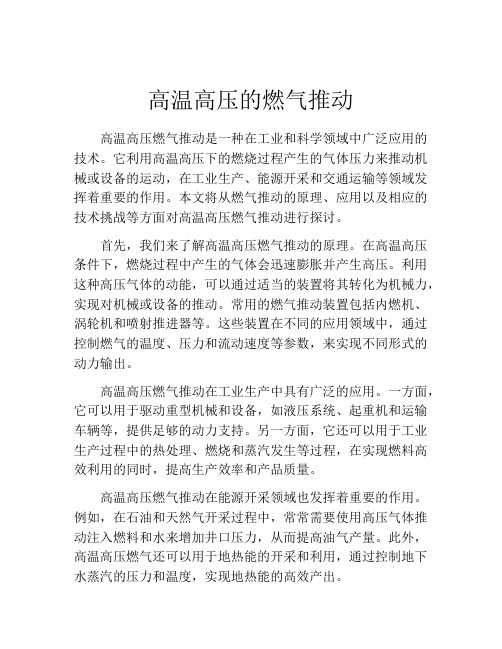
高温高压的燃气推动高温高压燃气推动是一种在工业和科学领域中广泛应用的技术。
它利用高温高压下的燃烧过程产生的气体压力来推动机械或设备的运动,在工业生产、能源开采和交通运输等领域发挥着重要的作用。
本文将从燃气推动的原理、应用以及相应的技术挑战等方面对高温高压燃气推动进行探讨。
首先,我们来了解高温高压燃气推动的原理。
在高温高压条件下,燃烧过程中产生的气体会迅速膨胀并产生高压。
利用这种高压气体的动能,可以通过适当的装置将其转化为机械力,实现对机械或设备的推动。
常用的燃气推动装置包括内燃机、涡轮机和喷射推进器等。
这些装置在不同的应用领域中,通过控制燃气的温度、压力和流动速度等参数,来实现不同形式的动力输出。
高温高压燃气推动在工业生产中具有广泛的应用。
一方面,它可以用于驱动重型机械和设备,如液压系统、起重机和运输车辆等,提供足够的动力支持。
另一方面,它还可以用于工业生产过程中的热处理、燃烧和蒸汽发生等过程,在实现燃料高效利用的同时,提高生产效率和产品质量。
高温高压燃气推动在能源开采领域也发挥着重要的作用。
例如,在石油和天然气开采过程中,常常需要使用高压气体推动注入燃料和水来增加井口压力,从而提高油气产量。
此外,高温高压燃气还可以用于地热能的开采和利用,通过控制地下水蒸汽的压力和温度,实现地热能的高效产出。
在交通运输领域,高温高压燃气推动是现代化运输工具的重要动力来源。
例如,内燃机被广泛应用于汽车、火车和飞机等交通工具中,通过高温高压燃气的推动来驱动车辆的运动。
此外,喷射推进器也是航空航天器的重要动力系统,通过高温高压燃气的喷射推进来实现飞行器的加速和运动控制。
然而,高温高压燃气推动技术也面临一些挑战。
首先,高温高压条件对设备和材料的要求更高。
燃气推动装置需要能够承受高温高压环境下的腐蚀、磨损和热应力等因素的影响,同时还要保持稳定的性能和可靠的运行。
其次,燃气推动过程中产生的高温高压气体对环境和人体安全构成潜在风险,需要采取有效的措施来控制和减少相应的排放和泄漏。
高温材料在发电燃气轮机中的应用和发展

高温材料在发电燃气轮机中的应用和发展发表时间:2016-04-27T16:09:42.910Z 来源:《电力设备》2015年第12期供稿作者:王家东[导读] 神华国华(北京)燃气热电有限公司在我国发电燃气轮机的发展中一直都想把效率更高、可靠性更强和使用寿命更长作为重要的发展目标和发展方向,而在发展的过程中,构件的材料发挥了十分重要的作用,所以一定要重视材料的选择,根据其特点还应该选择高温材料,以便能够更好的展现出其良好的性能。
(神华国华(北京)燃气热电有限公司北京 100000)摘要:在我国发电燃气轮机的发展中一直都想把效率更高、可靠性更强和使用寿命更长作为重要的发展目标和发展方向,而在发展的过程中,构件的材料发挥了十分重要的作用,所以一定要重视材料的选择,根据其特点还应该选择高温材料,以便能够更好的展现出其良好的性能。
本文主要分析了高温材料在发电燃气轮机中的应用及发展趋势。
关键词:高温材料发电燃气轮机应用发展引言近年来,燃气发电机在世界上发展十分迅速。
燃气发电机组是以天然气为燃料的新型节能环保发电机组,具有起动性能好、发电质量高、噪声低振动小等众多优势。
目前国内大型燃气轮机组多选用国外进口产品,高温材料的应用显得尤为关键。
随着燃气轮机的进气温度进一步提高,需要开发新型高温材料,如金属间化合物、难熔合金、碳-碳复合材料、陶瓷及其复合材料等,作为高温合金的替代材料,以减少冷却或者不使用冷却,从而提高燃气轮机的效率。
本文主要结合燃气轮机发电结构探讨高温材料在发电燃气轮机中的实际应用,以供参考。
一、燃气轮机浅析作为旋转式动力机械,气体以连续流动的方式在燃气轮机中通过热能向机械能的转化,进而推动发电机组旋转。
纵观世界范围内,瑞士一家企业于二十世纪三十年代末制造出了第一台燃气轮机。
经历了多年的发展与完善,燃气轮机已经在坦克动力、机车动力、发电、管线动力等方面有所应用。
通过结构的不同进行划分,工业燃气轮机主要包括轻型燃气轮机与重型燃气轮机。
高温高压的燃气
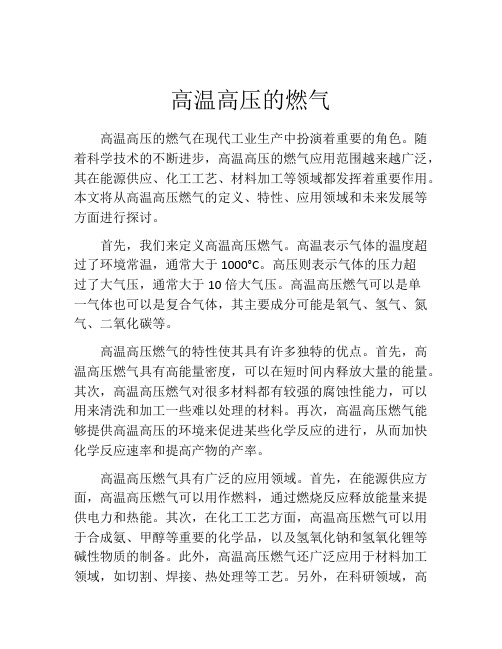
高温高压的燃气高温高压的燃气在现代工业生产中扮演着重要的角色。
随着科学技术的不断进步,高温高压的燃气应用范围越来越广泛,其在能源供应、化工工艺、材料加工等领域都发挥着重要作用。
本文将从高温高压燃气的定义、特性、应用领域和未来发展等方面进行探讨。
首先,我们来定义高温高压燃气。
高温表示气体的温度超过了环境常温,通常大于1000°C。
高压则表示气体的压力超过了大气压,通常大于10倍大气压。
高温高压燃气可以是单一气体也可以是复合气体,其主要成分可能是氧气、氢气、氮气、二氧化碳等。
高温高压燃气的特性使其具有许多独特的优点。
首先,高温高压燃气具有高能量密度,可以在短时间内释放大量的能量。
其次,高温高压燃气对很多材料都有较强的腐蚀性能力,可以用来清洗和加工一些难以处理的材料。
再次,高温高压燃气能够提供高温高压的环境来促进某些化学反应的进行,从而加快化学反应速率和提高产物的产率。
高温高压燃气具有广泛的应用领域。
首先,在能源供应方面,高温高压燃气可以用作燃料,通过燃烧反应释放能量来提供电力和热能。
其次,在化工工艺方面,高温高压燃气可以用于合成氨、甲醇等重要的化学品,以及氢氧化钠和氢氧化锂等碱性物质的制备。
此外,高温高压燃气还广泛应用于材料加工领域,如切割、焊接、热处理等工艺。
另外,在科研领域,高温高压燃气可以用于材料表征和性能测试,如高温高压下的材料变形、相变和耐久性测试等。
未来,高温高压燃气将继续发展并广泛应用于更多领域。
首先,随着清洁能源和可持续发展的要求不断增加,高温高压燃气在可再生能源的利用和储存方面将发挥重要作用。
其次,随着材料科学和工程的发展,高温高压燃气将带来更多的材料创新和加工技术的突破。
另外,高温高压燃气在航空航天、冶金矿业、生物医药等领域也将有更多的应用。
综上所述,高温高压燃气是一种重要的工业能源,其具有高能量密度、较强的腐蚀性和促进化学反应速率等特性。
高温高压燃气在能源供应、化工工艺、材料加工等领域具有广泛的应用。
- 1、下载文档前请自行甄别文档内容的完整性,平台不提供额外的编辑、内容补充、找答案等附加服务。
- 2、"仅部分预览"的文档,不可在线预览部分如存在完整性等问题,可反馈申请退款(可完整预览的文档不适用该条件!)。
- 3、如文档侵犯您的权益,请联系客服反馈,我们会尽快为您处理(人工客服工作时间:9:00-18:30)。
高温超高压技术在煤气发电中的应用
摘要:目前我国钢铁行业用于高炉煤气发电的机组大多为12~30 MW中温中压
参数机组,机组的热效率低。
本文重点讨论高温超高压煤气发电这种高效发电技
术在钢铁企业富余煤气资源利用方面的优势,分析高温超高压技术高效发电的具
体原因,并对比了该技术与燃气蒸汽联合循环发电技术之间的差异。
关键词:钢铁企业;节能;高温超高压;煤气
近年来钢铁工业产能的不断增加,以及钢铁工业节能措施的逐步推进,钢厂
煤气富余量将进一步提升,煤气需求与价格波动也将会扩大,而现有煤气电厂能
力不能满足需要,致使富余煤气的放散增多,浪费能源并污染环境。
一、煤气锅炉发电技术的发展历程
在早期钢厂煤气锅炉发电技术中,尽管能够有效控制钢铁企业的煤气放散率,但是由于受钢厂规模和煤气量的影响,燃气锅炉机组较小,效率偏低,煤气锅炉
发电技术并非一种高效的煤气利用方式。
随着钢铁行业技术的发展,钢铁生产过
程中逐渐减少了生产自用煤气的消耗量,煤气富裕量大大增加,提高煤气发电效
率带来的经济效益日益明显。
在钢厂企业效益和国家节能减排政策的要求下,钢
厂煤气锅炉发电技术也在逐步跟进。
到目前为止,钢厂富余煤气发电技术大致经
历了早期技术(中温中压或更低),第一代技术(中温中压或次高温次高压),第二代
技术(高温高压),第三代技术(高温超高压中间再热)等4个阶段。
随着技术发展,
煤气锅炉发电技术的主机参数越来越高;机组规模越来越大,从早期的12MW一
直到目前的135MW;全厂热效率越来越高,高温超高压技术的热效率比早期的
技术已经提高了近50%;但是每生产1 kWh电所消耗的煤气量则越来越低,从最初的4.53m3/kwh降低到目前的2.98m3/kWh。
目前,大多数钢铁企业的锅炉
煤气发电技术仍采用第二代(高温高压)技术,与高温超高压技术相比,高温高压
技术的发电效率要低近6%,钢厂最常见的50MW高温高压机组与65MW高温超
高压机组参数的比较,在同等煤气耗量(18.25万rn3/h)条件下,高温超高压机组
年供电量比高温高压机组年多发电0.72亿kWh,若按电价0.5元/kWh计算,年增效益近3600万元,在钢铁行业不景气的今天,对钢铁企业无异于雪中送炭。
随着技术发展,目前高温超高压煤气发电技术机组规模覆盖也越来越广,武汉都
市环保工程技术股份有限公司自主研发的高温超高压机组主机参数已经突破了
65MW的限制,可以向更低参数方向发展,该公司已相继在河北、广西、山东等
地的钢厂建设了数十台套高温超高压机组。
二、煤气锅炉发电技术
1.纯烧高炉煤气锅炉发电技术。
20世纪90年代中期,国内开始自主开发并引进国外全烧高炉煤气发电技术,纯烧高炉煤气锅炉发电技术由燃高炉煤气锅炉、
汽轮发电机及辅机等组成。
通过高炉煤气管道将减压阀组减压后或TRT装置后
的低压高炉煤气送入锅炉进行燃烧,产生的过热蒸汽进入汽轮机,驱动汽轮机带
动发电机进行发电。
2.TRT(高炉煤气余压透平发电装置)。
上世纪50年代中期,法国、比利时、
捷克、苏联等国开始对TRT进行试验研究。
其中法国成功的开发了湿式TRT系统,苏联则开发了干式TRT系统。
80年代,日本的TRT装置技术发展较快,三
井造船、日立造船、川崎重工等对TRT进行了改进,进一步提高了回收效率、
降低了投资。
我国从60年代中期由武汉钢铁设计研究院开始研究、消化吸收国外TRT技术。
80年代初期通过大量试验取得成功。
3.高炉煤气燃气-蒸汽联合发电(CCPP)。
CCPP是目前钢铁企业最先进的煤气
回收利用技术,该技术将钢铁生产过程中的富余煤气与空气燃烧后产生高温高压
烟气,烟气膨胀做功,将机械能转化为电能,之后用余热锅炉将烟气的余热回收
产生高温高压蒸汽,利用蒸汽轮机再次发电,最终实现联合循环发电。
目前低热值煤气为燃料的CCPP只被少数公司掌握,如ABB、日本川崎,美国GE等。
CCPP已在我国部分钢铁大型钢铁企业得到应用,如宝钢、莱钢、鞍钢、迁钢等等,为企业创造了明显的效益CCPP发电效率高、成本低、经济效益好,发电效率高
达45%,而同规模常规火力发电机组效率仅为23%—35%左右,两年即可收回投
资成本。
CCPP以低热值高炉煤气为主要燃料,能大幅度减少高炉煤气放散量,迁钢的高炉煤气基本上可以全部被回收利用,达到高炉煤气零排放,节能效果明显。
三、高温超高压技术高效发电原理分析
高温超高压煤气发电技术之所以高效的原因主要可以归结于:提高蒸汽参数
和增加一次中间再热。
常规中温中压发电技术的主蒸汽参数为3.82MPa、4500C,高温高压发电技术的主蒸汽参数为9.8MPa、540℃,而高温超高压发电技术的主
蒸汽参数已经达到了13.7MPa、540℃。
在保持主蒸汽初温()和机组背压()不变的
情况下,提高主蒸汽压力对机组循环热效率的影响如图1所示。
由图1中可以看出:在极限压力范围内,保持初温和背压一定,随着蒸汽压力升高,尽管主蒸汽
初始焓值h。
有所降低,但是汽轮机组的整个理想比焓降有所升高,因此机组的
循环热效率升高。
当主蒸汽初压大于极限压力时,随着主蒸汽初压升高,整个汽
轮机组的理想比焓降有所降低,循环热效率反而有所降低,但是实际工程中,主
蒸汽的压力均小于极限压力,因此在实际工程应用中保持和不变时,提高蒸汽初
压有利于提高机组循环热效率。
高温超高压机组发电效率高于高温高压机组的另
一个原因就是增加了中间一次再热,带中间一次再热和不带中间一次再热的煤气
发电系统。
对于不带再热的煤气发电机组,蒸汽在汽轮机中做完工后便会直接进
入冷凝器中冷凝,蒸汽中的大部分热量将会以气化潜热的形式损失,当增加一次
中间再热后,蒸汽从汽机中间级引出被重新加热至初始温度,降低了蒸汽的排汽
湿度,使得湿度损失减小,从而提高了汽轮机组的循环热效率。
四、案例分析
如N93-13.2/535/535型机组为高温、超高压、一次中间再热、凝汽式汽轮机,结构型式为单缸单排汽,汽缸由前、中、后三段通过垂直法兰螺栓连接为一体。
因进汽参数较高,为减小汽缸应力,增加机组启停及变负荷的灵活性,高压部分
设计为双层缸。
汽缸的中低压部分采用单层缸隔板套结构。
为简化汽缸结构和减
小热应力,高压和中压阀门与汽缸之间都是通过管道联接。
高压阀布置在汽机机
头侧运行层上面,中压阀置于汽缸中压进汽段左右两侧。
机组总长~9.4m。
高压
通流部分设计为反向流动,高压和中压进汽口都布置在前汽缸中部,是整个机组
工作温度最高的部位。
来自锅炉过热器的新蒸汽通过2根主蒸汽管分别进入左右
两个高压主汽调节阀,再经4根Φ133×17高压主汽管和装在前汽缸的4个高压进汽管分别从上下方向进入前汽缸内缸中的喷嘴室,然后进入高压通流部分。
蒸汽
经1个单列调节级和8个压力级做功后,由前汽缸前端下部的2个高压排汽口排出,汇合并经1根冷段再热汽管去锅炉再热器,管上装1个抽汽止回阀。
在第6
级后设第1段抽汽口供No.1 HP HTR,在第9级后(高压排汽)设第2段抽汽口
供No.2 HP HTR再热蒸汽通过2根热段再热汽管进入中压联合汽阀,再经2根
Ø410×55再热进汽管从前汽缸外缸中部下半两侧进入中低压通流部分。
中低压部
分共有13个压力级,蒸汽做功后,由后汽缸排汽口向下排入凝汽器。
在第13级
后设第3段回热抽汽口供除氧器,在第16级后设第4段回热抽汽口供No.4 LP HTR,在第18级后设第5段回热抽汽口供No.5 LP HTR,在第20级后设第6段回热抽汽口供No.6 LP HTR。
高温超高压煤气发电技术已逐渐成为钢铁厂应用最广的余能利用技术,相对高温高压、次高温次高压具有较好的优势,是一种重要的节能措施。
参考文献:
[1]李秦.一种高温超高压高炉煤气锅炉的应用与研究[J].冶金动力,2017,(12):35—38.
[2]马研.钢铁企业煤气发电方式的选型探讨[J].河南冶金,2017,(4):23—24.
[3]吴红.135MW超高压煤气锅炉与燃气一蒸汽联合循环发电技术经济比较[J].锅炉技术,2017,(4):23—26.。