最新离合器_文献综述知识讲解
离合器

离合器内容摘要:离合器是工程机械的重要总成,是主、从动部分在同轴线上传递动力或运动时,具有结合或分离功能的装置,其离合作用可以靠摩擦、啮合等方式来实现。
它的性能好坏关系着机车能否顺利起步和平稳换挡。
关键词:离合器功用、结构、原理AbstractClutch construction machinery assembly, is the Lord, the driven part of the coaxial transmission of power or motion, combination or separation of the function of the device, the clutch can rely on friction engagement. Its performance is good or bad the relationship between the locomotive to the smooth start-up and smooth shifting.Keywords:Clutch function、Clutch structure、Clutch principle、Failure Analysis一、离合器的功用1、保证汽车平稳起步:汽车起步前,应使变速器处于空挡位置,将发动机与驱动轮之间的联系断开,以卸除发动机负荷,此时离合器处于结合状态。
启动发动机,代发动机进入稳定怠速状态后(此时发动机处于最小平稳转速),然后踩离合器挂上一定挡位,使汽车起步(离合器处于脱开状态)。
然后逐渐松开离合器踏板,使离合器逐渐结合。
与此同时,逐渐踩下加速踏板,增加发动机的燃料供给,使发动机转速稳定,完成起步。
如果没有离合器,直接挂挡,则会瞬间产生很大的冲击,使发动机转速低于最小稳定转速,从而导致汽车熄火。
2、保证换挡工作平顺:在汽车行驶过程中,为了适应不断变化的行驶条件,传动系统经常要换用不同的挡位工作。
离合器工作原理

离合器工作原理引言概述:离合器作为汽车传动系统中的重要组成部份,扮演着连接发动机和变速器的角色。
它的工作原理直接影响着汽车的换挡平顺性和行驶安全性。
本文将详细介绍离合器的工作原理,包括离合器的结构和工作过程。
一、离合器的结构1.1 主动盘:主动盘是离合器的核心部件,也称为磨擦盘。
它是由磨擦材料和钢盘组成,磨擦材料通常采用耐磨性好的磨擦片。
主动盘通过与发动机的曲轴连接,承受发动机输出的扭矩。
1.2 从动盘:从动盘是离合器的另一个重要部件,也称为压盘。
它是由压盘弹簧、压盘盖和从动盘组成。
从动盘通过压盘弹簧与主动盘相连接,通过压盘盖与变速器的输入轴相连。
1.3 分离器:分离器位于主动盘和从动盘之间,是离合器的控制部件。
它通过离合器踏板的操作来控制离合器的开合状态。
当分离器处于开合状态时,主动盘和从动盘分离,发动机的动力不传递到变速器。
二、离合器的工作过程2.1 空挡状态:在空挡状态下,离合器处于彻底分离状态,主动盘和从动盘之间没有接触。
发动机的动力无法传递到变速器,车辆处于住手状态。
2.2 踩下离合器踏板:当驾驶员踩下离合器踏板时,分离器会将压盘与主动盘分离。
主动盘再也不与发动机的曲轴接触,发动机的动力无法传递到变速器。
车辆仍然处于住手状态。
2.3 松开离合器踏板:当驾驶员松开离合器踏板时,分离器会将压盘压紧到主动盘上。
主动盘与从动盘之间产生磨擦力,发动机的动力通过离合器传递到变速器。
车辆开始行驶。
三、离合器的工作原理3.1 磨擦传动:离合器的工作原理基于磨擦传动的原理。
当离合器处于闭合状态时,主动盘和从动盘之间产生磨擦力,使得两者之间的转速保持一致。
这样,发动机的动力可以顺利传递到变速器。
3.2 离合器的磨损:由于离合器在工作过程中需要承受高温、高压和高速运动等因素的影响,因此会产生磨损。
长期的使用会导致离合器片磨损严重,失去磨擦力,从而影响离合器的工作效果。
3.3 离合器的维护:为了保持离合器的正常工作,需要定期进行维护和保养。
膜片弹簧离合器文献综述和参考文献

膜片弹簧离合器文献综述和参考文献追溯到1891年,摩擦式汽车离合器第一次出现,之后经过半个世纪的发展,在1948年液力变矩器被发明,而现今,各种智能控制技术的发展日新月异。
一方面,可见汽车离合器技术的发展离不开汽车工业的创新和进步,另一方面,也预示了这个时代离合器的发展也将十分迅速,传统的汽车离合器必将随着新兴汽车传动技术的普及而逐渐被淘汰。
30465我国汽车离合器企业虽然发展迅速,但是与国外企业相比有诸多不足。
在内部能力方面不及国外,产品的质量与国外相比有着很大的差距,技术含量不高。
国内汽车离合器能在国际市场上排的上名的品牌很少,数一数二的都在国外,这是不争的事实。
同时,企业在技术研发、员工管理、人才培养、生产效率等方面想要与国际水平接轨还需时日[2]。
另一方面,我国企业也有优势的一面,如在劳动力成本方面较国外低,售价较低,销售渠道广。
而在采购成本、销售市场开发等方面,我国与国际水平相持。
论文网在产品研发和技术创新方面,国内取得了欣慰的成果。
借鉴国外的技术,我国的新一代产品的研发,如双质量飞轮、液力变矩器都有收获。
经过长足的发展,国内汽车离合器企业的产业结构得到了优化,国产膜片弹簧离合器的品种日趋丰富,已经达到能全面覆盖各类车型需求的技术水平[3]。
为了提高汽车的舒适性,更好地降低传动系的噪声,双质量飞轮的扭转减振器得到了更多的应用。
现如今商用车往大型化的方向发展,对于重型离合器,离合器的尺寸不能无限加大,因此离合器的使用条件显得尤为苛刻,如何提高离合器的扭转能力以及如何简化操作成了重型离合器发展需要解决的问题。
双片干式离合器可以提高离合器的扭转能力,曾广泛应用于重型车。
然而考虑到其他各种因素的作用,实际的效果并不理想。
在国外,湿式离合器在近几年作为新技术进入了人们的视野,不同于干式离合器,湿式离合器用油泵进行冷却,降低了摩擦表面的温度,从而起到了保护摩擦片的作用。
湿式离合器的使用寿命大大高于传统的干式离合器,唯一的缺点是,湿式离合器需要在一定的温度下才能正常工作,否则将会产生负面效应。
离合器常识
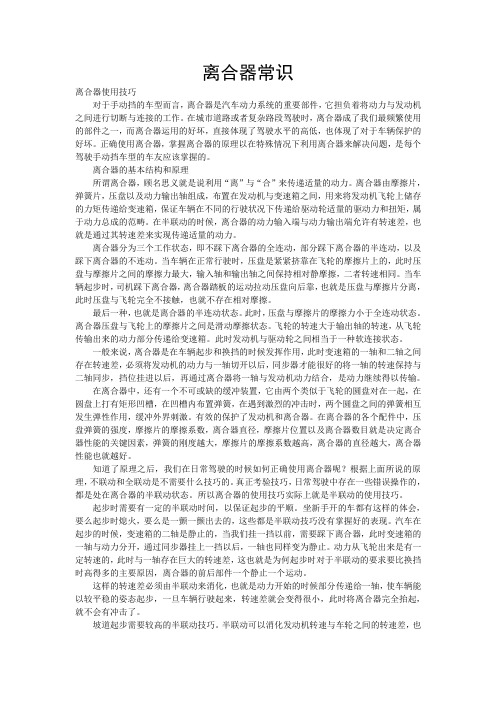
离合器常识离合器使用技巧对于手动挡的车型而言,离合器是汽车动力系统的重要部件,它担负着将动力与发动机之间进行切断与连接的工作。
在城市道路或者复杂路段驾驶时,离合器成了我们最频繁使用的部件之一,而离合器运用的好坏,直接体现了驾驶水平的高低,也体现了对于车辆保护的好坏。
正确使用离合器,掌握离合器的原理以在特殊情况下利用离合器来解决问题,是每个驾驶手动挡车型的车友应该掌握的。
离合器的基本结构和原理所谓离合器,顾名思义就是说利用“离”与“合”来传递适量的动力。
离合器由摩擦片,弹簧片,压盘以及动力输出轴组成,布置在发动机与变速箱之间,用来将发动机飞轮上储存的力矩传递给变速箱,保证车辆在不同的行驶状况下传递给驱动轮适量的驱动力和扭矩,属于动力总成的范畴。
在半联动的时候,离合器的动力输入端与动力输出端允许有转速差,也就是通过其转速差来实现传递适量的动力。
离合器分为三个工作状态,即不踩下离合器的全连动,部分踩下离合器的半连动,以及踩下离合器的不连动。
当车辆在正常行驶时,压盘是紧紧挤靠在飞轮的摩擦片上的,此时压盘与摩擦片之间的摩擦力最大,输入轴和输出轴之间保持相对静摩擦,二者转速相同。
当车辆起步时,司机踩下离合器,离合器踏板的运动拉动压盘向后靠,也就是压盘与摩擦片分离,此时压盘与飞轮完全不接触,也就不存在相对摩擦。
最后一种,也就是离合器的半连动状态。
此时,压盘与摩擦片的摩擦力小于全连动状态。
离合器压盘与飞轮上的摩擦片之间是滑动摩擦状态。
飞轮的转速大于输出轴的转速,从飞轮传输出来的动力部分传递给变速箱。
此时发动机与驱动轮之间相当于一种软连接状态。
一般来说,离合器是在车辆起步和换挡的时候发挥作用,此时变速箱的一轴和二轴之间存在转速差,必须将发动机的动力与一轴切开以后,同步器才能很好的将一轴的转速保持与二轴同步,挡位挂进以后,再通过离合器将一轴与发动机动力结合,是动力继续得以传输。
在离合器中,还有一个不可或缺的缓冲装置,它由两个类似于飞轮的圆盘对在一起,在圆盘上打有矩形凹槽,在凹槽内布置弹簧,在遇到激烈的冲击时,两个圆盘之间的弹簧相互发生弹性作用,缓冲外界刺激。
综述论文(离合器)
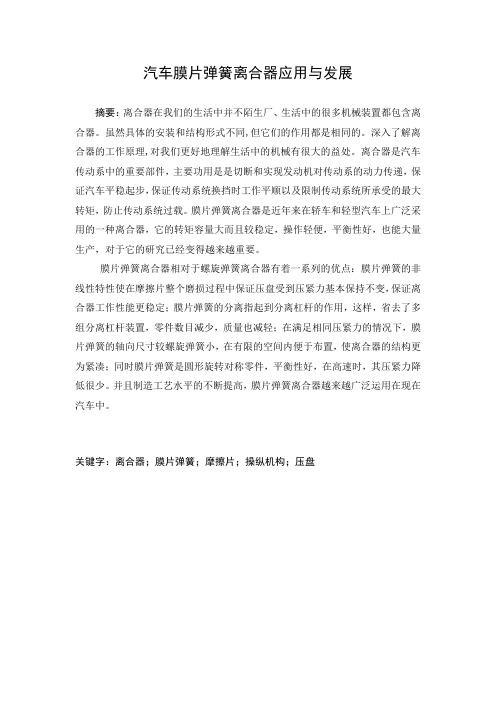
汽车膜片弹簧离合器应用与发展摘要:离合器在我们的生活中并不陌生厂、生活中的很多机械装置都包含离合器。
虽然具体的安装和结构形式不同,但它们的作用都是相同的。
深入了解离合器的工作原理,对我们更好地理解生活中的机械有很大的益处。
离合器是汽车传动系中的重要部件,主要功用是是切断和实现发动机对传动系的动力传递,保证汽车平稳起步,保证传动系统换挡时工作平顺以及限制传动系统所承受的最大转矩,防止传动系统过载。
膜片弹簧离合器是近年来在轿车和轻型汽车上广泛采用的一种离合器,它的转矩容量大而且较稳定,操作轻便,平衡性好,也能大量生产,对于它的研究已经变得越来越重要。
膜片弹簧离合器相对于螺旋弹簧离合器有着一系列的优点:膜片弹簧的非线性特性使在摩擦片整个磨损过程中保证压盘受到压紧力基本保持不变,保证离合器工作性能更稳定;膜片弹簧的分离指起到分离杠杆的作用,这样,省去了多组分离杠杆装置,零件数目减少,质量也减轻;在满足相同压紧力的情况下,膜片弹簧的轴向尺寸较螺旋弹簧小,在有限的空间内便于布置,使离合器的结构更为紧凑;同时膜片弹簧是圆形旋转对称零件,平衡性好,在高速时,其压紧力降低很少。
并且制造工艺水平的不断提高,膜片弹簧离合器越来越广泛运用在现在汽车中。
关键字:离合器;膜片弹簧;摩擦片;操纵机构;压盘Automobile diaphragm spring clutch application and developmentAbstract: the clutch in our life, life is no stranger to plant many mechanical devices are included in the clutch. Though the installation and structure is different, but their functions are the same. Insight into the working principle of the clutch for us to understand life better machinery is of great benefit. Clutch is an important part in automotive transmission system, is the main function is to cut off the and realize the engine to the transmission of power transmission, ensure smooth start of the car, for ensuring the smooth and transmission when shifting transmission system on the maximum torque, to prevent the transmission system overload. Diaphragm spring clutch is widely used in cars and light motor vehicles in recent years of a clutch, its great capacity of torque and relatively stable, convenient operation, good balance, can also be a large number of production, has become more and more important for its research.Diaphragm spring clutch is relative to the spiral spring clutch has a series of advantages: the nonlinear characteristics of diaphragm spring to make the whole process of wear and tear in friction, maintain invariable pressure plate by basic compaction force, to ensure the clutch performance is more stable; Separation of the diaphragm spring refers to the separation of leverage effect, in this way, eliminating the leverage multiple sets of separation device, part number, quality and to reduce; To meet the same compression force, axial size of the diaphragm spring is a spiral spring is small, within the limited space to decorate, make the structure of the clutch is more compact; Diaphragm spring is round rotation symmetric parts at the same time, good balance, at high speed, reduce the pressure force is seldom. And manufacturing technology level unceasing enhancement, the diaphragm spring clutch is more and more widely used in the car now.Key words: clutch; Diaphragm spring. friction plate. Operating mechanism; Pressure plate一、国内外研究现状多年的实践经验和技术上的改进使人们逐渐趋向于首选单片干式摩擦离合器,因为它具有从动部分转动惯量小、散热性好、结构简单、调整方便、尺寸紧凑、分离彻底等优点,而且由于在结构上采取一定措施,已能做到接合盘式平顺,因此现在广泛采用于大、中、小各类车型中。
离合器的工作原理
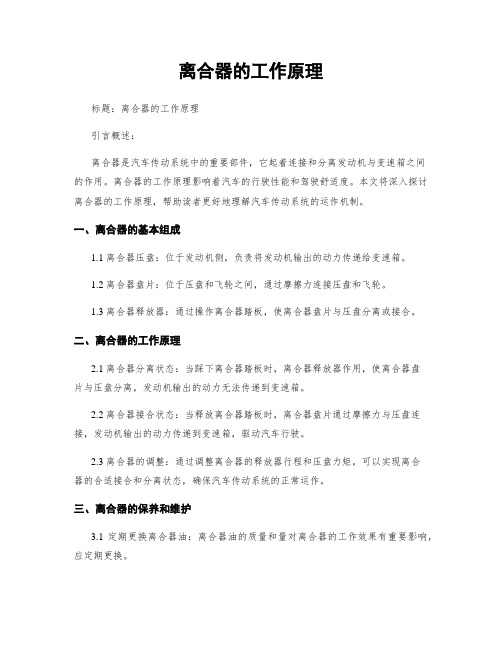
离合器的工作原理标题:离合器的工作原理引言概述:离合器是汽车传动系统中的重要部件,它起着连接和分离发动机与变速箱之间的作用。
离合器的工作原理影响着汽车的行驶性能和驾驶舒适度。
本文将深入探讨离合器的工作原理,帮助读者更好地理解汽车传动系统的运作机制。
一、离合器的基本组成1.1 离合器压盘:位于发动机侧,负责将发动机输出的动力传递给变速箱。
1.2 离合器盘片:位于压盘和飞轮之间,通过摩擦力连接压盘和飞轮。
1.3 离合器释放器:通过操作离合器踏板,使离合器盘片与压盘分离或接合。
二、离合器的工作原理2.1 离合器分离状态:当踩下离合器踏板时,离合器释放器作用,使离合器盘片与压盘分离,发动机输出的动力无法传递到变速箱。
2.2 离合器接合状态:当释放离合器踏板时,离合器盘片通过摩擦力与压盘连接,发动机输出的动力传递到变速箱,驱动汽车行驶。
2.3 离合器的调整:通过调整离合器的释放器行程和压盘力矩,可以实现离合器的合适接合和分离状态,确保汽车传动系统的正常运作。
三、离合器的保养和维护3.1 定期更换离合器油:离合器油的质量和量对离合器的工作效果有重要影响,应定期更换。
3.2 注意离合器的使用方式:避免长时间半离合状态或急剧踩离合器,可以延长离合器寿命。
3.3 定期检查离合器磨损情况:及时发现离合器磨损现象,可以及时更换离合器,避免对其他汽车部件造成损坏。
四、离合器故障及解决方法4.1 离合器打滑:可能是离合器盘片磨损过度或离合器压盘失效,需更换相应部件。
4.2 离合器异响:可能是离合器释放器弹簧松动或离合器盘片磨损不均,需及时检修。
4.3 离合器抖动:可能是离合器盘片失衡或离合器释放器调整不当,需进行调整或更换。
五、离合器的发展趋势5.1 自动离合器技术:随着科技的发展,自动离合器技术将逐渐普及,提高汽车驾驶的便利性和舒适性。
5.2 电动汽车离合器:随着电动汽车的兴起,电动汽车离合器将逐渐取代传统离合器,提高电动汽车的能效和驾驶性能。
文献综述-联轴器、离合器、制动器简介
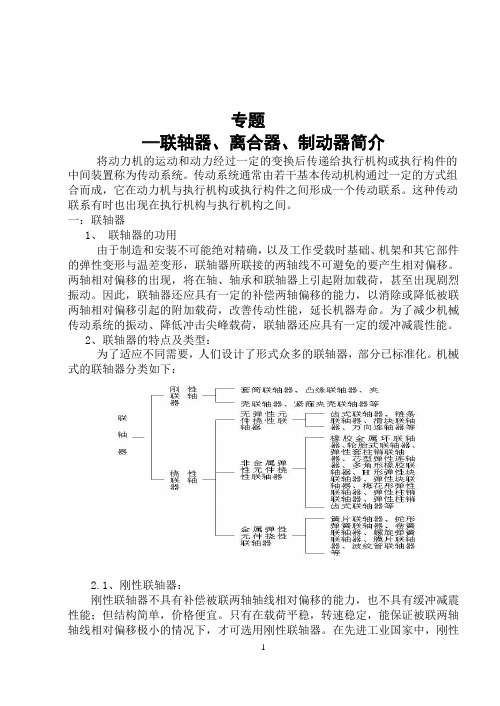
专题—联轴器、离合器、制动器简介将动力机的运动和动力经过一定的变换后传递给执行机构或执行构件的中间装置称为传动系统。
传动系统通常由若干基本传动机构通过一定的方式组合而成,它在动力机与执行机构或执行构件之间形成一个传动联系。
这种传动联系有时也出现在执行机构与执行机构之间。
一:联轴器1、联轴器的功用由于制造和安装不可能绝对精确,以及工作受载时基础、机架和其它部件的弹性变形与温差变形,联轴器所联接的两轴线不可避免的要产生相对偏移。
两轴相对偏移的出现,将在轴、轴承和联轴器上引起附加载荷,甚至出现剧烈振动。
因此,联轴器还应具有一定的补偿两轴偏移的能力,以消除或降低被联两轴相对偏移引起的附加载荷,改善传动性能,延长机器寿命。
为了减少机械传动系统的振动、降低冲击尖峰载荷,联轴器还应具有一定的缓冲减震性能。
2、联轴器的特点及类型:为了适应不同需要,人们设计了形式众多的联轴器,部分已标准化。
机械式的联轴器分类如下:2.1、刚性联轴器:刚性联轴器不具有补偿被联两轴轴线相对偏移的能力,也不具有缓冲减震性能;但结构简单,价格便宜。
只有在载荷平稳,转速稳定,能保证被联两轴轴线相对偏移极小的情况下,才可选用刚性联轴器。
在先进工业国家中,刚性联轴器已淘汰不用。
属于刚性联轴器的有套筒联轴器、夹壳联轴器和凸缘联轴器等。
2.2、挠性联轴器:挠性联轴器具有一定的补偿被联两轴轴线相对偏移的能力,最大补偿量随型号不同而异。
凡被联两轴的同轴度不易保证的场合,都应选用挠性联轴器。
无弹性元件的挠性联轴器:载能力大,但也不具有缓冲减震性能,在高速或转速不稳定或经常正、反转时,有冲击噪声。
使用于低速、重载、转速中。
链条联轴器:是由两个带有相同齿数链轮的半联轴器,用一条滚子链连接组成。
起结构简单,装拆方便,效率高,可在高温、多尘、油污、潮湿等恶劣环境下工作;但不能承受轴向力。
万向联轴器:主要用于两轴有较大角向偏移的场合,最大角向补偿可达35-45度。
离合器知识大全

离合器的作用和四大分类离合器是主、从动部分在同轴线上传递动力或运动时,具有接合或分离功能的装置。
离合器位于发动机和变速箱之间的飞轮壳内,用螺钉将离合器总成固定在飞轮的后平面上,离合器的输出轴就是变速箱的输入轴。
在汽车行驶过程中,驾驶员可根据需要踩下或松开离合器踏板,使发动机与变速箱暂时分离和逐渐接合,以切断或传递发动机向变速器输入的动力。
主要包括主动部分、从动部分、压紧机构和操纵机构。
主动部分有:飞轮、离合器盖和压盘;从动部分是从动盘;压紧机构是压紧弹簧;操纵机构有分离叉、分离轴承、离合器踏板和传动部件。
离合器的作用1、保证汽车平稳起步这是离合器的首要功能。
在汽车起步前,自然要先起动发动机。
而汽车起步时,汽车是从完全静止的状态逐步加速的。
如果传动系(它联系着整个汽车)与发动机刚性地联系,则变速器一挂上档,汽车将突然向前冲一下,但并不能起步。
这是因为汽车从静止到前冲时,具有很大的惯性,对发动机造成很大地阻力矩。
在这惯性阻力矩作用下,发动机在瞬时间转速急剧下降到最低稳定转速(一般300-500RPM)以下,发动机即熄火而不能工作,当然汽车也不能起步。
因此,我们就需要离合器的帮助了。
在发动机起动后,汽车起步之前,驾驶员先踩下离合器踏板,将离合器分离,使发动机和传动系脱开,再将变速器挂上档,然后逐渐松开离合器踏板,使离合器逐渐接合。
在接合过程中,发动机所受阻力矩逐渐增大,故应同时逐渐踩下加速踏板,即逐步增加对发动机的燃料供给量,使发动机的转速始终保持在最低稳定转速上,而不致熄火。
同时,由于离合器的接合紧密程度逐渐增大,发动机经传动系传给驱动车轮的转矩便逐渐增加,到牵引力足以克服起步阻力时,汽车即从静止开始运动并逐步加速2、实现平顺的换档在汽车行驶过程中,为适应不断变化的行驶条件,传动系经常要更换不同档位工作。
实现齿轮式变速器的换档,一般是拨动齿轮或其他挂档机构,使原用档位的某一齿轮副推出传动,再使另一档位的齿轮副进入工作。
离合器结构原理
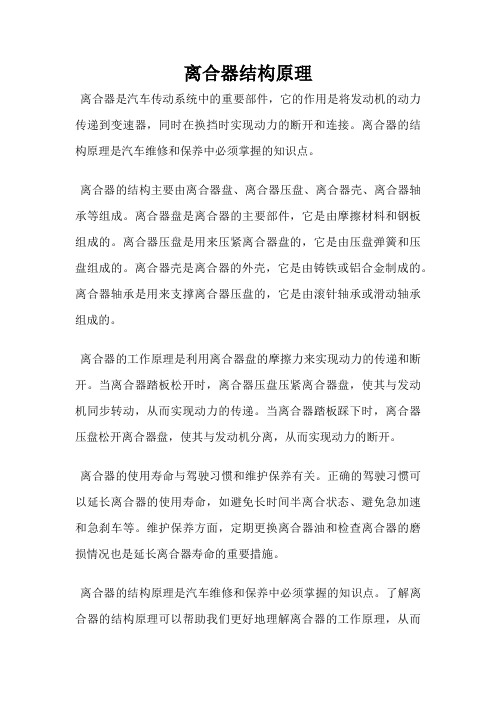
离合器结构原理
离合器是汽车传动系统中的重要部件,它的作用是将发动机的动力传递到变速器,同时在换挡时实现动力的断开和连接。
离合器的结构原理是汽车维修和保养中必须掌握的知识点。
离合器的结构主要由离合器盘、离合器压盘、离合器壳、离合器轴承等组成。
离合器盘是离合器的主要部件,它是由摩擦材料和钢板组成的。
离合器压盘是用来压紧离合器盘的,它是由压盘弹簧和压盘组成的。
离合器壳是离合器的外壳,它是由铸铁或铝合金制成的。
离合器轴承是用来支撑离合器压盘的,它是由滚针轴承或滑动轴承组成的。
离合器的工作原理是利用离合器盘的摩擦力来实现动力的传递和断开。
当离合器踏板松开时,离合器压盘压紧离合器盘,使其与发动机同步转动,从而实现动力的传递。
当离合器踏板踩下时,离合器压盘松开离合器盘,使其与发动机分离,从而实现动力的断开。
离合器的使用寿命与驾驶习惯和维护保养有关。
正确的驾驶习惯可以延长离合器的使用寿命,如避免长时间半离合状态、避免急加速和急刹车等。
维护保养方面,定期更换离合器油和检查离合器的磨损情况也是延长离合器寿命的重要措施。
离合器的结构原理是汽车维修和保养中必须掌握的知识点。
了解离合器的结构原理可以帮助我们更好地理解离合器的工作原理,从而
更好地维护和保养汽车。
双离合变速器文献综述
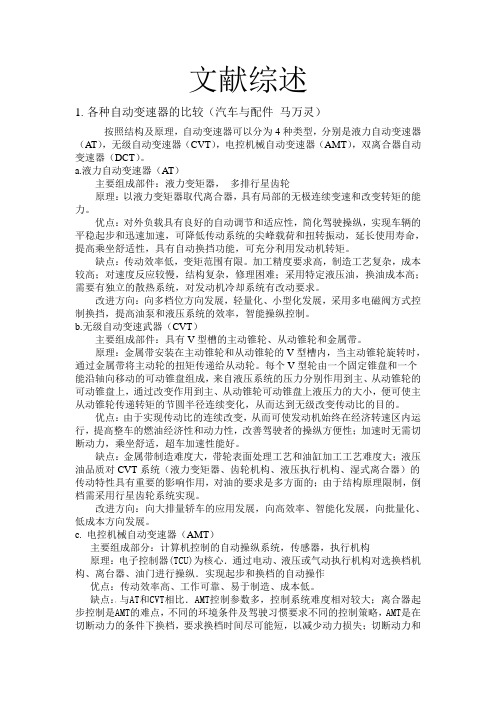
文献综述1.各种自动变速器的比较(汽车与配件马万灵)按照结构及原理,自动变速器可以分为4种类型,分别是液力自动变速器(AT),无级自动变速器(CVT),电控机械自动变速器(AMT),双离合器自动变速器(DCT)。
a.液力自动变速器(AT)主要组成部件:液力变矩器,多排行星齿轮原理:以液力变矩器取代离合器,具有局部的无极连续变速和改变转矩的能力。
优点:对外负载具有良好的自动调节和适应性,简化驾驶操纵,实现车辆的平稳起步和迅速加速,可降低传动系统的尖峰载荷和扭转振动,延长使用寿命,提高乘坐舒适性,具有自动换挡功能,可充分利用发动机转矩。
缺点:传动效率低,变矩范围有限。
加工精度要求高,制造工艺复杂,成本较高;对速度反应较慢,结构复杂,修理困难;采用特定液压油,换油成本高;需要有独立的散热系统,对发动机冷却系统有改动要求。
改进方向:向多档位方向发展,轻量化、小型化发展,采用多电磁阀方式控制换挡,提高油泵和液压系统的效率,智能操纵控制。
b.无级自动变速武器(CVT)主要组成部件:具有V型槽的主动锥轮、从动锥轮和金属带。
原理:金属带安装在主动锥轮和从动锥轮的V型槽内,当主动锥轮旋转时,通过金属带将主动轮的扭矩传递给从动轮。
每个V型轮由一个固定锥盘和一个能沿轴向移动的可动锥盘组成,来自液压系统的压力分别作用到主、从动锥轮的可动锥盘上,通过改变作用到主、从动锥轮可动锥盘上液压力的大小,便可使主从动锥轮传递转矩的节圆半径连续变化,从而达到无级改变传动比的目的。
优点:由于实现传动比的连续改变,从而可使发动机始终在经济转速区内运行,提高整车的燃油经济性和动力性,改善驾驶者的操纵方便性;加速时无需切断动力,乘坐舒适,超车加速性能好。
缺点:金属带制造难度大,带轮表面处理工艺和油缸加工工艺难度大;液压油品质对CVT系统(液力变矩器、齿轮机构、液压执行机构、湿式离合器)的传动特性具有重要的影响作用,对油的要求是多方面的;由于结构原理限制,倒档需采用行星齿轮系统实现。
离合器的简述-概念解析以及定义

离合器的简述-概述说明以及解释1.引言1.1 概述离合器是一种机械装置,用于连接和分离发动机与变速器之间的动力传递。
它在车辆的行驶过程中起着至关重要的作用,能够有效地控制发动机的输出,并使车辆平稳地启动和换挡。
本文将对离合器的作用、组成和工作原理进行详细介绍,同时探讨离合器在车辆维护和保养中的重要性,以及未来离合器技术的发展趋势。
通过深入了解离合器的相关知识,读者可以更好地理解车辆传动系统的运行原理,以及如何有效地维护和保养离合器,延长车辆的使用寿命。
文章结构部分内容如下:1.2 文章结构本文将分为三个部分来讨论离合器的相关内容。
首先,我们将介绍离合器的作用,包括它在汽车和机械设备中的重要性和功能。
接着,我们将深入探讨离合器的组成,包括其构造和组成部件。
最后,我们将详细解释离合器的工作原理,以便读者对其工作方式有更全面的了解。
通过这三个部分的分析,读者将对离合器有一个清晰的认识,并了解其在各种应用中的重要性和作用。
json"1.3 目的": {"content": "本文旨在介绍离合器的作用、组成和工作原理,以及强调离合器在汽车等机械设备中的重要性。
同时,也探讨了离合器的维护和保养方法,以及未来离合器技术的发展趋势。
通过本文的阐述,读者可以全面了解离合器的相关知识,为正确使用和维护离合器提供指导,促进离合器技术的进步和应用。
"}2.正文2.1 离合器的作用离合器是汽车传动系统中非常重要的一个部件,它的主要作用是将发动机和变速箱分离或连接,实现发动机与变速箱之间的有效传动。
离合器在汽车运行中起到了至关重要的作用,它能够实现发动机与变速箱的有效分离,在换挡时减少发动机转速的冲击,同时也能够在启动时将动力顺利传递给变速箱,为汽车的行驶提供了必要的保护和平稳性。
除了在换挡和启动时的作用之外,离合器还可以帮助汽车在行驶过程中提供一定的缓冲作用,减少变速箱和传动系统的损耗。
机车离合知识点总结
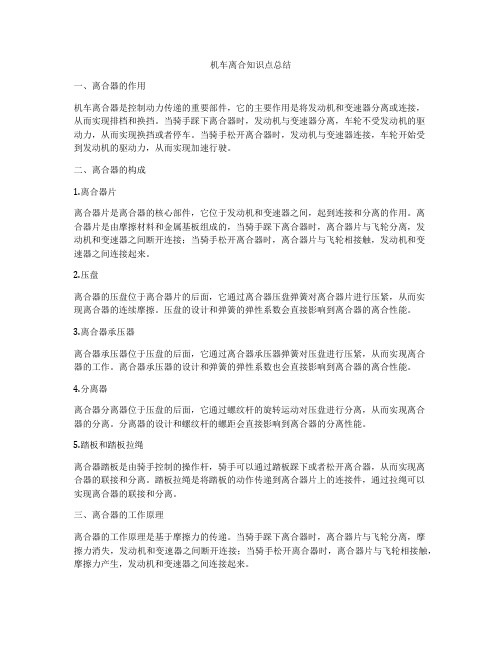
机车离合知识点总结一、离合器的作用机车离合器是控制动力传递的重要部件,它的主要作用是将发动机和变速器分离或连接,从而实现排档和换挡。
当骑手踩下离合器时,发动机与变速器分离,车轮不受发动机的驱动力,从而实现换挡或者停车。
当骑手松开离合器时,发动机与变速器连接,车轮开始受到发动机的驱动力,从而实现加速行驶。
二、离合器的构成1.离合器片离合器片是离合器的核心部件,它位于发动机和变速器之间,起到连接和分离的作用。
离合器片是由摩擦材料和金属基板组成的,当骑手踩下离合器时,离合器片与飞轮分离,发动机和变速器之间断开连接;当骑手松开离合器时,离合器片与飞轮相接触,发动机和变速器之间连接起来。
2.压盘离合器的压盘位于离合器片的后面,它通过离合器压盘弹簧对离合器片进行压紧,从而实现离合器的连续摩擦。
压盘的设计和弹簧的弹性系数会直接影响到离合器的离合性能。
3.离合器承压器离合器承压器位于压盘的后面,它通过离合器承压器弹簧对压盘进行压紧,从而实现离合器的工作。
离合器承压器的设计和弹簧的弹性系数也会直接影响到离合器的离合性能。
4.分离器离合器分离器位于压盘的后面,它通过螺纹杆的旋转运动对压盘进行分离,从而实现离合器的分离。
分离器的设计和螺纹杆的螺距会直接影响到离合器的分离性能。
5.踏板和踏板拉绳离合器踏板是由骑手控制的操作杆,骑手可以通过踏板踩下或者松开离合器,从而实现离合器的联接和分离。
踏板拉绳是将踏板的动作传递到离合器片上的连接件,通过拉绳可以实现离合器的联接和分离。
三、离合器的工作原理离合器的工作原理是基于摩擦力的传递。
当骑手踩下离合器时,离合器片与飞轮分离,摩擦力消失,发动机和变速器之间断开连接;当骑手松开离合器时,离合器片与飞轮相接触,摩擦力产生,发动机和变速器之间连接起来。
离合器的联接和分离是通过离合器承压器和分离器的协同作用实现的。
当骑手踩下离合器时,离合器承压器对压盘进行压紧,离合器片与飞轮分离;当骑手松开离合器时,分离器对压盘进行分离,离合器片与飞轮相接触。
离合器基础知识
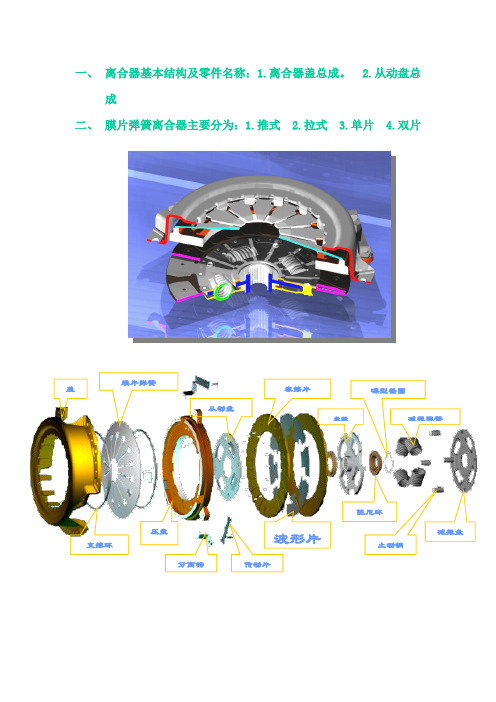
一、 离合器基本结构及零件名称:1.离合器盖总成。
2.从动盘总成二、 膜片弹簧离合器主要分为:1.推式 2.拉式 3.单片 4.双片盖 膜片弹簧支撑环 压盘 分离钩 传动片 从动盘 摩擦片 波形片 盘毂阻尼环 碟型垫圈 减振弹簧 止动销减振盘▲接合状态当离合器与发动机飞轮用螺栓紧固在一起时,膜片弹簧被预加压紧,离合器处于接合位置,此时,由于膜片弹簧力的作用,离合器压盘和飞轮将离合器从动盘压紧于飞轮和压盘之间,当离合器盖总成随飞轮转动时,就通过摩擦片上的摩擦转矩带动从动盘总成和驱动轴一起转动以传递发动机动力。
分离状态要分离离合器时,将离合器踏板踏下,通过操纵机构,使分离轴承前移推动分离指,膜片弹簧呈反锥形变形使其大端离开压盘,压盘在传动片的弹力作用下离开从动盘摩擦片,离合器处于分离位置,切断了发动机动力的传递。
离合器盖总成主要性能参数A、工作压紧力B、分离行程C、分离力D、压盘升程、压盘跳动E、总成的不平衡量F、分离指高度(装高)G、分离指端面跳动从动盘总成主要性能参数A、自由旋转量B、轴向压缩量C、压紧厚度、平行度D、扭转减振器的滞后值“一东”离合器的型号和编号1、用户有特殊要求的,按用户要求编号2、一汽图纸按汽研要求编号3、单片推式膜片弹簧离合器产品由产品的结构形式、摩擦片外径首用车,产地三部分组成。
4、拉式离合器的代号为DSP型。
5、对膜片弹簧双片离合器的编号为:后加(双片)字样。
6、对螺旋弹簧离合器编号为AS型。
7、当从动盘总成摩擦片装有石棉片和无石棉片,装无石棉摩擦片的加字母A以示区别。
8、零部件代号。
9、一汽编号及对照关系:一汽编号:膜片弹簧离合器用“CD”表示,单片离合器用“S”表示,双片离合器用“D”表示,螺旋弹簧离合器用“CC”表示。
这样一汽的CD330-S离合器对应我公司DS330,一汽的CD350-D双片离合器对应我公司DS350(双片)。
几种形式的离合器示意图DS型结构特点:膜簧与盖为有铆钉联接,有支承环、隔套、支撑圈如:DS330. DS350. DS380(K1.AIM.W3). DS395.DS400. DS430 DS400A3M(陶瓷)DKS型结构特点:盖与膜簧用支承铆钉联接,有前后支承环,无隔套如:DKS180(L8. L9. C11)DKS215. DKS225. DKS275.DKS260. DKS228DST型结构特点:膜簧与盖无铆钉联接,有支承环如:DST160 ,DST180(C5. H8)。
- 1、下载文档前请自行甄别文档内容的完整性,平台不提供额外的编辑、内容补充、找答案等附加服务。
- 2、"仅部分预览"的文档,不可在线预览部分如存在完整性等问题,可反馈申请退款(可完整预览的文档不适用该条件!)。
- 3、如文档侵犯您的权益,请联系客服反馈,我们会尽快为您处理(人工客服工作时间:9:00-18:30)。
文献综述前言汽车诞生100多年来,人们一直在研究汽车离合器技术,希望汽车运行更加快捷、舒适、安全、可靠。
对于以内燃机为动力的汽车,离合器在机械传动系统中作为一个独立的总成而存在的,它是汽车传动系中直接与发动机相连接的总成。
离合器的主动部分和从动部分借接触面间的摩擦作用,或是用液体作为传动介质,或是用磁力传动来传递转矩,使两者之间可以暂时分离,又可逐渐接合,在传动过程中又允许两部分相互转动。
目前在汽车上广泛采用的是用弹簧压紧的摩擦离合器。
发动机发出的转矩,通过飞轮及压盘与从动盘接触面的摩擦作用,传给从动盘。
当驾驶员踩下离合器踏板时,通过机件的传递,使膜片弹簧大端带动压盘后移,此时从动部分与主动部分分离。
摩擦离合器应能满足以下基本要求:(1)保证能传递发动机发出的最大转矩,并且还有一定的传递转矩余力。
(2)能作到分离时,彻底分离,接合时柔和,并具有良好的散热能力。
(3)从动部分的转动惯量尽量小一些。
这样,在分离离合器换档时,与变速器输入轴相连部分的转速就比较容易变化,从而减轻齿轮间冲击。
(4)具有缓和转动方向冲击,衰减该方向振动的能力,且噪音小。
(5)压盘压力和摩擦片的摩擦系数变化小,工作稳定。
(6)操纵省力,维修保养方便。
一、离合器的发展史在早期研发的离合器结构中,锥形离合器最为成功。
它的原型设计曾装在1889年德国戴姆勒公司生产的钢质车轮的小汽车上。
它是将发动机飞轮的内孔做成锥体作为离合器的主动件。
采用锥形离合器的方案一直延续到20世界20年代中叶,对当时来说,锥形离合器的制造比较容易,摩擦面容易修复。
它的摩擦材料曾用过驼毛带、皮革带等。
那时也曾出现过蹄-鼓式离合器来替代锥形离合器。
该结构采用内蹄-鼓式。
这种结构型式有利于在离心力作用下使蹄紧贴鼓面。
蹄-鼓式离合器用的摩擦元件为木块、皮革带等,蹄-鼓式离合器的重量较锥形离合器轻。
无论锥形离合器或蹄-鼓式式离合器,都容易造成分离不彻底甚至出现主、从动件根本无法分离的自锁现象(当时所提供的材料符合体的摩擦系数变化很大,容易引起自锁)。
现今所用的盘式离合器的先驱是多片盘式离合器,它是直到1925年以后才出现的。
多片离合器最主要的优点是,在汽车起步时离合器的接合比较平顺,无冲击。
早期的设计中,多片按成对布置设计,一个钢盘片对着一青铜盘片。
采用纯粹的金属对金属的摩擦副,把它们浸在油中工作,能达到更为满意的性能。
在1920年出现了单片干式离合器,这和发明了石棉基的摩擦面片有关。
但在那时相当一段时间内,由于技术设计上的缺陷,造成了单片离合器在接合时不够平顺等问题。
第一次世界大战后初期,单片离合器的从动盘金属片上是没有摩擦面片的,摩擦面片是帖附在主动件飞轮和压盘上,弹簧布置在中央,通过杠杆放大后作用在压盘上。
后来改用多个直径较小的弹簧(一般至少6个),沿着圆周布置直接压在压盘上,成为现今最为通用的螺旋弹簧布置方法。
这种布置在设计上带来了实实在在的好处,使压盘上弹簧的工作压力分布更均匀,并减小轴向尺寸。
多年的实践经验和技术上的改进使人们逐渐趋向于首选单片干式摩擦离合器,因为它具有从动部分转动惯量小、散热性好、结构简单、调整方便、尺寸紧凑、分离彻底等优点,而且由于在结构上采取一定措施,已能做到接合平顺,因此现在广泛用于大、中、小各类车型中。
如今单片干式摩擦离合器在结构设计方面相当完善。
采用具有轴向性的从动盘,提高了离合器的接合平顺性。
离合器从动盘总成中装有扭转减振器,防止了传动系统的扭转共振,减小了传动系噪声和动载荷。
随着人们对汽车舒适性要求的提高,离合器已在原有基础上得到不断改进,乘用车上越来越多地采用具有双质量飞轮的扭转减振器,能更有效地降低传动系的噪声。
二、国内现状从1891年摩擦式汽车离合器的诞生,到1948年液力变矩器的出现,再到各种智能控制技术不断应用于汽车工业,汽车离合器技术始终伴随着汽车工业的发展而发展。
随着新兴汽车传动技术的越来越普及应用,传统的汽车离合器将逐渐淡出历史舞台。
从企业内部能力分析,总体上看,我国汽车离合器企业与国外企业相比处于明显劣势。
在劳动力成本、售价、售后服务、客户关系和供应商关系等方面,我国企业处于明显优势;在市场营销能力、采购成本和交货期方面,我国企业与国外竞争者基本持平;在品牌价值、产品技术含量、产品质量、规模效应、生产效率、技术水平、研发能力和员工素质方面,我国企业与国际同类先进企业相比差距较大。
在产品技术方面,国内汽车离合器企业经过不断地产品结构调整,国产膜片弹簧离合器的品种已经能全面覆盖国内重、中、轻、轿、微及农用等车型的需求,跟踪国外动力传动系统技术,研发新一代产品也取得了可喜成果,如双质量飞轮、液力变矩器、适用于300马力以上动力配套的由430拉式膜片弹簧离合器都获得了成功。
在发展过程中,离合器企业无论是为了提高自身的竞争力,还是为了进入配套、出口市场,都十分重视强化企业内部管理。
三、离合器的分类汽车离合器有摩擦式离合器、液力偶合器、电磁离合器等几种。
摩擦式离合器又分为湿式和干式两种。
液力偶合器:靠工作液(油液)传递转矩,外壳与泵轮连为一体,是主动件;涡轮与泵轮相对,是从动件。
当泵轮转速较低时,涡轮不能被带动,主动件与从动件之间处于分离状态;随着泵轮转速的提高,涡轮被带动,主动件与从动件之间处于接合状态。
电磁离合器:靠线圈的通断电来控制离合器的接合与分离。
如在主动与从动件之间放置磁粉,则可以加强两者之间的接合力,这样的离合器称为磁粉式电磁离合器。
摩擦式离合器:按其从动盘的数目,又分为单盘式、双盘式和多盘式等几种。
湿式摩擦式离合器一般为多盘式的,浸在油中以便于散热。
1.从动盘数及干、湿式分类(1)单片干式摩擦离合器其结构简单,调整方便,轴向尺寸紧凑,分离彻底,从动件转动惯量小,散热性好,采用轴向有弹性的从动盘时也能接合平顺。
因此,广泛用于各级轿车及微、轻、中型客车与货车上,在发动机转矩不大于1000N·m的大型客车和重型货车上也有所推广。
当转矩更大时可采用双片离合器。
(2)双片干式摩擦离合器与单片离合器相比,由于摩擦面增多使传递转矩的能力增大,接合也更平顺、柔和;在传递相同转矩的情况下,其径向尺寸较小,踏板力较小。
但轴向尺寸加大且结构复杂;中间压盘的通风散热性差易引起过热而加快摩擦片的磨损甚至烧伤碎裂;分离行程大,调整不当分离也不易彻底;从动件转动惯量大易使换档困难等。
仅用于传递的转矩大且径向尺寸受到限制时。
(3)多片湿式离合器摩擦面更多,接合更加平顺柔和;摩擦片浸在油中工作,表面磨损小。
但分离行程大、分离也不易彻底,特别是在冬季油液粘度增大时;轴向尺寸大;从动部分的转动惯量大,故过去未得到推广。
近年来,由于多片湿式离合器在技术方面的不断完善,重型车上又有采用,并有不断增加的趋势。
因为它采用油泵对摩擦表面强制冷却,使起步时即使长时间打滑也不会过热,起步性能好,据称其使用寿命可较干式高出5~6倍。
2.压紧弹簧的结构型式及布置分类离合器压紧弹簧的结构型式有:圆柱螺旋弹簧、矩形断面的圆锥螺旋弹簧和膜片弹簧等。
可采用沿圆周布置、中央布置和斜置等布置型式。
根据压紧弹簧的型式及布置,离合器分为:(1)周置弹簧离合器周置弹簧离合器的压紧弹簧是采用圆柱螺旋弹簧并均匀布置在一个圆周上。
有的重型汽车将压紧弹簧布置在同心的两个圆周上。
周置弹簧离合器的结构简单、制造方便,过去广泛用于各种类型的汽车上。
现代由于轿车发动机转速的提高(最高转速高达5000~7000r/min或更高),在高转速离心力的作用下,周置弹簧易歪斜甚至严重弯曲鼓出而显著降低压紧力;另外,也使弹簧靠到定位座柱上而使接触部位严重磨损甚至出现断裂现象。
因此,现代轿车及微、轻、中型客车多改用膜片弹簧离合器。
但在中、重型货车上,周置弹簧离合器仍得到广泛采用。
(2)中央弹簧离合器采用一个矩形断面的圆锥螺旋弹簧或用1~2个圆柱螺旋弹簧做压簧并布置在离合接触,因此压盘由于摩擦而产生的热量不会直接传给弹簧而使其回火失效。
压簧的压紧力是经杠杆系统作用于压盘,并按杠杆比放大,因此可用力量较小的弹簧得到足够的压盘压紧力,使操纵较轻便。
采用中央圆柱螺旋弹簧时离合器的轴向尺寸较大,而矩形断面的锥形弹簧则可明显缩小轴向尺寸,但其制造却比较困难,故中央弹簧离合器多用在重型汽车上以减轻其操纵力。
根据国外的统计资料:当载货汽车的发动机转矩大于400~450N·m时,常常采用中央弹簧离合器。
(3)斜置弹簧离合器是重型汽车采用的一种新型结构。
以数目较多的一组圆柱螺旋弹簧为压紧弹簧,分别以倾角(弹簧中心线与离合器中心线间的夹角)斜向作用于传力套上,后者再推动压杆并按杠杆比放大后作用到压盘上。
这时,作用在压杆内端的轴向推力等于弹簧压力的轴向分力。
当摩擦片磨损后压杆内端随传力套前移,使弹簧伸长,压力减小,倾角亦减小,而cos值则增大。
这样即可使在摩擦片磨损范围内压紧弹簧的轴向推力几乎保持不变,从而使压盘的压紧力也几乎保持不变。
同样,当离合器分离时后移传力套,压盘的压紧力也大致不变。
因此,斜置弹簧离合器与前两种离合器相比,其突出优点是工作性能十分稳定。
与周置弹簧离合器比较,其踏板力约可降低35%。
(4)膜片弹簧离合器膜片弹簧离合器具有很多优点:首先,由于膜片弹簧具有非线性特性,因此可设计成当摩擦片磨损后,弹簧压力几乎可以保持不变,且可减轻分离离合器时的踏板力,使操纵轻便;其次,膜片弹簧的安装位置对离合器轴的中心线是对称的,因此其压力实际上不受离心力的影响,性能稳定,平衡性也好;再者,膜片弹簧本身兼起压紧弹簧和分离杠杆的作用,使离合器的结构大为简化,零件数目减少,质量减小并显著地缩短了其轴向尺寸;另外,由于膜片弹簧与压盘是以整个圆周接触,使压力分布均匀,摩擦片的接触良好,磨损均匀,也易于实现良好的散热通风等。
膜片弹簧离合器在轿车及微型、轻型客车上已得到广泛的采用,而且逐渐扩展到载货汽车上。
国外已设计生产了传递转矩为80~2000N·m、最大摩擦片外径达420mm的膜片弹簧离合器系列,广泛用于轿车、客车、轻型和中型货车上。
甚至某些总质量达28~32t的重型汽车也有采用膜片弹簧离合器的。
但膜片弹簧的制造成本比圆柱螺旋弹簧要高。
膜片弹簧离合器的操纵曾经都是采用压式结构。
当前,膜片弹簧离合器的压式操纵已为拉式操纵结构所取代。
后者的膜片弹簧为反装,并将支承圈移到膜片弹簧的大端附近,使结构简化、零件减少、拆装方便;膜片弹簧的应力分布也得到改善,最大应力下降;支承圈磨损后仍保持与膜片的接触使离合器踏板的自由行程不受影响。
而在压式结构中支承圈的磨损会形成间隙而增大踏板的自由行程。
四、离合器发展趋势近年来,出现了扭转减振器特性和性能价格比较理想的双质量飞轮结构,这种飞轮由初级飞轮、扭转减振器和次级飞轮组成。