数值模拟在铸造充型及凝固过程的应用进展
模具温控成形技术及其应用于凝固过程数值模拟的研究进展
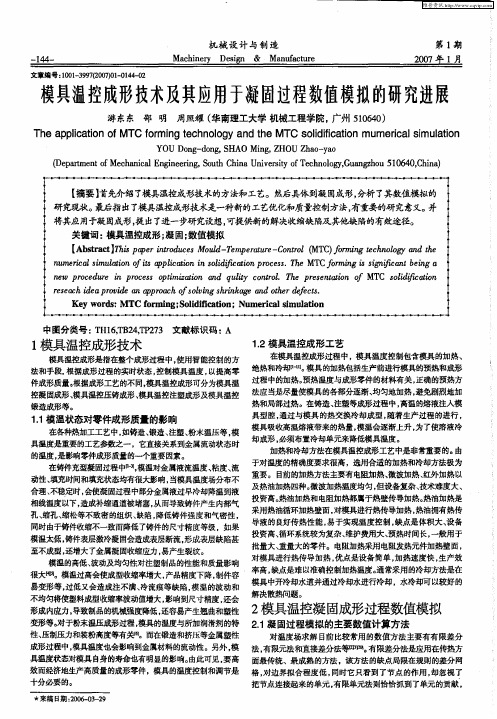
YOU Do g d n , HAO Mi g Z n — og S n , HOU Z a - a h o yo
维普资讯
机 械 设 计 与 制 造
一
第1 期
2o 0 7年 1月
1 4一 4
Ma hn r Dein & c iey sg
M a ua tr n fcue
模具温控成形技 术及其应 用于凝固 过程数 值模拟的 进展 研究
游东东 邵 明 周照耀 ( 华南理工大学 机械工程学院 。 广州 504 ) 160
【 摘要】 首先介绍了 模具温控成形技术的方法和工艺。然后具体到凝固成形, 分析了其数值模拟, 2, 23 T T A
1 模具温控成形技术
1 . 具温控成形工艺 2模
在模具温控成形过程中, 模具温度控制包含模具的加热、 模具温控成形是指在整个成形过程中, 使用智能控制的方 I。 _ I 法和手段, 根据成形过程的实 时状态 。 控制模具温度 , 以提高零 绝热和冷却【u模具的加热包括生产前进行模具的预热和成形 过程中的加热。 预热温度与成形零件的材料有关 。 正确的预热方 件成形质量 l 据成形工艺的不 同, 模具温控成形可分 为模具温 均匀地加热, 避免剧烈地加 控凝固 成形、 模具温控压铸成形、 模具温控注塑成形及模具温控 法应当是尽量使模具的各部分逐渐、 热和局部过热。在铸造、 注塑等成形过程中, 高温的熔液注人模 锻造成形等。
维普资讯
基于ANSYS软件二次开发的铸造充型和凝固耦合过程数值模拟研究

第33卷第5期四川大学学报(工程科学版)V ol.33N o.5 2001年9月JOURNA L OF SICH UAN UNI VERSITY(E NGI NEERI NG SCIE NCE E DITI ON)Sept.2001 文章编号:100923087(2001)0520047204基于ANSY S软件二次开发的铸造充型和凝固耦合过程数值模拟研究齐 慧,杨 屹,蒋玉明(四川大学制造科学与工程学院,四川成都610056)摘 要:对于ANSY S软件的通用性和缺乏专业针对性的特点。
采用ANSY S提供的二次开发工具开发了中文界面的铸造充型和凝固耦合过程数值模拟系统,实现了模块界面简洁和易操作性的预期功能,并证实了以ANSY S为平台开发专业模块的可行性。
关键词:ANSY S;二次开发;充型过程;数值模拟中图分类号:TG702文献标识码:ADeveloping System of Numerical Simulation of Mold Filling B ased on ANSYSQI Hui,Y ANG Yi,JIANG Yu2ming(C ollege of M anu facturing Sci.and Eng.,S ichuau Univ.,Chengdu610065,China)Abstract:According to ANSY S’s features of universality and lack of speciality,a numerical simulation program for m odel2 ing filling process of casting is developed based on ANSY S.The program has terse interface in Chinese.The feasibility of developing special m odules is verified by the practical applications of the simulation system.K ey w ords:ANSY S;redevelop;m old filling;numerical simulation ANSY S软件是融热、电、磁、流体、结构、声学于一体的大型通用有限元分析软件。
基于ANSYS铸件充型与凝固数值模拟的研究

型模拟 了一试验件 , 在模拟 的过 程 中分 别用 2种方 法对 流场进行 了模 拟 , 与 实测 结果进 行 比较 , 并 结果表 明 , 用充型过 程 的 采
维普资讯
铸 造技术
R I DRY T日C HN01 GY 0
V0 . 3 NO 4 12 .
J 12 0 u. 0 2
基 于 ANS YS铸件 充型 与凝 固数值 模拟 的研究
齐 慧, 杨 屹 ,蒋玉 明
( 四川 大学 , 四川 成 都 6 06 ) 10 5
方 法 更 接 近 实测 值 。
关键词 : 型过程 ; 值模 拟 ; 充 数 ANS S;流 动 Y
中图分类号 : 2 4 TG 4 文献标识码 : A 文章编号 : 008 6 2 0 )40 1 —3 10 —3 5(0 2 0 —2 60
Nu r c lS m u a i n u d F o a a a s e rn o d Filn fCa tn me i a i l to ofFl i w nd He tTr n f r Du i g M l li o s i l g g
此 采用 这 一模 型 。 e模 型 , K- 即用 两 个 紊 流 特 征 量 ( 紊
, + o = 0 、 。, 、
() 、, I 1
流动能 K 和紊流动能的耗散率 e 来表示动量守恒方 )
程 中 的紊 流粘 度 。 紊 流 动能 K 方 程 :
冷 隔等 缺 陷 , 而优 化铸 件 工 艺 , 进 实现 理想 的型 腔填 充 状 态 , 实 际 的铸 件 生产 具 有 重 要 的 指 导 意 义 。为 了 对 更精 确 地模 拟 铸 件 充 型 过 程 的 流 动 , 时 也 为 了能 够 同
铸造充型过程的数值模拟
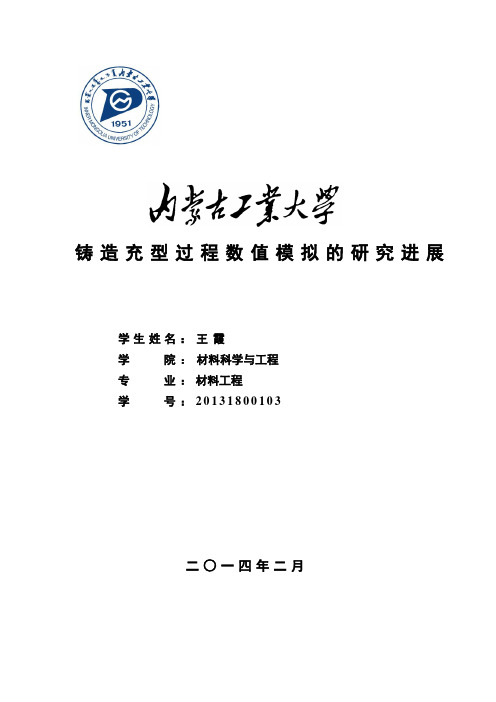
铸造充型过程数值模拟的研究进展(****:**学院:材料科学与工程专业:材料工程学号:20131800103二○一四年二月摘要铸造过程计算机数值模拟技术是当今材料科学的重要前沿领域。
本文从铸件充型数值模拟的发展过程、软件的开发状况、计算方法及验证方法等四个方面介绍了国内外铸件充型过程计算机数值模拟的概况。
关键词: 数值模拟; 充型过程; 铸件; 模拟软件AbstractThe technology of computernumerical simulation on casting process is an importangt frontal field of material science and technolgy.The present foreign and domestic research on compter digital simulation of casting process is summarized in the paper from four respects of evolution of numerical simulation of filling processes of castings,development state of software ,method to calculate and method to prove.Key words:numerical simulation ;filling process;castings;simulation software目录摘要 (1)Abstract (2)一前言 (1)二数值模拟的国内外发展概况 (1)三充型过程数值模拟技术新进展 (3)四铸造模拟软件的开发状况 (3)五充型过程数值模拟的计算方法 (4)4.1充型过程液体流动的数值模拟 (4)4.2 充型过程卷入缺陷的数值模拟 (5)六充型过程实验研究 (6)七结论与展望 (7)参考文献 (8)1 前言铸件充型过程数值模拟是随着电子计算机技术的飞速发展而发展起来的一种现代铸造工艺研究方法。
基于fluent的重力铸造充型凝固过程数值模拟研究
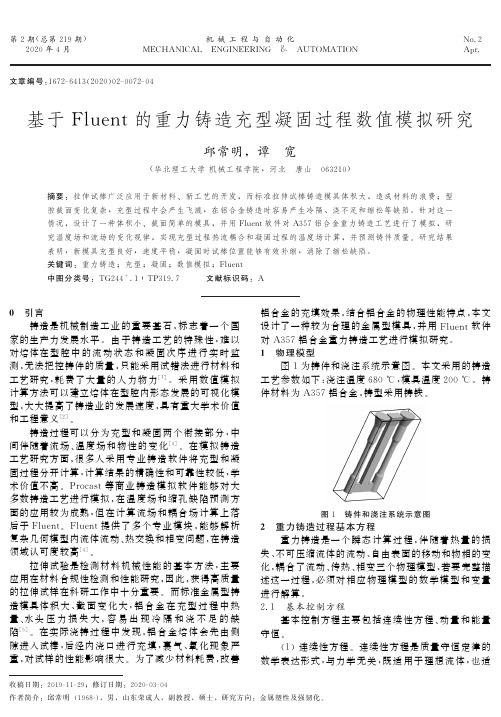
体和气体两相,自由表面移动前沿较为分明.
(
2)熔体到 达 横 浇 道 后 继 续 向 两 侧 充 填,直 浇 道
液体体积分数增大,但仍小于 1,两侧试 棒 底 端 液 体 体
积分数为 1,没有产生浇不足现象;此时 熔 体 由 内 浇 口
进入试棒进行反重力充填,液面较为平缓,无熔体飞溅
计算方法可以建立熔体在型腔内形态发展的可视化模
型,大大提高了铸造业的发展速度,具有重大学术价值
和工程意义 [2].
铸造过程可以分 为 充 型 和 凝 固 两 个 衔 接 部 分,中
间伴随着流 场、温 度 场 和 物 性 的 变 化 [3].在 模 拟 铸 造
工艺研究方面,很多 人 采 用 专 业 铸 造 软 件 将 充 型 和 凝
固过程分开计算,计算结果的精确性和可靠性较低,学
术价值不高.Pr
oc
a
s
t等 商 业 铸 造 模 拟 软 件 能 够 对 大
多数铸造工艺进行模 拟,在 温 度 场 和 缩 孔 缺 陷 预 测 方
面的应用较为成熟,但 在 计 算 流 场 和 耦 合 场 计 算 上 落
后于 F
l
uen
t.Fl
uen
t提供 了 多 个 专 业 模 块,能 够 解 析
2020 年第 2 期 邱常明,等:基于 F
l
uen
t的重力铸造充型凝固过程数值模拟研究
用于黏性流体.其数学形式为:
Əρ ▽( )
(
+ ρu =0 .
1)
Ə
t
其中:
kg/m3 ;
u 为流 体 的 速 度,
m/s;
t
《2024年低压铸造铝合金轮毂的数值模拟与工艺优化》范文
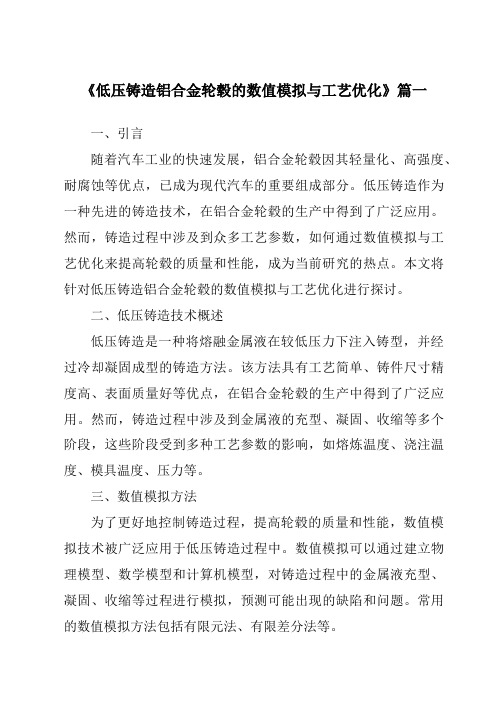
《低压铸造铝合金轮毂的数值模拟与工艺优化》篇一一、引言随着汽车工业的快速发展,铝合金轮毂因其轻量化、高强度、耐腐蚀等优点,已成为现代汽车的重要组成部分。
低压铸造作为一种先进的铸造技术,在铝合金轮毂的生产中得到了广泛应用。
然而,铸造过程中涉及到众多工艺参数,如何通过数值模拟与工艺优化来提高轮毂的质量和性能,成为当前研究的热点。
本文将针对低压铸造铝合金轮毂的数值模拟与工艺优化进行探讨。
二、低压铸造技术概述低压铸造是一种将熔融金属液在较低压力下注入铸型,并经过冷却凝固成型的铸造方法。
该方法具有工艺简单、铸件尺寸精度高、表面质量好等优点,在铝合金轮毂的生产中得到了广泛应用。
然而,铸造过程中涉及到金属液的充型、凝固、收缩等多个阶段,这些阶段受到多种工艺参数的影响,如熔炼温度、浇注温度、模具温度、压力等。
三、数值模拟方法为了更好地控制铸造过程,提高轮毂的质量和性能,数值模拟技术被广泛应用于低压铸造过程中。
数值模拟可以通过建立物理模型、数学模型和计算机模型,对铸造过程中的金属液充型、凝固、收缩等过程进行模拟,预测可能出现的缺陷和问题。
常用的数值模拟方法包括有限元法、有限差分法等。
四、工艺优化策略针对低压铸造铝合金轮毂的工艺优化,主要从以下几个方面进行:1. 优化熔炼工艺:通过调整熔炼温度、合金成分等参数,获得具有良好流动性和充型的金属液。
2. 优化浇注工艺:通过调整浇注温度、浇注速度等参数,控制金属液的充型过程,避免产生气孔、缩松等缺陷。
3. 优化模具设计:根据轮毂的结构特点和使用要求,设计合理的模具结构和尺寸,以提高轮毂的尺寸精度和表面质量。
4. 引入先进技术:如引入机器人自动化技术、在线检测技术等,实现铸造过程的自动化和智能化,提高生产效率和产品质量。
五、实例分析以某铝合金轮毂为例,通过数值模拟技术对其低压铸造过程进行模拟,分析不同工艺参数对轮毂质量和性能的影响。
在此基础上,对熔炼工艺、浇注工艺和模具设计进行优化,得到一组较佳的工艺参数。
熔铸AZS材料的铸造充型及凝固过程数值模拟

浇 注温度对铸 件 凝 固的影响 , 认 为较 为合 适 的浇 注温度在 1 8 1 0 左右 。 关 键词 : 熔铸 A Z S ; 充型 ; 凝固; 数 值模 拟
中图分类号 : T Q 1 7 5 文献标识码 : A 文章编 号 : 1 0 0 1— 1 9 3 5 ( 2 0 1 5 ) 0 5— 0 3 4 4— 0 5
的质量 。计算技术 的飞速发展为耐火砖熔铸成型过
程研 究提 供 了新 的研 究 手 段 。 。采 用 计 算 机 对 锆 刚玉熔 体 的充 型凝 固过程 进行 数值 仿 真分 析 , 可 以直
观地 观测 到其 充 型凝 固过 程 , 定量分析充型 、 传 热 凝 固规 律及 各 种 因 素 的 影 响 规 律 , 从 而 预 测 分 析 熔 铸
l 数 学及 物 理模 型 的建 立
1 . 1 数学 模型
由于充型 凝 固过程 的温度 场情 况 比较 复 杂 , 为 了
简 化模 型 , 进 行下列 假设 J : ( 1 )浇铸 的 A Z S 3 3熔 体 和 砂 型 的初 始 温 度 场均
匀 一致 ;
国 家科 技支 撑 计 划 课 题 资 助 项 目 ( 2 0 1 3 B AE 0 3 B 0 1 常庆 明 : 男, 1 9 6 4年 生 , 博士 , 教授 。
D O I : 1 0 . 3 9 6 9 / j . i s s n . 1 0 0 1 —1 9 3 5 . 2 0 1 5 . 0 5 . 0 0 6
熔铸锆刚玉 ( A Z S) 制 品 广 泛 应 用 于 玻 璃 制
备¨ 、 钢铁 冶 金行 业 , 是 一 种 非 常重 要 的 耐火 材
E- ma i l : q mc h a n g @ 1 6 3, t o n i
铸件凝固过程数值模拟的新进展

在处理奥氏体生长过程时
,Fras[ 4 ]等人采用了不
同于
Goettsch和
Dantzig的作法
,Fras等人认为奥氏
体枝晶的生长贯穿整个凝固过程
,并分别采用
:
xE = 1 -exp (-xe) (5)
xD = 1 -exp (-xd)= 1 -exp (-fix) (6)
μeΔTe
将共晶团内片层间距与晶粒半径相联系的模拟研究。
式
(9)中
,ε是共晶团的片层系数
;ΔTe是共晶生长的
—35 —
. 1995-2004 Tsinghua Tongfang Optical Disc Co., Ltd. All rights reserved.
以模拟铸件凝固过程中温度场变化规律为基础
内容的数值模拟
,如今已被许多学者称之为铸件凝固
过程的宏观模拟
(Macro2Modelling) [1~4]。铸件凝固
过程的宏观模拟经
30多年的不断发展
,目前已是成
熟技术
,它可以预测与铸件温度场直接相关的铸件的
宏观缺陷
,如
,有学者
[7、8 ]提出
:球墨铸铁凝固
的传统理论可能是不正确的。
在铸件凝固过程微观模拟的早期研究中
,研究者
们皆采用了完全形成共晶组织的合金或完全形成枝
晶组织的合金
,并且都是针对形状简单的小试样
(Biot数
< 0. 1)进行模拟研究的。显然
,这与实际铸
件的情况有很大差异
Rappaz对定向凝固的灰
计算机模拟技术在铸造中的应用

钩体是 ,工作中,承载最大 1
拉力 为 220k 5 N,主 要 集 中 在 主 、副 钩 上 ,因此
主、副钩部分不允许有缩孔 、缩松 、气孔等铸造缺 陷存在。由于钩体形状复杂 , 各部分厚薄不匀 ,且
曲面较多,仅凭设计人员按照理论计算铸件的质量 以及 各 部分 的模 数 ,冷铁 的大 小和 放置 的最 佳位 置 都极为困难。利用 “ 华铸 C E It A T凝 固模拟 A /n C S e 分析系统” 进行多次模拟 分析 ,最终制定 出合理
( 南阳二机石油装备 ( 团)有限公 司技术 中心) 集
摘要 铸件的凝固过程是一个复杂的高温、动态、瞬时的变化过程,在这个过程 中缩孔 、缩 松等铸造缺陷相继 出现。通过计算机模拟技术可 以在生产前发现这些缺陷的具体位置和 大小 ,并
将这些质量安全 隐患消灭在计算机模拟的反复比较优 化 中;利用计算机模拟技术可 以有效地控制 生产成本,使铸件获得很高的性价 比。
维普资讯
20 0 6年
第3 4卷
第 9期
张 良等 :计 算机模拟技术在铸造 中的应 用
了孤立液相区 ,最终在筒状 区中部形成缩松。主钩 区的缩松为对称分布 ,虽然在冒口的正下部 , 但主 钩根部较薄 ,两侧又放有冷铁 ,冷却快,造成在此 处 将 钢水 隔离 ,在 主钩头上 形成 孤立 液相 区 ,最 终
副钩
形成对称大小一样的缩松区域。由于负压危险区出 现在 冒1的正下部 ,只要将 冒口顶部挖 出适 当大小 3
的孔 洞 ,作 为排气 通道 即可解 决气 孔 问题 。
主钩
图 1 Y 25钩 体 三 维 图 G2
浇 挂持
6 ~ ~ 田
图 3 铸 件 的 充 型压 力 分 布
铸件充型凝固过程数值模拟实验报告

哈尔滨工业大学《材料加工过程数值模拟基础》实验课程铸件充型凝固过程数值模拟实验报告姓名:学号:班级:材料科学与工程学院铸件充型凝固过程数值模拟实验报告实验一:铸件凝固过程数值模拟一、实验目的1.学习有限差分法温度场模拟的数学模型和基本思路;2.掌握用AnyCasting 铸造模拟软件进行温度场模拟的方法。
二、实验原理1.有限差分法温度场模拟的基本思路:设计铸造工艺方案→根据定解条件求解能量方程→揭示凝固行为细节→预测凝固缺陷→改进工艺方案,返回第二步循环。
2.有限差分法温度场模拟的数学模型:222222T T T T L C t x y z t三、铸件凝固模拟过程及参数设置1.凝固模拟过程铸件、浇冒口等三维实体造型(输出STL 文件)→网格剖分、纯凝固过程参数设置等前处理→凝固温度场和收缩缺陷计算模拟数据→后处理得到动态的液相凝固、铸件色温图和缩孔缺陷等文件。
2.参数设置铸件材质:AC1B铸型材质:SM20C初始条件:上下模500℃,侧模400℃,升液管700℃。
边界条件:所有界面与空气间的界面传热系数都为10W/(m 2∙K),熔融金属液与模具之间的界面传热系数为4000 W/(m 2∙K),各部分模具间和模具与升液管间界面传热系数都为5000 W/(m 2∙K)。
四、模拟结果图1 冷却时间由于模拟中设置了水冷和空冷条件,所以铸件冷却速度较快。
由图1可知凝固首先发生在铸件表面,铸件的轮辋区厚度较薄,冷却速度比轮辐处冷却快。
内浇口先于轮辐凝固,在内浇口凝固后升液管内铝合金熔液无法对轮毂进行补缩,则在轮毂中最后凝固处容易产生缩松缩孔。
图2 冷却率由冷却率分布情况可知凝固过程中各部分冷却速率不同,可以判断出凝固时内应力较大的区域,在应力较大区域铸件容易产生裂纹缺陷。
由模拟结果中铸件的温度场情况,合理设置工艺参数减少缩松缩孔及裂纹的产生,合理布置冷却水管的分布位置。
实验二:铸件充型过程数值模拟一、实验目的1.学习有限差分法流动场模拟的数学模型和基本思路;2.掌握用AnyCasting 铸造模拟软件进行流动场模拟的方法。
铸造充型过程的FEM-MAC法数值模拟
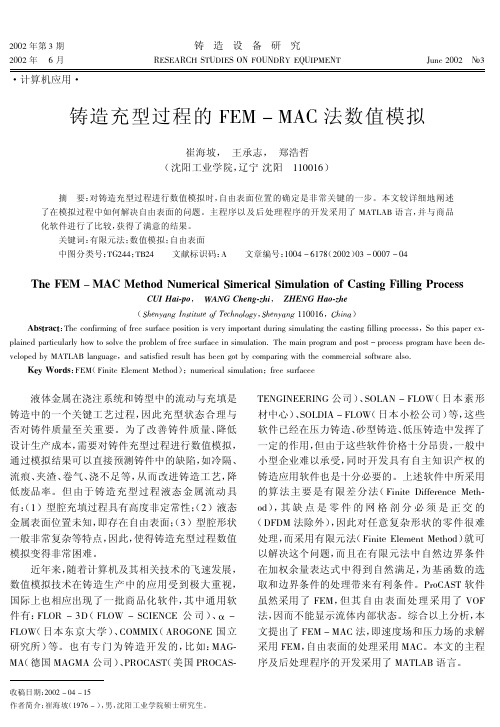
!"# $%& # &’( &#)"*+ ,-.#/0123 40.#/0123 40.-32)0*5 *6 (27)058 $033058 9/*1#77
!"# $%&’(),+ *+,- !./01’2.&,+ 3$4,- $%)’2./ ( !"#$%&$’ ($)*+*,*# -. /#0"$-1-’%,!"#$%&$’ %%""%),2"+$&) ’:7)/21):2F@ GH?IJKLJ?M HI IK@@ N>KIOG@ PHNJQJH? JN R@KS JLPHKQO?Q T>KJ?M NJL>UOQJ?M QF@ GONQJ?M IJUUJ?M PKHG@NNN,.H QFJN POP@K @VW PUOJ?@T POKQJG>UOKUS FHX QH NHUR@ QF@ PKHYU@L HI IK@@ N>KIOG@ J? NJL>UOQJH?Z 2F@ LOJ? PKHMKOL O?T PHNQ # PKHG@NN PKHMKOL FOR@ Y@@? T@W R@UHP@T YS </2B/C UO?M>OM@,O?T NOQJNIJ@T K@N>UQ FON Y@@? MHQ YS GHLPOKJ?M XJQF QF@ GHLL@KGJOU NHIQXOK@ OUNHZ ;#< =*/+7:8-<( 8J?JQ@ -U@L@?Q <@QFHT);?>L@KJGOU NJL>UOQJH?;IK@@ N>KIOG@@
!( .
镁合金半固态流变压铸充型凝固过程数值模拟及试验研究

s q e t l h n Ne o i nf i, h a e ih i ud c vt a e ds h r e n h u ly e u ni l ta wt na l d t e g s swhc mo l a i c n b ic a g d a d te q a i ay u n y t o h a t g c ud b mp o e ft e c s i o l e i r v d.Th e ut ft e n me ia i lt n a d t e e p r na n e r s l o h u r Ismua i n h x e i s c o me t I
.
a tmo i a d Itr dae S a ce lg (S P) o g e im aly a d s mi l uo bl n me neme it h f S rw P u e t IS fma n su l n e s i o od
m a n mu aly h v e n a ay e t h a g e m l a e b e n lz d wi t e s me m a h m a ia o e b t e wt na ud o h te t I c m d ewe n Ne o in f i l
a d s l ic t n p o e s o e io i a n su a ly a o tpa e m o e A i a t g p r o n oi f a i r c s fs m s l m g e im l b u lt di o d o d1 de c si a f n t
a d s mio i ud Th l l g c a a t ro n e s l f i. e mod fl h r ce fI dl ii n SSP t a h f i n h tr rd f cs o o e c l d a d te i e i e e t fI u n o SSP I n lz d o x e i na su is as b d n O t e SSP t r o - s h u r a S a ay e ,s me e p r me t I t de lo e o e t h I O p o f e t te n me i I t c
数值模拟在铸造充型及凝固过程的应用进展资料

数值模拟在铸造充型及凝固过程的应用进展摘要:综述了铸造过程中数值计算的基本理论,简要介绍了铸造充型及凝固当前国内外发展状况以及所存在的问题,并对铸造过程数值模拟的相关软件进行评述。
最后指出合理地利用铸造模拟软件,能够优化铸件的微观组织,提高产品质量,降低产品成本,缩短产品设计和试制周期。
关键词:铸造;充型过程;数值模拟;模拟软件The Application of Numerical Simulation in Mold Fillingand Solidification ProcessAbstract:The basic theory of numerical calculations is summarized, and a brief introduction of the developing situation and existing problems of the casting mold filling and solidification process at home and abroad,reviewed the numerical simulation software of casting process. In the end, it also clearly shows that it can optimize the casting microstructure, improve the quality, decrease the cost and reduce the design and trial cycle for the products by using the numerical simulation software properly.Key words: Casting; Filling and Solidification process; Numerical Simulation; Simulation Software1 前言铸造过程就是将高温的液态金属浇注到封闭的型腔中,通过充型和凝固过程最终获得所需形状铸件的热成形过程。
数值模拟在铸钢壳体铸件工艺优化中的应用

陷 ,按 比例 作 图法设 计 出 冒 口尺 寸 , 过 利 用 通 浇 注系 统来 对铸 件进 行
一
该铸件为铸钢件 , 铸造收缩率为 2 加工余量 %, 4mm, 水平 分 型 , 工水 玻 璃 砂 造 型 , 箱 一 型 , 手 一 铸 造工 艺 示意 见 图 2 。
收 稿 日期 :0 0 0 — 0 21~42
由于 华铸 C E分 析 系统 是 一 套基 于有 限 差分 A
原理编制的用 于模拟铸造充型凝 固过程的计算机 数值仿真软件 , 分为前置处理 、 计算处理和后 置处 理 三个 相对 独立 的模块 E。 前置处 理模 块 , 照不 在 按 同 的工 艺 方 案导 人 所 需 的组 成部 分 的 S L格式 文 T
定 的补 缩 。远 离浇 注
图 4 原始铸造 工艺 方案
系统 的部 位 用 2个 冒口 来 补 缩 , 寸 101I x 0 l 尺 2 I 20lm。见 图 4 TT I l 。
1 . 熔 化 工 艺 设 计 4
作者简 介 : 袁书仓 (9 2 )男 , 17 一 , 河南宜 阳人 , 工程 师 , 主要 从事铸 造 工艺设计和铸造凝固模拟应用 。
和发 生 的 时 间予 以有 效 的预 测 , 而优 化 铸 造 工 艺 从
1 . 浇 注 系统 设 计 2
根 据 铸 造 工 程
师手册 [, 结合现 场 生 产 经验 , 定 其 浇 确
注 系 统 尺 寸 ,直 浇 道 、 浇道 和 内 浇 口 横
设 计 , 保 铸件 质 量 l。 确 l l 本 设计 通 过采 用 PoE三维 造 型 软件 对 铸 钢壳 r/
2铸 件 的凝 固过程数 值模 拟
21 产 品 实体 建模 .
数值模拟技术在镁铝合金铸件工艺设计和优化中的应用

数 值模拟技术在镁铝合金铸件工艺设计 和 优 化 中 的应 用
A ppl i c at i on of num er i cal si m ul at i on t echnol ogy i n t h e desi gn and opt i mi z at i on o f m agnes i um al l o y ca st i ng pr ocess
品 。这 些 软 件 产 品都 是 基 于 有 限差 分 法 ( F DM ) 或 有 限 元法 ( F E M )的数 值 计 算 方 法 ,能 模拟 铸 件 的 充 型过 程 和 凝 固过 程 的 流 场 、 温 度场 分 布 , 铸 件 的缺 陷 分布 口 。因此 ,可 以说 铸 造模 拟软 件 的
浇 铸 、 消失 模 浇 铸 、熔 模 浇 铸 和 泥 模 浇铸 等 ,本 文 中镁铝 合金 铸件 的浇 铸方 式为金 属型 浇铸 。
D o i :1 0 . 3 9 6 9 / J . i s s n . 1 0 0 9 - 0 1 3 4 . 2 0 1 3 . 1 1 (I - ) . 1 1
0 引言
镁 铝 合 金 因其 优 良的 特 性 而 被 广 泛 使 用 。镁 铝 合 金 相较 于 其 他 应 用 广泛 的 金 属具 有 密 度 小 、 刚性 好 和 强度 高 等 特 点 ,而 其 优 良 的导 热 性 和 电
和An y Ca s t i n g 、美 国F i n i t e S o l u t i o n s 公 司设 计 的 S o l i d c a s t 、法国E S I 公 司 设 计 的P r o c a s t 等 软 件 产
造 工 艺 方 案 将 会 提 高 铸 件 的 质 量 和成 品率 ,保 证
铸造成形工艺过程的数值模拟仿真及其应用
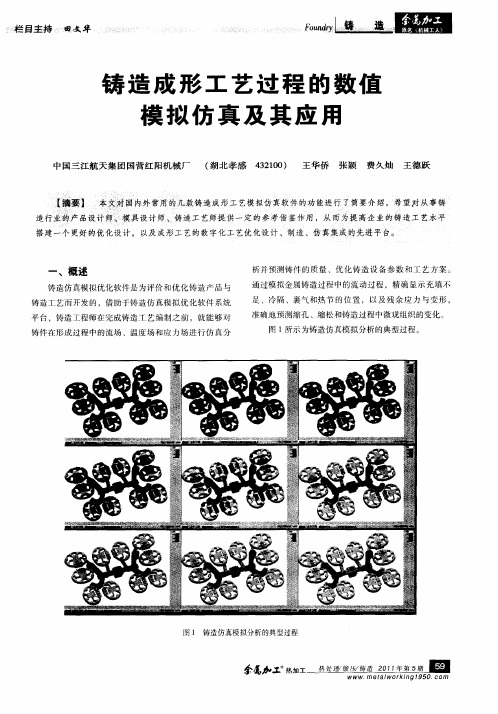
铸造仿真模拟优化软件是为评价 和优化铸 造产品 与
铸造工艺而开发 的,借助于铸造仿 真模拟优化 软件系统 平 台,铸造工程师在完成铸造『 艺 编制之前 ,就能够对 [
铸 件 在 形 成 过 程 中 的流 场 、温 度 场 和应 力 场 进 行 仿 真 分
通过模拟金属铸造 过程 中的流动过程 ,精确显 示充填不 足 、冷隔 、裹气和热节 的位置 ,以及 残余 应力 与变 形 , 准确地预测缩孑 、缩松 和铸造过程 中微观组织的变化 。 L
陷进行 预测 。数 据 库材 料 铸锌等各 类铸造 合金 ;可 针对 砂 型 、金属 型、熔模 、低压 、压力 、倾 斜铸造 及钢锭 模 铸 造等各种铸造方式进行真实 的模拟仿真分析 。 H C E系统 的前 置 处理 是 模 拟 过 程 的 准备 工作 , ZA 它实现 了 C D模 型 的导人 ,利 用 S L预览 检查 三维 造 A T 型是 否正确 ,进行有 限差分 网格的划分 。另外 ,还 可以 通过 H C E提供 的 C D功 能对 实体 造 型进 行 简 单 修 ZA A 改 。三维造型平 台用户可任选 ,绝大部 分三维造 型系 统
造行 业的 产 品设计 师 模 具设 计 师 、铸造 工 艺师提 供 一定 的参 考 借 鉴作 用 ,从 而为提 高 企 业 的铸 造 工 艺水平
搭建 一个更好 的优 化设计 , 以及 成形 工艺 的数 字化工 艺优 化设 计 、制 造 、仿 真集 成 的先进 平 台。
一
、
概述
析并预测铸件 的质量 、优化 铸造设 备参 数 和工艺方 案。
界面及模拟分析实例。
分布图及充型温度分 布图等。颜 色随意 调整 ,画面直接
毒 华 | ^
L 盈霉 _。 铸. 曩 曩 蓬
铝合金铸造充型凝固数值模拟的研究现状与发展
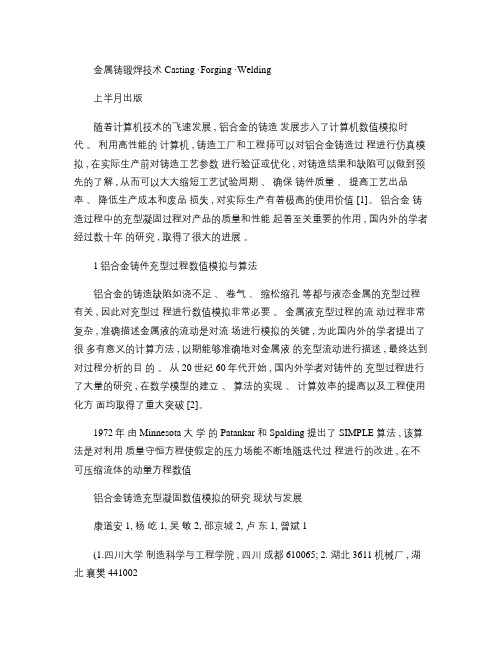
金属铸锻焊技术 Casting ·Forging ·Welding上半月出版随着计算机技术的飞速发展 , 铝合金的铸造发展步入了计算机数值模拟时代。
利用高性能的计算机 , 铸造工厂和工程师可以对铝合金铸造过程进行仿真模拟 , 在实际生产前对铸造工艺参数进行验证或优化 , 对铸造结果和缺陷可以做到预先的了解 , 从而可以大大缩短工艺试验周期、确保铸件质量、提高工艺出品率、降低生产成本和废品损失 , 对实际生产有着极高的使用价值 [1]。
铝合金铸造过程中的充型凝固过程对产品的质量和性能起着至关重要的作用 , 国内外的学者经过数十年的研究 , 取得了很大的进展。
1铝合金铸件充型过程数值模拟与算法铝合金的铸造缺陷如浇不足、卷气、缩松缩孔等都与液态金属的充型过程有关 , 因此对充型过程进行数值模拟非常必要。
金属液充型过程的流动过程非常复杂 , 准确描述金属液的流动是对流场进行模拟的关键 , 为此国内外的学者提出了很多有意义的计算方法 , 以期能够准确地对金属液的充型流动进行描述 , 最终达到对过程分析的目的。
从 20世纪 60年代开始 , 国内外学者对铸件的充型过程进行了大量的研究 , 在数学模型的建立、算法的实现、计算效率的提高以及工程使用化方面均取得了重大突破 [2]。
1972年由 Minnesota 大学的 Patankar 和 Spalding 提出了 SIMPLE 算法 , 该算法是对利用质量守恒方程使假定的压力场能不断地随迭代过程进行的改进 , 在不可压缩流体的动量方程数值铝合金铸造充型凝固数值模拟的研究现状与发展康道安 1, 杨屹 1, 吴敏 2, 邵京城 2, 卢东 1, 曾斌 1(1.四川大学制造科学与工程学院 , 四川成都 610065; 2. 湖北 3611机械厂 , 湖北襄樊 441002摘要 :铸造过程的计算机数值模拟是当前重要的研究方向 , 而铸件的充型凝固过程是整个模拟过程中的难点之一。
- 1、下载文档前请自行甄别文档内容的完整性,平台不提供额外的编辑、内容补充、找答案等附加服务。
- 2、"仅部分预览"的文档,不可在线预览部分如存在完整性等问题,可反馈申请退款(可完整预览的文档不适用该条件!)。
- 3、如文档侵犯您的权益,请联系客服反馈,我们会尽快为您处理(人工客服工作时间:9:00-18:30)。
数值模拟在铸造充型及凝固过程的应用进展摘要:综述了铸造过程中数值计算的基本理论,简要介绍了铸造充型及凝固当前国内外发展状况以及所存在的问题,并对铸造过程数值模拟的相关软件进行评述。
最后指出合理地利用铸造模拟软件,能够优化铸件的微观组织,提高产品质量,降低产品成本,缩短产品设计和试制周期。
关键词:铸造;充型过程;数值模拟;模拟软件The Application of Numerical Simulation in Mold Fillingand Solidification ProcessAbstract:The basic theory of numerical calculations is summarized, and a brief introduction of the developing situation and existing problems of the casting mold filling and solidification process at home and abroad,reviewed the numerical simulation software of casting process. In the end, it also clearly shows that it can optimize the casting microstructure, improve the quality, decrease the cost and reduce the design and trial cycle for the products by using the numerical simulation software properly.Key words: Casting; Filling and Solidification process; Numerical Simulation; Simulation Software1 前言铸造过程就是将高温的液态金属浇注到封闭的型腔中,通过充型和凝固过程最终获得所需形状铸件的热成形过程。
在整个过程中,速度场、应力场和温度场的相互耦合作用非常复杂,难以通过实时观察和测量得出科学的结果,因此利用计算机对铸造充型和凝固过程进行数值模拟显得非常必要。
从20世纪60年代开始凝固过程数值模拟,80年代初开始充型过程数值模拟和铸件应力应变数值模拟,到90年代兴起铸件微观组织数值模拟的研究,数值模拟技术已深入到铸件成形过程的各个方面,铸造过程的模拟仿真研究也正在向微观组织模拟、性能优化及使用寿命预测的方向发展,成为多功能、高保真、高效率的多学科模拟与仿真技术[1-2]。
根据美国科学研究院工程技术委员会的测定,计算机模拟仿真可提高产品质量5~15倍,提高产品合格率25%,降低生产成本13%~30%,降低人力成本5%~20%,增加投入设备利用率30%~60%,缩短产品设计和试制周期30%~60%。
由此可见,材料制备工艺的计算机模拟在材料研究领域的发展潜力是巨大的。
据悉,美国已经大量采用计算机模拟仿真方法来研究开发汽车、飞机、导弹、航空及航海等装备发动机的结构设计、成形加工及制造[2]。
铸造过程计算机数值模拟,包括凝固过程温度场的数值模拟、充型过程流动场的数值模拟、应力场数值模拟和微观组织形态的数值模拟。
通过对这些单一和耦合过程数值模拟的研究,可以对铸件成形过程中产生的诸如缩孔、缩松、气孔、夹渣、浇不足、裂纹等各种铸造质量问题进行分析,找出其产生的内在原因,达到优化铸造工艺,消除铸造缺陷,提高产品质量的作用。
可以在生产之前,通过铸造模拟软件对其过程质量进行预测,对不同的工艺方案进行质量对比,实施工艺优化[3-4]。
由于产品质量预测在计算机上进行,并没有经过实际生产,因而可以节省大量的人力、物力、财力。
尤其是新产品试制和大批量造型线生产的铸件,既方便快捷又有显著的经济效益。
通过计算机数值模拟还可以使一直建立在生产经验基础上的旧铸造工艺设计从经验走向科学。
2 充型和凝固过程模拟的发展概况2.1充型过程数值模拟发展及研究现状充型是铸造过程中一个重要的阶段,液态金属充型过程的不平稳和充填顺序不合理以及充型时间过长会造成卷气、冷隔和浇不足等缺陷。
但由于充型流动的模拟比起温度场的模拟更加复杂。
与凝固过程计算机模拟相比,充型过程计算机模拟起步较晚,在液态金属的充型过程中,金属液的流动绝大多数是紊流[5],而且充型时间非常短,并伴有传热现象,流场和温度场都在不断变化、相互影响。
此外,型腔内金属液与铸型间的热阻、型壁状况、入流条件、结晶潜热及固相率等都影响充型过程,使充型过程的计算机模拟成为一个相当复杂的数值模拟问题[6]。
由于离心铸造复合轧辊的充型过程中液态金属和铸型温度变化较大,因此充型模拟分析显得尤为重要。
进行充型模拟不仅可以模拟分析充型过程中液态金属的流动,预测缺陷,也为凝固模拟分析提供必要的初始温度场。
在美国国家科学基金会赞助下,台湾学者黄文星在美国匹兹堡大学与R.A.Stoehr教授一起开展了这方面的研究,并于1983年发表了一篇关于液态金属进入一水平方形铸型时金属流动情况的报道,显示了不同内浇口流速时流动模式的差异[7]。
开辟了充型过程研究的新领域,奠定了充型过程计算机模拟的基础。
1985年,黄文星在匹兹堡大学完成了题为“计算机辅助充型过程流体流动分析”的博士论文,较为准确地预测了阶梯试样内充型过程中的流速分布和流动模式[6],为进一步的热场分布计算和浇注系统设计打下理论基础。
我国虽然在该领域研究的起步较晚,但发展很快。
1987年沈阳铸造研究所的王君卿,在研究充型过程数值模拟的过程中,用SIMPLE, SMAC, SOLA-VOF三种方法进行计算,并对几种求解带自由表面的数值计算方法进行了比较。
清华大学的荆涛、柳百成用SOLA-VOF法对充型过程进行了模拟,并研究了充型过程对浇注完成后铸型内初始温度场的影响[8]。
90年代中后期,华中理工大学的袁浩扬、陈立亮等人以SOLA-VOF法为基础,结合他们提出的三维自由表面边界速度确定方法,实现了铸造充型流动过程的三维数值模拟,并在分析了低压铸造充型的传热、传质规律的基础上,提出了一套关于低压连续铸造充填的三维数学模型,并开发了适用于微机的充填过程模拟软件[9]。
安阁英等人将流体湍流流动计算技术和自由表面处理技术应用于液态金属充型过程数值模拟计算,并与层流计算和标准重力浇注试验进行对比,表明湍流与层流计算在在计算域内速度矢量分布上存在明显差别。
考虑湍流作用更接近实际铸造过程,有助于提高大中型重力铸件充型过程数值模拟计算的精度。
2001年,华北工学院徐宏等人采用混和差分格式离散方程,提出一种新的计算方法,三维近似盒迭代法(ABX)。
该方法可以准确而迅速地求解NS方程[10]。
2002年,沈阳工业学院的崔海坡等利用FEM-MAC法,详细地阐述了在模拟过程中如何解决自由表面的问题[11]。
并在模拟应用中,获得了满意的结果。
2.2 凝固过程数值模拟与研究现状在铸造生产过程中,铸件凝固是最重要的过程之一,大部分铸造缺陷产生于这一过程。
因此控制凝固过程,提高铸件质量,获得所要求的组织与性能,已经成为铸造技术的重要内容。
但大、中型铸件凝固过程的温度场难以实测,也不允许通过实验得出铸件的合理工艺方案。
因此,通过模拟计算,可在实际铸造前对铸件的凝固过程进行有效的预测。
铸件凝固过程数值模拟应用有限差分、有限元等方法来对凝固过程的温度场进行计算。
其特点是能定量的计算并描绘出研究对象的动态特征,模拟真实条件的能力强。
该技术是计算机在铸造生产中应用的最核心内容,是国际上公认的用电子计算机等高等高新技术拓宽和促进铸造学科向前发展的前沿领域,涉及铸造理论、凝固理论、传热学、工程力学、数值分析、计算机图形学等多种学科。
凝固过程的数值模拟对优化铸造工艺,预测和控制铸件质量和各种缺陷以及提高生产效率都非常重要。
计算机模拟铸件的凝固过程的意义,在于不仅为铸造工艺设计提供了一种科学依据,而且也是进一步发展铸造工艺CAD/CAM技术的基础之一[12]。
上世纪60年代,丹麦的Forsund第一个使用数字计算机及有限差分法进行铸件凝固过程的传热计算,温度场计算结果与实测结果相当接近[13],为凝固模拟开辟了新的途径。
70年代,美国麻省理工学院的M.C.Flemings教授指出可以用模拟技术来研究及预测大型铸件的缩孔、缩松、热裂及偏析等缺陷[14]。
在此之后,世界上许多国家都相继开展了铸件凝固过程数值模拟及相关的理论与实践研究。
在日本,以大中逸雄、新山英辅为代表,从传热学的基本原理出发进行了大量的工作研究,经过物理数值计算,以不计单元的形状影响建立能量守恒方程的计算方程,采用直接差分格式并兼有有限元部分分析方法对复杂铸件进行数值模拟。
我国从1978年开展铸件凝固数值模拟研究多年来,始终将研究与铸造生产实际密切结合,形成了我国凝固模拟技术研究的特色。
沈阳铸造研究所、大连理工大学、西安交通大学、西北工业大学、哈尔滨工业大学、华北工学院及清华大学等先后开展了凝固模拟的研究,并取得了较大进展。
其中清华大学和哈尔滨工业大学还分别针对大型锻件用大钢锭的逆偏析和Al-Cu合金的成分不均进行了化学成分偏析场的数值模拟研究。
目前国内在铸造数值模拟的研究方面已接近世界先进水平,在数学模型的选择、数值计算方法的改进及实际生产应用等方面都取得了较多的研究成果。
铸件传热是凝固过程中最基本的传输过程,也是最复杂、最具代表性的不稳定传热过程。
在实际生产中铸件的凝固过程,除了热量的传输之外,还同时存在质量传输和动量传输的现象,如合金凝固时晶间成分的再分配以及凝固收缩时产生的流体流动等等。
凝固中热量、质量和动量的传输,不仅直接影响铸件的凝固行为,而且还与许多凝固缺陷的形成密切相关。
因而,要实现铸件凝固行为的准确模拟,并精确预测包括宏观偏析在内的各种凝固缺陷,就必须综合考虑铸件凝固中的传热、传质和动量传输。
文献[15]推荐了一种描述合金铸锭、铸件凝固传热、传质和动量传输现象的统一数学模型。
铸件—铸型界面上的传热是一个非常复杂的过程,在凝固过程中铸件凝固收缩而铸型受热膨胀,就会在铸件—铸型界面上产生气隙,从而引起界面上传热量的变化,对铸件的凝固过程有很大的影响,同时也影响着铸件凝固过程数值模拟的精度,尤其在金属型和导热系数大或有冷铁的砂型铸造中,界面传热随界面气隙的形成而降低的现象非常明显。
曾有许多学者对铸件—铸型界面热交换过程进行了研究。
但是由实验方法得出的热交换参数值仅适用于特定的铸造条件和铸件尺寸,其通用化问题依然没有得到解决[16]。