二零二零年车间用电动小车结构设计word可直接编辑
电动小汽车设计(第四部分)电机驱动方案

驱动电路目前轮式机器人平台多采用前后轮分别控制的方式,普通直流电机驱动后轮提供动力,步进电机驱动前轮调整方向。
这种方式的驱动机构复杂,控制算法也比较复杂,并且转向不够灵活,图7选用左右轮分别控制小车的方案,各用一个普通直流电机控制小车的左右轮,通过左右轮速度的调节即可实现转向,控制非常方便,还可实现原地转动。
驱动电路的选择也是非常重要的,通常选用的驱动电路是由晶体管控制继电器来改变电机的转向和进退。
这种方法适用于大功率电机的驱动,但对于中小功率的电机则极不经济,因为每个继电器要消耗20-100ma的电流。
还可以使用组合三极管/mosfet管的方法,但比较麻烦,电路也比较复杂,笔者采用集成电路的驱动方法,极大增强了电路可靠性和简明性。
选用sgs公司的恒压恒流桥式驱动芯片l293,其内部包含4通道逻辑驱动电路,额定工作电流为1a,最大可达1.5a,vss为集成芯片工作电压,电压最小为4.5v,vs为输出给电机的电压,最大可达36v,vs电压必须比vss电压高。
由l293构成的电机驱动电路如图8所示。
直流电机转速采用spce061a两路pwm控制输出电压,通过编程使占空比以1/16的最小间隔在1/16-14/16间变化,以实现速度的调节。
2在实际制作中,我们选用大功率达林顿管TIP122或场效应管IRF530,效果都还不错,为了使电路简化,建议使用集成有桥式电路的电机专用驱动芯片,如L298、LMD18200,性能比较稳定可靠。
由于电机在正常工作时对电源的干扰很大,如果只用一组电源时会影响单片机的正常工作,所以我们选用双电源供电。
一组5V给单片机和控制电路供电,另外一组9V给电机供电。
在控制部分和电机驱动部分之间用光耦隔开,以免影响控制部分电源的品质,并在达林顿管的基极加三极管驱动,可以给达林顿管提供足够大的基极电流。
图3所示为采用TIP122的驱动电机电路,IOB8口为“0”,IOB9口输入PWM波时,电机正转,通过改变PWM的占空比可以调节电机的速度。
微型四轮电动代步车的设计设计-20页文档资料
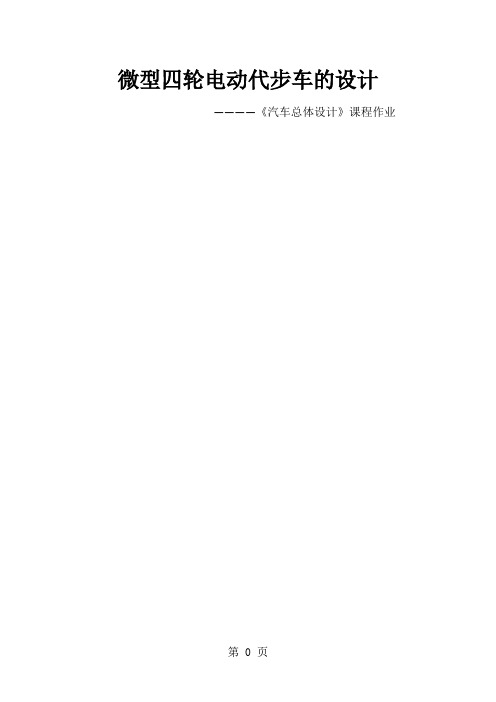
微型四轮电动代步车的设计————《汽车总体设计》课程作业毕业设计(论文)原创性声明和使用授权说明原创性声明本人郑重承诺:所呈交的毕业设计(论文),是我个人在指导教师的指导下进行的研究工作及取得的成果。
尽我所知,除文中特别加以标注和致谢的地方外,不包含其他人或组织已经发表或公布过的研究成果,也不包含我为获得及其它教育机构的学位或学历而使用过的材料。
对本研究提供过帮助和做出过贡献的个人或集体,均已在文中作了明确的说明并表示了谢意。
作者签名:日期:指导教师签名:日期:使用授权说明本人完全了解大学关于收集、保存、使用毕业设计(论文)的规定,即:按照学校要求提交毕业设计(论文)的印刷本和电子版本;学校有权保存毕业设计(论文)的印刷本和电子版,并提供目录检索与阅览服务;学校可以采用影印、缩印、数字化或其它复制手段保存论文;在不以赢利为目的前提下,学校可以公布论文的部分或全部内容。
作者签名:日期:学位论文原创性声明本人郑重声明:所呈交的论文是本人在导师的指导下独立进行研究所取得的研究成果。
除了文中特别加以标注引用的内容外,本论文不包含任何其他个人或集体已经发表或撰写的成果作品。
对本文的研究做出重要贡献的个人和集体,均已在文中以明确方式标明。
本人完全意识到本声明的法律后果由本人承担。
作者签名:日期:年月日学位论文版权使用授权书本学位论文作者完全了解学校有关保留、使用学位论文的规定,同意学校保留并向国家有关部门或机构送交论文的复印件和电子版,允许论文被查阅和借阅。
本人授权大学可以将本学位论文的全部或部分内容编入有关数据库进行检索,可以采用影印、缩印或扫描等复制手段保存和汇编本学位论文。
涉密论文按学校规定处理。
作者签名:日期:年月日导师签名:日期:年月日目录一.产品信息 (2)1.市场背景 (2)2.产品介绍 (3)二.调查问卷 (4)三.问卷分析 (5)四.产品对比 (9)五.层次分析 (11)六.需求转换 (15)七.参数设计 (18)1.设计目标 (18)2.设计原则 (19)3.具体参数 (19)4.总成选择 (21)八.设计总结 (24)一.产品信息1.市场信息现在生活中所见到的电动代步车越来越多,可以说这种电动代步车是应环境污染、人口老龄化、能源危机、交通拥堵等问题而兴起的。
车间用电动小车结构设计

车间用电动小车结构设计介绍车间用电动小车是一种用于在车间内运输物品的装置。
它可以代替人工搬运,提高工作效率,减少劳动强度。
本文将介绍车间用电动小车的结构设计,主要包括车身设计、驱动系统设计和控制系统设计等方面。
车身设计1. 车身材料车身材料应选择轻量、坚固的材料,以提高小车的载重能力和耐用性。
常见的材料包括钢材、铝合金和塑料等。
具体选择应根据实际情况进行权衡。
2. 车身结构车身结构应具备足够的稳定性和刚性,以保证小车在行驶过程中不易发生变形和抖动。
常见的车身结构有四轮结构和三轮结构。
四轮结构具有较好的稳定性,适合承载较大的货物;而三轮结构具有较小的转弯半径,适合在狭小空间内行驶。
驱动系统设计1. 电机选择电机是驱动系统的核心部件,应根据小车的载重要求和行驶速度要求选择合适的电机。
常见的电机有直流电机和交流电机。
直流电机具有调速范围广、响应速度快的特点,适合需要频繁调速的场合;而交流电机具有高效率和平稳运行的特点,适合长时间稳定运行的场合。
2. 传动系统传动系统用于将电机的转动力传递到车轮上,常见的传动系统包括链条传动和齿轮传动。
链条传动结构简单,可调节传动比,但噪音较大;齿轮传动传动效率高,噪音小,但传动比固定。
3. 制动系统制动系统用于控制小车的停止和减速。
常见的制动系统有摩擦制动和电子制动。
摩擦制动通过施加摩擦力来实现制动,适用于小车载重较轻的情况;电子制动通过电磁感应制动器实现制动,适用于小车载重较重或需要频繁制动的情况。
控制系统设计1. 控制方式控制系统应支持多种控制方式,例如手动控制和自动控制。
手动控制通过操纵杆或按钮来实现对小车的控制;自动控制通过预设的路径或目标来实现对小车的自动行驶。
2. 传感器选择传感器用于感知小车周围环境的信息,常见的传感器有红外线传感器、超声波传感器和激光传感器等。
根据实际需求选择合适的传感器,以实现对障碍物的检测、避障和定位等功能。
3. 控制算法控制算法是控制系统的核心部分,应根据实际需求选择合适的控制算法。
电动小汽车方案

电动小汽车设计本次设计的简易智能电动车,采用AT89c51单片机作为小车的检测和控制核心;采用金属感应器TL-Q5MC来检测路上感应到的铁片,从而把反馈到的信号送单片机,使单片机按照预定的工作模式控制小车在各区域按预定的速度行驶,并且单片机选择的工作模式不同。
采用霍尔元件A44E检测小车行驶速度;行驶后,轮流显示小车采用LED数码管实时显示小车行驶的时间以及速度,小车停止时,显示总的行驶时间、行驶距离、平均速度以及各速度区行驶的时间。
本设计结构简单,较容易实现。
1. 设计任务:设计并制作了一个智能电动车,其行驶路线满足所需的要求。
1.1 要求:1.1.1 基本要求:(1)分区控制:如(图1)所示:(图1)车辆从起跑线出发(出发前,车体不得超出起跑线)。
在第一个路程C~D区(3~6米)以低速行驶,通过时间不低于10s;第二个路程D~E区(2米)以高速行驶,通过时间不得多于4秒;第三个路程E~F区(3~6米)以低速行驶,通过时间不低于10s。
(2)小车能自动记录、显示行驶时间、行驶距离以及行驶速度,还能记录每段所走的时间,从而判断是否符合课程设计要求。
(记录显示装置安装在车上)。
2. 方案(主要有以下几模块)根据设计任务要求,并且根据我们自己的需要而附加的功能,该电路的总体框图可分为几个基本的模块,框图如(图3)所示:(图3)2.1 路面检测模块:采用铁片感应器TL-Q5MC来检测路面上的铁片从而给单片机中断脉冲。
原理图接线如(图4)所示:(图4)2.2 显示模块:采用由七段显示译码器7448配合外围电路来控制LED数码管的显示,当然当数码管驱动电压较小时,可以直接用7448进行驱动,而不用外加电源;LED基本驱动电路如下图所示:2.3 测速模块:2.3.1 方案1:采用采用霍尔开关元器件A44E检测轮子上的小磁铁从而给单片机中断脉冲,达到测量速度的作用。
霍尔元件具有体积小,频率响应宽度大,动态特性好,对外围电路要求简单,使用寿命长,价格低廉等特点,电源要求不高,安装也较为方便。
一种电力设备小车机构的制作方法

一种电力设备小车机构的制作方法引言随着科技的不断发展,电力设备自动化的需求也日益增长。
本文介绍了一种电力设备小车机构的制作方法,旨在实现电力设备的自动运输和操作,提高生产效率和安全性。
设计原理1. 小车机构的结构设计电力设备小车机构主要由底盘、驱动系统、导轨、控制系统和电源系统等组成。
在结构设计中,需要考虑小车的承载能力、稳定性和机动性等要素。
•底盘:选择强度高、耐磨损的材料制作底盘,确保整个机构的稳定性和承载能力。
•驱动系统:采用电动驱动系统,可通过电源系统提供的电能驱动小车的运动。
•导轨:为了保证小车运动轨迹的准确性和稳定性,选择高精度的导轨设计。
•控制系统:采用先进的控制系统,通过传感器对小车进行感知,并进行精确的控制与导航。
2. 小车机构的制造工艺制造电力设备小车机构需要经过以下几个步骤:1.设计和模拟:根据实际需求,使用CAD软件设计小车机构的结构,并进行运动学模拟和强度分析,以确保设计的可行性。
2.零部件制造:根据设计图纸,制造底盘、驱动系统、导轨等机构的零部件。
选择合适的机加工工艺和材料,确保零部件的精度和质量。
3.组装:将制造好的零部件按照设计要求进行组装,包括安装电动驱动系统、导轨以及控制系统等。
4.调试与测试:完成组装后,对小车机构进行调试与测试,确保机构能够正常工作,并根据测试结果进行必要的调整和优化。
制作方法详解1. 底盘制作底盘是整个机构的基础,其制作需要注意以下几个关键步骤:1.1 材料选择:选择强度高、耐磨损、具有良好韧性的材料,例如工程塑料或金属材料。
1.2 制作步骤: - 制作底盘的图纸:根据设计要求,使用CAD软件绘制底盘的图纸,并确定尺寸和结构。
- 材料切割:根据底盘图纸,将所选材料按照尺寸要求进行切割。
- 加工:对切割好的材料进行加工,包括钻孔、铣削等工序,以得到所需的底盘零部件。
- 组装:将加工好的底盘零部件按照设计要求进行组装,使用螺栓或焊接等方式进行连接。
图解新能源汽车的结构设计

图解新能源汽车的结构设计新能源汽车正逐渐成为汽车行业的新宠儿,其独特的结构设计更是引人注目。
本文将通过图解的方式,为大家详细解析新能源汽车的结构设计,让我们一起来深入了解吧。
电池系统新能源汽车的核心之一就是电池系统,它是提供动力的重要组成部分。
电池通常安装在车辆底盘上,通过高科技的管理系统控制电能的输出和充电。
图中展示了电池系统内部结构,包括电芯、电池模块和电池包等组件,彼此紧密相连,确保电能的储存和释放效率。
电动驱动系统在传统汽车中,发动机驱动车轮转动,而在新能源汽车中,电动驱动系统扮演着这一角色。
电机通过电控系统接受指令,输出扭矩驱动车轮前进。
这一系统结构简洁、效率高,使新能源汽车在动力性能上有了质的提升。
制动系统新能源汽车的制动系统也有所创新,采用了再生制动技术。
当车辆制动时,部分动能会转化为电能并储存在电池中,实现能量的回收再利用。
这一设计不仅提高了行驶里程,还减少了能源的浪费,符合可持续发展理念。
车身结构为了降低汽车重量、提高安全性能,新能源汽车采用了轻量化的车身结构设计。
采用高强度材料、空心结构等手段,使车身在碰撞时能有效吸收冲击力,保护乘客安全。
图中展示了一款新能源汽车的车身结构示意图,清晰展示了各部分的构造。
智能互联随着科技的发展,智能互联也成为新能源汽车的一大特点。
通过车载互联系统,驾驶者可以实时了解车辆状态、导航信息等,提供更便捷舒适的驾驶体验。
智能互联还实现了车辆远程控制、在线升级等功能,实现了车辆与用户之间的全面互动。
新能源汽车的结构设计融合了先进的科技和工艺,不仅提高了汽车性能,还降低了对环境的影响。
随着技术的不断发展,相信新能源汽车将在未来成为主流,推动汽车行业迈向更加绿色、智能的未来。
希望通过本文的介绍,读者对新能源汽车的结构设计有了更清晰的认识,让我们共同期待新能源汽车的光明未来!。
电动小车设计方案

电动小车设计方案一、引言电动小车是一种环保、高效的交通工具,在城市出行、物流配送、仓库运输等场景中有着广泛的应用。
本文将提出一种电动小车的设计方案,旨在满足各种使用场景下的需求。
二、设计目标本设计方案致力于打造一款功能全面、性能稳定、使用便捷的电动小车。
具体设计目标如下:1.载重能力:小车能够承载一定重量的货物,满足物流配送和仓库运输的需求;2.行驶距离:小车能够满足一定行驶里程,减少充电频率,提高工作效率;3.操控性能:小车能够灵活、稳定地转向和刹车,便于操作和驾驶;4.安全性:小车具备防滑、抗震、防护等功能,确保使用过程中的安全;5.节能环保:小车使用电动驱动,减少对环境的污染;6.维护成本:小车的维护成本低,易于维修和保养。
三、设计方案1. 载重能力为了满足物流配送和仓库运输的需求,小车将采用高强度的钢材作为车架材料,确保足够的承载能力。
另外,小车将设计一定大小的货物仓位,方便装载和卸货。
2. 电池系统为了满足长时间行驶需求,小车将搭载高容量的电池组。
采用锂电池作为电源,能够提供稳定的电力输出,并具备较长的寿命。
而且,电池组将采取可拆卸的设计,方便充电和更换。
3. 操控性能小车将装备灵活的转向系统和可靠的刹车系统。
转向系统采用前轮转向,通过电动方向盘进行操控,转向灵活、灵敏。
刹车系统采用液压刹车系统,具备快速、稳定的刹车响应,提高安全性。
4. 安全性小车将配备防滑胎,增加小车在湿滑路面上的抓地力,降低滑倒和侧翻的风险。
此外,小车还会加装护栏和保护装置,保护驾驶人员和货物的安全。
5. 节能环保小车使用电动驱动,不产生尾气排放,减少对环境的污染。
同时,小车在行驶过程中通过能量回收系统将制动能量转化为电能储存到电池中,提高能量利用效率。
6. 维护成本为了降低维护成本,小车将采用模块化设计,将各个部件进行模块化拆解,方便维修和更换。
另外,小车的维护手册将提供详细的维护保养指导,帮助用户进行日常维护工作。
电动小汽车设计(第三部分)

电动小汽车(跷跷板)一、任务设计并制作一个电动车跷跷板,在跷跷板起始端A一侧装有可移动的配重。
配重的位置可以在从始端开始的200mm~600mm范围内调整,调整步长不大于50mm;配重可拆卸。
电动车从起始端A出发,可以自动在跷跷板上行驶。
二、要求1.基本要求在不加配重的情况下,电动车完成以下运动:(1)电动车从起始端A出发,行驶到中心点C附近;(2)电动车在中心点C附近使跷跷板处于平衡状态,保持平衡数秒(>3s)。
(3)电动车从(2)中的平衡点出发,行驶到跷跷板末端B处(车头距跷跷板末端B不大于50mm)。
(4)电动车在B点停止数秒(3s)后,倒退回起始端A,完成整个行程;(5)在整个行驶过程中,电动车始终在跷跷板上。
三、说明(1)跷跷板长1600mm、宽300mm。
(2)跷跷板中心固定在直径不大于50mm的半圆轴上,轴两端支撑在支架上,并保证与支架圆滑接触,能灵活转动。
(3)电动车(含加在车体上的其它装置)外形尺寸规定为:长≤300mm,宽≤200mm。
(4)平衡的定义为A、B两端与地面的距离差d=∣dA-dB∣不大于40mm。
(5)测试过程中不允许人为控制电动车运动。
四、题目分析4.1 控制器模块方案一:采用ATMEL 公司的AT89C51。
51单片机价格便宜,应用广泛,但是功能单一,如果系统需要增加语音播报功能,还需外接语音芯片,实现较为复杂;另外51 单片机需要仿真器来实现软硬件调试,较为烦琐。
方案二:采用凌阳公司的SPCE061A 单片机作为控制器的方案。
该单片机I/O资源丰富,并集成了语音功能。
芯片内置JTAG电路,可在线仿真调试,大大简化了系统开发调试的复杂度。
根据本题的要求,我们选择第二种方案。
4.2 电机模块电机模块选择是整个方案设计的关键,按照设计要求,小车需在C点和有配重的情况下分别达到平衡状态,这需要对小车的精确控制,而且小车制动性能要好。
因此普通直流电机不能满足要求。
二零二零年158万吨宽厚板车间设计word可直接编辑

新建158万吨宽厚板车间设计摘要:中厚板轧机是轧钢行业中的主力轧机,其装备水平及拥有量是一个国家钢铁工业发展水平的重要标志。
因此,中厚钢板是国民经济发展不可缺少的钢材品种,各国对中厚板生产都很重视。
本设计书阐述了新建一个6~150×1200~3500×~32000mm的宽厚板车间设计的基本过程。
主要内容包括:制定产品大纲、生产工艺流程、产品技术指标;确定轧机主要参数和工艺制度;力能参数计算、主要辅助设备生产能力的计算;车间布置和主要经济技术指标以及环境保护,并对电机进行能力验算和校核。
设计主要产品及其产量:碳素板48万吨,船用板20万吨,桥梁板20万吨,建筑板20万吨,容器板30万吨,锅炉板20万吨。
其代表规格为:Q235_8×3000×27450mm的碳素板。
生产所用的板坯为200mm、240mm和300mm厚的连铸坯。
本设计共计算了5种厚度的产品的压下规程,分别为:8mm的碳素板、12mm 的建筑板、20mm的船用板、50mm的容器板和70mm的桥梁板。
关键词:宽厚板压下规程车间设计The New design of a wide -thick plate workshopw ith annual capacity of 1.35 million tonAbstract:Plate mill is the main rolling mill industry, and ownership of its equipment level is the level of a country's iron and steel industry an important symbol. Therefore, the thick steel plate is essential for national economic development, steel varieties, countries attach great importance to plate production.This paper mainly introduces the basic process of a wide heavy plate workshop with annual capacity of 1.58million ton. The deviation of product,the process,the main parameter of the mill, the calculations of parameter and the selection of main aided equipment. The layout figure of the workshop and main technology and economy index are showed in this paper.Main products and their output: Carbon is unnatural 0.48million ton, the boat uses 0.200million ton of board , bridge board builds 0.20million ton of board , 0.20 million ton of container board , 0.30 million ton of boiler plate 0.20million ton. The person represents specification By : Q235_8×3000×27400mm carbon board. The thickness producing the what be used slab is 200 mm , 240 mms and 300 mm are including the casting blank . Design that directive rules , difference having calculated 5 kinds thickness products pressing down on together are originally: 8 mm carbon board , 12 mm building board, 20mm boats use board , 50 mm container board and 70 mm bridges board.Key words: Wide-thick plate Rolling schedule The design ofWorkshop概述61 产品大纲与金属平衡91.1 产品大纲91.2 金属平衡102 设计方案112.1轧机型式112.1.1二辊可逆式轧机112.12三辊劳特式轧机112.1.3四辊可逆式轧机122.1.4万能式轧机122.2轧机布置132.3主要辅助设备型式132.3.1加热炉132.3.2矫直机142.3.3冷床152.3.4剪切机162.3.5热处理设备162.4车间自动化装置162.4.1四辊轧机电动(APC)和液压(AGC)172.4.2在线检测设施172.4.3计算机控制182.5工艺布置方案183生产工艺流程及工艺制度223.1工艺流程图223.2工艺流程简述223.3工艺制度243.3.1板坯准备制度243.3.2加热制度263.3.3轧制制度273.3.4精整制度274 车间工作制度及年工作小时294.1 工作制度 294.2 年工作时间295.轧机主要参数的确定和生产能力计算 315.1 轧机允许轧制压力的确定315.2 轧辊主要参数的确定315.2.1轧辊材质及轧辊轴承的确定315.2.2工作辊辊身长度的确定 315.2.3工作辊直径的确定315.2.4支撑辊直径的确定325.2.5支撑辊辊身长度的确定 325.2.6工作辊辊颈尺寸的确定 325.2.7支撑辊辊颈尺寸的确定 335.3 轧机允许轧制力矩的确定335.4 轧制速度和主电机主要参数的确定345.4.1轧制速度的确定345.4.2主电机型式的选择345.4.3主电机额定转速nH的确定345.4.4主电机额定功率PH的确定345.5压下规程设计365.5.1制定轧制制度的原则和要求365.5.2制定压下规程的方法和步骤365.5.3 压下规程375.6 轧机强度校核445.7电机校核465.7.1电机传动轧辊所需力矩的计算465.7.2轧制力矩475.7.3摩擦力矩475.7.4空转力矩485.7.5动力矩485.7.6电机发热校核485.7.7电机过载校核496轧机及辅助设备生产能力的计算526.1轧机生产能力计算526.2加热炉主要参数确定及生产能力计算526.2.1加热炉宽度的确定526.2.2加热炉长度的确定536.2.3加热炉生产能力计算546.2.4轧机负荷率556.3矫直机主要技术参数及生产能力计算566.3.1矫直机主要技术参数确定566.3.2矫直机生产能力及负荷率计算576.4冷床主要参数及生产能力计算586.4.1冷床宽度的确定586.4.2 冷床长度的确定586.4.3冷床生产能力计算596.5剪切机主要参数确定及生产能力计算606.5.1剪切机主要参数确定606.5.2火焰切割机主要参数确定626.5.3剪切机生产负荷率计算 626.6 热处理炉主要参数确定及生产能力计算636.6.1 热处理炉主要参数的确定636.6.2热处理炉生产能力的计算647车间平面布置与起重运输647.1原料库面积计算647.2中间仓库面积计算657.2.1成品库面积计算657.2.2车间组成及厂房面积657.3起重运输667.4吊车 667.5辊道 678. 主要经济技术指标67致谢69参考文献70附录A 压下规程程序71附录B 翻译:Mo对Nb-Mo合金钢动态再结晶的影响81概述中厚板主要用于船舰、桥梁、锅炉、容器、石油化工、工程机械及国防建设等方面,其品种繁多,使用温度区域较广(200~600℃),使用环境复杂(耐侯性、耐蚀性等),使用要求高(强韧性、焊接性等)。
2-电动汽车的结构与设计

二、电动汽车的典型工况与性能指标
根据电动汽车的不同用途,设计时电动汽车能克服的最大 坡度一般选18%~27%比较合获适(有特殊要求的除外)。 纯电动轿车由于受到电动机功率和动力电池的质量与尺寸 的限制,要达到同类汽油机轿车的加速性,目前还比较困难 。设计时,除预先根据特殊要求外,电动汽车的加速能力与 其最大爬坡能力相当即可。
四、电动汽车的行驶性能
1、电动汽车的驱动力与行驶阻力 (2)电动机的转矩特性
串激式直流电动机的功率与转矩特性
四、电动汽车的行驶性能
1、电动汽车的驱动力与行驶阻力 (2)电动机的转矩特性
串激式交流电动机的功率与转矩特性
四、电动汽车的行驶性能
1、电动汽车的驱动力与行驶阻力 (2)电动机的转矩特性
重庆电机厂50KW 交流感应电动机转矩特性
16980 15610
110.00 113.03
165.2 168.0
注:①表中数据为电池百公里能耗
0.665 0.672
0.039 0.043
四、电动汽车的行驶性能
5、电动汽车的续驶里程
电动汽车行驶所需功率与速度关系图
电动汽车行驶所需要能量与车速关系图
四、电动汽车的行驶性能
5、电动汽车的续驶里程
G型厢式电动汽车等速行驶的能耗与车速关系
四、电动汽车的行驶性能
车型 Impact G型厢式电动汽车 U.S电动轿车 大发HJ-IET
IZA 华利微型电动汽车 清华号电动汽车
三、传动装置
两档变速器和差速器一体化设计
两档行星齿轮变速传动简图
四、电动汽车的行驶性能
1、电动汽车的驱动力与行驶阻力 (1)驱动力
M t Migi0
Ft
车间用电动小车结构设计
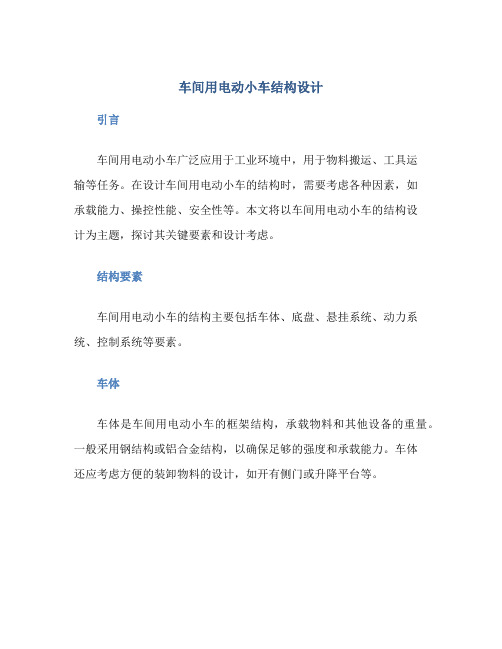
车间用电动小车结构设计引言车间用电动小车广泛应用于工业环境中,用于物料搬运、工具运输等任务。
在设计车间用电动小车的结构时,需要考虑各种因素,如承载能力、操控性能、安全性等。
本文将以车间用电动小车的结构设计为主题,探讨其关键要素和设计考虑。
结构要素车间用电动小车的结构主要包括车体、底盘、悬挂系统、动力系统、控制系统等要素。
车体车体是车间用电动小车的框架结构,承载物料和其他设备的重量。
一般采用钢结构或铝合金结构,以确保足够的强度和承载能力。
车体还应考虑方便的装卸物料的设计,如开有侧门或升降平台等。
底盘底盘是车间用电动小车的基础部分,承载车体和其他系统。
底盘的材料选择也需考虑强度和重量,常见的材料有钢、铝合金等。
底盘通常设计为平整的,以便于安装其他组件和设备。
悬挂系统悬挂系统是连接底盘和车轮的关键部分,对车辆的平稳性和操控性有重要影响。
悬挂系统通常采用弹簧和减震器来减缓车辆在不平路面上的颠簸和震动,提供更加舒适和稳定的行驶。
动力系统动力系统是车间用电动小车的核心,提供驱动力。
常见的动力系统包括电池、电机和传动系统。
电池作为能量源,供给电机提供动力。
电机通过传动系统传递动力给车轮,使车辆前进或后退。
控制系统控制系统是车间用电动小车的大脑,负责操控车辆的运动和任务。
控制系统通常由中央控制器、传感器和执行器组成。
中央控制器接收和处理来自传感器的信息,根据预设的程序控制执行器,实现车辆的自动化、智能化控制。
设计考虑在设计车间用电动小车结构时,需要综合考虑多个因素,下面列举几个设计考虑的要点。
承载能力车间用电动小车通常用于物料搬运,因此承载能力是一个重要的设计指标。
根据实际需求确定车辆的承载能力,确保其能够满足工作任务的需求。
操控性能良好的操控性能是车间用电动小车的核心需求之一。
设计时应注意车辆的转弯半径、加速度、制动效果等,使车辆能够在狭小的空间内灵活操作,并具备良好的行驶稳定性。
安全性安全性是车间用电动小车设计的重要考虑因素。
小车结构设计报告

无碳小车结构设计报告1、设计概述结构设计首先要求工作原理明确,能够达到预期的功能。
此次需要设计的无碳小车其主要功能是绕过前行道路上的障碍物,障碍物为等间距共线排列,因此转化成机械方面的原理即要求小车有周期往复运动装置;并且小车的能量来源为重物重力势能,因此需要有传动装置是重力势能传递到往复运动动装置。
无碳小车结构设计其次要求小车系统能够稳定运行,既有良好的机械性能,根据题目要求小车应在两米宽的轨道上行走,小车上装有的负载不能在小车前行过程中掉落,这要求使小车能够平稳前进,小车应不致翻到或冲出轨道。
结构设计再则要有良好的结构工艺性,以便高效、合格、经济地加工出所需要的产品。
既然是无碳小车,则要使小车成本低却性能好效率高。
当然一个好的结构设计还应具有良好的外观造型,产品在满足功能要求的前提下,具有良好的结构工艺性和漂亮的外观造型,是设计所追求的目标。
2、主要零件分析后轮由于后轮为驱动轮,稳定性要好,通过使其轮缘加厚,中间质量分布较少,转动惯量增大,达到蓄能的效果。
后轮轴重物下落时的绕线轮及皮带轮中较小的一个可以设计在轴上,轴上还应有与轴承配合的地方。
中轮轴为了方便小车在重物下降完毕之后重新启动,引入皮带轮,使手摇杆能独立于驱动轮的运动控制重物的上升。
蜗杆为使小车能绕开障碍物,其前进速度和转向角速度必须满足要求,也就是说,驱动系统和转向系统之间的传动比要适当,此处我们选用蜗杆传动齿轮轴齿轮轴需要带动曲柄滑块机构的曲柄转动,为减少中间传动环节,可将曲柄与齿轮轴作为一体。
连杆由于在曲柄滑块机构运转过程中,连杆上下运动会消耗重力势能,因此连杆质量应尽可能小,在设计中应去掉多余的材料。
前轮前轮作为转向轮,其与地面的接触面积越小越好,我们可将前轮外缘设计为圆弧状(橡胶套),与地面的接触为线接触,可使前轮转向对小车轨道偏移造成的误差降到最低。
当然还有其它零件,设计比较简单,这里不再赘述,但是所有零件的设计都应该能满足要求并以工艺合理与经济为前提。
制作简单电动小车的方法

制作简单电动小车的方法嘿,朋友们!想不想自己动手做一辆超酷的简单电动小车呀?这可不难哦!首先呢,咱得准备好材料。
就像盖房子得有砖头水泥一样,做电动小车也得有它的“砖头”和“水泥”呀。
你得有几个小轮子,这可是小车能跑起来的关键。
然后呢,找个小小的电动机,这就是小车的“心脏”啦。
再准备些电线呀、电池呀之类的,这些东西就像是小车的“血管”和“能量源”。
接下来,就开始组装啦!把轮子安装在合适的位置,让它们能顺畅地转动起来,就好像给小车穿上了合适的鞋子。
然后把电动机固定好,让它能稳稳地给小车提供动力。
用电线把电动机和电池连接起来,这一步可不能马虎,就跟给心脏接上血管一样重要呢。
等都连接好了,嘿,这小车就有点模样啦!你看,它就像个小生命一样,等待着你去启动它。
这时候,把电池装上,打开开关,哇塞!小车就“嗖”地跑起来啦,是不是特别有成就感?你想想啊,这可是你亲手做出来的小车,它就像你的小伙伴一样。
你可以带着它在房间里跑来跑去,也可以和小伙伴们来一场小车比赛。
哎呀呀,那得多有意思呀!做这个简单电动小车,就好像搭积木一样,一块一块地把它拼凑起来。
而且在这个过程中,你还能学到好多知识呢,什么电路呀,力学呀,多棒呀!这可比光看书有意思多啦。
别觉得这很难哦,只要你有耐心,一步一步来,肯定能做出属于你的超级酷的电动小车。
就像那句话说的,“世上无难事,只怕有心人”。
你就是那个有心人呀,一定能行的!所以呀,别再犹豫啦,赶紧动手试试吧!让你的创造力和动手能力都爆发出来,做出一辆独一无二的电动小车,然后骄傲地向大家展示吧!你会发现,原来自己这么厉害呢!。
车间用电动小车结构设计
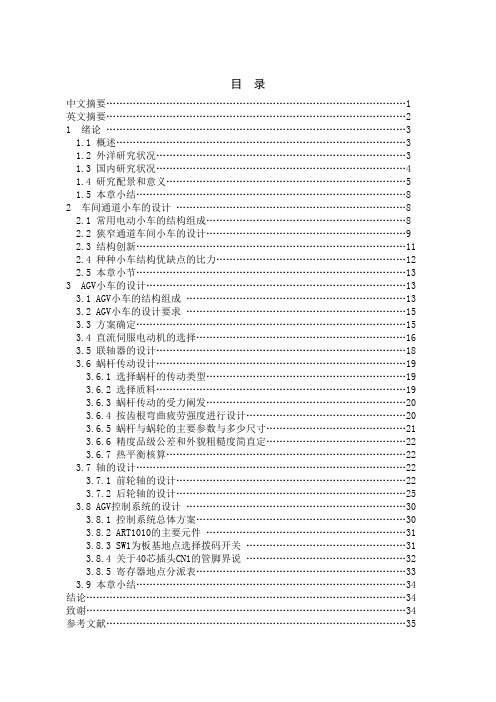
目录中文摘要 (1)英文摘要 (2)1 绪论 (3)1.1 概述 (3)1.2 外洋研究状况 (3)1.3 国内研究状况 (4)1.4 研究配景和意义 (5)1.5 本章小结 (8)2 车间通道小车的设计 (8)2.1 常用电动小车的结构组成 (8)2.2 狭窄通道车间小车的设计 (9)2.3 结构创新 (11)2.4 种种小车结构优缺点的比力 (12)2.5 本章小节 (13)3 AGV小车的设计 (13)3.1 AGV小车的结构组成 (13)3.2 AGV小车的设计要求 (15)3.3 方案确定 (15)3.4 直流伺服电动机的选择 (16)3.5 联轴器的设计 (18)3.6 蜗杆传动设计 (19)3.6.1 选择蜗杆的传动类型 (19)3.6.2 选择质料 (19)3.6.3 蜗杆传动的受力阐发 (20)3.6.4 按齿根弯曲疲劳强度进行设计 (20)3.6.5 蜗杆与蜗轮的主要参数与多少尺寸 (21)3.6.6 精度品级公差和外貌粗糙度简直定 (22)3.6.7 热平衡核算 (22)3.7 轴的设计 (22)3.7.1 前轮轴的设计 (22)3.7.2 后轮轴的设计 (25)3.8 AGV控制系统的设计 (30)3.8.1 控制系统总体方案 (30)3.8.2 ART1010的主要元件 (31)3.8.3 SW1为板基地点选择拨码开关 (31)3.8.4 关于40芯插头CN1的管脚界说 (32)3.8.5 寄存器地点分派表 (33)3.9 本章小结 (34)结论 (34)致谢 (34)参考文献 (35)车间用电动小车结构设计摘要:目前,车间通道两侧的呆板妨碍检测与排除、生产线上的物料调换;各车间之间的物料运送主要是靠人工完成,不但事情效率低下,并且工人的宁静得不到保障,倒霉于车间的流程化生产。
针对这种情况,本课题的主要任务是设计出能够满足车间要求的车间电动小车,参考市面上已有的电动小车设计出能够在狭窄的车间通道灵活行走的电动小车,凭据人机工程学的原理对已有的小车进行结构创新,使工人能长时间地在车上对车间通道两侧的呆板进行操纵。
- 1、下载文档前请自行甄别文档内容的完整性,平台不提供额外的编辑、内容补充、找答案等附加服务。
- 2、"仅部分预览"的文档,不可在线预览部分如存在完整性等问题,可反馈申请退款(可完整预览的文档不适用该条件!)。
- 3、如文档侵犯您的权益,请联系客服反馈,我们会尽快为您处理(人工客服工作时间:9:00-18:30)。
目录中文摘要 (1)英文摘要 (2)1 绪论 (3)1.1 概述 (3)1.2 国外研究状况 (3)1.3 国内研究状况 (4)1.4 研究背景和意义 (5)1.5 本章小结 (8)2 车间通道小车的设计 (8)2.1 常用电动小车的结构组成 (8)2.2 狭窄通道车间小车的设计 (9)2.3 结构创新 (11)2.4 各种小车结构优缺点的比较 (12)2.5 本章小节 (13)3 AGV小车的设计 (13)3.1 AGV小车的结构组成 (13)3.2 AGV小车的设计要求 (15)3.3 方案确定 (15)3.4 直流伺服电动机的选择 (16)3.5 联轴器的设计 (18)3.6 蜗杆传动设计 (19)3.6.1 选择蜗杆的传动类型 (19)3.6.2 选择材料 (19)3.6.3 蜗杆传动的受力分析 (20)3.6.4 按齿根弯曲疲劳强度进行设计 (20)3.6.5 蜗杆与蜗轮的主要参数与几何尺寸 (21)3.6.6 精度等级公差和表面粗糙度的确定 (22)3.6.7 热平衡核算 (22)3.7 轴的设计 (22)3.7.1 前轮轴的设计 (22)3.7.2 后轮轴的设计 (25)3.8 AGV控制系统的设计 (30)3.8.1 控制系统总体方案 (30)3.8.2 ART1010的主要元件 (31)3.8.3 SW1为板基地址选择拨码开关 (31)3.8.4 关于40芯插头CN1的管脚定义 (32)3.8.5 寄存器地址分配表 (33)3.9 本章小结 (34)结论 (34)致谢 (34)参考文献 (35)车间用电动小车结构设计摘要:目前,车间通道两侧的机器故障检测与排除、生产线上的物料更换;各车间之间的物料运送主要是靠人工完成,不仅工作效率低下,而且工人的安全得不到保障,不利于车间的流程化生产。
针对这种情况,本课题的主要任务是设计出能够满足车间要求的车间电动小车,参考市面上已有的电动小车设计出能够在狭窄的车间通道灵活行走的电动小车,根据人机工程学的原理对已有的小车进行结构创新,使工人能长时间地在车上对车间通道两侧的机器进行操作。
除了通道小车,还完成了AGV小车的结构设计,该小车主要承担的是车间之间物料的运送,使生产线之间的衔接更为融洽。
最终完成的工作是对设计的小车进行了Solidworks的三维建模,完成了小车的CAD装配体图,零件图。
车间通道小车的运用可以减轻工人的劳动强度,提高车间的工作效率。
AGV小车的运用不仅减少了工人劳动量,并且由于AGV的运送具有数字化的特征,利于车间的数据统计,减少库存,提高车间的流动资金,提升企业的竞争力。
关键词:车间小车,AGV,控制器,行走方案,人机工程学Abstract:Nowadays,many works such as: testing and removing machine stoppage on both sides of aisle, replacing materials on the production line andtransportation of supplies among all workshops are finished mostly bymanual work, which have low efficiency. What’s more, this kind of workingmethod brings threat to workers’safety, which will go against streamlineproduction.In allusion to this instance, the task of this paper is to design an electricvehicle which can satisfy the need of the factory. The new electric vehicleshould be flexible enough to run in the narrow aisle refer to the electricmodels sold in the market. According to the Man-Machine Engineering,some structure innovation should be operated to the existing electric vehiclesin order to provide longer time for the workers to operate machines on bothsides of aisle on the vehicle. Besides the designing of electric vehicle, thepaper has made structure design of AGV which is responsible fortransformation of supplies among all workshops and makes moreconvenience of production line joint. At last, the paper has finishedSolidworks 3-D modal, CAD Assembly Drawing Views and detail drawingof the electric vehicle.The electric vehicle used in the narrow aisle can lighten workers’workingstrength and improve working efficiency. The use of AGV can reduceworking tasks and it helps do data statistics, reduce inventories, improvecirculating capital and improve enterprise competition power for its digitalfeatures.Keywords:workshop car,the AGV,controller,walking program,man-machine engineering.1 绪论1.1 概述本文介绍了车间电动小车在国内外的发展现状和应用情况,在此基础上,结合毕业设计的课题要求,设计了不同类型的车间小车以满足车间不同的需求。
其研究内容主要包括以下几个方面:1.针对功能一,在市场上已有的电动小车、电动轮椅、segway电动小车的基础上进行改进,使得最终设计出来的电动小车能够在狭窄的车间通道灵活行走,工人能够在小车上对生产线上的设备进行进行监测,及时地发现故障并且排除故障,能够在小车上完成上下料工作。
同时设计改进的小车应当符合人机工程学的原理,这样使得人能够长时间的在小车上连续工作。
2.针对功能二,设计了一款简易的AGV小车,该小车能够在没有人操作的情况下自动完成导向行驶,能够在指定的位置自动停止并完成物料的移交,能够自动到指定的位置完成电池的充电。
简要介绍了AGV车体机械结构的设计,并根据小车的驱动方式和工作要求,对底盘、电机、蓄电池等进行了设计和选型。
根据AGV系统的控制和工艺要求,确定了控制系统的总体框架结构。
对AGV小车的重要零部件进行了设计计算。
3.在总结全文的基础上,对车间电动小车的设计和研究提出了展望。
1.2 国外研究状况世界上第一台AGV是美国Basrrett电子公司于20世纪50年代开发成功的,它是一种牵引式小车系统。
小车中有一个真空管组成的控制器,小车跟随一条钢丝索导引的路径行驶。
60年代和70年代初,除Basrrett公司以外,Webb和Clark公司在AGV市场中也占有相当的份额。
在这个时期,欧洲的AGV技术发展较快,这是由于欧洲公司已经对托盘的尺寸与结构进行了标准化,统一尺寸的托盆促进了AGV的发展。
欧洲的主要制造厂家有Schindler-Digitron, Wogner HJC, ACS, BT. CFC, FATA, Saxby, Denford和Blecbert等。
70年代中,欧洲约装备了520个AGV系统,共有4800台小车,1985年发展到一万台左右,为美、欧、日之首。
在机械制造行业的应用为:汽车工业(57%),柔性制造系统FMS(8%)和柔性装配系统FAS(4%)。
欧洲的AGV技术于80年代初,通过在美国的欧洲公司以许可证与合资经营的方式转移到美国。
芝加哥的Keebler分发中心从欧洲引进直接由计算机控制的AGV} 1981年John公司将AGV连接到AS/RS,以提供在制造过程中物料自动输送和跟踪。
1984年,通用汽车公司便成为AGV的最大用户,1986年已达1407台(包括牵引式小车、叉式小车和单元装载小车),1987年又新增加1662台。
美国各公司在欧洲技术的基础上将AGV发展到更为先进的水平。
他们采用更先进的计算机控制系统(可联网于FMS或CIMS),运输量更大,移载时问更短,具有在线充电功能,以便24小时运行,小车和控制器可靠性更高。
此时美国的AGV生产厂商从23家(1983年)骤增至74家(1985年)。
日本的第一家AGV工厂于1966年由一家运输设备供应厂与美国的Webb公司合资开设。
到1988年,日本AGV制造厂已达20多家,如大福、Fanuc公司、Murata(村田)公司等。
到1986年,日本己累计安装了2312个AGV系统,拥有5032台AGV。
1.3 国内研究状况国内自主研发方面:六十年代开始研究。
1976年,北京起重运输机械研究所研制的ZDB-1型自动搬运车是最早的实用型AGV。
1988年,原邮电部北京邮政科学技术研究所等单位研制了邮政枢纽AGV。
1991年,中科院沈阳自动化所与新松机器人自动化股份有限公司为沈阳金杯汽车公司总装线上设计的九台自动装配系统,并于1996年获得国家科学技术进步三等奖,是当时国内较先进的使用型AGV。
1992年,天津理工学院研制了核电站用光学导引AGV。
1998年昆明船舶设备公司在红河卷烟厂研究多模式激光导引无人自动车22辆,红河项目于2002年获国家科学技术进步二等奖。
同期天津师范大学、吉林大学、吉大易飞、北京军区后勤部、北京机科发展公司、北京易亨集团等也进行了试验研究。
在引进国外技术与产品方面:1980年,上海石化总厂为涤纶长丝作业从日本大福公司引进国内第一套AGVS。