提高连铸坯内部质量的方法
(三)保护浇注连铸坯质量新技术

• (3)初生坯壳的均匀性:结晶器弯月面初生坯壳 不均匀会导致铸坯产生纵裂和凹陷,以致造成
从工艺操作上,应采取以下措施: (1)无渣出钢:转炉采用挡渣球,电炉采用偏心炉
底出钢,防止出钢渣大量下到钢包。 (2)钢包精炼:根据钢种选择合适的精炼方法,以
均匀温度、微调成分、降低氧含量、去除气体夹杂 物等。
(3)无氧化浇注:钢水经钢包处理后,钢中总氧含 量可由130ppm下降到20ppm以下。如钢包→中间包 注流不保护或保护不良,则中间包钢水中总氧量又 上升到60~100ppm范围,恢复到炉外精炼前的水平, 使炉外精炼的效果前功尽弃。
➢连铸机的高生产率( 作业率、拉 速、设备可靠)
➢连铸坯的质量( 铸坯洁净度、铸 坯表面缺陷、铸坯内部缺陷)
一、 提高连铸机生产率
1.1 提高连铸机作业率 目前在钢铁工业发达国家, 现代化大型板坯连铸 机的作业率已达90%以上, 方坯连铸机的作业率 也在90%以上, 有的甚至达到了95%。
提高连铸机作业率的措施:
( 1 ) 提高连浇炉数。国外钢厂板坯连浇炉数在 1500炉以上, 方坯在1000 炉以上。
( 2 ) 提高结晶器的使用寿命。在日本结晶器寿命 由200~300 炉提高到1 000~3 000 炉。
( 3 ) 结晶器下部钢板采用多层电镀、先镀Ni 再镀 磷化物和Cr, 并改变镀层范围和厚度。
( 4 ) 改变结晶器冷却槽的形状和间隔, 铜板表面弯 月面附近温度可降到100 ℃左右, 寿命大大提高。
连铸坯夹杂物产生原因分析及改进

连铸坯夹杂物产生原因分析及改进一、引言连铸是现代钢铁生产中常用的一种工艺。
它可以提高生产效率、降低能耗、改善工作环境、减少劳动强度,因此被广泛应用。
在连铸过程中,一些夹杂物的产生会导致产品质量下降、生产效率降低,并严重影响设备寿命。
如何减少夹杂物的产生,提高产品质量,成为生产中亟需解决的问题。
二、夹杂物产生原因分析1.原料质量不稳定连铸坯的原料主要是钢水,而钢水的质量直接影响夹杂物的产生。
如果原料中含有较多的杂质、氧化物等,就会增加夹杂物的产生几率。
而且,原料的成分不稳定也是引起夹杂物产生的一个因素,一旦成分变化,就容易导致夹杂物出现。
2.连铸设备使用不当连铸设备的使用不当也是夹杂物产生的重要原因。
操作不规范、设备维护不到位、温度控制不稳定等都会导致夹杂物的产生。
当温度过高或过低时,容易使得钢水和坯料中的气体凝固,形成夹杂物。
3.连铸工艺参数不合理连铸过程中,工艺参数的设置直接影响了夹杂物的产生。
如果连铸速度过快或者过慢,结晶器冷却不均匀等,都会导致夹杂物产生。
结晶器振动频率、结晶器倾斜角度、结晶器冷却水温度等参数的选择也会影响夹杂物的产生。
4.人为因素在连铸过程中,人为操作失误也是夹杂物产生的一个主要原因。
操作工不熟练、设备检查不到位等都可能导致夹杂物的产生。
而且,人为因素不可控因素多,所以造成夹杂物的产生很容易。
三、改进措施1.原料质量监控首先要保证原料的质量稳定,及时清洁处理原料,确保原料的成分合理、纯净。
加强对原料的把控,对于原料中可能含有的杂质要及时剔除,确保连铸坯的质量。
2.加强设备维护连铸设备是关键的生产装备,要加强对设备的维护。
定期检查、保养设备,确保设备各项功能正常,减少因为设备问题导致的夹杂物的产生。
3.优化连铸工艺对于工艺参数的设置要进行优化,选择合适的连铸速度、结晶器振动频率、结晶器倾斜角度、结晶器冷却水温度等参数,保证连铸坯的质量。
要对工艺参数进行严格的控制,确保温度、速度等参数的稳定。
连铸坯的缺陷及控制

二冷段和末端区的电磁搅拌可有效抑制枝晶搭桥形成封闭 的液窝。
连铸主要工艺参数
① 拉坯速度及其控制 ② 铸坯的冷却(结晶器冷却、二次冷却)
连铸坯的内部凝固是在出结晶器后进行的,后继的二次水冷、 弯曲矫直等直接影响内部质量。
连铸坯的缺陷及控制
提高连铸坯内部质量的工艺措施:
① 控制二冷段的传热,使铸坯均匀凝固,提高等轴晶率; 偏析、缩孔、缩松
② 降低浇钢的过热度; ③ 使用性能好的保护渣,防止钢水二次氧化和污染; ④ 控制拉速,保证连铸机正常运行; ⑤ 电磁搅拌(二冷段和末端区)。 偏析、缩孔、缩松
连铸坯的缺陷及控制
提高连铸坯表面质量的工艺措施:
① 控制结晶器的传热,使初凝固壳均匀; 裂纹、凹陷
② 控制结晶器的振动;
振痕、横裂纹
③ 使用性能好的保护渣;
气孔、夹杂
④ 优化结晶器结构;
倒锥角度,弧形壁
⑤ 电磁搅拌;
气孔、夹杂
⑥ 软接触电磁连铸。
振痕、裂纹
电磁搅拌的部位:
结晶器电磁搅拌:
(1)借助旋转电磁场使连铸 机结晶器内的金属液产生平 面旋转,去除杂质、气体。
结晶器电磁搅拌:
(2)扩大等轴晶区改善宏观 偏析,减少粗大柱状晶区 。
软接触电磁连铸:
软接触电磁连铸:
(1)减轻结晶器振动对弯月 面的影响,液态渣膜连续均 匀。
软接触电磁连铸:
(2)减小初凝壳对结晶器的 连铸坯的内部缺陷
裂纹 气孔 夹杂 缩孔、缩松 成分偏析
连铸坯的缺陷及控制
连铸坯的缺陷及控制
1. 连铸坯的表面缺陷
裂纹 气孔 夹杂 振痕、凹陷 成分偏析
连铸坯的缺陷及控制
1. 连铸坯的表面缺陷
连铸坯质量的控制

连铸坯的质量控制系统专业:班级:姓名:XXX目录1连铸坯纯净度与产品质量 (1)1.1纯净度与质量的关系 (1)1。
2提高纯净度的措施 (2)2连铸坯质量............................................................ 错误!未定义书签。
2.1 连铸坯的几何形状质量 (3)2。
1.1 铸坯形状缺陷类型 (4)2。
1。
2 铸坯形状缺陷产生原因及防止措施 (4)2.1.3 铸坯鼓肚 (4)2.1.4 铸坯菱变 (4)2。
1。
5 铸坯变成梯形坯 (5)2.2 连铸坯表面质量 (5)2。
2。
1 连铸坯表面振痕 (5)2。
2。
2 振痕形成机理 (5)2。
2.3 振痕对铸坯质量的影响 (6)2。
2。
4 影响振痕深度的因素 (6)2.2.5 减少振痕深度的措施 (7)2。
2.6 铸坯表面裂纹 (7)2。
2。
7 表面纵裂纹 (8)2。
2.8 铸坯角部纵裂纹 (11)2。
2。
9 表面横裂纹 (12)2。
2.10 角部横裂纹 (14)2.2。
11 铸坯表面星状和网状裂纹 (15)2。
2.12 铸坯表面夹渣(杂) (16)2.2。
13 铸坯气孔和气泡 (17)2。
2.14 铸坯表面凹陷 (17)2。
2.15 铸坯表面增碳和偏析 (18)2。
2.16 重皮和重结及结疤 (19)2.3 连铸坯内部质量 (19)2。
3。
1 铸坯内部裂纹 (19)2。
3.2 皮下裂纹 (20)2.3.3 中间裂纹 (20)2.3.4 矫直裂纹 (21)2。
3。
5 压下裂纹 (22)2.3。
6 断面裂纹-——-中心线裂纹 (22)2。
3。
7三角区裂纹 (24)2。
3.8角部附近的裂纹 (25)2.3。
9白点及发纹 (25)2。
3。
10铸坯中心偏析、疏松和缩孔 (25)2.3。
11铸坯内部夹渣(杂) (26)3连铸坯星状缺陷 (27)3.1 鼓肚变形 (27)3。
2 菱形变形 (28)3.3 圆铸坯变形 (28)致谢 (29)摘要连铸坯质量决定着最终产品的质量。
连铸坯质量控制
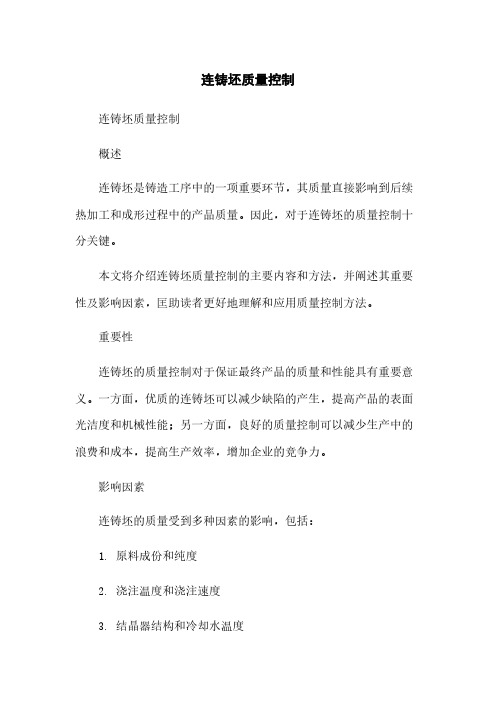
连铸坯质量控制连铸坯质量控制概述连铸坯是铸造工序中的一项重要环节,其质量直接影响到后续热加工和成形过程中的产品质量。
因此,对于连铸坯的质量控制十分关键。
本文将介绍连铸坯质量控制的主要内容和方法,并阐述其重要性及影响因素,匡助读者更好地理解和应用质量控制方法。
重要性连铸坯的质量控制对于保证最终产品的质量和性能具有重要意义。
一方面,优质的连铸坯可以减少缺陷的产生,提高产品的表面光洁度和机械性能;另一方面,良好的质量控制可以减少生产中的浪费和成本,提高生产效率,增加企业的竞争力。
影响因素连铸坯的质量受到多种因素的影响,包括:1. 原料成份和纯度2. 浇注温度和浇注速度3. 结晶器结构和冷却水温度4. 结晶器护盖的材质和形状5. 连铸速度和拉速6. 过度超熔度和段距这些因素的合理控制和调整,可以有效地提高连铸坯的质量。
质量控制方法质量控制步骤连铸坯质量控制主要包括以下几个步骤:1. 原料质量检验:对原料的成份、纯度及其它关键指标进行检验,确保原料的质量符合要求。
2. 浇注质量控制:合理控制浇注温度和速度,以避免过热或者过冷引起的坯体缺陷。
3. 结晶器质量控制:结晶器的结构和冷却水温度对坯体的结晶质量有直接影响,因此需加强结晶器的质量控制。
4. 连铸速度和拉速控制:坯体的连铸速度和拉速会影响坯体的晶粒细化程度和坯体的机械性能,需要进行合理的控制。
5. 坯体表面质量控制:通过加强护盖材料和形状的选取,合理调整过度超熔度和段距,以提高坯体表面的光洁度。
质量控制指标连铸坯的质量控制需要依据具体产品的要求和标准来制定相应的指标。
普通来说,常见的质量控制指标包括:1. 外观质量:包括表面光洁度、无裂纹、无疤痕等;2. 坯体几何尺寸:包括宽度、厚度、长度等;3. 结晶质量:包括坯体的晶粒细化程度、晶界清晰度等;4. 坯体力学性能:包括抗拉强度、屈服强度、延伸率等;以上指标应根据产品要求,通过实验和测试方法进行监控和评估。
连铸坯质量的控制

连铸坯质量的控制
一、引言
连铸是钢铁生产过程中的重要环节,其连铸坯的质量影响着钢质的稳定性、物
理性能和化学成分等方面。
因此,连铸坯质量控制一直是钢铁生产中的关键技术之一。
二、连铸坯质量的影响因素
1.原料质量:包括钢水、氧化渣等的质量;
2.坯型结构和尺寸:坯型结构和尺寸的设计直接影响坯料的冷却效果和
内部应力状态;
3.坯料表面状态:表面缺陷会在浇铸过程中暴露出来,影响坯料的质量;
4.坯料内部缺陷:坯料内部缺陷会影响钢材的使用寿命和物理性能;
5.连铸工艺参数:包括浇注速度、结晶器温度和冷却水流量等。
三、连铸坯质量控制的措施
为了控制连铸坯质量,需要在生产过程中采取以下措施:
1.加强原料质量控制:保证钢水、氧化渣等原料的质量,避免对坯料质
量的不利影响;
2.优化坯型设计:通过设计合理的坯型结构和尺寸,使坯料均匀冷却、
内部应力均匀分布;
3.改进坯料清理技术:减少表面缺陷的产生;
4.加强坯料表面处理:处理坯料表面缺陷,消除缺陷部位;
5.控制连铸工艺参数:调整浇注速度和结晶器温度等工艺参数控制坯料
成分,改善坯料品质。
四、
通过加强原料质量控制、优化坯型设计、改进坯料清理技术、加强坯料表面处
理和控制连铸工艺参数等措施,可以有效地控制连铸坯质量。
同时,连铸坯质量控制也是钢铁生产中不可或缺的环节,对于提高钢材质量和降低成本都具有非常重要的意义。
连铸坯夹杂物产生原因分析及改进

连铸坯夹杂物产生原因分析及改进连铸坯夹杂物是指在连铸过程中,铸坯表面或内部产生的杂质、夹杂等缺陷。
这些夹杂物不仅影响产品的质量,还可能导致设备损坏和能源浪费。
对连铸坯夹杂物的产生原因进行分析,并提出改进措施,对于提高产品质量和生产效率具有重要意义。
1. 铸造温度控制不当在连铸过程中,如果温度控制不当会导致金属流动迅速,易产生气泡、气孔和夹杂物。
尤其是温度过高时,金属流动性增强,易使附着在壁面的夹杂物被带入坯内。
2. 浇注速度过快浇注速度过快会导致金属在注入过程中发生湍流,从而带进大量氧化物和夹杂物,严重影响坯体质量。
3. 模具表面清洁度不足如果模具表面不干净或有杂质,会直接影响坯体表面质量,产生夹杂物。
4. 冷却不均匀冷却不均匀会导致坯体收缩速度不一致,易产生裂纹和夹杂物。
5. 金属液处理不当金属液中如果存在杂质或气体,会在连铸过程中被带入坯内,造成坯体夹杂物。
二、改进措施1. 严格控制铸造温度控制铸造温度是连铸生产的重要环节,合理控制温度能有效减少夹杂物的产生。
通过优化工艺参数、合理选择合金配比和调整造坯温度,实现杂质减少和坯体质量提高。
2. 合理控制浇注速度通过调整浇注速度,控制金属流动的平稳性,避免湍流的产生,减少氧化物和夹杂物的带入。
3. 加强模具表面清洁定期清洁和维护模具表面,保证模具表面清洁平整,避免杂质的带入,减少夹杂物。
5. 加强金属液处理加强金属液的过滤和净化,排除其中的杂质和气体,减少夹杂物的产生。
通过上述改进措施的实施,能够有效降低连铸坯夹杂物的产生,提高产品质量,降低生产成本,改进生产环境。
连铸坯夹杂物产生原因分析及改进对于企业的生产具有重要意义。
三、结语连铸坯夹杂物的产生对于产品质量和生产效率具有严重影响,因此加强对夹杂物产生原因的分析和改进措施的研究十分必要。
通过严格控制铸造温度、合理控制浇注速度、加强模具清洁、控制坯体冷却速度和加强金属液处理等改进措施的实施,能够有效减少夹杂物的产生,提高产品质量和生产效率。
提高铸坯质量的措施

一、判断题1、提高铸坯质量的措施,主要是采用提高铸坯柱状晶的比率。
( )2、小方坯使用刚性引锭杆时,在二冷区上段不需要支承导向装置,而二冷区下段需要导板。
( )3、等表面温度变负荷冷水是指二冷区各段给水量保持不变而达到铸坯表面温度均衡的目的。
( )4、钢水凝固过程中的收缩包括液态收缩、凝固收缩和固态收缩三部份。
( )5、CAS—OB 工艺是指在钢包内吹氩搅拌并合金化。
( )6、浇注过程中结晶器水蓦地压力上升,流量减少的原因是水管破裂或者脱落。
( )7、铸坯含 C 量小于或者等于 0.17%时,方能允许进冷库冷却。
( )8、结晶器长度,主要取决于拉坯速度,结晶器出口安全坯壳厚度和结晶器的冷却强度。
( )9、全面质量管理的五大要素是人、机、料、法、环。
( )10、炼钢中[Si]+[O ]= (SiO )是吸热反应。
( )2 211、含碳量在 0.17~0.22%的碳素钢铸坯对热裂纹的敏感性最大。
( )12、事故冷却水的水流量应不小于正常水流量的 1/5。
( )13、事故冷却水的冷却部位有结晶器冷却水和机械闭路水。
( )14、连铸计算贡控制系统的基本结构形式有主机控制和程序控制两种类型。
( )15、按正弦方式振动的结晶器,其结晶器内铸坯的平均拉速为结晶器振幅×振动频率。
( )16、钢水的浇注温度就是液相线温度。
( )17、CaF 在结晶器保护渣中主要起到调节碱度作用。
( )218、弧形连铸机的铸坯变形量=铸坯厚度×1/弧形半径。
( )19、弧形连铸机铸坯夹杂物往往会萃在 1/4 处的内弧位置。
( )20、连铸二冷水冷却强度越大,铸坯中心等轴晶越发达,而柱状晶越窄。
( )21、径电磁搅拌的铸坯等轴晶率提高,柱状晶率降低。
( )22、普碳钢按技术条件所分的甲类钢是指保证化学成份,但不保证机械性能的钢。
()23、钢包底吹氩透气砖放在底面正中比放在偏心处搅拌效果要好。
连铸坯质量控制技术

连铸坯质量控制技术引言连铸是一种重要的铸造工艺,用于生产大批量的金属坯料。
连铸坯的质量直接影响到后续工艺的效果和产品的质量。
因此,连铸坯质量控制技术是提高产品质量和降低生产成本的关键。
本文将介绍连铸坯质量控制技术的重要性,并详细探讨了影响连铸坯质量的因素和常用的质量控制方法。
连铸坯质量的重要性连铸坯是下一步金属加工的原料,其质量直接影响到成品的质量。
良好的连铸坯质量可以保证产品的力学性能、表面质量和尺寸精度。
同时,优质的连铸坯还可以减少加工过程中的金属损耗和工时,提高生产效率和经济效益。
此外,连铸坯质量控制也是减少缺陷和事故的重要环节。
通过合理的质量控制措施,可以有效预防坯料的开裂、缺口、气孔等缺陷,避免金属材料的浪费和安全事故的发生。
综上所述,连铸坯质量控制技术对于提高产品质量和生产效率具有重要意义。
影响连铸坯质量的因素连铸坯质量受到多个因素的影响。
以下是一些常见的影响因素:1. 喷水冷却水质量连铸过程中的喷水冷却是保证连铸坯结晶过程良好进行的重要环节。
冷却水的质量对连铸坯表面质量和内部组织均匀性有很大影响。
如果冷却水中含有过多的杂质和氯离子,容易导致坯料表面起泡、气孔等缺陷。
2. 浇注温度和速度浇注温度和速度是影响连铸坯结晶行为的关键参数。
过高的温度和过快的浇注速度会导致坯料表面凝固不均匀,产生质量缺陷。
而过低的温度和过慢的浇注速度则会引起结晶过程延长,出现细晶区、大晶区等组织缺陷。
3. 结晶器结构和材料结晶器是连铸过程中实现坯料结晶的关键部件。
结晶器的结构和材料选择直接影响到连铸坯的结晶行为和组织性能。
不合理的结构设计和材料选择可能导致结晶器磨损、结晶不良等问题。
4. 冷却方式和参数连铸坯的冷却方式和参数选择对坯料的宏观和微观组织均有影响。
合理的冷却方式和参数可以保证连铸坯结晶行为的均匀性和完整性,防止产生缺陷和组织不良现象。
常用的质量控制方法为了确保连铸坯质量的稳定和一致性,可以采用以下几种常用的质量控制方法:1. 自动化控制系统自动化控制系统可以通过实时监测和控制连铸过程的关键参数,如浇注温度、浇注速度和冷却水流量等,来确保连铸坯的质量符合要求。
连铸坯质量控制

连铸坯质量控制连铸坯质量控制引言连铸坯质量是决定钢铁产品质量的重要因素之一。
在连铸过程中,通过控制连铸坯的凝固结晶形貌、尺寸尺寸以及内部缺陷等,可以保证最终钢铁产品的质量稳定性。
本文将介绍连铸坯质量控制的基本原则和常用技术手段。
1. 连铸坯凝固结晶形貌控制1.1 凝固路径设计连铸坯的凝固路径设计是影响凝固结晶形貌的关键因素。
凝固路径包括主要凝固温度区间、凝固速度以及凝固过程中应有的温度梯度等要点。
通过科学合理地设计凝固路径,可以控制连铸坯的凝固结晶形貌,提高产品的均匀性和致密性。
1.2 凝固浸没深度控制凝固浸没深度是指连铸坯在铸机中浸没的深度。
凝固浸没深度的调整可以通过调整浇注速度、浇注高度和结晶器深度等因素来实现。
恰当地控制凝固浸没深度可以优化凝固结构,减少坯壳厚度和缩孔等缺陷的发生。
2. 连铸坯尺寸控制2.1 坯型设计连铸坯的尺寸控制需要科学合理地设计坯型。
坯型设计要考虑连铸机的性能和工艺条件,以及产品需要达到的尺寸要求。
有效的坯型设计可以保证连铸坯尺寸的精确控制,减少修磨损失并提高铸坯产量。
2.2 坯型换边控制连铸坯在连铸过程中,由于挤压力和引拉力的作用,容易发生坯型换边的情况。
坯型换边会导致铸轧过程中尺寸控制困难,甚至导致产品尺寸不合格。
通过控制连铸机的工艺参数和优化设备结构,可以有效地控制坯型换边,提高铸坯质量。
3. 连铸坯内部缺陷控制3.1 结晶器设计结晶器是连铸过程中控制坯内部缺陷的关键设备。
结晶器的设计应考虑到坯内部的流动状态,并通过合理的传热和传质方式,控制连铸坯内的气体和夹杂物等缺陷。
合理的结晶器设计可以有效减少坯内部夹杂物和气体等缺陷的产生。
3.2 液相线保护措施液相线是连铸过程中凝固结构变化的关键位置。
液相线的形成过早或过晚都会导致内部缺陷的产生。
通过合理的冷却水设定和轧制工艺,可以保证液相线的稳定形成,有效控制坯内部缺陷。
结论连铸坯质量控制是保证钢铁产品质量稳定的关键环节。
连铸坯质量控制

连铸坯质量控制连铸坯质量控制1. 引言2. 连铸坯质量特点连铸坯的质量特点主要包括以下几个方面:2.1 凝固结构连铸坯是通过冷却凝固过程形成的,其凝固过程直接影响到坯体的凝固结构。
凝固结构的好坏会对后续的加工以及材料性能产生重要影响。
2.2 化学成分均匀性连铸坯的化学成分均匀性是其质量的重要指标之一。
成分不均匀容易导致后续钢材性能不稳定,从而影响到产品的质量。
2.3 表面缺陷由于连铸坯制造过程中的一些不可避免的因素,气体夹杂、氧化皮等,会在坯体表面形成一些缺陷。
这些表面缺陷会对后续产品的外观质量产生负面影响。
2.4 尺寸偏差连铸坯的尺寸偏差是指坯体的实际尺寸与标准尺寸之间的差异。
尺寸偏差会影响到钢材的加工工艺和成形质量。
3. 连铸坯质量控制因素及措施连铸坯质量的影响因素众多,包括原料质量、连铸工艺参数、设备状况等。
针对这些影响因素,可以采取以下控制措施来提高连铸坯的质量:3.1 原料质量控制通过严格控制原料的化学成分和物理性能,确保连铸坯的化学成分均匀性和机械性能达到要求。
3.2 连铸工艺参数控制连铸工艺参数的合理设置对坯体的凝固结构和表面质量具有决定性影响。
需要通过优化连铸工艺参数,如冷却水流量、浇注速度等,来控制连铸坯的质量。
3.3 设备维护与改进连铸设备的状态对连铸坯质量也有重要影响。
定期进行设备维护和检修,及时处理设备故障,可以保证设备处于良好状态,进而提高连铸坯的质量。
3.4 检测手段与技术利用先进的检测手段和技术,如超声波检测、磁力检测等,可以对连铸坯进行质量检测,及时发现问题并采取相应措施。
4.连铸坯质量控制是钢铁生产中至关重要的环节。
通过对连铸坯质量特点的分析和影响因素的控制,可以采取相应的措施来提高连铸坯的质量。
这不仅对于保证下游产品质量,还对于提高工业生产效益和降低资源消耗具有重要意义。
开展连铸坯质量控制工作是必不可少的。
连铸坯夹杂物产生原因分析及改进

连铸坯夹杂物产生原因分析及改进连铸坯夹杂物是指连铸坯或铸坯中存在的非金属夹杂物,这些夹杂物严重影响了连铸坯的质量和性能,需要通过分析夹杂物产生原因并采取相应措施进行改进。
夹杂物产生的原因主要有以下几个方面:1. 原料质量问题:连铸坯夹杂物可能与原料中的非金属夹杂物有关。
原料中含有杂质、铁锈或其他非金属物质,这些杂质在铸态时会被包裹在连铸坯或铸坯中,形成夹杂物。
2. 连铸工艺问题:连铸过程中存在的操作不当或工艺参数控制不准确也会导致夹杂物的产生。
浇注速度过快、结晶器冷却不均匀、结晶器表面存在污染等都可能导致夹杂物的生成。
3. 环境污染问题:连铸过程中环境污染也是夹杂物的产生原因之一。
铸造车间内存在的灰尘、颗粒物和金属粉末等都可能污染铸造材料,导致夹杂物的产生。
夹杂物产生后,我们可以采取以下措施进行改进:1. 严格控制原料质量:及时对原料进行检测和筛选,清除杂质和铁锈,确保原料的纯净度和质量。
2. 优化连铸工艺:通过调整连铸工艺参数,例如控制浇注速度、提高结晶器冷却均匀性、加强结晶器清洁等,减少夹杂物的形成。
4. 加强设备维护和管理:定期对连铸设备进行检修和维护,确保设备的正常运转和工艺参数的准确控制,减少夹杂物的产生。
5. 引入先进设备和技术:引入先进的连铸设备和技术,例如真空连铸技术、电磁搅拌连铸技术等,可以有效减少夹杂物的生成。
连铸坯夹杂物产生的原因主要有原料质量问题、连铸工艺问题和环境污染问题。
为减少夹杂物的产生,我们可以从严格控制原料质量、优化连铸工艺、加强环境污染控制、加强设备维护和管理以及引入先进设备和技术等方面入手进行改进。
这些措施将有助于提高连铸坯的质量和性能,满足市场需求。
第五讲-连铸坯内部质量控制

第六讲连铸坯内部质量的控制北京科技大学课程主要内容1.绪论2.连铸技术的发展3.凝固理论(形核、长大、凝固组织控制)4.钢液的凝固原理(结晶器、二次冷却)5.连铸坯表面质量控制6.连铸坯内部质量控制7.连铸新技术主要内容1 连铸坯中心缺陷概念2 影响连铸坯中心缺陷形成因素3 防止铸坯中心缺陷的对策4 铸坯中心缺陷形成机理5 结语前言从结晶器拉出来带有液芯的坯壳,在连铸机内边传热、边凝固、边运行而形成很长液相穴的铸坯(少则几米多则十几或二十几米),由于受凝固、传热、传质和工艺的限制,沿液相穴路径常常发生钢水补缩不好,在铸坯完全凝固后,沿铸坯轴向(拉坯方向)某些局部区域常常发现疏松、缩孔和偏析,常称为中心缺陷。
根据钢种和产品用途不同,对连铸坯中心缺陷有严格要求,板坯中心缺陷严重会引起中厚板横向性能尤其是冲击韧性不合格,管线钢抵抗,氢脆(HIC)裂纹能力恶化。
对于中高碳大方坯轧制棒材或线材产品常常会因中心缺陷严重使大方坯低倍检验不合格而导致产品合格率降低。
因此减轻铸坯中心缺陷至不使产品产生废品,这是提高连铸坯内部质量的一个重要任务。
1 连铸坯中心缺陷概念1.1 铸坯中心缺陷形貌沿铸坯横向或纵向轴线剖开经硫印或酸浸后,可显示出低倍结构,(图1-1)沿铸坯纵剖面中心轴线可发现:y中心疏松y中心缩孔y中心偏析(宏观偏析,它与疏松缩孔伴生)y点状或V形偏析(半宏观偏析)沿铸坯横剖面,则中心区有点状疏松或缩孔。
图1-1 铸坯低倍形貌1.2 铸坯中心缺陷评价(1)宏观评级零级相当于中心结构致密,5级为中心疏松尺寸大且连续。
在高过热度浇铸时,约80%铸坯相当于1、2、3级,而20%铸坯相当于4、5级。
(3)化学元素分布从铸坯横断面从内弧到外弧隔一定距离钻样,分析C、Si、Mn、S、P元素以表征铸坯表面至中心的成分差异(图1-3)。
图1-3 铸坯横断面成分分布从铸坯纵向轴线剖开沿中心线隔一定距离钻样,分析C、Si、Mn、S、P成分,以表征铸坯中心线区域成分差异(图1-4)图1-4 铸坯中心成分分布表1-1 铸坯偏析比也可用SEM(Scanning Electron Microscope) 来描述铸坯或轧材试样上Mn偏析图谱,以表征微观偏析状况。
连铸坯质量及控制方法

连铸坯质量及控制方法1、连铸坯质量的含义是什么?最终产品质量决定于所供给的铸坯质量。
从广义来说,所谓连铸坯质量是指得到合格产品所允许的铸坯缺陷的严重程度。
它的含义是:——铸坯纯净度(夹杂物数量、形态、分布、气体等)。
——铸坯表面缺陷(裂纹、夹渣、气孔等)。
——铸坯内部缺陷(裂纹、偏析、夹杂等)。
铸坯纯净度主要决定于钢水进入结晶器之前处理过程。
也就是说要把钢水搞“干净”些,必须在钢水进入结晶器之前各工序下功夫,如冶炼及合金化过程控制、选择合适的炉外精炼、中间包冶金、保护浇注等。
铸坯的表面缺陷主要决定于钢水在结晶器的凝固过程。
它是与结晶器坯壳形成、结晶器液面波动、浸入式水口设计、保护渣性能有关的。
必须控制影响表面质量各参数在目标值以内,以生产无缺陷铸坯,这是热送和直接扎制的前提。
铸坯的内部缺陷主要决定于在二次冷却区铸坯冷却过程和铸坯支撑系统。
合理的二次冷却水分布、支承辊的对中、防止铸坯鼓肚等是提高铸坯内部质量的前担。
因此,为了获得良好的铸坯质量,可以根据钢种和产品的不同要求,在连铸的不同阶段如钢包、中间包、结晶器和二次冷却区采用不同的工艺技术,对铸坯质量进行有效控制。
2、提高连铸钢种的纯净度有哪些措施?纯净度是指钢中非金属夹杂物的数量、形态和分布。
要根据钢种和产品质量,把钢中夹杂物降到所要求的水平,应从以下五方面着手:——尽可能降低钢中[O]含量;——防止钢水与空气作用;——减少钢水与耐火材料的相互作用;——减少渣子卷入钢水内;——改善钢水流动性促进钢水中夹杂物上浮。
从工艺操作上,应采取以下措施:(1)无渣出钢:转炉采用挡渣球(或挡渣锥),防止钢渣大量下到钢包。
(2)钢包精炼:根据钢种选择合适的精炼方法,以均匀温度、微调成分、降低氧含量、去除气体夹杂物等。
(3)无氧化浇注:钢水经钢包精炼处理后,钢中总氧含量可由130ppm下降到20ppm以下。
如钢包→中间包注流不保护或保护不良,则中间包钢水中总氧量又上升到60~100ppm范围,恢复到接近炉外精炼前的水平,使炉外精炼的效果前功尽弃。
【方法】连铸坯质量及控制方法
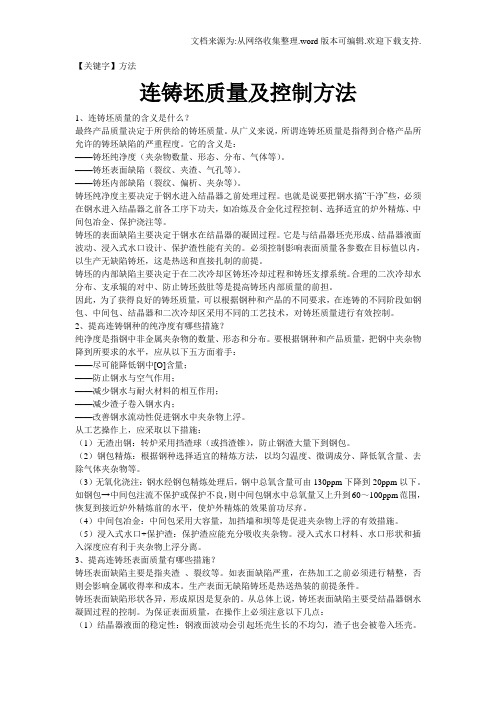
【关键字】方法连铸坯质量及控制方法1、连铸坯质量的含义是什么?最终产品质量决定于所供给的铸坯质量。
从广义来说,所谓连铸坯质量是指得到合格产品所允许的铸坯缺陷的严重程度。
它的含义是:——铸坯纯净度(夹杂物数量、形态、分布、气体等)。
——铸坯表面缺陷(裂纹、夹渣、气孔等)。
——铸坯内部缺陷(裂纹、偏析、夹杂等)。
铸坯纯净度主要决定于钢水进入结晶器之前处理过程。
也就是说要把钢水搞“干净”些,必须在钢水进入结晶器之前各工序下功夫,如冶炼及合金化过程控制、选择适宜的炉外精炼、中间包冶金、保护浇注等。
铸坯的表面缺陷主要决定于钢水在结晶器的凝固过程。
它是与结晶器坯壳形成、结晶器液面波动、浸入式水口设计、保护渣性能有关的。
必须控制影响表面质量各参数在目标值以内,以生产无缺陷铸坯,这是热送和直接扎制的前提。
铸坯的内部缺陷主要决定于在二次冷却区铸坯冷却过程和铸坯支撑系统。
合理的二次冷却水分布、支承辊的对中、防止铸坯鼓肚等是提高铸坯内部质量的前担。
因此,为了获得良好的铸坯质量,可以根据钢种和产品的不同要求,在连铸的不同阶段如钢包、中间包、结晶器和二次冷却区采用不同的工艺技术,对铸坯质量进行有效控制。
2、提高连铸钢种的纯净度有哪些措施?纯净度是指钢中非金属夹杂物的数量、形态和分布。
要根据钢种和产品质量,把钢中夹杂物降到所要求的水平,应从以下五方面着手:——尽可能降低钢中[O]含量;——防止钢水与空气作用;——减少钢水与耐火材料的相互作用;——减少渣子卷入钢水内;——改善钢水流动性促进钢水中夹杂物上浮。
从工艺操作上,应采取以下措施:(1)无渣出钢:转炉采用挡渣球(或挡渣锥),防止钢渣大量下到钢包。
(2)钢包精炼:根据钢种选择适宜的精炼方法,以均匀温度、微调成分、降低氧含量、去除气体夹杂物等。
(3)无氧化浇注:钢水经钢包精炼处理后,钢中总氧含量可由130ppm下降到20ppm以下。
如钢包→中间包注流不保护或保护不良,则中间包钢水中总氧量又上升到60~100ppm范围,恢复到接近炉外精炼前的水平,使炉外精炼的效果前功尽弃。
连铸坯夹杂物产生原因分析及改进

连铸坯夹杂物产生原因分析及改进一、引言连铸是一种重要的钢铁生产工艺,通过将液态金属直接连续浇注成坯,在一定程度上能够提高铸坯质量,提高生产效率。
在连铸生产过程中,常常会出现夹杂物问题,严重影响了铸坯的质量和使用性能。
对连铸坯夹杂物产生原因进行深入分析,找出问题根源,采取相应的改进措施,是非常有必要的。
二、连铸坯夹杂物的产生原因分析1.原料水分过高在连铸生产过程中,原料的水分含量过高是造成坯内夹杂物的一个重要原因。
当原料表面的水分在铸造过程中蒸发时,会产生气泡,导致坯内夹杂物的生成。
原料的水分控制非常重要。
2.连铸坯结晶器冷却不足结晶器的冷却不足也是连铸坯夹杂物的常见原因之一。
当结晶器温度过高时,坯内的气体无法充分排出,导致夹杂物的产生。
保证结晶器的有效冷却是减少坯内夹杂物的关键。
3.连铸过程中的气体包被排除不彻底在连铸过程中,气体包会随着液态金属一起进入坯内,如果气体包排除不彻底,就会在坯内停留,并在坯内形成夹杂物。
连铸过程中对气体排除的控制非常重要。
4.结晶器内流动状态不佳结晶器内的流动状态不佳也会导致坯内夹杂物的产生。
如果结晶器内的金属流动不畅,坯内的气体排出不畅,就会产生夹杂物。
结晶器内流动状态的改善对减少坯内夹杂物至关重要。
6.连铸坯冷却过程不足连铸坯冷却过程不足也是坯内夹杂物产生的一个重要原因。
在坯冷却过程中,如果冷却不足,坯内的气体和夹杂物无法充分排出,就会在坯内停留,影响坯的质量。
三、连铸坯夹杂物产生原因改进方案1.加强对原料水分的控制首先要加强对原料水分的控制,确保原料表面的水分含量符合要求。
通过调整原料的储存和运输环节,减少原料表面的水分含量,从源头上减少坯内夹杂物的产生。
2.优化结晶器冷却系统优化结晶器冷却系统,确保结晶器的冷却效果达到要求。
通过调整冷却水的流量和温度,确保结晶器内的金属流动状态良好,坯内的气体排出畅通。
3.加强气体排除措施在连铸过程中,加强气体排除措施,确保气体包在坯内充分排除。
连铸基础知识及提高连铸坯质量措施

连铸基础知识及提高连铸坯质量措施1.钢水由液体转变为固体的条件是什么?我们把一杯水(如20℃)放在-20℃的冷库里,当水的温度降到0℃时,杯子里就有晶体出现,此时是水和水的晶体共存,温度仍是0℃,只有当水完全结冰后,杯子整个温度下降到与冷库温度相同。
所以,把水开始结冰的温度叫凝固温度。
钢水的凝固结晶过程也同水一样,当温度降到凝固温度(1535℃)时,就有晶体出现。
由此可知,要实现液体转变为固体的过程,必须满足两个条件,即一定的过冷度和结晶核心。
所谓过冷度,就是实际温度低于凝固温度的度数。
如纯铁,只有过冷度达到295℃时,液体金属中许多体积很小、近程有序排列的原子集团才能形成胚胎晶核作为结晶核心而逐渐长大。
然而在实际生产中,把钢水浇到模子里,结晶所需的过冷度只有几度,这是因为:1)模子温度低,钢水温度高,模壁提供了冷却动力。
2)模型表面的凸凹不平,提供了“依托”,有利晶核形成。
3)钢水中悬浮的质点也可作为结晶核心。
2.钢水凝固过程中的收缩包括哪些?钢水由液态转变为固态,随着温度下降,收缩可分为: (1)液态收缩:由浇注温度降到液相线温度的收缩。
对于低碳钢一般为1%; (2)凝固收缩:液体完全变为固体的体积收缩。
对于钢一般为3~4%。
体积收缩会在钢锭中留下缩孔。
(3)固态收缩:从固相线温度冷却到室温的收缩。
一般为7~8%。
固态收缩表现为整个钢锭的线收缩,它与钢冷却过程的相变有关。
对钢锭产生裂纹有重要影响。
液体钢密度为7.0g/cm3,固体钢密度为7.8g/cm3,则液体变为固体收缩量为:((7.8-7.0)/7.0)×100%=11.4%,其中液态收缩量约1%,凝固收缩3~6%,固态收缩7~8%。
凝固时3~4%的体积收缩在钢锭中会留下缩孔,采用保护帽使缩孔集中在钢锭头部。
而连铸时钢水不断补充到液相,故连铸坯中无集中缩孔。
而带液芯的铸坯继续凝固时的线收缩对铸坯质量和生产安全性有重要影响。
因此结晶器应保持一定的倒锥度,二次冷却区支承辊的辊缝从上到下应符合铸坯线收缩的规律。
- 1、下载文档前请自行甄别文档内容的完整性,平台不提供额外的编辑、内容补充、找答案等附加服务。
- 2、"仅部分预览"的文档,不可在线预览部分如存在完整性等问题,可反馈申请退款(可完整预览的文档不适用该条件!)。
- 3、如文档侵犯您的权益,请联系客服反馈,我们会尽快为您处理(人工客服工作时间:9:00-18:30)。
提高连铸坯内部质量的方法
提高连铸坯内部质量的方法有以下几点:
1. 优化铸造工艺:合理控制浇注温度、浇注速度和冷却条件,确保铸造过程中连铸坯内部温度均匀,并避免温度梯度过大造成的结构变化。
2. 提高连铸机设备性能:增加转速变换频率、提高铸坯拉速和调整结晶器倾斜角度等,能够使连铸坯的结晶过程更加均匀,减少内部缺陷的产生。
3. 控制铸态组织:合理选择铸态结构和组织控制技术,避免连铸坯内部产生大片偏析、夹杂物等缺陷。
可以采用定向凝固技术、过冷等离子体熔炼技术、空载预轧等方法,减少组织缺陷。
4. 优化坯料质量:对坯料进行合理选择和处理,确保坯料化学成分和内部缺陷达到要求,减少连铸坯内部产生缺陷的概率。
5. 加强质量控制:加强连铸过程中的在线监测和控制,及时发现和处理连铸坯内部质量问题,避免次品的产生。
可以利用各种无损检测手段对连铸坯进行检测,如超声波检测、X射线检测等。
总之,提高连铸坯内部质量需要从铸造工艺、设备性能、铸态组织、坯料质量和质量控制等方面共同改进和优化。