论文:浅谈生产管理
浅谈安全生产管理及隐患排查治理重要性
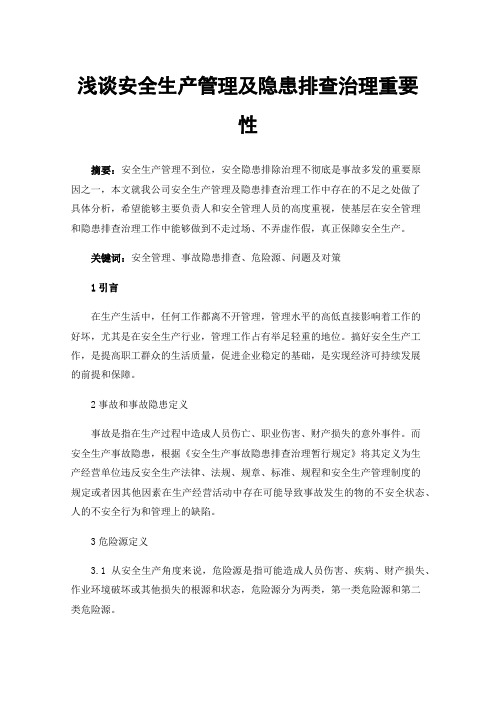
浅谈安全生产管理及隐患排查治理重要性摘要:安全生产管理不到位,安全隐患排除治理不彻底是事故多发的重要原因之一,本文就我公司安全生产管理及隐患排查治理工作中存在的不足之处做了具体分析,希望能够主要负责人和安全管理人员的高度重视,使基层在安全管理和隐患排查治理工作中能够做到不走过场、不弄虚作假,真正保障安全生产。
关键词:安全管理、事故隐患排查、危险源、问题及对策1引言在生产生活中,任何工作都离不开管理,管理水平的高低直接影响着工作的好坏,尤其是在安全生产行业,管理工作占有举足轻重的地位。
搞好安全生产工作,是提高职工群众的生活质量,促进企业稳定的基础,是实现经济可持续发展的前提和保障。
2事故和事故隐患定义事故是指在生产过程中造成人员伤亡、职业伤害、财产损失的意外事件。
而安全生产事故隐患,根据《安全生产事故隐患排查治理暂行规定》将其定义为生产经营单位违反安全生产法律、法规、规章、标准、规程和安全生产管理制度的规定或者因其他因素在生产经营活动中存在可能导致事故发生的物的不安全状态、人的不安全行为和管理上的缺陷。
3危险源定义3.1从安全生产角度来说,危险源是指可能造成人员伤害、疾病、财产损失、作业环境破坏或其他损失的根源和状态,危险源分为两类,第一类危险源和第二类危险源。
3.2第一类危险源指的是生产过程中存在的,可能发生意外释放的能量,包括生产过程中各种能量源、能量载体或危险物质。
以我公司为例,公司的主要业务为烟叶的生产、收购和储存,第一类危险源主要包括在育苗阶段易燃的漂盘、薄膜、育苗大棚、遮阳网、有毒的农药化肥等;收购阶段的烟叶、以及与之配套的麻片、麻绳、麻线等。
3.3第二类危险源是指导致能量或者危险物质约束或限制措施破坏或失效的各种因素,包括物的故障、人的失误、环境不良及管理缺陷等因素。
第二类危险源决定了事故发生的可能性,在公司的生产活动过程中对第二类危险源的控制尤为重要。
对这类危险源的控制离不开事故隐患的排查治理,这就要求我们把平时的安全检查做到位,及时发现和排除物的故障,减少人的失误,改善工作环境,完善各项安全管理制度,及时发现,并进行有效治理,事故就可能避免。
有关生产管理论文
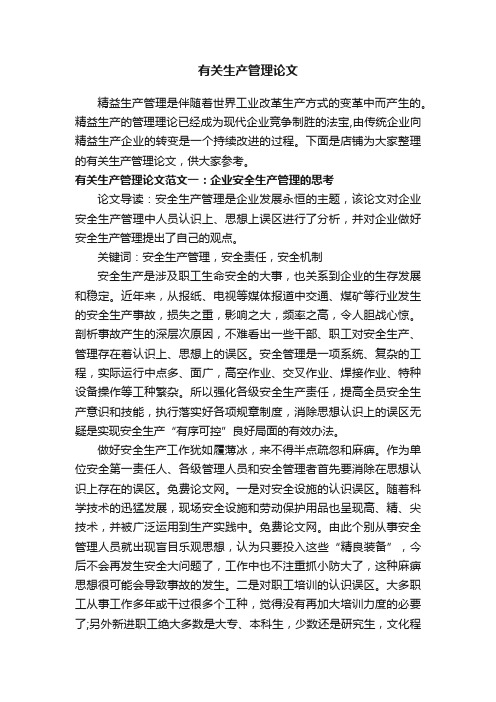
有关生产管理论文精益生产管理是伴随着世界工业改革生产方式的变革中而产生的。
精益生产的管理理论已经成为现代企业竞争制胜的法宝,由传统企业向精益生产企业的转变是一个持续改进的过程。
下面是店铺为大家整理的有关生产管理论文,供大家参考。
有关生产管理论文范文一:企业安全生产管理的思考论文导读:安全生产管理是企业发展永恒的主题,该论文对企业安全生产管理中人员认识上、思想上误区进行了分析,并对企业做好安全生产管理提出了自己的观点。
关键词:安全生产管理,安全责任,安全机制安全生产是涉及职工生命安全的大事,也关系到企业的生存发展和稳定。
近年来,从报纸、电视等媒体报道中交通、煤矿等行业发生的安全生产事故,损失之重,影响之大,频率之高,令人胆战心惊。
剖析事故产生的深层次原因,不难看出一些干部、职工对安全生产、管理存在着认识上、思想上的误区。
安全管理是一项系统、复杂的工程,实际运行中点多、面广,高空作业、交叉作业、焊接作业、特种设备操作等工种繁杂。
所以强化各级安全生产责任,提高全员安全生产意识和技能,执行落实好各项规章制度,消除思想认识上的误区无疑是实现安全生产“有序可控”良好局面的有效办法。
做好安全生产工作犹如履薄冰,来不得半点疏忽和麻痹。
作为单位安全第一责任人、各级管理人员和安全管理者首先要消除在思想认识上存在的误区。
免费论文网。
一是对安全设施的认识误区。
随着科学技术的迅猛发展,现场安全设施和劳动保护用品也呈现高、精、尖技术,并被广泛运用到生产实践中。
免费论文网。
由此个别从事安全管理人员就出现盲目乐观思想,认为只要投入这些“精良装备”,今后不会再发生安全大问题了,工作中也不注重抓小防大了,这种麻痹思想很可能会导致事故的发生。
二是对职工培训的认识误区。
大多职工从事工作多年或干过很多个工种,觉得没有再加大培训力度的必要了;另外新进职工绝大多数是大专、本科生,少数还是研究生,文化程度较高,于是就降低了三级教育网络的培训标准;还有一些企业因使用劳务人员流动性较大,实施三级安全教育较繁琐,于是便心存侥幸,省略或简化了三级安全教育。
生产管理方法范文

生产管理方法范文生产管理方法是企业管理的重要部分,它关乎企业的生产效率和质量,直接影响着企业的成本和市场竞争力。
因此,采用适当的生产管理方法可以在企业生产过程中提高效率和质量。
本文将从以下几个方面分析生产管理方法:生产计划、生产控制、质量管理和成本控制。
生产计划生产计划是企业生产管理中最基础也是最重要的一个环节。
正确的生产计划可以合理地安排各种资源的利用,使生产效率最大化。
而不合理的生产计划则可能导致原材料和设备的浪费,增加企业生产成本,甚至影响客户的满意度。
因此,企业应根据具体情况制定科学合理的生产计划,包括在合理的时间内完成特定的工作,采用现代化设备等。
生产控制企业的生产过程有许多不确定性和变量,生产控制就是能够实现对整个生产过程的实时监控。
通过对生产工艺、物流、库存、销售和客户需求的分析,确定必要的生产控制点。
这样就可以保证生产过程的稳定性和质量的可控性。
在生产控制方面,还可以采用电子商务平台,实现对生产线的监控和追踪。
其目的在于提高生产效率,优化生产资源,减少浪费。
质量管理质量管理是保证产品质量的重要手段。
通过管理和优化生产流程,能够提高产品的质量和可靠性,提高产品的市场占有率和客户的满意度。
在质量管理中,可采用ISO9000认证模式,对生产过程进行规范化管理,建立质量保证体系,保证产品质量达到标准要求。
同时,要通过对质量问题的分析和解决解决,不断提升产品的质量和服务水平。
成本控制成本控制是企业管理中的另一个重要环节。
通过合理地控制成本,企业可以将其生产成本降到最低限度,并提高企业的盈利能力。
成本控制涉及到产品设计、生产设备、原材料、库存管理等方面,要在满足生产质量的前提下,实现最大的成本效益。
因此,企业应关注并采用成本管理工具,如ABC分析法、成本核算法等,帮助企业更好地管理成本。
生产管理方法是企业管理不可短少的一部分。
通过科学合理的生产计划、高效的生产控制、高质量的质量管理和精准的成本控制,可以在企业的生产过程中达到最优的效果。
某橡胶制品厂生产管理系统论文
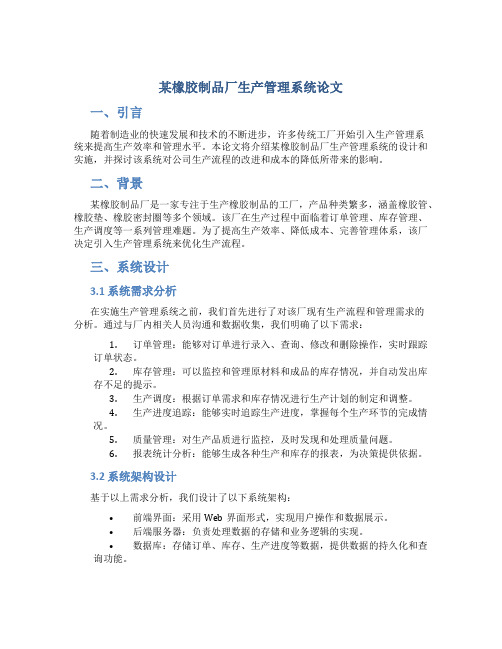
某橡胶制品厂生产管理系统论文一、引言随着制造业的快速发展和技术的不断进步,许多传统工厂开始引入生产管理系统来提高生产效率和管理水平。
本论文将介绍某橡胶制品厂生产管理系统的设计和实施,并探讨该系统对公司生产流程的改进和成本的降低所带来的影响。
二、背景某橡胶制品厂是一家专注于生产橡胶制品的工厂,产品种类繁多,涵盖橡胶管、橡胶垫、橡胶密封圈等多个领域。
该厂在生产过程中面临着订单管理、库存管理、生产调度等一系列管理难题。
为了提高生产效率、降低成本、完善管理体系,该厂决定引入生产管理系统来优化生产流程。
三、系统设计3.1 系统需求分析在实施生产管理系统之前,我们首先进行了对该厂现有生产流程和管理需求的分析。
通过与厂内相关人员沟通和数据收集,我们明确了以下需求:1.订单管理:能够对订单进行录入、查询、修改和删除操作,实时跟踪订单状态。
2.库存管理:可以监控和管理原材料和成品的库存情况,并自动发出库存不足的提示。
3.生产调度:根据订单需求和库存情况进行生产计划的制定和调整。
4.生产进度追踪:能够实时追踪生产进度,掌握每个生产环节的完成情况。
5.质量管理:对生产品质进行监控,及时发现和处理质量问题。
6.报表统计分析:能够生成各种生产和库存的报表,为决策提供依据。
3.2 系统架构设计基于以上需求分析,我们设计了以下系统架构:•前端界面:采用Web界面形式,实现用户操作和数据展示。
•后端服务器:负责处理数据的存储和业务逻辑的实现。
•数据库:存储订单、库存、生产进度等数据,提供数据的持久化和查询功能。
3.3 系统功能模块根据系统设计要求,我们将系统功能划分为以下模块:1.订单管理模块:实现订单的录入、查询、修改和删除功能。
2.库存管理模块:监控和管理原材料和成品的库存情况。
3.生产调度模块:根据订单需求和库存情况进行生产计划的制定和调整。
4.生产进度追踪模块:实时追踪生产进度,掌握每个生产环节的完成情况。
5.质量管理模块:监控生产品质,及时发现和处理质量问题。
车间管理论文
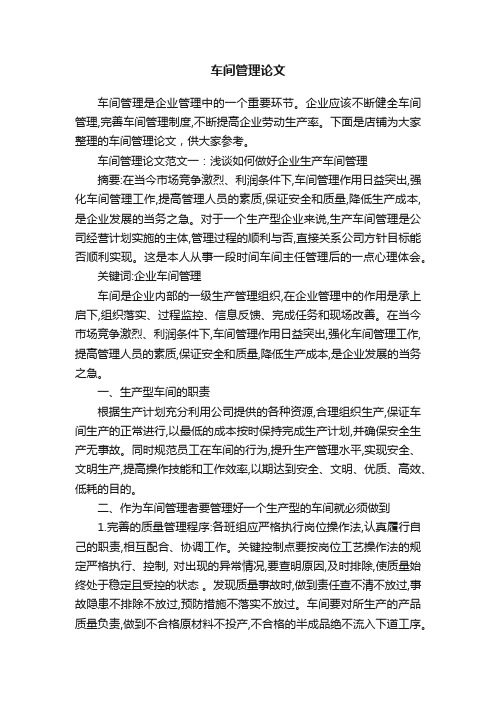
车间管理论文车间管理是企业管理中的一个重要环节。
企业应该不断健全车间管理,完善车间管理制度,不断提高企业劳动生产率。
下面是店铺为大家整理的车间管理论文,供大家参考。
车间管理论文范文一:浅谈如何做好企业生产车间管理摘要:在当今市场竞争激烈、利润条件下,车间管理作用日益突出,强化车间管理工作,提高管理人员的素质,保证安全和质量,降低生产成本,是企业发展的当务之急。
对于一个生产型企业来说,生产车间管理是公司经营计划实施的主体,管理过程的顺利与否,直接关系公司方针目标能否顺利实现。
这是本人从事一段时间车间主任管理后的一点心理体会。
关键词:企业车间管理车间是企业内部的一级生产管理组织,在企业管理中的作用是承上启下,组织落实、过程监控、信息反馈、完成任务和现场改善。
在当今市场竞争激烈、利润条件下,车间管理作用日益突出,强化车间管理工作,提高管理人员的素质,保证安全和质量,降低生产成本,是企业发展的当务之急。
一、生产型车间的职责根据生产计划充分利用公司提供的各种资源,合理组织生产,保证车间生产的正常进行,以最低的成本按时保持完成生产计划,并确保安全生产无事故。
同时规范员工在车间的行为,提升生产管理水平,实现安全、文明生产,提高操作技能和工作效率,以期达到安全、文明、优质、高效、低耗的目的。
二、作为车间管理者要管理好一个生产型的车间就必须做到1.完善的质量管理程序:各班组应严格执行岗位操作法,认真履行自己的职责,相互配合、协调工作。
关键控制点要按岗位工艺操作法的规定严格执行、控制, 对出现的异常情况,要查明原因,及时排除,使质量始终处于稳定且受控的状态。
发现质量事故时,做到责任查不清不放过,事故隐患不排除不放过,预防措施不落实不放过。
车间要对所生产的产品质量负责,做到不合格原材料不投产,不合格的半成品绝不流入下道工序。
2.严格的工艺管理制度:严格执行生产工艺规程,任何人不得擅自变更。
对新工人和工种变动人员进行岗位技能培训,经考核合格并有熟练工人指导方可上岗操作,生产车间要不定期检查工艺参数执行情况。
建筑施工安全生产管理几点措施论文
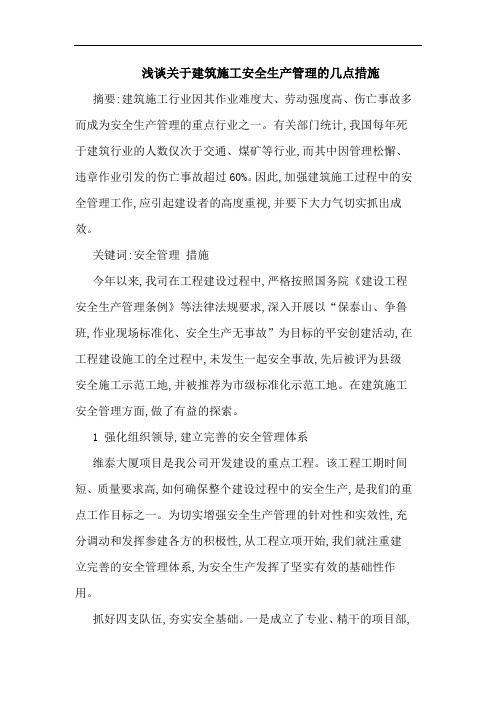
浅谈关于建筑施工安全生产管理的几点措施摘要:建筑施工行业因其作业难度大、劳动强度高、伤亡事故多而成为安全生产管理的重点行业之一。
有关部门统计,我国每年死于建筑行业的人数仅次于交通、煤矿等行业,而其中因管理松懈、违章作业引发的伤亡事故超过60%。
因此,加强建筑施工过程中的安全管理工作,应引起建设者的高度重视,并要下大力气切实抓出成效。
关键词:安全管理措施今年以来,我司在工程建设过程中,严格按照国务院《建设工程安全生产管理条例》等法律法规要求,深入开展以“保泰山、争鲁班,作业现场标准化、安全生产无事故”为目标的平安创建活动,在工程建设施工的全过程中,未发生一起安全事故,先后被评为县级安全施工示范工地,并被推荐为市级标准化示范工地。
在建筑施工安全管理方面,做了有益的探索。
1 强化组织领导,建立完善的安全管理体系维泰大厦项目是我公司开发建设的重点工程。
该工程工期时间短、质量要求高,如何确保整个建设过程中的安全生产,是我们的重点工作目标之一。
为切实增强安全生产管理的针对性和实效性,充分调动和发挥参建各方的积极性,从工程立项开始,我们就注重建立完善的安全管理体系,为安全生产发挥了坚实有效的基础性作用。
抓好四支队伍,夯实安全基础。
一是成立了专业、精干的项目部,具体负责工程的筹建工作。
二是公开招标具有甲级资质的新疆玉点建筑设计研究院设计,为实现包括建筑安全在内的各项目标提供了基础性保障。
三是公开招标具有二级资质的新疆维泰开发建设(集团)股份有限公司房建公司,作为安全生产的主体,这是非常重要的一支队伍。
四是公开招标具有甲级资质新疆昆仑工程监理有限公司,组成了强有力的监理项目部,负责工程施工的全程监理工作。
由我公司牵头,协调设计、施工、监理三方,加强监管调度,为整个工程建设包括安全生产工作目标任务的顺利完成,提供了有力的组织保证。
建立安全机构,健全安全体系。
项目开工前,我们即组织基建科、施工单位、监理单位负责人成立了安全生产工作领导小组,严格按照国务院《建设工程安全生产管理条例》要求,对施工单位、监理单位主体行为及职责做出明确要求,督促施工单位、监理单位各自健全安全机构,配齐安全管理人员,完善安全制度,落实安全措施,保障安全资金足额投入,健全安全生产管理机制。
管生产安全的管理

管生产安全的管理
《管生产安全的管理》
生产安全是企业经营中不可或缺的重要环节,而有效的生产安全管理则是保障生产安全的关键。
在现代工业生产中,管生产安全的管理变得越来越重要,因为生产安全事故不仅会造成人员伤亡和财产损失,还会影响企业的声誉和发展。
因此,建立完善的生产安全管理体系,对企业来说至关重要。
首先,管生产安全的管理需要建立健全的制度。
企业应该根据具体情况建立相应的安全管理制度,包括生产作业流程、安全操作规范、应急预案等。
这些制度可以规范员工的工作行为,提高生产安全的保障水平。
其次,企业需要加强生产安全的监督和检查。
通过设立专业的安全管理部门,加强对生产环境和设备的检查,及时发现和解决存在的安全隐患。
同时,加强员工的安全教育和培训,提高员工的安全意识和安全技能,减少因操作不当导致的事故发生。
另外,企业需要加强与政府主管部门的合作。
政府主管部门有权对企业的生产安全进行监督和检查,并对不符合安全标准的企业进行处罚。
因此,企业应积极配合政府部门的工作,接受政府的监督和指导,共同维护生产安全。
最后,企业还需要加强对生产安全管理的投入。
通过引进先进的生产安全管理技术和设备,提高安全管理水平,预防事故的发生。
同时,加大对生产安全管理人员的培训和奖励,提高其
管理水平和积极性,保障生产安全的顺利进行。
总之,管生产安全的管理是企业生产经营中不可或缺的一环,对于确保企业的稳定发展和员工的安全,都具有不可替代的作用。
企业应该加强生产安全管理,切实加强生产安全工作,从而保障企业的正常运营和发展。
浅谈如何搞好安全生产管理工作

浅谈如何搞好安全生产管理工作任何工作都离不开管理,管理水平的高低直接影响着工作的优劣,尤其是在安全生产工作中,管理工作占有举足轻重的地位。
对于安全来说,查处事故和事故苗头隐患固然重要,但更重要的是“防范于未然”,要在平日工作里兢兢业业地把好安全关,不留任何隐患。
在治黄和经济发展中要始终坚持“安全第一,预防为主,综合治理”的方针,突出抓好人员、设备、管理三个重要环节,广泛开展安全宣传教育活动,加强安全防范措施,筑牢安全堤防,才能有力促进治黄事业和经济发展。
下面结合几年来的工作实际谈一下安全管理方面的肤浅认识。
一、要树立安全重于泰山的安全意识,坚持以人为本,以全面提高职工的安全素子为核心,筑牢安全生产墙安全生产关键是要提高人的安全意识,关键就是始终坚持以人为本的思想,从确立意识主导地位入手,强调安全第一是管理者的责任,多层次提高职工队伍素质,筑牢安全墙。
结合黄河部门来讲就是要把安全第一意识与防汛、工程管理、经济发展等工作放到同等重要的位置来抓。
坚持“安全就是效益、安全就是稳定、安全就是政绩”的思想和观念,多形式、多渠道开展安全生产教育,处理好安全和生产,安全和治黄,安全和经济发展的关系。
一切工作都必须服从于安全,把安全列入单位重要的议事日程,坚持在计划、布置、检查、总结评比各项工作的同时把安全生产防范作为一项重要任务来布置,真正做到人人抓安全,事事讲安全,形成完善的安全网络。
二、要强化安全教育,切实提高全员安全意识,形成人人重视安全生产的良好氛围根据多年从事安全工作的经历,使我体会到,安全生产教育是做好安全生产工作的重要组成部分。
要安全就必须全员参与,要实现安全生产,就需要上下齐心,群策群力。
单位的每一位职工对安全生产工作的关心和重视层度,直接关系到整单位安全生产工作的状况。
人若没有安全意识,就是最大的事故隐患,一个潜在的“定时炸弹”,随时都有发生事故的可能。
因此,我们要做好安全教育,利用一切会议和场合做好宣传,提高全员安全意识。
关于生产车间现场管理的文章

关于生产车间现场管理的文章
生产车间现场管理是指对生产车间进行有效组织、协调和监督,以确保生产过程的顺利进行。
它涉及到生产设备、人员、材料等资源的优化配置和协调,以提高生产效率、降低成本、保证产品质量。
在生产车间现场管理中,有几个重要的方面需要注意。
首先是生产设备的管理。
生产设备是生产车间的核心,对于设备的正常运行和维护是确保生产效率的关键。
因此,需要制定设备维护计划,定期对设备进行检查、保养和维修,以及培训维修人员,确保设备的可靠性和稳定性。
其次是人员的管理。
人员是生产车间的重要资源,需要合理安排和管理。
要根据生产任务的需求,合理配置人员数量和工作岗位,确保每个岗位都有合适的人员。
此外,还需要培训和提升员工的技能水平,使其能够胜任各项工作任务。
再次是材料的管理。
材料是生产过程中不可或缺的一部分,需要合理采购、储存和使用。
要根据生产计划,及时采购所需材料,并进行合理储存,避免浪费和过期。
同时,要建立材料使用记录和盘点制度,确保材料的使用和消耗可追溯。
还需要建立现场管理的标准化和规范化。
通过制定一系列的操作规程和作业指导书,明确各项工作的要求和流程,以便员工能够按照标准化的方式工作。
同时,要进行现场巡查和检查,及时发现和解
决问题,确保生产过程的顺利进行。
生产车间现场管理是企业生产过程中不可或缺的一环。
通过合理管理生产设备、人员和材料,建立标准化和规范化的工作流程,可以提高生产效率、降低成本、保证产品质量,从而为企业的发展提供有力的支持。
生产的安全管理

生产的安全管理
《生产的安全管理》
生产是企业的核心活动,然而在生产过程中存在着各种各样的安全隐患,如果不及时加以管理和控制,就会给企业带来巨大的损失。
因此,生产的安全管理显得至关重要。
首先,企业需要建立健全的安全管理制度和规章制度,明确各个岗位的职责和权利,以及安全操作规程和急救预案等。
这样可以使员工明确自己在生产过程中应该注意的事项,提高员工的安全意识。
其次,企业应该加强安全生产培训,不仅包括操作技能的培训,还应该有相应的安全知识和应急处理能力的培训。
这样可以提高员工的安全操作能力,降低事故发生的可能性。
另外,企业还应该加强生产设备的维护和检修工作,保证生产设备处于良好的工作状态。
定期的设备检查和维护可以降低设备故障的可能性,降低生产事故的发生率。
此外,企业还可以利用现代科技手段,如智能监控系统、安全警示装置等,对生产过程进行实时监控和预警,及时发现问题并进行处理。
最后,企业应该建立健全的事故处理机制,对于可能发生的意外事故,要有明确的处理流程和应急预案,保证在事故发生时可以迅速有效地进行处理,减少事故带来的损失。
总之,生产安全管理是企业永恒的主题,只有做好安全管理工作,才能保障企业生产的顺利进行,保证员工的安全和健康。
企业应该从制度、培训、设备维护和事故处理等方面着手,全面提升生产的安全管理水平。
浅谈制造型企业生产管理现状
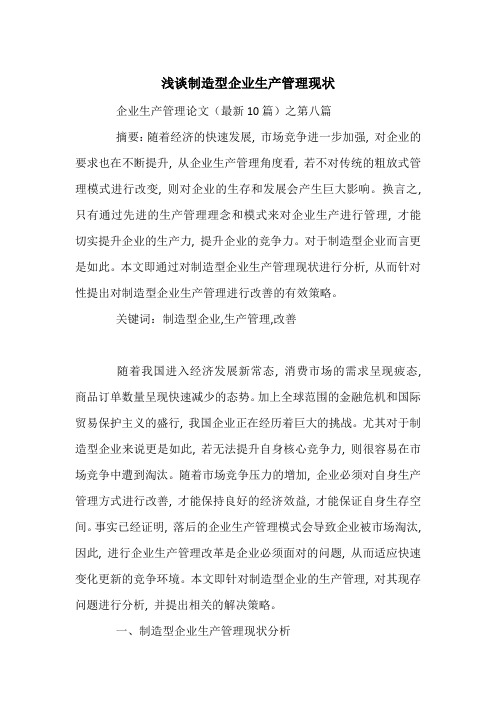
浅谈制造型企业生产管理现状企业生产管理论文(最新10篇)之第八篇摘要:随着经济的快速发展, 市场竞争进一步加强, 对企业的要求也在不断提升, 从企业生产管理角度看, 若不对传统的粗放式管理模式进行改变, 则对企业的生存和发展会产生巨大影响。
换言之, 只有通过先进的生产管理理念和模式来对企业生产进行管理, 才能切实提升企业的生产力, 提升企业的竞争力。
对于制造型企业而言更是如此。
本文即通过对制造型企业生产管理现状进行分析, 从而针对性提出对制造型企业生产管理进行改善的有效策略。
关键词:制造型企业,生产管理,改善随着我国进入经济发展新常态, 消费市场的需求呈现疲态, 商品订单数量呈现快速减少的态势。
加上全球范围的金融危机和国际贸易保护主义的盛行, 我国企业正在经历着巨大的挑战。
尤其对于制造型企业来说更是如此, 若无法提升自身核心竞争力, 则很容易在市场竞争中遭到淘汰。
随着市场竞争压力的增加, 企业必须对自身生产管理方式进行改善, 才能保持良好的经济效益, 才能保证自身生存空间。
事实已经证明, 落后的企业生产管理模式会导致企业被市场淘汰, 因此, 进行企业生产管理改革是企业必须面对的问题, 从而适应快速变化更新的竞争环境。
本文即针对制造型企业的生产管理, 对其现存问题进行分析, 并提出相关的解决策略。
一、制造型企业生产管理现状分析(一) 组织结构不合理企业只有具备合理的组织架构才能保证生产管理的有效和科学。
但对于制造型企业来说, 生产环节较为复杂, 不仅要做好产品调研、设计, 还要做好原料的采购和最后的产品流通。
对于这一系列环节, 必须做到组织结构的明确清晰, 且都有专门管理部门进行管理, 才能保证每一环节都不出现问题。
此外, 每个部门内部都要做好分工, 权责明确, 保证任务完成的高效性。
但当前许多制造企业存在着组织结构不合理的情况, 权责不明确, 结构臃肿, 从而严重影响了企业的运作, 也提升了企业的生产成本和管理成本。
生产管理管人范文

生产管理是企业中相当重要的一个环节,它涉及到企业生产的各个方面,包括企业的生产计划、生产过程的控制和协调等。
而要做好生产管理工作,管人是非常重要的一个方面,因为企业中的生产人员是生产的中心和最终落实者。
本文将从生产管理管人的角度出发,详细分析企业在生产管理中如何管好人。
一、人才的选择和培养企业的生产管理需要确保人才的选择和培养。
只有有专业素质和经验的生产人员才能够对生产过程进行有效管理和控制。
企业需要通过各种途径寻找和吸收高素质的生产人才,并通过培训和培养,提高员工的专业技能和综合素质,使之成为优秀的生产管理者。
二、建立有效的考评制度企业的生产管理也需要建立起科学、合理的考评制度。
考评制度是对生产人员的实际表现和工作水平进行评价的工具,它能够为企业提供科学的人才管理方案。
企业需要根据不同岗位和职责的要求,制定相应的考评标准,以确保考评的公正性和准确性。
三、建立,维护良好的沟通渠道生产管理需要建立和维护与生产员工之间的良好沟通渠道。
沟通渠道不仅可以加强生产管理的操作效率,还可以为实现预防性维护、安全生产等方面提供有力支持。
同时,生产人员也可以通过沟通渠道反馈生产中遇到的问题,以确保生产管理的科学化和规范化。
四、建立生产管理的文化企业需要建立和维护一种共同的文化氛围,使每一位生产人员都能够真正认识到生产管理对于企业发展的重要性和作用。
同时,企业需要加强对生产人员的考核和奖励,为员工创造良好的工作环境和条件,使生产管理成为每一位员工的主要目标和工作职责。
五、加强对技术的研发和应用随着时代变迁和科技进步,企业需要不断优化和改进生产管理的方式和方法,加强对技术的研发和应用。
通过采用智能化、自动化设备和信息技术,企业可以大大提升生产效率和质量,同时也能够深入了解生产员工的实际工作需要和情况,为生产管理提供更多有力的数据支持和指导。
生产管理是企业中不可或缺的一个重要环节,而生产管理管人则是保障企业生产管理质量的重要方面。
浅谈如何抓好安全生产管理工作

浅谈如何抓好安全生产管理工作抓好安全生产管理工作是贯彻落实科学发展观的具体体现,因为科学发展观的核心是以人为本,而安全生产的实践主体是人,安全生产本身是对人的生命权益的维护,“以人为本”是安全生产工作的出发点和落脚点,结合沙子镇安全生产管理工作的实际,谈一些安全生产管理的拙见。
一、用思想政治工作积极树立正确的安全生产理念安全生产各个领域安全意识的强弱,直接作用于他在生产经营活动中的安全行为,要深入细致地做好“要我安全”变为“我要安全”这一思想教育工作,牢固树立正确的安全生产理念,要把重视人的生命放在第一位,充分发挥安全生产主体和监管主体的职能作用,树立“安全发展”和“安全就是效益”理念。
二、重视安全生产环境的管理抓好安全生产管理工作,重要的是形成良好的安全生产环境,安全生产的环境不安全因素控制是一种细、实的管理过程管理,事故的发生,往往都是由小到大,由量变到质量的过程,保护人身安全是安全管理人员的本职所在,这就是“安全生产、重于泰山”,只有谨小慎微、防微杜渐,认真排查隐患,查找漏洞,加强安全自控能力,强化安全生产防御体系,才能最大限度地减少安全事故的发生,确保社会的平安与发展,安定与和谐,其正体现科学发展观。
三、安全生产管理需要不断创新近年来,国家对安全生产工作十分重视,但是习惯性违章屡禁不止,复生性事故时有发生,说明我们的安全生产管理理念和管理模式尚存在一定的缺陷和不足。
为此,安全生产管理必须与时俱进,不断创新。
理念创新是管理创新的前提和基础,只有以新的理念和科学的管理思想作指导,才能有科学的管理方法。
四、建立一支高素质的安全监管队伍现代安全管理确认了事故链中人、机、环境、管理综合要素,对安全员提出了很高的专业素质要求,不仅要组织开展风险防范工作,还要求熟悉安全生产领域的科技知识和相关法律法规,只有一支专业的安全管理和监督队伍,才能更好地促进安全生产管理工作。
五、加大安全生产的宣传力度宣传教育工作在安全生产上具有特殊功能,安全生产的方针是“安全第一,预防为主,综合治理”,预防除了必要的防范设施外,重要的是思想上的防范意识,筑起思想上的安全防线,这就需要加强安全生产的宣传,警钟长鸣,持之以恒。
车间管理论文

车间管理论文车间管理是制造企业中非常重要的一环,良好的车间管理可以提高生产效率、降低成本,保证产品质量。
本文将从五个方面详细探讨车间管理的重要性和实施方法。
一、合理规划生产流程1.1 制定生产计划:根据订单量、生产周期等因素制定合理的生产计划,确保生产任务按时完成。
1.2 优化生产流程:分析生产过程中的瓶颈环节,采取措施优化生产流程,提高生产效率。
1.3 配置设备设施:根据生产需求合理配置设备设施,确保生产过程顺利进行。
二、加强人员管理2.1 培训员工:为员工提供必要的技能培训,提高其生产技术水平,确保生产质量。
2.2 建立激励机制:制定奖惩制度,激励员工积极参与生产活动,提高生产效率。
2.3 定期评估绩效:定期对员工进行绩效评估,发现问题及时解决,提高整体生产水平。
三、严格质量控制3.1 制定质量标准:明确产品质量标准,建立质量检测体系,确保产品符合标准。
3.2 强化质量管理:加强对生产过程的监控,及时发现并解决质量问题,提高产品合格率。
3.3 完善质量反馈机制:建立质量反馈机制,及时收集客户反馈意见,不断改进产品质量。
四、优化物料管理4.1 精准采购计划:根据生产计划制定物料采购计划,确保物料供应及时、充足。
4.2 控制库存成本:合理控制库存量,避免过多库存导致资金占用,降低库存成本。
4.3 优化供应链管理:与供应商建立稳定的合作关系,提高供应链的稳定性和效率。
五、强化安全环保5.1 安全生产教育:加强员工安全意识培训,确保生产过程安全。
5.2 安全设施完善:建立健全的安全管理制度,配备必要的安全设施,保障员工安全。
5.3 环保意识提升:推行绿色生产理念,减少生产对环境的影响,实现可持续发展。
综上所述,车间管理对于制造企业的发展至关重要。
通过合理规划生产流程、加强人员管理、严格质量控制、优化物料管理和强化安全环保,企业可以提高生产效率、降低成本,保证产品质量,实现可持续发展。
浅谈电力安全生产管理论文
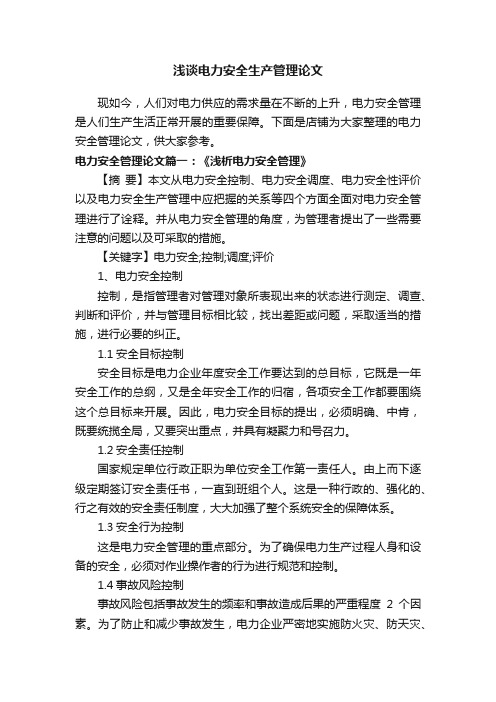
浅谈电力安全生产管理论文现如今,人们对电力供应的需求量在不断的上升,电力安全管理是人们生产生活正常开展的重要保障。
下面是店铺为大家整理的电力安全管理论文,供大家参考。
电力安全管理论文篇一:《浅析电力安全管理》【摘要】本文从电力安全控制、电力安全调度、电力安全性评价以及电力安全生产管理中应把握的关系等四个方面全面对电力安全管理进行了诠释。
并从电力安全管理的角度,为管理者提出了一些需要注意的问题以及可采取的措施。
【关键字】电力安全;控制;调度;评价1、电力安全控制控制,是指管理者对管理对象所表现出来的状态进行测定、调查、判断和评价,并与管理目标相比较,找出差距或问题,采取适当的措施,进行必要的纠正。
1.1安全目标控制安全目标是电力企业年度安全工作要达到的总目标,它既是一年安全工作的总纲,又是全年安全工作的归宿,各项安全工作都要围绕这个总目标来开展。
因此,电力安全目标的提出,必须明确、中肯,既要统揽全局,又要突出重点,并具有凝聚力和号召力。
1.2安全责任控制国家规定单位行政正职为单位安全工作第一责任人。
由上而下逐级定期签订安全责任书,一直到班组个人。
这是一种行政的、强化的、行之有效的安全责任制度,大大加强了整个系统安全的保障体系。
1.3安全行为控制这是电力安全管理的重点部分。
为了确保电力生产过程人身和设备的安全,必须对作业操作者的行为进行规范和控制。
1.4事故风险控制事故风险包括事故发生的频率和事故造成后果的严重程度2个因素。
为了防止和减少事故发生,电力企业严密地实施防火灾、防天灾、防人身伤亡的一系列技术措施,严格地对发、供电设备进行应急抢修和定期的、状态的预防修改或技改,开展设备的事故隐患普查和安全性评价等活动,组织专家对企业的事故风险进行预测等,都是力求使企业的事故风险值控制在最小的程度。
2、电力安全调度电网安全稳定运行是电力系统优质服务的重要指标之一。
电力调度的主要任务是指挥电网运行的倒闸操作,电网故障和事故处理,尽可能地保证电网的正常供电。
安全生产论文范文3篇

安全生产论文范文3篇1. 安全生产管理在企业生产中的重要性摘要:安全生产管理对于企业的持续健康发展具有至关重要的作用。
本文通过分析相关数据和案例,探讨了安全生产管理在企业生产中的重要性,并提出了一些有效的管理策略。
关键词:安全生产管理,企业生产,重要性,管理策略正文:在当今竞争激烈的市场经济环境下,企业要想实现持续健康发展,必须重视安全生产管理。
安全生产管理不仅可以确保员工的生命财产安全,还可以提高企业的生产效率和竞争力。
因此,安全生产管理在企业生产中具有重要的作用。
首先,安全生产管理可以保护员工的生命财产安全。
企业的员工是企业的重要资源,员工的生命和健康对企业的发展至关重要。
通过科学的安全生产管理,可以规范员工的工作行为,提高员工的安全意识,减少事故的发生。
同时,企业可以加强安全培训和教育,提高员工的安全技能和应急能力,有效预防和应对各种安全风险。
其次,安全生产管理可以提高企业的生产效率。
事故和意外事件会给企业的生产带来严重影响,导致生产停工、设备损坏等问题,进而影响企业的生产效率和经济效益。
通过科学的安全生产管理,可以规范生产流程,优化工作环境,降低安全风险,提高生产效率和产品质量。
此外,安全生产管理还可以促进企业内部的协作和团队精神,提升员工的工作积极性和创造力,进一步提高企业的生产效率。
最后,安全生产管理可以提高企业的竞争力。
在市场竞争激烈的环境下,企业需要不断提高竞争力才能够生存和发展。
安全生产管理作为企业的一项重要管理任务,可以提高企业的声誉和形象,增强消费者的信任和满意度,进而增加企业的市场份额和竞争力。
此外,安全生产管理还可以降低企业的法律风险和经济风险,在市场竞争中占据优势地位。
综上所述,安全生产管理是企业实现持续健康发展的重要保障。
企业应该加强对安全生产管理的重视,落实相关政策和制度,加强员工的安全教育和培训,提高安全生产管理水平,促进企业的可持续发展。
2. 安全生产责任的履行和监督机制摘要:安全生产责任是企业在安全生产管理中的核心要求。
(完整版)浅谈如何做好安全生产管理工作

浅谈怎样做好安全生产管理工作安全部是指在任何状况下,没有危险、没有威迫、没有事故、不受任何损害。
那么,用什么来保证不受以上的损害呢?第一我们在任何工作中都离不开管理,管理水平的高低直接影响着工作的好坏,特别是在安全生产工作中,管理工作据有举足轻重的地位。
安全管理是一项长久性、艰巨性的工作,在企业不停发展的今日,特别是在信息技术宽泛应用的局势下,只有专心管理,才能建立安全生产的有效屏障,才能保证安全生产工作有效连续展开。
一、抓安全生产管理,一定第一增强员工安全意识要增强员工的安全意识,除进行必需的正常的安全教育外,还一定创造一种警钟长鸣的气氛。
1、第一在全企业范围内成立强有力的严实的安全生产管理网络,做到安全生产层层有人抓,事事有人管,形成党政工团一齐抓,分管领导要点抓,专职人员详细抓,上下左右都配合的管理系统。
2、确立安全第一责任人,层层签订安全生产目标责任书,直至一线班组,真实做到各负其责,目注明确,任务详细。
3、鼎力展开各项安全活动,1)、开好安全例会活动,学习贯彻上司和企业的安全有关指示精神,部署安全生产与总结每周、月安全生产工作,剖析安全生产中的不利要素及存在的安全隐患,拟订出相应的防备举措,做到防微杜渐,防患于已然。
开好班前会,对员工进行危险预知活动,认真检查施工现场,作业人员身体素质、精神状态能否胜任工作。
安全组织举措、技术举措,安全制度能否落实到位。
落实“三个不”,就是拟订出“不损害别人,不损害自己,不被别人所损害”的有针对性的举措。
随时提示作业人员严格履行各项安全管理规定,严格根绝“三违”现象的发生。
2)、抓好每年展开的“安全万里行”、“安全生产月”、“安全演讲”、“安全知识比赛”警告教育等一系列活动。
以活动的展开带动整年安全工作,提升员工的安全意识,增强管理水平。
二、抓安全要仔细。
做到超前预防安全工作容不得半点虚假,来不得丝毫粗心,安全工作重在预防,制度预防,举措预防特别重要。
安全生产论文范文3篇

安全生产论文范文3篇论文一:《安全生产论文范文一》标题:提高企业安全生产管理水平的重要性摘要:安全生产管理是企业发展的基础和保障,对于保护职工生命财产安全、促进经济社会可持续发展具有重要意义。
本文通过分析企业安全生产管理的现状和存在的问题,提出了提高企业安全生产管理水平的几点建议。
关键词:安全生产管理,企业发展,职工安全,可持续发展一、引言安全生产是企业经营管理工作中不可忽视的重要环节。
企业的安全生产管理水平直接关系到企业的发展和职工的生命财产安全。
在当前经济发展速度快、全球化竞争日益激烈的时代,提高企业安全生产管理水平已经成为企业发展的重要任务。
二、现状分析目前,我国企业安全生产管理存在以下问题:1. 安全意识淡薄:许多企业的职工安全意识不强,容易忽视安全隐患;2. 安全生产责任不明确:企业内部安全生产责任划分不清晰,缺乏明确的执行机制;3. 安全设备落后:部分企业安全设备老化,不能有效预防和控制事故;4. 安全培训不到位:企业在安全培训方面的投入不足,导致职工对安全知识的了解不够。
三、提高企业安全生产管理水平的建议要提高企业安全生产管理水平,需要从以下几个方面入手:1. 加强安全宣传教育:通过组织安全培训、发放安全宣传材料等方式,提高职工对安全意识的认识和理解;2. 建立完善的安全责任制度:明确各级管理人员和职工的安全生产责任,加强安全管理的科学性和规范性;3. 大力推行安全设备更新换代:加强对企业安全设备的投入,及时更新老化设备,确保安全设备的完好性和有效性;4. 加强安全生产管理的监督和考核:建立健全安全管理的监督机制,对企业的安全生产管理进行定期评估和考核。
四、结论提高企业安全生产管理水平是企业可持续发展的重要保障,需要加强安全意识教育、建立完善的安全责任制度、更新安全设备和加强监督考核等方面的工作。
论文二:《安全生产管理的重要性与措施》摘要:安全生产管理是企业保护职工生命财产安全、促进经济社会可持续发展的重要环节。
- 1、下载文档前请自行甄别文档内容的完整性,平台不提供额外的编辑、内容补充、找答案等附加服务。
- 2、"仅部分预览"的文档,不可在线预览部分如存在完整性等问题,可反馈申请退款(可完整预览的文档不适用该条件!)。
- 3、如文档侵犯您的权益,请联系客服反馈,我们会尽快为您处理(人工客服工作时间:9:00-18:30)。
浅谈生产管理
摘要:
“时间紧、任务重、品质要求高”成为这一时期生产现场的重要特征,准时、保质、保量和以最小化的成本制造满足顾客需求的产品成为生产管理的目标,但在技能人员有限、设备等资源紧张瓶颈制约下,进度推进似乎愈来愈艰难。
我们在实践中可以尝试引入约束管理机制,通过这种机制能够迅速响应市场多样化和不确定的需求,快速提供满足顾客需求的产品。
关键词:生产管理约束管理策略虚拟制造
1我公司生产主要特征
1.1多品种并行
公司目前生产高压及防爆变频器等产品。
由于防爆产品是针对多个顾客做多种规格型号的产品。
不同的顾客有不同的需求,公司的资源置身于多个品种之中。
资源共享。
生产过程中的每个任务都需要资源,而在实际过程中能够使用的资源却非常有限。
例如,在生产过程中会遇到设备“打架”的问题,就是由于项目资源共享但调配不合理所造成的。
因此,必须对有限资源进行适当调配才能满足项目需求。
项目结果和生产周期的不确定性。
由于防爆产品的质量及稳定性有严格的要求,新研制的产品并不能保证一次设计就成功,在后续的过程中需要改进和完善的地方很多,一旦某项任务结果不理想,其它相关的任务也要相对调整,加大了过程的反复,对资源提出了新的挑战。
由于顾客的需求具有不稳定性,计划明确的节点与人、机、料、法、环等的齐套周期不一致等,生产的周期往往具有不确定性,周期不足的项目需要占用更多的资源,加大了生产控制的难度。
1.2生产流程稳定
由于公司生产的产品种类是基本不变的,这就决定了产品的关键路线及各个任务作为节点所构成的网络甘特图也基本一致。
如在防爆产品各项目的过程中,几乎所有的流程都是研发设计——工艺下发——物料准备——总装——调试老化——检验——入库等。
2约束条件
2.1虚拟制造大量存在
所谓虚拟制造,就是从产品设计开始,形成技术文件后委托外协厂加工制造,部件由外协厂进行加工、装配,构成部件总成,经过生产过程的质量检验、验收合格后送到工厂进行产品总装。
防爆产品具有系统集成的特点。
在长期的发展过程中,我公司虽然积累了一定的生产制造能力,但是仍有大量产品的制造过程不在公司内部,外购、外协产品大量存在,产品状态、进度及质量控制需要公司在外部复制出一套控制系统,这势必将耗用了一定的资源,也加大了生产管理控制的难度。
2.2物料控制、均衡生产难度大
零库存是基于JIT(Just In Time)模式建立的企业物料管理模式,它是在企业建立了稳定的供应链模式后采用的低成本物资管理模式,其基础是批量订货、低成本、及时供应。
在研制产品的生产管理过程中,小批量甚至单一产品的重复订货及较短的供货周期,极大地影响了供应商的及时性和整个供应链系统的稳定性,不愿意接受订单、无法满足周期以及产品质量不稳定导致重复订货等一系列问题,加大了系统齐套难度,影响了生产的顺利推进。
在多品种小批量产品的生产过程中,多个项目并行,而项目的相似性决定了其在一定时段内对设备、人力等资源的需求较强且存在冲突,而在另一时段,随着产品生产过程的逐步推进,紧张的资源又都闲置下来,资源的利用呈现波浪式的跳跃,影响了均衡生产。
2.3关键路线控制的局部性
目前的生产管理过程主要采用的是关键路线控制法,通过建立产品的生产
计划,找出关键、重要的产品来料,得出影响本次合同的关键路线,在资源利用上给与积极的支持,保证关键路线产品的顺利产出以保证批次产品的整体进度。
但是随着多批次产品的同时投入,各批次产品的关键路线存在着冲突的现象,如在生产过程中出现插单的现象,甚至出现需要领导“拍板”要求先加工哪个产品的现象。
由于各个批次的关键路线都集中在同一车间线体上,任何一个批次产品在关键路线上的延误都会导致无法满足生产周期的情况,关键路线管理的局部性影响了生产过程的整体推进。
3解决对策
3.1加强横向设计管理及工艺
方法的多样化研究目前的设计工要对加工方法进行多样化研究,保证一种产品在生产现场有多种可选择实现路径,如在目前的生产过程中,防爆产品外壳来料后还需要进行维修,这样就浪费了公司资源,从而导致生产成本及效率降低,如果来料品质可以保证,那么可以节省出公司资源。
当然,不能等到产品到达某工序时才考虑其工艺方法的可替代性,而是在投产前就提出可替代的方法,这样能较大地化解资源冲突的矛盾,促进生产有序推进。
另外,要加强成组技术研究,使不同型号相似模块成批、成组加工来保证加工效率和质量。
比如工装是加工产品的辅助手段,通常设计工装的目的是为了满足某一个产品的加工需求,而如果多个产品的加工需求具有通用性,在产品投产前先生产出具有通用性的工装,将会事半功倍。
3.2抓住关键核心
虚拟制造所带来的一系列问题主要表现在质量、进度不能完全满足需求,在过程中往往只提设计技术要求,产品设计制造出来后由于没有掌握核心,验收难度较大,有时候即使验收合格又存在不满足使用要求的情况。
因此,要保证虚拟制造满足需求必须进一步吃透技术,设计人员提出设计要求后,相关检验人员要对产品、实物进行详细分析,掌握关键数据和验收标准,如果短期内无法掌握,
则要对虚拟制造产品进行跟产,摸清其关键数据保证产品满足需求,提高虚拟制造的符合性。
3.3加强外协及计划管理
提前介入是保证物料及时供应的最好办法。
在目前的情况下,物资管理人员如果能提前了解产品的构成及主要性能,就能提前分析出影响生产的关键元素,提前做好相关准备。
通常的习惯是设计人员在设计开始前提一个长周期物料备料清单,但对其它物料(非关键却是重要的物料)需求却相对滞后,然而这类物料替代性相对较强且多型号均用,因此可考虑建立一个虚拟库存。
分年度、季度对此类物资进行分析,根据不同型号共用的特点进行预订、预购,并列出物资明细,在到货周期上进行分段设计,等产品正式图纸下达后,可通过平衡计划的方式进行物资管理,降低因小批量、单件订货增加的成本及管理难度,保证物料的及时供应。
多项目并行带来的最大问题是在一定时期内存在资源的漂移瓶颈。
根据年度、季度策划和能力平衡,不同项目长期看是均衡的,但因某一项目出现技术上、质量上、管理上的失误,造成各关键路线周期、节点变化,使原有的资源瓶颈发生变化,就是所谓的资源瓶颈漂移问题。
此时即使设备、人力资源满负荷也无法满足需求,资源在短期内也无法得到补充,外协的方式能够在很大程度上缓解资源瓶颈带来的挑战。
因此,要保障均衡生产就要加大外协管理的力度,要充分利用市场资源,做到各环节相互协调,保证生产需求。
在外协管理中要积极注意市场环境的基本情况及其变化,保证做到“拿的出去,带的回来”。
产生瓶颈漂移约束的另一个问题是投产日期。
目前的计划习惯是年前启动,经过设计、工艺、投产等各阶段,由于流程基本相似,到达生产现场的时间基本相同,在某一时间段可能基本上没有什么生产任务,但另一时间段却出现高潮,因此在投产期上也要依据批次产品的重要性、节点要求等进行排序,保证顺利推进又不相互影响,保障均衡生产的需要。
3.4变关键路线
为关键链路径首先要分析每个批次生产任务之间存在交叉的地方,如A、B两个型号的关键产品需要同样的生产资源,且都处于关键节点上,在具体的操作中就应首先对A、B任务的重要程度进行排序,确定优先任务并列入关键链路径。
但在优先任务的安排上对资源的可利用率只能设定70%,另外30%设定为缓冲。
随着B任务甚至C任务的节点要求,不断对缓冲值进行调整,以保证有一定的资源去实现多个任务(关键链以外任务)的需要。
如果B或C任务延迟生产不会影响B、C任务的需求,那么可将缓冲设定为临界值0,延迟B、C任务的开工,这样就可避开任务交错的影响。
在任务的实施过程中,最重要的是要及时更新每个任务的进程及缓冲的消耗情况,如果A任务的某关键节点还未完成而缓冲已经全部消耗,那么必须要通过增加资源来补充缓冲。
对于生产设备短缺的问题,可依靠产品外协、加班倒班等方式进行弥补。
缓冲的临界是不容易出现的,过程控制就是要依据整个生产系统中各任务链的完工程度及缓冲消耗程度的比值来决定资源使用权。
4结束语
我公司集研发、生产、销售为一体,这就要求我们在强大的研发团队下,不断研发新技术,创造新产品、并通过“高质、高效、低成本”的生产管理系统制造并提供出顾客所需产品。
生产管理是一个复杂系统的管理过程,任何一个环节的缺失都会影响整个系统的正常运行,约束条件出现时重要的是加强管理和引导,这样才能保证整个生产管理系统的正常运行。
达到顾客满意,并使公司朝着更高、更远的目标前进。