搅拌聚合反应器传热与传质
聚合反应工程基础试题及答案

聚合反应工程简答题第二章化学反应工程基础1.说明聚合反应工程的研究内容及其重要性。
研究内容:(1)工业规模的聚合过程为对象,以聚合反应动力学和聚合体系传递规律为基础;(2)将一般定性规律上升为数学模型,从而解决一般技术问题到复杂反应器设计,放大等提供定量分析方法和手段;(3)为聚合过程的开发,优化工艺条件等提供数学分析手段。
(背这个!)简而言之:聚合反应工程研究内容为:进行聚合反应器最佳设计;进行聚合反应操作的最佳设计和控制。
2.动力学方程建立时,数据收集方式和处理方式有哪些?收集方式:化学分析方法,物理化学分析方法处理方式:积分法,微分法。
3.(背!)反应器基本要求有哪些?①提供反应物料进行反应所需容积,保证设备一定生产能力;②具有足够传热面积;③保证参加反应的物料均匀混合4.基本物料衡算式,热量衡算式①物料衡算:反应物A流入速度-反应物A流出速度-反应物A反应消失速度-反应物A积累速度=0(简作:流入量-流出量-消失量-积累量=0)②热量衡算:随物料流入热量-随物料流出热量-反应系统与外界交换热量+反应过程的热效应-积累热量=05.(背!)何谓容积效率?影响容积效率的因素有哪些?(1)工业上,衡量单位反应器体积所能达到的生产能力称之为容积效率,它等于在同一反应,相同温度、产量、转化率条件下,平推流反应器与理想混合反应器所需总体积比:η=Vp/Vm=τp/τm。
(2)影响因素:反应器类型,反应级数,生产过程中转化率6.何为平推流和理想混合流?①反应物料在长径比很大的反应器中流动时,反应器内每一微元体积中流体均以同样速度向前移动,此种流动形态称平推流;②由于反应器强烈搅拌作用,使刚进入反应器物料微元与器内原有物料元瞬时达到充分混合,使各点浓度相等且不随时间变化,出口流体组成与器内相等此流动形态称理想混合流。
7.实现反应器的热稳定操作需满足哪些条件?①稳态条件:Qr=Qc。
②稳定条件:dQc/dT>dQr/dT。
反应器(反应釜)的结构和工作原理

反应器(反应釜)的结构和工作原理反应器是一种实现反应过程的设备,用于实现液相单相反应过程和液液、气液、液固、气液固等多相反应过程。
器内常设有搅拌(机械搅拌、气流搅拌等)装置。
在高径比较大时,可用多层搅拌桨叶。
在反应过程中物料需加热或冷却时,可在反应器壁处设置夹套,或在器内设置换热面,也可通过外循环进行换热。
第一部分:按操作方式分1、间歇釜式反应器或称间歇釜操作灵活,易于适应不同操作条件和产品品种,适用于小批量、多品种、反应时间较长的产品生产。
间歇釜的缺点是:需有装料和卸料等辅助操作,产品质量也不易稳定。
但有些反应过程,如一些发酵反应和聚合反应,实现连续生产尚有困难,至今还采用间歇釜。
间歇操作反应器系将原料按一定配比一次加入反应器,待反应达到一定要求后,一次卸出物料。
连续操作反应器系连续加入原料,连续排出反应产物。
当操作达到定态时,反应器内任何位置上物料的组成、温度等状态参数不随时间而变化。
半连续操作反应器也称为半间歇操作反应器,介于上述两者之间,通常是将一种反应物一次加入,然后连续加入另一种反应物。
反应达到一定要求后,停止操作并卸出物料。
间歇反应器的优点是设备简单,同一设备可用于生产多种产品,尤其适合于医药、染料等工业部门小批量、多品种的生产。
另外,间歇反应器中不存在物料的返混,对大多数反应有利。
缺点是需要装卸料、清洗等辅助工序,产品质量不易稳定。
2、连续釜式反应器,或称连续釜可避免间歇釜的缺点,但搅拌作用会造成釜内流体的返混。
在搅拌剧烈、液体粘度较低或平均停留时间较长的场合,釜内物料流型可视作全混流,反应釜相应地称作全混釜。
在要求转化率高或有串联副反应的场合,釜式反应器中的返混现象是不利因素。
此时可采用多釜串联反应器,以减小返混的不利影响,并可分釜控制反应条件。
大规模生产应尽可能采用连续反应器。
连续反应器的优点是产品质量稳定,易于操作控制。
其缺点是连续反应器中都存在程度不同的返混,这对大多数反应皆为不利因素,应通过反应器合理选型和结构设计加以抑制。
理想混合连续搅拌釜式反应器(CSTR)
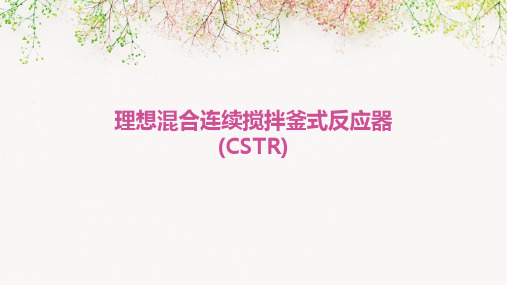
理想混合状态
物料在反应器内达到完全混合,不存在浓度和温度 的梯度分布。
反应器内各点的物料性质(如浓度、温度等)完全 相同,且随时间保持不变。
在理想混合状态下,反应器的性能达到最优,反应 效率和产物质量得到保证。
03
CSTR反应器的数学模型
物料平衡方程
进入反应器的物料流量与离开 反应器的物料流量相等,即输 入等于输出。
用于连续加入反应物和排出产物,实现连续化生产 。
工作流程
01
02
03
04
物料进入
反应物通过进料口连续加入反 应器内。
充分混合
在搅拌装置的作用下,物料在 反应器内充分混合,达到浓度 和温度的均匀分布。
反应进行
在适宜的反应条件下,物料在 反应器内进行化学反应。
产物排出
反应完成后,产物通过出料口 连续排出反应器。
100%
平均停留时间
表示物料在反应器内的平均停留 时间,影响反应器的生产能力和 产品质量。
80%
停留时间分布曲线
通过实验测定,可直观反映反应 器内物料的停留时间分布情况。
转化率与选择性
转化率
表示原料在反应器内转化为产 品的程度,是衡量反应器性能 的重要指标。
选择性
表示在给定转化率下,生成目 标产物的能力,反映反应器的 选择性能。
THANK YOU
感谢聆听
缺点与挑战
能耗较高
连续搅拌过程需要消耗大量能量,导致CSTR反应器的能耗相对较 高。
设备复杂度高
CSTR反应器结构复杂,涉及搅拌、传热、传质等多个过程,设备 设计、制造和维护难度较大。
放大效应
在将实验室规模的CSTR反应器放大至工业生产规模时,可能会遇到 放大效应问题,影响反应器的性能和产物质量。
《聚合反应工程与设备》课程教学大纲
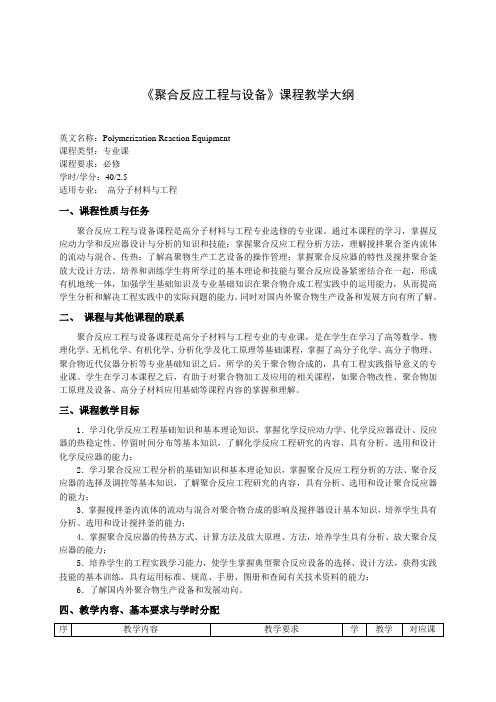
《聚合反应工程与设备》课程教学大纲英文名称:Polymerization Reaction Equipment课程类型:专业课课程要求:必修学时/学分:40/2.5适用专业:高分子材料与工程一、课程性质与任务聚合反应工程与设备课程是高分子材料与工程专业选修的专业课。
通过本课程的学习,掌握反应动力学和反应器设计与分析的知识和技能;掌握聚合反应工程分析方法,理解搅拌聚合釜内流体的流动与混合、传热;了解高聚物生产工艺设备的操作管理;掌握聚合反应器的特性及搅拌聚合釜放大设计方法。
培养和训练学生将所学过的基本理论和技能与聚合反应设备紧密结合在一起,形成有机地统一体,加强学生基础知识及专业基础知识在聚合物合成工程实践中的运用能力,从而提高学生分析和解决工程实践中的实际问题的能力。
同时对国内外聚合物生产设备和发展方向有所了解。
二、课程与其他课程的联系聚合反应工程与设备课程是高分子材料与工程专业的专业课,是在学生在学习了高等数学、物理化学、无机化学、有机化学、分析化学及化工原理等基础课程,掌握了高分子化学、高分子物理、聚合物近代仪器分析等专业基础知识之后,所学的关于聚合物合成的,具有工程实践指导意义的专业课。
学生在学习本课程之后,有助于对聚合物加工及应用的相关课程,如聚合物改性、聚合物加工原理及设备、高分子材料应用基础等课程内容的掌握和理解。
三、课程教学目标1.学习化学反应工程基础知识和基本理论知识,掌握化学反应动力学、化学反应器设计、反应器的热稳定性、停留时间分布等基本知识,了解化学反应工程研究的内容,具有分析、选用和设计化学反应器的能力;2.学习聚合反应工程分析的基础知识和基本理论知识,掌握聚合反应工程分析的方法、聚合反应器的选择及调控等基本知识,了解聚合反应工程研究的内容,具有分析、选用和设计聚合反应器的能力;3.掌握搅拌釜内流体的流动与混合对聚合物合成的影响及搅拌器设计基本知识,培养学生具有分析、选用和设计搅拌釜的能力;4.掌握聚合反应器的传热方式、计算方法及放大原理、方法,培养学生具有分析、放大聚合反应器的能力;5.培养学生的工程实践学习能力,使学生掌握典型聚合反应设备的选择、设计方法,获得实践技能的基本训练,具有运用标准、规范、手册、图册和查阅有关技术资料的能力;6.了解国内外聚合物生产设备和发展动向。
搅拌器设计
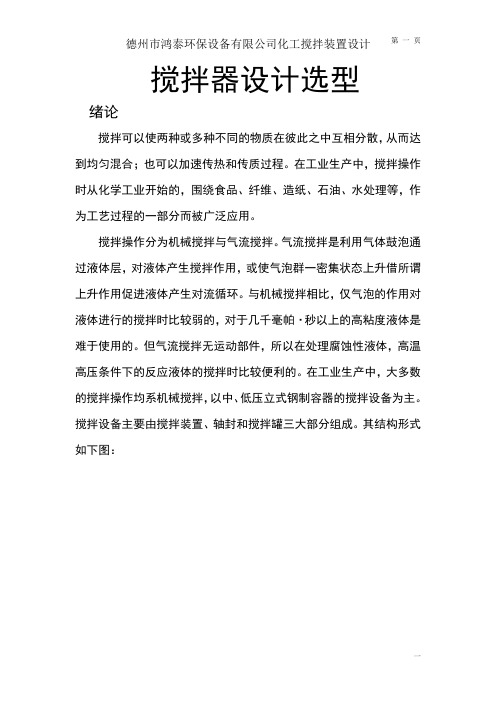
搅拌器设计选型绪论搅拌可以使两种或多种不同的物质在彼此之中互相分散,从而达到均匀混合;也可以加速传热和传质过程。
在工业生产中,搅拌操作时从化学工业开始的,围绕食品、纤维、造纸、石油、水处理等,作为工艺过程的一部分而被广泛应用。
搅拌操作分为机械搅拌与气流搅拌。
气流搅拌是利用气体鼓泡通过液体层,对液体产生搅拌作用,或使气泡群一密集状态上升借所谓上升作用促进液体产生对流循环。
与机械搅拌相比,仅气泡的作用对液体进行的搅拌时比较弱的,对于几千毫帕·秒以上的高粘度液体是难于使用的。
但气流搅拌无运动部件,所以在处理腐蚀性液体,高温高压条件下的反应液体的搅拌时比较便利的。
在工业生产中,大多数的搅拌操作均系机械搅拌,以中、低压立式钢制容器的搅拌设备为主。
搅拌设备主要由搅拌装置、轴封和搅拌罐三大部分组成。
其结构形式如下图:一搅拌装置结构图第一章搅拌装置第一节搅拌装置的使用范围及作用搅拌设备在工业生产中的应用范围很广,尤其是化学工业中,二很多的化工生产都或多或少地应用着搅拌操作。
搅拌设备在许多场合时作为反应器来应用的。
例如在三大合成材料的生产中,搅拌设备作为反应器约占反应器总数的99%。
搅拌设备的应用范围之所以这样广泛,还因搅拌设备操作条件(如浓度、温度、停留时间等)的可控范围较广,又能适应多样化的生产。
搅拌设备的作用如下:①使物料混合均匀;②使气体在液相中很好的分散;③使固体粒子(如催化剂)在液相中均匀的悬浮;④使不相溶的另一液相均匀悬浮或充分乳化;⑤强化相间的传质(如吸收等);⑥强化传热。
搅拌设备在石油化工生产中被用于物料混合、溶解、传热、植被悬浮液、聚合反应、制备催化剂等。
例如石油工业中,异种原油的混合调整和精制,汽油中添加四乙基铅等添加物而进行混合使原料液或产品均匀化。
化工生产中,制造苯乙烯、乙烯、高压聚乙烯、聚丙烯、合成橡胶、苯胺燃料和油漆颜料等工艺过程,都装备着各种型式的搅拌设备。
第二节搅拌物料的种类及特性搅拌物料的种类主要是指流体。
第六章 搅拌聚合釜的传热与传质讲解
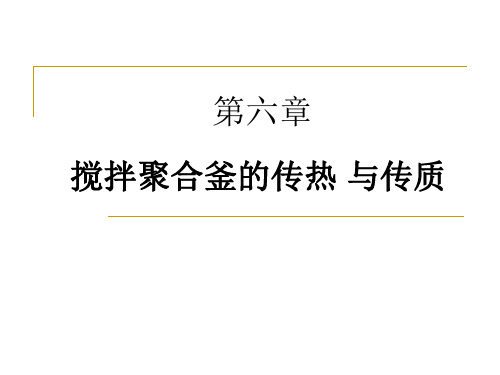
冷水
气相
冷水
冷水
液相
冷水 泵
(4)体外循环冷凝器:部分反应物料由反应器中用泵 抽出,经外部冷凝器冷却后再进入反应器.
还满足不了要求时,加容积及冷料降温。如顺丁胶 多釜聚合。
注意事项
(1)在容易结垢的聚合过程中,因为易结垢,且不易 清洗,所以釜聚合内不宜采用蛇管或管束冷却.乳液 聚合速率很快,常在釜内设置大量束管,帮助散热.
式中:α 被搅拌液体对壁面的传热系数;L定性长度,对夹 套釜L取釜径T;D为搅拌桨叶直径;N搅拌器转速;λ 导热系数 Cp 恒压热容,ρ 密度,μ b黏度μ w 为壁温下流 体的粘体黏度
湍流时, 取b=2/3,c=1/3, m=0.14
搅拌釜不同,a值不同.并限于指定标准釜。 标准几何尺寸釜为:T:D=3; H:T=1
假塑性流体大都处于层流区,常采用锚式,螺带 式搅拌器,传热关联式如下:
锚式:
i
T
1.5(NRe )0.5 (NPr )0.33(Vis )0.2 (50
N
Re
500)
螺带式 (0.1< N R en< N R e c)
此外最大传热速率可能不再反应阶段。
高粘体系注意刮壁作用设计。
第二节 搅拌聚合釜的传热方式
传热装置:夹套,内冷件,回流冷凝,体外循环 冷却器等.
(1)夹套:最常用.结构简单,但传热系数不高.
改进办法:提高夹套内传热介质的湍动
增加搅拌釜的总传热系数
(如在夹套内安装导流板或扰流喷嘴)
第六章 搅拌聚合釜的传热 与传质
第一节 聚合过程的传质问题
化学工程中的反应器设计

化学工程中的反应器设计在化学工程中,反应器设计是至关重要的一个环节。
一个好的反应器设计能够提高生产效率,降低投资成本,确保产品质量,并且减少环境污染。
本文将介绍反应器设计的基本原理和常见的反应器类型,并探讨一些反应器设计中需要考虑的关键因素。
反应器是化学反应过程中最常用的设备之一。
它是将反应物转化为所需产物的容器,在整个过程中起着决定性的作用。
反应器设计需要综合考虑多种因素,包括反应动力学、传热与传质、流体力学和材料的选择等。
一、反应器的基本原理反应器设计的基本原理是实现所需反应条件,使反应物尽可能地转化为产物,并控制反应速率以避免副反应和过程失控。
为了实现这些目标,我们需要了解反应动力学和反应环境的影响。
反应动力学是研究反应速率和反应机理的科学。
通过实验和模型建立,我们可以获得反应动力学数据,并构建适当的反应模型。
基于反应动力学,我们可以确定反应温度、压力、混合程度等操作条件,为反应器设计提供指导。
反应环境的影响也是反应器设计中需要考虑的因素之一。
例如,氧气和湿度对一些反应是重要的因素,需要在设计过程中充分考虑。
此外,反应物的浓度、酸碱度、催化剂等也会对反应器设计产生影响。
二、常见的反应器类型根据反应过程的不同要求,设计出了多种不同类型的反应器。
下面我们介绍几种常见的反应器类型。
1. 批量反应器(Batch Reactor)批量反应器是最简单、最常见的反应器类型之一。
它是一个密闭的容器,在一定时间内将反应物加入反应器中反应,然后将产物从反应器中取出。
批量反应器适用于小规模实验、多种反应物的反应和反应物浓度变化较大的情况。
2. 持续流动反应器(Continuous Flow Reactor)持续流动反应器是反应物连续流入,产物连续流出的反应器。
它可以根据需要进行连续的供料和产物提取,适用于大规模生产和长时间连续反应的情况。
常见的持续流动反应器类型包括管式反应器、搅拌槽反应器等。
3. 固定床反应器(Fixed Bed Reactor)固定床反应器是将催化剂或吸附剂装填在一定形状的床层中,通过流体在固定床上流动实现反应的一种反应器类型。
搅拌式反应器

搅拌釜式反应器的双区模型化学反应器是化工生产的核心设备,也是化学反应工程研究的核心,它的操作情况对整个生产过程起着决定性的作用。
在连续操作的反应器内,物料的流动与混合状况和因此而产生的反应时间、反应物浓度以及温度等反应参数的分布状况反映了工业反应器的最根本特征。
实际反应器内流体的流动状况存在着非理想流动,改变了物料的流动情况,进而改变了物料的浓度分布,最终则是影响结果。
为了准确地掌握反应器的性能,必须充分考虑实际反应器内的非理想流动对反应器的影响,根据实际情况与理想流型偏离的程度,建立一个较接近实际的流动模型。
造成反应器内流体流动情况变化的主要原因是返混。
由于返混改变物料的流动情况,从而改变反应器内物料浓度的分布,并使物料在反应器内部形成停留时间分布(RTD), RTD是流体流动情况的宏观体现,通过流体的RTD曲线能定量地估算每个流体相的混合物性和混合程度,以及每个流体相在反应器内的滞流量.当反应器没有外来传质和传热影响,它的特性就取决于特征动力学性质和RTD 曲线的性质。
在反应过程中。
反应的特征动力学性质不会改变。
所以,使用RTD 可以合理而又精确地描述反应器流体流动情况及混合特性,从而预测反应器的性能。
所以RTD模型即可反映物料的流动模型。
如何分析非理想流动和流型对反应器的影响,建立实际反应器内流体的流动模型,前人已经进行了大量的工作。
在许多的文献中,关于非理想因素对反应器性能的影响报道很多。
下面来讨论下反应器内可能存在的非理想因素的影响。
非理想流动和流型对化学反应产率和选择性的影响。
这两方面的影响因素进行综合考虑,用双区模型来描述实际反应器内流体的流动模型。
1、流动模型釜式反应器内的非理想流动主要有死区和短路。
死区主要存在于反应器的两个顶盖、畸形拐角、挡板与设备的交界处以及压力计的尾部等。
由于死区区域的流体几乎停滞不动,所以死区的存在减少了反应的有效体积;而短路则是当反应器的高径比较小时容易产生。
化学反应器设计中的传热传质分析

化学反应器设计中的传热传质分析化学反应器是化学工业中最重要的装置之一,用于合成和分解化学物质。
化学反应器的设计和操作对产品质量和生产成本至关重要。
其中,传热传质是反应器设计的一项重要考虑因素。
本文将介绍化学反应器设计中的传热传质分析。
一、传热传质基础传热传质是指物质间的热量和质量传递过程。
在化学反应器中,传热传质的效率决定着反应器的热量平衡和反应物的转化率。
在传热传质过程中,有五种基本的方式:对流传热传质、辐射传热传质、传导传热传质、扩散传质和对流传质。
在化学反应器中,主要使用对流传热传质和传导传热传质。
对流传热传质是指由于热量的差异,产生流体的运动和混合,从而使热量和质量得以传递。
传导传热传质是指热量沿着固体表面或物料内部由高温区向低温区传递。
二、传热传质计算为了确定化学反应器的传热传质效率,必须进行传热传质计算。
传热传质计算主要包括:汉德公式计算、Nusselt数计算、雷诺数的估算、Prandtl数的评估、基于传输理论的计算和有限元方法。
汉德公式计算是应用于传送实现强迫对流传热传质过程的公式。
Nusselt数计算是一种通用的方法,用于估算传送强迫对流过程的比率。
雷诺数和Prandtl数是流体力学参数,用于描述传导自然对流传热传质。
基于传输理论的计算是一种常用的方法,它基于传输模型对传热传质进行计算。
有限元方法是一种更加复杂的计算方法,可以模拟传热传质过程中材料的变化。
三、传热传质分析在反应器设计中的应用在化学反应器设计中,传热传质分析具有重要意义。
可以通过传热传质分析,优化反应器的设计,提高传热传质效率,减少能源消耗和环境污染。
反应器设计的传热传质分析需要考虑以下因素:反应器的几何形状、操作条件、反应物质的物理属性、反应物质的化学反应机理。
通过对这些因素的分析,可以确定反应器的传热传质模型和优化设计方案。
例如,改善反应器的流体混合效果,增加金属导热管的数量和相应的位置,改变反应器的流动性质,颗粒物相互碰撞的位置和速度等。
第三章制药反应工程基础之搅拌器教材

N—搅拌器层数
对非牛顿流体,由于其黏度随搅拌转速不同
而变化,因此: 先要求出表观黏度与转速之间的关系, 再依次确定NRe 、NP 、P和Pg。
通气将降低对搅拌器轴功率输出的要求,减少程度与通气
量存在一定的关系,为此,引入通气准数Na=QG /nd3 。 若Pg通气 搅拌功率, P0不通气 搅拌功率, 当Na ﹤ 0.035 Pg / P0 =1-12.6 Na 当Na ≥ 0.035 Pg / P0 =0.62-1.85 Na Brown提出Pg / P0 =a exp(- b QG) a ,b 与气体速度和搅拌直径等有关。
多臂行星式
真空乳化釜
新型卧式搅拌
HVR
SCR
(三菱重工)
砂磨机
LIAS-AP
瑞士LIST全相型
BIVOLAK
(住友重机全相型)
CONTERNA
(德国连续 捏和机)
常见搅拌桨及其结构形式
螺轴式搅拌
流体在搅拌容器中流型
在搅拌容器中,流体的流动型式(流型) 可以分为:
层流、转换区(过渡区)、和湍流
Bates算图:涡轮式,对尺寸要求,不考虑Fr的影响,根据Re大小查
Np,按公式P= Np ρn3d5进行计算。
其他算法:
不设挡板的快速搅拌下,对低黏度流体易漏斗状下陷的旋 涡,在液面形成下陷漏斗状程度与NRe,NFr有关,且由于不 能忽略重力的影响,在下列公式
Φ=Np/Fry
中,y=α-lgRe/β ∴搅拌功率计算公式演化为
的区域,同时速度低的流体微元也会带入速度较高的区域。
宏观流动:一般称为流况,包括径向流动和轴向流动,或者说,流体分
聚合反应器的分类介绍全解
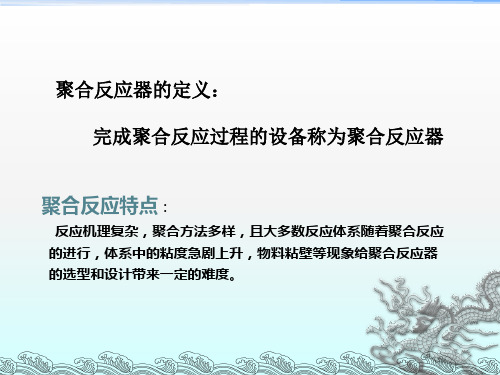
对处理高粘度的聚合体系,如本体聚合或缩聚反应后
期,反应物料的粘度可达500一5000Pa· s,故需采用特殊 型式反应器。该反应器一般采用卧式,主要型式有螺杆型 反应器(如尼龙66的后缩聚反应采用双螺杆)和表面更新型 反应器(如聚酯生产中的后缩聚采用单轴或双轴的表面更 新型圆盘式反应器)。
搅拌釜式反应器
1.管体
是带有夹套的长直圆管,为便于制造安装,常制
成若干段(每段3一5m),各段间用法兰联接。管体顶部可采 用凸形或平板封头,为便于高粘度物料流出,底部多采用锥 形封头。管外装有夹套,内通载热体,管体多采用不锈钢, 夹套可采用普通钢。
管体直径是影响聚合过程的重要因素,在同样聚合温度
和聚合时间下,管径愈小,愈易制取质量均匀、相对粘度较 高的聚合物。这是因为当管径较大时,反应物量增多,引发 剂加入量增多,温度相应增加,低分子物排除困难,并且随
卧式反应器
一、卧式反应器的工作原理 在聚合过程中,有时前后不同阶段物料的特性差异很大, 对反应条件的要求亦不尽相同如聚合前期物料体系粘度低,放 热多,流动较容易,而在聚合后期则往往相反,且希望在反应 进行的同时能去除生成的低分子物,此时在生产中往往采用卧 式反应器。 卧式反应器除需满足一般反应器的要求外,还有以下特殊 要求: 1.物料在反应器内能沿径向充分返混,轴向无返混,尽 量接近平推流。 2.根据聚合动力学理论,为达到预定的聚合度,要尽量 去除体系中生成的小分子,故应在反应器内将反应物料尽可能 展开,形成大面积的薄膜,增加蒸发表面积、且蒸发表面积能 不断更新。
质量,检修时需将釜内物料全部排净。该型式较常用于大型搅拌设备。
3.卧式搅拌反应器
该型式可设臵多个搅拌器,每个搅拌器之间用隔板分开,使物料在反应器 内流动状况类似于多级串联搅拌反应器,从而减少设备台数,降低安装高度。
多相反应器设计中的传质与传热优化

多相反应器设计中的传质与传热优化多相反应器是化学工程领域中常用的设备之一,用于进行液体与气体、液体与固体相之间的反应。
设计一台高效的多相反应器,传质与传热优化是至关重要的环节。
在本文中,将详细探讨在多相反应器设计中,如何进行传质与传热的优化,以提高反应效率和产品质量。
首先,多相反应器中的传质和传热过程是紧密联系的。
传质是指在液体相与固体或气体相之间的物质扩散过程,而传热则是指在反应过程中,热量的传递与转移。
为了实现传质与传热的优化,我们需要从以下几个方面进行考虑和设计。
首先是选择适当的反应器类型。
常见的多相反应器包括搅拌槽反应器、流化床反应器、固定床反应器等。
不同的反应器类型对传质和传热的要求不同,因此在设计过程中需要根据反应物性质、反应条件和反应器尺寸等因素综合考虑,选择合适的反应器类型。
其次是优化反应器的结构和布局。
反应器内部的结构和布局对传质和传热过程有重要影响。
对于液体与气体相之间的反应,可以采用高效搅拌装置来增加相接触的频率和程度,提高传质速率。
对于液体与固体相之间的反应,可以设计合适的固体颗粒床结构,增加反应表面积,提高传质速率。
此外,合理的管道和设备布局,可以减少热量的损失和传质阻力,提高传热效率。
第三点是优化传质和传热介质的选择。
在多相反应器中,常用的传质介质包括溶液、气体和固体颗粒,而传热介质则包括热油、蒸汽等。
选择适当的传质和传热介质可以提高反应速率和效率。
在选择传质介质时,需要考虑溶解度、扩散系数等因素;而在选择传热介质时,需要考虑传热系数、热容等因素。
此外,还可以通过设计合适的传质和传热装置来提高效率。
例如,可以采用填料床或膜分离技术来增加相接触的表面积,提高传质速率;使用换热器来增加热交换的效果,提高传热效率。
在选择和设计传质和传热装置时,需要考虑传质和传热装置的结构、材料和工作条件等因素。
最后,合理控制操作条件也是传质和传热优化的重要环节。
在多相反应器运行过程中,操作条件的控制直接影响到传质和传热的效果。
化学反应中应用催化剂的传热与传质控制方法
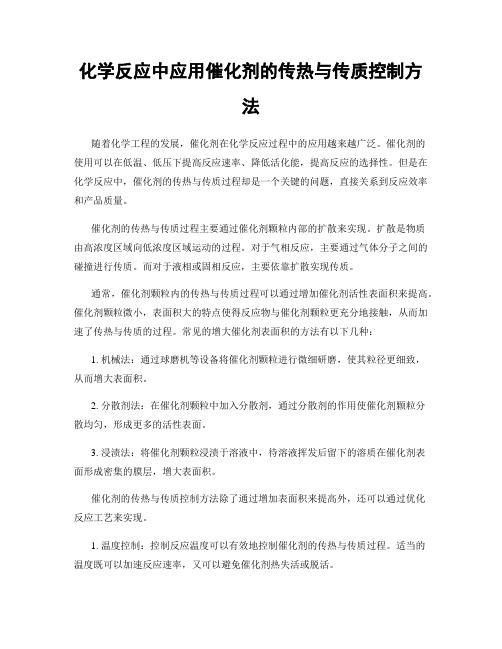
化学反应中应用催化剂的传热与传质控制方法随着化学工程的发展,催化剂在化学反应过程中的应用越来越广泛。
催化剂的使用可以在低温、低压下提高反应速率、降低活化能,提高反应的选择性。
但是在化学反应中,催化剂的传热与传质过程却是一个关键的问题,直接关系到反应效率和产品质量。
催化剂的传热与传质过程主要通过催化剂颗粒内部的扩散来实现。
扩散是物质由高浓度区域向低浓度区域运动的过程。
对于气相反应,主要通过气体分子之间的碰撞进行传质。
而对于液相或固相反应,主要依靠扩散实现传质。
通常,催化剂颗粒内的传热与传质过程可以通过增加催化剂活性表面积来提高。
催化剂颗粒微小,表面积大的特点使得反应物与催化剂颗粒更充分地接触,从而加速了传热与传质的过程。
常见的增大催化剂表面积的方法有以下几种:1. 机械法:通过球磨机等设备将催化剂颗粒进行微细研磨,使其粒径更细致,从而增大表面积。
2. 分散剂法:在催化剂颗粒中加入分散剂,通过分散剂的作用使催化剂颗粒分散均匀,形成更多的活性表面。
3. 浸渍法:将催化剂颗粒浸渍于溶液中,待溶液挥发后留下的溶质在催化剂表面形成密集的膜层,增大表面积。
催化剂的传热与传质控制方法除了通过增加表面积来提高外,还可以通过优化反应工艺来实现。
1. 温度控制:控制反应温度可以有效地控制催化剂的传热与传质过程。
适当的温度既可以加速反应速率,又可以避免催化剂热失活或脱活。
2. 反应物浓度控制:控制反应物浓度可以调节反应物的传质速率和催化剂的饱和度。
过高的浓度可能会导致反应物堵塞了催化剂表面,从而降低反应速率。
3. 混合强化:适当的搅拌或气体拖曳可以加强反应物与催化剂颗粒之间的接触,促进传热和传质过程。
这可以通过设计和选择合适的反应器形式和操作条件来实现。
此外,在实际应用中,还可以通过改进催化剂载体结构和添加促进剂来控制传热和传质过程。
催化剂载体结构的改进主要包括增加孔径和孔隙度,以提高扩散速率。
添加促进剂可以调节催化剂颗粒表面的酸碱性或催化剂表面的吸附活性位点,从而影响传质过程。
聚合反应传热与传质

b. 体外循环冷却器:部分反应物料由反应 器中用泵抽以,经外部冷却器冷却后再进 入反应器。这种液相外循热交换装置应用 于聚合反应时,由于物料在换热器个温度 下降1~10℃左右,所以对要求严格控制反 应温度的一类聚合反应就不宜采用。悬浮 聚合易造成结块也不宜采用。对胶乳的剪 切稳定性高的乳液聚合可以采用体外冷风 但对于剪切敏感的胶乳体系应使用,因为 循环泵里的剪切速率很大,容易破坏胶乳
传热装置有夹套、内冷件、回流冷凝、体 外循环冷却器等。
内冷件:在有衬里的聚合釜或釜壁采用导 热性不良的材质制造时(例如搪瓷釜),因传 热系数低不能仅用夹套传热。大型聚合釜, 由于单位体积的传热面积较小,仅仅采用夹 套传热也是不够的。为此除安装夹套外,还 需附加釜内传热装置。在釜内安装内冷件, 如内冷管和内冷挡板最常使用。
对于有挡板的搅拌釜,釜内不设置内冷蛇 管时:
非均相体系的传热
虽然管路中浆液流动传热的研究已有大量 报道,但对于搅拌牛顿型浆液的报道却很少。 非均相的液—固悬浮体系所形成的浆液,当 固体颗粒体积分率小于1%内,固体颗粒对 于传热影响很小,此时可以应用均相体系的 传热关联式进行传热计算。
聚合釜以夹套冷却时,釜外壁传热膜系数α0 的数值随玲却水的流况而定。如果冷却水 处于自然对流状态时,α0约为500,总传热 系数只能在300~350,当冷却水处于激烈 流动状态时,物可达3000~5000,此时总 传热系数提高到400~600。由此可见,夹 套中冷却水流况且提高传热系数的重要途 径。例如在夹套内按装导流挡板或扰流喷 咀,多点切向进水都是为促使冷却水能处 于激烈流动状态,提高传热膜系数α0所采取
第三节 搅拌聚合釜的传热计算
搅拌聚合釜的传热计算与—般传热计算相 同。传热速率同样取决于釜内流体与载热 休的温度差,传热面积及总传热系数。故 有
- 1、下载文档前请自行甄别文档内容的完整性,平台不提供额外的编辑、内容补充、找答案等附加服务。
- 2、"仅部分预览"的文档,不可在线预览部分如存在完整性等问题,可反馈申请退款(可完整预览的文档不适用该条件!)。
- 3、如文档侵犯您的权益,请联系客服反馈,我们会尽快为您处理(人工客服工作时间:9:00-18:30)。
由于单体在液相中存在浓度差分布,所以随扩散的进行, 聚合反应是在不同的单体浓度下进行的
图8-8 气-液-固体系聚合过程中的单体浓度分布
传质过程与聚合反应先后进行模式(Sequential Mode):
传热方式通常为间接传热,传热装置有夹套、 内冷件、回流冷凝、体外循环冷却器等等。
(1) 夹套传热
图8-2 搅拌聚合釜的 夹套传热装置
图8-3 安装导流挡板的 传热夹套
图8-4 常用夹套
空心夹套
喷咀
螺旋导流板夹套
半管夹套
内部夹套
(2) 内冷件传热
当采用导热性不良的材 料(如搪瓷)制作釜壁 时,传热系数低,仅采 用夹套传热不能充分及 时撤除聚合热,此时应 附加釜内传热装置。
在测定带有相间传质的聚合反应的化学动力学时,必 须排除传质阻力的影响,使实际速率与传递过程特性 无关,即所谓动力学控制。
伴有相间传质的聚合反应的传质计算
研究带有相间传质的聚合反应时,必须尽量提高搅拌 转速,直到转速不再影响实际反应速率为止。但在实 际生产过程中,由于能耗限制或产品质量要求,不能 完全排除传质阻力的存在。
扩散控制:若传质速率远小于聚合反应速率时,实际 反应速率完全取决于传质过程速率,表现为传递过程 特性而与聚合反应动力学无关。
扩散-聚合控制:若聚合速率和传质速率数量级相同, 则二种过程的特性对反应速率的影响都不可忽视。这 种带有相间传质阻力的聚合反应不仅影响实际反应速 率特性,同时还影响聚合产品的分子量及其分布。
若化学过程的速率大于物理的扩散过程,则扩散 过程的速率将对传质的总速率起控制作用。有必 要研究如何提高扩散过程的速率。
理论上增加搅拌强度可以增大传质膜系数,从而 增加传质速率,实践发现当传质面积一定时,搅 拌程度与传质膜系数几乎无关。
伴有相间传质的聚合反应的传质计算
Background 近年来PRE发展较为迅速,由于聚合反应过程的复
杂性给研究工作带来很大的困难,但在应用混合、 搅拌等理论来处理聚合反应过程还是取得很大成 功。 目前已把传质理论(包括吸收和解吸)和聚合反 应理论结合起来进行带有相际扩散的聚合反应的 研究。但相关设备设计和理论计算目前仍以专利 为主。
伴有相间传质的聚合反应的传质计算
伴有相间传质的聚合反应与低分子化学反应类似。以 气-液相聚合为例,在气相单体从气相→相界面→液相 进行聚合反应的过程中,存在传递阻力和化学反应阻 力。因此实际表现出来的反应速率是包括传质过程阻 力在内的综合反应速率,即所谓宏观动力学(MacroKinetics)。
传质阻力主要导致反应物或产物在体系中的浓度差, 尤其是当装置大型化后影响更为显著。
图8-7 气-液体系聚合过程中的单体浓度分布
PA、CAL(CBL)分别为单体(或引发剂)在气相本体和液相本体中的浓度;PAI、 CAI(CBI)分别为界面处单体(或引发剂)的浓度
传质过程与聚合反应同时进行模式(Simultaneous Mode):
除气体单体经气膜、液膜进入到液相本体的传递外,还存在有液 相本体经液-固膜到催化剂表面的传递过程,最后在催化剂表面 进行聚合反应。
气体单体所经的一系列传递过程均在聚合反应前进行,
聚合时的单体浓度是CAS,传质过程与聚合反应是相继串联进行
的。
伴有相间传质的聚合反应的传质计算
依气-液相反应理论,伴有化学反应的传质过程的速 率基本式是二阶偏微分方程:
聚合反应工程
第八章 搅拌聚合反应器的 传质与传热
§8.1 聚合过程的传热问题
Polymerization通常是放热的,Polymers的 分子量及其分布对温度十分敏感,传热是 控制聚合过程的重要问题。
聚合温度恒定的前提是传热速度与放热速 度相等。
放热速率 = 聚合速率 × 单体聚合热。
表8-1 常见Polymer单体的聚合热
系有关。 匀速型:主要通过调整引发剂半衰期,使聚合速率
达到均一,也可通过通过逐渐批次加入单体或催化 剂使聚合速率保持均衡。
1? 2? 3?
图8-1 常见聚合反应转化率-时间曲线
§8.2 搅拌聚合釜的传热方式
要求:传热效率高、结构简单,避免有易引 起挂粘的粗糙表面以及导致结垢的死角、易 于清洗。
釜内内冷件最常用的是 内冷管和内冷挡板。
图8-4 装有传热挡板 的搅拌釜
内冷管
(3) 回流冷凝器(体外循环)传热
图8-5 气相釜外循环热 交换装置
图8-6 液相釜外循环热 交换装置
§8.3 搅拌聚合釜内的传质问题
搅拌釜内分散体系的传质过程包括物理过程(如 气体、固体或液体在液体中的扩散和溶解)和化 学过程。
D:扩散系数,C:反应物浓度,:反应时间,RP:反映速率项
当RP对浓度关系比较简单时,扩散反应方程式可获得解析解、近
似解或数值解。
伴有相间传质的聚合反应的传质计算
三个Hypotheses 聚合反应可视为不可逆过程
体系中活性链浓度不变
当引发剂浓度一定时,聚合反应速率可 简化为拟一级反应
按传质速率和聚合速率的比值不同,对 拟一级反应可分为快速、中速、慢速和 无限慢反应。
ห้องสมุดไป่ตู้
单体名称
状态
聚合温度 聚合热
乙烯 丙烯
丁烯 异丁烯
单体 液态 液态 气态 液态 气态
聚合物 晶态 无定形 晶态 无定形 无定形
(oC) 25 25 25 25 25
(kJ/mol) 108 84 104 83.5 72
异戊二烯 液态 无定形 25
丙烯酸 溶液
液态
20
氯乙烯 气态 无定形 25
液态 无定形 25
(1)快速反应:单位面积内的最大反应速率大于纯传质 速率的2-3倍,此时主要受扩散控制,其传质速率:
苯乙烯 液态 无定形 25
75 77.5 132 111.5 70
聚合反应速率类型
减速型:离子型聚合、缩聚反应,其聚合速率随单 体浓度减低而降低
加速型:自由基聚合在高转化阶段有凝胶效应,出 现自动加速现象,放热速率不均匀,常用放热不均
匀系数(R)表示放热特性:R = Qmax/Qav,Qmax 和Qav分别为最大和平均放热速率。R值与引发剂体