铜及铜合金的焊接性分析
铜及铜合金的焊接

铜及铜合金的焊接铜合金的制造铜合金材料在运用于连接器的加工过程中,先是被加工成为薄片状的板材,然后切成条带形状以适应后面的冲压过程的需要。
线材同样应用于连接器中,但是在端子组件和其他类型的连接器中这样的材料应用得很少。
图4.1描述了一个典型的薄板和条带铜合金的制造流程。
此外在参考书目3中可以得到更详细的描述。
合金线材以同样的方式制造但具有几个显著的特点:热挤压,轧制,和通过冲模的拉拔以改变热轧制和冷轧制在板材中的应用,以及退火处理过程经常用于这种产品。
连接器技术之4.1.1 铜合金的制造溶炼和铸造铜合金是最先用于可回收的商业应用的金属之一,这是因为工业上能用经济的办法将铜合金中的杂质维持在一个较低的水平。
溶炼常用于电溶炉之中而少见于铜合金在真空和惰性气体下的溶炼和铸造过程中。
碳层能提供一足够的保护。
此外,利用真空或特殊的空气环境将会很大的增加合金制造的成本。
氢、氧和碳的污染影响由溶炼过程和热力学方法来平衡其溶炼层进行控制,其中氢能溶解于铜,氧能与铜和一些合金元素形成氧化物,而碳能与有碳化物组分的合金起反应。
溶炼控制包括纯电解阴极铜和有选择的兼容合金碎屑。
当一些纯组分如镍、锡、硅或起支配作用的合金如磷、铍、和铬合金组分增加时,都会引起合金成份改变。
板材锻造的制造过程是从不连续的铸造成大矩形横截面金属锭或薄铸片开始的。
前述大金属锭的典型尺寸为约150 毫米厚,300 到900 毫米宽,并且经过热轧制处理以有效的减少其厚度并消除在铸造过程中残余的铸造微片。
另一种铸造方法是薄铸片(常用于窄条状铸造材料),其典型的尺寸是约15 毫米厚,150 到450 毫米宽,这些薄铸片将直接转到冷轧过程之中。
选择条形铸造是基于经济上的考虑因素(热研磨需要较高的资金成本)以及合金的特性(一些铜合金不容易在热条件下工作)。
前述半连续且大的金属锭在铸造过程中垂直利用一个中空水冷的铜模,在开始时此铜模的下底部被封住。
溶化的金属实际上并未象图4.1中所示的直接进入溶模。
有色金属的焊接(Cu)
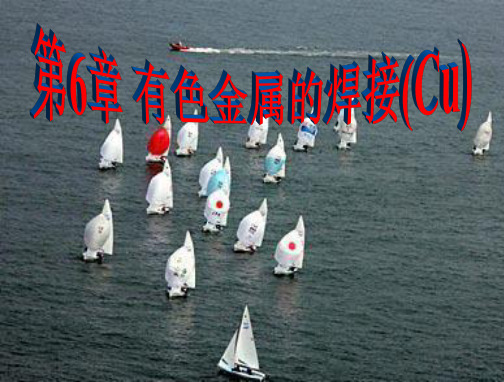
► 1、主要表现:熔化焊过程中,由于晶粒严重长大以及合金元 素蒸发,烧损与杂质的渗入使焊接接头的力学性能、导电性 能和耐蚀性能下降。
► 1)塑性显著降低
► 2)导电性下降
► 3)耐蚀性能下降
► 2、改善措施:主要是控制杂质的含量,减少合金烧损,通过 合金化对焊缝进行变质处理等;其次尽量减少热作用,焊后 进行消除应力处理等。
► 薄铜件焊后要立即对焊缝两侧的热影响区进行锤击。
► 5mm以上的中厚板,需要加热至500~600℃后进行锤 击。锤击后将焊件加热至500~600℃,然后在水中急冷, 可提高接头的塑性和韧性。
► 黄铜应在焊后尽快在500℃左右退火。
12
► 2.埋弧焊 ► 埋弧焊焊接铜及铜合金时,δ<20mm的焊件在不预热和不开坡口的条件
7
► 三、铜及铜合金的焊接工艺要点 ► (一)焊接方法的选择 ► 选用原则,应该根据被焊材料的成分、厚度、结
构特点及使用性能要求综合考虑。 ► 从铜是在常用的焊接金属中导热性最好这一点考
虑,焊接铜及其合金是需要大功率、高能量密度 的焊接方法,热效率越高、能量越集中越好。 ► 不同厚度的材料对各种焊接方法有其适应性。
► ①气焊薄板时应采用左焊法,这有利于抑制晶粒长大。当焊 件厚度大于6mm时,则采用右焊法;
► ②焊炬运动要尽可能的快,每条焊缝不要随意中断焊接过程, 最好单道焊,一次焊完。
► ③焊接长焊缝时,焊前必须留有合适的收缩余量,并要先点 固后焊接,焊接时应采用分段退焊法,以减少变形。
► ④对受力或较重要的铜焊件,必须采取焊后锤击接头和热处 理工艺措施。
热性强,焊缝易生成粗大晶粒。这也会加剧热裂纹的生成。 ► 2、铜及铜合金的焊接可采取哪些措施,防止热裂纹? ► 1)严格限制铜中杂质(氧、铋、铅、硫等)的含量。 ► 2)增强对焊缝的脱氧能力,通过焊丝加入硅、锰、磷等合金
铜及铜合金的焊接介绍

铜及铜合金的焊接介绍1铜及铜合金的分类纯铜是紫红色,俗称紫铜。
在纯铜的基础上加入不同的合金元素,可以成为不同性能的铜合金,常用的铜合金有黄铜、青铜及白铜等。
2铜及铜合金的焊接性铜及铜合金经辗压或拉伸成不同厚度的铜板及铜合金板,不同规格的管子或各种不同形状的材料,都可以用焊接的方法制成各种不同的产品。
铸造的铜及铜合金是通过模型直接浇铸成需要形状的部件或产品,焊接只用于修复或补焊。
在焊接与补焊中易产生下列不良影响:2.1难熔合:铜及铜合金的导热性比钢好的多,铜的导热系数是钢的7倍,大量的热被传导出去,母材难以象钢那样局部熔化,对厚大铜及铜合金材料的焊接应焊前预热,采用功率大,热量集中的焊接方法进行焊接或补焊为宜。
2.2易氧化:铜在常温时不易被氧化。
但随着温度的升高,当超过300℃时,其氧化能力很快增大,当温度接近熔点时,其氧化能力最强,氧化的结果生成氧化亚铜(Cu2O)。
焊缝金属结晶时,氧化亚铜和铜形成低熔点(1064℃)结晶。
分布在铜的晶界上,加上通过焊前预热,并采用功率大,热量集中的焊接方法使被焊工件热影响区很宽,焊缝区域晶粒较粗大,从而大大降低了焊接接头的机械性能,所以铜的焊接接头的性能一般低母材。
2.3易产生气孔:铜导热性好,焊接熔池,比钢凝固速度快,液态熔池中气体上浮的时间短来不及逸出也会形成气孔。
2.4易产生热裂纹:铜及铜合金焊接时在焊缝及熔合区易产生热裂纹。
形成裂纹的主要原因:2.4.1铜及铜合金的线膨胀系数几乎比低碳钢大50%以上,由液态转变到固态时的收缩率也较大,对于刚性大的工件,焊接时会产生较大的内应力。
2.4.2熔池结晶过程中,在晶界易形成低熔点的氧化亚铜—铜的共晶物(Cu+Cu2O)。
2.4.3凝固金属中的过饱和氢向金属的显微缺陷中扩散,或者它们与偏析物(如Cu2O)及应生成的H2O在金属中造成很大的压力。
2.4.4母材中的铋、铝等低熔点杂质在晶界上形成偏析。
2.4.5施焊时,由于合金元素的氧化及蒸发、有害杂质的侵入,焊缝金属及热影响区组织的粗大、加上一些焊接缺陷等问题,使焊接接头的强度、塑性、导电性、耐腐蚀性等往往低于母材所致。
铜及铜合金的焊接
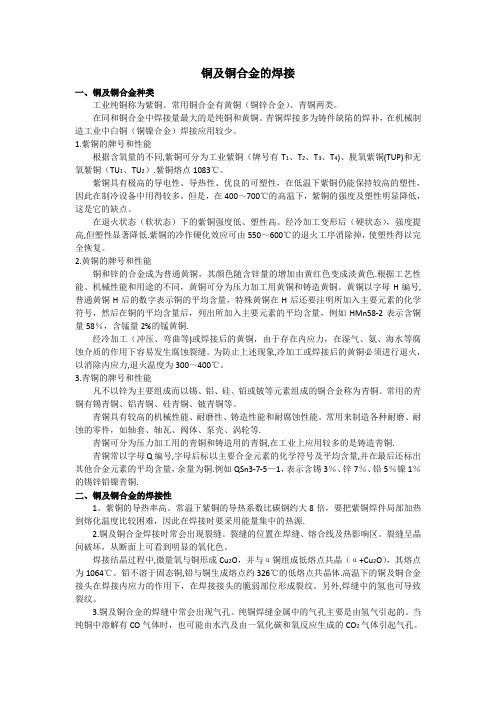
铜237可用于焊接铝青铜,用这种焊条焊材的焊缝中合金元素含量高,可以说是强度、耐磨性及耐腐蚀性最高的一种铜焊条。其焊条的通用性也比较大,主要用于铜合金制的各种化工机械、海水散热器、阀门的焊接,水泵、气缸堆焊及船舶螺旋桨的修补上。
青铜具有较高的机械性能、耐磨性、铸造性能和耐腐蚀性能。常用来制造各种耐磨、耐蚀的零件,如轴套、轴瓦、阀体、泵壳、涡轮等.
青铜可分为压力加工用的青铜和铸造用的青铜,在工业上应用较多的是铸造青铜.
青铜常以字母Q编号,字母后标以主要合金元素的化学符号及平均含量,并在最后还标出其他合金元素的平均含量,余量为铜.例如QSn3-7-5—1,表示含锡3%、锌7%、铅5%镍1%的锡锌铅镍青铜.
二、铜及铜合金的焊接性
1。紫铜的导热率高。常温下紫铜的导热系数比碳钢约大8倍,要把紫铜焊件局部加热到熔化温度比较困难,因此在焊接时要采用能量集中的热源.
2.铜及铜合金焊接时常会出现裂缝。裂缝的位置在焊缝、熔合线及热影响区。裂缝呈晶间破坏,从断面上可看到明显的氧化色。
焊接结晶过程中,微量氧与铜形成Cu2O,并与α铜组成低熔点共晶(α+Cu2O),其熔点为1064℃。铅不溶于固态铜,铅与铜生成熔点约326℃的低熔点共晶体.高温下的铜及铜合金接头在焊接内应力的作用下,在焊接接头的脆弱部位形成裂纹。另外,焊缝中的氢也可 Nhomakorabea致裂纹。
HS202
流动性较一般紫铜好,适用于氧乙炔气焊、亚弧焊紫铜.
HS221
流动性能和机械性能均较好,适用于氧-乙炔气焊黄铜和钎焊铜、铜镍合金、灰铸铁和钢,也用于镶嵌硬质合金刀具。
铜和铜合金的焊接工艺

铜和铜合金的焊接工艺1铜和铜合金的焊接操作纯铜又称紫铜,铜与锌的合金称为黄铜,铜与锡的合金称为青铜,含镍量低于50%的铜镍合金称为白铜,铜内有害杂质的含量对铜的性能影响很大,最危险的物质是铋和铅,铋和铅不熔于铜中而在晶粒周围形成了易熔薄层,此外,硫和氧在铜中形成脆化合物,给热加工和焊接带来困难。
铜及铜合金的焊接工艺差,在焊接时易出现以下问题:难熔合、流动性大、易变形、易氧化、易开裂、易产生气孔等缺陷。
铜及铜合金的焊接方法很多,如气焊、碳弧焊、焊条电弧焊和手工钨极氩弧焊等几种,其中紫铜和黄铜是比较难焊的材料,一般是不采用焊条电弧焊的焊接方法,锡青铜、铝青铜可采用焊条电弧焊,若采用手工钨极氩弧焊,不仅能保证焊缝的质量还能提生产效率。
2.焊条的选择焊条电弧焊焊接铜和铜合金的焊条有紫铜焊条(ECu)锡青铜焊条(EcuSn-B)和铝青铜焊条(EcuA1-C)等,焊条均为碱性低氢性,使用直流电源并反接。
铜及铜合金焊条在焊接时应预热,焊后应进行热处理。
3.焊接措施焊条电弧焊焊接铜和铜合金时,应严格控制氧氢的来源,焊接应仔细清除待焊处的油污,锈垢,采取焊前预热措施得当。
焊件厚不超过4mm 时,可以不开坡口,当焊件厚度为5mm~10mm时,可开单面V形和U形坡口,若采用垫板可获得单面焊双面成形的焊缝,若焊件厚度大于10mm,应双面开坡口,并提高预热温度,焊接时应采用直流反接短弧焊,焊条一般不做横向摆动,在焊接中断或要换焊条,动作要快,焊条的操作角度基本与焊接碳钢相同,较长的焊缝应尽量有较多的定位焊,并且应用分段焊法焊接,以减小焊接应力和变形,多层焊时应彻底消除层间熔渣,避免夹渣的产生,焊接结束后,应采取锤击式热处理的方法,消除焊接应力,由于铜的流动性好,所以应尽量采用平焊的位置进行焊接。
铜及铜合金焊材选用与匹配分析

铜及铜合金焊材选用与匹配分析铜及铜合金焊材的选用与匹配是焊接过程中至关重要的一环。
正确选择合适的焊材可以保证焊接接头的质量和性能,提高焊接工艺的可靠性。
本文将对铜及铜合金焊材的选用与匹配进行分析,帮助读者更好地理解并应用于实际操作。
一、铜及铜合金焊材的种类及特点铜及铜合金焊材主要分为硬焊材和软焊材两大类。
硬焊材通常为铜及其合金,如银基、镍基、铝基、锡基等。
软焊材则主要是铜磷焊丝和铜锡焊丝。
硬焊材具有高强度、高硬度、高耐热性和耐腐蚀性等特点,适用于焊接较大的工件和要求较高的工艺。
而软焊材则具有低熔点、良好的流动性和润湿性,适用于焊接较小的零件和对焊接温度和热影响较为敏感的工艺。
二、铜及铜合金焊材的选用原则1. 材料的选用要根据焊接的具体要求来确定。
例如,焊接紧固件时,要保证焊接点和基材的强度一致,选用强度相似的硬焊材;而对于精细焊接,选用软焊材可以降低热影响。
2. 材料的选用应考虑到焊接材料的熔点和熔化性能。
焊接材料的熔点应低于工件的熔点,而熔化性能要与工件相匹配,以确保焊接过程中能够充分润湿和扩散。
3. 材料的选用还要考虑到焊接材料的成本和可获得性。
根据具体情况选择性价比较高的焊接材料,确保在满足性能要求的前提下尽量节约成本。
三、铜及铜合金焊材的匹配原则1. 同种或相似材料的焊接,宜采用相同或相近的焊材。
例如,焊接紫铜件时,采用硬焊紫铜焊材;焊接黄铜件时,采用硬焊黄铜焊材。
2. 不同种类或相异材料的焊接,宜采用中间合金来进行匹配。
中间合金的选用要满足与两种材料的熔点相近、润湿性好、扩散性好等要求。
3. 在焊接不同金属之间时,还可以采用双金属焊材。
双金属焊材可以通过在不同金属的接合位置上形成一层新的金属层,从而实现焊接。
四、铜及铜合金焊材的应用案例1. 铜管的焊接:选用硬焊铜焊材,如铜锌焊材或铜锡焊材,采用熔化性能相近的焊接方法。
先进行外浸焊,再进行内浸焊,以确保焊接质量和工艺可控性。
2. 黄铜五金件的焊接:选用硬焊黄铜焊材,如铜锌焊材。
铜及铜合金的焊接特点

铜及铜合金的焊接性分析1.难熔合及易变形焊接纯铜及铜合金时,如果采用的焊接参数与焊接低碳钢差不多,母材散热太快,填充金属与母材不能很好地熔合,焊后变形也较严重,这与铜的热导率、线胀系数和收缩率有关。
铜的热导率大,20摄氏度时铜的热导率比铁大7倍多,1000摄氏度时大11倍多,焊接时热量迅速从加热区传导出去,焊接区难以达到熔化温度,使母材与填充金属很难熔合。
铜在熔化温度时的表面张力比铁小1/3,而流动性比铁大1~1.5倍,表面成形能力差。
铜的线胀系数大15%,凝固时的收缩率比铁大1倍以上,再加上铜的导热能力强,使焊接热影响区加宽,焊接时如被焊工件刚度低,又无防止变形的措施,很容易产生较大变形。
因此,焊接时必须采用功率大、热量集中的热源,并采取预热措施,不允许采用悬空单面焊接,单面焊时,反面必须加垫板或成形装置。
2.易产生热裂纹为了防止热裂纹的产生,焊接铜及铜合金时可采取以下一些治金措施。
(1)必须严格限制焊件和焊接材料的氧、铅、铋、硫等有害元素的含量。
(2)通过焊丝加入硅、锰、碳、磷等合金元素增强对焊缝的脱氧能力。
(3)选用能获得双相组织的焊丝,使焊缝晶粒细化、晶界增长,使易熔共晶分散,不连续。
(4)焊接时加强对熔池的保护,采用减小焊接应力的工艺措施,如选用热量集中的热源、焊前预热、选择合理的焊接顺序、焊后缓冷等。
3.易产生气孔气孔是铜及铜合金焊接时一个主要问题,只要在氩气中加入筒量的氢和水蒸气,焊缝即出现气孔,产生气孔的倾向比碳钢严重得多,原因如下:(1)铜的热导率比低碳钢高7倍以上,所以铜焊缝结晶很快,熔池易为氢所饱和而形成气泡,在凝固结晶很快的情况下,气泡不易析出,促使焊缝中形成气孔。
(2)氢在铜中的溶解度随温度升高而增大,直到熔点时氢在铜中的溶解度达最高值,温度再提高,液态铜开始蒸发,氢的溶解度下降。
(3)氩弧焊时氮也是形成气孔的原因,随着氩气中氮含量的增加,气孔数量随之上升。
铜及铜合金焊接时防止产生气孔的主要措施有:(1)防止焊缝金属吸收氢气及氧化,焊件表面在焊前应去油污、水分等,焊条、焊剂要烘干使用,焊丝表面不得有水分。
铜及铜合金具有难熔合及易变形性
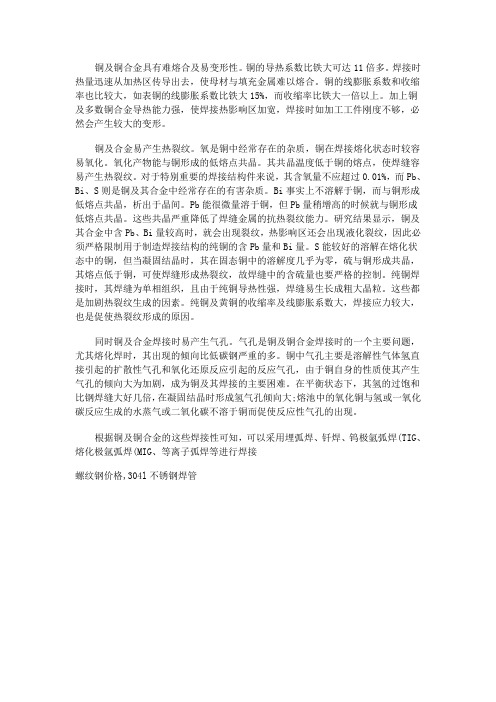
铜及铜合金具有难熔合及易变形性。
铜的导热系数比铁大可达11倍多。
焊接时热量迅速从加热区传导出去,使母材与填充金属难以熔合。
铜的线膨胀系数和收缩率也比较大,如表铜的线膨胀系数比铁大15%,而收缩率比铁大一倍以上。
加上铜及多数铜合金导热能力强,使焊接热影响区加宽,焊接时如加工工件刚度不够,必然会产生较大的变形。
铜及合金易产生热裂纹。
氧是铜中经常存在的杂质,铜在焊接熔化状态时较容易氧化。
氧化产物能与铜形成的低熔点共晶。
其共晶温度低于铜的熔点,使焊缝容易产生热裂纹。
对于特别重要的焊接结构件来说,其含氧量不应超过0.01%,而Pb、Bi、S则是铜及其合金中经常存在的有害杂质。
Bi事实上不溶解于铜,而与铜形成低熔点共晶,析出于晶间。
Pb能很微量溶于铜,但Pb量稍增高的时候就与铜形成低熔点共晶。
这些共晶严重降低了焊缝金属的抗热裂纹能力。
研究结果显示,铜及其合金中含Pb、Bi量较高时,就会出现裂纹,热影响区还会出现液化裂纹,因此必须严格限制用于制造焊接结构的纯铜的含Pb量和Bi量。
S能较好的溶解在熔化状态中的铜,但当凝固结晶时,其在固态铜中的溶解度几乎为零,硫与铜形成共晶,其熔点低于铜,可使焊缝形成热裂纹,故焊缝中的含硫量也要严格的控制。
纯铜焊接时,其焊缝为单相组织,且由于纯铜导热性强,焊缝易生长成粗大晶粒。
这些都是加剧热裂纹生成的因素。
纯铜及黄铜的收缩率及线膨胀系数大,焊接应力较大,也是促使热裂纹形成的原因。
同时铜及合金焊接时易产生气孔。
气孔是铜及铜合金焊接时的一个主要问题,尤其熔化焊时,其出现的倾向比低碳钢严重的多。
铜中气孔主要是溶解性气体氢直接引起的扩散性气孔和氧化还原反应引起的反应气孔,由于铜自身的性质使其产生气孔的倾向大为加剧,成为铜及其焊接的主要困难。
在平衡状态下,其氢的过饱和比钢焊缝大好几倍,在凝固结晶时形成氢气孔倾向大;熔池中的氧化铜与氢或一氧化碳反应生成的水蒸气或二氧化碳不溶于铜而促使反应性气孔的出现。
- 1、下载文档前请自行甄别文档内容的完整性,平台不提供额外的编辑、内容补充、找答案等附加服务。
- 2、"仅部分预览"的文档,不可在线预览部分如存在完整性等问题,可反馈申请退款(可完整预览的文档不适用该条件!)。
- 3、如文档侵犯您的权益,请联系客服反馈,我们会尽快为您处理(人工客服工作时间:9:00-18:30)。
铜及铜合金的焊接性分析
高导电用普通纯铜是铜的质量分数不低于99.7%,杂质含量极少。
工业最常用的牌号是T1、T2和T3,外观呈紫红色,故又称为紫铜。
其再结晶温度为200~280℃。
T1和T2是阴极重熔铜,含微量氧和杂质,具有高的导电、导热性,良好的耐腐蚀性和加工性能,可以熔焊和钎焊。
主要用作导电、导热和耐腐蚀元器件,如电线、电缆、导电螺钉、壳体和各种导管等,航空工业多使用T2。
T3是火法精炼铜,含氧和杂质较多,具有较好的导电、导热、耐腐蚀性和加工性能,可以熔焊和钎焊。
主要作为结构材料使用,如制作电器开关、垫圈、铆钉、管嘴和各种导管等;也用于不太重要的导电元件。
(1)焊接缺陷
1)未熔合与未焊透
铜导热性良好,焊接时易产生未熔合和未焊透。
因此,焊接铜时应采用能量集中,相对功率较大的热源。
2)焊接变形
铜及铜合金的线膨胀系数(确定铜的线膨胀系数)大,液态凝固时的收缩率比铁大一倍以上,再加上铜的导热性能良好,使得焊接热影响区加宽,在工件厚度较薄或结构刚度较小,又无防止变形的措施时,工件焊后很容易产生较大的变形。
(激光焊接时变形量的测量)当焊接接头受到较大的刚性约束时易产生焊接应力。
3)热裂纹
铜在液态时很容易被氧化生成氧化亚铜Cu
2O。
Cu
2
O与Cu可生成熔点为
1060℃的共晶,与Pb生成熔点为326℃的Cu+Pb共晶,与Bi生成熔点为270℃的共晶,与CuS生成熔点为1067℃共晶,这些共晶的熔点均低于紫铜1083℃的熔点。
在结晶过程中,由于低熔点共晶体分布在枝晶间或晶界处,使铜和铜合金具有明显的热脆性,加上焊接应力的作用,极易产生热裂纹。
工业纯铜中常见的杂质元素有氧、硫、铅、铋、砷、磷等,其中氧的危害性最大。
他们主要来自原材料及轧制和焊接的加工过程。
其中铅和铋基本上不溶于铜,其含量应分别控制在0.03%和0.005%以内,Cu2O可溶于液态铜,但不溶于固态铜,故重要的结构含氧量应小于0.01%,焊接结构用紫铜含氧量应小
于0.03%,S小于0.0015%。
4)气孔
气孔是铜及铜合金焊接时常见的缺陷,紫铜焊缝中的气孔主要是氢气孔。
氢气孔的形成与氢在铜中的溶解度随温度下降突变有关。
另一种气孔是由冶金反应生成的水蒸气和二氧化碳等,在焊接凝固时来不及逸出形成的。
5)焊接接头的塑性、导电性、耐蚀性
焊缝及热影响区受热循环后晶粒变粗,各种脆性的低熔点共晶出现在晶界,使塑性和韧性显著下降。
为脱氧加入的锰、硅等元素,以及焊接过程中溶入的杂质和合金元素,都会不同程度的降低铜接头的导电性能。
耐蚀性能的下降主要是有益元素如锌、镍、铝等的蒸发和烧损造成的。
焊接铜及铜合金时,尽量采用加热面积小、能量密度大、功率大的焊接方法。
对于薄板来讲,最好采用钨极氩弧焊(原因),与激光焊接相比的可行性分析。