微张力减径机轧后钢管产生青线的原因分析
钢管的缺陷与预防
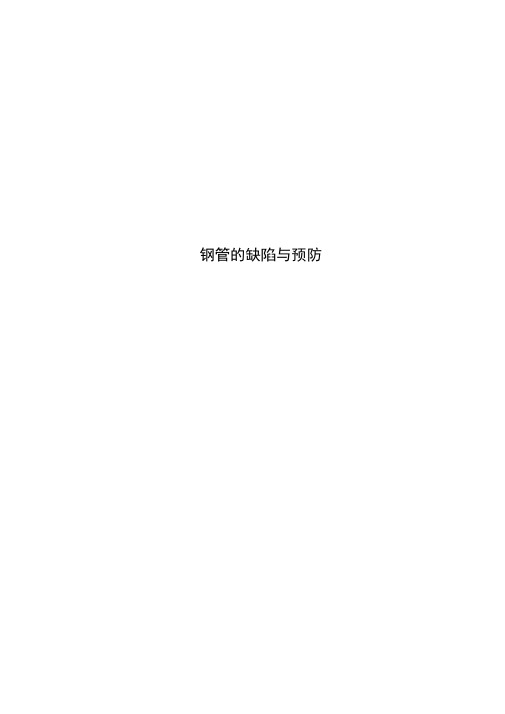
(1)钢管运送时防止碰伤,保持料架和斜篦条等存放处的光洁。
(2)清除管端的毛刺。
(3)正确调整矫直机,消除矫直过程中擦伤隐患
(4)改进吊具,防止钢绳直接吊勒管体。
检查判断
用肉眼检查,擦伤边缘比较圆滑,深宽比较小者,允许存在。缺陷边缘有尖锐 棱角或深宽比较大者,应予修磨,修磨后不超出直径和壁厚的负偏差者判为合 格。
(9)中间退火不均,变形量不足
预防消除方法
(1)提咼拔管模具的表面质量。
(2)氧化铁皮要冲洗干净,涂层要均匀、牢固。
(3)锤头过渡部分要圆滑无棱角。
(4)勤检查模具和钢管表面,发现问题及时处理。
检查判断
用肉眼检查。一般结构管和用于加工机械零件的钢管,当缺陷深度不超过壁厚 负偏差时允许存在。用于压力管道以及类似用途的钢管,按相应的技术标准判 断。
(3)管料局部壁薄(如修磨点)
预防消除方法
(1)无顶头拔制薄壁管时,要合理分配减径量。
(2)锤头端部应无棱角和折皱。
(3)对管料表面的局部缺陷,清理的深宽比要合格。
检查判断
用肉眼检查。拔凹是不允许存在的缺陷, 不能修磨,局部者切除,整根者报废。
8•
缺陷名称
空拔
缺陷特征
有顶头拔制时,因没给上顶头,产生壁厚超正差,外径稍小,内表面有环形台 阶的缺陷称空拔。多产生在锤头端部
(2)热处理保温时间不够或加热温度不足,在钢管横断面上,加工应力未能 充分消除而引起横裂。
(3)拔管时压下量过大,超过金属的抗拉强度。
(4)加热厚壁钢管的速度太快,产生热应力过大。
(5)空拔厚壁管造成内外壁延伸率不一致。
(6)厚壁管在加热状态下受到急冷(特别是在冬季)产生横裂。
张减机工艺

轧制力
140kN(最大)
入口速度
0.5~1.4m/s
出口速度
0.51~7m/s(最大)
2.1 定径前的除鳞设备
高压水压力: 25Mpa
喷水环类型:
a
5
3 传动设备
电机数 6
主电机I (1~8架) 名义输出功率90/900——900KW
最大输入功率162/1620——1620KW
输出速度80/800——2000 n/m
叠加电机(1~8架) 名义输出功率25/250——250KW
最大输入功率45/450——450KW
输出速度80/800——1600 n/m
主电机II (9~14架) 名义输出功率90/900——900KW
最大输入功率162/1620——1620KW
输出速度80/800——2000 n/m
叠加电机II(9~14架) 名义输出功率25/250——250KW
最大输入功率45/450——450KW
输出速度80/800——1600n/m
主电机Ⅲ(15~24架) 名义输出功率90/900——900KW
最大输入功率162/1620——1620KW
输出速度80/800——2000 n/m
叠加电机Ⅲ(15~24架) 名义输出功率63/630——630KW
最大输入功率113.4/1134——1134KW
入口辊道
除鳞箱
入口导嘴
24机架张减
出口导嘴
预留热飞锯
测量装 置
a
4
1 产品特性
入口荒管外径(热态) 175mm(132mm)
入口荒管壁厚(热态) 4.2~22.1mm(3.3~18.2mm)
入口荒管长度
10.2m~27.5m
钢管青线的总结报告
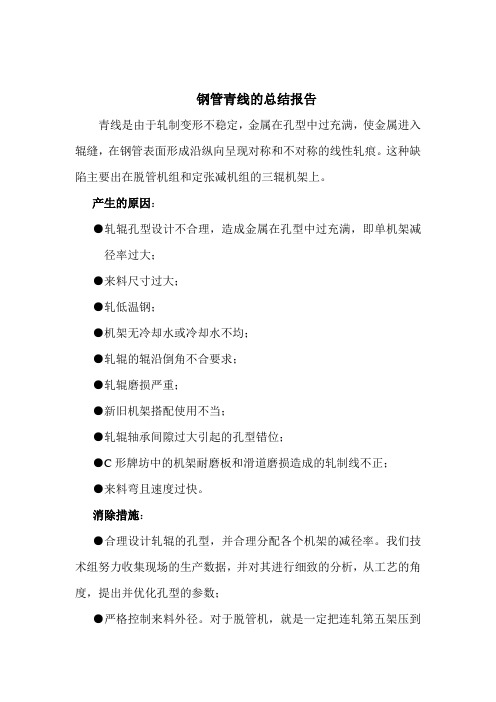
钢管青线的总结报告青线是由于轧制变形不稳定,金属在孔型中过充满,使金属进入辊缝,在钢管表面形成沿纵向呈现对称和不对称的线性轧痕。
这种缺陷主要出在脱管机组和定张减机组的三辊机架上。
产生的原因:●轧辊孔型设计不合理,造成金属在孔型中过充满,即单机架减径率过大;●来料尺寸过大;●轧低温钢;●机架无冷却水或冷却水不均;●轧辊的辊沿倒角不合要求;●轧辊磨损严重;●新旧机架搭配使用不当;●轧辊轴承间隙过大引起的孔型错位;●C形牌坊中的机架耐磨板和滑道磨损造成的轧制线不正;●来料弯且速度过快。
消除措施:●合理设计轧辊的孔型,并合理分配各个机架的减径率。
我们技术组努力收集现场的生产数据,并对其进行细致的分析,从工艺的角度,提出并优化孔型的参数;●严格控制来料外径。
对于脱管机,就是一定把连轧第五架压到位;对于定张减,就是控制好从脱管机出来的荒管的外径,做好脱管机轧制支数的跟踪统计,达到寿命及时更换脱管,若有中间掉队料,及时测量荒管的外径,保证其外径符合工艺要求。
●热轧车间最忌的就是轧制低温钢,后果很严重的。
低温钢变形抗力变大很容易把三辊机架的辊缝撑开,从而产生青线。
穿孔机组一定要控制好开轧温度,以实现生产的顺利进行。
长时间停料后复产的时候,要用测温仪实测坯料温度,对于不符合工艺温度要求的坚决剔掉。
定张减机组要不定时的对来料温度进行测量,操作员要跟踪每一根钢管轧制时电机的电流,发现异常,马上测量来料温度。
●机架没有冷却水或者冷却水不均很容易造成轧辊轴承的研死,形成单点的轧制力过大,进而把辊缝撑开。
现在我们技术组都已经把各个机组冷却水列入点巡检的范畴,并对其进行严格的考核。
再有我们技术组认真检查每一架上线机架的水嘴位置和快速接手,并随时到现场检查冷却水。
●轧辊辊沿倒角太小或者三个辊辊沿倒角大小不一致,都能造成青线。
我们技术组已经和工具提出加大倒角以及均匀倒角的要求,但是工具的倒角现在没有严格的数据来控制只能靠操作工的手感。
MPM连轧管机轧制力曲线异常原因分析及调整

的压力趋势以及限动芯棒电流、速度 、功率 、限动
力 的趋 势等 。
1 正常轧制时 的轧制 力曲线
正常轧制时的轧制力曲线如 图 1 所示 。
从 图 1 以看 出 .轧制 力在 毛管 开始 咬人 时 波 可
压头是利用磁性材料在机械力作用下导磁率发生变 化 的原理 工作 的。这些 测 压头通 过 接线 箱 与控 制单 元 MC 0 R相连 。控制单元给测压头供 电 .从测 40 压 头接收测量信号并且将测量值传 输给外部单元
征及其产生原 因,提出 了相应的预防及调整措施 ,对 已经 出现的故障给出了解决方案 ,为生产 的顺利进行创造 了 条件 。 关键词 :MP M连轧管机组 ;轧制力 曲线 ;异常 ;原因分析 ;调整
中图 分 类 号 :T 3 57 文 献 标 志 码 :B 文 章编 号 : 1 0 — 3 1 2 1 )3 0 1 — 5 G 3 .1 0 1 2 1 (0 10 — 0 7 0
Z a gJn h n i,WuQ a g in ,Ha in i ,Z a oa g nJa xn h oB g n ( ini ie ( o p op rt n t. ini 0 3 1 hn Ta j Pp Gru )C roai ,Ld,Ta j 3 0 0 ,C ia) n o n
pe e tt ea t n n du t n aue r rp sd n h ouinfr h xsigfut aew re rv nai ci sa da jsme t v o me srsaepo o e ,a d teslt o eeit a l r ok d o t n s
热轧(微)张力减径钢管的主要缺陷和消除方法

热轧(微)张力减径钢管的主要缺陷和消除方法
- 热轧(微)张力减径钢管的主要缺陷及消除方法
1、缺点:表面缺陷(毛发状缺陷、裂纹、气孔)
消除方法:提高表面洁净度,加强质量检验,严格控制张力差、减
径钢管精度及表面质量;定期作业前对减径钢管进行卷筒表面填充磨光,减少毛发样缺陷,并且要充分控制卷筒表面填充过程中的处理温度、进料收缩率及剩余应力等。
2、缺点:表面弯角不均匀以及错位等
消除方法:应采用实心轴或带有凹槽的轴,并要有足够的轴面硬度,以防止表面错位;减径钢管的低减径层使用放大器,以减少弯角不均
匀情况,还需要弯曲过程定期维护润滑,增强设备操作稳定性。
3、缺点:减径钢管叞边区减径精度较差
消除方法:提高减径工艺技术,提高减径钢管质量,如拉伸减径阶段,应采用刚性夹头、均匀减径以及调整减径速度等;同时,要及时
对减径钢管进行彻底维护,它才能确保拉伸减径的精度。
4、缺点:减径钢管的精度较差
消除方法:在减径钢管的生产过程中,应配备严格的检测,如采用液压系统定时监测拉伸减径的精度;同时进行原料批次检测,以保持安全性。
同时,要加强钢管表面处理,打磨质量,防止表面老化,提高减径钢管的使用性能和精度。
微张力定(减)径机轧辊机架的装配与调整
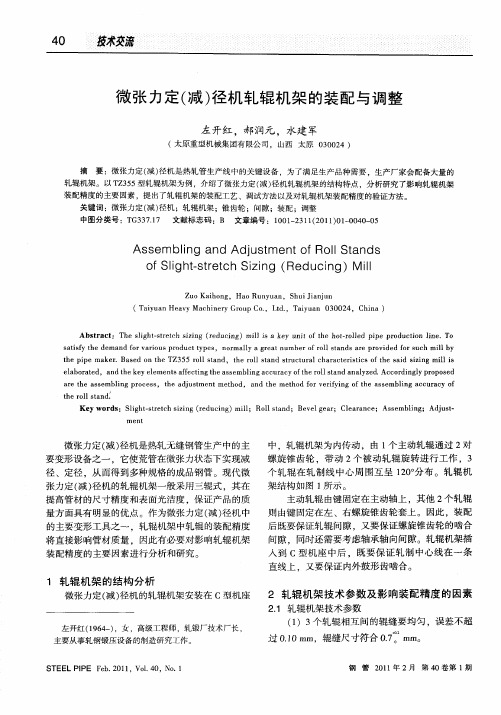
aeteasmbigp o es h du t n eh d n h to r ei igo easm l ga c rc f r h se l rc s,tea jsme t to ,a dtemeh df r yn f h se bi cua yo n m ov f t n
m ent
微 张力定 ( ) 减 径机 是热 轧无 缝钢 管生 产 中的主
中 .轧 辊机 架为 内传 动 ,由 1 主动 轧辊通 过 2对 个
要 变形 设备 之一 ,它使 荒 管在微 张力 状态 下实 现减 径 、定 径 ,从而 得到 多种 规格 的成 品钢管 。现 代微
张力定 ( ) 减 径机 的轧 辊机 架一般 采用 三辊 式 ,其在
s if he de a o ro r duc ype ats y t m nd f rva i us p o tt s, no m al e r ly a gr atnumbero o lsan r o i d f rs h m ilby fr l t ds a e pr v de o uc l t i he p pe make .Ba e he TZ3 o lsa r s d on t 55 r l t nd, t o ls a t u u a har c ersi ft ai szng mili he r l t nd sr ct r lc a t i tcso he s d i i l s
1 轧 辊 机 架 的结 构 分 析
微 张力定 ( ) 减 径机 的轧 辊机 架安装 在 C型机 座
2 轧辊机架技术参数及影响装配精度 的因素
21 轧辊机 架技 术参 数 .
( )3个 轧辊 相 互 间 的辊 缝 要均 匀 ,误 差不 超 1
张力减径机理论资料

计算管端增厚的方法很多,我认为德国 Meer 厂和考克斯公司的的方法是较为
实用的计算方法。
德国 Meer 厂计算方法介绍如下。
1》 已 知
机 架 间 距 (m): A
毛管 外 径(mm):D0、毛管壁厚(mm):S0;
钢管 外 径(mm):D 、钢管壁厚(mm):S
2》 计 算
1) 延 伸 系 数
µ= S0*(D0- S0)/[ S*(D- S)]
3
△ D= (D0- D)/D0 Zm— — 所 有 机 架 中 钢 管 总 的 平 均 张 力 系 数
3、 减 径 的 几 个 工 艺 问 题
3、1 管端增厚
1) 产生管端增厚的机理和特征
在 钢 管 头 部 出 了 第 一 机 架 但 还 没 有 进 入 第 二 机 架 时 ,这 一 段 钢 管 就 没 有 张 力 的
2) 毛 管 壁 厚 系 数
ν 0= S0/D0
3) 钢 管 壁 厚 系 数
ν = S/D
4) 平 均 壁 厚 系 数
ν m=[(ν0+ν)/2+(S0+S)/(D0+D)]/2
4
5) 减 径 率
ρ = 1- D/D0
6) 轴 向 对 数 变 形
Φ e= LN(µ)
7) 切 向 对 数 变 形
Φ t= LN((D- S)/(D0- S0))
δ i= 1- (1- ρ i)ε ε = [2Zi(ν i-1- 1)+ (1- ν i-1)]/[Zi(1- ν i-1)- (2- ν i-1)] δ i— — 第 机 架 中 钢 管 的 相 对 减 壁 量
δ i= (Si-1- Si)/Si-1 ρ i— — 第 机 架 中 钢 管 的 相 对 减 径 量
张力减径的工艺原理及主要问题

包头钢铁职业技术学院学生毕业论文论文题目:张力减径的工艺原理及主要问题专业:冶金班级:冶金一班学生:李咏光指导教师:魏宁日期: 2010年3月31日目录摘要 (1)关键词 (1)引言 (1)1 张力减径机技术的发展 (1)2 张力减径机的作用 (1)2.1张力减径机的形式 (2)3 钢管定径、减径的工艺原理 (3)3.1 张力减径的优点、缺点 (3)3.2三辊定径、减径机减径与二辊定径减径机相比 (4)3.3张力径机的孔型 (5)3.4张力减径机与微张力减径机的不同 (8)3.5 管材热扩径方法 (8)4张力减径时管端偏厚的原因 (10)4.1影响张力减径机管端增厚的因素 (10)4.2影响管内多边形的因素 (11)结语 (11)参考文献 (12)张力减径机的工艺原理及主要问题摘要:简介了三辊定径机定径和减径的作用及形式,提出了定减径机工作时常出现的问题,进行了三辊定减径机和两辊定减径机的比较。
关键词:定减径机;壁厚;斜轧;张力引言:在无缝钢管生产的三大机组——穿孔机组、轧管机组、定减径机组中,人们一直十分关注轧管机的研究,先后开发出自动轧管机组、顶管机组、新型顶管机组(CPE)、三辊轧管机组、连轧管机组(包括浮动芯棒MM、限动芯棒MPM和半浮动芯棒连轧管机组等)、AccuRoll轧管机组、改进型三辊轧管机组。
但对于穿孔机组,仅在20世纪80年代初才提出菌式穿孔机。
而定减径机一直使用二辊式和三辊式,直到20世纪90年代初才提出三辊可调式定径机技术。
新型三辊可调式定径机技术是为满足现代钢管生产高效、优质、低耗的要求而开发的,它的开发成功也为无缝钢管的生产注入新的活力。
1张力减径机技术的发展张减工艺主要特点是边连续多机架二辊或三辊无芯棒纵轧,采用适当的孔型系使毛管外径减缩,通过机架系列中轧辊速比的调节获得预定的壁厚变化。
20世纪40年代无缝管机组被美国和西欧所用,这时的张减机都是二辊式,到了20世纪50年代,西德曼乃斯曼公司成功地奕用了三辊式张力减径机,从而代替了二辊式。
架微张力减径机技术操作规程
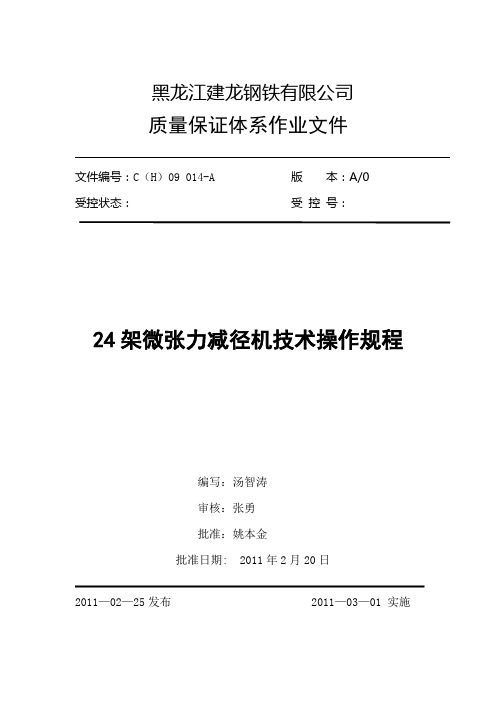
黑龙江建龙钢铁有限公司质量保证体系作业文件文件编号:C(H)09 014-A版本:A/0受控状态:受控号:24架微张力减径机技术操作规程编写:汤智涛审核:张勇批准:姚本金批准日期: 2011年2月20日2011—02—25发布 2011—03—01 实施第一章张减机工艺描述及安全检查一、区域概述及功能描述张减机本体属于热轧区域最后一道工序,分为前辊道、本体及后辊道,其中,前辊道上主要包括高压除磷水,其主要用于去除荒管外表面的氧化铁皮和控制荒管温度;本体属于空心轧制工艺,主要用于改变荒管外径尺寸,在改变外径的前提下,改变壁厚尺寸;后辊道包括升降辊道和取样锯,其中,升降辊道主要用于在轧制不同外径的钢管时,通过调整其高度来更好的输送钢管。
二、安全检查(1)安全注意事项1 交接班时,检查主操作台上相关操作开关是否置于零位,区域生产方式是否置于手动位。
2 检查所有转动部件上有无杂物,若有须清理彻底。
3 在相关区域进行工具检查和设备维护时,先检查该区域操作台各开关是否置于零位,动力电源是否已经切断,否则不能维护。
4 在对转动杆件(如传动轴)进行点动操作前,先检查杆件上有无缠绕物、有无人员在危险位置。
5 完成设备或变形工具的检查维护工作后,将相关工具(如扳手、钳子等)带到指定的地方安全摆放,并将现场的油污和杂物按规定进行收集处理,不得将污染物随意排放到地沟。
6 当控制电源合闸后,禁止任何人进入危险区域。
7 开机前,操作人员首先要进行视觉检查,确认设备以及其它的安全设施是否完好。
检查机器运转区域范围内(如:辊道上、横移链上以及其动作区域内)有无人员停留,并启动开机警报装置。
8 在“自动操作”或“手动操作”模式下,操作人员要密切监控设备运转情况;若无操作人员监控,严禁设备运行。
9 在自动操作模式过程中,任何人不允许在危险区域经过或逗留。
10 设备的检修和维护以及排除故障时,必须在设备停机并静止后进行;且未经允许的人员不得参与机械的处理工作。
钢管轧制存在质量问题的原因及改进措施

一穿轧制存在的质量问题1、毛管外径偏大或偏小原因:①辊距偏大或偏小②导板板距偏大或偏小③顶头位置向前或靠后④顶头直径偏大或偏小⑤轧辊径向串动量太大⑥上导板座没有固定,上下跳动量大改进措施:根据轧制表的参数选择合适的辊距,导板距,顶头伸入量及顶头直径,加强轧辊和导板的固定,正常轧制时,辊距和导板距保证相对稳定,不能轻易调整,若钢管偏厚或偏薄,可采取进、退顶杆的方法。
2、壁厚严重不均原因:①一穿三个轧辊的外径大小不一②三个轧辊偏离轧制线③三个轧辊调整后不成等边三角形,轧辊前后距轧机牌坊距离不一致;④定心辊未抱住顶杆甩动严重⑤定心孔不对中⑥穿孔机受料槽、一穿轧机、定心机架、顶杆小车的机械中心线不对⑦轧辊轧制过程中跳动太大;⑧顶杆位置过后;⑨轧辊直径过小,轧制大规格钢管时产生滑动现象;改进措施:①安装轧辊时先要测量三个轧辊的辊径,保持三个轧辊的辊径一致;②调整轧制中心线,俣证轧制中心线与穿孔中心线重合,然后可使轧制中心线略低于穿孔中心线0-5mm;③将三个轧辊调整后成等边三角形,保证三个轧辊在轧制过程中受力一致,轧辊前后距牌坊距离一致;④调整定心辊,保证在空载时能抱住顶杆,并使顶杆的水平线与穿孔中心线重合;⑤保证定心孔对中;⑥要求设备测试中心线,保证穿孔机受料槽、一穿轧机、定心机架、顶杆小车的机械中心线在一条水平直线上;⑦临时用铁片调整间隙,保证跳动值不超标。
⑧调整到合适的顶杆位置;⑨更换轧辊,选择合适辊径的轧辊,当辊径小于一定值,予以报废。
3、头尾外径不一致(头大尾小)原因:①坯料加热温度不均匀,头部温度偏低;②穿孔过程中轧辊在辊箱中抖动③穿孔中误动作侧压进装置④管坯开始变形时顶头的轴向阻力加大,轴向延伸受阻,延伸变形减小,横向变形(扩径)加大⑤管坯尾部顶透时轴向阻力减小,使延伸变形容易,同时横向辗轧减小,因而尾部直径变小改进措施:按加热制度加热,保证钢温一致;采取措施固定轧辊,使轧辊在辊箱中不串动;提高操作水平,减少误动作,加强调整,保证轴向变形与横向变形同步。
定径机轧管内六方缺陷的控制

定径机轧管内六方缺陷的控制定径机轧管内六方缺陷的控制摘要介绍了用增加轧制道次减少各机架的减径率控制厚壁管和合金中厚壁管内六方产生达到提高一极品率和金属收得率。
关键词内六方孔型减径率椭圆度 1 前言三辊定径机是Φ180限动芯棒连轧管机组热轧生产线金属热变形的最终一道工序是连轧管机组中的精轧机组。
定径机实际上是一种空心轧制的多机架连轧其任务是在较小的总减径率和较小的单机架减径率条件下将荒管轧成符合要求尺寸精度的成品管。
我厂Φ180限动芯棒连轧管机组于1999年投产试生产以来定径机轧制的热轧钢管由于受热工具工艺和操作水平等方面的影响各类缺陷的产生在所难免而内六方是其中的主要缺陷之一。
热轧管出现内六方缺陷后轻者影响成品管的外观重者因壁厚精度超差而改判甚至报废。
因此控制和减少内六方缺陷尤为重要。
本文结合现场生产实际在现场试验的基础上对内六方缺陷产生原因进行分析并制订出相应的控制措施。
2 内多边形形成的机理荒管减径时外径受到径缩而减小其减少量可以用钢管平均直径D的减少量表示外径减小意味着管子切向周长的减小。
按照金属流动规律出现一向压缩、两向拉伸的变形这样金属必然向另外两个方向流动在纵向产生延伸、在径向(即壁厚方向的自由内表面)产生增厚但是减径时如具有较大轴向张力也可能产生壁厚的减薄。
实际上由于三辊定径机(除最后一架)孔型是椭圆的见图1-1沿孔型周边上的管壁增厚分布以辊缝处为最大顶部最小由于轧机孔型辊缝互相呈60°。
因此第二架辊缝相当于第一架孔型顶部的位置。
这样第二架轧制后钢管的壁厚分布管壁增厚沿1/6周长的分布处于30°方向的壁厚最薄。
在顶部与辊缝方向的壁厚最厚结果钢管断面上呈内六方。
孔型不同部位的增厚亦不同其原因是钢管在孔型宽度上高度压缩量不均在顶部高度压下量最大变形时接触弧长、单位压力也比辊缝处大这样轴向摩擦力也大促使金属轴向流动这样就导致顶部壁厚增厚较小。
3影响内多边形的因素据许多文献介绍影响内多边形的因素有以下几方面: 3.1轧辊数目。
集中差速传动微张力减径机的生产工艺设计(下)

De i fM a u a t o e s o i ts r t h s gn o n f c u e Pr c s fSl r gh — te c
4 生 产 工 艺
4 1 轧制 表 .
与计算如下 :
p= 1 (-/O )] 10 X [一 1pl0 x 0 % p [一 1p l0 ] 10 = 1 (-d O ) x 0 % 生产车间各轧管机合理的变形分配虽不属减径 工艺 ,但有必要提一下 。在配置 ( ) 微 张力减径机 式 中 m—— 等效机架数。 对微 张力 减径 机 而 言 ,m 『 部 工作 机 架数 一 = 全 后 ,整个 轧管机组 的变形分 配应主要考虑 以下要 1 ~ . ]( 5 0 。 求 :①减径机合理 的总( 单架 ) 减径率和孔型系列 (. 2 ) 单架减径率小 ,则取小值) ()最 大单架 ( ) 2 总 减径 率 的确定 ( 确定外径时) ;②切头损失 ( 确定壁厚时 ) ;③“ 内
o ema uatr rc s ,temao c n lgc l ac lt na dted s nmeh d Al ecie r h f h n fcuepo es h jr e h oo ia c luai n h e i to . s d s r daete t t o g o b
R d cn l t e t l e ie e t l r eS se P r ) e u igMi wi C nr i d Df rni i y tm( atⅡ、 l h az f aD v
Q uYo ga i n ti
无缝钢管张力减径张力系数的理论计算与分析

无缝钢管张力减径张力系数的理论计算与分析李金锁;吕庆功【摘要】通过推导钢管张力减径塑性方程,提出了表征钢管张力减径时纵向、径向和切向变形的指标,计算和分析了张力系数对张力减径变形的影响特点,并定量分析了临晃张力系数的特点.分析结果表明:增大张力系数有利于促进钢管的纵向延伸变形和减壁变形,不利于减径变形;在3个方向的变形中,张力系数对壁厚变化的影响最为明显;钢管张力减径时,临界张力系数的大小只受钢管径壁比的影响,径壁比越大,临界张力系数越大;理论计算的临界张力系数的范围为0.35~0.50,任何情况下临界张力系数小于0.50.通过生产应用实例证实,根据钢管径壁比选择张力系数具有实用性和有效性.【期刊名称】《钢管》【年(卷),期】2015(044)003【总页数】4页(P40-43)【关键词】无缝钢管;张力减径;张力系数;塑性变形;径壁比【作者】李金锁;吕庆功【作者单位】天津冶金集团中兴盛达钢业有限公司,天津301616;北京科技大学高等工程师学院,北京100083【正文语种】中文【中图分类】TG333.8张力减径机是现代化的生产机组,可以实现钢管的增壁厚、等壁厚和减壁厚变形,在热轧无缝钢管生产过程中得到广泛使用[1-2]。
一般的减径机上单机架减径量只有3%~5%,而张力减径机的单机架减径量可达7%(甚至更高),总减径量可达85%,总减壁量可达38%[3-4]。
因此,张力减径机前面的轧管机可以只生产少数几种规格的荒管,通过张力减径机来得到各种规格的成品管,从而大大提高热轧无缝钢管机组的生产效率、扩大产品规格范围[5-6]。
张力系数是控制钢管壁厚变化的关键参数,其设定和控制水平对于成品钢管的壁厚精度具有重要的影响[7]。
通常情况下,张力减径机应尽可能采用大的张力系数,以强化张力减径工序的减壁变形能力,但必须结合具体工艺条件进行合理设定。
一般张力减径的张力系数为0.34~0.50时为等壁减径,张力系数为0~0.33时为增壁减径,张力系数大于0.50时为减壁减径,实际生产中的最大张力系数可取到0.65~0.85[8-10]。
张力减径中产品缺陷及预防

张力减径中产品缺陷及预防作者:武建兵来源:《科技创新与生产力》 2016年第4期武建兵(太原通泽重工有限公司,山西太原 030032)摘要:通过分析张力减径中产品青线形成、外径超差、管端增厚、鹅头弯、内六方等缺陷产生的原因,提出了预防或消除缺陷的相应措施。
关键词:减径机;青线;管端增厚;鹅头弯;内六方中图分类号:TG335 文献标志码:A DOI:10.3969/j.issn.1674-9146.2016.04.114收稿日期:2015-11-30;修回日期:2016-03-02作者简介:武建兵(1979-),男,山西平遥人,硕士,工程师,主要从事无缝钢管生产设备设计及生产工艺研究,E-mail:147362164@。
张力减径轧制作为无缝钢管生产的最后一道热轧工序,对产品质量的控制起着决定性作用。
无缝钢管的张力减径是一种不带芯棒的连续轧制过程,在轧制过程中,轧件受到轧辊的径向压力作用使外径、壁厚发生变化,轴向受到轧辊摩擦力作用,使壁厚发生改变,同时受到切向应力及以温度变化等各种因素作用。
由于其轧制过程的复杂性,因此容易引起许多种产品缺陷,其主要缺陷有青线、外径超差、内六方、管端增厚、鹅头弯等。
其中一些缺陷可以采用一定的措施消除,而另一些缺陷则可以加以控制或改善。
为此,笔者从理论与实践两方面就常见缺陷形成原因及预防措施做了简要分析。
1 青线形成原因及预防青线是指钢管表面沿长度方向有一条突起的直线。
青线产生的主要原因有:孔型设计时椭圆度过小、宽展量不合理,使钢管在轧制时金属过充满后被挤入辊缝,形成青线;轧辊沿轴向窜动,由于固定轧辊轴向移动的螺栓(或圆螺母)松动,使得轧辊可以沿轴向移动,造成辊面在辊缝处形成台阶,在钢管轧制时,形成青线。
为了预防青线出现,应根据生产现场情况,分析产生青线的原因。
首先检验每个机架轧辊是否在轴向窜动,如果有个别轧辊轴向窜动,则应维修轧辊机架,消除轧辊机架的窜动因素,随后重新修正孔型尺寸,进行轧制,最后检验产品是否合格。
钢管张力减速机的减径理论及工艺参数-未成稿

钢管张力减径机的减径理论及工艺参数太原重型机器有限公司技术中心轧钢所汤智辉前言张力钢管减径是钢管生产中的一项重大的发展,世界各国都十分重视。
张力减径机已经愈来愈广地得到应用。
用一般不带张力的减径机来生产小直径钢管,已经有很多年的历史了。
但是,由于减径出来的钢管壁厚增加、横向壁厚不均比较严重,减径管的质量不能令人满意;同时由于减径量较小,需要比较多的机架,因此,这种减径机应用范围多半局限在生产轧管机组不能或不容易直接生产的小直径钢管。
在一般减径机上,单架减径理只有3~5%,而在张力减径机上,单架减径量可以达到12~14%。
张力减径时,在减小直径的同时可以使钢管壁厚减薄或者保持不变,减径过程稳定并且钢管的横向壁厚不均也比较小。
因此,张力减径就成了生产薄壁小直径钢管的有效方法。
此外,由于张力减径时的变形量大,所需要的机架数目可以显著减少,因而使减径管的规格范围日益扩大。
这样,减径机就不仅用来生产小直径钢管,同时也用来生产较大规格的钢管。
在这种情况下,前面的轧管机组就可以只生产少数几种生产北最高、最便于生产的规格,通过张力减径机得到各种尺寸的成品管,从而大大提高了机组的生产能力,简化了生产。
目前,只要是在无缝钢管生产中,不论在连续生产还是单根钢管生产中,也不论在轧钢机还是在挤压机后,都广泛安设了张力减径机。
因此,可以说:张力减径机已经成为钢管生产中应用最广泛的设备之一。
张减理论一、 管材的壁厚变化与延伸在张力减径时过程中,管材的壁厚减薄与延伸,既发生在减径机的各机架上,也同样发生在减径机各机架之间。
㈠ 在机架上的变形当管材在机架上受压时,直径和壁厚都发生变化。
如果说直径的变化完全决 定于孔型的尺寸,那么壁厚的改变则同其它一些因素(张力、壁厚与直径之比等)有关。
现以管材在变形区的一个单元体为例,对其应力状态进行分析。
径向应力 σr 、切向应力σq 、轴向应力σx 在管材断面和在变形区的分布都是不均匀的。
这可以从管材出入口断面的应力不相等,和内外表面的应力不相等可以看出。
张力减径机钢管内六方成因分析
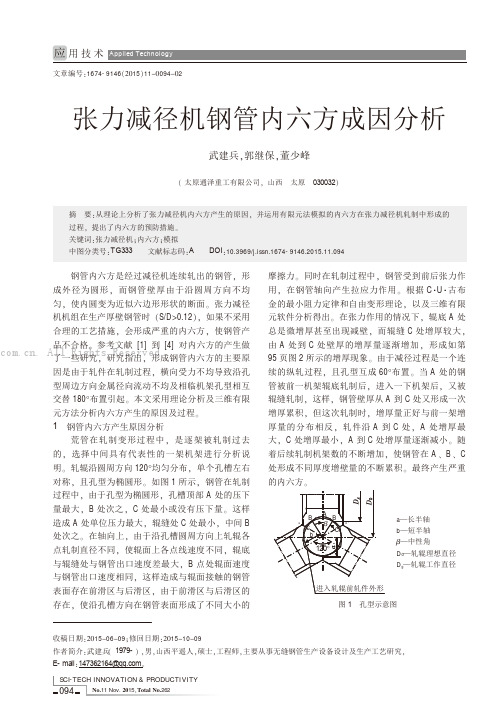
摩擦力遥 同时在轧制过程中袁 钢管受到前后张力作 用袁 在钢管轴向产生拉应力作用遥 根据 C窑U窑古布 金的最小阻力定律和自由变形理论袁 以及三维有限 元软件分析得出遥 在张力作用的情况下袁 辊底 A 处 总是微增厚甚至出现减壁袁 而辊缝 C 处增厚较大袁 由 A 处到 C 处壁厚的增厚量逐渐增加袁 形成如第 95 页图 2 所示的增厚现象遥 由于减径过程是一个连 续的纵轧过程袁 且孔型互成 60毅布置遥 当 A 处的钢 管被前一机架辊底轧制后袁 进入一下机架后袁 又被 辊缝轧制袁 这样袁 钢管壁厚从 A 到 C 处又形成一次 增厚累积袁 但这次轧制时袁 增厚量正好与前一架增 厚量的分布相反袁 轧件沿 A 到 C 处袁 A 处增厚最 大袁 C 处增厚最小袁 A 到 C 处增厚量逐渐减小遥 随 着后续轧制机架数的不断增加袁 使钢管在 A 尧 B尧 C 处形成不同厚度增壁量的不断累积遥 最终产生严重 的内六方遥
7 300 82.06 5.85 1.071 0 42.44 39.62 185.11
8 300 77.55 5.50 1.060 0 39.90 37.64 193.29
9 300 74.21 4.30 1.050 0 38.01 36.20 199.86
10 300 72.13 2.80 1.035 0 36.69 35.45 207.79
钢管内六方是经过减径机连续轧出的钢管袁 形 成外径为圆形袁 而钢管壁厚由于沿圆周方向不均 匀袁 使内圆变为近似六边形形状的断面遥 张力减径 机机组在生产厚壁钢管时 渊S/D跃0.12冤袁 如果不采用 合理的工艺措施袁 会形成严重的内六方袁 使钢管产 品不合格遥 参考文献 [1] 到 [4] 对内六方的产生做
11 300 70.84 1.80 1.020 0 35.77 35.07 209.94
无缝钢管张力减径过程中内六方的成因分析及解决办法
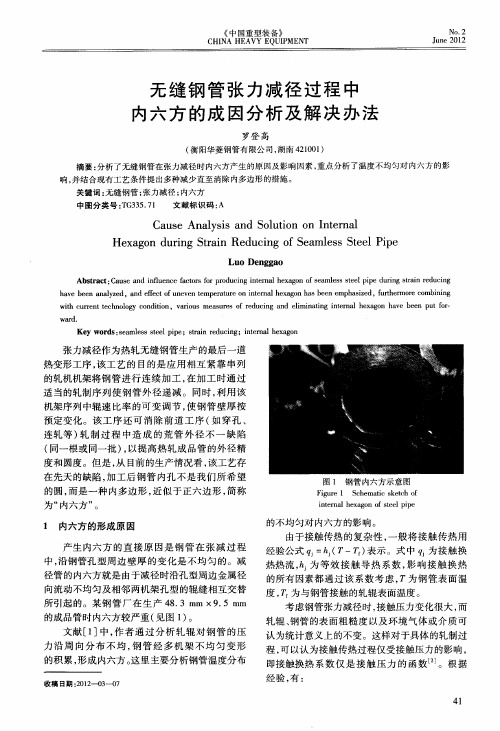
及 传 动上 的方便 , 邻 机架上 下倒 置摆 放 , 相 这相 当 于将 轧辊 每 次 旋 转 6 。 正 是 这 种 布 置 使 钢 管 的 0, 壁 厚变 化趋 势 叠 加 。如 果 采 用 不 同角 度 布 置 , 最
机 架叠 加后 , 管 金 属 在 沿 轧辊 孔 型 方 向流 动 不 钢 均 匀 。钢管 在 减 径 过程 中 , 薄 的部 位 在 不 断 减 减
2 解 决措 施
薄 , 厚 的部 位 在不 断增 厚 。如果 钢 管 此 时 能 产 增
生 一定 角度 的旋 转 , 则增 厚 和减 薄趋 势不会 叠 加 , 这 样金 属在 沿 轧 辊孔 型方 向 的流 动 趋 于 均 匀 , 内 六 方 问题将 得 到根本 上 的解决 。
中, 沿钢 管孔 型 周 边 壁 厚 的 变 化是 不 均 匀 的。减
的不 均 匀对 内六 方 的影 响。
由于接触传热的复杂性 , 一般将接触传热用
经验 公式 q =h( ) 示 。式 中 g 为 接触 换 iT— 表 i
热热 流 ,; 等 效 接 触 导 热 系数 , 响 接 触 换 热 h为 影
41
No. 2
J n 0l u e2 2
《 中国重型装备》 C N E V Q IME T HIA H A Y E U P N
单机架 轧 制后
第 二机架 轧制 后
图 2 沿 16周长 的 q 分布 图 / ;
F g r q it b t n ao g 1 6 p rmee iue2 Jdsr u i ln / e i tr i o
wih c re e hn l g o diin, v ro s t u r ntt c o o y c n to a iu me s r s o e u i g a d e i ia i ne a h x g n a e e n p fr a u e f r d c n n lm n tng i tr l e a o h v b e uto — n
微张力减径机轧后钢管产生青线的原因分析

收稿 日期 :o 5一 8一 5 2o O O
前言
突出 , 一般称 之 为青 线 。 可 能产 生 青 线 的原 因很
钢管 微张 力减 径机 主要 是针 对轧 后荒 管进 行
多: 如轧制速度制度的不合理 , 孔型的宽展量设置 太小 , 轧辊 的倒 角过 大 , 因材质 原 因而导致 的倒 或 角破碎等都可不同程度的造成青线缺陷。
2 工艺 因素 的排 除
Ch n F n e eg
Ab t a t Th 8 o h tp o u e e b a k t r a n t e s e b u i g t e rl n rc s y te 1 t n s s r c : e I 8 n t a r d c d t l c e d o t lt e d r o i g p o e sb 4 sa d  ̄ h h h e u n h l h mir c o—t n in r d cn m i a e n a ay e so e u i g— — h s b e n l ̄ l l i i r de n t s a t .wh c n ia e h ti i a s y o e oe a c - h i i h i d c ts ta t s c u e b v rtlr n e ma d
的 , 乎该 产 品的生 产工 艺 要求 。 合
出 直 状 耋 因棱上的金属变形程度和其 3~一 制 素 … ’ 现 线 的 曼 凸 棱 兰 孔 车因的除 的金属不 同, 因而这部分金属 的颜色 比较
该减 径机 为 三辊 Y型减 径机 , 三个 轧辊 呈
l孔型直径/ m l8 8 l5 4 l 18 18 1 o .4 l 10 9 .6 9 .3 9 .8 9 .4 8 .7 m 1 .2 l .9 l .o 0 . l 4 5 2 O .9 7 7 4 5 18 0 1 9 8 l l 轧辊转 速// i 5 . 6 .5 6 .l 6 .5 7 .0 7 .7 7 .9 7 .8 7 .4 8.3 8 .l r n 84 a r 0 o1 37 68 02 2 1 43 72 92 O2 O5
- 1、下载文档前请自行甄别文档内容的完整性,平台不提供额外的编辑、内容补充、找答案等附加服务。
- 2、"仅部分预览"的文档,不可在线预览部分如存在完整性等问题,可反馈申请退款(可完整预览的文档不适用该条件!)。
- 3、如文档侵犯您的权益,请联系客服反馈,我们会尽快为您处理(人工客服工作时间:9:00-18:30)。
微张力减径机轧后钢管产生青线的原因分析
陈峰
【摘要】分析出某厂14机架单独传动钢管微张力减径机在轧制过程中出现青线的原因是该减径机的主机架中滑板制造误差过大,机架受力倾斜造成的,整改后青线消失.
【期刊名称】《中国重型装备》
【年(卷),期】2006(000)001
【总页数】2页(P30-31)
【关键词】钢管;减径机;青线
【作者】陈峰
【作者单位】太原重型机械集团技术中心,山西,030024
【正文语种】中文
【中图分类】TG333.8
前言
钢管微张力减径机主要是针对轧后荒管进行减径和定径操作。
一般配备在三辊轧管机等一些斜轧机组之后。
张力减径机在轧制过程中根据规格要求设置轧辊速度,使各机架之间保持一定的张力以减少钢管的壁厚增加。
某厂的14机架单独传动钢管微张力减径机在轧制过程中频频出现青线缺陷。
经分析排除了其它因素,明确了是该主机座第7,8号方机架的滑板制造误差过大,造成轧制过程中方机架受力倾斜
从而在钢管上轧出青线。
整改后因设备原因带来的青线缺陷消失。
1 产生青线缺陷的原因
青线缺陷表现为在钢管的外表面连续稳定的出现直线状的凸棱,因棱上的金属变形程度和其它部位的金属不同,因而这部分金属的颜色比较突出,一般称之为青线。
可能产生青线的原因很多:如轧制速度制度的不合理,孔型的宽展量设置太小,轧辊的倒角过大,或因材质原因而导致的倒角破碎等都可不同程度的造成青线缺陷。
2 工艺因素的排除
该厂钢管减径轧制如表1所示。
分析该轧制表中单机架的减径率不超过3.5%,总减径率为26%,在30%以下。
宽展系数在1~1.12之间,满足普碳钢的宽展要求。
张力系数不大于0.55。
张力系数的分布满足建张、保持张力、释放张力的要求。
建张机架为三架,张力保持机架为五架,其余三架为张力释放机架。
可见该轧制表是规范的,合乎该产品的生产工艺要求。
3 孔型车制因素的排除
该减径机为三辊Y型减径机,三个轧辊呈120°布置如图1所示。
其轧辊结合面处的辊缝(图2)间隙以及辊缝处的倒角值是造成青线的原因之一。
为了排除该因素,
对该规格的孔型全部重车后进行轧制。
青线现象和重车之前相比几乎没有好转。
进一步观察使用过的轧辊倒角位置,没有剥落或缺口等缺陷。
实际测量三个辊缝值满足设计要求,在(0.5~0.7)mm之间。
所以断定孔型不是造成青线缺陷的原因。
表1 钢管减径轧制表Table.1The rolling schedule of the steel tube reducing
机架号1234567891011孔型直径/mm轧辊转速
/r/min118.8258.40115.4960.15111.8063.71108.1166.85104.5 4270.20101.0972.1797.7674.3994.5377.2891.8879.2490.148 0.2389.8780.51
图1 三辊Y型减径机轧辊布置示意图Figure.1 The arrangement schematic
sketch of the rolls in the Y type reducing mill
图2 辊缝间隙剖示图Figure.2 The section sketch of the roll clearance
4 主机架滑板因素的分析
用121 mm×6 mm的荒管进行减径操作,待管头刚出最后一架方机架时减径机传动装置停车,将减径未完的荒管从减径机入口退出,放置在检查台架上进行检查。
在钢管上对每机架的位置进行标示,发现在第7、8号机架的位置出现较为严重的青线缺陷。
在9、10、11号机架位置也有青线缺陷,但程度有所减轻。
为了进一步剖析原因,将7、8号机架位置用导管机架填充,保持总轧制机架数量不变,重新设置减径机轧辊转速,青线现象彻底消失。
说明产生青线的原因不是孔型问题,可能是方机架倾斜之后轧辊的辊缝位置和轧制线有了交角导致荒管外表面镶入辊缝中,从而形成了有规律的青线缺陷。
为证实这一点,测量了滑板和机架一些尺寸,机架能满足图纸要求,而滑板实际尺寸和图纸要求偏差过大。
滑板宽度在整个长度上呈现不均匀分布,最小为1.1 mm,最大为2.8 mm。
这样方机架的倾斜是一种空间的倾斜,与实际的缺陷位置相吻合。
5 解决措施
对7、8号滑板重新下料加工。
严格控制4块板的内侧平行度及上表面的水平度。
整改后,青线消失,轧制正常。
6 结论
通常在减径机发生青线轧制事故时,人们倾向于寻找工艺原因,而忽略了设备的加工制造原因。
上述事例说明应高度重视减径设备的加工制造以及日常维护。