张力减径机对无缝钢管造成的质量影响及处理
钢管“内六方”缺陷的产生原因及优化
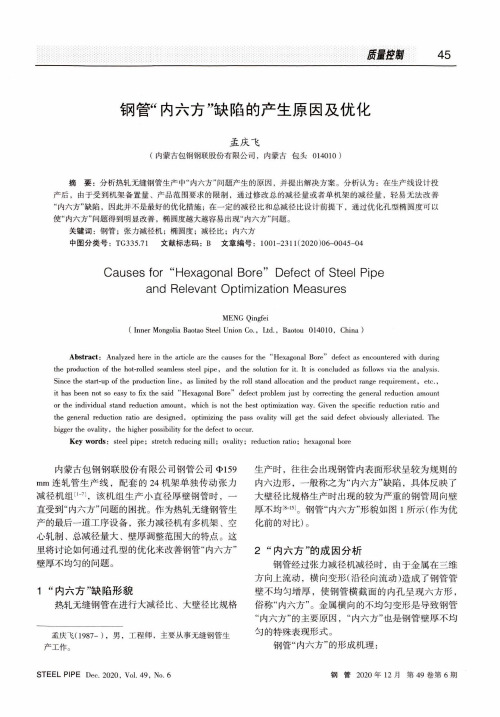
钢管“内六方”缺陷的产生原因及优化孟庆飞(内蒙古包钢钢联股份有限公司,内蒙古包头014010)摘要:分析热轧无缝钢管生产中“内六方”问题产生的原因,并提出解决方案。
分析认为:在生产线设计投产后,由于受到机架备置量、产品范围要求的限制,通过修改总的减径量或者单机架的减径量,轻易无法改善“内六方”缺陷,因此并不是最好的优化措施;在一定的减径比和总减径比设计前提下,通过优化孔型椭圆度可以使“内六方”问题得到明显改善,椭圆度越大越容易出现“内六方”问题。
关键词:钢管;张力减径机;楠圆度;减径比;内六方中图分类号:TG335.71 文献标志码:B文章编号:1001-2311(2020)06-0045-04Causes for “Hexagonal Bore” Defect of Steel Pipeand Relevant Optimization MeasuresMENG Qingfei(Inner Mongolia Baotao Steel Union Co.,Ltd.,Baotou014010,China )Abstract: Analyzed here in the article are the causes for the**Hexagonal Bore'defect as encountered with during the production of the hot-rolled seamless steel pipe,and the solution for it.It is concluded as follows via the analysis. Since the start-up of the production line,as limited by the roll stand allocation and the product range requirement,etc., it has been not so easy to fix the said“Hexagonal Bore”defect problem just by correcting the general reduction amount or the individual stand reduction amount,which is not the best optimization way.Given the specific reduction ratio and the general reduction ratio are designed,optimizing the pass ovality will get the said defect obviously alleviated.The bigger the ovality,the higher possibility for the defect to occur.Key words:steel pipe;stretch reducing mill;ovality;reduction ratio;hexagonal bore内蒙古包钢钢联股份有限公司钢管公司中159 mm连轧管生产线,配套的24机架单独传动张力 减径机组[|-7],该机组生产小直径厚壁钢管时,一直受到“内六方”问题的困扰。
改善无缝钢管的壁厚偏差

裹 2 新环形炉 管坯加 热工艺
f !翌 f l : 望 l 堑 !
( : 塑= 些 l 塑 ! =
塑 l 塑二
=
f 10 1o 10 1o 2  ̄3 f 2 —2 f 6 o 6 9 ; = l面 r厂
式中 A: 0壁厚 平均值 ; z: 孔坯 料长度 方 向用 f 穿 定义 i
A =(/) xc (K /) K 21 J“ )0 2 x t ̄ 6 s
维普资讯
—
—
8 — —
2O O2年第 2期
m ( 表 1 , 明顶 头 的精 度对壁厚 偏差 的 见 )表 影 响很 大 , 顶头 的 振 动 , 导致 斜 轧 穿 孔过 程
B :(/)ff )i 2 X 【 K 2 ( B ( / )x 5x n j
由各 自的周 期分 析 , 厚偏 差 主要 由下 壁 列 因素造 成 : () 料断 面的温度 。 1坯 () 头 的 振动 ( 头 中心 与 顶 杆 中心 2顶 顶 不 一致 ) 。 12 坯 料断面 温 差引起 的壁 厚偏 差 . 坯料 断面存 在温度 不均 时 , 圆周 方 向 在 上产 生变 形抗力 差 , 右两 侧 的压力 失 去 平 左 衡 ,1 2在 实 际 穿孔 时要 保 持 p :P , p≠p, l '顶 z 头 中心偏 离轧机 中心 e 离 .e 距 2 即为壁厚 偏
79 0 79 . 4 81 . 5 77 0 8l 0 81 . 5
偏心 15 的顶头 l 5 78 84 74 . m 76 . o . 0 .5 85 82 74 83 8 . 5 . 5 . 5 5
( : 中所 列 墼 厚 为 毛 管取 样 壁 厚 的 平 均值 ) 洼 表
钢管减径技术发展历史及工序质量控制
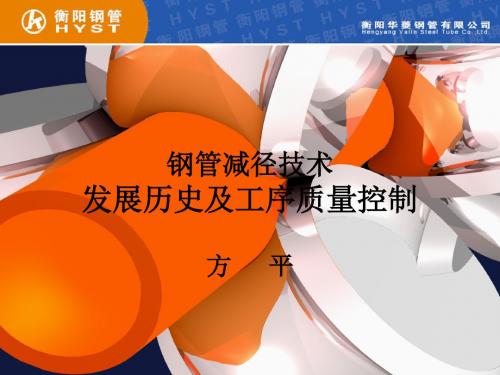
圆孔型
椭圆孔型
圆孔型
椭圆孔型
圆孔型
减径系列: B 荒管直径: 281 mm 最小荒管壁厚.: 6.35 mm 总减径率: 30.4 % 单机架减径率: 3.3 %
减径系列: C 荒管直径: 350 mm 最小荒管壁厚: 8.1 mm 总减径率: 21.3 % 单机架减径率: 2.2 %
⑤、减径机的型式和传动的方式
减径机的型式 传动的方式 美国 二辊式 单独电机传动 欧洲 三辊式 集中差动传动
钢管减径的优点
㈠、电焊钢管机组配减径机 ①可以大大提高小直径钢管的产量; ②可以减少调整成型机和电焊机的次数; ③可以减少所需要的坯料规格。 由于电焊钢管机组上可以生产很长很长的钢管,减径 机后面的飞锯技术也很成熟,因此在减径机同电焊机组联 合生产的情况下,切头损失是很小的。 ㈡、无缝钢管轧机配减径机 ①可以使无缝钢管轧机直接生产小直径(50mm以下) 热轧管,以前只能采用冷拔方法生产; ②大大提高较小规格钢管的产量,特别是一些石油工 业用的油管和输送管; ③可以大大简化穿孔机和轧管机的调整,提高生产效 率。
②工艺控制系统和工艺自动化系统 (CARTA®)
CARTA工艺系统主要有三部分组成:工艺 计划系统、工艺过程管理系统、工艺质量 保证管理系统
• 通过工艺计划系统,能使轧机和轧制工具达到最 佳化的基本调整; • 通过工艺过程管理系统,能使生产中所有的轧制 过程全部保持良好的轧制状态; • 通过工艺质量保证管理系统,能够记录生产中每 根钢管的有关数据并输送给工艺检测系统进行分 析评定。通过上位计算机与每个单机上的子程序 进行数据连接和工艺联网,进行各种工艺检测。
减径机CARTA系统的主要功能
• 局部壁厚控制系统(WTCL)
微张力减径机轧后钢管产生青线的原因分析

《 重型机械科技》 RS3TN A3URVQS.N =UVSQUS! 3QW ’SURQXYX(N
微张力减径机轧后钢管 产生青线的原因分析
陈! 峰
( 太原重型机械集团技术中心, 山西 "#""$% ) 摘要: 分析出某厂 &% 机架单独传动钢管微张力减径机在轧制过程中出现青线的原因是该减径机的主机架 中滑板制造误差过大, 机架受力倾斜造成的, 整改后青线消失。 关键词: 钢管; 减径机; 青线 中图分类号: ’(###) *! ! 文献标识码: +
万方数据
产业协调发展也具有十分重大的意义。 国家环保总局已与 :;;= 年 D 月 !D 日批复了 中国石油四川 B; 万吨 E 年乙烯工程项目的环境影 响评价报告书。该项目由中石油与成都石油化工 有限公司合作建设, 中石油控股, 是西南地区历史 上第一个大型乙烯项目, 计划于 “ 十一五” 期间建 成。 ( 摘自华西都市报第 D;F! 期) F!
责任编辑" 周南金
!:;< 布置如图 ! 所示。其轧辊结合面处的辊缝 ( 图 :) 间隙以及辊缝处的倒角值是造成青线的原 因之一。为了排除该因素, 对该规格的孔型全部 重车后进行轧制。青线现象和重车之前相比几乎 没有好转。进一步观察使用过的轧辊倒角位置, 没有剥落或缺口等缺陷。实际测量三个辊缝值满
22222222222222222222222222222222222222222222
四川省 %& 万吨乙烯工程在成都开建
" " :;;A 年 : 月 :B 日, 中国石油四川 B; 万吨 E 年 乙烯工程在彭州市隆丰镇拉开建设帷幕。 总投资 :!; 亿元的中国石油四川 B; 万吨乙 烯工程项目是国家实施西部大开发战略的重大项 目。项目的建设将对四川化工、 轻工、 纺织等产业 发展起到强有力的拉动作用, 对西南地区石油化 工产业结构调整产生重大影响, 对促进西部地区
热轧(微)张力减径钢管的主要缺陷和消除方法

热轧(微)张力减径钢管的主要缺陷和消除方法
- 热轧(微)张力减径钢管的主要缺陷及消除方法
1、缺点:表面缺陷(毛发状缺陷、裂纹、气孔)
消除方法:提高表面洁净度,加强质量检验,严格控制张力差、减
径钢管精度及表面质量;定期作业前对减径钢管进行卷筒表面填充磨光,减少毛发样缺陷,并且要充分控制卷筒表面填充过程中的处理温度、进料收缩率及剩余应力等。
2、缺点:表面弯角不均匀以及错位等
消除方法:应采用实心轴或带有凹槽的轴,并要有足够的轴面硬度,以防止表面错位;减径钢管的低减径层使用放大器,以减少弯角不均
匀情况,还需要弯曲过程定期维护润滑,增强设备操作稳定性。
3、缺点:减径钢管叞边区减径精度较差
消除方法:提高减径工艺技术,提高减径钢管质量,如拉伸减径阶段,应采用刚性夹头、均匀减径以及调整减径速度等;同时,要及时
对减径钢管进行彻底维护,它才能确保拉伸减径的精度。
4、缺点:减径钢管的精度较差
消除方法:在减径钢管的生产过程中,应配备严格的检测,如采用液压系统定时监测拉伸减径的精度;同时进行原料批次检测,以保持安全性。
同时,要加强钢管表面处理,打磨质量,防止表面老化,提高减径钢管的使用性能和精度。
张力减径的工艺特点

张力减径的工艺特点为了提高轧管机组的生产率和产量,在轧管机后配备了张力减径机。
这样,轧管机只需轧出1种或2种、最多3种外径的荒管,通过张力减径就可生产出多种不同直径和壁厚的成品钢管,使轧管机轧制的钢管单一化,从而减少了管坯和芯棒规格数量。
如宝钢无缝钢管厂的Φ140mm连轧管机组用两种直径,不同壁厚的70个规格的荒管,张力减径后就生产出成品管460个规格。
张力轧制减径中,钢管中间部分的壁厚受到张力作用而被拉薄,头尾两端的壁厚由于受不到张力或受到的张力不同,出现增厚或由厚到薄的过夜壁厚。
因而必须切去钢管两端增厚和过渡壁厚部分的管端。
因此,张力减径机只能配置在能轧制长荒管的轧管机组中,以减少切头损失率。
但是张力减径机如果采用限制管端增厚的电控技术,管端增厚的长度可以减少约1/3。
三辊张力减径机传动有内、外传动两种方式,采用内传动结构居多。
内传动的张力减径机,每个机架内设置有两对圆锥齿轮,简化了机座的结构,但在一定程度上影响了机架间距的缩小。
外传动式是双位机座,机架间距小,承载轧制力大,管端增厚长度也减少。
最大减径率和最大减壁率是张力减径机的两个主要参数。
在最大减径率及其允许的最大减壁率的条件下,用最薄壁的荒管生产出壁厚最薄的钢管,一般称为该台张力减径机的极限规格。
张力减径机组的总对数减径量可达90%,单架对数减径量最髙达12%〜17%。
为提高减径管质量,单架对数减径量常被限制在7%〜9%范围内。
主要机架的单架对数减径量一般为6%〜12%。
张力减径机的进出口速度由生产能力决定。
目前张力减径机的出口速度可达18m/s,进口速度大多在1〜3m/s。
张力减径机的张力系数z的最大允许值一般在0.5〜0.84之间波动,轧制温度高时取下限。
无缝钢管常见缺陷(欠)分析预防及处置
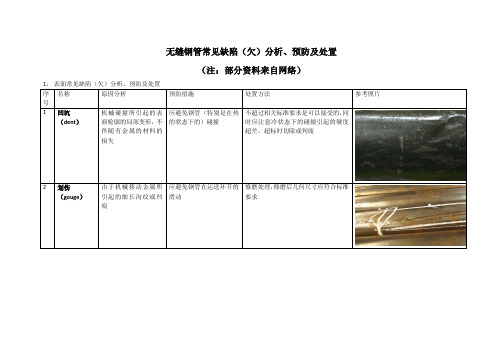
定径孔型设计不合理, 控制定径温度, 定径温度过高或过低 合理设计孔型尺寸 定径机架位置安装不 正确、 成品孔型磨损严 重、 轧制中心线偏移严 重。锯切时,夹紧装置 夹紧力不合理。 矫直辊 压下量或角度调整不 当。 调整安装位置,合理设置 成品孔型轧制量,调整夹 紧装置夹紧力、矫直辊压 下量或角度
3
无缝钢管常见缺陷(欠)分析、预防及处置 (注:部分资料来自网络)
1, 表面常见缺陷(欠)分析、预防及处置 序 号 1 名称 凹坑 (dent) 原因分析 机械碰撞所引起的表 面轮廓的局部变形, 不 伴随有金属的材料的 损失 预防措施 应避免钢管(特别是在热 的状态下的)碰撞 处置方法 不超过相关标准要求是可以接受的, 同 时应注意冷状态下的碰撞引起的硬度 超差。超标时切除或判废 参考照片
6
内直道 ( plug scores)
产生在无缝钢管内部 的细长型的凹槽, 通常 是粘着在精轧用芯棒 上的金属硬碎块引起 的
及时检查芯棒表面质量
钢管内表面允许存在深度不超过壁厚 5%(最大为0.4mm)的内直道;对深 度超标的内直道,应修磨或切除
7
辊 痕 ( rool mark)
由于轧辊调整不当或 轧辊表面有损坏所引 起的钢管表面缺欠
合理设计调质钢种、淬火 液,避免局部冷却
切除或判废
12
拉凹( stretch mill indentation)
连轧时张应力过大引 温度均匀、调整张应力 起,严重时形成拉裂、 空洞
拉凹处的实测壁厚, 不得小于壁厚所允 许的最小值;否则,应切除或判废
13
孔洞(与拉凹 相同)
2, 几何尺寸常见缺陷(欠)分析、预防及处置 序 号 1 2 名称 外径超差 椭圆度超差 原因分析 预防措施 处置方法 超上限时,重新定径; 超下限时,扩径,或改交合同 二次定径、管端定径或切除管端。 参考照片
钢管张力减径工艺特点及设备选型

钢管张力减径工艺特点及设备选型力减径机是钢管生产系统中应用最广泛的设备之一。
文章介绍了张力减径工艺的发展和特点、设备分类和特点,并对设备选型进行了初步分析指出:张力减径机对提高整个穿孔、延伸机组的生产能力有决定性作用;单独传动及双电机集中传动〔不包括单电机集中变速传动〕是张力减径工艺两种极端表现方式,分组传动及混合传动是这两种方式的中间方式;外传动方式的优点使其具有很大的市场潜力;根据工艺选择合适的张力减径机可实现方案的最正确化,效益的最大化。
为国内钢厂钢管张力减径的选型提供了参考依据。
张力减径机专利自1932年出现后,由于其特有的工艺,在连轧管机组及其他方式生产无缝管的机组后,都广泛安设了张力减径机。
张力减径机成为了三步轧管法〔穿孔、延伸、精轧〕中不可或缺的设备。
针对机组不同的工艺要求,对张力减径机机型的选择就显得尤为重要。
本文将介绍张力减径工艺的特点、各类张力减径机的特征及设备选型。
张力减径工艺的发展最早的张力减径机为二辊式,但由于三辊式张力减径机在变形均匀及防止内外外表缺陷的产生上有许多明显优势,故在解决了三辊式轧辊驱动结构设计问题后,目前的张力减径机都采用三辊式布置形式。
张力减径机传动系统由单电机集中变速传动演变到每个机架单独调速传动,在单独传动上除直流电机单独传动外,又出现了液压差动调速〔集中传动单独差动〕,针对这两种传动的特点又演变出了双电机集中变速传动,在双电机基础上又出现了分组传动系统〔串联集中变速传动系统〕,即三电机、四电机和六电机集中变速传动。
为了改善张减后钢管质量及提高钢管成材率,在张力减径机组上又应用了各种过程控制系统,如:切头尾控制〔CEC〕、平均壁厚控制〔WTCA〕、局部壁厚控制〔WTCL〕、管长控制、剪切长度最正确化控制等[1]。
由不可调机架发展到成品机架用可调机架,增加了产品的生产灵活性,并且对产品的尺寸精度有了更好的控制。
定径机+张力减径机的工艺布置对提高延伸机组的生产能力,简化其生产管理具有积极的作用。
张力减径机Ф133mm孔型的开发与应用

万方数据
张力减径机Ф133mm孔型的开发与应用
作者: 作者单位: 刊名:
英文刊名: 年,卷(期): 引用次数:
钟锡弟, 陶学智, 李金锁, 李培达, 赵永恒 天津市无缝钢管厂,
轧钢 STEEL ROLLING 2001,18(3) 0次
相似文献(10条)
1.期刊论文 谢麒麟.潘峰.郑坚敏.周志杨.王超峰.苏惠超.杨军.Xie Qilin.Pan Feng.Zheng Jianmin.Zhou
8.期刊论文 黄豪昌 CARTA系统在24机架张力减径机上的应用 -冶金自动化2004,28(z1)
主要讲述CARTA(Computer Aided Rolling Techology Application)系统如何应用于热轧无缝钢管终轧设备--张力减径机中.文中重点讲述CARTA的构 成,实时控制,CARTA系统功能与连锁以及它如何对张减机速度进行调控的.
可调机架技术是近年发展的一项新技术,能够满足不同的外径公差要求.本文介绍了可调机架技术原理、快速换辊技术以及可调机架技术在宝钢的应 用实绩.实践证明,该技术在满足钢管用户对管材外径公差特殊要求的同时,能减少张力定(减)径机机架储备,降低生产成本.
6.期刊论文 李辉.李青 张力减径机孔型设计初探 -一重技术2004(3)
Pei-da, ZHAO Yo【-g heng
(Tia嘶in Seaml黜Pipe Co.,Tianjm 300220.Chlm)
Abstract:The stands and r0【I rr。wn of imported tension reducing mill were improved.and the中133mm pass was developed in order to r瑚ize muhiple length production and increase finished product rate of APl oil well pipe
张力减径的工艺原理及主要问题

包头钢铁职业技术学院学生毕业论文论文题目:张力减径的工艺原理及主要问题专业:冶金班级:冶金一班学生:李咏光指导教师:魏宁日期: 2010年3月31日目录摘要 (1)关键词 (1)引言 (1)1 张力减径机技术的发展 (1)2 张力减径机的作用 (1)2.1张力减径机的形式 (2)3 钢管定径、减径的工艺原理 (3)3.1 张力减径的优点、缺点 (3)3.2三辊定径、减径机减径与二辊定径减径机相比 (4)3.3张力径机的孔型 (5)3.4张力减径机与微张力减径机的不同 (8)3.5 管材热扩径方法 (8)4张力减径时管端偏厚的原因 (10)4.1影响张力减径机管端增厚的因素 (10)4.2影响管内多边形的因素 (11)结语 (11)参考文献 (12)张力减径机的工艺原理及主要问题摘要:简介了三辊定径机定径和减径的作用及形式,提出了定减径机工作时常出现的问题,进行了三辊定减径机和两辊定减径机的比较。
关键词:定减径机;壁厚;斜轧;张力引言:在无缝钢管生产的三大机组——穿孔机组、轧管机组、定减径机组中,人们一直十分关注轧管机的研究,先后开发出自动轧管机组、顶管机组、新型顶管机组(CPE)、三辊轧管机组、连轧管机组(包括浮动芯棒MM、限动芯棒MPM和半浮动芯棒连轧管机组等)、AccuRoll轧管机组、改进型三辊轧管机组。
但对于穿孔机组,仅在20世纪80年代初才提出菌式穿孔机。
而定减径机一直使用二辊式和三辊式,直到20世纪90年代初才提出三辊可调式定径机技术。
新型三辊可调式定径机技术是为满足现代钢管生产高效、优质、低耗的要求而开发的,它的开发成功也为无缝钢管的生产注入新的活力。
1张力减径机技术的发展张减工艺主要特点是边连续多机架二辊或三辊无芯棒纵轧,采用适当的孔型系使毛管外径减缩,通过机架系列中轧辊速比的调节获得预定的壁厚变化。
20世纪40年代无缝管机组被美国和西欧所用,这时的张减机都是二辊式,到了20世纪50年代,西德曼乃斯曼公司成功地奕用了三辊式张力减径机,从而代替了二辊式。
无缝钢管张力减径过程内六方产生的模拟分析

无缝钢管张力减径过程内六方产生的模拟分析作者:于辉减新良杜凤山汪飞雪张力减径是热轧无缝钢管或焊管生产的一种加工方法,张力减径机(SRM)作为关键设备直接影响产品的成材率。
张力减径(简称张减)过程的金属变形发生在三维空间,受到孔型形状、道次减径量、机架间距等多种因素的影响,容易在钢管内部形成内六方缺陷。
为此,国内外有关学者做了许多研究工作,大多对内六方进行定性讨论,认为内六方是横向壁厚累加的结果,并从工艺上制定了一些相应的控制措施,但未从金属流动的角度对横向壁厚变化进行定量的分析研究。
本文针对某钢管公司18机架张减机组试轧产品出现内六方的状况,利用MSC.Marc软件进行三维热力藕合有限元建模分析,并与实测数据进行对比,验证模型的准确性。
通过研究钢管张减过程的金属变形,定量分析了各机架的横向壁厚分布,探讨内六方产生的原因,为提高无缝钢管产品质量具有重要指导作用。
1 有限元模型建立1.1 张减过程描述在热轧无缝钢管时,连轧荒管经过再加热炉加热到900一1000℃,高压水除鳞后,进人张减机组轧制。
张减时钢管内部不带芯棒,依次通过各机架孔型,对钢管进行连续加工,在减径的同时实现减壁。
张减机组的轧辊大多是椭圆孔型,构成孔型的3个轧辊曲面呈210阵列布置,奇数机架与偶数机架互成60°交替排列。
因此,张减机组孔型配置是否合理,是影响产品质量的主要因素之一。
1.2 热边界条件确定张减时管坯表面存在热传导、热对流和热辐射三类边界条件川,由于对流所产生的热损失所占比例较小,可将其与辐射统一作为一个边界条件处理,写为:管坯初始温度950 ℃,环境温度取20 ℃,轧辊温度取100℃。
在确定热边界条件时,对流和辐射的等效换热系数取150w/(m2·℃),管坯与轧辊的接触换热系数取20kW/(m2·℃),变形功转换系数取0.9,摩擦功转换系数取0.9。
1.3 几何模型的建立每个机架轧辊孔型的几何特点是孔型曲面为相对于轧辊轴线对称的旋转面,因此可以取与钢管对应的半个轧辊曲面作为研究对象,把管坯的计算模型减少到整个截面的六分之一,在此基础上建立全系统有限元连轧模型。
无缝钢管张力减径张力系数的理论计算与分析

无缝钢管张力减径张力系数的理论计算与分析李金锁;吕庆功【摘要】通过推导钢管张力减径塑性方程,提出了表征钢管张力减径时纵向、径向和切向变形的指标,计算和分析了张力系数对张力减径变形的影响特点,并定量分析了临晃张力系数的特点.分析结果表明:增大张力系数有利于促进钢管的纵向延伸变形和减壁变形,不利于减径变形;在3个方向的变形中,张力系数对壁厚变化的影响最为明显;钢管张力减径时,临界张力系数的大小只受钢管径壁比的影响,径壁比越大,临界张力系数越大;理论计算的临界张力系数的范围为0.35~0.50,任何情况下临界张力系数小于0.50.通过生产应用实例证实,根据钢管径壁比选择张力系数具有实用性和有效性.【期刊名称】《钢管》【年(卷),期】2015(044)003【总页数】4页(P40-43)【关键词】无缝钢管;张力减径;张力系数;塑性变形;径壁比【作者】李金锁;吕庆功【作者单位】天津冶金集团中兴盛达钢业有限公司,天津301616;北京科技大学高等工程师学院,北京100083【正文语种】中文【中图分类】TG333.8张力减径机是现代化的生产机组,可以实现钢管的增壁厚、等壁厚和减壁厚变形,在热轧无缝钢管生产过程中得到广泛使用[1-2]。
一般的减径机上单机架减径量只有3%~5%,而张力减径机的单机架减径量可达7%(甚至更高),总减径量可达85%,总减壁量可达38%[3-4]。
因此,张力减径机前面的轧管机可以只生产少数几种规格的荒管,通过张力减径机来得到各种规格的成品管,从而大大提高热轧无缝钢管机组的生产效率、扩大产品规格范围[5-6]。
张力系数是控制钢管壁厚变化的关键参数,其设定和控制水平对于成品钢管的壁厚精度具有重要的影响[7]。
通常情况下,张力减径机应尽可能采用大的张力系数,以强化张力减径工序的减壁变形能力,但必须结合具体工艺条件进行合理设定。
一般张力减径的张力系数为0.34~0.50时为等壁减径,张力系数为0~0.33时为增壁减径,张力系数大于0.50时为减壁减径,实际生产中的最大张力系数可取到0.65~0.85[8-10]。
张力减径中产品缺陷及预防

张力减径中产品缺陷及预防作者:武建兵来源:《科技创新与生产力》 2016年第4期武建兵(太原通泽重工有限公司,山西太原 030032)摘要:通过分析张力减径中产品青线形成、外径超差、管端增厚、鹅头弯、内六方等缺陷产生的原因,提出了预防或消除缺陷的相应措施。
关键词:减径机;青线;管端增厚;鹅头弯;内六方中图分类号:TG335 文献标志码:A DOI:10.3969/j.issn.1674-9146.2016.04.114收稿日期:2015-11-30;修回日期:2016-03-02作者简介:武建兵(1979-),男,山西平遥人,硕士,工程师,主要从事无缝钢管生产设备设计及生产工艺研究,E-mail:147362164@。
张力减径轧制作为无缝钢管生产的最后一道热轧工序,对产品质量的控制起着决定性作用。
无缝钢管的张力减径是一种不带芯棒的连续轧制过程,在轧制过程中,轧件受到轧辊的径向压力作用使外径、壁厚发生变化,轴向受到轧辊摩擦力作用,使壁厚发生改变,同时受到切向应力及以温度变化等各种因素作用。
由于其轧制过程的复杂性,因此容易引起许多种产品缺陷,其主要缺陷有青线、外径超差、内六方、管端增厚、鹅头弯等。
其中一些缺陷可以采用一定的措施消除,而另一些缺陷则可以加以控制或改善。
为此,笔者从理论与实践两方面就常见缺陷形成原因及预防措施做了简要分析。
1 青线形成原因及预防青线是指钢管表面沿长度方向有一条突起的直线。
青线产生的主要原因有:孔型设计时椭圆度过小、宽展量不合理,使钢管在轧制时金属过充满后被挤入辊缝,形成青线;轧辊沿轴向窜动,由于固定轧辊轴向移动的螺栓(或圆螺母)松动,使得轧辊可以沿轴向移动,造成辊面在辊缝处形成台阶,在钢管轧制时,形成青线。
为了预防青线出现,应根据生产现场情况,分析产生青线的原因。
首先检验每个机架轧辊是否在轴向窜动,如果有个别轧辊轴向窜动,则应维修轧辊机架,消除轧辊机架的窜动因素,随后重新修正孔型尺寸,进行轧制,最后检验产品是否合格。
电阻焊张力减径钢管的切削性能研究
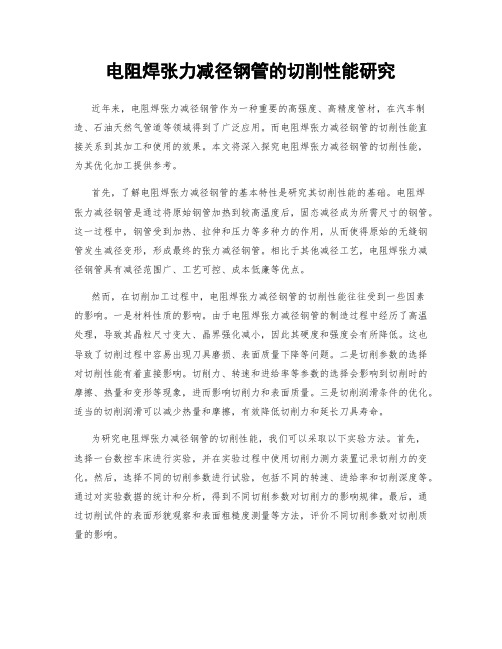
电阻焊张力减径钢管的切削性能研究近年来,电阻焊张力减径钢管作为一种重要的高强度、高精度管材,在汽车制造、石油天然气管道等领域得到了广泛应用。
而电阻焊张力减径钢管的切削性能直接关系到其加工和使用的效果。
本文将深入探究电阻焊张力减径钢管的切削性能,为其优化加工提供参考。
首先,了解电阻焊张力减径钢管的基本特性是研究其切削性能的基础。
电阻焊张力减径钢管是通过将原始钢管加热到较高温度后,固态减径成为所需尺寸的钢管。
这一过程中,钢管受到加热、拉伸和压力等多种力的作用,从而使得原始的无缝钢管发生减径变形,形成最终的张力减径钢管。
相比于其他减径工艺,电阻焊张力减径钢管具有减径范围广、工艺可控、成本低廉等优点。
然而,在切削加工过程中,电阻焊张力减径钢管的切削性能往往受到一些因素的影响。
一是材料性质的影响。
由于电阻焊张力减径钢管的制造过程中经历了高温处理,导致其晶粒尺寸变大、晶界强化减小,因此其硬度和强度会有所降低。
这也导致了切削过程中容易出现刀具磨损、表面质量下降等问题。
二是切削参数的选择对切削性能有着直接影响。
切削力、转速和进给率等参数的选择会影响到切削时的摩擦、热量和变形等现象,进而影响切削力和表面质量。
三是切削润滑条件的优化。
适当的切削润滑可以减少热量和摩擦,有效降低切削力和延长刀具寿命。
为研究电阻焊张力减径钢管的切削性能,我们可以采取以下实验方法。
首先,选择一台数控车床进行实验,并在实验过程中使用切削力测力装置记录切削力的变化。
然后,选择不同的切削参数进行试验,包括不同的转速、进给率和切削深度等。
通过对实验数据的统计和分析,得到不同切削参数对切削力的影响规律。
最后,通过切削试件的表面形貌观察和表面粗糙度测量等方法,评价不同切削参数对切削质量的影响。
在实验进行过程中,我们需要注意以下几点。
首先,要选择合适的切削润滑剂,并在不同实验条件下加以比较。
其次,在实验过程中要及时记录切削力的变化,并进行数据的准确统计。
电阻焊张力减径钢管的力学性能研究
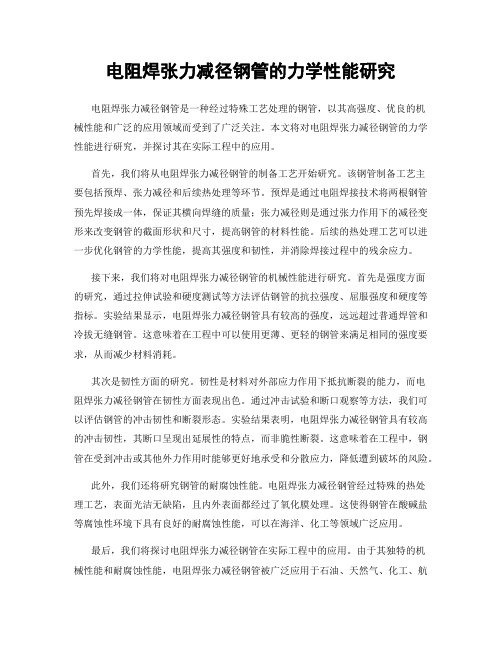
电阻焊张力减径钢管的力学性能研究电阻焊张力减径钢管是一种经过特殊工艺处理的钢管,以其高强度、优良的机械性能和广泛的应用领域而受到了广泛关注。
本文将对电阻焊张力减径钢管的力学性能进行研究,并探讨其在实际工程中的应用。
首先,我们将从电阻焊张力减径钢管的制备工艺开始研究。
该钢管制备工艺主要包括预焊、张力减径和后续热处理等环节。
预焊是通过电阻焊接技术将两根钢管预先焊接成一体,保证其横向焊缝的质量;张力减径则是通过张力作用下的减径变形来改变钢管的截面形状和尺寸,提高钢管的材料性能。
后续的热处理工艺可以进一步优化钢管的力学性能,提高其强度和韧性,并消除焊接过程中的残余应力。
接下来,我们将对电阻焊张力减径钢管的机械性能进行研究。
首先是强度方面的研究,通过拉伸试验和硬度测试等方法评估钢管的抗拉强度、屈服强度和硬度等指标。
实验结果显示,电阻焊张力减径钢管具有较高的强度,远远超过普通焊管和冷拔无缝钢管。
这意味着在工程中可以使用更薄、更轻的钢管来满足相同的强度要求,从而减少材料消耗。
其次是韧性方面的研究。
韧性是材料对外部应力作用下抵抗断裂的能力,而电阻焊张力减径钢管在韧性方面表现出色。
通过冲击试验和断口观察等方法,我们可以评估钢管的冲击韧性和断裂形态。
实验结果表明,电阻焊张力减径钢管具有较高的冲击韧性,其断口呈现出延展性的特点,而非脆性断裂。
这意味着在工程中,钢管在受到冲击或其他外力作用时能够更好地承受和分散应力,降低遭到破坏的风险。
此外,我们还将研究钢管的耐腐蚀性能。
电阻焊张力减径钢管经过特殊的热处理工艺,表面光洁无缺陷,且内外表面都经过了氧化膜处理。
这使得钢管在酸碱盐等腐蚀性环境下具有良好的耐腐蚀性能,可以在海洋、化工等领域广泛应用。
最后,我们将探讨电阻焊张力减径钢管在实际工程中的应用。
由于其独特的机械性能和耐腐蚀性能,电阻焊张力减径钢管被广泛应用于石油、天然气、化工、航空航天等领域。
在输送管道方面,其高强度和良好的耐腐蚀性能可以有效降低管道的重量和成本,并提高输送效率和安全性。
钢管张力减速机的减径理论及工艺参数-未成稿

钢管张力减径机的减径理论及工艺参数太原重型机器有限公司技术中心轧钢所汤智辉前言张力钢管减径是钢管生产中的一项重大的发展,世界各国都十分重视。
张力减径机已经愈来愈广地得到应用。
用一般不带张力的减径机来生产小直径钢管,已经有很多年的历史了。
但是,由于减径出来的钢管壁厚增加、横向壁厚不均比较严重,减径管的质量不能令人满意;同时由于减径量较小,需要比较多的机架,因此,这种减径机应用范围多半局限在生产轧管机组不能或不容易直接生产的小直径钢管。
在一般减径机上,单架减径理只有3~5%,而在张力减径机上,单架减径量可以达到12~14%。
张力减径时,在减小直径的同时可以使钢管壁厚减薄或者保持不变,减径过程稳定并且钢管的横向壁厚不均也比较小。
因此,张力减径就成了生产薄壁小直径钢管的有效方法。
此外,由于张力减径时的变形量大,所需要的机架数目可以显著减少,因而使减径管的规格范围日益扩大。
这样,减径机就不仅用来生产小直径钢管,同时也用来生产较大规格的钢管。
在这种情况下,前面的轧管机组就可以只生产少数几种生产北最高、最便于生产的规格,通过张力减径机得到各种尺寸的成品管,从而大大提高了机组的生产能力,简化了生产。
目前,只要是在无缝钢管生产中,不论在连续生产还是单根钢管生产中,也不论在轧钢机还是在挤压机后,都广泛安设了张力减径机。
因此,可以说:张力减径机已经成为钢管生产中应用最广泛的设备之一。
张减理论一、 管材的壁厚变化与延伸在张力减径时过程中,管材的壁厚减薄与延伸,既发生在减径机的各机架上,也同样发生在减径机各机架之间。
㈠ 在机架上的变形当管材在机架上受压时,直径和壁厚都发生变化。
如果说直径的变化完全决 定于孔型的尺寸,那么壁厚的改变则同其它一些因素(张力、壁厚与直径之比等)有关。
现以管材在变形区的一个单元体为例,对其应力状态进行分析。
径向应力 σr 、切向应力σq 、轴向应力σx 在管材断面和在变形区的分布都是不均匀的。
这可以从管材出入口断面的应力不相等,和内外表面的应力不相等可以看出。
无缝钢管张减过程张力对壁厚分布的影响

无缝钢管张减过程张力对壁厚分布的影响
无缝钢管对精密的加工作业和高要求的测量工作性能和精度提出来的要求越来
越高。
然而,无缝钢管在张减过程中经常出现壁厚不均匀分布,这不仅会降低无缝钢管的性能,而且会使整个张减过程变得方向与困难。
因此,对无缝钢管张减过程张力对壁厚分布的影响进行研究是很有必要的。
首先,要确定无缝钢管张减过程张力对壁厚分布的影响,需要两个重要的参数:受力角度和受力面积。
由于无缝钢管的碳含量不同,其受力面积也不同,因此采用无缝钢管所能承受的最大张力大小也随着钢管的碳含量和受力面积的变化而变化。
此外,无缝钢管张减过程中张力分布也会影响壁厚分布,张力强度越大,产生
的壁厚偏差越大。
因此,针对无缝钢管张减过程,必须准确控制张力的分布,以保证壁厚的均匀性。
另外,在无缝钢管的张减过程中,张力的大小也会和外力的类型有关系,例如
轮模张减可以使得张力更加均匀,而拉模设计的受力角度也会比均角设计更大以及滚筒等设备可以通过张力控制来弥补模具设计的角度误差等,因此,正确控制外力的张紧,可以有效地改善无缝钢管的壁厚分布。
通过以上分析可以得出,无缝钢管张减过程张力对壁厚分布的影响是很明显的。
正确控制受力面积、受力角度以及外力的类型和张紧度,可以明显降低壁厚偏差,保证无缝钢管的性能和精度。
无缝钢管张力减径过程中内六方的成因分析及解决办法
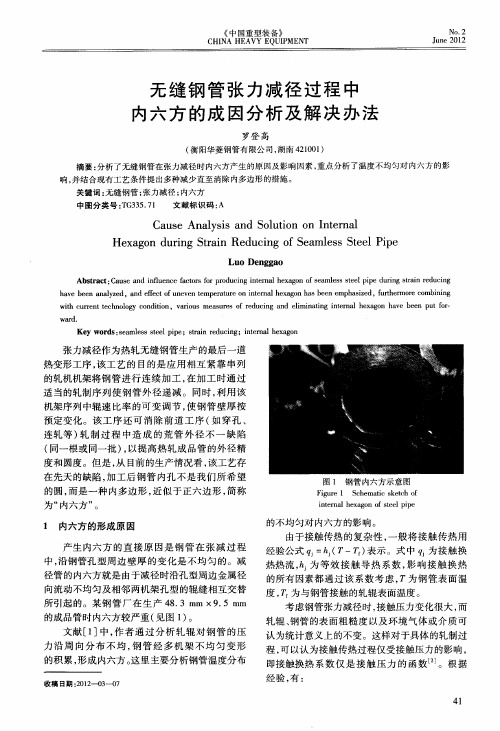
及 传 动上 的方便 , 邻 机架上 下倒 置摆 放 , 相 这相 当 于将 轧辊 每 次 旋 转 6 。 正 是 这 种 布 置 使 钢 管 的 0, 壁 厚变 化趋 势 叠 加 。如 果 采 用 不 同角 度 布 置 , 最
机 架叠 加后 , 管 金 属 在 沿 轧辊 孔 型 方 向流 动 不 钢 均 匀 。钢管 在 减 径 过程 中 , 薄 的部 位 在 不 断 减 减
2 解 决措 施
薄 , 厚 的部 位 在不 断增 厚 。如果 钢 管 此 时 能 产 增
生 一定 角度 的旋 转 , 则增 厚 和减 薄趋 势不会 叠 加 , 这 样金 属在 沿 轧 辊孔 型方 向 的流 动 趋 于 均 匀 , 内 六 方 问题将 得 到根本 上 的解决 。
中, 沿钢 管孔 型 周 边 壁 厚 的 变 化是 不 均 匀 的。减
的不 均 匀对 内六 方 的影 响。
由于接触传热的复杂性 , 一般将接触传热用
经验 公式 q =h( ) 示 。式 中 g 为 接触 换 iT— 表 i
热热 流 ,; 等 效 接 触 导 热 系数 , 响 接 触 换 热 h为 影
41
No. 2
J n 0l u e2 2
《 中国重型装备》 C N E V Q IME T HIA H A Y E U P N
单机架 轧 制后
第 二机架 轧制 后
图 2 沿 16周长 的 q 分布 图 / ;
F g r q it b t n ao g 1 6 p rmee iue2 Jdsr u i ln / e i tr i o
wih c re e hn l g o diin, v ro s t u r ntt c o o y c n to a iu me s r s o e u i g a d e i ia i ne a h x g n a e e n p fr a u e f r d c n n lm n tng i tr l e a o h v b e uto — n
微张力减径机轧后钢管产生青线的原因分析

收稿 日期 :o 5一 8一 5 2o O O
前言
突出 , 一般称 之 为青 线 。 可 能产 生 青 线 的原 因很
钢管 微张 力减 径机 主要 是针 对轧 后荒 管进 行
多: 如轧制速度制度的不合理 , 孔型的宽展量设置 太小 , 轧辊 的倒 角过 大 , 因材质 原 因而导致 的倒 或 角破碎等都可不同程度的造成青线缺陷。
2 工艺 因素 的排 除
Ch n F n e eg
Ab t a t Th 8 o h tp o u e e b a k t r a n t e s e b u i g t e rl n rc s y te 1 t n s s r c : e I 8 n t a r d c d t l c e d o t lt e d r o i g p o e sb 4 sa d  ̄ h h h e u n h l h mir c o—t n in r d cn m i a e n a ay e so e u i g— — h s b e n l ̄ l l i i r de n t s a t .wh c n ia e h ti i a s y o e oe a c - h i i h i d c ts ta t s c u e b v rtlr n e ma d
的 , 乎该 产 品的生 产工 艺 要求 。 合
出 直 状 耋 因棱上的金属变形程度和其 3~一 制 素 … ’ 现 线 的 曼 凸 棱 兰 孔 车因的除 的金属不 同, 因而这部分金属 的颜色 比较
该减 径机 为 三辊 Y型减 径机 , 三个 轧辊 呈
l孔型直径/ m l8 8 l5 4 l 18 18 1 o .4 l 10 9 .6 9 .3 9 .8 9 .4 8 .7 m 1 .2 l .9 l .o 0 . l 4 5 2 O .9 7 7 4 5 18 0 1 9 8 l l 轧辊转 速// i 5 . 6 .5 6 .l 6 .5 7 .0 7 .7 7 .9 7 .8 7 .4 8.3 8 .l r n 84 a r 0 o1 37 68 02 2 1 43 72 92 O2 O5
张力减径张力系数对无缝钢管壁厚不均的影响
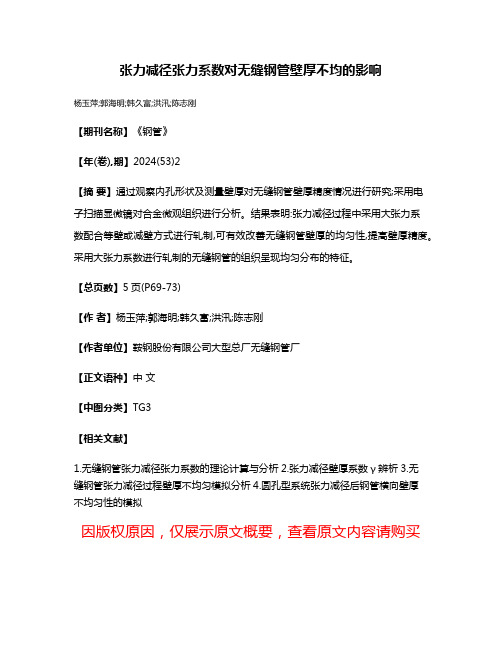
张力减径张力系数对无缝钢管壁厚不均的影响
杨玉萍;郭海明;韩久富;洪汛;陈志刚
【期刊名称】《钢管》
【年(卷),期】2024(53)2
【摘要】通过观察内孔形状及测量壁厚对无缝钢管壁厚精度情况进行研究;采用电子扫描显微镜对合金微观组织进行分析。
结果表明:张力减径过程中采用大张力系
数配合等壁或减壁方式进行轧制,可有效改善无缝钢管壁厚的均匀性,提高壁厚精度。
采用大张力系数进行轧制的无缝钢管的组织呈现均匀分布的特征。
【总页数】5页(P69-73)
【作者】杨玉萍;郭海明;韩久富;洪汛;陈志刚
【作者单位】鞍钢股份有限公司大型总厂无缝钢管厂
【正文语种】中文
【中图分类】TG3
【相关文献】
1.无缝钢管张力减径张力系数的理论计算与分析
2.张力减径壁厚系数γ辨析
3.无
缝钢管张力减径过程壁厚不均匀模拟分析4.圆孔型系统张力减径后钢管横向壁厚
不均匀性的模拟
因版权原因,仅展示原文概要,查看原文内容请购买。
- 1、下载文档前请自行甄别文档内容的完整性,平台不提供额外的编辑、内容补充、找答案等附加服务。
- 2、"仅部分预览"的文档,不可在线预览部分如存在完整性等问题,可反馈申请退款(可完整预览的文档不适用该条件!)。
- 3、如文档侵犯您的权益,请联系客服反馈,我们会尽快为您处理(人工客服工作时间:9:00-18:30)。
包头钢铁职业技术学院学生毕业论文论文题目:张力减径机对无缝钢管造成的质量影响及处理专业:冶金技术班级:冶金(2)班学生:仲禹琨指导教师:***日期:2010 年3 月15日目录内容摘要 (01)前言 (01)1 机组的概况及流程 (01)1.1 机组的概况 (01)1.2 工艺流程 (02)1.3 14架定减径机组定减径的工艺目的 (02)2 况及产生的原因 (05)2.1 定减径区主要缺陷 (05)2.1.1结疤 (05)2.1.2麻面 (07)2.1.3青线 (07)2.1.4轧折 (11)2.1.5长度超差、直径超差、壁厚超差 (11)2.2 确定轧机调整是正确的条件标准 (13)3实施结果 (13)4结论 (14)5参考文献 (14)张力减径机对无缝钢管质量造成的影响及处理[内容摘要]介绍了包头市无缝钢管厂阿塞尔轧管机组生产Φ120m无缝钢管的工艺技术的改进情况,通过对轧制工具的改进及工艺参数的调整和辅助设备的改造,生产出符合现行产品标准要求的流体用无缝钢管和结构用无缝钢管及低、中压锅炉用无缝钢管。
关键词张力减径机机架工艺参数转速孔型表前言包头市无缝钢管厂热轧管生产线的核心设备是引进德国曼内斯曼·米尔公司的具有九十年代初世界先进水平的阿塞尔轧管机组,它与国内配套的Φ16M中径的环形加热炉、菌式穿孔机、十四机架二辊定径机、再加热炉、60M步进式冷床,以及相应的精整设备和检测设备构成产品范围为Φ25~Φ141mm的热轧管生产线。
随着钢管市场竞争的日益激烈,企业要生存就得结合本企业工艺技术和装备水平的条件,尽一切可能充分挖掘设备的潜能,以提高整体装备综合能力为手段,以追求效益最大化为目标,开发生产适销对路的产品。
为了适应市场竞争的需求,我们在现有设备条件基础上充分挖掘设备潜能对无缝钢管质量问题作出改进本文只对张力减径机部分做详细论证及分析。
和改进通过实验得出的结果。
1.机组概况及流程1.1机组概况:该厂使用的张力减径机设备结构紧凑、控制系统目前比较先进,工艺调整方便,轧制的外径精度高,规格品种适应性强,是操作和使用方便精确的机型,主减速机14个输出轴与C形主机座之间有14根安全联轴器相连。
安全联轴器中设置有(安全销),当轧制力矩超过一定范围后(安全销被剪断,动力无法传递,从而其到保护设备的作用。
减径机轧辊理想直径为(Φ420) mm,轧辊辊身宽度为(180)mm,机架间距为(400)。
减径机主减速机第(1~3)架速比为17.953,第(4~6)架速比为17.664,第(7~8)架速比为17.137,第(9~10)架速比为16.688,第11~14架速比为16.192。
1、减径机前摆动辊道由辊道、(升降台架)及驱动装置等组成。
为了保证不同规格的荒管(即荒管中心线变化)能够顺利进入减径机(即轧制中心线固定)轧制,在进入减径机前,要对荒管在辊道上的高度进行调整,由(摆动辊道)实现。
1.2 工艺流程;(图1)1.314架定减径机组定减径的工艺目的钢管的定减径过程是从被Aeesl轧管机轧制后的钢管(经再加热或不经再加热)在14架定减机组上连续轧制的过程。
定减径的目的是,在一定的急减以采用一种规格管材能够生产多种规模成品管的任务。
Ф140mmAssel轧管机组定减径采用14架单独转动的微张力定减径机组,除了上述要求外,还要求定减径后的钢管外表面光洁、无划痕等,进一步改善钢管的外表面质量。
最大总减径率微35%,单机架减经率最大3.5%。
定减径机的轧辊孔型设计孔型设计根据轧制表给定地毛管和成品管地尺寸,求出总变形量(总减径率、总延伸系数)选定单机架减径率,求出所需机架数目:n=ln(Dn/De)/in(1-εD)+qn---机架数目Dn De---定径后、定径前钢管外径εD ---平均单机架减径率q---减径率较小时机架地折合数q一般取2减径率地分配分配各机架减径率,求出各机架孔型的平均直径Di,通常第一架减径率约为平均减径率的50%左右,以适应来料尺寸波动,成品前二架为平均减径率的一半,成品前一架即成品机架一般没有减径率,以保证成品钢管的外径尺寸精度及其圆度,其余机架的减径率平均,由此,便可求出孔型的标准直径Di:εi=(Di-1-Di)/D(i-1)D2=(D1(1-ε2))…D13=(D12(1-ε13))这样,根据孔型系列,便可确定孔型其他尺寸及相应得加工孔型的工具尺寸。
<文献1>张减速度制度原理钢管的张减过程是在一定张力的条件下,将来自脱管机的荒管轧制成符合成品外径和壁厚尺寸要求的钢管。
整个过程是一个空心体连轧的过程,机架间的张力需要在一定压下率下,在电机允许的范围内调速实现。
在张减机轧制的过程中,现场工艺参数调节相对较少,张力的控制也受孔型(减径率)的制约,所以在轧制过程中,只能在秒流量相等的原则下,通过合理调节主叠加电机的转速来保证一定张力,进行壁厚微调(一般不会超过l mm)。
<文献2>质量检查概括:张减中容易引起的缺陷有:◆结疤其原因是出再加热炉时,氧化铁皮粘结在硬杂质残留在管面上,在张减机中压入表层而引起(加强除鳞效果)。
◆麻面主要由轧辊孔型磨损引起,轻者通过修磨孔型来解决,严重要换辊。
◆轧折主要是单机压下率过大,辊缝设置不正确,还与孔型的正负宽展,速度制度不匹配引起。
◆直径超差由孔型设计不当、孔型磨损或轧机调整不正确所引起。
这时起一定的椭圆度的增加,所以要根据成品的公差范围和~定的椭圆偏信值来合理选定调整,如果不行,则应更换机架。
◆壁厚偏差主要由来料尺寸波动和各机架张力系数设置不当引起。
主要措施是严格控制来料尺寸波动,并根据壁厚超差设置相应的速度制度。
下面重点单独介绍两种常见的质量缺陷:a.内六方缺陷定义:当在张减机中轧制总减径量较大的厚壁管时,内部形状可能会出现六角形,通常这种轧制缺陷我们称作内六方缺陷,这种轧制缺陷是由轧制中实际情况决定的。
机理:在实际轧制中,沿管圆周截面压下量不同,造成张力不同,而形成的不均匀壁厚造成了内六角。
通常孔型底部压下量大,大部分接触区处在前滑区,形成的张力较大,管壁容易拉簿。
在前后机架成60度布置的孔型中,有六个点被反复地加工,增厚减簿,最后总体趋势仍然是减簿,而在孔型底部顶点左右30度处,相对孔型底部金属来说形成一段内六角增厚段,这就形成了内六方缺陷。
方案:通常这种缺陷是可以通过合适的孔型来消除的,其实质就是沿管周方向建立合适的张力条件,通过改善轧辊接触轧件的长度来改善张力条件,保证管周有均匀张力。
b.青线定义:这是在轧制中辊缝处形成的一种纵向的轧制痕迹,俗称青线。
机理:由于减径率太大,而在辊缝处形成的。
一般在前一机架轧制时件宽展量,如果连续几个机架都出现这种情况,很容易出现过充满。
这时,除了表面青线存在外,还可能出现轧件内部轧折。
一般在孔型中可以通过合适的宽展有效改善。
方案:选择椭孔型用负宽展轧制,尽可能用小的单机架减径率分配方案(具体根据提供的孔型特点选择) <文献3>(图2)2、质量状况及缺陷产生原因(张力减径机部分对无缝钢管造成的问题造成的主要缺陷及原因):2.1、定减径区主要缺陷有:结疤、麻面、青线、轧折、断裂、钢管长度超差、直径超差、壁厚超差、壁厚不均等一些常见的问题这些问题是直接影响无缝钢管的质量的重要的原因,通过改造完成以后,虽然产品的质量比以前有了很大的提高,但在实际生产中影响产品质量的因素依然存在,主要以结疤、麻面、青线、轧折、断裂、钢管长度超差、直径超差、壁厚超差,这些因素的存在,有时使一部分用户对我厂的产品质量提出异议,但从所有用户的反馈信息看,我厂的产品质量还是赢得了用户的认可。
针对产品的这些缺陷做如下分析。
2.1.1结疤:造成结疤的原音有许多主要的原因,通过对积累的数据分析认为产生原因有如下几种:1)设备方面的原因该厂使用的张力减径机机架是由山西太原制造的,由于国内该技术有限造成的机架在加工过程中就产生了问题我们都知道荒管在通过张力减径机时必须保证所有参与轧制变形的机架必很大造成机架在放入主机时高低不平导致轧制中心线不一致造成管子质量问题而结疤就是其中一种。
为了拟补该设备造成的问题结合实际的情况针对此类问题做如下方案:根据该设备造成问题的原因主要就是轧制中心线不一致解决方案利用填补机架之间的差距来解决,具体操作的方法是找出与其他机架不一致的机架利用高度差用等厚的薄铁板或锯带来填补空余的部分,此方法简单实用。
2)由于荒管的原因造成的该原因主要是由于荒管的外经太大主要是头部的外经太大造成荒管与轧辊接触时不能顺利的咬人而是撞在轧辊上造成轧辊掉肉或是荒管掉肉总之掉下的部分会随轧辊转动最终导致粘在管子的表面形成结疤,对于该种原因造成的结疤可以预防:要控制好钢的温度(840-880之间)控制荒管的外径前后配合完成轧制。
还有最重要的一点是注意机架的合理选取和排放。
结疤产生的原因还很多这里就做主要的问题来分析解决3)减径机的入口导嘴如果没有打磨光滑,且必须和荒管配套才能正常的进入减径机不会出现卡钢、划伤、结疤等问题。
<文献4>下图为减径机的导嘴图:(2.1.2、麻面:产生麻面的原因很简单就是两种可能:1)除磷系统出现故障造成除磷不干净除不净等现象,在出现此种情况下可以启动后被系统。
2)再者就是由于钢管在炉子里高温加热时间过长早成外表面的氧化铁皮过多不能被除磷机很好的除净经过减径机架在轧辊作用下造成了麻面,这种情况有时候是难免的因为有时候由于故障钢管不能及时的出炉造成长时间高温加热导致的氧化铁皮过厚不能被除磷机除去,出现这种情况的时候应该同时开启两个除磷泵同时工作来解决该问题。
3)由于轧辊磨损引起或由于在再加热炉中钢管过氧化或由于定径机前入口除鳞机除鳞效果不好而引起的。
解决办法:轻者可通过修磨孔型或处理除鳞机来解决,严重时要分别情况处理:通过更换轧辊、减小再加炉热温度及荒管的在炉时间或处理除鳞机的水压和喷嘴可以解决。
2.1.3青线:在轧制中辊缝处形成的一种纵向的轧制痕迹,俗称青线。
青线是无缝管存在的最普遍最常见的问题产生原因:1)定、减径机减径率过大。
主要是由于机架搭配不当早成的单架的减径量太大造成无缝钢管在表面产生一条或多条青线,经过分析得出原因就是所使用的机架过少而需要的单架减径量过大造成的此时必须制定合理的工艺安排制订好一套配套的孔型表来,这样可以解决和避免由于该种原因造成的青线。
以下为孔型配合的一套数据:A)七架定径机组变形量分配,定径孔型如图:(图3)单位:毫米序号平均直径孔高孔宽偏心距孔型半径倒角辊缝椭圆度Dc A B eR rΔζ0 236.001 234.58 231.08 238.07 3.55 119.09 16 7 1.03(表1)2)定、减径机孔型错位或磨损严重,该种情况就是属于设备的原因了,前面提到的设备加工的误差大技术水平落后造成的单架机架稳定性非常的差会经常的突发性没有任何预兆的辊撺位造成的青线,该问题因为属于随即的问题只能要求操作人员精心操作及时的发现问题及时的更换机架。