水煮花生工艺流程
水煮花生米的小窍门
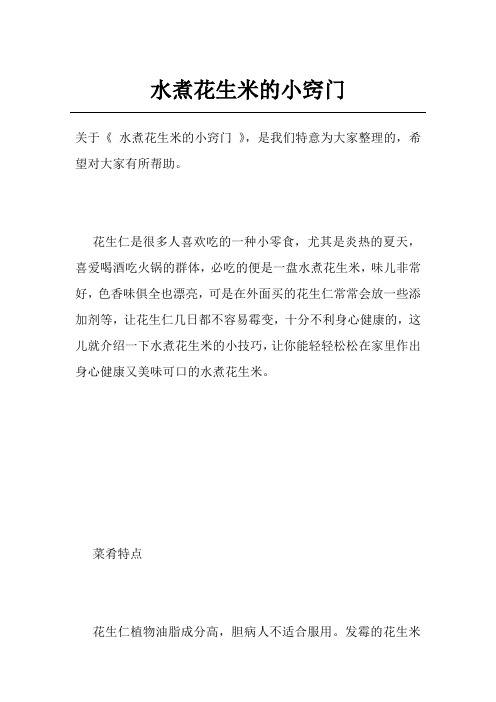
水煮花生米的小窍门关于《水煮花生米的小窍门》,是我们特意为大家整理的,希望对大家有所帮助。
花生仁是很多人喜欢吃的一种小零食,尤其是炎热的夏天,喜爱喝酒吃火锅的群体,必吃的便是一盘水煮花生米,味儿非常好,色香味俱全也漂亮,可是在外面买的花生仁常常会放一些添加剂等,让花生仁几日都不容易霉变,十分不利身心健康的,这儿就介绍一下水煮花生米的小技巧,让你能轻轻松松在家里作出身心健康又美味可口的水煮花生米。
菜肴特点花生仁植物油脂成分高,胆病人不适合服用。
发霉的花生米不能吃。
作法一1、把调料与花生仁放进1000ml凉水中一起煮;2、中火烤开,文火慢煮;3、20分钟后添加盐再煮10分钟;4、最终用大火收汁,熟花生仁在锅中焖一会儿;5、盛起摆盘,当零食下葡萄酒都可以。
作法二在花生仁的众多食用方法中以煮为最好。
水煮花生米是花生仁非常简单、最科学研究的食用方法,它能完好无损的储存花生仁的营养元素,并且味儿十分美味。
水煮花生米米的做法尽管非常简单,可是要煮的入味道還是要有小技巧的。
要是把握一点,就可以在短期内内,作出很进味﹑正宗的农家院花生仁的味儿。
这重要的一点方法便是:把花生仁前边的一头,用大拇指和无名指轻轻地按一下,花生仁壳就开裂一个小口子,那样煮的情况下不但节约时间,并且料汁的味儿就非常容易的到里边来到。
原材料:2斤花生仁,2个八角,2勺盐,1块八角茴香。
1、花生仁自来水清理干净,洗到沒有细沙沉定才行。
2、用大拇指和无名指轻轻地按花生仁前边的一头,使花生仁壳开裂一个小口子。
先后把全部的花生仁都按开一个小口子,那样煮的情况下较为非常容易入味道。
3、把解决好的花生仁,倒进压力锅里边。
4、放水进来,水和花生仁的占比1:1就可以。
5、放进一块八角茴香,2个八角(喜爱口重的,家中有哪些香辛料都能够放点进来,喜爱辣的能够放好多个辣椒干一起煮)。
6、放进4勺盐,大约20克。
一斤花生仁10克盐较为适合。
7、用铁铲把花生仁拌和一下,使盐与花生仁混和的较为匀称。
水煮花生的制作方法
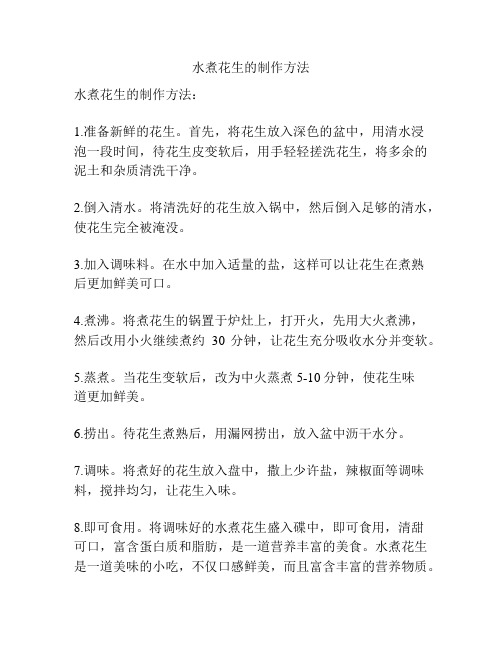
水煮花生的制作方法水煮花生的制作方法:1.准备新鲜的花生。
首先,将花生放入深色的盆中,用清水浸泡一段时间,待花生皮变软后,用手轻轻搓洗花生,将多余的泥土和杂质清洗干净。
2.倒入清水。
将清洗好的花生放入锅中,然后倒入足够的清水,使花生完全被淹没。
3.加入调味料。
在水中加入适量的盐,这样可以让花生在煮熟后更加鲜美可口。
4.煮沸。
将煮花生的锅置于炉灶上,打开火,先用大火煮沸,然后改用小火继续煮约30分钟,让花生充分吸收水分并变软。
5.蒸煮。
当花生变软后,改为中火蒸煮5-10分钟,使花生味道更加鲜美。
6.捞出。
待花生煮熟后,用漏网捞出,放入盆中沥干水分。
7.调味。
将煮好的花生放入盘中,撒上少许盐,辣椒面等调味料,搅拌均匀,让花生入味。
8.即可食用。
将调味好的水煮花生盛入碟中,即可食用,清甜可口,富含蛋白质和脂肪,是一道营养丰富的美食。
水煮花生是一道美味的小吃,不仅口感鲜美,而且富含丰富的营养物质。
花生含有丰富的蛋白质、维生素B、维生素E、核黄素、烟酸等,有利于增强人体免疫力,提高脑部活力,有益于心血管健康,还能帮助预防糖尿病等慢性疾病。
因此,水煮花生成为许多人喜爱的早餐或零食之一。
除了直接食用之外,水煮花生还可以作为许多菜肴的主要材料之一,如凉拌花生、花生浸豆腐、花生糊等等。
它不仅美味可口,而且能够增加菜肴的营养价值。
而且制作过程并不复杂,下面将来介绍如何用水煮花生来制作另外一款美味佳肴——花生糊。
首先准备水煮花生,然后将水煮花生放入锅中加水煮熟再过滤干水分后放入搅拌机打成花生酱状,这样就可以做成花生糊。
在做花生糊的时候,还可以加入适量的白糖或冰糖,使得花生糊更加美味可口。
也可以根据个人口味加入一些可可粉或者巧克力粉来增加香味和口感。
除了花生糊之外,水煮花生还可以用于制作其他各种菜肴,比如凉拌花生,将煮好的花生去皮后切碎,然后加入适量盐、糖、醋、蒜末、生抽、辣椒油等调料拌匀即可,酸辣可口,爽口开胃。
另外一个常见的做法是花生拌豆腐,将水煮花生捣碎,浇在切好的嫩豆腐上,然后淋上香油,加入适量的盐和葱花即可。
一种水煮花生配制工艺方法
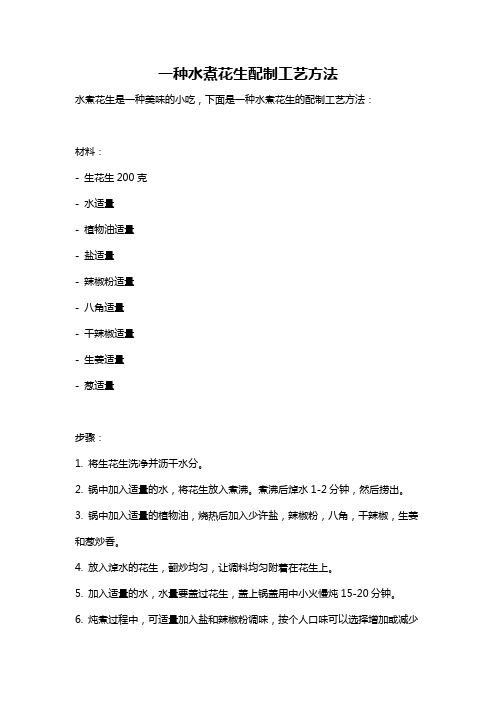
一种水煮花生配制工艺方法
水煮花生是一种美味的小吃,下面是一种水煮花生的配制工艺方法:
材料:
- 生花生200克
- 水适量
- 植物油适量
- 盐适量
- 辣椒粉适量
- 八角适量
- 干辣椒适量
- 生姜适量
- 葱适量
步骤:
1. 将生花生洗净并沥干水分。
2. 锅中加入适量的水,将花生放入煮沸。
煮沸后焯水1-2分钟,然后捞出。
3. 锅中加入适量的植物油,烧热后加入少许盐,辣椒粉,八角,干辣椒,生姜和葱炒香。
4. 放入焯水的花生,翻炒均匀,让调料均匀附着在花生上。
5. 加入适量的水,水量要盖过花生,盖上锅盖用中小火慢炖15-20分钟。
6. 炖煮过程中,可适量加入盐和辣椒粉调味,按个人口味可以选择增加或减少
辣椒的量。
7. 炖煮时间结束后,将花生取出装盘即可享用。
注意事项:
1. 煮沸生花生时,加入少许食盐可以提高花生口感。
2. 炒香调料时要用中小火,避免调料糊焦。
3. 炖煮过程中要随时加水,以免花生煮干。
4. 根据个人口味可以增加或减少辣椒粉和干辣椒的量。
这是一种简单的水煮花生配制工艺方法,你可以根据个人口味进行调整。
希望能帮到你!。
酱卤水煮花生米的工艺流程
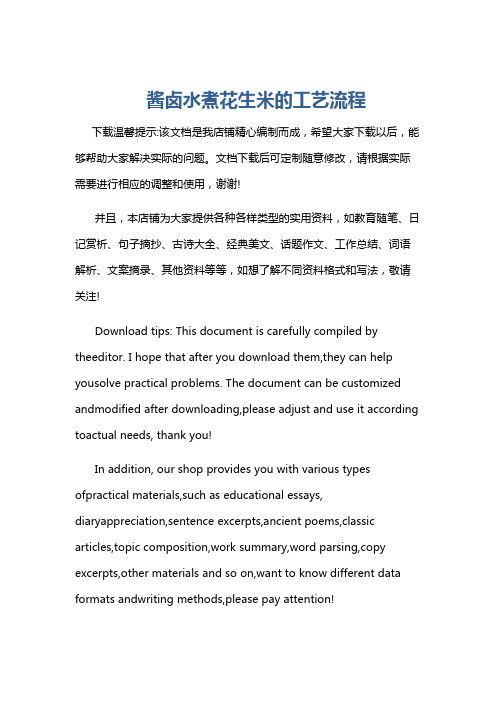
酱卤水煮花生米的工艺流程下载温馨提示:该文档是我店铺精心编制而成,希望大家下载以后,能够帮助大家解决实际的问题。
文档下载后可定制随意修改,请根据实际需要进行相应的调整和使用,谢谢!并且,本店铺为大家提供各种各样类型的实用资料,如教育随笔、日记赏析、句子摘抄、古诗大全、经典美文、话题作文、工作总结、词语解析、文案摘录、其他资料等等,如想了解不同资料格式和写法,敬请关注!Download tips: This document is carefully compiled by theeditor. I hope that after you download them,they can help yousolve practical problems. The document can be customized andmodified after downloading,please adjust and use it according toactual needs, thank you!In addition, our shop provides you with various types ofpractical materials,such as educational essays, diaryappreciation,sentence excerpts,ancient poems,classic articles,topic composition,work summary,word parsing,copy excerpts,other materials and so on,want to know different data formats andwriting methods,please pay attention!酱卤水煮花生米的工艺流程一、准备工作阶段。
在进行酱卤水煮花生米的制作之前,需要准备好所需的材料和工具。
花生需要煮多久
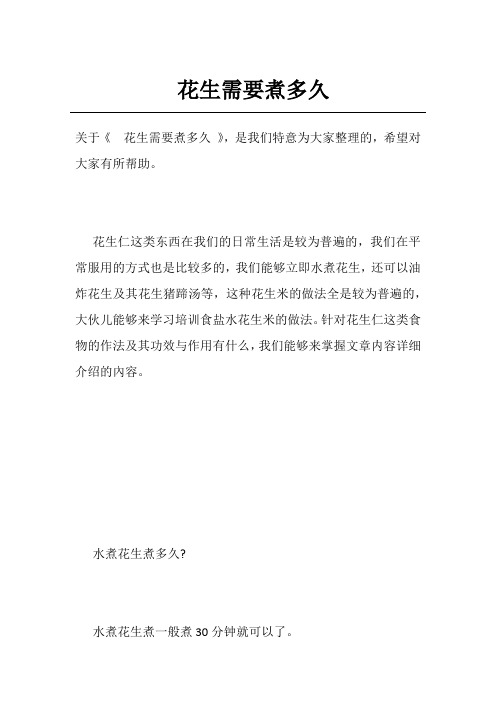
花生需要煮多久关于《花生需要煮多久》,是我们特意为大家整理的,希望对大家有所帮助。
花生仁这类东西在我们的日常生活是较为普遍的,我们在平常服用的方式也是比较多的,我们能够立即水煮花生,还可以油炸花生及其花生猪蹄汤等,这种花生米的做法全是较为普遍的,大伙儿能够来学习培训食盐水花生米的做法。
针对花生仁这类食物的作法及其功效与作用有什么,我们能够来掌握文章内容详细介绍的內容。
水煮花生煮多久?水煮花生煮一般煮30分钟就可以了。
水煮花生的作法原材料:2斤花生仁,2个八角,2勺盐,1块八角茴香。
作法:1、花生仁自来水清理干净,洗到沒有细沙沉定才行。
2、用大拇指和无名指轻轻地按花生仁前边的一头,使花生壳开裂一个小口子。
先后把全部的花生仁都按开一个小口子,那样煮的情况下较为非常容易入味道。
3、把解决好的花生仁,倒进压力锅里边。
4、放水进来,水和花生仁的占比1:1就可以。
5、放进一块八角茴香,2个八角(喜爱口重的,家中有哪些香辛料都能够放点进来,喜爱辣的能够放好多个辣椒干一起煮)。
6、放进4勺盐,大约20克。
一斤花生仁10克盐较为适合。
7、用铁铲把花生仁拌和一下,使盐与花生仁混和的较为匀称。
8、盖上外盖煮20分钟,煮开后不必马上开盖子,要再焖三十分钟再开盖子。
9、把花生仁捞出来,沥干水分,就可以吃完。
剩余的再次泡在汁里边,泡的情况下越久越进味。
做菜方法:1、花生仁一定要清理干净至泡在水里沒有细沙沉定哟,要不然就并不是盐水花生只是泥土花生仁了!2、在煮花生以前,把花生仁前边的一头,用大拇指和无名指轻轻地按一下,花生壳就开裂一个小口子,那样煮的情况下料汁的味儿就非常容易的到里边来到,花生米就能迅速进味。
3、煮花生的水不必扔掉,让花生仁自始至终泡在这个汁液里,吃的情况下取下一些。
4、吃剩的花生仁,要放到密封罐中放进电冰箱储存,储存的情况下倒进一些煮花生的汤,那样花生仁不容易变干。
花生的功效和功效花生仁做为普通百姓钟爱的传统式食品之一,从古至今就会有“长生果”的美名。
水煮花生多久才熟
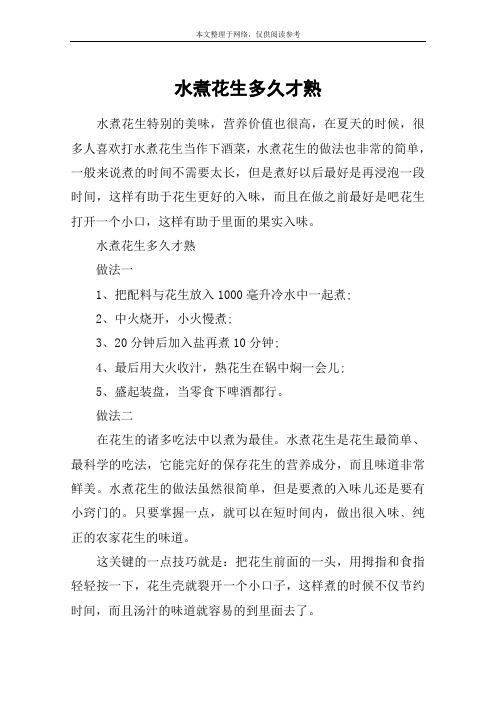
水煮花生多久才熟水煮花生特别的美味,营养价值也很高,在夏天的时候,很多人喜欢打水煮花生当作下酒菜,水煮花生的做法也非常的简单,一般来说煮的时间不需要太长,但是煮好以后最好是再浸泡一段时间,这样有助于花生更好的入味,而且在做之前最好是吧花生打开一个小口,这样有助于里面的果实入味。
水煮花生多久才熟做法一1、把配料与花生放入1000毫升冷水中一起煮;2、中火烧开,小火慢煮;3、20分钟后加入盐再煮10分钟;4、最后用大火收汁,熟花生在锅中焖一会儿;5、盛起装盘,当零食下啤酒都行。
做法二在花生的诸多吃法中以煮为最佳。
水煮花生是花生最简单、最科学的吃法,它能完好的保存花生的营养成分,而且味道非常鲜美。
水煮花生的做法虽然很简单,但是要煮的入味儿还是要有小窍门的。
只要掌握一点,就可以在短时间内,做出很入味﹑纯正的农家花生的味道。
这关键的一点技巧就是:把花生前面的一头,用拇指和食指轻轻按一下,花生壳就裂开一个小口子,这样煮的时候不仅节约时间,而且汤汁的味道就容易的到里面去了。
原料:2斤花生,2个八角,2勺盐,1块桂皮1.花生用水清洗干净,洗到没有泥沙沉淀为止。
2.用拇指和食指轻轻按花生前面的一头,使花生壳裂开一个小口子。
依次把所有的花生都按开一个小口子,这样煮的时候比较容易入味儿。
3.把处理好的花生,倒进高压锅里面。
4.加水进去,水和花生的比例1:1就可以。
5.放入一块桂皮,两个八角(喜欢口味重的,家里有什么香料都可以放点进去,喜欢辣的可以放几个干辣椒一起煮)。
6.放入4勺盐,大概20克。
一斤花生10克盐比较合适。
7.用铲子把花生搅拌一下,使盐与花生混合的比较均匀。
8.盖上盖子煮20分钟,煮熟后不要马上开锅盖,要再焖半小时再开锅盖。
9.把花生捞出来,控水,就可以吃了。
剩下的继续泡在汁里面,泡的时候越长越入味。
水煮干花生的做法是怎样?

水煮干花生的做法是怎样?
花生是一种很好的食材,不仅可以生吃,还可以有各种各样的加工方法,如油炸、熬汤、水煮等。
而且经过不同方法加工的花生,其口感也是不一样的的。
同时,花生的营养价值也特别高。
在这里,小编主要为大家介绍水煮花生的做法,当然该过程还需要很多其他的配料。
水煮花生保留了花生中植物活性物质,对防止营养不良,预防糖尿病、大肠癌、前列腺癌、乳腺癌及心血管病具有显著作用。
材料:新鲜花生2斤;清水适量;盐4勺;八角;桂皮;草果;花椒;干辣椒;陈皮;生姜;
做法及步骤
1、新鲜花生先用自来水冲洗干净外皮的泥土和沙粒。
准备好所有的调料。
2、锅里加入没过花生的清水,放入所有调料,煮开。
调入4——5勺盐(尝一下,水比平时炒菜的咸度要咸一些就好),盖盖,转中小火,30分钟。
3、关火后,再继续浸泡半个小时,会更加入味。
注意:1、2斤花生加足量水,觉得水开后算时间,煮30分钟口感刚刚好,这样吃稍微有点嚼头的,想软一点就适当延长煮制时间咯,生花生入味与否,在于浸泡的时间,浸泡时间越长越入味。
2、有一点需要特别注意的是,煮好的花生在20——30度的常温下,特别容易变质,煮好的花生,应放在保鲜盒里,倒入一
些煮花生的汤,放进冰箱冷藏保存,吃多少取多少。
虽然花生的营养价值很高,它可以帮助人们预防癌症、心血管、糖尿病等,但是需要注意的是,本身花生就比较容易感染黄曲霉菌,而黄曲霉素又是迄今为止最强的致癌物,所以吃煮熟的花生较为安全,且可以保留其营养成分。
水煮花生米要煮多久
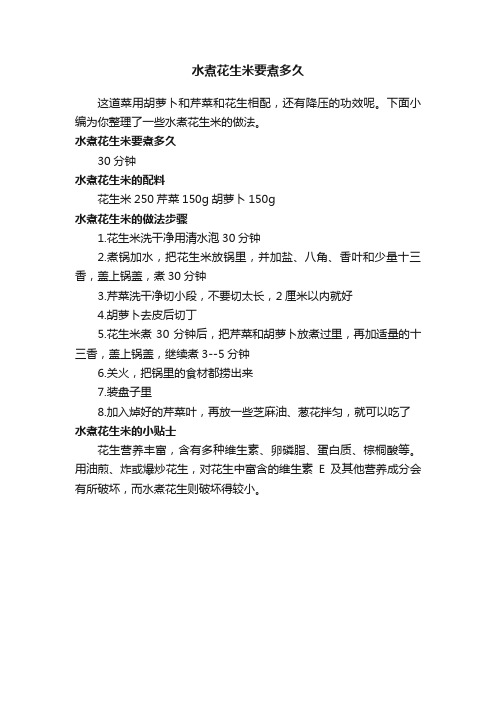
水煮花生米要煮多久
这道菜用胡萝卜和芹菜和花生相配,还有降压的功效呢。
下面小编为你整理了一些水煮花生米的做法。
水煮花生米要煮多久
30分钟
水煮花生米的配料
花生米250芹菜150g胡萝卜150g
水煮花生米的做法步骤
1.花生米洗干净用清水泡30分钟
2.煮锅加水,把花生米放锅里,并加盐、八角、香叶和少量十三香,盖上锅盖,煮30分钟
3.芹菜洗干净切小段,不要切太长,2厘米以内就好
4.胡萝卜去皮后切丁
5.花生米煮30分钟后,把芹菜和胡萝卜放煮过里,再加适量的十三香,盖上锅盖,继续煮3--5分钟
6.关火,把锅里的食材都捞出来
7.装盘子里
8.加入焯好的芹菜叶,再放一些芝麻油、葱花拌匀,就可以吃了水煮花生米的小贴士
花生营养丰富,含有多种维生素、卵磷脂、蛋白质、棕桐酸等。
用油煎、炸或爆炒花生,对花生中富含的维生素E及其他营养成分会有所破坏,而水煮花生则破坏得较小。
水煮花生米的正确做法

水煮花生米的正确做法水煮花生米是花生米最简单的一种做法,花生酥烂、咸鲜适口,是下酒菜不二的选择。
水煮花生米的原料非常简单,除了花生米之外,主要就是一些大料,有些做法中还会加入芹菜,色泽和口感都会得到提升,掌握了方法,就能在家经常享用到。
那么,水煮花生米的正确做法是什么?下面咱们就来看看吧。
水煮花生米1食材主料:花生米500g辅料:油适量、盐适量步骤1.这是已经泡了一晚上的花生米,因为中午煮,所以又泡了一上午。
里面放了大料一起泡的2.把花生米捞出来备用3.锅里坐上水4.将泡好的花生米倒入锅中5.大火煮开后转小火煮半个小时6.煮好后加入食盐,再泡一会儿,就可以出盘了。
小贴士花生米一定要多泡一些时候,不然不好吃哦水煮花生米2用料主料:花生500克调料:食盐2勺、八角2个、花椒1小、撮水适量、五香粉1勺、茴香籽1小撮水煮花生米的做法1.将花生仁清洗干净,放入碗中,加满清水,至少泡上2个小时2.将泡好的花生米放入锅中,加入盐和调料,混合均匀,加入足量的水,水沸之后转小火,大约20分钟至半个小时,待花生米煮熟入味,略焖一会儿,即可盛盘食用了营养价值1.促进人体的生长发育花生中钙含量极高,钙是构成人体骨骼的主要成分,故多食花生,可以促进人体的生长发育。
2.促进细胞发育,提高智力花生蛋白中含十多种人体所需的氨基酸,其中赖氨酸可使儿童提高智力,谷氨酸和天门冬氨酸可促使细胞发育和增强大脑的记忆能力。
3.抗老化,防早衰花生中所含有的儿茶素对人体具有很强的抗老化的作用,赖氨酸也是防止过早衰老的重要成分。
常食花生,有益于人体延缓衰老,故花生又有“长生果”之称。
4.润肺止咳花生中含有丰富的脂肪油、可以起到润肺止咳的作用,常用于久咳气喘,咯痰带血等病症。
5.凝血止血花生衣中含有油脂和多种维生素,并含有使凝血时间缩短的物质,能对抗纤维蛋白的溶解,有促进骨髓制造血小板的功能,对多种出血性疾病,不但有止血的作用,而且对原发病有一定的治疗作用,对人体造血功能有益。
水煮花生制造工艺流程
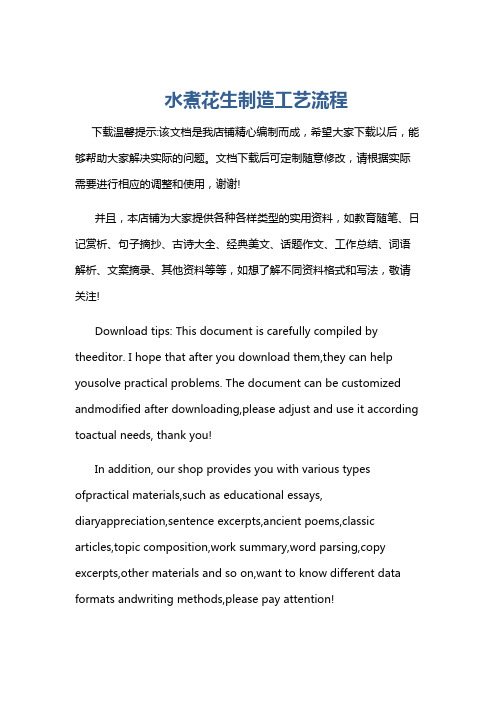
水煮花生制造工艺流程下载温馨提示:该文档是我店铺精心编制而成,希望大家下载以后,能够帮助大家解决实际的问题。
文档下载后可定制随意修改,请根据实际需要进行相应的调整和使用,谢谢!并且,本店铺为大家提供各种各样类型的实用资料,如教育随笔、日记赏析、句子摘抄、古诗大全、经典美文、话题作文、工作总结、词语解析、文案摘录、其他资料等等,如想了解不同资料格式和写法,敬请关注!Download tips: This document is carefully compiled by theeditor. I hope that after you download them,they can help yousolve practical problems. The document can be customized andmodified after downloading,please adjust and use it according toactual needs, thank you!In addition, our shop provides you with various types ofpractical materials,such as educational essays, diaryappreciation,sentence excerpts,ancient poems,classic articles,topic composition,work summary,word parsing,copy excerpts,other materials and so on,want to know different data formats andwriting methods,please pay attention!水煮花生制造工艺流程一、准备工作阶段在进行水煮花生的制造之前,首先需要准备好所需的原材料和工具。
水煮花生工艺流程
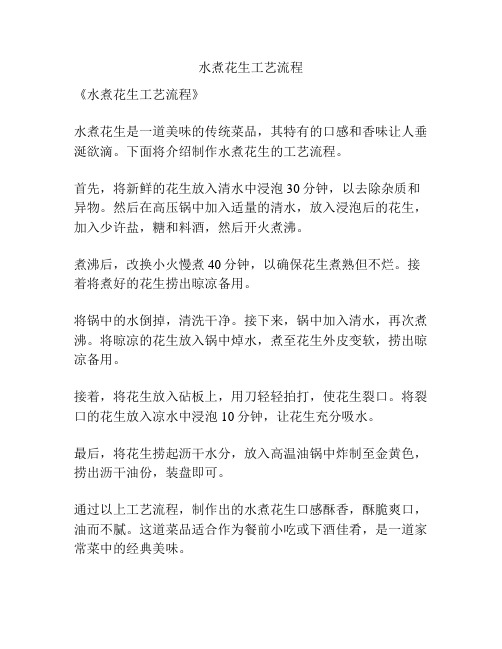
水煮花生工艺流程
《水煮花生工艺流程》
水煮花生是一道美味的传统菜品,其特有的口感和香味让人垂涎欲滴。
下面将介绍制作水煮花生的工艺流程。
首先,将新鲜的花生放入清水中浸泡30分钟,以去除杂质和异物。
然后在高压锅中加入适量的清水,放入浸泡后的花生,加入少许盐,糖和料酒,然后开火煮沸。
煮沸后,改换小火慢煮40分钟,以确保花生煮熟但不烂。
接着将煮好的花生捞出晾凉备用。
将锅中的水倒掉,清洗干净。
接下来,锅中加入清水,再次煮沸。
将晾凉的花生放入锅中焯水,煮至花生外皮变软,捞出晾凉备用。
接着,将花生放入砧板上,用刀轻轻拍打,使花生裂口。
将裂口的花生放入凉水中浸泡10分钟,让花生充分吸水。
最后,将花生捞起沥干水分,放入高温油锅中炸制至金黄色,捞出沥干油份,装盘即可。
通过以上工艺流程,制作出的水煮花生口感酥香,酥脆爽口,油而不腻。
这道菜品适合作为餐前小吃或下酒佳肴,是一道家常菜中的经典美味。
水煮花生煮多长时间
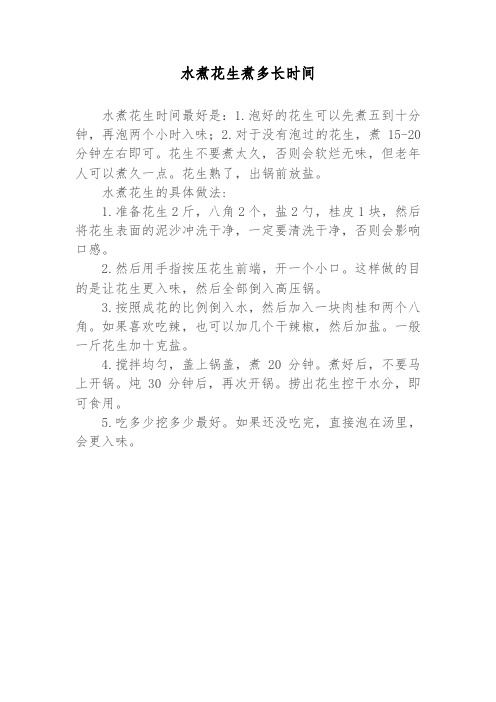
水煮花生煮多长时间
水煮花生时间最好是:1.泡好的花生可以先煮五到十分钟,再泡两个小时入味;2.对于没有泡过的花生,煮15-20分钟左右即可。
花生不要煮太久,否则会软烂无味,但老年人可以煮久一点。
花生熟了,出锅前放盐。
水煮花生的具体做法:
1.准备花生2斤,八角2个,盐2勺,桂皮1块,然后将花生表面的泥沙冲洗干净,一定要清洗干净,否则会影响口感。
2.然后用手指按压花生前端,开一个小口。
这样做的目的是让花生更入味,然后全部倒入高压锅。
3.按照成花的比例倒入水,然后加入一块肉桂和两个八角。
如果喜欢吃辣,也可以加几个干辣椒,然后加盐。
一般一斤花生加十克盐。
4.搅拌均匀,盖上锅盖,煮20分钟。
煮好后,不要马上开锅。
炖30分钟后,再次开锅。
捞出花生控干水分,即可食用。
5.吃多少挖多少最好。
如果还没吃完,直接泡在汤里,会更入味。
水煮花生工艺流程
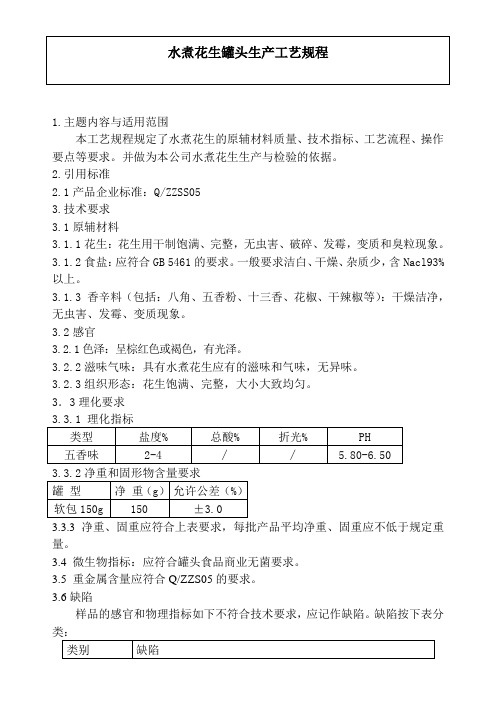
1.主题内容与适用范围本工艺规程规定了水煮花生的原辅材料质量、技术指标、工艺流程、操作要点等要求。
并做为本公司水煮花生生产与检验的依据。
2.引用标准2.1产品企业标准:Q/ZZSS053.技术要求3.1原辅材料3.1.1花生:花生用干制饱满、完整,无虫害、破碎、发霉,变质和臭粒现象。
3.1.2食盐:应符合GB 5461的要求。
一般要求洁白、干燥、杂质少,含Nacl93%以上。
3.1.3 香辛料(包括:八角、五香粉、十三香、花椒、干辣椒等):干燥洁净,无虫害、发霉、变质现象。
3.2感官3.2.1色泽:呈棕红色或褐色,有光泽。
3.2.2滋味气味:具有水煮花生应有的滋味和气味,无异味。
3.2.3组织形态:花生饱满、完整,大小大致均匀。
3.3理化要求3.3.3 净重、固重应符合上表要求,每批产品平均净重、固重应不低于规定重量。
3.4 微生物指标:应符合罐头食品商业无菌要求。
3.5 重金属含量应符合Q/ZZS05的要求。
3.6缺陷样品的感官和物理指标如下不符合技术要求,应记作缺陷。
缺陷按下表分4.试验方法、检验规则及标志、包装、运输、贮存执行Q/ZZSS05。
5.工艺流程:原料验收→挑选、清洗→汤汁熬制→预煮→浸泡→淋干→装罐→封口→装蓝→杀菌冷却→擦包入库5.1原料验收:原料到厂后,验收人员要严格验收数量和质量,要求采用干制良好,完整,无虫害、破碎,发霉和变质现象。
5.2挑选、清洗:挑选剔除颗粒较小的、破粒、臭粒、鼠咬、杂质等,用清水清洗干净。
5.3汤汁熬制:见汤汁配制表。
5.4预煮:将洗好的花生淋干后放入熬制好的汤汁中煮沸15分钟,预煮时用孔网罩覆盖,以防上浮花生没有浸没汤汁。
5.5浸泡:将预煮好的花生趁热在预煮液中浸泡1个小时。
5.6淋干:淋干预煮液以备装袋。
5.7装袋:150g5.8封口:用软包装封口机封口,封口时把花生粒摊平,并尽量抽出袋内空气,封口线要平整,拉力≥30N。
5.9装蓝:平铺于杀菌蓝中进行杀菌。
水煮花生这几种做法,覆盖了从商业到家常式的各种工艺
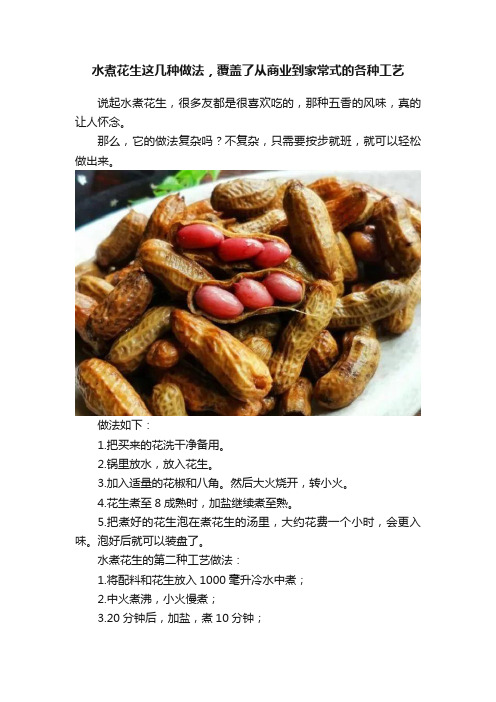
水煮花生这几种做法,覆盖了从商业到家常式的各种工艺说起水煮花生,很多友都是很喜欢吃的,那种五香的风味,真的让人怀念。
那么,它的做法复杂吗?不复杂,只需要按步就班,就可以轻松做出来。
做法如下:1.把买来的花洗干净备用。
2.锅里放水,放入花生。
3.加入适量的花椒和八角。
然后大火烧开,转小火。
4.花生煮至8成熟时,加盐继续煮至熟。
5.把煮好的花生泡在煮花生的汤里,大约花费一个小时,会更入味。
泡好后就可以装盘了。
水煮花生的第二种工艺做法:1.将配料和花生放入1000毫升冷水中煮;2.中火煮沸,小火慢煮;3.20分钟后,加盐,煮10分钟;4.最后用大火收汁,将煮好的花生在锅里煨一会儿;5.端盘子,当零食下酒菜,很受大众欢迎。
水煮花生的第三种工艺方法1.花生用清水洗净至无沉淀物。
2.用拇指和食指轻轻按压花生的前端,让花生壳裂开——一个小洞。
将所有花生依次压入一个小洞,这样煮的时候更容易入味。
3.将加工好的花生倒入高压锅中。
4.加水,水和花生的比例是1,333,601。
5.加一片桂皮和两个八角(喜欢口味重的可以在家里放点香料,喜欢辣的可以放点干辣椒一起)。
6.加入4勺盐,约20克。
每斤花生放10克盐比较合适。
7.用铲子搅拌花生,使盐和花生混合均匀。
8.盖上盖子煮20分钟。
煮好后不要马上开盖,要再焖半个小时再开盖:9.捞出花生,控水,就可以吃了。
剩下的继续泡在汁里,泡的时间越长越入味。
商业版水煮花生工艺流程:原料验收——挑选——清洗——煎煮——预煮——浸泡沥干——装袋——封口——灭菌——冷却——擦包入库。
1.原料验收:原料到厂后,验收人员要严格验收数量和质量,要求烘干后的物料完好完整,无虫害、破损、霉变、变质。
2.选择和清洁。
选择并清除小颗粒、破碎颗粒、有臭味的颗粒、老鼠咬痕、杂质等。
用泡沫清洁剂和喷水清洁它们。
3.将盐:五香粉,八角,花椒,干辣椒,十三香在汤中煮沸。
4.预煮。
将洗净的花生沥干,放入煮好的汤中煮15分钟。
水煮花生
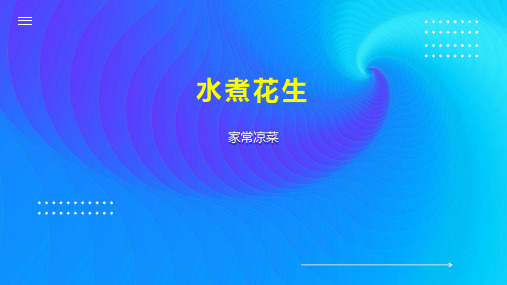
营养价值
花生味甘、性平,入脾、肺经。花生的营养价值比粮食高,可以与鸡蛋、牛奶、肉类等一些动物性食物媲美。 花生含有维生素E和一定量的锌,能增强记忆、抗老化、延缓脑功能衰退、滋润皮肤。花生含有的维生素C有降低 胆固醇的作用,有助于防治动脉硬化、高血压和冠心病。花生还有扶正补虚、悦脾和胃、润肺化痰、滋养调气、 利水消肿、止血生乳、清咽止疟的作用。
宜忌人群
煮花生花生油脂含量高,胆病患者不宜食用。发霉的花生不能吃。
谢谢观看
主料:新鲜花生。 辅料:桂皮、花椒、盐。 步骤: 1、花生倒入盆里,加入适量清水。反复清洗,直至把花生壳上泥巴洗干净; 2、取出,沥干水分,把沥干水分的花生倒入电压锅中,加入盐; 3、加入花椒、加入桂皮、再加入清水; 4、加入清水的量要以浸过花生为准,盖上锅盖,压20分钟。 小贴士: 1、煮花生的水不要倒掉,让花生始终泡在这个汁水里,吃的时候取出一些。 2、吃不完的花生,一定要放在保鲜盒中放入冰箱保存,保存的时候倒入一些煮花生的汤,这样花生不会变干 而影响口感。
煮花生诸多吃法中以煮为最佳。水煮花生是最简单、最科学的吃法,它能完好的保存营养成分,味道非常鲜 美。做法虽然简单,但是要煮的入味儿还是有小窍门的。只要掌握,就可以在短时间内,做出很入味﹑纯正的农 家花生的味道。
关键技巧就是:把花生前面的一头,用拇指和食指轻轻按一下,花生壳就裂开一个小口子,这样煮的时候不 仅节约时间,而且汤汁的味道就容易的到里面去了。
原料: 2斤花生, 2个八角,2勺盐,1块桂皮。 步骤: 1、花生用水清洗干净,洗到没有泥沙沉淀为止; 2、用拇指和食指轻轻按花生前面的一头,使花生壳裂开一个小口子,这样煮的时候容易入味儿。 3、把处理好的花生,倒进高压锅里面; 4、加水进去,水和花生的比例1:1; 5、放入一块桂皮、两个八角,喜欢口味重的,家里有什么香料都可以放点进去作方法
- 1、下载文档前请自行甄别文档内容的完整性,平台不提供额外的编辑、内容补充、找答案等附加服务。
- 2、"仅部分预览"的文档,不可在线预览部分如存在完整性等问题,可反馈申请退款(可完整预览的文档不适用该条件!)。
- 3、如文档侵犯您的权益,请联系客服反馈,我们会尽快为您处理(人工客服工作时间:9:00-18:30)。
1.主题内容与适用范围
本工艺规程规定了水煮花生的原辅材料质量、技术指标、工艺流程、操作要点等要求。
并做为本公司水煮花生生产与检验的依据。
2.引用标准
2.1产品企业标准:Q/ZZSS05
3.技术要求
3.1原辅材料
3.1.1花生:花生用干制饱满、完整,无虫害、破碎、发霉,变质和臭粒现象。
3.1.2食盐:应符合GB 5461的要求。
一般要求洁白、干燥、杂质少,含Nacl93%以上。
3.1.3 香辛料(包括:八角、五香粉、十三香、花椒、干辣椒等):干燥洁净,无虫害、发霉、变质现象。
3.2感官
3.2.1色泽:呈棕红色或褐色,有光泽。
3.2.2滋味气味:具有水煮花生应有的滋味和气味,无异味。
3.2.3组织形态:花生饱满、完整,大小大致均匀。
3.3理化要求
3.3.3 净重、固重应符合上表要求,每批产品平均净重、固重应不低于规定重量。
3.4 微生物指标:应符合罐头食品商业无菌要求。
3.5 重金属含量应符合Q/ZZS05的要求。
3.6缺陷
样品的感官和物理指标如下不符合技术要求,应记作缺陷。
缺陷按下表分
4.试验方法、检验规则及标志、包装、运输、贮存执行Q/ZZSS05。
5.工艺流程:
原料验收→挑选、清洗→汤汁熬制→预煮→浸泡→淋干→装罐→封口→装蓝→杀菌冷却→擦包入库
5.1原料验收:原料到厂后,验收人员要严格验收数量和质量,要求采用干制良好,完整,无虫害、破碎,发霉和变质现象。
5.2挑选、清洗:挑选剔除颗粒较小的、破粒、臭粒、鼠咬、杂质等,用清水
清洗干净。
5.3汤汁熬制:见汤汁配制表。
5.4预煮:将洗好的花生淋干后放入熬制好的汤汁中煮沸15分钟,预煮时用孔网罩覆盖,以防上浮花生没有浸没汤汁。
5.5浸泡:将预煮好的花生趁热在预煮液中浸泡1个小时。
5.6淋干:淋干预煮液以备装袋。
5.7装袋:150g
5.8封口:用软包装封口机封口,封口时把花生粒摊平,并尽量抽出袋内空气,
封口线要平整,拉力≥30N。
5.9装蓝:平铺于杀菌蓝中进行杀菌。
5.10杀菌:10′-50′/108℃
5.11擦包、入库:冷却至40℃左右立即擦干水分装箱入库。