注塑成型五要素
注塑工艺应注意的五大要素
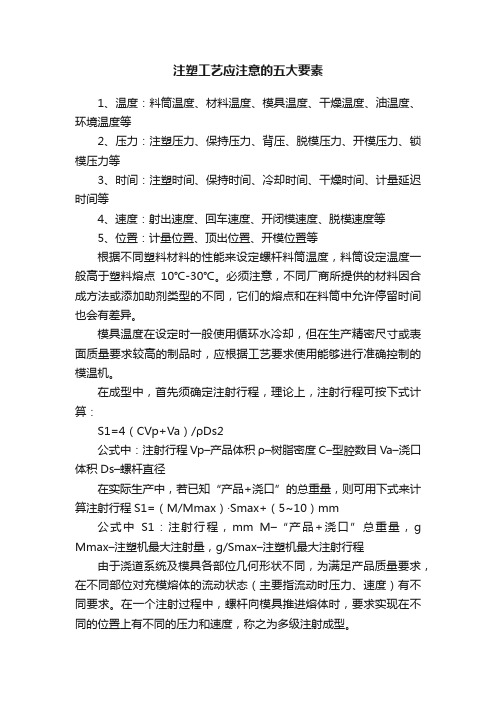
注塑工艺应注意的五大要素1、温度:料筒温度、材料温度、模具温度、干燥温度、油温度、环境温度等2、压力:注塑压力、保持压力、背压、脱模压力、开模压力、锁模压力等3、时间:注塑时间、保持时间、冷却时间、干燥时间、计量延迟时间等4、速度:射出速度、回车速度、开闭模速度、脱模速度等5、位置:计量位置、顶出位置、开模位置等根据不同塑料材料的性能来设定螺杆料筒温度,料筒设定温度一般高于塑料熔点10℃-30℃。
必须注意,不同厂商所提供的材料因合成方法或添加助剂类型的不同,它们的熔点和在料筒中允许停留时间也会有差异。
模具温度在设定时一般使用循环水冷却,但在生产精密尺寸或表面质量要求较高的制品时,应根据工艺要求使用能够进行准确控制的模温机。
在成型中,首先须确定注射行程,理论上,注射行程可按下式计算:S1=4(CVp+Va)/ρDs2公式中:注射行程Vp–产品体积ρ–树脂密度C–型腔数目Va–浇口体积Ds–螺杆直径在实际生产中,若已知“产品+浇口”的总重量,则可用下式来计算注射行程S1=(M/Mmax)·Smax+(5~10)mm公式中S1:注射行程,mm M–“产品+浇口”总重量,g Mmax–注塑机最大注射量,g/Smax–注塑机最大注射行程由于浇道系统及模具各部位几何形状不同,为满足产品质量要求,在不同部位对充模熔体的流动状态(主要指流动时压力、速度)有不同要求。
在一个注射过程中,螺杆向模具推进熔体时,要求实现在不同的位置上有不同的压力和速度,称之为多级注射成型。
一般塑件在成型时至少设定三段或四段以上注射才是比较科学的,即主流道处为第一段,分流道至浇口处为第二段,产品充满型腔约90%为第三段,剩余部分为第四段,可用计算重量法来确定各段的切换位置点;实际生产中,应根据产品质量要求、流道结构、模具排气状况等对多级注射工艺参数进行科学分析,合理设定。
通常可采用调试观察法进行设定,将注射时所需找切换位置点的压力/速度设定为0,观察熔体的走向位置及产品缺陷状况,逐步进行调整,直至找出合理的位置点。
注塑成型五大要素调机

注塑成型五大要素调机注塑成型是一种重要的塑料加工方法,广泛应用于各个领域。
在注塑成型过程中,调机是非常关键的环节,它直接影响到成品的质量和生产效率。
本文将介绍注塑成型的五大要素以及如何进行调机。
一、温度调控温度调控是注塑成型中必不可缺的一项要素。
合理的温度调控可以保证塑料原料的熔融状态,使其能够顺利进入模具中进行成型。
温度过低会导致塑料无法完全熔化或熔化不均匀,从而出现不良品;而温度过高则容易造成模具磨损或塑料变质。
因此,在调机过程中,需要根据具体的塑料种类和注塑机型号来合理设置温度,确保塑料的熔融状态处于最佳范围。
二、压力调控压力调控是注塑成型过程中另一个重要的要素。
通过调整注塑机的压力大小,可以控制塑料在模具中的流动速度和压实程度。
如果压力过小,塑料可能无法填充整个模具腔道,导致成品缺陷;而压力过大则容易造成模具损坏或超出产品要求的尺寸。
因此,在调机时需要根据产品要求和模具设计来合理设置压力,保证塑料能够在模具中达到理想的充填状态。
三、速度调控速度调控也是注塑成型中需要特别注意的要素。
注塑机的进料速度、射胶速度和回退速度等都需要在调机过程中进行合理设置,以确保塑料在模具中的流动和充填能够按照预定的要求进行。
不同的塑料种类和产品要求可能需要不同的速度设置,因此在调机时需要仔细研究产品的特点和要求进行相应设置。
四、冷却调控冷却调控是注塑成型中一个重要但常常被忽视的要素。
在塑料完成充填、压实后,需要进行冷却来使其固化成型。
冷却过程对成品的质量有着很大的影响,因此需要合理设置冷却时间和冷却介质的温度。
如果冷却不足,塑料可能会在脱模时变形或容易受到外界环境的影响;而过度冷却则可能导致产品表面出现气泡、翘曲等问题。
因此,在调机时需要根据具体情况合理控制冷却时间和温度,确保成品能够达到最佳的冷却效果。
五、保压调控保压调控是注塑成型过程中需要特别注意的一项要素。
在注塑机射胶结束后,需要进行一段时间的保压来确保产品在模具中的密实度和尺寸稳定性。
注塑机调机必备--成型条件五要素
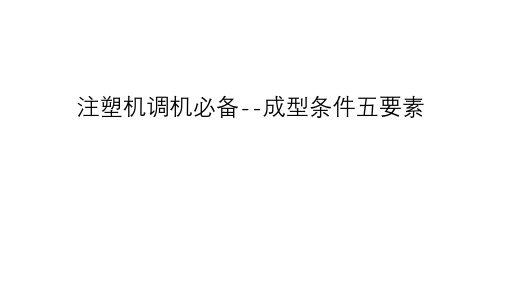
4.冷却时间 定义: 产品冷却固化而脱模后又不致于发生变形所需的时间
作用: (1)让制品固化 (2)防止制品变形
设定原则: (1)冷却时间是周期时间的重要组成部分,在保证制品质量的前提 下尽可能使其短. (2)冷却时间因熔体的温度,模具温度,产品大小及厚度而定.
5.滞留时间
定义:指注塑工艺中塑料树脂在注塑机中注射装置滚筒中的驻留时间(通常以分钟或秒计算)。换言之, 滞留时间也即塑料树脂从滚筒料斗仓口移动到喷嘴尖端的时间。滞留时间长就会导致塑料分解,塑料流动性增强, 塑料的性能发生变化。
4.缓冲量
定义: 螺杆注塑完拮,并不希望把螺杆中头部的熔料全部射出,还希望留一些.形成一个祭料量,此料量即为缓冲量. 作用: (1)防止螺杆头部与喷嘴接触发生机械破坏事故. (2)控制注射量的重复精度 设定原则: (1)缓冲量不宜过大,也不宜过小,过大,会使得余料过多,造成压力损失及原料降解,过小,则达不到缓冲之目的. (2)缓冲量的确定,一般取3~5mm为宜.
2.背压(塑化压力)
定义: 塑料在塑化过程建立在熔腔中的压力 .在塑料熔融、塑化过程中,熔料不断移向料筒前端(计量室内), 且越来越多,逐渐形成一个压力,推动螺杆向后退。为了阻止螺杆后退过快,确保熔料均匀压实,需要给螺 杆提供一个反方向的压力,这个反方向阻止螺杆后退的压力称为背压 。 作用: (1)提高熔体的比重. (2)使熔体塑化均匀. (3)使熔体中含气量降低.提高塑化质量 设定原则: (1)背压的调整应考虑塑料原料的性质. (2)背压的调整应参考制品的表观质量和尺寸精度 这种压力的大小是可以通过液压系统中的溢流阀来调整的。 在注射中,塑化压力的大小是随螺杆的设计、制品质量的要求以及塑料的种类不同而需要改变的,如果说这 些情况和螺杆的转速都不变,则增加塑化压力会加强剪切作用,即会提高熔体的温度,但会减小塑化的效率, 增大逆流和漏流,增加驱动功率。 此外,增加塑化压力常能使熔体的温度均匀,色料的混合均匀和排出熔体中的气体。 一般塑成型中的压力曲线操作中,塑化压力的决定应在保证制品质量优良的前提下越低越好,其具体数值是 随所用的塑料的品种而异的,但通常很少超过20公斤/平方厘米。 采用高背压有利于色料的分散和塑料的融化,但却同时延长了螺杆回缩时间,降低了塑料纤维的长度,增加 了注塑机的压力,因此背压应该低一些,一般不超过注塑压力的20%。
注塑成型条件五要素

60-120 220-310 (1.06) (0.6)
N-A
14
PC
120~ 2-4
80-100 270-310 (1.2) (0.6) 137
15
PET
130~ 4-
60-100 250-280 (1.33) (0.3) 67
16
PBT
130~ 3-4
60-90
230-260 (1.3) (1.7) 152
射 出 壓 力
時間
高保壓會使成品內部有相當大的殘留應力而使成品表面造成細小之切 割痕跡造成裂縫.此情況下,要在澆口凝固前(gate seal) 徐徐降低保壓壓力即 可改善之.
▪
背压
1.在塑化时,螺杆不断旋转将塑胶送到螺杆头部,这些被推进到螺杆前端的 塑胶就会对螺杆产生压力,这就是背压。在注射成型时,它可以由调整射出油压 缸的退油压力来调节,背压的增加可以取得以下的效果:原料塑化更均匀,利于 塑胶内气体排出,计量更精确;使熔料温度增加,加速分解,容易造成流涎现象, 塑化时间变长等。背压的大小是依塑料的粘度及其热稳定性来决定一般为5-
例一
射出壓力: 為安定射出速度而設定高壓力 射出二次壓: 為防止因殘留應力造成之彎曲龜裂或過保壓造成之離形不良等現 象,保壓值應保持下降
射 一次壓
出 壓
P1
力
0
二次壓
設定壓力 實際壓力
P2
三次壓
P3 四次壓 T2
P4 T3 T4
時間
例二.
慮時:
模具不當或合模力不足造成毛边,而有凹痕.熔接線之顧
射 出 壓 力
15kg/cm2左右. 2.若螺桿背壓大,則塑料自入料口被輸送到螺桿前端,所經歷的時間較長,因
注塑成型--射出成型五要素

設定原則: (1)設定調試前一定先調模厚. (2)初設值應盡量低,不能超過鎖模力的20%. (3)不能修正合模時,應慢慢提高設定值.
頂出壓力
定義:為使制品從模具上落下而所需要克服制品和模具的 附著力.
作用:使制品脫離模面.
設定原則: (1)能使制品從模具上脫離下來. (2)制品頂出時不致于破裂,變形. (3)彈簧复位之頂杆頂出力必需能使頂針頂到預設位置.
背壓
定義:塑膠在塑化過程建立在熔腔中的壓力 作用:
(1)提高熔體的比重. (2)使熔體塑化均勻. (3)使熔體中含氣量降低.提高塑化質量.
設定原則: (1)背壓的調整應考慮塑膠原料的性質. (2)背壓的調整應參考製品的表觀質量和呎寸精度.
鎖模壓力
定義:合模系統為克服在注射和保壓階段使模具分開的脹模力 而施加在模具上的閉緊力.
注塑成型發展至今已有140多年歷史。 目前,成型制品普遍應用于各個領域,成為人們 生活中不可缺少的必須品。特別是近年來,科 學家們利用高科技制成的復合材料制品用于 航空。航天領域,顯示塑料工藝的輝煌前程。 但人們“以塑“以塑代本”的願望,還需我們 一代繼一代的努力、發展、創新。
簡介
成型五大要素 各要素之定義、作用及設定原則 實際設定中注意事項
周期
定義: 從開模終了開始到下一次注射冷卻完畢后的開模終了 所用的時間
作用: 保證制品成型並完全冷卻定型
設定原則: (1)周期盡可能短. (2)縮短周期必須在保證產品質量的前提下進行
冷卻時間
定義: 產品冷卻固化而脫模后又不致於發生變形所需的時間
作用: (1)讓制品固化 (2)防止制品變形
設定原則: (1)冷卻時間是周期時間的重要組成部分,在保證制 品質量的前提下盡可能使其短. (2)冷卻時間因熔體的溫度,模具溫度,產品大小及厚 度而定.
注塑品质的五大要素
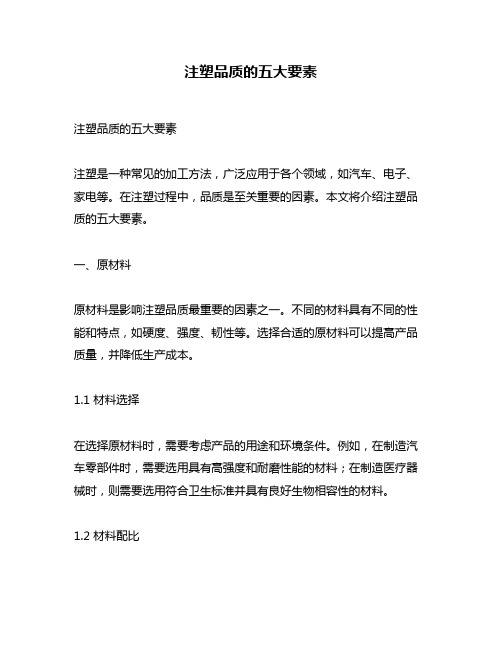
注塑品质的五大要素注塑品质的五大要素注塑是一种常见的加工方法,广泛应用于各个领域,如汽车、电子、家电等。
在注塑过程中,品质是至关重要的因素。
本文将介绍注塑品质的五大要素。
一、原材料原材料是影响注塑品质最重要的因素之一。
不同的材料具有不同的性能和特点,如硬度、强度、韧性等。
选择合适的原材料可以提高产品质量,并降低生产成本。
1.1 材料选择在选择原材料时,需要考虑产品的用途和环境条件。
例如,在制造汽车零部件时,需要选用具有高强度和耐磨性能的材料;在制造医疗器械时,则需要选用符合卫生标准并具有良好生物相容性的材料。
1.2 材料配比除了选择合适的原材料外,还需要注意不同原材料之间的配比。
正确的配比可以保证产品具有良好的物理特性和化学稳定性。
二、模具设计模具设计是影响注塑品质另一个重要因素。
模具设计直接影响到产品尺寸、外观和精度等方面。
因此,合理的模具设计可以提高产品质量,并降低生产成本。
2.1 模具材料模具材料需要具有高强度、高硬度和良好的耐磨性能。
常用的模具材料有钢铁、铜合金和铝合金等。
2.2 模具结构模具结构需要考虑到产品的形状和尺寸,以及注塑过程中的压力和温度等因素。
例如,在制造复杂形状的产品时,需要采用多腔模或者转移模等结构。
三、注塑机注塑机是注塑过程中最重要的设备之一。
不同类型和规格的注塑机对产品品质有着不同程度的影响。
3.1 机型选择在选择注塑机时,需要考虑到产品尺寸、重量和生产效率等因素。
例如,在制造大型零部件时,需要选用大型注塑机;在制造小型零部件时,则可以选用小型注塑机。
3.2 控制系统控制系统是影响注塑品质另一个重要因素。
控制系统可以控制温度、压力和速度等参数,以确保产品尺寸精确,并防止产品变形和缺陷等问题。
四、注塑工艺注塑工艺是影响注塑品质另一个重要因素。
不同的注塑工艺对产品品质有着不同程度的影响。
4.1 注塑温度注塑温度是影响产品品质的关键因素之一。
过高或过低的温度都会导致产品尺寸不准确、表面不光滑以及气泡等缺陷。
注塑成型参数的定义

成型条件设定一、成型四大要素图一二、注塑工艺五大要素温度、压力、时间、行程(位置)、速度三、料温定义:料温是指塑化物料的温度和以喷嘴注射出的温度,图二其中,前者称为塑化温度,后者称为注射温度.料温设定有利于塑化,降低熔体粘度,流动阻力或注射压力损失.增强流动性,提高料温还能对制品的一些性能带来好的影响,如结合线强度增加,但是料温过高又很容易引起热降解,最终反而导致制品的物理和力学性能变差.料温设定不利于塑化,塑料熔融后粘度较大,流动性差,成型后的制品容易出现熔接痕迹,表面无光泽和缺料等缺陷.料温设定的几个原则1.对于薄壁制品或形状复杂以及带有嵌件的制品,因流动困难或容易冷却,应选用较高的机筒温度,反之,对原壁制品,简单制品及无嵌件制品,均可选用较低的机筒温度.2.避免成型物料在机筒中过热降解,除应严格控制机筒最高温度之外,还必须控制物料或熔体在机筒内的停留时间.3.避免流涎, 喷嘴温度可略低于机筒最高温度,但不解太低.4.判断料温是否合适,可采用对空注射法观察,对空注射时,料流均匀,光滑,无泡,色泽均匀,刚劲有力.四、模温模具温度指和制品接触的模腔温度,它直接影响熔体的充模流动行为,制品的冷却速度和成型后的制品性解.一般来讲,提高模温可以改善熔体在模内的流动性,增加制品的密度和结晶度,以减小充模压力和制品的应力,但制品冷却时间延长,收缩率和脱模后的翘曲变形将会延长或增大,是生产率随冷却时间延长下降.反之,若降低模温,虽然缩短冷却时间和提高生产率,但在温度过低的情况下,熔体在模内的流动性能将会变差,并使制品产生较大的应力或明显的熔接痕迹等缺陷.此外,除了模腔表壁的粗糙度之外,模温还是影响制品表面质量的因素,适当地提高模温,制品表面的粗糙度也会下降。
关于成型条件设定要点总则:一般情况下条件设定越简单,生产越稳定,尤其是对于形状较简单或外观要求不高产品尽量使用较简单条件,如射出速度、射出压力及保压压力均使用1段即可。
成型条件的五大要素
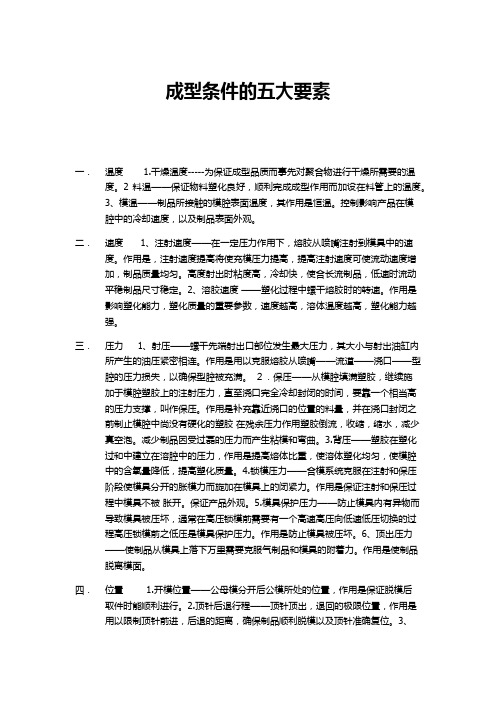
成型条件的五大要素一.温度 1.干燥温度-----为保证成型品质而事先对聚合物进行干燥所需要的温度。
2料温——保证物料塑化良好,顺利完成成型作用而加设在料管上的温度。
3、模温——制品所接触的模腔表面温度,其作用是恒温。
控制影响产品在模腔中的冷却速度,以及制品表面外观。
二.速度 1、注射速度——在一定压力作用下,熔胶从喷嘴注射到模具中的速度。
作用是,注射速度提高将使充模压力提高,提高注射速度可使流动速度增加,制品质量均匀。
高度射出时粘度高,冷却快,使合长流制品,低速时流动平稳制品尺寸稳定。
2、溶胶速度——塑化过程中螺干熔胶时的转速。
作用是影响塑化能力,塑化质量的重要参数,速度越高,溶体温度越高,塑化能力越强。
三.压力 1、射压——螺干先端射出口部位发生最大压力,其大小与射出油缸内所产生的油压紧密相连。
作用是用以克服熔胶从喷嘴——流道——浇口——型腔的压力损失,以确保型腔被充满。
2.保压——从模腔填满塑胶,继续施加于模腔塑胶上的注射压力,直至浇口完全冷却封闭的时间,要靠一个相当高的压力支撑,叫作保压。
作用是补充靠近浇口的位置的料量,并在浇口封闭之前制止模腔中尚没有硬化的塑胶在残余压力作用塑胶倒流,收缩,缩水,减少真空泡。
减少制品因受过磊的压力而产生粘模和弯曲。
3.背压——塑胶在塑化过和中建立在溶腔中的压力,作用是提高熔体比重,使溶体塑化均匀,使模腔中的含氧量降低,提高塑化质量。
4.锁模压力——合模系统克服在注射和保压阶段使模具分开的胀模力而旋加在模具上的闭紧力。
作用是保证注射和保压过程中模具不被胀开。
保证产品外观。
5.模具保护压力——防止模具内有异物而导致模具被压坏,通常在高压锁模前需要有一个高速高压向低速低压切换的过程高压锁模前之低压是模具保护压力。
作用是防止模具被压坏。
6、顶出压力——使制品从模具上落下万里需要克服气制品和模具的附着力。
作用是使制品脱离模面。
四.位置 1.开模位置——公母模分开后公模所处的位置,作用是保证脱模后取件时能顺利进行。
塑胶成型的五大要素

塑胶成型的五大要素塑胶成型这件事情,就像是在厨房做一道美味佳肴,需要掌握好几个关键要素才能做出好产品。
今天我们就来聊聊这五个要素,保证说得通俗易懂,让大家一听就明白!温度可是个大boss!就像煮饭一样,火候太大会糊,太小又煮不熟。
塑胶成型时的温度控制也是这个道理,要是温度不对,塑料就会闹脾气。
温度太高,塑料会变得跟糊糊似的,做出来的东西歪歪扭扭;温度太低,塑料又会变得特别倔强,根本不听话,跟石头似的难以成型。
压力这个要素,就像是给面团揉面时的力道。
力道太大,面团都给你挤扁了;力道太小,面团又不能充分混合。
塑胶成型时的压力也是这个道理,压力要是掌握不好,产品要么密度不均,要么表面会起泡,就像发霉的馒头一样难看。
时间控制简直就是个艺术!就像煮鸡蛋,三分钟是溏心,五分钟是半熟,七分钟是全熟。
塑胶成型的时间也得掌握得恰到好处,时间太短,里面还没熟透呢;时间太长,又会把塑料给憋坏了,搞不好还会变色,那可就尴尬了。
说到速度,这可真是个有意思的要素。
想象一下,你在倒果汁,倒得太快会溅得到处都是,倒得太慢又浪费时间。
塑胶成型的速度也是这样,注塑速度要是太快,塑料会像受惊的小兔子一样乱窜;速度太慢,又会影响生产效率,而且容易在产品表面留下难看的痕迹。
冷却这个要素,就像是刚出炉的面包需要晾一会儿才能切。
塑胶制品也需要适当的冷却时间,要是冷却不当,产品就会变形,就像晒太阳晒蔫了的塑料花一样难看。
冷却时间太短,产品会变形;太长,又会影响生产效率。
这五个要素之间还特别爱搞对象,它们互相之间都有着千丝万缕的关系。
就像温度和压力是一对好搭档,温度高了,压力就得适当调整;时间和速度又是一对,速度快了,时间自然要跟着变。
在实际生产中,这五个要素就像是在演奏一首交响乐,每个要素都是一件乐器,必须协调一致才能奏出美妙的音乐。
要是哪个要素走调了,整个产品就会变得不伦不类。
有趣的是,不同的塑料材料对这五个要素的要求还不一样。
有的塑料特别娇气,温度稍微高一点点就会变质;有的塑料倒是挺耐造,温度范围可以放宽一些。
注塑成型作业指导书

编号:ZY-QC-30 制定日:2013-07-29 实施日:2013-07-29 版次:A/0 页码:1/6注塑成型作业指导书一.注塑成型的原理:1.注塑成型:指将注射用的置于能加热的料筒内,受热、塑化,再施加压力,使熔体塑料注入到所需形状的模具中,经过冷却定型后脱模,得到所需形状的制品。
2.注塑成型三要素:注塑机、模具、原料3.注塑成型条件五大要素:压力-时间-速度-位置-温度。
二.注塑机:.注射机的结构:a.注射系统:主要使塑料塑化和使熔体塑料注入模具功能b.合模系统:主要模具的开模、锁模、调模、顶出功能c.传动系统:主要控制注射机的动作能力。
如油压阀、电动机d.电气控制系统:主要注射机内部电路、开关、电路板3.注射机的操作:a.打开注射机总电源及各开关,旋开紧急停止键b.按下操作板上马达启动键与电热键,开启马达与料筒温度(按1次左上角灯亮为开启,再按1次左上角灯灭为停止)c.选用操作方式c-2手动:选用此方式时操作板上的相应开关,只在按下时作相应动作,手指放开即停止c-3半自动:选用此方式时,只需按动两合模开关即可完成,合模,锁模,射胶,保压。
冷却,开模一系列动作。
d.开关模动作设定:开模一般设定为慢快慢,关模一般设定为快速低压低速高压锁模。
低压压力最大不可以大于15kg/cm²低压与高压之间位置不可大2mm,快速与低压间位置一般在50mme.成型温度设定:根据各种原料成型所需温度设定,在改变设定温度时一次不可超过5°,加料段温度比熔融段温度最少要低10°,待机器上显示实际温度达到设定温度时,在改变设定温度时一次不可超过5°再过二十分钟才可进行熔胶,射出射退动作。
f.射出/保压的设定:射出设定分多段和一段,根据制品质量所需设定,能使用高速尽量使用高速,射满成型制品95%左右即转换保压。
在需加速加压和位置时间时一次不能超过5KG和2%,第一模产品不可超过产品的70%,防止产品粘模。
注塑成型五要素ppt课件
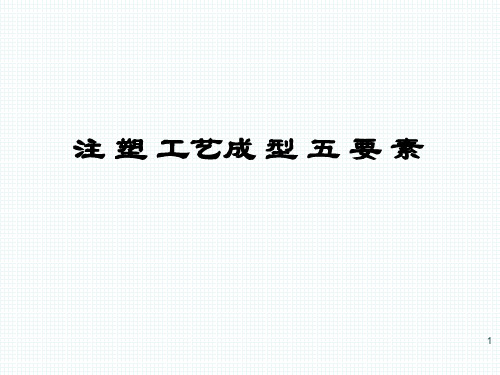
注射油缸泄油的速度,使油缸保持一定的压力,全电动机的螺杆后移速度(阻力)是由 AC伺服阀控
制的。
• 二.适当调校背压的好处:
• 1. 能将炮筒内的熔料压实,增加密度,提高射胶量、制品重量和尺寸的稳定性 2.可将熔料内的气体“ 挤出 ”,减少制品表面的气纹、内部气泡、提高光泽均匀性 3.减慢螺杆后退速度,使炮筒内的熔料充分塑化,增加色粉、色母与熔料的混合均匀度,避免制 品出现 混色 现象
柱之磨擦阻力,动定模接触后导柱导套磨擦阻力,斜导柱滑块之磨擦阻力,还有动模板与支撑部件 之磨擦阻力等等)即可 • b 要设置充分的低压保护行程(应大于产品的尺寸,有机械手时应大于机械手的夹具尺寸),太 大的低压保护行程会影响低压保护压力与低压保护时间的准确设置,所以要设置合理合适 • c 要测算低压保护开始至结束的实际时间,把低压时间设置成略大于实际时间(余量0.1秒以下, 以保证在有异物时及时停止合模动作信号输出),低压保护的原理就是在一定的低压时间内,电脑 无法采样到高压信号,电脑则判定模腔内有异物,此时电脑原则上应停止合模信号输出,同时报警 并输出开模信号。 • 2:高压压力设定 • 根据理论锁模力计算方法算出理论所需锁模力,根据理论锁模力的大小设定实际锁模力,实际 高压压力一般略大于理论锁模力即可。 • 把高压行程位置先设定偏大,此时依经验逐步减小高压行程位置,直到无法起高压或注塑机曲臂无 法伸直时再略微调大高压行程,使锁模力能够可靠实现即可。以下图为例:1.3位置不能起高压, 1.7位置可以起高压,那么我们则在1.7的基础上再增0.1-0.3即可,设定小了合不上模异常报警多 ,设定大了保护系数降低。
3
注射成型工艺界面
4
注塑压力曲线图
5
注射速度曲线
6
注塑保压设定
04.注塑成型五大要素

开发者:实施者:调试者:对前期工作的认定、确认工作,在调试过程中对模具的问题点、产品成形方面存在的问题,作综合分析,并于后期有再确认的工作。
检验者:通过对客户要求、产品结构的了解,对产品尺寸、性能、结构等作综合判定,工作的完善程度对后期工作的顺利有决定性作用。
操作者:通过前期工作的总结并给于操作者的培训,后期工作得以持续进行。
取决于操作者:对产品的了解程度(熟练怎么做)、加工包装的熟练程度(生产周期)、品质要求的认知程度(品质判断)、专业知识(优化作业方法)、敬业精神(怎样做好工作)。
注塑机:机械任何一个部分出现问题,无论大小对持续稳定的生产都是有影响的。
所以机械必须有详细的保养计划,并能够确实执行,出现问题带伤工作,对产品而言稳定性降低,机械会导致损伤(可以维修的零件变成毁灭性的只有更换)。
附属设备:包括料桶、抽料机、模温机、冷水机、循环供水系统、温控箱、气压泵、气压阀、机械手等,定期维修保养工作,都是保持稳定生产的重要环节。
任何一个环节出现故障,都会导致生产暂停。
专用设备:全自动闭环式供料系统、专用机器人、气辅成形设备、移模机等专用设备需要特殊的保养计划。
模具:模具的前期维护、确认、保养工作,生产过程中的保养工作,后期的全面保养工作,都必须有一个统一标准,特殊模具还必须有一个单一的保养计划。
模具的持续生产都与每个环节的工作息息相关,这也是保持模具寿命的重点。
加工工具:操作者工具(刀、剪、钳、手套等)的正确使用,较形治具、工装、专用检具的保养,都是保持生产的重要环节。
测量仪器:根据产品需要合理选择测量仪器,还包括使用者是否用正确的方法,测量仪器的检查校正工作。
仓存运输:是品质保证的最后环节,也是最重要的环节,前期工作的完善与否都必须通过这个环节来实现。
包装材料:根据产品需要选用正确的包装,对后期的仓存运输过程(松动、磨擦过大、包装损坏)有很大影响,塑胶材料:根据材料的物性表,正确的进行仓存及前期生产的料桶清洁、预烘干,是注塑成形的基本保证。
注塑成型五大要素分析
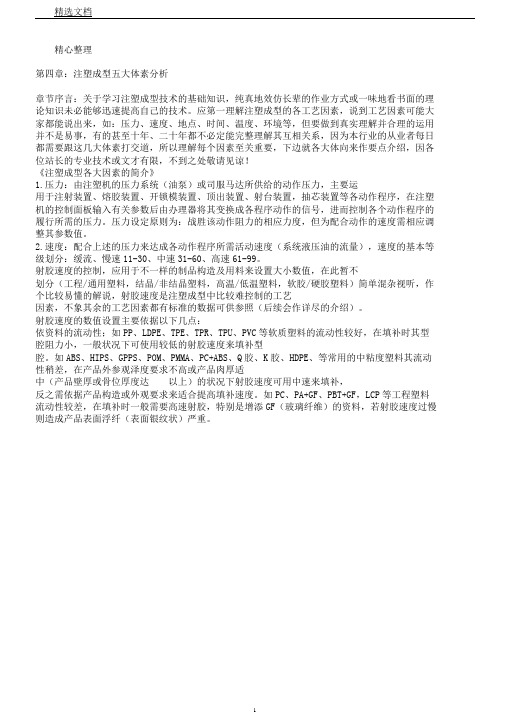
精心整理第四章:注塑成型五大体素分析章节序言:关于学习注塑成型技术的基础知识,纯真地效仿长辈的作业方式或一味地看书面的理论知识未必能够迅速提高自己的技术。
应第一理解注塑成型的各工艺因素,说到工艺因素可能大家都能说出来,如:压力、速度、地点、时间、温度、环境等,但要做到真实理解并合理的运用并不是易事,有的甚至十年、二十年都不必定能完整理解其互相关系,因为本行业的从业者每日都需要跟这几大体素打交道,所以理解每个因素至关重要,下边就各大体向来作要点介绍,因各位站长的专业技术或文才有限,不到之处敬请见谅!《注塑成型各大因素的简介》1.压力:由注塑机的压力系统(油泵)或司服马达所供给的动作压力,主要运用于注射装置、熔胶装置、开锁模装置、顶出装置、射台装置,抽芯装置等各动作程序,在注塑机的控制面板输入有关参数后由办理器将其变换成各程序动作的信号,进而控制各个动作程序的履行所需的压力。
压力设定原则为:战胜该动作阻力的相应力度,但为配合动作的速度需相应调整其参数值。
2.速度:配合上述的压力来达成各动作程序所需活动速度(系统液压油的流量),速度的基本等级划分:缓流、慢速11-30、中速31-60、高速61-99。
射胶速度的控制,应用于不一样的制品构造及用料来设置大小数值,在此暂不划分(工程/通用塑料,结晶/非结晶塑料,高温/低温塑料,软胶/硬胶塑料)简单混杂视听,作个比较易懂的解说,射胶速度是注塑成型中比较难控制的工艺因素,不象其余的工艺因素都有标准的数据可供参照(后续会作详尽的介绍)。
射胶速度的数值设置主要依据以下几点:依资料的流动性;如PP、LDPE、TPE、TPR、TPU、PVC等软质塑料的流动性较好,在填补时其型腔阻力小,一般状况下可使用较低的射胶速度来填补型腔。
如ABS、HIPS、GPPS、POM、PMMA、PC+ABS、Q胶、K胶、HDPE、等常用的中粘度塑料其流动性稍差,在产品外参观泽度要求不高或产品肉厚适中(产品壁厚或骨位厚度达以上)的状况下射胶速度可用中速来填补,反之需依据产品构造或外观要求来适合提高填补速度。
注塑成型的五大要素
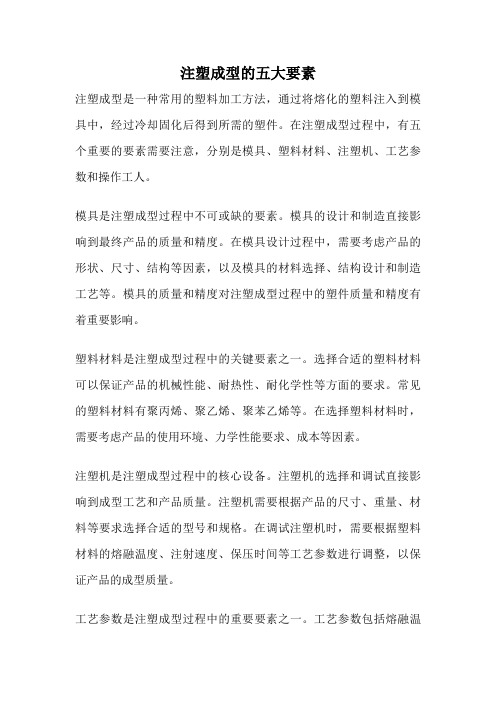
注塑成型的五大要素注塑成型是一种常用的塑料加工方法,通过将熔化的塑料注入到模具中,经过冷却固化后得到所需的塑件。
在注塑成型过程中,有五个重要的要素需要注意,分别是模具、塑料材料、注塑机、工艺参数和操作工人。
模具是注塑成型过程中不可或缺的要素。
模具的设计和制造直接影响到最终产品的质量和精度。
在模具设计过程中,需要考虑产品的形状、尺寸、结构等因素,以及模具的材料选择、结构设计和制造工艺等。
模具的质量和精度对注塑成型过程中的塑件质量和精度有着重要影响。
塑料材料是注塑成型过程中的关键要素之一。
选择合适的塑料材料可以保证产品的机械性能、耐热性、耐化学性等方面的要求。
常见的塑料材料有聚丙烯、聚乙烯、聚苯乙烯等。
在选择塑料材料时,需要考虑产品的使用环境、力学性能要求、成本等因素。
注塑机是注塑成型过程中的核心设备。
注塑机的选择和调试直接影响到成型工艺和产品质量。
注塑机需要根据产品的尺寸、重量、材料等要求选择合适的型号和规格。
在调试注塑机时,需要根据塑料材料的熔融温度、注射速度、保压时间等工艺参数进行调整,以保证产品的成型质量。
工艺参数是注塑成型过程中的重要要素之一。
工艺参数包括熔融温度、注射速度、保压时间、冷却时间等。
合理的工艺参数可以保证产品的质量和生产效率。
不同的塑料材料和产品形状需要不同的工艺参数,因此需要根据具体情况进行调整和优化。
操作工人是注塑成型过程中的重要环节。
操作工人需要熟悉注塑机的操作和调试方法,能够根据产品要求进行合理的操作。
操作工人需要掌握注塑成型的基本知识和技能,能够及时处理生产过程中的异常情况,并进行必要的调整和修正。
模具、塑料材料、注塑机、工艺参数和操作工人是注塑成型过程中的五大要素。
它们之间相互关联、相互作用,共同决定了最终产品的质量和精度。
在注塑成型过程中,需要综合考虑这些要素,并根据具体情况进行合理的选择和调整,以确保产品达到预期的要求。
注塑成型参数的定义

成型条件设定一、成型四大要素图一二、注塑工艺五大要素温度、压力、时间、行程(位置)、速度三、料温定义:料温是指塑化物料的温度和以喷嘴注射出的温度,图二其中,前者称为塑化温度,后者称为注射温度.料温设定有利于塑化,降低熔体粘度,流动阻力或注射压力损失.增强流动性,提高料温还能对制品的一些性能带来好的影响,如结合线强度增加,但是料温过高又很容易引起热降解,最终反而导致制品的物理和力学性能变差.料温设定不利于塑化,塑料熔融后粘度较大,流动性差,成型后的制品容易出现熔接痕迹,表面无光泽和缺料等缺陷.料温设定的几个原则1.对于薄壁制品或形状复杂以及带有嵌件的制品,因流动困难或容易冷却,应选用较高的机筒温度,反之,对原壁制品,简单制品及无嵌件制品,均可选用较低的机筒温度.2.避免成型物料在机筒中过热降解,除应严格控制机筒最高温度之外,还必须控制物料或熔体在机筒内的停留时间.3.避免流涎, 喷嘴温度可略低于机筒最高温度,但不解太低.4.判断料温是否合适,可采用对空注射法观察,对空注射时,料流均匀,光滑,无泡,色泽均匀,刚劲有力.四、模温模具温度指和制品接触的模腔温度,它直接影响熔体的充模流动行为,制品的冷却速度和成型后的制品性解.一般来讲,提高模温可以改善熔体在模内的流动性,增加制品的密度和结晶度,以减小充模压力和制品的应力,但制品冷却时间延长,收缩率和脱模后的翘曲变形将会延长或增大,是生产率随冷却时间延长下降.反之,若降低模温,虽然缩短冷却时间和提高生产率,但在温度过低的情况下,熔体在模内的流动性能将会变差,并使制品产生较大的应力或明显的熔接痕迹等缺陷.此外,除了模腔表壁的粗糙度之外,模温还是影响制品表面质量的因素,适当地提高模温,制品表面的粗糙度也会下降。
关于成型条件设定要点总则:一般情况下条件设定越简单,生产越稳定,尤其是对于形状较简单或外观要求不高产品尽量使用较简单条件,如射出速度、射出压力及保压压力均使用1段即可。
注塑工艺的五大要素
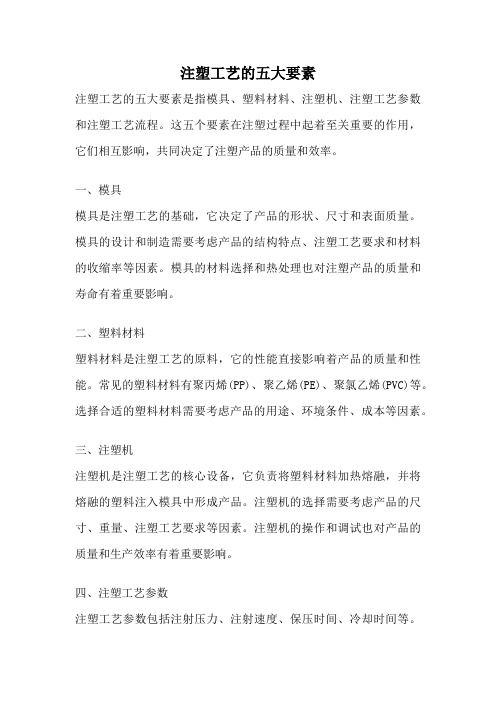
注塑工艺的五大要素注塑工艺的五大要素是指模具、塑料材料、注塑机、注塑工艺参数和注塑工艺流程。
这五个要素在注塑过程中起着至关重要的作用,它们相互影响,共同决定了注塑产品的质量和效率。
一、模具模具是注塑工艺的基础,它决定了产品的形状、尺寸和表面质量。
模具的设计和制造需要考虑产品的结构特点、注塑工艺要求和材料的收缩率等因素。
模具的材料选择和热处理也对注塑产品的质量和寿命有着重要影响。
二、塑料材料塑料材料是注塑工艺的原料,它的性能直接影响着产品的质量和性能。
常见的塑料材料有聚丙烯(PP)、聚乙烯(PE)、聚氯乙烯(PVC)等。
选择合适的塑料材料需要考虑产品的用途、环境条件、成本等因素。
三、注塑机注塑机是注塑工艺的核心设备,它负责将塑料材料加热熔融,并将熔融的塑料注入模具中形成产品。
注塑机的选择需要考虑产品的尺寸、重量、注塑工艺要求等因素。
注塑机的操作和调试也对产品的质量和生产效率有着重要影响。
四、注塑工艺参数注塑工艺参数包括注射压力、注射速度、保压时间、冷却时间等。
这些参数的设置需要根据产品的要求和材料的特性进行调整。
合理的注塑工艺参数能够保证产品的尺寸精度、表面质量和物理性能。
五、注塑工艺流程注塑工艺流程包括模具安装、塑料材料的配料与干燥、注塑机的调试和运行、产品的冷却与脱模等。
每个环节都需要严格控制,确保注塑过程的稳定性和一致性。
合理的注塑工艺流程能够提高产品的生产效率和质量。
总结起来,注塑工艺的五大要素相互关联、相互影响,共同决定了注塑产品的质量和效率。
注塑工艺的优化需要综合考虑这五个要素,并进行合理的调整和控制。
只有在五大要素的协同作用下,才能生产出高质量的注塑产品。
注塑工艺的发展离不开对这五个要素的不断研究和创新,只有不断优化和改进,才能满足市场对注塑产品的需求。
注塑工艺的五大要素

注塑工艺的五大要素
一、温度:注塑过程中的温度控制是非常重要的,温度的不同会影响到熔融状态的塑料流动性、填充性和稳定性。
在注塑模具中,塑料熔融后会注入到模具腔中进行冷却成型,温度的控制可以影响到产品的尺寸和表面质量。
如果温度过高,塑料容易炭化或分解,而温度过低则会导致产品尺寸收缩不够。
二、压力:注塑过程中的压力控制也非常关键,它可以影响到塑料的流动性和填充性。
在注塑过程中,塑料会受到注塑机的压力作用被挤压入模具腔中,同时也可以起到排除空气、充实模具腔的作用。
过高或过低的压力都会影响到产品的质量和尺寸。
三、流速:流速是指塑料在注塑过程中的流动速度,它直接影响到塑料充实模具腔的速度和填充性。
流速过快会导致塑料在模具腔中的充实不充分,从而产生缩孔、短射等缺陷;而流速过慢则会导致模具腔中塑料的熔融温度过高,容易损坏模具。
四、冷却时间:冷却时间指的是塑料在模具腔中冷却固化的时间,这个时间对于产品的尺寸、收缩率和密度等都有着重要影响。
适当的冷却时间可以使产品充分固化,从而保证其尺寸稳定性和表面质量。
五、卸模时间:卸模时间指的是产品在模具中冷却固化后,从模具中取出的时间。
如果卸模时间过早,产品可能还没有完全固化就会变形或损坏;而如果卸模时间过晚,产品可能会粘附在模具上,难以取出。
因此,合理的卸模时间对于产品的成型质量和模具的使用寿命都是非常重要的。
总结起来,注塑工艺的五大要素包括温度、压力、流速、冷却时间和卸模时间,它们在注塑过程中相互关联、相互作用,对于产品的质量、尺
寸和表面质量都有着重要的影响。
注塑工艺的优化和控制需要综合考虑以上要素,以实现最佳的成型效果。
注塑成型五大要素解析
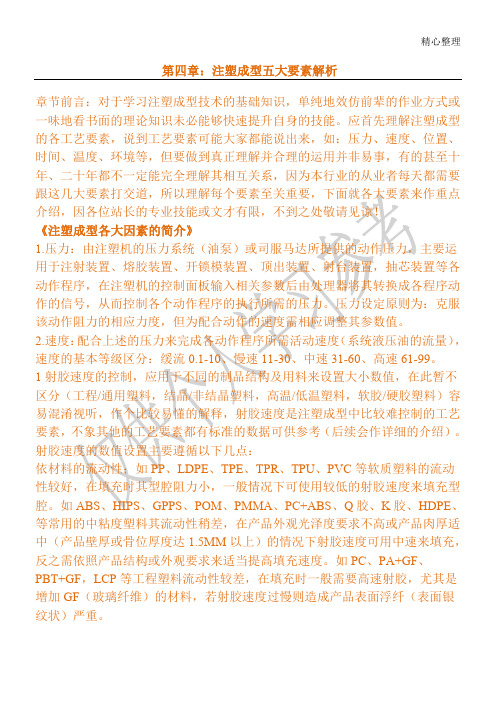
精心整理第四章:注塑成型五大要素解析章节前言:对于学习注塑成型技术的基础知识,单纯地效仿前辈的作业方式或一味地看书面的理论知识未必能够快速提升自身的技能。
应首先理解注塑成型的各工艺要素,说到工艺要素可能大家都能说出来,如:压力、速度、位置、时间、温度、环境等,但要做到真正理解并合理的运用并非易事,有的甚至十年、二十年都不一定能完全理解其相互关系,因为本行业的从业者每天都需要1.2.,。
1要素,。
腔。
如HDPE 、等常用的中粘度塑料其流动性稍差,在产品外观光泽度要求不高或产品肉厚适中(产品壁厚或骨位厚度达1.5MM 以上)的情况下射胶速度可用中速来填充,反之需依照产品结构或外观要求来适当提高填充速度。
如PC 、PA+GF 、PBT+GF ,LCP 等工程塑料流动性较差,在填充时一般需要高速射胶,尤其是增加GF (玻璃纤维)的材料,若射胶速度过慢则造成产品表面浮纤(表面银纹状)严重。
2.熔胶速度的控制;此参数在日常工作中是最容易被忽略的工艺之一,因大多数同仁认为该工艺对成型影响不大,参数随便调整都能做出产品来,但在注塑成型中熔胶参数是同射胶速度一样重要的,熔胶速度可直接影响到熔体混炼效果,成型周期等重要环节,在后面的章节中会作详细的介绍。
3.开锁模速度的控制;主要针对不同的模具结构来设置不同的参数,如两板平面模具在启动锁模低压前调整高速锁模及在产品脱离模具型腔后调整至快速开模可有效提高生产效率。
但有行位的模具在调整开锁模的速度时需根据行位的4.3.1.2.概括地理解为应对成型制品的所需射胶量来设置熔胶距离,多数同仁无视熔胶的三段切换位置,只会关注熔胶终点位置,当然;一般难度的成型制品在调整熔胶位置时不必对其进行快慢速或高低背压的切换,照样可以达到所需的制品质量,但在生产色母料、热敏性高的塑料适当切换熔胶速度及背压的调整位置,可更好地控制制品质量。
3.开锁模的位置控制;主要配合开锁模速度的需要来设置切换点3.1一般情况下开模速度的切换点为成型制品脱离模具型腔前(约5-15MM)为慢速,后转快速,可有效缩短开模所需时间,最后转慢速(即开模缓冲位置,一般离所需开模终止位置20-40MM为佳开始切换,(终止位置视产品结构及是否使用机械手而定),可有效延长注塑机机绞的使用寿命和开模动作的稳定)。
注塑五大要素,你可能有不知道的

注塑五大要素,你可能有不知道的玩注塑了解更多详情注塑就是塑胶材料在注塑机的料筒中经过外部的加热和螺杆的旋转而产生的剪切热对树脂材料进行塑化成熔体后,通过施加一定的压力,把熔体注射到具有一定的形状的型腔中经过冷却定型后所产生的物品就为注塑。
注塑工艺的五大要素1、温度A、油温:对于液压机而言是由于机器的不停运作液压油运动摩擦而产生的热能,它是由冷却水来控制,在开机时要确认油温在45℃左右,若油温过高或过低均会影响压力的传递。
B、料温:即炮筒温度,此温度要根据材料和产品的形状和功能去设定,若有文件则根据文件去设定它。
C、模温:此温度也是一个重要的参数,它的高低对于产品的性能影响很大,故设定时一定要考虑产品的功能和结构,同时还要考虑到材料和周期。
2、速度A、开合模的速度设定,开合模的设定一般是按慢—快—慢的原理,这样设定主要考虑机器、模具、周期去考虑。
B、顶出设定:可根据产品的结构来设定,结构复杂的最好用慢速顶出一些再用快速脱模,缩短周期。
C、射速:根据产品的大小,结构去设定,若结构复杂较为壁薄的可快速,若结构简单壁厚的可用慢速,还要根据材料的性能,由慢到快设定。
3、压力A、射胶压力:根据产品的大小,壁的厚薄,由低到高,调试时考虑其他因素。
B、保压压力:保压压力主要是确保产品的定型,稳定尺寸,其设定也要根据产品的结构、形状来设定。
C、低压保护压力:此压力主要对模具的保护作用,使模具的损坏达到最低限度。
D、锁模力:是指模具合模起高压所需要的力,有些机器可以调节锁模力,有些则不能。
4、时间A、射胶时间:此时间设定一定要比实际的时间长,也可起到射胶保护的作用,在射定时设定值比实际值大0.2秒左右,设定时应考虑与压力、速度、温度的配合。
B、低压保护时间:此时间在手动状态下,首先把时间设定为2秒,再根据实际时间追加0.02秒左右输入。
C、冷却时间:此时间一般根据产品的大小、薄厚来设定,但熔胶时间不要大于冷却时间,能使产品充分定型即可。
注塑成型五要素

注塑成形的五要素1、温度:料筒温度、材料温度、模具温度、干燥温度、油温度、环境温度等2、压力:注塑压力、保持压力、背压、脱模压力、开模压力、锁模压力等3、时间:注塑时间、保持时间、冷却时间、干燥时间、计量延迟时间等4、速度:射出速度、回车速度、开闭模速度、脱模速度等5、行程:计量行程、脱模行程、开模行程等在注塑成形中,这些要素是相互关联的,不能独立进行任意设定,而要把成形品的形状,树脂的种类,模具的构造等关系,都进行考虑,按注塑成形的最佳状态进行设定在进行成形条件的设定中,如何进行最佳设定和制品发生缺陷是如何改变设定是一件比较困难的事,因为诸因素都是相互影响的。
有些因素对某缺陷影响大些,有些则小些,而且对不同的材料也是不同的不正确的操作条件、损坏的机器及模具会产生很多成型缺陷,下面提供了一些解决方法供参考,为了减少停机的时间及能尽快找出问题的原因,操作人员应把最好的注塑成型条件记录在“注塑成型条件记录表”上,以供日后解决问题时参考之用。
浇口的尺寸大小与成型性关系尺寸大小(浇口尺寸)是同熔融材料流入型腔的流动性直接关联的因素。
浇口如果较大,不仅会产生充填不足(缺料),而且制品的凹痕,糊斑,熔接痕等外观不良的缺陷也容易发生。
还有在浇口小的场合,有成型收缩性变大的倾向。
而且从成型制品的强度来看,浇口太小,强度变弱。
然而相反的如果浇口太大,浇口的周围产生过剩的残余应力,是产生变形和裂纹的原因。
还有大的浇口横截面也大,这时固化的时间增长度,成型的产能不好。
考虑到以上各点,浇口的大小同成型品的生产性、品质等的关联,列表如下:浇口的方式同成形性,成型品品质的关系有特别大的关联 有关联一、填充不足通常情况下,填充不足是指塑料流动性不足不能充满整个型腔而得不到设计的制品形 状,填充不足还可能有以下方面的原因。
1、注射成型机注射能力不足这是对注射机的能力估计过高而产生的,由于塑化能力不足或者注射量不足也会发生。
其中,塑化能力不足可通过延长加热时间、增加螺杆转数、提高背压来提高塑化能力。
- 1、下载文档前请自行甄别文档内容的完整性,平台不提供额外的编辑、内容补充、找答案等附加服务。
- 2、"仅部分预览"的文档,不可在线预览部分如存在完整性等问题,可反馈申请退款(可完整预览的文档不适用该条件!)。
- 3、如文档侵犯您的权益,请联系客服反馈,我们会尽快为您处理(人工客服工作时间:9:00-18:30)。
注塑成形的五要素1、温度:料筒温度、材料温度、模具温度、干燥温度、油温度、环境温度等2、压力:注塑压力、保持压力、背压、脱模压力、开模压力、锁模压力等3、时间:注塑时间、保持时间、冷却时间、干燥时间、计量延迟时间等4、速度:射出速度、回车速度、开闭模速度、脱模速度等5、行程:计量行程、脱模行程、开模行程等在注塑成形中,这些要素是相互关联的,不能独立进行任意设定,而要把成形品的形状,树脂的种类,模具的构造等关系,都进行考虑,按注塑成形的最佳状态进行设定在进行成形条件的设定中,如何进行最佳设定和制品发生缺陷是如何改变设定是一件比较困难的事,因为诸因素都是相互影响的。
有些因素对某缺陷影响大些,有些则小些,而且对不同的材料也是不同的不正确的操作条件、损坏的机器及模具会产生很多成型缺陷,下面提供了一些解决方法供参考,为了减少停机的时间及能尽快找出问题的原因,操作人员应把最好的注塑成型条件记录在“注塑成型条件记录表”上,以供日后解决问题时参考之用。
浇口的尺寸大小与成型性关系尺寸大小(浇口尺寸)是同熔融材料流入型腔的流动性直接关联的因素。
浇口如果较大,不仅会产生充填不足(缺料),而且制品的凹痕,糊斑,熔接痕等外观不良的缺陷也容易发生。
还有在浇口小的场合,有成型收缩性变大的倾向。
而且从成型制品的强度来看,浇口太小,强度变弱。
然而相反的如果浇口太大,浇口的周围产生过剩的残余应力,是产生变形和裂纹的原因。
还有大的浇口横截面也大,这时固化的时间增长度,成型的产能不好。
考虑到以上各点,浇口的大小同成型品的生产性、品质等的关联,列表如下:浇口的方式同成形性,成型品品质的关系有特别大的关联有关联为了消除这种缺陷可提高溶料温度,提高模具温度,提高注射压力,加快注射速度,在熔料冷凝前使熔料流到型腔末端。
在这种场合,塑料良好的流动性特别重要,所以更换流动性好的塑料也是一种解决方法。
4、熔体的流程过大,流动阻力过大阻碍熔料流动的部位有喷嘴、主浇道、浇道、浇口和制件的薄壁处等。
采用如下方法可减小喷嘴流动阻力:加大喷嘴直径,提高喷嘴温度,使用流动阻力较小的喷嘴。
对于主浇道可增大其直径:对于浇道应避免采用流动阻力大的半圆形浇道,而采用圆形或梯形浇道,若增大直径则更好,同时必须使其长度为最短。
至于壁厚太薄造成的填充不足,可增加整个壁厚或增加局部壁厚,亦可在填充不足处的附近,设置辅助浇道或浇口来解决。
特别是被喷嘴最先注射出的熔料因被主浇道和浇道冷却,导致流动阻力变大,在这种情况下应开设大的冷料穴。
若因模具温度低而使流动阻力增大,提高模具温度也就可以了。
根据模具具体情况改变冷却水出入口位置,或者变更冷却水的流径路线,也会取得良好效果(因为模具温度不均匀)。
5、型腔内排气不良,充填模腔时,夹入空气,造成反压当熔料被注入型腔时,往往是一开始熔料就把型腔封闭,在局部未填充处残留有空气。
还因填充过快,空气有时来不及从分型面溢出而被压缩,造成局部未填充塑料,成型制件填充不足。
这种缺陷特别容易出现在模腔的转角处,深凹陷处和被厚壁部分包围着的薄壁部分。
即大多发生在用侧浇口成型时薄底的壳形件及长凸台的头部。
这样被封闭的空气受绝热压缩而达高温,有时会烧焦制件的局部(参照烧伤和黑色条纹部分)。
消除这种缺陷的措施是降低注射速度,给予一定的排气时间,若将模腔内的空气用真空泵排除,一般情况下很有效。
最好的方法是设置排气孔道,选择浇口位置使空气易于先排出,或从模具结构上考虑排气方式。
如把模腔局部制成镶件,使用空气从镶件缝隙溢出,或者在分型面上开设浅槽,还可以利用顶杆的缝隙来排气。
6、锁模力不足虽然可认为锁模力与填充不足没有关系,但有时这也是造成填充不足的原因。
即使使用注射量相同的成型机,有时也会出现锁模力不足的现象。
如果锁模力不足,在注射压力作用下动模稍微后退,将产生飞边毛刺而使制件注射量不足,也会产生填充不足的现象。
7、塑料供应不足尽管注射机能力足够,而从喷嘴注射出的熔料达不到所需数量,也可产生填充不足。
其原因,一是料斗的塑料粘边落不到料筒中(因塑料在料斗干燥机内局部熔化结块,使粉料或不规则颗粒料无法进入料斗;因为静电作用而吸附在料筒壁);一个是使用螺杆式注射成型机时,塑料在料筒内滑移,不能前进(塑料等级选择不当,颗粒料的润滑剂过多造成的,如改为配比正确的原料就可解决)。
一个是止逆环、过胶圈、熔胶螺杆磨损,导致熔料回流;一个是成型机的射嘴与模具的浇口衬套配合有间隙,溢胶导致。
8、塑料供给过剩如果进入料筒的塑料过多,注射压力因压缩颗粒而损耗,因此降低了注射成型所必需的从喷嘴射出熔料的压力,从而造成注射压力不足。
其解决方法是调整供料数量,使之恰好适合成型所需的塑料量。
二、开裂、裂纹、微裂和发白有的成型制件并没有局部破碎,只是表面产生微细的开裂,根据其程度和外观上的差别,把较严重的叫开裂或裂缝,较轻微的叫做微裂或龟裂,龟裂同裂纹看起来很像,但本质上是差异的两种意思,即龟裂不是象空隙样的缺陷,因加上的应力在平行方向排列的高分子自身,因而如对其加热,就能返回没有龟裂的状态,用这种方法就能够区分出龟裂和裂纹。
其中微裂不仅在成型后产生;放置后或与溶剂蒸气等接触时也会发生。
而ABS和耐冲击聚苯乙烯根本不产生这种现象,却以顶杆推顶部位发白的形式表现出来,采用热风加温则可消除这种发白现象。
产生上述现象的原因有下两几点。
白化指应力白色化,从图上应力屈服曲线同裂纹)身较脆、表面要求有光泽,大多采用镀铬模具成型。
然而电镀具有平面不易镀覆的性质,却易放覆到转角处;因而成为倒拔模斜度,所以必须予以特别注意。
另外,因聚碳酸脂(PC)、PVC等材料容易粘在模具的镀铬层上,特别在角落上成为倒锥体,所以要给以注意。
聚碳酸脂(PC)容易在模具镶块处产生裂纹,象这样的情况最好在材料里加进增强玻璃纤维为好。
有残余应力的制品因溶剂、油、药品的付着,会产生裂纹(以下讲的应力龟裂),微量的油付上后会产生很多的裂纹效应。
脱模斜度要足够,脱模销要分布平衡,制品上不要设计有锐角,还有要尽量避免制品的厚度差异。
只要仔细观察龟裂产生的位置,即可确定原因。
2、过填充由于过分担心成型缩孔,结果注入模腔的熔料过多,使成型制件内部产生极大的应变。
这时收缩变得很小,不但容易开裂,并且放置一段时间后内部应变更容易造成微裂。
要消除过填充的开裂可提高熔料温度、降低注射压力、提高模具温度,但只要保证熔料易于注入模腔即可。
根据成型制件外观等有关原因,必须以过填充的方式成型时,为使制件不发生微裂,成型后应进行后处理(如热处理),这对消除内部应变是有效的。
3、冷却不充分在未完全硬化时就将制件顶出,有时顶針周圍开裂或发白。
通过充分冷却或改变模具本身的冷却方式,等完全硬化后方可顶出。
也可以降低模具温度、延长冷却时间。
然而,有的模具的局部冷却不充分,在通常成型条件下还有时不能防止变形。
这种情况应考虑变更冷却水的路径、冷却水道的位置或追加冷却梢孔,尤其应考虑不用水冷,采用空气冷却等方式。
4、嵌件周围开裂置入嵌件成型时由于塑料的收缩,应力显著地集中在嵌件周围。
这个力虽然能牢固地保持住嵌件,但是应力过大时嵌件周围塑料往往开裂。
在注射成型的同时嵌入金属件时,最容易产生应力,而且容易在经过一段时间后才产生龟裂,危害极大。
这主要是由于金属和树脂的热膨胀系数相差悬殊产生应力,而且随着时间的推移,应超过逐渐劣化的树脂材料的强度而产生裂纹。
要减少嵌件周围的开裂,有效的是预热嵌件或尽量缩小收缩差,进行塑化处理效果更明显(即金属镶块预先加热,则可以缓和成型时的残余应力,同样的原理,用成型后的退火代替镶块加热也是一种方法)。
三、毛刺、溢料、彼峰多发生在分合面上,即动模与静模之间、滑块的滑配部位、镶件的缝隙、顶杆孔隙等处流入熔料,在制件上形成多余的飞边毛刺,这样的飞边毛刺,在成型时起杠杆作用、会使飞边毛刺进一步增大,从而造成模具局部的凹陷,使成型时飞边毛刺进一增大的恶性循环。
所以,如果一开始发现产生了飞边毛刺,就必须尽早修整模具。
毛刺的产生有下面几种原因。
1、锁模力不足.与成型制件的投影面积相比,如果锁模力较小,由于注射压力的作用使动、静模之间将出现缝隙,这样势必就会出现飞边毛刺。
特别是把侧浇口置于制件中央附近的孔上时,因为这种成型浇口需要较大的注射压力,所以极易出现毛刺。
降低注射压力或者提高锁模力都可消除这种缺陷,若根据具体情况改用流动性好的塑料采用低压成型,有时也是很有成效的。
2、模具局部配合不严密首先讨论动、静模合模不严的问题,尽管棋具本身合模严密,当采用肘杆式锁模机构的注射机成型时,往往因模具平行度不佳或者锁模装置调整的不良,产生诸如左右两边锁模不均衡的现象,即左右两侧只有—边被锁紧,另—边不密贴,此时必须调整拉杆(二根或四根拉扦)使之均衡,其次,也有因模具本身研配不佳造成密贴不严。
特别是制件中心有成型孔时,由于这部分的支承作用,当锁模力不充足时也容易出现毛刺。
另外是滑动型芯,因滑动型芯是动作机构,往往产生毛刺,所以滑动型芯的配合很重要。
尤其是对左右分型的哈夫模,其侧面的投影面积也受成型压力作用,如果设计不能完全承受这个压力也常会出现毛刺。
关于镶件缝隙和顶杆孔隙,不仅会产生毛刺恶性循环增大的现象,而且还会增大顶出阻力。
3、模具翘曲引起如果模具钢度不足,受注射压力作用将产生翘曲,这时若中心附近有孔,孔的周边就会产生毛刺;还有利用中心孔开侧浇口时,孔和浇道周边也会产生毛刺。
这种原因产生的毛刺,是由模具制作不良造成的,所以较难修理。
采取补强模具,可使毛刺减小。
4、塑料流动性过好塑料流动性过好,在理论上并不是产生毛刺的原因。
可是,当塑料流动性过好时,那怕是微细的缝隙塑料也能钻进去,所以极易出现毛刺。
要消除这种毛刺,可降低熔料温度或注射压力,也可降低模具温度或注射速度,5、注入熔料过多这也不是产生毛刺的直接原因。
为了防止缩孔而注入过多熔料的作法是错误的,应采取增加注射时间或保压时间来成型(参照缩孔)。
6、模具表面有异物模具合模面上有异物,必然会产生毛刺。
解决这个问题,显然应清扫于净模具表面,使合模面密贴即可。
7、根据不同材料确定不同排气槽的尺寸,因为排气槽过大,导致飞边的产生。
四、翘曲、弯曲和扭曲注射成型时塑料的成型收缩率随流动方向的不同而不同,就是说流动方向的收缩率远比垂直方向大(收缩率各向异性),有时收缩率在方向上的差值达1%以上;成型收缩率还受成型制件壁厚和温度的影响,由于收缩率的不同,致使制件产生变形。
注射成型是把粘流态的高聚物挤压到模腔中成型的一种方法,所以不可避免在成型制件内部残留有内部应力,此应力也将引起制件的变形。
此外还有一些原因也往往引起变形。
如制件未完全硬化就顶出的变形;还有顶杆推力造成的变形。
由于上述原因,将成型制件从模腔顶出后,就达不到内部应变最小的理想形状,而出现翘曲、弯曲和扭曲等现象。