电镀盐雾标准
电镀盐雾测试标准

电镀盐雾测试标准电镀盐雾测试是一种常用的腐蚀性测试方法,用于评估电镀表面处理的耐腐蚀性能。
本标准旨在规定电镀盐雾测试的方法和要求,以确保测试结果的准确性和可比性。
1. 范围。
本标准适用于各种金属材料的电镀层,包括镀铜、镀镍、镀铬、镀锌等。
它主要用于评估电镀层在盐雾环境中的耐腐蚀性能,以及相关材料的质量控制和产品改进。
2. 设备和试剂。
2.1 盐雾测试箱,应符合国家标准,能够稳定地产生盐雾环境,并能够控制温度和湿度。
2.2 试剂,使用符合规定浓度的NaCl溶液作为盐雾测试的试剂。
3. 试验条件。
3.1 温度,在35°C±2°C的条件下进行测试。
3.2 盐雾浓度,使用5%的NaCl溶液进行测试。
3.3 试验时间,根据不同的要求,测试时间可设定为24小时、48小时、96小时等。
4. 试验方法。
4.1 样品制备,将待测试的样品表面处理好,确保表面光洁、无油污和杂质。
4.2 测试装载,将样品放置在盐雾测试箱内,确保样品之间有足够的间隙,以保证盐雾的均匀覆盖。
4.3 试验过程,根据设定的试验条件,启动盐雾测试箱进行测试。
4.4 试验结束,根据设定的试验时间,停止测试并取出样品,进行评估和记录。
5. 评定标准。
5.1 腐蚀程度评定,根据样品表面的腐蚀程度进行评定,可采用GB/T 10125-2012《盐雾试验》中的相关标准进行评定。
5.2 试验结果记录,记录样品的腐蚀程度、试验时间、试验条件等相关信息,以备查阅和分析。
6. 注意事项。
6.1 样品制备时应注意避免表面污染,以免影响测试结果。
6.2 在测试过程中,应定期检查盐雾测试箱的工作状态,确保测试条件的稳定性。
6.3 在评定标准时,应严格按照相关标准进行评定,以确保结果的准确性和可比性。
7. 结论。
电镀盐雾测试是一项重要的腐蚀性测试方法,通过本标准规定的试验方法和要求,可对电镀层的耐腐蚀性能进行准确评定,为产品质量控制和改进提供可靠依据。
电镀产品做盐雾的标准方式

电镀产品盐雾测试标准方法一、目的本标准规定了电镀产品盐雾测试的设备、测试条件、测试程序和测试报告的编制。
通过本标准的应用,旨在确保电镀产品的耐腐蚀性能能够满足设计要求,并为产品质量评估和改进提供依据。
二、适用范围本标准适用于各种电镀产品(如镀锌、镀铬、镀镍等)的盐雾测试。
三、设备与材料1.盐雾试验箱:应具备温度控制、湿度控制和喷盐雾等功能,箱体应满足防腐蚀要求。
2.盐水溶液:应使用质量分数为5%的NaCl溶液。
3.计时器:用于记录盐雾测试的时间。
4.温度计:用于测量盐雾试验箱内的温度。
5.湿度计:用于测量盐雾试验箱内的湿度。
6.漆膜厚度计:用于测量电镀产品的漆膜厚度。
7.照度计:用于测量盐雾试验箱内的光照强度。
四、测试条件1.温度:应控制在35℃±2℃范围内。
2.湿度:应控制在95%±5%范围内。
3.盐水溶液浓度:应控制在5%±0.5%范围内。
4.喷盐雾量:应控制在1~2ml/h范围内。
5.测试时间:应不少于24小时,具体时间根据产品要求和实际情况确定。
6.光照强度:应控制在300~500 lux范围内。
五、测试程序1.电镀产品应在符合要求的盐雾试验箱内进行测试。
2.测试前应对电镀产品进行清洁处理,去除表面的污垢和杂质。
3.将电镀产品放置在盐雾试验箱内的支架上,确保产品表面与喷嘴距离适中,以便盐雾能够均匀地喷洒在产品表面上。
4.开启盐雾试验箱,设定测试温度、湿度和喷盐雾量等参数,启动设备开始测试。
5.在测试期间,应定期检查电镀产品的表面状况,观察是否出现腐蚀现象。
如发现异常情况,应及时记录并处理。
6.测试结束后,关闭盐雾试验箱,取出电镀产品进行清洁处理,并记录测试结果。
7.根据测试结果对电镀产品的耐腐蚀性能进行评价,并提出改进意见或建议。
六、测试报告编制1.测试报告应包括以下内容:测试产品名称、规格型号、生产厂家、测试时间、温度、湿度、盐水溶液浓度、喷盐雾量、光照强度等参数信息。
金属电镀产品做盐雾腐蚀性试验的试验方法和判定标准.doc

金属电镀产品做盐雾腐蚀性试验的试验方法和判定标准
金属电镀产品做盐雾腐蚀性试验的试验方法和判定标准为:金属材料无论是铁还是不锈钢,电镀层可以为锌/铜 /银 / 镍等等,喷塑金属件应为铁框。
试验方法:
1.温度设定为35°C;
2.使用 5+/-1% 的 NaCl 溶液;
3.盐雾沉降量为2+/-1ml/80cm2/h ;
4.PH 值为 6.5~7.2 ;
5.试验持续时间为48h。
试验判断标准:
表面处理层有无氧化,脱落,褪色,锈迹,腐蚀等现象。
金属材料是铁还是不锈钢,电镀层为锌 /铜 /银 /镍等等,喷塑金属件应为铁框。
附表:国家有关镀层盐雾试验的规定和判定方法
基体
金属零件类别
材料
碳钢一般结构件
紧≥ M16
固M8-M1
件 4
<M16
弹性件
铜及一般结构件
铜合
金紧固件
弹性件
后使用条
镀层类别处件最小厚度试验周期及合格要求
理
Ⅰ24+12+0.3 4
Cu+Ni+Cr 抛Ⅱ12+12+0.3 3 主要表面无棕色锈点
光Ⅲ6+6+0.3 2
Ⅰ36+0.3
Zn 钝Ⅱ24+0.3
化Ⅲ12+0.3
Ⅰ、Ⅱ、12
Zn Ⅲ9 4 主要表面无白色或灰黑色腐蚀物
6
除Ⅰ、Ⅱ12
Zn 氢Ⅲ 6
钝
化
Ni+Cr 抛Ⅰ、Ⅱ9+0.3
光Ⅲ6+0.3 6主要表面无浅绿色腐蚀物
Ni 或高锡Ⅰ、Ⅱ、主要表面无浅绿色或灰黑色腐蚀物青铜Ⅲ 6 3
Ni。
电镀锌盐雾试验标准

电镀锌盐雾试验标准电镀锌是一种常见的防腐蚀处理方法,通过在金属表面镀上一层锌来防止金属氧化腐蚀。
然而,电镀锌的质量和耐腐蚀性能需要经过一系列的测试和试验来验证。
其中,盐雾试验是一种常用的测试方法,用于评估电镀锌在盐雾环境中的耐腐蚀性能。
本文将介绍电镀锌盐雾试验的标准及相关内容。
首先,电镀锌盐雾试验的标准主要包括GB/T 10125-2012《电镀层耐腐蚀试验》和ASTM B117-16《盐雾试验标准方法》。
这两项标准分别由中国国家标准化管理委员会和美国材料与试验协会发布,是国际上公认的电镀锌盐雾试验标准。
在进行电镀锌盐雾试验时,需要严格遵循这两项标准的要求,以确保测试结果的准确性和可靠性。
其次,电镀锌盐雾试验的具体步骤包括样品准备、试验条件设定、试验时间安排、试验结果评定等。
在样品准备阶段,需要选择代表性的电镀锌样品,并进行表面清洁和处理,以确保试验结果的准确性。
在试验条件设定阶段,需要根据标准要求设置盐雾试验箱的温度、湿度和盐水浓度等参数,以模拟真实的盐雾腐蚀环境。
在试验时间安排阶段,需要根据标准要求确定试验的持续时间,通常情况下为24小时、48小时、96小时甚至更长时间。
在试验结果评定阶段,需要对试验后的样品进行表面观察和质量评定,以判断电镀锌的耐腐蚀性能。
此外,电镀锌盐雾试验的结果评定主要包括试验后的样品表面状况、腐蚀产物的数量和分布、试验时间内的腐蚀速率等。
通过对这些指标的评定,可以客观地评估电镀锌在盐雾环境中的耐腐蚀性能,为产品质量的控制和改进提供依据。
总之,电镀锌盐雾试验是评估电镀锌耐腐蚀性能的重要方法,其标准和步骤对于确保测试结果的准确性和可靠性至关重要。
只有严格遵循标准要求,并结合实际情况进行合理的试验设计和结果评定,才能有效地评估电镀锌的耐腐蚀性能,为产品质量的提升和改进提供可靠的依据。
电镀产品盐雾测试标准

电镀产品盐雾测试标准
电镀产品盐雾测试是指将电镀产品放置在盐雾环境中进行测试,以评估其防腐
蚀性能。
盐雾测试是电镀产品质量控制的重要环节,也是客户对产品质量的重要检验标准之一。
本文将详细介绍电镀产品盐雾测试的标准及相关注意事项。
首先,电镀产品盐雾测试的标准应符合国家相关标准,如GB/T 10125-2012
《盐雾试验室技术条件》和GB/T 2423.17-2008《电工电子产品盐雾试验》等。
这
些标准规定了盐雾测试的试验条件、试验方法、试验设备、试验周期等内容,确保了测试的科学性和可靠性。
在进行电镀产品盐雾测试时,应注意以下几点,首先,要选择合适的测试设备
和试验条件,确保测试结果的准确性。
其次,应根据产品的具体材料和工艺特点,确定合理的测试周期和试验方法。
同时,还应注意测试样品的制备和标定,确保测试结果的可比性和可靠性。
另外,还需要注意测试过程中的环境控制和数据记录,避免外界因素对测试结
果的影响。
同时,要定期对测试设备进行维护和校准,确保测试的准确性和可靠性。
最后,要对测试结果进行合理的分析和评价,及时发现问题并采取相应的改进措施。
总之,电镀产品盐雾测试是评估产品防腐蚀性能的重要手段,其标准和注意事
项对产品质量控制至关重要。
只有严格遵循标准要求,合理设计测试方案,科学进行测试,才能确保产品质量的稳定和可靠。
希望本文所述内容能为相关从业人员提供一定的参考和帮助。
电镀件盐雾试验判定标准

电镀件盐雾试验判定标准电镀件在使用过程中,常常会遭受到化学腐蚀和电化学腐蚀的影响,为了保证电镀件在使用过程中的质量和耐用性,盐雾试验成为了检测电镀件性能的必要手段之一。
电镀件盐雾试验是指将被测物理放入盐雾试验箱中,置于指定的温度和湿度条件下,以模拟实际环境中的化学腐蚀或电化学腐蚀等恶劣环境,判定其表面质量等级的试验。
一、盐雾试验的分类目前,国际上对电镀件盐雾试验一般分为两种不同的测试方法,分别是NSS测试和CASS测试。
1.NSS测试NSS测试全称为中性盐雾测试,是指将pH值为6.5~7.2的盐雾液喷射在试样表面,在相对湿度为95%的条件下,在规定的测试时间内进行腐蚀测试,测试时间一般为24小时、48小时、72小时、96小时等。
1.试样的初期腐蚀状态试样的初期腐蚀状态是指在规定的测试时间内,被测物表面出现的腐蚀程度。
腐蚀情况如下表所示:腐蚀程度解释0级试样表面未发现任何腐蚀1级试样表面腐蚀程度极轻微,只有零星点状或者灰尘状的腐蚀斑点4级试样表面腐蚀程度较重,表面开始分层脱落5级试样表面腐蚀程度严重,出现明显的划痕和磨损3级试样表面腐蚀程度中等,且腐蚀斑点面积不超过35%3.试样的气孔和开裂状况1级无气孔和开裂2级气孔和开裂面积不超过5%三、结论通过对电镀件盐雾试验判定标准的了解,我们可以知道,盐雾试验对于检验电镀件的质量和耐用性具有重要作用。
在盐雾试验中,试样的初期腐蚀状态、总体腐蚀状态和气孔开裂状况是判定被测物是否合格的重要因素,根据相关规定和要求,对试样的各项指标进行评估,最终得出判定结果。
此外,需要注意的是,盐雾试验仅能反映被测试电镀件在特定环境下的性能,不足以代表其在实际使用过程中的全部性能,因此,应加强检验管理,从多个角度综合评估电镀件的质量和可靠性。
盐雾试验国家标准

GB6458-86 盐雾试验国家标准表面处理用盐水喷雾试验法Method of Salt Spray Fog Test for Surface Finishing 1.适用范围:本标准规定为各项金属底材于电镀后、有机或无机涂装后等各项表面处理用盐水喷雾耐蚀性试验方法..2.试验方法:本法是使用盐水喷雾试验机将氯化钠溶液的试验液;以雾状喷于电镀被覆膜上之一种腐蚀试验方法..试验的主要条件如表1所示..表1主要的试验条件项目配制时试验中备注氯化钠溶液浓度g/l 50 40~60 最好每天标定浓度一次收集后测定试验中的pH值压缩空气压力kgf/cm2……1.00kgf/cm20.01连续不得中断喷雾量ml/80cm2/h……1.0~2.0ml应至少收集16小时;求其平均值压力桶温度℃……47℃±1℃监水桶温度℃……35℃±1℃试验室温度℃……35℃±1℃每天至少测两次;其间隔至少7小时试验室相对湿度……85%以上其它湿度要求由买卖双方协议之试验时间:即由开始喷雾至终了的连续时间;或由买卖双方协议之..3.试验液之配制:溶解试药级氯化钠1 于蒸馏水或总溶解固体量小于200ppm以下的水中;调配成浓度为5%的试验液2 此试验液在35℃喷雾后;其收集液pH值应为6.5~7.33 且喷雾前;此试验液不能含有悬浮物4 注1:氯化钠不能含有铜与镍的不纯物;固体内的碘化钠含量须小于0.1%..因为不纯物中可能含有腐蚀抑制剂;所以不纯物总含量须小于0.3%..2:在33~35℃间测量此试验液的比重应为1.0258~1.0402;在25℃测量时的比重则为 1.0292~1.0443..此试验液的浓度亦可利用硝酸银溶液滴定法或其它方法标定..3:试验液须以试药的监酸或氢氧化钠稀溶液调整pH值;并以pH仪或其它可靠方法测量之由于配制试验液的水中含有二氧化碳;二氧化碳在水中的溶解度随温度改变而影响溶液的pH值;故须小心控制pH值..pH值则可依下列任一方法调整:a.常温配制试验液;于35℃喷雾;因为温度的升高而使部份二氧化碳逸出溶液而升高pH值..故在常温配制试验液时;pH值应调整在6.5内;才可以使收集液的pH值在6.5~7.2之间b.pH值调整前;使试验液先煮沸再冷至35℃;或维持在35℃温度48小时..如此调整的pH值在35℃喷雾时;将不会产生太大变化..c.先将水加热至35℃以上;以去除溶解的二氧化碳;而后再调制试验液并调整pH值..如此在35℃喷雾时;所调整的pH值也不会产生太大变化..4:为避免喷雾嘴阻塞;此试验液须过滤或小心倾斜注入盐水桶;或于喷雾吸水管前端处装上玻璃过滤器或适当之纱布为宜..4.试验设备: 本试验所需之设备为喷雾嘴、盐水桶、试验片支持架、喷雾液收集容器、试验室5、盐水补给桶、压力桶、压缩空气之供给设备与排气设备等所构成;并依照如下条件试验..备注5:试验室大小;须在0.48m3以上..4.1盐水喷雾试验机与其所需的管路应采用纯性材料;不能对喷雾之腐蚀试验有影响或本身被腐蚀者..4.2喷雾嘴不可直接将试验液喷向试样;喷雾室顶部聚集之溶液不得滴落在试验片上..4.3试验片滴下之试验液不可流回盐水桶;而再用于试验..4.4压缩空气不能含有油脂及灰尘;所以须有空气清净器..空气压力须保持在1.000.01kgf/cm2;因为压缩空气于膨胀时;有吸热现象;所以须事先有预热6;如附表1;以获取均一温度的喷雾..注6:预热以增加压缩空气的温度与湿度..4.5喷雾采取器其水平采取面积为80cm2;直径约为10cm;置于试验片附近靠近喷嘴最近与最远之处的两个地方..4.6喷雾液量以整个时间计算;在采取容器上;应每小时平均可收集 1.0至2.0ml之盐水溶液..喷雾液至少应收集16小时;以其平均值表示喷雾量..4.7试验中盐水桶;其氯化钠溶液浓度应维持40~60g/l..4.8压力桶之温度须保持在471℃;盐水桶之温度在351℃..4.9试验室的相对湿度须保持在85%以上;更高的相对湿度的要求可由买卖双方协议之..5.试样:5.1采取位置:试样可从制品之主要表面采取或以制品本身做为试样..但如无法以制品试验或判定时;可由当事者双方协议以试验片代替..此试验片必须能代表该制品者..5.2尺度:试验片之标准尺寸为15070mm;或为10065mm..5.3数目:试样之数目由买卖双方协议之..5.4试验前处理5.4.1试样依镀层性质与清洁程度而须做适当清洗;不能使用研磨剂7及具有腐蚀或抑制作用之溶剂清洗;且清洗方法不得损伤表面..至于不锈钢试样可由买卖双方协议使用硝酸清洗与钝化..试样经清净后通过拨水性试验;以干净之布或吸水纸将水份擦干;或用无油之干燥空气吹干.. 注7:不得已时;可使用氧化镁膏..此膏状物乃10g试药级氧化镁加入100ml的蒸馏水中..5.4.2若非另有规定;否则试样切口及因挂勾而造成底材露出部份;或因识别记号所造成镀层缺陷处; 于试验时应覆以合适之保护层..如硬蜡ceresinwax;乙烯胶带等绝缘物..5.4.3手纹污染会造成严重的不良试验结果;试样于清净后不得有任何手纹的污染..6.试样之置放:试验中;试验室内之试样的位置须符合下列条件:6.1试样之主要表面与铅垂线成15度至30度之倾斜;又自试验室上方俯视时应与喷雾之主要流动方向平行..特殊零件具有很多方向的主要表面需要同时测试时;可取多件试样置放;务必使每个主要表面能同时接受监水的喷雾..6.2试样之排列;应使喷雾自由地落至全部试片上;不应防碍喷雾之自由落下..6.3试样不可互相接触;也不可接触到金属性导体或有毛细现象作用之物质;以及其它支持架以外之物..6.4盐水溶液勿从一个试样滴流至其它试样上..6.5试样识别记号或装配孔应覆于下方..7.试验操作:将试验室及盐水桶之温度调整至摄氏35度;压力桶之温度为摄氏47度;喷雾压力保持在时;即可开始喷雾..7.1试验条件:试验条件如表1..7.2试验时间:为自喷雾开始至终了之连续时间..试验时间为电镀层的一重要质量数据;其所需时间可由买卖双方协议之..7.3试验后处理:喷雾试验完毕;开启试验室上盖时;勿使溶液滴下而小心取出试样;不得损伤主要表面;尽速以低于38℃之清水洗去黏附之盐粒;用毛刷或海棉去除腐蚀点以外之腐蚀生成物;并立即以干净压缩空气干燥之..8.试验记录:若非买卖双方另有协议;否则本试验应有下列之记录:附表2为参考性记录表8.1配制监水时;所使用的监与水的质量..8.2试验温度记录..8.3喷雾采取器的装置;每天应如下列记录:8.3.1喷雾量8.3.2收集溶液在室温时的比重或浓度..8.3.3收集溶液的pH值..8.4试样的种类、形状、尺度与数目..8.5试样的前处理清洗与后处理清洗方法..8.6试样于试验室内的置放方法..8.7依第5.4.2节所用的被覆方法..8.8喷雾时间..8.9试验时间若有中断;则须记录其中断的原因与时间..8.10其它检查的所有结果..9.判定方法:测定面腐蚀状况判定;可依照图2至13所示之等级号码标准图表施行..起泡、裂痕等使用标准图表难以判定者;可用附有标尺的放大镜判定;或由买卖双方事先协定之方法判定之..盐雾试验标准可做试验有:中性盐雾试验简称NSS 酸性盐雾试验简称ASS铜盐加速乙酸试验简称CASS适用国家标准CNS 3627、3385、4159、7669、8886JIS D0201、H8502、H8610、K5400、Z2371ISO 3768、 3769、3770ASTM 8117、B268试验室温度: NSS.ACSS 35 ±1℃/ CASS 50℃±1℃饱和桶温度: NSS.ACSS 47℃±1℃/ CASS 63℃±1℃1 GB/T 10125-1997人造气氛腐蚀试验盐雾试验简介等效采用ISO 9227:1990人造气氛腐蚀试验-盐雾试验制定的GB/T 10125-1997;自发布实施日起代替:GB 6458-86金属覆盖层中性盐雾试验NSS试验GB 6459-86金属覆盖层醋酸盐雾试验ASS试验GB 64060-86金属覆盖层铜加速醋酸盐雾试验CASS试验GB 10125-88人造气氛中的腐蚀试验盐雾试验SS试验与ISO 9227比较;该标准考虑到试验初期试样的变化较大;将推荐的试验周期定为2 h; 4 h;6 h;8h;24h;48h;96 h;168 h;240 h;480 h;720 h;1 000 h;增加了4 h 和8 h..标准中规定了中性盐雾NSS、乙酸盐雾ASS和铜加速乙酸盐雾CASS试验使用的设备、试剂和方法;规定了评估试验箱环境腐蚀性的方法;未规定试样尺寸、特殊产品的试验周期和结果解释;这些内容参见相应的产品规范..该标准适用于评价金属材料及覆盖层的耐蚀性;被测试对象可以是具有永久性或暂时性防蚀性能的;也可以是不具有永久性或暂时性防蚀性能的..标准中的中性盐雾试验适用于金属及其合金、金属覆盖层、有机覆盖层、阳极氧化膜和转化膜;乙酸盐雾试验和铜加速乙酸盐雾试验适用于铜+镍+铬或镍+铬装饰性镀层;也适用于铝的阳极氧化膜..2 标准制修订1999年计划完成的标准制定项目:GB/T金属覆盖层孔隙率试验潮湿硫硫花试验相当于ISO12687:1996;负责起草单位:武汉材料保护研究所GB/T金属磷化粉负责起草单位:成都祥和磷化有限公司GB/T水性涂料涂装体系选择通则负责起草单位:武汉材料保护研究所3 表面工程最新国际标准目录ISO 11474-1998金属和合金的腐蚀人造大气中的腐蚀试验用盐溶液间歇式喷射户外验收试验疤点试验ISO 14918:1998热喷涂热喷涂操作人员的资格考核ISO/DIS 4525金属覆盖层塑料上的镍+铬电镀层修订ISO4525:1985ISO/DIS 15730金属及其他无机涂层不锈钢镘光和钝化的电抛光工艺4 金属表面处理日本标准目录基础部分JIS B 0601:1994表面粗糙度--定义及表示方法JIS C 0023:1989 环境试验方法电气.电子盐水喷雾试验方法JIS C 0024:1989环境试验方法电气.电子盐水喷雾循环试验方法JIS Z 0103:1996防锈防蚀术语JIS Z 0304:197485金属防锈处理大气暴露试验方法JIS Z 2243:1992维氏硬度试验方法JIS Z 2246:1992 肖氏硬度试验方法JIS Z 2247:1993埃里克森杯突试验方法JIS Z 2248:1996金属材料弯曲试验方法JIS Z 2249:196389 圆锥杯实试验方法JIS Z 2251:1998 努氏硬度试验--试验方法JIS Z 2371:1994盐水喷雾试验方法JIS Z 2381:1987室外暴露试验方法通则JIS Z 8701:1995颜色的表示方法--XYZ表色系与X10Y10Z10表色系JIS Z 8716:1991 用于比较表面颜色的常用光源萤光灯D65--形式和性能 .. JIS Z 8723:1988表面颜色的视觉比较方法JIS Z 8741:1997镜面光泽度--测定方法JIS Z 8802:1984 pH测定方法待续表面处理用醋酸铜盐水喷雾试验法1.适用范围:本标准规定了各项金属底材于电镀装饰用铜-镍-铬、铜铁或锌压铸件底材于电镀镍-铬后;以及铝阳极处理后等各项表面处理的醋酸铜盐水喷雾耐蚀性试验方法..2.试验方法:本方法是使用盐水喷雾试验机将含有氯化铜的醋酸-氯化铜试样液;以雾状喷于电镀被覆膜或氧化膜上之一种腐蚀试验方法..试验的主要条件如下表所示..项目配制时试验中备注氯化钠溶液浓度g/l5045-55最好每天标定一次氯化铜溶液浓度g/l0.26--------PH值3.03.0-3.2收集后测定试验中的PH值压缩空气压力㎏f/㎝2------1.00±0.01连续中不得中断喷雾量ml/80㎝2/h------1.0-2.0应至少收集16小时;求平均值压力桶温度℃------63±1盐水桶温度℃------50±1试验室温度℃------50±1每天至少测试两次;其间隔至少7小时试验室相对湿度------85%以上其他湿度要求;由买卖双方协议而定试验时间------------即由开始喷雾至终了的时间;或由买卖双方协定3. 试验液的配制:试验液依下列顺序配制..3.1溶解试剂氯化钠于蒸馏水中或总溶解固体量小于200ppm以下的水中;调配成浓度为5%的盐水液①..此盐水液的PH值应在6-7之间;否则蒸馏水或氯化钠中可能有不纯物存在..3.2于每公升的盐水液中添加0.26g试剂氯化铜CuCl2·2H2O;混合搅拌使其完全溶解.3.3并以试药剂冰醋酸调整此含氯化铜的盐水液的酸碱值;使其收集液的PH值为3.0-3.2②;即成试验液.3.4 喷雾前;此试验液不能含有固体悬浮物③ . 注①:在25℃测量试验液的比重应为1.03-1.04之间.此试验液中的氯化钠浓度亦可利用硝酸银溶液滴定法或其他方法标定. ②:每公升盐水液中所需的冰醋酸调整量;如果大于1.6ml或小于1.3ml;则试验系统中可能有某些问题存在.例如PH值不标准、蒸馏水或氯化钠含有不纯物或者试验系统不清洁. ③:为避免喷雾喷嘴阻塞;此试验液须过滤或小心倾斜地注入盐水桶;或于喷雾吸水管前端处装上玻璃过滤器或适当的纱布为宜.4.设备:本试验所需之设备为喷雾喷嘴、盐水桶、试验片支架、喷雾液收集水桶、试验室④、盐水补给桶、压力桶、压缩空气的供给设备与排气设备等构成;其装置如图1所示;并按照如下条件试验..注: ④试验室的大小;须在0.43m3以上.4.1盐水喷雾试验机与其所需的管路应采用纯性材料;不能对喷雾液的腐蚀试验产生影响或本身会被腐蚀者.4.2 喷雾喷嘴不可直接将试验液喷向试样;喷雾室顶部聚集的溶液不得滴落在试验片上.4.3 试验片滴下的试验液不可流回盐水桶;而再用于试验.4.4压缩空气不能含有油脂及灰尘;所以必须有空气清净器;空气压力调整为获取适宜喷雾量为准.因为压缩空气于膨胀时;有吸热现象;所以须事先预热;以获取均匀温度的喷雾⑤注⑤:预热以增加压缩空气的温度和湿度.4.5喷雾采取器其水平采取面积为80㎝2;直径为10㎝;置于试验片附近靠近喷嘴最近与最远之处的两个地方.4.6喷雾液量以调个时间计算;在采取容器上;应每小时平均可收集1.0ml-2.0ml的试验液.喷雾液至少应收集16小时;以其平均值表示喷雾量.4.7 试验中盐水桶;其氯化钠浓度应维持45-55 g/l.4.8 压力桶的温度须保持在63±1℃;盐水桶的温度应保持在50±1℃.4.9 试验室的相对湿度须保持在85%以上;更高相对湿度的要求可由买卖双方协定.5. 试样5.1采取位置:试样可从制品的主要表面采取或以制品本身作为试样.但如无法以制品试验或判断时;可由当事者双方协定以试验片代替.此试验片必须能代替该制品.5.2 尺度:试验片的标准尺寸为150×70㎜;或为100×65㎜.5.3 数目:试样的数目由买卖双方协定.5.4 试验前处理5.4.1试样依镀层性质与清洁程度而须作适当清洗;不能使用研磨剂⑥及具有腐蚀或抑制作用的溶剂清洗;且清洗方法不得损伤表面.但是阳极处理的铝试片须以含有抑制剂的三氯乙烷溶剂清洗⑦.至于不锈钢试样可由买卖双方协定使用硝酸清洗与钝化;试样经清净后通过拨水性试验;以干净的布或吸水纸将水分擦干;或者用无油的干燥空气吹干. 注:⑥不得已时;可使用氧化镁膏.此膏状物是10g试药剂氧化镁加入100ml蒸馏水中形成的. ⑦:使用此有机溶剂清洗时;须在通风良好而无火焰处.5.4.2若非另有规定;否则试样切口及因挂勾而造成底材露出部分;或因识别记号所造成镀层的缺陷处;在试验时应覆以适当的保护层;如硬蜡、乙烯胶带等绝缘物.5.4.3 手纹污染会造成严重的不良试验结果;故试样于清净后不得有任何手纹的污染.6. 试样的放置:试验中;试验室内试样位置须符合下列条件6.1试样的主要表面与铅垂线成15±2度的倾斜或由买卖双方协定其他角度;又自试验室上方俯视时应与喷雾的主要活动方向平行.特殊零件具有多方向的主要表面需要同时测试时;可取多件试样同时放置;务必使每个主要表面能同时接受盐水的喷雾.6.2 试样的排列方式应使喷雾自由地落至全部试片上;不应妨碍喷雾的自由落下.6.3试样不可互相接触.也不可接触到金属性导体或毛细现象作用的物质;及其他支持架以外之物.6.4 盐水溶液勿从一个试样滴流至其他试样上.6.5 试样识别记号或装配孔应覆于下方.7.操作:将试验室及盐水桶的温度调整至50度;压力桶的温度为63度;喷雾压力保持在1.00±0.01㎏f/㎝2时;即可开始喷雾.7.1试验条件:试验条件如表1.7.2试验时间:为喷雾开始至结束的连续时间.试验时间为电镀层的一项重要品质资料;其所需时间可由买卖双方协定..7.3试验后处理:喷雾试验完毕;开启试验室上盖时;勿使溶液滴下而小心取出试样;不得损伤主要表面迅速以低于38度的清水洗去黏附的盐粒;用毛刷或海棉去除腐蚀点以外的腐蚀生成物;并立即以干净压缩空气干燥.8. 记录:若非买卖双方另有协定;否则本试验应有如下记录8.1 配制盐水时;所使用的盐和水的品质.8.2 试验室温度记录.8.3 喷雾采取器的装置;每天应具有下列记录:8.3.1 喷雾量8.3.2 收集溶液在室温时比重或浓度.8.3.3 收集溶液的PH值.8.4 试样的种类、形状、尺度与数目8.5 试样的前处理清洗与后处理清洗方法.8.6 试样于试验室内的置放方法.8.7 依第5.4.2节所用的被覆方法.8.8 喷雾时间.8.9 试验时间若有中断;则需记录其中断的原因与时间.8.10 其他检查所有结果.9.判定方法:测定腐蚀状况判定;可按国家标准中的标准图对照施行.起泡、裂痕等使用标准图难以判定的;可用附有标尺的放大镜判定;或由买卖双方协定.1> 中性盐雾试验NSS本方法是我国广泛采用的试验方法;它是用来模拟沿海地区大气环境条件;适用于金属及其合金、金属覆盖层、有机覆盖层、阳极氧化膜和转化膜等..间歇盐水喷雾比连续喷雾更接近于海洋及沿海条件..间歇试验可使腐蚀产物吸湿后影响腐蚀;如两次喷射间的时间足够长;腐蚀产物便会干燥、发硬、开裂;这与自然条件下出现的现象往往类似..有孔隙的镀层;可作极短暂的盐水喷雾;以免由于腐蚀而产生新的孔隙..2> 醋酸盐雾试验ASS试验针对在城市大气中行驶的汽车等镀件;为了缩短实验时间;在盐溶液中加入酸乙酸..它适用于各种无机及有镀层和涂层、黑色及有色金色;如铜-镍-铬镀层、镍-铬镀层、铝的阳极氧化膜等..除溶液配制与中性盐雾试验不同外;其它均相同..3> 铜加速的醋酸盐雾试验CASS试验通过对地区雨水成分的分析以及对试验加速添加剂进行大量研究;发现往醋酸盐雾试验中添加氧化铜可大大增加介质腐蚀性;且腐蚀特征与实际情况下发生严重腐蚀的特征十分相似;因而进步制定了加速的CASS试验方法..而在我们的工作中;对不锈钢工件做的是中性盐雾试验NSS;间歇盐水喷雾。
电镀件盐雾试验标准

电镀件盐雾试验标准电镀件在工业生产中广泛应用,其表面处理工艺中的盐雾试验是非常重要的一环。
盐雾试验是指将试验样品放置在一定浓度的盐水溶液中,通过模拟海洋气候条件对材料进行腐蚀性能的评定。
本文将介绍电镀件盐雾试验标准,以便相关行业人士了解和掌握相关知识。
首先,电镀件盐雾试验的标准主要包括试验方法、试验设备、试验条件和试验评定等内容。
试验方法一般包括连续盐雾试验、间歇盐雾试验和循环盐雾试验等,不同的试验方法适用于不同的电镀件材料和工艺要求。
试验设备包括盐雾试验箱、喷雾器等,这些设备的选用和使用对试验结果具有重要影响。
试验条件包括试验温度、盐水浓度、喷雾时间等,这些条件的设定需要符合相关标准和规范要求。
试验评定则是根据试验结果对电镀件的腐蚀性能进行等级评定,以指导产品的质量控制和改进工艺。
其次,电镀件盐雾试验标准的制定和执行对于保障产品质量和延长使用寿命具有重要意义。
制定科学合理的盐雾试验标准,可以有效评定电镀件的耐腐蚀性能,指导生产工艺和改进材料配方,提高产品质量和市场竞争力。
同时,严格执行盐雾试验标准,可以及时发现产品质量问题,防止不合格品流入市场,保障消费者的权益和企业的声誉。
最后,电镀件盐雾试验标准的不断完善和提高对于推动行业的发展和技术创新具有重要作用。
随着电镀件在汽车、航空航天、电子等领域的广泛应用,对材料的耐腐蚀性能要求越来越高,盐雾试验标准也需要不断更新和完善,以适应新材料、新工艺和新应用的需求。
同时,加强盐雾试验标准的国际合作和交流,可以促进全球电镀件行业的共同发展,推动技术创新和质量提升。
综上所述,电镀件盐雾试验标准是电镀件生产和质量控制中不可或缺的重要环节。
只有严格遵守标准规范,不断完善和提高试验方法和评定标准,才能有效保障产品质量,满足市场需求,推动行业的可持续发展。
希望本文能够对相关行业人士有所帮助,促进电镀件盐雾试验标准的科学实施和推广应用。
电镀件盐雾测试标准

电镀件盐雾测试标准电镀件盐雾测试是指将电镀件放置在盐雾环境中进行测试,以评估其在腐蚀条件下的耐蚀性能。
这项测试在工业领域中被广泛应用,特别是对于需要长期暴露在潮湿或腐蚀环境中的电镀件来说,盐雾测试是一项至关重要的质量评定指标。
首先,盐雾测试的标准是非常重要的。
目前国际上广泛使用的盐雾测试标准有ASTM B117-16、ISO 9227:2017等。
这些标准规定了测试设备、测试条件、测试周期等方面的具体要求,确保了测试结果的可比性和可靠性。
在进行电镀件盐雾测试时,必须严格按照相关标准进行操作,以确保测试结果的准确性和可靠性。
其次,电镀件盐雾测试的目的是为了评估电镀件在盐雾环境中的耐蚀性能。
通过将电镀件暴露在盐雾环境中一定时间后,观察其表面是否出现腐蚀、氧化等现象,从而判断其在实际使用中的耐蚀能力。
这对于一些需要长期暴露在潮湿或腐蚀环境中的电镀件来说,可以提前发现潜在的质量问题,从而采取相应的改进措施,提高产品的可靠性和使用寿命。
另外,电镀件盐雾测试的结果对于产品质量的控制和改进具有重要意义。
通过盐雾测试,可以及时发现电镀件在腐蚀条件下的性能表现,为生产工艺的改进和产品质量的控制提供重要依据。
在实际生产中,经常进行盐雾测试可以有效提高产品的质量稳定性,降低售后风险,提升企业的市场竞争力。
最后,电镀件盐雾测试在实际应用中需要注意一些问题。
首先是测试条件的选择,要根据实际使用环境和要求确定测试周期和盐雾浓度。
其次是测试设备的维护和校准,确保测试设备的正常运行和测试结果的准确性。
另外,测试结果的分析和评估也是至关重要的,要对测试结果进行科学的分析和评估,及时采取相应的改进措施。
总之,电镀件盐雾测试是评估电镀件耐蚀性能的重要手段,对于产品质量的控制和改进具有重要意义。
只有严格按照相关标准进行测试,并结合实际情况进行科学分析和评估,才能取得准确可靠的测试结果,为产品的质量提升和改进提供重要依据。
电镀盐雾测试标准

电镀盐雾测试标准电镀盐雾测试是指将被测物品放置在盐水喷雾试验箱内,通过模拟盐雾环境对被测物品的腐蚀性能进行检测的一种测试方法。
该测试方法被广泛应用于金属材料、电镀件、汽车零部件等领域,以评估材料或涂层的耐腐蚀性能。
本文将介绍电镀盐雾测试的标准要求和测试流程。
一、标准要求。
1. ASTM B117-16。
ASTM B117-16是美国材料与试验协会制定的电镀盐雾测试标准,适用于金属材料和镀层的耐腐蚀性能评定。
该标准规定了盐雾试验箱的工作条件、试验样品的准备、试验周期和评定方法等内容,是电镀盐雾测试中最常用的标准之一。
2. GB/T 2423.17-2008。
GB/T 2423.17-2008是中国国家标准中关于电镀盐雾测试的规定,适用于各种材料和涂层的耐腐蚀性能评定。
该标准对盐雾试验箱的性能要求、试验条件、试样的制备和评定方法等进行了详细规定,是国内企业进行电镀盐雾测试的重要依据。
二、测试流程。
1. 试样准备。
在进行电镀盐雾测试之前,首先需要准备好试样。
试样的准备包括清洗、去油、打磨和清洁等步骤,确保试样表面没有污染物和氧化层。
对于涂层试样,还需要注意涂层的均匀性和厚度是否符合要求。
2. 设置试验条件。
根据所选用的标准要求,设置盐雾试验箱的工作条件,包括温度、湿度、盐水浓度和喷雾时间等参数。
在进行测试之前,需要对盐雾试验箱进行校准和调试,确保其工作稳定可靠。
3. 进行测试。
将准备好的试样放置在盐雾试验箱内,按照设定的试验条件进行测试。
在测试过程中,需要定期观察试样的表面状态,记录腐蚀情况,并在测试结束后进行评定。
4. 评定测试结果。
根据所选用的标准要求,对测试结果进行评定。
评定的内容包括试样表面的腐蚀程度、腐蚀形貌和腐蚀面积等,根据评定结果判断试样的耐腐蚀性能是否符合要求。
三、总结。
电镀盐雾测试是一项重要的材料性能评定方法,通过模拟盐雾环境对材料的腐蚀性能进行检测,可以有效评估材料或涂层的耐腐蚀性能。
五金电镀盐雾测试标准

修订日 期:
2010.12. 08
修订生效日:2010.12.08
发文日 期:
2006.11. 07
版本:B
一、适 用范
二、电镀品外观品质要求:电镀品外观需光泽均之、细致结合好,有光亮度,以4倍放大镜检 三、测视不能有起泡、起皮、脱落、条纹、斑点、底材露出、烧焦、粗糙等不良现象。 试标
1、 客户有 特殊要 求时, 依据客 户盐雾 测试标 准判定.
12
四、试验结里判定:试验后以4倍放大镜进行观察,无生锈及蓝绿色腐蚀物现象,即为合格;
参考标
反之则为NG。
准:①
核准:
审核:
12-08
制表:王月梅2010-
2、 试验条 件:
项目
试验中
备注
氯化钠溶液浓度
5%
每天标定浓度一次
PH值 压缩空气压力(kgf/cm2) 喷雾量(ml/80cm2/H)
压力桶温度
6.5-7.2 1.00±0.01
1.0-2.0 47±1
收集后溶液测定试验中的PH值 连续不得中断
应至少收集16小时,求其平均值
盐水桶温度
35±1
试验室温度
35±1
3、试验 时间:
试验室相对湿度 材料类型
85%以上 规格
试验时间(单位:H)
2.35X0.7
48±4
4.0X1.7
48±4
EIAJ
4.75X1.7
48±4
5.5X1.0
48±4
6.5X1.4
48±4
铜钉
铜材电镀
48±4外壳(铁材电镀)
8
主体内端子
12
不锈钢材质
72
其它类五金电镀部品
电镀盐雾测试标准

电镀盐雾测试标准电镀盐雾测试是一种常见的腐蚀测试方法,用于评估金属和非金属材料的抗腐蚀性能。
本文将介绍电镀盐雾测试的标准,包括测试原理、测试方法和相关标准的选择。
电镀盐雾测试是通过模拟盐雾环境,加速材料的腐蚀过程,从而评估材料的抗腐蚀性能。
在实际应用中,金属制品经常需要进行电镀处理,以提高其表面的硬度和耐腐蚀性能。
因此,电镀盐雾测试对于评估电镀层的质量和耐腐蚀性能至关重要。
在进行电镀盐雾测试时,首先需要准备好测试样品,并在测试室中设置好盐雾测试设备。
测试样品应当代表实际应用中的使用情况,例如不同种类的电镀层、不同厚度的电镀层等。
测试设备应当能够产生稳定的盐雾环境,并能够控制温度、湿度等参数。
在进行测试之前,需要根据相关标准选择合适的测试方法。
目前国际上常用的电镀盐雾测试标准包括ASTM B117、ISO 9227、JIS Z 2371等。
这些标准对于测试样品的准备、测试条件、测试周期等方面都有详细的规定,用户可以根据自己的需求选择合适的标准进行测试。
在测试过程中,需要严格按照标准规定的测试条件进行操作,包括盐水浓度、喷雾方式、温度、湿度等参数。
同时,需要定期对测试样品进行观察和记录,包括表面的腐蚀情况、腐蚀面积的变化等。
通过长期的测试观察,可以评估电镀层的耐腐蚀性能,并且可以比较不同材料、不同电镀层的性能差异。
除了常规的盐雾测试,还可以进行其他形式的腐蚀测试,例如循环盐雾测试、醋酸盐雾测试等。
这些测试方法可以更加真实地模拟实际使用环境中的腐蚀情况,对于评估材料的耐腐蚀性能具有重要意义。
总之,电镀盐雾测试是一种重要的腐蚀测试方法,对于评估电镀层的质量和耐腐蚀性能具有重要意义。
在进行测试时,需要选择合适的测试标准和方法,并严格按照标准规定的条件进行操作。
通过测试观察和记录,可以准确评估材料的耐腐蚀性能,为实际应用提供可靠的参考依据。
电镀盐雾测试标准

电镀盐雾测试标准
电镀盐雾测试是一种常用的腐蚀性测试方法,用于评估金属材料的耐蚀性能。
本文将介绍电镀盐雾测试的标准及其相关内容。
首先,电镀盐雾测试的标准主要包括ASTM B117、ISO 9227、GB/T 10125等。
这些标准规定了测试的样品制备、测试条件、测试方法、评定标准等内容,是进行电镀盐雾测试时必须遵循的规范。
在进行电镀盐雾测试之前,首先需要准备好测试样品。
样品的制备应符合相关
标准的要求,包括材料的选择、表面处理、镀层厚度等。
只有样品制备得当,才能保证测试结果的准确性和可靠性。
接下来是测试条件的设定。
电镀盐雾测试通常在恒温恒湿的测试箱中进行,测
试时间一般为24小时、48小时、96小时甚至更长。
在测试过程中,需要保持测试
箱内的盐水喷雾浓度、温度、湿度等参数稳定,以确保测试的可比性和一致性。
测试方法是电镀盐雾测试的核心内容。
在测试过程中,需要定期观察样品的腐
蚀情况,记录腐蚀面积、腐蚀程度等数据。
同时,还需要对腐蚀后的样品进行清洗、干燥、评定等处理,以获取最终的测试结果。
最后是评定标准的确定。
根据相关标准的规定,可以对测试样品进行评定,判
断其腐蚀性能是否符合要求。
评定标准通常包括腐蚀面积、腐蚀程度等指标,对样品的腐蚀性能进行定量化的评价。
总的来说,电镀盐雾测试标准是保证测试结果准确可靠的重要依据,只有严格
遵循标准规范,才能得到具有参考价值的测试数据。
希望本文对电镀盐雾测试的标准有所帮助,使大家能够更好地理解和应用这一测试方法。
电镀盐雾测试标准

电镀盐雾测试标准电镀盐雾测试是一种常用的环境试验方法,用于评估金属和非金属材料的防腐蚀性能。
本文将介绍电镀盐雾测试的标准及其相关内容。
1. 测试目的。
电镀盐雾测试的主要目的是模拟材料在恶劣环境下的抗腐蚀能力,以便评估材料的耐久性和可靠性。
通过测试,可以确定材料的表面涂层、防护膜或防腐蚀涂料的性能,为产品的设计和改进提供依据。
2. 测试标准。
电镀盐雾测试的标准通常包括国际标准、行业标准和企业标准。
国际标准主要有ISO 9227、ASTM B117等;行业标准则由各行业协会或组织制定,如汽车行业的GMW14872、电子行业的IEC 60068-2-11等;企业标准则由企业根据自身需求和实际情况制定。
3. 测试设备。
电镀盐雾测试通常使用盐雾试验箱进行,其工作原理是通过电解制备盐水溶液,然后将溶液喷洒在被测样品表面,模拟盐雾环境。
盐雾试验箱的关键参数包括温度、湿度、盐水浓度、喷雾压力等。
4. 测试方法。
电镀盐雾测试的方法包括常规盐雾测试、周期盐雾测试、循环盐雾测试等。
常规盐雾测试是将样品放置在盐雾试验箱中连续喷雾一定时间;周期盐雾测试是在盐雾和干燥环境之间交替进行;循环盐雾测试则是在盐雾、干燥和常温环境之间交替进行。
5. 测试评定。
电镀盐雾测试的评定标准通常包括表面腐蚀程度、腐蚀产物形貌、腐蚀裂纹、腐蚀面积等。
评定标准可以根据具体产品的要求和标准进行制定,一般包括等级划分和评定方法。
6. 注意事项。
在进行电镀盐雾测试时,需要注意以下事项,首先是样品的准备,包括清洁、表面处理和标记;其次是测试条件的控制,包括盐水浓度、温湿度、喷雾压力等;最后是测试结果的记录和分析,包括腐蚀程度、腐蚀形貌、腐蚀裂纹等。
7. 结论。
电镀盐雾测试是一种重要的环境试验方法,对于材料的抗腐蚀性能评估具有重要意义。
通过了解电镀盐雾测试的标准和相关内容,可以更好地进行测试工作,为产品质量和可靠性提供保障。
总之,电镀盐雾测试标准的了解和掌握对于材料的质量控制和产品的改进具有重要意义,希望本文能够为相关人员提供一定的参考价值。
盐雾试验判定标准

盐雾试验判定标准盐雾试验判定标准1. 盐雾试验判定标准1.1 为了确保经过盐雾测试后产品抗盐雾腐蚀能力质量基本的判断,检查方法的正确性;1.2 本标准用于考核材料及其防护层的抗盐雾腐蚀能力,以及相似防护层的工艺质量比较,也可用来考核某些产品抗盐雾腐蚀能力;1.3 本标准不作为通用的腐蚀试验方法;1.4 本标准是参照国家标准GB6461;GB12335,GB/T9798 1997的附录(eqvISO1462.1973)中性盐雾试验标准(NSS)编写;2. 适用范围:2.1 对电镀零件和可用于盐雾实验的产品进行测试后,检查方法及判断;2.2 测定面腐蚀状况测定,也可由买卖双方事先协定之方法判定之;3. 检验方法:3.1 试验结果的评价:a 试验后的外观;b 除去表面腐蚀产物后的外观;c 腐蚀缺陷如点蚀、裂纹、气泡等的分布和数量和状态;d 被腐蚀时间;3.2 评级原则:1 对镀件外观或使用性能起重要作用的部分镀层表面,即主要表面进行外观和保护等级评定。
2 试样检查结果用(/)把两种等级分别记录,保护等级记录在第一位。
3 除记录试样的级别外,还应注明评级的缺陷种类和严重程度。
3.3 缺陷的类型:1 保护缺陷包括凹坑腐蚀、针孔腐蚀、鼓泡、腐蚀产物以及金属腐蚀产物的其他缺陷;2 外观缺陷除了因底材金属引起的缺陷外,还包括试样外观所有的损坏。
典型的缺陷油;表面麻点、“鸡爪状”缺陷、开裂、表面沾污和失去光泽;3.4 保护等级(Rp)的评定根据腐蚀缺陷所覆盖的面积按以下的计算方法得出保护等级;像镀锌等对底材呈阳性的电镀层,其表面的外观变化包括变色、失光,覆盖层腐蚀和基体金属腐蚀等;把其产生的各种变化分成A~I等共9个级别,各级外观的变化如下表所示。
对镀层的评级可参照表中所列现象进行评定。
3.4.1等级与外观外观评级样品表面外观的变化A级无变化B级轻微到中度的变色C级严重变色或极轻微的失光D级轻微的失光或出现极轻微的腐蚀产物E级严重失光,或试样表面局部有薄层的腐蚀产物或点蚀F级有腐蚀产物或点蚀,且其中之一种分布在整个试样表面上G级整个表满上布有厚的腐蚀产物或点蚀,并有深的点蚀H级整个表面布有非常厚的腐蚀产物和点蚀,并有深的点蚀I级出现基体金属腐蚀3.4.2 金属镀层的腐蚀评级是根据腐蚀缺陷所占总面积的百分数,按下列公式计算而得到:R=3(2-10g10A)式中R-腐蚀评级数/保护等级(为一修约的整数)A—蚀缺陷所占总面积的百分数。
出口欧盟的电镀产品盐雾试验标准
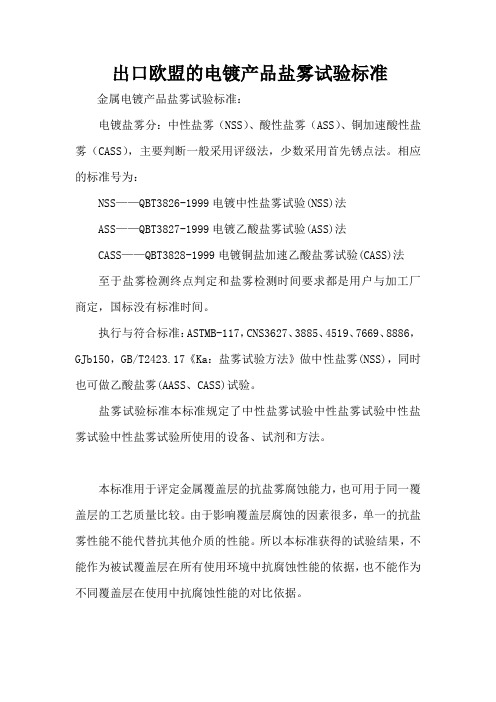
出口欧盟的电镀产品盐雾试验标准金属电镀产品盐雾试验标准:
电镀盐雾分:中性盐雾(NSS)、酸性盐雾(ASS)、铜加速酸性盐雾(CASS),主要判断一般采用评级法,少数采用首先锈点法。
相应的标准号为:
NSS——QBT3826-1999电镀中性盐雾试验(NSS)法
ASS——QBT3827-1999电镀乙酸盐雾试验(ASS)法
CASS——QBT3828-1999电镀铜盐加速乙酸盐雾试验(CASS)法
至于盐雾检测终点判定和盐雾检测时间要求都是用户与加工厂商定,国标没有标准时间。
执行与符合标准:ASTMB-117,CNS3627、3885、4519、7669、8886,GJb150,GB/T2423.17《Ka:盐雾试验方法》做中性盐雾(NSS),同时也可做乙酸盐雾(AASS、CASS)试验。
盐雾试验标准本标准规定了中性盐雾试验中性盐雾试验中性盐雾试验中性盐雾试验所使用的设备、试剂和方法。
本标准用于评定金属覆盖层的抗盐雾腐蚀能力,也可用于同一覆盖层的工艺质量比较。
由于影响覆盖层腐蚀的因素很多,单一的抗盐雾性能不能代替抗其他介质的性能。
所以本标准获得的试验结果,不能作为被试覆盖层在所有使用环境中抗腐蚀性能的依据,也不能作为不同覆盖层在使用中抗腐蚀性能的对比依据。
- 1、下载文档前请自行甄别文档内容的完整性,平台不提供额外的编辑、内容补充、找答案等附加服务。
- 2、"仅部分预览"的文档,不可在线预览部分如存在完整性等问题,可反馈申请退款(可完整预览的文档不适用该条件!)。
- 3、如文档侵犯您的权益,请联系客服反馈,我们会尽快为您处理(人工客服工作时间:9:00-18:30)。
CASS
-
80
-C 一般
72
152
MFNi1
-
-
-
-G 一般
72
152
MFNi2
一般
-
24
-GS 一般
120
200
MZNi1
-
-
-
-K 一般
72
152
MBNi1
-
-
-
MFZn13-防锈 一般
-
96
MBNi2
-
-
-
Cr3+ 三价铬
MFZnCr3+ 3B 一般
72
-B
一般
-
144
-C
一般
72
192
-G
一般
72
192
MFZnCr3+ 5B 一般 MFZnCr3 + 8B 一般
48
96 120
-GS 一般
120
240
-K
一般
72
192
MFZnCr3+ 13B 一般
144
MFZn20-防锈 一般
-
152
M
MFZn25-C 一般
72
400
MFZnCr3+ 5C 一般 MFZnCr3+ 8C 一般
2.Zn→锌(亚铅);Cr→铬 3.标准来源:Cr6+ -厦杏机车;Cr3+ -协源电镀
4.NSS(一般):
中性盐雾试验;
CASS(酸性):醋
酸铜盐雾试验
批准:
审核:
制表:
制表日期:
长春阔尔科技股份有限公司 电镀耐蚀盐雾试验标准
电镀种类
不得生白 不得生红锈
电镀种类
不得生白锈 不得生红锈
锈(hr)
(hr)
(hr)
(hr)
电镀代号
盐雾种类
电镀代号
盐雾种类
Cr6+ 六价铬
MFCr1
一般
-
24
MFZn1-B
一般
48
-
MFCr2
CASS
-
16
-C 一般
72
-
MFCr3
CASS
-
16
-D/K 一般
72
-
MFCr4
CASS
-
32
-G 一般
72
-
MFCr5
CASS
-
80
MFZn2-B
一般
48
96
MZCr1
一般
-
24
-C
一般
72
-
MZCr2
一般
-
48
-D/K 一般
-
96
MZCr3
CASS
-
16
-G
一般
72
-
MZCr4
CASS
-
16
MFZn3-B
一般
-
-
MZCr5
CASS
-
80
-C 一般
72
144
MBCr1
-
-
-
MFZn4-C
一般
-
288
MBCr2
-
-
-
MFZn5-B
一般
-
56
MBCr3
-
-
-
-C 一般
72
132
MBCr4
CASS
-
80
-G 一般
72
132
MRCr1
CASS
-
16
-GS 一般
120
180
MRCr2
CASS
-
16
-K
一般
72
132
MRCr3
CASS
-
32
MFZn8-B
一般
-
96
MRCr4
72
144
达可锈
一般
-
192
二硫化钼
一般
5
240
MFZnCr3+ 13C 一般
240 MFZn 8B+JS500 一般
120
500
MFZn 8B+TR401 一般
120
240
MFZn 8C+JS500 一般
120
500
MFZn 8C+TR401 一般
120
240
1.K/D→黑色;G→绿色;C→五彩;B→白色