转炉除尘风机在线监测及故障诊断系统
风机状态监测与故障诊断PPT

2006GB/T1982.9?石油天然气工业寿命周期费
用分析?
设备综合工程学
重初期投资,轻后期费用;重当前费用节
约,轻后期费用效益;重技术决策,轻经
济决策
企业各部门难以实行整体决策
缺少推行LCC技术的开展规划、制度、政策
措施及奖惩机制
缺少数据的收集和积累,建立模型困难
全员生产维修体制〔TPM〕
电气接头
电机控制中心
电气室
相不平衡
红外诊断的方法
外表温度判断法〔参考国标〕
相对温差判断法
趋势跟踪法
GB763-90?交流高压电器在长期工作时的发热?
危急热缺陷〔Ⅰ〕:电气设备外表温度超过90℃,
或温升超过75℃或相对温差〔温差〕超过55℃
严重热缺陷〔Ⅱ〕:电气设备外表温度超过75℃,
30度
度
铜接头与镀银电缆连接
45度
度
空气开关、接点〔铜〕
33度
度
空气开关、接点〔铜与其他金属〕43度
实际温
70
85
75
90度
影响因素
发射率
距离系数
太阳光-温度叠加;反射或漫反射波长为
3~14微米〔阴天或加太阳滤片〕
风力
临近辐射体
设备负荷率
油液监测技术
是监测、诊断设备润滑系统故障的重要手
段,尤其是对设备早期磨损隐患的发现与
识别,是其他方法无法替代的
适合监测于磨损类故障
对某些类型的振动确实认可以起到很大的
作用
对润滑油液的要求
理化性能:粘度、极压性、闪点、酸值、
电机
绕阻或轴承过热, 冷却通路阻塞, 摩擦, 阻尼,
基于可靠性的状态监控预知系统——转炉风机在线监测及诊断系统技术方案

振动传感器、 垂直方向安装 1 个振动传感器、 轴向安装 1 个振动传感器。 2 . 2电机本体安装 2 个冲击脉冲传感器: 两个轴承位各安装 1 个冲 击 脉冲传感器 。 2 . 3电机和风机 之 间安装 1 个转速 传感器 。 2 . 4电机控制柜上: 控制柜上电机电流y g -  ̄ - 接人 V C N。 3风机在线监 测系统功能 要求 3 . 1按照设备状态在线监测和故障诊断的需求 , 风机上实施在线监 测, 并 具有故 障诊断和故 障报警功 能 。 3 . 2利用传感器捕捉振动、 冲击脉冲、 转速 、 电流信号 ; 进行信号处 理、 模式识 别 、 预报 决策 , 及 计算机 技术 , 监测 机组 在运行 过程 中的振 动 参数及 有关 l 生 能参数 及其 动态变化 , 在机组运 行过程 中, 做 出是否 有故 障、 故障种类 、 故障部位 、 故障严重程度、 故障发展变化趋势等诊断结果 , 判断机 组性 能劣化 趋势 。 3 . 3通过振动准确监测风机系统的不平衡、 不对中、 松动等问题。 3 . 4通过冲击脉冲准确监测风机系统的轴承问题 , 做到准确预知与 诊断 。 3 . 5通过电机电流信号的监测 , 反映风机载荷的变化 , 提高系统诊
断 的准确性 。 4主要 系统硬件 的技术条件 4 . 1振动 监测 模块 ( v c M - 2 o ) 。V C M - 2 0是 连 续测 量单元 , 供 采用
1 . 2 . 3根据设 备的多棒 性, 有 时设备总体 振动不大 , 但 是短 时工作后 便 造成事故停 机现象 , “ E V A M ”根据 3 0多项参数 的趋势 变化可 以捕捉 设 备的故障原 因 , 并 报警提示 。 1 . 2 . 4根据设 备的基本参 数和正常状 态下 的参 量 ,形成适合 该设备 的企 业标准 , 从而 为设备后期更 准确判 断设备运行 状态 。 1 . 3轴承监测——冲击脉冲技术 冲击脉冲技术简单易用 , 只须在轴承座上安装冲击脉冲传感器 , 系 统会直接给出轴承运转状态值及国际标准的“ 绿、 黄、 红” 状态指示。 该技术的优势是其独特设计的冲击脉冲传感器, 仅对轴承运转、 齿 轮啮合时产生的瞬态冲击做出反应 ,而对其它低频振动的干扰不作反 应, 因此可以得到纯净的早期信号。对冲击脉冲信号进行频谱分析 , 即 专利 的 S P M S p e c t r u m T M, 具有其 它常规 带通滤 波 、 包络技 术无法 比拟 的优势 , 可得 到极为清 晰的频谱 图。 1 4通过企 业 内部 网络实现 网络共享 , - 同时支 持 5 个用 户 同时上 网 查看设备 目前 的工作 状况 。 1 _ 5系统内置 的 T I J T自检功能 , 自 动监 测 网络 系统的连接 质量和硬 件品质 , 保证采集数据的真实可靠。 l I 6本 系统 自 成 体系 , 不受 网络系统 的故 障干扰 。 1 . 7本 系统可 以同时接 收在线或离 线便携 式数采 器的数 据 , 进入 系 统 进行统一管 理。 1 . 8可以按企业内部的设备统一编号或 自己编排 的编号 ( 任意) 编
简易故障诊断技术及应用

l 2●
8 2●
8 3●
4 3●
表 2 振 动 幅 值 测 试 数 据
3
l
2● 2 2 ●
4
3 ● 6 4 ●
O
mm/ s
次 数
A B
1 2 3 4 5 6 7 8 9 1 1 1 0 1 2
C
。 D
4 3 ● 9 4 ●
3 2 数 据 整 理及 趋 势预 报 .
3
由表 2可 以看 出, 风机在 运行初 期其各项指 标基本趋
于平稳 , 运行中后舸, 而在 其振幅开 商较侠 。 阿时 , 和甩机械
故 障听诊器监测 , 其噪声明显加尉 , 且仪表显示轴承温度也
存在安全隐患的主要原因。
一
般来讲 , 在风机允许的振动限值范 围内, 幅值随着时
间的增大是线性相关 的 , 因而可 以应用最小 二乘 法拟合 曲
线 , 行趋势分析。 进
根据所测数据 ( 见表 2 , ) 设所 拟合 的曲线方程式m为
●
行采集 。测量时选择 相同的炼钢时段 , 每个点进行 多次测
2
●
8
试, 取其平均值 。
7
l
●
9
l
●
5
2
●
l
2
●
9 6 5 O () 3 采用振动的速度 值作为其 幅值。测 量数据见 表2 。2● l● Fra bibliotek 2 ● 2 ●
有 随 振 幅 升 高 而 明显 上升 的趋 势 。这 是 风 叶在 粘 灰 较 多 的
情况下 , 其动平衡受到破坏 , 而且附着在 叶轮上的灰尘极易
转炉一次除尘系统(OG系统)

• 4、在锅炉(汽包)运行中要密切注意各水位 计、压力表等仪表状态,发现问题及时汇报处 理。如汽包运行中缺水时,不得立即补水,立 即通知炉前停炼并等锅炉温度下降后再补水。 • 5、每小时巡视、检查运行中的汽包安全阀启 始压力应在规定值范围内;各水封、各防爆板 必须处于正常状态。巡检时应避免停留在安全 门、防爆装置、法兰盘、水位计等有可能发生 爆炸或泄漏的位置。 • 6、每班冲洗水位计一次,以免造成假水位, 危及安全。
OG系统特点
• 净化系统设备紧凑。系统设备实现了管道化, 系统阻损小,不存在死角,煤气不易滞留,生 产安全。 • 设备装备水平较高。通过炉口的微差压来控制 二级文氏管喉口的开度,以适应吹炼各期烟气 量的变化及回收、放散的切换,实现了自动控 制。 • 烟气净化效率高。 • 系统的安全装置完善。
流程简述
一级文氏管
• 文氏管即为文丘里洗涤器,亦名快速收尘器, 于1946年开始在工业中应用。它是湿式除尘器 中除尘效果最好的一种。 • 气体经过喉部的速度一般是在50~120m/s的范 围,依靠这样高速把供给喉部喷射速度约 10m/s的液体分散成细小液滴。虽然细小的水 滴很快就加速到和气体差不多的速度,但因以 气流速度运动的尘料和刚产生的水滴之间相对 速度很高,所以在很短促的期间,尘料和水滴 已经能够发生有效的碰撞,而且在
• 为防止煤气发生回火,煤气在烟道内流 动的最低速度应大于回火速度,在 12~18m/s为宜,以保安全。
80t转炉OG系统技术参数
• • • • • • • 原始最大炉气量:65000Nm3/h 最大烟气量:150000 m3/h 一文前烟气温度:~900℃ 一文后烟气温度:~70℃ 一文阻力:5000Pa 二文阻力:10000~14000Pa 风机流量:2500 m3/min
主通风机在线监测与故障诊断系统方案(修改)
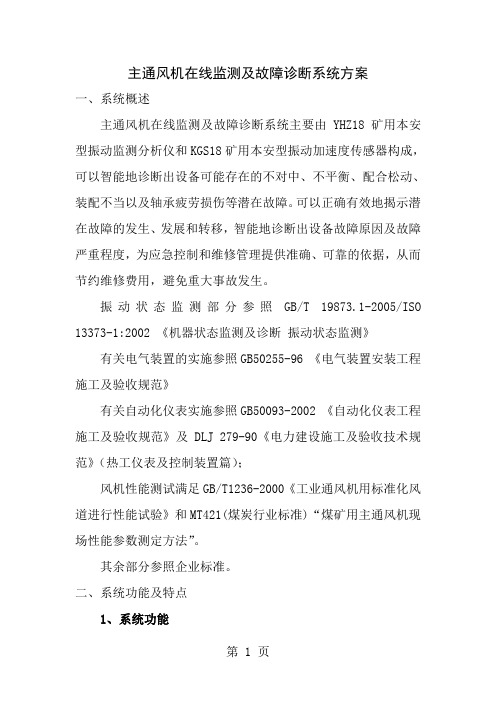
主通风机在线监测及故障诊断系统方案一、系统概述主通风机在线监测及故障诊断系统主要由YHZ18矿用本安型振动监测分析仪和KGS18矿用本安型振动加速度传感器构成,可以智能地诊断出设备可能存在的不对中、不平衡、配合松动、装配不当以及轴承疲劳损伤等潜在故障。
可以正确有效地揭示潜在故障的发生、发展和转移,智能地诊断出设备故障原因及故障严重程度,为应急控制和维修管理提供准确、可靠的依据,从而节约维修费用,避免重大事故发生。
振动状态监测部分参照GB/T 19873.1-2005/ISO 13373-1:2002 《机器状态监测及诊断振动状态监测》有关电气装置的实施参照GB50255-96 《电气装置安装工程施工及验收规范》有关自动化仪表实施参照GB50093-2002 《自动化仪表工程施工及验收规范》及DLJ 279-90《电力建设施工及验收技术规范》(热工仪表及控制装置篇);风机性能测试满足GB/T1236-2000《工业通风机用标准化风道进行性能试验》和MT421(煤炭行业标准)“煤矿用主通风机现场性能参数测定方法”。
其余部分参照企业标准。
二、系统功能及特点1、系统功能系统主要由在线监测、轴承实时诊断及状态预报、离线数据分析三部分组成。
(1)在线监测功能①在线监测通风机所在地点的环境大气参数,包括大气压力、大气温度、和大气湿度。
②在线监测通风机的流量、风压、轴功率、效率、振动等工况状态参数。
③在线监测电气设备的电气参数,包括电流、电压、功率因数,开关状态及系统保护信息。
④当运行中的通风机设备性能出现异常时,系统按照不同的故障类型,依据用户设定的模式进行提示、报警。
系统能够对于温度、振动等关键参数给出预警。
系统对各种故障点具有记忆功能,以对故障的分析提供帮助。
⑤系统具有运行状态实时数据显示、历史纪录查询、特性曲线或工况参数列表显示、报表打印及网络通讯传输等功能。
⑥系统及矿集中控制系统留有通讯接口,可接入矿局域网,在中央控制室内可实施对通风机设备的远程监测。
矿井主通风机在线监测与故障诊断系统
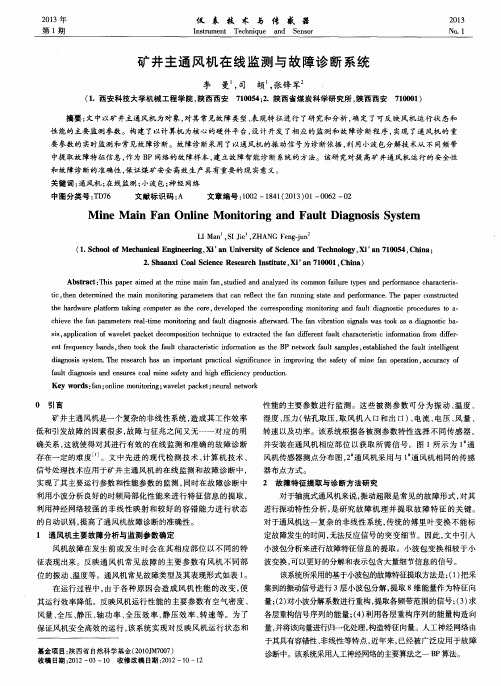
摘要 : 文中以矿 井主通风机 为对 象, 对其常见故障类型 、 表现 特征进行 了研究和 分析 , 确 定 了可反 映风机 运行状 态和 性能的主要监测参数。构建 了以计算机为核心的硬 件平 台, 设 计开发 了相 应的监 测和故障诊 断程序 , 实现 了通风机 的重
要参数的 实时监测和常见故 障诊 断。故障诊断采用 了以通风机的振动信号 为诊 断依据 , 利用小波 包分解技术从 不 同频 带
中提取故障特征信 息, 作为B P网络 的故 障样本 , 建立故障智能诊断 系统的方法。该研 究对提 高矿 井通风机运行 的安全性 和故 障诊 断的 准确性 , 保证 煤矿 安全高效生产具有重要 的现实意义。
L I Ma n . S I J i e . Z H A N G F e n g  ̄ u n
( 1 . S c h o o l o f Me c h a n i c a l E n g i n e e r i n g , X i ’ a n U n i v e r s i t y f o S c i e n c e a n d T e c h n o l g y , Xi ’ a l l 7 1 0 0 5 4, C h i n a ;
关键词 : 通风机 ; 在线监测 ; 小波包 ; 神 经网络 中图分类号 : T D 7 6 文献标识码 : A 文章编号 : 1 0 0 2—1 8 4 1 ( 2 0 1 3 ) 0 1 — 0 0 6 2— 0 2
Mi n e Ma i n F a n On l i n e Mo n i t o r i n g a n d F a u l t Di a g n o s i s S y s t e m
锅炉风机故障诊断及状态维修
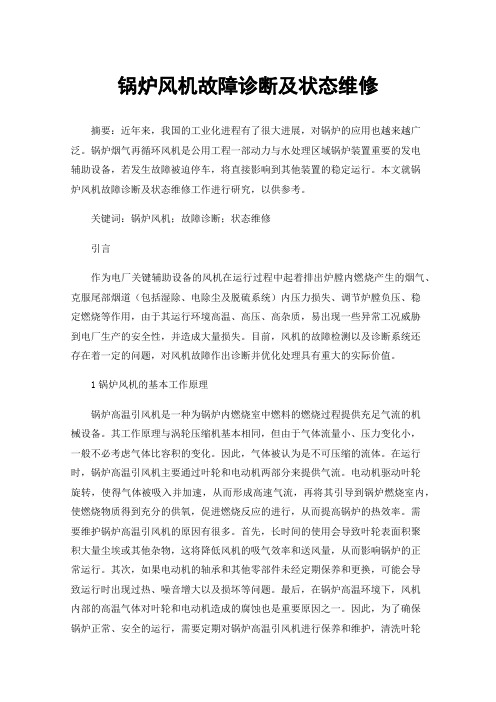
锅炉风机故障诊断及状态维修摘要:近年来,我国的工业化进程有了很大进展,对锅炉的应用也越来越广泛。
锅炉烟气再循环风机是公用工程一部动力与水处理区域锅炉装置重要的发电辅助设备,若发生故障被迫停车,将直接影响到其他装置的稳定运行。
本文就锅炉风机故障诊断及状态维修工作进行研究,以供参考。
关键词:锅炉风机;故障诊断;状态维修引言作为电厂关键辅助设备的风机在运行过程中起着排出炉膛内燃烧产生的烟气、克服尾部烟道(包括湿除、电除尘及脱硫系统)内压力损失、调节炉膛负压、稳定燃烧等作用,由于其运行环境高温、高压、高杂质,易出现一些异常工况威胁到电厂生产的安全性,并造成大量损失。
目前,风机的故障检测以及诊断系统还存在着一定的问题,对风机故障作出诊断并优化处理具有重大的实际价值。
1锅炉风机的基本工作原理锅炉高温引风机是一种为锅炉内燃烧室中燃料的燃烧过程提供充足气流的机械设备。
其工作原理与涡轮压缩机基本相同,但由于气体流量小、压力变化小,一般不必考虑气体比容积的变化。
因此,气体被认为是不可压缩的流体。
在运行时,锅炉高温引风机主要通过叶轮和电动机两部分来提供气流。
电动机驱动叶轮旋转,使得气体被吸入并加速,从而形成高速气流,再将其引导到锅炉燃烧室内,使燃烧物质得到充分的供氧,促进燃烧反应的进行,从而提高锅炉的热效率。
需要维护锅炉高温引风机的原因有很多。
首先,长时间的使用会导致叶轮表面积聚积大量尘埃或其他杂物,这将降低风机的吸气效率和送风量,从而影响锅炉的正常运行。
其次,如果电动机的轴承和其他零部件未经定期保养和更换,可能会导致运行时出现过热、噪音增大以及损坏等问题。
最后,在锅炉高温环境下,风机内部的高温气体对叶轮和电动机造成的腐蚀也是重要原因之一。
因此,为了确保锅炉正常、安全的运行,需要定期对锅炉高温引风机进行保养和维护,清洗叶轮表面上的灰尘和杂物、更换电动机轴承、定期检查电路等,并及时处理故障,确保其在长时间使用情况下能够正常工作,提高锅炉的可靠性和安全性。
重钢转炉干法除尘风机转子故障原因及解决措施

2 # 转炉转子 曾经于 2 0 1 2 年6 月用于 3 #转炉除尘 风机 , 7月 振 动 大 更 换 ; 8月 用 于 1 #转 炉 风 机 , 1 0
故 障的 建议和措 施 。 关键 词 干 法除尘 风机转 子 故 障原 因 解决措施
1 设备概 况
和2 2 2 2 6的轴 承支 撑 , 采用 强 制润 滑 方 式 , 由高压 变频 电机 直接驱 动转子 , 有轴 承在 线振 动和 温度等 监 测 ,采用 P L C控制 方 式 。分析 所有 转 子故 障情 况, 其主要 原 因有转子 安装精 度 、 轴承选 择 与质量 、 转 子动平 衡 、 控 制系统 的影 响等 。 2 . 1 转子安 装精度 分析 据调查 , 在转 炉 除尘 转 子安 装 过程 中 , 施 工单 位 确有 不规范施 工行 为 , 但 经纠正 后基 本能 按规 范
应在 低速 平衡 , 然后 提高 转速 。
2 - 3 转 子动 平衡 问题 除尘 风机 振动 大 , 最大 的可 能 为转 子动 平衡 失 效 ,而 每次更 换转 子后 ,都 要送 外 检校 动 平衡 , 如
某H M 6 U通用平衡机 ( 三峰使用 的)技术参
数:
在 两支 承架 上转子 重量 最大 : 1 2 5 0 0 k g , 允 许转 子 回转直径 : 最大 2 1 0 0 mm
1 4— —
重 钢 机 动 能 源
第2 6卷 2 0 1 3 年第 2期( 总第 1 0 4期 )
范安 装 , 调整好轴承安装游 隙 0 . 0 3 — 0 . 0 5 m m, 该轴
承可 以满足使用 , 不存在轴承质量及其游隙偏小的
问题 。
根据经验 ,当转子重量在支 承重量 l / 3以下 时, 应该开高速进行平衡调整 , 如不平衡量大 , 转子
风机叶片装备状态监测与故障诊断技术

风机叶片装备状态监测与故障诊断技术近年来,随着能源需求和环境保护的双重压力的增加,风力发电作为一种清洁能源逐渐受到人们的重视。
风力发电的核心装备之一就是风机,而风机叶片作为风机的重要组成部分,其状态的监测和故障的诊断显得尤为重要。
本文将重点介绍风机叶片装备状态监测与故障诊断技术的相关内容,以期为风力发电行业的发展提供一些借鉴意义和技术支持。
一、风机叶片装备状态监测技术风机叶片的状态监测技术主要是基于传感器和数据采集系统的应用,通过监测风机叶片各项指标的实时数据来了解风机叶片的工作状态。
其中,常见的监测指标包括叶片的振动、温度、应力等。
通过对这些指标的监测和分析,可以及时发现叶片存在的问题,并进行相应的维护和修复工作,以确保风机的正常运行。
1.1 叶片振动监测技术叶片振动是风机叶片故障的一个重要指标,它直接影响到风机的运行稳定性和安全性。
传统的叶片振动监测技术主要依靠加速度传感器和振动传感器来实现,通过测量叶片振动的幅值、频率等数据,从而评估叶片的工作状态。
近年来,随着无线通信技术的发展,基于传感器网络的叶片振动监测技术逐渐兴起,可以实现对多个叶片的同时监测,并通过云端分析,实现远程监测与管理。
1.2 叶片温度监测技术叶片温度是评估叶片工作状态的一个关键指标,过高的温度可能导致叶片的热熔或变形,进而影响风机的性能和寿命。
传统的叶片温度监测技术主要采用红外线测温和接触式测温等方式,通过测量叶片的表面温度来判断叶片的工作状态。
此外,近年来,光纤传感技术逐渐应用于叶片温度的监测,具有快速响应、高精度等优势。
1.3 叶片应力监测技术叶片应力是叶片工作状态的一个重要示性指标,过大的应力可能会导致叶片的断裂和破损。
传统的叶片应力监测技术主要基于应变片和应力勘测仪等设备,通过监测叶片的应变和应力来评估叶片的工作状态。
近年来,无损检测技术逐渐应用于叶片应力监测领域,通过超声波和红外线等技术,实现对叶片内部的应力进行非接触式监测。
除尘风机振动故障诊断与处理
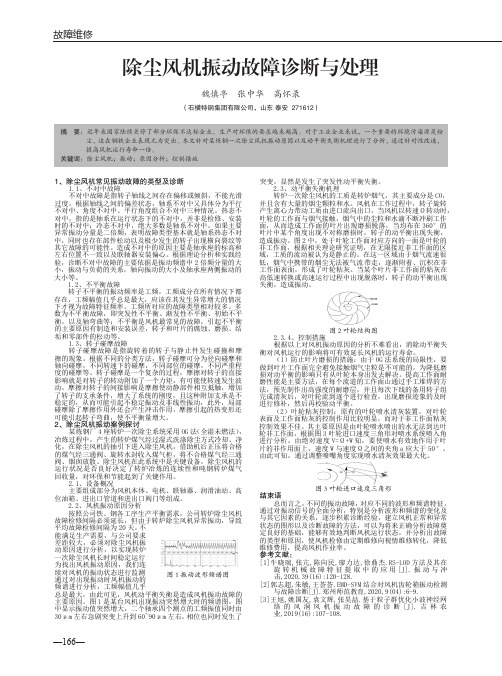
—166—故障维修摘..要:近年来国家陆续关停了部分环保不达标企业,生产对环保的要求越来越高。
对于工业企业来说,一个重要的环境污染源是粉尘,这在钢铁企业表现尤为突出。
本文针对某炼钢一次除尘风机振动原因以及动平衡失衡机理进行了分析,通过针对性改造,提高风机运行寿命一倍。
关键词:除尘风机;振动;原因分析;控制措施除尘风机振动故障诊断与处理魏慎亭 张中华 高怀录(石横特钢集团有限公司,山东 泰安 271612)1、除尘风机常见振动故障的类型及诊断1.1、不对中故障不对中故障是指转子轴线之间存在偏移或倾斜,不能光滑过度。
根据轴线之间的偏差状态,轴系不对中又具体分为平行不对中、角度不对中、平行角度组合不对中三种情况。
热态不对中,指的是轴系在运行状态下的不对中,并非是检修、安装时的不对中;冷态不对中,绝大多数是轴系不对中。
如果主要异常振动分量是二倍频,表明故障类型基本就是轴系热态不对中,同时也存在部件松动以及极少发生的转子出现横向裂纹等其它故障的可能性。
造成不对中的原因主要是轴承座的标高和左右位置不一致以及联轴器安装偏心。
根据理论分析和实践经验,诊断不对中故障的主要依据是振动频谱中2倍频分量的大小,振动与负荷的关系,轴向振动的大小及轴承座两侧振动的大小等。
1.2、不平衡故障转子不平衡的振动频率是工频,工频成分在所有情况下都存在,工频幅值几乎总是最大,应该在其发生异常增大的情况下才视为故障特征频率。
工频所对应的故障类型相对较多。
多数为不平衡故障,即突发性不平衡、渐发性不平衡、初始不平衡,以及轴弯曲等;不平衡是风机最常见的故障,引起不平衡的主要原因有制造和安装误差,转子和叶片的腐蚀、磨损、结垢和零部件的松动等。
1.3、转子碰摩故障转子碰摩故障是指旋转着的转子与静止件发生碰撞和摩擦的现象。
根据不同的分类方法,转子碰摩可分为径向碰摩和轴向碰摩,不同转速下的碰摩,不同部位的碰摩,不同严重程度的碰摩等。
转子碰摩是一个复杂的过程,摩擦对转子的直接影响就是对转子的转动附加了一个力矩,有可能使转速发生波动。
风电机组在线监测与故障诊断系统在风电场运维中的应用效果评估

风电机组在线监测与故障诊断系统在风电场运维中的应用效果评估随着可再生能源的快速发展,风力发电已成为全球范围内主要的清洁能源之一。
然而,风力发电设备在运行过程中常常面临着各种故障和异常情况,给运维工作带来了极大的挑战。
为了最大程度地提高风力发电设备的可靠性和可用性,近年来,风电机组在线监测与故障诊断系统开始在风电场运维中得到广泛应用。
本文将评估该系统在风电场运维中的应用效果。
风电机组在线监测与故障诊断系统是一种基于物联网技术的智能管理系统,通过实时监测和分析风力发电设备的运行状态,能够及时发现设备的异常情况,并对故障进行诊断。
该系统主要由传感器、数据采集器、数据处理平台和故障诊断算法组成。
首先,风电机组在线监测与故障诊断系统能够实现对风力发电设备的实时监测。
传感器可以采集设备的振动、温度、电流、电压等关键参数,并将数据传输给数据采集器。
监测系统通过数据处理平台对这些数据进行实时的分析和处理,能够准确地了解设备的运行状况。
当设备发生故障或异常时,系统能够自动发出警报,通知工作人员进行相应处理。
这种实时监测的能力可以极大地节省人力和时间成本,提高运维效果。
其次,风电机组在线监测与故障诊断系统具备故障诊断的能力。
系统通过与历史数据和故障数据库的比对分析,能够根据设备的异常行为准确地诊断故障类型和原因,并给出修复建议。
这种自动化的故障诊断与分析能够有效地指导运维人员进行维修和维护工作,提高故障处理效率和设备稳定性。
此外,通过系统对故障数据的记录和分析,可以识别和预测设备的寿命和潜在故障,有效地规避设备的损坏和停机。
再次,风电机组在线监测与故障诊断系统通过数据分析提供设备运行情况的综合评估。
该系统能够对设备的运行状况、性能指标进行实时监测和分析,生成相应的报告和统计数据。
基于这些数据,管理人员可以评估设备的可靠性、可用性和维护水平,并根据评估结果优化风电场的运维策略和计划。
这种综合评估的能力可以帮助管理人员更好地了解设备的健康状况和运行情况,提前预防和处理潜在问题,保证设备的持续运行和发电能力。
转炉烟气净化系统常见故障分析

十四、转炉烟气净化系统常见故障及分析1、转炉喷溅造成固定烟道大量结渣1.1 原因及可能危害转炉生产节奏越来越快,吹氧强度也不断增加,且超装现象严重,造成转炉喷溅现象频繁发生;而汽化冷却设备改造跟不上,往往冷却能力不够。
转炉的喷溅常常造成较大量的渣钢粘结在固定烟道的不同部位,粘结在固定烟道上的渣钢占据烟道中烟气的流通面积,造成气流阻力过大,使大量的炉气无法吸入烟道,直接在炉口外溢,烧坏炉口设备,污染环境。
一旦固定烟道中粘结的渣钢达到一定的体积,烟道中的阻力上升到一定值,一文的溢流盘水封水会被抽干(风机抽力作用),这时一方面炉口大量外溢烟,造成严重的环境污染,另一方面造成空气进入转炉煤气中,可能引发煤气爆炸。
1.2 故障现象随着风机转速的提高,一文溢流盘的水位不断下降,甚至溢流水全部被吸干,且吹氧时转炉炉口大量冒黄烟;检查汽化冷却烟道弯头处,没有堵塞,就证明是烟道沾渣,一般从氧枪口可以直接观察到沾渣情况。
1.3 处理方法及预防措施1.3.1 处理方法冲刷固定烟道(视结渣部位定氧枪 小面积的渣钢,可以用氧枪吹N2枪位),使渣钢脱落;大面积的渣钢,处理难度很大。
河北某厂3#40吨转炉(20吨转炉扩容)发现一文溢流水封中水急剧下降,紧急停吹,检查发现汽化冷却烟道弯头处没有堵塞,从而断定汽化冷却烟道沾渣,从氧枪口检查确认在氧枪口下沾渣。
经炉前工人从炉口、氧枪口等处用钢管、钢钎捅,落下直径1500mm左右,2吨多重的渣钢。
安徽某厂2#95吨转炉也曾出现固定烟道大面积结渣,导致一文溢流水被吸干,发生煤气爆炸,被迫停产,最后在固定烟道中连续放了7根雷管,才使大面积渣钢震碎脱落。
1.3.2预防措施A、尽量减少钢水喷溅—-选择转炉合适的装入量,控制合适的氧压和流量;B、每天从氧枪孔处检查固定烟道中结渣情况,发现少量的渣钢要及时处理干净;C、每周利用周检时间开固定烟道弯头人孔检查,若有结渣必须及时清理;D、利用大修机会改造汽化冷却系统,从而改善汽化冷却烟道的冷却状况,降低锅炉管靠近烟气侧的温度,也可以减少沾渣。
大型风机在线监测系统

大型风机在线监测系统第一章. ARJC系统硬件部分第1节系统功能与技术指标1.系统功能2.技术指标3.监测参数范围4.系统特点5.系统的组成6.系统的工作原理第2节气体流量的监测1.气体流量计算的基本原理2.负压测点的布置3.微差压变送器的基本技术指标与使用方法4.EDA9017模拟量采集模块5.EDA485C 有源隔离转换器6.气体温度的测量与JWB系列温度变送器7.负压的采集与气体流量的计算第3节电机的轴承温度、绕组温度的测量1.简介2.PT100电阻介绍3.EDA9018温度采集模块4.ARJC温度采集工作原理第4节电气参数的测量1.EDA9033A三相电参数采集模块2.ARJC系统电参数的采集第5节振动的测量1.系统组成2.一体化振动变送器介绍3.振动的测量第6节 ARJC系统的报警1.系统报警的基本原理2.EDA9060继电器输出模块第7节系统的硬件滤波、电子滤波与软件滤波1.气体的滤波与稳压2.电子滤波3.软件滤波第8节计算机及数据打印设备1.ARJC对计算机、打印机的需求第1节系统功能与技术指标1 系统功能系统的主要功能有:实时监测通风系统参数、通风机的性能参数、电机的电气参数、轴承温度、电机振动、数据管理、报表管理、性能测试、远程通讯等,详述如下:⏹实时监测通风系统入口静压、入口温度、风量。
⏹实时监测通风机性能参数:流量、全/静压、效率。
⏹实时监测风机配用电机的电气参数:电流、电压、功率。
⏹实时监测轴承温度并在超限时报警。
⏹实时监测定子温度并在超限时报警。
⏹实时监测电机振动。
⏹数据实时显示、存储、查询、打印。
⏹报表自动生成、存储、查询、打印⏹兼容多种国际计算机通讯协议(DDE、OPC、FTP)。
⏹局域网IE浏览功能⏹Internet信息发布与存贮功能⏹GPRS远程信息服务⏹GPRS手机短信功能2 技术指标⏹工作电压:~220V±10%⏹环境温度:-10℃~+50℃⏹环境湿度:≯85%⏹变送器精度:≮0.5级监测精度:⏹流量:2.5级⏹压力:0.5级⏹电参数:0.25级⏹温度:0.5级⏹振动:0.5级⏹其它:1.5级3 监测参数范围⏹流量:4000~125000 m3/min⏹压力:-1000~0 mmH2O⏹温度:0~150℃⏹电压:0~10kV⏹电流:由互感器确定⏹功率:无限制⏹振动: 0~20 mm/s4 系统特点⏹采用了先进的计算机技术,功能强大,智能化程度高;以图形界面显示工作状态,画面丰富,直观生动。
基于可靠性的状态监控预知系统

基于可靠性的状态监控预知系统摘要:炼钢生产中的除尘风机是将炼钢生产过程中的烟气及时排出。
炼钢过程中产生大量的烟尘,烟尘中含有易燃气体和金属颗粒,经风机将其排至烟囱放散或输送至煤气回收系统,在排出过程中烟气经过风机转子,烟尘中的小金属颗粒会沾在转子表面从而造成风机转子表面不均匀,在高速运转的情况下,风机振动幅度变大,使风机故障增大,利用效率大大减小。
风机在线监测系统通过监测风机的振动、振幅、速度及风机和电机的轴承脉冲信号,通过一系列运算、判断,及时通知操作人员进行定期维修,减少风机跳闸故障,提高风机作业率,同时提高转炉利用效率,产生更高的效益。
关键词:风机;在线监测及诊断;技术方案此系统通过建立关键设备在线监测体系,实时监控设备振动参量状态,及时报警,防止重大设备事故的发生;同时采用最先进的监控技术,最大程度延长设备的预警时间,从而实现预知维修,并通过智能的专家诊断,精确诊断故障源,实现精密维修,缩短维修用时,为检测维修制度合理化提供准确的数据基础。
1 cms在线监测系统功能本系统采用瑞典spm公司著名的cms网络监控系统,全中文操作界面,提供windows窗口形式和树状结构形式两种操作方式,真正做到会使用计算机就能操作软件。
1.1 在线监控设备振动指标,长期趋势监控,智能型“绿、黄、红”报警指示。
1.2 通过“evam”专利技术实现:1.2.1 智能诊断故障,对位移、加速度、速度、歪度、峭度、4个等级摩擦量以及不平衡、不对中、松动、轴承故障、转子断条等30多项参数与征兆独立评估,分别给出“绿、黄、红”状态指示,实现智能专家诊断。
1.2.2 针对转炉风机工况的复杂性,对于变速设备、载荷变化较大的设备,可根据转速和载荷的变化量预先设定设备不同工况下的不同标准。
1.2.3 根据设备的多样性,有时设备总体振动不大,但是短时工作后便造成事故停机现象,“evam”根据30多项参数的趋势变化可以捕捉设备的故障原因,并报警提示。
转炉除尘风机在线监测及故障诊断系统

基于可靠性的状态监控预知系统------风机在线监测及诊断系统技术方案一、概况:监控设备:对于炼钢厂转炉风机,实施在线状态监测,精确了解设备运行状态,实施有计划的预知维修,同时根据运行状态与根源分析,进一步提高设备运行的可靠性,为合理安排设备维修和优化备件提供有力保障;实施目标:该系统通过建立关键设备在线监测体系,实时监控设备振动参量状态,及时报警,防止重大设备事故的发生;同时采用最先进的监控技术,最大程度延长设备的预警时间,从而实现预知维修,并通过智能的专家诊断,精确诊断故障源,实现精密维修,缩短维修用时,为检测维修制度合理化提供准确的数据基础;二、项目意义利用传感器捕捉振动、冲击脉冲、转速、电流信号;进行信号处理、模式识别、预报决策,及计算机技术,监测机组在运行过程中的振动参数及有关性能参数及其动态变化,在机组运行过程中,作出是否有故障、故障种类、故障部位、故障严重程度、故障发展变化趋势等诊断结果,判断机组性能劣化趋势;使运行、维护、管理人员能在维修之前做好有关准备,做到预知维修,并可根据监测诊断结果,进行技术改造,避免类似事故再次发生;实施本项目的意义在于:1、通过本项目实现对机组的连续在线监测和劣化趋势预测达到预知维修的目的,以保证无故障运行;2、利用监测诊断系统可以及时判别设备是否有故障,并且能够迅速查明故障原因、部位、预测故障影响;从而实现有针对性的按状态维修,那里坏了修那里,而不是大拆大卸,延长检修周期,缩短检修时间,提高检修质量,减少备件储备,提高设备的维修管理水平;3、向运行人员提供及时的信息,有效地支援运行,提高设备使用的合理性、运行的安全性和经济性,充分挖掘设备潜力,延长服役期限,以便尽量合理地使用设备;从而降低设备故障停机时间,减少计划检修时间和非计划检修时间;4、向维修管理人员及时提供设备运行情况,及时准备备品备件,及时处理有关故障,真正实现预知维修,以最少的代价发挥设备最佳的效益,做到最佳运行,使设备维修费用、设备性能劣化与停机损失费用最低;根据监测诊断结果确定维修时间、维修部位和维修方法,并根据诊断结果进行技术改造,可以降低设备故障停机时间,减少计划检修时间和非计划检修时间;提高开工率,增加产品产量,减少同类事故发生的次数;三、CMS在线监测系统功能说明:系统功能:1)本系统为瑞典SPM公司着名的CMS网络监控系统,在世界范围内拥有40年的历史,更为ABB、西门子、英格索兰、西马克、阿尔斯通等着名设备制造商应用,进行产品出厂配套或进行出厂质量校核;2) 全中文操作界面,提供WINDOWS 窗口形式和树状结构形式两种操作方式,真正做到会使用计算机就能操作软件;3) 在线监控设备振动指标,长期趋势监控,智能型“绿、黄、红”报警指示;4) 通过专利的“EVAM ”专利技术,实现:① 智能诊断故障原因,对位移、加速度、速度、歪度、峭度、4个等级摩擦量以及不平衡、不对中、松动、轴承故障、转子断条等30多项参数与征兆独立评估,分别给出“绿、黄、红”状态指示,实现智能专家诊断;② 针对设备工况的复杂性,对于变速设备、载荷变化较大的设备,可根据转速和载荷的变化量预先设定设备不同工况下的不同标准;③ 根据设备的多样性,有时设备总体振动不大,但是短时工作后便造成事故停机现象,“EVAM ”根据30多项参数的趋势变化可以捕捉设备的故障原因,并报警提示;④ 根据设备的基本参数和正常状态下的参量,形成适合该设备的企业标准,从而为设备后期更准确判断设备运行状态;⑤ 内置的“专家系统”和庞大的轴承库,方便具有一定专业知识、习惯用频谱来分析设备故障的管理人员来判断如不平衡、不对中、松动、轴承故障、转子断条等等故障;5) 轴承监测 —— 冲击脉冲技术① 振动监测解决不了早期预警问题已是世界公认的事实,原因是轴承早期的问题如润滑不良,点蚀等所产生的是较弱的瞬态信号,常规振动传感器及振动分析方法根本无法捕捉得到;如下图实例中,振动未报警,但轴承冲击脉冲峰值LR 已远远超出报警值,损伤程度值COND 逐渐加大,说明轴承已经失效,继续运行将导致严重隐患;② “冲击脉冲技术”是完全不同于振动监测的技术,该技术已服务世界各国30多年,被公认为是解决滚动轴承、齿轮问题的最佳途径,因此应用极为广泛,仅在中国就已成功应用于上千家企业;绝大多数世界知名设备制造商,如ABB 、英格索兰、苏尔寿、GE,都已在其设备出厂前安装冲击脉冲传感器,或使用该技术进行出厂检验;为数众多的进口石化挤出机、造纸机、船用发动机的齿轮箱上,已经安装了冲击脉冲监测保护系统;③该技术简单易用,只须在轴承座上安装冲击脉冲传感器,系统会直接给出轴承运转状态值及国际标准的“绿、黄、红”状态指示,同时给出:专利的LR/HR 技术,给出强冲击与平均冲击指标;状态代码CodeA 为最佳,B 为干磨擦,C 为轻度损伤,D 为严重损伤;润滑状态代码LUB 油膜厚度:0,1,2,3,4…;损伤程度值Cond<30为轻度,30-40为中度,>40为重度;它包括一个庞大而丰富的轴承库,以及专利的 LUBMASTER 轴承润滑寿命分析模块;见下图④ 冲击脉冲技术的优势是其独特设计的冲击脉冲传感器,仅对轴承运转、齿轮啮合时产生的瞬态冲击做出反应,而对其它低频振动的干扰不作反应,因此可以得到纯净的早期信号;对冲击脉冲信号进行频谱分析,即专利的SPM Spectrum TM,具有其它常规带通滤波、包络技术无法比拟的优势,可得到极为清晰的频谱图;6) 通过企业内部网络实现网络共享,同时支持5个用户同时上网查看设备目前的工作状况; 轴承状态冲击脉冲LR/HR损伤程度COND 润滑指标LUB 水平振动VIB7)系统内置的TLT自检功能,自动监测网络系统的连接质量和硬件品质,保证采集数据的真实可靠;8)本系统自成体系,不受网络系统的故障干扰;9)本系统可以同时接收在线或离线便携式数采器的数据,进入系统进行统一管理;10)可以按企业内部的设备统一编号或自己编排的编号任意编辑测点名,方便查找;11)可以根据管理人员的职责范围来设定管理权限,真正做到职责分明;12)对于问题设备或检修过设备处理的过程、方法和结论可在当时的测定数据中加以注解,便于将来查阅、参考和制定恰当的处理方案;13)本系统采用WINDOWS自带的SQL SERVER 数据库,可以利用SQL SERVER 数据库自身的软件进行备份,也可以在客户端自行备份数据;14)数据可与企业EAM或ERP体系实现数据共享;15)本系统采用模块化的方式,可以根据用户的需求扩展功能,如:脉冲技术、油膜分析功能等更深层次的分析功能;16)可以通过网络系统,输入软件序列号,在互联网上免费升级软件;实施方法:1)安装振动传感器,监控设备的振动变化;2)安装冲击脉冲传感器,监控轴承的冲击变化和润滑的状况;3)安装转速传感器,实现转速监控,并实现变速设备智能诊断;4)通过现场监测单元多通道信号处理,将数据通过企业互联网传输;5)服务器运行监控软件与数据库,客户端实现有权限地数据共享与诊断分析;五、在线系统结VCM+BMU1、结构图2、风机测点分布测点说明如下:风机本体安装3个振动传感器:风机本体轴承位水平安装1个振动传感器、垂直方向安装1个振动传感器、轴向安装1个振动传感器,;电机本体安装2个冲击脉冲传感器:两个轴承位各安装1个冲击脉冲传感器;电机和风机之间安装1个转速传感器;电机控制柜上:控制柜上电机电流信号接入VCM;一、风机在线监测系统功能要求;1、按照设备状态在线监测和故障诊断的需求,风机上实施在线监测,并具有故障诊断和故障报警功能;2、利用传感器捕捉振动、冲击脉冲、转速、电流信号;进行信号处理、模式识别、预报决策,及计算机技术,监测机组在运行过程中的振动参数及有关性能参数及其动态变化,在机组运行过程中,做出是否有故障、故障种类、故障部位、故障严重程度、故障发展变化趋势等诊断结果,判断机组性能劣化趋势;3、通过振动准确监测风机系统的不平衡、不对中、松动等问题;4、通过冲击脉冲准确监测风机系统的轴承问题,做到准确预知与诊断;5、通过电机电流信号的监测,反映风机载荷的变化,提高系统诊断的准确性;6、有关诊断分析软件中能实现不同岗位人员的权限设定,并能在局域网内实现数据共享,以便提高各级专业人员利用系统及时了解所监测设备的能力和水平,以便提高此类重要设备管理的效率;二、主要系统硬件的技术条件1、振动监测模块VCM-20VCM-20 是连续测量单元,供采用 EVAM 专家方法进行振动分析;单元内部配有 CPU、硬盘和多路复用测量逻辑模块;VCM-20-8 配有 8个振动测量通道,8 个 RPM 测量通道;可插接4-20mA模拟量输入板,可扩充8-16通道模拟量,监控温度、压力等,也可通过负载电流监控,实现变载分析;VCM-20 可通过以太网与安装 Condmaster Nova 软件的计算机连接;测量设定值在软件中设置;通信程序 DBL 向 VCM-20 单元传送测量设定值,并读取这个单元的结果文件;处理器: 1GHz存储器: 256 Mb RAM硬盘容量: > 20 Gb通道:振动20,转速 8频率范围: 0 –20KHz包络频率: 100, 200, 500, 1000, 2000, 5000, 10 000 Hz检测窗口:矩形、汉宁、海明等分辩线数: 200, 400, 800, 1600, 3200, 64002、轴承监测模块BMU-07BMU-07配有7个测量滚动轴承冲击脉冲通道,与测量单元 VCM20连接,根据 VCM20的请求进行测量、传输数据;BMU 提供冲击振幅值和包络冲击脉冲信号,用于频谱分析;VCM20单元测量轴承转速,计算 SPM 频谱,评估轴承工作状态;测量条件在 Condmaster Nova 中设置,包括冲击脉冲方法、频谱类型、用于识别轴承故障的征兆及告警极限等;测量方法:冲击脉冲 LR/HR, 和 SPM 频谱测量范围: -19 到99 dBsv LR/HR测量通道: 7电源: 5 V DC ±10%温度范围: -10°到60° C尺寸: 139 x 145 x 46 mm3、冲击脉冲传感器42000测量范围:最大值100 dBsv机架基础:不锈钢SS 2382设计:密封温度范围:-30到+150° C外部压力:最大1 MPa 10 bar 扭矩:15 Nm, 最大20 Nm4、振动传感器SLD144B灵敏度:100 mV/m/s2,精度:1%工作环境温度:-50~125℃频率范围:~10KHz适用公制M8内螺纹孔,传感器垂直输出传输距离:400米以内。
风电机组在线监测与故障诊断系统的数据采集与处理方法分析

风电机组在线监测与故障诊断系统的数据采集与处理方法分析风电机组是一种重要的可再生能源发电设备,为了保证其安全性、可靠性和有效性,需要使用在线监测与故障诊断系统对其进行监测和诊断。
数据采集与处理是整个系统的核心环节,本文将对风电机组在线监测与故障诊断系统的数据采集与处理方法进行分析。
一、数据采集方法分析1. 传感器数据采集风电机组在线监测与故障诊断系统通常使用各种传感器来获取风机的运行数据。
传感器可以测量风机的转速、温度、振动、电流等参数。
这些传感器可以安装在风机的各个关键部位,比如轴承、齿轮箱和发电机等,以获取全面的运行数据。
传感器数据采集的准确性和稳定性对于系统的性能和可靠性至关重要。
2. 远程监测数据采集风电机组通常分布在广阔的地域范围内,传统的现场数据采集方式不太实用。
因此,使用远程监测数据采集技术可以有效地获取远程风机的数据。
远程监测系统通过网络实时传输风机的运行数据,可以随时随地对风机进行监测与诊断。
这种技术可以大幅提高数据采集的效率和准确性。
3. 数据采集频率为了充分了解风机的运行状况,数据采集的频率非常重要。
对于需要准确监测风机运行状态的任务,应该选择较高的数据采集频率。
通常,数据采集频率应根据风机运行速度和重要参数的变化来确定。
二、数据处理方法分析1. 数据预处理由于风电机组在线监测与故障诊断系统监测的数据量大且复杂,需要进行数据预处理。
数据预处理的目的是清除无效数据和噪声,提高数据质量,并对数据进行合理的缺失值处理。
数据预处理可以采用滤波、归一化、插值等方法,以达到更好的数据分析结果。
2. 特征提取特征提取是指从大量的原始数据中提取出有用的特征来表示风机的运行状态。
这些特征可以是统计特征,如均值、方差等,也可以是频域特征或时域特征。
特征提取的目的是降低数据的维度并准确地描述风机的状态。
3. 数据建模数据建模是根据提取的特征建立风机的运行模型。
常用的数据建模方法包括统计分析、回归分析、神经网络等。
转炉一次除尘风机控制系统改造研究与应用分析

转炉一次除尘风机控制系统改造研究与应用分析作者:李维花来源:《数字化用户》2013年第20期【摘要】本文以某公司为例,详细阐述了怎样让转炉一次除尘风机控制系统实现转速的自动调节、保护、参数记录以及转炉煤气的回收等。
并对转炉一次除尘风机控制系统的的改造进行了探索和研究。
【关键词】转炉除尘风机控制系统改造研究一、转炉一次除尘风机控制系统的工作流程某公司原来的除尘风机使用的是技术非常落后的液力耦合器对风机的速度进行调节。
对于这种液力耦合器而言,它并不能够让除尘风机对速度进行自我调节,因此当使用时,该除尘风机一直处于高速运转状态,如果这样长期运转下去,则会大大降低该除尘风机的使用寿命,同时还会导致大量电流的流失。
为了提升工作效率,尽可能节约更多的电能,便对该转炉一次除尘风机进行了系统改造。
当对该转炉一次除尘风机进行改造之后,使用的是高压变频器对其进行调节,并且通过可编程序控制器,实现了该转炉一次除尘风机的远程控制、自动控制和煤气回收系统等功能。
在吹炼过程中,会产生1500℃至1700℃的转炉煤气,当这些高温煤气在除尘风机的抽引下,会通过内部的汽水烟道以及活动烟罩,通过这两项装置之后,使最终的转炉煤气温度降低到700℃以下,当温度随之降低后,则会进入文氏管,在文氏管中进行灭火工作。
经过这道工序之后,转炉煤气的温度会持续降低,并且在重力脱水器中脱去水滴,接着便会进入二级文氏管。
在二级文氏管中,内部的矩形侯口会根据转炉的微差压进行自动调整,当达到最佳的状态时,便会对转炉煤气进行一个精准除尘。
当完成一系列工作之后,转炉煤气会经过脱水器(弯头)、分离器(水雾)、脱水塔脱水,当所有步骤一一完成后,最后才会进入除尘风机。
在除尘风机中,会对煤气的质量以及其它条件作出分析,并通过除尘风机对其正压,在内部的三通切换阀中,会对煤气进行切换,最后会通过烟囱向大气排放。
转炉一次除尘风机的工作原理如下图1:二、转炉一次除尘风机控制系统的改造和应用(一)除尘风机的控制条件当转炉的氧枪在吹炼位时,应该高速运转;而当转炉在停止工作或者没在吹炼的情况下,则应该低速运行;当转炉闲置或者尚未工作的情况下,便不能开氧。
- 1、下载文档前请自行甄别文档内容的完整性,平台不提供额外的编辑、内容补充、找答案等附加服务。
- 2、"仅部分预览"的文档,不可在线预览部分如存在完整性等问题,可反馈申请退款(可完整预览的文档不适用该条件!)。
- 3、如文档侵犯您的权益,请联系客服反馈,我们会尽快为您处理(人工客服工作时间:9:00-18:30)。
转炉除尘风机在线监测及故障诊断系统文档编制序号:[KKIDT-LLE0828-LLETD298-POI08]基于可靠性的状态监控预知系统------风机在线监测及诊断系统技术方案一、概况:[监控设备]:对于炼钢厂转炉风机,实施在线状态监测,精确了解设备运行状态,实施有计划的预知维修,同时根据运行状态与根源分析,进一步提高设备运行的可靠性,为合理安排设备维修和优化备件提供有力保障。
[实施目标]:该系统通过建立关键设备在线监测体系,实时监控设备振动参量状态,及时报警,防止重大设备事故的发生;同时采用最先进的监控技术,最大程度延长设备的预警时间,从而实现预知维修,并通过智能的专家诊断,精确诊断故障源,实现精密维修,缩短维修用时,为检测维修制度合理化提供准确的数据基础。
二、项目意义利用传感器捕捉振动、冲击脉冲、转速、电流信号;进行信号处理、模式识别、预报决策,及计算机技术,监测机组在运行过程中的振动参数及有关性能参数及其动态变化,在机组运行过程中,作出是否有故障、故障种类、故障部位、故障严重程度、故障发展变化趋势等诊断结果,判断机组性能劣化趋势。
使运行、维护、管理人员能在维修之前做好有关准备,做到预知维修,并可根据监测诊断结果,进行技术改造,避免类似事故再次发生。
实施本项目的意义在于:1、通过本项目实现对机组的连续在线监测和劣化趋势预测达到预知维修的目的,以保证无故障运行。
2、利用监测诊断系统可以及时判别设备是否有故障,并且能够迅速查明故障原因、部位、预测故障影响。
从而实现有针对性的按状态维修,那里坏了修那里,而不是大拆大卸,延长检修周期,缩短检修时间,提高检修质量,减少备件储备,提高设备的维修管理水平。
3、向运行人员提供及时的信息,有效地支援运行,提高设备使用的合理性、运行的安全性和经济性,充分挖掘设备潜力,延长服役期限,以便尽量合理地使用设备。
从而降低设备故障停机时间,减少计划检修时间和非计划检修时间。
4、向维修管理人员及时提供设备运行情况,及时准备备品备件,及时处理有关故障,真正实现预知维修,以最少的代价发挥设备最佳的效益,做到最佳运行,使设备维修费用、设备性能劣化与停机损失费用最低。
根据监测诊断结果确定维修时间、维修部位和维修方法,并根据诊断结果进行技术改造,可以降低设备故障停机时间,减少计划检修时间和非计划检修时间。
提高开工率,增加产品产量,减少同类事故发生的次数。
三、CMS在线监测系统功能说明:系统功能:1) 本系统为瑞典SPM 公司着名的CMS 网络监控系统,在世界范围内拥有40年的历史,更为ABB 、西门子、英格索兰、西马克、阿尔斯通等着名设备制造商应用,进行产品出厂配套或进行出厂质量校核;2) 全中文操作界面,提供WINDOWS 窗口形式和树状结构形式两种操作方式,真正做到会使用计算机就能操作软件;3) 在线监控设备振动指标,长期趋势监控,智能型“绿、黄、红”报警指示;4) 通过专利的“EVAM ”专利技术,实现:① 智能诊断故障原因,对位移、加速度、速度、歪度、峭度、4个等级摩擦量以及不平衡、不对中、松动、轴承故障、转子断条等30多项参数与征兆独立评估,分别给出“绿、黄、红”状态指示,实现智能专家诊断;② 针对设备工况的复杂性,对于变速设备、载荷变化较大的设备,可根据转速和载荷的变化量预先设定设备不同工况下的不同标准;③ 根据设备的多样性,有时设备总体振动不大,但是短时工作后便造成事故停机现象,“EVAM ”根据30多项参数的趋势变化可以捕捉设备的故障原因,并报警提示;④ 根据设备的基本参数和正常状态下的参量,形成适合该设备的企业标准,从而为设备后期更准确判断设备运行状态;⑤ 内置的“专家系统”和庞大的轴承库,方便具有一定专业知识、习惯用频谱来分析设备故障的管理人员来判断如不平衡、不对中、松动、轴承故障、转子断条等等故障。
5) 轴承监测 —— 冲击脉冲技术① 振动监测解决不了早期预警问题已是世界公认的事实,原因是轴承早期的问题(如润滑不良,点蚀等)所产生的是较弱的瞬态信号,常规振动传感器及振动分析方法根本无法捕捉得到。
如下图实例中,振动未报警,但轴承冲击脉冲峰值LR 已远远超出报警值,损伤程度值COND 逐渐加大,说明轴承已经失效,继续运行将导致严重隐患。
② “冲击脉冲技术”是完全不同于振动监测的技术,该技术已服务世界各国30多年,被公认为是解决滚动轴承、齿轮问题的最佳途径,因此应用极为广泛,仅在中国就已成功应用于上千家企业。
绝大多数世界知名设备制造商,如ABB 、英格索兰、苏尔寿、GE ,都已在其设备出厂前安装冲击脉冲传感器,或使用该技术进行出厂检验;为数众多的进口石化挤出机、造纸机、船用发动机的齿轮箱上,已经安装了冲击脉冲监测保护系统。
③ 该技术简单易用,只须在轴承座上安装冲击脉冲传感器,系统会直接给出轴承运转状态值及国际标准的“绿、黄、红”状态指示,同时给出:⏹ 专利的LR/HR 技术,给出强冲击与平均冲击指标; ⏹ 状态代码Code (A 为最佳,B 为干磨擦,C 为轻度损伤,D 为严重损伤); 轴承状态 冲击脉冲LR/HR 损伤程度COND 润滑指标LUB水平振动VIB⏹润滑状态代码LUB(油膜厚度:0,1,2,3,4…);⏹损伤程度值Cond(<30为轻度,30-40为中度,>40为重度);⏹它包括一个庞大而丰富的轴承库,以及专利的 LUBMASTER 轴承润滑寿命分析模块。
(见下图)④冲击脉冲技术的优势是其独特设计的冲击脉冲传感器,仅对轴承运转、齿轮啮合时产生的瞬态冲击做出反应,而对其它低频振动的干扰不作反应,因此可以得到纯净的早期信号。
对冲击脉冲信号进行频谱分析,即专利的SPMSpectrum TM,具有其它常规带通滤波、包络技术无法比拟的优势,可得到极为清晰的频谱图。
6)通过企业内部网络实现网络共享,同时支持5个用户同时上网查看设备目前的工作状况;7)系统内置的TLT自检功能,自动监测网络系统的连接质量和硬件品质,保证采集数据的真实可靠;8)本系统自成体系,不受网络系统的故障干扰;9)本系统可以同时接收在线或离线便携式数采器的数据,进入系统进行统一管理;10)可以按企业内部的设备统一编号或自己编排的编号(任意)编辑测点名,方便查找;11)可以根据管理人员的职责范围来设定管理权限,真正做到职责分明;12)对于问题设备或检修过设备处理的过程、方法和结论可在当时的测定数据中加以注解,便于将来查阅、参考和制定恰当的处理方案;13)本系统采用WINDOWS自带的SQL SERVER 数据库,可以利用SQL SERVER 数据库自身的软件进行备份,也可以在客户端自行备份数据;14)数据可与企业EAM或ERP体系实现数据共享;15)本系统采用模块化的方式,可以根据用户的需求扩展功能,如:脉冲技术、油膜分析功能等更深层次的分析功能;16)可以通过网络系统,输入软件序列号,在互联网上免费升级软件。
实施方法:1)安装振动传感器,监控设备的振动变化;2)安装冲击脉冲传感器,监控轴承的冲击变化和润滑的状况;3)安装转速传感器,实现转速监控,并实现变速设备智能诊断;4)通过现场监测单元(多通道信号处理),将数据通过企业互联网传输;5)服务器运行监控软件与数据库,客户端实现有权限地数据共享与诊断分析。
五、在线系统结1、结构图VCM+BMU2、风机测点分布测点说明如下:◆风机本体安装3个振动传感器:风机本体轴承位水平安装1个振动传感器、垂直方向安装1个振动传感器、轴向安装1个振动传感器,。
◆电机本体安装2个冲击脉冲传感器:两个轴承位各安装1个冲击脉冲传感器。
◆电机和风机之间安装1个转速传感器。
◆电机控制柜上:控制柜上电机电流信号接入VCM。
一、风机在线监测系统功能要求;1、按照设备状态在线监测和故障诊断的需求,风机上实施在线监测,并具有故障诊断和故障报警功能。
2、利用传感器捕捉振动、冲击脉冲、转速、电流信号;进行信号处理、模式识别、预报决策,及计算机技术,监测机组在运行过程中的振动参数及有关性能参数及其动态变化,在机组运行过程中,做出是否有故障、故障种类、故障部位、故障严重程度、故障发展变化趋势等诊断结果,判断机组性能劣化趋势。
3、通过振动准确监测风机系统的不平衡、不对中、松动等问题;4、通过冲击脉冲准确监测风机系统的轴承问题,做到准确预知与诊断;5、通过电机电流信号的监测,反映风机载荷的变化,提高系统诊断的准确性;6、有关诊断分析软件中能实现不同岗位人员的权限设定,并能在局域网内实现数据共享,以便提高各级专业人员利用系统及时了解所监测设备的能力和水平,以便提高此类重要设备管理的效率。
二、主要系统硬件的技术条件1、振动监测模块(VCM-20)VCM-20 是连续测量单元,供采用 EVAM 专家方法进行振动分析。
单元内部配有CPU、硬盘和多路复用测量逻辑模块。
VCM-20-8 配有 8个振动测量通道,8 个 RPM 测量通道。
可插接4-20mA模拟量输入板,可扩充8-16通道模拟量,监控温度、压力等,也可通过负载电流监控,实现变载分析。
VCM-20 可通过以太网与安装 Condmaster Nova 软件的计算机连接。
测量设定值在软件中设置。
通信程序 DBL 向 VCM-20 单元传送测量设定值,并读取这个单元的结果文件。
●处理器: 1GHz●存储器: 256 Mb RAM●硬盘容量: > 20 Gb●通道:振动20,转速 8●频率范围: 0 –20KHz●包络频率: 100, 200, 500, 1000, 2000, 5000, 10 000 Hz●检测窗口:矩形、汉宁、海明等●分辩线数: 200, 400, 800, 1600, 3200, 64002、轴承监测模块(BMU-07)BMU-07配有7个测量滚动轴承冲击脉冲通道,与测量单元 VCM20连接,根据 VCM20的请求进行测量、传输数据。
BMU 提供冲击振幅值和包络冲击脉冲信号,用于频谱分析。
VCM20单元测量轴承转速,计算 SPM 频谱,评估轴承工作状态。
测量条件在Condmaster Nova 中设置,包括冲击脉冲方法、频谱类型、用于识别轴承故障的征兆及告警极限等。
●测量方法:冲击脉冲 LR/HR, 和 SPM 频谱●测量范围: -19 到99 dBsv (LR/HR)●测量通道: 7●电源: 5 V DC ±10%●温度范围: -10°到60° C●尺寸: 139 x 145 x 46 mm3、冲击脉冲传感器(42000)●测量范围:最大值100 dBsv●机架基础:不锈钢SS 2382●设计:密封●温度范围:-30到+150° C●外部压力:最大1 MPa (10 bar)●扭矩:15 Nm, 最大20 Nm4、振动传感器(SLD144B)●灵敏度:100 mV/m/s2,精度:1%●工作环境温度:-50~125℃●频率范围:~10KHz●适用公制M8内螺纹孔,传感器垂直输出●传输距离:400米以内。