煤液化技术的重要性
煤的液化技术
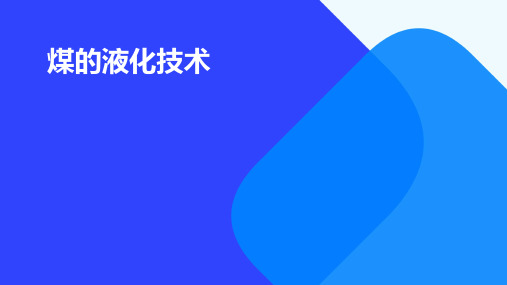
市场发展前景
1 2 3
替代石油资源
随着石油资源的日益枯竭,煤液化技术作为一种 替代石油的能源资源,具有广阔的市场前景。
满足环保要求
煤液化技术能够降低煤炭燃烧过程中的污染物排 放,符合环保要求,有助于推动清洁能源市场的 发展。
对煤液化技术企业给予税收优惠政策,降低企业税负,提高市场 竞争力。
THANKS FOR WATCHING
感谢您的观看
出口潜力
煤液化产品如柴油、汽油等可作为燃料或化工原 料,具有较大的出口潜力,有助于提升我国能源 产业的国际竞争力。
政策支持与推动
产业政策引导
政府通过制定产业政策,鼓励和支持煤液化技术的研发和应用, 推动产业健康发展。
资金扶持
政府提供资金扶持,支持企业进行技术研发和产业化推广,减轻 企业负担。
税收优惠
润滑油
煤液化过程中产生的润滑油具有 优良的润滑性能和稳定性,可用 于机械设备的润滑。
民用燃料
燃气
通过煤液化技术得到的液化石油气可作为居民生活和商业用 途的燃气。
供暖
煤液化燃料可用于集中供暖和家庭采暖,提高居民生活质量 。
化工原料
乙烯
煤液化技术可以生产乙烯等化工原料 ,进一步用于生产塑料、合成纤维等 高分子材料。
该技术最早由南非开发,主要 产品是柴油和航空煤油等。
间接液化技术的优点是工艺流 程相对简单,对原料煤的适应 性较强,但转化效率较低,且 催化剂消耗较大。
合成气液化
合成气液化是指将合成气在一定 条件下转化为液体燃料的过程。
该技术通常采用费托合成工艺, 将合成气在催化剂作用下转化为
煤液化的作用

煤液化的作用一、什么是煤液化呢?煤液化就是把固体的煤转化成液体的燃料或者化工原料。
这就好比把一块硬邦邦的石头变成了能流动的水,是不是很神奇呀?二、煤液化的能源方面的作用1. 增加能源供应形式我们都知道,煤是一种很重要的能源资源,但是固体煤在使用和运输等方面有一些局限性。
煤液化之后呢,就变成了液体燃料,比如变成类似于汽油、柴油这样的东西。
这样就给我们提供了更多的能源供应形式,就像我们吃饭,不能只吃一种菜,能源供应也不能只有一种形式呀。
对于一些缺油少气的地区,煤液化产生的液体燃料可以满足当地的能源需求,不至于让那里的汽车、机器都干等着没油用。
2. 提高能源利用效率液体燃料在燃烧的时候,往往比固体煤燃烧得更充分。
打个比方,就像把一团乱麻梳理整齐了再用,肯定比乱麻直接用要好用得多。
煤液化后燃烧更充分,就能把煤里蕴含的能量更多地释放出来,不至于浪费掉。
三、煤液化在化工方面的作用1. 生产化工原料煤液化之后可以得到很多有价值的化工原料,这些化工原料就像是魔法世界里的魔法原料一样,可以用来制造各种各样的化学品。
比如说,可以制造塑料、合成纤维等。
想象一下,如果没有煤液化得到的这些原料,我们的生活中可能就没有那么多五颜六色的塑料制品,也没有那些柔软舒适的合成纤维衣物了。
它还能用于制造一些高附加值的化学品,像医药中间体之类的。
这就好比煤液化是一个魔法工厂,能把普普通通的煤变成可以治病救人的医药原料呢。
2. 促进化工产业发展有了煤液化提供的丰富化工原料,化工产业就有了更多的“食材”来“烹饪”各种化工产品。
这就会带动化工产业的发展,会有更多的企业参与进来,创造更多的就业机会,也能让我们国家的化工产业在国际上更有竞争力。
就像一个热闹的集市,有了更多的货物,就会吸引更多的人来买卖一样。
煤液化技术研究现状及其发展趋势
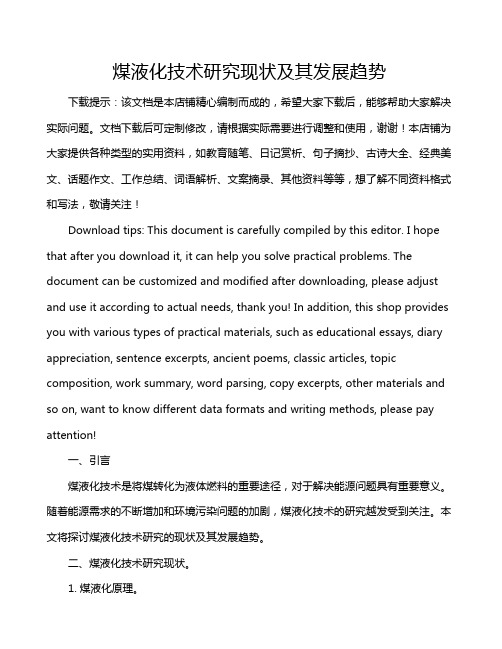
煤液化技术研究现状及其发展趋势下载提示:该文档是本店铺精心编制而成的,希望大家下载后,能够帮助大家解决实际问题。
文档下载后可定制修改,请根据实际需要进行调整和使用,谢谢!本店铺为大家提供各种类型的实用资料,如教育随笔、日记赏析、句子摘抄、古诗大全、经典美文、话题作文、工作总结、词语解析、文案摘录、其他资料等等,想了解不同资料格式和写法,敬请关注!Download tips: This document is carefully compiled by this editor. I hope that after you download it, it can help you solve practical problems. The document can be customized and modified after downloading, please adjust and use it according to actual needs, thank you! In addition, this shop provides you with various types of practical materials, such as educational essays, diary appreciation, sentence excerpts, ancient poems, classic articles, topic composition, work summary, word parsing, copy excerpts, other materials and so on, want to know different data formats and writing methods, please pay attention!一、引言煤液化技术是将煤转化为液体燃料的重要途径,对于解决能源问题具有重要意义。
煤的液化的原理范文
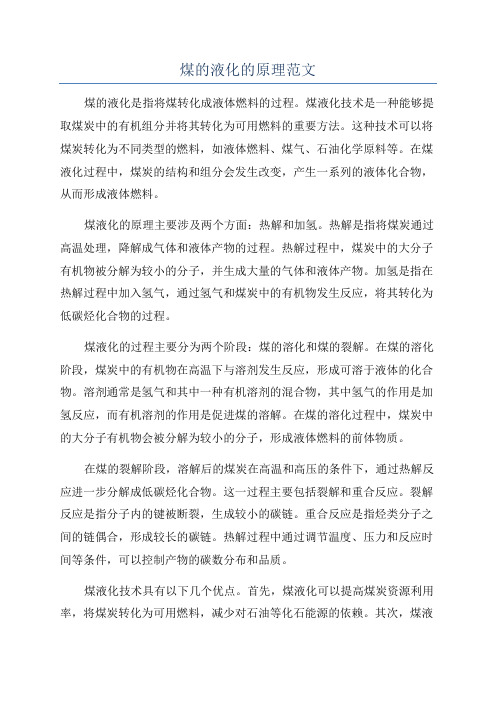
煤的液化的原理范文煤的液化是指将煤转化成液体燃料的过程。
煤液化技术是一种能够提取煤炭中的有机组分并将其转化为可用燃料的重要方法。
这种技术可以将煤炭转化为不同类型的燃料,如液体燃料、煤气、石油化学原料等。
在煤液化过程中,煤炭的结构和组分会发生改变,产生一系列的液体化合物,从而形成液体燃料。
煤液化的原理主要涉及两个方面:热解和加氢。
热解是指将煤炭通过高温处理,降解成气体和液体产物的过程。
热解过程中,煤炭中的大分子有机物被分解为较小的分子,并生成大量的气体和液体产物。
加氢是指在热解过程中加入氢气,通过氢气和煤炭中的有机物发生反应,将其转化为低碳烃化合物的过程。
煤液化的过程主要分为两个阶段:煤的溶化和煤的裂解。
在煤的溶化阶段,煤炭中的有机物在高温下与溶剂发生反应,形成可溶于液体的化合物。
溶剂通常是氢气和其中一种有机溶剂的混合物,其中氢气的作用是加氢反应,而有机溶剂的作用是促进煤的溶解。
在煤的溶化过程中,煤炭中的大分子有机物会被分解为较小的分子,形成液体燃料的前体物质。
在煤的裂解阶段,溶解后的煤炭在高温和高压的条件下,通过热解反应进一步分解成低碳烃化合物。
这一过程主要包括裂解和重合反应。
裂解反应是指分子内的键被断裂,生成较小的碳链。
重合反应是指烃类分子之间的链偶合,形成较长的碳链。
热解过程中通过调节温度、压力和反应时间等条件,可以控制产物的碳数分布和品质。
煤液化技术具有以下几个优点。
首先,煤液化可以提高煤炭资源利用率,将煤炭转化为可用燃料,减少对石油等化石能源的依赖。
其次,煤液化可以降低燃料的污染性,减少大气污染和温室气体排放。
此外,煤液化还可以生产出更多的高附加值化学产品,提高煤炭综合利用的经济和环境效益。
总之,煤液化是一种可以将煤炭转化为液体燃料的重要技术。
通过热解和加氢两个过程,煤炭中的有机组分可以转化为液体化合物,形成液体燃料的前体物质。
煤液化技术有望成为未来能源领域的重要发展方向,为可持续能源的发展做出贡献。
煤液化生产工艺

液固分离
01
02
03
04
分离方法
液固分离的目的是将液化反应 后的液体和固体残渣进行分离 ,得到尽可能多的液体燃料。
离心分离
利用离心机将液化产物进行固 液分离。
过滤分离
通过过滤器将液化产物中的固 体残渣进行分离。
分离效果
液固分离的效果对后续的提质 加工和液体燃料的品质有直接
影响。
提质加工
提质加工目的
成熟阶段
20世纪中叶,德国科学家 开发出间接液化的合成气 制油技术,实现了大规模 商业化应用。
现代发展
随着科技的不断进步,煤 液化技术也在不断改进和 完善,出现了多种新型的 煤液化工艺。
煤液化生产工艺流
02
程
原料准备
原料准备
选择适合煤液化工艺的煤种,并进行 预处理,如去除杂质、破碎大块煤等 ,以确保后续工艺的顺利进行。
煤液化生产中的问
04
题与解决方案
技术问题
总结词
技术问题是煤液化生产中的主要挑战之一,包括工艺流程、设备、操作等方面的问题。
详细描述
煤液化生产工艺需要高技术水平,包括催化剂选择、反应条件控制、分离和提纯等环节,任何一个环 节出现问题都可能导致生产效率低下或产品质量不合格。此外,煤液化生产过程中还可能产生大量的 废气、废水和固废等,需要采取有效的处理措施。
经济问题
要点一
总结词
煤液化生产成本较高,市场竞争激烈,经济压力较大。
要点二
详细描述
煤液化生产需要大量的原料和能源,同时还需要高技术水 平的工艺和设备,导致生产成本较高。此外,随着环保要 求的提高和市场竞争的加剧,煤液化产品的价格优势逐渐 减弱,企业面临着较大的经济压力。为了降低成本和提高 竞争力,企业需要加强技术创新和资源优化配置,同时政 府也需要给予一定的政策和资金支持。
煤液化技术的重要性

煤液化技术的重要性煤液化技术是指将固态的煤炭转化为液态燃料或化学品的过程。
这项技术对于能源产业和经济发展具有重要的意义。
煤是世界上最丰富的化石能源之一,但一般来说,燃煤会排放大量的二氧化碳、二氧化硫等有害气体,对环境和人类健康都造成极大的损害。
相对于原油资源的逐渐枯竭和国际能源形势的愈发严峻,发展煤液化技术具有重要的振兴煤炭工业、增加能源供给等方面的意义。
首先,在资源保障方面,煤液化技术有助于解决石油资源的不足和不平衡的问题。
近年来,发展煤液化技术成为国际上一项热门的研究课题,许多国家都开始大力支持和投入重资发展煤液化产业。
我国是煤炭资源大国,而且资源丰富分布广泛,发展煤液化产业可以更好地开发和利用煤炭资源,增加石化产业的供给。
此外,由于我国地广人多,能源需求量大,发展煤液化产业有助于增加我国能源类型的多样性,减少对外部能源的依赖,稳定国家能源供给,提高能源安全保障能力。
其次,在经济发展方面,发展煤液化技术有助于实现经济增长和就业创造。
随着科技不断发展和进步,液化煤产业逐渐成为一个风险较小、利润较高的支柱产业。
一旦煤液化生产线能够投入生产,它将会带来巨大的经济效益和社会效益。
一方面,煤液化技术可实现对所有煤种的利用,提高资源利用率,降低成本操作成本,对经济发展提供了更多的支撑和保障。
另一方面,发展煤液化技术还将带来新的就业机会,增加农村劳动力的就业渠道,促进农民就业,提高居民收入水平,改善民生福祉。
最后,在环境保护方面,煤液化技术有助于减少环境污染和温室气体排放。
液化煤产业可解决煤炭燃烧所产生的大量环境污染问题,同时也使排放温室气体的量大大减少。
液化煤技术的发展使得煤炭能够逐渐从一个相对短暂、不可持续的能源向一个更为可持续、环保的能源转型。
这样,在保护环境方面,煤液化技术的应用和发展也为我们国家的长远发展提供了更多的保障。
总之,煤液化技术是一个重要的科技领域,具有巨大的发展潜力和应用空间。
它的应用和发展有助于解决石油资源不足、对外部依赖以及环境污染等各种问题,提高了能源的利用效率、经济发展水平和环境质量,具有重要的经济、社会和环境意义。
煤的气化与液化技术及应用前景
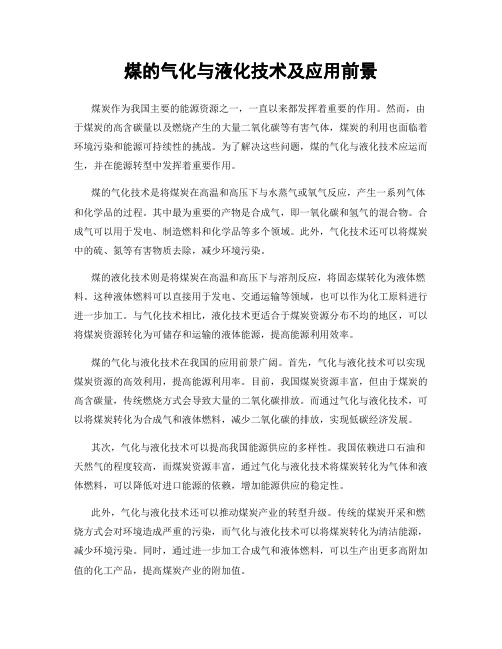
煤的气化与液化技术及应用前景煤炭作为我国主要的能源资源之一,一直以来都发挥着重要的作用。
然而,由于煤炭的高含碳量以及燃烧产生的大量二氧化碳等有害气体,煤炭的利用也面临着环境污染和能源可持续性的挑战。
为了解决这些问题,煤的气化与液化技术应运而生,并在能源转型中发挥着重要作用。
煤的气化技术是将煤炭在高温和高压下与水蒸气或氧气反应,产生一系列气体和化学品的过程。
其中最为重要的产物是合成气,即一氧化碳和氢气的混合物。
合成气可以用于发电、制造燃料和化学品等多个领域。
此外,气化技术还可以将煤炭中的硫、氮等有害物质去除,减少环境污染。
煤的液化技术则是将煤炭在高温和高压下与溶剂反应,将固态煤转化为液体燃料。
这种液体燃料可以直接用于发电、交通运输等领域,也可以作为化工原料进行进一步加工。
与气化技术相比,液化技术更适合于煤炭资源分布不均的地区,可以将煤炭资源转化为可储存和运输的液体能源,提高能源利用效率。
煤的气化与液化技术在我国的应用前景广阔。
首先,气化与液化技术可以实现煤炭资源的高效利用,提高能源利用率。
目前,我国煤炭资源丰富,但由于煤炭的高含碳量,传统燃烧方式会导致大量的二氧化碳排放。
而通过气化与液化技术,可以将煤炭转化为合成气和液体燃料,减少二氧化碳的排放,实现低碳经济发展。
其次,气化与液化技术可以提高我国能源供应的多样性。
我国依赖进口石油和天然气的程度较高,而煤炭资源丰富,通过气化与液化技术将煤炭转化为气体和液体燃料,可以降低对进口能源的依赖,增加能源供应的稳定性。
此外,气化与液化技术还可以推动煤炭产业的转型升级。
传统的煤炭开采和燃烧方式会对环境造成严重的污染,而气化与液化技术可以将煤炭转化为清洁能源,减少环境污染。
同时,通过进一步加工合成气和液体燃料,可以生产出更多高附加值的化工产品,提高煤炭产业的附加值。
然而,煤的气化与液化技术也面临一些挑战。
首先是技术难题。
气化与液化技术需要高温和高压的条件,对设备和工艺要求较高,技术难度较大。
浅析煤炭液化技术

氢脱氧 、氮、硫等杂原 子以及加氢 裂化等。根据加氢 条件 的约 束程度不同 ,可 以控制加氢催化剂活性 已近加氢反应深度。 接下来对煤加碱 预处理过程进行 研究实验 :预 处理 的主要 作用就是提 高煤 的活性 ,本 实验采用 0 .4 % 一1 .6 %的 N a O H 碱溶液对煤进行预处 理 ,以研 究碱处理后 的煤经过 液化其油 出 率 的变化。表 1 给出了实验结果。
量 的 沥青 烯 、油 以及 烃 类 气 体 。 同样 ,沥 青 烯 在 经 过 加 氢 反 应 后 也 可 以生 成 油 或 者烃 类 物 质 。 3 、加 氢 :煤 液 化 反 应过 程 中 ,氢 气 分 子 在 压 力 以及 催 化 剂 的作 用 下 活化 ,之 后 这些 H 分 子 可 以直 接 与热 裂 解 所 形 成 的 自 由基 或 者稳 定 分 子 进 行 反 应 。该 过 程 主 要 有 芳 烃 加 氢 饱 和 ,加
商 界论坛
前 沿探 索
浅 析 煤 炭 液 化 技 术
陈 时 争
摘 要 :能 源是 一 个 国 家工 业及 经 济 发展 的基 础 ,是 国家 可 以发 展 的 重要 保 障 。我 国 的 煤炭 资 源较 为 丰 富 ,但 是 长期 以来煤炭的低利用率,使得大量的煤炭 资源被浪费。鉴 于我 国在 未来发展 的一段 时间 内,仍 然要 以煤炭 资源为基础 的前提 下 ,研 究提 高煤 炭利 用 率 、煤 炭 液化 技 术就 显得 尤 为 重要 。
关 键 词 :煤 炭 液化 ; 直接 液 化
能源安全关系到一个 国家 的长期稳定 发展 ,我国 的煤 炭资 源相对于其他形 式 的资 源而言较 为丰富 。但是长 期以来 ,我 国 的煤炭资源一直处 于低利用率 水平 ,造成 了大量 的资 源浪费 以 及 环 境 污染 等 问 题 。随 着 资 源 的 日益 减 少 ,如 何 提 高 资 源 利 用 率 成 为需 要研 究 的 关 键 问题 。本 文 根 据 当 前 我 国煤 炭 资 源 利 用 存在的问题 ,对煤 炭液化技 术进行 了分析 ,并且针对 煤炭直接 液 化 过 程 中煤 加 碱 预 处 理 进 行 了 系统 的 研 究 ,希 望 能 够 为 煤 炭 资 源 的充 分 利用 提 供 一 些 可 借 鉴 的研 究 成 果 。 煤 炭 液化 技 术 可 以 分 为 直 接 、间 接 两 种 。所 谓 煤 炭 直 接 液 化技术是指将粉状煤炭与循环溶 剂制 备成 的混合油煤浆在定温 、 定压 以及催化 剂条件下 ,进 行加氢化 学反应 ,最终 生成所需要 的液态和气态烃类 化合 物 。同时要 对所 生成 的 物体 进行 脱硫 、 脱氮处理等有 害物 质处理 ;煤 炭的 间接 液化技术 先进行 的是 气 化处理 ,将煤气化后并 在催 化剂 的作用 下 ,通过 F—T费托 过 程 ,得到相应的烃类化 合物 。相对 于煤炭 间接 液化而 言 ,直接 液化在 同样原料的基 础 上 ,所能 够生 产 出的油 品率 更 高一些 。 直接液化将煤 中所包含 的芳烃加氢、C—C键 断裂 和 C— O、C— N、C—S键氢解 等在一 定条件 下 ,直接生 产 出高 P C比的汽、 柴 、煤油等液态能 源。这样就能 够在较小 污染 的前提 下 ,将煤 炭资源转化为其他形式的能源进行储存或者运输 。 煤液化过程可 以通 过 图 1 来 表示 :煤 中所存 在的能量 较小 的 c—c 、C— N、c一0和 C—S等化学键 ,在反 应的过程 中发 生断裂 ,形成 了数 量众多 的 自由基碎 片。然 而大量存 在 的 自由 基碎片又可以通过化学反应 ,与溶剂 和氢气 中的活性氢相结合 , 形 成 较 为 稳定 的化 合 物 。该 化合 物 中 的 P C原 子 比将 有 0 .8 % 上升至 2 .O %。在一系列 的化 学反应后 ,之前煤 中的 固态 大分 子成为 了液态小分 子化合物 。煤液 化后就可 以形成液 化油 、沥 青烯 、前沥青烯 、液化残 渣、少量 的水 和气体 。煤液 化可 以大 致分为热溶解裂解 、氢转移和加氢三大步骤 。
煤直接液化工艺
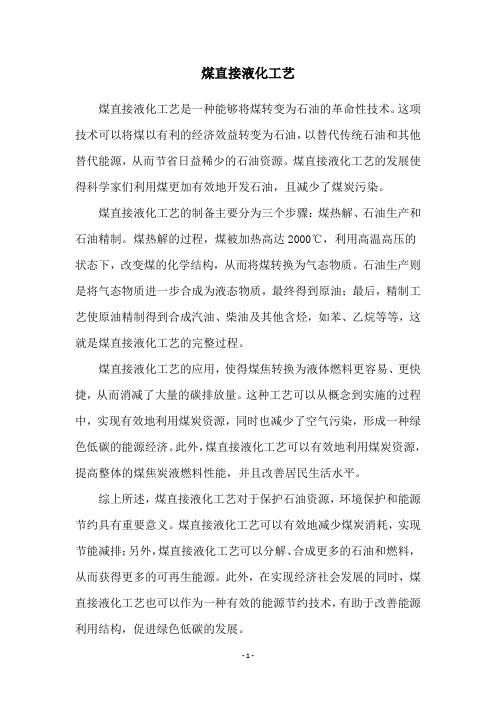
煤直接液化工艺
煤直接液化工艺是一种能够将煤转变为石油的革命性技术。
这项技术可以将煤以有利的经济效益转变为石油,以替代传统石油和其他替代能源,从而节省日益稀少的石油资源。
煤直接液化工艺的发展使得科学家们利用煤更加有效地开发石油,且减少了煤炭污染。
煤直接液化工艺的制备主要分为三个步骤:煤热解、石油生产和石油精制。
煤热解的过程,煤被加热高达2000℃,利用高温高压的状态下,改变煤的化学结构,从而将煤转换为气态物质。
石油生产则是将气态物质进一步合成为液态物质,最终得到原油;最后,精制工艺使原油精制得到合成汽油、柴油及其他含烃,如苯、乙烷等等,这就是煤直接液化工艺的完整过程。
煤直接液化工艺的应用,使得煤焦转换为液体燃料更容易、更快捷,从而消减了大量的碳排放量。
这种工艺可以从概念到实施的过程中,实现有效地利用煤炭资源,同时也减少了空气污染,形成一种绿色低碳的能源经济。
此外,煤直接液化工艺可以有效地利用煤炭资源,提高整体的煤焦炭液燃料性能,并且改善居民生活水平。
综上所述,煤直接液化工艺对于保护石油资源,环境保护和能源节约具有重要意义。
煤直接液化工艺可以有效地减少煤炭消耗,实现节能减排;另外,煤直接液化工艺可以分解、合成更多的石油和燃料,从而获得更多的可再生能源。
此外,在实现经济社会发展的同时,煤直接液化工艺也可以作为一种有效的能源节约技术,有助于改善能源利用结构,促进绿色低碳的发展。
随着人们日益重视环境保护,开发煤直接液化工艺也变得越来越重要。
为了促进能源节约,应提升煤直接液化工艺的社会应用水平,并倡导利用煤直接液化工艺维护环境的理念,以促进各方努力实施煤直接液化工艺,节省能源,保护环境。
煤的气化与液化技术及应用前景
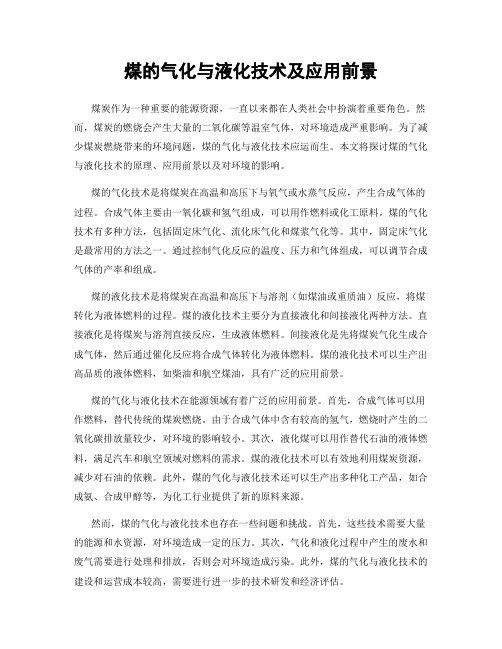
煤的气化与液化技术及应用前景煤炭作为一种重要的能源资源,一直以来都在人类社会中扮演着重要角色。
然而,煤炭的燃烧会产生大量的二氧化碳等温室气体,对环境造成严重影响。
为了减少煤炭燃烧带来的环境问题,煤的气化与液化技术应运而生。
本文将探讨煤的气化与液化技术的原理、应用前景以及对环境的影响。
煤的气化技术是将煤炭在高温和高压下与氧气或水蒸气反应,产生合成气体的过程。
合成气体主要由一氧化碳和氢气组成,可以用作燃料或化工原料。
煤的气化技术有多种方法,包括固定床气化、流化床气化和煤浆气化等。
其中,固定床气化是最常用的方法之一。
通过控制气化反应的温度、压力和气体组成,可以调节合成气体的产率和组成。
煤的液化技术是将煤炭在高温和高压下与溶剂(如煤油或重质油)反应,将煤转化为液体燃料的过程。
煤的液化技术主要分为直接液化和间接液化两种方法。
直接液化是将煤炭与溶剂直接反应,生成液体燃料。
间接液化是先将煤炭气化生成合成气体,然后通过催化反应将合成气体转化为液体燃料。
煤的液化技术可以生产出高品质的液体燃料,如柴油和航空煤油,具有广泛的应用前景。
煤的气化与液化技术在能源领域有着广泛的应用前景。
首先,合成气体可以用作燃料,替代传统的煤炭燃烧。
由于合成气体中含有较高的氢气,燃烧时产生的二氧化碳排放量较少,对环境的影响较小。
其次,液化煤可以用作替代石油的液体燃料,满足汽车和航空领域对燃料的需求。
煤的液化技术可以有效地利用煤炭资源,减少对石油的依赖。
此外,煤的气化与液化技术还可以生产出多种化工产品,如合成氨、合成甲醇等,为化工行业提供了新的原料来源。
然而,煤的气化与液化技术也存在一些问题和挑战。
首先,这些技术需要大量的能源和水资源,对环境造成一定的压力。
其次,气化和液化过程中产生的废水和废气需要进行处理和排放,否则会对环境造成污染。
此外,煤的气化与液化技术的建设和运营成本较高,需要进行进一步的技术研发和经济评估。
综上所述,煤的气化与液化技术具有重要的应用前景。
煤炭资源的煤炭清洁利用技术

煤炭资源的煤炭清洁利用技术煤炭一直以来都是世界上主要的能源之一。
然而,煤炭的燃烧会产生大量的污染物和温室气体,对环境和人类健康带来了严重的影响。
为了减少煤炭燃烧对环境的负面影响,煤炭清洁利用技术应运而生。
本文将探讨煤炭资源的煤炭清洁利用技术以及其对环境和能源行业的重要意义。
一、煤炭清洁利用技术的概述随着环保意识的增强和能源结构调整的推进,煤炭清洁利用技术逐渐成为了能源领域的研究热点。
煤炭清洁利用技术主要包括煤气化、煤炭液化和煤炭气化等。
这些技术可以有效地降低煤炭的污染物排放,提高能源利用效率。
二、煤气化技术的应用与发展煤气化技术是通过将煤炭加热转化为可燃气体来实现煤炭清洁利用的一种技术。
在煤气化过程中,煤炭中的有机物质会被分解成气体,同时还能产生高温高压下的热力学反应。
煤气化技术的应用已经在煤炭化工、城市燃气供应和发电等领域得到了广泛推广。
三、煤炭液化技术的优势与挑战煤炭液化是指将煤炭转化为液体燃料的过程。
与传统的煤炭利用方式相比,煤炭液化技术具有很多优势。
首先,利用煤炭液化技术可以将煤炭的能量得到充分利用,提高能源利用效率。
其次,煤炭液化技术可以降低煤炭燃烧产生的污染物排放。
然而,煤炭液化技术也面临着一些挑战,如技术成本高、能耗大等问题,这些都需要通过持续的研究和改进来解决。
四、煤炭气化技术的发展前景煤炭气化技术是将固态煤炭转化为气态燃料的一种技术。
通过煤炭气化技术,可以将煤炭中的有机物质转化为合成气,进而生产合成燃料、化工原料等。
煤炭气化技术的发展前景非常广阔,可以有效地利用煤炭资源,减少燃煤排放对环境的影响。
五、煤炭清洁利用技术的重要意义煤炭清洁利用技术对环境和能源行业具有重要的意义。
首先,煤炭清洁利用技术可以有效地降低煤炭燃烧产生的污染物和温室气体排放,减少对大气、水体和土壤的污染。
其次,煤炭清洁利用技术可以提高煤炭资源的利用效率,促进能源结构的调整与优化。
最后,煤炭清洁利用技术的研发和推广可以推动我国能源技术和煤炭产业的转型升级,提高国家能源的安全性和可持续性。
2024年煤液化市场前景分析

2024年煤液化市场前景分析简介煤液化是将煤炭转化为可燃性液体燃料的过程。
随着全球对可再生能源和减少碳排放的需求日益增长,煤液化技术逐渐受到重视。
本文将对煤液化市场的前景进行分析,并探讨其在能源行业中的发展潜力。
煤液化市场规模和趋势按照市场研究报告,煤液化市场在过去几年中取得了显著增长。
随着全球能源需求的增长和化石燃料价格的波动,煤液化作为一种可替代能源的技术备受关注。
煤液化市场预计将在未来几年持续扩大,估计年均增长率将达到x%。
煤液化技术的优势相比于传统煤炭的燃烧,煤液化技术具有以下几个优势: - 可持续性:煤液化是一种利用煤炭资源的可持续方法,有助于减少对传统石油和天然气资源的依赖。
- 低碳排放:煤液化过程能有效减少二氧化碳和其他有害气体的排放,有助于应对气候变化挑战。
- 高能效:煤液化技术可以使煤炭的能源潜力充分释放,提高能源利用效率。
煤液化市场的挑战尽管煤液化市场有广阔的发展前景,但也面临着一些挑战和限制因素: - 技术成本:煤液化技术的研发和实施成本相对较高,需要大量的资金投入和相关设施建设。
- 环境问题:煤液化过程中产生的废水和废气排放可能对环境造成一定的影响,需要加强环境监管和控制措施。
- 竞争压力:与其他可再生能源和替代能源相比,煤液化市场面临竞争压力,需要不断提升技术水平和市场竞争力。
煤液化市场的机遇尽管面临挑战,煤液化市场依然存在许多机遇: - 新兴市场需求增长:一些新兴经济体的能源需求不断增长,煤液化作为一种可替代能源具有巨大市场潜力。
- 政策支持:各国政府在可再生能源和减少碳排放方面采取积极政策,为煤液化市场的发展提供了有利环境。
- 技术创新:煤液化技术不断创新,新的技术进展有望降低成本、提高效率,进一步推动市场发展。
结论综上所述,煤液化市场具有广阔的前景和发展潜力。
随着全球能源需求的增长和可再生能源的发展,煤液化作为一种可替代能源技术将扮演重要角色。
然而,煤液化市场仍然面临一些挑战,需要加强技术创新和环境管理,以提高市场竞争力和可持续发展能力。
2024年现代化煤直接液化技术进展
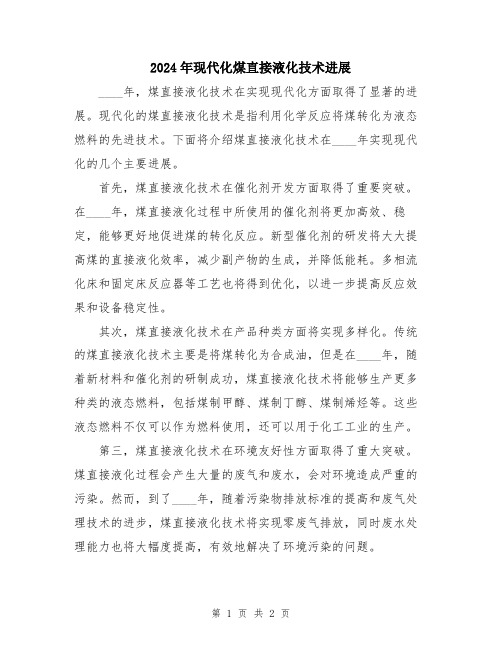
2024年现代化煤直接液化技术进展____年,煤直接液化技术在实现现代化方面取得了显著的进展。
现代化的煤直接液化技术是指利用化学反应将煤转化为液态燃料的先进技术。
下面将介绍煤直接液化技术在____年实现现代化的几个主要进展。
首先,煤直接液化技术在催化剂开发方面取得了重要突破。
在____年,煤直接液化过程中所使用的催化剂将更加高效、稳定,能够更好地促进煤的转化反应。
新型催化剂的研发将大大提高煤的直接液化效率,减少副产物的生成,并降低能耗。
多相流化床和固定床反应器等工艺也将得到优化,以进一步提高反应效果和设备稳定性。
其次,煤直接液化技术在产品种类方面将实现多样化。
传统的煤直接液化技术主要是将煤转化为合成油,但是在____年,随着新材料和催化剂的研制成功,煤直接液化技术将能够生产更多种类的液态燃料,包括煤制甲醇、煤制丁醇、煤制烯烃等。
这些液态燃料不仅可以作为燃料使用,还可以用于化工工业的生产。
第三,煤直接液化技术在环境友好性方面取得了重大突破。
煤直接液化过程会产生大量的废气和废水,会对环境造成严重的污染。
然而,到了____年,随着污染物排放标准的提高和废气处理技术的进步,煤直接液化技术将实现零废气排放,同时废水处理能力也将大幅度提高,有效地解决了环境污染的问题。
此外,煤直接液化技术在能源资源利用方面将变得更加高效。
煤是一种丰富的能源资源,但由于其固态结构和高含灰、硫等元素的特性,煤的利用率相对较低。
在____年,煤直接液化技术将能够更有效地提取煤中的有用能源,并最大程度地减少能源的浪费。
通过煤直接液化技术,可以充分利用煤炭资源,满足人们对能源的需求,并减少对传统能源的依赖。
综上所述,____年现代化的煤直接液化技术将会在催化剂开发、产品种类、环境友好性和能源资源利用等方面取得重要进展。
这些进展将使煤直接液化技术成为一种更加高效、多样化、环保和节能的能源转化技术,为人们提供更多种类和更可持续的液态燃料。
煤的液化技术
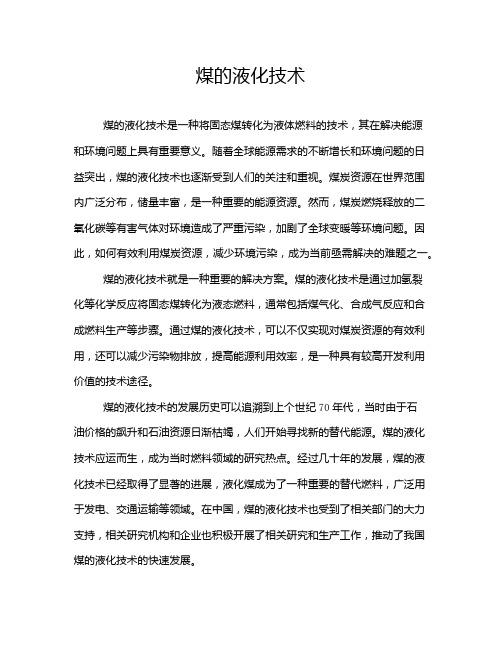
煤的液化技术煤的液化技术是一种将固态煤转化为液体燃料的技术,其在解决能源和环境问题上具有重要意义。
随着全球能源需求的不断增长和环境问题的日益突出,煤的液化技术也逐渐受到人们的关注和重视。
煤炭资源在世界范围内广泛分布,储量丰富,是一种重要的能源资源。
然而,煤炭燃烧释放的二氧化碳等有害气体对环境造成了严重污染,加剧了全球变暖等环境问题。
因此,如何有效利用煤炭资源,减少环境污染,成为当前亟需解决的难题之一。
煤的液化技术就是一种重要的解决方案。
煤的液化技术是通过加氢裂化等化学反应将固态煤转化为液态燃料,通常包括煤气化、合成气反应和合成燃料生产等步骤。
通过煤的液化技术,可以不仅实现对煤炭资源的有效利用,还可以减少污染物排放,提高能源利用效率,是一种具有较高开发利用价值的技术途径。
煤的液化技术的发展历史可以追溯到上个世纪70年代,当时由于石油价格的飙升和石油资源日渐枯竭,人们开始寻找新的替代能源。
煤的液化技术应运而生,成为当时燃料领域的研究热点。
经过几十年的发展,煤的液化技术已经取得了显著的进展,液化煤成为了一种重要的替代燃料,广泛用于发电、交通运输等领域。
在中国,煤的液化技术也受到了相关部门的大力支持,相关研究机构和企业也积极开展了相关研究和生产工作,推动了我国煤的液化技术的快速发展。
煤的液化技术主要包括两种类型,一种是直接煤液化技术,另一种是间接煤液化技术。
直接煤液化技术是将煤直接转化为液体燃料,其中包括常压煤泥浆化、催化煤液化等方法。
而间接煤液化技术则是先将煤气化生成合成气,再通过合成气反应制备液体燃料,这种方法主要包括费舍尔-托普希合成、马来酸技术等。
这两种技术各有优缺点,应用范围也有所不同,但都对煤的液化技术的发展起到了重要的推动作用。
煤的液化技术在实际应用中面临着一些挑战和难题。
首先,煤的液化技术的生产成本较高,设备复杂,需要大量的能源和原材料,同时也会产生大量的废水和废气,对环境造成一定污染。
煤炭液化

CO2 +3H2 = CH3O + H2O - 49.8kJ/mol
一氧化碳加氢除合成甲醇外,还可能发生不同的副反应 :
CO +3H2 = CH4 +H2O - 206.4kJ/mol CO2 +4H2= CH4 +2H2O - 164.9kJ/mol 2CO+2H2= CH4 + CO2 -247kJ/mol
CO + H2O = CO2 + H2 - 41.5J/mol 2CO +4H2 = (CH3)2O +H2O 2CH3OH = (CH3)2O + H2O 另外,还可能生成少量的乙醇和微量的醛、 酮、酯等副产物。
2、催化剂及反应条件
①催化剂 :锌基催化剂和铜基催化剂 ②反应条件 : 反应温度和压力 空速 ③合成气的组成 :
液化率随时间延长,开始时增加很快,以后逐渐减慢。
四、煤炭直接液化工艺
1、氢-煤法(H-Coal)工艺 以褐煤、次烟煤或烟煤为原料,在 沸腾床反应器中,高温、高压并在催化 剂作用下,经过加氢生产合成原油或低 硫燃料油。 合成原油可进一步加工提质成发动 机燃料; 低硫燃料油作锅炉燃料。
煤 沸 腾 床 反 应 器
Δ 200~600t/d H-Coal工艺沸 腾床反应器
沸腾床催化反应器
①循环泵出口液体(油)与进料煤浆和氢气 混合后一起进入到反应器底部的分布室, 经过分布板产生分布均匀的向上流动的液 速,使催化剂床层膨胀,并达到沸腾状态。 ②分布板上方的反应器圆筒为颗粒催化剂床 层。 ③在反应器底部设有液体循环泵以提高液相 速度 ④颗粒催化剂床层的膨胀和沸腾主要靠较高 的向上流动的液相速度来实现;
煤的液化原理及应用现状

煤的液化原理及应用现状1. 煤的液化原理煤的液化是指将固体煤炭转化为液体燃料的过程。
液化煤技术是利用化学反应将煤炭转化为可以燃烧的液体燃料,以满足能源需求。
下面是煤的液化原理的一些关键点:•加热:将煤炭加热到高温。
高温有助于打破煤炭的化学键,使其分解为较小的分子。
•催化剂:使用催化剂促进液化反应。
催化剂能够降低反应的活化能,提高反应速率。
•溶剂:使用合适的溶剂来使煤炭与催化剂接触,并促进反应的进行。
•氢气:向反应体系中加入氢气,可以提高液化反应的效率并降低产物中的杂质含量。
2. 煤的液化应用现状煤的液化技术已经在工业生产中得到广泛应用。
下面是煤的液化应用现状的一些主要方面:2.1 燃料煤的液化产物可以用作燃料,用于替代传统的石油燃料。
液化煤燃料的热值高,可以用于发电、汽车燃料等领域。
液化煤燃料还可以降低燃烧产生的污染物排放。
2.2 化工原料煤的液化产物可以用作化工原料,在合成某些化学产品时起到重要作用。
例如,液化煤产物可以用于合成合成氨、甲醇等化学品。
2.3 煤基化学品煤的液化技术还可以用于生产煤基化学品。
通过煤的液化过程,可以获得具有高附加值的煤基化学品,例如煤油、煤焦油等。
2.4 国内外应用现状在中国,煤的液化技术已经得到了广泛的应用。
中国是全球煤炭资源最丰富的国家之一,因此煤的液化技术在中国具有重要意义。
国外一些发达国家也在开展煤的液化研究,并将其应用于能源转化和化工领域。
3. 结论煤的液化技术可以将固体煤炭转化为液体燃料或化工原料,具有广泛的应用前景。
煤的液化在燃料和化工行业发挥着重要作用,能够提高能源的利用效率,减少环境污染。
随着煤炭资源的减少和环境保护意识的增强,煤的液化技术将会得到更广泛的应用和研究。
名词解释煤的直接液化
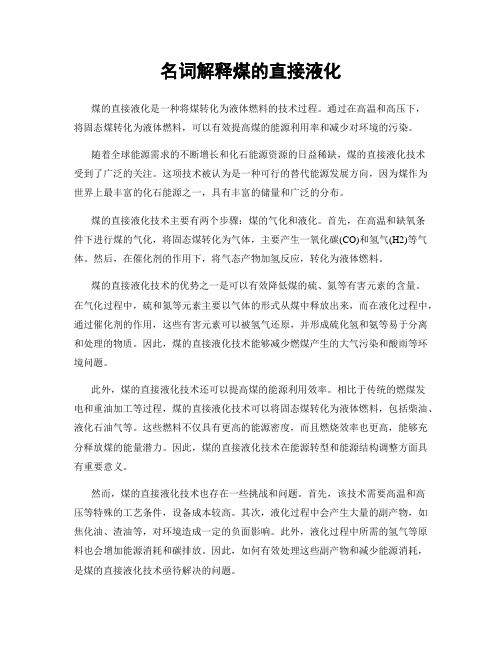
名词解释煤的直接液化煤的直接液化是一种将煤转化为液体燃料的技术过程。
通过在高温和高压下,将固态煤转化为液体燃料,可以有效提高煤的能源利用率和减少对环境的污染。
随着全球能源需求的不断增长和化石能源资源的日益稀缺,煤的直接液化技术受到了广泛的关注。
这项技术被认为是一种可行的替代能源发展方向,因为煤作为世界上最丰富的化石能源之一,具有丰富的储量和广泛的分布。
煤的直接液化技术主要有两个步骤:煤的气化和液化。
首先,在高温和缺氧条件下进行煤的气化,将固态煤转化为气体,主要产生一氧化碳(CO)和氢气(H2)等气体。
然后,在催化剂的作用下,将气态产物加氢反应,转化为液体燃料。
煤的直接液化技术的优势之一是可以有效降低煤的硫、氮等有害元素的含量。
在气化过程中,硫和氮等元素主要以气体的形式从煤中释放出来,而在液化过程中,通过催化剂的作用,这些有害元素可以被氢气还原,并形成硫化氢和氨等易于分离和处理的物质。
因此,煤的直接液化技术能够减少燃煤产生的大气污染和酸雨等环境问题。
此外,煤的直接液化技术还可以提高煤的能源利用效率。
相比于传统的燃煤发电和重油加工等过程,煤的直接液化技术可以将固态煤转化为液体燃料,包括柴油、液化石油气等。
这些燃料不仅具有更高的能源密度,而且燃烧效率也更高,能够充分释放煤的能量潜力。
因此,煤的直接液化技术在能源转型和能源结构调整方面具有重要意义。
然而,煤的直接液化技术也存在一些挑战和问题。
首先,该技术需要高温和高压等特殊的工艺条件,设备成本较高。
其次,液化过程中会产生大量的副产物,如焦化油、渣油等,对环境造成一定的负面影响。
此外,液化过程中所需的氢气等原料也会增加能源消耗和碳排放。
因此,如何有效处理这些副产物和减少能源消耗,是煤的直接液化技术亟待解决的问题。
总的来说,煤的直接液化技术具有可行性和重要性,可以有效提高煤的能源利用率和减少环境污染。
尽管存在一些挑战和问题,但通过技术创新和工艺改进,可以进一步提升该技术的经济性和环境友好性。
煤制气液化分离工艺技术的运用分析

煤制气液化分离工艺技术的运用分析
煤制气液化分离工艺技术是指将煤制气进行液化后,通过分离技术将不同成分的液态产品分开的工艺。
该技术在煤炭资源利用领域具有重要的意义,可以有效提高煤炭资源的利用率和经济效益。
煤制气液化分离工艺技术的主要流程包括煤制气、液化和分离三个步骤。
首先,通过煤制气工艺将煤转化为合成气,即氢气和一氧化碳的混合气体;其次,将合成气进行液化处理,使其变为液态烃类产物,包括甲烷、乙烷、丙烷等低碳烃和苯、甲苯、二甲苯等芳香烃;最后,通过分离技术将不同成分的液态产品进行分离,得到高纯度的液态燃料和化工原料。
煤制气液化分离工艺技术的运用可以有效地解决煤炭资源利用和环境问题。
首先,该技术可以将煤的碳含量转化为能源和化工原料,使煤炭得到了充分的利用,并减少了对化石燃料的依赖;其次,液化处理可以将合成气的体积大幅减小,节约了存储空间和运输成本;最后,分离技术可以得到高品质的液态烃类产物,满足了工业和民生领域的不同需求。
在运用煤制气液化分离工艺技术时需要注意以下几点:首先,合成气的含硫量和含硫化物的种类会对液化和分离工艺产生影响,需要进行预处理;其次,液化和分离条件需要进行优化来提高产物的纯度和收率;最后,由于煤制气需要高温和高压来触媒反应,系统需要考虑安全性,减少事故发生的概率。
总的来说,煤制气液化分离工艺技术的运用对煤炭资源的综合利用和环境保护意义重大。
该技术在提高煤炭资源利用率和促进产业结构升级等方面具有重要的作用,在未来的应用中有着广阔的发展前景。
煤液化技术的重要性

煤液化技术的重要性1.1 中国的能源现状随着我国经济的快速开展,能源消费急剧增加,20世纪90年代我国已成为石油净进口国。
2003年,我国已是全球仅次于美国的第二大石油进口国和消耗国,2021年我国石油净进口量超过19985万t,进口原由占国内消费比重达53.1%。
石油资源匮乏和国内石油供给缺乏已成为中国能源开展的一个严峻现实, 随着国民经济的开展,石油供需矛盾将呈持续性扩大趋势。
经济高速增长、石油资源缺乏的中国已经把石油平安置于能源战略的核心位置。
我国“多煤炭、少石油、缺天然气〞的能源资源特点决定了我国能源在较长时期内以煤为主的格局不会改变,确立我国的能源平安战略,必须从这一根本条件出发。
充分利用我国丰富的煤炭资源解决石油短缺问题并保证能源平安供给,是我国能源平安战略的一条有效而又可行的途径。
煤液化技术在我国应用前景在替代石油的化石资源中,只有煤炭可以在近中期内满足与千万吨数量级的油品缺口相匹配的需要。
在这样的背景下,合理利用中国丰富的煤炭资源, 开发“煤制油〞技术, 作为石油资源的补充, 解决目前燃油短缺、环境污染两大难题, 对中国具有十分重要的战略意义[1]。
假设以目前已查证的煤炭资源量的2 0 %作为直接液化原料,那么相当于为中国增加了约4 5 0亿吨的原油资源量。
有专家预计,到2 0 2 0 年中国的“煤制油〞工程将形成年产5 0 0 0万吨油品的生产能力,加上届时将有年产2 0 0 0万吨的生物质油品投入使用,中国原油对外依赖程度有望从6 0 %以上下降到45%以下。
到2030 年,在全球替代能源中非石油替代能源将到达日产1 0 0 0万桶,其中煤制油将占2 9%。
就中国来说,煤炭储量丰富,政府有意愿开展这一产业,煤制油工业有着光明的前景。
煤液化技术在我国中战略地位中国将长期坚持能源供给根本立足国内的方针, 把煤炭作为主体能源, 这是中国能源平安的基石。
长期以来, 中国政府坚持能源生产、消费与环境保护并重的方针, 把支持清洁煤技术的开发应用作为一项重要的战略任务。
煤炭液化技术几发展意义

1 我国煤炭现状我国煤炭资源丰富,煤种齐全,煤炭资源占能源储量的92%,这就决定了我国的能源生产和消费在相当长的时期仍以煤炭为主,目前占70%左右。
随着能源消费总量的增加,煤炭需求总量将增加,大幅度减少煤炭消费是较难办到的。
另外,我国能源分布不均,重心偏西偏北,而经济发达区域偏南偏东,常规能源需要长途运输才能满足需求,而且烟煤型污染已经给生态环境带来严重问题。
因此为了减少环境污染,提高煤炭利用效率,减少消费,降低CO2 排放量,生产便于运输的燃料,开发出了煤炭液化技术。
煤炭液化技术是指煤炭转化为液态烃的技术,可将煤转化为汽油、柴油、LPG等产品。
2 煤的结构煤是由彼此相似的“结构单元”通过各种桥键连接而成的立体网状大分子,煤的“结构单元”主要是由缩合芳香环组成,“结构单元”外围有烷基侧链和官能团。
此外,还存在一定量的非化学键力结合的低分子化合物。
尽管由于生成的地质年代不同,造成煤的组成也不同,但基本元素成分为碳、氢、氧、氮、硫。
此外还包括一些成灰元素如硅、铝、铁、钙、镁、碱金属,和一些微量重金属,如汞、硒等。
3 煤的液化技术煤炭是一种碳含量高,但氢含量只有5%的固体,与液体燃料相比,煤炭不便于运输,最主要的一点是煤炭不能直接提供给内燃机和其他内燃设备,而这些设备都广泛应用于车辆。
目前,车辆的燃料主要来自石油,石油中氢含量为煤炭的 2 倍。
如果利用煤炭来代替车辆燃料,煤炭必须转化成类似氢含量的液体物质。
为此需要直接或间接地从煤中脱炭加氢,煤炭液化技术由此产生。
煤炭液化分直接液化和间接液化两种。
3.1 直接液化直接液化工艺旨在向煤的有机结构中加氢,破坏煤结构产生可蒸馏液体。
目前已经开发出多种直接液化工艺,但就其基本化学反应而言,具有以下共同特征:在温和高压的条件下在溶剂中将较高比例的煤溶解,然后加入氢气和催化剂进行加氢裂化,生成液态烃类,在此过程中会生成少量气体,脱除了煤中氮、氧和硫等杂质。
直接液化是目前可采用的最有效的液化方式。
- 1、下载文档前请自行甄别文档内容的完整性,平台不提供额外的编辑、内容补充、找答案等附加服务。
- 2、"仅部分预览"的文档,不可在线预览部分如存在完整性等问题,可反馈申请退款(可完整预览的文档不适用该条件!)。
- 3、如文档侵犯您的权益,请联系客服反馈,我们会尽快为您处理(人工客服工作时间:9:00-18:30)。
煤液化技术的重要性1.1 中国的能源现状随着我国经济的快速发展,能源消费急剧增加,20世纪90年代我国已成为石油净进口国。
2003年,我国已是全球仅次于美国的第二大石油进口国和消耗国,2008年我国石油净进口量超过19985万t,进口原由占国消费比重达53.1%。
石油资源匮乏和国石油供应不足已成为中国能源发展的一个严峻现实, 随着国民经济的发展,石油供需矛盾将呈持续性扩大趋势。
经济高速增长、石油资源缺乏的中国已经把石油安全置于能源战略的核心位置。
我国“多煤炭、少石油、缺天然气”的能源资源特点决定了我国能源在较长时期以煤为主的格局不会改变,确立我国的能源安全战略,必须从这一基本条件出发。
充分利用我国丰富的煤炭资源解决石油短缺问题并保证能源安全供给,是我国能源安全战略的一条有效而又可行的途径。
1.2 煤液化技术在我国应用前景在替代石油的化石资源中,只有煤炭可以在近中期满足与千万吨数量级的油品缺口相匹配的需要。
在这样的背景下,合理利用中国丰富的煤炭资源, 开发“煤制油”技术, 作为石油资源的补充, 解决目前燃油短缺、环境污染两大难题, 对中国具有十分重要的战略意义[1]。
若以目前已查证的煤炭资源量的2 0 %作为直接液化原料,则相当于为中国增加了约4 5 0亿吨的原油资源量。
有专家预计,到2 0 2 0 年中国的“煤制油”项目将形成年产5 0 0 0万吨油品的生产能力,加上届时将有年产2 0 0 0万吨的生物质油品投入使用,中国原油对外依赖程度有望从6 0 %以上下降到45%以下。
到2030 年,在全球替代能源中非石油替代能源将达到日产1 0 0 0万桶,其中煤制油将占2 9%。
就中国来说,煤炭储量丰富,政府有意愿发展这一产业,煤制油工业有着光明的前景。
1.3 煤液化技术在我国中战略地位中国将长期坚持能源供应基本立足国的方针, 把煤炭作为主体能源, 这是中国能源安全的基石。
长期以来, 中国政府坚持能源生产、消费与环境保护并重的方针, 把支持清洁煤技术的开发应用作为一项重要的战略任务。
煤炭直接液化是中国能源战略的组成部分, 对充分利用国资源, 解决石油安全具有重要的战略和现实意义。
2 煤液化的发展状况2.1 煤液化技术简介煤液化工艺大致可分为两大部分,即在高温高压条件下把粉煤催化加氢生产液化粗油的液化工艺和把液化粗油加氢裂解的提质加工精制工艺。
其中煤液化技术又包括直接液化技术和间接液化技术。
2.1.1 煤直接液化技术煤的直接液化法,就是以煤为原料,在高温高压条件下,通过催化加氢直接液化成烃类化合物,再通过精馏制取汽油、柴油、燃料油等成品油[ 1 ]。
典型的煤直接液化技术是在400 ℃、150 个大气压左右将合适的煤催化加氢液化,产出的油品芳烃含量高,硫氮等杂质需要经过后续深度加氢精制才能达到目前石油产品的等级[ 2 ]。
煤直接液化工艺单元主要包括:①煤浆配制、输送和预热过程的煤浆制备单元;②煤在高温高压条件下进行加氢反应,生成液体产物的反应单元;③将反应生成的残渣、液化油、气态产物分离的分离单元;④稳定加氢提质单元。
2.1.2 煤间接液化技术煤间接液化就是将煤通过气化炉生成的气化气转化成合成气,并以合成气为基础原料,采用合成工艺路线费托( F-T ) 法转化为烃类化合物,并通过精馏生产出液体燃料和各种化学品。
其中,以煤为原料先经气化制合成气(CO + H),2再以合成气为原料的催化剂作用下合成液态烃类产品,称为费托(F-T)合成。
煤间接液化的操作条件温和,几乎不依赖于煤种。
典型的煤间接液化的合成过程在250 ℃、15 -4 个大气压下操作,合成的产品不含硫氮等污染物,合成的汽油的辛烷值不低于90号,合成柴油的十六烷值高达75,且不含芳烃,质量高于第四代洁净油品[ 2 ]。
煤炭间接液化工艺单元主要包括:①大型加压煤气化、备煤和脱硫、除尘净化系统的造气单元;②在固定床、循环流化床、固定流化床和浆态床等合成反应器中进行合成反应的F- T 合成单元;③将反应产物进行分离的分离单元;④后加工提质单元。
2.1.3 液化粗油提质加工技术从液化工艺得到的液化粗油中含有较多的芳烃和氧、氮、硫等杂原子。
虽然液化粗油可以作为锅炉燃料直接使用,但硫和氮在燃烧时会严重地污染大气。
如果要把液化油制成符合质量标准的汽、柴油等产品,就必须进行深度加氢处理以便降低其芳香度和脱除氮、氧、硫等杂原子,得到可以接受的液体燃料,这个过程就是液化粗油提质加工过程。
2.2 煤液化技术的发展状况2.2.1 直接液化的典型工艺煤直接液化是在高温高压下,在溶剂和催化剂存在下对煤加氢裂解直接转化为液化油的工艺过程。
煤直接液化的操作条件苛刻,对煤种的依赖性强。
20世纪70年代以后,美国、德国、日本和前联等主要工业发达国家相继开发出多种工艺,试验规模也从试验室小试到每天数百吨级的大型中试应有尽有。
表1.1列出具有代表性的几种工艺开发情况,分述如下:表 1.1 煤直接液化的典型工艺开发情况国别装置或工艺试验规模地点开发机构美国EDS 250 Baytown EXXON美国H-COAL 600 Catlettsburg HRI美国HTI-Process 3 Lawrenceville HTI德国IGOR 200 Bottrop RAG/VEBA日本NEDOL 150 日本鹿岛NEDO 2.2.1.1 美国HIT工艺HIT工艺是在H-COAL工艺和CTSL工艺的基础上发展起来的,而H-COAL工艺已进行600t/h大型中试,其前身是已经普遍得到工业应用的沸腾床重油加氢裂化H-OIL工艺,CTSL工艺是在H-COAL单段液化工艺的基础上研制而成的两段液化工艺。
HIT工艺的主要特点是:采用特殊的液体循环沸腾床(悬沸床)反应器,达到全返混反应器模式;采用超细、高分散铁系催化剂,用量少;在高温分离器后面增加了一个液化油加氢提质固定床反应器,对液化油进行加氢精制;固液分离采用临界溶剂萃取的方法,从液化残渣中最大限度地回收重质油,从而大幅提高了液化油收率。
2.2.1.2 德国IGOR工艺IGOR工艺是在40年代德国商业化规模IG工艺的基础上改进而成的,原料煤经磨碎、干燥后与催化剂、循环油一起制成煤浆,加压至30MPa并与氢气混合,进入反应器进行加氢液化反应。
此工艺在德国的Bottrop 建造有200t/d中试厂,设备运转了2.2万小时,处理了17万t煤,生产了8.5万t馏出产品。
其工艺主要特点是:把循环溶剂加氢和液化油提质加工与煤的直接液化串联在一套高压系统中,避免了分立流程物料降温降压又升温升压带来的能量损失;催化剂采用和CO甲烷化,使碳的损炼铝工业的废渣(赤泥);在固定床催化剂上还能把CO2失量降到最低限度;循环溶剂是加氢油,供氢性能好,煤液化转化率高。
2.2.1.3 日本NEDOL工艺NEDOL液化工艺是在美国EXXON石油公司1977-1984年开发的EDS工艺基础上的改进型,在1t/d装置试验成功的基础上,设计建设了150t/d的大型中试厂,主要对次烟煤和低阶烟煤进行液化。
该工艺特点是:主反应器是一个简单的液体向上流动的管束反应器,操作温度为430℃-465℃,操作压力17Mpa-19MPa;催化剂采用合成的铁系催化剂或天然黄铁矿;大部分的中质油和全部的重质油馏分经加氢后被循环作为供氢溶剂,供氢性能优于EDS工艺;固液分离采用减压蒸馏的方法;该液化工艺的液体产品中含有较多的杂原子,液化油的质量较低,还须加氢提质才能获得合格产品。
2.2.1.4 HRI煤油共炼工艺该工艺是介于石油加氢裂化和煤直接液化之间的工艺,将煤和石油渣油同时加氢裂解,转化成轻、中质馏分油,生产各种运输燃料的工艺技术,溶剂不进行循环使用。
在HRI煤油共炼中,煤油浆一次通过两段反应器,固液分离只用常减压蒸馏,在加氢液化反应过程中,渣油作煤液化供氢溶剂,煤和煤中矿物质促进渣油转变成轻油、中质油馏分,防止渣油结焦。
由于煤、油之间呈现一种协同作用,使该工艺不但具有较高的油收率,而且共炼的油品比煤直接液化油更易加工成汽油、柴油,整个工艺过程氢耗低、氢利用率高、重金属脱除率高,还可处理劣质渣油。
在经济上,煤油共炼要比直接液化更具竞争性。
2.2.1.5 中国煤直接液化技术的开发研究我国自1980年重新开展煤炭直接液化技术研究,主要由煤炭科学研究总院煤化学研究所承担。
该所建成具有先进水平的煤炭直接液化、油品提质加工、催化剂开发和分析检验实验室,通过国际合作引进了三套煤直接液化小型连续试验装置,开展了“煤种评价与选择”、“工艺条件与催化剂的研究”、“液化油的提质加工”等基础研究和技术开发,取得了一批科研成果。
例如,对我国十几个省、自治区的上百个煤种进行了液化特性试验研究,优选出14种液化特性较好的煤种;分别与日本、美国、德国有关政府部门和公司合作完成了在中国建设3个煤液化商业化示工厂的可行性究。
目前我过集团正在建设二战后第一个煤直接液化示厂,2008年12月煤直接液化百万吨级示工程一次试车成功。
截止2009年1月7日14时,工程已连续运转逾190小时,生产出合格的石脑油和柴油。
尽管国际上已进行大型中试的各种煤直接液化工艺至今均未商业化,但围绕改进这些工艺的应用基础研究却始终不断,主要集中在反应器的改善、反应机理的探讨、煤的组成对煤浆流变特性的影响、溶剂作用及其性质、催化作用和新的催化剂、逆反应对液化的影响和抑制、降低液化过程中的氢耗等方面。
2.2.2 间接液化的典型工艺煤的间接液化是以煤基合成气为原料,在一定的温度和压力下,定向地催化合成烃类燃料油和化工原料的工艺,典型的工艺是F-T合成法。
南非Sasol的F-T合成工艺是目前世界上唯一以煤为原料制取液体燃料并实现商业化的公司,据1996年报导,该公司年耗煤4200万t,生产汽油、柴油、蜡、氨、聚合物等130多种产品,总产量达170万t,其中油品约占75%[3]。
世界上首例浆态床反应器工业化F-T合成技术于1993年在Sasol投产,用于生产蜡和重质燃料油,每天生产液体燃料2500桶。
80年代初,中科院煤炭化学研究所开始进行F-T合成的研究,对传统F-T合成进行了很大改进,提出将传统的F-T合成与沸石分子筛相结合的固定床两段合成(简称SMFT法),SMFT合成于1990年完成模试,MFT 合成油厂于1994年11月完成了70余天的2000t/ a工业性试验[4],为进一步商业化生产奠定了基础。
此外,化学物理研究所等科研单位也对F-T合成进行了多方面的研究与探索。
近年来,国外对F - T 合成烃类液体燃料技术的研究开发工作都集中于如何提高产品的选择性和降低成本方面。
造气单元中,煤气化技术的发展趋势主要为:增大气化炉的断面,以提高产量;提高气化炉温度和压力,以增加空收率;采用粉煤气化,以降低对煤质的要求;研制气化新工艺和气化炉新结构,以减少基本建设投资和操作费用。