连铸工艺与操作
连铸工艺与操作

连铸工艺与操作连铸工艺与操作是指将熔化的金属连续浇铸成板坯、板材或形状复杂的铸锭的一种工艺。
连铸工艺与操作包括浇注、结晶器、凝固过程、拉拔速度、铸坯形状控制等方面。
本文将从工艺参数调整、结晶凝固行为控制、机械操作等方面进行详细介绍。
首先,连铸工艺参数的调整对于连铸工艺与操作至关重要。
例如,浇注温度的控制是保证连铸质量的关键因素之一、合理的浇注温度既要保证金属液在连铸道中均匀流动,又要保证凝固能够稳定进行。
此外,还需要注意调整喷口位置和数量的控制,以实现均匀的铸坯形成。
另外,还需要控制下料速度,使得铸坯能够以适当的速度进入冷却设备,保证坯壳质量以及铸坯的尺寸准确。
其次,连铸过程中的结晶器的设计和操作也是非常重要的。
结晶器的设计和选择应根据铸造的金属类型和产品要求来确定。
合理的结晶器设计可以改善坯壳的质量,减少坯壳的热裂纹以及减少坯壳的非均匀性。
此外,在操作过程中,需要注意结晶器的冷却水的流量和温度的控制,以保证坯壳的质量。
再次,连铸过程中的凝固行为的控制也是非常重要的。
凝固过程中的凝固速度和温度梯度等参数对于金属的组织结构和性能具有很大影响。
因此,需要通过调整拉拔速度、浇注温度和结晶器的冷却水等控制参数来实现凝固行为的控制。
合理的凝固行为的控制可以改善铸坯的坯壳质量和组织结构稳定性,提高成材率。
最后,连铸工艺与操作中的机械操作也是非常重要的。
机械操作主要包括轧制、扒皮、拉拔等。
轧制是将铸坯通过轧机辊牵拉成连续板坯或板材的过程。
在轧制过程中,需要注意辊缝的控制以及轧辊的选择,以保证板坯或板材的尺寸精度和表面质量。
扒皮是将板坯或板材的表面不良的层剥离掉,以减少金属表面缺陷和提高表面质量。
拉拔是将板坯或板材进行拉伸,以改变其尺寸和形状。
在拉拔过程中,需要注意拉拔速度的控制,以保证拉拔过程中板坯或板材的机械性能不受到损害。
总之,连铸工艺与操作涉及到很多方面的工艺参数调整和操作控制。
合理的工艺参数调整和操作控制可以保证金属铸造的质量和产品的性能。
方坯连铸机工艺技术操作规程

一、连铸机主要参数:序号名称单位参数1 机型刚性引锭杆全弧形连铸机(罗可普机型)2 浇铸钢种普碳钢、低合金钢、合金结构钢、焊条钢、冷墩钢、弹簧钢、高碳钢、标准件用钢3 基本弧形半径m 1#机:R6;2#、3#机、5#机:R84 台数×机数×流数1#、2#、3#机:1×4×4;5#机:1×5×55 流间距mm 12006 铸坯断面尺寸mm×mm 120×120、150×150、180×180 160×220、160×2807 工作拉速m/min 1#、2#、3#机:0.5-3.3;5#机0.5-3.58 中包容量t 1#、2#、3#机工作液位:18t;(液面深度700mm),溢流液位:19t(液面深度800mm);5#机工作液位:30t(液面深度800mm),溢流液位:35t(液面深度900mm)9 结晶器型式管式结晶器,5#机带一对足辊10 结晶器铜管长度mm 小方坯1#机:850;2#、3#:900;矩形坯均为:850;5#机:100011 振动方式1#、2#、3#机:短臂四连杆正弦振动;5#机:双偏心半板簧正弦振动12 振幅mm 413 铸坯定尺长度m 3~1214 铸坯切割方式火焰切割机自动切割二、连铸机工艺流程图转炉出钢→钢包回转台→中间罐→结晶器→二次冷却→拉矫机→火焰切割机→输送辊道→翻钢机、移坯机→出坯三、中间包的准备与烘烤1、定径水口技术要求:定径水口技术参数控制表项目ZrO2含量显气孔率体积密度指标≥92% ≤18% 3.9g/cm3左右2、中间包的检查:必须认真检查中间包水口座砖,发现座砖有问题,应及时更换。
绝热板包应认真检查中间包绝热板和绝热板之间的泥料,发现问题,及时处理;然后方可安装定径水口。
干式料中包应认真检查中包快换机构工作是否正常,是否存在滑块打不到位,滑块打不正等情况。
连铸工序安全操作规程
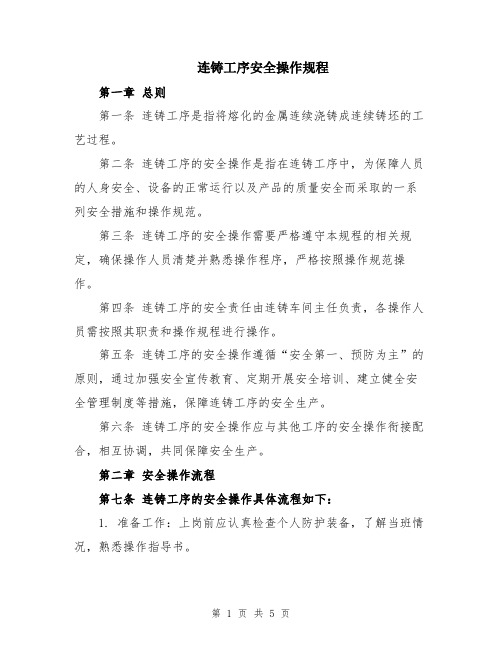
连铸工序安全操作规程第一章总则第一条连铸工序是指将熔化的金属连续浇铸成连续铸坯的工艺过程。
第二条连铸工序的安全操作是指在连铸工序中,为保障人员的人身安全、设备的正常运行以及产品的质量安全而采取的一系列安全措施和操作规范。
第三条连铸工序的安全操作需要严格遵守本规程的相关规定,确保操作人员清楚并熟悉操作程序,严格按照操作规范操作。
第四条连铸工序的安全责任由连铸车间主任负责,各操作人员需按照其职责和操作规程进行操作。
第五条连铸工序的安全操作遵循“安全第一、预防为主”的原则,通过加强安全宣传教育、定期开展安全培训、建立健全安全管理制度等措施,保障连铸工序的安全生产。
第六条连铸工序的安全操作应与其他工序的安全操作衔接配合,相互协调,共同保障安全生产。
第二章安全操作流程第七条连铸工序的安全操作具体流程如下:1. 准备工作:上岗前应认真检查个人防护装备,了解当班情况,熟悉操作指导书。
2. 操作准备:根据操作指导书准备所需设备、工具和资料,确保器材完好,设备运行正常。
3. 操作过程:根据操作指导书进行操作,确保操作规范,严禁违章操作。
4. 临时工作:如需进行临时工作时,应按照操作指导书和有关规定进行操作,并及时上报。
5. 结束工作:工作结束后将设备、工具进行清理,收拾工作环境,做好记录并交接。
第八条连铸工序的安全操作需要严格按照操作指导书来进行,确保工艺操作规范,保障工序的安全生产。
第三章安全防护措施第九条连铸工序的安全操作需要进行严格的安全防护措施。
1. 个人防护:操作人员在连铸工序中应佩戴安全帽、防护眼镜、防护手套、防护鞋等个人防护装备,保障人身安全。
2. 设备防护:连铸设备应进行定期维护保养,故障及时修理,确保设备的正常运行,消除安全隐患。
3. 安全信号:建立连铸工序的安全信号系统,确保人员之间的有效沟通,做好安全警示和应急处理。
4. 工作环境:连铸工序的作业场所应保持清洁,无杂物,作业环境要通风良好,避免因气体积聚引发事故。
连铸工艺技术操作规程

连铸操作规程一、主控操作1 生产前准备1.1水准备1.1.1机长确认具备送水条件后,通知水泵房送各路生产用水。
1.1.2与中间包班长配合,检查四个流次的足辊段、活动段、固定段水压及流量情况,如有异常,及时向机长汇报。
1.2上引锭1.2.1上引锭前与机长联系,切割班长确认辊道上及拉矫辊内有无障碍物,中间包班长确认二冷室引锭通道是否安全无阻。
1.2.2与液压工联系,确认液压站有无异常情况,开启大包及中包液压、主液压、振动台液压,出坯区液压。
泵开启后,如发现问题及时与相关人员联系解决。
1.2.3与切割工联系确认拉矫辊运转是否正常。
1.2.4确认自动上引锭条件是否达到,如没达到,确定哪项条件不满足,应通知相关人员及时处理。
1.2.5以上条件具备时,启动各流自动上引锭。
1.2.6上引锭时在电脑屏幕及监视器中监视上引锭情况,如发现哪流引锭中途停止或其他异常情况,应立即停止该流,并向机长汇报,检查故障与相关人员联系处理。
处理后,如要继续上引锭,则手动将引锭送上;如要自动再上该流引锭,则需手动将引锭退回原位并收集,待自动上引锭条件满足后,启动自动将引锭送上。
1.2.7浇钢工将引锭杆定位于结晶器后主控工在人机界面进行引锭杆强制在原位操作。
1.3生产前检查及准备工作1.3.1确认结晶器水流量、压力是否在正常范围内,如有异常及时向机长汇报与水泵房联系。
1.3.2确认事故水塔水位是否正常,正常水位不低于4m;结晶器总管压力是否正常,水量调节阀开口度是否正常。
1.3.3检查设备水压力及流量是否达到,正常压力应大于0.35MPa,流量大于450L/min。
1.3.4检查冲渣水压力及水泵状况。
1.3.5检查压缩空气及切割气体是否达到要求。
1.3.6确认电搅水系统水位,启动电磁搅拌水泵,检查压力、流量,确认电磁搅拌无故障。
1.3.7开浇前15分钟打开结晶器水逆止阀及设备水逆止阀。
1.3.8检查浇注许可条件是否达到,浇注前出坯区是否是远程控制。
连铸工序安全操作规程范本(2篇)

连铸工序安全操作规程范本一、设备安全操作规程1. 操作人员在进行连铸设备操作前,应熟悉设备的工作原理、操作方法及安全操作规程。
2. 操作前应仔细检查设备是否完好无损,包括各种传动装置、开关按钮和保护装置是否正常运行。
3. 操作人员必须佩戴适当的劳动保护用具,包括安全帽、防护眼镜、耳塞等。
特殊工种还需佩戴防护服和防护鞋。
4. 操作人员在接触设备前,应确保设备已停止运行并断电。
5. 对连铸设备的各种液压和气压系统进行操作前,必须了解各种压力设定和安全阀的定位。
二、检查设备问题1. 操作人员在连铸设备操作过程中,若发现设备发生异常噪音、震动或漏液等情况,应立即停止操作并上报主管。
2. 操作人员在发现设备出现损坏、断裂或松动等问题时,不得随意修理,而需上报主管并等待维修工人处理。
3. 设备操作过程中,若出现异常温度升高或冷却不良等问题,操作人员应立即停止操作,并上报主管。
4. 设备各种传动装置和液压系统的工作情况,应定期检查和保养。
三、设备操作规程1. 设备供电前,操作人员应确保所有开关按钮处于关闭状态,并且电源已接地。
2. 操作人员在设备启动前,应先确保所有防护装置已经安装到位,并进行测试。
3. 设备启动后,操作人员应随时关注设备的运行情况,如发现异常应立即停止设备并上报主管。
4. 设备操作中不得随意改变设备的设定参数,如需更改应上报主管并在主管允许下进行调整。
5. 设备操作过程中,操作人员应随时保持警惕,避免操作过程中发生摔倒、滑倒或碰撞等事故。
四、防范化学危害1. 在连铸操作过程中,操作人员应佩戴适当的防护用具以防止化学品溅入眼睛、口腔或皮肤。
2. 所有化学品及危险物品必须按规定存放,严禁将其与食品或饮料放在同一处。
3. 连铸设备操作过程中,如涉及到化学品的使用,应在通风良好的地方进行操作。
4. 设备操作结束后,所有使用的化学品都应妥善存放,以免引发火灾或爆炸事故。
五、紧急情况处理1. 在紧急情况下,如设备发生故障或事故,操作人员应立即停止设备并采取紧急救援措施。
炼钢厂连铸工艺操作流程
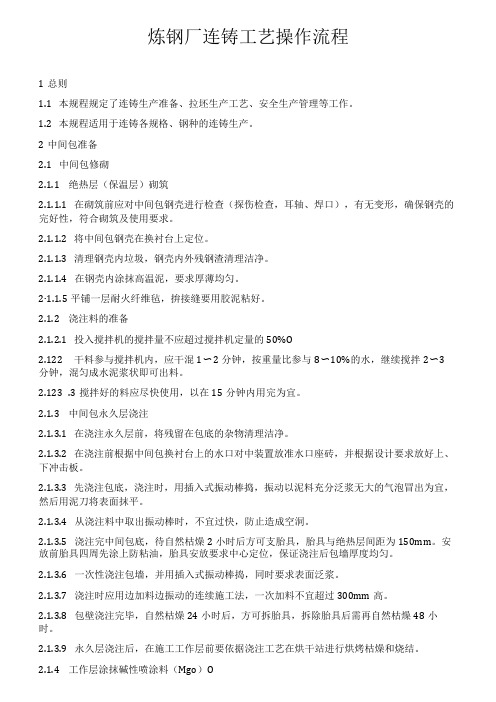
炼钢厂连铸工艺操作流程1总则1.1本规程规定了连铸生产准备、拉坯生产工艺、安全生产管理等工作。
1.2本规程适用于连铸各规格、钢种的连铸生产。
2中间包准备2.1中间包修砌2.1.1绝热层(保温层)砌筑2.1.1.1在砌筑前应对中间包钢壳进行检查(探伤检查,耳轴、焊口),有无变形,确保钢壳的完好性,符合砌筑及使用要求。
2.1.1.2将中间包钢壳在换衬台上定位。
2.1.1.3清理钢壳内垃圾,钢壳内外残钢渣清理洁净。
2.1.1.4在钢壳内涂抹高温泥,要求厚薄均匀。
2∙1.1.5平铺一层耐火纤维毡,拚接缝要用胶泥粘好。
2.1.2浇注料的准备2.1.2.1投入搅拌机的搅拌量不应超过搅拌机定量的50%O2.122干料参与搅拌机内,应干混1〜2分钟,按重量比参与8〜10%的水,继续搅拌2〜3分钟,混匀成水泥浆状即可出料。
2.123.3搅拌好的料应尽快使用,以在15分钟内用完为宜。
2.1.3中间包永久层浇注2.1.3.1在浇注永久层前,将残留在包底的杂物清理洁净。
2.1.3.2在浇注前根据中间包换衬台上的水口对中装置放准水口座砖,并根据设计要求放好上、下冲击板。
2.1.3.3先浇注包底,浇注时,用插入式振动棒捣,振动以泥料充分泛浆无大的气泡冒出为宜,然后用泥刀将表面抹平。
2.1.3.4从浇注料中取出振动棒时,不宜过快,防止造成空洞。
2.1.3.5浇注完中间包底,待自然枯燥2小时后方可支胎具,胎具与绝热层间距为150mm。
安放前胎具四周先涂上防粘油,胎具安放要求中心定位,保证浇注后包墙厚度均匀。
2.1.3.6一次性浇注包墙,并用插入式振动棒捣,同时要求表面泛浆。
2.1.3.7浇注时应用边加料边振动的连续施工法,一次加料不宜超过300mm高。
2.1.3.8包壁浇注完毕,自然枯燥24小时后,方可拆胎具,拆除胎具后需再自然枯燥48小时。
2.1.3.9永久层浇注后,在施工工作层前要依据浇注工艺在烘干站进行烘烤枯燥和烧结。
2.1.4工作层涂抹碱性喷涂料(Mgo)O1.1.1.1中间包内倒入干式料,用木板或其他工具刮平,厚度大于30mm,小于冲击板厚度20mm;在中间包烘烤器外表均匀涂一层石墨,将其放入中间包内,调整其位置,使其与冲击板下口吻合,并且与中间包四周的间距保持一致,大约30mm。
连铸机工艺技术操作规程
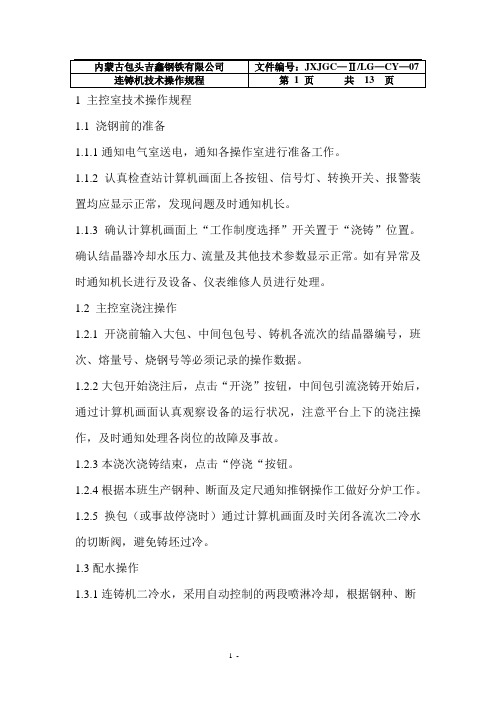
1 主控室技术操作规程1.1浇钢前的准备1.1.1通知电气室送电,通知各操作室进行准备工作。
1.1.2认真检查站计算机画面上各按钮、信号灯、转换开关、报警装置均应显示正常,发现问题及时通知机长。
1.1.3确认计算机画面上“工作制度选择”开关置于“浇铸”位置。
确认结晶器冷却水压力、流量及其他技术参数显示正常。
如有异常及时通知机长进行及设备、仪表维修人员进行处理。
1.2 主控室浇注操作1.2.1开浇前输入大包、中间包包号、铸机各流次的结晶器编号,班次、熔量号、烧钢号等必须记录的操作数据。
1.2.2大包开始浇注后,点击“开浇”按钮,中间包引流浇铸开始后,通过计算机画面认真观察设备的运行状况,注意平台上下的浇注操作,及时通知处理各岗位的故障及事故。
1.2.3本浇次浇铸结束,点击“停浇“按钮。
1.2.4根据本班生产钢种、断面及定尺通知推钢操作工做好分炉工作。
1.2.5换包(或事故停浇时)通过计算机画面及时关闭各流次二冷水的切断阀,避免铸坯过冷。
1.3配水操作1.3.1连铸机二冷水,采用自动控制的两段喷淋冷却,根据钢种、断面、钢水温度和拉坯速度等因素,由计算机自动调节二冷配水。
1.3.2检查所有水系统管道、手动、电动阀门,应开启灵活无泄漏,各种压力表、流量计、温度表、报警器完好无损。
1.3.3检查喷淋管是否对中并及时校正,喷嘴应配备齐全,无堵塞。
1.3.4检查二冷段导向架、托板、支承辊,、夹管是否完好畅通,辊子运转情况良好。
1.3.5检查各种冷却水水质是否符合工艺要求,各软管、接头无漏点。
1.3.6通知计算机操作站将“二冷水手动/自动”选择“手动”方式,然后打开水系统各阀门,同主控一起依据当班浇钢断面、钢种预先确认各段水压及水量见工艺卡。
1.3.7检查事故水球阀,应灵活好用。
拉钢前打开所有设备冷却水阀门,并检查供水是否正常,发现问题及时处理。
1.3.8认真观察水系统仪表情况是否正常。
发现问题应及时报告当班机长及维修人员处理。
连铸基本工艺及操作规程

1540-1560
1610-1660
30CrMnSi
1496
1515-1535
1590-1610
1570-1590
1545-1565
1610-1660
20CrMnTi
1510
1530-1550
1615-1635
1595-1615
1555-1575
1610-1660
45MnMoB
1489
编制:陶辉友审核:廖友祥批准:陈三芽
编号:DW/JS03
页码:第2页,共9页
D合金钢:03 04 05
E碳工钢:03 04 05
轴承钢:03 04
不同钢种选择合理的供水曲线,附表各钢种连铸工艺参数。
d.浇注全过程采用全保护浇注,结晶器保护渣加入量0.5-1.0kg/t。
e.各钢种浇注工艺参数见附表。
新余新良特殊钢有限责任公司
质量体系作业文件
连铸基本工艺及操作规程
1.目的
确保浇注按照工艺进行操作,钢锭坯质量符合相应的技术标准。
2.适用范围
本规程适用于连铸车间钢水成锭坯的生产过程。
3.职责与权限
3.1生产技术部负责钢水成锭坯的归口管理。
3.2连铸车间负责钢水成锭坯的实施,连铸主控室监督连铸工艺执行并做好记录。
1555-1575
1610-1660
25#
1507
1525-1545
1605-1625
1585-1605
1555-1575
1610-1660
30#
1502
1525-1545
1600-1620
1580-1600
1550-1570
1610-1660
连铸操作规程

连铸操作规程⽬录1、连铸机主要技术参数及技术要求 (2)1.1⽣产⼯艺流程 (2)1.2主要技术参数 (2)1.3结晶器主要参数 (2)1.4振动装臵主要参数 (3)1.5拉矫机主要参数 (3)1.6⽕焰切割机 (3)1.7技术要求 (4)2、岗位技术操作规程 (5)2.1⼤包浇钢⼯技术操作规程 (6)2.2中间包浇钢⼯技术操作规程 (8)2.3主控⼯技术操作规程 (11)2.4拉矫、切割、出坯⼯技术操作规程 (12)2.5配⽔⼯技术操作规程 (14)2.6推钢⼯技术操作规程 (16)3、中间包快速更换技术操作规程 (17)3.1准备⼯作 (17)3.2换包操作 (18)4、中间包准备操作规程 (18)4.1中间包永久层打结规程 (18)4.2中间包机件安装技术操作规程 (19)4.3中间包⼲式料修砌技术操作规程 (20)4.4翻包操作 (20)1、连铸机主要技术参数及技术要求1.1⽣产⼯艺流程⼤包——中间包——结晶器——⼆冷段——拉矫机——切割机——辊道——移钢机——冷床——码垛(热送)——精整——装车外运1.2主要技术参数机型:STEL—TEK弧型连铸机铸机半径:1#、2#机(R6/12m)3#机4#机(R8/16m)流数:1#、3#、4#机(5流)2#机(4流)流间距:1#、2#机(1200mm)3#机(1250mm)4#机(1400mm)浇注断⾯:130×130mm 165×225mm2150×150mm 165×280mm2180×180mm2 Ф150~Ф220 mm定尺:2.8~12.0m浇注⽅式:定径⽔⼝、塞棒式+浸⼊式⽔⼝全保护浇注拉速:平均拉速最⼤拉速130×130mm 3.0m/min 3.5m/min150×150mm 2.7m/min 3.2m/min180×180mm2 1.8m/min 2.4m/min165×225mm2 1.7m/min 2.0m/min165×280mm2 1.3m/min 1.6m/minФ150~Ф220 mm 2.1~1.2 m/min浇铸钢种:普碳钢、低合⾦钢﹑优质碳结钢﹑弹簧钢。
1#方圆坯连铸工艺技术操作规程

1 连铸工艺流程1.1炼钢厂工艺流程高炉铁水→炉外脱硫→转炉→LF炉(或VD炉)→1#方/圆坯连铸机→连铸方/圆坯1.2方/圆坯连铸工艺流程钢包回转台→中间包→结晶器→二冷区铸坯导向→拉矫机→中间辊道→辅助拉矫→切割机→输送辊道→活动挡板→固定挡板→翻钢机→捞钢机→翻转冷床→收集台架2 主要设备性能及工艺参数连铸机主要的技术性能及工艺参数3 连铸钢水要求3.1对钢水化学成分要求到站钢水化学成分符合钢种要求。
品种钢连铸钢水必须经过炉外精练,保证充分脱氧。
连铸钢水要求成份均匀,温度均匀,连浇炉次炉与炉之间成份波动范围小。
3.2钢水温度控制3.2.1液相线温度计算:1)C<0.51%TL=1534℃-〖90.4×%C+8×%Si+5×%Mn+34×%P+40×%S+10×%Sn+14×%As+1.5×%Cr+4×%Ni+7×%Nb+2×%V+60×%B+2×%Mo+17×%Ti+1%W〗2)C≥0.51%TL=1521℃-〖65×%C+8×%Si+5×%Mn+34×%P+40×%S+10×%Sn+14×%As+1.5×%Cr+4×%Ni+7×%Nb+2×%V+60×%B+2×%Mo+17×%Ti+1%W〗3.2.2中间包中钢水温度:T = TL +T中过TL:钢水液相线温度T中过:中间包中钢水过热度到达连铸平台的钢水温度应符合连铸浇铸的规定。
连铸中间包钢水温度应符合钢种规定要求。
对于新砌钢包及连铸五个流浇注的情况,到达连铸的钢包钢水温度可提高5-10℃。
浇注过程中每减少一个流,到达连铸的钢包钢水温度可提高5℃。
新包、挖补包不能作为第一炉。
连铸工艺技术操作规程

连铸操作规程一、主控操作1生产前准备1.1水准备1.1.1机长确认具备送水条件后,通知水泵房送各路生产用水。
1.1.2与中间包班长配合,检查四个流次的足辊段、活动段、固定段水压及流量情况,如有异常,及时向机长汇报。
1.2上引锭1.2.1上引锭前与机长联系,切割班长确认辊道上及拉矫辊内有无障碍物,中间包班长确认二冷室引锭通道是否安全无阻。
1.2.2与液压工联系,确认液压站有无异常情况,开启大包及中包液压、主液压、振动台液压,出坯区液压。
泵开启后,如发现问题及时与相关人员联系解决。
1.2.3与切割工联系确认拉矫辊运转是否正常。
1.2.4确认自动上引锭条件是否达到,如没达到,确定哪项条件不满足,应通知相关人员及时处理。
1.2.5以上条件具备时,启动各流自动上引锭。
1.2.6上引锭时在电脑屏幕及监视器中监视上引锭情况,如发现哪流引锭中途停止或其他异常情况,应立即停止该流,并向机长汇报,检查故障与相关人员联系处理。
处理后,如要继续上引锭,则手动将引锭送上;如要自动再上该流引锭,则需手动将引锭退回原位并收集,待自动上引锭条件满足后,启动自动将引锭送上。
1.2.7浇钢工将引锭杆定位于结晶器后主控工在人机界面进行引锭杆强制在原位操作。
1.3生产前检查及准备工作1.3.1确认结晶器水流量、压力是否在正常范围内,如有异常及时向机长汇报与水泵房联系。
1.3.2确认事故水塔水位是否正常,正常水位不低于4m;结晶器总管压力是否正常,水量调节阀开口度是否正常。
1.3.3检查设备水压力及流量是否达到,正常压力应大于0.35MPa,流量大于450L/min。
1.3.4检查冲渣水压力及水泵状况。
1.3.5检查压缩空气及切割气体是否达到要求。
1.3.6确认电搅水系统水位,启动电磁搅拌水泵,检查压力、流量,确认电磁搅拌无故障。
1.3.7开浇前15分钟打开结晶器水逆止阀及设备水逆止阀。
1.3.8检查浇注许可条件是否达到,浇注前出坯区是否是远程控制。
连铸机主要工艺概况(五流机操作规程)
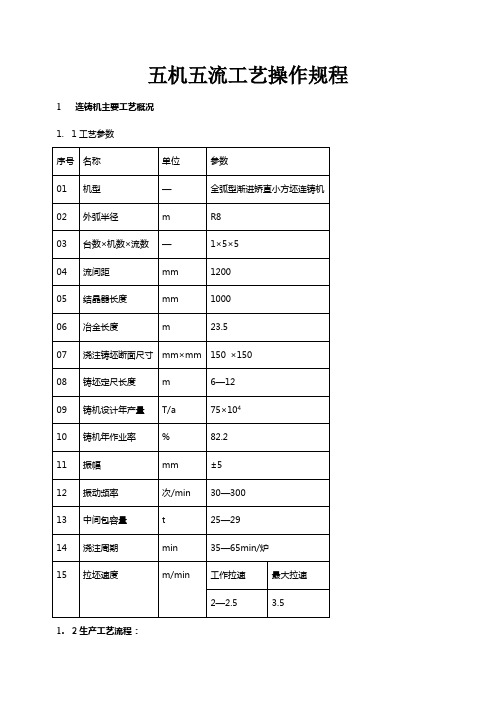
五机五流工艺操作规程1 连铸机主要工艺概况1.1工艺参数1.2生产工艺流程:1.3主浇钢种1.3. 1 低合金钢1.3. 2 优质碳素结构钢2 大包浇钢工操作规程2.1浇铸前的准备2.1.1检查大包平台上仪表控制台有无故障显示,若有应及时通知有关人员检修。
2.1.2按下“试验灯光”钮,检查台面上全部信号灯,确保正常,若有异常应及时通知电工检修。
2.1.3检查钢包回转台的空载运行情况,两台驱动装置的正、反转和点动情况,及备用气动传动装置的运行情况。
2.1.4检查水口液压站压力、油位指示是否正常,试运行油缸启闭情况,液压推杆是否到位。
2.1.5检查大包回转台升降是否到位。
2.1.6指挥行车将事故钢包放置于事故平台上。
2.1.7准备好大包浇铸所需的工具:大包保护管、吹氧管、测温枪、取样器、冷料、堵水球。
2.1.8准备好大包浇铸所需的的原材料:铬质引流砂、中间包覆盖剂、测温偶头及纸管。
2.1.9上述工作完成后,将回转台的一臂转到接收钢水位置做接收钢水的准备,接收钢水时,应将摆臂升起。
2.2浇注操作2.2.1钢包放上回转臂前,必须在记录表上认真填写钢水到回转台的时间,并从传票上了解该炉钢种及小平台温度,钢水温度应严格按下表执行,当钢水温度低于要求的下限时,应直接回炉。
备注:1、其它钢种或新开发钢种,其温度制度执行有关的补充规定;2、直上钢水连浇炉温度按上表执行。
2.2.2当装满钢水的大包座落在回转臂后,操作主令控制手柄,将其转道“浇铸”位置,控制升降开关按钮将装满钢水的大包水口距离中间包底部冲击区1000—1200mm。
2.2.3大包开浇前,清净水口周围杂物,保证水口畅通用堵锥堵住水口后向每流水口部位加满铬质引流砂。
2.2.4大包开浇要迅速到位,钢水不能自流时立即烧氧引流。
2.2.5当中间包钢水液面高达200mm—300mm时,加入4袋中间包钢水覆盖剂(20kg/包)将液面覆盖起来。
2.2.6当中间包钢水液面高达400mm时,关小水口并通知中间包浇钢工开浇,开浇后迅速将中间包液位控制在700mm—800mm之间,为保证正常浇注,应来回调节水口开度控制中间包钢液面在700mm—800mm之间,直至大包钢水浇完。
- 1、下载文档前请自行甄别文档内容的完整性,平台不提供额外的编辑、内容补充、找答案等附加服务。
- 2、"仅部分预览"的文档,不可在线预览部分如存在完整性等问题,可反馈申请退款(可完整预览的文档不适用该条件!)。
- 3、如文档侵犯您的权益,请联系客服反馈,我们会尽快为您处理(人工客服工作时间:9:00-18:30)。
路漫漫其修远兮, 吾将上下而求索
3.连铸机的机型
立式连铸机: 钢水从结晶器内开始
凝固到铸坯完全凝固后切 成定尺,铸坯始终沿直线 运动,中间包、结晶器、 导辊、拉坯辊和切割机都 沿直线布置。 优 点:
电 磁 搅 拌 设 备
二 冷 段
拉
引
锭
矫
装
机
置
切 割 机
路漫漫其修远兮, 吾将上下而求索
1.钢包及回转台
钢包又称盛钢桶、 钢水包、大包等; 它是用于盛装、运 勇载于开钢始液,才并能找进到成行浇注 功的的路设备,也是钢液 炉外精炼的容器。
路漫漫其修远兮, 吾将上下而求索
➢作 用: 存储钢水,并将钢水运输至连铸机,同时 底部设吹Ar管起精炼作用;
8.停 车
路漫漫其修远兮, 吾将上下而求索
大包和中包滑动 水口关闭。当中包水口 关闭时向结晶器内加冷
勇于开始,才能找到成
功钢的路,以加速尾坯凝固。 降低拉速到0.5m/min, 同时二冷强度下降。待 尾坯凝固后,将其拉出 。
四、连铸设备
中
钢
间
包
包
及
及
回
中
转
间
台
包
车
等 离 子 加 热 装 置
结 晶 器 及 振 动 台
➢ 钢水温度过低的危害:①容易发生水口堵塞,浇 铸中断;②连铸表面容易产生结疱、夹渣、裂纹 等缺陷; ③非金属夹杂不易上浮,影响铸坯内在 质量。
路漫漫其修远兮, 吾将上下而求索
钢水在钢包中的温度控制
根据冶炼钢种严格控制出钢温度,使其在较窄的范围 内变化;其次,要最大限度地减少从出钢、钢包中 、 钢包运送途中及进入中间包的整个过程中的温降 。
从中间包开浇到拉矫机启动 时间为10-15s,开始拉坯速度为 0.5m/min。2min后达正常速度, 之后根据钢水过热度调整拉速, 启动拉矫机同时结晶器振动,二 冷喷水;
勇于加开保始护,才渣能:找到成
功的路 中间包开浇后加保护渣, 勤加少加,均匀覆盖;0.50.6kg/t;
拉 坯:
结晶器液面波动80-120mm±3mm;
铸坯切割长度 由PLC系统自动调节 ,当满足用户和下 勇功于的开路部始,工才序能找要到成求时,夹 钳夹住铸坯并与之 同步,切割枪开始 工作,切割完毕, 夹钳松开,切割机 复位。
6.钢包更换
路漫漫其修远兮, 吾将上下而求索
根据回转台上重 力传感器指示的钢水状 态,在浇注近结束时控 勇于制开滑始,动才水能找口到成开度,根据 功的大路包下渣检测装置测定 下渣情况,关闭水口。 大包提起,脱长水口, 回转180°,将待浇钢 包旋至中间包上方,实 现多炉连浇。
介于大包和结晶器之 间,接受来自大包的钢水 ,并向结晶器分流,起到 勇于减开压始、,才稳能流找、到成除渣、储钢 功的分路流、均匀温度和成分的 作用;
结 构:
呈“T”型,由包体、 包盖组成,底部设有滑动 水口机构,浸入式水口及 夹持装置,并设溢流槽。
➢中间包的容量是钢包容量的20%~40%。 在通常浇注条件下,钢液在中间包内应停 留8~10min,才能起到夹杂物上浮和稳定 注流的作用
➢简化了工序,缩短了流程
省去了脱模、整模、钢锭均热、初轧开坯等工 序。由此可节省基建投资费用约40%,减少占地 面积约30%,劳动力节省约70%。
➢提高了金属收得率
采用模铸工艺,从钢水到钢坯,金属收得率为 84%-88%,而连铸工艺则为95-96%,金属收得 率提高10-14%。
路漫漫其修远兮, 吾将上下而求索
路漫漫其修远兮, 吾将上下而求索
连铸的发展史
1、现代炼钢技术的发展(连铸技术的作用) (1) 1947年-1974年: 技术特点:转炉、高炉的大型化;以模铸-初轧
为核心,生产外延扩大。 (2) 1974年-1989年: 技术特点:全连铸工艺,以连铸机为核心。 (3) 1989年-现在: 技术特点:连铸-连轧工艺,以薄板坯,连铸-
2.开 浇
路漫漫其修远兮, 吾将上下而求索
精炼处理后钢水→ 连铸回转台→加保温盖 →转至浇注工位→中间 勇功于的包开路始小,车才能至找浇到成注工位→中 间包基座下降→水口与 结晶器对中→开大包水 口→中间包加保温剂→ 开中间包滑动水口→实 现开浇
3.启车拉矫
路漫漫其修远兮, 吾将上下而求索
启 车:
容汉斯提出连铸振动系统,1943年建成第一台实
验性连铸机。80年代后世界各国连铸技术迅速发
展。
目前国外对于中低碳钢、普通高碳钢、沸腾
钢代用钢、低合金钢、弹簧钢、轴承钢等已实现
连铸。
路漫漫其修远兮, 吾将上下而求索
2. 连铸工艺流程
打开钢包底部的滑动水口 —钢水从钢包流入 中间包—当中间包里的钢液面达到一定高度时打 开中间包底部的滑动水口—钢水流入到强制水冷 的结晶器—当结晶器内钢液面达到 一定高度时并 且钢液四周已凝固成具有一定厚度的坯壳—启动 拉矫机咬住引锭杆向下移动—因钢水与引锭杆黏 结一起故钢水被拉出结晶器—钢坯进入二冷区— 因坯壳很薄内部是钢液故喷水冷却—完全凝固的 钢坯经矫直切成所需长度。
路漫漫其修远兮, 吾将上下而求索
水平连铸机:
其主要设备结晶器 、二冷装置、拉矫机和 切割设备等均不止在水 平线上,水平连铸机的 结晶器和中间包是紧密 相连的,在中间包水口 和结晶器连接处安装有 分离环。此外,拉坯时 结晶器不振动,而是拉 坯机带着铸坯作“拉-反 推-停”不同组合的周期 运动。
路漫漫其修远兮, 吾将上下而求索
路漫漫其修远兮, 吾将上下而求索
亨利·贝塞麦
连续浇铸最早由亨利·贝塞麦提出,并于1846 年开始试验,但是直到1937年才实现了铜 合金的连铸,1950年制出钢液的连铸机。
连铸技术在钢铁生产中的应用是钢铁冶金工 业的一次技术革命,它不仅大大提高了生 产率,减少了材料消耗,提高了能源效率 ,并且提高了材料的质量。此后还出现了 连铸连轧O.C.C技术。
连铸工艺与操作
路漫漫其修远兮, 吾将上下而求索
2020年4月8日星期三
主要内容
一、概 二、生产模拟 三、生产工艺 四、连铸设备 五、工艺参数
路漫漫其修远兮, 吾将上下而求索
一、概 述 1.连铸的发展概况 2.连铸机的特点 3.连铸机的机型
路漫漫其修远兮, 吾将上下而求索
1.连铸的发展概况
连续铸钢(连铸)是将钢水通过连铸机直接铸成钢坯 ,从而取代模铸和初轧开坯的一种钢铁生产先进 工艺。世界各国都以连铸比(连铸坯产量占钢总产 量比例)的高低来衡量钢铁工业生产结构优化的程 度和技术水平的高低。连铸的好处在于节能和提 高金属收得率。
四周冷却均匀,不易 产生内部和表面裂纹,有 利于夹杂物上浮; 缺 点:
设备高度大,投资费 用高,铸坯断面和定尺长 度及拉速受到限制。
路漫漫其修远兮, 吾将上下而求索
立弯式连铸机: 可适应较长定尺的
要求(2m),钢水从 结晶器开始凝固,完 全凝固后进入弯曲段 ,在水平方向出坯, 铸机的中间包、结晶 器、导辊、引锭杆沿 垂线布置,拉矫机、 切割机沿水平布置。 缺 点:
连轧为代 表,钢厂向紧凑化发展。
路漫漫其修远兮, 吾将上下而求索
2、 21世纪钢铁工业发展趋势
(1) 产品更加纯洁化 (2) 生产工艺更加高效低耗 (3) 生产过程对环境更加友好
路漫漫其修远兮, 吾将上下而求索
•
连铸液体金属是19世纪提出的。最初只能用
于浇铸低熔点的有色金属。1933年现代连铸之父
矫 直:
铸坯在高温下通过拉矫机 连续矫直,使弧形坯变成直线铸 坯.
4.脱引锭杆
路漫漫其修远兮, 吾将上下而求索
引锭杆头部凹 槽与注入结晶器钢 水接触凝固成凸台
勇于开始,才能找到成
功的路 ,将铸坯与引锭杆 挂接一起,拉出拉 矫机后,将引锭头 抬起,实现铸坯与 引锭杆分离。
5.切 割
路漫漫其修远兮, 吾将上下而求索
7.中间包更换
路漫漫其修远兮, 吾将上下而求索
根据包衬和浸入式水 口寿命决定,一般10-15次 。
更换过程:
勇于开始,大才包能找长到水成口关闭后, 功的提路升并脱长水口,至中间
包液面高度200mm时,关中 包滑动水口并停拉矫,中 包升起至待机位,另一预 热好的中包开到浇钢位, 机座下降,对中水口,按 开浇操作进行。
➢结构与功能: 由本体、滑动水口连接板、透气砖、倾翻 吊环组成;
➢滑动水口: 由上、下滑板、弹性压紧装置、开关驱动 机构及座砖组成。
路漫漫其修远兮, 吾将上下而求索
图 滑动水口控制原理图 (a)全开; (b)半开;(c)全闭 1一上水口; 2一上滑板;3一下滑板;
4一下水口
钢包通过滑动水口开启、关闭来调节钢液注流。
路漫漫其修远兮, 吾将上下而求索
连续铸钢
路漫漫其修远兮, 吾将上下而求索
1.连铸的发展概况
• 钢液凝固成型有两种方法: 模注—获得钢锭 连铸—获得钢坯
一般钢材的生产工艺是: • 若采用模注
钢锭—轧制或锻压—钢坯—轧制—钢材 若采用连铸 钢坯—轧制—钢材
路漫漫其修远兮, 吾将上下而求索
连铸的特点
全弧型连铸机:
铸坯的运动轨迹是一条弧 线.结晶器,二冷段全为弧型,拉 矫机、切割机和出坯系统布置 在水平线上.
路漫漫其修远兮, 吾将上下而求索
椭圆连铸机:
又称带有多点矫直 的弧型连铸机,又称超 低头连铸机。它分段依 次改变圆弧部分的曲率 半径,使结晶器和二冷 段夹棍布置在1/4椭圆 上。这种结构的机型除 了弧形区是采用多半径 外,其它基本特点与弧 型连铸机相同。该机型 与纯净钢水的生产技术 相结合,可生产无缺陷 铸坯。