塑料挤出机机头结构设计
塑料成型工艺及模具设计--挤出成型及机头设计

塑料成型工艺及模具设计--挤出成型及机头设计塑料挤出成型是一种常用的塑料加工方法,通过将塑料材料加热熔融,然后通过挤出机器将熔融的塑料挤出成型,最后通过冷却固化形成所需的塑料制品。
在挤出成型过程中,机头是起着关键作用的部件,它的设计直接影响着成型品的质量。
下面本文将主要介绍塑料挤出成型工艺及机头的设计。
塑料挤出成型工艺主要包括材料的预处理、熔融、挤出、冷却固化以及后续的修整工序等。
首先是材料的预处理,对于塑料颗粒来说,需要将其进行干燥处理以去除其中的水分,从而避免在挤出过程中出现气泡的问题。
然后将塑料颗粒放入挤出机中,通过传热系统将其加热到熔融状态。
接下来是挤出过程,将熔融的塑料提供给机头,然后通过机头的尺寸和形状来决定挤出产品的形状。
挤出成型的最后一步是冷却固化,通过冷却水或者风扇等方式将挤出的塑料制品迅速冷却,使其固化定型。
机头的设计是塑料挤出成型中的关键环节,它决定了挤出产品的形状和质量。
在机头的设计中应注意的几个要点如下:首先是机头的出料口结构,出料口的尺寸和形状直接影响到产品的尺寸和外观。
出料口的设计应根据产品的形状和尺寸来确定,通常采用方形、圆形或者其他一些特殊形状。
出料口的尺寸要与挤出机的产量匹配,保证挤出的塑料在出料口出现均匀流动,从而避免产生流痕或者厚薄不均的现象。
其次是机头的冷却方式,机头的冷却方式直接影响产品的冷却效果和固化速度。
常用的机头冷却方式有水冷却和风冷却两种。
水冷却能够快速降低塑料温度,适用于大批量生产;而风冷却则适用于小批量生产,具有灵活性和节约能源的优势。
此外,机头的加热和保温系统也很重要,通过控制机头的温度来保证塑料的熔融状态和流动性。
机头的加热系统一般采用电加热或者油加热,保温方法可采用加热套或者外加热器等。
最后,机头的结构与塑料材料的特性密切相关。
不同的塑料材料具有不同的流动性和熔融温度,需要选择相应的机头结构来适应。
同时,机头的结构应该尽量简洁,减少塑料的滞留,避免塑料材料的分解和变质。
塑料成型工艺及模具设计--挤出成型及机头设计
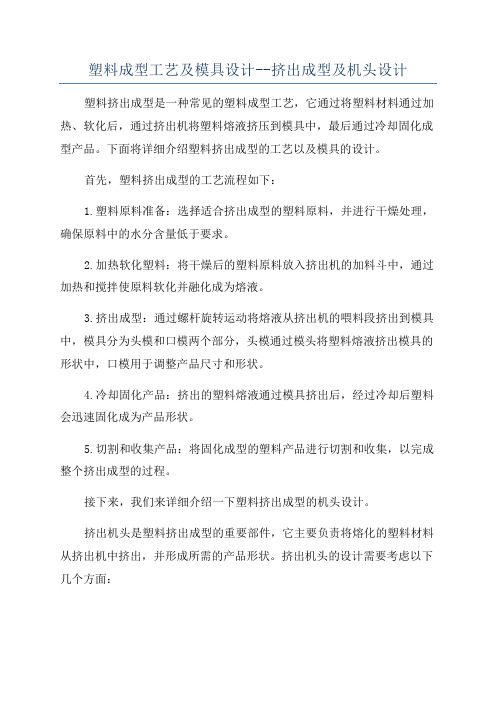
塑料成型工艺及模具设计--挤出成型及机头设计塑料挤出成型是一种常见的塑料成型工艺,它通过将塑料材料通过加热、软化后,通过挤出机将塑料熔液挤压到模具中,最后通过冷却固化成型产品。
下面将详细介绍塑料挤出成型的工艺以及模具的设计。
首先,塑料挤出成型的工艺流程如下:1.塑料原料准备:选择适合挤出成型的塑料原料,并进行干燥处理,确保原料中的水分含量低于要求。
2.加热软化塑料:将干燥后的塑料原料放入挤出机的加料斗中,通过加热和搅拌使原料软化并融化成为熔液。
3.挤出成型:通过螺杆旋转运动将熔液从挤出机的喂料段挤出到模具中,模具分为头模和口模两个部分,头模通过模头将塑料熔液挤出模具的形状中,口模用于调整产品尺寸和形状。
4.冷却固化产品:挤出的塑料熔液通过模具挤出后,经过冷却后塑料会迅速固化成为产品形状。
5.切割和收集产品:将固化成型的塑料产品进行切割和收集,以完成整个挤出成型的过程。
接下来,我们来详细介绍一下塑料挤出成型的机头设计。
挤出机头是塑料挤出成型的重要部件,它主要负责将熔化的塑料材料从挤出机中挤出,并形成所需的产品形状。
挤出机头的设计需要考虑以下几个方面:1.挤出机头的结构:挤出机头通常由挤出机芯、流道和模头组成。
挤出机芯用于将熔化的塑料材料从挤出机中挤出,流道负责将熔液引导到模头当中,模头则通过调整挤出物料的流量和形状来控制最终产品的形状。
2.流道设计:流道的设计需要考虑熔液的流动特性,合理设计流道的尺寸和形状,以确保熔液在流道中流动顺畅,不发生堵塞和死角。
同时,流道的设计还需要考虑产品的外形和尺寸要求,以保证挤出的塑料产品形状准确。
3.模头设计:模头是挤出成型中最重要的部分,它通过模头的形状和结构来决定产品的外形。
模头的设计需要考虑产品的尺寸、形状以及挤出速度等因素,合理设计模头的流道和出口形状,以保证产品的成型质量。
4.温度控制:塑料挤出成型中,温度对产品的成型质量和表面光洁度有很大影响,因此挤出机头的设计需要考虑温度的控制。
机头常用结构形式
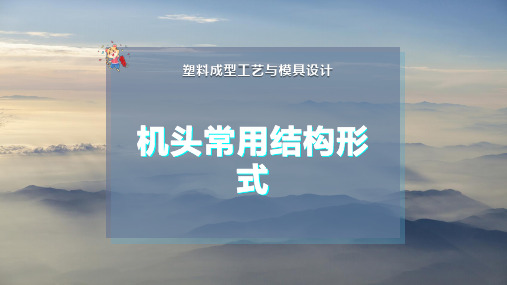
优点: 结构简单、容易制造; 缺点: 塑料熔体经过分流器和分流器支架时
形成的熔接痕不易消除、长度较大、 整体结构笨重;
2.
直角式挤管机头适用于挤出成型聚乙 烯、聚丙烯等塑料管材,以及对管材尺寸 要求较高的场合。
其优点为:生产率高; 定径精度高; 料流稳定均匀; 成型质量也较高; 熔体的流动阻力较小;
其出管方向与螺杆轴线一致,挤出的 管材没有分流痕迹,强度较高,尤其适用 于生产口径较大的聚烯烃类塑料管材。
特点:体积小、结构紧凑、料流稳定且流
塑料成型工艺与模具设计
缺点为:
3. 旁侧式挤管机头与直角式相似,如
图4.7所示,其结构更为复杂,熔体流 测 温孔; 2 口模; 3 型芯; 4、7 外加热圈; 5 调节螺钉; 6 机头体; 9 连接体; 11 内加热圈
4. 微孔流道挤管机头又称毛细管机头,如
图4.8所示。
图4.8微孔流道机头
塑料成型工艺与模具设计
机头常用结构形式
挤出成型管材时,常用的机头结构有: 1)直通式 2)直角式 3)旁侧式 4)微孔流道管机头
SJ-单螺杆塑料挤出机 PE PP-R管材生产线参数
1. 直通式挤管机头如图4.4所示,
图4.4 管材挤出 成型机头
1 管材;2 定径 套; 3 口模;4 芯棒;5 调节 螺钉;6 分流 器;7 分流器 支架;8 机头 体;9 过滤板; 10、11 加热器
挤出机头

系数n的取值表
硬聚 软聚 聚酰 聚乙 聚丙 烯 烯 氯乙 氯乙 胺 烯 烯 (PA) (PE) (PP) PA) PE) PP) (HPV (SPV C) C) 系数n 18- 15- 13- 14- 14- 系数n 18- 15- 13- 14- 14- 33 25 22 22 22 塑料 品种
压缩比
• 压缩比 E 所谓管材的压缩比是机头和多孔 板相接处最大进料截面积与口模和芯棒的 环隙截面积之比,反映出塑料熔体的压实 程度。 • 低粘度塑料 E=4-10 • 高粘度塑料 E=2.5-6.0
分流器和分流器支架的结构图
R
α
A A-A放 大 a a
A
压缩空气
分流器和过滤板的相对位置
• 1-分流器 3-过滤板 2-螺杆
• • • • •
补偿系数K
• 塑料种类 定径套定管材内径 定径套定 管材外径 • 聚氯乙烯(PVC) 0.95-1.05 • 聚乙烯(PE) 1.05-1.10 • 聚烯烃 1.20-1.30 0.90-1.05
定型段长度L1
• 按管材外径计算: • L1=(0.5—3)D • 通常当管子直径较大时定型长度取小值,因为 此时管子的被定型面积较大,阻力较大,反之就 取大值。同时考虑到塑料的性质,一般挤软管取 大值,挤硬管取小值。 • 按管材壁厚计算: • L1=nt • 式中 t一管材壁厚(mm); • n一 系数
挤出机头的设计
——2012
挤出机头设计原则
• 1.内腔呈流线型 • 为了使塑料熔体能沿着机头中的流道 均匀平稳地流动而顺利挤出,机头的内腔 应呈光滑的流线型,表面粗糙度应小于1.6 -3.2m. 3.2m. • 2.足够的压缩比 • 为使制品密实和消除因分流器支架造 成的结合缝,根据制品和塑料种类不同, 应设计足够的压缩比。 •
塑料挤出机机械结构设计

哈尔滨石油学院毕业设计(论文)任务书本次毕业设计主要工作内容是完成塑料挤出机的机械结构设计。
通过本次设计,建立正确的产品设计思想、掌握产品设计的流程、各个设计阶段解决问题的方法和手段。
为毕业后实际设计产品奠定良好基础。
基本要求1.用多种方法查找相关文献资料。
2.参照以有的设备数据拟定多种设计方案,比较设计方案,选择最佳方案进行设计。
3.利用CAD完成装配图和零件图,。
4.撰写毕业设计论文。
主要参考资料1 刘立春. 塑料机械设计.北京.机械工业出版社,1993.22 于德水. 塑料加工机械.北京.机械工业出版社,2001.123 陈露.AutoCAD2006基础及应用教程.电子工业出版社,2006.8摘要此次设计的题目是SJ-65塑料挤出机机械结构设计。
挤出成型是塑料成型加工的重要成型方法之一,而挤出成型是在挤出机上进行的,所以挤出机是塑料成型加工机械的主要设备。
用挤出机生产的产品广泛地应用于人们生活以及农业、建筑业、石油化工、机械制造、国防等工业部门。
挤出机主要用不高于把聚合物主原料与所需添加的辅助原料混合、混炼塑化熔融,最终加工成具有各种截面形状和几何尺寸的挤出类塑料制品。
其主要的特点是:生产过程连续;生产效率高;应用范围广;投资小,收效快。
[1]挤出机主要由挤压系统、加料系统、传动系统和加热冷却系统组成。
本次设计就是围绕这几部分进行设计的。
挤压系统主要由螺杆和机筒组成,是挤出机的关键部分。
加工的塑料是高分子聚合物。
综合各个方面的因素考虑,螺杆的结构形式选定为等距变深型螺杆。
机筒结构是选用的衬套式机筒,即在整体式机筒内加一衬套,衬套磨损后可以拆出加以更换,这样可以节省贵金属材料,很经济。
本次设计就是基于在结构合理、易于加工和维修等条件的要求下,进行挤出机的设计。
关键词:挤出机;传动系统;加热冷却AbstractThis design topic is SJ-65 plastic extruder mechanical structure design. Extrusion molding is plastic forming the important method of forming process, and extrusion molding in extrusion machine is the extruder, so is the plastic molding processing machinery major equipment. Extruder production with the products widely used in people life and agriculture, construction, petroleum chemical industry, machinery manufacturing, defense industries as well.Extruder is not higher than the polymerization with raw materials and add the owner needed assistance raw material mixing, mixing rubber plasticizing melting, eventually processed into has all kinds of cross-section shape and geometry size of plastic extrusion products. Its main characteristic is: production continuous; High production efficiency; Application range; Small investment, fast convergence.Extrusion machine mainly by extrusion system, charging system and transmission system and heating, cooling systems. This design is a few parts around this design. Extrusion system mainly by the screw and barrel composition, is a key part of the extruder. Processing of plastic is the high polymer. Comprehensive all aspects of the factors, screw structure of the selected for isometric darker type screw. Machine tube structure is to choose the bushing type of barrel, that is, in the integral within a barrel and bushing, liner wear can be replaced after pulled out, this can save precious metal materials, very economy.The design is based on the reasonable structure, easy to processing and maintenance of the conditions of the request, for the design of the extruder.Keywords:plastic extrusion ; transmission system; heating and cooling.目录第1章绪论 (1)1.1课题背景 (1)1.2课题研究意义 (2)1.3国内外综述 (2)1.4研究内容 (2)第2章挤压系统设计 (4)2.1螺杆设计 (4)2.2机筒设计 (9)2.3螺杆和机筒的材料选择 (10)2.4螺杆和机筒的配合要求 (10)2.5分流板设计 (11)2.6本章小结 (11)第3章挤出机传动系统设计 (12)3.1挤出机驱动功率的确定 (12)3.2挤出机转速的调节范围 (12)3.3传动系统的组成及其设计 (12)3.4挤出机螺杆轴承部分的结构及其布置形式 (16)3.5挤出机螺杆轴承和齿轮的UG造型 (17)3.6本章小结 (21)结论 (22)致谢 (23)参考文献 (24)附录 (25)第1章绪论1.1课题背景在我国塑料加工业中,几乎1/3-1/2的塑料制品是通过挤出成型来完成。
第3章-热塑性塑料挤出成型机头

二 分类
1. 按用途:挤管机头;吹膜机头;板材机头。 2. 按制品出口方向:直向机头;横向机头。
横向机头内料流方向与挤出螺杆轴成某一角度。 3. 按机头内压力:低压机头(≤40kg/cm2);中压机
头(≤100kg/cm2);高压机头(>100kg/cm2)。
三 设计原则
1. 内腔呈流线型:不能急剧地扩大或缩小,更不能有死角和停 滞区,表面粗糙度Ra<0.4µm。
(10)
对异形孔,一般可视为等厚宽扁孔,主要是怎样确定其有效宽度。
对异形孔,如果各段厚度不相同,则应对各段分别进行计算。
在机头结构上,将不同厚度各段在模具内用薄的分隔板隔开,在出模之间
再汇合熔合成一体。
对各段厚度不同的情况,有两种设计方法:
① 各段剪应力相等来决定口模尺寸。
② 各段流出速度相等来决定口模尺寸。
各段剪应力相等,制品表面粗糙度一致,但出模后各段存在不同的牵伸比,
因而靠成内应力不一致,易产生翘曲变形。
各段流出速度相等,制品表面粗糙度不一致。
两种方法都要求,各段厚度不能相差太大。
3 二维流动的讨论
异形材中还有一类其断面为各种形状的实心异形材,常见的有三角形、矩
形、椭圆形等,这些属于二维流动。
对于二维流动情况,仅能对牛顿流体求得压差与流率关系的准确解,对非
对于非牛顿流体来说,为减小计算误差,式中粘度η应带入该剪切速率和
挤出温度下的表现粘度ηn。
对于某些机头的过渡部分可简化为园锥形管或宽度远大于高度的锥形槽。
对这种锥形流道,横断面上的流速变化可用一个坐标表示,沿流动方向流 速变化用另一坐标表示,因此,仍属二维流动。 处理锥形通道的压差与流率关系最简单的办法是将长的锥形通道分成数段 较短的通道,将其中每段作等直径管处理,其横向尺寸等于该段的最小直 径,再用(5)式计算,结果稍有些保守。 也可用下式计算: Q=π/4η(3τgα/2n)m(1/r23/n-1/r13/n) -m×△Pm 其中,α---斜角,r1、r2---大端、小端半径。 对牛顿液体(n=1),有 Q=3π/8µτgα×1/(1/r23-h/r13)×△P, 其中µ---牛顿粘度。 对锥形扁槽 Q=2w/3η(2τgβ/n)m(1/h22/n- 1/h12/n)-m×△Pm 其中,β---斜角,h1、h2---大端、小端厚度之半。 如为牛顿液体时,则Q=4wτgβ/3µ(1/(1/h22-1/h12)) △P
塑料挤出模具设计
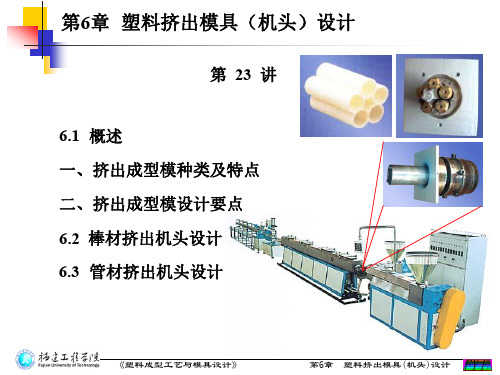
《塑料成型工艺与模具设计》
第6章 塑料挤出模具(机头)设计
一、管材挤出机头结构设计
(1)直管式机头 结构:由扩张分配段、压缩段、成型段组成; 适用于PVC、PA、PC、PE、PP等薄壁小口径管材挤出。
口模间隙 调节螺钉
《塑料成型工艺与模具设计》
第6章 塑料挤出模具(机头)设计
(2)直角式挤管机头
二、定径套设计
内压定径套内径:定径套直径应稍大于口模内径;100mm 以下管材定径套内径比口模大0.5~0.8mm;100~300mm的管 材定径套内径比口模约大1mm。
真空外径定径套:定径套内壁开有许多抽真空小孔或窄缝 (孔径或缝宽0.8mm,孔间距约10mm),使管材紧贴于定 径内壁,同时冷却定型。
棒材种类:PE、PP、 PC、PA、PMMA、 PTFE、ABS、POM、 PVC……
《塑料成型工艺与模具设计》
第6章 塑料挤出模具(机头)设计
一、棒材挤出机头结构设计
棒材机头种类: • 带分流梭的机头 • 不带分流梭的机头
聚四氟乙 烯绝热垫
过滤板和 过滤网
《塑料成型工艺与模具设计》
第6章 塑料挤出模具(机头)设计
特点:挤出管材轴线与挤出机 螺杆轴线成直角,便于进气、 芯模的加热,以及芯线、复合 管的导入包覆。
适用于内定径的PE、PP、PA 等塑料管挤出,大小口径管材 均适用。
熔接痕在进料口对面,设计时 要尽量减少管材沿圆周各点流 动距离不等和压力不平衡。
《塑料成型工艺与模具设计》
第6章 塑料挤出模具(机头)设计
《塑料成型工艺与模具设计》
第6章 塑料挤出模具(机头)设计
(3)芯棒设计
芯棒由收缩段和平直段组成,与分流锥之间用螺纹连接; 平直段长度等于口模长度。
塑料管材挤出模具设计
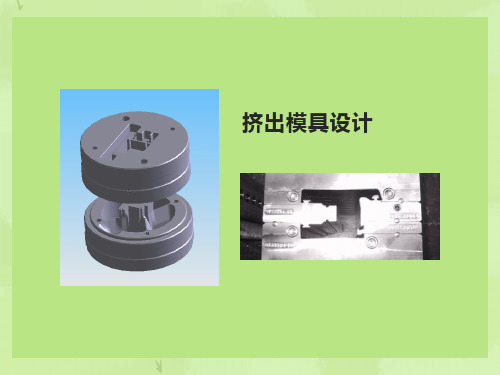
(直径<80mm)硬管挤出模具
下图所示是成型管材直径小于80mm用成型模具结构。采用内压法定径,定径套外腔是带有能通冷却循环水的环形套,冷却管坯;生产时,通过分流锥支架肋上的小孔,把压缩空气输入管坯内,管坯前端装有气堵,防止管内压缩空气逸出。分流锥、支架和芯轴也是用螺纹连接成一体,依靠分流锥支架外圆与模具体内圆紧密配合定位。保证分流锥、支架和芯轴与模具体装配后的同心精度。
PP
1.0.~1.2
HDPE
1.1~1.2
LDPE
1.2~1.5
口模定型段长度L1,与塑料性质、管材的形状、壁厚、直径大小及牵引速度有关。其值可按管材外径或管材壁厚来确定:
单击此处添加小标题
1
口模结构尺寸从图中可 以看到,主要是平直段 长度、内径和压缩角。 平直段(也叫定型段) 长度L1=(0.5~3)D 内径 d1= D/k 式中D —管材外径( mm) k—系数,k=1. 01~1.06。 压缩角α取14 °~50 °之间。
(4)结构紧凑
(5)选材要合理
02
01
03
04
05
常见的挤出机头有:
2典型挤出机头及设计
管材挤出机头、
异型材挤出机头
电线电缆包覆机头
1.管材挤出机头的结构形式
常见的管材挤出机头结构形式有以下三种: 直管式机头 图示为直管式机头。其结构 简单,具有分流器支架,芯模加热困难,定型长度较长:适用于PVC、PA、PC、PE、PP等塑 料的薄壁小口径的管材挤出。是挤出成型塑料 管材应用最广泛的一种模具结构
口模内径不等于塑料管材外
塑料挤出机机械结构设计

哈尔滨石油学院毕业设计(论文)任务书本次毕业设计主要工作内容是完成塑料挤出机的机械结构设计。
通过本次设计,建立正确的产品设计思想、掌握产品设计的流程、各个设计阶段解决问题的方法和手段。
为毕业后实际设计产品奠定良好基础。
基本要求1.用多种方法查找相关文献资料。
2.参照以有的设备数据拟定多种设计方案,比较设计方案,选择最佳方案进行设计。
3.利用CAD完成装配图和零件图,。
4.撰写毕业设计论文。
主要参考资料1 刘立春. 塑料机械设计.北京.机械工业出版社,1993.22 于德水. 塑料加工机械.北京.机械工业出版社,2001.123 陈露.AutoCAD2006基础及应用教程.电子工业出版社,2006.8摘要此次设计的题目是SJ-65塑料挤出机机械结构设计。
挤出成型是塑料成型加工的重要成型方法之一,而挤出成型是在挤出机上进行的,所以挤出机是塑料成型加工机械的主要设备。
用挤出机生产的产品广泛地应用于人们生活以及农业、建筑业、石油化工、机械制造、国防等工业部门。
挤出机主要用不高于把聚合物主原料与所需添加的辅助原料混合、混炼塑化熔融,最终加工成具有各种截面形状和几何尺寸的挤出类塑料制品。
其主要的特点是:生产过程连续;生产效率高;应用范围广;投资小,收效快。
[1]挤出机主要由挤压系统、加料系统、传动系统和加热冷却系统组成。
本次设计就是围绕这几部分进行设计的。
挤压系统主要由螺杆和机筒组成,是挤出机的关键部分。
加工的塑料是高分子聚合物。
综合各个方面的因素考虑,螺杆的结构形式选定为等距变深型螺杆。
机筒结构是选用的衬套式机筒,即在整体式机筒内加一衬套,衬套磨损后可以拆出加以更换,这样可以节省贵金属材料,很经济。
本次设计就是基于在结构合理、易于加工和维修等条件的要求下,进行挤出机的设计。
关键词:挤出机;传动系统;加热冷却AbstractThis design topic is SJ-65 plastic extruder mechanical structure design. Extrusion molding is plastic forming the important method of forming process, and extrusion molding in extrusion machine is the extruder, so is the plastic molding processing machinery major equipment. Extruder production with the products widely used in people life and agriculture, construction, petroleum chemical industry, machinery manufacturing, defense industries as well.Extruder is not higher than the polymerization with raw materials and add the owner needed assistance raw material mixing, mixing rubber plasticizing melting, eventually processed into has all kinds of cross-section shape and geometry size of plastic extrusion products. Its main characteristic is: production continuous; High production efficiency; Application range; Small investment, fast convergence.Extrusion machine mainly by extrusion system, charging system and transmission system and heating, cooling systems. This design is a few parts around this design. Extrusion system mainly by the screw and barrel composition, is a key part of the extruder. Processing of plastic is the high polymer. Comprehensive all aspects of the factors, screw structure of the selected for isometric darker type screw. Machine tube structure is to choose the bushing type of barrel, that is, in the integral within a barrel and bushing, liner wear can be replaced after pulled out, this can save precious metal materials, very economy.The design is based on the reasonable structure, easy to processing and maintenance of the conditions of the request, for the design of the extruder.Keywords:plastic extrusion ; transmission system; heating and cooling.目录第1章绪论 (1)1.1课题背景 (1)1.2课题研究意义 (2)1.3国内外综述 (2)1.4研究内容 (2)第2章挤压系统设计 (4)2.1螺杆设计 (4)2.2机筒设计 (9)2.3螺杆和机筒的材料选择 (10)2.4螺杆和机筒的配合要求 (10)2.5分流板设计 (11)2.6本章小结 (11)第3章挤出机传动系统设计 (12)3.1挤出机驱动功率的确定 (12)3.2挤出机转速的调节范围 (12)3.3传动系统的组成及其设计 (12)3.4挤出机螺杆轴承部分的结构及其布置形式 (16)3.5挤出机螺杆轴承和齿轮的UG造型 (17)3.6本章小结 (21)结论 (22)致谢 (23)参考文献 (24)附录 (25)第1章绪论1.1课题背景在我国塑料加工业中,几乎1/3-1/2的塑料制品是通过挤出成型来完成。
挤出机头口模设计-PPT

3.模具的吊装
2.吊装方式 1)水平尺寸大于拉杆水平距离时,采用侧面滑
入(中小型模具) 2)模具厚度小于拉杆水平间距,将模具长方向
平行拉杆轴线方向,吊入后再旋转90度。 3)整体吊装: 4)分体吊装:起重设备受限时,可采用;先定
筛孔直径 1-2.5mm
熔体压力损失小、结构紧凑,易于装拆、清理 适于流动性好和热稳定性好的聚烯烃类大口径管 材。
螺旋供料机头
星形螺旋供料机头 环形螺旋供料机头
槽深变浅 芯模与外壁间距增大,保证流速一致,均匀 无芯棒支架,无熔接痕。
复式机头
三管机头
小型薄壁管
2.管材挤出机头参数确定
1.成型段长度 口模平直部分长度L1 作用:增加料流阻力,使管材更密实;使 料流稳定均匀,消除熔接痕 L1=(0.5-3.0)ds, L1=nt
成型段长度:棒材直径的4-15倍
无分流锥棒材机头
有强力冷却作 用的定型模
定型模
绝热垫
• 机头压缩角影响表面粗 糙度а=30-60°,出口扩
张角β =45°以下。
• 机头口模定型长度 L= (4-10)d,太短,会挤
出胀大明显,太长,阻
力过大卡滞
大家应该也有点累了,稍作休息
大家有疑问的,可以询问和交流 ‹#›
3)内定径 管材与定径棒直接接触,冷却定径 ,内应力均匀,保证尺寸精度和表面粗糙度
3.管材定型装置
(2)定径模尺寸
长度:管材尺寸、塑料性能、挤出速度、冷 却效果、热传导性能有关
过长—牵引阻力大;过短—冷却不 足易变形
RPVC ds300内,3-6ds, 35mm10ds; PO2-5ds 直径:外定径大0.8-1.2%;内定径大2-4% 锥度:出口直径略小于入口
挤出成型机头的设计要点
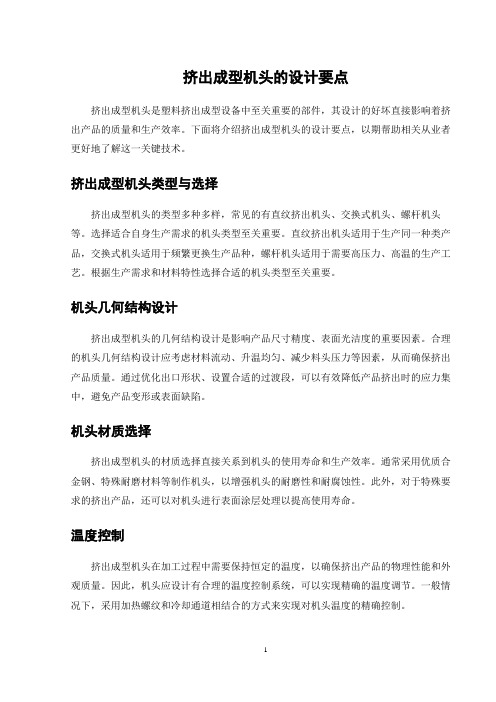
挤出成型机头的设计要点挤出成型机头是塑料挤出成型设备中至关重要的部件,其设计的好坏直接影响着挤出产品的质量和生产效率。
下面将介绍挤出成型机头的设计要点,以期帮助相关从业者更好地了解这一关键技术。
挤出成型机头类型与选择挤出成型机头的类型多种多样,常见的有直纹挤出机头、交换式机头、螺杆机头等。
选择适合自身生产需求的机头类型至关重要。
直纹挤出机头适用于生产同一种类产品,交换式机头适用于频繁更换生产品种,螺杆机头适用于需要高压力、高温的生产工艺。
根据生产需求和材料特性选择合适的机头类型至关重要。
机头几何结构设计挤出成型机头的几何结构设计是影响产品尺寸精度、表面光洁度的重要因素。
合理的机头几何结构设计应考虑材料流动、升温均匀、减少料头压力等因素,从而确保挤出产品质量。
通过优化出口形状、设置合适的过渡段,可以有效降低产品挤出时的应力集中,避免产品变形或表面缺陷。
机头材质选择挤出成型机头的材质选择直接关系到机头的使用寿命和生产效率。
通常采用优质合金钢、特殊耐磨材料等制作机头,以增强机头的耐磨性和耐腐蚀性。
此外,对于特殊要求的挤出产品,还可以对机头进行表面涂层处理以提高使用寿命。
温度控制挤出成型机头在加工过程中需要保持恒定的温度,以确保挤出产品的物理性能和外观质量。
因此,机头应设计有合理的温度控制系统,可以实现精确的温度调节。
一般情况下,采用加热螺纹和冷却通道相结合的方式来实现对机头温度的精确控制。
清洁与维护挤出成型机头在生产过程中容易受到塑料材料残渣的堵塞,因此需要定期清洁和维护。
清洁机头时应谨慎操作,避免损坏机头表面,影响其挤出产品的质量。
定期检查机头的磨损情况,并根据需要进行及时更换。
综上所述,挤出成型机头的设计要点包括机头类型选择、几何结构设计、材质选择、温度控制以及清洁与维护等方面。
只有全面考虑这些因素,合理设计和维护机头,才能确保挤出产品的质量和生产效率,提高生产制造的竞争力。
第五章 塑料挤出机

二、 辅机
① 机头(口模):它是制件成型的主要部件,熔 融塑料通过它获得一定的几何截面和尺寸。
② 定型装臵:它的作用是将从机头中挤出的塑料 的既定形状稳定下来,对其进行精整,从而得 到更为精确的截面形状、尺寸和光亮的表面。 ③ 冷却装臵:由定型装臵出来的塑料在此得到充 分的冷却,获得最终的形状和尺寸。
塑化
挤出成形
冷却定形
挤出机工作过程如下:
塑料从料斗进入挤出机,在螺杆的转动作用下将其向前输 送,塑料在向前移动的过程中,受到 料筒的加热、螺杆的剪切 和压缩作用 使塑料熔融,并实现由 玻璃态、高弹态及粘流态 的 三态变化。
在加压的情况 下,使处于粘 流态的塑料通 过具有一定的 形状的 口模 而 成为截面与口 模形状相仿的 连续体 。 然后 冷却定型 为玻 璃态, 得到所 需的制件。
三、 按挤出机加工中是否排气
① 非排气式挤出机
② 排气式挤出机——可排出物料中的水分、溶 剂、不凝气体等。
图5-3 单螺杆挤出机
图5-4 卧式单螺杆挤出机结构图
1、机头连接法兰 2、过滤板 3、冷却水管 4、加热器 5、螺杆 6、料筒 7、液压泵 8、测速电动机 9、推力轴承 10、料斗 11、减速箱 12、螺杆冷却装置
图5-14 单螺杆塑料排气挤出机
5.1.4 单螺杆挤出机的技术参数与型号
一、单螺杆挤出机的技术参数
① 螺杆直径Ds:指螺杆的外径,单位为mm。 ② 螺杆长径比L/Ds:其中L为螺杆的工作部分长度,Ds 为螺杆直径。 ③ 螺杆的转速范围:Nmax~Nmin,单位为r/min。
④ 驱动电动机功率:P,单位为kW。
(第20讲)第四章 第九节 其它挤出机头设计

福建工程学院《塑料成型工艺及模具设计》
第四章 塑料挤塑成型模具
四、塑料网挤出机头 管状塑料网机头:由可分别单独旋转的芯棒和口模外 管状塑料网机头:由可分别单独旋转的芯棒和口模外 组成,口模和芯棒分别开设有相应的半圆孔( 圈组成,口模和芯棒分别开设有相应的半圆孔(或其它 形状孔),其余部分互相密合, ),其余部分互相密合 形状孔),其余部分互相密合,熔体仅能中半圆孔中挤 出(图4-9-6)。
模唇运动:当上、下模唇半圆孔对正时, 模唇运动:当上、下模唇半圆孔对正时,挤出为圆形线 正好形成网的结点,错开时,挤出的为网眼间的网线。 条,正好形成网的结点,错开时,挤出的为网眼间的网线。
福建工程学院《塑料成型工艺及模具设计》 第四章 塑料挤塑成型模具
四、塑料网挤出机头 塑料网孔形式:改变上、下模唇往复运动的方向、速 塑料网孔形式:改变上、下模唇往复运动的方向、 挤出速度则可形成不同的网型( 度、挤出速度则可形成不同的网型(图4-9-5)。
四、塑料网挤出机头 塑料网:分片状和管状塑料网。 塑料网:分片状和管状塑料网。 片状塑料网机头:由上下两片模唇组成, 片状塑料网机头:由上下两片模唇组成,模唇分别设有 相应的半圆孔(或其它断面形状的孔),且相互紧密接触, ),且相互紧密接触 相应的半圆孔(或其它断面形状的孔),且相互紧密接触, 下模唇可单独或同时做方向相反的往复运动。 上、下模唇可单独或同时做方向相反的往复运动。
塑料网孔形式:改变芯棒和口模圈的回转方向、 塑料网孔形式:改变芯棒和口模圈的回转方向、回转速 挤出速度则可形成不同的网型( 度、挤出速度则可形成不同的网型(图4-9-5)。
福建工程学院《塑料成型工艺及模具设计》 第四章 塑料挤塑成型模具
四、塑料网挤出机头 管状塑料网机头:图4-9-7所示;挤出设备见图4-9-8。 管状塑料网机头: 所示;挤出设备见图4
挤出塑料造粒机头的结构优化设计

作者简介:张友新(1958-),男,教授级高级工程师,主要从事模具设计、塑料管材加工及塑料改性研发工作。
收稿日期:2022-07-14挤出造粒机头的结构是挤出生产的核心部分,结构设计的合理性直接影响着物料的塑化,产品性能和生产效率,因此,研究设计挤出机头尤为重要。
为了更好优化造粒机头的结构设计,综合考虑了流道的结构,物料的塑化,设计了分流器。
在物料的流动稳定性,各料条出料速度的均匀性,设计了缓冲区。
为了防止挤出的高温料条不会纠缠或黏结在机头的出料板上,在机头上设计了一个出料倾斜面。
进一步为了提高产品性能,并防止料条在高温状态下被拉断,控制料条在玻璃化温度与熔融温度之间的条件下,对料条进行冷却,使料条处于在高弹态下进行分子取向拉伸,设计了在机头的出料板两端厚度中开设一条出风口。
经实践应用,优化设计的拉伸取向塑料挤出造粒机头结构,物料塑化均匀,料流稳定,表面光泽,经拉伸取向后,造粒料的物理性能明显得到提高。
1 挤出造粒成型工艺分析挤出塑料拉条造粒机包括挤出机、机头、冷却系统、切料机和包装机,热塑性树脂在挤出机加热后通过螺杆剪切输送使塑料受热熔体由螺旋运动通过机头变为直线运动,并进入机头充满模腔,在一定的压力作用下从出料板设置的出料孔挤出,挤出的料条再经过冷却,切粒制成所需的颗粒成品。
由于挤出的切粒料的配方体系有多种材料和助剂组成,物料的熔体指数不一定相同和相近,当熔融物料进入模腔内可能含有尚未塑化的塑料原料存于机头的模腔内,使尚未塑挤出塑料造粒机头的结构优化设计张友新(浙江伟星新型建材股份有限公司,浙江 临海 317000)摘要:针对现有技术的挤出塑料造粒机头在生产实际中存在的物料塑化不良,料条容易拉断,料条纠缠在一起或黏结在机头的出料板上等缺陷,进行了优化设计,对料条进行拉伸取向,通过在机头设计了分流器,吹风冷却装置,梯形储料缓冲槽等方面的改进,实现了对料条的拉伸取向,解决了料条的纠缠或黏结,实践证明,该机头结构的适应性更强,物料塑化和产品性能更好,其优化设计后的机头结构特点和实用性便一目了然。
第6章 塑料挤出模具(机头)设计 6.4~6.5(第24讲)

一、吹膜机头的分类及特点
(2)机头特点 ) 上吹法:泡管形状稳定,占地面积小,易生产折径大、 上吹法:泡管形状稳定,占地面积小,易生产折径大、厚 度大的薄膜;但要求厂房较高,不适用于粘度小的原料, 度大的薄膜;但要求厂房较高,不适用于粘度小的原料,不 利于薄膜冷却。 利于薄膜冷却。 下吹法:生产线速度较高,有利于薄膜的冷却, 下吹法:生产线速度较高,有利于薄膜的冷却,适用于粘 度小的原料,但不适于生产较薄的薄膜,设备安装位置高, 度小的原料,但不适于生产较薄的薄膜,设备安装位置高, 不便维修。 不便维修。 平吹法:引膜容易、操作方便、辅机结构简单; 平吹法:引膜容易、操作方便、辅机结构简单;但占地面 积大,膜管自重下垂,薄膜厚度不均, 积大,膜管自重下垂,薄膜厚度不均,不适用于生产折径大 的薄膜。 的薄膜。
第 24 讲 6.4 吹塑薄膜机头设计 一、吹膜机头的分类及特点 二、吹膜机头的结构设计
6.5 板材挤出机头设计 一、板片材挤出机头类型及特点 二、平缝式机头的设计要点
《塑料成型工艺与模具设计》 第6章 塑料挤出模具(机头)设计
6.4 吹塑薄膜机头设计
一、吹膜机头的分类及特点 (1)吹膜机头分类 ) 根据管膜牵引方向不同分为上吹、下吹和平吹三种。 根据管膜牵引方向不同分为上吹、下吹和平吹三种。 按机头结构分:芯棒式机头、十字机头、螺旋式机头、 按机头结构分:芯棒式机头、十字机头、螺旋式机头、 径向流道莲花瓣(或多流道)机头、旋转式机头等。 径向流道莲花瓣(或多流道)机头、旋转式机头等。
《塑料成型工艺与模具设计》
第6章 塑料挤出模具(机头)设计
4、径向流道吹膜机头(多流道或莲花瓣机头) 径向流道吹膜机头(多流道或莲花瓣机头)
特点: 特点: •机头高度短、体积小、重量轻,管 机头高度短、体积小、重量轻, 机头高度短 坯直径可达256mm 256mm; 坯直径可达256mm; •环隙宽度0.6~1.6mm; 环隙宽度0.6 1.6mm 环隙宽度0.6 1.6mm; •适用于吹塑大口径薄膜; 适用于吹塑大口径薄膜; 适用于吹塑大口径薄膜 •熔接痕多,机头流动阻力较大,不 熔接痕多,机头流动阻力较大, 熔接痕多 适于高粘度和热敏性的树脂。 适于高粘度和热敏性的树脂。
- 1、下载文档前请自行甄别文档内容的完整性,平台不提供额外的编辑、内容补充、找答案等附加服务。
- 2、"仅部分预览"的文档,不可在线预览部分如存在完整性等问题,可反馈申请退款(可完整预览的文档不适用该条件!)。
- 3、如文档侵犯您的权益,请联系客服反馈,我们会尽快为您处理(人工客服工作时间:9:00-18:30)。
塑料挤出机机头结构设计塑料挤出机机头结构设计摘要:挤出成型方法广泛应用于管材、棒材、异型材、中空制品以及单丝等产品的生产。
挤出机同时还可以对塑料进行混合、塑化、脱水、造粒、和喂料等准备工序或半成品加工。
因此挤出成型已成为最普遍的塑料成形加工方法之一。
挤出成型是在挤出机中通过加热、加压而使物料以流动状态连续通过口模成型的方法,是一种技术要求较高的成型方法。
挤出模的设计要求设计者对塑料特性的完全掌握和对挤出模具设计具有的丰富经验。
单螺杆挤出机做为应用范围最广泛的挤出机,而在设计过程中,实际遇到的问题很复杂,由于塑料的种类不同,它们的剪切速度、表面粘度不同,以及润滑剂、填充剂由于种类和配量的不同,其流动性也不同。
故挤出模的结构设计仍以实际经验为主,多数采用最终试模的方式确定其形状。
本设计中主要设计的是挤出模中各零件的工作面尺寸、外形尺寸、整体结构形式,由于塑料材质特性对于挤出模的要求非常的高,所以进行了主要零件的加工制造工艺的设计,还进行了机头和挤出主机的连接方式的设计。
关键词:挤出机;挤出模;硬质PVC;1绪论1.1挤出机的发展历程自第一台挤出机问世以来,挤出技术得到的良好快速的发展。
从开始的柱塞式到更为先进的螺杆式,从原始的手动操作到完全的自动控制,从产品单一到产品的多元化,挤出成型技术正逐渐成熟。
如今,挤出成型具有生产效率高,制造方便,可以连续化生产等特点,他、它在塑料成型加工工业中占有很重要的地位。
半个世纪以来,我国的塑料工业经历了从无到有,从小到大的发展过程,尤其是改革开放二十年来得到高速发展,已初步形成了部类齐全的工业体系,从产量上已跻身于世界先进行列。
塑料机械行业是为塑料工业提供技术装备的行业,强劲的市场需求促进塑料机械工业的发展。
挤出成型技术得到了很好的发展。
1.2挤出机的分类及挤出制品用途1.2.1 挤出机分类塑料挤出机按其螺杆数量分为单螺杆、双螺杆和多螺杆挤出机。
目前以单螺杆挤出机应用最为广泛,适宜于一般材料的挤出加工。
双螺杆挤出机由于具有由摩擦产生的热量较少、物料所受到的剪切比较均匀、螺杆的输送能力较大、挤出量比较稳定、物料在机筒内停留长,混合均匀。
单螺杆挤出机无论作为塑化造粒机械还是成型加工机械都占有重要地位。
其发展的主要标志在于其关键零件——螺杆的发展。
近几年以来,人们对螺杆进行了大量的理论和实验研究,至今已有近百种螺杆且已标准化。
常见的有分离型、剪切型、屏障型、分流型与波状型等。
从单螺杆发展来看,尽管近年来单螺杆挤出机已较为完善,但随着高分子材料和塑料制品不断的发展,还会涌现出更有特点的新型螺杆和特殊单螺杆挤出机。
从总体而言,单螺杆挤出机向着高速、高效、专用化方向发展。
1.2.2 挤出制品的用途热塑性塑料和部分热固性塑料适用于挤出成型。
其制品主要有管材、棒材、板材、异型材、薄膜、单丝、扁带和电线电缆等。
塑料挤出制品广泛应用于国民经济各个领域。
薄膜、中空制品、打包带等是包装材料的重要组成部分;农副业大量使用塑料薄膜作育秧薄膜、棚模;机械工业使用塑料棒材可以方便的加工各种零部件;建筑工业使用的挤出成型的制品越来越多,如墙壁装饰板、窗用密封条等;石油工业大量使用塑料管材作输油管道。
挤出机同时还可以对塑料进行混合、塑化、脱水、造粒、和喂料等准备工序或半成品加工。
因此挤出成型已成为最普遍的塑料成形加工方法之一。
1.3 挤出机的发展趋势1)模块化和专业化塑料挤出机模块化生产可以适应不同用户的特殊要求,缩短新产品的研发周期,争取更大的市场份额;而专业化生产可以将挤出成型装备的各个系统模块部件安排定点生产甚至进行全球采购,这对保证整期质量、降低成本、加速资金周转都非常有利。
2)高效、多功能化塑料挤出机的高效主要体现在高产出、低能耗、低制造成本方面。
在功能方面,螺杆塑料挤出机已不仅用于高分子材料的挤出成型和混炼加工,它的用途已拓宽到食品、饲料、电极、炸药、建材、包装、纸浆、陶瓷等领域。
3)大型化和精密化实现塑料挤出机的大型化可以降低生产成本,这在大型双螺杆塑料造粒机组、吹膜机组、管材挤出机组等方面优势更为明显。
国家重点建设服务所需的重大技术装备,大型乙烯工程配套的三大关键设备之一的大型挤压造粒机组长期依靠进口,因此必须加快国产化进程,满足石化工业发展需要。
4)智能化和网络化发达国家的塑料挤出机已普遍采用现代电子和计算机控制技术,对整个挤出过程的工艺参数如熔体压力及温度、各段机身温度、主螺杆和喂料螺杆转速、喂料量,各种原料的配比、电机的电流电压等参数进行在线检测,并采用微机闭环控制。
这对保证工艺条件的稳定、提高产品的精度都极为有利。
2 挤出模结构及功能挤出模又称挤出机机头。
塑料在经过螺杆和料筒后成为熔融态,再通过挤出机机头,经过挤出模的定型而产出产品。
在挤出机的整体结构中,机头应与主机相配合。
即使是性能良好的主机,若无相应的机头与之配合是很难生产出高质量的产品。
所以挤出模的设计好坏将直接影响挤出机的性能。
2.1 挤出模结构及功能2.1.1 挤出模结构挤出模的主要零件有口模、芯棒、过滤板、过滤网、分流器、分流器支架、调节螺钉、定型套和机头体。
各自作用如下:1)口模是成形塑件的外表面,2)芯棒是成形塑件的内表面,3)过滤板是将塑料熔体由螺旋运动变为直线运动并造成一定压力,促进熔体塑化均匀及支撑滤网的作用,4)过滤网主要是过滤杂质和造成一定压力,5)分流器是使通过它的熔体变成薄环状,平稳地进入成形区。
同时,进一步加热和塑化塑料,6)分流器支架主要用于支撑分流器和芯棒,同时也能对分流后的塑料熔体加强混合作用,7)定型套对成形管材进行冷却定型,以保证制品良好质量,正确的尺寸和几何形状,8)调节螺钉用来控制成形区内的口模和芯棒之间的间隙及同轴度,以保证挤出塑件壁厚的均匀,9)机头体用来组装机头各零件并与挤出机相连接。
2.2.2 挤出模功能挤出模做为挤出成型装置,其结构形式就决定其功能如何。
根据挤出成型特点知其主要功能如下:a:使来自挤出机的塑料熔体由螺旋运动转化为直线运动;主要是通过过滤板来完成的,b:通过模腔流道的剪切流动使塑料熔体进一步塑化均匀;这是由塑料粘度决定的,c:通过模腔几何形状与尺寸的变化产生成形压力,以使型材致密;主要是由于压缩比的存在,d:通过成形段及模唇的调节作用,获得所需截面形状的连续型材。
2.3 挤出模设计准则及设计步骤2.3.1挤出模设计准则根据挤出模的功能可知挤出机头的设计不但要满足塑料成型工艺的要求,而且其结构要简单,故确定具体设计方案如下:1)正确选择机头结构形式,应按照所要挤出的制品的原料和要求及成型工艺的特点,正确选用和确定机头结构形式;2)具有一定的成形功能和作用,机头应能将塑料熔体从挤出的螺旋运动转换成直线运动,并在机头内产生适当的压力;3)应设计出压缩区保证足够的压缩比;4)内腔呈光滑流线型,保证塑料熔体在机头内均匀平稳流动顺利挤出,且机头的截面变化要均匀,避免死角、凹槽等;5)要设计有调节装置;6)机头要有足够的刚度和强度,结构要简单、紧凑、与机筒连接紧密、装卸方便、易加工、易操作,同时机头设计成对称形状,以保证受热均匀;7)机头成型区应有正确的截面形状,设计时要合理的确定流道尺寸,控制成型长度,从而保证截面形状,保证制品质量;8)合理选择机头材料。
与塑料熔体相接触的部分,由于摩擦磨损及塑料成型时产生的气体对机头的腐蚀,机头体、口模、芯棒和分流器及支架等零件的材料应选取耐热、耐磨、耐腐蚀、韧性高、硬度高、热处理变形小及加工性能好的钢材和合金钢。
2.3.2 挤出模设计步骤根据以上设计原则,挤出模的设计不是简单的几何尺寸的计算,设计时需要确定机头中各零件的功能作用,同时要准确掌握挤出成型工艺特点。
设计步骤如下:1)根据设计要求了解材料材质特性并确定挤出机形式,2)计算口模内径和芯棒外径尺寸,3)确定过滤板出口处直径D0,4)确定拉伸比和压缩比,5)确定机头内其他尺寸,6)机头结构的具体设计,7)冷却定型套的设计与计算,8)机头主要零件的加工工艺设计,9)机头和挤出主机的连接方式的设计。
3 挤出模参数设计计算3.1材料材质特性根据任务书要求,我所设计的挤出机要加工的塑料是硬质聚氯乙烯。
硬质PVC主要性能:机械强度高,电气性能优良,化学稳定性好,粘度高。
其成型性能:非结晶材料,吸湿性小,流动性差,极易分解,在高温下与钢、铜接触更易分解。
高粘度使得与其相接触的零件表面粗糙度要求高,同时非结晶性、流动性差、极易分解等都是设计时必须考虑的因素。
硬质PVC的性能及成型性能决定了挤出机中所有与PVC接触的零件的性能要求要高,在设计过程中这些性能是这些零件的设计准则。
3.2 挤出机形式的确定根据任务书所给数据知挤出机型号为SJ-45。
即该挤出机为单螺杆,螺杆直径为45mm,机头为直通式。
直通式机头结构简单,容易制造,但经过分流器及分流器支架时形成的分流痕不易消除,其结构笨重、长度较大。
其主要特点:熔体在机头内挤出流向与挤出机螺杆平行。
再根据硬质PVC 材料的特性以及挤出加工的要求选择机头中与PVC直接接触的零件的材料为38CrMoALA(铬钼钢)。
3.3 挤出模各零件尺寸设计根据管材的挤出特点,对于不同塑料的管机头的主要零件尺寸及其工艺参数都有一定的限制,以保证挤出的管材质量及其优良的成型工艺。
本设计中采用的塑料是硬质PVC。
根据硬质PVC的性能特点可以确定一些零件在设计过程是用到的公式中的系数,同时可以确定挤出模的压缩比和分流器扩展角。
3.3.1挤出模各零件工作表面尺寸设计计算1、口模的设计计算口模是成型管材外部轮廓的机头零件,其结构如图,管材离开口模后,塑料会因为压力的解除当即发生离模膨胀,和长度收缩,是管材的断面积增大,且又因牵引和冷收缩的关系,管材的断面积又有缩小的趋势,这种增大和缩小综合作用的结果,难以从理论上正确计算,所以通常是根据口模与芯棒在出口端缩形成的空间截面积与挤出管材截面积之比,即所谓的拉伸比来计算口模成型段内径,或者根据其主要尺寸有口模内径D、定型长度L1、压缩段长度L2和压缩区锥角β。
尺寸的设计主要靠经验公式来确定:L=πR图1:口模结构图1)、口模内径D:D= d1/k 3-1式中: D——口模内径(mm)d1 ——塑料管材外径(mm)k——系数(见表1)表1系数k选取表2)、口模定型段长度L1:L1=(0.3~3.0)d1 3-2或L1=ct 3-3式中: L1——口模定型段长度(mm)d1——塑料管材外径(mm)c——系数(见表2)t——塑料管材壁厚(mm)表2系数c选取表3)、压缩区锥角β:压缩区的锥角一般在10°~60°范围内选取,当β过大时,挤出的管材表面会较粗糙,对于低粘度材料可选取较大值,反之取较小值。